Discover Top Filter Paper Suppliers: A Complete Buyer’s Guide (2025)
Introduction: Navigating the Global Market for filter paper supplier
In an increasingly interconnected world, sourcing the right filter paper supplier can be a daunting challenge for international B2B buyers, especially those navigating diverse markets in Africa, South America, the Middle East, and Europe. With varying quality standards, compliance regulations, and supplier capabilities, making an informed decision is crucial. This guide is designed to demystify the complexities of the global filter paper market, offering insights into types of filter paper, their various applications, and essential criteria for supplier vetting.
Understanding the myriad of options available—from qualitative to quantitative filter papers—will empower buyers to select products that align with their specific industry needs. Furthermore, we will delve into the cost structures associated with filter paper procurement, providing actionable strategies to negotiate favorable terms without compromising on quality.
This comprehensive resource not only equips B2B buyers with the knowledge to make informed purchasing decisions but also enhances their ability to build sustainable partnerships with reliable suppliers. Whether you are operating in Poland, the UK, or any other region, our insights will guide you through the nuances of sourcing filter paper, ensuring that your organization remains competitive and compliant in today’s global marketplace.
Understanding filter paper supplier Types and Variations
Type Name | Key Distinguishing Features | Primary B2B Applications | Brief Pros & Cons for Buyers |
---|---|---|---|
Qualitative Filter Paper | High purity, designed for qualitative analysis | Laboratories, environmental testing | Pros: Accurate results; Cons: Higher cost |
Quantitative Filter Paper | Designed for precise measurements, retains solids | Chemical analysis, pharmaceuticals | Pros: High precision; Cons: Limited use |
Ashless Filter Paper | Low ash content, ideal for sensitive applications | Food and beverage, pharmaceuticals | Pros: Reduces contamination; Cons: Fragile |
Glass Fiber Filter Paper | High flow rate, durable, and resistant to chemicals | Water filtration, industrial processes | Pros: Efficient and durable; Cons: More expensive |
Cellulose Filter Paper | Made from cellulose fibers, versatile and cost-effective | General laboratory use, educational purposes | Pros: Affordable; Cons: Not suitable for all chemicals |
What are the characteristics and suitability of Qualitative Filter Paper?
Qualitative filter paper is designed primarily for applications requiring high purity and clarity. It is commonly used in laboratories and environmental testing, where the accuracy of results is paramount. Buyers should consider the specific grades available, as they can vary in thickness and pore size, affecting filtration speed and capacity. While qualitative papers provide reliable results, their higher cost may be a drawback for budget-conscious buyers.
How does Quantitative Filter Paper differ in application?
Quantitative filter paper is engineered for precise measurements and is often used in chemical analysis and pharmaceutical applications. This type of filter paper is designed to retain solids, making it essential for applications where accurate mass measurements are required. Buyers should ensure they select the appropriate grade based on the specific analytical methods employed. The main disadvantage is that its specialized nature can limit its use in other applications, making it less versatile than other types.
What makes Ashless Filter Paper a preferred choice in certain industries?
Ashless filter paper is characterized by its low ash content, which makes it ideal for sensitive applications like food and beverage processing, as well as pharmaceuticals. This type of filter paper minimizes contamination risks, ensuring that the final product meets stringent quality standards. However, buyers should be aware that ashless filter papers can be more fragile, requiring careful handling during use. This trade-off between purity and durability is an important consideration for B2B buyers.
When should Glass Fiber Filter Paper be utilized?
Glass fiber filter paper is known for its high flow rate and durability, making it suitable for demanding applications such as water filtration and various industrial processes. Its chemical resistance allows it to be used in environments that would degrade other types of filter paper. While glass fiber filters are efficient, they tend to be more expensive, which may deter some buyers. It is crucial for businesses to weigh the cost against the performance benefits for their specific applications.
Why is Cellulose Filter Paper widely used in laboratories?
Cellulose filter paper is made from natural cellulose fibers, making it a versatile and cost-effective option for general laboratory use and educational purposes. It is suitable for a wide range of applications, from simple filtration tasks to more complex analytical processes. Although it is affordable, buyers should note that cellulose filter paper may not be suitable for all chemical applications, particularly those involving aggressive solvents. Understanding the chemical compatibility is essential for effective use.
Related Video: How Billion Tons Of Paper Made in Factory – Wood Harvesting And Processing – Paper Factory
Key Industrial Applications of filter paper supplier
Industry/Sector | Specific Application of Filter Paper Supplier | Value/Benefit for the Business | Key Sourcing Considerations for this Application |
---|---|---|---|
Pharmaceutical | Drug Filtration and Purification | Ensures high purity levels, critical for safety and compliance. | Quality certifications (e.g., ISO, FDA), compatibility with solvents. |
Food and Beverage | Beverage Clarification | Improves product quality and shelf life by removing impurities. | Food-grade certifications, pore size specifications, and bulk purchasing options. |
Environmental Testing | Water Quality Analysis | Facilitates accurate testing for contaminants, aiding regulatory compliance. | Environmental certifications, availability of various filter grades, and consistency in supply. |
Laboratory Research | Sample Preparation and Analysis | Enhances analytical accuracy and reproducibility in experiments. | Technical support for custom solutions, compatibility with various solvents, and rapid delivery options. |
Chemical Manufacturing | Chemical Filtration and Separation | Increases process efficiency and product purity in chemical processes. | Chemical compatibility, durability under specific conditions, and cost-effectiveness for bulk orders. |
How is Filter Paper Used in the Pharmaceutical Industry?
In the pharmaceutical sector, filter paper is critical for drug filtration and purification processes. Suppliers provide high-quality filter paper that meets stringent standards for purity, ensuring that contaminants do not compromise drug safety and efficacy. International buyers should prioritize suppliers with relevant certifications such as ISO and FDA compliance. Additionally, compatibility with various solvents is essential to ensure effective filtration during production.
What Role Does Filter Paper Play in the Food and Beverage Sector?
Filter paper is widely used in the food and beverage industry for beverage clarification, such as in the production of juices and wines. By removing particulates and impurities, filter paper enhances the final product’s quality and extends its shelf life. For B2B buyers, it is crucial to source food-grade certified filter paper that meets specific pore size requirements. Bulk purchasing can also provide cost savings while ensuring a consistent supply for production needs.
How is Filter Paper Essential for Environmental Testing?
In environmental testing, filter paper is vital for water quality analysis, enabling laboratories to accurately test for contaminants. This application is crucial for regulatory compliance and environmental protection. Buyers from Africa, South America, the Middle East, and Europe should consider suppliers that offer a range of filter grades and possess environmental certifications. Consistency in supply is also critical, as testing schedules can be affected by availability.
Why is Filter Paper Important for Laboratory Research?
Laboratory research relies on filter paper for sample preparation and analysis, where it enhances the accuracy and reproducibility of experiments. Filter paper aids in the separation of solids from liquids, ensuring that results are not skewed by impurities. B2B buyers should seek suppliers who provide technical support for custom filter solutions and ensure compatibility with various solvents. Rapid delivery options can also mitigate delays in research timelines.
How Does Filter Paper Benefit Chemical Manufacturing?
In chemical manufacturing, filter paper is utilized for chemical filtration and separation processes, which are essential for maintaining product purity and process efficiency. The right filter paper can significantly impact production outcomes, making it vital for buyers to focus on chemical compatibility and durability under specific processing conditions. Cost-effectiveness is another consideration, especially for businesses looking to order in bulk to streamline production processes.
Related Video: Uses and Gratifications Theory – UGT
3 Common User Pain Points for ‘filter paper supplier’ & Their Solutions
Scenario 1: Inconsistent Quality Across Different Suppliers
The Problem:
B2B buyers often encounter significant challenges when sourcing filter paper, particularly regarding quality consistency. For companies in industries such as pharmaceuticals or food processing, even minor variations in filter paper performance can lead to costly production delays or compromised product integrity. Buyers may find that one batch from a particular supplier performs well, while the next batch falls short of expectations, leading to frustration and potential liability issues.
The Solution:
To mitigate this issue, it’s essential to establish a robust supplier evaluation process. Start by identifying suppliers with certifications relevant to your industry, such as ISO 9001 for quality management systems. Request product samples from multiple suppliers and conduct comparative testing to ensure the filter paper meets your specifications consistently. Additionally, maintaining open lines of communication with your supplier can help address quality issues proactively. Consider setting up a quality assurance protocol that includes regular audits and performance reviews to ensure ongoing compliance with your standards.
Scenario 2: Difficulty in Finding the Right Specifications for Filter Paper
The Problem:
B2B buyers often struggle to navigate the technical specifications of filter paper, which can vary significantly based on the intended application. For example, a laboratory in South America may require specific pore sizes and thicknesses for precision filtration, while a manufacturing plant in Europe may need a different set of characteristics for bulk processing. This lack of clarity can lead to the selection of inappropriate filter paper, resulting in inefficiencies or product failures.
The Solution:
To address this challenge, buyers should invest time in understanding the specific filtration needs of their applications. This can be achieved by collaborating closely with engineers or technical staff to define the required parameters, such as particle retention size, flow rate, and chemical compatibility. It’s also beneficial to engage with filter paper suppliers who offer technical support and can provide guidance on the best products for your unique needs. Creating a detailed specification document that outlines all necessary characteristics can streamline the sourcing process and reduce the likelihood of errors.
Scenario 3: Long Lead Times and Supply Chain Disruptions
The Problem:
Global supply chain disruptions have become a common concern, particularly for international B2B buyers. Delays in shipping or unexpected shortages can significantly impact production schedules, especially in regions like Africa and the Middle East where logistics can be more challenging. Buyers may find themselves in a situation where they cannot procure essential filter paper in a timely manner, leading to halted operations and financial losses.
The Solution:
To combat supply chain issues, buyers should diversify their supplier base. Instead of relying on a single source, consider establishing relationships with multiple suppliers across different regions. This approach not only increases the chances of finding available stock but also allows for competitive pricing. Additionally, implementing a just-in-time inventory system can help manage stock levels more efficiently, reducing the risk of running out of critical materials. Lastly, maintaining regular communication with suppliers about lead times and potential disruptions can help buyers plan better and mitigate the impact of unexpected delays.
Strategic Material Selection Guide for filter paper supplier
When selecting filter paper for industrial applications, the choice of material is crucial for ensuring optimal performance and compliance with industry standards. Below, we analyze four common materials used in filter paper production, highlighting their properties, advantages, disadvantages, and considerations for international B2B buyers, particularly from regions such as Africa, South America, the Middle East, and Europe.
What Are the Key Properties of Cellulose Filter Paper?
Cellulose filter paper is one of the most widely used materials due to its excellent filtration capabilities and cost-effectiveness. It typically operates well under moderate temperatures and pressures, making it suitable for a variety of applications, including laboratory testing and industrial processes. Cellulose is also biodegradable, aligning with increasing environmental regulations.
Pros & Cons: The primary advantage of cellulose filter paper is its affordability and availability. However, it may not withstand harsh chemical environments, which can lead to degradation over time. Additionally, cellulose filter paper may have limited compatibility with certain solvents, which can restrict its use in specific applications.
Impact on Application: Cellulose is ideal for aqueous solutions but may not perform well with organic solvents. Buyers in Europe, particularly in countries like Poland and the UK, should ensure that cellulose filter paper meets relevant standards such as ISO 9071 for filtration efficiency.
How Does Polypropylene Filter Paper Compare?
Polypropylene filter paper is recognized for its excellent chemical resistance and durability. It can withstand higher temperatures and pressures compared to cellulose, making it suitable for more demanding applications, such as in the pharmaceutical and chemical industries.
Pros & Cons: The key advantage of polypropylene is its resistance to a wide range of chemicals, allowing for versatile applications. However, it tends to be more expensive than cellulose and may require more complex manufacturing processes. This can impact lead times and availability, particularly for international buyers.
Impact on Application: Polypropylene is compatible with a variety of solvents and is often used in applications requiring high purity. Buyers from the Middle East and Africa should consider local regulations regarding plastic materials, as compliance with environmental standards is becoming increasingly stringent.
What Are the Benefits of Glass Fiber Filter Paper?
Glass fiber filter paper is known for its high strength and thermal stability, making it suitable for high-temperature applications. It is often used in industrial processes that require rapid filtration and high flow rates.
Pros & Cons: The primary advantage of glass fiber is its ability to perform under extreme conditions, including high temperatures and aggressive chemicals. However, it is generally more expensive and may not be as readily available in all markets. Additionally, glass fibers can pose health risks if inhaled, necessitating careful handling.
Impact on Application: Glass fiber is particularly effective for air and liquid filtration in industrial settings. Buyers in South America should be aware of local safety regulations when sourcing glass fiber products, as compliance with health and safety standards is critical.
Why Consider Synthetic Filter Paper?
Synthetic filter paper, often made from polyester or nylon, offers unique properties such as high tensile strength and excellent chemical resistance. These materials can be engineered to meet specific filtration needs, making them highly versatile.
Pros & Cons: The main advantage of synthetic filter paper is its tailored performance for specialized applications, including those requiring high filtration efficiency. However, the cost can be significantly higher than traditional materials, which may deter some buyers. Additionally, synthetic materials may not be biodegradable, raising environmental concerns.
Impact on Application: Synthetic filter papers are suitable for a wide range of applications, including food and beverage processing, where contamination control is paramount. Buyers from Europe should ensure that synthetic materials comply with food safety standards, such as those set by the European Food Safety Authority (EFSA).
Summary Table of Filter Paper Materials
Material | Typical Use Case for filter paper supplier | Key Advantage | Key Disadvantage/Limitation | Relative Cost (Low/Med/High) |
---|---|---|---|---|
Cellulose | Laboratory testing, general filtration | Cost-effective and widely available | Limited chemical resistance | Low |
Polypropylene | Chemical and pharmaceutical applications | Excellent chemical resistance | Higher cost and complex manufacturing | Med |
Glass Fiber | Industrial air and liquid filtration | High strength and thermal stability | Expensive and health risks from fibers | High |
Synthetic | Food processing, specialized filtration | Tailored performance for specific needs | Higher cost and potential environmental concerns | High |
This strategic material selection guide serves as a valuable resource for international B2B buyers, enabling them to make informed decisions based on their specific application needs and regional compliance requirements.
In-depth Look: Manufacturing Processes and Quality Assurance for filter paper supplier
What Are the Main Stages in the Manufacturing Process of Filter Paper?
The manufacturing process for filter paper involves several critical stages that ensure the final product meets the necessary specifications for various applications. Understanding these stages can help B2B buyers make informed decisions when selecting suppliers.
-
Material Preparation: The first step involves sourcing high-quality raw materials, typically cellulose fibers. Suppliers often choose specific grades of wood pulp or recycled paper, depending on the desired properties of the filter paper. The quality of the raw material directly influences the filtration efficiency and the strength of the final product.
-
Forming: In this stage, the prepared fibers are mixed with water to create a slurry. This slurry is then spread onto a moving screen or mesh to form a wet sheet. The sheet’s thickness and density can be adjusted based on the application requirements, such as air or liquid filtration. Advanced techniques, such as wet-laid or dry-laid processes, may be employed to enhance the paper’s performance.
-
Pressing: Once the sheet is formed, it is pressed to remove excess water. This step also helps to bond the fibers together, increasing the paper’s strength. The pressing process may involve the use of heated rollers to achieve the desired moisture content and density.
-
Drying: The pressed sheets are then dried, often using heated air or infrared dryers. This step is crucial for achieving the correct moisture level, which is essential for the filter paper’s performance. Proper drying also prevents mold growth and degradation of the material.
-
Finishing: After drying, the filter paper undergoes finishing processes, which may include calendaring (smoothing the surface), cutting to size, and packaging. Some suppliers may also apply coatings or treatments to enhance specific properties, such as chemical resistance or hydrophobicity.
How Is Quality Assurance Implemented in Filter Paper Manufacturing?
Quality assurance (QA) is vital in ensuring that filter paper meets international standards and customer specifications. Here are key components of the QA process that B2B buyers should consider:
-
International Standards and Certifications: Many filter paper suppliers adhere to international quality standards such as ISO 9001, which outlines requirements for a quality management system. Additional certifications like CE mark or API (American Petroleum Institute) are also relevant, particularly for suppliers targeting specific industries. B2B buyers should verify these certifications as they indicate a supplier’s commitment to quality.
-
Quality Control Checkpoints: The quality control process typically includes several checkpoints:
– Incoming Quality Control (IQC): Raw materials are inspected upon arrival to ensure they meet predefined specifications.
– In-Process Quality Control (IPQC): Continuous monitoring during the manufacturing process helps identify defects early. This may involve checking parameters such as thickness, tensile strength, and filtration efficiency.
– Final Quality Control (FQC): After production, the finished product undergoes rigorous testing to ensure it meets all quality standards before shipment. -
Common Testing Methods: Various testing methods are utilized to assess the quality of filter paper, including:
– Gravimetric Analysis: Measures the weight of the paper to determine its density and thickness.
– Filtration Tests: Assess the paper’s efficiency in filtering specific particles or substances.
– Chemical Resistance Tests: Evaluate how the filter paper reacts to different chemicals, important for applications in laboratories and industrial settings.
How Can B2B Buyers Verify Supplier Quality Control?
For international B2B buyers, especially from regions like Africa, South America, the Middle East, and Europe, verifying a supplier’s quality control processes is essential. Here are actionable steps:
-
Conduct Supplier Audits: Regular audits can provide insights into a supplier’s manufacturing and quality assurance processes. Buyers should inquire about the frequency of these audits and whether they are conducted by internal teams or third-party organizations.
-
Request Quality Assurance Reports: Suppliers should be willing to provide documentation of their QA processes, including records of quality checks, test results, and compliance with international standards. This transparency is crucial for building trust.
-
Engage Third-Party Inspectors: Utilizing independent inspection services can help validate a supplier’s claims about quality. These inspectors can conduct on-site evaluations and testing, offering an unbiased assessment of the supplier’s capabilities.
What Are the Nuances of Quality Control and Certification for International Buyers?
Understanding the nuances of quality control and certification is critical for B2B buyers navigating the international landscape. Here are some considerations:
-
Regional Standards: Different regions may have varying standards for filter paper quality. For example, European buyers may prioritize compliance with EU regulations, while buyers in the Middle East might focus on adherence to local standards. It’s essential to clarify these requirements with potential suppliers.
-
Supply Chain Transparency: In some regions, especially in Africa and South America, supply chain transparency can be a concern. Buyers should inquire about the sourcing of raw materials and the ethical practices of the supplier, as these factors can affect product quality and reliability.
-
Language and Cultural Barriers: When dealing with suppliers from different regions, language and cultural differences can impact communication regarding quality expectations. Buyers should ensure that they have clear and concise documentation and consider working with a local intermediary if necessary.
Conclusion
By understanding the manufacturing processes and quality assurance practices in filter paper production, B2B buyers can make informed decisions when selecting suppliers. Emphasizing international standards and effective quality control measures will enhance the reliability and performance of the filter paper, ultimately benefiting their operations.
Practical Sourcing Guide: A Step-by-Step Checklist for ‘filter paper supplier’
Introduction
Sourcing filter paper from reliable suppliers is a critical step for businesses in various industries, including pharmaceuticals, food and beverage, and environmental testing. This checklist is designed to guide international B2B buyers, particularly from Africa, South America, the Middle East, and Europe, through the essential steps of selecting a filter paper supplier that meets their specific needs.
Step 1: Define Your Technical Specifications
Clearly outlining your technical requirements is the first step in the sourcing process. Specify the type of filter paper needed, including pore size, thickness, and material composition. This ensures that potential suppliers can meet your specific application needs, which is crucial for maintaining product quality and compliance with industry standards.
Step 2: Conduct Market Research on Suppliers
Researching potential suppliers is essential for making informed decisions. Utilize online platforms, trade shows, and industry directories to identify manufacturers and distributors specializing in filter paper. Pay attention to their market reputation, customer reviews, and the range of products offered to gauge their capabilities and reliability.
Step 3: Evaluate Potential Suppliers
Before making a commitment, it’s crucial to thoroughly vet potential suppliers. Request company profiles, product catalogs, and case studies, and ask for references from clients in similar industries or regions. This step helps ensure that the supplier has a proven track record and can deliver on their promises.
Step 4: Verify Supplier Certifications
Supplier certifications can be a strong indicator of quality and compliance. Check if the supplier holds relevant certifications such as ISO 9001 for quality management systems or any industry-specific certifications. These credentials demonstrate a commitment to quality and can help mitigate risks in your supply chain.
Step 5: Request Samples for Testing
Obtaining samples is a critical step to verify the quality of the filter paper. Ask suppliers for samples that match your specifications to evaluate their performance in real-world applications. This allows you to test for compatibility with your processes and ensures that the product meets your expectations.
Step 6: Discuss Terms and Conditions
Once you have narrowed down your options, engage in discussions about pricing, lead times, and payment terms. Be clear about your expectations and any potential penalties for delays or quality issues. Establishing mutually beneficial terms can help foster a positive long-term relationship with the supplier.
Step 7: Evaluate Logistics and Delivery Options
Understanding the logistics involved in sourcing filter paper is vital for timely procurement. Discuss shipping methods, delivery timelines, and customs requirements with your suppliers. This step ensures that you can plan your inventory effectively and minimize disruptions in your operations.
By following this practical sourcing checklist, B2B buyers can streamline their procurement process and make informed decisions when selecting a filter paper supplier that aligns with their business needs and operational goals.
Comprehensive Cost and Pricing Analysis for filter paper supplier Sourcing
When sourcing filter paper, understanding the comprehensive cost structure is crucial for international B2B buyers. Each component of the cost structure contributes to the final pricing, and being aware of these elements can aid in making informed purchasing decisions.
What Are the Key Cost Components in Filter Paper Manufacturing?
-
Materials: The primary raw materials for filter paper include cellulose fibers, fillers, and additives. The quality and type of these materials directly impact the price. Higher-grade materials that offer superior filtration properties will typically command a higher cost.
-
Labor: Labor costs vary significantly by region. In countries with higher labor costs, such as those in Western Europe, the overall price of filter paper may increase. Conversely, suppliers in regions with lower labor costs may offer more competitive pricing.
-
Manufacturing Overhead: This includes costs related to facility operations, utilities, and equipment maintenance. Efficient manufacturing processes can reduce overhead costs, allowing suppliers to offer better prices.
-
Tooling: The initial investment in tools and machinery for producing specific types of filter paper can be substantial. Suppliers that have already invested in advanced tooling may be able to produce at a lower cost per unit, especially for high-volume orders.
-
Quality Control (QC): Ensuring product quality through rigorous testing and quality assurance processes incurs additional costs. Suppliers that adhere to stringent quality standards may charge more, but this can lead to better performance and reliability.
-
Logistics: Shipping and handling costs can fluctuate based on distance, mode of transport, and customs duties. Buyers should consider these factors, especially when sourcing from international suppliers.
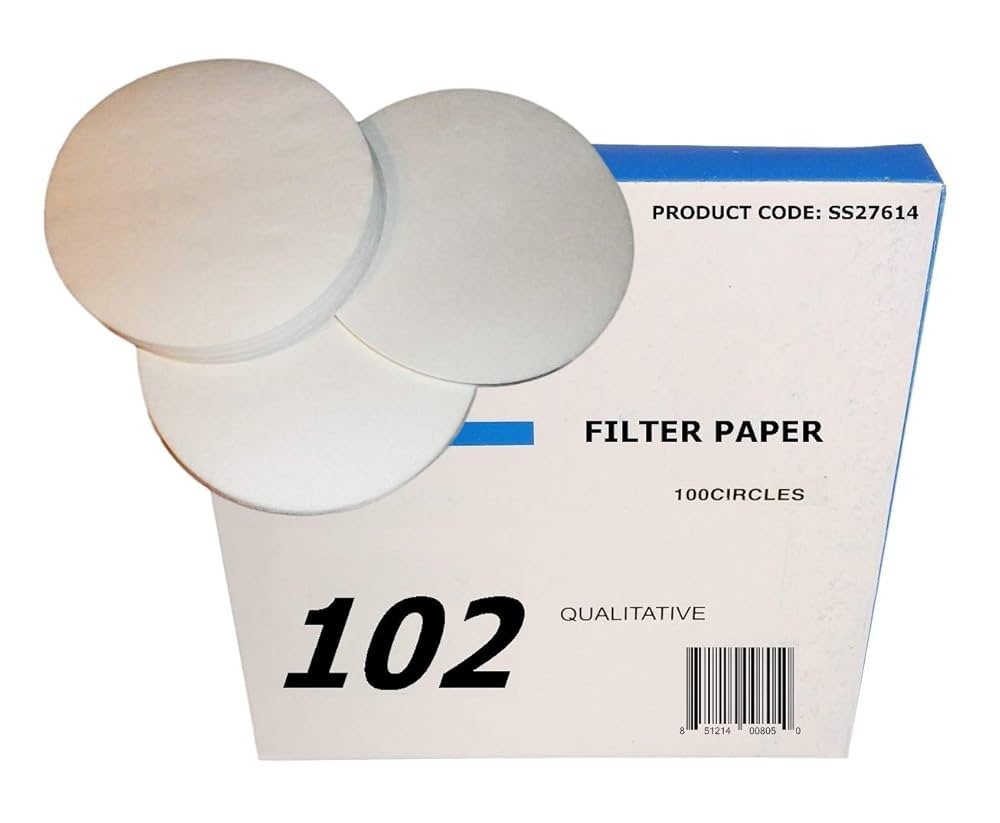
A stock image related to filter paper supplier.
- Margin: Suppliers typically add a profit margin to their costs, which can vary based on market conditions and competition. Understanding the typical margins in your target market can help in negotiating better prices.
How Do Price Influencers Affect Filter Paper Costs?
-
Volume and Minimum Order Quantity (MOQ): Larger orders often lead to lower per-unit costs. Buyers should negotiate for better pricing on bulk orders, which can significantly reduce overall expenses.
-
Specifications and Customization: Custom specifications can increase costs due to the need for specialized materials or manufacturing processes. Buyers should weigh the necessity of customization against the potential increase in price.
-
Material Quality and Certifications: Higher quality materials and certifications (e.g., ISO, FDA compliance) can raise costs. Buyers should assess whether the additional expense aligns with their operational needs.
-
Supplier Factors: The reputation and reliability of a supplier can influence pricing. Established suppliers may charge a premium for their proven track record, while newer entrants may offer lower prices to gain market share.
-
Incoterms: The terms of shipping (e.g., FOB, CIF) can affect the overall cost structure. Understanding Incoterms is essential for buyers to calculate total landed costs accurately.
What Are the Best Practices for Negotiating Filter Paper Prices?
-
Leverage Volume Discounts: When possible, consolidate orders to meet or exceed the MOQ to benefit from lower pricing.
-
Evaluate Total Cost of Ownership (TCO): Consider not just the purchase price but also the costs associated with shipping, handling, and potential wastage. A slightly higher upfront cost may yield savings over time.
-
Conduct Market Research: Understanding regional pricing norms can empower buyers during negotiations. This knowledge can also help in identifying fair pricing ranges.
-
Build Relationships with Suppliers: Establishing long-term partnerships can lead to better pricing and terms, as suppliers may be more willing to negotiate with trusted clients.
-
Request Detailed Quotes: Ask suppliers for breakdowns of their pricing to better understand cost components and identify areas for negotiation.
Conclusion
In summary, a comprehensive understanding of the cost structure and pricing influences is essential for international B2B buyers sourcing filter paper. By considering the aforementioned factors and employing strategic negotiation techniques, buyers can optimize their sourcing processes and achieve better value for their investments. Always remember to request indicative prices, as they can fluctuate based on market conditions and supplier capabilities.
Alternatives Analysis: Comparing filter paper supplier With Other Solutions
Understanding the Importance of Evaluating Alternatives for Filter Paper Suppliers
When selecting a filter paper supplier, it’s crucial for international B2B buyers to consider various alternatives that may fulfill similar roles in filtration processes. Different solutions can offer unique advantages depending on specific requirements such as performance, cost, and ease of implementation. By comparing filter paper with viable alternatives, buyers can make informed decisions that align with their operational goals.
Comparison of Filter Paper Supplier with Alternative Solutions
Comparison Aspect | Filter Paper Supplier | Membrane Filtration | Centrifugation |
---|---|---|---|
Performance | High filtration efficiency, suitable for various applications | Excellent for fine particle separation | Effective for large volume processing |
Cost | Moderate, depending on quality | Generally higher due to equipment costs | High initial investment but cost-effective for large volumes |
Ease of Implementation | Easy to integrate into existing processes | Requires specialized training and equipment | Complex setup and operation |
Maintenance | Low maintenance, replace as needed | Regular maintenance required for equipment | Moderate maintenance, regular checks needed |
Best Use Case | Ideal for laboratory and small-scale applications | Best for sterile applications and microfiltration | Suitable for large-scale processing in chemical industries |
What Are the Advantages and Disadvantages of Membrane Filtration?
Membrane filtration is a sophisticated alternative that employs semi-permeable membranes to separate particles from liquids. This method excels in applications requiring high purity, such as pharmaceuticals and food processing. However, the cost of membrane filtration systems can be significant, particularly for initial installation and maintenance. While the performance is superior in terms of particle size reduction, the complexity of the system may require specialized training for personnel, making it less accessible for some businesses.
How Does Centrifugation Compare in Filtration Processes?
Centrifugation uses centrifugal force to separate components based on density differences, making it a robust option for large-scale processing. This method is highly efficient for separating solids from liquids and is commonly used in industries such as chemical manufacturing and wastewater treatment. However, the initial investment for centrifuge equipment can be high, and the operation may require skilled personnel to manage the system effectively. Despite these drawbacks, centrifugation can be a cost-effective solution for operations that process large volumes regularly.
Conclusion: How to Choose the Right Solution for Your Needs
In deciding between a filter paper supplier and its alternatives, B2B buyers must assess their specific operational requirements. If cost is a significant factor and the application is less complex, filter paper may be the most practical choice. For industries demanding high purity and sterile conditions, membrane filtration could be worth the investment. Conversely, for large-scale operations where volume is critical, centrifugation might offer the best long-term value. By carefully evaluating the performance, cost, and ease of implementation of each option, international buyers can select the most suitable filtration solution for their needs.
Essential Technical Properties and Trade Terminology for filter paper supplier
What Are the Key Technical Properties of Filter Paper?
Understanding the technical properties of filter paper is crucial for B2B buyers to ensure they select the right product for their applications. Here are some essential specifications:
1. Material Grade
Material grade refers to the quality and type of fibers used in the production of filter paper. Common materials include cellulose, glass fiber, and synthetic polymers. The grade impacts the filter’s strength, chemical resistance, and filtration efficiency. For instance, high-grade cellulose filters are suitable for general laboratory use, while glass fiber filters are preferred for high-temperature applications. Buyers should match the material grade with their specific operational needs to ensure optimal performance.
2. Filtration Efficiency
Filtration efficiency indicates the ability of the filter paper to remove particulates from liquids or gases. This property is often expressed in terms of retention rate, which measures the percentage of particles retained by the filter. High filtration efficiency is critical for applications in laboratories, pharmaceuticals, and food processing where purity is essential. Buyers should seek detailed specifications on retention rates to ensure compliance with industry standards.
3. Thickness and Weight
Thickness and weight are vital specifications that influence the filter’s performance and handling. Thicker filters generally have a higher capacity for retaining particulates but may also reduce flow rates. Conversely, thinner filters allow for quicker flow but might not capture larger particles effectively. Understanding the balance between thickness, weight, and application requirements helps buyers choose the right filter for their processes.
4. Chemical Compatibility
Chemical compatibility refers to the filter’s ability to withstand various solvents, acids, and bases without degradation. This property is particularly important for industries such as chemicals and pharmaceuticals, where aggressive substances are frequently used. Buyers should inquire about the chemical compatibility of the filter paper with the specific chemicals they will be using to prevent premature failure or contamination.
5. Tolerance Levels
Tolerance levels indicate the acceptable variations in the filter’s dimensions and performance characteristics. This specification is crucial for ensuring that the filter paper fits properly in equipment and performs as expected. Understanding tolerance levels helps buyers avoid issues related to improper fit, which can lead to inefficiencies and increased operational costs.
What Are Common Trade Terms Used in the Filter Paper Industry?
Familiarity with industry-specific terminology can enhance communication and negotiation processes for B2B buyers. Here are some common trade terms:
1. OEM (Original Equipment Manufacturer)
An OEM is a company that produces parts or equipment that may be marketed by another manufacturer. In the context of filter paper, an OEM may provide custom solutions tailored to specific machinery or applications. Buyers should consider OEM options when looking for specialized filter papers that fit their unique requirements.
2. MOQ (Minimum Order Quantity)
MOQ refers to the smallest number of units that a supplier is willing to sell. Understanding the MOQ is essential for buyers to manage inventory effectively and control costs. Suppliers often set MOQs based on production efficiency and material costs, so negotiating favorable terms can lead to significant savings.
3. RFQ (Request for Quotation)
An RFQ is a document that buyers send to suppliers to request pricing for specific products. It typically includes details such as quantities, specifications, and delivery timelines. Utilizing an RFQ process allows buyers to compare offers from multiple suppliers, ensuring they receive the best value for their investments.
4. Incoterms (International Commercial Terms)
Incoterms are internationally recognized rules that define the responsibilities of buyers and sellers in the shipping process. They clarify who is responsible for shipping costs, insurance, and risk during transport. Understanding Incoterms is vital for international buyers to avoid misunderstandings and ensure smooth transactions.
5. Lead Time
Lead time refers to the amount of time it takes from placing an order to receiving the product. This metric is crucial for planning and inventory management. Buyers should always clarify lead times with suppliers to ensure they can meet their operational deadlines.
By grasping these technical properties and trade terms, international B2B buyers can make informed decisions when sourcing filter paper, ultimately leading to more efficient operations and successful partnerships.
Navigating Market Dynamics and Sourcing Trends in the filter paper supplier Sector
What Are the Current Market Dynamics and Key Trends in the Filter Paper Supplier Sector?
The filter paper supplier sector is undergoing significant transformations driven by various global factors. Increased demand for high-quality filtration solutions in industries such as pharmaceuticals, food and beverage, and environmental testing is leading to a surge in production capabilities. Notably, the rise of automation and digital technologies is enhancing operational efficiency and product quality. International B2B buyers, particularly from Africa, South America, the Middle East, and Europe, should be aware of these advancements as they can greatly influence sourcing decisions.
Emerging trends in B2B technology are also shaping the landscape of filter paper suppliers. The adoption of e-commerce platforms is streamlining procurement processes, allowing buyers to access a broader range of suppliers and products. Additionally, data analytics and AI are being leveraged for demand forecasting and inventory management, enabling companies to optimize their supply chains. Buyers in regions like Poland and the UK are encouraged to explore these technologies, as they offer significant cost savings and improved service delivery.
Another key dynamic is the shift towards customization. Many suppliers are now offering tailored solutions to meet specific industry needs, which is particularly relevant for B2B buyers looking for unique filtration applications. Understanding these market dynamics is essential for navigating the complexities of sourcing filter paper effectively.
How Is Sustainability Influencing Sourcing Decisions in the Filter Paper Sector?
The importance of sustainability and ethical sourcing has become a pivotal concern for B2B buyers in the filter paper supplier sector. As environmental regulations tighten globally, companies are increasingly expected to demonstrate a commitment to sustainable practices. This includes sourcing materials that have minimal environmental impact and ensuring that production processes are energy-efficient.
Buyers should prioritize suppliers that provide certifications such as FSC (Forest Stewardship Council) and PEFC (Programme for the Endorsement of Forest Certification). These certifications indicate that the paper products are sourced from sustainably managed forests, which is crucial for maintaining a responsible supply chain. Moreover, the use of biodegradable and recyclable materials is gaining traction, offering additional options for companies aiming to reduce their ecological footprint.
Ethical sourcing not only enhances brand reputation but also meets the growing consumer demand for transparency and responsibility. B2B buyers from regions such as Africa and the Middle East should consider these factors when selecting suppliers, as aligning with sustainable practices can lead to long-term partnerships and competitive advantages in the market.
How Has the Filter Paper Supplier Sector Evolved Over Time?
The evolution of the filter paper supplier sector reflects broader changes in industrial practices and consumer demands. Initially, filter paper was primarily used in laboratory settings, but its applications have expanded significantly due to advancements in technology and manufacturing processes. The introduction of synthetic fibers and innovative production techniques has enhanced the performance of filter papers, making them suitable for various applications, including industrial filtration and environmental testing.
In recent years, the sector has seen increased globalization, with suppliers from different regions competing in the international market. This has allowed B2B buyers to access a wider array of products and pricing options. Additionally, the emphasis on sustainability has reshaped supplier relationships, with a growing number of companies adopting eco-friendly practices in response to consumer pressure and regulatory requirements. Understanding this historical context is vital for buyers aiming to make informed decisions in today’s competitive and environmentally conscious landscape.
Frequently Asked Questions (FAQs) for B2B Buyers of filter paper supplier
-
How do I choose the right filter paper supplier for my business needs?
Choosing the right filter paper supplier involves evaluating several factors, including product quality, range of specifications, and industry expertise. Start by assessing the supplier’s certifications and compliance with international standards. Look for suppliers with a proven track record in your specific industry, whether it’s pharmaceuticals, food and beverage, or environmental testing. Also, consider their ability to provide customization options and their responsiveness to inquiries. Engaging in direct communication and requesting samples can help you gauge their reliability and product suitability. -
What is the minimum order quantity (MOQ) for filter paper products?
Minimum order quantities (MOQ) can vary significantly among filter paper suppliers, influenced by factors such as the type of filter paper and the supplier’s production capabilities. Typically, MOQs range from 500 to 1,000 sheets, but some suppliers may offer smaller quantities for specific products or custom orders. It’s crucial to discuss your requirements directly with the supplier to negotiate MOQs that align with your purchasing strategy, especially if you’re a smaller buyer or looking to test new products. -
What are the common payment terms for international filter paper suppliers?
Payment terms can vary widely based on the supplier’s policies and the buyer’s location. Common arrangements include advance payment, net 30, or net 60 terms. For international transactions, options like letters of credit or escrow services may be employed for added security. It’s advisable to clarify payment terms upfront and consider factors such as currency exchange rates and transaction fees, which can impact the overall cost. Establishing clear terms can help avoid misunderstandings and foster a smoother purchasing process. -
How can I ensure the quality of filter paper products before making a purchase?
To ensure product quality, request samples from potential suppliers to evaluate their filter paper’s performance against your specific requirements. Additionally, inquire about the supplier’s quality assurance processes, including testing methods and compliance with international standards like ISO. Certifications such as FDA approval or REACH compliance can also indicate a supplier’s commitment to quality. Engaging in third-party audits or reviews can provide further assurance of the supplier’s capabilities. -
What customization options are available for filter paper products?
Many filter paper suppliers offer customization options to meet specific application needs. This can include variations in thickness, pore size, and material composition. When discussing customization, clearly outline your requirements, such as the desired filtration efficiency and intended use. Some suppliers may also provide tailored packaging solutions or branding options, which can be beneficial for marketing purposes. Be proactive in exploring these options to ensure the final product aligns with your operational needs.
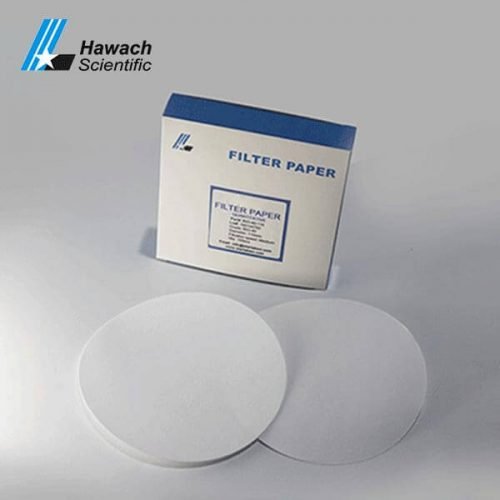
A stock image related to filter paper supplier.
-
What logistics considerations should I keep in mind when sourcing filter paper internationally?
Logistics play a critical role in international sourcing, particularly for perishable or sensitive items like filter paper. Consider factors such as shipping methods, lead times, and customs regulations specific to your country. Working with suppliers that have experience in international shipping can streamline the process. Additionally, inquire about the supplier’s ability to handle potential delays and their policies on damaged or lost shipments. Building a solid logistics plan will help mitigate risks and ensure timely delivery. -
How do I vet potential filter paper suppliers for reliability?
Vetting potential suppliers involves a thorough review of their business history, client testimonials, and industry reputation. Utilize platforms like LinkedIn or industry-specific directories to gather insights and reviews. Request references from existing clients to understand their experiences. Additionally, assess the supplier’s responsiveness and willingness to provide detailed information during your inquiry process. A reliable supplier should demonstrate transparency and a commitment to customer service, which can be critical for long-term partnerships. -
What should I know about compliance and certifications when sourcing filter paper?
Compliance and certifications are crucial when sourcing filter paper, especially for industries like pharmaceuticals and food production. Familiarize yourself with the relevant standards that apply to your sector, such as ISO, FDA, or EU regulations. Ensure that your chosen supplier has the necessary certifications and can provide documentation to verify compliance. This not only guarantees product safety but also helps avoid potential legal issues. Conducting thorough due diligence in this area will safeguard your business and maintain product integrity.
Important Disclaimer & Terms of Use
⚠️ Important Disclaimer
The information provided in this guide, including content regarding manufacturers, technical specifications, and market analysis, is for informational and educational purposes only. It does not constitute professional procurement advice, financial advice, or legal advice.
While we have made every effort to ensure the accuracy and timeliness of the information, we are not responsible for any errors, omissions, or outdated information. Market conditions, company details, and technical standards are subject to change.
B2B buyers must conduct their own independent and thorough due diligence before making any purchasing decisions. This includes contacting suppliers directly, verifying certifications, requesting samples, and seeking professional consultation. The risk of relying on any information in this guide is borne solely by the reader.
Strategic Sourcing Conclusion and Outlook for filter paper supplier
As the global market for filter paper continues to evolve, international B2B buyers must prioritize strategic sourcing to ensure they secure the best quality products at competitive prices. The key takeaways highlight the importance of understanding supplier capabilities, market trends, and the specific needs of different industries. By leveraging supplier partnerships and focusing on quality assurance, businesses can enhance their operational efficiency while reducing costs.
How Can International B2B Buyers Optimize Their Filter Paper Sourcing Strategy?
Investing in long-term relationships with filter paper suppliers can lead to improved service levels and access to innovative products. Buyers from Africa, South America, the Middle East, and Europe should assess suppliers not just on price, but also on their ability to meet regulatory standards, sustainability practices, and delivery reliability.
What Should Buyers Anticipate in the Future of Filter Paper Supply?
Looking ahead, the demand for specialized filter paper is expected to rise, particularly in industries such as pharmaceuticals, food and beverage, and environmental monitoring. This presents an opportunity for businesses to enhance their sourcing strategies by identifying suppliers who can adapt to changing market needs.
In conclusion, as you navigate the complexities of sourcing filter paper, remain proactive in your approach. Engage with suppliers who are aligned with your values and operational goals, and stay informed on industry trends to maximize your procurement success. Embrace this opportunity to refine your sourcing strategies and drive business growth in an increasingly competitive landscape.