Discover Top Composite Panel Suppliers: Your Ultimate Guide (2025)
Introduction: Navigating the Global Market for composite panel supplier
Navigating the complexities of sourcing composite panels can be a daunting task for international B2B buyers, especially when seeking reliable suppliers who meet specific quality and performance standards. In today’s competitive market, understanding the different types of composite panels, their various applications, and the nuances of supplier vetting is crucial for making informed purchasing decisions. This guide serves as a comprehensive resource, providing insights into the myriad of composite materials available, including polymer, metal, and hybrid composites, and their suitability for industries such as construction, automotive, and aerospace.
With a focus on empowering buyers from regions such as Africa, South America, the Middle East, and Europe—particularly in countries like Colombia and the UK—this guide addresses the key challenges faced in sourcing composite panels. It covers essential topics such as evaluating supplier capabilities, understanding cost factors, and recognizing the importance of compliance with international quality standards. By equipping buyers with actionable insights and a thorough understanding of the composite panel market, this guide aims to streamline the sourcing process, reduce risks, and enhance overall procurement strategies.
Whether you are looking to improve your supply chain efficiency or seeking innovative solutions to meet specific project requirements, this guide will provide the critical information needed to navigate the global market for composite panel suppliers successfully.
Understanding composite panel supplier Types and Variations
Type Name | Key Distinguishing Features | Primary B2B Applications | Brief Pros & Cons for Buyers |
---|---|---|---|
Polymer Composite Panels | Lightweight, corrosion-resistant, and versatile | Construction, automotive, marine | Pros: Cost-effective, easy to mold. Cons: Less durable under extreme conditions. |
Metal Composite Panels | Combines metals with polymer layers for enhanced strength | Building facades, signage, interior design | Pros: High durability, aesthetic appeal. Cons: Heavier, higher cost. |
Ceramic Matrix Composites | High temperature resistance and excellent mechanical strength | Aerospace, defense, industrial applications | Pros: Superior performance in harsh environments. Cons: Typically more expensive and less available. |
Fiberglass Panels | Reinforced with glass fibers, lightweight and strong | Infrastructure, automotive, marine | Pros: Excellent strength-to-weight ratio. Cons: Can be less impact-resistant than metals. |
Hybrid Composite Panels | Combination of different materials for tailored properties | Advanced manufacturing, aerospace | Pros: Customizable properties, versatile. Cons: Complexity in sourcing and manufacturing. |
What Are Polymer Composite Panels and Their Suitability for B2B Buyers?
Polymer composite panels are engineered from a polymer matrix reinforced with fibers such as glass or carbon. They are lightweight and exhibit excellent corrosion resistance, making them suitable for applications in construction, automotive, and marine sectors. B2B buyers should consider the cost-effectiveness and ease of manufacturing when selecting polymer composites, particularly for projects requiring rapid production and adaptability. However, they may not perform well under extreme conditions, which should be accounted for in high-stress applications.
Why Choose Metal Composite Panels for Your Business Needs?
Metal composite panels consist of two thin layers of metal enclosing a non-metal core, typically made from a polymer. These panels are known for their high durability and aesthetic appeal, making them a popular choice for building facades, signage, and interior design. B2B buyers can benefit from their ability to withstand harsh weather conditions while providing a modern look. However, the higher cost and increased weight compared to other types may be a consideration for budget-conscious projects.
What Advantages Do Ceramic Matrix Composites Offer to B2B Buyers?
Ceramic matrix composites are composed of ceramic fibers embedded in a ceramic matrix, providing exceptional high-temperature resistance and mechanical strength. They are primarily used in aerospace, defense, and various industrial applications where performance in extreme environments is critical. Buyers should note that while these composites offer superior capabilities, they are typically more expensive and may have limited availability, necessitating careful supplier selection.
How Do Fiberglass Panels Enhance Structural Integrity?
Fiberglass panels are reinforced with glass fibers, resulting in a lightweight yet strong material commonly used in infrastructure, automotive, and marine industries. Their excellent strength-to-weight ratio makes them an attractive option for B2B buyers looking to reduce weight without sacrificing performance. However, potential buyers should be aware that fiberglass can be less impact-resistant than metals, which may limit its application in certain high-impact environments.
What Are the Benefits of Hybrid Composite Panels for Diverse Applications?
Hybrid composite panels incorporate multiple materials, allowing for tailored properties to meet specific performance requirements. They are increasingly used in advanced manufacturing and aerospace sectors where unique combinations of strength, weight, and flexibility are necessary. B2B buyers should consider the customization options available, as well as the complexity involved in sourcing and manufacturing hybrid composites, which may influence project timelines and costs.
Related Video: Aluminium Composite Panel Details | ACP Sheet | ACP Sheet Price And Information
Key Industrial Applications of composite panel supplier
Industry/Sector | Specific Application of Composite Panel Supplier | Value/Benefit for the Business | Key Sourcing Considerations for this Application |
---|---|---|---|
Construction | Facades and wall panels for commercial buildings | Lightweight, energy-efficient, and durable solutions | Compliance with local building codes and standards |
Aerospace | Interior cabin panels and structural components | Enhanced strength-to-weight ratio and corrosion resistance | Supplier certifications (e.g., AS9100) and traceability |
Automotive | Body panels and interior components | Improved fuel efficiency and reduced manufacturing costs | Material compatibility and performance testing |
Marine | Hulls and deck structures for boats and ships | Resistance to harsh marine environments and reduced weight | Availability of marine-grade composites and certifications |
Energy | Wind turbine blades and energy storage systems | Increased efficiency and longevity of components | Understanding of specific energy sector requirements |
How Are Composite Panels Used in the Construction Industry?
In the construction industry, composite panel suppliers provide facades and wall panels that enhance the aesthetic appeal and energy efficiency of buildings. These panels are lightweight yet strong, reducing the structural load on foundations while improving insulation properties. For international buyers, especially in regions like Africa and South America, sourcing panels that comply with local building regulations and standards is crucial to avoid project delays and ensure safety.
What Role Do Composite Panels Play in Aerospace Applications?
In aerospace, composite panels are critical for manufacturing interior cabin components and structural elements of aircraft. Their high strength-to-weight ratio allows for significant weight savings, which translates to lower fuel consumption and operational costs. Buyers from Europe and the Middle East should prioritize suppliers with relevant certifications, such as AS9100, to ensure compliance with stringent aerospace industry standards and traceability of materials used.
How Are Composite Panels Beneficial in the Automotive Sector?
Composite panels are increasingly utilized in the automotive industry for body panels and interior components. These materials contribute to improved fuel efficiency by reducing vehicle weight, while also lowering manufacturing costs through streamlined production processes. International B2B buyers should consider the compatibility of composite materials with existing manufacturing methods and conduct thorough performance testing to meet safety standards.
What Are the Advantages of Composite Panels in Marine Applications?
In the marine sector, composite panels are essential for constructing hulls and deck structures due to their resistance to corrosion and harsh environmental conditions. These panels significantly reduce the weight of vessels, enhancing performance and fuel efficiency. Buyers in regions with active maritime industries, such as the Middle East, should ensure that their suppliers offer marine-grade composites that meet industry-specific certifications to guarantee durability and performance.
How Do Composite Panels Enhance Energy Sector Solutions?
Composite panels are vital in the energy sector, particularly for wind turbine blades and energy storage systems. Their lightweight and durable nature leads to increased efficiency and longevity of energy components, which is crucial for maximizing output and reducing maintenance costs. Buyers from South America and Europe must understand the specific requirements of the energy sector, including compliance with sustainability standards and the availability of advanced composite materials.
Related Video: Aluminium Composite Panel Installation
3 Common User Pain Points for ‘composite panel supplier’ & Their Solutions
Scenario 1: Difficulty in Understanding Composite Panel Specifications
The Problem:
B2B buyers often struggle to interpret the technical specifications of composite panels. For instance, a construction firm in South America may find it challenging to differentiate between various types of composite materials like fiberglass and carbon fiber. This lack of clarity can lead to the selection of inappropriate materials for specific applications, resulting in structural inefficiencies or increased costs.
The Solution:
To overcome this challenge, buyers should request detailed product datasheets from their composite panel suppliers. These datasheets should include information on mechanical properties (like tensile strength and impact resistance), thermal properties (such as thermal conductivity), and chemical resistance ratings. Additionally, potential buyers can engage in consultations with suppliers to discuss project requirements and get tailored advice. It is beneficial to use a standardized set of questions to guide these discussions, ensuring all relevant factors—such as environmental conditions and load-bearing requirements—are considered. Establishing a collaborative relationship with suppliers can enhance understanding and lead to more effective material selection.
Scenario 2: Concerns Over Supply Chain Reliability
The Problem:
International buyers, particularly from Africa and the Middle East, often face anxiety regarding the reliability of their composite panel suppliers. Fluctuating shipping schedules and unexpected tariffs can disrupt project timelines, causing delays and financial losses. For example, a contractor might rely on composite panels for a major infrastructure project and find that delays in supply lead to significant penalties.
The Solution:
To mitigate these risks, buyers should prioritize suppliers with a proven track record of reliability and transparency in their supply chains. Conducting due diligence through supplier audits and requesting references from other clients can provide insights into a supplier’s operational stability. Additionally, buyers should explore establishing long-term contracts with suppliers that include clauses for timely delivery and penalties for non-compliance. This approach not only fosters a sense of security but also encourages suppliers to invest in better logistics and inventory management practices.
Scenario 3: Limited Knowledge on Installation Techniques
The Problem:
Another common pain point for B2B buyers is the lack of knowledge regarding the proper installation techniques for composite panels. In Europe, for example, architects and builders may specify composite materials without fully understanding the nuances of their installation, leading to improper fittings or structural weaknesses. This oversight can result in costly repairs or redesigns, undermining project integrity.
The Solution:
To address this issue, buyers should seek suppliers that provide comprehensive installation guidelines and training resources. This may include detailed manuals, video tutorials, and on-site training sessions led by experienced technicians. Furthermore, buyers should consider collaborating with certified installers who have expertise in working with composite materials. By investing time in training and ensuring that all team members understand installation protocols, companies can significantly reduce the risk of errors and enhance the longevity of their projects. Engaging with suppliers for ongoing support during the installation phase can also facilitate smoother project execution and better end results.
Strategic Material Selection Guide for composite panel supplier
What Are the Most Common Materials Used by Composite Panel Suppliers?
When selecting composite materials for panel applications, international B2B buyers must consider various factors, including performance properties, cost, and regional compliance standards. Below are analyses of four common composite materials used by suppliers, focusing on their properties, advantages, limitations, and specific considerations for buyers from Africa, South America, the Middle East, and Europe.
What Are the Key Properties of Fiber-Reinforced Polymer (FRP)?
Fiber-Reinforced Polymer (FRP) is a composite material made from a polymer matrix reinforced with fibers, typically glass or carbon.
- Key Properties: FRP exhibits high strength-to-weight ratios, excellent corrosion resistance, and good thermal stability. It can withstand temperatures up to 100°C (212°F) and pressures depending on the specific resin used.
- Pros & Cons: The durability of FRP is notable, making it suitable for harsh environments. However, manufacturing can be complex and costly, especially when using carbon fibers. FRP panels are ideal for applications in marine, automotive, and construction sectors.
- Impact on Application: FRP is compatible with various media, including chemicals and moisture, making it suitable for environments like wastewater treatment plants.
- Considerations for International Buyers: Buyers must ensure compliance with international standards such as ASTM D638 for tensile properties. In regions like Europe, adherence to the EN 13706 standard is essential.
How Does Aluminum Composite Material (ACM) Perform?
Aluminum Composite Material (ACM) consists of two thin layers of aluminum enclosing a non-aluminum core, often made of polyethylene.
- Key Properties: ACM is lightweight, offers good thermal insulation, and has a fire resistance rating depending on the core material. It typically withstands temperatures up to 80°C (176°F).
- Pros & Cons: ACM is cost-effective and easy to fabricate, making it popular for architectural applications. However, it may not be as durable as other composites in extreme conditions, and its core material can be susceptible to environmental degradation.
- Impact on Application: ACM is widely used in building facades and interior applications, providing aesthetic appeal and functionality.
- Considerations for International Buyers: Compliance with fire safety standards (e.g., EN 13501) is crucial, especially in Europe. Buyers should also consider local regulations regarding aluminum recycling.
What Are the Advantages of Using Polypropylene Composite Panels?
Polypropylene composites consist of a polypropylene matrix reinforced with various fillers or fibers.
- Key Properties: These panels are lightweight, have excellent chemical resistance, and can operate in temperatures up to 90°C (194°F). They also offer good impact resistance.
- Pros & Cons: Polypropylene composites are relatively inexpensive and easy to process, making them suitable for a variety of applications. However, they may not provide the same strength as FRP or ACM, limiting their use in high-stress environments.
- Impact on Application: Ideal for applications requiring chemical resistance, such as in the food and pharmaceutical industries.
- Considerations for International Buyers: Buyers should check compliance with FDA regulations for food contact materials in regions like the US and EU.
Why Choose Reinforced Concrete for Composite Panels?
Reinforced concrete is a composite material where concrete is reinforced with steel bars or fibers.
- Key Properties: This material offers high compressive strength, durability, and fire resistance. It can withstand temperatures exceeding 200°C (392°F) and is suitable for high-load applications.
- Pros & Cons: Reinforced concrete is highly durable and cost-effective for large-scale applications. However, it is significantly heavier than other composites, which may increase transportation costs and limit design flexibility.
- Impact on Application: Commonly used in construction for structural panels, bridges, and foundations, particularly in seismic zones.
- Considerations for International Buyers: Compliance with local building codes and standards, such as Eurocode in Europe, is essential for ensuring safety and quality.
Summary Table of Composite Materials for Panel Applications
Material | Typical Use Case for Composite Panel Supplier | Key Advantage | Key Disadvantage/Limitation | Relative Cost (Low/Med/High) |
---|---|---|---|---|
Fiber-Reinforced Polymer (FRP) | Marine, automotive, construction | High strength-to-weight ratio | Complex manufacturing process | High |
Aluminum Composite Material (ACM) | Architectural facades, interior applications | Cost-effective and easy to fabricate | Less durable in extreme conditions | Medium |
Polypropylene Composite Panels | Food and pharmaceutical industries | Excellent chemical resistance | Lower strength compared to other composites | Low |
Reinforced Concrete | Structural panels, bridges, foundations | High durability and fire resistance | Heavy, limiting design flexibility | Medium |
This guide provides a comprehensive overview of the strategic material selection process for composite panel suppliers, ensuring that international B2B buyers can make informed decisions tailored to their specific needs and regional requirements.
In-depth Look: Manufacturing Processes and Quality Assurance for composite panel supplier
What Are the Main Stages of the Manufacturing Process for Composite Panels?
The manufacturing process for composite panels involves several critical stages that ensure the final product meets the necessary performance and quality standards. Understanding these stages can help B2B buyers assess potential suppliers more effectively.
1. Material Preparation: What Is Involved?
Material preparation is the first step in the composite panel manufacturing process. This involves selecting the appropriate matrix and reinforcement materials. Common matrices include thermosetting resins like epoxy or polyester, while reinforcements often consist of fiberglass, carbon fiber, or natural fibers.
During this stage, raw materials are inspected for quality and specifications. Proper handling and storage are crucial to prevent contamination or degradation of materials, which can affect the final product’s performance.
2. Forming: How Are Composite Panels Shaped?
The forming process typically involves methods such as molding, laminating, or pultrusion, depending on the desired panel thickness and application.
- Molding: This technique includes processes like compression and injection molding, where the prepared materials are placed into molds to achieve the desired shape.
- Laminating: In this method, layers of materials are bonded together using heat and pressure to create a strong composite structure.
- Pultrusion: This continuous process pulls raw materials through a heated die to form long, uniform composite shapes, ideal for panels.
Each method has its advantages and specific applications, making it essential for buyers to understand which process aligns best with their needs.
3. Assembly: How Are Components Joined?
Once the panels are formed, the assembly stage involves joining various components if the panel is part of a larger system. Techniques such as adhesive bonding, mechanical fastening, or welding may be utilized, depending on the panel’s design and application requirements.
Adhesive bonding is particularly common in composite applications due to its ability to create strong, lightweight joints without adding significant weight.
4. Finishing: What Techniques Ensure Quality?
The finishing stage includes surface treatment, coating, and any additional modifications required for aesthetic or functional purposes. This may involve sanding, painting, or applying protective coatings to enhance durability and resistance to environmental factors.
Finishing processes are essential for ensuring that the panels meet specific performance criteria, such as UV resistance or corrosion protection, making them suitable for various applications, from construction to automotive.
What Quality Assurance Standards Should B2B Buyers Be Aware Of?
Quality assurance (QA) is a critical aspect of the composite panel manufacturing process, ensuring that products meet international and industry-specific standards. Understanding these can help buyers make informed decisions when selecting suppliers.
Relevant International Standards: What Should You Look For?
ISO 9001 is one of the most recognized quality management system standards globally. Suppliers adhering to this standard demonstrate a commitment to consistent quality and customer satisfaction. Additionally, industry-specific certifications such as CE (Conformité Européenne) for products sold in Europe or API (American Petroleum Institute) standards for oil and gas applications are essential for ensuring compliance with safety and performance regulations.
What Are the Key Quality Control Checkpoints?
Quality control (QC) checkpoints are integral throughout the manufacturing process. Key checkpoints include:
- Incoming Quality Control (IQC): This step involves inspecting raw materials upon arrival to ensure they meet specified requirements.
- In-Process Quality Control (IPQC): Conducted during the manufacturing process, IPQC checks ensure that production processes are running smoothly and that the panels are being produced to the required specifications.
- Final Quality Control (FQC): This final inspection verifies that the finished products meet all quality standards before they are shipped to customers.
Implementing these checkpoints helps mitigate risks and ensures that any defects are identified and rectified before reaching the market.
What Testing Methods Are Common in Composite Panel Quality Assurance?
Various testing methods are employed to evaluate the performance and durability of composite panels. Understanding these methods is essential for B2B buyers who wish to verify the quality of their suppliers’ products.
- Mechanical Testing: Tests such as tensile strength, flexural strength, and impact resistance are crucial for determining the structural integrity of composite panels.
- Thermal Testing: Evaluating how panels respond to temperature fluctuations ensures they can withstand varying environmental conditions.
- Chemical Resistance Testing: This assesses how well the composite material can resist degradation from exposure to chemicals, which is particularly important for panels used in industrial settings.
How Can B2B Buyers Verify Supplier Quality Control?
B2B buyers should take proactive steps to verify a supplier’s quality control processes to ensure they receive high-quality products.
1. Conducting Audits: What Should You Look For?
Conducting on-site audits of potential suppliers is a crucial step in assessing their manufacturing and quality control practices. During an audit, buyers should evaluate the supplier’s adherence to quality standards, inspect production facilities, and review documentation related to their quality management system.
2. Reviewing Quality Reports: What Information Is Essential?
Buyers should request and review quality control reports that detail the results of IQC, IPQC, and FQC processes. These reports provide insights into the supplier’s consistency in meeting quality standards and any corrective actions taken in response to identified issues.
3. Utilizing Third-Party Inspections: How Can This Enhance Assurance?
Engaging third-party inspection services can provide an unbiased assessment of a supplier’s manufacturing processes and quality control measures. Third-party inspectors can conduct thorough evaluations and testing, offering buyers additional confidence in the supplier’s ability to deliver high-quality composite panels.
What Are the Quality Control Nuances for International B2B Buyers?
For international buyers, particularly those from Africa, South America, the Middle East, and Europe, understanding the nuances of quality control can impact procurement decisions significantly.
- Cultural Differences: Different regions may have varying interpretations of quality standards. It’s crucial for buyers to communicate their expectations clearly and ensure that suppliers are aligned with their quality requirements.
- Regulatory Compliance: Buyers must be aware of the regulatory requirements in their home countries, as these may differ from the supplier’s local regulations. Ensuring compliance with both sets of standards is vital for successful international transactions.
- Logistical Considerations: Quality assurance does not end at the production facility. Buyers should consider how products will be transported and stored, as improper handling can compromise quality. Engaging suppliers who understand international shipping protocols can mitigate these risks.
By focusing on these aspects of the manufacturing and quality assurance processes, B2B buyers can make informed decisions when selecting composite panel suppliers, ensuring they receive products that meet their specific needs and quality standards.
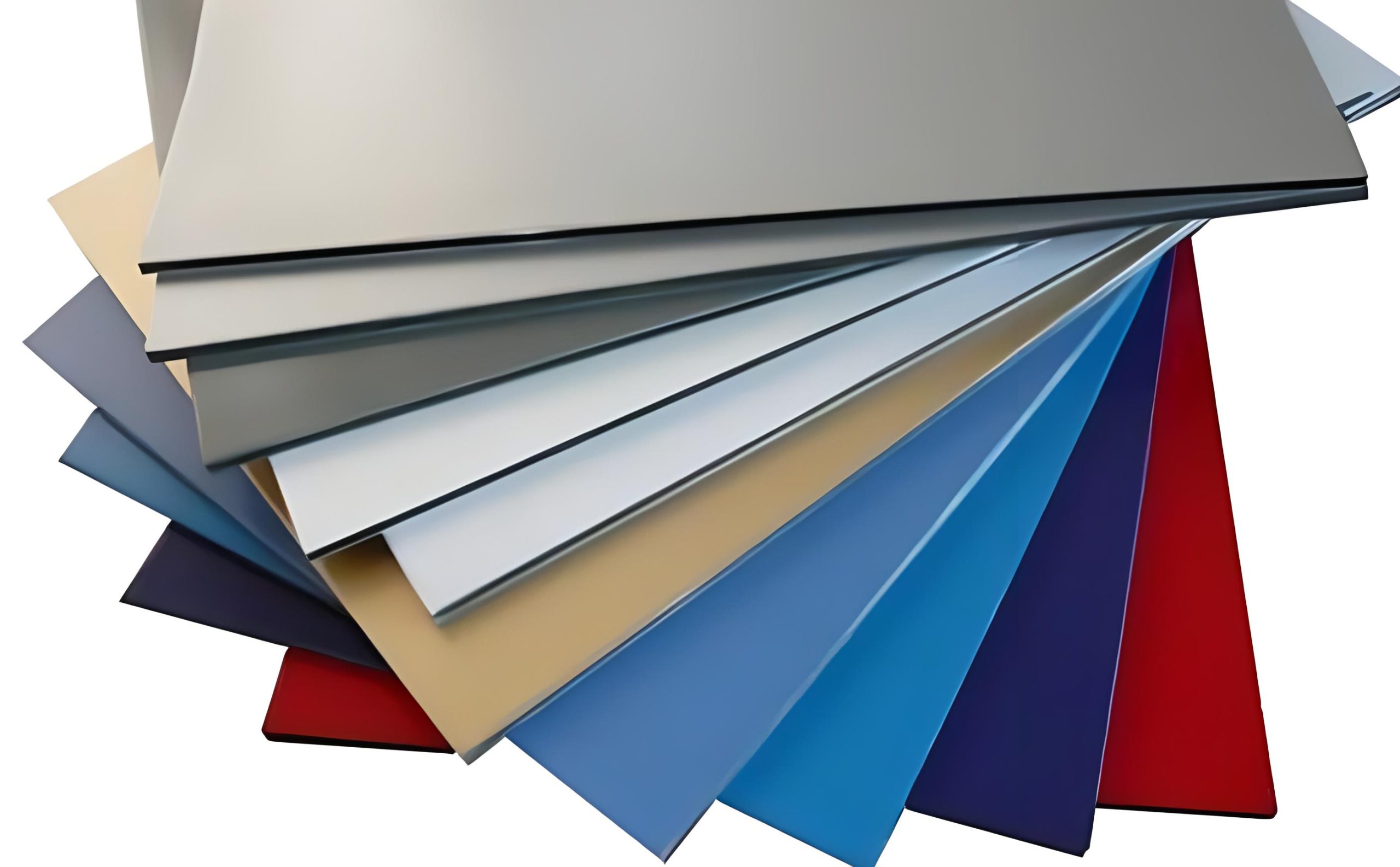
A stock image related to composite panel supplier.
Practical Sourcing Guide: A Step-by-Step Checklist for ‘composite panel supplier’
In today’s competitive marketplace, sourcing composite panels effectively is vital for ensuring quality and performance in your projects. This practical guide provides a step-by-step checklist to help international B2B buyers, particularly from Africa, South America, the Middle East, and Europe, navigate the procurement process for composite panel suppliers.
Step 1: Define Your Technical Specifications
Establishing clear technical specifications is essential for ensuring that the composite panels meet your project requirements. Consider the intended application, environmental conditions, and performance metrics such as strength, weight, and durability. This clarity helps in aligning your needs with supplier capabilities.
- Key Considerations:
- Material type (e.g., polymer matrix, fiberglass)
- Thickness and dimensions
- Desired mechanical properties (e.g., tensile strength)
Step 2: Conduct Market Research for Suppliers
Researching potential suppliers can provide insights into their market presence and reputation. Utilize online directories, industry forums, and trade shows to identify suppliers specializing in composite panels. This initial research lays the groundwork for a more informed selection process.
- Where to Look:
- Industry-specific trade shows
- Online marketplaces and supplier directories
- Recommendations from industry peers
Step 3: Evaluate Supplier Credentials and Experience
Before making a commitment, it’s crucial to assess the credentials and experience of potential suppliers. Review their certifications, industry affiliations, and years of experience in manufacturing composite panels. This evaluation helps ensure you are partnering with a reliable and knowledgeable supplier.
- What to Check:
- ISO certifications or other quality assurance standards
- Case studies and testimonials from similar projects
- Experience with international shipping and compliance
Step 4: Request Samples for Quality Assessment
Obtaining samples is a critical step in evaluating the quality of the composite panels. This allows you to assess their physical properties, finish, and overall suitability for your application. A hands-on evaluation can help prevent costly mistakes later in the procurement process.
- Sample Evaluation Focus:
- Surface finish and aesthetic qualities
- Mechanical testing results (e.g., tensile tests)
- Performance in real-world conditions (if applicable)
Step 5: Understand Pricing Structures and Terms
Gaining a clear understanding of pricing is essential for budget management. Inquire about pricing structures, including bulk discounts, shipping costs, and payment terms. This knowledge can help you negotiate better terms and avoid unexpected expenses.
- Important Pricing Factors:
- Cost per unit vs. bulk pricing
- Shipping and handling fees
- Payment terms (e.g., upfront payment vs. net terms)
Step 6: Assess Customer Service and Support
A supplier’s customer service can significantly impact your procurement experience. Evaluate their responsiveness, support during the sourcing process, and willingness to provide technical assistance. Strong customer support can enhance communication and resolve issues quickly.
- Indicators of Good Support:
- Availability of a dedicated account manager
- Technical support for installation and maintenance
- Clarity of communication regarding order status
Step 7: Finalize the Contract with Clear Terms
Once you have selected a supplier, ensure that the contract clearly outlines all terms and conditions, including delivery schedules, quality standards, and penalties for non-compliance. A well-defined contract protects both parties and fosters a transparent business relationship.
- Key Elements to Include:
- Delivery timelines and logistics
- Quality assurance metrics
- Terms for returns and disputes
Following this checklist can streamline your sourcing process and help you secure a reliable composite panel supplier that meets your specific needs.
Comprehensive Cost and Pricing Analysis for composite panel supplier Sourcing
What Are the Key Cost Components for Composite Panel Suppliers?
When sourcing composite panels, understanding the cost structure is crucial for international B2B buyers. The primary components that contribute to the overall cost include materials, labor, manufacturing overhead, tooling, quality control (QC), logistics, and supplier margin.
-
Materials: The choice of materials significantly impacts the cost. Composite panels are typically made from a combination of matrix resins and reinforcing fibers. For instance, fiberglass and carbon fiber are common choices. Prices can fluctuate based on global supply chain dynamics and availability of raw materials.
-
Labor: Labor costs vary by region. In countries with higher labor costs, such as those in Western Europe, the production expenses will be higher compared to emerging markets in Africa or South America. Understanding local labor market conditions can help buyers anticipate these costs.
-
Manufacturing Overhead: This includes expenses related to the facilities and equipment used in production. Overhead costs can vary significantly based on the supplier’s operational efficiency and technology used in the manufacturing process.
-
Tooling: Custom tooling for specific panel designs can add significant costs. If you require unique specifications, be prepared for higher initial investments in tooling. This is particularly relevant for buyers looking to produce high volumes of specialized composite panels.
-
Quality Control: Ensuring product quality involves additional costs. Suppliers who adhere to international certifications (e.g., ISO, ASTM) may charge a premium for their processes but can provide reassurance regarding product reliability.
-
Logistics: Transporting composite panels can be costly, especially for international shipments. Factors such as distance, shipping mode (air vs. sea), and insurance impact logistics costs. Buyers should consider these when calculating total expenses.
-
Supplier Margin: Different suppliers will have varying margins based on their market position, reputation, and service offerings. Understanding these margins can help buyers negotiate better pricing.
What Influences Pricing for Composite Panels?
Several factors can influence the pricing of composite panels, particularly for international buyers from diverse regions such as Africa, South America, the Middle East, and Europe.
-
Volume/MOQ: Higher order volumes often result in lower per-unit costs. Suppliers may have minimum order quantities (MOQs) which can affect pricing for smaller buyers.
-
Specifications and Customization: Customized panels tailored to specific applications can incur additional costs. Buyers should be clear about their requirements to avoid unexpected expenses.
-
Material Quality and Certifications: The quality of materials and the presence of certifications can significantly affect pricing. Higher-quality materials often lead to better performance and durability, justifying the increased cost.
-
Supplier Factors: The experience and reputation of the supplier can also dictate pricing. Established suppliers with a proven track record may charge more but can offer reliability and superior customer service.
-
Incoterms: The terms of shipping (Incoterms) can influence total costs. For example, DDP (Delivered Duty Paid) pricing includes shipping and customs duties, which can be beneficial for buyers unfamiliar with import regulations.
What Are the Best Negotiation Strategies for International Buyers?
For international B2B buyers, particularly those from regions like Africa, South America, the Middle East, and Europe, effective negotiation strategies can lead to significant cost savings.
-
Understand Total Cost of Ownership: Consider all costs associated with the product, including maintenance, shipping, and potential delays. This holistic view can guide you to make better purchasing decisions.
-
Leverage Volume Discounts: If your business can commit to larger volumes, use this as leverage in negotiations. Suppliers are often willing to offer better pricing for bulk orders.
-
Seek Multiple Quotes: Don’t settle for the first offer. Gathering multiple quotes can provide insight into market rates and help in negotiating better terms.
-
Build Long-Term Relationships: Establishing a strong relationship with suppliers can lead to preferential pricing and terms in the future.
-
Be Aware of Pricing Nuances: Understand the local market conditions and currency fluctuations that may affect pricing. This knowledge can help you negotiate more effectively.
Conclusion
While sourcing composite panels, understanding the comprehensive cost structure and pricing influencers is essential for international buyers. By being informed about cost components, leveraging negotiation strategies, and considering the total cost of ownership, buyers can make strategic decisions that lead to cost-effective sourcing. Always remember to account for the specific market dynamics of your region, as they can significantly impact the overall procurement strategy.
Alternatives Analysis: Comparing composite panel supplier With Other Solutions
When considering a composite panel supplier, it’s essential for international B2B buyers to evaluate viable alternatives that can meet their specific needs. Each option has unique attributes that may better align with project requirements, budget constraints, or operational capabilities. Below, we compare composite panel suppliers with two alternatives: aluminum panels and traditional wood panels.
Comparison Table of Composite Panel Supplier and Alternatives
Comparison Aspect | Composite Panel Supplier | Aluminum Panels | Traditional Wood Panels |
---|---|---|---|
Performance | High strength-to-weight ratio, excellent durability, and corrosion resistance | Strong, lightweight, and resistant to rust and corrosion | Good strength, but can warp or rot over time |
Cost | Mid-range to high; initial investment may be offset by longevity | Generally higher initial cost but can be cost-effective over time due to low maintenance | Low initial cost but may require more frequent replacements |
Ease of Implementation | Requires specialized tools for cutting and installation | Easy to install; available in pre-fabricated sections | Simple to work with; can be cut with standard tools |
Maintenance | Minimal maintenance required; resistant to environmental damage | Very low maintenance; does not require painting or sealing | Requires regular maintenance and treatment to prevent damage |
Best Use Case | Ideal for high-performance applications in construction, automotive, and aerospace | Suitable for exterior applications, facades, and architectural elements | Best for decorative applications and traditional construction |
Detailed Breakdown of Each Alternative
How Do Aluminum Panels Compare to Composite Panels?
Aluminum panels are a popular alternative due to their inherent strength and lightweight nature. They provide excellent resistance to environmental factors, making them ideal for outdoor applications. However, the initial cost can be higher compared to composite panels. While they require minimal maintenance, the manufacturing process can be energy-intensive, which may be a consideration for environmentally conscious buyers. Aluminum panels are particularly well-suited for modern architectural designs where aesthetics and performance are critical.
What Are the Advantages and Disadvantages of Traditional Wood Panels?
Traditional wood panels represent a classic choice with a lower initial investment. They are widely available and easy to work with, allowing for quick installation and customization. However, wood can be prone to warping, rot, and insect damage, necessitating regular maintenance to ensure longevity. In applications where aesthetics are prioritized, wood provides a warm, natural look that composite materials may not replicate. Nonetheless, for projects requiring high durability and environmental resistance, wood may fall short compared to composite panels.
Conclusion: How to Choose the Right Solution for Your Needs
When deciding between a composite panel supplier and alternative materials, B2B buyers should assess their specific project requirements, including performance criteria, budget, and long-term maintenance expectations. Composite panels excel in demanding environments, offering enhanced durability and reduced maintenance needs. In contrast, aluminum panels may serve well in architectural applications, while traditional wood panels can be more suitable for aesthetic-focused projects. Ultimately, the right choice will depend on balancing performance, cost, and application suitability to achieve the best results for your business.
Essential Technical Properties and Trade Terminology for composite panel supplier
What Are the Key Technical Properties of Composite Panels?
Understanding the essential technical properties of composite panels is crucial for international B2B buyers, particularly those in Africa, South America, the Middle East, and Europe. These properties not only influence the performance of the panels but also impact cost-effectiveness and suitability for various applications.
1. Material Grade
Material grade refers to the quality and type of materials used in the composite panel. This specification is critical because it determines the panel’s strength, durability, and resistance to environmental factors. Higher-grade materials often come at a premium but can offer significant long-term savings due to reduced maintenance and replacement costs.
2. Tolerance
Tolerance defines the allowable deviation from specified dimensions during manufacturing. In composite panels, this is vital for ensuring that components fit together correctly in assembly. Tight tolerances can enhance the structural integrity and aesthetic appeal of the final product, making it a key consideration for projects requiring precision, such as aerospace or automotive applications.
3. Weight-to-Strength Ratio
The weight-to-strength ratio is a measure of how much strength a material offers relative to its weight. Composite panels often boast superior ratios compared to traditional materials like metals. This property is particularly beneficial in industries such as transportation and construction, where reducing weight can lead to lower fuel consumption and improved overall efficiency.
4. Thermal Resistance
Thermal resistance indicates how well a composite panel can withstand temperature fluctuations without degrading. This property is essential for applications exposed to extreme conditions, such as aerospace or outdoor constructions. Understanding thermal resistance helps buyers select the right materials for their specific environmental challenges, ensuring longevity and reliability.
5. Corrosion Resistance
Corrosion resistance is the ability of a composite material to withstand degradation due to environmental factors such as moisture and chemicals. For industries operating in harsh conditions, selecting composite panels with high corrosion resistance can prevent costly repairs and downtime, making this a critical factor in procurement decisions.
What Are Common Trade Terms Used in Composite Panel Supply?
Familiarity with industry jargon is essential for effective communication and negotiation in the B2B marketplace. Here are some common terms that buyers should understand:
1. OEM (Original Equipment Manufacturer)
An OEM is a company that produces parts or equipment that may be marketed by another manufacturer. In the context of composite panels, buyers often seek OEM suppliers to ensure they receive components that meet specific performance and quality standards.
2. MOQ (Minimum Order Quantity)
MOQ refers to the smallest quantity of a product that a supplier is willing to sell. Understanding MOQs is vital for buyers, as it can impact inventory costs and cash flow. Negotiating favorable MOQs can lead to significant savings, especially for smaller companies or those testing new products.
3. RFQ (Request for Quotation)
An RFQ is a document that buyers send to suppliers to request pricing and terms for specific products. This process is crucial for comparing different suppliers and ensuring that the best value is obtained. Buyers should be precise in their RFQs to receive accurate and relevant quotes.
4. Incoterms (International Commercial Terms)
Incoterms are a set of predefined international trade terms that clarify the responsibilities of buyers and sellers regarding shipping, insurance, and tariffs. Familiarity with Incoterms helps B2B buyers manage their logistics and understand the costs associated with importing composite panels.
5. Lead Time
Lead time is the time taken from placing an order until the delivery of the product. This term is particularly significant in industries with tight deadlines. Buyers should always clarify lead times to ensure that their project schedules align with supplier capabilities.
By grasping these technical properties and trade terminologies, international B2B buyers can make informed decisions when sourcing composite panels, ultimately enhancing their operational efficiency and cost-effectiveness.
Navigating Market Dynamics and Sourcing Trends in the composite panel supplier Sector
What Are the Current Market Dynamics and Key Trends for Composite Panel Suppliers?
The composite panel supplier sector is witnessing significant growth driven by several global factors, including increasing demand for lightweight materials across industries such as construction, automotive, and aerospace. International B2B buyers, particularly from Africa, South America, the Middle East, and Europe, are increasingly seeking composite materials due to their superior strength-to-weight ratios and resistance to environmental degradation.
Emerging technologies, such as advanced manufacturing techniques and digital supply chain solutions, are reshaping sourcing trends. For instance, the rise of additive manufacturing and CNC machining has enabled more precise production of composite panels tailored to specific applications. This technological shift also facilitates shorter lead times and reduces waste, appealing to environmentally conscious buyers. Additionally, the integration of Industry 4.0 technologies allows for real-time monitoring and data analytics, enhancing supply chain transparency and efficiency.
The market is also characterized by a growing emphasis on customization. As industries move towards more specialized applications, suppliers who can offer bespoke solutions will have a competitive edge. Buyers from regions like Colombia and the UK are increasingly looking for suppliers who can adapt their offerings to meet unique project requirements, thus fostering collaboration and innovation.
How Is Sustainability Influencing Sourcing Decisions in the Composite Panel Sector?
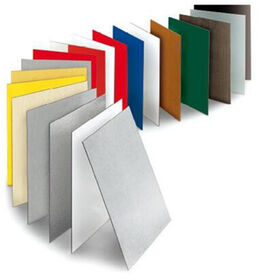
A stock image related to composite panel supplier.
Sustainability is becoming a crucial consideration for B2B buyers in the composite panel sector. The environmental impact of materials is under scrutiny, with companies seeking suppliers that prioritize eco-friendly practices. This trend is particularly relevant for international buyers in regions like Africa and South America, where environmental regulations are becoming stricter and consumer demand for sustainable products is rising.
Ethical sourcing is equally important. Buyers are increasingly concerned about the transparency of supply chains and the ethical implications of sourcing materials. This includes the use of responsibly sourced raw materials and adherence to fair labor practices. Suppliers who can demonstrate compliance with international sustainability standards and who possess certifications such as ISO 14001 (Environmental Management) or FSC (Forest Stewardship Council) certification for wood-based composites will appeal to ethically-minded buyers.
Moreover, the development of ‘green’ composite materials—those made from renewable resources or recycled content—is gaining traction. These materials not only reduce the carbon footprint but also align with the broader goals of circular economy initiatives. As a result, buyers are encouraged to seek out composite panel suppliers who are actively investing in sustainable innovations and can provide environmentally friendly options.
What Is the Historical Context of Composite Materials in B2B?
The use of composite materials can be traced back thousands of years, with early examples including plywood from ancient Iraq and the linen-based death masks of Egyptian mummies. Fast forward to the 20th century, the industrial revolution catalyzed the development of synthetic composites, such as Bakelite and fiberglass, revolutionizing various industries.
The aerospace sector marked a significant turning point in the adoption of composite materials, particularly with the introduction of carbon fiber-reinforced polymers in aircraft manufacturing. By the mid-1990s, composite panels became mainstream in construction and automotive applications due to their cost-effectiveness and enhanced performance characteristics. Today, the evolution of composites continues, driven by advancements in technology and a growing emphasis on sustainability, setting the stage for future innovations that will further impact the B2B landscape.
In conclusion, international B2B buyers must navigate a dynamic market characterized by technological advancements, sustainability considerations, and historical context to make informed sourcing decisions in the composite panel supplier sector.
Frequently Asked Questions (FAQs) for B2B Buyers of composite panel supplier
-
How do I choose the right composite panel supplier for my business needs?
Choosing the right composite panel supplier involves evaluating several key factors. Start by assessing the supplier’s experience in the industry and their track record with similar projects. Request samples of their products to evaluate quality and compliance with your specifications. Additionally, consider their ability to customize products to meet your specific requirements, as well as their capacity to handle your expected order volume. Finally, review their customer service and support capabilities, including responsiveness to inquiries and willingness to provide technical assistance. -
What are the most important certifications to look for in a composite panel supplier?
When sourcing composite panels, it’s essential to look for suppliers with relevant industry certifications. Key certifications include ISO 9001 for quality management systems, ASTM standards for material specifications, and CE marking for compliance with European safety standards. Additionally, check for any environmental certifications such as ISO 14001 or adherence to the REACH regulation in Europe, which ensures that chemicals used in products are safe. These certifications indicate a supplier’s commitment to quality, safety, and environmental responsibility. -
What customization options are typically available for composite panels?
Composite panel suppliers often provide a range of customization options to meet specific project needs. Common customization options include variations in thickness, size, and surface finishes. You can also request specific material compositions to enhance properties like insulation, fire resistance, or aesthetic appeal. Some suppliers may offer additional features such as pre-drilled holes for easy installation or custom colors. Discussing your requirements upfront with potential suppliers can help you understand the extent of their customization capabilities. -
What is the minimum order quantity (MOQ) for composite panels?
Minimum order quantities (MOQs) for composite panels can vary significantly between suppliers and depend on factors such as material type and customization options. Typically, MOQs can range from a few hundred square meters to several thousand, especially for specialized products. It’s crucial to communicate your specific needs with suppliers to find one that can accommodate your order size without compromising quality or increasing costs. Some suppliers may offer flexibility in MOQs for first-time buyers or long-term partnerships. -
What payment terms should I expect when working with international suppliers?
Payment terms for international orders of composite panels can vary widely based on the supplier’s policies and the buyer’s location. Common payment methods include letters of credit, wire transfers, and payment in advance. Suppliers may offer terms such as 30% upfront payment with the balance due upon delivery. Always clarify payment terms before finalizing an agreement to avoid misunderstandings. Additionally, consider discussing options for installment payments if your order is large, as this can help manage cash flow. -
How can I ensure quality assurance for my composite panels?
To ensure quality assurance, establish clear specifications and performance criteria before placing an order. Ask the supplier about their quality control processes, including testing methods and inspection protocols. Request documentation, such as certificates of compliance and test reports, to validate that the products meet your standards. Additionally, consider conducting an on-site audit of the supplier’s manufacturing facilities if feasible, or request third-party inspections to verify quality before shipment.
-
What are the logistics considerations for importing composite panels?
When importing composite panels, logistics considerations are critical to ensure timely delivery and cost-effectiveness. Evaluate shipping options, including air freight for urgent needs or sea freight for larger shipments to save costs. Understand the customs regulations and duties applicable in your country, as these can impact overall costs and delivery times. Collaborating with a logistics partner familiar with international trade can streamline the process, helping you navigate documentation and compliance requirements efficiently. -
What are the common applications for composite panels in various industries?
Composite panels are versatile materials used across multiple industries due to their enhanced properties. In construction, they are often utilized for wall cladding, roofing, and flooring solutions due to their lightweight and insulation capabilities. The automotive industry employs composite panels for bodywork and interior components to reduce weight and improve fuel efficiency. Additionally, they are used in aerospace applications for structural components, and in marine settings for boat hulls. Understanding the applications relevant to your industry can guide your selection process when sourcing composite panels.
Important Disclaimer & Terms of Use
⚠️ Important Disclaimer
The information provided in this guide, including content regarding manufacturers, technical specifications, and market analysis, is for informational and educational purposes only. It does not constitute professional procurement advice, financial advice, or legal advice.
While we have made every effort to ensure the accuracy and timeliness of the information, we are not responsible for any errors, omissions, or outdated information. Market conditions, company details, and technical standards are subject to change.
B2B buyers must conduct their own independent and thorough due diligence before making any purchasing decisions. This includes contacting suppliers directly, verifying certifications, requesting samples, and seeking professional consultation. The risk of relying on any information in this guide is borne solely by the reader.
Strategic Sourcing Conclusion and Outlook for composite panel supplier
As the global demand for composite panels continues to rise, international B2B buyers must prioritize strategic sourcing to leverage the unique advantages these materials offer. Key takeaways emphasize the importance of understanding composite materials’ properties, such as their lightweight strength, corrosion resistance, and design flexibility, which can significantly enhance product performance across various industries, including construction, automotive, and aerospace.
Strategic sourcing not only ensures access to high-quality composite panels but also fosters strong relationships with reliable suppliers. This can lead to better pricing, improved supply chain efficiency, and enhanced innovation through collaborative development. For buyers in Africa, South America, the Middle East, and Europe, understanding regional market dynamics and supplier capabilities is crucial for making informed decisions that align with their specific needs and challenges.
Looking ahead, as the composite materials market evolves, embracing sustainable sourcing practices and advanced technologies will be vital. By staying informed and proactive, international B2B buyers can position themselves to harness the full potential of composite panels, driving growth and competitiveness in their respective markets. Engage with trusted suppliers today to explore innovative solutions that can elevate your business.