Discover Top Globe Valves Manufacturers: Cost-Saving Insights (2025)
Introduction: Navigating the Global Market for Globe Valves Manufacturers
Navigating the complexities of sourcing globe valves can be a significant challenge for international B2B buyers, especially those from regions like Africa, South America, the Middle East, and Europe, including countries such as Mexico and Turkey. With a vast array of manufacturers and product types, understanding which globe valves best meet your operational needs while also adhering to local regulations can be overwhelming. This guide aims to demystify the global market for globe valves manufacturers, offering insights into various types, applications, and critical supplier vetting processes.
In the subsequent sections, we will explore the different materials used in globe valve manufacturing, such as cast iron, bronze, and stainless steel, and their respective applications across industries like oil and gas, water treatment, and chemical processing. Additionally, we will provide actionable tips on evaluating potential suppliers, including considerations for quality certifications, lead times, and cost structures.
Armed with this comprehensive knowledge, B2B buyers will be empowered to make informed purchasing decisions that not only fulfill their technical requirements but also align with their strategic goals. By understanding the nuances of the globe valve market, you can ensure that your procurement process is efficient, cost-effective, and conducive to long-term operational success.
Understanding Globe Valves Manufacturers Types and Variations
Type Name | Key Distinguishing Features | Primary B2B Applications | Brief Pros & Cons for Buyers |
---|---|---|---|
Cast Steel Globe Valves | Durable, high strength, suitable for high-pressure systems | Oil & Gas, Petrochemical, Power Generation | Pros: High durability; Cons: Heavier and more expensive. |
Forged Steel Globe Valves | Compact design, better for high-pressure applications | Chemical Processing, Water Treatment | Pros: Stronger and lighter; Cons: Limited size options. |
Bronze Globe Valves | Corrosion-resistant, suitable for smaller pipelines | Marine, HVAC, Water Distribution | Pros: Excellent corrosion resistance; Cons: Lower pressure ratings. |
Stainless Steel Globe Valves | High resistance to corrosion and temperature variations | Food & Beverage, Pharmaceutical, Cryogenics | Pros: Clean and hygienic; Cons: Higher initial cost. |
Pressure Seal Globe Valves | Designed for high-pressure applications with a seal design | Power Plants, Oil Refineries | Pros: Effective sealing under pressure; Cons: More complex maintenance. |
What Are the Characteristics of Cast Steel Globe Valves?
Cast steel globe valves are known for their robustness and ability to withstand high pressures and temperatures, making them ideal for demanding environments such as oil and gas, petrochemical, and power generation industries. Their construction typically involves a solid cast, ensuring longevity and resistance to wear. When purchasing, buyers should consider the valve’s pressure rating and compatibility with the fluid being handled, as these factors will influence performance and safety.
How Do Forged Steel Globe Valves Differ from Other Types?
Forged steel globe valves are distinguished by their compact design and superior strength, making them suitable for high-pressure applications. They are often preferred in chemical processing and water treatment facilities due to their ability to maintain integrity under stress. Buyers should evaluate the valve’s size options and pressure ratings, as these factors can limit application in certain systems compared to larger cast steel variants.
Why Choose Bronze Globe Valves for Specific Applications?
Bronze globe valves are particularly favored in marine and HVAC applications due to their excellent corrosion resistance and ability to handle smaller pipelines effectively. They provide a reliable option for systems where exposure to moisture is common. However, their lower pressure ratings compared to steel variants mean buyers must assess the specific requirements of their application to ensure safe and effective operation.
What Are the Advantages of Stainless Steel Globe Valves?
Stainless steel globe valves are prized for their hygienic properties and resistance to both corrosion and temperature fluctuations, making them ideal for industries such as food and beverage, pharmaceuticals, and cryogenics. Their cleanliness and durability can justify the higher initial investment for companies focused on quality and safety. Buyers should consider the specific stainless steel grade to ensure compatibility with their operational environment.
When Should You Use Pressure Seal Globe Valves?
Pressure seal globe valves are designed specifically for high-pressure applications, featuring a unique sealing mechanism that enhances performance under extreme conditions. Commonly utilized in power plants and oil refineries, these valves require careful consideration regarding maintenance and installation due to their complexity. Buyers must weigh the benefits of effective sealing against potential maintenance challenges when selecting this type of valve for their operations.
Related Video: Valves Explained – Control Valve Types (Gate Valve, Globe Valve, Ball Valve, Butterfly Valve, etc.)!
Key Industrial Applications of Globe Valves Manufacturers
Industry/Sector | Specific Application of Globe Valves Manufacturers | Value/Benefit for the Business | Key Sourcing Considerations for this Application |
---|---|---|---|
Oil & Gas | Flow regulation in pipeline systems | Ensures precise flow control, enhancing safety and efficiency | Material compatibility with fluids, pressure ratings, and certifications |
Petrochemical | Throttling in chemical processing | Optimizes chemical reactions and minimizes waste | Chemical resistance, temperature ratings, and compliance with standards |
Water Treatment | Flow control in water distribution systems | Maintains water quality and system integrity | Corrosion resistance, size specifications, and maintenance requirements |
Power Generation | Pressure regulation in steam and gas systems | Increases operational reliability and energy efficiency | High-temperature ratings, material selection, and valve actuation types |
HVAC Systems | Balancing flow in heating and cooling systems | Enhances system performance and energy savings | Size, pressure drop specifications, and compatibility with system design |
How Are Globe Valves Used in the Oil & Gas Industry?
In the oil and gas sector, globe valves are essential for flow regulation in pipeline systems. They allow for precise control over fluid flow, which is critical for maintaining safety and operational efficiency. For international buyers, especially those in regions like Africa and the Middle East, sourcing valves that can withstand harsh environmental conditions is crucial. Buyers should consider materials that are compatible with the specific fluids being transported, as well as pressure ratings that meet industry standards.
What Role Do Globe Valves Play in Petrochemical Applications?
In petrochemical processing, globe valves are used for throttling applications, which regulate the flow of chemicals during various stages of production. This capability helps optimize chemical reactions, thereby minimizing waste and enhancing overall process efficiency. Buyers from South America and Europe should prioritize valves that offer chemical resistance and can handle high temperatures. Compliance with safety and environmental regulations is also a key consideration in sourcing these valves.
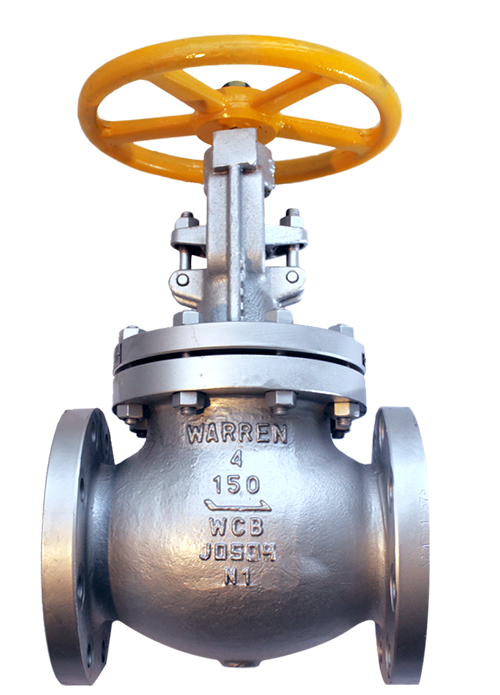
A stock image related to Globe Valves Manufacturers.
Why Are Globe Valves Important for Water Treatment?
Globe valves play a critical role in water treatment facilities by controlling the flow of water through distribution systems. They help maintain water quality and ensure the integrity of the entire system. For international buyers, particularly from Africa and Europe, selecting valves with high corrosion resistance and proper sizing is vital to ensure longevity and reliability. Additionally, understanding the maintenance requirements of these valves can lead to reduced downtime and operational costs.
How Do Globe Valves Enhance Power Generation Efficiency?

A stock image related to Globe Valves Manufacturers.
In power generation, globe valves are employed for pressure regulation in steam and gas systems. Their ability to control the flow effectively increases operational reliability and energy efficiency, which is paramount in this industry. Buyers, especially in the Middle East and Europe, should focus on high-temperature ratings and appropriate material selection to ensure optimal performance under varying operational conditions. The choice of valve actuation types also plays a significant role in overall system efficiency.
What Benefits Do Globe Valves Provide in HVAC Systems?
In HVAC systems, globe valves are utilized to balance flow in heating and cooling applications. This balancing is crucial for optimizing system performance and achieving energy savings. For international buyers, particularly in regions like Turkey and South America, it is important to consider the size and pressure drop specifications of the valves, as well as their compatibility with existing system designs. Proper sourcing can lead to enhanced comfort and reduced operational costs.
Related Video: How Globe Valves Work
3 Common User Pain Points for ‘Globe Valves Manufacturers’ & Their Solutions
Scenario 1: Sourcing Quality Globe Valves for Diverse Applications
The Problem: International B2B buyers often struggle to find high-quality globe valves that meet specific application requirements. This challenge is particularly acute for businesses in sectors like oil and gas or petrochemical industries, where the valves must withstand extreme pressures and temperatures. Buyers frequently encounter inconsistent quality from manufacturers, leading to potential failures and costly downtime. The difficulty in assessing the manufacturing standards and certifications of suppliers further complicates the sourcing process, especially for companies operating in regions with stringent regulatory frameworks.
The Solution: To effectively source quality globe valves, B2B buyers should prioritize manufacturers that provide comprehensive documentation, including Material Test Reports (MTRs) and compliance with international standards such as API and ASME. Engaging directly with manufacturers to discuss specific application needs can also yield better results. Buyers should conduct thorough due diligence, including factory visits or virtual inspections, to assess the production capabilities and quality control processes of potential suppliers. Building long-term relationships with reputable manufacturers can ensure consistent supply and quality, ultimately reducing the risk of failures in critical applications.
Scenario 2: Understanding Globe Valve Specifications and Performance
The Problem: Many B2B buyers face difficulties in understanding the technical specifications and performance characteristics of globe valves. This knowledge gap can lead to the selection of inappropriate valves for their systems, resulting in inefficiencies or failures. For instance, selecting a valve without considering factors such as flow coefficient (Cv), pressure drop, and material compatibility can have significant repercussions on system performance and longevity. Buyers often find the myriad of options overwhelming and may struggle to align technical specifications with operational needs.
The Solution: To bridge this knowledge gap, B2B buyers should invest time in educating themselves about the key performance indicators of globe valves. Manufacturers often provide technical resources, including catalogs, datasheets, and online tools to assist buyers in understanding specifications. Engaging with technical support teams from manufacturers can provide personalized guidance tailored to specific applications. Additionally, participating in industry webinars and workshops can enhance knowledge about the latest advancements in valve technology and application best practices, empowering buyers to make informed decisions.
Scenario 3: Navigating Lead Times and Supply Chain Disruptions
The Problem: Another common pain point for international B2B buyers is navigating lead times and supply chain disruptions associated with globe valve procurement. Recent global events have exacerbated these issues, leading to unpredictable delivery schedules and increased costs. Buyers often find themselves in a precarious position, needing valves urgently to maintain operational continuity, only to be met with lengthy delays from suppliers. This situation can be particularly detrimental for projects with strict timelines and budget constraints.
The Solution: To mitigate supply chain risks, buyers should adopt a proactive approach by establishing relationships with multiple suppliers to diversify their sourcing options. Maintaining an open line of communication with manufacturers can also provide insights into potential delays and allow for contingency planning. Buyers should consider forecasting their valve needs based on project timelines and stockpiling critical components where feasible. Utilizing just-in-time inventory strategies, alongside regular reviews of lead times and supplier performance, can help buyers navigate uncertainties in the supply chain while ensuring they have the necessary components available when needed.
Strategic Material Selection Guide for Globe Valves Manufacturers
When selecting materials for globe valves, international B2B buyers must consider various factors that affect performance, durability, and cost. The following analysis covers four common materials used in globe valve manufacturing: cast iron, carbon steel, stainless steel, and bronze. Each material has unique properties that influence its suitability for different applications.
What Are the Key Properties of Cast Iron for Globe Valves?
Cast iron is widely used in the manufacturing of globe valves due to its excellent machinability and good wear resistance. It typically has a temperature rating of up to 350°F (175°C) and can handle moderate pressure levels. Its corrosion resistance is limited, making it less suitable for aggressive media.
Pros & Cons: Cast iron is durable and cost-effective, ideal for applications involving water or non-corrosive fluids. However, its brittleness can lead to cracking under high-stress conditions, and it may not be suitable for high-pressure applications.
Impact on Application: Cast iron valves are commonly used in municipal water systems and HVAC applications. Buyers should ensure compatibility with the specific media being transported.
Considerations for International Buyers: Compliance with standards like ASTM A126 for cast iron is crucial. Buyers in regions like Africa and South America should consider local environmental conditions that may affect the longevity of cast iron valves.
How Does Carbon Steel Perform in Globe Valve Applications?
Carbon steel is another popular choice for globe valves, offering high strength and excellent pressure ratings, often exceeding 2,000 psi. It is suitable for temperatures up to 800°F (427°C) and exhibits good corrosion resistance when properly coated.
Pros & Cons: The primary advantage of carbon steel is its durability and high-pressure handling capability. However, it requires protective coatings to prevent rust, which can add to manufacturing complexity and cost.
Impact on Application: Carbon steel valves are ideal for oil and gas applications, where high pressure and temperature are common. Buyers must ensure that the selected coating is compatible with the specific media.
Considerations for International Buyers: Compliance with standards such as ASTM A216 is essential. Buyers from the Middle East, where high temperatures are prevalent, should prioritize carbon steel for its thermal resilience.
Why Choose Stainless Steel for Globe Valves?
Stainless steel offers superior corrosion resistance and is often used in applications involving aggressive chemicals or high-purity requirements. It maintains its integrity at temperatures up to 1,500°F (815°C) and can handle high pressures.
Pros & Cons: The main advantage of stainless steel is its resistance to corrosion, making it suitable for a wide range of applications. However, it is typically more expensive than other materials, which can be a limiting factor for budget-conscious buyers.
Impact on Application: Stainless steel valves are commonly found in pharmaceutical, food processing, and chemical industries. Buyers must consider the specific grade of stainless steel to ensure compatibility with the media.
Considerations for International Buyers: Compliance with standards like ASTM A312 is critical. European buyers, in particular, may prefer stainless steel due to stringent regulations on material safety and hygiene.
What Are the Benefits of Using Bronze in Globe Valves?
Bronze is known for its excellent corrosion resistance and is particularly effective in marine applications. It can withstand temperatures up to 400°F (204°C) and offers good pressure ratings.
Pros & Cons: Bronze valves are durable and resistant to seawater and other corrosive environments. However, they are typically more expensive than cast iron or carbon steel options, which may deter some buyers.
Impact on Application: Bronze is ideal for applications in marine environments and chemical processing where corrosion is a significant concern. Buyers should assess the specific media to ensure compatibility.
Considerations for International Buyers: Compliance with standards such as ASTM B62 is important. Buyers from coastal regions in Africa and South America should consider bronze for its long-lasting performance in corrosive environments.
Summary Table of Material Selection for Globe Valves
Material | Typical Use Case for Globe Valves Manufacturers | Key Advantage | Key Disadvantage/Limitation | Relative Cost (Low/Med/High) |
---|---|---|---|---|
Cast Iron | Municipal water systems, HVAC | Cost-effective, durable | Brittle, limited pressure rating | Low |
Carbon Steel | Oil and gas applications | High strength, good pressure rating | Requires protective coatings | Medium |
Stainless Steel | Pharmaceutical, food processing, chemical | Excellent corrosion resistance | Higher cost compared to others | High |
Bronze | Marine applications, chemical processing | Superior corrosion resistance | Higher cost than cast iron and steel | High |
This strategic material selection guide equips international B2B buyers with the insights needed to make informed decisions when sourcing globe valves, considering both performance requirements and regional compliance standards.
In-depth Look: Manufacturing Processes and Quality Assurance for Globe Valves Manufacturers
What Are the Key Stages in the Manufacturing Process of Globe Valves?
The manufacturing process of globe valves involves several critical stages, ensuring that the final product meets both functional and quality standards. Understanding these stages is essential for B2B buyers looking to source reliable valves for industrial applications.
-
Material Preparation
The first step in globe valve manufacturing is selecting the appropriate materials, which can include cast iron, stainless steel, or bronze. The chosen material undergoes rigorous quality checks to ensure it meets the necessary specifications. This stage may involve cutting and shaping raw materials into manageable sizes, ready for further processing. -
Forming Techniques
Globe valves are typically formed using casting, forging, or machining processes.
– Casting involves pouring molten metal into a mold to create the valve body. This method is cost-effective for large production runs.
– Forging is used for high-strength applications, where the metal is shaped under pressure, enhancing its mechanical properties.
– Machining involves removing material from a solid block to create precise dimensions and tolerances, ensuring the valve operates efficiently. -
Assembly Process
After the individual components are formed, they are assembled. This involves fitting the body, bonnet, and internal parts like the disc and seat. Proper assembly is critical, as any misalignment can lead to leaks or operational failures. During this phase, manufacturers may employ automated systems to enhance precision and efficiency. -
Finishing Touches
The final stage includes surface finishing, which can involve grinding, polishing, and applying protective coatings. This not only improves aesthetics but also enhances corrosion resistance and extends the valve’s lifespan.
How Do Globe Valve Manufacturers Ensure Quality Assurance?
Quality assurance (QA) is paramount in the manufacturing of globe valves, as these components play a crucial role in fluid control systems across various industries. Buyers should be aware of the following QA practices:
-
Adhering to International Standards
Many globe valve manufacturers comply with international standards such as ISO 9001, which outlines a framework for quality management systems. Additionally, industry-specific certifications like CE marking (for European markets) and API (American Petroleum Institute) standards ensure that products meet safety and performance criteria. -
Quality Control Checkpoints
Effective quality control involves multiple checkpoints throughout the manufacturing process:
– Incoming Quality Control (IQC): This stage verifies the quality of raw materials before they enter production. It includes testing for chemical composition and physical properties.
– In-Process Quality Control (IPQC): During manufacturing, ongoing inspections ensure that processes adhere to specified tolerances and standards.
– Final Quality Control (FQC): Once assembly is complete, the finished valves undergo comprehensive testing, including pressure testing and functional tests, to confirm they meet performance standards. -
Common Testing Methods for Globe Valves
Manufacturers utilize various testing methods to ensure reliability:
– Hydrostatic Testing: This checks the valve’s ability to withstand pressure without leaking.
– Functional Testing: Ensures the valve operates correctly under simulated conditions.
– Visual Inspections: Examines the exterior for defects and ensures proper finishing.
How Can B2B Buyers Verify Supplier Quality Control?
For international B2B buyers, especially those from Africa, South America, the Middle East, and Europe, verifying a supplier’s quality control processes is crucial. Here are actionable steps to ensure you select a reliable globe valve manufacturer:
-
Conduct Supplier Audits
Regular audits of potential suppliers can provide insights into their manufacturing processes and quality control systems. During these audits, buyers should assess compliance with international standards and review quality management documentation. -
Request Quality Assurance Documentation
Buyers should request relevant certifications, such as ISO 9001 or API standards, along with quality control reports. These documents provide evidence of the manufacturer’s commitment to quality. -
Engage Third-Party Inspection Services
Utilizing third-party inspection services can offer an unbiased assessment of a manufacturer’s quality control practices. These services often conduct inspections at various stages of production, ensuring compliance with agreed specifications. -
Evaluate Past Performance and References
Reviewing past performance and obtaining references from other clients can help gauge the reliability of a supplier. Look for testimonials regarding the quality of their globe valves and the effectiveness of their quality assurance processes.
What Are the Quality Control Nuances for International Buyers?
When sourcing globe valves from manufacturers across different regions, B2B buyers should be aware of specific nuances related to quality control:
-
Regional Standards and Compliance
Different regions may have varying standards for valve manufacturing. For instance, European standards may differ from those in the Middle East or Africa. Understanding these differences is vital to ensure compliance and performance in your specific application. -
Cultural Considerations
Cultural differences can influence communication and expectations regarding quality. Establishing clear lines of communication and setting explicit quality expectations from the outset can help mitigate misunderstandings. -
Logistical Challenges
International shipping may introduce additional risks, such as damage during transit. Buyers should consider suppliers who offer robust packaging solutions and insurance to safeguard their investment.
By understanding the manufacturing processes and quality assurance measures in place at globe valve manufacturers, B2B buyers can make informed decisions that align with their operational needs and compliance requirements.
Practical Sourcing Guide: A Step-by-Step Checklist for ‘Globe Valves Manufacturers’
In the competitive landscape of industrial procurement, sourcing globe valves requires a strategic approach to ensure quality, reliability, and compliance with specific industry standards. This guide provides a practical step-by-step checklist for B2B buyers looking to procure globe valves from reputable manufacturers.
Step 1: Define Your Technical Specifications
Before reaching out to suppliers, clearly outline your technical requirements. Consider factors such as valve size, material (e.g., bronze, stainless steel, cast iron), pressure ratings, and application-specific features.
– Why It Matters: A well-defined specification helps suppliers provide accurate quotes and ensures that the valves meet your operational needs.
– What to Look For: Ensure that your specifications align with industry standards like API or ANSI to facilitate compatibility.
Step 2: Research Potential Suppliers
Conduct thorough research to identify manufacturers specializing in globe valves. Look for companies with a strong reputation in your region, particularly those with a track record of servicing industries relevant to your operations.
– Why It Matters: Selecting a reputable supplier reduces the risk of quality issues and supply chain disruptions.
– What to Look For: Check online reviews, industry forums, and supplier databases to gather insights about the manufacturers’ capabilities and reliability.
Step 3: Evaluate Supplier Certifications
Verify the certifications and compliance of potential suppliers. Key certifications include ISO 9001 for quality management systems and API certifications relevant to valve manufacturing.
– Why It Matters: Certification ensures that the supplier adheres to industry standards, which is critical for safety and performance.
– What to Look For: Request copies of certifications and verify them with the issuing bodies to confirm authenticity.
Step 4: Request Detailed Quotations
Once you have shortlisted suppliers, request detailed quotations that include pricing, lead times, and terms of sale. Ensure that the quotes specify any additional costs, such as shipping and handling.
– Why It Matters: A detailed quotation provides transparency and allows for better comparison between suppliers.
– What to Look For: Be wary of unusually low prices; they may indicate compromised quality or hidden costs.
Step 5: Assess Production Capabilities
Inquire about the production capabilities of your shortlisted suppliers. This includes their manufacturing processes, technology used, and their ability to handle large orders or custom specifications.
– Why It Matters: Understanding production capabilities ensures that the supplier can meet your order requirements within your timeline.
– What to Look For: Consider visiting the manufacturing facility if feasible, or request virtual tours to assess equipment and processes.
Step 6: Check References and Past Projects
Ask potential suppliers for references and case studies related to previous projects, especially those similar to yours. Contact these references to gauge their satisfaction with the supplier’s products and services.
– Why It Matters: References provide real-world insights into the supplier’s reliability and product performance.
– What to Look For: Pay attention to feedback regarding customer service, delivery times, and product quality.
Step 7: Negotiate Terms and Finalize Agreements
Once you have selected a supplier, negotiate the terms of the contract. This includes payment terms, delivery schedules, and warranties on the products.
– Why It Matters: Clear agreements protect both parties and establish expectations, reducing the likelihood of disputes.
– What to Look For: Ensure that the contract includes terms for quality assurance and recourse in case of product defects or non-compliance.
By following these steps, B2B buyers can effectively navigate the sourcing process for globe valves, ensuring they partner with reliable manufacturers who can meet their specific needs.
Comprehensive Cost and Pricing Analysis for Globe Valves Manufacturers Sourcing
When sourcing globe valves, international B2B buyers must understand the comprehensive cost structure and pricing dynamics that influence their purchasing decisions. This analysis focuses on the critical components of costs, factors influencing pricing, and actionable insights tailored for buyers from Africa, South America, the Middle East, and Europe, including countries like Mexico and Turkey.
What Are the Key Cost Components in Globe Valve Manufacturing?
The total cost of globe valves encompasses several key components:
-
Materials: The type of materials used (e.g., cast iron, stainless steel, bronze) significantly impacts the cost. Premium materials may increase durability and performance but will also raise the price. Understanding the specific material requirements for your application is essential for cost management.
-
Labor: Labor costs can vary widely based on the region of production. Countries with higher labor costs, such as those in Western Europe, may result in higher prices compared to those in emerging markets.
-
Manufacturing Overhead: This includes expenses related to factory operations, utilities, and administrative costs. Efficient manufacturing processes can help control these overheads, influencing the final price.
-
Tooling: Custom tooling for specialized valve designs can add to upfront costs. Buyers should consider whether the investment in custom tooling is justified based on their volume needs.
-
Quality Control (QC): Stringent QC measures ensure that products meet industry standards, impacting both production costs and pricing. Certifications (e.g., ISO, API) may also affect the price due to the additional resources needed for compliance.
-
Logistics: Shipping and handling costs can vary based on distance and shipping methods. Incoterms (International Commercial Terms) play a crucial role in determining who bears these costs, impacting overall pricing.
-
Margin: Suppliers will include a profit margin in their pricing, which can vary based on market competition and the perceived value of their products.
How Do Pricing Influencers Affect Globe Valve Costs?
Several factors can influence the pricing of globe valves:
-
Volume/MOQ (Minimum Order Quantity): Larger orders often lead to lower per-unit costs due to economies of scale. Buyers should assess their needs to negotiate favorable terms.
-
Specifications and Customization: Custom specifications can increase costs. Buyers should be clear about their requirements and consider whether standard products can meet their needs to save on costs.
-
Materials and Quality Certifications: Higher quality materials and recognized certifications can command higher prices. Buyers should evaluate the necessity of these features based on their operational requirements.
-
Supplier Factors: The supplier’s reputation, reliability, and service capabilities can influence pricing. Engaging with established suppliers may lead to better pricing through negotiation and long-term partnerships.
What Are Effective Buyer Tips for Cost-Efficiency?
To enhance cost-efficiency when sourcing globe valves, international buyers should consider the following strategies:
-
Negotiation: Be prepared to negotiate prices based on volume, payment terms, and delivery schedules. Building a relationship with suppliers can also lead to better terms.
-
Total Cost of Ownership (TCO): Assess not just the purchase price but the total cost of ownership, including maintenance, downtime, and replacement costs. This holistic view can lead to better long-term decisions.
-
Understand Pricing Nuances for International Sourcing: Be aware of local market conditions, currency fluctuations, and trade tariffs that can affect pricing. Buyers in regions like Africa and South America should consider local suppliers for more stable pricing.
-
Leverage Incoterms: Understanding and negotiating Incoterms can help manage logistics costs effectively. Choosing terms that minimize risk and cost can significantly impact the overall expenditure.
Disclaimer on Pricing Information
Prices for globe valves can vary widely based on the factors mentioned above. The information provided is indicative and should be verified with suppliers for accurate quotations tailored to specific project requirements. It is advisable to gather multiple quotes and conduct thorough due diligence before finalizing any procurement decisions.
Alternatives Analysis: Comparing Globe Valves Manufacturers With Other Solutions
In the realm of industrial fluid control, selecting the right valve type can significantly impact operational efficiency and cost-effectiveness. While globe valves are a popular choice among manufacturers, it’s crucial for international B2B buyers to explore alternative solutions that may better suit their specific operational needs. This section will compare globe valves with two viable alternatives: ball valves and gate valves.
Comparison Table of Globe Valves and Alternatives
Comparison Aspect | Globe Valves Manufacturers | Ball Valves | Gate Valves |
---|---|---|---|
Performance | Excellent throttling control; ideal for flow regulation | Quick on/off control; minimal pressure drop | Low resistance to flow; not for throttling |
Cost | Generally higher due to complexity | Typically lower; cost-effective for large flows | Moderate; less expensive than globe valves |
Ease of Implementation | Requires careful installation and alignment | Simple installation; compact design | Easy installation; requires space for operation |
Maintenance | Moderate; regular checks needed due to wear | Low; fewer moving parts | Low; less frequent maintenance needed |
Best Use Case | Ideal for applications requiring precise flow control | Suitable for on/off applications in large pipelines | Best for applications requiring full flow with minimal obstruction |
What Are the Pros and Cons of Ball Valves?
Pros:
– Efficiency: Ball valves provide a tight seal and minimal pressure drop, making them efficient for large flow rates.
– Quick Operation: They can be opened or closed with a quarter turn, allowing for rapid operation.
– Durability: With fewer moving parts, ball valves are less prone to wear and require less maintenance.
Cons:
– Limited Throttling: Ball valves are not suitable for throttling applications as they can cause turbulence and damage.
– Size Constraints: In high-pressure applications, larger ball valves may become more expensive and require additional support.
Why Consider Gate Valves?
Pros:
– Low Flow Resistance: Gate valves allow for full flow with minimal obstruction, making them ideal for applications where fluid dynamics are critical.
– Cost-Effective: They are generally less expensive than globe valves, making them a budget-friendly option for many industries.
– Simplicity: Their straightforward design leads to easy installation and low maintenance requirements.
Cons:
– Not Suitable for Throttling: Gate valves are designed for fully open or fully closed positions and are not ideal for regulating flow.
– Space Requirements: They require more space for operation due to their design, which may not be feasible in compact installations.
How Should B2B Buyers Choose the Right Valve Solution?
When selecting the appropriate valve solution, international B2B buyers must consider several factors, including the specific application requirements, budget constraints, and the operational environment. Globe valves are often preferred for applications requiring precise flow control, while ball valves are ideal for quick shut-off needs. Gate valves may be the best choice for applications demanding minimal flow resistance and cost-efficiency. Conducting a thorough analysis of operational needs and potential challenges will guide buyers in making informed decisions that align with their unique requirements. By weighing the advantages and disadvantages of each option, buyers can ensure they select a valve solution that optimizes performance and minimizes costs.
Essential Technical Properties and Trade Terminology for Globe Valves Manufacturers
What Are the Essential Technical Properties of Globe Valves?
When sourcing globe valves, international B2B buyers should consider several critical technical specifications that can significantly impact performance and suitability for specific applications. Below are key properties to evaluate:
1. Material Grade
The material of a globe valve determines its durability, corrosion resistance, and overall performance in various environments. Common materials include carbon steel, stainless steel, and bronze. For instance, stainless steel is preferred in corrosive environments, while carbon steel is often used in oil and gas applications. Understanding the material grade is crucial for ensuring the valve’s longevity and compatibility with the fluid being controlled.
2. Pressure Rating
Pressure rating, typically expressed in pounds per square inch (psi) or bar, indicates the maximum pressure the valve can handle. For example, a valve rated for 150 psi is suitable for lower-pressure applications, while higher ratings are necessary for oil and gas pipelines. Buyers must match the pressure rating with their system requirements to avoid leaks or valve failure.
3. Temperature Rating
Temperature rating defines the maximum and minimum temperatures at which a valve can operate efficiently. This is particularly important in industries such as petrochemical and power generation, where extreme temperatures are common. Selecting a valve with an appropriate temperature rating ensures reliable performance and safety.
4. Tolerance Levels
Tolerance refers to the acceptable limits of variation in dimensions and performance. For globe valves, tighter tolerances can lead to better sealing and reduced leakage. It is essential for buyers to understand these tolerances, especially in applications where precision is critical, such as in pharmaceutical or food processing industries.
5. End Connections
The type of end connection (e.g., flanged, threaded, or welded) affects how the valve integrates into existing piping systems. Understanding the compatibility of end connections with your pipeline is vital for ensuring a secure and leak-free installation.
6. Actuation Type
Globe valves can be operated manually or with automation, such as electric or pneumatic actuators. The choice of actuation type depends on operational needs and control requirements. Automated valves can improve efficiency and reduce labor costs, making them a preferred choice in larger operations.
What Are Common Trade Terms Used in the Globe Valve Industry?
Familiarity with industry jargon is essential for effective communication and negotiation in the B2B marketplace. Here are some common terms you should know:
1. OEM (Original Equipment Manufacturer)
An OEM refers to a company that produces parts or equipment that may be marketed by another manufacturer. In the context of globe valves, buyers may seek OEMs for custom solutions or specifications that meet particular operational needs.
2. MOQ (Minimum Order Quantity)
MOQ signifies the smallest quantity of products that a supplier is willing to sell. Understanding MOQ is critical for budget planning and inventory management, especially for smaller buyers or those entering new markets.
3. RFQ (Request for Quotation)
An RFQ is a document sent to suppliers to solicit price quotes for specific products or services. Crafting an effective RFQ can help ensure that you receive competitive pricing and favorable terms, which is essential for maximizing procurement efficiency.
4. Incoterms
Incoterms (International Commercial Terms) are standardized terms that define the responsibilities of buyers and sellers regarding shipping, insurance, and tariffs. Familiarity with these terms is crucial for international transactions, as they can significantly impact total landed costs.
5. Lead Time
Lead time is the period between placing an order and receiving the goods. Understanding lead times is essential for planning and ensuring that projects stay on schedule, particularly in industries with tight timelines.
6. Certification Standards
Certification standards (e.g., API, ANSI, ISO) are essential for verifying the quality and compliance of valves with international regulations. Buyers should seek valves that meet relevant certification standards to ensure safety, reliability, and acceptance in their respective markets.
By understanding these technical properties and trade terms, B2B buyers can make informed decisions when sourcing globe valves, ensuring that their selections meet operational requirements and industry standards.
Navigating Market Dynamics and Sourcing Trends in the Globe Valves Manufacturers Sector
What Are the Current Market Dynamics and Key Trends in the Globe Valves Manufacturers Sector?
The global market for globe valves is experiencing significant growth, driven by several factors including the expansion of oil and gas industries, increasing investments in infrastructure, and a rising demand for energy-efficient systems. Notably, the shift towards automation and Industry 4.0 technologies is influencing sourcing trends, as manufacturers integrate smart valve technologies and IoT capabilities into their products. This trend presents an opportunity for international B2B buyers, particularly in Africa, South America, the Middle East, and Europe, to source advanced globe valves that enhance operational efficiency and reduce maintenance costs.
Emerging markets in Africa and South America are witnessing substantial investments in energy and water management projects, which increases the demand for high-quality globe valves. In regions like Turkey and the Middle East, rapid urbanization and industrialization are propelling the need for reliable valve solutions in construction and manufacturing sectors. Buyers should focus on suppliers that offer customizable solutions and scalable manufacturing capabilities to meet their specific project requirements.
Additionally, sustainability is becoming a focal point in procurement decisions. Buyers are now prioritizing manufacturers that adhere to international quality standards and offer products designed for durability and reduced environmental impact. This focus not only aligns with global sustainability goals but also reflects a growing awareness among businesses of the long-term benefits of investing in eco-friendly technologies.
How Important Is Sustainability and Ethical Sourcing for Globe Valves Manufacturers?
Sustainability and ethical sourcing are increasingly critical in the globe valves manufacturing sector, driven by regulatory pressures and consumer demand for environmentally responsible practices. The environmental impact of valve production, including resource extraction and waste generation, necessitates a shift towards sustainable manufacturing processes. Buyers from regions such as Africa and Europe should prioritize suppliers that utilize recycled materials and implement energy-efficient production techniques.
Ethical supply chains are essential for ensuring that raw materials are sourced responsibly, minimizing negative impacts on local communities and ecosystems. This is particularly relevant in regions rich in natural resources, where the extraction of metals and other materials can lead to significant social and environmental challenges. By choosing manufacturers committed to ethical practices, B2B buyers can enhance their corporate social responsibility (CSR) profiles and foster long-term partnerships based on shared values.
Furthermore, certifications such as ISO 14001 (Environmental Management) and ISO 9001 (Quality Management) can serve as indicators of a manufacturer’s commitment to sustainability. Buyers should seek out globe valve manufacturers that not only comply with these standards but also transparently report their sustainability initiatives and progress.
What Is the Brief Evolution and History of Globe Valves?
Globe valves have a storied history dating back to the 19th century, initially designed for the steam and water systems of the Industrial Revolution. Their ability to control flow effectively made them a staple in various industries, including oil and gas, water treatment, and power generation. Over the years, advancements in materials and design have led to the development of more durable and efficient globe valves, capable of withstanding higher pressures and temperatures.
The evolution of globe valves has been marked by innovations such as the introduction of automated control systems and smart valve technologies, which allow for remote monitoring and operation. As industries continue to evolve, the demand for advanced globe valves that meet stringent safety and environmental standards is expected to rise, further driving innovation in the sector. For international B2B buyers, understanding this evolution is key to making informed sourcing decisions that align with current and future market needs.
Frequently Asked Questions (FAQs) for B2B Buyers of Globe Valves Manufacturers
-
How can I assess the quality of globe valves before making a purchase?
To evaluate the quality of globe valves, request product specifications and certifications from manufacturers. Look for compliance with international standards such as API, ANSI, or ISO. Additionally, inquire about the materials used in manufacturing, as higher-quality materials typically result in better durability. It’s also beneficial to seek customer reviews or case studies from other businesses in your industry, which can provide insights into the reliability and performance of the valves. -
What are the key factors to consider when choosing a globe valve manufacturer?
When selecting a globe valve manufacturer, consider their industry experience, reputation, and range of products. Evaluate their production capabilities, including customization options for unique applications. Assess their customer service and support, including response times and technical assistance. Finally, consider logistics and delivery times, as these can significantly impact your project’s timeline. -
What customization options are typically available for globe valves?
Many globe valve manufacturers offer customization options to meet specific operational requirements. Customizations may include alterations in size, material, pressure rating, and end connections. Additionally, manufacturers can often provide unique features such as special coatings for corrosion resistance or modifications to handle specific fluid types. Discuss your specific needs with the supplier to explore available options.
-
What is the minimum order quantity (MOQ) for globe valves from manufacturers?
The minimum order quantity for globe valves varies by manufacturer and can depend on factors like the type of valve, material, and customization requirements. Generally, larger manufacturers may have higher MOQs due to production efficiencies, while smaller manufacturers might offer more flexibility. Always confirm MOQs during negotiations to ensure they align with your purchasing capabilities and project requirements. -
What payment terms should I expect when sourcing globe valves internationally?
Payment terms can vary widely among globe valve manufacturers. Common terms include upfront payments, partial payments upon order confirmation, and balance payments upon shipment or delivery. For international transactions, consider discussing options such as Letters of Credit (LC) or PayPal to enhance security. Ensure that all terms are clearly documented in the purchase agreement to avoid any misunderstandings. -
How do I verify the reliability of a globe valve supplier?
To verify the reliability of a globe valve supplier, conduct thorough research on their business history and reputation. Check for industry certifications and customer testimonials. Engage in direct communication to assess their responsiveness and willingness to provide detailed product information. Additionally, consider requesting samples or visiting their facility if possible, to observe their operations and quality control processes firsthand. -
What quality assurance processes should globe valve manufacturers have in place?
Reputable globe valve manufacturers typically implement stringent quality assurance processes, including material inspections, in-process quality checks, and final testing. Look for manufacturers that conduct pressure tests, leak tests, and performance assessments to ensure product reliability. Ask for documentation of these processes, as well as any relevant certifications, to ensure that the products meet your quality standards. -
What logistics considerations should I keep in mind when importing globe valves?
When importing globe valves, consider factors such as shipping methods, lead times, and customs regulations. Choose a reliable logistics partner familiar with international trade, especially in your region (e.g., Africa, South America, Middle East, or Europe). Ensure that the supplier provides all necessary documentation for customs clearance to avoid delays. Also, factor in potential tariffs or import duties, as these can impact your total costs significantly.
Important Disclaimer & Terms of Use
⚠️ Important Disclaimer
The information provided in this guide, including content regarding manufacturers, technical specifications, and market analysis, is for informational and educational purposes only. It does not constitute professional procurement advice, financial advice, or legal advice.
While we have made every effort to ensure the accuracy and timeliness of the information, we are not responsible for any errors, omissions, or outdated information. Market conditions, company details, and technical standards are subject to change.
B2B buyers must conduct their own independent and thorough due diligence before making any purchasing decisions. This includes contacting suppliers directly, verifying certifications, requesting samples, and seeking professional consultation. The risk of relying on any information in this guide is borne solely by the reader.
Strategic Sourcing Conclusion and Outlook for Globe Valves Manufacturers
What Are the Key Takeaways for Strategic Sourcing of Globe Valves?
In conclusion, strategic sourcing of globe valves is vital for international B2B buyers looking to optimize their procurement processes. Understanding the various materials, designs, and manufacturers can significantly impact operational efficiency and cost-effectiveness. By evaluating suppliers based on their industry experience, product reliability, and compliance with international standards, buyers can ensure they are making informed decisions that align with their project requirements.
How Can International Buyers Enhance Their Sourcing Strategy?
As the global demand for globe valves continues to rise, especially in sectors like oil and gas, water treatment, and manufacturing, buyers from Africa, South America, the Middle East, and Europe must remain proactive. Engaging with multiple suppliers and leveraging technology for real-time data can enhance negotiation power and supply chain resilience.
What Does the Future Hold for Globe Valve Procurement?
Looking ahead, the landscape of globe valve manufacturing is expected to evolve with advancements in materials and smart technologies. International buyers should keep abreast of these trends to capitalize on innovative solutions that can improve system performance. By prioritizing strategic sourcing and fostering strong relationships with manufacturers, B2B buyers can position themselves for success in an increasingly competitive market.