Discover Top Engine Manufacturers: Your Ultimate Sourcing Guide (2025)
Introduction: Navigating the Global Market for engine manufacturer
Navigating the complexities of sourcing high-quality engine manufacturers can be a daunting challenge for international B2B buyers, particularly those from regions such as Africa, South America, the Middle East, and Europe. The diversity of engine types—from automotive to industrial and marine—combined with varying applications and regulatory standards, necessitates a strategic approach to procurement. This guide aims to equip decision-makers with the essential insights required to navigate the global market effectively.
Throughout this comprehensive resource, we will cover critical aspects of the engine manufacturing landscape, including the different types of engines available, their specific applications, and strategies for vetting suppliers. Additionally, we will delve into cost considerations, ensuring that buyers are well-informed to make prudent purchasing decisions. By understanding the intricacies of the market, B2B buyers can mitigate risks associated with supply chain disruptions and quality inconsistencies.
This guide empowers international buyers by providing actionable insights tailored to the unique challenges faced by companies in regions like Kenya and Saudi Arabia. With a focus on fostering informed decision-making, it offers a pathway to establishing reliable partnerships with engine manufacturers that align with specific business needs and compliance requirements. Ultimately, this resource is designed to enhance your sourcing strategy, ensuring that you acquire the best possible engines for your operational demands.
Understanding engine manufacturer Types and Variations
Type Name | Key Distinguishing Features | Primary B2B Applications | Brief Pros & Cons for Buyers |
---|---|---|---|
Internal Combustion Engines | Operate on gasoline or diesel; widely used; high power output | Automotive, industrial machinery, marine | Pros: Established technology, high power. Cons: Environmental concerns, fuel dependency. |
Electric Engines | Powered by batteries; lower emissions; quieter operation | Electric vehicles, renewable energy systems | Pros: Eco-friendly, lower operating costs. Cons: Limited range, longer refueling times. |
Hybrid Engines | Combination of internal combustion and electric; versatile | Automotive, public transport, logistics | Pros: Flexibility, reduced emissions. Cons: Complex systems, higher maintenance costs. |
Gas Turbine Engines | High efficiency at large scales; used in aviation and power generation | Aviation, energy production, marine | Pros: High power-to-weight ratio, reliability. Cons: High initial investment, specialized maintenance. |
Stirling Engines | External combustion; uses heat to generate power; efficient | Renewable energy, niche applications | Pros: High efficiency, low emissions. Cons: Limited application, complex design. |
What Are Internal Combustion Engines and Their B2B Relevance?
Internal combustion engines (ICE) are the backbone of traditional automotive and industrial applications. These engines utilize gasoline or diesel fuel to produce power through combustion. Their widespread use in vehicles, machinery, and marine applications makes them crucial for many B2B sectors. Buyers should consider factors like fuel efficiency, availability of parts, and adherence to emission regulations, especially in regions with stringent environmental laws. While ICEs offer high power output and established technology, their environmental impact is a growing concern.
How Do Electric Engines Benefit B2B Buyers?
Electric engines are increasingly popular due to their efficiency and reduced environmental impact. They are primarily used in electric vehicles and renewable energy systems. B2B buyers should evaluate the total cost of ownership, including battery replacement cycles and charging infrastructure. The benefits include lower operating costs and compliance with green initiatives, although the limitations in range and longer refueling times may pose challenges for certain applications, particularly in regions with less developed charging networks.
What Makes Hybrid Engines a Flexible Choice for Businesses?
Hybrid engines combine internal combustion and electric power, offering flexibility and reduced emissions. They are commonly found in automotive applications and public transport systems. Buyers should assess the operational efficiency and maintenance requirements of hybrid systems, which tend to be more complex than traditional engines. While hybrids can significantly reduce fuel consumption and emissions, the initial investment and ongoing maintenance can be higher, making thorough cost-benefit analysis essential.
Why Choose Gas Turbine Engines for Large-Scale Applications?
Gas turbine engines are known for their high efficiency and power-to-weight ratio, making them ideal for aviation and energy production. B2B buyers in sectors such as aerospace and power generation should consider the reliability and performance characteristics of these engines. However, the high initial investment and the need for specialized maintenance can be drawbacks. Understanding the operational context and expected lifespan is critical for businesses contemplating gas turbine adoption.
What Are the Advantages and Limitations of Stirling Engines?
Stirling engines operate using external combustion and are known for their efficiency and low emissions. They find niche applications in renewable energy systems. B2B buyers should weigh the benefits of high efficiency against the complexity and limited application scope of Stirling engines. While they present a sustainable option, the specialized design may require a higher level of expertise for maintenance and implementation, which could be a barrier for some businesses.
Related Video: Car Engine Parts & Their Functions Explained in Details | The Engineers Post
Key Industrial Applications of engine manufacturer
Industry/Sector | Specific Application of Engine Manufacturer | Value/Benefit for the Business | Key Sourcing Considerations for this Application |
---|---|---|---|
Agriculture | Diesel Engines for Tractors | Increased fuel efficiency and durability for heavy-duty tasks | Compliance with local emissions regulations; availability of service parts |
Construction | Heavy Machinery Engines | Enhanced power output for construction equipment, leading to reduced operational costs | Engine size and compatibility with existing machinery; warranty and support services |
Marine | Marine Propulsion Engines | Reliable power for vessels, ensuring operational safety and efficiency | Saltwater corrosion resistance; fuel type compatibility; service and maintenance availability |
Transportation | Commercial Vehicle Engines | Improved fuel economy and lower emissions for freight transport | Compliance with international emissions standards; reliability and after-sales service |
Power Generation | Generator Engines | Continuous power supply solutions for various industries | Fuel type (diesel, natural gas); noise levels; emissions compliance; service agreements |
How is Engine Manufacturing Applied in Agriculture?
In the agricultural sector, diesel engines are critical for powering tractors and other farming equipment. These engines are designed to provide high torque and efficiency, allowing for effective tillage, planting, and harvesting. For international buyers, particularly in regions like Africa and South America, sourcing engines that comply with local emissions standards while providing robust performance is essential. Additionally, the availability of spare parts and service networks can significantly impact operational uptime and maintenance costs.
What Role Do Engine Manufacturers Play in Construction?
Heavy machinery engines are vital in the construction industry, where equipment such as excavators, bulldozers, and cranes require powerful and reliable engines to perform efficiently. The right engine can enhance fuel efficiency and reduce operational costs, a crucial factor for construction firms operating in competitive markets. Buyers from the Middle East and Europe should consider engine compatibility with existing machinery and the warranty and support services offered by manufacturers to ensure longevity and reliability in their operations.
How Are Marine Engines Used in the Shipping Industry?
In the marine sector, propulsion engines are essential for the operation of various vessels, including cargo ships, fishing boats, and recreational crafts. These engines must be reliable and efficient to ensure safety and minimize downtime. For buyers in Europe and Africa, considerations such as resistance to saltwater corrosion and compatibility with different fuel types are paramount. Additionally, access to maintenance services and parts is critical to ensure that vessels remain operational and compliant with maritime regulations.
What Are the Benefits of Commercial Vehicle Engines?
Commercial vehicle engines are designed to enhance fuel economy and reduce emissions, making them ideal for freight transportation. In regions like South America and the Middle East, where logistics is crucial for economic growth, sourcing engines that meet international emissions standards while providing high reliability is essential. Buyers should evaluate the engine’s performance metrics and the manufacturer’s after-sales service capabilities to ensure a smooth operation over the vehicle’s lifespan.
How Do Generator Engines Impact Power Generation?
Generator engines are pivotal in providing continuous power supply solutions across various industries. They are commonly used in remote areas where grid power is unreliable. For international buyers, particularly in developing regions, considerations such as fuel type, noise levels, and emissions compliance are critical when sourcing engines. Establishing service agreements with manufacturers can also ensure that businesses have access to timely maintenance and support, thereby enhancing operational reliability.
Related Video: Types of Valves | All in One Guide to Industrial Valve Types
3 Common User Pain Points for ‘engine manufacturer’ & Their Solutions
Scenario 1: Navigating Complex Engine Specifications
The Problem: B2B buyers often face the daunting task of selecting the right engine for their specific applications, especially in diverse markets such as Africa and South America. With varying requirements based on local regulations, environmental conditions, and operational needs, buyers can struggle to sift through technical jargon and specifications. Misunderstanding these nuances can lead to costly mistakes, such as purchasing an engine that doesn’t meet performance expectations or compliance standards.
The Solution: To overcome this challenge, it’s crucial for buyers to conduct thorough market research and engage directly with manufacturers. Start by identifying your specific needs—consider factors such as load requirements, fuel types, and environmental conditions. Then, request detailed technical documentation from manufacturers, including performance graphs and compliance certifications. Engage with technical sales representatives who can provide tailored advice based on your application. Additionally, consider partnering with local experts or consultants who understand regional requirements and can guide you in selecting the most suitable engine. This proactive approach not only mitigates risks but also ensures that you invest in an engine that delivers optimal performance.
Scenario 2: Managing Supply Chain Disruptions
The Problem: International B2B buyers are increasingly facing supply chain disruptions that affect the timely delivery of engines. Factors such as geopolitical tensions, local regulations, and logistical challenges can lead to delays, increased costs, and project overruns. For businesses in regions like the Middle East and Europe, where project timelines are critical, these disruptions can severely impact operational efficiency and profitability.
The Solution: To effectively manage these risks, it is essential to establish robust relationships with multiple suppliers. Diversifying your supplier base can provide alternatives should one manufacturer face delays. Additionally, negotiate terms that include clear delivery timelines and penalties for non-compliance to hold suppliers accountable. Leveraging technology, such as supply chain management software, can help monitor inventory levels and predict potential disruptions. Engage in proactive communication with your suppliers to stay informed about potential delays and work collaboratively to devise contingency plans. This strategic approach will enhance your resilience against supply chain challenges and maintain project timelines.
Scenario 3: Ensuring Long-Term Support and Maintenance
The Problem: Another common pain point for B2B buyers is the concern over long-term support and maintenance for the engines purchased. Many buyers worry about the availability of spare parts and technical support, especially when dealing with manufacturers from different regions. This uncertainty can lead to significant downtime and increased operational costs if an engine requires repairs or servicing.
The Solution: To address these concerns, prioritize manufacturers that offer comprehensive post-purchase support. When evaluating potential suppliers, inquire about their warranty policies, service agreements, and the availability of spare parts. Opt for manufacturers that have established service networks in your region or that can provide remote support. It may also be beneficial to invest in training for your maintenance staff to handle routine upkeep and minor repairs, thus reducing dependency on external support. Lastly, consider establishing a maintenance contract with the manufacturer to ensure timely service and access to parts. By taking these steps, buyers can secure peace of mind regarding the longevity and reliability of their engine investments.
Strategic Material Selection Guide for engine manufacturer
What Are the Key Materials Used in Engine Manufacturing?
When selecting materials for engine manufacturing, it is crucial to consider properties that directly affect performance, durability, and cost. Here, we analyze four common materials used in engine components, focusing on their key properties, advantages, disadvantages, and considerations for international B2B buyers.
How Does Aluminum Benefit Engine Manufacturers?
Aluminum is a lightweight material known for its excellent thermal conductivity and corrosion resistance. It typically has a temperature rating of up to 400°C and can withstand moderate pressure levels, making it suitable for engine blocks and cylinder heads.
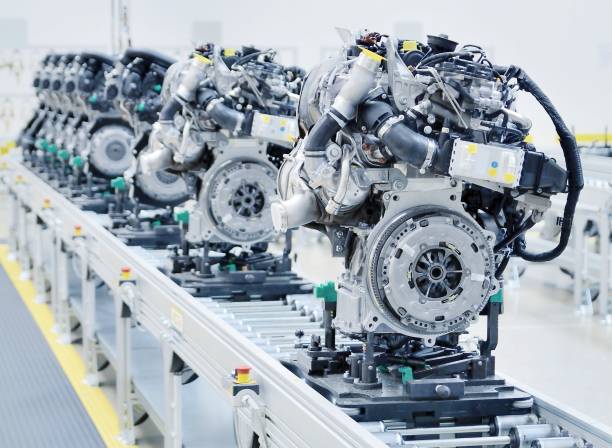
A stock image related to engine manufacturer.
Pros: Aluminum’s low density contributes to reduced overall vehicle weight, improving fuel efficiency. It is also relatively easy to machine, which simplifies manufacturing processes.
Cons: The main drawback is its lower strength compared to steel, which can lead to deformation under high-stress conditions. Additionally, aluminum components can be more expensive than their steel counterparts.
Impact on Application: Aluminum is compatible with various media, including engine oils and coolants, but care must be taken in applications involving high-temperature exhaust gases.
Considerations for International Buyers: Buyers from regions like Africa and the Middle East should consider local sourcing capabilities and compliance with standards such as ASTM and DIN, which may influence material availability and cost.
Why Is Steel a Preferred Choice for Engine Components?
Steel is one of the most widely used materials in engine manufacturing, particularly for crankshafts, camshafts, and other critical components. It offers high strength and excellent wear resistance, with temperature ratings that can exceed 600°C.
Pros: Steel’s durability and strength make it ideal for high-stress applications. It is also relatively cost-effective compared to other materials, making it a popular choice for mass production.
Cons: Steel is heavier than aluminum, which can negatively impact fuel efficiency. Additionally, it is more susceptible to corrosion if not properly treated.
Impact on Application: Steel components are generally compatible with a wide range of fluids, including fuels and lubricants, but may require additional coatings for corrosion resistance in harsh environments.
Considerations for International Buyers: Buyers in Europe and South America should be aware of local regulations regarding emissions and material standards, as these can affect the selection of steel grades.
How Do Composites Enhance Engine Performance?
Composite materials, particularly carbon fiber and fiberglass, are increasingly being used in high-performance engines. They offer excellent strength-to-weight ratios and can withstand high temperatures and pressures.
Pros: Composites significantly reduce weight without compromising strength, leading to improved performance and fuel efficiency. They also exhibit excellent corrosion resistance.
Cons: The primary limitation is the high manufacturing cost and complexity associated with composite materials. Additionally, they may require specialized skills for repair and maintenance.
Impact on Application: Composites are suitable for components exposed to extreme conditions, such as racing engines, but may not be ideal for everyday applications due to their cost.
Considerations for International Buyers: Buyers should evaluate the availability of composite materials and the expertise required for their application and maintenance, especially in regions with less developed manufacturing capabilities.
What Role Does Cast Iron Play in Engine Manufacturing?
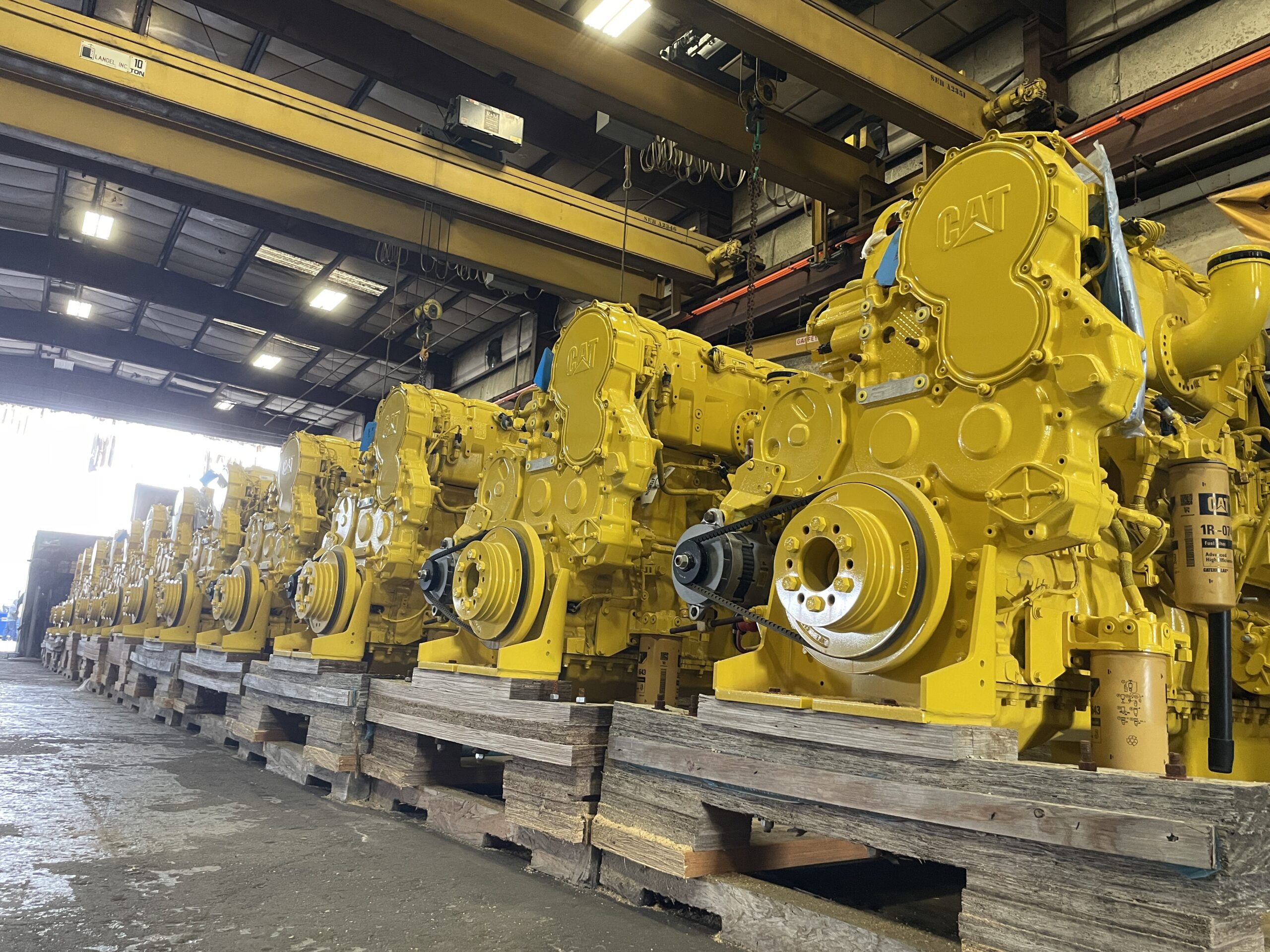
A stock image related to engine manufacturer.
Cast iron is a traditional material used in engine blocks and cylinder heads due to its excellent wear resistance and ability to dampen vibrations. It can handle high temperatures and pressures, making it suitable for heavy-duty applications.
Pros: Cast iron is highly durable and cost-effective, making it a staple in many engine designs. Its ability to absorb vibrations contributes to a smoother engine operation.
Cons: The main drawback is its weight, which can negatively impact overall vehicle performance. Additionally, cast iron can be brittle, leading to potential failure under extreme stress.
Impact on Application: Cast iron is compatible with various engine fluids, but its weight can be a disadvantage in performance-oriented applications.
Considerations for International Buyers: Buyers in regions like Kenya and Saudi Arabia should consider the local market for cast iron components and any relevant industry standards that might affect material selection.
Summary Table of Material Selection for Engine Manufacturing
Material | Typical Use Case for Engine Manufacturer | Key Advantage | Key Disadvantage/Limitation | Relative Cost (Low/Med/High) |
---|---|---|---|---|
Aluminum | Engine blocks, cylinder heads | Lightweight, good thermal conductivity | Lower strength than steel | Medium |
Steel | Crankshafts, camshafts | High strength, cost-effective | Heavier, susceptible to corrosion | Low |
Composites | High-performance engine components | Excellent strength-to-weight ratio | High manufacturing cost | High |
Cast Iron | Engine blocks, cylinder heads | Highly durable, vibration dampening | Heavy, can be brittle | Low |
This strategic material selection guide provides valuable insights for international B2B buyers in the engine manufacturing sector, aiding them in making informed decisions based on performance requirements, cost considerations, and regional compliance.
In-depth Look: Manufacturing Processes and Quality Assurance for engine manufacturer
What Are the Key Stages in the Engine Manufacturing Process?
The engine manufacturing process is complex and involves several critical stages to ensure the final product meets the necessary performance and quality standards. Understanding these stages can help B2B buyers from Africa, South America, the Middle East, and Europe make informed decisions when selecting suppliers.
Material Preparation: What Materials Are Used in Engine Manufacturing?
The first step in the engine manufacturing process is material preparation. Common materials used in engine production include aluminum, cast iron, and various alloys. These materials are chosen for their strength, durability, and resistance to heat and corrosion.
-
Sourcing Raw Materials: B2B buyers should ensure that suppliers source high-quality raw materials from reputable suppliers. This could involve reviewing supplier certifications and material specifications.
-
Material Testing: Before manufacturing begins, materials undergo rigorous testing to verify their properties, ensuring they meet international standards such as ASTM or ISO.
How Is Engine Forming Achieved?
Once materials are prepared, the next step is forming. This stage involves shaping the raw materials into components that will eventually form the engine.
-
Casting: This is a prevalent method where molten metal is poured into molds to create engine blocks, cylinder heads, and other parts. Buyers should inquire about the casting techniques used, such as sand casting or die casting, as these can affect the quality of the final product.
-
Machining: After casting, components are machined to achieve precise dimensions. This includes processes like milling, turning, and grinding. B2B buyers should verify the machining capabilities of potential suppliers to ensure they can produce parts within tight tolerances.
-
Assembly Techniques: Various assembly methods, including robotic assembly and manual assembly, can be employed. Understanding a supplier’s assembly process can provide insights into their efficiency and potential for quality control.
What Finishing Processes Are Important for Engine Components?
Finishing is critical in enhancing the performance and appearance of engine components. Key finishing processes include:
-
Surface Treatment: Techniques such as anodizing, plating, and painting improve corrosion resistance and aesthetic appeal. B2B buyers should ask about the specific treatments applied to ensure durability.
-
Quality Checks During Finishing: It is essential to implement quality checks at this stage to identify any defects before the components move to the next phase.
How Does Quality Assurance Fit into the Engine Manufacturing Process?
Quality assurance (QA) is a vital aspect of engine manufacturing, ensuring that each component meets specified standards and regulations.
What International Standards Should Buyers Be Aware Of?
To maintain high-quality manufacturing, suppliers must adhere to international standards. Key standards include:
-
ISO 9001: This standard focuses on quality management systems and is crucial for ensuring consistent quality in products and services. B2B buyers should confirm that suppliers are ISO 9001 certified.
-
Industry-Specific Standards: Depending on the market, other certifications may be relevant. For example, CE marking is essential for products sold in the European Union, while API standards may apply to suppliers in the oil and gas industry.
What Are the Key Quality Control Checkpoints in Manufacturing?
Quality control (QC) checkpoints play an essential role in identifying defects and ensuring compliance with standards. Key checkpoints include:
-
Incoming Quality Control (IQC): This involves inspecting raw materials upon arrival. Buyers can request IQC reports to verify that materials meet specifications.
-
In-Process Quality Control (IPQC): During production, continuous monitoring is performed to ensure that the manufacturing process remains within established parameters. Buyers should inquire about the frequency and methods of IPQC checks.
-
Final Quality Control (FQC): Before products are shipped, a final inspection ensures that all components meet quality standards. Buyers can request FQC reports to understand the final checks performed.
How Can B2B Buyers Verify Supplier Quality Control?
B2B buyers must be proactive in verifying the quality control processes of potential suppliers. Here are some actionable steps:
-
Conduct Audits: Regular audits of suppliers can provide insights into their manufacturing processes and adherence to quality standards. Buyers should consider scheduling these audits, either directly or through third-party services.
-
Request Documentation: Suppliers should provide documentation of their quality control processes, including inspection reports and certifications. This documentation can help buyers assess the supplier’s commitment to quality.
-
Third-Party Inspections: Engaging third-party inspection services can offer an unbiased assessment of the supplier’s quality control measures. This is especially important for international buyers who may not be able to conduct on-site inspections.
What Are the Challenges and Considerations for International B2B Buyers?
When sourcing engines from suppliers in different regions, B2B buyers must navigate various challenges:
- Regulatory Compliance: Different countries have varying regulations regarding manufacturing standards. Buyers should be aware of these regulations in their target markets to ensure compliance.
-
Cultural and Communication Barriers: Time zone differences and language barriers can complicate communication with suppliers. Establishing clear communication channels is vital for successful collaboration.
-
Logistics and Supply Chain Management: Understanding the logistics involved in international shipping is crucial for timely delivery. Buyers should evaluate potential suppliers’ logistics capabilities to avoid delays.
By focusing on these manufacturing processes and quality assurance practices, B2B buyers can make informed decisions when selecting engine manufacturers, ensuring that they partner with suppliers who prioritize quality and reliability.
Practical Sourcing Guide: A Step-by-Step Checklist for ‘engine manufacturer’
Introduction
In the competitive landscape of engine manufacturing, selecting the right supplier is critical for international B2B buyers, especially from Africa, South America, the Middle East, and Europe. This step-by-step sourcing guide provides a practical checklist to streamline your procurement process, ensuring you find a manufacturer that meets your technical requirements, budget, and operational standards.
Step 1: Define Your Technical Specifications
Clearly outlining your technical specifications is the foundation of a successful sourcing process. Consider the type of engines required, performance metrics, and compliance with industry standards. This clarity will help you communicate effectively with potential suppliers and ensure that you receive accurate proposals.
- Performance Requirements: Specify horsepower, fuel type, and efficiency standards.
- Regulatory Compliance: Identify any local or international regulations that must be adhered to.
Step 2: Conduct Market Research on Engine Manufacturers
Researching the market landscape helps you identify potential suppliers and understand their capabilities. Utilize online directories, industry forums, and trade shows to gather information about engine manufacturers.
- Reputation and Experience: Look for manufacturers with a strong track record in your specific sector.
- Geographic Presence: Consider manufacturers that have a regional presence, as this may facilitate easier communication and logistics.
Step 3: Evaluate Potential Suppliers
Before making a commitment, it’s essential to thoroughly vet suppliers. Request detailed company profiles, case studies, and references from buyers in similar industries or regions.
- Quality Assurance: Inquire about quality control processes and certifications (e.g., ISO 9001).
- Production Capacity: Ensure that the supplier can meet your volume requirements and timelines.
Step 4: Request and Analyze Quotes
Once you have a shortlist of potential suppliers, request detailed quotations. Analyzing these quotes is not just about comparing prices; it also involves evaluating the overall value offered.
- Cost Breakdown: Look for transparency in pricing, including all associated costs (shipping, duties, etc.).
- Payment Terms: Consider the payment options and terms offered by each supplier.
Step 5: Verify Supplier Certifications and Compliance
Confirming that suppliers possess the necessary certifications and comply with relevant regulations is crucial. This step minimizes risks associated with quality and legal compliance.
- Certifications: Check for industry-specific certifications that demonstrate adherence to quality standards.
- Regulatory Compliance: Ensure that the supplier complies with local laws in your region, particularly in terms of environmental standards.
Step 6: Conduct Site Visits or Virtual Inspections
If possible, conduct site visits or virtual inspections to assess the manufacturing facilities. This firsthand evaluation can provide insights into the supplier’s operational capabilities and commitment to quality.
- Facility Conditions: Look for well-maintained equipment and a clean working environment.
- Workforce Competence: Assess the skill level of the workforce and their adherence to safety standards.
Step 7: Establish Clear Communication Channels
Finally, ensure that clear communication channels are established with your chosen supplier. Effective communication is vital for addressing any issues that may arise during the manufacturing process.
- Point of Contact: Designate a primary contact person for smoother interactions.
- Regular Updates: Set expectations for regular updates on production status and any potential delays.
By following this checklist, B2B buyers can navigate the complexities of sourcing engine manufacturers more effectively, ultimately leading to successful procurement outcomes.
Comprehensive Cost and Pricing Analysis for engine manufacturer Sourcing
What Are the Key Cost Components in Engine Manufacturing?
When sourcing engines, it’s essential to understand the various cost components that contribute to the final pricing. The primary cost factors include:
-
Materials: The cost of raw materials such as aluminum, steel, and specialized alloys can fluctuate based on market demand and supply chain issues. Buyers should consider sourcing materials locally to mitigate import costs.
-
Labor: Labor costs can vary significantly by region. For instance, labor is generally more affordable in certain African and South American countries compared to Europe. However, the skill level and experience of the workforce can impact the overall quality of the engine.
-
Manufacturing Overhead: This includes costs related to utilities, facility maintenance, and equipment depreciation. Efficient manufacturing processes can help reduce these overheads, leading to lower overall costs.
-
Tooling: Specialized tooling is often required for engine production, and the cost can be substantial. Investing in high-quality tooling can enhance production efficiency and reduce defects.
-
Quality Control (QC): Implementing robust QC measures is crucial for ensuring product reliability. While this adds to the cost, it can prevent costly recalls and enhance brand reputation.
-
Logistics: Shipping and handling costs must be factored in, especially for international buyers. Understanding Incoterms can help clarify responsibilities and potential costs associated with transportation.
-
Margin: Manufacturers typically add a margin to cover risks and ensure profitability. Understanding typical industry margins can aid buyers in negotiating better pricing.
How Do Price Influencers Affect Engine Sourcing Decisions?
Several factors can influence the pricing of engines, which buyers should be aware of:
-
Volume and Minimum Order Quantity (MOQ): Larger orders often lead to discounts. Buyers should assess their needs and consider consolidating orders to meet MOQ requirements.
-
Specifications and Customization: Customized engines tailored to specific applications may incur additional costs. Buyers should clearly define their requirements to avoid unexpected expenses.
-
Materials and Quality Certifications: High-quality materials and certifications, such as ISO standards, can increase costs. However, these can also enhance performance and longevity, providing better value in the long run.
-
Supplier Factors: The reputation and reliability of the supplier can impact pricing. Established suppliers may charge a premium but often deliver better quality and service.
-
Incoterms: Understanding the implications of different Incoterms is vital for managing costs related to shipping and responsibilities. For instance, choosing FOB (Free On Board) might shift some shipping costs to the buyer.
What Are the Best Negotiation Tips for B2B Buyers in Engine Manufacturing?
To achieve cost-efficiency in engine sourcing, consider these negotiation strategies:
-
Benchmarking Prices: Research market rates and compare prices from multiple suppliers. This knowledge can empower you during negotiations.
-
Total Cost of Ownership (TCO): Evaluate not just the purchase price but also the long-term costs associated with maintenance, warranty, and operational efficiency. A slightly higher upfront cost may lead to lower overall expenses.
-
Long-Term Partnerships: Building strong relationships with suppliers can lead to better pricing and terms. Suppliers may offer discounts for repeat business or long-term contracts.
-
Flexibility in Specifications: If possible, consider flexibility in engine specifications. This can lead to cost savings, especially if standard components can be used instead of custom ones.
-
Leverage Volume Orders: If your company can commit to larger orders, use this as leverage to negotiate better pricing.
What Should International Buyers Consider Regarding Pricing Nuances?
For international buyers, especially those from Africa, South America, the Middle East, and Europe, pricing nuances can significantly affect sourcing decisions. Currency fluctuations, import tariffs, and local regulations can all impact final costs. It’s advisable to stay informed about economic conditions in both the home and supplier countries. Additionally, understanding local market dynamics, including competition and demand, can provide insights into potential pricing strategies.
Disclaimer on Indicative Prices
It’s important to note that prices can vary widely based on a multitude of factors including market conditions, supply chain dynamics, and specific buyer requirements. Always seek quotes from multiple suppliers and consider all cost components before making purchasing decisions.
Alternatives Analysis: Comparing engine manufacturer With Other Solutions
When considering engine manufacturing solutions, it is vital for international B2B buyers to explore various alternatives that may better suit their operational needs, cost constraints, and performance expectations. This section provides a comparative analysis of traditional engine manufacturing against two promising alternatives: electric motors and hybrid systems.
Comparison Table of Engine Manufacturer vs. Alternatives
Comparison Aspect | Engine Manufacturer | Electric Motors | Hybrid Systems |
---|---|---|---|
Performance | High torque, reliable | Excellent efficiency, lower maintenance | Versatile performance, combined efficiency |
Cost | High initial investment | Moderate initial cost, lower operational cost | Higher initial cost, long-term savings |
Ease of Implementation | Complex setup | Simple installation with fewer components | Moderate complexity, integration required |
Maintenance | Regular servicing needed | Minimal maintenance required | Moderate maintenance, depending on usage |
Best Use Case | Heavy-duty applications | Urban transport, renewable energy | Diverse applications, energy efficiency |
What Are the Pros and Cons of Electric Motors?
Electric motors are becoming increasingly popular due to their efficiency and low maintenance needs. They offer excellent performance in terms of torque and speed, making them suitable for urban transport applications where emissions are a concern.
Pros:
– Efficiency: Electric motors convert a high percentage of energy into usable power, resulting in lower operational costs.
– Maintenance: Fewer moving parts mean less wear and tear, leading to reduced maintenance requirements.
Cons:
– Initial Cost: The upfront investment can be significant, especially for high-performance models.
– Limited Range: Depending on battery technology, range can be a limitation for certain applications.
How Do Hybrid Systems Compare?
Hybrid systems combine both traditional combustion engines and electric motors, providing flexibility in performance and energy use. This technology is particularly advantageous for applications requiring versatility and fuel efficiency.
Pros:
– Versatility: Hybrid systems can operate in various modes, adapting to different driving conditions and enhancing fuel economy.
– Reduced Emissions: They lower overall emissions compared to traditional engines, aligning with sustainability goals.
Cons:
– Complexity: The integration of two systems can lead to more complex maintenance and repair needs.
– Higher Initial Cost: The upfront cost of hybrid systems tends to be higher than that of conventional engines, although they can save money over time.
How Can B2B Buyers Choose the Right Solution?
When selecting the right solution, B2B buyers should assess their specific operational requirements, budget constraints, and long-term sustainability goals. For example, if efficiency and low emissions are paramount, electric motors may be the best choice. Conversely, companies that require flexibility and the ability to operate in diverse conditions may find hybrid systems more advantageous. Traditional engine manufacturing may still be preferable for heavy-duty applications where high torque and reliability are critical.
Ultimately, the decision should be based on a thorough analysis of the pros and cons of each option, aligning them with the company’s operational strategies and market demands. By carefully considering these factors, buyers can make informed decisions that will enhance their operational efficiency and competitive edge in the marketplace.
Essential Technical Properties and Trade Terminology for engine manufacturer
What Are the Essential Technical Properties in Engine Manufacturing?
When considering engine manufacturing, understanding specific technical properties is crucial for ensuring optimal performance and reliability. Here are some key specifications that B2B buyers should be familiar with:
-
Material Grade
– Material grade refers to the classification of materials based on their composition and properties, such as tensile strength and corrosion resistance. Common materials include aluminum alloys, cast iron, and high-strength steel. Choosing the right material grade is vital for the durability and efficiency of the engine, particularly in demanding environments often found in Africa and the Middle East. -
Tolerances
– Tolerance defines the allowable variations in dimensions of manufactured parts. Precise tolerances are critical in engine manufacturing to ensure that components fit together correctly and operate smoothly. For B2B buyers, understanding tolerances helps in assessing the quality of suppliers and ensuring that the engine will meet operational specifications. -
Thermal Conductivity
– This property measures a material’s ability to conduct heat. In engines, effective thermal management is essential to prevent overheating and ensure efficient operation. Buyers should evaluate the thermal conductivity of engine components, especially in regions with high ambient temperatures like parts of South America. -
Fatigue Strength
– Fatigue strength indicates how much stress a material can withstand before failing due to repeated loading and unloading. This is particularly important for engine components that experience cyclical forces during operation. A thorough understanding of fatigue strength helps buyers choose reliable engines that will perform well over time. -
Weight-to-Power Ratio
– This ratio compares the weight of the engine to its power output. A lower weight-to-power ratio indicates a more efficient engine, which is essential for applications requiring high performance without excessive weight, such as in automotive and aerospace industries. B2B buyers should prioritize engines with favorable weight-to-power ratios to enhance overall vehicle performance.
What Are Common Trade Terms in Engine Manufacturing?
Familiarity with industry terminology is essential for effective communication and negotiation in engine manufacturing. Here are some common terms B2B buyers should know:
-
OEM (Original Equipment Manufacturer)
– OEM refers to companies that produce parts or equipment that may be marketed by another manufacturer. Understanding OEM relationships is crucial for buyers looking to source quality components that meet specific standards. -
MOQ (Minimum Order Quantity)
– MOQ denotes the smallest quantity of a product that a supplier is willing to sell. Knowing the MOQ is important for buyers to manage inventory costs and ensure that they are not overcommitting to a purchase that may exceed their immediate needs. -
RFQ (Request for Quotation)
– An RFQ is a document issued by a buyer to solicit price quotes from suppliers for specific products or services. Buyers should use RFQs to compare prices, terms, and capabilities among different manufacturers, facilitating informed decision-making. -
Incoterms (International Commercial Terms)
– Incoterms are a series of international rules that define the responsibilities of buyers and sellers in international transactions. Familiarity with these terms helps buyers understand shipping costs, risks, and responsibilities associated with the delivery of engine components. -
Lead Time
– Lead time is the period between the initiation of an order and its completion. Understanding lead times is essential for buyers to plan production schedules and manage supply chain expectations effectively.
By familiarizing themselves with these technical properties and trade terms, international B2B buyers can make informed decisions, negotiate effectively, and ultimately select the right engine manufacturers that meet their operational needs.
Navigating Market Dynamics and Sourcing Trends in the engine manufacturer Sector
What Are the Current Market Dynamics and Sourcing Trends in the Engine Manufacturer Sector?
The engine manufacturing sector is experiencing transformative shifts driven by global economic factors, technological advancements, and changing buyer preferences. Notably, the push for electrification is reshaping market dynamics, with a growing demand for electric and hybrid engines. Buyers from regions such as Africa, South America, the Middle East, and Europe should be aware that this transition is not merely technological but also strategic; companies are investing in R&D to create more efficient, eco-friendly products that meet regulatory demands and consumer expectations.
Another significant trend is the increased integration of Industry 4.0 technologies in manufacturing processes. Automation, artificial intelligence, and IoT are being utilized to enhance production efficiency and supply chain management. For B2B buyers, understanding these technologies can lead to better sourcing decisions, allowing for real-time data analytics and improved inventory management. Furthermore, the rise of digital platforms for procurement is streamlining the sourcing process, enabling buyers to access a wider range of suppliers and products globally.
As international trade dynamics evolve, buyers must also consider geopolitical factors that may influence sourcing strategies. Tariffs, trade agreements, and local regulations can impact the costs and availability of engine components. Therefore, B2B buyers should conduct thorough market research and engage with local suppliers to mitigate risks associated with global sourcing.
How Is Sustainability Shaping Sourcing Practices in the Engine Manufacturer Sector?
Sustainability has become a cornerstone of sourcing strategies in the engine manufacturing sector. As environmental concerns escalate, companies are increasingly prioritizing ethical sourcing practices that minimize ecological impact. This shift is particularly relevant for buyers in regions like Europe and the Middle East, where regulatory frameworks are stringent and consumer demand for green products is high.
Ethical supply chains not only contribute to sustainability but also enhance brand reputation. B2B buyers are encouraged to seek suppliers who demonstrate a commitment to environmental stewardship through certifications such as ISO 14001, which focuses on effective environmental management systems. Additionally, sourcing materials with lower carbon footprints, such as recycled metals and bio-based plastics, can significantly reduce the overall environmental impact of engine production.
Moreover, the importance of transparency in the supply chain cannot be overstated. Buyers should demand visibility into their suppliers’ sourcing practices, ensuring that materials are ethically obtained and that labor practices comply with international standards. This not only fosters trust but also aligns with the growing consumer expectation for corporate social responsibility.
What Is the Historical Context of the Engine Manufacturing Sector?
The evolution of the engine manufacturing sector is marked by significant technological advancements and market adaptations. Beginning in the late 19th century, the industry saw the introduction of the internal combustion engine, which revolutionized transportation and machinery. Over the decades, advancements in materials science and manufacturing processes have enabled the production of more powerful and efficient engines.
In recent years, the sector has shifted focus towards sustainability and innovation, driven by both consumer demand and regulatory pressures. The rise of electric vehicles (EVs) and hybrid technologies illustrates this evolution, with manufacturers now investing heavily in R&D to remain competitive. Understanding this historical context is crucial for B2B buyers, as it highlights the industry’s trajectory and informs future sourcing decisions that align with emerging trends and technologies.
Frequently Asked Questions (FAQs) for B2B Buyers of engine manufacturer
-
How do I select the right engine manufacturer for my business needs?
Choosing the right engine manufacturer involves evaluating several factors, including quality certifications, production capacity, and customization options. Assess the manufacturer’s experience in your specific industry, such as automotive, marine, or industrial applications. Request references and case studies from previous clients to understand their reliability and service quality. Additionally, visiting the manufacturing facility, if possible, can provide insights into their processes and capabilities. -
What are the key considerations for international shipping of engines?
When arranging international shipping for engines, consider logistics partners’ expertise in handling heavy machinery and compliance with local regulations. Evaluate shipping costs, delivery times, and customs clearance procedures. It’s essential to ensure that the engines are packed securely to prevent damage during transit. Understanding the Incoterms (International Commercial Terms) applicable to your transaction will also help clarify responsibilities regarding shipping, insurance, and customs duties. -
What are the minimum order quantities (MOQ) for engines from manufacturers?
Minimum order quantities (MOQ) can vary significantly between manufacturers and depend on factors such as production capabilities and materials used. Some manufacturers may have a flexible MOQ based on the specific engine type or customization requirements. It’s advisable to communicate your needs directly with manufacturers to negotiate the best terms, particularly if you are a new business or looking to make smaller initial orders. -
What payment terms should I expect when sourcing engines internationally?
Payment terms can vary widely among engine manufacturers and may include options such as upfront deposits, letters of credit, or payment upon delivery. Common practice is to negotiate terms that protect both parties, such as a 30% deposit with the balance due before shipment. Ensure that all payment arrangements are documented in the contract to avoid disputes. Consider using secure payment methods that offer buyer protection, especially in international transactions. -
How do I ensure quality assurance when purchasing engines?
To ensure quality assurance, request detailed documentation of the manufacturing process, including quality control measures and compliance with international standards (e.g., ISO certifications). Consider arranging for third-party inspections at various production stages. Additionally, reviewing warranty and service agreements can provide insights into the manufacturer’s commitment to quality and after-sales support. -
What customization options are typically available for engines?
Many engine manufacturers offer customization options to meet specific performance or application needs. Customizations can include variations in power output, fuel type, size, and additional features such as emission controls. Discuss your requirements with the manufacturer early in the sourcing process to explore available options and any implications for pricing and lead times. -
How can I vet potential engine suppliers effectively?
Vetting potential engine suppliers involves conducting thorough research into their reputation, financial stability, and production capabilities. Look for online reviews, industry certifications, and customer testimonials. Request samples or prototypes to evaluate product quality firsthand. Additionally, attending industry trade shows or networking events can provide opportunities to meet manufacturers and assess their offerings in person. -
What are the common challenges faced when sourcing engines from international manufacturers?
Common challenges include language barriers, differing regulatory standards, and potential delays in shipping or customs clearance. Cultural differences may also impact communication and business practices. To mitigate these issues, establish clear lines of communication, work with local partners or representatives when necessary, and conduct due diligence on the manufacturer’s compliance with your country’s regulations. Consider using trade finance solutions to ease cash flow concerns during the sourcing process.
Important Disclaimer & Terms of Use
⚠️ Important Disclaimer
The information provided in this guide, including content regarding manufacturers, technical specifications, and market analysis, is for informational and educational purposes only. It does not constitute professional procurement advice, financial advice, or legal advice.
While we have made every effort to ensure the accuracy and timeliness of the information, we are not responsible for any errors, omissions, or outdated information. Market conditions, company details, and technical standards are subject to change.
B2B buyers must conduct their own independent and thorough due diligence before making any purchasing decisions. This includes contacting suppliers directly, verifying certifications, requesting samples, and seeking professional consultation. The risk of relying on any information in this guide is borne solely by the reader.
Strategic Sourcing Conclusion and Outlook for engine manufacturer
In the rapidly evolving landscape of engine manufacturing, strategic sourcing has emerged as a crucial element for businesses aiming to enhance efficiency and reduce costs. By prioritizing long-term partnerships with reliable suppliers, companies can secure high-quality components while also benefiting from the latest technological advancements. This approach is especially pertinent for international B2B buyers from regions such as Africa, South America, the Middle East, and Europe, where diverse market demands require tailored sourcing strategies.
What are the key advantages of strategic sourcing for B2B buyers in engine manufacturing? By implementing a systematic sourcing process, organizations can identify and engage with suppliers who not only meet their quality standards but also align with their sustainability goals. This is particularly vital in today’s market, where environmental considerations are increasingly influencing purchasing decisions.
Looking ahead, the global engine manufacturing industry is poised for significant transformation driven by innovation and sustainability. B2B buyers are encouraged to embrace strategic sourcing as a proactive measure to stay competitive. By cultivating relationships with suppliers who share a commitment to excellence and environmental responsibility, businesses can position themselves for success in an increasingly interconnected world. Now is the time to rethink sourcing strategies and invest in partnerships that will drive growth and sustainability.