Discover Top Gardening Tool Manufacturers: Save Costs in 2025
Introduction: Navigating the Global Market for gardening tool manufacturer
In today’s rapidly evolving market, sourcing high-quality gardening tools can be a daunting task for international B2B buyers, particularly those in regions like Africa, South America, the Middle East, and Europe. The challenge lies not only in identifying reliable manufacturers but also in understanding the diverse applications and specifications required for different gardening tasks. This comprehensive guide on gardening tool manufacturers aims to equip buyers with actionable insights, covering everything from the types of tools available, their specific applications, to effective supplier vetting processes and cost considerations.
By delving into the nuances of gardening tools, this guide empowers businesses to make informed purchasing decisions that align with their operational needs and budgetary constraints. Whether you are a buyer in Brazil seeking eco-friendly solutions or a distributor in Nigeria looking to expand your product range, understanding the global market landscape is crucial. We will explore key factors such as market trends, technological advancements in gardening tools, and strategies for establishing fruitful supplier relationships.
This resource serves as a roadmap, helping you navigate the complexities of the gardening tool supply chain, ensuring that you not only meet the demands of your customers but also enhance your competitive edge in the market. Prepare to transform your sourcing strategy and foster growth in your gardening business with the insights provided in this guide.
Understanding gardening tool manufacturer Types and Variations
Type Name | Key Distinguishing Features | Primary B2B Applications | Brief Pros & Cons for Buyers |
---|---|---|---|
Hand Tool Manufacturers | Focus on manual tools like pruners, shovels | Nurseries, landscaping companies | Pros: Affordable, easy to use. Cons: Limited durability compared to powered tools. |
Power Tool Manufacturers | Production of electric/gas-powered tools | Large-scale agricultural operations | Pros: High efficiency, saves time. Cons: Higher initial investment, maintenance required. |
Garden Accessory Manufacturers | Production of accessories like gloves and aprons | Retailers, garden centers | Pros: Complements main tools, enhances user experience. Cons: Lower profit margins. |
Specialty Tool Manufacturers | Production of tools for specific tasks (e.g., bonsai, hydroponics) | Specialized gardening businesses | Pros: Niche market appeal, tailored solutions. Cons: Limited market size. |
Eco-Friendly Tool Manufacturers | Focus on sustainable materials and practices | Environmentally conscious buyers | Pros: Appeals to eco-friendly consumers. Cons: Potentially higher costs. |
What Are the Characteristics of Hand Tool Manufacturers?
Hand tool manufacturers specialize in creating manual gardening tools such as pruners, hoes, and shovels. These tools are essential for smaller-scale gardening operations, nurseries, and landscaping companies. When purchasing, B2B buyers should consider the ergonomic design, material quality, and ease of replacement parts. While hand tools are generally more affordable and user-friendly, they may not offer the durability needed for heavy-duty tasks.
How Do Power Tool Manufacturers Differ?
Power tool manufacturers produce equipment like electric trimmers, tillers, and gas-powered mowers. These tools are typically used in large-scale agricultural operations where efficiency is paramount. Buyers should evaluate the power output, battery life, and service availability when selecting these tools. Although power tools significantly reduce labor time, they require a higher initial investment and ongoing maintenance, which can be a consideration for budget-conscious businesses.
What Should Buyers Know About Garden Accessory Manufacturers?
Garden accessory manufacturers focus on items that enhance the gardening experience, such as gloves, aprons, and tool belts. These products are often sold through retailers and garden centers. B2B buyers should prioritize quality, comfort, and brand reputation when sourcing these accessories. While they may offer lower profit margins compared to primary tools, they can be bundled with tool sales to increase overall revenue.
Why Consider Specialty Tool Manufacturers?
Specialty tool manufacturers create products designed for specific gardening tasks, such as bonsai trimming or hydroponic gardening. These tools cater to niche markets, making them ideal for specialized gardening businesses. Buyers should assess the uniqueness of the product offering and the potential demand within their target market. Although these tools can command higher prices, the limited market size may restrict sales volume.
What Are the Benefits of Eco-Friendly Tool Manufacturers?
Eco-friendly tool manufacturers emphasize sustainable materials and environmentally friendly practices in their production processes. These tools appeal to environmentally conscious buyers, particularly in regions where sustainability is a key concern. B2B buyers should consider the sourcing practices and certifications of these manufacturers. While eco-friendly tools may come with a higher price tag, they can enhance brand loyalty and attract a growing segment of eco-aware consumers.
Related Video: 12 Essential Gardening Tools for Beginner and Advanced Gardeners
Key Industrial Applications of gardening tool manufacturer
Industry/Sector | Specific Application of Gardening Tool Manufacturer | Value/Benefit for the Business | Key Sourcing Considerations for this Application |
---|---|---|---|
Agriculture | Hand tools for small-scale farmers | Enhances efficiency and productivity in crop management | Durability, cost-effectiveness, and availability of spare parts |
Landscaping | Professional-grade landscaping tools | Improves service quality and client satisfaction | Ergonomics, weight, and ease of use |
Horticulture | Specialized tools for nurseries | Supports plant health and growth, leading to higher yields | Variety of tools, compatibility with different plant types |
Municipal Services | Tools for public parks and gardens | Maintains aesthetic appeal and community satisfaction | Bulk purchasing options and long-term warranty |
Retail Gardening | Consumer-grade tools for garden centers | Attracts customers with quality products | Brand reputation, product variety, and price competitiveness |
How Are Gardening Tools Applied in Agriculture?
In the agriculture sector, gardening tool manufacturers provide essential hand tools that cater to small-scale farmers, especially in regions like Africa and South America. These tools, such as hoes, shovels, and pruners, significantly enhance efficiency in crop management, allowing farmers to work faster and with less physical strain. B2B buyers should consider the durability and cost-effectiveness of these tools, as well as the availability of spare parts to ensure longevity and minimize downtime in operations.
What Role Do Gardening Tools Play in Landscaping?
Landscaping professionals rely on high-quality, professional-grade gardening tools to deliver superior service to their clients. Tools such as hedge trimmers, lawnmowers, and rakes are crucial for maintaining the aesthetic appeal of outdoor spaces. The value of investing in these tools lies in their ability to improve service quality, leading to increased client satisfaction and repeat business. Buyers should prioritize ergonomics and weight, as tools that are easy to handle can reduce fatigue and enhance productivity.
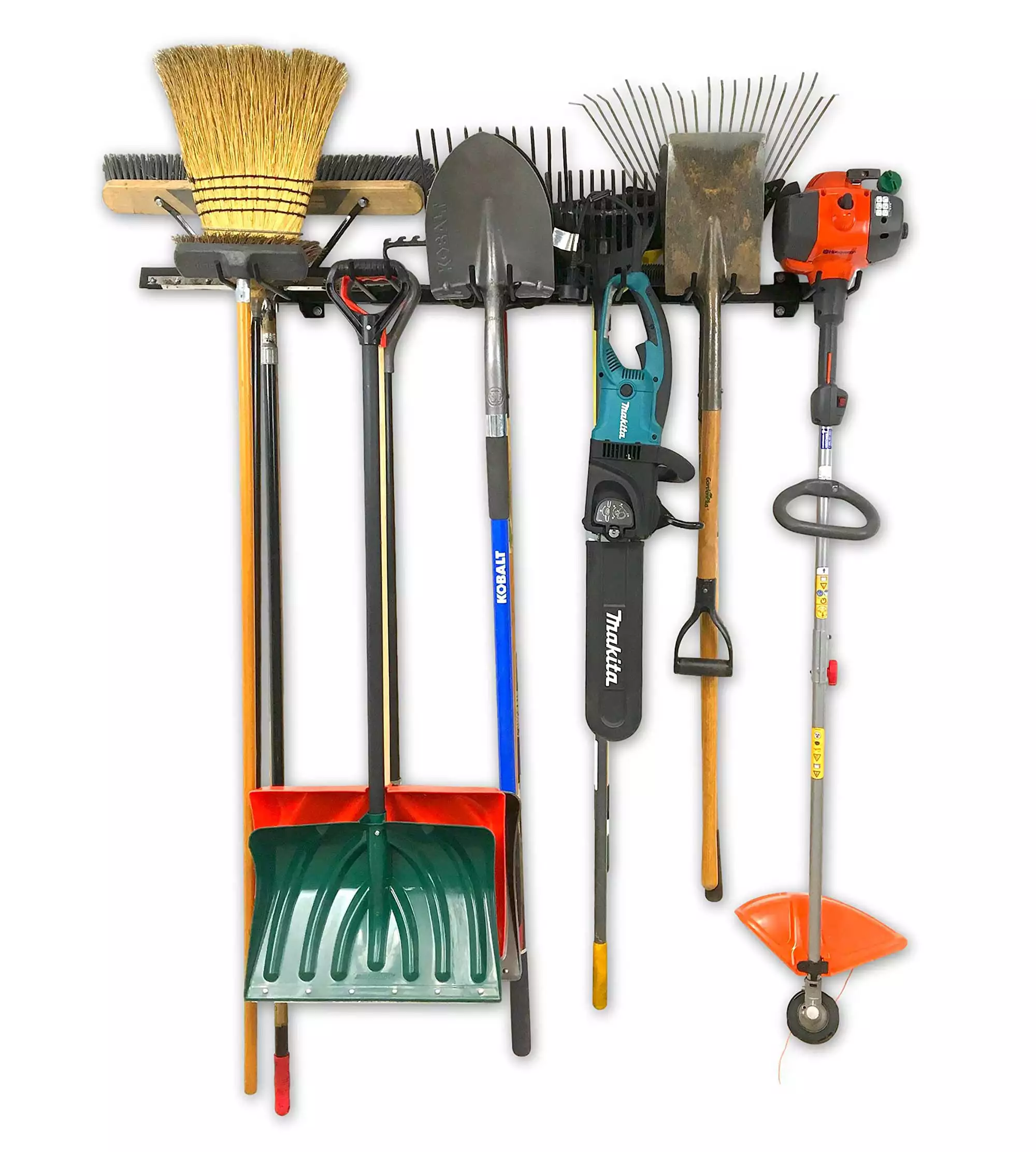
A stock image related to gardening tool manufacturer.
How Are Gardening Tools Utilized in Horticulture?
In horticulture, specialized tools designed for nurseries are vital for supporting plant health and growth. These tools, including grafting knives and transplanting spades, enable horticulturists to manage delicate plants effectively, ensuring higher yields and better quality produce. International buyers must consider the variety of tools available and their compatibility with different plant types, as this can significantly impact the success of their horticultural endeavors.
Why Are Gardening Tools Important for Municipal Services?
Municipal services utilize gardening tools to maintain public parks and gardens, which are essential for community aesthetics and well-being. High-quality tools help ensure that these public spaces are well-kept, thereby enhancing community satisfaction and encouraging public use. When sourcing tools for municipal applications, buyers should explore bulk purchasing options and look for suppliers that offer long-term warranties, ensuring that investments are protected over time.
How Do Gardening Tools Benefit Retail Gardening?
Retail gardening centers benefit from offering consumer-grade tools that attract customers looking for quality products for their personal gardens. Tools such as trowels, watering cans, and seeders not only enhance the gardening experience for consumers but also drive sales for the business. B2B buyers in this sector should focus on brand reputation, product variety, and price competitiveness to effectively meet consumer demands and stay ahead in a competitive market.
Related Video: Uses Technology in the Conduct of Survey || Joel Vacalares
3 Common User Pain Points for ‘gardening tool manufacturer’ & Their Solutions
Scenario 1: Sourcing High-Quality Gardening Tools in Emerging Markets
The Problem: B2B buyers in regions such as Africa and South America often struggle to find reliable suppliers of high-quality gardening tools. The challenge is exacerbated by limited access to information about manufacturers and concerns over product durability, especially in climates that can be harsh on equipment. Buyers may also face issues with inconsistent product quality and after-sales support, leading to frustration and potential losses in their business operations.
The Solution: To effectively source high-quality gardening tools, buyers should prioritize manufacturers with a proven track record in their specific market. Researching manufacturers who have experience supplying to similar climates can provide insights into the durability and suitability of their products. Establishing direct communication with manufacturers can help clarify specifications, warranties, and after-sales services. Utilizing platforms like trade shows or industry-specific online marketplaces can also facilitate connections with reputable suppliers. Additionally, buyers should consider requesting samples before making large orders to evaluate the quality firsthand.
Scenario 2: Navigating Import Regulations and Logistics for Gardening Tools
The Problem: International buyers often encounter complex import regulations and logistics challenges when sourcing gardening tools from foreign manufacturers. This can lead to delays, unexpected costs, and compliance issues, particularly in regions with stringent customs regulations, such as the Middle East and Europe. The lack of clarity on shipping logistics, tariffs, and import duties can complicate the purchasing process and negatively impact timelines.
The Solution: To navigate these challenges, buyers should familiarize themselves with the import regulations of their home country and the country of the manufacturer. Engaging with a local customs broker or logistics expert can provide valuable insights and ensure compliance with all necessary regulations. Additionally, buyers should consider working with manufacturers who have experience exporting to their region, as these companies are likely to understand the intricacies of shipping logistics and can assist in handling necessary documentation. Establishing a clear line of communication regarding shipping timelines and costs upfront can also help mitigate delays and unexpected expenses.
Scenario 3: Ensuring Sustainable Practices in Gardening Tool Manufacturing
The Problem: With an increasing focus on sustainability, B2B buyers are increasingly concerned about the environmental impact of the gardening tools they purchase. Many buyers from Europe and other environmentally conscious markets seek products that are made from sustainable materials and produced through ethical manufacturing practices. However, it can be challenging to find manufacturers who are transparent about their sustainability efforts.
The Solution: Buyers should actively seek manufacturers that prioritize sustainable practices and can provide certifications or documentation to support their claims. Engaging in direct conversations with potential suppliers about their sourcing of materials, production processes, and waste management strategies can provide clarity on their commitment to sustainability. Additionally, buyers can consider forming partnerships with manufacturers who offer eco-friendly product lines or who are involved in environmental initiatives. Utilizing platforms that specialize in sustainable products can also assist buyers in identifying and sourcing from environmentally responsible manufacturers, ensuring that their purchases align with their sustainability goals.
Strategic Material Selection Guide for gardening tool manufacturer
What Are the Key Properties of Common Materials Used in Gardening Tools?
When selecting materials for gardening tools, manufacturers must consider several key properties that affect product performance. The most common materials include stainless steel, carbon steel, aluminum, and plastic. Each material has unique characteristics that influence durability, cost, and suitability for various gardening applications.
How Does Stainless Steel Perform in Gardening Tools?
Stainless steel is favored for its excellent corrosion resistance and durability. It can withstand harsh environmental conditions, making it ideal for tools exposed to moisture and soil. The temperature rating for stainless steel is high, which allows it to maintain integrity even under extreme conditions.
Pros:
– Highly durable and resistant to rust and corrosion.
– Easy to clean, which is essential for maintaining hygiene in gardening tools.
Cons:
– Generally more expensive than other materials.
– Can be heavier, which may affect user comfort during prolonged use.
Impact on Application: Stainless steel tools are particularly suitable for applications involving wet soils or when working with acidic materials, as they won’t degrade over time.
Considerations for International Buyers: Compliance with international standards such as ASTM and DIN is crucial. Buyers in regions like Europe and the Middle East may prefer tools made from stainless steel due to its longevity and performance.
What Are the Benefits and Drawbacks of Carbon Steel?
Carbon steel is another popular choice for gardening tools due to its strength and edge retention. It is often used for blades and cutting tools because it can be sharpened to a fine edge.
Pros:
– Excellent sharpness and edge retention.
– Generally less expensive than stainless steel.
Cons:
– Prone to rust if not properly maintained.
– Requires regular oiling to prevent corrosion.
Impact on Application: Carbon steel is best suited for dry conditions or applications where tools can be cleaned and dried immediately after use.
Considerations for International Buyers: In regions like Africa and South America, where humidity can be high, buyers should consider the maintenance requirements of carbon steel tools to ensure longevity.
Why Is Aluminum a Viable Option for Gardening Tools?
Aluminum is lightweight and resistant to corrosion, making it an attractive option for gardening tools that require frequent handling. Its low density allows for easy maneuverability.
Pros:
– Lightweight and easy to handle.
– Resistant to corrosion, making it suitable for various weather conditions.
Cons:
– Less durable than steel options, which may lead to bending under heavy use.
– Can be more expensive than plastic alternatives.
Impact on Application: Aluminum tools are ideal for light-duty gardening tasks and are often used in hand tools like trowels and cultivators.
Considerations for International Buyers: Buyers should ensure that aluminum tools meet regional standards for durability, especially in demanding environments found in parts of Africa and South America.
What Role Does Plastic Play in Gardening Tool Manufacturing?
Plastic is commonly used for gardening tools due to its versatility and cost-effectiveness. It is often used in handles and lightweight tools.
Pros:
– Cost-effective and lightweight.
– Resistant to corrosion and easy to mold into various shapes.
Cons:
– Less durable than metal tools; can break under stress.
– Limited temperature resistance, which may affect performance in extreme conditions.
Impact on Application: Plastic tools are suitable for light gardening tasks and are often used in educational or casual gardening settings.
Considerations for International Buyers: Buyers should check for compliance with safety standards and durability tests, especially in regions with high UV exposure, which can degrade plastic over time.
Summary Table of Material Selection for Gardening Tools
Material | Typical Use Case for gardening tool manufacturer | Key Advantage | Key Disadvantage/Limitation | Relative Cost (Low/Med/High) |
---|---|---|---|---|
Stainless Steel | Heavy-duty tools, pruners, and shovels | Excellent corrosion resistance | Higher cost and weight | High |
Carbon Steel | Blades and cutting tools | Sharpness and edge retention | Prone to rust without maintenance | Medium |
Aluminum | Hand tools like trowels and cultivators | Lightweight and corrosion-resistant | Less durable under heavy use | Medium |
Plastic | Lightweight tools and handles | Cost-effective and versatile | Limited durability and temperature resistance | Low |
This strategic material selection guide offers actionable insights for international B2B buyers, helping them make informed decisions based on their specific market needs and environmental conditions.
In-depth Look: Manufacturing Processes and Quality Assurance for gardening tool manufacturer
What Are the Key Stages in the Manufacturing Process of Gardening Tools?
Manufacturing gardening tools involves several critical stages that ensure both efficiency and quality. The primary stages include:
-
Material Preparation: This is the initial phase where raw materials such as metals (steel, aluminum), plastics, and rubber are sourced and prepped. Material quality is paramount; suppliers often need to provide certification of material properties to meet international standards.
-
Forming: In this stage, the prepared materials are shaped into the desired forms using techniques such as forging, casting, or stamping. For instance, steel tools may undergo forging to enhance strength and durability. Advanced technologies like CNC machining are increasingly used for precision.
-
Assembly: After forming, the components are assembled. This may include attaching handles to blades or combining various parts of multi-functional tools. Effective assembly lines ensure that tools are not only correctly assembled but also meet ergonomic standards for user comfort.
-
Finishing: This final stage involves surface treatments such as powder coating, painting, or galvanizing to improve aesthetics and prevent corrosion. Quality checks are crucial here to ensure the finish is uniform and durable.
How Is Quality Assurance Implemented in Gardening Tool Manufacturing?
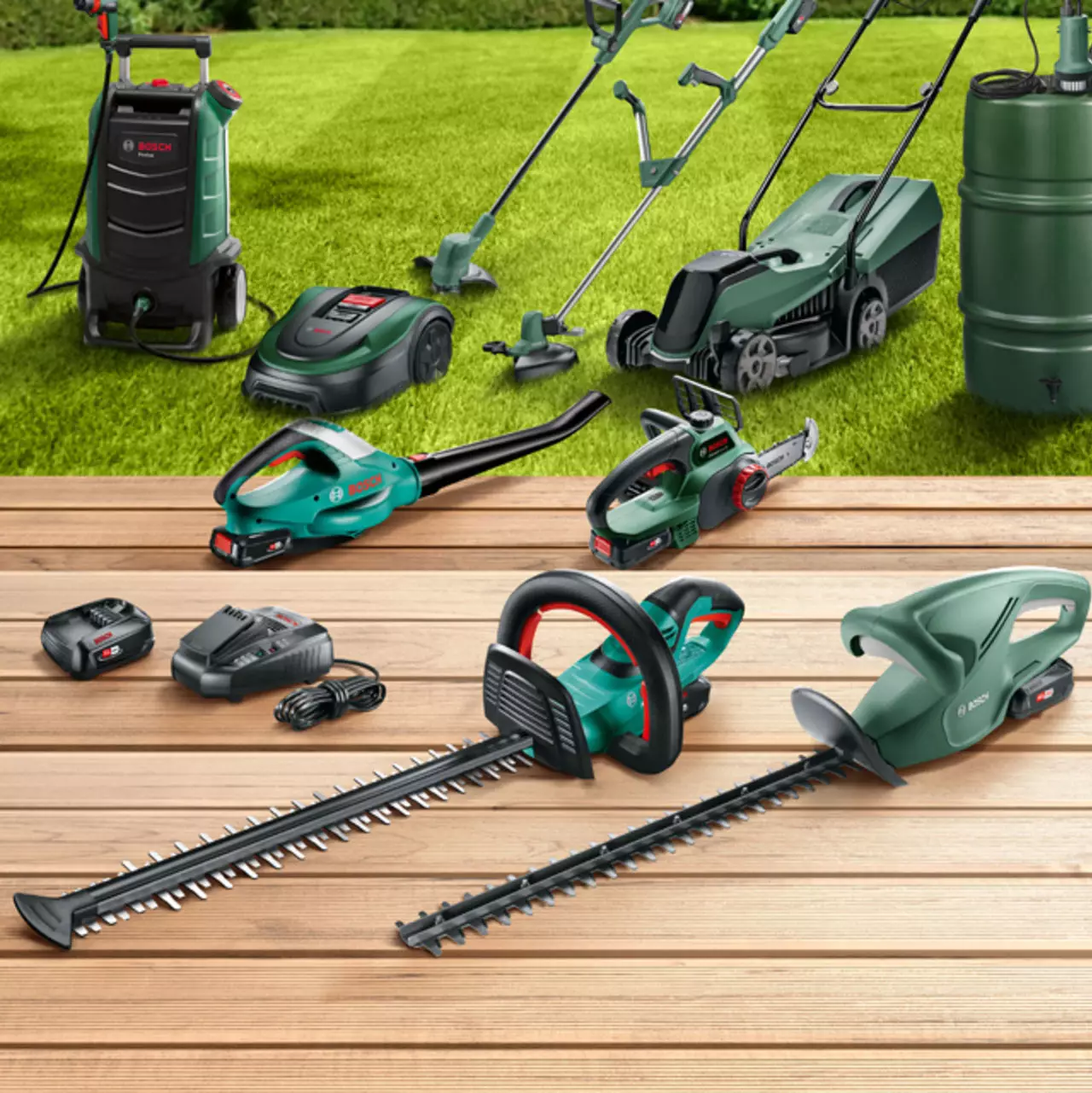
A stock image related to gardening tool manufacturer.
Quality assurance (QA) in gardening tool manufacturing is vital for maintaining product standards and ensuring customer satisfaction. The process typically adheres to several international and industry-specific standards, including:
-
ISO 9001: This internationally recognized standard focuses on quality management systems (QMS). Compliance indicates that the manufacturer has effective processes in place to consistently provide products that meet customer and regulatory requirements.
-
CE Marking: For products sold in the European market, CE marking signifies compliance with safety, health, and environmental protection standards.
-
API Standards: For specific tools used in agriculture, API (American Petroleum Institute) standards may apply, especially for tools interacting with chemicals.
What Are the Key Quality Control Checkpoints During Manufacturing?
Quality control (QC) checkpoints are essential for ensuring that products meet the required specifications throughout the manufacturing process. Common QC checkpoints include:
-
Incoming Quality Control (IQC): This involves inspecting raw materials upon arrival to ensure they meet specifications before they enter the production line. This step is crucial for preventing defects in the final product.
-
In-Process Quality Control (IPQC): During manufacturing, ongoing inspections are conducted at various stages to identify defects early. This may include checking dimensions, tolerances, and assembly quality.
-
Final Quality Control (FQC): Once the tools are fully assembled, a final inspection is performed. This may involve functional testing, visual inspections, and verification of compliance with standards like ISO and CE.
What Testing Methods Are Commonly Used in Gardening Tool Quality Assurance?
Several testing methods are employed to ensure that gardening tools perform as expected and meet safety standards:
-
Mechanical Testing: Tools are subjected to stress tests to determine their strength and durability. This includes tensile testing, impact testing, and fatigue testing.
-
Corrosion Resistance Testing: Given that gardening tools are often exposed to moisture, tests like salt spray testing are conducted to evaluate how well tools resist rust and corrosion.
-
Ergonomics Testing: Tools are tested for user comfort and usability, ensuring that handles are appropriately shaped and sized for ease of use.
How Can B2B Buyers Verify Supplier Quality Control?
For international B2B buyers, particularly from regions like Africa, South America, the Middle East, and Europe, verifying the quality control processes of suppliers is crucial. Here are actionable steps:
-
Conduct Supplier Audits: Regular audits can provide insight into the supplier’s manufacturing practices, adherence to quality standards, and overall operational efficiency.
-
Request Quality Control Reports: Suppliers should provide documentation of their QC processes, including inspection results and compliance certifications. This transparency helps buyers assess reliability.
-
Third-Party Inspections: Engaging third-party inspection services can offer an unbiased evaluation of the manufacturing process and product quality before shipment.
What Nuances Should International Buyers Consider Regarding Quality Control?
When dealing with suppliers from different regions, international B2B buyers must navigate various nuances:
-
Cultural Differences: Understanding the local culture can help in negotiating and establishing trust with suppliers. This can influence how QC processes are perceived and executed.
-
Regulatory Compliance: Different regions may have varying regulations regarding product safety and quality. Buyers should ensure that their suppliers are compliant with both local and international standards relevant to their market.
-
Supply Chain Logistics: Buyers should consider the logistics of sourcing materials and finished products, as delays or quality issues can arise from disruptions in the supply chain.
Conclusion: Ensuring Quality in Gardening Tool Manufacturing
In summary, understanding the manufacturing processes and quality assurance measures in gardening tool production is crucial for international B2B buyers. By focusing on key stages of manufacturing, implementing robust QC checkpoints, and ensuring compliance with relevant standards, manufacturers can produce high-quality tools that meet the expectations of diverse markets. Buyers must take proactive steps to verify supplier quality control, considering the unique challenges and opportunities presented by different regions.
Practical Sourcing Guide: A Step-by-Step Checklist for ‘gardening tool manufacturer’
In today’s global marketplace, sourcing gardening tools requires a strategic approach to ensure quality, reliability, and value. This guide provides a step-by-step checklist designed specifically for B2B buyers in regions such as Africa, South America, the Middle East, and Europe. By following these steps, buyers can navigate the complexities of procurement and establish fruitful partnerships with gardening tool manufacturers.
Step 1: Define Your Technical Specifications
Before engaging with suppliers, clearly outline the technical specifications of the gardening tools you need. This includes dimensions, materials, and functionalities. Detailed specifications help in filtering suppliers who can meet your requirements and ensure that you receive products that align with your operational needs.
- Consider the end-use: Are the tools intended for commercial landscaping or personal gardening? This will impact the durability and quality required.
- List essential features: Identify specific features that are critical for your target market, such as ergonomic designs or eco-friendly materials.
Step 2: Conduct Market Research
Understanding the market landscape is crucial for informed decision-making. Research potential suppliers and their reputation in the industry. Look for reviews, ratings, and feedback from previous clients.
- Utilize trade platforms: Websites like Alibaba and Global Sources can provide insights into various manufacturers.
- Engage with industry forums: These platforms can offer real-time feedback and recommendations from other B2B buyers.
Step 3: Evaluate Potential Suppliers
Before committing to any supplier, it’s essential to conduct a thorough evaluation. Request company profiles, case studies, and references from buyers in similar industries or regions. This step is critical to ensure that the supplier has a proven track record.
- Assess their production capabilities: Verify if they can handle your order volume and specific requirements.
- Check compliance and certifications: Ensure that the supplier adheres to international standards and regulations relevant to gardening tools.
Step 4: Request Samples
Once you narrow down your list of suppliers, request samples of the tools you intend to procure. This allows you to assess the quality firsthand and determine if they meet your specifications.
- Evaluate functionality: Test the tools for usability, durability, and comfort.
- Inspect materials: Ensure that the materials used align with your sustainability goals, if applicable.
Step 5: Negotiate Terms and Pricing
Effective negotiation can lead to better pricing and terms that benefit both parties. Be clear about your budget constraints and expectations regarding lead times and payment terms.
- Discuss bulk discounts: If you’re planning to place large orders, inquire about potential discounts.
- Clarify shipping and handling costs: Ensure all logistics are discussed upfront to avoid unexpected expenses later.
Step 6: Finalize the Contract
Once you’ve settled on a supplier, it’s time to formalize the agreement. A well-structured contract protects both parties and outlines all terms of the deal, including delivery timelines, payment schedules, and quality expectations.
- Include clauses for quality assurance: Specify what actions will be taken if the products do not meet agreed standards.
- Consider dispute resolution options: Outline how disputes will be handled to avoid potential conflicts in the future.
Step 7: Establish a Relationship for Long-Term Collaboration
Building a strong relationship with your supplier can lead to better service and potential future negotiations. Maintain open communication and provide feedback on the products received.
- Schedule regular reviews: Periodically assess the performance of the supplier to ensure ongoing satisfaction.
- Explore opportunities for collaboration: Discuss potential product innovations or customizations that could benefit both parties.
By following this structured checklist, B2B buyers can streamline their sourcing process for gardening tools, ensuring they select the best manufacturers to meet their needs.
Comprehensive Cost and Pricing Analysis for gardening tool manufacturer Sourcing
What Are the Key Cost Components in Gardening Tool Manufacturing?
When sourcing gardening tools, understanding the cost structure is essential for making informed purchasing decisions. The primary cost components include:
-
Materials: This is often the largest expense, comprising raw materials such as steel, aluminum, and plastics. Prices can fluctuate based on market demand and availability, so buyers should consider sourcing from regions with stable supply chains.
-
Labor: Labor costs vary significantly by region. In countries like Brazil and Nigeria, labor may be less expensive compared to Europe. However, it’s essential to factor in the skill level required for manufacturing quality gardening tools.
-
Manufacturing Overhead: This includes costs associated with utilities, facility maintenance, and administrative expenses. Efficient manufacturing processes can help reduce these costs.
-
Tooling: The initial investment in molds and machinery can be substantial. However, high-quality tooling can lead to better production efficiency and lower per-unit costs over time.
-
Quality Control (QC): Implementing strict QC measures ensures that products meet industry standards and specifications, which can prevent costly returns and enhance customer satisfaction.
-
Logistics: Transportation costs can vary based on the distance from the manufacturing site to the buyer’s location. Understanding the best shipping methods and routes can lead to significant savings.
-
Margin: Manufacturers typically add a margin to cover costs and ensure profitability. This margin can vary based on competition and market demand.
How Do Price Influencers Affect Gardening Tool Sourcing?
Several factors influence the pricing of gardening tools, and being aware of these can help buyers negotiate better deals:
-
Volume and Minimum Order Quantity (MOQ): Larger orders often lead to lower per-unit costs. Buyers should evaluate their needs and consider bulk purchasing to maximize savings.
-
Specifications and Customization: Customized tools may incur additional costs. Buyers should clearly define their requirements to avoid unexpected price increases.
-
Materials and Quality Certifications: Tools made from higher-quality materials or those that meet specific certifications (like ISO standards) may come at a premium. Buyers should balance quality with cost to meet their target market’s expectations.
-
Supplier Factors: The reputation and reliability of suppliers can impact pricing. Established suppliers may offer better terms due to their experience and lower risk of production issues.
-
Incoterms: Understanding shipping terms can affect overall costs. Incoterms dictate who is responsible for shipping, insurance, and tariffs, so clarifying these details can prevent misunderstandings and additional charges.
What Are the Best Negotiation Tips for International B2B Buyers?
Negotiating effectively is crucial for securing favorable pricing and terms. Here are some actionable tips for international buyers from Africa, South America, the Middle East, and Europe:
-
Research and Prepare: Understand the market pricing for gardening tools in your region. This knowledge allows you to negotiate from a position of strength.
-
Emphasize Total Cost of Ownership (TCO): Discuss not only the initial purchase price but also the long-term costs associated with maintenance, replacement, and logistics. Highlighting TCO can persuade suppliers to offer better terms.
-
Build Relationships: Establishing a good rapport with suppliers can lead to more favorable pricing and terms. Consider long-term partnerships rather than one-off transactions.
-
Be Clear About Expectations: Clearly communicate your needs and expectations regarding quality and delivery times. This clarity can help avoid disputes and ensure smoother transactions.
-
Consider Local Regulations: Familiarize yourself with import tariffs and regulations in your country. This knowledge can aid in negotiating prices that account for these additional costs.
Conclusion
While pricing for gardening tools can vary widely based on several factors, a comprehensive understanding of the cost components and price influencers can empower B2B buyers to make informed decisions. By leveraging negotiation strategies and considering the total cost of ownership, buyers can optimize their sourcing process and achieve better value in their investments. Keep in mind that prices are indicative and may vary based on market conditions and supplier negotiations.
Alternatives Analysis: Comparing gardening tool manufacturer With Other Solutions
When considering the procurement of gardening tools, it is essential for international B2B buyers to explore alternatives that may offer similar functionalities or advantages. This analysis compares traditional gardening tool manufacturers with alternative solutions such as automated gardening systems and rental services. Understanding these options can guide buyers in making informed decisions that align with their business objectives and operational needs.
Comparison Aspect | Gardening Tool Manufacturer | Automated Gardening Systems | Tool Rental Services |
---|---|---|---|
Performance | High quality, durable tools for manual gardening tasks | Enhanced efficiency with automation for tasks like watering and weeding | Access to a wide variety of tools as needed |
Cost | Initial investment can be high, but long-term savings on tool life | Higher upfront costs due to technology and installation | Lower initial costs but ongoing rental fees |
Ease of Implementation | Requires training and knowledge of gardening | May require setup and technical understanding | Simple process, tools delivered as needed |
Maintenance | Regular maintenance needed to keep tools functional | Requires occasional software updates and system checks | No maintenance; tools are returned after use |
Best Use Case | Ideal for traditional gardening practices and smaller operations | Best for larger operations or those seeking efficiency | Suitable for businesses with occasional gardening needs |
What Are the Pros and Cons of Automated Gardening Systems?
Automated gardening systems represent a modern approach to gardening, utilizing technology to streamline processes such as irrigation and pest control. The primary advantage of these systems is their efficiency; they can significantly reduce labor costs and time spent on routine tasks. However, the initial investment can be substantial, and there may be a learning curve for staff unfamiliar with the technology. Additionally, these systems may not provide the same tactile experience as traditional gardening, which can be a drawback for businesses focused on hands-on cultivation.
How Do Tool Rental Services Compare?
Tool rental services offer a flexible and cost-effective solution for businesses that require gardening tools on an as-needed basis. This option allows companies to access a diverse range of equipment without the commitment of purchasing and maintaining tools. The main advantage is the reduced upfront costs and no maintenance obligations. However, this model can lead to higher long-term costs if tools are frequently rented. Additionally, the availability of specific tools may vary, which could delay projects if a tool is not on hand when needed.
Conclusion: How Should B2B Buyers Choose the Right Gardening Solution?
When selecting between gardening tool manufacturers and alternative solutions, B2B buyers must evaluate their specific operational needs, budget constraints, and maintenance capabilities. For businesses with consistent gardening tasks, investing in high-quality tools from manufacturers may provide the best long-term value. Conversely, organizations looking for flexibility or those with sporadic gardening needs might benefit more from automated systems or rental services. Ultimately, the choice should align with the overall strategy and goals of the business, ensuring that the selected solution enhances productivity and efficiency in gardening operations.
Essential Technical Properties and Trade Terminology for gardening tool manufacturer
What Are the Essential Technical Properties for Gardening Tools?
Understanding the technical properties of gardening tools is crucial for B2B buyers, especially when sourcing products that meet specific operational standards. Here are some key specifications to consider:
1. Material Grade
Material grade refers to the specific type of metal, plastic, or wood used in the construction of gardening tools. Common materials include stainless steel, carbon steel, and high-density polyethylene (HDPE). The choice of material impacts durability, weight, and resistance to corrosion, which are vital for tools used in diverse climates across Africa, South America, the Middle East, and Europe.
2. Tolerance
Tolerance indicates the allowable variation in dimensions during manufacturing. For gardening tools, tight tolerances ensure that components fit together properly, enhancing performance and longevity. Buyers should seek manufacturers who can guarantee precise tolerances to avoid issues like tool misalignment or premature wear.
3. Ergonomic Design
Ergonomic design focuses on user comfort and efficiency. Tools should be designed to minimize strain on the body, particularly in regions where manual labor is prevalent. Features such as cushioned grips, adjustable handles, and lightweight materials can significantly improve user experience, making them attractive to buyers looking for tools that enhance productivity.
4. Weight Capacity
For tools like wheelbarrows or heavy-duty shovels, weight capacity is a critical property. It indicates the maximum load the tool can safely carry or handle. Understanding weight limits helps prevent accidents and ensures that the tools will perform well in demanding environments, which is particularly important for commercial buyers.
5. Rust Resistance
Rust resistance is crucial for tools exposed to moisture, especially in humid climates. Many manufacturers apply coatings or use stainless steel to enhance resistance to rust and corrosion. B2B buyers should prioritize tools with proven rust-resistant properties to ensure longevity and reduce replacement costs.
What Are Common Trade Terms in the Gardening Tools Industry?
Navigating the terminology used in the gardening tools industry can be challenging for international buyers. Here are some essential terms to know:
1. OEM (Original Equipment Manufacturer)
An OEM is a company that produces parts or equipment that may be marketed by another manufacturer. Understanding OEM relationships is vital for buyers looking to source high-quality tools that can be branded or customized for specific markets.
2. MOQ (Minimum Order Quantity)
MOQ refers to the smallest quantity of a product that a supplier is willing to sell. For B2B buyers, understanding MOQ is essential for budgeting and planning inventory. Higher MOQs may lead to cost savings per unit, but they also require careful stock management.
3. RFQ (Request for Quotation)
An RFQ is a document sent to suppliers to request pricing and terms for specific products or services. This is a crucial step for buyers to ensure they receive competitive pricing and understand the specifications and delivery timelines of the gardening tools they intend to purchase.
4. Incoterms
Incoterms (International Commercial Terms) define the responsibilities of buyers and sellers in international transactions. Understanding these terms is essential for international B2B buyers to clarify who bears the risk and cost during shipping and delivery. Common terms include FOB (Free On Board) and CIF (Cost, Insurance, and Freight).
5. Lead Time
Lead time is the amount of time it takes from placing an order to receiving the goods. For gardening tools, this can vary based on manufacturing location and shipping methods. Buyers should account for lead times when planning their procurement processes to avoid stock shortages during peak gardening seasons.
By familiarizing themselves with these essential technical properties and trade terms, international B2B buyers can make informed decisions, ensuring they select high-quality gardening tools that meet their operational needs.
Navigating Market Dynamics and Sourcing Trends in the gardening tool manufacturer Sector
What Are the Current Market Dynamics Affecting Gardening Tool Manufacturers?
The gardening tool manufacturing sector is experiencing significant transformations driven by various global factors. Notably, there is a rising demand for innovative tools that enhance efficiency and user experience. This shift is largely fueled by the increasing popularity of gardening as a hobby and its therapeutic benefits, especially during and post-pandemic. The global gardening market is projected to grow, with a particular surge in regions such as Africa, South America, the Middle East, and Europe, where urban gardening and sustainable practices are becoming more prevalent.
In terms of technology, the integration of smart tools equipped with IoT capabilities is emerging. These innovations provide users with real-time data on soil conditions and plant health, appealing to tech-savvy gardeners in both residential and commercial settings. Additionally, the rise of e-commerce platforms is reshaping how B2B buyers source gardening tools. Buyers from diverse regions can now access a broader range of products and suppliers, facilitating better price comparisons and streamlined procurement processes.
Moreover, sustainability is becoming a core consideration for international buyers. Manufacturers are increasingly adopting eco-friendly practices, with a focus on sustainable materials and production processes. This trend not only meets consumer demand but also aligns with global efforts to combat climate change.
How Is Sustainability Shaping Sourcing Trends in Gardening Tools?
Sustainability is no longer just a buzzword; it is a critical factor influencing sourcing decisions for B2B buyers in the gardening tool sector. Environmental concerns are driving manufacturers to minimize their carbon footprint and ensure that their supply chains are ethically managed. This includes sourcing materials that are renewable, recyclable, or biodegradable, which appeals to a growing demographic of environmentally conscious consumers.
The importance of ethical sourcing cannot be overstated. Buyers are increasingly scrutinizing their suppliers’ practices, seeking certifications that demonstrate compliance with environmental standards. Certifications such as ISO 14001 for environmental management and FSC (Forest Stewardship Council) for responsibly sourced wood are becoming essential for manufacturers aiming to build trust and credibility in the market.
Furthermore, the adoption of green materials, such as bamboo and recycled metals, is on the rise. These materials not only reduce the environmental impact but also cater to a market that values eco-friendly products. By prioritizing sustainability, manufacturers can differentiate themselves and align their offerings with the values of modern consumers, ultimately leading to enhanced brand loyalty and market competitiveness.
What Is the Historical Context of the Gardening Tool Manufacturing Sector?
The gardening tool manufacturing sector has evolved significantly from its rudimentary beginnings. Historically, tools were handcrafted from materials like wood and metal, serving basic agricultural needs. Over the centuries, as gardening transitioned from necessity to a popular leisure activity, the demand for more specialized and efficient tools surged.
The industrial revolution marked a pivotal point in the sector, introducing mass production techniques that made gardening tools more accessible. The latter half of the 20th century saw the rise of power tools and advanced materials, revolutionizing how gardening was approached. Today, manufacturers are not only focused on functionality but also on integrating technology and sustainability into their product lines, reflecting a broader shift towards a more informed and responsible consumer base.
In conclusion, understanding these market dynamics, sustainability trends, and the historical context can empower international B2B buyers to make informed sourcing decisions in the gardening tool sector, ultimately enhancing their competitive edge in an evolving marketplace.
Frequently Asked Questions (FAQs) for B2B Buyers of gardening tool manufacturer
-
How can I choose the right gardening tool manufacturer for my business?
When selecting a gardening tool manufacturer, consider their production capabilities, quality certifications, and reputation in the market. Look for manufacturers who specialize in the specific types of tools you need, such as hand tools, power tools, or sustainable options. Additionally, request samples to assess product quality and ensure they can meet your customization requirements. It’s also beneficial to read reviews or seek testimonials from other businesses that have worked with the manufacturer. -
What are the key factors to consider when vetting a gardening tool supplier?
Key factors include the supplier’s experience in the industry, compliance with international quality standards, and their ability to provide certifications (like ISO). Evaluate their production capacity, lead times, and minimum order quantities (MOQs) to ensure they align with your business needs. Communication is vital; a responsive supplier is often more reliable. Finally, consider their payment terms and logistics capabilities, especially if you are importing from different regions. -
What is the typical minimum order quantity (MOQ) for gardening tools?
MOQs can vary significantly based on the manufacturer and the specific tools you are interested in. Generally, MOQs for gardening tools range from 100 to 1,000 units per order. Some manufacturers may offer lower MOQs for custom designs, while others might require higher quantities for standard products. It’s advisable to discuss your needs directly with potential suppliers to negotiate terms that work for both parties. -
What are the best payment terms for international B2B transactions with gardening tool manufacturers?
Payment terms can include options like a deposit upfront (typically 30% to 50%) with the balance due upon shipment or delivery. For new relationships, consider using a letter of credit to mitigate risks. Some manufacturers may also accept payment through escrow services for additional security. Always clarify payment methods and terms before finalizing contracts to ensure transparency and avoid misunderstandings. -
How do I ensure quality assurance when sourcing gardening tools internationally?
To ensure quality, request samples from potential suppliers before placing large orders. Establish clear quality standards and specifications in your contracts. Consider conducting factory audits or hiring third-party inspection services to verify production processes and material quality. Additionally, set up a robust feedback loop with your supplier to address any quality issues promptly. -
What are the logistics considerations for importing gardening tools from manufacturers?
Logistics considerations include shipping methods, customs regulations, and delivery timelines. Choose a reliable freight forwarder experienced in handling gardening tools to navigate international shipping complexities. Ensure your supplier provides the necessary documentation for customs clearance. Discuss delivery terms (like FOB or CIF) to clarify who bears shipping costs and risks at various points in the process. -
How can I customize gardening tools to meet my market’s demands?
Many manufacturers offer customization options, such as branded packaging, unique tool designs, or specific material choices. When discussing customization, provide clear specifications and design ideas to your supplier. Be prepared to work closely with them during the prototyping phase to refine your designs. Establish a timeline for development and ensure they can accommodate your customization needs without significantly increasing lead times. -
What are the current trends in gardening tools that I should be aware of?
Current trends include the rise of eco-friendly gardening tools made from sustainable materials and ergonomic designs that enhance user comfort. There is also increasing demand for multi-functional tools that save space and improve efficiency. Smart gardening tools that integrate technology for better monitoring and maintenance are gaining popularity as well. Stay updated on these trends to align your product offerings with market demands and differentiate your business.
Important Disclaimer & Terms of Use
⚠️ Important Disclaimer
The information provided in this guide, including content regarding manufacturers, technical specifications, and market analysis, is for informational and educational purposes only. It does not constitute professional procurement advice, financial advice, or legal advice.
While we have made every effort to ensure the accuracy and timeliness of the information, we are not responsible for any errors, omissions, or outdated information. Market conditions, company details, and technical standards are subject to change.
B2B buyers must conduct their own independent and thorough due diligence before making any purchasing decisions. This includes contacting suppliers directly, verifying certifications, requesting samples, and seeking professional consultation. The risk of relying on any information in this guide is borne solely by the reader.
Strategic Sourcing Conclusion and Outlook for gardening tool manufacturer
What Are the Key Takeaways for B2B Buyers in the Gardening Tool Industry?
In conclusion, effective strategic sourcing is paramount for international B2B buyers looking to optimize their procurement processes in the gardening tool sector. Key takeaways include understanding local market demands, fostering relationships with reliable suppliers, and leveraging technology to streamline sourcing operations. By prioritizing quality, sustainability, and cost-effectiveness, buyers can secure a competitive edge in their respective markets.
How Can B2B Buyers Prepare for Future Trends in Gardening Tools?
As we look to the future, the gardening tool industry is poised for growth, particularly with the increasing trend towards sustainable gardening practices. International buyers from Africa, South America, the Middle East, and Europe, including countries like Brazil and Nigeria, should remain agile and adaptable to changing consumer preferences. Investing in innovative tools that cater to eco-friendly gardening will not only meet market demands but also align with global sustainability goals.
What Steps Should B2B Buyers Take to Enhance Their Sourcing Strategies?
Now is the time for B2B buyers to take action. By conducting thorough market research, engaging with diverse suppliers, and utilizing digital platforms for sourcing, companies can enhance their procurement strategies. Embrace the future of gardening tools by partnering with manufacturers who prioritize innovation and sustainability, ensuring that your business remains at the forefront of this evolving industry.