Discover Top Injection Molding Machine Manufacturers (2025)
Introduction: Navigating the Global Market for Injection Molding Machine Manufacturers
In the competitive landscape of global manufacturing, sourcing the right injection molding machines can be a daunting task for international B2B buyers, especially those from Africa, South America, the Middle East, and Europe. With diverse applications ranging from automotive parts to consumer goods, understanding the nuances of injection molding technology is crucial for making informed purchasing decisions. This guide delves into the multifaceted world of injection molding machine manufacturers, providing insights into various types of machines, their applications, and the latest technological advancements.
Navigating the complexities of supplier vetting, this comprehensive resource empowers buyers to assess potential manufacturers based on quality, pricing, and service capabilities. Key considerations such as production capacity, machine efficiency, and after-sales support are outlined, ensuring that buyers can effectively compare options tailored to their specific needs. Furthermore, the guide discusses cost factors, enabling businesses to align their budgets with realistic expectations in the injection molding market.
By equipping international buyers with actionable insights, this guide serves as an essential tool for enhancing procurement strategies, minimizing risks, and ultimately driving business growth. Whether you are in Thailand or France, understanding the intricacies of injection molding machinery is vital for staying competitive in today’s fast-paced manufacturing environment.
Understanding Injection Molding Machine Manufacturers Types and Variations
Type Name | Key Distinguishing Features | Primary B2B Applications | Brief Pros & Cons for Buyers |
---|---|---|---|
Hydraulic Injection Molding Machines | Utilizes hydraulic systems for high pressure and speed | Automotive, packaging, consumer goods | Pros: High efficiency, good for large parts. Cons: Higher energy consumption. |
Electric Injection Molding Machines | Operated by electric motors, offering precision control | Electronics, medical devices | Pros: Energy-efficient, low noise. Cons: Higher initial investment. |
Hybrid Injection Molding Machines | Combines hydraulic and electric technologies | Complex and varied production | Pros: Versatile, balanced performance. Cons: Maintenance complexity. |
Vertical Injection Molding Machines | Operates in a vertical orientation, saving floor space | Small parts, insert molding | Pros: Space-saving, efficient for small parts. Cons: Limited to smaller molds. |
Multi-color Injection Molding Machines | Allows for the production of multi-colored parts | Toys, automotive interiors | Pros: Aesthetic versatility, complex designs. Cons: More expensive setup. |
What are the Characteristics of Hydraulic Injection Molding Machines?
Hydraulic injection molding machines are characterized by their use of hydraulic systems to generate the high pressure needed for molding processes. They are particularly well-suited for large parts, making them a popular choice in the automotive and packaging industries. When purchasing hydraulic machines, buyers should consider the machine’s energy consumption and maintenance requirements, as they typically have a higher operational cost compared to other types.
How Do Electric Injection Molding Machines Stand Out?
Electric injection molding machines are distinguished by their electric motor operation, which provides precise control over the injection process. This type of machine is ideal for applications in electronics and medical devices, where precision and repeatability are critical. Buyers should weigh the benefits of energy efficiency and lower noise levels against the higher initial investment costs, especially if their production volumes are not high.
What Makes Hybrid Injection Molding Machines a Good Choice?
Hybrid injection molding machines blend the best features of hydraulic and electric technologies, offering a versatile solution for manufacturers. They are particularly effective for complex and varied production scenarios, allowing for faster cycles and reduced energy consumption. When considering a hybrid machine, B2B buyers should assess the balance of performance and maintenance complexity, as these machines may require specialized knowledge for upkeep.
Why Choose Vertical Injection Molding Machines?
Vertical injection molding machines operate in a vertical orientation, which can save significant floor space in manufacturing environments. They are particularly effective for small parts and insert molding applications, making them a common choice for industries producing components that require precise placement of inserts. Buyers should consider the machine’s limitations regarding mold size and production volume when evaluating their options.
What are the Benefits of Multi-color Injection Molding Machines?
Multi-color injection molding machines allow manufacturers to create parts with multiple colors in a single production run, enhancing the aesthetic appeal of products. This capability is especially valuable in industries like toy manufacturing and automotive interiors, where design plays a crucial role. However, buyers should be aware of the higher setup costs associated with these machines, as well as the need for skilled operators to manage the more complex processes involved.
Related Video: Lesson 1-HD – Molding Machine Parts and Operation – Technology of Injection Molding
Key Industrial Applications of Injection Molding Machine Manufacturers
Industry/Sector | Specific Application of Injection Molding Machine Manufacturers | Value/Benefit for the Business | Key Sourcing Considerations for this Application |
---|---|---|---|
Automotive | Production of automotive components such as dashboards and panels | High precision and consistency in manufacturing critical parts | Supplier reliability, machine speed, and customization options |
Consumer Electronics | Manufacturing casings for devices like smartphones and tablets | Enhanced aesthetics and durability of products | Material compatibility, energy efficiency, and scalability |
Medical Devices | Creation of specialized medical components like syringes and housings | Compliance with stringent health regulations and safety standards | Certification processes, material purity, and production volume |
Packaging | Production of plastic containers and packaging solutions | Cost-effective production with reduced waste | Recyclability of materials, design flexibility, and lead times |
Construction | Fabrication of durable building materials like fittings and fixtures | Improved product longevity and performance under stress | Technological advancements, tooling costs, and design specifications |
How Are Injection Molding Machines Used in the Automotive Industry?
Injection molding machines are critical in the automotive sector for producing high-quality components such as dashboards, panels, and exterior trims. These machines allow for mass production with tight tolerances, ensuring parts fit seamlessly together. For international buyers, especially from regions like Africa and South America, understanding the local automotive regulations and quality standards is essential. Buyers should also consider the machine’s capability to produce lightweight materials, which are increasingly important for fuel efficiency.
What Role Do Injection Molding Machines Play in Consumer Electronics?
In the consumer electronics industry, injection molding machines are used to create robust and aesthetically pleasing casings for smartphones, tablets, and other devices. These machines offer high precision, allowing for intricate designs that enhance product appeal. For buyers in Europe and the Middle East, sourcing machines that support rapid prototyping and small batch production can be advantageous, as market demands shift quickly. Buyers should prioritize suppliers who offer advanced materials that improve durability and can withstand daily usage.
How Are Injection Molding Machines Essential for Medical Devices?
Injection molding is indispensable for the medical device industry, where precision and compliance with health regulations are paramount. Machines produce components like syringes, surgical tools, and housings for diagnostic equipment. Buyers from Africa and South America need to be aware of the stringent certification processes required for medical products. It’s crucial to source machines that can handle high-purity materials and maintain strict hygiene standards during production to avoid contamination.
In What Ways Are Injection Molding Machines Used in Packaging?
In the packaging industry, injection molding machines are utilized to manufacture a wide range of plastic containers, caps, and other packaging solutions. This process is cost-effective and minimizes waste, making it ideal for high-volume production. Buyers, particularly from regions with growing consumer markets like South America and Africa, should consider the recyclability of the materials used and the machine’s ability to produce lightweight packaging that meets sustainability goals. Flexibility in design and rapid changeover capabilities are also critical factors.
How Do Injection Molding Machines Contribute to the Construction Sector?
Injection molding machines play a significant role in the construction industry by fabricating durable fittings and fixtures that meet specific building standards. These machines enable the production of components that can withstand harsh environmental conditions, ensuring longevity and performance. For international buyers, especially from Europe and the Middle East, understanding the technological advancements in molding processes can lead to better sourcing decisions. Key considerations include tooling costs, production volume requirements, and the ability to customize designs according to project specifications.
3 Common User Pain Points for ‘Injection Molding Machine Manufacturers’ & Their Solutions
Scenario 1: Overcoming Production Downtime Due to Machine Failures
The Problem: One significant pain point for B2B buyers in the injection molding sector is the unexpected downtime caused by machine malfunctions. This issue can severely disrupt production schedules, leading to delayed deliveries and lost revenue. Buyers often face challenges in identifying the root cause of these failures, whether they stem from mechanical wear, software issues, or inadequate maintenance practices. As a result, they might find themselves at a standstill, incurring costs not only from halted production but also from overtime labor required to catch up on lost output.
The Solution: To mitigate the risk of production downtime, B2B buyers should prioritize working with injection molding machine manufacturers that offer robust support services, including comprehensive maintenance packages. It is essential to establish a proactive maintenance plan that includes regular check-ups and predictive analytics to identify potential issues before they escalate. Buyers should also invest in training for their operational staff on basic troubleshooting techniques, enabling them to quickly assess and potentially resolve minor issues without waiting for external service. Additionally, consider integrating IoT-enabled monitoring solutions that provide real-time data on machine performance, allowing for immediate intervention when anomalies are detected.
Scenario 2: Navigating Complex Specifications and Customizations
The Problem: Many B2B buyers encounter difficulties when trying to navigate the complex specifications and customization options offered by injection molding machine manufacturers. This challenge often arises from a lack of clarity about the specific requirements for their production needs, which can result in selecting machines that do not meet their operational goals. Misalignment can lead to inefficiencies, increased production costs, and wasted materials, ultimately affecting the buyer’s bottom line.
The Solution: To effectively navigate these complexities, buyers should conduct a thorough assessment of their production requirements before engaging with manufacturers. This includes understanding the materials to be used, the desired production volume, and the specific features needed for their end products. Engaging in detailed discussions with manufacturers about customization options is crucial; buyers should not hesitate to ask for case studies or examples of similar projects. Furthermore, leveraging the expertise of industry consultants can provide valuable insights into the latest technologies and trends, ensuring that buyers make informed decisions that align with their long-term production strategies.
Scenario 3: Addressing Cost Concerns Without Sacrificing Quality
The Problem: Cost management is a persistent concern for B2B buyers in the injection molding industry. As raw material prices fluctuate and operational costs rise, buyers often feel pressured to cut expenses, which can lead to compromises on quality. This dilemma can be particularly challenging when sourcing machines, as cheaper options may result in lower performance, increased maintenance costs, and ultimately, a decrease in product quality.
The Solution: To address cost concerns while maintaining quality, buyers should focus on building long-term partnerships with reputable injection molding machine manufacturers who offer value rather than just low prices. Conducting a total cost of ownership (TCO) analysis can help buyers understand the long-term implications of their investment, factoring in maintenance, energy consumption, and operational efficiencies. Additionally, considering refurbished or certified pre-owned machines can be a cost-effective strategy without sacrificing quality. Buyers should also negotiate flexible payment terms or financing options with manufacturers, allowing for budget management that does not compromise on the quality of machinery needed for production.
Strategic Material Selection Guide for Injection Molding Machine Manufacturers
What Are the Key Properties of Common Materials Used in Injection Molding?
When selecting materials for injection molding, manufacturers often consider several key properties that directly affect product performance. Here, we analyze four common materials: Polypropylene (PP), Acrylonitrile Butadiene Styrene (ABS), Polycarbonate (PC), and Nylon (PA). Each material offers distinct advantages and limitations that can influence the final product’s suitability and performance.

A stock image related to Injection Molding Machine Manufacturers.
How Does Polypropylene (PP) Perform in Injection Molding Applications?
Polypropylene is a widely used thermoplastic known for its excellent chemical resistance and low density. It has a temperature rating of approximately 100°C (212°F) and can withstand moderate pressure.
Pros: PP is lightweight, cost-effective, and exhibits good fatigue resistance, making it suitable for applications like automotive parts and consumer goods.
Cons: However, it has lower impact resistance compared to other materials and can be prone to warping during cooling.
Impact on Application: PP is compatible with a variety of media, including chemicals, making it ideal for containers and packaging.
Considerations for International Buyers: Compliance with standards such as ASTM D4101 is essential. Buyers from regions like Africa and South America should consider local availability and cost-effectiveness.
What Are the Advantages of Using Acrylonitrile Butadiene Styrene (ABS)?
ABS is another popular choice for injection molding due to its excellent impact resistance and toughness. It operates well at temperatures up to 80°C (176°F) and has good dimensional stability.
Pros: Its ability to be easily machined and painted makes it ideal for consumer electronics and automotive applications.
Cons: ABS is susceptible to UV degradation and can become brittle over time when exposed to sunlight.
Impact on Application: Its compatibility with various media allows for versatile applications, although care must be taken in outdoor settings.
Considerations for International Buyers: Buyers should ensure compliance with international standards like ISO 1043-1. In Europe, the REACH regulation may also apply, affecting material sourcing.
How Does Polycarbonate (PC) Compare in Terms of Performance?
Polycarbonate is known for its high impact resistance and transparency, making it suitable for applications requiring visibility and strength. It can withstand temperatures up to 135°C (275°F).
Pros: PC is highly durable and can be used in applications like safety goggles and automotive components due to its excellent mechanical properties.
Cons: It is more expensive than PP and ABS and can be prone to scratching unless treated.
Impact on Application: PC is compatible with various media, including water and oils, making it suitable for both industrial and consumer applications.
Considerations for International Buyers: Compliance with standards such as ISO 7391 is important. Buyers in the Middle East should consider the material’s performance under high temperatures.
What Makes Nylon (PA) a Preferred Material for Specific Applications?
Nylon is a versatile engineering thermoplastic known for its excellent wear resistance and mechanical strength. It operates effectively at temperatures up to 120°C (248°F).
Pros: Nylon is ideal for applications requiring high strength and flexibility, such as gears and bearings.
Cons: It can absorb moisture, which may affect its dimensional stability and mechanical properties.
Impact on Application: Nylon’s compatibility with various media makes it suitable for automotive and industrial applications.
Considerations for International Buyers: Compliance with ASTM D6779 is critical. Buyers from Europe should be aware of EU regulations on material safety and performance.
Summary Table of Material Selection for Injection Molding
Material | Typical Use Case for Injection Molding Machine Manufacturers | Key Advantage | Key Disadvantage/Limitation | Relative Cost (Low/Med/High) |
---|---|---|---|---|
Polypropylene (PP) | Automotive parts, consumer goods | Lightweight and cost-effective | Lower impact resistance | Low |
Acrylonitrile Butadiene Styrene (ABS) | Consumer electronics, automotive | Excellent impact resistance | Susceptible to UV degradation | Medium |
Polycarbonate (PC) | Safety goggles, automotive components | High durability and transparency | More expensive and prone to scratching | High |
Nylon (PA) | Gears, bearings | High strength and flexibility | Moisture absorption affects stability | Medium |
This guide provides a comprehensive overview of material selection for injection molding machine manufacturers, focusing on properties, advantages, limitations, and considerations for international buyers. Understanding these factors can aid in making informed purchasing decisions tailored to specific regional needs and compliance standards.
In-depth Look: Manufacturing Processes and Quality Assurance for Injection Molding Machine Manufacturers
What Are the Key Manufacturing Processes for Injection Molding Machines?
The manufacturing of injection molding machines involves several critical stages that ensure the production of high-quality equipment capable of meeting various industrial needs. Understanding these stages can help international B2B buyers, especially those from Africa, South America, the Middle East, and Europe, make informed purchasing decisions.
How Is Material Prepared for Injection Molding Machines?
Material preparation is the foundational step in the manufacturing process. Typically, this involves the selection and preparation of raw materials, primarily thermoplastics or thermosetting polymers. The process includes:
- Material Selection: Choosing the appropriate resin based on the desired properties of the end product (e.g., strength, flexibility).
- Drying: Many plastics absorb moisture, which can cause defects during molding. Therefore, the materials must be dried to a specific moisture content using drying ovens or desiccant systems.
- Mixing: Additives such as colorants, stabilizers, and fillers are mixed with the base resin to enhance performance characteristics.
What Are the Forming Techniques Used in Injection Molding?
The forming stage is where the prepared materials are transformed into the desired shapes. The main techniques include:
- Injection Molding: This is the primary method where molten plastic is injected into a mold under high pressure. The mold is cooled, and the solidified part is ejected.
- Blow Molding: Used for producing hollow parts, this technique involves inflating a hot plastic tube within a mold.
- Compression Molding: This method is often used for thermosetting plastics, where the material is placed in a heated mold and compressed to form the part.
How Is Assembly Conducted for Injection Molding Machines?
After forming, the components of the injection molding machine undergo assembly. This stage may involve:
- Component Assembly: Major parts like the injection unit, clamping unit, and control systems are assembled. Precision in this stage is crucial to ensure the machine operates efficiently.
- Integration of Electrical Systems: Electrical components, including sensors and control panels, are integrated to facilitate automation and monitoring.
- Final Assembly: All components are brought together, and the machine undergoes a series of functional tests to ensure everything is working as intended.
What Finishing Processes Are Commonly Used?
Finishing processes enhance the aesthetic and functional qualities of the injection molding machines. Common practices include:
- Surface Treatment: Techniques like polishing, painting, or coating improve the machine’s appearance and durability.
- Calibration: Ensuring that the machine operates within specified parameters is vital. Calibration involves adjusting settings based on testing results to achieve desired outputs.
- Quality Checks: Before final delivery, machines undergo rigorous quality checks to verify that they meet industry standards.
What Quality Assurance Standards Should International Buyers Consider?
Quality assurance (QA) is a critical aspect of the manufacturing process, especially for international B2B buyers looking for reliable suppliers. Various international standards govern the quality of injection molding machines.
Which International Standards Are Relevant for Injection Molding Machine Manufacturers?
- ISO 9001: This is the most recognized quality management standard that ensures manufacturers consistently meet customer and regulatory requirements.
- CE Marking: For machines sold in the European market, compliance with CE marking indicates adherence to health, safety, and environmental protection standards.
- API Standards: For manufacturers producing machines for the oil and gas industry, API standards ensure that equipment meets specific safety and quality benchmarks.
What Are the Key Quality Control Checkpoints in the Manufacturing Process?
Quality control (QC) is integral to maintaining high standards throughout the manufacturing process. Key QC checkpoints include:
- Incoming Quality Control (IQC): Raw materials are inspected upon arrival to ensure they meet specified standards.
- In-Process Quality Control (IPQC): This involves monitoring the manufacturing process at various stages to identify and rectify any issues immediately.
- Final Quality Control (FQC): Before shipment, the completed machines undergo extensive testing to verify functionality and compliance with specifications.
How Can B2B Buyers Verify Supplier Quality Control?
International B2B buyers should adopt specific strategies to verify the quality control processes of potential suppliers:
- Supplier Audits: Conducting on-site audits allows buyers to assess the manufacturing environment, processes, and adherence to quality standards.
- Quality Reports: Requesting detailed quality reports that outline testing results and compliance with standards can provide insights into a manufacturer’s commitment to quality.
- Third-Party Inspections: Engaging independent inspection agencies can offer unbiased evaluations of the manufacturing processes and final products.
What Are the Nuances of Quality Control Certification for International Buyers?
For international buyers, understanding the nuances of quality control certifications is vital. Here are a few considerations:
- Regional Variations: Different regions may have varying standards and certifications. Buyers must ensure suppliers comply with relevant local regulations.
- Documentation: Requesting certifications and documentation from suppliers can help verify their quality assurance processes and compliance with international standards.
- Cultural Differences: Buyers should be aware of cultural attitudes towards quality and compliance in different regions, which may affect supplier practices.
By comprehensively understanding the manufacturing processes and quality assurance standards, international B2B buyers can make informed decisions when selecting injection molding machine manufacturers. This knowledge not only helps in identifying reliable suppliers but also ensures that the machinery procured meets the required operational standards and regulatory compliance.
Practical Sourcing Guide: A Step-by-Step Checklist for ‘Injection Molding Machine Manufacturers’
The following is a practical sourcing guide designed for international B2B buyers seeking to procure injection molding machines from reputable manufacturers. This checklist will help streamline the procurement process and ensure that buyers make informed decisions.
Step 1: Define Your Technical Specifications
Before reaching out to manufacturers, it’s essential to clearly define your technical specifications. Consider factors such as the materials you will use, the size of the parts, production volume, and the complexity of the designs. This clarity will enable you to communicate effectively with potential suppliers and ensure they can meet your specific needs.
- Material Compatibility: Identify the types of plastics and other materials you plan to use.
- Production Capacity: Estimate the quantity of parts you need to produce daily or monthly.
Step 2: Conduct Market Research on Manufacturers
Research potential manufacturers to identify those that specialize in injection molding machines suited to your requirements. Use online resources, industry reports, and trade shows to gather information about their capabilities, reputation, and market presence.
- Reputation Analysis: Look for customer reviews and testimonials to gauge reliability.
- Industry Experience: Prioritize manufacturers with extensive experience in your specific industry sector.
Step 3: Evaluate Potential Suppliers
Before committing, it’s crucial to vet suppliers thoroughly. Request company profiles, case studies, and references from buyers in a similar industry or region. Don’t just rely on their website; conduct independent research to validate their claims.
- Certifications and Compliance: Ensure that the suppliers adhere to international quality standards such as ISO 9001.
- Visit Facilities if Possible: If feasible, a factory visit can provide insights into their production capabilities and quality control processes.
Step 4: Verify Supplier Certifications
Ensure that the manufacturers hold relevant certifications that demonstrate their commitment to quality and safety. Certifications can be a strong indicator of a company’s credibility and operational standards.
- ISO Certifications: Look for ISO certifications that apply to manufacturing and quality management.
- Environmental Certifications: Check for compliance with environmental standards, especially if sustainability is a priority for your company.
Step 5: Request Quotes and Compare Pricing
Once you have identified potential suppliers, request detailed quotes that include pricing, delivery times, and payment terms. Comparing these quotes will help you understand the market rate and identify any discrepancies.
- Breakdown of Costs: Ensure that the quotes specify costs for machinery, shipping, and any additional services.
- Negotiation Leverage: Use the information gathered to negotiate better terms with suppliers.
Step 6: Assess After-Sales Support and Warranty
Evaluate the after-sales support provided by the manufacturer, including warranty terms, maintenance services, and availability of spare parts. Strong after-sales support can significantly reduce downtime and operational risks.
- Warranty Duration: Check the warranty period and what it covers.
- Technical Support: Understand the level of technical assistance available and response times for service requests.
Step 7: Finalize Contract and Purchase Agreement
Once you have selected a supplier, ensure that you draft a comprehensive contract that outlines all terms of the agreement. This should include payment terms, delivery schedules, and responsibilities for both parties.
- Legal Review: Consider having a legal expert review the contract to protect your interests.
- Clear Terms: Ensure that all terms are clear and agreeable to avoid disputes in the future.
Following this practical sourcing guide will help international B2B buyers, particularly from Africa, South America, the Middle East, and Europe, make informed decisions when procuring injection molding machines. By thoroughly researching and evaluating potential suppliers, you can ensure a successful purchasing experience.
Comprehensive Cost and Pricing Analysis for Injection Molding Machine Manufacturers Sourcing
What Are the Key Cost Components in Injection Molding Machine Manufacturing?
When sourcing injection molding machines, understanding the cost structure is crucial for international B2B buyers. The primary components that contribute to the total cost include:
-
Materials: The quality and type of raw materials used, such as steel and aluminum, significantly impact costs. High-grade materials enhance durability but come at a premium.
-
Labor: Labor costs vary by region and skill level. Countries with lower labor costs, such as some in Africa and South America, may offer competitive pricing, but the trade-off could be in skill and expertise.
-
Manufacturing Overhead: This includes indirect costs such as utilities, rent, and administrative expenses. Efficient manufacturing processes can help reduce overhead, thus lowering prices for buyers.
-
Tooling: Tooling costs can be substantial, particularly for custom machines. These costs often depend on the complexity of the mold and the materials used.
-
Quality Control (QC): Investing in QC processes ensures that machines meet specific standards, which may increase upfront costs but can save buyers from future maintenance and operational issues.
-
Logistics: Shipping and handling fees can vary greatly depending on the distance and method of transportation. Understanding these costs is essential, especially for international shipments.
-
Margin: Manufacturers typically add a margin to cover profits. This margin can fluctuate based on market demand and competition.
How Do Price Influencers Affect Injection Molding Machine Costs?
Several factors can influence the pricing of injection molding machines:
-
Volume and Minimum Order Quantity (MOQ): Larger orders often qualify for bulk discounts, making it crucial for buyers to assess their needs carefully.
-
Specifications and Customization: Custom machines tailored to specific production needs usually come at a higher price. Buyers must weigh the benefits of customization against the additional costs.
-
Materials and Quality Certifications: Machines made with premium materials and certified for quality assurance (ISO, CE) tend to be more expensive but offer better performance and reliability.
-
Supplier Factors: The reputation and reliability of the supplier can also impact pricing. Established manufacturers may charge higher prices due to their track record.
-
Incoterms: Understanding shipping terms and responsibilities is vital. Different Incoterms (like FOB, CIF) can significantly affect the total landed cost of the machinery.
What Tips Can International B2B Buyers Use for Cost-Efficiency in Sourcing?
International buyers, particularly from Africa, South America, the Middle East, and Europe, should consider the following strategies to enhance cost-efficiency:
-
Negotiate Wisely: Don’t hesitate to negotiate prices and terms. Suppliers often have flexibility, especially for larger orders.
-
Total Cost of Ownership (TCO): Evaluate the TCO, which includes purchase price, maintenance, and operational costs. A cheaper machine may lead to higher long-term expenses if it requires frequent repairs or has lower efficiency.
-
Understand Pricing Nuances: Be aware of regional pricing differences. For instance, suppliers in Europe may have different pricing structures compared to those in Asia, influenced by labor costs and material availability.
-
Conduct Due Diligence: Research potential suppliers thoroughly. Request quotes from multiple manufacturers to compare not just prices, but also quality and service levels.
Conclusion
A comprehensive understanding of the cost structure and pricing dynamics of injection molding machines is vital for international B2B buyers. By being aware of the key cost components, price influencers, and strategic negotiation tactics, buyers can make informed decisions that enhance their procurement efficiency and ultimately lead to better investment outcomes. Always remember to consider the total cost of ownership to ensure that your investment aligns with your long-term production goals.
Alternatives Analysis: Comparing Injection Molding Machine Manufacturers With Other Solutions
Understanding Alternatives to Injection Molding Machine Manufacturers
In the competitive landscape of manufacturing, B2B buyers often seek various solutions to meet their production needs. Injection molding is a prevalent method for producing parts and products efficiently, but several alternatives may provide unique benefits depending on specific requirements, such as budget constraints, production volume, and product complexity. This analysis compares injection molding machine manufacturers with two viable alternatives: 3D printing and compression molding.
Comparison Table of Manufacturing Methods
Comparison Aspect | Injection Molding Machine Manufacturers | 3D Printing | Compression Molding |
---|---|---|---|
Performance | High precision and speed for mass production | Lower precision; slower for large volumes | Good for medium to large parts; decent precision |
Cost | High initial investment; lower per unit cost for mass production | Lower initial cost; higher per unit cost for small runs | Moderate initial investment; cost-effective for large batches |
Ease of Implementation | Requires skilled labor and setup time | Easy to start; minimal setup | Moderate complexity; requires mold creation |
Maintenance | Regular maintenance needed for longevity | Minimal maintenance; depends on printer type | Moderate; molds require upkeep |
Best Use Case | High-volume production with complex designs | Prototyping and low-volume production | Large parts and simpler designs |
In-Depth Analysis of Alternatives
What Are the Advantages and Disadvantages of 3D Printing?
3D printing, also known as additive manufacturing, allows for the creation of complex geometries that would be difficult or impossible to achieve with traditional methods. Its main advantage lies in flexibility; it allows for rapid prototyping and customization without the need for expensive molds. However, the limitations include slower production speeds and a generally higher cost per unit for larger runs. Additionally, the material properties may not match those produced through injection molding, which can be a critical factor for certain applications.
How Does Compression Molding Compare?
Compression molding is another alternative that is particularly effective for producing large parts, such as automotive components. This method involves placing a material, often thermosetting polymers, into a heated mold, where it is compressed and shaped. The main advantages of compression molding include lower material waste and the ability to produce larger parts efficiently. However, it requires a moderate initial investment for mold creation and is less suited for complex designs compared to injection molding. The setup time can also be longer, impacting production timelines.
Conclusion: How to Choose the Right Solution for Your Needs
When selecting the most suitable manufacturing method, B2B buyers should consider factors such as production volume, complexity of design, and budget constraints. Injection molding remains the best option for high-volume production with complex parts due to its efficiency and cost-effectiveness at scale. However, for businesses focusing on rapid prototyping or smaller production runs, 3D printing offers flexibility and lower initial costs. Compression molding serves as a solid middle-ground for larger parts with simpler designs. Evaluating these factors in alignment with specific project requirements will guide buyers toward the most effective solution for their manufacturing needs.
Essential Technical Properties and Trade Terminology for Injection Molding Machine Manufacturers
What Are the Essential Technical Properties of Injection Molding Machines?
When considering an investment in injection molding machinery, understanding the critical technical properties is paramount. Here are some of the key specifications that B2B buyers should prioritize:
1. Material Grade: Why Is It Important?
Material grade refers to the type of plastic that an injection molding machine can process. Common grades include ABS, PS, and PP, each with unique properties suited for different applications. Selecting the right material grade ensures the durability, strength, and flexibility of the final product. For manufacturers in Africa and South America, understanding local material availability can optimize production costs and timelines.
2. Tolerance: How Does It Affect Product Quality?
Tolerance indicates the allowable deviation from specified dimensions in molded parts. High precision is crucial in industries such as automotive and medical, where even minor discrepancies can lead to product failure. B2B buyers should seek machines capable of achieving tight tolerances to ensure that components fit together seamlessly, enhancing overall product quality.
3. Clamping Force: What Role Does It Play in Production?
Clamping force is the pressure applied to keep the mold closed during the injection process. It is measured in tons and must match the size and complexity of the part being produced. A machine with insufficient clamping force may lead to flash (excess material) or incomplete molds. Buyers should assess their production needs to choose a machine with the appropriate clamping force, ensuring optimal performance and reduced waste.
4. Injection Speed: Why Is It Critical for Efficiency?
Injection speed refers to the rate at which material is injected into the mold. Faster injection speeds can significantly reduce cycle times, allowing for greater production efficiency. However, too high a speed may lead to defects. B2B buyers should balance speed with quality to maximize output without compromising the integrity of the molded parts.
5. Shot Size: How Does It Influence Production Volume?
Shot size is the maximum volume of material that can be injected in a single cycle. It is crucial for determining production capacity and is directly linked to the types of products a company can manufacture. Understanding your production volume requirements will help in selecting a machine that aligns with your business goals.
What Are Common Trade Terms in the Injection Molding Industry?
Familiarity with industry jargon is essential for effective communication and negotiation in the B2B space. Here are some common terms you should know:
1. OEM (Original Equipment Manufacturer): What Does It Mean?
An OEM is a company that produces parts and equipment that may be marketed by another manufacturer. In injection molding, OEMs often require specific designs and materials, making it vital for buyers to understand their specifications and quality standards.
2. MOQ (Minimum Order Quantity): Why Is It Relevant?
MOQ refers to the smallest quantity of a product that a supplier is willing to sell. For international buyers, especially from emerging markets, understanding MOQ can help in budgeting and inventory management, as lower MOQs may reduce upfront investment.
3. RFQ (Request for Quotation): How to Use It Effectively?
An RFQ is a document sent to suppliers requesting a quote for specific products or services. It is a critical step in the procurement process, allowing buyers to compare prices and services. Including detailed specifications in an RFQ can lead to more accurate quotes and better negotiation outcomes.
4. Incoterms (International Commercial Terms): What Are They?
Incoterms are internationally recognized rules that define the responsibilities of buyers and sellers in shipping goods. Understanding these terms is essential for international B2B transactions, as they clarify who is responsible for shipping costs, insurance, and risk during transit.
5. Lead Time: Why Should It Be Considered?
Lead time is the time taken from placing an order to receiving the goods. In the injection molding industry, longer lead times can impact production schedules and market responsiveness. Buyers should consider suppliers with competitive lead times to enhance operational efficiency.
By grasping these technical properties and trade terminologies, international B2B buyers can make informed decisions, fostering successful partnerships and optimizing their manufacturing processes.
Navigating Market Dynamics and Sourcing Trends in the Injection Molding Machine Manufacturers Sector
What Are the Key Market Dynamics and Sourcing Trends in the Injection Molding Machine Manufacturers Sector?
The injection molding machine manufacturing sector is experiencing significant growth, driven by rising demand across various industries, including automotive, consumer goods, and medical devices. Globalization and technological advancements are reshaping market dynamics, allowing international B2B buyers from regions such as Africa, South America, the Middle East, and Europe to access diverse suppliers and innovative technologies. Notably, the integration of Industry 4.0 technologies—such as IoT, automation, and AI—enhances operational efficiency and product quality, making it essential for buyers to consider suppliers that embrace these innovations.
Emerging trends also highlight the importance of customization and flexibility in manufacturing processes. As customer preferences shift towards personalized products, injection molding machine manufacturers are increasingly offering customizable solutions to meet specific client needs. Additionally, the rise of e-commerce has accelerated the demand for rapid prototyping and short production runs, prompting manufacturers to adapt their sourcing strategies to ensure agility and responsiveness.
Furthermore, the global push for sustainability is influencing sourcing decisions. Buyers are now prioritizing suppliers who demonstrate a commitment to environmentally friendly practices and materials. Understanding these market dynamics will enable international B2B buyers to make informed sourcing decisions that align with their operational goals and sustainability objectives.
How Are Sustainability and Ethical Sourcing Shaping the Injection Molding Machine Sector?
Sustainability is becoming a critical factor in the injection molding machine manufacturing sector. The environmental impact of plastic production and waste management has raised concerns, prompting manufacturers to adopt eco-friendly practices. For B2B buyers, partnering with suppliers who prioritize sustainability can enhance brand reputation and fulfill corporate social responsibility (CSR) commitments.
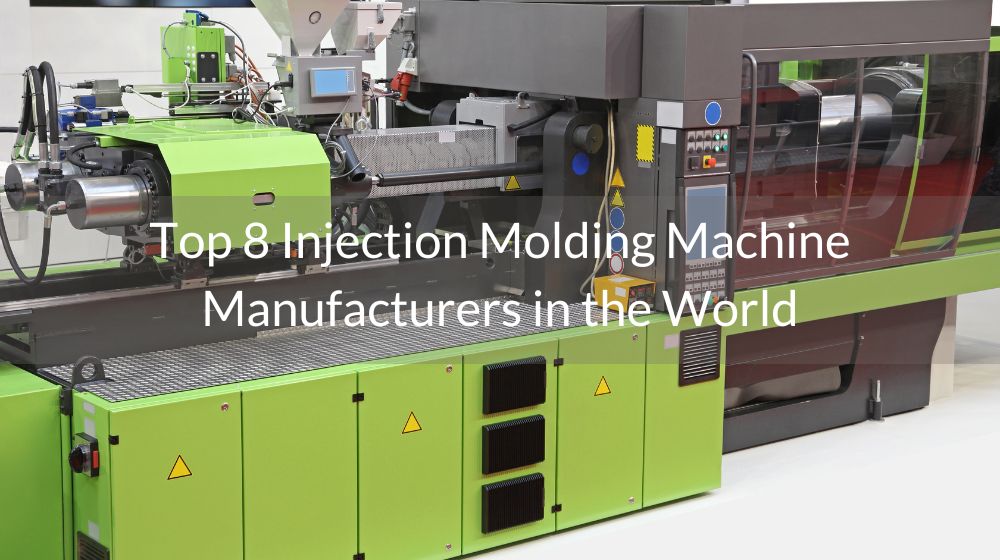
A stock image related to Injection Molding Machine Manufacturers.
Ethical sourcing is increasingly important as consumers demand transparency in supply chains. Buyers should look for manufacturers that adhere to ethical labor practices and have certifications such as ISO 14001, which demonstrates a commitment to environmental management. Additionally, the use of biodegradable and recyclable materials in injection molding processes is gaining traction, offering buyers the opportunity to promote sustainable products in their markets.
Investing in suppliers with ‘green’ certifications not only supports environmental goals but can also lead to long-term cost savings through efficient resource utilization. As global regulations on plastic use tighten, aligning with sustainable manufacturers will help B2B buyers mitigate risks and capitalize on emerging market opportunities.
What Is the Brief Evolution of Injection Molding Machine Manufacturers?
The evolution of injection molding machine manufacturers dates back to the early 20th century when the first machines were developed for producing simple plastic parts. Over the decades, advancements in technology have transformed the industry, enabling manufacturers to produce complex components with greater precision and efficiency. The introduction of electric injection molding machines in the 1990s marked a significant turning point, providing energy savings and improved control over the molding process.
In recent years, the focus has shifted towards automation and the integration of smart technologies, aligning with global trends in Industry 4.0. This evolution has enabled manufacturers to enhance production capabilities while reducing waste and energy consumption. For B2B buyers, understanding this historical context is crucial in identifying suppliers that not only offer advanced technology but also align with contemporary market demands for sustainability and customization.
Frequently Asked Questions (FAQs) for B2B Buyers of Injection Molding Machine Manufacturers
-
How do I choose the right injection molding machine for my business needs?
Selecting the right injection molding machine involves assessing your production requirements, including part size, complexity, and material type. Consider the machine’s clamping force, injection speed, and energy efficiency. Additionally, evaluate the manufacturer’s reputation, customer service, and support capabilities. It’s beneficial to request samples or trial runs to gauge machine performance before making a commitment. -
What are the key features to look for in injection molding machines?
Key features to consider include the machine’s clamping force, injection volume, cycle time, and energy consumption. Advanced technology options, such as programmable controls and automation capabilities, can enhance efficiency. Furthermore, look for features that facilitate easy maintenance and upgrades, as these can significantly reduce downtime and operational costs. -
What is the minimum order quantity (MOQ) for injection molding machines?
The MOQ for injection molding machines varies by manufacturer and can range from a single unit to several machines, depending on the complexity and customization involved. When sourcing from suppliers, it’s essential to clarify MOQ requirements early in the discussions to align production capabilities with your business needs and budget constraints. -
How can I effectively vet injection molding machine manufacturers?
To vet manufacturers, research their industry reputation through customer reviews and case studies. Request references from previous clients and assess their production capabilities, quality certifications, and compliance with international standards. Additionally, consider visiting the manufacturing facility if possible, as this can provide insight into their processes and quality control measures. -
What payment terms should I expect when purchasing injection molding machines?
Payment terms can vary widely among manufacturers but typically include options such as upfront deposits (often 30-50%), progress payments during production, and final payment upon delivery. Ensure to negotiate terms that protect your interests, including warranties and after-sales support. Understanding the terms clearly can prevent disputes and ensure a smoother transaction process. -
How do logistics and shipping affect the purchase of injection molding machines?
Logistics and shipping are critical factors when purchasing injection molding machines, particularly for international buyers. Consider the shipping costs, customs duties, and transit times involved. Work with manufacturers who provide reliable shipping options and clear documentation to facilitate customs clearance. It’s also advisable to have a local logistics partner familiar with importing machinery to streamline the process. -
What quality assurance measures should I look for in injection molding machines?
Quality assurance is vital in ensuring the machines meet specified performance standards. Look for manufacturers that implement rigorous testing protocols, including pre-shipment inspections and certifications such as ISO 9001. Inquire about their after-sales support and warranty policies, as these can indicate the manufacturer’s commitment to quality and customer satisfaction. -
Can injection molding machines be customized to suit specific production requirements?
Yes, many manufacturers offer customization options for injection molding machines to meet specific production needs. Customizations can include modifications in size, injection speed, and material compatibility. When discussing your requirements with suppliers, provide detailed specifications to ensure they can deliver a machine that aligns with your operational goals.
Important Disclaimer & Terms of Use
⚠️ Important Disclaimer
The information provided in this guide, including content regarding manufacturers, technical specifications, and market analysis, is for informational and educational purposes only. It does not constitute professional procurement advice, financial advice, or legal advice.
While we have made every effort to ensure the accuracy and timeliness of the information, we are not responsible for any errors, omissions, or outdated information. Market conditions, company details, and technical standards are subject to change.
B2B buyers must conduct their own independent and thorough due diligence before making any purchasing decisions. This includes contacting suppliers directly, verifying certifications, requesting samples, and seeking professional consultation. The risk of relying on any information in this guide is borne solely by the reader.
Strategic Sourcing Conclusion and Outlook for Injection Molding Machine Manufacturers
In the rapidly evolving landscape of injection molding, the importance of strategic sourcing cannot be overstated. For international B2B buyers, particularly in regions such as Africa, South America, the Middle East, and Europe, understanding the dynamics of sourcing high-quality injection molding machines is crucial. By leveraging strategic sourcing, companies can optimize their supply chains, reduce costs, and enhance product quality, thereby gaining a competitive edge in their respective markets.
How Can Buyers Maximize Value in Strategic Sourcing?
To maximize value, buyers should conduct thorough market research, engage in supplier relationship management, and evaluate the total cost of ownership rather than just the purchase price. Building strong partnerships with manufacturers and understanding the local regulations and market conditions can also facilitate smoother transactions and better service delivery.
What Does the Future Hold for Injection Molding Machine Buyers?
Looking ahead, the injection molding industry is poised for innovation, particularly with advancements in automation and sustainability. As technology continues to evolve, buyers should remain agile and informed, ready to adapt to new trends and shifts in consumer demand.
In conclusion, now is the time to reassess your sourcing strategies and embrace the opportunities that lie ahead. Connect with reputable manufacturers, explore new technologies, and ensure your operations are future-ready. The landscape is changing, and proactive engagement will be key to success in the injection molding sector.