Discover Top Injection Molding Machinery Manufacturers (2025)
Introduction: Navigating the Global Market for Injection Molding Machinery Manufacturers
In the rapidly evolving landscape of global manufacturing, sourcing reliable injection molding machinery manufacturers presents a formidable challenge for international B2B buyers. With the growing demand for high-quality plastic products across diverse industries, from automotive to healthcare, businesses must navigate a complex array of suppliers, technologies, and pricing structures. This guide serves as a comprehensive resource for buyers looking to understand the intricacies of injection molding machinery, offering insights into the various types of machines, their applications, and the critical factors to consider during the supplier vetting process.
Our exploration covers the latest advancements in injection molding technology, including electric and hybrid machines, as well as hydraulic systems. We delve into the essential aspects of cost analysis and return on investment, empowering buyers from regions such as Africa, South America, the Middle East, and Europe to make informed purchasing decisions. By highlighting key manufacturers and their unique offerings, this guide equips you with the knowledge to identify the best partners for your manufacturing needs.
Whether you are a seasoned industry player or a newcomer to the injection molding sector, understanding the market landscape is crucial. This guide not only simplifies the complexities of sourcing but also enhances your ability to negotiate effectively and secure the most suitable machinery for your operations. Prepare to elevate your manufacturing capabilities as you navigate the global market with confidence.
Understanding Injection Molding Machinery Manufacturers Types and Variations
Type Name | Key Distinguishing Features | Primary B2B Applications | Brief Pros & Cons for Buyers |
---|---|---|---|
Electric Injection Molding | High precision, energy-efficient, low maintenance | Automotive, Electronics, Medical Devices | Pros: Energy savings, precision; Cons: Higher initial cost. |
Hydraulic Injection Molding | High clamping force, versatile for large parts | Packaging, Consumer Goods, Automotive | Pros: Cost-effective for large volumes; Cons: Higher energy consumption. |
Hybrid Injection Molding | Combines benefits of electric and hydraulic systems | Medical Devices, Automotive, Consumer Goods | Pros: Flexibility, energy efficiency; Cons: Complexity in maintenance. |
Vertical Injection Molding | Space-saving design, ideal for insert molding | Electronics, Small Parts, Medical Devices | Pros: Compact footprint; Cons: Limited clamping force options. |
Multi-component Injection Molding | Ability to produce parts with multiple materials in one cycle | Automotive, Household Goods, Toys | Pros: Cost-effective for complex parts; Cons: Requires specialized molds. |
What Are the Characteristics of Electric Injection Molding Machines?
Electric injection molding machines are known for their high precision and energy efficiency. They utilize servo motors to drive the injection process, resulting in minimal energy consumption and noise. These machines are particularly suitable for applications requiring tight tolerances, such as in the automotive and medical device industries. When considering an electric machine, buyers should evaluate the initial investment against potential long-term savings in operational costs and maintenance.
Why Choose Hydraulic Injection Molding Machines?
Hydraulic injection molding machines are characterized by their ability to exert high clamping forces, making them ideal for producing large parts and complex shapes. They are widely used in industries such as packaging and consumer goods due to their cost-effectiveness in mass production. Buyers should weigh the benefits of lower upfront costs and operational flexibility against the higher energy consumption and maintenance needs compared to electric counterparts.
What Are the Benefits of Hybrid Injection Molding Machines?
Hybrid injection molding machines combine the advantages of both electric and hydraulic technologies. They offer enhanced flexibility, energy efficiency, and speed, making them suitable for applications in the medical and automotive sectors. When purchasing hybrid machines, buyers should consider the complexity of the technology and the potential for higher maintenance costs, balanced by the operational efficiencies they can provide.
How Do Vertical Injection Molding Machines Stand Out?
Vertical injection molding machines feature a compact design that allows for efficient use of space, making them ideal for small parts and insert molding applications. These machines are commonly used in electronics and medical devices. Buyers should evaluate their production needs, as vertical machines may offer limited clamping force options, which could impact the types of parts that can be produced.
What Are the Advantages of Multi-component Injection Molding?
Multi-component injection molding machines enable the production of complex parts using multiple materials in a single cycle. This technology is particularly beneficial in the automotive and toy industries, where parts often require different properties. Buyers should consider the specialized molds and production processes needed for multi-component systems, which may lead to increased costs but can result in significant time and resource savings in the long run.
Related Video: Lesson 1-HD – Molding Machine Parts and Operation – Technology of Injection Molding
Key Industrial Applications of Injection Molding Machinery Manufacturers
Industry/Sector | Specific Application of Injection Molding Machinery Manufacturers | Value/Benefit for the Business | Key Sourcing Considerations for this Application |
---|---|---|---|
Automotive | Production of dashboard components and exterior panels | High precision and repeatability, reducing waste and costs | Compatibility with industry standards, energy efficiency, and after-sales support |
Packaging | Manufacturing of bottles, containers, and packaging materials | Increased speed of production and customization options | Material compatibility, mold design flexibility, and supplier reliability |
Healthcare | Creation of medical devices and components | Ensures compliance with stringent safety standards | Certifications, cleanroom capabilities, and material traceability |
Consumer Goods | Production of household items like toys and kitchenware | Ability to produce complex designs at scale | Design support, tooling options, and lead time for production |
Electronics | Fabrication of casings and components for gadgets | Enhances product durability and aesthetics | Precision engineering, rapid prototyping capabilities, and technical support |
How Are Injection Molding Machinery Manufacturers Used in the Automotive Sector?
In the automotive industry, injection molding machinery is crucial for producing high-precision components such as dashboard parts and exterior panels. These machines allow manufacturers to create intricate designs with consistent quality, minimizing waste and reducing production costs. International buyers must consider compatibility with automotive industry standards, energy efficiency, and the availability of after-sales support when sourcing machinery.
What Are the Applications of Injection Molding in Packaging?
Packaging is another key sector benefiting from injection molding. Manufacturers use these machines to create a wide variety of containers, bottles, and packaging materials. The technology allows for rapid production cycles and customization, meeting diverse market demands. B2B buyers should focus on material compatibility, mold design flexibility, and the reliability of suppliers to ensure they meet the specific needs of their packaging applications.
How Does Injection Molding Machinery Benefit the Healthcare Industry?
In healthcare, injection molding machines are utilized to produce medical devices and components, ensuring compliance with rigorous safety and regulatory standards. These machines enable the creation of complex shapes and designs that are vital for medical applications. Buyers in this sector must prioritize sourcing from manufacturers with relevant certifications, cleanroom capabilities, and material traceability to guarantee product safety and quality.
What Are the Key Applications for Injection Molding in Consumer Goods?
For consumer goods, injection molding is widely used to manufacture household items such as toys and kitchenware. This process allows for the efficient production of complex designs at scale, enhancing both functionality and aesthetic appeal. When sourcing machinery, international buyers should consider design support, tooling options, and lead times to optimize their production processes and meet market demands effectively.
How Is Injection Molding Utilized in Electronics Manufacturing?
In the electronics sector, injection molding is employed to fabricate casings and internal components for various gadgets. This technology not only improves product durability but also contributes to the overall aesthetics of electronic devices. Buyers should seek precision engineering, rapid prototyping capabilities, and robust technical support to ensure that their injection molding solutions align with the fast-paced nature of the electronics market.
Related Video: How Injection Molding Works
3 Common User Pain Points for ‘Injection Molding Machinery Manufacturers’ & Their Solutions
Scenario 1: The Challenge of Finding Reliable Suppliers for Injection Molding Machinery
The Problem:
B2B buyers often struggle to identify trustworthy injection molding machinery manufacturers, especially in emerging markets like Africa and South America. With numerous suppliers claiming to offer high-quality machines, it can be overwhelming to discern which manufacturers have a proven track record. This uncertainty can lead to costly mistakes, such as purchasing inferior machinery that fails to meet production standards or results in frequent breakdowns.
The Solution:
To navigate this landscape effectively, international buyers should conduct thorough due diligence before making any commitments. Start by leveraging industry networks and online platforms to gather information about potential manufacturers. Platforms like LinkedIn can be invaluable for connecting with other industry professionals and gathering firsthand reviews of manufacturers’ reputations. Furthermore, consider requesting case studies or references from the manufacturers to understand their past performance in similar markets.
Once a shortlist of potential suppliers is created, buyers should engage in detailed discussions about machine specifications, support services, and warranties. This conversation should include inquiries about the manufacturer’s quality control processes and any certifications they hold, such as ISO standards. Additionally, arranging factory visits or virtual tours can provide deeper insights into their operations and commitment to quality.
Scenario 2: Managing High Initial Investment Costs
The Problem:
The capital investment required for injection molding machinery can be a significant hurdle for many B2B buyers, particularly small to medium-sized enterprises (SMEs) in developing regions. The high costs associated with advanced machinery can deter businesses from upgrading or expanding their production capabilities, leading to missed opportunities in competitive markets.
The Solution:
To address these financial constraints, buyers should explore financing options such as leasing or payment plans that allow for lower upfront costs. Many manufacturers offer flexible financing solutions tailored to the needs of their clients. Researching government grants or subsidies for manufacturing upgrades in your region can also help alleviate some of the financial burden.
Additionally, buyers should prioritize purchasing energy-efficient machines that reduce operational costs over time. While the initial price may be higher, these machines can lead to significant savings in energy consumption and maintenance expenses, making them a more economical choice in the long run. Conducting a total cost of ownership (TCO) analysis can be instrumental in understanding the long-term financial benefits of investing in higher-quality machinery.
Scenario 3: Ensuring Technical Support and After-Sales Service
The Problem:
After purchasing injection molding machinery, buyers often face challenges related to technical support and maintenance. Inadequate after-sales service can result in prolonged downtime, which can severely impact production schedules and profitability. Buyers from regions with less established manufacturing infrastructure may find it particularly difficult to obtain timely support.
The Solution:
To mitigate these risks, it is crucial for buyers to thoroughly evaluate the after-sales support offered by manufacturers before making a purchase. This includes understanding the availability of spare parts, the responsiveness of their technical support team, and the options for remote troubleshooting. Engaging with manufacturers that have a local presence or established service networks can provide peace of mind in terms of accessibility to support.
Additionally, buyers should consider investing in training programs for their staff. Many manufacturers offer training sessions that can empower operators and maintenance personnel to handle minor issues independently, thereby reducing reliance on external support. Establishing a proactive maintenance schedule can also help identify and address potential problems before they lead to significant downtimes.
By approaching the procurement process with these strategies, international B2B buyers can navigate the complexities of working with injection molding machinery manufacturers more effectively, ensuring that they make informed decisions that support their business growth.
Strategic Material Selection Guide for Injection Molding Machinery Manufacturers
When selecting materials for injection molding machinery, it is crucial for manufacturers to consider properties that directly impact product performance, manufacturing complexity, and end-use applications. Here, we analyze four common materials used in injection molding, focusing on their key properties, advantages and disadvantages, and considerations for international B2B buyers.
What Are the Key Properties of Polypropylene (PP) for Injection Molding?
Polypropylene (PP) is a widely used thermoplastic known for its versatility. It has a melting temperature range of approximately 160-170°C and exhibits good chemical resistance, making it suitable for various applications. Its low density contributes to lightweight products, while its moderate tensile strength ensures durability.
Pros: Polypropylene is cost-effective, has excellent fatigue resistance, and is easy to mold, making it suitable for high-volume production. Its recyclability is an added advantage for environmentally conscious buyers.
Cons: However, PP has lower temperature resistance compared to other materials, which may limit its use in high-heat applications. It can also be prone to warping if not processed correctly.
Impact on Application: PP is commonly used in packaging, automotive components, and consumer goods. Its chemical resistance makes it suitable for containers and lids, but buyers should ensure compatibility with specific media.
Considerations for International Buyers: Compliance with standards such as ASTM D4101 is essential. Buyers from regions like Africa and South America should consider local regulations regarding recycling and material safety.
How Does Polycarbonate (PC) Perform in Injection Molding?
Polycarbonate (PC) is known for its exceptional impact resistance and clarity. It has a high glass transition temperature of around 147°C, making it suitable for applications requiring durability and transparency, such as safety goggles and automotive parts.
Pros: Its high strength-to-weight ratio and excellent dimensional stability are significant advantages. PC is also resistant to UV light, which is beneficial for outdoor applications.
Cons: The primary drawback is its susceptibility to scratching, which can affect product aesthetics. Additionally, PC can be more expensive than other materials, impacting overall project budgets.
Impact on Application: PC is ideal for applications requiring transparency and strength, such as optical lenses and protective covers. However, the potential for scratching should be considered in design.
Considerations for International Buyers: Buyers should ensure compliance with standards such as ISO 7391 for safety-related applications. In regions like the Middle East, where UV exposure is high, selecting UV-stabilized grades of PC is advisable.
What Are the Advantages of Acrylonitrile Butadiene Styrene (ABS)?
Acrylonitrile Butadiene Styrene (ABS) is a popular thermoplastic known for its toughness and impact resistance. It has a processing temperature range of 220-250°C and offers good dimensional stability.
Pros: ABS is easy to machine and can be painted or glued, making it versatile for various applications. Its resistance to heat and chemicals makes it suitable for automotive and consumer products.
Cons: However, ABS is less resistant to UV light, which can lead to degradation in outdoor applications. It is also more expensive than some alternatives like PP.
Impact on Application: ABS is commonly used in the production of housings, toys, and automotive parts. Its versatility allows for a broad range of applications, but UV exposure must be managed.
Considerations for International Buyers: Compliance with ASTM D4673 is crucial. Buyers from Europe may prefer materials that meet REACH regulations, ensuring safety and environmental compliance.
Why Choose Nylon (Polyamide) for Injection Molding?
Nylon, or polyamide, is known for its excellent mechanical properties and resistance to wear and abrasion. It has a melting point of approximately 220-260°C, making it suitable for high-temperature applications.
Pros: Nylon exhibits high tensile strength and flexibility, making it ideal for components that undergo stress. Its chemical resistance is also noteworthy, particularly against oils and fuels.
Cons: The main limitations include its hygroscopic nature, which can lead to dimensional changes if not properly dried before processing. Additionally, nylon can be more expensive than other thermoplastics.
Impact on Application: Nylon is widely used in automotive, industrial, and electrical applications. Its strength and flexibility make it suitable for gears and bearings, but moisture control is essential.
Considerations for International Buyers: Buyers should be aware of standards such as ISO 1874 for nylon applications. In regions like South America, where humidity may be high, ensuring proper material storage and handling is critical.
Summary Table of Material Selection for Injection Molding Machinery Manufacturers
Material | Typical Use Case for Injection Molding Machinery Manufacturers | Key Advantage | Key Disadvantage/Limitation | Relative Cost (Low/Med/High) |
---|---|---|---|---|
Polypropylene (PP) | Packaging, automotive components, consumer goods | Cost-effective and easy to mold | Lower temperature resistance | Low |
Polycarbonate (PC) | Safety goggles, automotive parts, optical lenses | Exceptional impact resistance | Susceptible to scratching | High |
Acrylonitrile Butadiene Styrene (ABS) | Housings, toys, automotive parts | Toughness and impact resistance | Less UV resistance | Medium |
Nylon (Polyamide) | Automotive, industrial components, gears | High tensile strength and flexibility | Hygroscopic nature | Medium |
This strategic material selection guide provides actionable insights for international B2B buyers, helping them make informed decisions when sourcing injection molding machinery and materials.
In-depth Look: Manufacturing Processes and Quality Assurance for Injection Molding Machinery Manufacturers
What Are the Key Manufacturing Processes for Injection Molding Machinery?
The manufacturing process for injection molding machinery is complex and involves several critical stages that ensure high quality and efficiency. Understanding these stages is essential for B2B buyers looking to invest in reliable machinery.
What Are the Main Stages of Manufacturing Injection Molding Machinery?
-
Material Preparation
– The first stage involves selecting and preparing raw materials, typically thermoplastics or thermosetting plastics. These materials are sourced based on the specific requirements of the intended application, such as strength, flexibility, or temperature resistance.
– The materials are then dried, granulated, and fed into the injection molding machine. This preparation is crucial, as moisture or impurities can lead to defects in the final product. -
Forming
– The forming process involves melting the prepared plastic material and injecting it into a mold under high pressure. This stage is critical for achieving the desired shape and detail in the final product.
– Key techniques in this phase include injection molding, blow molding, and compression molding. Each technique has its advantages depending on the complexity and type of the part being produced. -
Assembly
– After forming, the various components of the injection molding machine are assembled. This includes integrating the injection unit, clamping unit, and control systems.
– Precision in assembly is vital, as any misalignment can affect the performance and durability of the machine. Advanced assembly techniques often employ automation to enhance accuracy. -
Finishing
– The final stage involves surface treatment and finishing processes, such as polishing, coating, or painting, to ensure the machinery not only functions well but also meets aesthetic standards.
– Finishing processes may also include quality checks to ensure that the machine meets specified tolerances and performance metrics.
How Do Quality Assurance Practices Ensure the Reliability of Injection Molding Machinery?
Quality assurance (QA) is an integral part of the manufacturing process for injection molding machinery. Implementing robust QA practices ensures that the machines produced are reliable, efficient, and meet international standards.
What Are the Relevant International Standards for Injection Molding Machinery?
-
ISO 9001
– This standard focuses on quality management systems and is essential for manufacturers aiming to enhance customer satisfaction through effective system implementation. Compliance with ISO 9001 demonstrates a commitment to quality and continuous improvement. -
CE Marking
– For machinery sold in Europe, CE marking indicates compliance with EU safety, health, and environmental protection standards. This certification is crucial for international buyers to ensure that the machinery meets stringent European regulations. -
API Standards
– In specific industries, such as oil and gas, adherence to American Petroleum Institute (API) standards is necessary. This ensures that the machinery can withstand demanding conditions and meet industry-specific requirements.
What Are the Key Quality Control Checkpoints in the Manufacturing Process?
Quality control (QC) involves several checkpoints throughout the manufacturing process to ensure that each stage meets predefined standards:
-
Incoming Quality Control (IQC)
– This step involves inspecting raw materials upon arrival to verify that they meet quality specifications. Any materials that do not meet standards are rejected or returned. -
In-Process Quality Control (IPQC)
– During the manufacturing process, various inspections are conducted to monitor the production line’s performance. This includes checking the temperature, pressure, and timing during the injection process. -
Final Quality Control (FQC)
– After assembly, the final product undergoes comprehensive testing to ensure it meets all specifications. This may include functional tests, performance evaluations, and safety checks.
What Common Testing Methods Are Used in Quality Assurance for Injection Molding Machinery?
Various testing methods are employed to validate the quality and performance of injection molding machinery:
- Functional Testing: Ensures that all parts of the machine operate correctly under normal and peak conditions.
- Dimensional Inspection: Uses precision measuring tools to verify that the dimensions of the components are within specified tolerances.
- Material Testing: Involves testing the mechanical properties of the materials used in the machinery to ensure they meet industry standards.
How Can B2B Buyers Verify the Quality Control Practices of Injection Molding Machinery Manufacturers?
For international B2B buyers, verifying the quality control practices of potential suppliers is crucial in ensuring a reliable partnership:
-
Supplier Audits
– Conducting on-site audits allows buyers to evaluate the manufacturing processes, quality control measures, and overall operational efficiency of the supplier. -
Requesting Quality Reports
– Buyers should request quality assurance reports that detail the QC processes, testing methods used, and compliance with relevant standards. This transparency builds trust and confidence. -
Third-Party Inspections
– Engaging third-party inspection services can provide an unbiased assessment of the supplier’s quality practices. These inspections can validate compliance with international standards and identify any potential issues.
What Are the Quality Control Nuances for International B2B Buyers from Africa, South America, the Middle East, and Europe?
Understanding regional differences in quality assurance practices is essential for international buyers:
- Regional Standards: Buyers should be aware of local regulations and standards that may differ from international norms. For instance, while ISO standards are widely recognized, some regions may have specific local certifications that are equally important.
- Cultural Considerations: Building relationships with suppliers from different cultural backgrounds can impact communication and negotiation processes. Understanding these nuances can facilitate smoother transactions.
- Logistics and Supply Chain: Buyers must consider the logistics involved in sourcing machinery from different regions, including shipping times, customs regulations, and potential tariffs that could affect overall costs.
By comprehensively understanding the manufacturing processes and quality assurance practices associated with injection molding machinery, B2B buyers can make informed decisions, ensuring that they partner with manufacturers that meet their stringent requirements for quality and reliability.
Practical Sourcing Guide: A Step-by-Step Checklist for ‘Injection Molding Machinery Manufacturers’
In today’s competitive landscape, selecting the right injection molding machinery manufacturer is crucial for ensuring operational efficiency and product quality. This practical sourcing guide provides a structured approach for B2B buyers, particularly those operating in Africa, South America, the Middle East, and Europe, to navigate the complexities of procurement in this industry.
Step 1: Define Your Technical Specifications
Establishing clear technical specifications is the foundation of your sourcing process. Identify the types of products you intend to manufacture, the required production volume, and specific attributes like size, weight, and material compatibility. This clarity will help you communicate effectively with potential suppliers and ensure they can meet your needs.
Step 2: Research Reputable Manufacturers
Conduct thorough research to identify established injection molding machine manufacturers. Look for companies with a strong track record in your industry, positive customer reviews, and proven technological innovations. Consider their geographical presence, as local suppliers may offer better support and lower shipping costs.
- Long-Tail Keyword: What are the top injection molding machinery manufacturers?
- Action: Compile a list of at least five manufacturers that meet your criteria.
Step 3: Evaluate Supplier Certifications
Before proceeding with any supplier, verify their certifications and compliance with international quality standards. Look for ISO certifications, CE marking, and any industry-specific accreditations that demonstrate their commitment to quality and safety. This step is vital to ensure that the machinery meets regulatory requirements in your region.
Step 4: Request Detailed Quotations
Once you’ve narrowed down your list, request detailed quotations from the selected manufacturers. Ensure that the quotes include not only the machine prices but also shipping costs, warranty terms, and any additional service agreements. This comprehensive view will aid in making a cost-effective decision.
- Long-Tail Keyword: How to compare quotes for injection molding machinery?
- Action: Create a comparison chart to analyze key features, pricing, and terms side by side.
Step 5: Assess After-Sales Support and Services
After-sales support is crucial for maintaining machine performance and minimizing downtime. Inquire about the manufacturer’s service offerings, including training, maintenance, and spare parts availability. A supplier that provides robust after-sales support can significantly enhance your operational efficiency.
Step 6: Visit Manufacturing Facilities (If Possible)
If feasible, plan a visit to the manufacturing facilities of your shortlisted suppliers. This visit can provide valuable insights into their production capabilities, quality control processes, and overall operational efficiency. Additionally, meeting the team behind the machinery can foster better communication and trust.
Step 7: Check Customer References
Finally, reach out to existing customers of the manufacturers you are considering. Ask them about their experiences regarding machine performance, reliability, and the quality of customer service. This firsthand feedback can provide critical insights that are not available through marketing materials alone.
By following this structured checklist, B2B buyers can make informed decisions when sourcing injection molding machinery, ensuring that they choose a supplier that aligns with their specific needs and business objectives.
Comprehensive Cost and Pricing Analysis for Injection Molding Machinery Manufacturers Sourcing
What are the Key Cost Components in Injection Molding Machinery Manufacturing?
When sourcing injection molding machinery, understanding the cost structure is vital for making informed purchasing decisions. The primary cost components include:
-
Materials: The raw materials used in manufacturing injection molding machines, such as steel, aluminum, and various polymers, contribute significantly to the overall cost. Fluctuations in material prices can directly impact the final machine pricing.
-
Labor: Skilled labor is essential in the production of injection molding machines. Labor costs vary by region; for instance, countries in Europe may have higher labor costs compared to those in South America or Africa, affecting the overall pricing strategy.
-
Manufacturing Overhead: This includes costs related to utilities, equipment maintenance, and factory space. Manufacturers with advanced technology or those that prioritize sustainability may have higher overhead costs, which can influence pricing.
-
Tooling: Custom tooling is often required for specific machine configurations. The complexity and precision of tooling can significantly affect the cost, especially for bespoke machinery tailored to unique specifications.
-
Quality Control (QC): Ensuring the machinery meets international standards often requires rigorous QC processes. This adds to the manufacturing costs but is critical for maintaining quality and performance, especially for high-stakes industries like automotive and healthcare.
-
Logistics: Transportation and shipping costs must be factored in, particularly for international buyers. These costs can vary significantly based on the Incoterms agreed upon, the distance from the manufacturer, and the mode of transportation used.
-
Margin: Manufacturers typically include a profit margin in their pricing. This margin can vary based on the manufacturer’s reputation, market demand, and competitive landscape.
How Do Price Influencers Impact Injection Molding Machinery Costs?
Several factors influence the pricing of injection molding machinery:
-
Volume and Minimum Order Quantity (MOQ): Larger orders often lead to reduced per-unit costs due to economies of scale. Buyers should negotiate MOQs that align with their production needs to maximize cost efficiency.
-
Specifications and Customization: Customized machines tailored to specific requirements will generally incur higher costs. Buyers should clearly define their needs to avoid unnecessary expenses.
-
Materials and Quality Certifications: The choice of materials directly impacts durability and performance. Additionally, machines with recognized quality certifications may command a premium price but often result in lower maintenance costs over time.
-
Supplier Factors: The reputation and reliability of the supplier can influence pricing. Established manufacturers may charge more due to their proven track record, while emerging suppliers might offer competitive rates to gain market share.
-
Incoterms: Understanding Incoterms is crucial for international buyers. Terms like FOB (Free on Board) and CIF (Cost, Insurance, and Freight) affect the total landed cost of the machinery, influencing budget decisions.
What are the Best Buyer Tips for Sourcing Injection Molding Machinery?
International B2B buyers, especially from Africa, South America, the Middle East, and Europe, should consider the following tips:
-
Negotiate Wisely: Leverage your purchasing power, especially if ordering in bulk. Establishing long-term relationships with suppliers can lead to better pricing and terms.
-
Evaluate Total Cost of Ownership (TCO): Look beyond the initial purchase price. Consider maintenance, operational efficiency, and energy consumption, which can significantly affect long-term costs.
-
Understand Pricing Nuances for International Markets: Different regions may experience varying pricing structures due to local market conditions, tariffs, and currency fluctuations. Being aware of these factors can help buyers make more informed decisions.
-
Request Detailed Quotations: Ensure that all cost components are transparently listed in quotations. This will help in comparing offers from different manufacturers and avoiding hidden costs.
Disclaimer
The prices discussed in this analysis are indicative and can vary based on market conditions, specific machine configurations, and other factors. It is recommended that buyers conduct thorough research and engage directly with manufacturers for accurate pricing.
Alternatives Analysis: Comparing Injection Molding Machinery Manufacturers With Other Solutions
In the competitive landscape of manufacturing, B2B buyers often seek the most effective methods for producing high-quality plastic products. While injection molding machinery is a dominant choice due to its efficiency and precision, exploring alternative solutions can provide additional options that may better fit specific operational needs or budget constraints. Below, we compare injection molding machinery manufacturers with two viable alternatives: 3D printing and blow molding.
Comparison Table of Injection Molding vs. Alternatives
Comparison Aspect | Injection Molding Machinery Manufacturers | 3D Printing | Blow Molding |
---|---|---|---|
Performance | High precision, capable of mass production | Variable precision, suitable for prototyping and low-volume production | High speed, ideal for hollow objects |
Cost | High initial investment, lower cost per unit at scale | Lower initial cost, higher cost per unit for larger runs | Moderate initial investment, cost-effective for larger volumes |
Ease of Implementation | Requires specialized knowledge and training | User-friendly, minimal training required | Moderate complexity, requires specific machinery |
Maintenance | Regular maintenance needed, parts replacement common | Low maintenance, limited wear and tear | Moderate maintenance, machinery upkeep necessary |
Best Use Case | Large-scale production of complex parts | Rapid prototyping, customized designs | Production of containers and hollow shapes |
What Are the Pros and Cons of 3D Printing as an Alternative?
3D printing, or additive manufacturing, presents a compelling alternative, particularly for businesses focused on innovation and customization. Its primary advantage lies in its capability to produce complex geometries without the need for expensive molds. This makes it ideal for prototyping and small-scale production runs, allowing businesses to iterate designs quickly. However, the limitations of 3D printing become apparent when it comes to speed and material properties, as it is generally slower than injection molding and may not achieve the same level of material strength or surface finish.
How Does Blow Molding Compare to Injection Molding Machinery?
Blow molding serves as another viable alternative, especially for manufacturers specializing in hollow products such as bottles and containers. This method is known for its high-speed production capabilities, making it cost-effective for large volumes. While the initial investment in blow molding machinery can be moderate, the cost per unit decreases significantly at scale. However, blow molding is limited to specific applications and does not offer the same versatility in part design as injection molding. As such, businesses must assess their product line to determine if blow molding aligns with their manufacturing needs.
How Can B2B Buyers Choose the Right Solution?
When selecting the appropriate manufacturing solution, B2B buyers should consider several factors, including production volume, product complexity, and budget. If the goal is to produce intricate designs in large quantities, injection molding machinery may be the best choice despite the higher initial costs. Conversely, if the need is for flexibility and rapid prototyping, 3D printing could be more beneficial. For those focused on producing hollow objects efficiently, blow molding presents a strong case. Ultimately, understanding the specific requirements of your production process will guide you in making the most informed decision for your business.
Essential Technical Properties and Trade Terminology for Injection Molding Machinery Manufacturers
What Are the Key Technical Properties of Injection Molding Machinery?
When selecting injection molding machinery, understanding specific technical properties is crucial for B2B buyers to ensure optimal performance and efficiency. Here are some essential specifications to consider:
1. Clamping Force
Clamping force is the amount of pressure applied to hold the mold closed during the injection process, measured in kilonewtons (kN) or tons. This force is critical because it affects the quality of the molded part. Insufficient clamping force can lead to defects such as flashing, while excessive force may cause mold damage. For buyers, selecting a machine with the appropriate clamping force for their specific applications ensures product quality and reduces waste.
2. Injection Speed
Injection speed refers to how quickly the molten plastic is injected into the mold. Measured in millimeters per second (mm/s), this specification is vital for producing intricate designs and high-volume parts. Faster injection speeds can improve cycle times but may require careful management to avoid issues like short shots or material degradation. Understanding the required injection speed helps buyers align machine capabilities with production goals.
3. Material Compatibility
Different injection molding machines are designed to process various types of materials, such as thermoplastics, thermosets, or elastomers. It’s essential for buyers to assess the machine’s compatibility with the materials they intend to use, as this can significantly impact production efficiency and product quality. Machines that can handle a broader range of materials often provide greater flexibility and adaptability for changing market demands.
4. Tolerances
Tolerances define the allowable variation in dimensions of molded parts. High precision is crucial in industries such as automotive and medical, where even slight deviations can lead to significant failures. Buyers should look for machines that can consistently achieve the required tolerances for their specific applications, as this will affect both part performance and assembly processes.
5. Energy Consumption
With increasing pressure on manufacturers to reduce costs and environmental impact, energy consumption is a vital consideration. Machines with lower energy requirements can lead to significant savings over time. Buyers should evaluate the energy efficiency ratings of different machines, as this can influence long-term operational costs and sustainability initiatives.
What Are the Common Trade Terms in Injection Molding?
Understanding industry jargon is essential for effective communication and negotiation with injection molding machinery manufacturers. Here are some common terms used in the trade:
1. OEM (Original Equipment Manufacturer)
An OEM is a company that produces parts or equipment that may be marketed by another manufacturer. In the context of injection molding, this term is relevant when discussing machine sourcing and the quality of components. Buyers should consider whether they are purchasing from an OEM or a reseller, as this can impact warranty and support services.
2. MOQ (Minimum Order Quantity)
MOQ refers to the smallest quantity of a product that a supplier is willing to sell. This term is crucial for buyers who need to manage costs while ensuring they meet production requirements. Understanding the MOQ can help in budgeting and determining whether a supplier can accommodate small or large production runs effectively.
3. RFQ (Request for Quotation)
An RFQ is a document sent to suppliers requesting pricing for specific products or services. In injection molding, RFQs are often used to solicit competitive bids for machinery or parts. Buyers should be prepared to provide detailed specifications to receive accurate quotations, ensuring they select the best option based on price and capability.
4. Incoterms
Incoterms (International Commercial Terms) are a series of predefined commercial terms used in international trade. These terms clarify the responsibilities of buyers and sellers regarding shipping, insurance, and tariffs. Familiarity with Incoterms helps buyers understand their obligations and risks when importing machinery or materials from other countries.
5. Cycle Time
Cycle time is the total time required to complete one production cycle, including injection, cooling, and ejection of the molded part. Reducing cycle time is essential for improving productivity and profitability. Buyers should inquire about the cycle times of different machines to ensure they meet their production schedules.
By grasping these technical properties and trade terms, B2B buyers can make informed decisions that align with their operational needs and strategic goals in the injection molding sector.
Navigating Market Dynamics and Sourcing Trends in the Injection Molding Machinery Manufacturers Sector
What Are the Current Market Dynamics and Key Trends in Injection Molding Machinery?
The injection molding machinery market is witnessing robust growth, driven by increasing demand for plastic products across various sectors, including automotive, healthcare, and consumer goods. Key global drivers include rapid industrialization in emerging economies such as South Africa, Brazil, and Vietnam, which are investing heavily in manufacturing capabilities. Additionally, advancements in technology, such as automation and Industry 4.0, are revolutionizing production processes, making them more efficient and cost-effective.
For international B2B buyers, understanding current and emerging sourcing trends is critical. The rise of smart manufacturing technologies, including IoT-enabled machinery, is enhancing operational efficiency and reducing downtime. Moreover, there is a growing preference for suppliers that offer comprehensive service packages, including training and technical support, which can be crucial for ensuring smooth operations post-purchase.
A notable trend is the shift towards customized solutions. Manufacturers are increasingly focusing on modular and adaptable machinery that can be tailored to specific production needs. This flexibility is particularly advantageous for businesses looking to scale operations or pivot to different product lines without incurring significant overhead costs. Buyers from Africa, South America, the Middle East, and Europe should prioritize manufacturers that exhibit innovation and offer scalable solutions to stay competitive in a dynamic market.
How Does Sustainability Impact Sourcing in the Injection Molding Machinery Sector?
Sustainability is becoming a pivotal factor in the sourcing decisions of B2B buyers in the injection molding machinery sector. The environmental impact of plastic production, coupled with increasing regulatory pressures, is driving manufacturers to adopt greener practices. Buyers should consider suppliers that prioritize sustainability in their operations, including those that use recycled materials or environmentally friendly production processes.
Ethical sourcing is equally important; buyers are encouraged to engage with manufacturers that demonstrate transparency in their supply chains. This includes adherence to labor standards and responsible sourcing of raw materials. Certifications such as ISO 14001 (Environmental Management) or OHSAS 18001 (Occupational Health and Safety) can serve as indicators of a manufacturer’s commitment to sustainable practices.
In addition to compliance, manufacturers are increasingly offering ‘green’ certifications for their machinery, which can help buyers meet their own sustainability goals. Investing in energy-efficient machines can lead to significant long-term savings and reduced environmental footprints, making it a strategic choice for B2B buyers who are mindful of both costs and environmental impact.
What Is the Evolution of Injection Molding Machinery Manufacturing?
The evolution of injection molding machinery manufacturing has been marked by technological advancements and increasing complexity in production requirements. Initially, injection molding machines were predominantly hydraulic and mechanically operated. However, the transition to electric and hybrid systems has significantly enhanced precision, efficiency, and energy consumption.
Over the years, manufacturers have increasingly focused on automation and smart technology integration, enabling real-time monitoring and data analytics to optimize production processes. This evolution is not merely about machinery but also encompasses the entire ecosystem of services, including maintenance, training, and post-sale support, making it crucial for international B2B buyers to choose suppliers that can deliver comprehensive solutions.
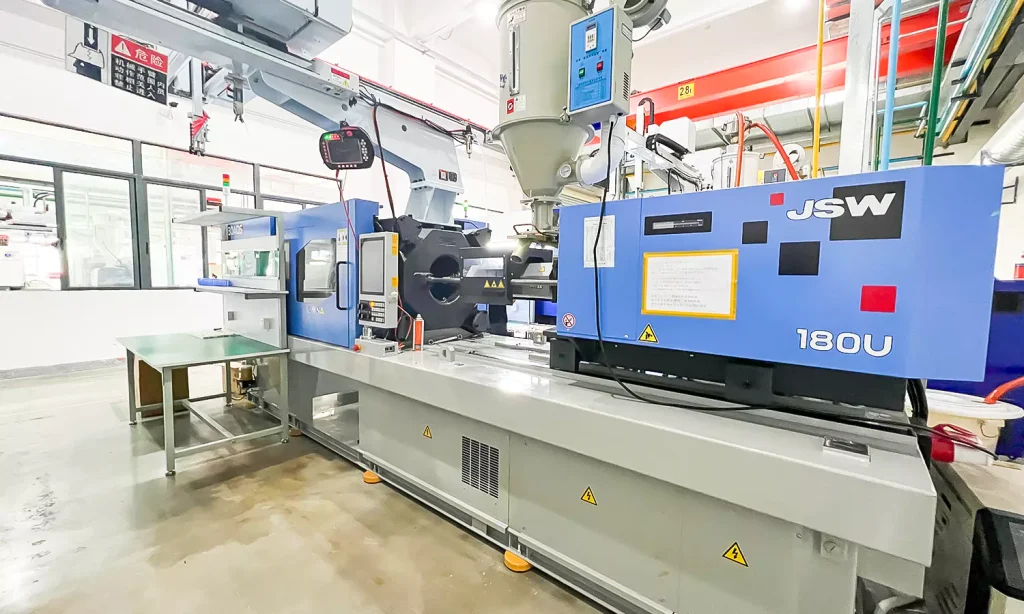
A stock image related to Injection Molding Machinery Manufacturers.
As the industry continues to innovate, understanding these historical shifts can provide buyers with the insights needed to make informed purchasing decisions and leverage the latest technologies for their operational needs.
Frequently Asked Questions (FAQs) for B2B Buyers of Injection Molding Machinery Manufacturers
-
How do I choose the right injection molding machinery manufacturer for my business?
Choosing the right injection molding machinery manufacturer involves evaluating several factors. First, assess the manufacturer’s reputation in the industry, looking for reviews and testimonials from previous clients. Next, consider their specialization—do they offer machines suitable for your specific applications, such as automotive or medical? Additionally, inquire about their customer support and after-sales services, as ongoing support is crucial for operational efficiency. Lastly, consider their production capacity, lead times, and whether they can accommodate your specific needs regarding customization. -
What are the key factors to consider when evaluating injection molding machines?
When evaluating injection molding machines, consider the machine’s clamping force, cycle time, and energy efficiency. Clamping force affects the type of materials and the complexity of parts you can produce. Cycle time determines productivity and overall efficiency, while energy consumption can impact operational costs. Additionally, assess the machine’s flexibility for different applications, ease of maintenance, and availability of spare parts. Lastly, consider any technological advancements, such as automation features, that can enhance your manufacturing process. -
What is the minimum order quantity (MOQ) when sourcing injection molding machinery?
The minimum order quantity (MOQ) for injection molding machinery can vary significantly among manufacturers. Some manufacturers may have no MOQ for standard machines, while others may require orders for multiple units to justify production costs. It’s essential to communicate your specific needs and production plans with potential suppliers. This dialogue can help you negotiate better terms, especially if you are a small to mid-sized company. Always confirm the MOQ before entering into a contract to avoid unexpected costs. -
What payment terms should I expect when purchasing injection molding machinery?
Payment terms for injection molding machinery can range from upfront payments to installments based on production milestones. Many manufacturers require a deposit (often 30-50%) upon order confirmation, with the balance due before shipment or upon delivery. It’s crucial to negotiate terms that align with your cash flow and financing options. Additionally, consider discussing the possibility of letters of credit or escrow services for larger purchases to ensure security for both parties. Always review the terms in your contract carefully. -
How can I ensure quality assurance when sourcing injection molding machinery?
To ensure quality assurance when sourcing injection molding machinery, request detailed specifications and certifications from manufacturers. Look for compliance with international standards such as ISO or CE, which can indicate a commitment to quality. Additionally, inquire about their quality control processes and whether they conduct regular inspections during production. If possible, visit the manufacturing facility or request a virtual tour. Finally, consider requesting samples or trial runs of the machinery to evaluate performance before making a significant investment. -
What are the logistics considerations when importing injection molding machinery?
Logistics for importing injection molding machinery involve several key considerations, including shipping methods, customs clearance, and transportation costs. Determine whether you will use air freight for faster delivery or sea freight for cost-effectiveness. Understand the customs regulations in your country to ensure compliance, as duties and tariffs can significantly impact overall costs. Additionally, work with a reliable logistics partner who can assist with transportation and customs processes, ensuring your machinery arrives safely and on time. -
How do I vet potential injection molding machinery suppliers effectively?
Vetting potential injection molding machinery suppliers involves researching their background, capabilities, and reliability. Start by checking their industry reputation through online reviews and referrals. Request case studies or examples of their previous work to evaluate their experience in your specific industry. Additionally, assess their production capacity and lead times to ensure they can meet your demands. Finally, conduct a site visit if possible, or arrange a virtual meeting to discuss your requirements and gauge their customer service approach. -
Can injection molding machines be customized for specific applications?
Yes, many injection molding machines can be customized to suit specific applications. Manufacturers often offer various configurations and options, such as different clamping forces, injection speeds, and specialized molds. When discussing customization, provide detailed specifications regarding your production needs, including material types and part complexity. This dialogue will help the manufacturer suggest the best solutions tailored to your requirements. Keep in mind that customization may affect lead times and costs, so be prepared for potential adjustments to your project timeline and budget.
Important Disclaimer & Terms of Use
⚠️ Important Disclaimer
The information provided in this guide, including content regarding manufacturers, technical specifications, and market analysis, is for informational and educational purposes only. It does not constitute professional procurement advice, financial advice, or legal advice.
While we have made every effort to ensure the accuracy and timeliness of the information, we are not responsible for any errors, omissions, or outdated information. Market conditions, company details, and technical standards are subject to change.
B2B buyers must conduct their own independent and thorough due diligence before making any purchasing decisions. This includes contacting suppliers directly, verifying certifications, requesting samples, and seeking professional consultation. The risk of relying on any information in this guide is borne solely by the reader.
Strategic Sourcing Conclusion and Outlook for Injection Molding Machinery Manufacturers
In conclusion, strategic sourcing of injection molding machinery is paramount for international B2B buyers, particularly in emerging markets across Africa, South America, the Middle East, and Europe. By prioritizing manufacturers that offer high-quality, innovative solutions like Haitian International, ENGEL, and Milacron, businesses can enhance their operational efficiency and product quality. Understanding the unique strengths and offerings of top manufacturers allows buyers to make informed decisions, ensuring they select partners that align with their specific industry needs, whether it be automotive, healthcare, or consumer goods.
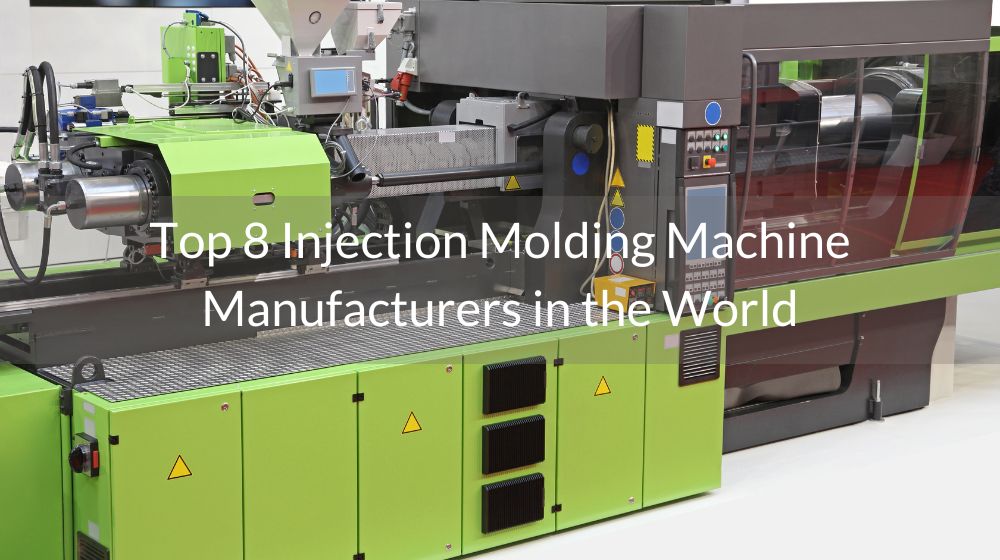
A stock image related to Injection Molding Machinery Manufacturers.
Moreover, the dynamic landscape of injection molding technology—characterized by advancements in automation, energy efficiency, and customization—presents significant opportunities for competitive advantage. As you explore potential partnerships, consider not only the machinery’s capabilities but also the manufacturer’s commitment to customer service and support.
Looking ahead, the demand for injection-molded products is expected to grow, driven by innovations and sustainability trends. Now is the time for B2B buyers to engage with reputable manufacturers and explore how strategic sourcing can lead to long-term success in a rapidly evolving marketplace. Take the next step in your sourcing journey and invest in machinery that propels your business forward.