Discover Top Benefits: Your Donaldson Filter Supplier Guide (2025)
Introduction: Navigating the Global Market for donaldson filter supplier
Navigating the complexities of sourcing Donaldson filters can be a significant challenge for international B2B buyers, particularly those operating in diverse markets across Africa, South America, the Middle East, and Europe. As industries increasingly prioritize efficiency and sustainability, the demand for high-quality filtration solutions has never been greater. This guide is designed to equip you with the essential knowledge to confidently source Donaldson filters, covering various types, applications, and the intricacies of supplier vetting.
In this comprehensive resource, you will find detailed insights into the different categories of Donaldson filters, including air, oil, and liquid filtration systems. We will explore their applications across various sectors such as automotive, aerospace, and manufacturing, ensuring that you understand which products best meet your operational needs. Moreover, we will provide actionable strategies for evaluating suppliers, discussing key factors such as reliability, pricing, and service support.
By leveraging this guide, B2B buyers can make informed purchasing decisions, ultimately enhancing their operational efficiency and reducing downtime. Whether you are based in bustling cities like Buenos Aires or Berlin, the insights offered here will empower you to navigate the global market for Donaldson filters effectively. Prepare to streamline your procurement processes and secure the best filtration solutions tailored to your business requirements.
Understanding donaldson filter supplier Types and Variations
Type Name | Key Distinguishing Features | Primary B2B Applications | Brief Pros & Cons for Buyers |
---|---|---|---|
Engine Filters | High-efficiency particulate air (HEPA) options, durable construction | Automotive, industrial machinery, construction | Pros: High filtration efficiency, durable. Cons: Higher initial cost. |
Compressed Air Filters | Removes moisture and contaminants, available in various sizes | Manufacturing, food processing, pharmaceuticals | Pros: Improves equipment lifespan, reduces downtime. Cons: Maintenance can be complex. |
Hydraulic Filters | Specially designed for hydraulic systems, various micron ratings | Construction, agriculture, mining | Pros: Protects hydraulic components, enhances performance. Cons: Can require frequent replacement. |
Industrial Dust Filters | Specialized for capturing fine dust, customizable options | Manufacturing, woodworking, metalworking | Pros: Improves air quality, compliant with safety regulations. Cons: Initial setup can be costly. |
Liquid Filtration Systems | Multi-stage filtration, tailored for specific liquid types | Oil & gas, chemical processing, water treatment | Pros: Tailored solutions, effective contaminant removal. Cons: May require extensive system integration. |
What Are Engine Filters and Their B2B Relevance?
Engine filters are designed to enhance the performance and longevity of engines by ensuring that air and oil are free from contaminants. They are particularly suitable for automotive applications, industrial machinery, and construction equipment. When purchasing engine filters, B2B buyers should consider the filter’s efficiency ratings and compatibility with existing systems, as well as the balance between upfront costs and long-term maintenance savings.
How Do Compressed Air Filters Benefit Manufacturing?
Compressed air filters are essential for removing moisture and contaminants from compressed air systems, which is crucial in sectors like manufacturing, food processing, and pharmaceuticals. These filters contribute to improved equipment lifespan and reduced downtime. B2B buyers should evaluate the filter’s size, maintenance requirements, and filtration levels to ensure optimal performance in their operations.
Why Are Hydraulic Filters Critical in Heavy Industries?
Hydraulic filters play a pivotal role in protecting hydraulic systems from dirt and particulate matter, making them indispensable in industries such as construction, agriculture, and mining. With various micron ratings available, these filters help maintain hydraulic efficiency and extend the life of expensive machinery. Buyers should consider the filter’s micron rating, compatibility, and replacement frequency when making purchasing decisions.
What Makes Industrial Dust Filters Essential for Safety Compliance?
Industrial dust filters are specifically designed to capture fine dust particles, which is vital in manufacturing, woodworking, and metalworking environments. These filters not only improve air quality but also help companies comply with safety regulations. B2B buyers should assess the filter’s efficiency, customization options, and initial setup costs to ensure they meet both operational and regulatory needs.
How Do Liquid Filtration Systems Cater to Diverse Industries?
Liquid filtration systems are tailored to meet the specific needs of various liquids, making them critical in oil and gas, chemical processing, and water treatment industries. These systems effectively remove contaminants and protect downstream processes. When selecting a liquid filtration system, B2B buyers should consider the specific application, integration capabilities, and overall system design to ensure optimal performance and reliability.
Related Video: Donanldson Filter and custom Snorkel
Key Industrial Applications of donaldson filter supplier
Industry/Sector | Specific Application of Donaldson Filter Supplier | Value/Benefit for the Business | Key Sourcing Considerations for this Application |
---|---|---|---|
Aerospace | Filtration for aircraft engines and hydraulic systems | Enhances engine performance and safety, reducing downtime | Compliance with aviation standards, availability of specific filters |
Construction | Dust and fume filtration in heavy machinery | Improves air quality and worker safety, minimizing health risks | Durability under harsh conditions, ease of maintenance |
Food & Beverage | Liquid filtration in processing and packaging | Ensures product purity and compliance with health regulations | Certification for food safety standards, compatibility with equipment |
Mining | Air filtration for equipment and personnel protection | Reduces equipment wear and improves worker safety | Resistance to abrasive materials, local regulations compliance |
Energy | Filtration in gas turbine and power generation systems | Increases efficiency and extends equipment lifespan | Availability of high-performance filters, support for international shipping |
How is Donaldson Filter Supplier Used in Aerospace Applications?
In the aerospace industry, Donaldson filters are critical for ensuring the optimal performance of aircraft engines and hydraulic systems. These filters help to remove contaminants from fuel and hydraulic fluids, which can otherwise lead to engine failure or reduced efficiency. International B2B buyers, particularly from Europe and the Middle East, must consider compliance with stringent aviation regulations and the specific requirements for filter types based on aircraft models. Ensuring availability and compatibility with existing systems is also essential for minimizing operational disruptions.
What Role Do Donaldson Filters Play in Construction?
In construction, Donaldson filters are utilized in heavy machinery to manage dust and fumes generated during operations. By improving air quality, these filters not only protect the health of workers but also enhance the performance and longevity of machinery. Buyers from Africa and South America should focus on the durability and maintenance requirements of these filters, particularly in harsh environments. Selecting filters that can withstand extreme conditions while ensuring compliance with local regulations is crucial for successful sourcing.
How Does Donaldson Filter Supplier Ensure Safety in Food & Beverage Processing?
Donaldson filters are essential in the food and beverage sector, particularly for liquid filtration during processing and packaging. These filters help maintain product purity and ensure compliance with health and safety regulations, which is critical for international markets. Buyers, especially in Europe and South America, need to prioritize filters that meet food safety certifications and are compatible with their processing equipment. This focus on quality and compliance can significantly impact product integrity and brand reputation.
Why Are Donaldson Filters Important for Mining Operations?
In the mining industry, Donaldson filters serve a dual purpose: protecting both equipment and personnel. Air filtration systems mitigate the risks associated with dust and particulate matter, which can lead to equipment wear and health issues for workers. For international buyers from regions like Africa, sourcing filters that are resistant to abrasive materials and comply with local health regulations is vital. This ensures a safer working environment and prolongs the life of expensive machinery.
How Do Donaldson Filters Enhance Energy Production?
In energy production, particularly in gas turbine applications, Donaldson filters play a crucial role in enhancing efficiency and extending the lifespan of equipment. By preventing contaminants from entering the system, these filters help maintain optimal performance levels. B2B buyers from Europe and the Middle East should consider the availability of high-performance filters that can handle specific operational demands. Additionally, understanding the logistics of international shipping and support services can facilitate smoother procurement processes.
Related Video: What are all the Laboratory Apparatus and their uses?
3 Common User Pain Points for ‘donaldson filter supplier’ & Their Solutions
Scenario 1: Complicated Ordering Process for International Buyers
The Problem: B2B buyers from regions like Africa and South America often face hurdles when ordering Donaldson filters due to a complicated online ordering system. This can include issues with selecting the correct filters for specific machinery, navigating various agreements based on regions, and understanding pricing that fluctuates with different agreements. These challenges lead to delays in procurement, increased operational costs, and potential downtime due to incorrect or delayed shipments.
The Solution: To streamline the ordering process, buyers should first familiarize themselves with the Donaldson website and its specific regional sections. Utilize the ‘Where to Buy’ feature to locate authorized distributors within your region, ensuring compliance with local regulations and availability. Before placing an order, create a detailed list of required filter parts, including model numbers and specifications. Engage directly with customer service for assistance in confirming compatibility and availability, which can prevent errors. Additionally, consider establishing a long-term agreement with a local distributor to lock in prices and simplify future orders.
Scenario 2: Difficulty in Understanding Product Specifications
The Problem: Many international buyers, especially those in technical industries, struggle to interpret the specifications and compatibility of Donaldson filters for their unique applications. This often leads to the procurement of unsuitable filters, causing operational inefficiencies and increased costs due to the need for replacements or repairs.
The Solution: Buyers should invest time in understanding the specifications by leveraging the extensive resources available on the Donaldson website, including product datasheets and installation guides. It is beneficial to utilize tools such as filter cross-reference guides to match existing parts with new filters accurately. For complex applications, consider consulting with Donaldson’s technical support team or engaging with industry experts who can provide tailored recommendations based on specific operational needs. Additionally, attending industry trade shows or workshops where Donaldson representatives are present can facilitate a better understanding of product applications and innovations.
Scenario 3: Limited Support for Maintenance and After-Sales Service
The Problem: After purchasing Donaldson filters, international buyers often find limited access to maintenance support and after-sales services. This can be particularly frustrating in regions where local expertise is scarce, leading to misunderstandings in filter maintenance, installation, and troubleshooting, ultimately affecting machine performance and longevity.
The Solution: To address this issue, buyers should proactively seek out comprehensive after-sales support options provided by Donaldson. This includes accessing online training resources, such as webinars and instructional videos that guide users through proper maintenance procedures. Additionally, buyers can consider forming partnerships with local service providers who are trained in Donaldson products, ensuring that they have the support needed for installation and maintenance. Establishing a direct line of communication with the supplier for ongoing support can also help resolve issues quickly, minimizing downtime and enhancing the overall efficiency of operations.
Strategic Material Selection Guide for donaldson filter supplier
What Are the Key Materials Used in Donaldson Filters?
When selecting materials for Donaldson filters, international B2B buyers must consider several factors that influence performance, durability, and compatibility with specific applications. Below, we analyze four common materials used in Donaldson filters: fiberglass, cellulose, metal mesh, and synthetic media. Each material has unique properties and implications for various industries, particularly for buyers in Africa, South America, the Middle East, and Europe.
How Does Fiberglass Perform in Donaldson Filters?
Fiberglass is a widely used material in Donaldson filters due to its excellent filtration capabilities and resistance to high temperatures. It can withstand temperatures up to 500°F (260°C) and pressures up to 300 psi, making it suitable for demanding applications.
Pros: Fiberglass is durable and offers superior filtration efficiency, especially for fine particles. It is also resistant to moisture and corrosion, which enhances its longevity.
Cons: The manufacturing process for fiberglass can be complex and costly. Additionally, its rigidity may limit its application in certain flexible filter designs.
Impact on Application: Fiberglass filters are particularly effective in environments with high humidity or corrosive elements, making them ideal for the chemical and petrochemical industries.
Considerations for International Buyers: Compliance with international standards such as ASTM and DIN is crucial. Buyers from regions like Germany may prefer fiberglass filters that meet stringent European regulations.
What Advantages Does Cellulose Offer for Filter Applications?
Cellulose is another common material used in Donaldson filters, particularly in applications requiring high dirt-holding capacity. This organic material is biodegradable and provides good filtration performance.
Pros: Cellulose is cost-effective and readily available. It also has a high dirt-holding capacity, which can extend the life of the filter.
Cons: While cellulose is effective, it has lower temperature and pressure ratings compared to fiberglass, making it less suitable for extreme conditions. It is also prone to moisture absorption, which can lead to degradation.
Impact on Application: Cellulose filters are often used in automotive and light-duty applications where cost efficiency is a priority.
Considerations for International Buyers: Buyers in regions like Argentina may appreciate the lower cost of cellulose filters, but they should be aware of the limitations in high-temperature applications.
How Does Metal Mesh Enhance Filter Durability?
Metal mesh is used in Donaldson filters for applications requiring high durability and reusability. It can withstand extreme temperatures and pressures, making it suitable for heavy-duty applications.
Pros: Metal mesh filters are highly durable and can be cleaned and reused, which reduces long-term costs. They also provide excellent structural integrity under high flow rates.
Cons: The initial cost of metal mesh filters can be high, and they may require more complex manufacturing processes. Additionally, they may not filter out fine particles as effectively as other materials.
Impact on Application: Metal mesh is ideal for industrial applications where durability and reusability are critical, such as in mining or heavy machinery.
Considerations for International Buyers: Buyers in the Middle East may prioritize metal mesh filters for their robustness in harsh environments, ensuring compliance with local standards.
What Role Does Synthetic Media Play in Filtration?
Synthetic media, often made from polyester or polypropylene, is increasingly popular in Donaldson filters due to its versatility and efficiency. These materials can be engineered for specific filtration needs.
Pros: Synthetic media offers excellent filtration efficiency and can be designed to meet various temperature and pressure requirements. They are also resistant to moisture and chemicals.
Cons: The cost of synthetic media can be higher than traditional materials, and the manufacturing process may be more complex. Additionally, some synthetic materials may not be biodegradable.
Impact on Application: Synthetic filters are suitable for a wide range of applications, including automotive, aerospace, and food processing, where specific filtration characteristics are required.
Considerations for International Buyers: Buyers in Europe may favor synthetic media for its performance in strict regulatory environments, ensuring compliance with both safety and environmental standards.
Summary Table of Material Selection for Donaldson Filters
Material | Typical Use Case for Donaldson Filter Supplier | Key Advantage | Key Disadvantage/Limitation | Relative Cost (Low/Med/High) |
---|---|---|---|---|
Fiberglass | Chemical and petrochemical industries | High temperature and pressure resistance | Complex manufacturing process | Medium |
Cellulose | Automotive and light-duty applications | Cost-effective and biodegradable | Lower temperature and pressure ratings | Low |
Metal Mesh | Mining and heavy machinery applications | Durable and reusable | High initial cost and lower fine filtration | High |
Synthetic Media | Aerospace and food processing | Excellent filtration efficiency | Higher cost and potential non-biodegradability | High |
By understanding the properties and applications of these materials, international B2B buyers can make informed decisions that align with their operational needs and regional compliance standards.
In-depth Look: Manufacturing Processes and Quality Assurance for donaldson filter supplier
What Are the Main Stages of Manufacturing for Donaldson Filters?
When engaging with a Donaldson filter supplier, understanding the manufacturing process is crucial for B2B buyers. The typical manufacturing stages include material preparation, forming, assembly, and finishing, each employing specific techniques to ensure high-quality products.
Material Preparation: How Are Raw Materials Selected and Processed?
The manufacturing journey begins with the selection of raw materials. Donaldson filters often use advanced media materials such as synthetic fibers and microglass, chosen for their durability and filtration efficiency. The preparation phase involves cutting and shaping these materials into suitable forms for further processing. Quality assurance starts here, as suppliers must ensure that all raw materials meet specific standards before they proceed to the next phase.
Forming: What Techniques Are Used to Shape Filter Components?
In the forming stage, various techniques such as die-cutting and molding are used to create the individual components of the filters. For example, filter media may be pleated to increase surface area, enhancing filtration capabilities. This process requires precision machinery to ensure that each piece meets the design specifications. The use of advanced technology, such as computer numerical control (CNC) machines, is common to achieve high accuracy.
Assembly: How Are Components Joined Together?
Once the components are formed, they move to the assembly stage. This involves joining the different parts, such as the filter media, end caps, and support structures. Techniques like ultrasonic welding and adhesive bonding are often employed to ensure strong, leak-proof seals. During assembly, it’s vital to monitor for defects, as any imperfection can lead to reduced filter performance.
Finishing: What Quality Control Measures Are Implemented?
The finishing stage includes surface treatments and coatings that enhance the filter’s durability and performance. This may involve applying protective layers or conducting final inspections before the products are packaged. Proper finishing is essential, as it directly affects the filter’s lifespan and effectiveness in various applications.
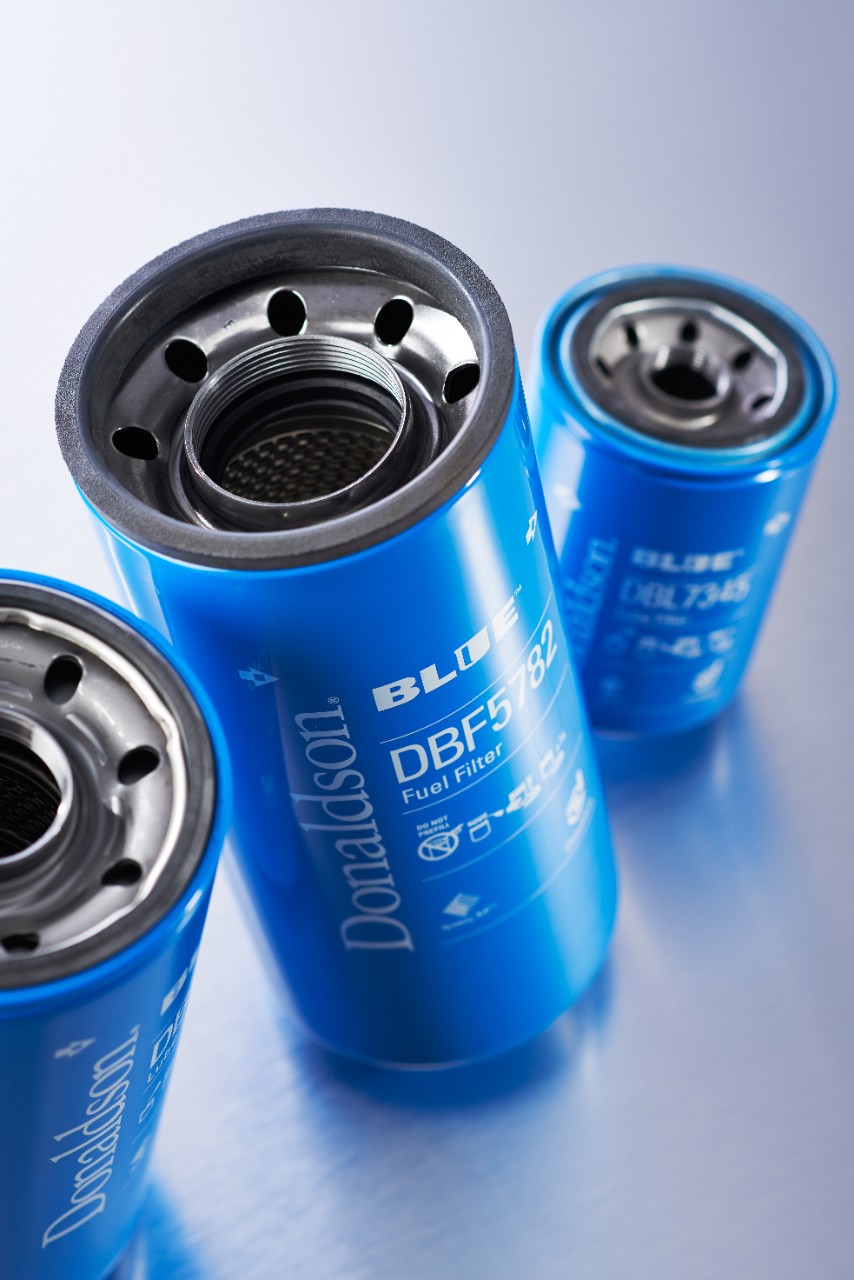
A stock image related to donaldson filter supplier.
What Quality Assurance Standards Should B2B Buyers Look For?
Quality assurance is a cornerstone of the manufacturing process for Donaldson filters. International standards such as ISO 9001 ensure that manufacturers maintain high-quality processes and continuous improvement. Additionally, industry-specific certifications like CE (Conformité Européenne) and API (American Petroleum Institute) are crucial, particularly for filters used in specialized applications.
Which Quality Control Checkpoints Are Critical in the Manufacturing Process?
Quality control (QC) checkpoints are integrated throughout the manufacturing process, ensuring that each stage meets the required standards. Key checkpoints include:
- Incoming Quality Control (IQC): This involves inspecting raw materials upon arrival to ensure they meet specifications.
- In-Process Quality Control (IPQC): Continuous monitoring during manufacturing to detect and rectify issues in real-time.
- Final Quality Control (FQC): A thorough inspection of the finished product before packaging and shipment.
These checkpoints help maintain consistent quality and reliability, which are essential for B2B buyers who require dependable filtration solutions.
How Can B2B Buyers Verify Supplier Quality Control?
For international B2B buyers, particularly from regions like Africa, South America, the Middle East, and Europe, verifying a supplier’s quality control processes is critical. Here are several methods to ensure that suppliers meet the necessary standards:
What Audits and Reports Should Buyers Request?
Buyers should request regular quality audits and reports from suppliers. These documents should detail the QC processes, including any certifications obtained and results from internal audits. Engaging in direct communication with suppliers about their QC protocols can also provide insights into their commitment to quality.
How Can Third-Party Inspections Enhance Quality Assurance?
Utilizing third-party inspection services can further enhance quality assurance. These independent entities can perform audits and inspections at various stages of production, ensuring that the filters meet both industry standards and buyer specifications. This level of scrutiny can provide additional peace of mind, particularly when dealing with international suppliers.
What Are the Nuances of Quality Control and Certification for International Buyers?
International buyers must navigate various nuances regarding quality control and certification. Different regions may have distinct regulatory requirements, which can affect the certification process. For instance, European buyers might prioritize CE certification, while buyers in the Middle East may focus on local standards.
How Do Regional Standards Impact Supplier Selection?
Understanding regional standards is vital for making informed supplier selections. Buyers should consider whether the supplier’s certifications align with their local regulations and industry requirements. This ensures compliance and can prevent potential issues during importation.
What Challenges Might Buyers Face When Working with Suppliers from Different Regions?
When sourcing from suppliers in different regions, buyers may encounter challenges such as language barriers, differing quality expectations, and variations in manufacturing practices. Establishing clear communication and understanding the supplier’s quality assurance processes can mitigate these challenges.
Conclusion: Ensuring Quality in Your Supply Chain
For B2B buyers, particularly those operating in diverse international markets, a comprehensive understanding of the manufacturing processes and quality assurance measures of Donaldson filter suppliers is essential. By focusing on these aspects, buyers can make informed decisions, ensuring they select suppliers that align with their quality standards and business needs.
Practical Sourcing Guide: A Step-by-Step Checklist for ‘donaldson filter supplier’
The following checklist serves as a practical guide for international B2B buyers looking to source from Donaldson filter suppliers. This step-by-step approach will help streamline your procurement process, ensuring that you partner with the right suppliers to meet your specific needs.
Step 1: Define Your Technical Specifications
Before reaching out to suppliers, clearly outline your technical requirements. This includes identifying the specific types of Donaldson filters you need, such as air, oil, or liquid filtration systems. By having detailed specifications, you can ensure that suppliers understand your needs and can provide suitable products.
- Consider factors such as:
- Filter size and compatibility with existing equipment.
- Performance standards and certifications required for your industry.
Step 2: Research Potential Suppliers
Conduct thorough research on potential Donaldson filter suppliers. Utilize online platforms, industry directories, and trade shows to compile a list of candidates. Investigating suppliers’ backgrounds can save time and resources later in the process.
- Key points to evaluate include:
- The supplier’s reputation in the market.
- Previous customer reviews and testimonials.
Step 3: ✅ Verify Supplier Certifications
Ensure that the suppliers you are considering hold relevant certifications. Compliance with international standards such as ISO 9001 or industry-specific certifications can indicate a supplier’s commitment to quality and reliability.
- Look for certifications related to:
- Environmental management (ISO 14001).
- Occupational health and safety (ISO 45001).
Step 4: Request Samples and Product Information
Once you have shortlisted potential suppliers, request samples of the filters you intend to procure. This allows you to assess product quality firsthand and determine if they meet your specifications.
- What to analyze:
- The material used in the filters.
- The efficiency and effectiveness of the filtration process.
Step 5: Evaluate Pricing and Payment Terms
Discuss pricing structures and payment terms with each supplier. Understanding the total cost of ownership, including shipping and handling, is crucial for budgeting.
- Consider negotiating on:
- Bulk purchase discounts.
- Flexible payment options that may benefit cash flow.
Step 6: Assess Supplier Support and Customer Service
Evaluate the level of support and customer service offered by each supplier. A reliable supplier should provide comprehensive support, including after-sales service, technical assistance, and easy communication channels.
- Key questions to ask:
- How quickly can they respond to inquiries?
- What is their policy for handling product issues or returns?
Step 7: Finalize Agreements and Contracts
Once you have chosen a supplier, ensure that all agreements are documented in a formal contract. This contract should outline pricing, delivery schedules, warranties, and any other terms of service.
- Important elements to include:
- Clauses regarding confidentiality and compliance with local laws.
- Clear penalties for late deliveries or non-compliance.
By following this checklist, you can ensure a streamlined sourcing process for Donaldson filters that meets your operational needs while fostering strong supplier relationships.
Comprehensive Cost and Pricing Analysis for donaldson filter supplier Sourcing
What Are the Key Cost Components in Donaldson Filter Sourcing?
When sourcing Donaldson filters, understanding the cost structure is essential for international B2B buyers. The primary cost components include:
-
Materials: The quality of materials used in manufacturing Donaldson filters significantly impacts pricing. High-quality filtration media and durable components typically incur higher costs but offer better performance and longevity.
-
Labor: Labor costs vary by region and are influenced by local wage standards. Countries with higher labor costs, such as Germany, may reflect this in the pricing of filters.
-
Manufacturing Overhead: This encompasses expenses related to factory operations, such as utilities, rent, and equipment maintenance. Efficient production processes can help minimize these costs.
-
Tooling: Initial tooling costs for specialized or custom filter designs can be substantial. Buyers should consider these costs when evaluating the total price, especially for non-standard filter types.
-
Quality Control (QC): Rigorous QC processes are essential to ensure product reliability. Suppliers may charge more for filters that meet higher certification standards, which is crucial for industries like aerospace or pharmaceuticals.
-
Logistics: Shipping costs, including freight, customs duties, and insurance, can vary based on the destination. Understanding the logistics involved can help buyers anticipate total costs.
-
Margin: Suppliers typically add a profit margin to cover their costs and ensure sustainability. This margin can vary significantly based on the supplier’s business model and market competition.
How Do Price Influencers Affect Donaldson Filter Sourcing?
Several factors influence the pricing of Donaldson filters, particularly for international buyers:
-
Volume/MOQ: Ordering in bulk can lead to significant discounts. Minimum order quantities (MOQ) may be required, impacting the overall cost structure.
-
Specifications/Customization: Custom filters designed for specific applications may incur additional charges. Buyers should clearly define their requirements to avoid unexpected costs.
-
Materials: The choice of materials can affect both performance and price. Filters made from advanced materials, while more expensive, may result in lower maintenance costs over time.
-
Quality and Certifications: Higher quality filters with certifications (like ISO or CE) usually come at a premium. However, these certifications often justify the higher cost due to the assurance of product reliability.
-
Supplier Factors: The reputation and reliability of the supplier play a crucial role in pricing. Established suppliers like Donaldson may offer premium prices due to their brand equity and product guarantees.
-
Incoterms: Understanding the terms of shipping and delivery is vital. Different Incoterms (e.g., FOB, CIF) can significantly affect the total landed cost of the filters.
What Are Some Effective Buyer Tips for Negotiating Costs?
International B2B buyers can adopt several strategies to optimize costs when sourcing Donaldson filters:
-
Negotiate Terms: Always negotiate pricing and payment terms. Building a long-term relationship with suppliers can lead to better pricing over time.
-
Focus on Total Cost of Ownership (TCO): Evaluate the long-term costs associated with filter use, including maintenance and replacement. A higher upfront cost might be justified by lower operating costs.
-
Research Market Prices: Stay informed about market prices and trends. Knowledge of competitive pricing can empower buyers during negotiations.
-
Consider Local Suppliers: If feasible, sourcing from local suppliers in regions such as Africa or South America may reduce logistics costs and lead times.
-
Be Aware of Pricing Nuances: Different regions may have varying pricing strategies based on local demand, regulations, and market conditions. Understanding these nuances can provide leverage in negotiations.
Conclusion
In conclusion, a comprehensive understanding of the cost components and price influencers associated with Donaldson filter sourcing is crucial for international B2B buyers. By applying effective negotiation strategies and being aware of total costs, buyers can make informed decisions that enhance their procurement process while ensuring quality and reliability in filtration solutions.
Alternatives Analysis: Comparing donaldson filter supplier With Other Solutions
When exploring filtration solutions for industrial applications, it’s essential for B2B buyers to consider various alternatives to the Donaldson filter supplier. Understanding these options can help in making informed decisions based on performance, cost-effectiveness, and operational needs. Below, we compare Donaldson filters with two viable alternatives: Parker Hannifin Filters and Hydac Filtration Systems.
Comparison Table of Filtration Solutions
Comparison Aspect | Donaldson Filter Supplier | Parker Hannifin Filters | Hydac Filtration Systems |
---|---|---|---|
Performance | High efficiency, durable | Comparable efficiency, robust design | High filtration accuracy, wide range of applications |
Cost | Moderate to high | Competitive pricing, offers value | Generally high due to advanced technology |
Ease of Implementation | User-friendly, supported by extensive documentation | Easy integration with existing systems | May require specialized installation |
Maintenance | Low maintenance, easy to replace | Moderate maintenance needs | Higher maintenance due to complex systems |
Best Use Case | Heavy-duty industrial use | Versatile, suitable for various sectors | Best for precision applications in pharmaceuticals and food processing |
In-Depth Look at Alternatives
What are the Benefits and Drawbacks of Parker Hannifin Filters?
Parker Hannifin Filters offer a competitive alternative to Donaldson. They are known for their robust design and reliability, suitable for various industrial sectors. The cost is generally competitive, providing good value, especially for companies looking for budget-friendly options. However, while they offer comparable efficiency, they may not have the same level of brand recognition or extensive support network as Donaldson, which could be a concern for companies needing comprehensive service support.
How Do Hydac Filtration Systems Compare?
Hydac Filtration Systems are recognized for their high filtration accuracy and innovative technology. They are particularly well-suited for precision applications in industries such as pharmaceuticals and food processing. However, the advanced technology comes at a higher price point, and the systems may require more specialized installation and maintenance. This makes them less ideal for companies looking for straightforward, low-maintenance options.
Conclusion: How Can B2B Buyers Choose the Right Filtration Solution?
When selecting a filtration solution, B2B buyers should assess their specific needs in terms of application, budget, and operational requirements. Donaldson filters are an excellent choice for those in heavy-duty industrial sectors requiring reliable performance. In contrast, Parker Hannifin filters offer competitive pricing and versatility, while Hydac systems excel in precision applications but may involve higher costs and maintenance. Ultimately, buyers should consider factors such as total cost of ownership, ease of maintenance, and the specific requirements of their operational environment to make the most informed decision.
Essential Technical Properties and Trade Terminology for donaldson filter supplier
What Are the Essential Technical Properties of Donaldson Filters?
When considering the procurement of Donaldson filters, understanding specific technical properties is crucial for making informed decisions. Here are some key specifications:
-
Material Grade
– Definition: The quality of materials used in filter construction, such as fiberglass, cellulose, or synthetic materials.
– B2B Importance: Higher-grade materials often result in better filtration efficiency and longer service life. For international buyers, selecting the right material grade can significantly impact operational costs and maintenance schedules. -
Filtration Efficiency
– Definition: A measure of a filter’s ability to remove particles from air or liquid, typically expressed as a percentage.
– B2B Importance: High filtration efficiency translates to improved equipment performance and longevity. B2B buyers must evaluate the efficiency ratings to ensure compliance with industry standards, particularly in sectors like food processing or pharmaceuticals. -
Pressure Drop
– Definition: The reduction in pressure as air or liquid passes through the filter, usually measured in inches of water column (in WC).
– B2B Importance: A lower pressure drop indicates that the filter allows for better airflow, which can enhance system performance and reduce energy consumption. This is vital for buyers in regions with high energy costs, such as Europe. -
Operating Temperature Range
– Definition: The range of temperatures within which the filter can effectively operate without degradation.
– B2B Importance: Understanding the operating temperature is essential for applications in extreme environments, such as industrial manufacturing or automotive engines. Selecting filters that can withstand specific temperature ranges ensures reliability and safety. -
Service Life
– Definition: The expected duration a filter can operate before needing replacement, usually indicated in hours or months.
– B2B Importance: Longer service life reduces the frequency of replacements, which is beneficial for inventory management and cost efficiency. For international buyers, this can lead to significant savings, especially in remote locations.
What Are Common Trade Terms Used in the Donaldson Filter Industry?
Familiarity with industry jargon is essential for effective communication and negotiation in B2B transactions. Here are some common terms:
-
OEM (Original Equipment Manufacturer)
– Definition: A company that produces parts or equipment that may be marketed by another manufacturer.
– Importance: Understanding OEM relationships helps buyers ensure compatibility and quality when sourcing filters. This is particularly important for industries requiring precise specifications, like aerospace or automotive. -
MOQ (Minimum Order Quantity)
– Definition: The smallest quantity of a product that a supplier is willing to sell.
– Importance: Knowing the MOQ is essential for budgeting and inventory management. For buyers in Africa or South America, it can impact cash flow and storage capabilities. -
RFQ (Request for Quotation)
– Definition: A document sent to suppliers requesting a quote for specific goods or services.
– Importance: An RFQ helps buyers compare prices and terms across suppliers, ensuring they secure the best deal. This is especially useful in competitive markets in Europe or the Middle East. -
Incoterms (International Commercial Terms)
– Definition: A series of pre-defined commercial terms published by the International Chamber of Commerce (ICC) relating to international commercial law.
– Importance: Understanding Incoterms helps buyers clarify shipping responsibilities, costs, and risks involved in international transactions. This knowledge is crucial for buyers operating across borders, particularly in diverse regions like Africa and Europe. -
Lead Time
– Definition: The amount of time that elapses from the initiation of a process until its completion.
– Importance: Knowing the lead time for filter delivery can help buyers plan their operations more effectively. This is particularly relevant for industries with tight production schedules.
By grasping these technical properties and trade terms, international B2B buyers can navigate the procurement process more effectively, ensuring they select the right Donaldson filters for their specific applications.
Navigating Market Dynamics and Sourcing Trends in the donaldson filter supplier Sector
What Are the Current Market Dynamics and Key Trends in the Donaldson Filter Supplier Sector?
The global filtration market is experiencing significant transformation driven by various factors, including technological advancements, environmental regulations, and shifting consumer preferences. For international B2B buyers, particularly in regions like Africa, South America, the Middle East, and Europe, understanding these dynamics is crucial for effective sourcing decisions.
One of the primary drivers is the increasing demand for high-efficiency filtration systems, particularly in industries such as automotive, manufacturing, and agriculture. As businesses strive for operational efficiency and compliance with stringent environmental regulations, there is a growing preference for suppliers like Donaldson that offer advanced filtration solutions. Additionally, the rise of digital technologies, such as IoT and AI, is reshaping sourcing strategies, enabling predictive maintenance, and enhancing supply chain transparency.
Emerging trends include the adoption of cloud-based platforms for inventory management and procurement processes, which facilitate real-time data access for better decision-making. Buyers are also increasingly looking for suppliers who can demonstrate agility in responding to market changes, such as fluctuations in raw material prices or shifts in demand. This trend is particularly relevant in volatile regions where political and economic instability can affect supply chains.
How Does Sustainability and Ethical Sourcing Impact the Donaldson Filter Supplier Sector?
Sustainability has become a core consideration for B2B buyers globally. Environmental impact assessments and sustainable sourcing practices are not just trends but essential components of strategic sourcing. For Donaldson filter suppliers, this means an increased focus on minimizing waste and reducing carbon footprints throughout the supply chain.
Buyers are increasingly prioritizing suppliers who can offer ‘green’ certifications, such as ISO 14001, which indicates a commitment to environmental management. Additionally, the use of recyclable materials and the implementation of energy-efficient manufacturing processes are becoming critical criteria in supplier selection. For buyers from regions like Europe, where environmental regulations are stringent, sourcing from suppliers that prioritize sustainability can also lead to compliance with local laws and regulations.
Ethical sourcing is equally important, as consumers and businesses alike demand transparency in supply chains. Suppliers who can demonstrate responsible sourcing practices—such as fair labor conditions and ethical procurement of raw materials—are more likely to build trust and long-term relationships with B2B buyers.
What Is the Brief Evolution of the Donaldson Filter Supplier Sector?
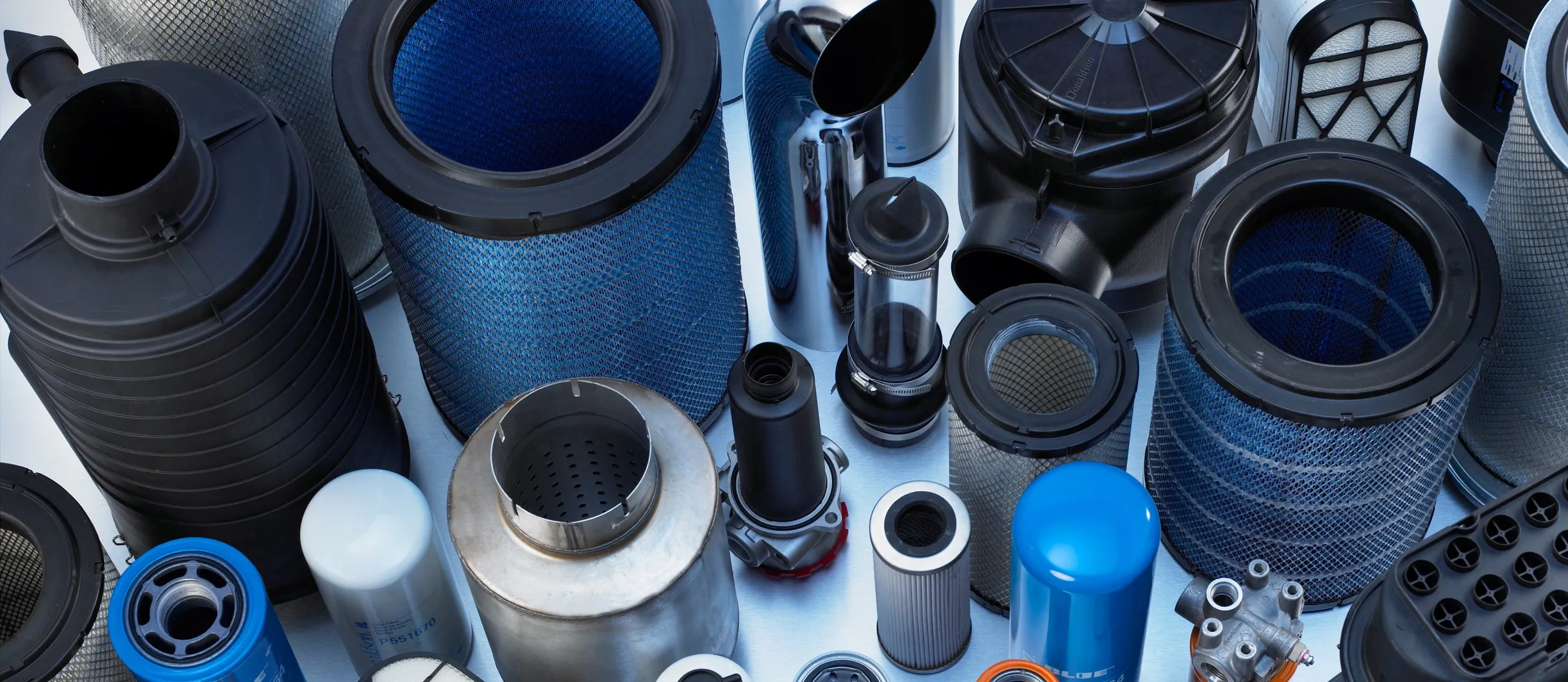
A stock image related to donaldson filter supplier.
The Donaldson Company, established in 1915, has evolved into a leading player in the filtration industry, adapting to changing market demands and technological advancements over the decades. Initially focused on air filtration, Donaldson expanded its product offerings to include liquid filtration, hydraulic filtration, and specialized filtration systems for various industries, including aerospace, automotive, and food processing.
This evolution has been marked by strategic investments in research and development, allowing the company to introduce innovative products that meet the increasing needs for efficiency and sustainability. Today, Donaldson stands out not only for its extensive product range but also for its commitment to quality and customer service, making it a preferred choice for international B2B buyers looking for reliable filtration solutions.
Understanding these market dynamics, sustainability concerns, and the historical context of Donaldson’s growth can empower B2B buyers to make informed sourcing decisions that align with their operational goals and ethical standards.
Frequently Asked Questions (FAQs) for B2B Buyers of donaldson filter supplier
-
How do I solve issues related to the availability of Donaldson filters in my region?
To address availability issues, first confirm your region and the specific filters you need through the Donaldson website. It’s crucial to select the correct region to see accurate product listings and stock levels. If a specific filter is out of stock, consider contacting Donaldson directly for alternative solutions or to check on lead times for restocking. Additionally, building a relationship with local distributors can provide insights into inventory levels and potential custom orders. -
What is the best method to verify the quality of Donaldson filters before purchasing?
To ensure the quality of Donaldson filters, request product certifications and specifications from the supplier. You can also ask for samples to conduct your own testing or rely on third-party testing facilities for an unbiased evaluation. Checking customer reviews and case studies can also provide insights into product performance in similar applications. Establishing a dialogue with the supplier about their quality assurance processes will further assure you of their product reliability. -
How can I effectively communicate my customization needs for Donaldson filters?
When communicating customization needs, be specific about your requirements, including dimensions, filtration capacity, and any unique operational conditions. It’s beneficial to provide technical drawings or specifications if available. Engaging in direct discussions with the supplier’s engineering team can facilitate better understanding and solutions. Documenting all agreed-upon specifications in writing ensures clarity and sets the stage for quality control throughout the production process. -
What are the common payment terms for international purchases of Donaldson filters?
Payment terms can vary widely depending on the supplier and the buyer’s relationship. Common terms include advance payment, net 30/60/90 days, or letters of credit for larger orders. It’s advisable to clarify these terms before placing an order. Additionally, consider the implications of currency exchange rates and transaction fees, especially for cross-border transactions. Establishing a clear payment agreement can help prevent misunderstandings and ensure smooth transactions. -
What are the minimum order quantities (MOQ) for Donaldson filters?
Minimum order quantities (MOQ) for Donaldson filters can vary based on the specific product and the supplier’s policies. Typically, larger orders may reduce the per-unit cost, while smaller orders might incur higher shipping fees. It’s essential to inquire directly with the supplier to understand their MOQ and the rationale behind it. If your needs are below the MOQ, consider discussing potential exceptions or joining with other buyers to meet the minimum requirements. -
How can I vet a Donaldson filter supplier for reliability and performance?
To vet a Donaldson filter supplier, begin by researching their reputation through online reviews and industry forums. Request references from existing clients and inquire about their experiences. Additionally, assess the supplier’s certifications and compliance with international quality standards such as ISO. A site visit or a virtual tour of their facility can provide insights into their operational capabilities and quality control measures. -
What logistics considerations should I keep in mind when importing Donaldson filters?
When importing Donaldson filters, consider shipping methods, customs clearance processes, and local regulations that may affect delivery times and costs. Assess whether the supplier provides door-to-door shipping or if you need to arrange logistics separately. Understanding import duties and taxes in your country will help you estimate total costs. Collaborating with a reliable freight forwarder can streamline the logistics process and ensure timely delivery. -
What support options are available for troubleshooting Donaldson filter issues post-purchase?
Post-purchase support for troubleshooting Donaldson filter issues typically includes access to technical support teams via phone or email. Many suppliers also offer online resources such as installation guides, maintenance tips, and troubleshooting FAQs. Ensure that your supplier provides warranty information and service agreements to facilitate repairs or replacements as needed. Establishing a good relationship with the supplier can also lead to quicker response times for support inquiries.
Important Disclaimer & Terms of Use
⚠️ Important Disclaimer
The information provided in this guide, including content regarding manufacturers, technical specifications, and market analysis, is for informational and educational purposes only. It does not constitute professional procurement advice, financial advice, or legal advice.
While we have made every effort to ensure the accuracy and timeliness of the information, we are not responsible for any errors, omissions, or outdated information. Market conditions, company details, and technical standards are subject to change.
B2B buyers must conduct their own independent and thorough due diligence before making any purchasing decisions. This includes contacting suppliers directly, verifying certifications, requesting samples, and seeking professional consultation. The risk of relying on any information in this guide is borne solely by the reader.
Strategic Sourcing Conclusion and Outlook for donaldson filter supplier
What are the Key Takeaways for B2B Buyers Considering Donaldson Filters?
In conclusion, strategic sourcing of Donaldson filters offers international B2B buyers an opportunity to enhance operational efficiency while ensuring compliance with quality standards. Buyers from regions like Africa, South America, the Middle East, and Europe can leverage Donaldson’s extensive product range tailored to various industries, including agriculture, automotive, and energy. Understanding the regional availability and adapting procurement strategies to local market conditions is crucial for maximizing value.
How Can Strategic Sourcing Impact Your Business?
By implementing a strategic sourcing approach, buyers can not only reduce costs but also foster long-term partnerships with reliable suppliers. Engaging with Donaldson’s dedicated support for international clients can streamline procurement processes and facilitate better inventory management, ensuring that businesses remain competitive in their respective markets.
What’s Next for International Buyers?
As the global market continues to evolve, the demand for high-quality filtration solutions will only increase. International buyers are encouraged to explore the latest innovations from Donaldson and to consider establishing agreements that align with their operational needs. Engage proactively with the supplier to capitalize on new opportunities and ensure your business is equipped for future challenges.