Discover Top Benefits of Working with an Abrasive Manufacturer (2025)
Introduction: Navigating the Global Market for abrasive manufacturer
In the rapidly evolving landscape of global trade, sourcing high-quality abrasive manufacturers can pose significant challenges for international B2B buyers. With the increasing demand for precision engineering and efficient manufacturing processes, understanding the nuances of abrasive materials becomes crucial. This guide delves into the diverse types of abrasives available, their applications across various industries, and the factors that influence sourcing decisions. By providing insights into supplier vetting, cost considerations, and market trends, we aim to equip buyers from regions such as Africa, South America, the Middle East, and Europe—specifically in countries like Egypt and Colombia—with the knowledge necessary to make informed purchasing decisions.
Navigating the complexities of the abrasive market requires a strategic approach. This guide not only highlights the essential characteristics of different abrasives—such as natural versus synthetic options—but also discusses how to assess supplier reliability and quality assurance practices. Furthermore, we explore the cost implications of sourcing abrasives and offer tips on negotiating favorable terms. By the end of this guide, B2B buyers will be empowered with actionable insights to streamline their procurement processes, reduce risks, and ultimately enhance their operational efficiencies. Whether you’re looking to optimize your supply chain or seeking innovative abrasive solutions, our comprehensive resource is designed to meet your needs in today’s competitive market.
Understanding abrasive manufacturer Types and Variations
Type Name | Key Distinguishing Features | Primary B2B Applications | Brief Pros & Cons for Buyers |
---|---|---|---|
Bonded Abrasives | Composed of abrasive grains bonded with a matrix | Grinding, cutting, polishing | Pros: Durable, effective for heavy-duty tasks. Cons: Can be expensive; requires specific machinery. |
Coated Abrasives | Abrasive grains attached to a flexible backing material | Sanding, finishing, surface preparation | Pros: Versatile, easy to use. Cons: Shorter lifespan compared to bonded abrasives. |
Superabrasives | Made from synthetic materials like diamond and CBN | Precision cutting, grinding hard materials | Pros: Exceptional performance, longer lifespan. Cons: Higher initial investment; requires specialized equipment. |
Loose Abrasives | Free-flowing abrasive particles without a binding agent | Blasting, cleaning, polishing | Pros: Cost-effective, customizable for various applications. Cons: Requires careful handling and containment. |
Specialty Abrasives | Tailored formulations for specific industries or applications | Aerospace, automotive, electronics | Pros: Highly effective for niche applications. Cons: Limited availability; may require minimum order quantities. |
What Are Bonded Abrasives and Their B2B Applications?
Bonded abrasives are composed of abrasive grains that are firmly held together by a binding matrix, often made of materials such as resin or ceramic. These abrasives are ideal for heavy-duty applications like grinding, cutting, and polishing, making them a staple in manufacturing and metalworking industries. When purchasing bonded abrasives, buyers should consider the type of machinery they have, as these products often require specific setups and can be more costly than other types.
How Do Coated Abrasives Differ in Usage?
Coated abrasives consist of abrasive grains that are adhered to a flexible backing material, such as paper or cloth. This type of abrasive is widely used for sanding and surface finishing, making it suitable for woodworking and automotive refinishing applications. Buyers should evaluate the specific grit sizes and backing materials needed for their projects, as these factors can significantly influence the performance and lifespan of the product.
Why Choose Superabrasives for Precision Work?
Superabrasives, which include materials like diamond and cubic boron nitride (CBN), are engineered for high-performance applications requiring precision cutting and grinding, especially on hard materials. These abrasives are favored in industries such as aerospace and automotive manufacturing. While they offer exceptional durability and efficiency, buyers must be prepared for a higher initial investment and ensure they have the necessary equipment to utilize these advanced materials effectively.
What Are the Benefits of Using Loose Abrasives?
Loose abrasives are free-flowing particles that can be utilized for various applications, including blasting and polishing. Their versatility makes them a cost-effective option for many industries. However, buyers should be mindful of the handling and containment requirements, as loose abrasives can create dust and waste if not managed properly. Customization options are often available, allowing companies to tailor their abrasive solutions to specific needs.
What Makes Specialty Abrasives Unique for Specific Industries?
Specialty abrasives are designed with formulations tailored for specific applications, such as aerospace or electronics manufacturing. These abrasives provide targeted performance, enhancing efficiency in specialized tasks. However, buyers should consider the availability and potential minimum order quantities, as these products may not be as widely stocked as standard abrasives. Understanding the unique requirements of their industry will help buyers make informed decisions when sourcing specialty abrasives.
Related Video: Variations In Construction Projects Explained
Key Industrial Applications of abrasive manufacturer
Industry/Sector | Specific Application of Abrasive Manufacturer | Value/Benefit for the Business | Key Sourcing Considerations for this Application |
---|---|---|---|
Metal Fabrication | Precision Grinding and Finishing | Enhanced product quality and surface finish | Consistency in grit size and material compatibility |
Automotive Manufacturing | Sanding and Surface Preparation for Components | Improved adhesion for coatings and longevity | Availability of specialized abrasives for automotive needs |
Construction and Renovation | Concrete Cutting and Surface Preparation | Increased efficiency and reduced labor costs | Durability of abrasives in harsh environments |
Electronics Manufacturing | Wafer Polishing and Surface Cleaning | High precision and minimal defect rates | Cleanroom compliance and contamination control |
Aerospace and Defense | Surface Treatment for Components | Enhanced performance and safety standards | Compliance with industry regulations and certifications |
How is Abrasive Manufacturing Used in Metal Fabrication?
In the metal fabrication industry, abrasive manufacturers play a crucial role in precision grinding and finishing processes. These abrasives are essential for achieving a high-quality surface finish on various metal components. By using the right abrasives, businesses can significantly reduce the risk of defects and improve the overall quality of their products. For international buyers, it is critical to ensure that the abrasives sourced maintain consistent grit size and are compatible with the specific metals being processed, especially in regions like Africa and South America where local suppliers may have varying product standards.
What Are the Applications of Abrasives in Automotive Manufacturing?
In automotive manufacturing, abrasives are primarily used for sanding and surface preparation of components before painting or coating. This application is vital for ensuring proper adhesion and longevity of finishes on vehicles. The right abrasive materials can enhance the durability of the surface and reduce the likelihood of rust or corrosion. Buyers, particularly from the Middle East and Europe, should consider sourcing specialized abrasives tailored for automotive applications, keeping in mind factors like availability and performance in extreme temperatures.
How Are Abrasives Used in Construction and Renovation Projects?
Abrasive manufacturers provide essential tools for concrete cutting and surface preparation in the construction and renovation sectors. These abrasives improve efficiency by enabling faster cutting and leveling of surfaces, leading to reduced labor costs and project timelines. For B2B buyers in regions like Africa, where construction projects are booming, sourcing durable and effective abrasives that can withstand harsh conditions is critical. Understanding the environmental impact and longevity of the abrasives is also vital for compliance with local regulations.
What Role Do Abrasives Play in Electronics Manufacturing?
In the electronics manufacturing sector, abrasive manufacturers supply products for wafer polishing and surface cleaning. This application requires high precision, as even minor defects can result in significant failures in electronic components. Buyers must ensure that the abrasives sourced comply with cleanroom standards to prevent contamination. For international buyers in South America and Europe, it’s important to partner with manufacturers who can guarantee consistent quality and adherence to stringent industry regulations to maintain product integrity.
Why Are Abrasives Important in Aerospace and Defense Industries?
In the aerospace and defense industries, abrasives are used for surface treatment of components, ensuring enhanced performance and adherence to safety standards. The quality of abrasives directly impacts the reliability and durability of critical parts. For B2B buyers in these sectors, sourcing abrasives that comply with strict industry regulations and certifications is essential. Considerations include the abrasives’ performance under extreme conditions and their compatibility with advanced materials commonly used in aerospace applications.
Related Video: Industrial Cleaning Applications for Dry Ice Blasting
3 Common User Pain Points for ‘abrasive manufacturer’ & Their Solutions
Scenario 1: Inconsistent Quality of Abrasives
The Problem:
B2B buyers often face challenges with inconsistent quality in abrasive products. For companies in sectors such as metalworking and construction, the performance of abrasives is crucial for maintaining production efficiency and product quality. An abrasive that wears too quickly or fails to deliver the expected finish can lead to increased downtime, wasted materials, and ultimately, dissatisfied customers. This problem is particularly acute for buyers in regions like Africa and South America, where local suppliers may not adhere to stringent quality standards.
The Solution:
To combat quality inconsistencies, buyers should establish clear specifications and performance benchmarks when sourcing abrasives. This includes detailed discussions with manufacturers about the grit size, bonding agents, and material composition. Buyers should also request samples for testing before placing larger orders. Implementing a robust supplier evaluation process, including quality audits and certifications (like ISO), can ensure that manufacturers meet required standards. Regular communication with suppliers about performance issues can also help in refining product offerings and ensuring that quality remains consistent over time.
Scenario 2: High Cost of Abrasives Affecting Profit Margins
The Problem:
High abrasive costs can significantly impact profit margins, especially for small to medium-sized enterprises (SMEs) in the Middle East and Europe. When abrasive materials are priced too high, it can lead to cost-cutting measures that compromise quality or production timelines. Buyers often struggle to balance cost with the need for high-performance abrasives, leading to tough decisions that may affect their competitive edge in the market.
The Solution:
Buyers can alleviate cost pressures by exploring bulk purchasing agreements or long-term contracts with manufacturers. Negotiating pricing based on consistent order volumes can yield better rates. Additionally, consider alternatives such as purchasing direct from manufacturers instead of through distributors to eliminate markup costs. Investing in higher-quality abrasives that last longer may also reduce overall expenses in the long run, as they minimize the frequency of replacements and maintenance downtime. Conducting a total cost of ownership analysis can help buyers understand the long-term savings associated with investing in quality abrasives.
Scenario 3: Difficulty in Finding the Right Abrasive for Specific Applications
The Problem:
Many B2B buyers encounter the challenge of selecting the right abrasive for specific applications. With a multitude of options available, from aluminum oxide to silicon carbide, the decision-making process can become overwhelming. This is particularly relevant for businesses in diverse sectors such as automotive or aerospace, where the wrong choice can lead to surface damage and additional costs. Buyers in regions like Egypt and Colombia may lack access to comprehensive resources or expert guidance to make informed decisions.
The Solution:
To navigate this complexity, buyers should invest time in understanding their specific application requirements. Engaging with technical experts from abrasive manufacturers can provide valuable insights tailored to unique needs. Buyers should also utilize application charts and technical data sheets provided by manufacturers to match the right abrasive with their processes. Conducting trials with different abrasives under real working conditions can yield practical data on performance, helping to refine choices. Additionally, building a relationship with a knowledgeable distributor or manufacturer can facilitate access to ongoing support and recommendations for future projects.
Strategic Material Selection Guide for abrasive manufacturer
When selecting materials for abrasive manufacturing, international B2B buyers must consider a variety of factors that impact performance, cost, and compliance. Below is an analysis of four common materials used in abrasive products, focusing on their properties, advantages and disadvantages, application impacts, and specific considerations for buyers from Africa, South America, the Middle East, and Europe.
What Are the Key Properties of Aluminum Oxide in Abrasives?
Aluminum oxide is one of the most widely used materials in abrasive manufacturing due to its excellent hardness and durability. It has a high temperature and pressure rating, making it suitable for heavy-duty applications. Additionally, it exhibits good corrosion resistance, which is vital for maintaining performance in various environments.
Pros & Cons: The key advantages of aluminum oxide include its long lifespan and effectiveness in grinding and cutting applications. However, it can be more expensive than other materials, and the manufacturing process can be complex, requiring specialized equipment.
Impact on Application: Aluminum oxide is compatible with a wide range of media, including metals, plastics, and ceramics, making it versatile for different industries.
Considerations for International Buyers: Buyers should ensure compliance with local standards such as ASTM and DIN, particularly in regions like Europe where regulations may be stringent. Understanding the local market’s preferences for abrasive types can also influence purchasing decisions.
How Does Silicon Carbide Compare for Abrasive Applications?
Silicon carbide is another popular abrasive material known for its exceptional hardness and sharpness. It performs well under high temperatures and is particularly effective on hard materials like glass and ceramics.
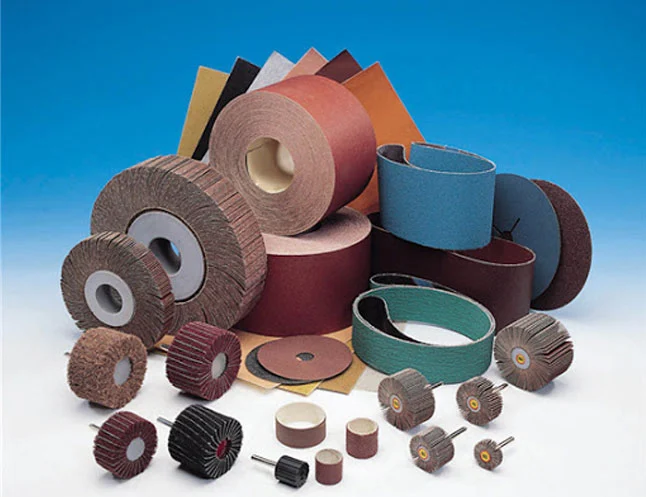
A stock image related to abrasive manufacturer.
Pros & Cons: The primary advantage of silicon carbide is its ability to cut through tough materials quickly, making it ideal for applications requiring precision. However, it is more brittle than aluminum oxide, which can lead to breakage during manufacturing or use.
Impact on Application: Silicon carbide is particularly suited for applications in the automotive and electronics industries, where precision is crucial. Its compatibility with various substrates enhances its usability.
Considerations for International Buyers: Buyers in regions such as the Middle East and Africa should consider the availability of silicon carbide and its cost implications, as it may be subject to import tariffs or local market fluctuations.
What Are the Advantages of Ceramic Abrasives?
Ceramic abrasives are engineered materials designed for high-performance applications. They offer excellent durability and are resistant to wear, making them suitable for heavy grinding and finishing operations.
Pros & Cons: The main advantage of ceramic abrasives is their ability to maintain sharpness longer than traditional materials, leading to reduced downtime. However, they can be more costly to produce, which may affect pricing strategies.
Impact on Application: Ceramic abrasives are particularly effective in the metalworking industry, where they are used for grinding and finishing applications that require high precision.
Considerations for International Buyers: Buyers should evaluate the total cost of ownership, including potential savings from reduced tool wear. Compliance with international standards is also crucial, especially for buyers in Europe and South America, where quality assurance is paramount.
Why Choose Garnet for Eco-Friendly Abrasive Solutions?
Garnet is a natural abrasive material that is gaining popularity due to its eco-friendly characteristics. It is non-toxic and does not produce harmful dust, making it a safer choice for workers.
Pros & Cons: The key advantage of garnet is its environmental friendliness, coupled with good performance in waterjet cutting applications. However, it may not be as durable as synthetic abrasives, leading to higher consumption rates.
Impact on Application: Garnet is particularly effective in applications involving waterjet cutting and surface preparation, especially in industries focused on sustainability.
Considerations for International Buyers: Buyers in environmentally conscious markets, such as those in Europe, may prioritize garnet for its eco-friendly properties. Understanding local regulations regarding material sourcing and environmental impact can also influence purchasing decisions.
Summary Table of Abrasive Materials
Material | Typical Use Case for abrasive manufacturer | Key Advantage | Key Disadvantage/Limitation | Relative Cost (Low/Med/High) |
---|---|---|---|---|
Aluminum Oxide | Grinding metals and ceramics | High durability and hardness | Higher manufacturing complexity | Medium |
Silicon Carbide | Precision cutting in automotive industries | Exceptional cutting efficiency | Brittle nature can lead to breakage | High |
Ceramic | Heavy grinding and finishing operations | Maintains sharpness over time | Higher production costs | High |
Garnet | Waterjet cutting and surface preparation | Eco-friendly and non-toxic | Less durable than synthetic options | Medium |
This guide provides a comprehensive overview of the strategic material selection process for abrasive manufacturers. By understanding the properties, advantages, and limitations of each material, international B2B buyers can make informed decisions that align with their operational needs and compliance requirements.
In-depth Look: Manufacturing Processes and Quality Assurance for abrasive manufacturer
What Are the Main Stages of the Manufacturing Process for Abrasives?
The manufacturing of abrasives is a complex and meticulous process that involves several critical stages to ensure high-quality products. Understanding these stages can help international B2B buyers make informed decisions when selecting suppliers.
Material Preparation: How Are Raw Materials Selected and Processed?
The first step in the manufacturing process is material preparation, which involves the selection and processing of raw materials such as corundum, silicon carbide, and garnet. Manufacturers typically analyze the mineral properties of these materials to ensure they meet specific performance standards. This stage may include crushing, screening, and grinding the raw materials to achieve the desired particle size.
Additionally, the quality of the raw materials directly impacts the performance of the final abrasive product. Buyers should inquire about the sources of raw materials and whether suppliers conduct thorough testing to ensure consistency and quality.
Forming: What Techniques Are Used to Shape Abrasives?
Once the materials are prepared, they undergo the forming stage. This can involve various techniques, including:
- Pressing: Using hydraulic or mechanical presses to shape the abrasive into desired forms.
- Casting: Pouring a molten mixture into molds to create specific shapes.
- Bonding: Combining abrasives with bonding agents to enhance durability.
The choice of technique often depends on the intended application of the abrasive product. Buyers should assess whether the supplier utilizes advanced technology and equipment in this stage to ensure precision and quality.
Assembly: How Are Abrasives Assembled for Final Products?
The assembly stage involves the integration of different components, such as backing materials and bonding agents, to create the final abrasive product. This can include attaching abrasives to discs, belts, or wheels, depending on the end-use.
Buyers should consider the supplier’s capabilities in terms of customization and scalability. A manufacturer that can adapt to specific requirements and produce both standard and custom abrasive products can offer a significant advantage.
Finishing: What Processes Ensure the Quality of Abrasives?
Finishing processes are crucial for enhancing the performance and aesthetics of abrasives. This stage may involve:
- Surface Treatment: Techniques such as coating or polishing to improve durability and performance.
- Quality Inspections: Performing thorough inspections to detect any defects or inconsistencies.
Buyers should inquire about the finishing techniques used by suppliers and whether they adhere to industry standards to ensure that the abrasives meet their specific performance requirements.
What Are the Key Quality Assurance Standards for Abrasive Manufacturers?
Quality assurance (QA) is essential in the abrasive manufacturing industry to ensure that products meet both customer expectations and regulatory requirements. Understanding the relevant standards can guide B2B buyers in their supplier evaluations.
Which International Standards Should B2B Buyers Consider?
ISO 9001 is the most widely recognized international quality management standard. It outlines criteria for a quality management system and emphasizes continuous improvement and customer satisfaction. Manufacturers certified under ISO 9001 demonstrate their commitment to quality and process efficiency.
In addition to ISO standards, industry-specific certifications like CE marking (for compliance with European safety standards) and API certification (for the oil and gas industry) are crucial. These certifications indicate that the products meet specific regulatory requirements and performance standards.
What Are the Key Quality Control Checkpoints in Abrasive Manufacturing?
Quality control (QC) involves systematic monitoring and testing at various stages of the manufacturing process. Key checkpoints include:
- Incoming Quality Control (IQC): Assessing raw materials before production to ensure they meet specifications.
- In-Process Quality Control (IPQC): Monitoring the manufacturing process to identify any deviations from quality standards.
- Final Quality Control (FQC): Conducting tests on finished products to ensure they meet quality benchmarks before shipment.
B2B buyers should ask suppliers about their QC processes and whether they maintain records of inspections and test results.
How Can B2B Buyers Verify Supplier Quality Assurance Practices?
Verifying the quality assurance practices of abrasive manufacturers is crucial for ensuring reliable partnerships. Buyers should consider several strategies:
What Auditing Methods Can Buyers Use to Assess Supplier Quality?
Conducting audits of potential suppliers can provide valuable insights into their manufacturing and quality control processes. Buyers can perform:
- On-site Audits: Visiting the manufacturing facility to observe processes and practices firsthand.
- Documentation Reviews: Examining quality control records, certifications, and compliance reports.
Buyers from Africa, South America, the Middle East, and Europe should also be aware of regional compliance requirements and how they may affect the supplier’s operations.
How Can Buyers Utilize Third-Party Inspections?
Engaging third-party inspection services can offer an unbiased assessment of a supplier’s quality practices. These services can conduct inspections at various stages of production and provide detailed reports. This is particularly beneficial for international buyers who may not have the resources to perform in-depth audits themselves.
What Are Common Testing Methods for Abrasive Products?
Testing methods for abrasives can vary based on the product type and intended application. Common tests include:
- Hardness Tests: Evaluating the abrasive’s ability to withstand wear and tear.
- Bond Strength Tests: Measuring the adhesion strength between the abrasive and its backing.
- Grain Distribution Analysis: Ensuring uniformity in particle size and distribution for consistent performance.
B2B buyers should inquire about the specific testing methods used by suppliers and request test results to validate product quality.
How Do Quality Assurance Nuances Impact International B2B Buyers?
International buyers, especially from diverse regions such as Africa, South America, the Middle East, and Europe, must navigate varying regulations and standards. Understanding local compliance requirements and how they align with international standards can facilitate smoother transactions.
Buyers should also consider the implications of language barriers and cultural differences when negotiating quality assurance practices. Clear communication regarding quality expectations is essential to avoid misunderstandings and ensure product satisfaction.
Conclusion: How Can International Buyers Ensure Quality in Abrasive Manufacturing?
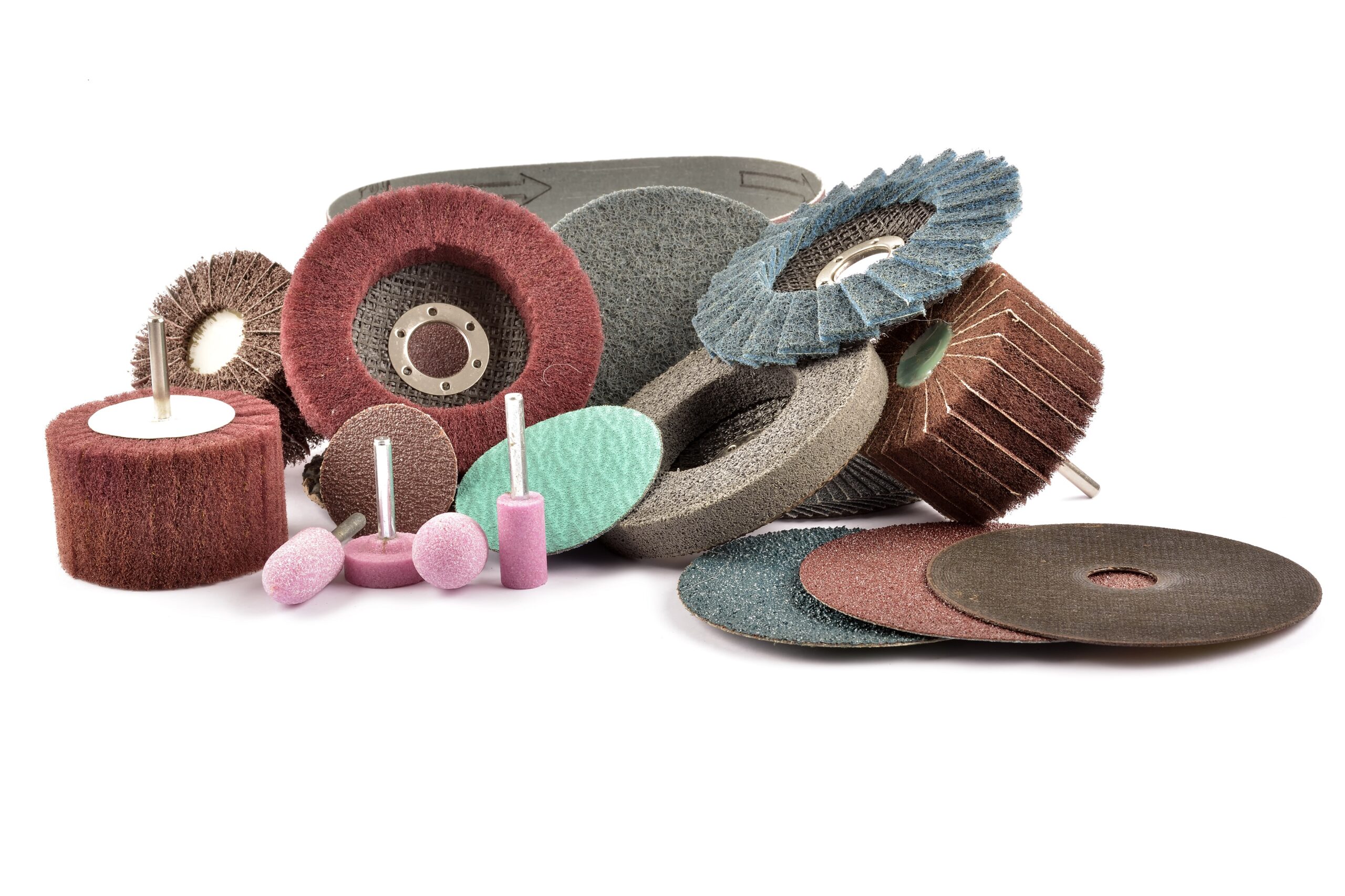
A stock image related to abrasive manufacturer.
In summary, B2B buyers looking to source abrasives should take a comprehensive approach to evaluate manufacturing processes and quality assurance practices. By understanding the key stages of manufacturing, relevant standards, and effective verification methods, buyers can make informed decisions and establish reliable partnerships with abrasive manufacturers.
Practical Sourcing Guide: A Step-by-Step Checklist for ‘abrasive manufacturer’
The following practical sourcing guide provides actionable steps for international B2B buyers looking to procure abrasive manufacturing solutions. This checklist is designed to streamline the sourcing process, ensuring that buyers from regions like Africa, South America, the Middle East, and Europe can make informed decisions.
Step 1: Define Your Technical Specifications
Start by clearly outlining the technical specifications required for your abrasive materials. This includes factors such as grit size, bond type, and the specific applications for which the abrasives will be used. A well-defined specification will help you communicate effectively with potential suppliers and ensure that the products meet your operational needs.
- Consider the application: Different applications (e.g., grinding, cutting, polishing) may require unique abrasive characteristics.
- Research industry standards: Familiarize yourself with industry standards to ensure compatibility with your machinery and processes.
Step 2: Conduct Market Research
Understanding the market landscape is essential for identifying potential suppliers. Research the leading abrasive manufacturers in your target regions and analyze their market presence, product offerings, and customer reviews.
- Utilize online resources: Leverage platforms like LinkedIn, industry forums, and trade publications to gather insights on suppliers.
- Attend trade shows: Participate in relevant trade exhibitions to meet suppliers face-to-face and assess their offerings firsthand.
Step 3: Evaluate Potential Suppliers
Before committing to any supplier, it’s crucial to conduct a thorough evaluation. Request company profiles, case studies, and references from other buyers within your industry.
- Check their credentials: Verify certifications such as ISO 9001, which indicate a commitment to quality management.
- Assess production capabilities: Ensure the supplier can meet your volume requirements and timelines.
Step 4: Request Samples
Once you have shortlisted potential suppliers, request samples of their abrasive products. Testing samples will allow you to evaluate the quality and performance against your specifications.
- Test in real conditions: Use the samples in your actual production environment to assess their performance.
- Evaluate durability and efficiency: Measure how well the abrasives perform under your specific operational conditions.
Step 5: Negotiate Terms and Pricing
When you’ve identified a suitable supplier, initiate negotiations regarding pricing, payment terms, and delivery schedules. Clear communication at this stage is crucial to avoid misunderstandings later on.
- Discuss bulk purchasing discounts: If you plan to order in large quantities, inquire about potential discounts or favorable payment terms.
- Clarify shipping and logistics: Understand the shipping options available, especially for international buyers, to avoid delays.
Step 6: Establish a Quality Assurance Process
Implement a quality assurance process to monitor the performance of the abrasives post-purchase. This step is essential to maintain product quality and consistency.
- Set performance benchmarks: Define key performance indicators (KPIs) for the abrasives based on your operational goals.
- Plan for regular reviews: Schedule periodic assessments of the supplier’s performance and product quality to ensure ongoing satisfaction.
Step 7: Build a Long-Term Relationship
Finally, focus on building a long-term relationship with your chosen supplier. Strong partnerships can lead to better pricing, priority service, and access to new products.
- Communicate regularly: Maintain open lines of communication to address any concerns promptly.
- Collaborate on innovations: Work together on product developments that can enhance your operations.
By following this step-by-step checklist, B2B buyers can streamline their sourcing process and make informed decisions when procuring abrasive manufacturing solutions.
Comprehensive Cost and Pricing Analysis for abrasive manufacturer Sourcing
What Are the Key Cost Components in Abrasive Manufacturing?
When sourcing abrasives, understanding the comprehensive cost structure is critical for international B2B buyers. The primary components of the cost structure include:
-
Materials: The choice of raw materials, such as alumina, silicon carbide, or diamond, significantly impacts the cost. High-performance materials may come at a premium but can offer better durability and efficiency.
-
Labor: Labor costs can vary greatly depending on the region of the manufacturer. For example, countries in Africa and South America may offer lower labor costs compared to Europe, but this can also affect the quality and consistency of production.
-
Manufacturing Overhead: This includes costs related to utilities, facility maintenance, and administrative expenses. Efficient manufacturing processes can minimize overhead, leading to more competitive pricing.
-
Tooling: The initial investment in tooling and equipment can be substantial. However, high-quality tooling can enhance production efficiency and product quality, ultimately impacting the pricing of abrasives.
-
Quality Control (QC): Rigorous QC processes ensure that products meet international standards. The costs associated with QC can influence the final pricing of abrasives, especially if certifications like ISO are required.
-
Logistics: Shipping and handling costs are crucial, particularly for international buyers. Factors such as distance, shipping method, and freight rates play a significant role in the total cost.
-
Margin: Manufacturers will include a profit margin, which can vary based on market demand and competitive landscape. Understanding the typical margins in different regions can aid in negotiation.
How Do Price Influencers Affect Abrasive Manufacturing Costs?
Several factors can influence pricing when sourcing abrasives. Key influencers include:
-
Volume and Minimum Order Quantity (MOQ): Higher order volumes often lead to better pricing due to economies of scale. Buyers should negotiate MOQs that align with their needs while maximizing cost efficiency.
-
Specifications and Customization: Custom abrasives tailored to specific applications may incur additional costs. Understanding the balance between customization and standard products can help buyers optimize their spending.
-
Material Quality and Certifications: Products that meet higher quality standards or come with certifications can command higher prices. It’s essential for buyers to assess whether these certifications add value to their operations.
-
Supplier Factors: The reputation and reliability of suppliers can significantly affect pricing. Established suppliers with proven track records may charge a premium, but this can lead to better overall value through reliability and support.
-
Incoterms: The chosen Incoterms dictate the responsibilities of buyers and sellers in shipping and logistics. Understanding the implications of different Incoterms can help buyers avoid unexpected costs.
What Are Effective Buyer Tips for Negotiating Abrasive Manufacturing Prices?
For international B2B buyers, particularly from regions like Africa, South America, the Middle East, and Europe, here are actionable tips:
-
Negotiate Based on Total Cost of Ownership (TCO): Evaluate not just the purchase price but also the long-term costs associated with quality, reliability, and maintenance. This approach can justify a higher upfront cost if it leads to lower TCO.
-
Seek Volume Discounts: If your business has the capacity, consider consolidating orders to achieve better pricing. Suppliers are often willing to offer discounts for bulk purchases.
-
Understand Pricing Nuances: Each region may have unique pricing dynamics influenced by local economic conditions, currency fluctuations, and supply chain issues. Stay informed about these factors to negotiate effectively.
-
Build Relationships with Suppliers: Establishing long-term relationships can lead to better pricing and terms. Suppliers are more likely to offer favorable conditions to reliable partners.
Disclaimer on Indicative Prices
While this analysis provides a framework for understanding costs and pricing in abrasive manufacturing, actual prices can vary significantly based on market conditions, specific supplier agreements, and regional factors. Buyers are encouraged to conduct thorough market research and engage in direct negotiations to obtain the most accurate pricing tailored to their needs.
Alternatives Analysis: Comparing abrasive manufacturer With Other Solutions
Understanding Alternatives to Abrasive Manufacturers in B2B Solutions
In the competitive landscape of industrial manufacturing, the choice of abrasives is crucial for productivity and cost-effectiveness. However, businesses must consider various alternatives to traditional abrasive manufacturers to optimize their processes. This analysis provides a comparative overview of abrasive manufacturers against two viable alternatives: laser cutting technology and waterjet cutting systems.
Comparison Table of Abrasive Solutions
Comparison Aspect | Abrasive Manufacturer | Laser Cutting Technology | Waterjet Cutting Systems |
---|---|---|---|
Performance | High material removal rate, effective on hard materials | Precision cutting, minimal heat-affected zone | Versatile material compatibility, no thermal distortion |
Cost | Generally lower initial cost but may incur higher long-term costs due to consumables | Higher initial investment, but lower operational costs | Moderate initial cost, but high operational and maintenance costs |
Ease of Implementation | Relatively easy to integrate into existing processes | Requires specialized training and setup | Complex setup and requires skilled operators |
Maintenance | Moderate maintenance, regular replacement of abrasives needed | Low maintenance; mainly software updates | High maintenance due to pumps and nozzles |
Best Use Case | Metal fabrication, woodworking, and surface finishing | Thin metals and intricate designs | Thick materials and complex shapes |
In-Depth Analysis of Alternatives
How Does Laser Cutting Technology Compare to Abrasive Manufacturing?
Laser cutting technology utilizes focused light beams to cut materials with high precision. Its primary advantage lies in its ability to create intricate designs and cuts with minimal heat-affected zones, making it ideal for applications requiring high precision. However, the initial investment is significant, and the technology demands specialized training for operators. For businesses focused on reducing waste and achieving precise cuts, laser cutting may offer a compelling alternative despite its higher upfront costs.
What Are the Benefits and Drawbacks of Waterjet Cutting Systems?
Waterjet cutting systems employ high-pressure water jets mixed with abrasives to slice through various materials. This method excels in versatility, capable of cutting metals, ceramics, glass, and even food products without introducing thermal distortions. However, it comes with a moderate initial investment coupled with high operational costs, particularly for maintenance and replacement of wear parts. Businesses that require cutting thick materials or complex shapes may find waterjet systems more beneficial, although the need for skilled operators can pose a challenge.
Conclusion: How Can B2B Buyers Choose the Right Solution?
Selecting the appropriate solution among abrasive manufacturers, laser cutting, and waterjet cutting systems depends on several factors, including the specific applications, budget constraints, and the required precision. B2B buyers from regions like Africa, South America, the Middle East, and Europe should assess their operational needs, potential ROI, and long-term maintenance requirements. By carefully evaluating these aspects, businesses can make informed decisions that align with their production goals and enhance overall efficiency.
Essential Technical Properties and Trade Terminology for abrasive manufacturer
When engaging with abrasive manufacturers, understanding the essential technical properties and trade terminology is crucial for international B2B buyers. This knowledge not only aids in product selection but also enhances negotiation and communication with suppliers.
What Are the Key Technical Properties of Abrasives?
1. Material Grade
Material grade refers to the quality of the abrasive material used, such as aluminum oxide or silicon carbide. Each grade has specific hardness and durability characteristics, impacting performance in various applications. For buyers in Africa and South America, selecting the right material grade ensures optimal cost-effectiveness and efficiency in manufacturing processes.
2. Grit Size
Grit size indicates the size of the abrasive particles. It is typically measured in microns or grit numbers, with lower numbers representing coarser abrasives and higher numbers indicating finer abrasives. Choosing the appropriate grit size is vital for achieving the desired finish on materials, affecting both product quality and production speed.
3. Bonding Agent
The bonding agent is the material that holds the abrasive grains together, which can be resin, rubber, or ceramic. The choice of bonding agent influences the performance and lifespan of the abrasive product. Buyers should consider the specific applications—whether cutting, grinding, or polishing—to select a suitable bonding agent that meets their operational needs.
4. Tolerance
Tolerance refers to the permissible limit of variation in the dimensions of the abrasive product. High-precision applications, especially in industries such as automotive and aerospace, require tighter tolerances. Understanding tolerance specifications is essential for ensuring compatibility with machinery and achieving desired outcomes.
5. Hardness
Hardness measures the resistance of the abrasive material to deformation or scratching. It is usually assessed using standardized tests. For B2B buyers, selecting abrasives with appropriate hardness levels is critical for specific applications, as it directly affects wear rates and efficiency in material removal processes.
What Are Common Trade Terms in the Abrasive Manufacturing Industry?
1. OEM (Original Equipment Manufacturer)
OEM refers to companies that produce parts or equipment that may be marketed by another manufacturer. In the context of abrasives, understanding OEM relationships can help buyers identify reliable suppliers who provide high-quality products tailored to specific machinery requirements.
2. MOQ (Minimum Order Quantity)
MOQ indicates the smallest quantity of an item that a supplier is willing to sell. For buyers, understanding MOQ is essential for budgeting and inventory management. It can also influence negotiations, particularly for smaller companies or those just entering the market.
3. RFQ (Request for Quotation)
An RFQ is a document issued by a buyer to solicit price quotes from suppliers for specific products or services. For international B2B buyers, submitting a well-structured RFQ can lead to better pricing and terms, making it a crucial tool in procurement processes.
4. Incoterms (International Commercial Terms)
Incoterms are standardized international trade terms that define the responsibilities of buyers and sellers in shipping and logistics. Familiarity with Incoterms helps buyers understand shipping costs, risks, and delivery responsibilities, facilitating smoother transactions across borders.
5. Lead Time
Lead time refers to the time taken from placing an order to the delivery of goods. Understanding lead times is vital for supply chain planning and ensures that production schedules are met. Buyers should clarify lead times with suppliers to avoid disruptions in their operations.
By familiarizing themselves with these technical properties and trade terms, international B2B buyers can make informed decisions, negotiate effectively, and foster successful partnerships with abrasive manufacturers.
Navigating Market Dynamics and Sourcing Trends in the abrasive manufacturer Sector
What Are the Current Market Dynamics and Key Trends in the Abrasive Manufacturer Sector?
The abrasive manufacturing sector is undergoing significant transformation driven by global economic shifts and technological advancements. Key market dynamics include a growing demand for high-performance abrasives in diverse industries such as automotive, aerospace, and construction. This is particularly evident in emerging markets across Africa, South America, the Middle East, and Europe, where industrialization is accelerating. International B2B buyers must stay informed about the increasing preference for customized solutions that cater to specific applications, as manufacturers increasingly focus on product innovation and differentiation.
Another trend reshaping the sector is the integration of advanced technologies like artificial intelligence (AI) and automation in manufacturing processes. These technologies not only enhance production efficiency but also improve product quality and consistency, which are critical for competitive advantage. Additionally, the rise of e-commerce platforms has transformed sourcing practices, allowing buyers to access global suppliers more easily, facilitating price comparisons, and enhancing supply chain transparency.
Buyers from Africa and South America should also be aware of the shifting trade policies and tariffs that can affect sourcing strategies. Understanding local regulations and the implications of international trade agreements will be crucial in optimizing procurement processes and ensuring compliance.
How Important Is Sustainability and Ethical Sourcing in the Abrasive Manufacturing Industry?
Sustainability has become a focal point for many industries, including abrasive manufacturing. The environmental impact of abrasive production processes, particularly concerning resource extraction and waste generation, is prompting international buyers to prioritize suppliers with sustainable practices. Ethical sourcing is not just a regulatory requirement; it is increasingly a market demand, as stakeholders—including consumers and investors—expect businesses to demonstrate corporate social responsibility.
Buyers should look for manufacturers who utilize ‘green’ certifications such as ISO 14001 or those that adhere to sustainability standards like the Global Reporting Initiative (GRI). These certifications indicate that a manufacturer is committed to reducing its environmental footprint and maintaining ethical supply chains. Moreover, the utilization of eco-friendly materials, such as recycled abrasives or biodegradable options, can also enhance a company’s market appeal and align with the values of environmentally conscious consumers.
As markets in Africa and the Middle East evolve, buyers should engage with suppliers who can demonstrate their sustainability credentials. This not only helps mitigate risks associated with environmental regulations but also positions buyers favorably in an increasingly eco-conscious market landscape.
How Has the Abrasive Manufacturing Sector Evolved Over Time?
The abrasive manufacturing industry has experienced significant evolution since its inception. Initially reliant on natural materials, the sector transitioned to synthetic alternatives in the mid-20th century, driven by advancements in chemistry and manufacturing processes. This shift allowed for the production of more durable and efficient abrasives, meeting the growing demands of industrial applications.
In recent decades, the focus has shifted towards innovation and specialization, with manufacturers investing in research and development to create tailored solutions for specific applications. The rise of digital technologies has also transformed the landscape, enabling better tracking of supply chains and enhancing customer engagement through data-driven insights. As international B2B buyers navigate this complex market, understanding its historical context and current trajectory will be essential for making informed sourcing decisions.
Frequently Asked Questions (FAQs) for B2B Buyers of abrasive manufacturer
-
How do I select the right abrasive manufacturer for my business needs?
Choosing the right abrasive manufacturer involves several critical steps. First, assess your specific requirements, such as the type of abrasive material, application, and volume. Research potential manufacturers by reviewing their product catalogs, certifications, and industry reputation. It’s beneficial to request samples to evaluate quality. Additionally, consider their capacity for customization, lead times, and logistics capabilities. Engaging with existing clients can provide insights into their reliability and service levels. -
What factors should I consider when evaluating abrasive product quality?
To evaluate abrasive product quality, focus on material composition, durability, and performance metrics. Review certifications like ISO standards that indicate adherence to quality management systems. Testing products under real-world conditions can also provide valuable feedback on effectiveness and lifespan. Additionally, look for manufacturers that offer comprehensive quality assurance processes, including batch testing and third-party validations, to ensure consistent performance. -
What customization options are typically available from abrasive manufacturers?
Many abrasive manufacturers offer customization options to meet specific client needs. These may include variations in grit size, bonding agents, and dimensions tailored to particular applications. Some manufacturers can also develop proprietary formulations for unique materials or processes. When discussing customization, clearly articulate your requirements and ask for samples to ensure that the final product aligns with your expectations. -
What are the minimum order quantities (MOQs) for abrasive products?
Minimum order quantities (MOQs) can vary significantly between manufacturers and product types. Typically, MOQs can range from a few hundred to several thousand units, depending on the complexity and customization of the abrasive products. It’s essential to discuss MOQs upfront with potential suppliers to determine if they can accommodate your needs without incurring excessive costs. Some manufacturers may offer lower MOQs for first-time buyers or specific promotional periods. -
What payment terms should I expect when dealing with international abrasive manufacturers?
Payment terms can vary widely among manufacturers, influenced by factors such as order size and shipping destination. Common arrangements include upfront payments, partial payments upon order confirmation, and net 30 or 60 terms post-delivery. International buyers should be cautious and discuss secure payment methods, such as letters of credit or escrow services, to mitigate risks. Always ensure that terms are clearly outlined in the purchase agreement to avoid misunderstandings. -
How can I ensure reliable logistics and timely delivery of abrasive products?
To ensure reliable logistics, partner with manufacturers who have established shipping processes and a good track record of on-time deliveries. Discuss their logistics capabilities, including shipping partners, customs handling, and lead times. It’s beneficial to have a clear communication plan in place for updates on shipping status. Consider utilizing third-party logistics providers (3PL) for more complex supply chains, especially for international shipments, to streamline the process. -
What quality assurance processes should I expect from abrasive manufacturers?
A reputable abrasive manufacturer will implement stringent quality assurance processes. This includes in-house testing of products during production and before shipment. Look for manufacturers who provide transparency in their QA protocols, such as detailed reports or certificates of analysis. Additionally, inquire about their response strategies for addressing quality complaints and how they handle returns or replacements. -
What are the common challenges when sourcing abrasives internationally, and how can I overcome them?
Common challenges in international sourcing of abrasives include language barriers, regulatory compliance, and fluctuating shipping costs. To overcome these, consider working with local representatives or consultants who understand the regional market dynamics. Conduct thorough due diligence to ensure manufacturers comply with local regulations. Additionally, building strong relationships with suppliers can facilitate smoother communication and problem resolution, ultimately enhancing the sourcing experience.
Important Disclaimer & Terms of Use
⚠️ Important Disclaimer
The information provided in this guide, including content regarding manufacturers, technical specifications, and market analysis, is for informational and educational purposes only. It does not constitute professional procurement advice, financial advice, or legal advice.
While we have made every effort to ensure the accuracy and timeliness of the information, we are not responsible for any errors, omissions, or outdated information. Market conditions, company details, and technical standards are subject to change.
B2B buyers must conduct their own independent and thorough due diligence before making any purchasing decisions. This includes contacting suppliers directly, verifying certifications, requesting samples, and seeking professional consultation. The risk of relying on any information in this guide is borne solely by the reader.
Strategic Sourcing Conclusion and Outlook for abrasive manufacturer
What Are the Key Takeaways for B2B Buyers in the Abrasive Industry?
As we conclude our exploration of strategic sourcing in the abrasive manufacturing sector, it is vital to highlight the importance of building strong supplier relationships. For international B2B buyers, particularly in regions like Africa, South America, the Middle East, and Europe, understanding local market dynamics and supplier capabilities can significantly enhance procurement efficiency. Leveraging technology and data analytics is essential for optimizing sourcing strategies, ensuring that buyers can make informed decisions that align with their operational needs.
How Can Strategic Sourcing Enhance Competitive Advantage?
Strategic sourcing is not merely a cost-saving exercise; it is a pathway to innovation and quality improvement. By focusing on sustainable sourcing practices, buyers can also align with global trends towards environmental responsibility, which is increasingly becoming a purchase criterion. Establishing partnerships with reliable suppliers can lead to better product availability and reduced lead times, ultimately enhancing the overall supply chain resilience.
What Should B2B Buyers Do Next in the Abrasive Market?
Looking ahead, B2B buyers should actively seek opportunities to collaborate with abrasive manufacturers that prioritize quality, sustainability, and technological advancement. Engaging in industry forums and trade shows can provide valuable insights and connections. As the market continues to evolve, staying proactive in sourcing strategies will be key to thriving in an increasingly competitive landscape. Embrace the future of procurement by prioritizing strategic sourcing, and position your business for long-term success in the abrasive manufacturing industry.