Discover Top Benefits of Working with a Rice Mill Manufacturer (2025)
Introduction: Navigating the Global Market for rice mill manufacturer
In the quest for sourcing reliable rice mill manufacturers, international B2B buyers face a myriad of challenges, from identifying reputable suppliers to navigating complex logistics and varying quality standards. With rice being a staple food in many regions, including Africa, South America, the Middle East, and Europe, understanding the nuances of the global rice milling market is crucial for making informed purchasing decisions. This guide is designed to equip buyers with the essential knowledge they need to successfully navigate this competitive landscape.
Covering a comprehensive range of topics, the guide delves into different types of rice mills, their specific applications, and the vital considerations for supplier vetting. It provides insights into pricing structures, cost-saving strategies, and best practices for negotiation to ensure you get the most value for your investment. Additionally, we explore the latest technological advancements in rice milling, which can enhance productivity and efficiency for your operations.
By leveraging this guide, B2B buyers will gain a deeper understanding of the rice mill manufacturing sector, enabling them to select the right partners and make strategic decisions that align with their business goals. Whether you are a buyer from Thailand seeking the latest milling technology or a procurement officer in Spain looking for cost-effective solutions, this guide serves as an invaluable resource to streamline your sourcing process and mitigate risks in the global market.
Understanding rice mill manufacturer Types and Variations
Type Name | Key Distinguishing Features | Primary B2B Applications | Brief Pros & Cons for Buyers |
---|---|---|---|
Traditional Rice Mills | Manual operation, low capacity | Small-scale farming, local markets | Pros: Low initial investment; Cons: High labor costs, limited scalability. |
Modern Automated Mills | High capacity, mechanized processes | Large-scale production, export markets | Pros: High efficiency, consistent quality; Cons: High upfront costs, maintenance complexity. |
Mini Rice Mills | Compact design, suitable for small operations | Rural areas, cooperatives | Pros: Affordable, easy to operate; Cons: Limited output, may require frequent maintenance. |
Floating Rice Mills | Mobile units, adaptable to various locations | Disaster relief, remote areas | Pros: Flexibility, quick deployment; Cons: Potentially less durable, variable performance. |
Integrated Rice Processing Plants | Comprehensive processing capabilities | Large agribusinesses, export-oriented | Pros: All-in-one solution, maximizes efficiency; Cons: High capital investment, complex logistics. |
What are the Characteristics of Traditional Rice Mills?
Traditional rice mills are primarily characterized by their manual operation and lower production capacity. These mills are often found in rural areas, catering to small-scale farmers and local markets. B2B buyers looking to support local agriculture may find these mills appealing due to their lower initial investment. However, they come with high labor costs and limited scalability, making them less suitable for larger operations.
How Do Modern Automated Mills Enhance Production?
Modern automated rice mills utilize advanced technology to achieve high capacity and efficiency. They are designed for large-scale production and are often used in export markets. Buyers interested in maximizing output and ensuring consistent product quality will find these mills advantageous. However, the high upfront costs and potential maintenance complexity should be considered in the purchasing decision.
What Makes Mini Rice Mills Ideal for Small Operations?
Mini rice mills are compact and specifically designed for small-scale operations, making them suitable for rural areas and cooperatives. They offer affordability and ease of operation, appealing to buyers with limited budgets. While they are an excellent choice for localized production, their output is limited, and they may require more frequent maintenance, which could impact long-term viability.
How Do Floating Rice Mills Meet Specific Needs?
Floating rice mills are unique mobile units that can be deployed in various locations, making them ideal for disaster relief efforts or remote areas where infrastructure is lacking. Their flexibility allows for quick deployment, which is crucial in urgent situations. However, buyers should be aware that floating mills may be less durable and exhibit variable performance compared to stationary options.
What Are the Advantages of Integrated Rice Processing Plants?
Integrated rice processing plants offer a comprehensive solution for large agribusinesses and export-oriented operations. These facilities handle all aspects of rice processing, maximizing efficiency and minimizing logistical challenges. While they provide significant advantages in terms of production capacity and operational integration, the high capital investment and complexity of logistics can deter smaller buyers.
Related Video: Best Combined Rice Mill (Capacity – 1.5 ton per hour) New setup
Key Industrial Applications of rice mill manufacturer
Industry/Sector | Specific Application of Rice Mill Manufacturer | Value/Benefit for the Business | Key Sourcing Considerations for this Application |
---|---|---|---|
Food Processing | Production of rice flour and by-products | Diversifies product range and increases revenue | Quality of milling technology, capacity, and after-sales support |
Agricultural Export | Processing paddy for export | Enhances product quality and marketability | Compliance with international standards, efficiency, and cost |
Bioenergy | Utilizing rice husks for energy production | Reduces waste and creates additional revenue streams | Technology for husk processing, energy efficiency, and scalability |
Animal Feed Production | Producing rice bran for animal feed | Provides high-nutrition feed options | Nutritional value, sourcing of raw materials, and processing time |
Ethanol Production | Fermenting rice for biofuel | Supports renewable energy initiatives | Processing efficiency, technology compatibility, and ROI analysis |
How is Rice Mill Manufacturing Used in Food Processing?
In the food processing sector, rice mill manufacturers are instrumental in producing rice flour and various by-products. This application allows businesses to diversify their product offerings, catering to the growing demand for gluten-free and health-conscious food alternatives. By investing in advanced milling technology, companies can achieve a finer flour consistency and minimize waste, which directly enhances profitability. B2B buyers from Africa and South America should prioritize suppliers that offer robust technology and reliable after-sales support to ensure continuous operation.
What Role Does Rice Mill Manufacturing Play in Agricultural Export?
For agricultural exporters, rice mill manufacturers are critical in processing paddy for international markets. The quality of milling directly impacts the final product’s marketability, making it essential for exporters to invest in mills that adhere to international quality standards. This not only improves the product’s appeal but also helps in securing better pricing. Buyers from the Middle East and Europe should consider sourcing mills that provide comprehensive quality assurance and efficient processing capabilities to meet global demands.
How Can Rice Husk Be Used in Bioenergy?
Rice husks, a by-product of the milling process, can be transformed into bioenergy, providing an eco-friendly solution to waste management. Rice mill manufacturers equipped with technology for husk processing enable businesses to convert this waste into energy, thus creating additional revenue streams while supporting sustainability initiatives. B2B buyers should focus on sourcing mills that demonstrate energy-efficient processing solutions and scalability to meet future energy needs, especially in regions like Africa where renewable energy is gaining traction.
In What Ways is Rice Bran Utilized in Animal Feed Production?
Rice bran, a nutritious by-product of rice milling, is increasingly used in the animal feed industry. Rice mill manufacturers play a vital role in producing high-quality rice bran that meets the nutritional needs of livestock. This application is particularly beneficial for businesses looking to enhance their feed offerings with high-nutrition ingredients. Buyers from South America and Europe should evaluate suppliers based on the nutritional profile of the bran, the sourcing of raw materials, and processing timelines to ensure timely delivery and quality.
How is Rice Used in Ethanol Production?
Rice can be fermented to produce ethanol, making it a valuable resource in the renewable energy sector. Rice mill manufacturers contribute to this process by providing the necessary milling technology that optimizes starch extraction from rice grains. This application aligns with global trends toward renewable energy, enabling businesses to participate in sustainable practices. B2B buyers should assess the processing efficiency of mills and their compatibility with existing production systems to maximize return on investment in this sector.
3 Common User Pain Points for ‘rice mill manufacturer’ & Their Solutions
Scenario 1: Inconsistent Quality of Rice Processing Equipment
The Problem: One of the most pressing challenges faced by B2B buyers of rice mill manufacturing equipment is the inconsistency in product quality. Buyers may receive machinery that fails to meet the promised specifications or standards, leading to poor processing efficiency and reduced yield. This issue can cause significant financial losses, especially for buyers operating in competitive markets in Africa and South America, where margins are already thin. When the equipment malfunctions or underperforms, it not only hampers production but also affects the overall quality of the rice being processed, ultimately impacting customer satisfaction.
The Solution: To mitigate this issue, buyers should prioritize sourcing manufacturers with robust quality assurance processes. It’s advisable to request detailed product specifications and certifications, such as ISO standards, during the sourcing process. Additionally, buyers can benefit from visiting manufacturing facilities or attending industry trade shows to see the equipment firsthand. Establishing a strong relationship with the manufacturer can also facilitate better communication regarding quality expectations. Consider implementing a trial period for the equipment, where performance metrics can be evaluated before full-scale deployment. This proactive approach helps ensure that the equipment meets the required standards before significant investments are made.
Scenario 2: Lack of After-Sales Support and Technical Assistance
The Problem: B2B buyers often encounter difficulties with after-sales support once they purchase rice milling machinery. In regions like the Middle East and Europe, where advanced technology is integrated into rice mills, the lack of technical assistance can lead to prolonged downtimes when issues arise. Buyers may struggle to get timely repairs or maintenance support, affecting their operations and profitability. This gap in support can be particularly problematic for small to medium-sized enterprises that may not have in-house technical expertise.
The Solution: When evaluating potential rice mill manufacturers, buyers should thoroughly investigate the after-sales support services offered. This includes checking for warranties, available spare parts, and the accessibility of technical support. Buyers can request a detailed service level agreement (SLA) that outlines response times for service requests, maintenance schedules, and availability of on-site support. Furthermore, establishing a comprehensive training program for staff on equipment operation and troubleshooting can empower buyers to address minor issues independently, reducing dependence on external support. Engaging with manufacturers that provide remote monitoring services can also enhance operational efficiency, as they can identify issues before they escalate.
Scenario 3: Difficulty in Customizing Equipment for Local Needs
The Problem: International buyers often face challenges when trying to customize rice milling equipment to meet local agricultural practices or specific market demands. For example, rice varieties, moisture content, and local processing methods can vary significantly across regions such as Africa and South America. Standardized machinery may not adequately address these variations, leading to inefficiencies and subpar product quality.
The Solution: To overcome this challenge, buyers should engage with manufacturers who offer customizable solutions. Before making a purchase, it’s crucial to communicate specific processing requirements and local conditions to the manufacturer. Conducting thorough market research to understand the unique characteristics of the local rice varieties and processing techniques can inform these discussions. Collaborating with local agricultural experts can also provide insights into necessary modifications. Buyers should consider manufacturers that have a proven track record of working with diverse markets and can tailor their offerings accordingly. Additionally, establishing a partnership with the manufacturer during the design phase can ensure that the final product aligns with local needs, resulting in better performance and customer satisfaction.
Strategic Material Selection Guide for rice mill manufacturer
When selecting materials for rice mill manufacturing, it is crucial to consider properties that directly affect performance, durability, and cost-effectiveness. Below is an analysis of four common materials used in rice mill manufacturing, focusing on their key properties, advantages, disadvantages, and specific considerations for international B2B buyers.
What are the Key Properties of Stainless Steel for Rice Mill Manufacturing?
Stainless steel is a popular choice for rice mill components due to its excellent corrosion resistance and high-temperature tolerance. It typically withstands temperatures up to 800°C and pressures relevant to milling processes. The material’s non-reactive nature ensures that it does not contaminate the rice, maintaining product quality.
Pros & Cons: Stainless steel is highly durable and resistant to wear, making it ideal for long-term use. However, its higher cost compared to other metals can be a drawback for budget-conscious manufacturers. Additionally, the complexity of manufacturing processes can increase production timelines.
Impact on Application: Stainless steel is compatible with various media, including water and rice husks, making it suitable for different milling operations. Its hygienic properties are particularly important in regions with strict food safety regulations.
Considerations for International Buyers: Buyers from Africa, South America, the Middle East, and Europe should ensure compliance with international standards such as ASTM and DIN. In regions like Thailand, where rice milling is a significant industry, local preferences for stainless steel grades can influence material selection.
How Does Carbon Steel Compare for Rice Mill Components?
Carbon steel is another commonly used material in rice mills, known for its strength and toughness. It can handle high pressures and is often used in structural components of the milling machinery.
Pros & Cons: The primary advantage of carbon steel is its lower cost compared to stainless steel, making it an attractive option for manufacturers looking to minimize expenses. However, its susceptibility to corrosion can lead to shorter lifespans in humid environments, necessitating regular maintenance.
Impact on Application: Carbon steel is suitable for components that do not come into direct contact with food products, such as frames and supports. Its robustness is beneficial in heavy-duty applications.
Considerations for International Buyers: Buyers should be aware of the need for protective coatings or treatments to enhance corrosion resistance, especially in regions with high humidity. Compliance with local standards is also essential to ensure product safety and longevity.
What are the Advantages of Using Aluminum in Rice Mill Manufacturing?
Aluminum is increasingly being utilized in rice mill manufacturing due to its lightweight and excellent corrosion resistance. It typically performs well under moderate temperatures and pressures, making it suitable for various components.
Pros & Cons: The lightweight nature of aluminum allows for easier handling and installation, which can reduce labor costs. However, it may not be as durable as stainless or carbon steel under heavy loads, leading to potential wear and tear.
Impact on Application: Aluminum is ideal for components that require mobility or frequent adjustments, such as hoppers and conveyors. Its resistance to oxidation is beneficial in maintaining product integrity.
Considerations for International Buyers: Buyers should consider the specific grades of aluminum that meet local standards and regulations. In Europe, for instance, adherence to EN standards is crucial for compliance and safety.
Why is Plastic a Viable Option for Certain Rice Mill Components?
Plastic materials, particularly high-density polyethylene (HDPE) and polypropylene, are gaining traction in rice mill applications. These materials offer excellent chemical resistance and are lightweight, making them suitable for various non-structural components.
Pros & Cons: Plastics are cost-effective and resistant to moisture, which is advantageous in rice milling environments. However, they may not withstand high temperatures or heavy loads, limiting their use in certain applications.
Impact on Application: Plastic components are often used for storage bins, chutes, and other areas where corrosion resistance is essential. Their non-reactive nature ensures that they do not affect the quality of the rice.
Considerations for International Buyers: Buyers should ensure that the plastics used comply with food safety regulations in their respective countries. In regions like South America, where plastic recycling is gaining momentum, sourcing sustainable materials can also be an attractive option.
Summary Table of Material Selection for Rice Mill Manufacturing
Material | Typical Use Case for rice mill manufacturer | Key Advantage | Key Disadvantage/Limitation | Relative Cost (Low/Med/High) |
---|---|---|---|---|
Stainless Steel | Milling machinery components | Excellent corrosion resistance | Higher cost | High |
Carbon Steel | Structural supports | Lower cost | Susceptible to corrosion | Medium |
Aluminum | Hoppers and conveyors | Lightweight and easy to handle | Less durable under heavy loads | Medium |
Plastic | Storage bins and chutes | Cost-effective and moisture resistant | Limited temperature tolerance | Low |
This strategic material selection guide provides international B2B buyers with essential insights into the materials used in rice mill manufacturing, helping them make informed decisions that align with their operational needs and regional compliance standards.
In-depth Look: Manufacturing Processes and Quality Assurance for rice mill manufacturer
What Are the Key Stages in the Manufacturing Process for Rice Mills?
The manufacturing process for rice mills involves several critical stages that ensure the final product meets quality standards and fulfills operational requirements. Understanding these stages can help B2B buyers make informed decisions when selecting a supplier.
-
Material Preparation: This initial stage involves sourcing high-quality raw materials, primarily stainless steel and other alloys, which are essential for building durable machinery. Suppliers should provide documentation regarding the origins and quality certifications of these materials. International buyers should look for suppliers who adhere to globally recognized material standards, such as ASTM or EN.
-
Forming: In this stage, raw materials are shaped into components using various techniques such as cutting, bending, and welding. Advanced techniques like laser cutting and CNC machining are often employed to ensure precision. Buyers should inquire about the technology used in this phase, as it significantly impacts the efficiency and longevity of the rice mill.
-
Assembly: Once individual components are formed, they are assembled into larger units. This stage often involves intricate processes, including the installation of electrical systems, sensors, and control panels. B2B buyers should assess the assembly process for automation, as automated assembly can enhance consistency and reduce the likelihood of human error.
-
Finishing: The final stage involves surface treatment and coating to protect against corrosion and wear. Techniques such as powder coating and galvanization are commonly used. Buyers should ensure that the finishing processes meet international standards for durability, especially in regions with harsh environmental conditions.
What Quality Assurance Measures Should B2B Buyers Expect from Rice Mill Manufacturers?
Quality assurance is crucial in the manufacturing of rice mills, as it directly affects performance, reliability, and longevity. Understanding the quality control processes can help buyers ensure they are partnering with reputable suppliers.
-
International Standards Compliance: Suppliers should adhere to international quality management standards such as ISO 9001. This certification indicates that the manufacturer has established a quality management system that consistently meets customer and regulatory requirements. Buyers should request copies of these certifications to verify compliance.
-
Industry-Specific Certifications: In addition to ISO standards, industry-specific certifications such as CE marking for European markets or API standards for equipment in certain applications are vital. These certifications ensure that the products meet safety and performance criteria specific to the industry.
-
Quality Control Checkpoints:
– Incoming Quality Control (IQC): This involves inspecting raw materials upon arrival to ensure they meet the required specifications.
– In-Process Quality Control (IPQC): Continuous monitoring during the manufacturing process helps identify and rectify issues as they arise, reducing waste and ensuring product consistency.
– Final Quality Control (FQC): Before shipment, a thorough inspection is conducted to ensure that the finished product meets all specifications and standards. -
Common Testing Methods: Manufacturers often employ various testing methods, including:
– Dimensional Testing: Ensures components meet specified measurements.
– Functional Testing: Verifies that the machinery operates as intended.
– Stress Testing: Assesses the durability of components under operational conditions.
How Can B2B Buyers Verify Supplier Quality Control Practices?
Verification of a supplier’s quality control practices is essential for mitigating risks and ensuring product reliability. Here are actionable steps for B2B buyers:
-
Conduct Supplier Audits: Buyers should perform on-site audits of potential suppliers to evaluate their manufacturing processes and quality control systems. This allows for firsthand observation of their operational practices and adherence to quality standards.
-
Request Quality Assurance Reports: Suppliers should be able to provide detailed reports on their quality assurance processes, including data on defect rates, corrective actions taken, and compliance with relevant standards. These documents serve as evidence of a supplier’s commitment to quality.
-
Engage Third-Party Inspection Services: Hiring independent third-party inspectors can provide an unbiased assessment of the supplier’s quality control practices. This is particularly important for international buyers who may not have the resources for on-site evaluations.
-
Understand Quality Control Nuances: Different regions may have varying expectations regarding quality control. For instance, suppliers in Europe may be subject to stricter regulations than those in Africa or South America. Buyers should familiarize themselves with these nuances to ensure they are negotiating with suppliers who can meet their specific quality requirements.
What Are the Challenges and Considerations for B2B Buyers in Different Regions?
When sourcing rice mills, B2B buyers from Africa, South America, the Middle East, and Europe face unique challenges and considerations:
-
Regional Compliance Standards: Understanding the local regulations and compliance standards in the buyer’s region is critical. For example, in Europe, CE marking is mandatory for many types of machinery, while in South America, there may be different certifications required.
-
Supply Chain Logistics: Buyers should consider the logistical challenges of importing rice mills from abroad. Factors such as shipping times, customs regulations, and potential tariffs can impact the overall cost and delivery timeline.
-
Cultural Differences in Business Practices: Different regions have varied business customs and practices. Understanding these cultural nuances can facilitate smoother negotiations and foster better supplier relationships.
-
Technology and Innovation Trends: Buyers should stay updated on the latest technology trends in rice milling. Suppliers who invest in innovative technologies can provide more efficient and sustainable solutions, which may be particularly appealing to buyers looking to improve their operational efficiency.
By thoroughly understanding the manufacturing processes and quality assurance measures, B2B buyers can make well-informed decisions when selecting rice mill manufacturers, ultimately ensuring that they receive high-quality products that meet their operational needs.
Practical Sourcing Guide: A Step-by-Step Checklist for ‘rice mill manufacturer’
The process of sourcing a rice mill manufacturer involves several critical steps that ensure you partner with a reliable supplier capable of meeting your operational needs. This checklist is designed to guide international B2B buyers, particularly those from Africa, South America, the Middle East, and Europe, through the essential actions necessary for successful procurement.
Step 1: Define Your Technical Specifications
Clearly outlining your technical specifications is vital in ensuring that the rice mill meets your production requirements. Consider aspects such as milling capacity, energy efficiency, and the types of rice you plan to process. Having detailed specifications helps potential suppliers understand your needs and provide accurate proposals.
Step 2: Research Potential Suppliers
Conduct thorough research to identify a shortlist of potential rice mill manufacturers. Utilize online platforms, industry directories, and trade shows to gather information. Pay attention to suppliers with a proven track record in your region, as they will be more familiar with local regulations and market conditions.
Step 3: Verify Supplier Certifications
Before moving forward, it’s crucial to verify that suppliers possess the necessary certifications. Look for ISO certifications or local compliance certifications relevant to machinery and food processing. This step not only ensures quality but also indicates that the manufacturer adheres to international safety and operational standards.
Step 4: Evaluate Production Capabilities
Assess the production capabilities of each shortlisted supplier. Inquire about their manufacturing processes, technology used, and scalability options. Understanding their capacity to handle your volume requirements is essential, especially if you anticipate growth or fluctuations in demand.
Step 5: Request for Quotes and Proposals
Once you have narrowed down your options, request detailed quotes and proposals from your selected suppliers. Ensure that these documents include pricing, lead times, and warranty information. Comparing these proposals will help you gauge which supplier offers the best value while meeting your specifications.
Step 6: Conduct Site Visits or Virtual Tours
If feasible, conduct site visits or arrange virtual tours of the manufacturing facilities. This firsthand observation allows you to assess their operations, quality control measures, and overall working conditions. Observing the environment can provide insights into the reliability and professionalism of the supplier.
Step 7: Establish Clear Communication Channels
Effective communication is key to a successful partnership. Establish clear communication channels and protocols early on. Ensure that you have dedicated contacts within the supplier’s organization who can provide timely updates and address any concerns that may arise throughout the procurement process.
By following this step-by-step checklist, international B2B buyers can confidently navigate the sourcing process for rice mill manufacturers, ensuring they make informed decisions that align with their operational goals.
Comprehensive Cost and Pricing Analysis for rice mill manufacturer Sourcing
What Are the Key Cost Components in Sourcing Rice Mill Manufacturers?
When sourcing rice mill manufacturers, understanding the comprehensive cost structure is crucial for international B2B buyers. The primary cost components include:
-
Materials: The raw materials used in manufacturing rice mills, such as steel, electronics, and other components, significantly influence the overall cost. Fluctuations in global commodity prices can affect these costs, so it’s essential to monitor market trends.
-
Labor: Labor costs vary greatly by region. For instance, manufacturers in Southeast Asia might have lower labor costs compared to those in Europe. However, it’s important to consider the skill level and expertise required for specific manufacturing processes, as this can impact the quality and efficiency of production.
-
Manufacturing Overhead: This encompasses all indirect costs associated with production, including utilities, rent, and administrative expenses. Efficient management of overhead can lead to cost savings, which can be passed on to buyers.
-
Tooling: The cost of tools and machinery used in the manufacturing process can be substantial, especially for custom solutions. Buyers should inquire about tooling costs upfront, as these can affect the overall pricing structure.
-
Quality Control (QC): Implementing robust QC measures ensures that the rice mills meet international standards. While this might increase initial costs, it can reduce long-term expenses related to defects and returns.
-
Logistics: Transportation costs play a significant role in the total cost of ownership. These include shipping, customs, and any tariffs that may apply when importing machinery from another country.
-
Margin: Manufacturers typically include a profit margin in their pricing. Understanding the average margins in the industry can help buyers gauge whether a quote is reasonable.
How Do Price Influencers Affect Rice Mill Manufacturing Costs?
Several factors can influence the pricing of rice mill manufacturing:
-
Volume/MOQ (Minimum Order Quantity): Higher order volumes often lead to lower per-unit costs. Buyers should negotiate terms based on their anticipated needs to leverage better pricing.
-
Specifications/Customization: Custom features and specifications can significantly raise costs. Buyers should clearly communicate their requirements to avoid unexpected expenses.
-
Materials: The choice of materials impacts both the quality and cost. Higher-quality materials may increase upfront costs but can lead to savings through reduced maintenance and longer lifespan.
-
Quality and Certifications: Compliance with international quality standards and certifications can add to the cost but is often necessary for market acceptance. Buyers should weigh the benefits against the additional costs.
-
Supplier Factors: The reputation and reliability of suppliers can affect pricing. Established suppliers might charge a premium for their experience and quality assurance.
-
Incoterms: Understanding Incoterms is essential for determining responsibility for shipping costs, insurance, and customs duties. This can significantly affect the total price paid by the buyer.
What Tips Can Help Buyers Negotiate Better Prices?
When negotiating prices with rice mill manufacturers, consider the following actionable tips:
-
Conduct Thorough Market Research: Familiarize yourself with average pricing in the industry and regional variations. This knowledge will empower you during negotiations.
-
Focus on Total Cost of Ownership (TCO): Evaluate not just the purchase price but also long-term costs, including maintenance, operational efficiency, and potential downtime. A higher initial investment might be justified if it leads to lower TCO.
-
Build Relationships with Suppliers: Establishing long-term relationships can lead to better pricing and terms. Suppliers are often more willing to negotiate with repeat customers.
-
Be Transparent About Your Needs: Clearly communicate your requirements and budget constraints. This transparency can foster trust and lead to mutually beneficial arrangements.
-
Consider Alternative Suppliers: Don’t hesitate to explore multiple suppliers. Competitive quotes can enhance your bargaining power.
Conclusion: Why Understanding Cost and Pricing Analysis is Critical for International Buyers
Navigating the complexities of cost and pricing in the rice mill manufacturing sector is essential for international B2B buyers, especially those from Africa, South America, the Middle East, and Europe. By grasping the various cost components, pricing influencers, and employing effective negotiation strategies, buyers can make informed decisions that align with their operational needs and budget constraints.
Disclaimer: Prices and costs mentioned in this analysis are indicative and can vary significantly based on market conditions, supplier capabilities, and specific buyer requirements. Always seek tailored quotes and conduct due diligence before making purchasing decisions.
Alternatives Analysis: Comparing rice mill manufacturer With Other Solutions
Introduction to Alternative Solutions for Rice Milling
In the global agricultural landscape, the demand for efficient rice milling solutions is paramount. While traditional rice mill manufacturers offer a reliable means of processing rice, it’s crucial for B2B buyers to explore alternative technologies and methods that may better suit their operational needs. This analysis presents a comparative view of rice mill manufacturers against two viable alternatives: mobile rice milling units and automated rice processing systems.
Comparison Table: Rice Mill Manufacturer vs. Alternatives
Comparison Aspect | Rice Mill Manufacturer | Mobile Rice Milling Unit | Automated Rice Processing System |
---|---|---|---|
Performance | High throughput, consistent quality | Moderate throughput, adaptable | Very high throughput, precise quality control |
Cost | Higher initial investment, long-term ROI | Lower initial investment, variable costs | High initial investment, lower operational costs |
Ease of Implementation | Requires infrastructure setup | Quick setup, portable | Complex setup, requires technical expertise |
Maintenance | Regular maintenance needed | Low maintenance, easy to service | High maintenance, specialized technicians required |
Best Use Case | Large-scale production | Rural areas, small-scale operations | Large-scale, automated production facilities |
What Are the Advantages and Disadvantages of Mobile Rice Milling Units?
Mobile rice milling units are an innovative solution tailored for rural and small-scale operations. These units are designed for flexibility and ease of transport, allowing users to mill rice close to the source. The primary advantage is the lower initial investment, making it accessible for smaller enterprises or farmers’ cooperatives. However, they come with moderate throughput and may not provide the same quality consistency as traditional mill manufacturers. This option is ideal for regions where access to large-scale milling infrastructure is limited.
How Do Automated Rice Processing Systems Enhance Efficiency?
Automated rice processing systems represent the pinnacle of technological advancement in rice milling. These systems utilize advanced machinery to achieve high throughput and ensure precise quality control. While the initial investment is substantial, the operational costs are lower due to reduced labor and increased efficiency. The challenge lies in the complexity of the setup, which requires specialized technical knowledge. These systems are best suited for large-scale production facilities that demand high efficiency and consistent output.
Conclusion: How to Choose the Right Rice Milling Solution for Your Business
When deciding between a rice mill manufacturer and its alternatives, B2B buyers must consider several factors, including the scale of operations, budget constraints, and specific processing needs. For large enterprises looking for high throughput and quality control, automated systems may provide the best long-term investment. Conversely, small-scale operations or those in rural areas might find mobile rice milling units more practical and cost-effective. Ultimately, a thorough analysis of operational requirements and market conditions will guide buyers in selecting the most appropriate rice milling solution.
Essential Technical Properties and Trade Terminology for rice mill manufacturer
What Are the Key Technical Properties to Consider When Sourcing Rice Mill Equipment?
When purchasing rice milling equipment, understanding the technical specifications is crucial for ensuring optimal performance and longevity. Here are several key properties to consider:
-
Material Grade
– The material grade refers to the type of steel or alloy used in the construction of the rice mill. Common materials include stainless steel and carbon steel. The choice of material affects durability, resistance to corrosion, and overall maintenance costs. For buyers in regions with high humidity, such as parts of Africa and South America, stainless steel is often preferred due to its longevity and lower maintenance needs. -
Capacity
– Capacity indicates the volume of rice that can be processed within a specific timeframe, typically measured in tons per hour (TPH). This specification is vital for businesses aiming to meet market demand without over-investing in machinery. For instance, a mill with a capacity of 1 TPH may suffice for small-scale operations, while larger enterprises in Europe may require equipment capable of processing 5 TPH or more. -
Tolerance Levels
– Tolerance levels refer to the permissible limits of variation in the dimensions of the components. High tolerance levels are essential for ensuring the efficient operation of the mill, as even slight deviations can lead to increased wear and tear. Buyers should prioritize equipment that maintains tight tolerances to minimize operational disruptions and maximize yield. -
Energy Efficiency
– Energy efficiency ratings indicate how much energy the mill consumes relative to its output. Efficient machines not only reduce operational costs but also align with sustainability goals, which are increasingly important in global markets. B2B buyers should evaluate energy consumption metrics to understand the long-term cost implications. -
Automation Features
– Automation features include programmable logic controllers (PLCs), sensor-based monitoring, and automated cleaning systems. These technologies enhance productivity and reduce labor costs. For international buyers, particularly in the Middle East and Europe, investing in automation can lead to significant operational improvements and cost savings. -
Maintenance Requirements
– Understanding the maintenance needs of the equipment is essential for ensuring continuous operation. Key considerations include the frequency of required maintenance, availability of spare parts, and ease of access to components. Buyers should inquire about the manufacturer’s support services and the availability of local technicians.
What Are Common Trade Terms Relevant to Rice Mill Manufacturing?
Familiarity with industry jargon is critical for effective communication and negotiation in the B2B landscape. Here are some essential terms:
-
OEM (Original Equipment Manufacturer)
– An OEM is a company that produces parts and equipment that may be marketed by another manufacturer. Understanding OEM relationships can help buyers identify reputable suppliers and ensure they are sourcing high-quality components. -
MOQ (Minimum Order Quantity)
– MOQ refers to the smallest quantity of a product that a supplier is willing to sell. This term is crucial for buyers, as it can affect inventory management and cash flow. Buyers should clarify MOQs early in negotiations to avoid unexpected costs. -
RFQ (Request for Quotation)
– An RFQ is a document sent to suppliers requesting pricing information for specific products or services. It is a standard practice in B2B transactions and helps buyers compare offers systematically. Crafting a clear and detailed RFQ can lead to more accurate quotes. -
Incoterms (International Commercial Terms)
– Incoterms are predefined international trade terms that clarify the responsibilities of buyers and sellers in a transaction. Understanding these terms helps buyers in Africa and South America navigate shipping costs, risks, and responsibilities effectively. -
Lead Time
– Lead time refers to the time taken from placing an order to the delivery of the product. For international buyers, understanding lead times is essential for planning and managing supply chain logistics effectively. -
Warranty Period
– The warranty period is the timeframe during which a manufacturer is responsible for repairing or replacing defective equipment. Buyers should carefully evaluate warranty terms, as they reflect the manufacturer’s confidence in their product quality.
By understanding these essential technical properties and trade terms, international B2B buyers can make informed decisions when sourcing rice mill equipment, ultimately enhancing their operational efficiency and competitiveness in the market.
Navigating Market Dynamics and Sourcing Trends in the rice mill manufacturer Sector
What Are the Current Market Dynamics and Key Trends in the Rice Mill Manufacturer Sector?
The global rice mill manufacturer sector is currently influenced by several key drivers, including rising demand for rice, technological advancements, and increasing mechanization in agriculture. With Asia being the largest producer and consumer, markets in Africa, South America, the Middle East, and Europe are also experiencing growth as they seek to enhance their local production capabilities. Notably, countries like Thailand and Spain are at the forefront, leveraging innovative machinery and efficient processing techniques to improve yield and reduce waste.
Emerging B2B tech trends are transforming the landscape of rice milling. Automation, IoT, and AI are becoming integral in enhancing productivity and monitoring quality. For international buyers, particularly those from developing regions, adopting these technologies can lead to better operational efficiency and cost reduction. Additionally, there is a noticeable shift towards digital platforms for sourcing equipment, allowing buyers to compare products, read reviews, and access global suppliers more easily.
Furthermore, as consumer preferences evolve, there is increasing pressure on manufacturers to ensure quality and traceability in their supply chains. International buyers are now focusing on suppliers who can provide detailed information about their products, from sourcing to processing, which aligns with the growing trend of transparency in B2B transactions.
How Is Sustainability and Ethical Sourcing Impacting the Rice Mill Manufacturer Sector?
Sustainability is no longer just a buzzword; it is a crucial factor for B2B buyers in the rice mill manufacturer sector. The environmental impact of rice milling, particularly in terms of water usage and waste management, is significant. Manufacturers that prioritize sustainable practices can not only reduce their ecological footprint but also appeal to a growing segment of environmentally conscious buyers.
Ethical sourcing is equally important, as international buyers are increasingly aware of the social implications of their procurement decisions. This includes understanding the labor conditions in supply chains and the sourcing of raw materials. Certifications such as Fair Trade and organic can enhance a manufacturer’s credibility and appeal in the global market, especially in regions like Europe where consumers are willing to pay a premium for sustainably sourced products.
Moreover, adopting ‘green’ technologies in rice milling, such as energy-efficient machinery and waste recycling systems, can lead to significant cost savings and improved operational efficiency. For international buyers, partnering with manufacturers who prioritize sustainability not only aligns with corporate social responsibility goals but also positions them favorably in a competitive market.
What Is the Historical Context of the Rice Mill Manufacturer Sector?
The rice mill manufacturer sector has evolved significantly over the past century. Initially characterized by manual milling processes, the industry has transitioned to more mechanized operations, particularly post-World War II. This shift was driven by the need for increased efficiency and the ability to meet the burgeoning global demand for rice.
In recent decades, advancements in technology have revolutionized rice milling, introducing automated systems that enhance precision and reduce labor costs. The introduction of modern milling equipment has allowed manufacturers to improve product quality and consistency, catering to the diverse needs of international markets. This evolution underscores the importance of staying abreast of technological trends for B2B buyers looking to invest in reliable and efficient rice milling solutions.
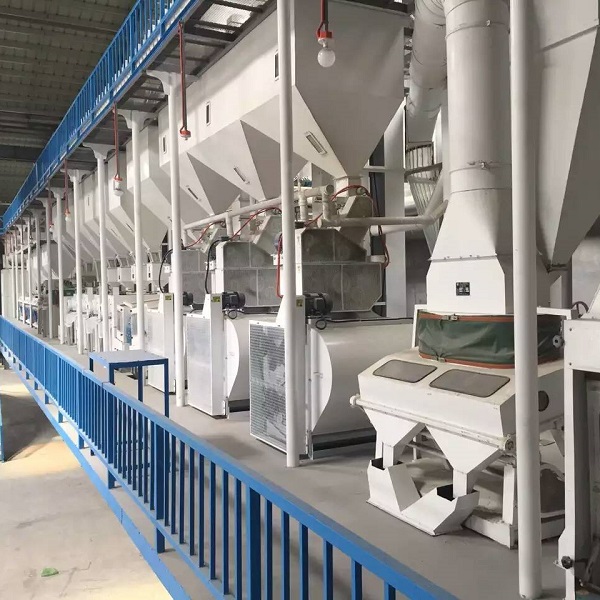
A stock image related to rice mill manufacturer.
Frequently Asked Questions (FAQs) for B2B Buyers of rice mill manufacturer
-
How do I choose the right rice mill manufacturer for my business needs?
Selecting the right rice mill manufacturer involves evaluating several factors. Start by assessing the manufacturer’s reputation and track record in the industry. Look for testimonials and case studies from existing clients, particularly those in regions similar to yours, such as Africa or South America. Additionally, consider the technological capabilities of the equipment, customization options, after-sales support, and warranty terms. It’s also beneficial to request a visit to their facility if possible, to see the production process firsthand and to build trust. -
What are the typical minimum order quantities (MOQs) when sourcing rice mills?
Minimum order quantities (MOQs) can vary significantly between manufacturers. Generally, MOQs for rice mills can range from a single unit for smaller manufacturers to several units for larger companies. When negotiating, communicate your business needs clearly; some manufacturers may offer flexibility based on your long-term purchasing commitments or the potential for future orders. Always inquire about the MOQ upfront to avoid any surprises during the procurement process. -
What payment terms should I expect when working with rice mill manufacturers?
Payment terms can differ widely among rice mill manufacturers, influenced by factors such as the size of the order and the relationship with the supplier. Common arrangements include a deposit upfront (typically 30-50%) with the balance due before shipment or upon delivery. It’s crucial to clarify payment methods accepted (e.g., bank transfer, letter of credit) and any applicable currency exchanges. Always ensure that the payment terms are documented in a formal contract to protect your interests. -
How can I ensure quality assurance (QA) when sourcing rice mills?
To ensure quality assurance when sourcing rice mills, request detailed specifications and certifications from the manufacturer. Many reputable manufacturers will have ISO certifications or other industry-standard quality certifications. It’s advisable to conduct factory audits or inspections, either personally or through a third-party service. Additionally, consider negotiating for a trial run or a pilot project to test the equipment’s performance before committing to a full order. -
What logistics considerations should I keep in mind when importing rice mills?
Logistics play a crucial role in the procurement of rice mills, particularly for international buyers. Evaluate shipping options, including freight costs, shipping times, and customs clearance procedures specific to your country. Collaborate with logistics experts or freight forwarders who have experience in handling agricultural machinery. Ensure that the manufacturer provides all necessary shipping documents and complies with international shipping regulations to avoid delays. -
Are there customization options available for rice mills?
Most rice mill manufacturers offer customization options to meet specific operational needs. Customizations may include adjustments in milling capacity, design modifications, and the inclusion of additional features like automation or energy-efficient technologies. When discussing your requirements, provide detailed specifications and inquire about the manufacturer’s past customization projects. This can give you insights into their flexibility and expertise in delivering tailored solutions. -
What are the key features to consider in a rice mill?
When evaluating rice mills, consider features that enhance efficiency and productivity. Key features include milling capacity, energy consumption, ease of operation, maintenance requirements, and the quality of the final product. Look for mills equipped with advanced technology, such as automated controls and monitoring systems, which can reduce labor costs and improve output consistency. Additionally, ensure the mill can handle the specific types of rice you plan to process. -
How do I evaluate the reliability of a rice mill supplier?
To evaluate the reliability of a rice mill supplier, conduct thorough research on their history and performance in the market. Check for industry certifications, customer reviews, and case studies to gauge their reputation. Engage in direct communication to assess their responsiveness and willingness to provide support. Establishing a relationship with existing clients can also provide insights into the supplier’s reliability and the quality of their customer service.
Important Disclaimer & Terms of Use
⚠️ Important Disclaimer
The information provided in this guide, including content regarding manufacturers, technical specifications, and market analysis, is for informational and educational purposes only. It does not constitute professional procurement advice, financial advice, or legal advice.
While we have made every effort to ensure the accuracy and timeliness of the information, we are not responsible for any errors, omissions, or outdated information. Market conditions, company details, and technical standards are subject to change.
B2B buyers must conduct their own independent and thorough due diligence before making any purchasing decisions. This includes contacting suppliers directly, verifying certifications, requesting samples, and seeking professional consultation. The risk of relying on any information in this guide is borne solely by the reader.
Strategic Sourcing Conclusion and Outlook for rice mill manufacturer
In the ever-evolving landscape of the rice milling industry, strategic sourcing emerges as a pivotal element for international B2B buyers. By prioritizing quality, cost-efficiency, and supplier reliability, businesses can significantly enhance their operational performance. Understanding the regional nuances—such as local demand in Africa, import regulations in South America, and technological advancements in Europe—will allow buyers to make informed decisions that align with their unique market needs.
What are the key factors to consider when sourcing rice mill equipment? It’s essential to evaluate not only the technological capabilities of manufacturers but also their after-sales support and spare parts availability. Establishing strong partnerships with reputable suppliers can lead to long-term benefits, including improved production efficiency and reduced downtime.
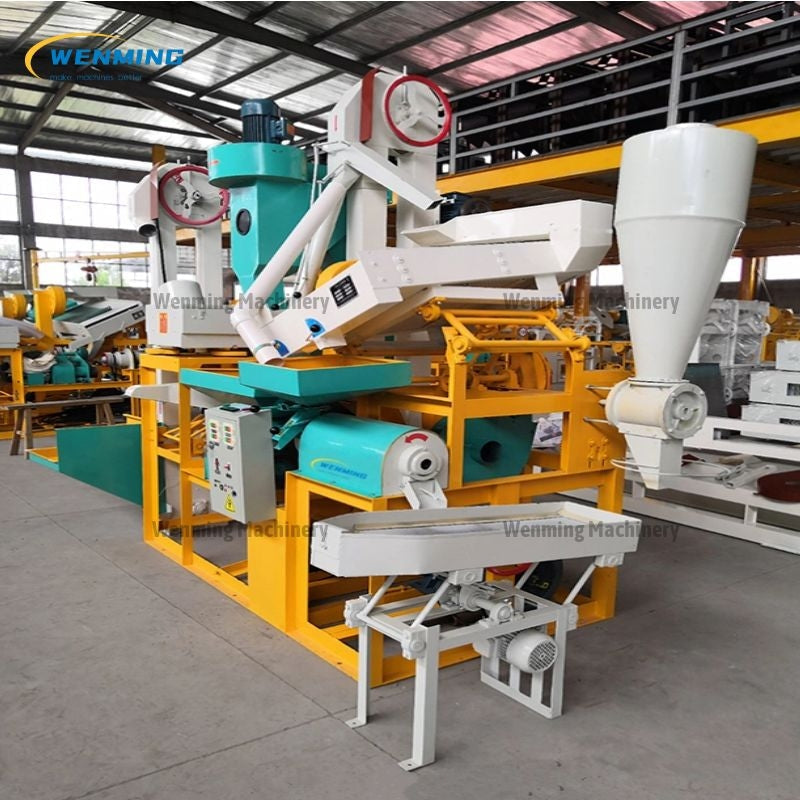
A stock image related to rice mill manufacturer.
Looking ahead, the demand for sustainable and innovative rice milling solutions will only continue to grow. Buyers are encouraged to leverage data-driven insights and market research to identify emerging trends and technologies. By taking proactive steps now, international buyers can position themselves for success in a competitive market. Embrace strategic sourcing as a tool to not only meet current needs but also to drive future growth and sustainability in your operations.