Discover Top Container House Suppliers: Save Costs Today (2025)
Introduction: Navigating the Global Market for container house supplier
In today’s rapidly evolving global market, sourcing a reliable container house supplier can pose significant challenges for international B2B buyers. Whether you’re seeking innovative housing solutions for urban development in South Africa or sustainable living spaces in Europe, the variety of options available can be overwhelming. This guide aims to demystify the complexities of selecting the right container house supplier by providing actionable insights and detailed information on various types of container houses, their applications, and the nuances of supplier vetting.
Buyers from diverse regions, including Africa, South America, the Middle East, and Europe, will find tailored strategies to navigate the intricacies of the container housing market. We will explore critical aspects such as cost considerations, quality standards, and logistical challenges that can influence your purchasing decisions. Additionally, we will address how to assess suppliers effectively, ensuring that you choose partners who align with your project goals and sustainability requirements.
By leveraging this comprehensive guide, international B2B buyers can make informed decisions that not only meet their immediate needs but also contribute to long-term project success. From understanding market trends to evaluating supplier credibility, this resource is designed to empower you in selecting the most suitable container house solutions for your unique business objectives.
Understanding container house supplier Types and Variations
Type Name | Key Distinguishing Features | Primary B2B Applications | Brief Pros & Cons for Buyers |
---|---|---|---|
Standard Shipping Containers | Basic, modular units available in various sizes. | Temporary housing, storage solutions | Pros: Cost-effective, widely available. Cons: Limited customization options. |
Modified Container Homes | Containers reconfigured for living or working spaces. | Residential, offices, pop-up shops | Pros: Customizable designs, energy-efficient. Cons: Higher upfront costs. |
Luxury Container Homes | High-end finishes and amenities, often multi-story. | Luxury housing, boutique hotels | Pros: Aesthetic appeal, premium materials. Cons: Significant investment required. |
Eco-Friendly Containers | Built using sustainable materials and practices. | Green building projects, eco-villages | Pros: Sustainable, lower environmental impact. Cons: May have limited availability. |
Container Office Solutions | Configured for professional workspaces, often mobile. | Remote offices, construction sites | Pros: Quick setup, mobility. Cons: Space constraints for larger teams. |
What Are Standard Shipping Containers and Their B2B Relevance?
Standard shipping containers are the most common type utilized in the container housing market. They are primarily made of steel, providing durability and security. With dimensions typically ranging from 20 to 40 feet, they serve various applications, including temporary housing and storage solutions. For B2B buyers, their cost-effectiveness is a significant advantage, as they are readily available in numerous locations worldwide. However, the lack of customization options can be a drawback for businesses looking for unique designs or specific functionalities.
How Do Modified Container Homes Meet Diverse Business Needs?
Modified container homes are standard shipping containers that have been reconfigured for various living or working purposes. These units often include insulation, plumbing, and electrical systems, making them suitable for residential use, offices, or pop-up retail spaces. The primary appeal for B2B buyers lies in their customizable designs, allowing businesses to create tailored solutions that meet specific needs. However, the initial investment can be higher than that of standard containers, necessitating careful budgeting and planning.
What Makes Luxury Container Homes a Unique Investment?
Luxury container homes are designed with high-end finishes and amenities, often featuring multiple stories and sophisticated layouts. These units are ideal for businesses looking to establish a premium presence in the housing or hospitality market, such as boutique hotels. The aesthetic appeal and use of premium materials can attract discerning clients. However, the significant investment required for luxury container homes may pose a barrier for some businesses, making thorough market research and financial planning essential.
Why Choose Eco-Friendly Containers for Sustainable Projects?
Eco-friendly containers are constructed using sustainable materials and practices, making them an excellent choice for businesses focused on green building initiatives. These units are often utilized in eco-villages or sustainable community projects. B2B buyers can benefit from their lower environmental impact, aligning with corporate social responsibility goals. However, the availability of eco-friendly options may be limited, and sourcing these units can require additional effort and time.
How Can Container Office Solutions Enhance Business Operations?
Container office solutions are designed specifically for professional workspaces, often featuring mobile configurations that allow for quick setup at construction sites or remote locations. These units provide a practical solution for businesses needing flexible office space without the commitment of traditional leases. The primary advantage for B2B buyers is the mobility and rapid deployment of these offices. However, potential space constraints can limit their effectiveness for larger teams, necessitating careful planning regarding team size and functionality.
Related Video: How to Build Prefabricated Detachable Container House / Porta Cabin? (2021)
Key Industrial Applications of container house supplier
Industry/Sector | Specific Application of Container House Supplier | Value/Benefit for the Business | Key Sourcing Considerations for this Application |
---|---|---|---|
Construction | Temporary Site Offices | Cost-effective and portable workspace solutions | Ensure compliance with local building regulations |
Mining | Worker Accommodation Camps | Enhanced living conditions for remote workers | Assess durability and insulation for extreme climates |
Disaster Relief | Emergency Shelters | Rapid deployment and scalable housing solutions | Evaluate logistics for transportation and setup |
Agriculture | Mobile Field Offices | Improved communication and operational efficiency | Consider modular design for flexibility |
Education | Portable Classrooms | Accessible learning environments in remote areas | Check for local educational standards and safety |
How are Container Houses Used in Construction Projects?
In the construction industry, container houses serve as temporary site offices, providing a cost-effective and portable workspace for project managers and teams. These units can be quickly deployed to various locations, facilitating project coordination and communication. For international buyers, it’s essential to ensure that these containers comply with local building regulations and safety standards, particularly in regions like Africa and South America, where regulatory frameworks may vary significantly.
What Role Do Container Houses Play in Mining Operations?
In mining, container houses are commonly utilized as worker accommodation camps, offering enhanced living conditions for employees in remote areas. These structures can be outfitted with essential amenities, such as kitchens and bathrooms, ensuring a comfortable living environment. Buyers from the Middle East and Europe should assess the durability and insulation of these units, as they need to withstand harsh climates and provide adequate protection against environmental factors.
How Can Container Houses Support Disaster Relief Efforts?
During natural disasters, container houses are invaluable for providing emergency shelters. Their rapid deployment capabilities allow for immediate housing solutions in affected areas, offering a scalable approach to disaster recovery. For B2B buyers involved in humanitarian efforts, evaluating the logistics of transportation and setup is crucial to ensure that these shelters can be efficiently deployed and assembled in crisis situations.
In What Ways Do Container Houses Benefit Agricultural Operations?
Agricultural businesses utilize container houses as mobile field offices, enhancing communication and operational efficiency in remote farming locations. These units can be customized to serve various purposes, from office space to storage for equipment. Buyers should consider modular designs that allow for easy relocation and expansion, particularly in regions like South America, where agricultural operations may require flexibility due to changing conditions.
How Are Container Houses Transforming Education in Remote Areas?
Container houses can also be repurposed as portable classrooms, providing accessible learning environments in rural or underserved regions. These structures can be equipped with educational resources and technology, bridging the gap in educational access. When sourcing these units, it is vital for buyers to check for compliance with local educational standards and safety regulations, ensuring a conducive learning atmosphere for students.
Related Video: Three-bedroom Prefab Container House Design in the Philippines
3 Common User Pain Points for ‘container house supplier’ & Their Solutions
Scenario 1: Navigating Regulatory Compliance in Container House Projects
The Problem:
B2B buyers often encounter significant challenges when it comes to regulatory compliance for container housing projects. Different regions, especially in Africa and the Middle East, have varying building codes and safety regulations that can be confusing and complex. Buyers may find themselves stuck in a web of bureaucracy, unsure of how to ensure that their container homes meet local standards. This not only delays project timelines but can also lead to increased costs due to potential fines or the need for modifications.
The Solution:
To effectively navigate regulatory compliance, buyers should first conduct thorough research on local regulations before initiating a project. Engaging with a container house supplier that has experience in the specific region can provide invaluable insights. Suppliers often have established relationships with local authorities and can assist in obtaining necessary permits. Additionally, buyers should consider hiring a local consultant who specializes in construction regulations to help guide them through the process. This proactive approach ensures that all legal requirements are met from the outset, thereby avoiding costly delays and modifications down the line.
Scenario 2: Ensuring Quality and Durability in Container Houses
The Problem:
Quality assurance is a significant concern for B2B buyers investing in container homes. Many suppliers may offer attractive pricing but compromise on materials and construction standards. This can lead to issues such as poor insulation, rusting, or structural weaknesses that not only impact the longevity of the buildings but also the safety of the occupants. Buyers in regions with harsh climates, like parts of South America and Africa, are particularly vulnerable to these issues.
The Solution:
To ensure quality and durability, buyers should prioritize sourcing from reputable suppliers with a proven track record. Request detailed specifications about the materials used, including insulation types and steel grades. Additionally, consider visiting manufacturing facilities if feasible, or request third-party inspections for added assurance. Look for suppliers who offer warranties or guarantees on their products, as this can be a strong indicator of their commitment to quality. Establishing a long-term partnership with a reliable supplier can also facilitate ongoing support and maintenance, further ensuring the durability of the container houses.
Scenario 3: Managing Logistics and Transportation Costs Effectively
The Problem:
Logistics and transportation present another significant pain point for B2B buyers of container houses, especially those located in remote areas or regions with limited infrastructure. High shipping costs, delays, and damage during transit can severely impact budgets and timelines. Buyers may struggle to find efficient shipping solutions that balance cost and reliability, leading to frustration and potential project delays.
The Solution:
To manage logistics and transportation effectively, buyers should collaborate closely with their chosen container house supplier. Suppliers often have established logistics networks and can provide insights into the most cost-effective shipping methods. Consider consolidating shipments to reduce costs, and explore local transportation options that may offer greater efficiency. It’s also beneficial to create a detailed timeline that includes all logistical steps, from manufacturing to delivery, ensuring that all parties are aligned. Lastly, investing in insurance for shipments can mitigate financial risks associated with potential damage or delays, providing peace of mind throughout the process.
Strategic Material Selection Guide for container house supplier
When selecting materials for container houses, international B2B buyers must consider various factors that influence the performance, durability, and compliance of the structures. Here, we analyze four common materials used in the construction of container houses, focusing on their properties, advantages, disadvantages, and specific considerations for buyers from Africa, South America, the Middle East, and Europe.
What Are the Key Properties of Steel in Container House Construction?
Steel is the most prevalent material used in container houses due to its strength and durability. It boasts high tensile strength, excellent corrosion resistance when treated, and can withstand significant temperature variations. Steel containers are designed to endure harsh environmental conditions, making them suitable for diverse climates.
Pros & Cons:
The primary advantage of steel is its durability and structural integrity, which ensures longevity. However, the cost of high-quality steel can be significant, and the manufacturing process may involve complex welding and fabrication techniques. Additionally, without proper insulation, steel can conduct heat, leading to temperature control challenges.
Impact on Application:
Steel is compatible with various insulation materials, making it a versatile choice for different climates. However, buyers must ensure that the steel meets local compliance standards, such as ASTM in the U.S. or EN in Europe.
How Does Wood Compare as a Material for Container Houses?
Wood is another popular choice for container house interiors and exteriors. It provides natural insulation and aesthetic appeal, contributing to a warm, inviting atmosphere. Wood is lightweight and relatively easy to work with, allowing for flexible design options.
Pros & Cons:
The key advantage of wood is its thermal insulation properties, which can significantly reduce energy costs. However, wood is susceptible to pests, rot, and fire, necessitating regular maintenance and treatment. Additionally, sourcing sustainably harvested wood can pose challenges in regions with strict environmental regulations.
Impact on Application:
Wood’s compatibility with insulation materials makes it suitable for various climates, but buyers must consider local building codes and standards regarding fire safety and sustainability.
What Are the Benefits and Drawbacks of Using Concrete?
Concrete is increasingly being used in container house construction due to its strength and thermal mass properties. It provides excellent fire resistance and can be molded into various shapes, allowing for creative architectural designs.
Pros & Cons:
The main advantage of concrete is its durability and low maintenance requirements. However, it can be heavy and may require additional structural support, increasing overall costs. The curing process can also be time-consuming, delaying project timelines.
Impact on Application:
Concrete is suitable for a variety of climates due to its thermal mass, but international buyers must be aware of local regulations regarding concrete composition and strength standards, such as DIN in Europe.
Why Is Insulation Material Critical for Container Houses?
Insulation materials are essential for maintaining temperature control and energy efficiency in container houses. Common insulation options include spray foam, fiberglass, and rigid foam boards, each with unique properties.
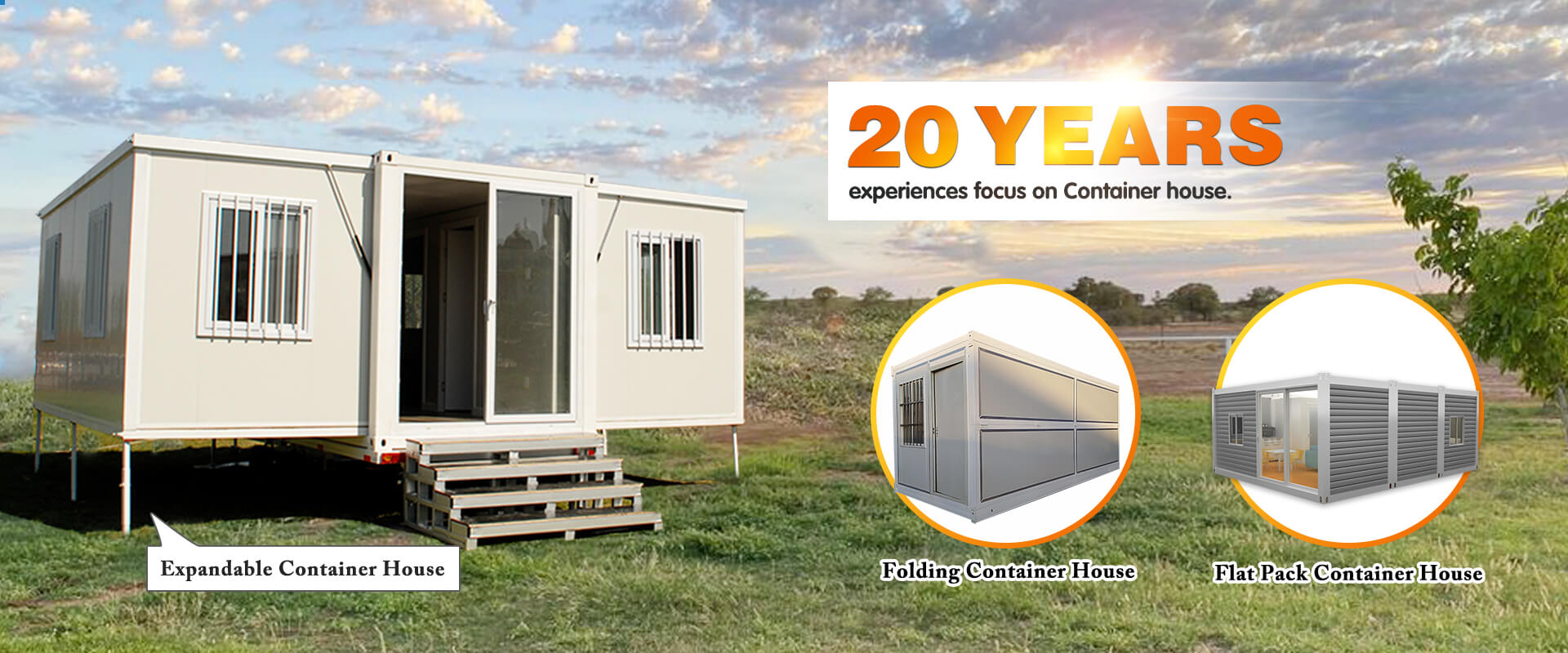
A stock image related to container house supplier.
Pros & Cons:
The key advantage of insulation materials is their ability to enhance energy efficiency, reducing heating and cooling costs. However, some insulation types can be costly or may require specialized installation techniques. Additionally, certain insulation materials may not comply with fire safety regulations in specific regions.
Impact on Application:
Insulation must be chosen based on the local climate and building codes. For instance, buyers in colder climates may prioritize materials with higher R-values, while those in warmer regions may focus on reflective insulation properties.
Summary Table of Material Selection for Container Houses
Material | Typical Use Case for container house supplier | Key Advantage | Key Disadvantage/Limitation | Relative Cost (Low/Med/High) |
---|---|---|---|---|
Steel | Structural framework and exterior cladding | High durability and strength | Expensive and requires insulation | High |
Wood | Interior finishes and structural elements | Natural insulation and aesthetic | Susceptible to pests and fire | Medium |
Concrete | Foundations and walls | Excellent fire resistance | Heavy and requires curing time | High |
Insulation | Thermal control and energy efficiency | Reduces energy costs | Can be costly and may require special installation | Medium |
In conclusion, selecting the right materials for container houses involves a careful assessment of properties, advantages, disadvantages, and compliance with local regulations. By understanding these factors, international B2B buyers can make informed decisions that align with their project goals and regional requirements.
In-depth Look: Manufacturing Processes and Quality Assurance for container house supplier
What Are the Main Stages of Manufacturing Container Houses?
Container houses are increasingly popular for various applications, including residential, commercial, and temporary structures. The manufacturing process involves several critical stages, each contributing to the overall quality and functionality of the final product.
1. Material Preparation
The first step in the manufacturing process is material preparation. This involves sourcing high-quality shipping containers, typically made of corten steel, which provides durability and resistance to weather elements. Suppliers should ensure that the containers are free from rust, damage, and contaminants. In addition, any necessary modifications, such as cutting or welding, should be planned at this stage to meet the specific design requirements of the container house.
2. Forming the Structure
Once the materials are prepared, the next stage is forming the structure. This involves modifying the containers to create openings for windows and doors and reinforcing the structure as necessary. Techniques such as plasma cutting, oxy-fuel cutting, and welding are commonly used. It’s crucial for suppliers to utilize skilled labor and appropriate machinery to ensure precision and structural integrity.
3. Assembly of Components
The assembly stage involves bringing together various components, including insulation, electrical wiring, plumbing, and interior finishes. This stage is critical for ensuring that the container house is not only functional but also comfortable and aesthetically pleasing. Suppliers often use modular construction techniques, allowing for quicker assembly and reduced labor costs.
4. Finishing Touches
The final stage is finishing, which includes painting, sealing, and installing fixtures. Quality finishes not only enhance aesthetics but also protect the container from environmental damage. Suppliers should be aware of the best practices for applying protective coatings, which can significantly extend the lifespan of the container house.
How Is Quality Assurance Implemented in Container House Manufacturing?
Quality assurance (QA) is integral to the manufacturing process of container houses, ensuring that each unit meets both customer expectations and regulatory standards.
What International Standards Should B2B Buyers Look For?
International standards play a crucial role in the quality assurance process. The ISO 9001 certification is a key indicator of a supplier’s commitment to quality management systems. This certification ensures that the manufacturing processes are consistently monitored and improved.
Additionally, industry-specific certifications such as CE marking in Europe and API standards for oil and gas applications are essential. These certifications demonstrate compliance with safety, health, and environmental protection standards, which are crucial for B2B buyers, especially in regions with stringent regulatory frameworks.
What Are the Key Quality Control Checkpoints?
Quality control (QC) is typically segmented into several checkpoints throughout the manufacturing process:
1. Incoming Quality Control (IQC)
The IQC phase involves inspecting raw materials upon arrival at the manufacturing facility. This step ensures that all materials meet specified standards and are suitable for use in container house production. B2B buyers should inquire about the supplier’s IQC processes to ensure they are thorough and documented.
2. In-Process Quality Control (IPQC)
During the manufacturing process, IPQC checkpoints are established to monitor ongoing operations. This may involve periodic inspections of welding quality, dimensional accuracy, and assembly integrity. Suppliers should maintain detailed records of these inspections to provide transparency to B2B buyers.
3. Final Quality Control (FQC)
The FQC stage occurs after assembly and finishing. This involves comprehensive testing of the container house to ensure it meets all design specifications and safety standards. Common testing methods include pressure testing for plumbing systems, electrical testing for wiring, and thermal imaging to assess insulation effectiveness.
How Can B2B Buyers Verify Supplier Quality Control?
For international B2B buyers, particularly those from Africa, South America, the Middle East, and Europe, verifying a supplier’s quality control processes is vital. Here are several actionable insights:
Conducting Audits
Buyers should consider conducting on-site audits of potential suppliers. This allows them to assess the manufacturing environment, observe QA processes in action, and verify compliance with international standards. Audits can be carried out by internal teams or third-party organizations specializing in supplier assessments.
Reviewing Quality Control Reports
Suppliers should provide detailed QC reports that outline their processes, inspection results, and any corrective actions taken. Buyers should request these reports as part of their due diligence to ensure that the supplier adheres to their stated quality standards.
Engaging Third-Party Inspection Services
Utilizing third-party inspection services can offer an unbiased evaluation of a supplier’s quality assurance practices. These services often conduct inspections at various stages of the manufacturing process, providing buyers with peace of mind regarding the integrity of their container houses.
What Are the Quality Control Nuances for International B2B Buyers?
Navigating quality control in international trade can be complex. B2B buyers must be aware of the specific regulatory requirements in their own countries as well as those of the supplier’s country.
Understanding Regional Standards
For buyers in Africa and South America, understanding local building codes and safety regulations is crucial. In many cases, compliance with local standards is as important as international certifications. Buyers should ensure that their suppliers are knowledgeable about these regional standards and can provide evidence of compliance.
Building Relationships with Suppliers
Establishing strong relationships with suppliers can facilitate better communication regarding quality control. Regular updates on manufacturing processes and quality assurance can help build trust and ensure that buyers receive the highest quality products.
In conclusion, understanding the manufacturing processes and quality assurance practices of container house suppliers is essential for international B2B buyers. By focusing on these aspects, buyers can make informed decisions that align with their project requirements and regulatory standards, ultimately leading to successful procurement outcomes.
Practical Sourcing Guide: A Step-by-Step Checklist for ‘container house supplier’
The process of sourcing a reliable container house supplier requires careful consideration and systematic evaluation. This checklist aims to equip international B2B buyers, particularly those from Africa, South America, the Middle East, and Europe, with a structured approach to ensure they select the best supplier for their needs.
Step 1: Define Your Technical Specifications
Before reaching out to potential suppliers, it’s essential to clearly outline your requirements. This includes the size, type, and intended use of the container houses. Defining specifications helps in filtering suppliers who can meet your specific needs, ensuring a more efficient sourcing process.
– Consider the insulation, design, and layout that suit your climate and usage.
– Determine any additional features, such as plumbing or electrical systems, that may be required.
Step 2: Conduct Market Research
Understanding the market landscape is crucial in identifying the right suppliers. Research various container house suppliers across different regions to gauge their offerings, pricing, and reputation.
– Look for suppliers who have experience in your geographic area, as they may better understand local regulations and market conditions.
– Utilize online platforms, industry reports, and trade shows to gather insights about potential suppliers.
Step 3: Evaluate Potential Suppliers
Before committing, it’s vital to vet suppliers thoroughly. Request company profiles, case studies, and references from buyers in a similar industry or region. This step ensures that you are engaging with reputable suppliers who have a proven track record.
– Ask for examples of past projects that are similar to your requirements.
– Verify the legitimacy of references provided by the supplier.
Step 4: Verify Supplier Certifications
Certifications can indicate a supplier’s commitment to quality and compliance with industry standards. Ensure that the suppliers you consider have relevant certifications, such as ISO or safety compliance certifications.
– Check if they adhere to international standards, which is particularly important for buyers in diverse regions.
– Review their manufacturing processes and quality control measures.
Step 5: Request Samples or Prototypes
Before making a bulk purchase, ask for samples or prototypes of the container houses. This allows you to assess the quality of materials and craftsmanship firsthand.
– Evaluate the durability, insulation, and overall finish of the containers.
– Consider conducting site visits to see completed projects in use, if possible.
Step 6: Understand Pricing Structures
Pricing can vary widely among suppliers, influenced by factors like materials, labor, and transportation costs. Request detailed quotations from multiple suppliers to make informed comparisons.
– Look for transparency in pricing, including any additional fees for customization or delivery.
– Consider the total cost of ownership, including maintenance and energy efficiency over time.
Step 7: Negotiate Terms and Conditions
Once you’ve identified a suitable supplier, it’s important to negotiate terms that protect your interests. Discuss payment terms, delivery schedules, warranties, and after-sales support to ensure clarity.
– Be clear about your expectations and any potential penalties for missed deadlines.
– Document all agreements to avoid misunderstandings later in the procurement process.
By following this checklist, international B2B buyers can streamline their sourcing process for container house suppliers, making informed decisions that align with their operational needs and budget constraints.
Comprehensive Cost and Pricing Analysis for container house supplier Sourcing
What Are the Key Cost Components in Container House Supplier Sourcing?
When sourcing container houses, understanding the cost structure is crucial for international B2B buyers. The primary cost components include:
-
Materials: The cost of shipping containers, insulation, windows, doors, and interior finishes can vary significantly based on quality and source. Opting for sustainable or recycled materials can influence pricing but may also offer long-term cost benefits.
-
Labor: Labor costs can fluctuate depending on the region and the complexity of the design. Skilled labor is often required for custom builds, which may increase overall costs.
-
Manufacturing Overhead: This encompasses utilities, equipment maintenance, and facility costs. Suppliers with higher overhead may charge more, but they might also offer better quality assurance and service.
-
Tooling: Custom tooling for specific designs can be a significant upfront investment. Buyers should inquire about these costs, especially for large orders or unique specifications.
-
Quality Control (QC): Rigorous QC processes ensure that products meet industry standards. Suppliers that invest in quality assurance may charge a premium, but this can prevent costly issues later.
-
Logistics: Shipping costs, which include freight, insurance, and handling fees, can vary based on distance and shipping methods. International buyers should consider these costs as they can significantly impact the total cost.
-
Margin: Supplier profit margins can vary widely. Understanding a supplier’s pricing strategy can help buyers negotiate better terms.
How Do Price Influencers Affect Container House Sourcing?
Several factors can influence the pricing of container houses.
-
Volume and Minimum Order Quantity (MOQ): Larger orders often attract bulk discounts. Establishing a solid relationship with suppliers can also lead to better pricing for future orders.
-
Specifications and Customization: Custom designs or specific materials may increase costs. Clearly defining requirements upfront can help avoid unexpected expenses.
-
Material Quality and Certifications: Higher-quality materials and recognized certifications (e.g., ISO, CE) can elevate costs but may also enhance durability and compliance with local regulations.
-
Supplier Factors: The supplier’s reputation, experience, and location can affect pricing. Established suppliers with a proven track record may charge more, but they often deliver better reliability and service.
-
Incoterms: Understanding Incoterms (International Commercial Terms) is essential for international buyers. These terms define the responsibilities of buyers and sellers in shipping and can significantly impact pricing and logistics.
What Tips Can Help International B2B Buyers Optimize Costs?
For B2B buyers in Africa, South America, the Middle East, and Europe, optimizing costs while sourcing container houses involves strategic planning and negotiation.
-
Negotiate Terms: Always negotiate pricing and payment terms. Many suppliers are open to discussions, especially for long-term partnerships.
-
Consider Total Cost of Ownership (TCO): Evaluate not only the purchase price but also long-term operational costs, maintenance, and potential resale value. This approach can reveal better overall value.
-
Understand Pricing Nuances: International markets may have different pricing structures. Research local market conditions and currency fluctuations to better assess supplier quotes.
-
Explore Local Suppliers: Sourcing from local suppliers can reduce shipping costs and lead times, making it easier to manage logistics.
-
Request Detailed Quotes: Ask for itemized quotes that break down each cost component. This transparency can help in comparing different suppliers and understanding where potential savings lie.
What Should Buyers Keep in Mind Regarding Indicative Prices?
While this analysis provides a framework for understanding the costs associated with container house sourcing, it’s important to note that prices can vary widely based on market conditions, supplier relationships, and specific project requirements. Always request updated quotes and consider obtaining multiple offers to ensure competitive pricing.
Alternatives Analysis: Comparing container house supplier With Other Solutions
Introduction: Why Consider Alternatives to Container House Suppliers?
When evaluating the best housing solutions for international projects, B2B buyers must consider various alternatives to container houses. While container homes offer unique advantages, understanding other viable options can help buyers make informed decisions tailored to their specific needs, budgets, and operational contexts. This section compares container house suppliers with modular building systems and traditional construction methods, highlighting key performance metrics, costs, and practical applications.
Comparison Table: Container House Suppliers vs. Alternatives
Comparison Aspect | Container House Supplier | Modular Building Systems | Traditional Construction |
---|---|---|---|
Performance | Durable, weather-resistant | Flexible designs, quick assembly | High customization, longevity |
Cost | Moderate initial investment | Generally lower costs, faster ROI | Higher initial costs, variable ROI |
Ease of Implementation | Requires transportation and site preparation | Quick setup with pre-fabricated units | Longer timelines, often complex |
Maintenance | Low maintenance, easy repairs | Similar to container houses | Higher maintenance, labor-intensive |
Best Use Case | Temporary and permanent housing | Rapid deployment, remote locations | Long-term residential and commercial projects |
What Are the Advantages and Disadvantages of Modular Building Systems?
Modular building systems are prefabricated structures that can be assembled on-site. They often provide a more flexible design compared to container houses, allowing for various configurations and uses. One of the main advantages is the speed of construction; modular systems can be erected in a fraction of the time compared to traditional methods. However, they may lack the unique aesthetic appeal of container homes and can be limited by local zoning laws. Additionally, while the initial costs are often lower, the need for specialized transport and assembly can add complexity.
How Does Traditional Construction Compare to Container Houses?
Traditional construction is the time-honored method of building with bricks, wood, and concrete. It allows for extensive customization and is generally perceived as more aesthetically pleasing, particularly for permanent residential solutions. However, traditional methods are often slower and more expensive due to labor costs and longer project timelines. Maintenance can also be a significant concern, as traditional structures may require more frequent repairs and upgrades. For projects where longevity and customization are paramount, traditional construction may still be the preferred option.
Conclusion: How to Choose the Right Housing Solution for Your Needs?
In deciding between container house suppliers and alternative solutions like modular building systems or traditional construction, international B2B buyers must weigh factors such as performance, cost, and ease of implementation. Understanding the specific requirements of a project—whether it’s a temporary facility in a remote area or a permanent residential development—will guide this decision. By carefully analyzing the benefits and limitations of each option, buyers can select the most effective housing solution that aligns with their operational goals and budgetary constraints.
Essential Technical Properties and Trade Terminology for container house supplier
What Are the Essential Technical Properties of Container Houses?
When considering container houses for international projects, understanding the technical properties is crucial for ensuring quality and durability. Here are key specifications that B2B buyers should prioritize:
1. Material Grade and Thickness
Container houses are typically constructed from high-grade steel, often designated as Corten steel or marine-grade steel. The thickness of the steel, usually ranging from 1.6 mm to 3 mm, affects the overall strength and resistance to environmental factors. For B2B buyers, selecting the right material grade and thickness can lead to improved longevity and reduced maintenance costs, which are critical for projects in diverse climates.
2. Insulation Properties
Effective insulation is essential for maintaining comfortable living conditions within a container house. Buyers should inquire about the R-value of the insulation materials used, which indicates their thermal resistance. High R-values translate to better energy efficiency, crucial for reducing heating and cooling costs in regions with extreme temperatures, such as parts of Africa and the Middle East.
3. Structural Tolerance
Structural tolerance refers to the allowable deviation in dimensions and alignment during construction. Understanding the tolerances that suppliers adhere to can help buyers ensure that their container houses are built to specifications, minimizing issues during assembly and installation. This is particularly important for large-scale projects where precision is paramount.
4. Load-Bearing Capacity
The load-bearing capacity of a container house indicates how much weight the structure can support without compromising safety. This specification is vital for projects that may require additional amenities or multi-story designs. Buyers should request detailed load calculations to ensure that the chosen container house meets the needs of their specific application.
5. Weather Resistance Ratings
Given the varying climates across Africa, South America, the Middle East, and Europe, understanding the weather resistance ratings of a container house is essential. This includes ratings for wind, water, and fire resistance. Suppliers should provide certification for these properties, as they directly influence the safety and durability of the structure.
What Are the Common Trade Terms in the Container House Industry?
Familiarity with industry terminology can significantly enhance communication and negotiation processes for international B2B buyers. Here are some essential terms:
1. OEM (Original Equipment Manufacturer)
In the context of container houses, an OEM refers to a company that produces the containers or components that are then branded and sold by another company. Understanding OEM relationships helps buyers identify the quality and origin of the products they are sourcing.
2. MOQ (Minimum Order Quantity)
MOQ is the smallest number of units a supplier is willing to sell. For buyers, knowing the MOQ is vital for budgeting and inventory management. This term is especially relevant for large-scale projects, where bulk purchases may lead to cost savings.
3. RFQ (Request for Quotation)
An RFQ is a formal document sent to suppliers requesting pricing and terms for specific products or services. For B2B buyers, issuing an RFQ can streamline the procurement process, enabling them to compare multiple suppliers and make informed decisions based on price and specifications.
4. Incoterms (International Commercial Terms)
Incoterms are a set of predefined international trade terms published by the International Chamber of Commerce. They define the responsibilities of buyers and sellers regarding shipping, insurance, and tariffs. Familiarity with Incoterms is crucial for B2B buyers to understand their obligations and risks in international transactions.
5. Lead Time
Lead time refers to the amount of time from placing an order to receiving the goods. For container house projects, lead time can vary significantly based on design complexity and supplier location. Buyers should factor in lead times when planning their projects to avoid delays.
By understanding these technical properties and trade terms, B2B buyers can make more informed decisions, ensuring successful procurement and implementation of container houses in their respective markets.
Navigating Market Dynamics and Sourcing Trends in the container house supplier Sector
What Are the Key Market Dynamics and Trends in the Container House Supplier Sector?
The container house supplier sector has seen significant growth fueled by a combination of global economic shifts and technological advancements. As urbanization continues to rise, particularly in regions like Africa and South America, the demand for affordable, flexible housing solutions has surged. Additionally, the COVID-19 pandemic has heightened awareness around the need for rapid deployment of housing solutions, making container houses a viable option for both residential and commercial purposes.
Emerging B2B technologies, such as Building Information Modeling (BIM) and modular construction techniques, are revolutionizing the way container houses are designed and produced. These technologies enable suppliers to offer customizable solutions that cater to specific buyer needs, enhancing efficiency and reducing lead times. Furthermore, the rise of e-commerce platforms allows international buyers to source container houses more easily, providing access to a wider range of suppliers from various regions, including Europe and the Middle East.
As buyers navigate this evolving landscape, understanding local market dynamics is essential. Factors such as regulatory frameworks, import/export tariffs, and local labor costs can significantly impact sourcing decisions. For instance, in regions like South Africa, regulations regarding building codes and sustainability standards must be adhered to, which can influence supplier selection. Additionally, the competitive landscape is becoming more fragmented, with both established suppliers and new entrants vying for market share, making it crucial for B2B buyers to conduct thorough due diligence.
How Is Sustainability Influencing Sourcing Decisions in the Container House Sector?
Sustainability has emerged as a pivotal consideration in the container house supplier sector, driven by increasing awareness of environmental impact and a growing demand for ethical sourcing practices. Container houses, often made from repurposed shipping containers, inherently promote recycling and resource efficiency. However, the sourcing of materials used in the construction process also plays a crucial role in determining the overall environmental footprint.
International B2B buyers are increasingly prioritizing suppliers who demonstrate commitment to sustainable practices. This includes obtaining certifications such as LEED (Leadership in Energy and Environmental Design) or BREEAM (Building Research Establishment Environmental Assessment Method), which indicate adherence to rigorous environmental standards. Furthermore, sourcing materials that are certified as eco-friendly or sustainably harvested can enhance a buyer’s reputation and meet the expectations of environmentally conscious consumers.
In addition to certifications, transparency in the supply chain is becoming increasingly important. Buyers are looking for suppliers who can provide detailed information about their sourcing processes, including the origin of materials and labor practices. This shift towards ethical sourcing not only mitigates risks associated with supply chain disruptions but also aligns with the values of consumers who prefer companies that prioritize sustainability.
What Is the Brief Evolution of the Container House Supplier Sector?
The container house supplier sector has evolved significantly over the past few decades. Initially, the concept of using shipping containers as building materials was seen as a niche solution, primarily for temporary structures or low-cost housing. However, advancements in design and construction methods have transformed container houses into a viable option for permanent housing, commercial buildings, and even luxury accommodations.
The evolution has been marked by increased acceptance of container homes in mainstream architecture, spurred by successful projects and innovative designs. As sustainability became a focal point in construction, the inherent benefits of container houses—such as durability, cost-effectiveness, and reduced environmental impact—have garnered attention from both consumers and investors. Today, the sector is characterized by a diverse range of suppliers offering customizable solutions, catering to an expanding market that spans continents and addresses varied housing needs.
Frequently Asked Questions (FAQs) for B2B Buyers of container house supplier
-
How do I assess the reliability of a container house supplier?
To evaluate a container house supplier’s reliability, start by researching their reputation in the industry. Look for customer testimonials, case studies, and reviews on independent platforms. Verify their business registration and certifications, which indicate compliance with local and international standards. Additionally, consider their experience in the market—longer-standing suppliers often have more robust operational practices. Engaging in direct communication can also provide insights into their customer service and responsiveness. Finally, request references from previous clients to gain firsthand insights into their reliability and delivery capabilities. -
What are the key features to look for in a container house supplier?
When selecting a container house supplier, prioritize several key features: product quality, customization options, and after-sales support. Investigate the materials used in their containers, ensuring they meet your durability and insulation requirements. Customization capabilities are crucial, especially for specific regional needs; confirm they can tailor designs and layouts. Additionally, assess their logistical capabilities to ensure timely delivery. Finally, strong after-sales support, including warranties and maintenance services, is essential for a long-term partnership, particularly in complex projects. -
What is the typical minimum order quantity (MOQ) for container houses?
Minimum order quantities for container houses can vary significantly depending on the supplier and your specific needs. Generally, MOQs can range from a single unit for smaller suppliers to several units for larger manufacturers. It’s essential to clarify the MOQ during initial discussions, as some suppliers may offer flexibility for first-time buyers or bulk orders. Understanding the MOQ is crucial for budgeting and planning your project timeline, especially for international orders where logistics may complicate smaller shipments. -
What payment terms should I expect from a container house supplier?
Payment terms with container house suppliers typically vary by company and region. Common arrangements include a deposit (often 30-50%) before production, with the balance due upon completion or before shipment. Some suppliers may offer financing options or extended payment terms for larger orders. It’s vital to clarify these terms upfront and ensure they align with your cash flow and project timeline. Additionally, consider the payment methods accepted, such as bank transfers, letters of credit, or online payment platforms, to facilitate smooth transactions. -
How can I customize my container house to meet specific needs?
Customizing a container house to meet specific needs involves discussing your requirements with the supplier early in the process. Most suppliers offer various customization options, including layout changes, insulation types, windows, and doors. You may also want to discuss additional features like plumbing, electrical installations, and eco-friendly materials. Providing detailed specifications or design ideas can help suppliers understand your vision better. Always request a prototype or 3D visualization if available, to ensure the final product aligns with your expectations. -
What quality assurance measures should I expect from a container house supplier?
Quality assurance measures from a container house supplier should include rigorous testing and inspection processes throughout the production cycle. Suppliers should adhere to international standards for construction and safety. Look for certifications such as ISO or local building codes compliance. It’s also beneficial to inquire about their quality control protocols, including material sourcing, assembly inspections, and post-production evaluations. A reliable supplier should be transparent about their QA processes and willing to provide documentation to verify compliance. -
What logistics considerations should I keep in mind when importing container houses?
When importing container houses, logistics considerations are crucial for ensuring timely delivery and cost efficiency. Start by understanding the shipping terms (Incoterms) that apply to your order, which dictate the responsibilities of both buyer and seller. Assess the shipping methods available, such as sea freight, which is often more economical for large shipments. Additionally, factor in customs regulations and duties specific to your country, as these can affect total costs. Collaborating with a freight forwarder can streamline the logistics process and help navigate any challenges. -
How do I handle potential disputes with a container house supplier?
Handling disputes with a container house supplier requires clear communication and a well-defined contract. Ensure that your agreement includes detailed terms regarding product specifications, delivery timelines, and quality standards. In the event of a dispute, address the issue promptly and directly with the supplier, providing documentation to support your claims. If necessary, consider mediation or arbitration as a resolution method, as these are often less costly than litigation. Building a positive relationship with your supplier can also help mitigate conflicts before they escalate.
Important Disclaimer & Terms of Use
⚠️ Important Disclaimer
The information provided in this guide, including content regarding manufacturers, technical specifications, and market analysis, is for informational and educational purposes only. It does not constitute professional procurement advice, financial advice, or legal advice.
While we have made every effort to ensure the accuracy and timeliness of the information, we are not responsible for any errors, omissions, or outdated information. Market conditions, company details, and technical standards are subject to change.
B2B buyers must conduct their own independent and thorough due diligence before making any purchasing decisions. This includes contacting suppliers directly, verifying certifications, requesting samples, and seeking professional consultation. The risk of relying on any information in this guide is borne solely by the reader.
Strategic Sourcing Conclusion and Outlook for container house supplier
In the evolving landscape of global construction, strategic sourcing emerges as a crucial driver for businesses aiming to procure container houses efficiently. By prioritizing long-term partnerships with reliable suppliers, buyers can ensure not only cost-effectiveness but also quality assurance and timely delivery. This approach mitigates risks associated with fluctuating market conditions, particularly relevant for buyers in regions like Africa, South America, the Middle East, and Europe, where infrastructure demands are rapidly increasing.
How Can International Buyers Benefit from Strategic Sourcing?
International B2B buyers can leverage strategic sourcing to access innovative designs and sustainable building practices that are integral to modern container house solutions. Engaging with suppliers who understand local regulations and cultural nuances can lead to smoother project implementations and enhanced customer satisfaction.
What’s Next for Container House Procurement?
As we look to the future, the demand for container houses is anticipated to grow, driven by urbanization and the need for affordable housing solutions. Buyers should actively seek partnerships with suppliers who are not only responsive but also forward-thinking in their approach to sustainability and technology integration.
Embrace the opportunity to refine your sourcing strategy today, and position your business at the forefront of this dynamic market. Start exploring your options with trusted container house suppliers to ensure your projects are both innovative and economically viable.