Discover Top FRP Cable Tray Manufacturers: A Cost-Saving Guide (2025)
Introduction: Navigating the Global Market for frp cable tray manufacturers
In the ever-evolving landscape of industrial infrastructure, sourcing FRP cable tray manufacturers presents a unique challenge for international B2B buyers. As businesses expand and modernize their electrical systems, the demand for durable and lightweight cable management solutions increases. However, navigating the global market can be daunting due to varying quality standards, regulatory compliance, and supplier reliability, particularly for buyers in regions such as Africa, South America, the Middle East, and Europe.
This comprehensive guide aims to demystify the complexities of sourcing FRP cable trays by covering essential topics such as types and applications, supplier vetting processes, cost considerations, and regional compliance requirements. Whether you are looking for solutions to support renewable energy projects in South America or seeking reliable suppliers in Europe, this guide is tailored to empower your purchasing decisions.
By providing actionable insights and expert analysis, we equip B2B buyers with the knowledge necessary to make informed choices that align with their specific operational needs. Understanding the intricacies of FRP cable trays not only enhances project efficiency but also ensures that your organization remains competitive in a global marketplace. Get ready to explore the opportunities and best practices that will help you successfully navigate the world of FRP cable tray manufacturing.
Understanding frp cable tray manufacturers Types and Variations
Type Name | Key Distinguishing Features | Primary B2B Applications | Brief Pros & Cons for Buyers |
---|---|---|---|
Ladder Cable Trays | Rung-like design for optimal ventilation; easy access. | Industrial plants, data centers. | Pros: Excellent airflow; easy installation. Cons: May require more space. |
Solid Bottom Trays | Continuous solid base; provides maximum protection. | Power generation, telecommunications. | Pros: Enhanced protection against debris; robust. Cons: Limited airflow. |
Trough Cable Trays | U-shaped design; supports heavier cables and equipment. | Mining, oil & gas sectors. | Pros: High load capacity; good for outdoor use. Cons: More complex installation. |
Wire Mesh Trays | Lightweight; flexible design for various configurations. | Commercial buildings, retail spaces. | Pros: Cost-effective; easy to modify. Cons: Less protective against environmental factors. |
Custom Fabricated Trays | Tailored designs to meet specific project needs. | Specialized industries, unique setups. | Pros: Perfect fit for specific applications; maximizes space. Cons: Higher cost; longer lead time. |
What Are Ladder Cable Trays and Their B2B Relevance?
Ladder cable trays feature a rung-like design that allows for optimal ventilation, making them ideal for environments where heat dissipation is critical. They are commonly used in industrial plants and data centers where cable management is essential. When considering ladder trays, buyers should evaluate the installation space, as they typically require more room than other types, but their ease of access and airflow benefits often justify the footprint.
Why Choose Solid Bottom Trays?
Solid bottom trays offer a continuous solid base that provides maximum protection for cables against debris and environmental hazards. They are particularly suitable for applications in power generation and telecommunications, where cable integrity is paramount. B2B buyers should weigh the advantages of enhanced protection against the potential downsides of limited airflow, which may necessitate additional cooling solutions in certain installations.
How Do Trough Cable Trays Function?
Trough cable trays are designed with a U-shaped structure, making them capable of supporting heavier cables and equipment. They are often found in demanding industries such as mining and oil & gas, where robust solutions are required. When purchasing trough trays, businesses should consider the installation complexity and overall weight capacity, as these trays can handle significant loads but may require more intricate support structures.
What Are the Benefits of Wire Mesh Trays?
Wire mesh trays are lightweight and offer flexibility in configuration, making them a popular choice for commercial buildings and retail spaces. Their cost-effectiveness and ease of modification allow businesses to adapt to changing needs without incurring high expenses. However, buyers should note that while wire mesh trays are economical, they provide less protection against environmental factors, which may be a consideration in certain applications.
Why Consider Custom Fabricated Trays?
Custom fabricated trays are designed to meet the specific requirements of unique projects, making them ideal for specialized industries with unique setups. They ensure a perfect fit for the installation space, maximizing efficiency and functionality. However, buyers should be aware that while these trays provide tailored solutions, they often come with higher costs and longer lead times, which can impact project timelines.
Related Video: Composite System (FRP) – Cable Ladder & Cable Tray
Key Industrial Applications of frp cable tray manufacturers
Industry/Sector | Specific Application of frp cable tray manufacturers | Value/Benefit for the Business | Key Sourcing Considerations for this Application |
---|---|---|---|
Oil and Gas | Cable management in refineries and offshore platforms | Enhanced safety and reduced maintenance costs | Compliance with industry standards, corrosion resistance, and load capacity. |
Telecommunications | Support for fiber optic and data cables in urban networks | Improved infrastructure reliability | UV resistance, lightweight properties, and ease of installation. |
Manufacturing | Electrical and data cable routing in production facilities | Increased operational efficiency | Customization options, durability under extreme conditions, and fire resistance. |
Renewable Energy | Cable support systems in solar and wind farms | Long-term cost savings and sustainability | Resistance to environmental factors, structural integrity, and scalability. |
Transportation | Cable management in railways and airports | Enhanced safety and operational reliability | Compliance with safety regulations, ease of installation, and maintenance access. |
How Are FRP Cable Trays Used in the Oil and Gas Industry?
In the oil and gas sector, FRP cable trays are crucial for managing cables in refineries and offshore platforms. They provide a robust solution for routing electrical and communication cables while resisting harsh environmental conditions, including corrosion from chemicals and saltwater. This durability translates into enhanced safety and reduced maintenance costs, making them a preferred choice for international buyers in regions with extreme climates, such as Africa and the Middle East. Buyers should prioritize compliance with industry standards and ensure that the trays meet specific load-bearing requirements.
What Role Do FRP Cable Trays Play in Telecommunications?
Telecommunications companies utilize FRP cable trays for organizing and protecting fiber optic and data cables in urban networks. These trays enhance infrastructure reliability by minimizing signal interference and damage during installation or maintenance. The lightweight and UV-resistant properties of FRP make it an ideal choice for outdoor settings, especially in regions like South America, where exposure to sunlight can degrade materials quickly. When sourcing, buyers should focus on the ease of installation and the capacity for future scalability to accommodate growing network demands.
How Are FRP Cable Trays Beneficial in Manufacturing?
In manufacturing facilities, FRP cable trays facilitate efficient routing of electrical and data cables, which is essential for maintaining operational continuity. These trays can withstand extreme temperatures and mechanical stresses, thus ensuring durability in demanding environments. By reducing the risk of cable damage and providing easy access for maintenance, businesses can improve productivity. For international buyers, especially in Europe and Asia, customization options to fit unique facility layouts and adherence to safety regulations are critical factors during sourcing.
Why Are FRP Cable Trays Important for Renewable Energy Projects?
In the renewable energy sector, FRP cable trays are employed in solar and wind farms to support electrical cables. Their lightweight and corrosion-resistant properties contribute to long-term cost savings and sustainability, making them an attractive option for environmentally conscious projects. Buyers from regions like Africa and South America, where renewable energy initiatives are expanding, should consider the trays’ resistance to environmental factors and the ability to scale as project demands grow. Ensuring the structural integrity of the trays under varying loads is also crucial.
How Do FRP Cable Trays Enhance Safety in Transportation?
FRP cable trays play a vital role in managing cables in transportation infrastructure, such as railways and airports. They help maintain safety by organizing and protecting critical electrical systems, reducing the risk of cable damage that could lead to failures. The ease of installation and maintenance access is particularly beneficial in high-traffic environments. Buyers must ensure that the trays comply with safety regulations and are designed for quick installation to minimize disruptions during upgrades or repairs, which is especially important in busy regions across Europe and the Middle East.
3 Common User Pain Points for ‘frp cable tray manufacturers’ & Their Solutions
Scenario 1: Navigating Regulatory Compliance for FRP Cable Trays
The Problem: International B2B buyers often face the challenge of ensuring that the FRP (Fiberglass Reinforced Plastic) cable trays they purchase meet local and international regulatory standards. This is particularly critical in regions like Africa and the Middle East, where regulations can vary significantly between countries and industries. Buyers may struggle to keep track of these requirements, leading to potential project delays, increased costs, and even legal ramifications if non-compliant products are used.
The Solution: To overcome this hurdle, B2B buyers should conduct thorough research on the specific compliance standards applicable in their region. Engaging directly with FRP cable tray manufacturers can provide clarity on certifications and compliance documentation. Buyers should request detailed product specifications and compliance certificates, such as ISO certifications or local regulatory approvals. Additionally, maintaining a checklist of local regulations and collaborating with a compliance consultant can streamline the process, ensuring that all materials sourced are compliant from the outset, thus minimizing project risks.
Scenario 2: Ensuring Product Durability and Performance
The Problem: One significant concern for buyers is the durability and performance of FRP cable trays in various environmental conditions. In regions like South America, where humidity and temperature fluctuations are common, buyers may find that some products do not perform as expected, leading to costly maintenance and replacements. This can cause frustration, especially when projects are time-sensitive and depend on reliable infrastructure.
The Solution: To address this issue, buyers should prioritize sourcing from manufacturers that offer product testing and performance guarantees. It’s crucial to inquire about the materials used in production and to request data on the trays’ resistance to corrosion, UV radiation, and thermal expansion. Engaging in pilot testing with the selected products in a controlled environment can provide insights into their performance before full-scale installation. Additionally, establishing strong relationships with manufacturers can facilitate access to ongoing support and warranty options, ensuring that the products maintain their integrity over time.
Scenario 3: Managing Supply Chain Disruptions
The Problem: Global supply chain disruptions have become a significant pain point for B2B buyers, particularly in the context of sourcing FRP cable trays. Buyers in Europe, for instance, may experience delays due to transportation issues or raw material shortages, leading to project delays and budget overruns. The unpredictability of supply chain logistics can create a frustrating environment for buyers who need timely delivery to adhere to project timelines.
The Solution: To mitigate supply chain risks, buyers should adopt a proactive approach by diversifying their supplier base. Engaging with multiple FRP cable tray manufacturers from different geographic locations can provide alternatives if one supplier faces disruptions. Additionally, buyers should consider establishing long-term contracts with key suppliers to secure consistent supply and potentially better pricing. Implementing inventory management systems that account for lead times and buffer stocks can also help in managing expectations and ensuring that projects stay on track despite unforeseen delays. Regular communication with suppliers regarding their capacity and potential risks can further enhance supply chain resilience.
By addressing these common pain points with actionable solutions, international B2B buyers can make informed decisions when sourcing FRP cable trays, ultimately leading to smoother project execution and enhanced operational efficiency.
Strategic Material Selection Guide for frp cable tray manufacturers
When selecting materials for FRP (Fiber Reinforced Polymer) cable trays, manufacturers must consider various factors that affect performance, durability, and compliance with international standards. Here, we analyze four common materials used in FRP cable tray manufacturing, focusing on their key properties, advantages and disadvantages, application impacts, and considerations for international B2B buyers.
What Are the Key Properties of Polyester Resin in FRP Cable Trays?
Polyester resin is one of the most commonly used materials in FRP cable tray manufacturing. It offers a good balance of strength and weight, making it suitable for various applications.
- Key Properties: Polyester resin typically has a temperature rating of up to 90°C and exhibits moderate corrosion resistance against chemicals like acids and alkalis.
- Pros & Cons: The advantages include lower cost and ease of manufacturing, while the downsides are its susceptibility to UV degradation and limited high-temperature performance.
- Impact on Application: Polyester resin is well-suited for indoor applications but may not perform optimally in harsh outdoor environments or extreme temperatures.
- Considerations for International Buyers: Buyers in regions like Africa and South America should ensure compliance with local standards (e.g., ASTM D638) and consider UV protection additives for outdoor use.
How Does Vinyl Ester Resin Compare for FRP Cable Tray Applications?
Vinyl ester resin is another popular choice, particularly in environments where chemical resistance is paramount.
- Key Properties: Vinyl ester resins can withstand temperatures up to 120°C and offer superior corrosion resistance compared to polyester.
- Pros & Cons: The main advantages are its excellent durability and chemical resistance, making it suitable for harsh environments. However, it is generally more expensive and can be more complex to manufacture.
- Impact on Application: This material is ideal for industrial applications involving corrosive substances, making it a preferred choice in chemical plants.
- Considerations for International Buyers: Compliance with standards such as DIN EN 13121 is crucial, especially for buyers in Europe and the Middle East.
What Are the Advantages of Using Epoxy Resin in FRP Cable Trays?
Epoxy resin is known for its exceptional mechanical properties and versatility.
- Key Properties: It can handle temperatures up to 150°C and offers excellent adhesion and mechanical strength.
- Pros & Cons: The advantages include high durability and resistance to moisture and chemicals. However, epoxy is typically more expensive and has a longer curing time.
- Impact on Application: Epoxy resin is suitable for high-stress applications, such as in power plants or offshore installations.
- Considerations for International Buyers: Buyers should be aware of the specific curing conditions required and ensure compliance with international standards like JIS K 6911.
What Role Does Glass Fiber Reinforcement Play in FRP Cable Tray Manufacturing?
Glass fiber reinforcement enhances the mechanical properties of FRP cable trays.
- Key Properties: The addition of glass fibers significantly increases tensile strength and impact resistance while maintaining lightweight characteristics.
- Pros & Cons: The primary advantage is the improved strength-to-weight ratio, making it suitable for various applications. However, the complexity of manufacturing and higher costs can be limiting factors.
- Impact on Application: Glass fiber-reinforced trays are ideal for heavy-duty applications where mechanical stress is a concern.
- Considerations for International Buyers: Buyers should assess the glass fiber quality and ensure it meets relevant standards, such as ASTM D578, particularly in regions like Europe.
Summary Table of Material Comparisons
Material | Typical Use Case for frp cable tray manufacturers | Key Advantage | Key Disadvantage/Limitation | Relative Cost (Low/Med/High) |
---|---|---|---|---|
Polyester Resin | Indoor applications with moderate exposure | Cost-effective and easy to manufacture | UV degradation over time | Low |
Vinyl Ester Resin | Chemical plants and harsh environments | Superior chemical resistance | Higher cost and manufacturing complexity | High |
Epoxy Resin | High-stress applications (e.g., power plants) | Excellent mechanical properties | Longer curing time and higher cost | High |
Glass Fiber Reinforcement | Heavy-duty applications requiring strength | Improved strength-to-weight ratio | Complex manufacturing process | Medium |
This guide provides a comprehensive overview of the materials available for FRP cable tray manufacturing, enabling international B2B buyers to make informed decisions based on their specific needs and regional compliance requirements.
In-depth Look: Manufacturing Processes and Quality Assurance for frp cable tray manufacturers
What Are the Main Stages of Manufacturing FRP Cable Trays?
The manufacturing process for Fiberglass Reinforced Plastic (FRP) cable trays involves several key stages, each critical for ensuring the final product meets quality and performance standards. Understanding these stages can help B2B buyers assess suppliers more effectively.
How Is Material Prepared for FRP Cable Tray Manufacturing?
Material preparation is the first and foremost step in manufacturing FRP cable trays. This involves selecting high-quality fiberglass and resin, which are essential for the structural integrity and longevity of the trays. The fiberglass is usually in the form of woven roving or chopped strands, while the resin can be a polyester or vinyl ester, depending on the application requirements.
During this stage, the raw materials are inspected for quality and consistency. Suppliers often utilize suppliers with ISO 9001 certification to ensure material quality. Buyers should inquire about the supplier’s sourcing and handling practices to ensure the materials meet their specific needs.
What Techniques Are Used in Forming FRP Cable Trays?
The forming stage involves shaping the prepared materials into the desired tray configuration. Common techniques include:
-
Hand Lay-Up: A manual process where fiberglass mats are layered with resin in a mold. This method is cost-effective for small batches but may lead to variability in quality.
-
Spray-Up: This technique uses a spray gun to apply resin and fiberglass into a mold. It allows for faster production rates and is often used for larger trays.
-
Filament Winding: This automated process involves winding continuous strands of fiberglass around a rotating mandrel. It provides high strength and uniform thickness, making it ideal for specialized applications.
B2B buyers should consider the forming techniques used by suppliers, as they can influence the durability and performance of the final product.
How Is Assembly Conducted for FRP Cable Trays?
Once the individual components are formed, the assembly stage begins. This typically includes:
-
Joining Sections: Sections of cable trays are joined using adhesive or mechanical fasteners. Adhesives are often preferred for their ability to maintain the integrity of the fiberglass.
-
Adding Accessories: Features such as bends, tees, and end caps are added during assembly. This step is crucial for ensuring the trays meet specific installation requirements.
-
Quality Checks: Assemblies undergo initial quality checks to ensure proper fit and alignment. Buyers should verify the supplier’s assembly processes and whether they conduct any in-process inspections.
What Finishing Processes Are Employed for FRP Cable Trays?
The finishing stage is essential for enhancing the aesthetic and functional properties of the cable trays. Common finishing processes include:
-
Surface Coating: A gel coat or protective layer is applied to improve corrosion resistance and UV stability. This is particularly important for trays used in harsh environments.
-
Trimming and Smoothing: Edges are trimmed, and surfaces are smoothed to ensure safety and ease of installation. This step can significantly affect the final product’s usability.
-
Final Inspection: After finishing, trays undergo a final inspection to ensure they meet the specified standards. B2B buyers should inquire about the certifications and standards that the finished products comply with.
What Are the Quality Assurance Practices for FRP Cable Tray Manufacturers?
Quality assurance (QA) is a critical aspect of the manufacturing process for FRP cable trays. It ensures that products not only meet customer expectations but also comply with international standards.
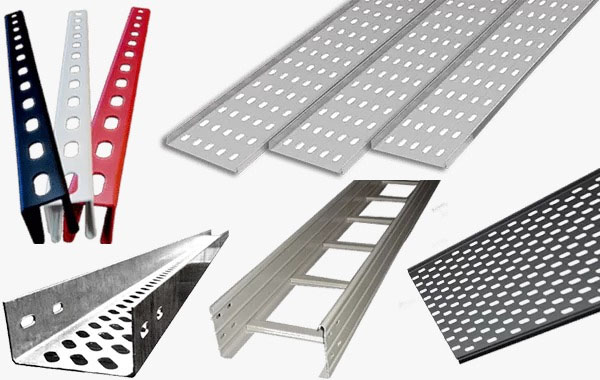
A stock image related to frp cable tray manufacturers.
Which International Standards Should B2B Buyers Be Aware Of?
Many FRP cable tray manufacturers adhere to international quality standards such as ISO 9001, which outlines the requirements for a quality management system. Additionally, industry-specific certifications may include:
-
CE Marking: Indicates compliance with EU safety, health, and environmental protection standards.
-
API Standards: Relevant for manufacturers supplying to the oil and gas industry, ensuring the product meets specific performance criteria.
B2B buyers should request documentation of these certifications to confirm compliance.
How Are Quality Control Checkpoints Established?
Quality control (QC) checkpoints are established at various stages of the manufacturing process to ensure product quality. Key checkpoints include:
-
Incoming Quality Control (IQC): At this stage, raw materials are inspected for quality before production begins.
-
In-Process Quality Control (IPQC): Ongoing inspections occur during the manufacturing process to catch defects early.
-
Final Quality Control (FQC): The final inspection ensures that the finished product meets all specifications before shipment.
Buyers should inquire about the frequency and methods of inspections used by suppliers.
What Common Testing Methods Are Used in Quality Assurance?
Various testing methods are employed to ensure the quality and durability of FRP cable trays. These may include:
-
Load Testing: Assessing the tray’s ability to support specified loads.
-
Corrosion Testing: Evaluating resistance to environmental factors, especially for outdoor applications.
-
Thermal Testing: Ensuring performance under temperature fluctuations.
Understanding these methods can help buyers evaluate the reliability of potential suppliers.
How Can B2B Buyers Verify Supplier Quality Control?
Verifying a supplier’s quality control processes is essential for B2B buyers to ensure they receive high-quality products. Here are several actionable steps:
-
Request Audits and Reports: Buyers should ask for documentation of recent audits and quality reports. This provides insight into the supplier’s adherence to quality standards.
-
Third-Party Inspections: Engaging third-party inspection services can provide an unbiased assessment of the supplier’s manufacturing processes and product quality.
-
Site Visits: If possible, conducting site visits can help buyers assess the manufacturing environment and practices firsthand.
-
References and Reviews: Speaking with other businesses that have worked with the supplier can provide valuable feedback on quality and reliability.
What Are the QC and Certification Nuances for International Buyers?
International B2B buyers, particularly from Africa, South America, the Middle East, and Europe, should be aware of specific nuances in quality control and certification. These may include:
-
Regional Compliance: Different regions may have unique regulatory requirements that products must meet. Buyers should ensure that suppliers are familiar with these regulations.
-
Documentation for Customs: Proper documentation of certifications is essential for smooth customs clearance. Buyers should verify that suppliers can provide necessary paperwork.
-
Cultural Differences: Understanding cultural differences in business practices can help facilitate smoother communication and negotiations regarding quality expectations.
By grasping these aspects of manufacturing processes and quality assurance, international B2B buyers can make informed decisions when selecting FRP cable tray manufacturers. This knowledge not only enhances procurement strategies but also contributes to building long-term partnerships with reliable suppliers.
Practical Sourcing Guide: A Step-by-Step Checklist for ‘frp cable tray manufacturers’
The following checklist provides a structured approach for international B2B buyers looking to procure FRP (Fiberglass Reinforced Plastic) cable trays. This guide aims to streamline the sourcing process, ensuring that buyers make informed decisions when selecting manufacturers.
Step 1: Define Your Technical Specifications
Before reaching out to manufacturers, clearly outline your technical requirements. This includes dimensions, load capacity, environmental conditions, and any specific compliance standards relevant to your industry. Having well-defined specifications helps in communicating effectively with suppliers and ensures that the products meet your needs.
Step 2: Conduct Market Research
Investigate the market landscape for FRP cable trays. This involves identifying potential suppliers across different regions, particularly focusing on manufacturers from Africa, South America, the Middle East, and Europe. Look for suppliers with a strong reputation and proven track record in delivering high-quality products.
Step 3: Evaluate Potential Suppliers
Thoroughly vet potential suppliers before making a commitment. Request detailed company profiles, product catalogs, and case studies to understand their capabilities. Additionally, seek references from other buyers in your industry or region to gauge their performance and reliability.
- Considerations:
- Look for suppliers who specialize in FRP products.
- Assess their experience in handling similar projects.
Step 4: Verify Supplier Certifications
Check if the manufacturers hold relevant certifications and comply with industry standards such as ISO 9001 or ASTM. Certifications are indicative of a supplier’s commitment to quality and can provide reassurance regarding the durability and safety of the products.
- What to Look For:
- Compliance with local and international safety standards.
- Certifications that reflect their manufacturing processes and product quality.
Step 5: Request Samples for Evaluation
Before finalizing any orders, request samples of the FRP cable trays. Evaluating samples allows you to assess the quality, finish, and overall suitability for your specific application. This step also helps in identifying any potential issues before committing to a large order.
Step 6: Discuss Terms and Conditions Clearly
Once you have selected a supplier, negotiate the terms and conditions of the contract. This includes pricing, payment terms, delivery schedules, and warranty conditions. Clear communication can prevent misunderstandings and ensure that both parties are aligned on expectations.
Step 7: Establish Ongoing Communication
After placing an order, maintain open lines of communication with the supplier. Regular updates on production status, shipping, and any potential delays are crucial for effective project management. Establishing a good relationship can lead to better service and support in future transactions.
By following this checklist, B2B buyers can ensure a more efficient and effective procurement process for FRP cable trays, leading to better project outcomes and stronger supplier partnerships.
Comprehensive Cost and Pricing Analysis for frp cable tray manufacturers Sourcing
What Are the Key Cost Components for FRP Cable Tray Manufacturers?
When sourcing from FRP (Fiberglass Reinforced Plastic) cable tray manufacturers, understanding the cost structure is crucial for making informed purchasing decisions. The main components of cost include:
-
Materials: The primary raw materials for FRP cable trays, such as fiberglass and resin, can vary significantly in price based on quality and availability. Suppliers may source materials from local or international markets, affecting costs.
-
Labor: Labor costs are influenced by the manufacturing location. Countries with lower labor costs may offer competitive pricing, but it’s essential to evaluate the quality of craftsmanship as well.
-
Manufacturing Overhead: This includes indirect costs related to production facilities, utilities, and administrative expenses. Efficient production processes can help lower overhead costs, which may be reflected in the final price.
-
Tooling: Custom tooling for specific designs can lead to higher initial costs but may be necessary for meeting unique specifications. Consider whether the tooling costs are included in the quoted price or if they are additional.
-
Quality Control (QC): Implementing rigorous QC measures ensures that the products meet industry standards. Higher QC standards may increase costs but can reduce the risk of defects and associated costs in the long run.
-
Logistics: Shipping costs depend on the size and weight of the trays, as well as the distance to the destination. International shipping can significantly impact overall costs, especially when considering tariffs and customs fees.
-
Margin: Manufacturers will factor in their profit margin, which can vary based on competition, market demand, and brand reputation.
How Do Price Influencers Impact FRP Cable Tray Sourcing?
Several factors can influence the pricing of FRP cable trays:
-
Volume/MOQ (Minimum Order Quantity): Purchasing in bulk often results in lower unit prices. However, consider your storage capabilities and future needs when determining order size.
-
Specifications and Customization: Customized solutions may come with higher costs due to additional design and production efforts. Ensure that the specifications align with your project requirements to avoid unnecessary expenses.
-
Materials and Quality Certifications: Higher-quality materials or certifications (e.g., ISO, UL) can justify premium pricing. Evaluate whether the additional costs are worth the benefits in durability and compliance.
-
Supplier Factors: The reputation and reliability of suppliers can influence pricing. Established suppliers may charge more but could offer better service and product consistency.
-
Incoterms: The chosen Incoterms (e.g., FOB, CIF) affect shipping costs and responsibilities. Understanding these terms can help you better estimate total costs and negotiate favorable terms.
What Negotiation Tips Can Help Optimize Costs for International Buyers?
To ensure cost efficiency when sourcing FRP cable trays, especially for international buyers from Africa, South America, the Middle East, and Europe, consider the following strategies:
-
Conduct Market Research: Familiarize yourself with pricing trends and supplier options in the regions you are targeting. This knowledge will strengthen your negotiation position.
-
Leverage Total Cost of Ownership (TCO): When evaluating suppliers, consider not just the purchase price but also long-term costs, including maintenance, lifespan, and potential downtime costs.
-
Build Relationships: Establishing long-term relationships with suppliers can lead to better pricing and terms. Frequent communication and collaboration can foster trust and reliability.
-
Negotiate Payment Terms: Flexible payment options can ease cash flow concerns. Discussing terms such as deferred payments or installment plans can be beneficial.
-
Be Transparent: Clearly communicate your needs and concerns to suppliers. Transparency can lead to more tailored solutions and pricing structures that suit both parties.
Conclusion: Understanding Costs and Pricing for Informed Decisions
While prices may vary significantly among FRP cable tray manufacturers, understanding the key cost components, price influencers, and effective negotiation strategies can empower international buyers. Always seek multiple quotes and conduct thorough due diligence to ensure that you are making the best purchasing decisions for your business needs. Remember, prices are indicative and can fluctuate based on market conditions, so stay informed and flexible in your sourcing strategy.
Alternatives Analysis: Comparing frp cable tray manufacturers With Other Solutions
Understanding Alternatives to FRP Cable Tray Manufacturers
When considering solutions for cable management in industrial and commercial settings, FRP (Fiberglass Reinforced Plastic) cable trays are a popular choice. However, buyers should explore viable alternatives that may better suit their specific needs or budget constraints. This section compares FRP cable trays with two alternative solutions: metal cable trays and plastic cable trays.
Comparison Table of FRP Cable Tray Manufacturers and Alternatives
Comparison Aspect | FRP Cable Tray Manufacturers | Metal Cable Trays | Plastic Cable Trays |
---|---|---|---|
Performance | High corrosion resistance and strength; suitable for harsh environments. | Strong but susceptible to corrosion; good load-bearing capacity. | Lightweight and flexible; lower load capacity. |
Cost | Generally higher initial cost; long-term savings due to durability. | Moderate cost; may incur additional costs for anti-corrosion treatments. | Lower upfront cost; may require replacement more frequently. |
Ease of Implementation | Moderate; requires specific installation techniques due to material properties. | Easy to install with standard tools; widely available. | Very easy to install; often designed for DIY applications. |
Maintenance | Low maintenance; resistant to environmental factors. | Requires regular inspections and possible treatments for corrosion. | Minimal maintenance; prone to wear and tear. |
Best Use Case | Ideal for chemical plants, offshore applications, and areas with high humidity. | Suitable for general industrial applications and heavy-duty environments. | Best for light-duty applications in non-corrosive environments. |
In-Depth Analysis of Alternatives
What are the Advantages and Disadvantages of Metal Cable Trays?
Metal cable trays, typically made from steel or aluminum, offer robust performance and are widely recognized for their strength. They are suitable for a variety of industrial applications, especially where heavy cables are involved. However, they are prone to corrosion, particularly in humid or chemically aggressive environments, necessitating protective coatings or treatments. While the initial cost is moderate, ongoing maintenance may add to the total cost over time.
How Do Plastic Cable Trays Compare to FRP Solutions?
Plastic cable trays are known for their lightweight and flexible design, making them easy to handle and install. They are particularly advantageous in low-load applications and environments where corrosion is not a concern. The upfront cost is typically lower than both FRP and metal options, but plastic trays may not withstand heavy loads or extreme temperatures as effectively. Consequently, they may require replacement more frequently, which could offset initial savings.
Conclusion: How Should B2B Buyers Choose the Right Cable Management Solution?
Selecting the appropriate cable management solution involves evaluating specific project requirements, environmental conditions, and budget constraints. For buyers operating in harsh environments with high humidity or chemical exposure, FRP cable trays may provide the best long-term value despite their higher upfront cost. Conversely, metal cable trays are suitable for general industrial applications, while plastic trays serve well in lighter-duty situations. Ultimately, understanding the unique advantages and limitations of each option will enable B2B buyers to make informed decisions that align with their operational needs and financial objectives.
Essential Technical Properties and Trade Terminology for frp cable tray manufacturers
What Are the Key Technical Properties of FRP Cable Trays?
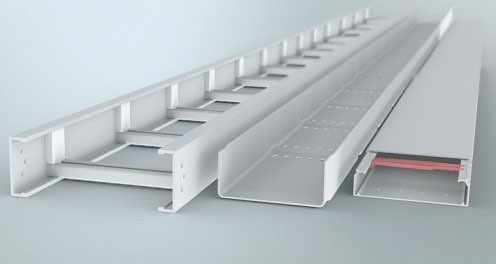
A stock image related to frp cable tray manufacturers.
When considering FRP (Fiberglass Reinforced Plastic) cable trays, several technical specifications are essential for international buyers to understand. These specifications not only impact the performance and durability of the trays but also influence procurement decisions.
1. Material Grade: What Types of FRP Are Available?
FRP cable trays are manufactured from different grades of fiberglass resin, which determine their strength, flexibility, and resistance to environmental factors. Common grades include polyester, vinyl ester, and epoxy. Each grade has unique properties suitable for various applications, such as chemical resistance or temperature tolerance. Understanding material grades helps buyers select the right product for their specific industrial needs, ensuring longevity and reliability.
2. Load-Bearing Capacity: How Much Weight Can They Support?
The load-bearing capacity of an FRP cable tray is crucial for its application in electrical installations. This specification is usually expressed in pounds per linear foot (PLF) and indicates the maximum weight the tray can safely support without deformation. Buyers must assess their cable weight requirements against the tray’s load capacity to prevent system failures, especially in sectors such as telecommunications and power distribution.
3. Tolerance: Why Is Precision Important?
Tolerance refers to the permissible limit of variation in a physical dimension of the cable tray. High tolerance levels ensure that the trays fit together correctly and align with other components in a system. For buyers, understanding the tolerance levels can help mitigate installation issues and facilitate smoother project execution, especially in large-scale industrial settings.
4. Corrosion Resistance: How Do They Perform in Harsh Environments?
One of the standout features of FRP cable trays is their resistance to corrosion from chemicals and environmental factors. This property is vital for industries operating in corrosive environments, such as oil and gas or chemical manufacturing. Buyers should inquire about the specific corrosion resistance ratings to ensure that the trays will maintain integrity over time.
5. Flame Retardancy: Is Safety a Concern?
Flame retardancy is a critical specification that indicates how well a material can resist ignition and limit fire spread. FRP cable trays can be treated with additives to enhance their flame-resistant properties. Understanding this property is vital for buyers in sectors where fire safety is paramount, ensuring compliance with safety regulations.
What Are Common Trade Terms Used in the FRP Cable Tray Industry?
Navigating the procurement process for FRP cable trays involves familiarizing oneself with specific trade terminology. Here are some key terms that buyers should understand.
1. OEM (Original Equipment Manufacturer): What Does It Mean?
An OEM is a company that produces parts or equipment that may be marketed by another manufacturer. In the context of FRP cable trays, buyers may engage with OEMs to source customized solutions that fit their specific operational needs. Knowing the role of OEMs can streamline sourcing and ensure product compatibility.
2. MOQ (Minimum Order Quantity): How Does It Affect Purchasing?
MOQ refers to the minimum number of units a supplier is willing to sell in a single order. Understanding MOQ is essential for buyers, as it can impact inventory management and cash flow. Buyers should negotiate MOQs to align with their project requirements and budget constraints.
3. RFQ (Request for Quotation): What Is the Process?
An RFQ is a formal document sent to suppliers to solicit price quotes for specific products. For buyers, issuing an RFQ is a critical step in the procurement process, enabling them to compare pricing and terms across multiple suppliers, thus ensuring competitive offers.
4. Incoterms: How Do They Affect Shipping?
Incoterms (International Commercial Terms) define the responsibilities of buyers and sellers regarding the transportation of goods. Familiarity with these terms helps buyers understand shipping costs, insurance, and liability during transit, which is especially important for international transactions.
5. Lead Time: Why Is It Important?
Lead time refers to the amount of time between placing an order and receiving the goods. This term is crucial for project planning and scheduling. Buyers should inquire about lead times when sourcing FRP cable trays to ensure timely delivery and avoid project delays.
By understanding these technical properties and trade terms, international B2B buyers can make informed decisions when sourcing FRP cable trays, optimizing their procurement processes, and ensuring successful project outcomes.
Navigating Market Dynamics and Sourcing Trends in the frp cable tray manufacturers Sector
What Are the Current Market Dynamics and Key Trends for FRP Cable Tray Manufacturers?
The global market for Fiber Reinforced Plastic (FRP) cable trays is witnessing significant growth, driven by increased demand in various sectors including construction, telecommunications, and renewable energy. International B2B buyers, particularly in regions such as Africa, South America, the Middle East, and Europe, are increasingly looking for reliable sourcing options that can meet their diverse needs. The rise of smart cities and the need for sustainable infrastructure are also key drivers, as FRP cable trays are favored for their lightweight, corrosion-resistant properties and adaptability in various environments.
Emerging technologies such as IoT and automation are reshaping the sourcing landscape. Buyers are increasingly utilizing digital platforms to streamline procurement processes and gain access to a broader range of suppliers. Additionally, many manufacturers are investing in advanced production techniques, such as 3D printing and automated manufacturing, to enhance efficiency and reduce lead times. This shift towards digitalization and automation allows B2B buyers to benefit from improved transparency, better pricing strategies, and enhanced product customization options.
How Does Sustainability Impact Sourcing Decisions for FRP Cable Trays?
As environmental concerns become more prominent, sustainability is emerging as a critical factor in sourcing decisions for FRP cable trays. The production of these trays often involves materials that can be harmful to the environment if not sourced responsibly. Thus, B2B buyers are increasingly prioritizing suppliers that adhere to ethical sourcing practices and possess relevant green certifications.
Using eco-friendly materials, such as recycled plastics and sustainably sourced fibers, is becoming a standard expectation. Certifications like ISO 14001 (Environmental Management) and LEED (Leadership in Energy and Environmental Design) are essential for manufacturers to demonstrate their commitment to sustainability. Buyers should also consider suppliers who can provide comprehensive documentation on the lifecycle impact of their products, ensuring that their sourcing choices align with corporate sustainability goals.
What Is the Historical Context of FRP Cable Tray Manufacturing?
The FRP cable tray manufacturing sector has evolved significantly since its inception in the late 20th century. Initially developed for lightweight and corrosion-resistant applications, these products quickly gained traction in industries such as oil and gas, telecommunications, and electrical infrastructure. The material’s ability to withstand harsh environmental conditions made it an attractive choice for various applications.
Over the years, technological advancements have led to improved manufacturing processes, enhancing the durability and performance of FRP cable trays. This evolution has also seen an increase in the diversity of product offerings, catering to the specific needs of different industries. B2B buyers today benefit from a rich selection of innovative solutions that not only meet functional requirements but also align with emerging trends in sustainability and efficiency.
Conclusion
Navigating the market dynamics and sourcing trends in the FRP cable tray manufacturing sector is essential for international B2B buyers. By understanding the current drivers, prioritizing sustainability in sourcing decisions, and recognizing the historical context of product development, businesses can make informed choices that will enhance their operational efficiency and contribute to their long-term success.
Frequently Asked Questions (FAQs) for B2B Buyers of frp cable tray manufacturers
-
How do I choose the right FRP cable tray manufacturer for my business needs?
Selecting the right FRP cable tray manufacturer involves assessing several key factors. Start by evaluating the manufacturer’s reputation and experience in the industry, particularly their expertise with the specific standards required in your region. Check for certifications that ensure product quality and compliance with safety regulations. Additionally, consider their capacity for customization, lead times, and their ability to provide technical support. Engaging in direct communication can also help gauge their customer service and responsiveness. -
What is the typical minimum order quantity (MOQ) for FRP cable trays?
The minimum order quantity (MOQ) for FRP cable trays can vary significantly among manufacturers, often ranging from 50 to 500 units depending on the specific design and materials required. It’s essential to discuss your project needs upfront with potential suppliers to understand their MOQ policies. Some manufacturers may offer flexible MOQs for larger projects or repeat orders, so negotiating can be beneficial, especially for international buyers looking to minimize upfront costs. -
What customization options are available when sourcing FRP cable trays?
Most FRP cable tray manufacturers offer a range of customization options, including size, color, load capacity, and additional features such as ventilation slots or specific coatings for chemical resistance. When discussing customization, provide clear specifications and applications to ensure the manufacturer can meet your requirements. Additionally, inquire about the possibility of producing prototypes or samples to evaluate the design and functionality before placing a larger order. -
How can I verify the quality of FRP cable trays from a manufacturer?
To verify the quality of FRP cable trays, request product samples and certifications that demonstrate compliance with international standards such as ISO or ASTM. Additionally, consider asking for test reports that detail the physical and mechanical properties of the trays, including tensile strength and resistance to corrosion. Reviewing customer testimonials and case studies can also provide insights into the manufacturer’s quality assurance practices and overall reliability in delivering durable products. -
What payment terms should I expect when sourcing FRP cable trays internationally?
Payment terms for international purchases of FRP cable trays can vary widely but typically include options such as advance payment, letters of credit, or payment upon delivery. It’s crucial to discuss and negotiate terms that align with your cash flow requirements while ensuring security for both parties. Additionally, consider using escrow services for larger transactions to mitigate risks. Be aware of currency exchange rates and transaction fees that may affect the total cost. -
What logistics considerations should I keep in mind when importing FRP cable trays?
Logistics for importing FRP cable trays involve several considerations, including shipping methods, customs regulations, and import duties specific to your country. Determine whether you prefer air or sea freight based on your budget and delivery timeline. Ensure that the manufacturer provides necessary documentation, such as invoices and packing lists, to facilitate smooth customs clearance. Working with a freight forwarder can also help navigate the complexities of international shipping and ensure timely delivery. -
How can I assess the reliability of a potential FRP cable tray supplier?
Assessing the reliability of a potential supplier involves conducting thorough due diligence. Start by reviewing their business history, including years of operation and client portfolio. Request references from previous clients, particularly those from your region, to gain insights into their experience. Additionally, consider visiting the manufacturer’s facilities if possible or utilizing third-party inspection services to evaluate their production capabilities and quality control processes firsthand.
- What are the common applications for FRP cable trays in various industries?
FRP cable trays are widely used across various industries, including telecommunications, oil and gas, power generation, and construction. Their corrosion resistance makes them ideal for environments with high humidity or exposure to chemicals, such as wastewater treatment plants and chemical processing facilities. In electrical installations, they provide a safe and organized method for routing cables, helping to maintain compliance with safety regulations. Understanding the specific applications relevant to your industry can help you select the appropriate tray type and configuration.
Important Disclaimer & Terms of Use
⚠️ Important Disclaimer
The information provided in this guide, including content regarding manufacturers, technical specifications, and market analysis, is for informational and educational purposes only. It does not constitute professional procurement advice, financial advice, or legal advice.
While we have made every effort to ensure the accuracy and timeliness of the information, we are not responsible for any errors, omissions, or outdated information. Market conditions, company details, and technical standards are subject to change.
B2B buyers must conduct their own independent and thorough due diligence before making any purchasing decisions. This includes contacting suppliers directly, verifying certifications, requesting samples, and seeking professional consultation. The risk of relying on any information in this guide is borne solely by the reader.
Strategic Sourcing Conclusion and Outlook for frp cable tray manufacturers
In summary, strategic sourcing plays a pivotal role in enhancing the procurement processes for frp cable tray manufacturers. By focusing on long-term supplier relationships, buyers can secure not only cost-effective pricing but also quality materials that meet international standards. Buyers from Africa, South America, the Middle East, and Europe should prioritize evaluating suppliers based on their technical capabilities, reputation, and compliance with local regulations, ensuring that their sourcing decisions align with their operational needs and sustainability goals.
As the demand for frp cable trays continues to rise in various industries, especially in renewable energy and construction, leveraging strategic sourcing will become increasingly crucial. Engaging with manufacturers who demonstrate innovation and adaptability will provide a competitive edge.
Looking ahead, international B2B buyers are encouraged to actively seek partnerships that foster collaboration and transparency. By prioritizing these values, businesses can navigate the evolving landscape of frp cable tray manufacturing with confidence, ensuring they are well-positioned to meet future challenges and opportunities.