Discover Top Drive Shaft Manufacturers to Cut Costs (2025)
Introduction: Navigating the Global Market for drive shaft manufacturer
In today’s competitive landscape, sourcing high-quality drive shafts is a pivotal challenge for international B2B buyers. As industries increasingly demand reliable and efficient components, understanding the nuances of the drive shaft manufacturing market becomes essential. This comprehensive guide delves into the various types of drive shafts, their applications across diverse sectors, and best practices for vetting suppliers. By addressing critical considerations such as cost analysis and quality assurance, this resource equips buyers from Africa, South America, the Middle East, and Europe—including key markets like Germany and Italy—with the knowledge needed to make informed purchasing decisions.
The complexities of the global market can overwhelm even seasoned professionals, making it crucial to have a structured approach to sourcing. This guide not only highlights the specifications and standards to look for but also offers insights into the latest trends and innovations in drive shaft technology. By leveraging this information, buyers can enhance their procurement strategies, mitigate risks, and ensure they are partnering with reputable manufacturers. Ultimately, this guide serves as a vital tool for fostering successful collaborations and achieving operational excellence in an increasingly interconnected world.
Understanding drive shaft manufacturer Types and Variations
Type Name | Key Distinguishing Features | Primary B2B Applications | Brief Pros & Cons for Buyers |
---|---|---|---|
Solid Drive Shafts | Single-piece construction, high strength, and rigidity | Heavy machinery, trucks, and industrial equipment | Pros: Durable, less maintenance; Cons: Heavier, limited flexibility. |
Hollow Drive Shafts | Lightweight design, reduced inertia, and increased torque | Automotive, aerospace, and racing sectors | Pros: Lighter, better performance; Cons: May have lower strength than solid shafts. |
Double Cardan Shafts | Two universal joints, high angle flexibility | Off-road vehicles, heavy-duty trucks | Pros: Excellent for high-angle applications; Cons: More complex, higher cost. |
Telescopic Drive Shafts | Adjustable length, accommodates suspension movement | Construction equipment, agricultural machinery | Pros: Versatile, adaptable; Cons: Potential for wear over time. |
Composite Drive Shafts | Made from materials like carbon fiber, lightweight and corrosion-resistant | High-performance vehicles, aerospace | Pros: Lightweight, high strength-to-weight ratio; Cons: Higher initial cost, may require specialized maintenance. |
What Are Solid Drive Shafts and Their B2B Suitability?
Solid drive shafts are characterized by their single-piece construction, which provides exceptional strength and rigidity. They are commonly used in heavy machinery, trucks, and industrial equipment where durability is paramount. When considering a purchase, B2B buyers should evaluate the application environment, as these shafts are less prone to failure under extreme conditions. However, their weight can be a disadvantage in applications where reduced mass is advantageous.
How Do Hollow Drive Shafts Benefit B2B Applications?
Hollow drive shafts offer a lightweight alternative, allowing for reduced inertia and improved torque delivery. This design is particularly beneficial in automotive applications, aerospace, and racing sectors where performance is critical. Buyers should consider the balance between weight and strength when selecting hollow shafts, as they may not withstand the same loads as their solid counterparts. Their performance benefits often justify the investment in high-speed applications.
What Are the Advantages of Double Cardan Shafts for B2B Buyers?
Double Cardan shafts are designed with two universal joints, providing exceptional flexibility at high angles. This makes them ideal for off-road vehicles and heavy-duty trucks that encounter varying terrain. While they offer superior performance in challenging conditions, buyers should be aware of their complexity and potential for higher costs due to the additional components. Evaluating the specific operational needs will help determine if the benefits outweigh the drawbacks.
Why Choose Telescopic Drive Shafts for Your Business?
Telescopic drive shafts are adjustable in length, making them suitable for applications where suspension movement is a factor, such as in construction and agricultural machinery. Their versatility allows them to adapt to different operational requirements. However, buyers must consider the potential for wear and tear over time, which could lead to maintenance challenges. Ensuring compatibility with existing systems is crucial for effective utilization.
What Are the Key Features of Composite Drive Shafts?
Composite drive shafts, often made from materials like carbon fiber, are known for their lightweight and corrosion-resistant properties. They are primarily used in high-performance vehicles and aerospace applications, where a high strength-to-weight ratio is essential. While the initial cost may be higher than traditional materials, the long-term performance and durability can offer significant value. Buyers should assess their specific needs to determine if the advantages of composite shafts align with their operational goals.
Key Industrial Applications of drive shaft manufacturer
Industry/Sector | Specific Application of Drive Shaft Manufacturer | Value/Benefit for the Business | Key Sourcing Considerations for this Application |
---|---|---|---|
Automotive | Power Transmission in Vehicles | Enhanced vehicle performance and fuel efficiency | Compliance with international safety standards, durability under diverse conditions, and customization options for different vehicle types. |
Agriculture | Drive Systems in Agricultural Machinery | Increased productivity and reduced downtime | Availability of parts in remote areas, resistance to harsh environments, and compatibility with various machinery brands. |
Mining | Heavy-Duty Drive Shafts for Mining Equipment | Improved operational efficiency and equipment longevity | Ability to withstand extreme loads, corrosion resistance, and reliable after-sales support. |
Construction | Drive Shafts in Construction Equipment | Enhanced reliability and reduced maintenance costs | Sourcing from manufacturers with proven track records in heavy-duty applications and availability of spare parts. |
Industrial Manufacturing | Drive Shafts in Conveyor Systems | Streamlined operations and reduced operational costs | Precision engineering, adherence to quality standards, and options for custom lengths and materials. |
How Are Drive Shafts Used in the Automotive Industry?
In the automotive sector, drive shafts play a crucial role in power transmission, connecting the engine to the wheels. They ensure that torque is efficiently delivered, enhancing overall vehicle performance and fuel efficiency. For B2B buyers, particularly in regions like Germany and Italy, it is essential to source drive shafts that comply with stringent safety standards and are durable enough to handle varying road conditions. Customization options are also vital, as they allow manufacturers to adapt to specific vehicle models and designs.
What Role Do Drive Shafts Play in Agriculture?
Drive shafts are integral to agricultural machinery, facilitating power transfer from the engine to various implements like plows and harvesters. This application significantly boosts productivity by enabling faster and more efficient operations. Buyers in Africa and South America must consider sourcing drive shafts that are robust and capable of enduring harsh environmental conditions, as well as ensuring parts availability for maintenance in rural areas where access may be limited.
How Are Drive Shafts Utilized in the Mining Industry?
In the mining industry, drive shafts are essential for heavy-duty equipment such as excavators and haul trucks. They are designed to withstand extreme loads and harsh operating conditions, contributing to improved operational efficiency and equipment longevity. B2B buyers should prioritize sourcing from manufacturers who offer drive shafts with high corrosion resistance and reliable after-sales support, as these features are critical for minimizing downtime and ensuring safety in challenging environments.
Why Are Drive Shafts Important for Construction Equipment?
Construction equipment relies heavily on drive shafts for effective operation. They provide the necessary power to machinery like bulldozers and cranes, enhancing reliability and reducing maintenance costs. When sourcing drive shafts, buyers should look for manufacturers with a strong reputation in heavy-duty applications and ensure that spare parts are readily available to avoid project delays.
How Do Drive Shafts Enhance Industrial Manufacturing Processes?
In industrial manufacturing, drive shafts are commonly used in conveyor systems, facilitating the movement of materials and products throughout the production line. This application streamlines operations and can lead to significant cost reductions. Buyers should focus on precision-engineered drive shafts that adhere to high-quality standards, as well as options for custom lengths and materials to fit specific machinery configurations.
Related Video: Drive Shaft Angles Explained
3 Common User Pain Points for ‘drive shaft manufacturer’ & Their Solutions
Scenario 1: Challenges in Customization for Specific Applications
The Problem: Many B2B buyers face difficulties when sourcing drive shafts that meet specific application requirements, such as unique length, diameter, or material specifications. This issue can lead to performance inefficiencies, increased downtime, and even equipment failure if the drive shafts do not align with the operational needs of machinery or vehicles. Furthermore, the lack of effective communication between the buyer and the manufacturer can exacerbate misunderstandings, leading to costly errors and delays in production.
The Solution: To overcome customization challenges, B2B buyers should adopt a proactive approach in their sourcing strategy. Begin by conducting a thorough needs assessment, documenting precise specifications, including torque requirements, environmental conditions, and any regulatory standards that must be met. Engage in open communication with potential drive shaft manufacturers, providing them with detailed technical drawings or specifications to ensure alignment. Consider manufacturers that offer design consultation services, as they can provide insights into material selection and design optimization. Utilize prototypes or pilot runs to test drive shafts under real-world conditions before committing to larger orders, ensuring that the final product meets all operational criteria.
Scenario 2: Difficulty in Quality Assurance and Compliance
The Problem: International buyers often struggle with ensuring that the drive shafts they source meet quality and safety standards, especially when dealing with manufacturers from different regions. Variations in manufacturing processes, material quality, and compliance with international standards can lead to significant risks, such as product recalls or liability issues. This is particularly concerning for industries like automotive and aerospace, where safety is paramount.
The Solution: To mitigate quality assurance challenges, buyers should prioritize manufacturers who adhere to recognized quality management systems, such as ISO 9001. Request documentation of quality control measures and certifications, and consider conducting on-site audits or inspections before finalizing contracts. Establish a clear agreement on quality expectations, including tolerance levels, testing requirements, and compliance with international standards. Additionally, investing in third-party inspection services can provide an extra layer of assurance, ensuring that the products delivered meet all specified criteria. Regular communication throughout the production process can also help in promptly addressing any quality concerns that may arise.
Scenario 3: Supply Chain Disruptions and Lead Times
The Problem: B2B buyers frequently encounter issues related to supply chain disruptions, which can lead to extended lead times and unpredictable delivery schedules for drive shafts. These delays can significantly impact production timelines, leading to lost revenue and strained relationships with end customers. Factors such as geopolitical tensions, natural disasters, or even unexpected spikes in demand can further complicate supply chain reliability.
The Solution: To navigate supply chain challenges effectively, buyers should diversify their supplier base to include multiple manufacturers across different regions. This approach reduces dependency on a single source and allows for greater flexibility in case of disruptions. Implementing a robust supply chain management system can help track inventory levels, forecast demand, and identify potential bottlenecks early. Establishing clear communication channels with suppliers regarding lead times and potential risks is crucial. Additionally, consider negotiating flexible contracts that include clauses for expedited shipping or alternative sourcing options in case of emergencies. Regularly reviewing supplier performance can also help in identifying reliable partners and making informed sourcing decisions in the future.
Strategic Material Selection Guide for drive shaft manufacturer
What Are the Key Materials Used in Drive Shaft Manufacturing?
When selecting materials for drive shafts, manufacturers must consider a range of factors including mechanical properties, cost, and application suitability. Here, we analyze four common materials used in drive shaft manufacturing: Steel, Aluminum, Composite Materials, and Titanium.
How Does Steel Perform as a Drive Shaft Material?
Steel is one of the most widely used materials for drive shafts due to its excellent strength and durability. It typically has a high tensile strength, allowing it to withstand significant loads and stresses. Steel drive shafts can also handle high temperatures and pressures, making them suitable for heavy-duty applications.
Pros: Steel is highly durable and cost-effective, which is appealing for mass production. Its mechanical properties can be enhanced through heat treatment, resulting in a product that can endure harsh environments.
Cons: The primary drawback of steel is its weight, which can affect the overall efficiency of the vehicle or machinery. Additionally, steel is prone to corrosion, necessitating protective coatings or treatments.
Impact on Application: Steel drive shafts are compatible with a variety of media, including oil and water, but may require additional corrosion protection in saline environments.
Considerations for International Buyers: Buyers from regions like Europe (Germany, Italy) should ensure compliance with standards such as ASTM A36 or DIN 17100. In Africa and South America, local sourcing may affect availability and cost.
What Are the Benefits of Using Aluminum for Drive Shafts?
Aluminum is increasingly popular in drive shaft manufacturing due to its lightweight nature and resistance to corrosion. Aluminum drive shafts can reduce the overall weight of vehicles, improving fuel efficiency and performance.
Pros: The primary advantage of aluminum is its lightweight, which enhances vehicle dynamics. It also offers good corrosion resistance, making it suitable for environments with high humidity or exposure to chemicals.
Cons: Aluminum has lower tensile strength compared to steel, which may limit its use in high-stress applications. Additionally, the manufacturing process can be more complex and costly due to the need for specialized welding techniques.
Impact on Application: Aluminum drive shafts are particularly effective in automotive applications where weight reduction is crucial. However, they may not be suitable for heavy-duty machinery that requires high strength.
Considerations for International Buyers: Compliance with standards such as ASTM B221 is essential. Buyers in regions with high humidity should prioritize aluminum for its corrosion resistance.
How Do Composite Materials Compare in Drive Shaft Applications?
Composite materials, often made from a combination of carbon fiber and resin, are gaining traction in drive shaft applications due to their high strength-to-weight ratio. They are particularly favored in high-performance automotive and aerospace applications.
Pros: The main advantage of composite materials is their lightweight nature combined with high strength, which can significantly improve performance. They also exhibit excellent fatigue resistance and are less prone to corrosion.
Cons: The cost of composite materials is typically higher than that of metals, and the manufacturing process can be complex. Additionally, they may not be suitable for all applications, particularly those requiring high impact resistance.
Impact on Application: Composite drive shafts are ideal for high-performance applications, but their compatibility with certain media should be assessed to avoid chemical degradation.
Considerations for International Buyers: Buyers should ensure compliance with relevant standards such as ASTM D3039. The higher initial investment may be justified by long-term performance benefits.
What Role Does Titanium Play in Drive Shaft Manufacturing?
Titanium is known for its exceptional strength and lightweight properties, making it an attractive option for high-performance drive shafts. It offers excellent corrosion resistance and can withstand extreme temperatures.
Pros: The key advantage of titanium is its high strength-to-weight ratio, making it suitable for applications where both performance and durability are critical. It is also highly resistant to corrosion, which extends the lifespan of the drive shaft.
Cons: The primary disadvantage is the cost, as titanium is significantly more expensive than other materials. Additionally, the manufacturing process can be challenging, requiring specialized equipment.
Impact on Application: Titanium drive shafts are particularly effective in aerospace and high-performance automotive applications, where weight and strength are paramount.
Considerations for International Buyers: Compliance with ASTM B348 is necessary. Buyers should also be aware of the higher costs associated with titanium and evaluate their budget accordingly.
Summary Table of Materials for Drive Shaft Manufacturing
Material | Typical Use Case for drive shaft manufacturer | Key Advantage | Key Disadvantage/Limitation | Relative Cost (Low/Med/High) |
---|---|---|---|---|
Steel | Heavy-duty vehicles and machinery | High durability and strength | Heavier and prone to corrosion | Medium |
Aluminum | Automotive applications | Lightweight and corrosion-resistant | Lower strength than steel | Medium |
Composite | High-performance automotive and aerospace | High strength-to-weight ratio | Higher cost and complex manufacturing | High |
Titanium | Aerospace and high-performance automotive | Exceptional strength and lightness | Very high cost and difficult to manufacture | High |
This strategic material selection guide provides international B2B buyers with valuable insights into the materials commonly used in drive shaft manufacturing, enabling informed purchasing decisions tailored to specific applications and regional requirements.
In-depth Look: Manufacturing Processes and Quality Assurance for drive shaft manufacturer
What Are the Key Stages in the Manufacturing Process of Drive Shafts?
Manufacturing drive shafts involves several critical stages that ensure the final product meets the rigorous demands of various industries, particularly in automotive and machinery. The primary stages include:
1. Material Preparation: How Is the Right Material Chosen for Drive Shafts?
The first step in manufacturing drive shafts is selecting the appropriate materials. Common materials include carbon steel, alloy steel, and sometimes aluminum or composite materials for lightweight applications. The choice of material directly affects the drive shaft’s strength, flexibility, and resistance to wear.
Once selected, the materials undergo rigorous testing for mechanical properties, such as tensile strength and fatigue resistance. This ensures that they can withstand the operational stresses they will encounter.
2. Forming: What Techniques Are Used to Shape Drive Shafts?
After material preparation, the next stage is forming the drive shaft. Key techniques include:
- Hot and Cold Forging: These methods shape the metal while it’s in a malleable state, enhancing its strength and durability.
- Machining: Precision machining processes like turning, milling, and grinding are employed to achieve the exact dimensions and surface finishes required for optimal performance.
- Welding: For multi-piece drive shafts, welding techniques such as MIG or TIG welding are used to join sections securely.
These forming processes are critical as they define the drive shaft’s overall geometry and performance characteristics.
3. Assembly: How Are Drive Shafts Assembled for Optimal Performance?
In the assembly stage, various components of the drive shaft are brought together. This may involve integrating universal joints, yokes, and other components that allow for flexibility and transmission of torque.
The assembly process often requires precision tooling and fixtures to maintain alignment and ensure that all components fit together correctly. Additionally, each assembly is checked against specifications to avoid issues during operation.
4. Finishing: What Finishing Techniques Enhance Drive Shaft Durability?
Finishing processes are essential for improving the drive shaft’s resistance to corrosion and wear. Common techniques include:
- Surface Treatment: Processes such as shot peening, electroplating, or powder coating are used to enhance surface hardness and protect against environmental factors.
- Balancing: Dynamic balancing is performed to eliminate vibrations during operation, which can lead to premature wear or failure.
These finishing touches not only improve performance but also extend the lifespan of the drive shafts.
How Is Quality Assurance Implemented in Drive Shaft Manufacturing?
Quality assurance (QA) is integral to the manufacturing process of drive shafts. It ensures that every product meets international and industry-specific standards.
What International Standards Are Relevant for Drive Shaft Manufacturers?
Drive shaft manufacturers often adhere to several international standards, including:
- ISO 9001: This standard emphasizes quality management systems and continuous improvement. Compliance ensures a consistent approach to quality across all manufacturing stages.
- CE Marking: Particularly relevant for European markets, CE marking indicates compliance with health, safety, and environmental protection standards.
- API Standards: For drive shafts used in the oil and gas industry, API standards provide guidelines for quality and safety.
Adhering to these standards is crucial for B2B buyers, ensuring that suppliers meet recognized quality benchmarks.
What Are the Key Quality Control Checkpoints in Drive Shaft Manufacturing?
Quality control (QC) checkpoints are established throughout the manufacturing process to catch any defects early. Common checkpoints include:
- Incoming Quality Control (IQC): This involves inspecting raw materials upon delivery to ensure they meet specifications.
- In-Process Quality Control (IPQC): During manufacturing, ongoing inspections are conducted to monitor the quality of work in progress.
- Final Quality Control (FQC): Before shipping, the completed drive shafts undergo a final inspection to verify that they meet all specifications and standards.
These checkpoints help maintain high quality and reduce the risk of defects reaching customers.
What Testing Methods Are Commonly Used for Drive Shafts?
Drive shafts are subjected to various testing methods to ensure they can withstand operational stresses:
- Tensile Testing: Measures the material’s strength and elasticity.
- Fatigue Testing: Assesses how the drive shaft performs under repeated loading cycles.
- Non-Destructive Testing (NDT): Techniques such as ultrasonic testing or magnetic particle inspection are used to detect internal flaws without damaging the component.
B2B buyers should inquire about the specific testing methods employed by suppliers, as these can vary significantly and affect product reliability.
How Can B2B Buyers Verify Supplier Quality Control?
B2B buyers should take proactive steps to verify the quality control processes of potential suppliers. Here are several strategies:
- Supplier Audits: Conducting on-site audits allows buyers to assess the manufacturing processes, quality control measures, and compliance with standards firsthand.
- Requesting Quality Reports: Suppliers should be willing to provide documentation of their quality control processes, including results from IQC, IPQC, and FQC.
- Third-Party Inspections: Engaging independent inspection services can provide an unbiased assessment of the supplier’s operations and product quality.
For buyers from regions such as Africa, South America, the Middle East, and Europe, understanding these nuances in quality control and certification can significantly impact procurement decisions.
What Are the QC and Certification Nuances for International B2B Buyers?
When purchasing drive shafts internationally, buyers should be aware of specific nuances related to quality control and certification:
- Regulatory Compliance: Each region may have different regulations and standards. For example, the EU has stringent requirements for CE marking, while North America may focus on ASTM standards.
- Cultural Differences: Understanding cultural approaches to quality and business practices can influence communication and negotiation.
- Logistics and Transportation: Quality assurance extends beyond manufacturing. Ensuring products arrive safely and meet specifications upon delivery is critical.
By considering these factors, B2B buyers can make informed decisions and foster successful partnerships with drive shaft manufacturers globally.
Practical Sourcing Guide: A Step-by-Step Checklist for ‘drive shaft manufacturer’
The following guide serves as a practical checklist for international B2B buyers looking to procure drive shaft manufacturing services. This step-by-step approach is designed to streamline your sourcing process, ensuring you identify and select the best suppliers for your specific needs.
Step 1: Define Your Technical Specifications
Clarifying your technical requirements is the cornerstone of successful sourcing. Specifications such as dimensions, materials, and performance standards will guide your search and help suppliers understand your needs.
– Consider factors like load capacity, torque requirements, and environmental conditions.
– Document these specifications to share with potential suppliers for accurate quotations.
Step 2: Conduct Market Research
Before engaging with suppliers, it’s essential to understand the market landscape. Research the leading drive shaft manufacturers in your target regions, such as Europe, Africa, and South America.
– Use online databases and trade publications to identify reputable companies.
– Look for industry reports that provide insights into market trends and supplier capabilities.
Step 3: Evaluate Potential Suppliers
Before committing, it’s crucial to vet suppliers thoroughly. Request company profiles, case studies, and references from buyers in a similar industry or region.
– Focus on their experience with drive shafts and any specialization in your required specifications.
– Don’t just rely on their website; check reviews and testimonials from previous clients.
Step 4: Verify Supplier Certifications
Ensuring that potential suppliers have the necessary certifications is vital for quality assurance. Look for ISO certifications or industry-specific accreditations that demonstrate compliance with quality standards.
– Certifications such as ISO 9001 can indicate a commitment to quality management.
– Inquire about any additional testing or quality control processes they have in place.
Step 5: Request Samples and Prototypes
Once you have shortlisted suppliers, request samples or prototypes of their drive shafts. This step allows you to assess the quality and craftsmanship of their products firsthand.
– Evaluate the materials, finish, and overall design against your specifications.
– Use this opportunity to clarify any doubts regarding manufacturing processes or capabilities.
Step 6: Discuss Terms and Conditions
Before finalizing your supplier, ensure clear communication regarding terms and conditions. Discuss pricing, lead times, payment terms, and warranties.
– Ensure all agreements are documented and transparent to avoid future misunderstandings.
– Consider negotiating terms that protect your interests, such as penalties for late delivery.
Step 7: Establish a Communication Plan
Effective communication is essential for a successful supplier relationship. Establish a clear communication plan outlining points of contact, preferred communication channels, and frequency of updates.
– Regular check-ins can help monitor progress and address any issues promptly.
– Ensure that both parties understand the importance of transparency and responsiveness throughout the manufacturing process.
By following this comprehensive checklist, B2B buyers can make informed decisions when sourcing drive shaft manufacturers, ultimately ensuring a successful procurement process that meets their technical and business needs.
Comprehensive Cost and Pricing Analysis for drive shaft manufacturer Sourcing
What Are the Key Cost Components in Drive Shaft Manufacturing?
When sourcing drive shafts, understanding the cost structure is crucial. The primary components that contribute to the overall cost include:
-
Materials: The choice of materials significantly impacts the pricing. Common materials include steel, aluminum, and composite materials. High-strength materials can increase durability but may also raise costs.
-
Labor: Labor costs vary by region and depend on the complexity of the manufacturing process. Skilled labor is often required for precision machining and assembly, which can increase the overall cost.
-
Manufacturing Overhead: This includes costs related to utilities, facility maintenance, and administrative expenses. Overhead is typically allocated based on production volume, affecting pricing.
-
Tooling: Specialized tools and molds for manufacturing drive shafts can be expensive. The initial investment in tooling is often amortized over large production runs, influencing unit costs.
-
Quality Control (QC): Ensuring the drive shafts meet industry standards requires investment in testing and inspection processes. High-quality standards can increase costs but are essential for reliability and safety.
-
Logistics: Shipping and handling costs play a significant role, particularly for international buyers. These costs can fluctuate based on the shipping method and distance.
-
Margin: Manufacturers typically add a profit margin to cover risks and ensure sustainability. This margin varies based on competition and market demand.
How Do Price Influencers Affect Drive Shaft Sourcing?
Several factors can influence the price of drive shafts, making it essential for buyers to understand these variables:
-
Volume/MOQ (Minimum Order Quantity): Larger orders often lead to lower unit prices due to economies of scale. Negotiating a favorable MOQ can significantly reduce costs.
-
Specifications and Customization: Custom designs or specific performance requirements may increase costs. Clear communication about specifications can help mitigate unexpected price hikes.
-
Materials and Quality Certifications: Premium materials and certifications (such as ISO or industry-specific standards) can increase costs. Buyers should weigh the benefits of quality against their budget.
-
Supplier Factors: Supplier reputation, reliability, and location can impact pricing. Established suppliers may charge a premium but offer better quality assurance and service.
-
Incoterms: Understanding Incoterms (International Commercial Terms) is vital for international transactions. They define responsibilities for shipping, insurance, and tariffs, which can affect the total landed cost.
What Are the Best Practices for Negotiating Drive Shaft Prices?
For international B2B buyers, particularly from Africa, South America, the Middle East, and Europe, effective negotiation strategies can lead to significant cost savings:
-
Research and Benchmarking: Conduct thorough market research to understand typical pricing and identify benchmarks. This knowledge empowers buyers during negotiations.
-
Focus on Total Cost of Ownership (TCO): Assess not just the purchase price, but also maintenance, logistics, and operational costs over the product’s lifespan. A higher upfront cost may be justified by lower long-term expenses.
-
Leverage Relationships: Building strong relationships with suppliers can lead to better pricing and terms. Long-term partnerships often result in discounts and priority service.
-
Be Transparent About Needs: Clearly communicate volume expectations and any specific requirements. Transparency can lead to tailored solutions that meet budget constraints.
-
Consider Alternative Suppliers: Diversifying the supplier base can enhance competitive pricing. Always have backup options to ensure flexibility and leverage in negotiations.
Disclaimer on Indicative Prices
It’s important to note that prices for drive shafts can vary widely based on the factors discussed above. Buyers should seek quotes from multiple suppliers and consider the total cost implications to make informed decisions.
Alternatives Analysis: Comparing drive shaft manufacturer With Other Solutions
Understanding Alternatives to Drive Shaft Manufacturing
In the realm of B2B operations, especially for industries reliant on mechanical systems, selecting the right drive shaft solution is paramount. While traditional drive shaft manufacturing remains a popular choice, various alternatives can also fulfill the functional requirements of power transmission in vehicles and machinery. This section explores viable alternatives to conventional drive shaft manufacturing, enabling international buyers to make informed decisions.
Comparison Table of Drive Shaft Solutions
Comparison Aspect | Drive Shaft Manufacturer | Flexible Coupling | Chain Drive System |
---|---|---|---|
Performance | High torque capacity; reliable under stress | Good for misalignment; reduces vibration | High power transmission; effective for long distances |
Cost | Moderate to high cost; varying by material and customization | Lower initial cost; can be economical | Generally low cost; maintenance can add up |
Ease of Implementation | Requires specialized installation | Easier to install; adaptable | Simple installation; standard components available |
Maintenance | Regular inspection needed; durable | Minimal maintenance required | Requires periodic lubrication and adjustment |
Best Use Case | Heavy-duty applications; precision engineering | Applications with alignment issues | High-torque, low-speed applications; power transmission in simple designs |
What Are the Advantages and Disadvantages of Flexible Couplings?
Flexible couplings serve as a significant alternative to traditional drive shafts, especially in situations where misalignment might occur. They are designed to accommodate slight misalignments between connected shafts, thereby reducing wear and tear on machinery.
Pros:
– Cost-effective: They typically have a lower initial cost compared to drive shafts.
– Easy installation: Flexible couplings are simpler to install and adjust, making them suitable for rapid deployment.
Cons:
– Lower torque capacity: While they can handle misalignment well, they may not support high torque applications as effectively as drive shafts.
– Limited longevity: Under extreme conditions, they may wear out faster than traditional drive shafts.
How Do Chain Drive Systems Compare to Drive Shaft Manufacturing?
Chain drive systems, another alternative, utilize a chain to transmit power between sprockets. This mechanism is common in various applications, from bicycles to industrial machinery.
Pros:
– Cost-effective: Generally, chain drive systems have a lower upfront cost, making them attractive for budget-conscious projects.
– High efficiency: They can transmit power over significant distances without significant energy loss.
Cons:
– Maintenance requirements: They require regular lubrication and adjustment to maintain optimal performance, which can accumulate costs over time.
– Noise and vibration: Chain drives can be noisier compared to drive shafts, which might not be suitable for all operational environments.
How Can B2B Buyers Choose the Right Solution?
When selecting between a drive shaft manufacturer and its alternatives, international B2B buyers should consider several critical factors. Assessing the specific application requirements, including torque demands, installation environment, and budget constraints, is vital.
Moreover, understanding the long-term maintenance implications and the operational efficiencies of each solution can significantly influence the decision-making process. By aligning the choice of technology with the unique operational needs of their business, buyers can enhance productivity while minimizing costs and downtime. Ultimately, the right solution will depend on a careful evaluation of performance, cost, and ease of integration into existing systems.
Essential Technical Properties and Trade Terminology for drive shaft manufacturer
What Are the Essential Technical Properties of Drive Shafts for B2B Buyers?
When sourcing drive shafts, understanding the technical properties is crucial for ensuring product quality and performance. Here are several key specifications that B2B buyers should consider:
1. Material Grade: Why Does It Matter?
The material grade of a drive shaft typically refers to the type of steel or alloy used in its construction. Common grades include carbon steel, stainless steel, and alloy steel. Each material has distinct properties regarding strength, corrosion resistance, and weight, which can significantly affect performance in various applications. For example, stainless steel is preferred for environments prone to corrosion, while carbon steel may be more suitable for heavy-duty applications.
2. Tolerance: What Is Its Role in Performance?
Tolerance defines the permissible limits of variation in a drive shaft’s dimensions. It is critical to ensure that the components fit together seamlessly within machinery. Tight tolerances are often necessary for high-performance applications, such as in automotive or aerospace industries, where even minor deviations can lead to failure. Understanding tolerance specifications helps buyers assess whether the drive shaft will meet their operational needs.
3. Length and Diameter: How Do They Impact Compatibility?
The length and diameter of the drive shaft are essential for compatibility with the machinery it is intended to operate within. A mismatch in size can lead to inefficiencies or even equipment damage. Therefore, buyers must ensure that the dimensions align with their equipment specifications to maintain optimal performance.
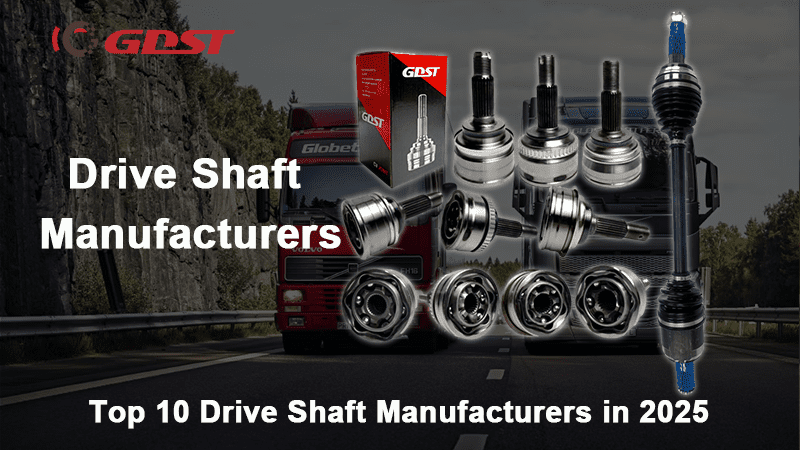
A stock image related to drive shaft manufacturer.
4. Weight: Why Is It Important in Design?
The weight of a drive shaft can influence the overall design and efficiency of a machine. Lighter shafts may reduce the load on the engine, improving fuel efficiency and performance. Conversely, heavier shafts may be necessary for high-torque applications. Buyers should consider the weight in relation to their specific use case to ensure it aligns with their operational goals.
5. Surface Finish: What Is Its Significance?
The surface finish of a drive shaft can affect its performance and longevity. A smoother finish reduces friction, enhancing efficiency, while a rougher finish might be necessary for certain applications to provide better grip. Buyers should inquire about the surface treatment processes used, such as hardening or coating, to ensure they meet the operational requirements.
What Are Common Trade Terminology and Their Implications for Drive Shaft Manufacturers?
Understanding industry jargon can facilitate smoother negotiations and ensure clarity in specifications and agreements. Here are some common terms used in the drive shaft manufacturing sector:
1. OEM (Original Equipment Manufacturer): What Does It Signify?
OEM refers to companies that produce parts or equipment that may be marketed by another manufacturer. In the context of drive shafts, OEMs typically supply components that meet specific standards set by original manufacturers. B2B buyers should verify if a supplier is an OEM to ensure they are receiving high-quality, compatible parts.
2. MOQ (Minimum Order Quantity): How Does It Affect Purchasing?
MOQ is the smallest quantity of a product that a supplier is willing to sell. Understanding MOQ is essential for buyers to manage inventory effectively and avoid over-purchasing. It is also a critical factor in cost negotiations, as larger orders often lead to better pricing.
3. RFQ (Request for Quotation): Why Is It Important?
An RFQ is a document sent to suppliers to request pricing and terms for specific products. It is a vital tool for buyers in comparing offers and ensuring they receive competitive pricing. Crafting a detailed RFQ can lead to more accurate quotes and better supplier relationships.
4. Incoterms: What Are They and Why Do They Matter?
Incoterms are international commercial terms that define the responsibilities of buyers and sellers in shipping goods. Familiarity with Incoterms helps buyers understand their obligations regarding shipping costs, insurance, and risk during transport. This knowledge is crucial for international transactions, especially for buyers from regions like Africa and South America, where logistics can be complex.
By grasping these technical properties and trade terminologies, B2B buyers can make informed decisions when sourcing drive shafts, ensuring they select the right products for their specific applications.
Navigating Market Dynamics and Sourcing Trends in the drive shaft manufacturer Sector
What Are the Current Market Dynamics and Key Trends in the Drive Shaft Manufacturer Sector?
The drive shaft manufacturing sector is currently experiencing a significant evolution driven by globalization, technological advancements, and shifting consumer preferences. International B2B buyers, particularly from regions like Africa, South America, the Middle East, and Europe, must navigate these dynamics to make informed sourcing decisions. One of the key global drivers is the increasing demand for fuel-efficient and high-performance vehicles, which has led manufacturers to innovate and refine their products.
Current trends in B2B technology include the integration of Industry 4.0 practices, such as IoT (Internet of Things) and AI (Artificial Intelligence), into manufacturing processes. These technologies enhance predictive maintenance, reduce downtime, and improve supply chain transparency. Moreover, the rise of e-commerce platforms has facilitated direct access to manufacturers, allowing buyers to compare options more efficiently and make data-driven purchasing decisions.
Additionally, sustainability is becoming a pivotal aspect of the sourcing strategy. Buyers are increasingly favoring manufacturers that demonstrate a commitment to environmental responsibility and ethical sourcing practices. This shift is particularly relevant in Europe, where regulations are tightening around emissions and sustainability standards.
How Is Sustainability Reshaping the Drive Shaft Manufacturer Sector?
Sustainability and ethical sourcing are no longer optional but essential components of the drive shaft manufacturing sector. The environmental impact of manufacturing processes, particularly in terms of carbon emissions and waste, has come under scrutiny. International B2B buyers are increasingly aware of the ecological footprint of their suppliers, prompting a demand for manufacturers that prioritize sustainability.
Ethical supply chains are gaining importance, with buyers seeking partners who not only comply with labor laws but also promote fair trade practices. Certifications such as ISO 14001 (Environmental Management) and ISO 45001 (Occupational Health and Safety) are becoming prerequisites for manufacturers looking to engage with international buyers.
Furthermore, the use of ‘green’ materials—such as recycled metals and composites—has emerged as a trend among manufacturers aiming to reduce their environmental impact. Buyers are encouraged to inquire about the materials used in drive shafts and to seek suppliers who can provide transparency about their sourcing practices.
What Is the Historical Context of Drive Shaft Manufacturing?
The drive shaft manufacturing sector has evolved significantly since its inception in the early 20th century. Originally designed to transmit power from engines to wheels, drive shafts have undergone considerable advancements in materials and engineering techniques.
In the 1970s and 1980s, the introduction of lightweight materials such as aluminum and composite materials revolutionized the industry, enhancing performance and fuel efficiency. The late 1990s and early 2000s saw the integration of computer-aided design (CAD) and manufacturing (CAM) technologies, allowing for more precise and efficient production processes.
Today, the sector is marked by a blend of traditional manufacturing practices and cutting-edge technologies, with a strong emphasis on sustainability and ethical sourcing. This historical context provides B2B buyers with insights into the reliability and innovation of potential suppliers, helping them make informed decisions in an increasingly competitive marketplace.
Frequently Asked Questions (FAQs) for B2B Buyers of drive shaft manufacturer
-
How do I evaluate the quality of a drive shaft manufacturer?
To assess the quality of a drive shaft manufacturer, consider their certifications, such as ISO 9001, which indicates adherence to international quality management standards. Request samples of their products and inquire about their manufacturing processes, including the materials used and the technology implemented. Additionally, review client testimonials and case studies to gauge their reliability and quality assurance practices. Engaging in a site visit can also provide insights into their production capabilities and operational standards. -
What are the common customization options available from drive shaft manufacturers?
Drive shaft manufacturers often provide various customization options to meet specific application requirements. Common modifications include length adjustments, material specifications (e.g., steel, aluminum), and design adaptations for unique vehicle models. It’s crucial to communicate your technical requirements clearly and discuss any potential limitations or additional costs associated with customizations. A collaborative approach in the design phase can lead to optimal solutions tailored to your operational needs. -
What is the typical minimum order quantity (MOQ) for drive shafts?
Minimum order quantities (MOQs) for drive shafts can vary significantly based on the manufacturer and the type of product. Generally, MOQs can range from a few dozen to several hundred units. For small or specialized orders, some manufacturers may offer flexible terms, especially if you are open to discussing pricing and lead times. It’s advisable to inquire directly with potential suppliers to understand their MOQ policies and any options for smaller orders. -
What payment terms should I expect when sourcing from international drive shaft manufacturers?
Payment terms can vary widely among international suppliers. Common arrangements include upfront payments, deposits (typically 30-50%), and balance payments upon delivery or after inspection. Some manufacturers may offer credit terms for established clients. It’s essential to clarify these terms before committing to a purchase and to understand the implications of currency exchange rates and international payment processing fees. Engaging with a financial advisor may help you navigate these complexities effectively. -
How do I ensure compliance with international trade regulations when importing drive shafts?
To ensure compliance with international trade regulations, familiarize yourself with the customs requirements of both your country and the exporting country. This includes understanding tariffs, import duties, and necessary documentation such as certificates of origin and compliance. Working with a customs broker can streamline the process, ensuring that all paperwork is completed accurately. Additionally, ensure that the drive shafts meet relevant safety and quality standards for your market to avoid potential legal issues. -
What logistics considerations should I keep in mind when sourcing drive shafts internationally?
When sourcing drive shafts internationally, consider shipping methods, lead times, and costs. Air freight is faster but more expensive, while sea freight is cost-effective for bulk orders. Be aware of the potential for delays in customs clearance and plan accordingly. Collaborating with a reliable logistics partner can help you navigate these challenges and optimize your supply chain. Additionally, ensure you have a clear understanding of incoterms to define responsibilities for shipping, insurance, and risk. -
How can I verify the credibility of a drive shaft manufacturer?
To verify a manufacturer’s credibility, start by checking their business registration and certifications. Look for online reviews and references from previous clients to gauge their reputation. It can also be beneficial to visit their manufacturing facility if possible, or to engage in video calls for a virtual tour. Joining industry forums and networking with other buyers can provide insights into the manufacturer’s reliability and performance in the market. -
What quality assurance practices should drive shaft manufacturers have in place?
Effective quality assurance practices include routine inspections at various stages of the manufacturing process, adherence to industry standards, and thorough testing of finished products. Manufacturers should implement a robust quality management system that includes documentation of processes, traceability of materials, and corrective action protocols for defects. Ask potential suppliers about their QA methodologies and any third-party audits they undergo to ensure consistent product quality and reliability.
Important Disclaimer & Terms of Use
⚠️ Important Disclaimer
The information provided in this guide, including content regarding manufacturers, technical specifications, and market analysis, is for informational and educational purposes only. It does not constitute professional procurement advice, financial advice, or legal advice.
While we have made every effort to ensure the accuracy and timeliness of the information, we are not responsible for any errors, omissions, or outdated information. Market conditions, company details, and technical standards are subject to change.
B2B buyers must conduct their own independent and thorough due diligence before making any purchasing decisions. This includes contacting suppliers directly, verifying certifications, requesting samples, and seeking professional consultation. The risk of relying on any information in this guide is borne solely by the reader.
Strategic Sourcing Conclusion and Outlook for drive shaft manufacturer
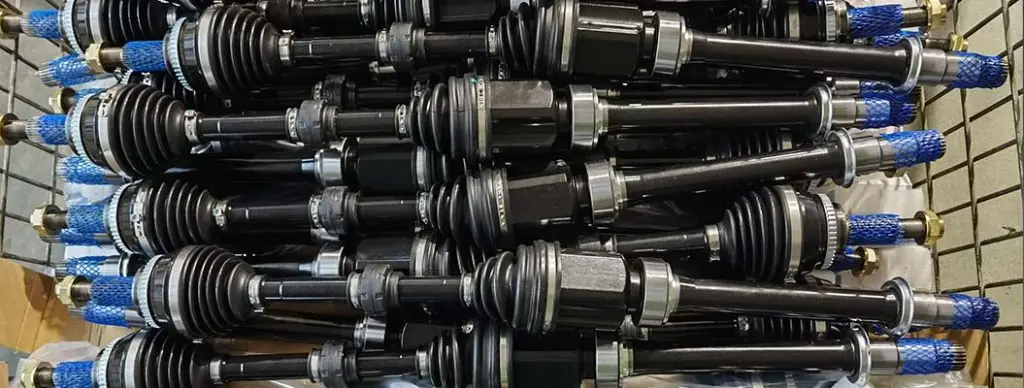
A stock image related to drive shaft manufacturer.
In the dynamic landscape of drive shaft manufacturing, strategic sourcing emerges as a critical component for international B2B buyers. Engaging with a diverse array of suppliers across Africa, South America, the Middle East, and Europe can significantly enhance supply chain resilience and cost-effectiveness. By leveraging local insights and global expertise, buyers can ensure that they not only meet current market demands but also anticipate future trends.
How Can Strategic Sourcing Enhance Your Competitive Advantage?
Investing in strategic sourcing allows businesses to optimize their procurement processes, reduce lead times, and improve product quality. Establishing strong relationships with reliable manufacturers ensures that you have access to innovative solutions tailored to your specific needs. Moreover, understanding regional manufacturing capabilities can provide unique advantages, such as lower transportation costs and compliance with local regulations.
What Does the Future Hold for Drive Shaft Manufacturers?
As we look ahead, the drive shaft manufacturing industry is poised for growth fueled by technological advancements and increasing demand for efficiency. International buyers are encouraged to remain proactive, exploring new partnerships and technologies that can further enhance their operations. By prioritizing strategic sourcing, you position your business not just to survive but to thrive in an increasingly competitive market. Embrace these opportunities and take the next step in securing your supply chain today.