Discover Top Fire Engine Manufacturers: Your Sourcing Guide (2025)
Introduction: Navigating the Global Market for fire engine manufacturer
As the global demand for fire safety equipment rises, navigating the complex landscape of fire engine manufacturers presents both challenges and opportunities for international B2B buyers. Sourcing reliable fire engines that meet rigorous safety standards while also considering budget constraints can be daunting, particularly for stakeholders in regions like Africa, South America, the Middle East, and Europe. This guide is meticulously designed to address these challenges by providing a comprehensive overview of the fire engine manufacturing market, encompassing various types of fire engines, their applications, and essential supplier vetting processes.
Understanding the intricacies of fire engine procurement is crucial for making informed purchasing decisions. Throughout this guide, we will delve into the different categories of fire engines available, from urban to rural models, and explore their specific functionalities. We will also discuss key factors influencing costs and provide actionable insights on how to evaluate suppliers effectively.
By equipping international buyers with the knowledge necessary to navigate this market, this guide empowers you to secure high-quality fire engines that meet your operational needs while ensuring compliance with local regulations. Whether you are a procurement officer in Egypt, a safety officer in Italy, or a fleet manager in Brazil, our insights will help streamline your purchasing process and enhance your organization’s fire safety capabilities.
Understanding fire engine manufacturer Types and Variations
Type Name | Key Distinguishing Features | Primary B2B Applications | Brief Pros & Cons for Buyers |
---|---|---|---|
Pumper Fire Engines | Equipped with a water pump and storage tanks for firefighting. | Urban firefighting, industrial sites | Pros: High water delivery rate; versatile. Cons: Requires maintenance; may be costly. |
Aerial Fire Engines | Features extendable ladders or platforms for high-rise access. | High-rise buildings, large events | Pros: Access to elevated structures; specialized. Cons: Limited maneuverability; higher price. |
Wildland Fire Engines | Designed for off-road capabilities and rugged terrains. | Rural areas, wildland firefighting | Pros: Excellent mobility; lightweight. Cons: Limited water capacity; less suited for urban areas. |
Rescue Fire Engines | Focused on emergency medical services and rescue operations. | Urban emergencies, disaster response | Pros: Multi-functional; equipped for various emergencies. Cons: Less firefighting capacity; specialized training needed. |
Fire Tankers | Primarily used for transporting water to remote locations. | Rural firefighting, infrastructure support | Pros: High water capacity; essential for remote areas. Cons: Limited firefighting capabilities; slower response time. |
What Are the Characteristics of Pumper Fire Engines?
Pumper fire engines are the backbone of urban firefighting. They are equipped with powerful water pumps and storage tanks that allow for rapid water delivery to extinguish fires. These engines are suitable for a variety of B2B applications, particularly in urban settings and industrial sites where swift response is crucial. When purchasing, consider the engine’s pump capacity, water tank size, and maintenance requirements, as these factors directly impact operational efficiency.
How Do Aerial Fire Engines Support Firefighting Operations?
Aerial fire engines are distinguished by their extendable ladders or platforms, enabling access to high-rise buildings and elevated structures. These vehicles are essential for firefighting in urban environments, especially during large events or in densely populated areas. Buyers should evaluate the ladder reach, platform capacity, and stability features to ensure they meet specific operational needs, as these factors can significantly affect performance in emergency situations.
Why Are Wildland Fire Engines Essential for Rural Firefighting?
Wildland fire engines are specifically designed for rugged terrains, making them ideal for rural firefighting scenarios. Their lightweight construction and off-road capabilities allow them to navigate challenging landscapes effectively. When considering a purchase, B2B buyers should assess the vehicle’s water capacity, maneuverability, and compatibility with firefighting equipment, as these elements are crucial for successful operations in less accessible areas.
What Are the Key Features of Rescue Fire Engines?
Rescue fire engines focus on emergency medical services and rescue operations, making them versatile assets for urban emergencies and disaster response scenarios. These vehicles are equipped with specialized tools and medical equipment, which allow them to handle various emergencies beyond firefighting. Buyers should consider the engine’s space for equipment, response time, and training requirements for personnel, as these factors will influence the effectiveness of rescue operations.
How Do Fire Tankers Contribute to Firefighting Efforts?
Fire tankers are primarily designed for transporting large volumes of water to remote locations where hydrants are not available. They play a critical role in supporting firefighting efforts in rural areas and infrastructure projects. When evaluating fire tankers, B2B buyers should focus on water capacity, pump systems, and the vehicle’s overall durability, as these attributes are essential for ensuring a reliable water supply during critical firefighting operations.
Related Video: Variations In Construction Projects Explained
Key Industrial Applications of fire engine manufacturer
Industry/Sector | Specific Application of Fire Engine Manufacturer | Value/Benefit for the Business | Key Sourcing Considerations for this Application |
---|---|---|---|
Oil & Gas | Emergency Response Vehicles for Oil Fields | Quick mobilization reduces downtime and enhances safety | Compliance with industry standards and certifications |
Mining | Fire Suppression Systems for Mining Operations | Protects equipment and personnel from fire hazards | Customization options for rugged environments |
Manufacturing | On-Site Fire Safety Equipment for Factories | Minimizes risk of production halts due to fire | Maintenance support and availability of spare parts |
Agriculture | Fire Control Units for Agricultural Land Management | Prevents large-scale losses from wildfires | Adaptability to local fire regulations and conditions |
Construction | Fire Safety Solutions for Construction Sites | Ensures compliance with safety regulations | Robustness and mobility for various terrains |
How Are Fire Engines Utilized in the Oil & Gas Sector?
In the oil and gas industry, fire engine manufacturers provide specialized emergency response vehicles designed for rapid deployment in remote locations. These vehicles are equipped with advanced firefighting technology, including high-capacity water pumps and foam systems. The primary challenge addressed is the high risk of fire due to volatile materials, making quick response critical. Buyers in this sector must ensure that the vehicles comply with stringent safety regulations and are built to withstand harsh environmental conditions typical of oil fields, especially in regions like the Middle East and Africa.
What Are the Applications of Fire Suppression Systems in Mining?
Mining operations utilize fire suppression systems manufactured for high-risk environments where flammable materials and equipment are prevalent. These systems are vital for protecting both personnel and expensive machinery from fire hazards. The key requirement for buyers is the ability to customize systems that fit specific site layouts and operational needs. Additionally, international buyers must consider the availability of local support and maintenance services, particularly in remote mining regions of South America and Africa.
How Do Manufacturing Facilities Benefit from On-Site Fire Safety Equipment?
In manufacturing settings, on-site fire safety equipment is crucial for preventing fires that could disrupt production. Fire engine manufacturers provide tailored solutions, including mobile fire units that can be quickly deployed in case of an emergency. This capability minimizes downtime and ensures employee safety, which is paramount for maintaining operational efficiency. Buyers must evaluate the reliability of the equipment and the manufacturer’s ability to provide ongoing maintenance and spare parts, especially in Europe where regulations are stringent.
Why Are Fire Control Units Important for Agriculture?
Fire control units are essential for managing fire risks in agricultural settings, particularly in areas prone to wildfires. These units help prevent significant losses by enabling farmers to respond swiftly to fire outbreaks. Buyers must ensure that these units are adaptable to local regulations and can operate effectively under varying climatic conditions. For international buyers, understanding the regional fire management practices in places like South America and Africa is crucial for effective implementation.
What Fire Safety Solutions Are Needed for Construction Sites?
Construction sites require robust fire safety solutions to comply with safety regulations and protect workers. Fire engine manufacturers supply various products, including mobile fire units and fixed suppression systems. The primary challenge is ensuring these solutions are effective across diverse terrains and project scales. Buyers should prioritize sourcing from manufacturers that offer durable equipment and can provide training for site personnel, particularly in regions like Italy where construction standards are rigorously enforced.
Related Video: FANUC Industrial Robots | AUDI Case Study
3 Common User Pain Points for ‘fire engine manufacturer’ & Their Solutions
Scenario 1: Navigating Compliance and Safety Standards in Fire Engine Procurement
The Problem: B2B buyers from regions such as Africa and the Middle East often face the daunting challenge of navigating complex local and international safety regulations when purchasing fire engines. Compliance with stringent safety standards is crucial, yet the specifications can vary widely between countries. Buyers may struggle to find manufacturers that meet these requirements, leading to potential delays in procurement and increased costs.
The Solution: To effectively address this challenge, international buyers should conduct thorough research on the relevant safety and compliance standards specific to their region. This includes understanding both local regulations and international guidelines set by organizations such as NFPA (National Fire Protection Association) or ISO (International Organization for Standardization). Engaging with a fire engine manufacturer that has a strong reputation for compliance can mitigate risks. Buyers should also request detailed documentation and certifications from manufacturers to ensure all safety standards are met. Establishing a direct line of communication with the manufacturer’s compliance team can provide clarity and expedite the procurement process, allowing for a smoother acquisition experience.
Scenario 2: The Challenge of Customization for Diverse Operational Needs
The Problem: Buyers from South America and Europe often encounter difficulties when seeking fire engines that can be customized to meet unique operational requirements. Different municipalities may have specific needs based on local geography, climate, and the types of emergencies they frequently face. This lack of customization can lead to purchasing vehicles that do not fully serve their intended purpose, resulting in operational inefficiencies.
The Solution: To overcome this hurdle, buyers should engage in early discussions with fire engine manufacturers about their customization capabilities. Clearly outline the specific needs and challenges faced by your local fire services, and inquire about previous projects that involved similar customizations. Manufacturers who are willing to collaborate on design and functionality will not only provide a better product but also foster a long-term partnership. Utilizing simulation tools and prototypes can also help visualize how the customizations will perform in real-world scenarios, ensuring that the final product is tailored to the buyer’s precise needs.
Scenario 3: Addressing Maintenance and Service Support Concerns
The Problem: One of the most pressing issues for B2B buyers is ensuring that there is adequate maintenance and service support after the purchase of fire engines. In regions like Africa and parts of the Middle East, access to parts and skilled technicians can be limited, which may lead to prolonged downtimes and increased operational costs. Buyers may feel anxious about their investment if they cannot secure reliable post-sale support.
The Solution: To tackle this concern, it is crucial for buyers to prioritize manufacturers that offer comprehensive service packages, including training for local technicians and readily available spare parts. Before making a purchase, inquire about the manufacturer’s service history and their approach to after-sales support. Establishing a service level agreement (SLA) can also ensure timely response times for maintenance and repairs. Additionally, consider negotiating a warranty that covers parts and labor for an extended period. This proactive approach not only protects the investment but also enhances the overall reliability of the fire engines in service.
Strategic Material Selection Guide for fire engine manufacturer
What Are the Key Materials Used in Fire Engine Manufacturing?
When selecting materials for fire engines, manufacturers must consider properties such as temperature resistance, corrosion resistance, and overall durability. The choice of material directly affects the performance, lifespan, and safety of the fire engine, making it crucial for international B2B buyers to understand the implications of each option.
How Does Aluminum Benefit Fire Engine Construction?
Aluminum is a lightweight metal known for its excellent strength-to-weight ratio. It boasts a high corrosion resistance, making it suitable for environments exposed to water and chemicals. Fire engines made from aluminum can endure high temperatures, which is essential for fire-fighting applications.
Pros: Aluminum is durable and can be easily molded into complex shapes, which is beneficial for intricate designs. Its lightweight nature enhances fuel efficiency and maneuverability.
Cons: However, aluminum can be more expensive than steel, and its manufacturing process may require specialized techniques, which could complicate production for some manufacturers.
Impact on Application: Aluminum is particularly compatible with various fire-fighting media, including water and foam agents, ensuring that the material does not degrade over time.
Considerations for International Buyers: Buyers from regions like Europe may need to adhere to specific standards such as EN 573 for aluminum alloys. In Africa and South America, understanding local regulations regarding material sourcing and environmental impact is vital.
What Role Does Steel Play in Fire Engine Manufacturing?
Steel, particularly high-strength low-alloy (HSLA) steel, is another common material used in fire engine construction. Known for its robustness and impact resistance, steel is often utilized in the chassis and structural components of fire engines.
Pros: Steel offers excellent durability and is relatively cost-effective. Its high tensile strength makes it suitable for heavy-duty applications, ensuring that the fire engine can withstand extreme conditions.
Cons: On the downside, steel is heavier than aluminum, which may affect fuel efficiency. Additionally, it requires protective coatings to prevent corrosion, which can add to manufacturing complexity and costs.
Impact on Application: Steel is compatible with a wide range of firefighting equipment and can endure high-pressure situations, making it ideal for structural integrity.
Considerations for International Buyers: Compliance with standards such as ASTM A572 or DIN EN 10025 is essential for buyers in Europe and the Middle East. African and South American buyers should consider local sourcing of steel to reduce costs and improve logistics.
Why Is Composite Material Gaining Popularity in Fire Engine Design?
Composite materials, particularly fiberglass and carbon fiber, are increasingly used in fire engine manufacturing due to their lightweight and high-strength properties. These materials can be molded into complex shapes, offering design flexibility.
Pros: Composites are highly resistant to corrosion and can withstand high temperatures, making them suitable for various fire-fighting applications. Their lightweight nature can significantly reduce the overall weight of the fire engine.
Cons: However, composites can be more expensive than traditional materials like steel and aluminum. Additionally, their manufacturing processes can be complex, requiring specialized knowledge and equipment.
Impact on Application: Composites are particularly effective in components exposed to harsh environmental conditions, such as water tanks and body panels.
Considerations for International Buyers: Buyers in Europe may need to comply with EN 13121 standards for composite materials. In regions like Africa and South America, understanding the local market for composites and potential sourcing challenges is essential.
How Does Stainless Steel Compare in Fire Engine Applications?
Stainless steel is often used for components that require high corrosion resistance, such as water tanks and piping systems. Its ability to withstand extreme temperatures and pressures makes it a reliable choice for fire engine manufacturers.
Pros: Stainless steel is incredibly durable and requires minimal maintenance, which is beneficial for long-term use in demanding environments.
Cons: The primary drawback is its higher cost compared to carbon steel and aluminum, which can impact the overall budget for fire engine production.
Impact on Application: Stainless steel is compatible with various firefighting agents and can maintain structural integrity under high-pressure conditions.
Considerations for International Buyers: Buyers should ensure compliance with standards such as ASTM A240 for stainless steel. In regions like the Middle East, understanding local sourcing and supply chain logistics is crucial for timely delivery.
Summary Table of Material Selection for Fire Engine Manufacturing
Material | Typical Use Case for fire engine manufacturer | Key Advantage | Key Disadvantage/Limitation | Relative Cost (Low/Med/High) |
---|---|---|---|---|
Aluminum | Body panels, structural components | Lightweight, corrosion resistant | Higher cost, complex manufacturing | High |
Steel | Chassis, structural components | Durable, cost-effective | Heavier, requires corrosion protection | Medium |
Composite | Water tanks, body panels | Lightweight, high strength | Higher cost, complex manufacturing | High |
Stainless Steel | Water tanks, piping systems | High corrosion resistance | Higher cost compared to carbon steel | High |
In-depth Look: Manufacturing Processes and Quality Assurance for fire engine manufacturer
What Are the Key Manufacturing Processes for Fire Engine Production?
The manufacturing of fire engines is a complex and multi-faceted process, comprising several key stages that ensure the final product meets stringent safety and performance standards. Understanding these stages is crucial for international B2B buyers looking to procure reliable fire engines.
Material Preparation: How Are Raw Materials Selected and Processed?
The first step in fire engine manufacturing involves the careful selection and preparation of raw materials. Common materials include high-strength steel, aluminum alloys, and composite materials for lightweight and durability. Buyers should inquire about the material sourcing practices of potential suppliers, including certifications and traceability.
Once selected, materials undergo processes such as cutting, welding, and machining to achieve the desired specifications. Advanced techniques like laser cutting and CNC machining are often employed for precision, ensuring that components fit together seamlessly during assembly.
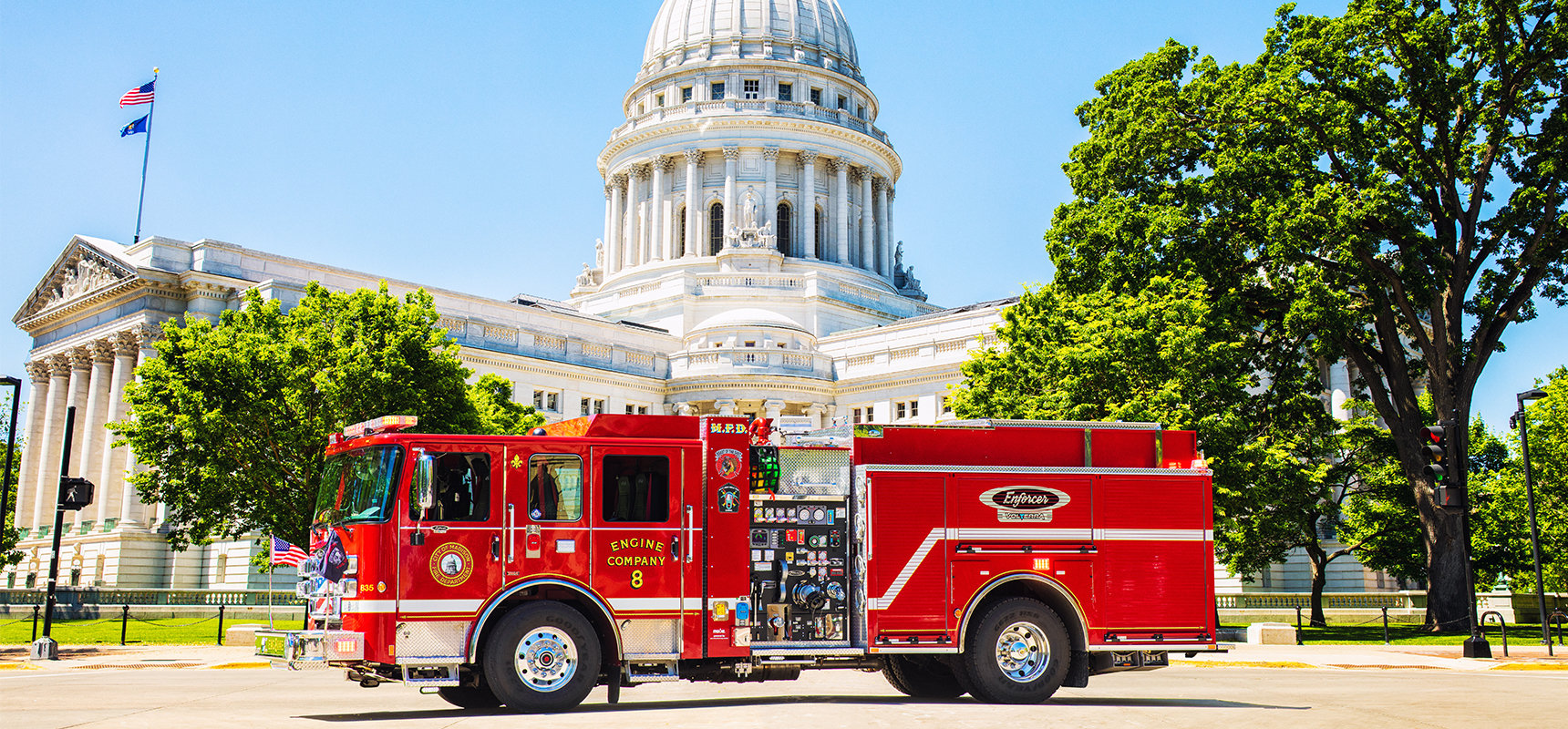
A stock image related to fire engine manufacturer.
What Techniques Are Used in the Forming Stage of Fire Engine Manufacturing?
The forming stage focuses on shaping the prepared materials into specific components such as chassis, body, and tank structures. Techniques such as stamping, bending, and extrusion are frequently used to create complex shapes necessary for functionality and aesthetics.
Innovative forming technologies, including hydroforming and 3D printing, are becoming more prevalent, allowing manufacturers to produce intricate designs that optimize weight and strength. International buyers should evaluate suppliers’ capabilities in these advanced techniques to ensure they can meet modern design requirements.
How Is Assembly Conducted in Fire Engine Manufacturing?
Assembly is a critical stage where all components come together to form the complete fire engine. This process typically involves multiple sub-assemblies, including the engine, pump, water tank, and control systems. Coordinated assembly lines facilitate efficient workflows, often integrating robotics for precision tasks.
For buyers, it’s essential to understand the assembly process’s layout and efficiency. Inquire about the use of lean manufacturing principles, which can minimize waste and reduce lead times, ultimately benefiting procurement schedules.
What Quality Assurance Standards Are Essential for Fire Engine Manufacturers?
Quality assurance (QA) is paramount in the fire engine manufacturing process. Compliance with international standards such as ISO 9001 ensures that manufacturers maintain consistent quality management systems. This is particularly crucial for buyers from regions like Africa and South America, where quality assurance may vary significantly.
In addition to ISO standards, fire engines must meet industry-specific certifications such as CE marking in Europe and API standards in the United States. These certifications guarantee that the fire engines are safe and effective for use in emergency situations.
What Are the Key Quality Control Checkpoints in Fire Engine Manufacturing?
Quality control (QC) involves systematic checks throughout the manufacturing process to ensure that each component meets predefined standards. Key QC checkpoints include:
-
Incoming Quality Control (IQC): This stage involves inspecting raw materials and components before they enter the production line. Buyers should request detailed IQC reports from suppliers to verify material quality.
-
In-Process Quality Control (IPQC): Conducted during the manufacturing process, IPQC ensures that each stage of production adheres to quality standards. This may involve regular inspections and testing of components as they are assembled.
-
Final Quality Control (FQC): The final inspection before the fire engine is shipped involves comprehensive testing of the complete unit. This includes performance tests, safety checks, and compliance verifications.
B2B buyers should ask suppliers about their QC protocols and request access to inspection reports to ensure transparency and accountability.
What Common Testing Methods Are Used in Fire Engine Manufacturing?
Testing is integral to ensuring that fire engines meet safety and performance specifications. Common testing methods include:
-
Functional Testing: Evaluating the operational capabilities of the fire engine, including pump performance and engine diagnostics.
-
Pressure Testing: Ensuring that the water tank and pump systems can withstand operational pressures without leakage.
-
Crash Testing: Assessing the fire engine’s structural integrity and safety features under simulated collision conditions.
-
Environmental Testing: Verifying that the fire engine can operate effectively in various climatic conditions, which is particularly relevant for buyers in diverse environments across Africa and the Middle East.
How Can B2B Buyers Verify Supplier Quality Control Practices?
For international B2B buyers, verifying a supplier’s quality control practices is essential to mitigate risks associated with procurement. Here are actionable steps to consider:
-
Conduct Supplier Audits: Regular audits of potential suppliers can provide insights into their manufacturing processes and QA protocols. This includes reviewing documentation, observing manufacturing practices, and assessing compliance with international standards.
-
Request Quality Reports: Suppliers should provide comprehensive quality reports, including IQC, IPQC, and FQC findings. These documents are crucial for understanding the consistency of quality across batches.
-
Engage Third-Party Inspection Services: Utilizing independent inspection agencies can offer an unbiased assessment of a supplier’s quality assurance processes. This can be particularly beneficial for buyers unfamiliar with local manufacturing standards.
What Are the Quality Control Nuances for International Buyers?
When engaging with fire engine manufacturers, international buyers must navigate several quality control nuances:
-
Understanding Regional Standards: Familiarize yourself with the quality standards relevant to your region. For example, CE certification is essential for buyers in Europe, while specific certifications may apply in Middle Eastern countries.
-
Cultural Differences in Quality Perception: Different regions may have varying expectations regarding quality. Buyers from Africa and South America should communicate their quality expectations clearly to avoid misunderstandings.
-
Logistics and Supply Chain Considerations: Quality assurance does not end at the factory. Ensure that logistics and transportation methods maintain the integrity of the fire engines during shipping.
By comprehensively understanding the manufacturing processes and quality assurance measures involved in fire engine production, B2B buyers can make informed decisions that align with their operational needs and safety standards.
Practical Sourcing Guide: A Step-by-Step Checklist for ‘fire engine manufacturer’
Introduction
Navigating the procurement process for fire engines can be daunting, particularly for international B2B buyers from diverse regions like Africa, South America, the Middle East, and Europe. This guide aims to provide a clear and actionable checklist that ensures you make informed decisions throughout your sourcing journey. By following these steps, you can effectively identify reliable manufacturers, assess their capabilities, and secure the best solutions for your fire-fighting needs.
Step 1: Define Your Technical Specifications
Clearly outlining your technical specifications is the foundation of a successful procurement process. Consider factors such as the type of fire engine (e.g., pumper, aerial, or tanker), capacity requirements, and compliance with local regulations. This clarity helps you communicate effectively with potential suppliers and ensures that the products meet your operational needs.
- Identify the specific features required for your region, such as water tank size, pump capacity, and additional firefighting equipment.
- Research local regulations that may dictate design specifications or safety standards.
Step 2: Conduct Market Research for Fire Engine Manufacturers
Understanding the market landscape is essential before engaging with suppliers. Research manufacturers that specialize in fire engines and have a proven track record in your target regions. This step will help you identify potential suppliers who can meet your needs.
- Utilize industry reports, trade shows, and online directories to compile a list of manufacturers.
- Look for manufacturers with experience in your geographic region, as they will be familiar with local requirements and challenges.
Step 3: Evaluate Potential Suppliers
Before committing, it’s crucial to vet suppliers thoroughly. Request company profiles, case studies, and references from buyers in a similar industry or region. Don’t just rely on their website; look for third-party reviews and testimonials to gauge reliability.
- Assess their production capabilities, including technology used, workforce expertise, and quality control processes.
- Inquire about their experience in exporting to your region, which can impact shipping and compliance.
Step 4: Verify Supplier Certifications and Compliance
Ensuring that potential suppliers hold the necessary certifications is vital for maintaining safety and quality standards. Look for ISO certifications, compliance with local regulations, and any specific industry standards relevant to fire engines.
- Confirm that the supplier adheres to international safety standards, such as NFPA (National Fire Protection Association) guidelines.
- Ask for documentation that proves their compliance with local regulations in your country.
Step 5: Request Detailed Quotations
Once you’ve shortlisted suppliers, request detailed quotations that break down costs, including manufacturing, shipping, and any additional services. This will provide clarity on pricing and help you compare different suppliers effectively.
- Ensure the quotations include warranty information, delivery timelines, and payment terms.
- Analyze the total cost of ownership rather than just the initial purchase price, considering maintenance and operational costs.
Step 6: Negotiate Terms and Conditions
Negotiating favorable terms is crucial for securing a beneficial agreement. Discuss payment terms, delivery schedules, and post-sale support to ensure alignment with your operational needs.
- Be clear about your expectations for service and support, especially regarding spare parts and maintenance.
- Ensure that the contract includes provisions for any potential delays or issues that may arise during the procurement process.
Step 7: Finalize the Contract and Monitor Delivery
Once all terms are agreed upon, finalize the contract and monitor the delivery process closely. Ensure that the supplier adheres to the agreed timelines and specifications to mitigate risks.
- Establish clear communication channels for updates and potential issues during the delivery phase.
- Conduct an inspection upon delivery to verify that the fire engines meet your specified requirements and standards.
By following this step-by-step checklist, international B2B buyers can effectively navigate the complexities of sourcing fire engines, ensuring a successful procurement process that meets their specific needs.
Comprehensive Cost and Pricing Analysis for fire engine manufacturer Sourcing
Understanding the cost structure and pricing dynamics of fire engine manufacturing is crucial for international B2B buyers, particularly those operating in Africa, South America, the Middle East, and Europe. This section provides an in-depth analysis of the key cost components and price influencers, along with actionable buyer tips to optimize procurement strategies.
What Are the Key Cost Components in Fire Engine Manufacturing?
-
Materials: The most significant component of the cost structure is the raw materials used in fire engines. This includes metals, plastics, and specialized components such as pumps and hoses. Prices can fluctuate based on global supply chain conditions and local market availability, making it essential for buyers to stay informed about material trends.
-
Labor: Labor costs encompass the wages of skilled workers involved in the assembly and quality assurance processes. In regions like Europe, labor costs tend to be higher due to stringent labor laws and wage standards, while in some African and South American countries, the costs may be lower but come with varying skill levels.
-
Manufacturing Overhead: This includes indirect costs related to production, such as utilities, rent, and administrative expenses. Manufacturers often allocate these costs across production lines, impacting pricing strategies.
-
Tooling: Fire engine production often requires specialized tooling and machinery. The initial investment in these tools can significantly affect the overall pricing, particularly for custom-engineered solutions.
-
Quality Control (QC): Ensuring the safety and reliability of fire engines is paramount. Rigorous QC processes can add to production costs but are essential for compliance with international safety standards.
-
Logistics: The cost of transporting fire engines from the manufacturer to the buyer’s location can vary widely based on distance, shipping methods, and import duties. Buyers should factor these logistics costs into their total budget.
-
Margin: Manufacturers typically include a profit margin in their pricing. Understanding the average margin for fire engine manufacturers in different regions can provide leverage in negotiations.
How Do Price Influencers Impact Fire Engine Procurement?
-
Volume and Minimum Order Quantity (MOQ): Bulk purchases often result in lower per-unit costs. Buyers should assess their needs and negotiate MOQs to secure better pricing.
-
Specifications and Customization: Custom specifications can drive up costs due to the need for specialized materials and labor. Buyers should carefully evaluate whether customization is necessary for their operational needs.
-
Materials Quality and Certifications: Higher quality materials and certifications (such as ISO standards) may increase initial costs but can lead to long-term savings through reduced maintenance and increased reliability.
-
Supplier Factors: The reputation and reliability of suppliers can influence pricing. Established manufacturers with a track record of quality may charge more but can provide peace of mind and consistent service.
-
Incoterms: Understanding Incoterms is crucial for managing logistics costs and responsibilities. Buyers should clarify shipping terms to avoid unexpected charges.
What Buyer Tips Can Help Optimize Fire Engine Sourcing?
-
Negotiate Effectively: Engage in open discussions with suppliers about pricing structures. Leverage information about competitors and market conditions to negotiate better terms.
-
Focus on Cost-Efficiency: Evaluate the total cost of ownership rather than just the purchase price. Consider factors such as maintenance, fuel efficiency, and resale value in your analysis.
-
Research Pricing Nuances: Different regions may have unique pricing structures based on local regulations, import duties, and market competition. Understanding these nuances can provide a competitive edge.
-
Build Relationships with Suppliers: Establishing long-term partnerships with manufacturers can lead to better pricing, priority service, and more favorable terms over time.
-
Stay Informed on Market Trends: Regularly monitor industry trends, material prices, and technological advancements to make informed purchasing decisions.
Disclaimer on Indicative Prices
The pricing analysis provided here is indicative and subject to change based on market conditions, supplier negotiations, and regional economic factors. Buyers are encouraged to conduct thorough due diligence and seek multiple quotes to ensure competitive pricing.
Alternatives Analysis: Comparing fire engine manufacturer With Other Solutions
Introduction: What Are the Alternatives to Traditional Fire Engines?
When considering fire safety solutions, international B2B buyers must evaluate not only traditional fire engines but also alternative methods and technologies that may suit their specific needs. This analysis focuses on comparing fire engine manufacturers with two viable alternatives: fire suppression drones and mobile fire suppression systems. Each option offers unique advantages and potential drawbacks, making it crucial for buyers to assess which solution aligns best with their operational requirements and budget constraints.
Comparison Table of Fire Engine Manufacturer and Alternatives
Comparison Aspect | Fire Engine Manufacturer | Fire Suppression Drones | Mobile Fire Suppression Systems |
---|---|---|---|
Performance | High, designed for large-scale fires | Moderate, effective for targeted areas | High, versatile for various environments |
Cost | High initial investment | Moderate, lower than fire engines | Lower than fire engines, variable based on capacity |
Ease of Implementation | Complex, requires training and infrastructure | Easy to deploy, minimal setup | Moderate, requires some training but less than fire engines |
Maintenance | High, regular checks and repairs needed | Low, minimal maintenance required | Moderate, regular inspections needed |
Best Use Case | Large urban areas, industrial sites | Remote or hard-to-reach areas, quick response | Small to medium-sized fires, urban and rural settings |
What Are the Advantages and Disadvantages of Fire Suppression Drones?
Fire suppression drones represent a rapidly evolving technology that can provide targeted fire response, particularly in areas that are difficult to access. These drones can be equipped with water or fire retardants and are ideal for immediate deployment in emergency situations.
Pros:
– Quick Deployment: Drones can be deployed almost instantly and can reach areas that are otherwise inaccessible.
– Cost-Effective: Generally, they require a lower initial investment compared to traditional fire engines.
– Minimal Maintenance: Drones require less frequent maintenance, making them a cost-effective solution in the long term.
Cons:
– Limited Capacity: Drones typically have a lower payload capacity compared to fire engines, which can limit their effectiveness in large-scale fires.
– Weather Dependency: Their operational effectiveness can be hindered by adverse weather conditions.
How Do Mobile Fire Suppression Systems Compare?
Mobile fire suppression systems offer a flexible approach to fire management. These systems can be mounted on various vehicles, making them versatile for different operational needs, from urban to rural settings.
Pros:
– Versatility: They can be used in multiple environments, including construction sites, warehouses, and rural areas.
– Lower Cost: They are generally less expensive than traditional fire engines, making them accessible for smaller municipalities or businesses.
– Effective for Various Fire Types: They can be tailored to combat different types of fires, including chemical or electrical fires.
Cons:
– Training Required: While easier to implement than fire engines, personnel still need training to operate these systems effectively.
– Maintenance Needs: Although maintenance is less demanding than that of traditional fire engines, it is still necessary to ensure reliability.
Conclusion: How Can B2B Buyers Choose the Right Fire Safety Solution?
Selecting the right fire safety solution requires a thorough understanding of your specific needs and constraints. Buyers should consider factors such as the scale of operations, budgetary limitations, and the types of environments in which they operate. For large urban areas or industrial sites, traditional fire engines may be necessary. However, for remote locations or smaller operations, fire suppression drones or mobile fire suppression systems may provide adequate protection at a lower cost. By carefully analyzing these alternatives, B2B buyers can make informed decisions that enhance their fire safety capabilities.
Essential Technical Properties and Trade Terminology for fire engine manufacturer
What Are the Key Technical Properties of Fire Engines?
When selecting fire engines, understanding their technical specifications is crucial for B2B buyers. Here are some essential properties to consider:
1. Material Grade
The material grade of a fire engine refers to the quality and type of materials used in its construction, such as steel, aluminum, and composite materials. Higher-grade materials offer better durability and resistance to corrosion and wear, which is vital for vehicles that operate in harsh environments. B2B buyers should ensure that the material grade meets international standards to guarantee longevity and reliability.
2. Tolerance Levels
Tolerance levels indicate the permissible limits of variation in the dimensions of components. In fire engines, precise tolerances are critical for ensuring the proper fit and function of mechanical systems, such as the pump and chassis. Understanding tolerance specifications helps buyers assess the quality control processes of manufacturers and the overall performance reliability of the fire engine.
3. Pump Capacity
The pump capacity, measured in gallons per minute (GPM), is a key performance indicator for fire engines. It determines how quickly and effectively a fire engine can deliver water to extinguish fires. Buyers should evaluate the pump capacity in relation to the specific firefighting needs of their region, as higher capacity may be necessary in urban areas with high-rise buildings or in rural areas with limited water supply.
4. Engine Power Rating
Engine power rating, typically expressed in horsepower (HP), directly affects the fire engine’s performance, including acceleration, speed, and overall operational efficiency. A higher power rating enables the fire engine to navigate challenging terrains, which is particularly important in regions with diverse geographical landscapes. B2B buyers should consider the power rating in conjunction with fuel efficiency to ensure optimal operational costs.
5. Weight Distribution
Weight distribution refers to how the weight of the fire engine is balanced across its chassis. Proper weight distribution is essential for stability, especially when maneuvering on uneven surfaces or during emergency operations. Buyers should inquire about the design features that enhance weight distribution to ensure safe handling and effective performance in various conditions.
What Common Trade Terms Should B2B Buyers Know?
Understanding industry terminology can streamline communication and negotiation processes. Here are some common trade terms relevant to fire engine manufacturing:
1. OEM (Original Equipment Manufacturer)
An OEM is a company that produces parts or equipment that may be marketed by another manufacturer. In the fire engine industry, OEMs provide essential components such as pumps, hoses, and electronics. B2B buyers should verify the OEM status of parts to ensure quality and compatibility.
2. MOQ (Minimum Order Quantity)
MOQ refers to the minimum quantity of products that a supplier is willing to sell. For fire engine components, knowing the MOQ can help buyers plan their purchases effectively and avoid excess inventory costs. It is advisable to negotiate MOQs, especially when sourcing from international suppliers.
3. RFQ (Request for Quotation)
An RFQ is a document sent to suppliers to request pricing and terms for specific products or services. B2B buyers should prepare detailed RFQs that outline their requirements clearly, enabling suppliers to provide accurate quotes. This process is essential for budgeting and comparing options.
4. Incoterms (International Commercial Terms)
Incoterms are standardized trade terms that define the responsibilities of buyers and sellers in international transactions. Understanding Incoterms is critical for B2B buyers, as they dictate aspects such as shipping costs, delivery responsibilities, and risk transfer. Familiarity with these terms can prevent misunderstandings and disputes during the procurement process.
How Can These Technical Properties and Terms Influence Purchase Decisions?
By grasping the essential technical properties and trade terminology, B2B buyers can make informed decisions that align with their operational needs and budget constraints. This knowledge facilitates effective supplier negotiations and helps ensure the selection of high-quality fire engines that meet specific firefighting requirements.
Navigating Market Dynamics and Sourcing Trends in the fire engine manufacturer Sector
What Are the Key Market Dynamics in the Fire Engine Manufacturing Sector?
The fire engine manufacturing sector is currently experiencing notable shifts influenced by several global drivers. Increasing urbanization, especially in Africa and South America, is leading to higher demand for advanced firefighting solutions. Countries like Egypt and Italy are investing heavily in upgrading their emergency services, necessitating state-of-the-art fire engines that can handle complex urban emergencies.
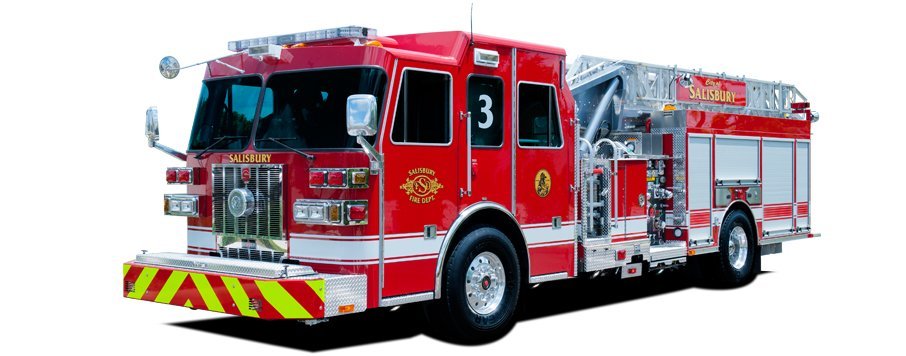
A stock image related to fire engine manufacturer.
Emerging technologies are reshaping the industry, with innovations such as IoT-enabled vehicles and autonomous firefighting systems gaining traction. These technologies not only enhance operational efficiency but also improve response times during emergencies. Additionally, international B2B buyers should be aware of the growing trend towards modular fire engines that can be customized based on specific regional needs, particularly in diverse markets like the Middle East and Europe.
Furthermore, sustainability is becoming a critical factor in purchasing decisions. As environmental regulations tighten globally, manufacturers are increasingly focusing on producing vehicles that meet stringent emission standards. Buyers from regions such as Africa and South America should prioritize suppliers who are compliant with these regulations, ensuring that they invest in equipment that aligns with future regulatory landscapes.
How Important Is Sustainability and Ethical Sourcing for Fire Engine Manufacturers?
Sustainability and ethical sourcing have emerged as pivotal considerations in the fire engine manufacturing sector. The environmental impact of manufacturing processes, including carbon emissions and resource depletion, is under scrutiny. International B2B buyers are encouraged to seek suppliers who prioritize sustainable practices, as this not only mitigates environmental harm but also enhances brand reputation.
The importance of ethical supply chains cannot be overstated. Buyers should assess the sourcing of materials, ensuring that they are derived from responsible suppliers who adhere to labor and environmental standards. Certifications such as ISO 14001 for environmental management and FSC certification for sustainable materials can serve as benchmarks for evaluating potential suppliers.
Incorporating ‘green’ materials in fire engine manufacturing—such as recycled metals and bio-based plastics—can significantly reduce the ecological footprint of these vehicles. Buyers from the Middle East and Europe, in particular, are increasingly demanding transparency in sourcing, making it essential for manufacturers to clearly communicate their sustainability efforts.
What Is the Historical Context of Fire Engine Manufacturing?
The fire engine manufacturing sector has evolved significantly over the last century. Initially, fire engines were horse-drawn vehicles equipped with hand-pumped water systems. The introduction of motorized fire engines in the early 20th century marked a turning point, enhancing the speed and efficiency of firefighting efforts.
Throughout the decades, advancements in technology have transformed fire engines into sophisticated machines equipped with advanced firefighting systems, aerial ladders, and specialized equipment for various emergencies. The focus has shifted from merely transporting firefighters to providing them with the tools necessary for effective emergency response. This evolution highlights the importance of staying abreast of historical trends and technological advancements, enabling international B2B buyers to make informed decisions when sourcing fire engine solutions.
Frequently Asked Questions (FAQs) for B2B Buyers of fire engine manufacturer
-
How can I effectively vet a fire engine manufacturer for international sourcing?
To effectively vet a fire engine manufacturer, start by researching their industry reputation and customer reviews. Check for certifications that demonstrate compliance with international safety standards, such as ISO or NFPA certifications. Engage directly with previous clients to understand their experiences. Additionally, assess the manufacturer’s production capacity and technological capabilities. Request detailed product specifications and inquire about their after-sales service. Conducting a factory visit, if feasible, can provide deeper insights into their operations and quality control processes. -
What are the key factors to consider when customizing fire engines for my region?
When customizing fire engines, consider regional climate, terrain, and specific firefighting needs. Assess the availability of local spare parts and maintenance services to ensure longevity and operational efficiency. Collaborate with local fire departments to understand their unique requirements, such as water capacity, hose length, and equipment storage. It’s also important to factor in regulatory compliance with local safety standards. Engage the manufacturer in discussions about design flexibility to accommodate these regional demands effectively. -
What minimum order quantities (MOQs) should I expect from fire engine manufacturers?
Minimum order quantities (MOQs) can vary significantly among manufacturers, often depending on their production capacity and the specific models requested. Typically, MOQs for fire engines can range from one unit for specialized custom builds to several units for standard models. It’s essential to communicate your needs clearly and negotiate MOQs that align with your budget and operational requirements. Some manufacturers may offer more favorable terms for repeat orders or long-term contracts, which can be beneficial for ongoing procurement. -
What payment terms are standard for international fire engine purchases?
Standard payment terms for international fire engine purchases often include a combination of upfront deposits and milestone payments. Many manufacturers require a deposit of 30-50% upon order confirmation, with the balance due before shipment or upon delivery. Letter of Credit (LC) is a common method used to secure transactions, providing assurance to both parties. It’s advisable to clarify payment terms early in negotiations, including any implications for financing options, currency exchange risks, and payment timelines to avoid potential disputes. -
How can I ensure quality assurance (QA) for my fire engine order?
To ensure quality assurance (QA) for your fire engine order, request a comprehensive QA plan from the manufacturer that outlines their testing and inspection processes. It’s beneficial to establish clear quality standards that the products must meet before shipment. Consider hiring a third-party inspection service to assess the engines before they leave the manufacturing facility. Additionally, inquire about warranty terms and after-sales support, which can provide further assurance of the manufacturer’s commitment to quality. -
What logistical considerations should I account for when importing fire engines?
When importing fire engines, consider logistics such as shipping methods, customs clearance, and delivery timelines. Choose between sea freight and air freight based on urgency and budget constraints. Engage a freight forwarder experienced in handling heavy machinery to navigate the complexities of international shipping. Ensure you have all necessary documentation, including import permits and customs declarations, to avoid delays. Additionally, factor in local transportation logistics for delivering the engines from the port to your facility. -
How can I assess the manufacturer’s compliance with international safety standards?
Assessing a manufacturer’s compliance with international safety standards involves reviewing their certifications and regulatory approvals. Request documentation for relevant certifications such as ISO 9001 for quality management and NFPA standards for fire protection. Evaluate their adherence to local regulations, especially if you are sourcing from regions with different safety requirements. Engaging with industry associations or regulatory bodies can provide additional verification of the manufacturer’s compliance status and commitment to safety. -
What are the best practices for establishing a long-term relationship with a fire engine manufacturer?
Establishing a long-term relationship with a fire engine manufacturer begins with transparent communication and mutual understanding of expectations. Regularly engage in discussions about product performance, market trends, and potential innovations. Provide feedback on their products and services to help them improve. Consider entering into a long-term supply agreement that benefits both parties, including favorable pricing and priority service. Building a partnership based on trust, reliability, and collaboration can lead to advantageous terms and enhanced service over time.
Important Disclaimer & Terms of Use
⚠️ Important Disclaimer
The information provided in this guide, including content regarding manufacturers, technical specifications, and market analysis, is for informational and educational purposes only. It does not constitute professional procurement advice, financial advice, or legal advice.
While we have made every effort to ensure the accuracy and timeliness of the information, we are not responsible for any errors, omissions, or outdated information. Market conditions, company details, and technical standards are subject to change.
B2B buyers must conduct their own independent and thorough due diligence before making any purchasing decisions. This includes contacting suppliers directly, verifying certifications, requesting samples, and seeking professional consultation. The risk of relying on any information in this guide is borne solely by the reader.
Strategic Sourcing Conclusion and Outlook for fire engine manufacturer
What Are the Key Takeaways for International B2B Buyers in the Fire Engine Market?
In the competitive landscape of fire engine manufacturing, strategic sourcing emerges as a critical component for international B2B buyers. By understanding regional market dynamics and supplier capabilities, buyers can optimize their procurement processes, ensuring both cost-efficiency and high-quality standards. Leveraging local partnerships can significantly reduce lead times and enhance service delivery, especially in regions like Africa and South America, where logistical challenges may arise.
How Can Buyers Leverage Strategic Sourcing for Better Outcomes?
Engaging in thorough supplier evaluations and establishing long-term relationships can lead to better negotiation outcomes and innovation in product development. Buyers are encouraged to prioritize sustainability and compliance with regional safety standards, which not only fosters trust but also enhances the brand reputation in local markets.
What Does the Future Hold for Fire Engine Manufacturers and Buyers?
As the fire engine industry evolves, embracing technological advancements such as smart firefighting systems and eco-friendly materials will be paramount. International buyers should remain agile and informed about emerging trends and regulatory changes, positioning themselves to seize new opportunities.
In conclusion, the future of fire engine procurement is bright for proactive buyers. By adopting a strategic sourcing approach, B2B buyers from Africa, South America, the Middle East, and Europe can ensure they are not only meeting current needs but also anticipating future demands. Now is the time to take decisive action and strengthen your sourcing strategies to secure a competitive edge in this vital industry.