Discover Top Kitchen Basket Manufacturers: Your Essential Guide (2025)
Introduction: Navigating the Global Market for kitchen basket manufacturer
Navigating the global market for kitchen basket manufacturers can present significant challenges for international B2B buyers. Sourcing quality kitchen baskets that meet diverse consumer preferences and regulatory standards is crucial for success in this competitive landscape. Buyers from regions like Africa, South America, the Middle East, and Europe face unique hurdles, including varying market demands and supply chain complexities. This guide aims to demystify the procurement process, offering actionable insights to streamline your sourcing strategy.
Within this comprehensive resource, we will explore the various types of kitchen baskets available, their applications in both residential and commercial settings, and the critical factors to consider when vetting suppliers. Understanding the intricacies of cost structures and pricing strategies will also be covered, empowering buyers to negotiate better deals and maximize value. Additionally, we will provide tips on assessing quality assurance measures and compliance with international standards, ensuring that your chosen products not only meet but exceed expectations.
By equipping yourself with the knowledge contained in this guide, you will be able to make informed purchasing decisions that align with your business goals. Whether you’re looking to enhance your product line or enter new markets, our insights will help you navigate the complexities of the global kitchen basket industry with confidence.
Understanding kitchen basket manufacturer Types and Variations
Type Name | Key Distinguishing Features | Primary B2B Applications | Brief Pros & Cons for Buyers |
---|---|---|---|
Wire Kitchen Baskets | Made from stainless steel or coated wire; lightweight and durable | Food storage and organization in restaurants, catering services | Pros: Easy to clean, good airflow; Cons: Can rust if not coated properly. |
Plastic Kitchen Baskets | Molded from high-density polyethylene; lightweight and colorful | Food prep, storage in supermarkets, and retail environments | Pros: Cost-effective, versatile; Cons: May not withstand high temperatures. |
Wooden Kitchen Baskets | Crafted from various woods; often handcrafted for aesthetic appeal | Gourmet food stores, artisanal markets | Pros: Attractive, sturdy; Cons: Higher cost, requires maintenance to prevent damage. |
Collapsible Kitchen Baskets | Made from flexible materials; can be folded for storage | Food delivery services, event catering | Pros: Space-saving, portable; Cons: Less durable than rigid options. |
Specialty Kitchen Baskets | Designed for specific food items (e.g., bread, fruits); often custom-made | Bakeries, fruit markets, specialty food retailers | Pros: Tailored solutions for specific needs; Cons: May require larger minimum orders. |
What Are Wire Kitchen Baskets and Their B2B Relevance?
Wire kitchen baskets are primarily constructed from stainless steel or coated wire, making them both lightweight and durable. Their design allows for good airflow, which is essential for preserving food items. B2B buyers in the restaurant and catering industries favor these baskets due to their ease of cleaning and effectiveness in food storage. However, buyers should consider the potential for rust if the wire is not properly coated, particularly in humid environments.
How Do Plastic Kitchen Baskets Serve B2B Needs?
Plastic kitchen baskets are molded from high-density polyethylene, offering a colorful and lightweight solution for food storage. These baskets are particularly suitable for supermarkets and retail environments where cost-effectiveness and versatility are paramount. While they are an economical choice, buyers should be aware that plastic baskets may not perform well under high temperatures, which could limit their use in certain food preparation settings.
What Advantages Do Wooden Kitchen Baskets Offer to B2B Buyers?
Wooden kitchen baskets are often handcrafted from various types of wood, providing a unique aesthetic that appeals to gourmet food stores and artisanal markets. Their sturdiness and visual appeal make them an attractive option for buyers looking to enhance their product presentation. However, the higher cost and need for regular maintenance to avoid damage may pose challenges for some businesses, particularly those operating on tighter budgets.
Why Choose Collapsible Kitchen Baskets for B2B Applications?
Collapsible kitchen baskets are made from flexible materials, allowing them to be easily folded for storage when not in use. This space-saving feature is particularly beneficial for food delivery services and event catering businesses that require portability. While they offer convenience, buyers should consider that these baskets may be less durable than their rigid counterparts, which could affect long-term usability.
What Are Specialty Kitchen Baskets and Their Unique Benefits?
Specialty kitchen baskets are designed for specific food items, such as bread or fruits, and are often custom-made to suit particular business needs. These baskets are ideal for bakeries and specialty food retailers looking to provide tailored solutions. However, buyers should note that these products may require larger minimum orders, which could impact inventory management for smaller businesses.
Key Industrial Applications of kitchen basket manufacturer
Industry/Sector | Specific Application of Kitchen Basket Manufacturer | Value/Benefit for the Business | Key Sourcing Considerations for this Application |
---|---|---|---|
Food Processing | Storage and Transport of Ingredients | Enhances efficiency in inventory management and reduces spoilage | Ensure baskets are food-grade, durable, and easy to clean |
Hospitality and Catering | Serving and Display Baskets | Improves presentation, enhances customer experience | Look for customizable options and aesthetic designs |
Retail and Supermarkets | Product Display and Organization | Maximizes retail space and attracts customers | Consider stackability and material durability |
Healthcare and Pharmaceuticals | Sterilization and Transport of Medical Supplies | Ensures compliance with health standards and prevents contamination | Verify materials are non-reactive and easy to sterilize |
Home and Kitchenware Retail | Consumer Storage Solutions | Meets demand for organization and space-saving solutions | Focus on design trends and consumer preferences |
How are Kitchen Baskets Used in Food Processing?
In the food processing industry, kitchen baskets are essential for the storage and transport of ingredients. These baskets help streamline operations by allowing for efficient organization and easy access to raw materials. By reducing spoilage and ensuring that ingredients are stored properly, businesses can significantly enhance their inventory management. International buyers should prioritize sourcing baskets that are food-grade, durable, and easy to clean to meet regulatory standards and operational needs.
What Role Do Kitchen Baskets Play in Hospitality and Catering?
In the hospitality and catering sector, kitchen baskets are utilized for serving and displaying food. These baskets not only improve the presentation of dishes but also enhance the overall customer experience by providing an appealing visual aesthetic. For B2B buyers in this industry, customizable options and aesthetically pleasing designs are crucial considerations, as they can reflect the brand’s identity and cater to diverse customer preferences.
How Do Retailers Use Kitchen Baskets for Product Display?
Retail and supermarket industries leverage kitchen baskets for product display and organization. By maximizing retail space and improving product visibility, these baskets attract customers and facilitate easier shopping experiences. B2B buyers should consider stackability and material durability when sourcing these baskets, as they need to withstand frequent handling while maintaining an appealing appearance.
Why are Kitchen Baskets Important in Healthcare and Pharmaceuticals?
In healthcare and pharmaceuticals, kitchen baskets are used for the sterilization and transport of medical supplies. These baskets must comply with strict health standards to prevent contamination and ensure patient safety. International buyers should verify that the materials used are non-reactive and easy to sterilize, as these features are critical for maintaining hygiene and safety in medical environments.
How Do Kitchen Baskets Enhance Home and Kitchenware Retail?
In the home and kitchenware retail sector, kitchen baskets serve as consumer storage solutions that meet the increasing demand for organization and space-saving products. These baskets help consumers declutter their living spaces while adding a decorative touch. B2B buyers should focus on current design trends and consumer preferences when sourcing these products to ensure they meet market demands and enhance sales potential.
Related Video: COOKERY LESSON 2 -Classify the types of appropriate cleaning tools and equipment based on their uses
3 Common User Pain Points for ‘kitchen basket manufacturer’ & Their Solutions
Scenario 1: Quality Assurance Challenges in Kitchen Basket Manufacturing
The Problem: One of the primary concerns for B2B buyers is the inconsistency in product quality. A kitchen basket manufacturer may produce items that vary significantly in materials, design, and durability. This inconsistency can lead to dissatisfaction from end customers, increased returns, and ultimately a damaged reputation. For buyers in regions like Africa or South America, where market standards may vary, ensuring that the manufactured kitchen baskets meet local regulations and consumer expectations is crucial.
The Solution: To mitigate quality assurance challenges, international buyers should conduct thorough research into potential manufacturers. Start by requesting samples of their products and performing quality tests, such as weight capacity and material resilience. Establish clear specifications and quality standards in your purchase agreements. Additionally, consider implementing a vendor audit process, where you can evaluate the manufacturing facilities and their quality control measures. Leveraging third-party inspection services can also help ensure that the products meet the desired quality before shipping. By setting these standards upfront and maintaining open communication with the manufacturer, you can significantly reduce the risks associated with product quality.
Scenario 2: Supply Chain Disruptions Impacting Delivery Timelines
The Problem: Supply chain disruptions can severely impact the timely delivery of kitchen baskets, affecting your inventory management and customer satisfaction. In regions like the Middle East and Europe, where consumer demand can fluctuate rapidly, delays can lead to lost sales and strained relationships with retailers. Factors such as political instability, transportation issues, or raw material shortages can all contribute to these delays.
The Solution: To navigate supply chain challenges, B2B buyers should diversify their supplier base. Rather than relying on a single manufacturer, consider establishing relationships with multiple kitchen basket manufacturers across different regions. This strategy allows for greater flexibility and reduces dependency on one source. Additionally, implementing an effective inventory management system can help predict demand and maintain optimal stock levels, even during unexpected delays. Regularly communicating with your suppliers to understand their capabilities and constraints can also help you proactively manage potential disruptions. Finally, exploring local manufacturers in your region can reduce shipping times and costs while providing a more reliable supply chain.
Scenario 3: Navigating Regulatory Compliance in Different Markets
The Problem: For international B2B buyers, understanding and complying with various regulatory requirements can be daunting. Each region may have different standards regarding materials, safety regulations, and environmental compliance. For example, kitchen baskets made from certain plastics may be banned in Europe, while those same materials might be acceptable in parts of Africa or South America. This complexity can lead to costly mistakes and legal issues if not addressed correctly.
The Solution: To effectively navigate regulatory compliance, B2B buyers should invest time in understanding the specific requirements of their target markets. Start by consulting local regulations and standards related to kitchenware and materials. Engaging with legal experts or compliance consultants can provide clarity on the requirements specific to each region. When selecting kitchen basket manufacturers, prioritize those who demonstrate compliance with international standards and can provide necessary certifications. Additionally, consider manufacturers who are transparent about their materials and production processes. Establishing a compliance checklist can help streamline the evaluation process, ensuring that your products meet the necessary regulations before they reach your customers. By taking a proactive approach to compliance, you can avoid potential pitfalls and build a trustworthy brand in your target market.
Strategic Material Selection Guide for kitchen basket manufacturer
When selecting materials for kitchen baskets, manufacturers must consider various factors that affect performance, durability, and compliance with international standards. Here’s an analysis of four common materials used in the production of kitchen baskets, focusing on their properties, advantages, disadvantages, and considerations for international B2B buyers.
What are the Key Properties of Stainless Steel for Kitchen Baskets?
Stainless steel is a popular choice for kitchen baskets due to its excellent corrosion resistance and high strength. It can withstand temperatures up to 1,600°F (870°C) without deforming, making it suitable for various cooking and storage applications. Additionally, stainless steel is non-reactive, meaning it won’t alter the taste or quality of food items.
Pros & Cons: The durability of stainless steel is a significant advantage, as it can last for years with minimal maintenance. However, it tends to be more expensive than other materials, which can impact overall manufacturing costs. The complexity of manufacturing processes, such as welding and polishing, can also increase production time.
Impact on Application: Stainless steel kitchen baskets are ideal for environments where hygiene is paramount, such as restaurants and food processing facilities. They are compatible with a wide range of media, including liquids and solids, making them versatile.
Considerations for International Buyers: Buyers in regions like Europe and the Middle East should ensure compliance with standards such as ASTM and DIN for food safety. Additionally, the availability of stainless steel grades may vary by region, affecting sourcing decisions.
How Does Plastic Compare as a Material for Kitchen Baskets?
Plastic, particularly high-density polyethylene (HDPE) and polypropylene, is widely used in kitchen baskets due to its lightweight nature and resistance to moisture. These materials can handle temperatures up to 230°F (110°C) and are generally resistant to many chemicals.
Pros & Cons: The primary advantage of plastic is its cost-effectiveness, making it an attractive option for budget-conscious manufacturers. However, plastic may not be as durable as stainless steel and can become brittle over time, especially when exposed to high temperatures.
Impact on Application: Plastic kitchen baskets are suitable for dry storage and food preparation but may not be ideal for cooking applications due to heat sensitivity. They are often used in home kitchens and catering services.
Considerations for International Buyers: Compliance with food safety standards, such as FDA regulations in the U.S. and EU regulations in Europe, is crucial. Buyers in Africa and South America should also consider local recycling capabilities for plastic materials.
What are the Benefits of Bamboo in Kitchen Basket Manufacturing?
Bamboo is an eco-friendly material that has gained popularity in kitchen basket manufacturing due to its sustainability and natural aesthetic. It is lightweight and has a natural resistance to moisture, making it suitable for food storage.
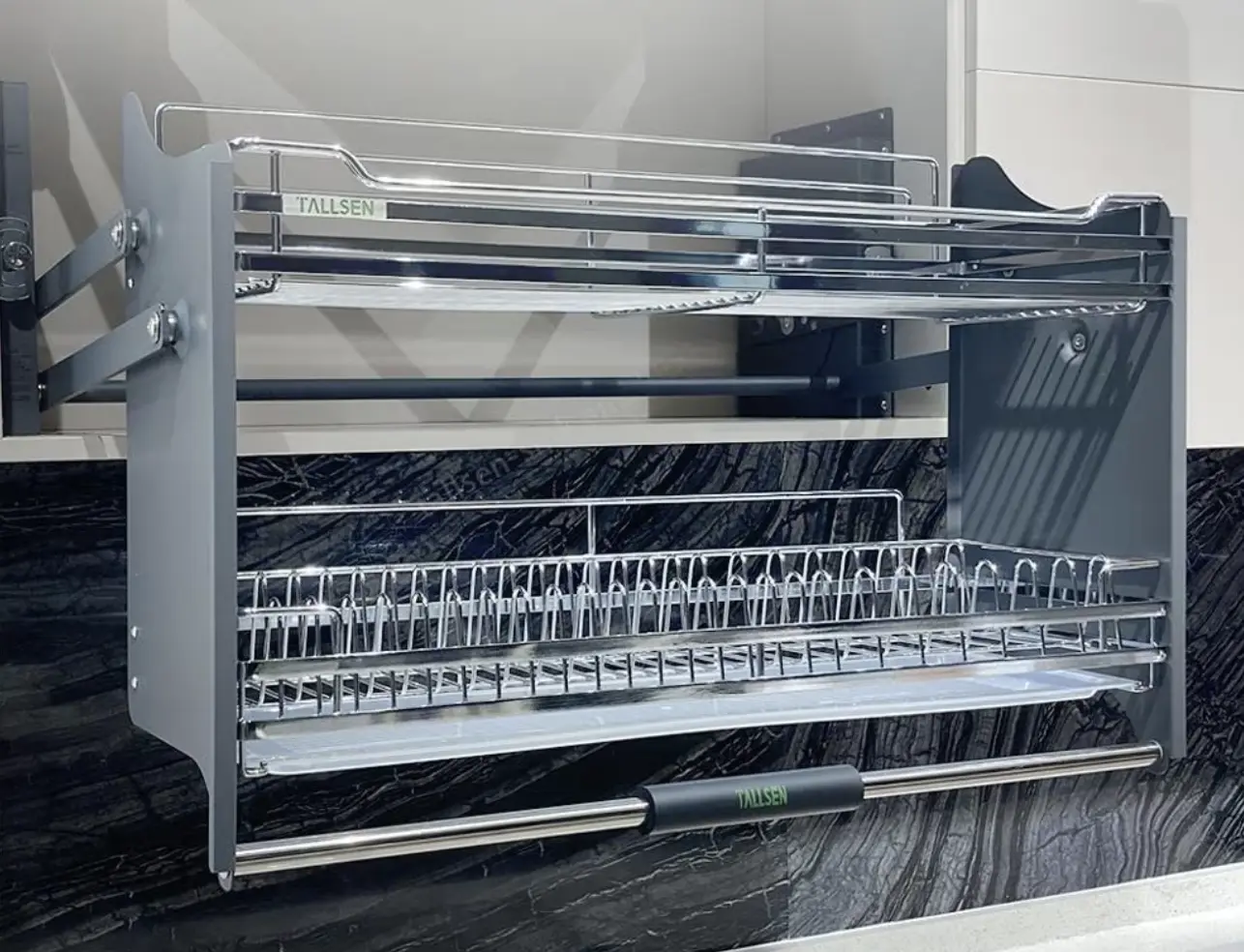
A stock image related to kitchen basket manufacturer.
Pros & Cons: The key advantage of bamboo is its environmental friendliness, appealing to consumers looking for sustainable options. However, bamboo can be less durable than metal or plastic, particularly in high-moisture environments, which may limit its lifespan.
Impact on Application: Bamboo baskets are ideal for dry storage and decorative uses but may not withstand high temperatures or heavy loads. They are commonly used in homes and artisanal markets.
Considerations for International Buyers: Buyers should verify that bamboo products comply with international sustainability standards. In regions like Europe, certifications such as FSC (Forest Stewardship Council) may be required.
How Does Aluminum Stack Up as a Material for Kitchen Baskets?
Aluminum is another viable option for kitchen baskets, known for its lightweight and corrosion-resistant properties. It can handle temperatures up to 1,200°F (650°C), making it suitable for various cooking applications.
Pros & Cons: Aluminum is relatively inexpensive and easy to manufacture, which can lower production costs. However, it is softer than stainless steel and may dent or scratch easily, affecting the aesthetic appeal of the product over time.
Impact on Application: Aluminum baskets are versatile and can be used in both cooking and storage applications. They are particularly effective for grilling and steaming due to their excellent heat conduction.
Considerations for International Buyers: Compliance with standards like ASTM for aluminum products is essential. Buyers from the Middle East should also consider the impact of high humidity on aluminum’s performance.
Summary Table of Material Selection for Kitchen Baskets
Material | Typical Use Case for kitchen basket manufacturer | Key Advantage | Key Disadvantage/Limitation | Relative Cost (Low/Med/High) |
---|---|---|---|---|
Stainless Steel | Professional kitchens, food processing | High durability and corrosion resistance | Higher cost and manufacturing complexity | High |
Plastic | Home kitchens, catering services | Cost-effective and lightweight | Less durable, heat sensitivity | Low |
Bamboo | Decorative storage, dry food storage | Eco-friendly and sustainable | Limited durability in high moisture | Medium |
Aluminum | Cooking, grilling, and steaming applications | Lightweight and good heat conduction | Soft material, prone to dents | Medium |
This strategic material selection guide provides B2B buyers with essential insights into the properties and applications of various materials used in kitchen basket manufacturing. By understanding these factors, buyers can make informed decisions that align with their operational needs and market demands.
In-depth Look: Manufacturing Processes and Quality Assurance for kitchen basket manufacturer
What Are the Key Manufacturing Processes for Kitchen Baskets?
The manufacturing of kitchen baskets involves several key stages, each critical to ensuring that the final product meets quality and functionality standards. These stages include material preparation, forming, assembly, and finishing.
How Is Material Prepared for Kitchen Basket Manufacturing?
Material preparation is the foundational step in the manufacturing process. Common materials used for kitchen baskets include stainless steel, woven metal, plastic, and natural fibers. The choice of material often depends on the intended use of the basket and the target market’s preferences.
- Selection: Suppliers must source high-quality materials that comply with international standards to ensure durability and safety.
- Processing: This stage may involve cutting, treating, or conditioning the materials to make them suitable for forming. For example, metal might be treated to resist corrosion, while natural fibers might undergo drying and treatment processes.
What Techniques Are Used in Forming Kitchen Baskets?
Forming is the next step, where the prepared materials are shaped into the desired basket form. Various techniques can be employed:
- Welding: For metal baskets, welding is a common technique used to join different components securely.
- Molding: Plastic baskets often utilize injection molding, which allows for intricate designs and uniformity.
- Weaving: Natural fiber baskets are typically woven by hand or machine, which adds a unique aesthetic quality to the product.
These techniques not only affect the appearance of the baskets but also their functionality, making it essential for manufacturers to choose the right method based on the product specifications.
How Is the Assembly of Kitchen Baskets Conducted?
Once the components are formed, the assembly process begins. This process varies depending on the complexity of the design.
- Manual Assembly: For intricate designs or smaller production runs, skilled workers may assemble the baskets by hand, ensuring attention to detail.
- Automated Assembly: For larger production volumes, automated machinery may be used to speed up the assembly process while maintaining consistency.
Quality control during assembly is crucial, as improper assembly can lead to structural failures or aesthetic defects.
What Are the Finishing Processes for Kitchen Baskets?
Finishing is the final stage of manufacturing, where the baskets are treated to enhance their appearance and durability.
- Surface Treatment: This may include polishing, coating, or painting, which not only improves the visual appeal but also protects the materials.
- Quality Inspection: Before packaging, each basket undergoes a thorough inspection to ensure it meets the specified quality standards.
How Is Quality Assurance Managed in Kitchen Basket Manufacturing?
Quality assurance (QA) is integral to the manufacturing process, ensuring that products meet both international and industry-specific standards. Understanding these standards is critical for B2B buyers.
What International Quality Standards Should Kitchen Basket Manufacturers Meet?
International standards such as ISO 9001 play a vital role in the manufacturing process. ISO 9001 focuses on quality management systems, ensuring that manufacturers consistently produce products that meet customer and regulatory requirements.
- ISO 9001 Certification: B2B buyers should prioritize suppliers that are ISO 9001 certified, as this indicates a commitment to quality and continuous improvement.
In addition to ISO standards, specific certifications like CE (Conformité Européenne) for products sold in Europe and API (American Petroleum Institute) for certain industrial applications may also be relevant.
What Are the Key Quality Control Checkpoints in Manufacturing?
Implementing a robust quality control (QC) system involves several checkpoints throughout the manufacturing process:
- Incoming Quality Control (IQC): This initial checkpoint assesses the quality of raw materials before they enter the production line.
- In-Process Quality Control (IPQC): During production, samples are taken at various stages to ensure compliance with quality standards.
- Final Quality Control (FQC): Once manufacturing is complete, the final products are inspected for defects and conformance to specifications.
By understanding these checkpoints, B2B buyers can better evaluate a supplier’s commitment to quality.
What Common Testing Methods Are Used in Quality Assurance for Kitchen Baskets?
Several testing methods are employed to verify the quality of kitchen baskets:
- Durability Tests: Assessing the strength and longevity of materials through stress tests.
- Safety Tests: Ensuring that materials are safe for food contact, especially for baskets intended for kitchen use.
- Aesthetic Evaluations: Checking for visual defects, such as scratches or uneven finishes.
B2B buyers should inquire about the specific testing methods used by suppliers to ensure they align with their quality expectations.
How Can B2B Buyers Verify Supplier Quality Control?
To ensure that a supplier meets quality standards, B2B buyers can employ several verification methods:
- Supplier Audits: Conducting on-site audits allows buyers to assess manufacturing practices and quality control processes directly.
- Quality Reports: Requesting detailed quality reports can provide insight into the supplier’s adherence to standards and their QC processes.
- Third-Party Inspections: Engaging third-party inspection services can offer an unbiased assessment of the supplier’s quality practices.
What Are the Quality Control Nuances for International B2B Buyers?
For international B2B buyers, particularly those from Africa, South America, the Middle East, and Europe, understanding the nuances of quality control is essential:
- Cultural Expectations: Different regions may have varying quality expectations based on local standards and consumer behavior.
- Regulatory Compliance: Buyers must ensure that their suppliers comply with both local and international regulations, which can differ significantly from one market to another.
By prioritizing these aspects, B2B buyers can make informed decisions and establish long-term partnerships with reliable kitchen basket manufacturers.
Practical Sourcing Guide: A Step-by-Step Checklist for ‘kitchen basket manufacturer’
This guide aims to provide international B2B buyers with a structured approach to sourcing kitchen basket manufacturers effectively. By following this checklist, buyers from diverse regions such as Africa, South America, the Middle East, and Europe can ensure they select the right suppliers that meet their needs and standards.
Step 1: Define Your Technical Specifications
Before initiating the sourcing process, clearly outline your technical requirements for kitchen baskets. This includes material preferences (e.g., metal, plastic, wicker), dimensions, weight capacity, and any unique design features. Having a comprehensive specification helps streamline communication with potential suppliers and ensures they understand your exact needs.
Step 2: Conduct Market Research on Suppliers
Invest time in researching potential suppliers in various markets. Look for manufacturers who specialize in kitchen baskets and have a proven track record. Utilize online platforms, trade shows, and industry directories to gather information. Pay attention to their market presence, product range, and customer reviews, as these can provide insights into their reliability and quality.
Step 3: Evaluate Potential Suppliers
Before committing, it’s crucial to vet suppliers thoroughly. Request company profiles, case studies, and references from buyers in a similar industry or region. Consider their production capabilities and experience in exporting to your country, as this can affect lead times and compliance with local regulations.
- What to look for:
- Manufacturing capacity and technology.
- Previous clients or projects that align with your needs.
Step 4: Verify Supplier Certifications
Ensure that the suppliers you consider hold relevant certifications that demonstrate compliance with industry standards. Certifications such as ISO 9001 for quality management or specific safety standards relevant to kitchen products can indicate a commitment to quality and safety.
- Why it matters:
- Certifications can reduce the risk of sourcing low-quality products.
- They ensure that the manufacturer adheres to necessary health and safety regulations.
Step 5: Request Samples for Quality Assessment
Before placing a large order, request product samples from your shortlisted suppliers. This allows you to assess the quality, craftsmanship, and functionality of the kitchen baskets firsthand. Evaluate the samples against your defined specifications to ensure they meet your standards.
- Key considerations:
- Check for durability and finish quality.
- Ensure that the samples align with your brand’s aesthetic.
Step 6: Negotiate Pricing and Payment Terms
Once you have identified a suitable supplier, engage in negotiations regarding pricing, payment terms, and delivery schedules. Be transparent about your budget and discuss bulk order discounts or flexible payment options. Understanding the total cost, including shipping and customs duties, is essential for accurate budgeting.
Step 7: Establish a Clear Communication Plan
Effective communication is crucial throughout the sourcing process. Set expectations for regular updates and establish a point of contact for any inquiries. A clear communication plan helps mitigate misunderstandings and fosters a collaborative relationship with your chosen supplier.
By following these steps, B2B buyers can navigate the complex landscape of sourcing kitchen basket manufacturers, ensuring they make informed decisions that align with their business needs and market expectations.
Comprehensive Cost and Pricing Analysis for kitchen basket manufacturer Sourcing
What Are the Key Cost Components in Kitchen Basket Manufacturing?
Understanding the cost structure of kitchen basket manufacturing is essential for international B2B buyers. The primary cost components include:
-
Materials: The choice of materials significantly impacts the overall cost. Common materials for kitchen baskets include metal, plastic, and natural fibers. High-quality materials often come with a premium price but can enhance durability and aesthetic appeal, which may justify the investment.
-
Labor: Labor costs vary by region. For example, countries in South America may have different wage standards compared to those in Africa or Europe. It’s crucial to consider not just the hourly wage but also the skill level required for production, as skilled labor can lead to higher quality outputs.
-
Manufacturing Overhead: This includes utilities, rent, equipment maintenance, and administrative expenses. Manufacturers in regions with higher operational costs may pass these expenses onto buyers, affecting the pricing strategy.
-
Tooling: Initial tooling costs can be significant, especially for custom designs. Buyers should inquire about tooling fees and whether these can be amortized over larger orders to reduce per-unit costs.
-
Quality Control (QC): Investing in robust quality control processes ensures that the products meet specific standards and certifications, which can be critical for international markets. However, these processes add to the manufacturing costs.
-
Logistics: Freight and shipping costs can vary widely based on the supplier’s location and the destination. Incoterms (International Commercial Terms) also play a role in defining who bears the transportation costs and risks, which can affect the total pricing.
-
Margin: The supplier’s profit margin is the final piece of the puzzle. Understanding the competitive landscape and the supplier’s position can provide insights into how much flexibility there is in pricing negotiations.
How Do Price Influencers Affect Kitchen Basket Sourcing?
Several factors influence the pricing of kitchen baskets, including:
-
Volume and Minimum Order Quantity (MOQ): Larger orders typically lead to lower per-unit costs due to economies of scale. Buyers should assess their demand and negotiate MOQs that align with their purchasing power.
-
Specifications and Customization: Custom designs or specific material requirements can increase costs. Buyers should evaluate whether the benefits of customization outweigh the additional expenses.
-
Material Choices: Higher-grade materials or environmentally friendly options may come with increased costs. Buyers should consider their target market’s preferences and willingness to pay for premium features.
-
Quality and Certifications: Products that meet certain quality standards or certifications may command higher prices. Buyers in regulated markets, such as Europe, should factor in these requirements when budgeting.
-
Supplier Factors: The supplier’s reputation, reliability, and production capacity can also impact pricing. Established suppliers with a proven track record may charge more but offer better service and quality assurance.
-
Incoterms: Understanding the implications of Incoterms is crucial. Different terms can shift costs and responsibilities, affecting the final price of the kitchen baskets.
What Are the Best Negotiation and Cost-Efficiency Tips for International Buyers?
-
Conduct Market Research: Familiarize yourself with local market rates and competitor pricing. This knowledge will empower you during negotiations and help you identify fair pricing.
-
Negotiate Terms: Don’t hesitate to negotiate both price and terms. Discuss payment options, delivery timelines, and potential discounts for larger orders to improve overall cost efficiency.
-
Consider Total Cost of Ownership (TCO): Look beyond the initial price. Assess long-term costs, including maintenance, replacement, and shipping. A lower upfront cost may lead to higher overall expenses if quality or durability is compromised.
-
Understand Pricing Nuances: Different regions may have varying pricing structures due to local economic conditions. Buyers from Africa, South America, the Middle East, and Europe should consider how these factors play into their sourcing strategy.
-
Build Relationships with Suppliers: Establishing long-term relationships with suppliers can lead to better pricing and service. Trust and mutual understanding often yield more favorable terms and conditions.
Disclaimer on Indicative Prices
Prices for kitchen baskets can fluctuate based on numerous factors, including market conditions, raw material costs, and currency exchange rates. Therefore, always seek updated quotes and be prepared for potential changes in pricing throughout the sourcing process.
Alternatives Analysis: Comparing kitchen basket manufacturer With Other Solutions
Understanding Alternative Solutions for Kitchen Baskets
When considering the procurement of kitchen baskets, B2B buyers often explore various options to determine the best fit for their operational needs. This analysis focuses on the kitchen basket manufacturer and compares it with two viable alternatives: plastic basket suppliers and modular storage systems. Each alternative presents distinct benefits and limitations, which can significantly impact purchasing decisions.
Comparison Table of Kitchen Basket Solutions
Comparison Aspect | Kitchen Basket Manufacturer | Plastic Basket Suppliers | Modular Storage Systems |
---|---|---|---|
Performance | High durability and design flexibility | Good durability but less customizable | Versatile, adaptable designs for various needs |
Cost | Higher initial investment but long-term value | Lower cost upfront but may require replacement | Moderate cost with scalability options |
Ease of Implementation | Requires setup and customization | Ready-to-use, minimal setup needed | Can be complex depending on configuration |
Maintenance | Low maintenance with proper care | Moderate maintenance; replacements may be necessary | Varies; some systems require regular adjustments |
Best Use Case | High-end commercial kitchens requiring custom solutions | Small to medium businesses needing cost-effective options | Dynamic environments needing flexibility in storage |
What Are the Pros and Cons of Plastic Basket Suppliers?
Plastic basket suppliers offer an affordable alternative for businesses looking to minimize initial expenditures. They are typically ready-to-use, requiring minimal setup time, which is advantageous for businesses needing immediate solutions. However, while they provide good durability, they often lack the customization options that a kitchen basket manufacturer can offer. Over time, the need for replacements can increase operational costs, making them less viable for long-term use in high-demand environments.
How Do Modular Storage Systems Compare?
Modular storage systems provide an adaptable solution that can be tailored to a variety of kitchen environments. They excel in dynamic settings where storage needs may change frequently, allowing businesses to reconfigure their storage solutions as required. However, the complexity of setup can be a drawback, particularly for businesses without dedicated staff for installation and maintenance. Additionally, while they offer moderate cost benefits, the need for ongoing adjustments and maintenance can lead to unexpected expenses.
Conclusion: How to Choose the Right Kitchen Basket Solution
In determining the best kitchen basket solution, international B2B buyers must assess their specific needs, including budget constraints, operational requirements, and long-term goals. A kitchen basket manufacturer may offer superior durability and customization for high-end operations, while plastic basket suppliers provide a cost-effective solution for smaller enterprises. Conversely, modular storage systems cater to businesses seeking flexibility but may require more management. By weighing these factors, buyers can make informed decisions that align with their strategic objectives and operational efficiencies.
Essential Technical Properties and Trade Terminology for kitchen basket manufacturer
What Are the Key Technical Properties for Kitchen Basket Manufacturing?
When sourcing kitchen baskets, understanding the technical properties is crucial for ensuring product quality, performance, and compliance with international standards. Here are several essential specifications that B2B buyers should consider:
1. Material Grade
The material grade refers to the type and quality of materials used in the production of kitchen baskets. Common materials include stainless steel, polypropylene, and bamboo. Each material offers distinct advantages; for instance, stainless steel is durable and resistant to rust, while bamboo is eco-friendly and lightweight. Selecting the right material impacts not only the basket’s longevity but also its suitability for different kitchen environments, which is essential for buyers aiming to meet specific customer needs.
2. Tolerance
Tolerance indicates the allowable deviation from specified dimensions during manufacturing. In kitchen basket production, maintaining tight tolerances is vital for ensuring that baskets fit seamlessly into designated spaces, such as cabinets or dishwashers. Poor tolerance can lead to functional issues, affecting customer satisfaction. For B2B buyers, understanding tolerance specifications helps in assessing a manufacturer’s precision and quality control processes.
3. Load Capacity
Load capacity refers to the maximum weight a kitchen basket can safely hold without deformation or failure. This property is particularly important for commercial kitchen environments, where baskets may need to support heavy items. Buyers should inquire about the load capacity to ensure that the products will perform reliably under expected usage conditions, which is essential for avoiding costly replacements or customer complaints.
4. Finish and Coating
The finish and coating of a kitchen basket can significantly affect its appearance and functionality. Options may include powder coating, electroplating, or a natural finish. These treatments enhance aesthetics, increase resistance to corrosion, and improve hygiene. For international buyers, understanding the implications of different finishes is important for compliance with local regulations and consumer preferences.
5. Dimensions
The dimensions of kitchen baskets, including height, width, and depth, are critical for ensuring they fit in intended spaces. Buyers should specify their requirements clearly and verify that manufacturers can produce baskets that meet these specifications. This helps avoid logistical issues and ensures that the products serve their intended purpose effectively.
Which Trade Terms Are Essential for Kitchen Basket Manufacturing?
Understanding trade terminology is crucial for effective communication with suppliers and ensuring smooth transactions. Here are some common terms that B2B buyers should be familiar with:
1. OEM (Original Equipment Manufacturer)
OEM refers to a company that produces parts or products that are then sold under another brand’s name. In the context of kitchen baskets, buyers may choose to work with OEMs to customize products that align with their brand identity. This relationship can enhance product differentiation and marketability.
2. MOQ (Minimum Order Quantity)
MOQ indicates the smallest quantity of a product that a supplier is willing to sell. Understanding MOQ is essential for buyers as it impacts inventory management and initial investment costs. Negotiating favorable MOQs can help businesses optimize their supply chain and reduce excess inventory.
3. RFQ (Request for Quotation)
An RFQ is a document sent to suppliers requesting pricing information for specific products. It allows buyers to compare costs and terms from multiple manufacturers. Crafting a clear and detailed RFQ can facilitate better responses and ensure that buyers receive accurate quotes that meet their project requirements.
4. Incoterms (International Commercial Terms)
Incoterms are a set of predefined international trade terms that delineate responsibilities between buyers and sellers in shipping arrangements. Familiarity with terms like FOB (Free on Board) or CIF (Cost, Insurance, and Freight) helps buyers understand shipping costs and risk transfer, enabling them to make informed decisions about their procurement strategy.
5. Lead Time
Lead time is the duration from the placement of an order to its delivery. Understanding lead times is crucial for effective supply chain management, particularly in international transactions where delays can impact business operations. Buyers should always inquire about lead times to better align their inventory needs with production schedules.
By grasping these essential technical properties and trade terms, international B2B buyers can enhance their procurement strategies, ensuring they select the right kitchen baskets that meet their operational needs and customer expectations.
Navigating Market Dynamics and Sourcing Trends in the kitchen basket manufacturer Sector
What Are the Current Market Dynamics and Key Trends in the Kitchen Basket Manufacturing Sector?
The kitchen basket manufacturing sector has seen significant shifts driven by globalization, technological advancements, and evolving consumer preferences. International B2B buyers, particularly from Africa, South America, the Middle East, and Europe, should be aware of several key trends. The demand for innovative designs and multifunctional products is rising, influenced by urbanization and smaller living spaces, particularly in emerging markets. Buyers should consider sourcing manufacturers that can provide customizable options to cater to these unique needs.
Moreover, digital transformation is reshaping sourcing strategies. Technologies such as AI, IoT, and blockchain are enhancing supply chain transparency, enabling buyers to track product origins and ensure quality. This is particularly relevant for B2B buyers in regions like Argentina and Vietnam, where supply chain integrity can be a concern. Implementing digital tools can streamline procurement processes, reduce costs, and improve overall efficiency.
Additionally, the growing preference for eco-friendly materials is reshaping market dynamics. As consumers become more environmentally conscious, B2B buyers must align their sourcing strategies with sustainable practices. This trend is evident across various markets, including Europe, where regulatory frameworks are increasingly favoring sustainable manufacturing processes. Understanding these dynamics is crucial for international buyers looking to navigate the complexities of sourcing in the kitchen basket manufacturing sector.
How Is Sustainability Influencing Sourcing Decisions in the Kitchen Basket Sector?
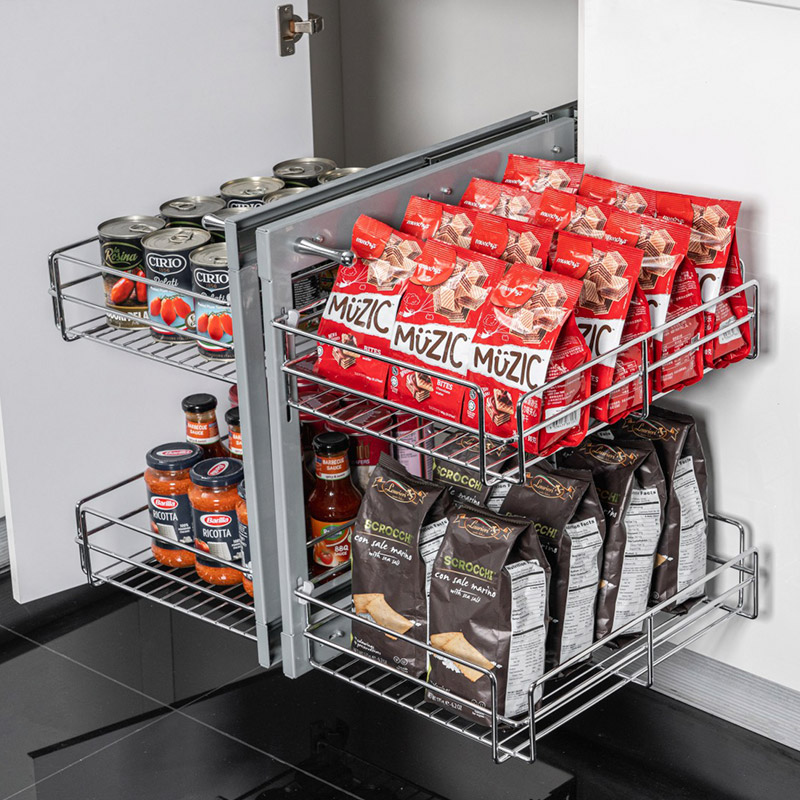
A stock image related to kitchen basket manufacturer.
Sustainability has become a cornerstone of strategic sourcing in the kitchen basket manufacturing sector. The environmental impact of production processes is under scrutiny, pushing manufacturers to adopt sustainable practices. B2B buyers from regions such as Africa and the Middle East should prioritize suppliers that demonstrate a commitment to reducing their carbon footprint through energy-efficient manufacturing and waste reduction initiatives.
Ethical sourcing is equally important, as consumers increasingly demand transparency regarding the origins of their products. Buyers should look for suppliers who adhere to ethical labor practices and provide certifications that validate their commitment to social responsibility. This is especially pertinent in regions where labor exploitation may be a concern.
Green certifications and sustainable materials are key factors that buyers should consider. Materials such as bamboo, recycled plastics, and other biodegradable options are gaining traction. By selecting manufacturers who utilize these materials, international B2B buyers can not only meet consumer demand for sustainable products but also enhance their brand reputation. Implementing these practices can lead to long-term savings and foster loyalty among environmentally conscious consumers.
What Is the Historical Evolution of the Kitchen Basket Manufacturing Sector?
The kitchen basket manufacturing sector has evolved significantly over the past few decades. Initially dominated by traditional craftsmanship, the industry has transformed with the advent of mass production techniques in the late 20th century. This shift allowed for increased efficiency and lower costs, making kitchen baskets more accessible to a broader market.
As the 21st century progressed, the sector began to embrace technological advancements, leading to innovations in design and materials. The introduction of computer-aided design (CAD) software and automated manufacturing processes enhanced the customization capabilities of kitchen baskets. Today, manufacturers are not only focused on functionality but also on aesthetic appeal, catering to a diverse range of consumer preferences worldwide.
This historical context is essential for international B2B buyers as it highlights the industry’s adaptability and the importance of staying informed about ongoing changes. Understanding these shifts can help buyers make informed decisions regarding supplier partnerships and product offerings in a competitive global market.
Frequently Asked Questions (FAQs) for B2B Buyers of kitchen basket manufacturer
-
How do I identify a reliable kitchen basket manufacturer for my business?
To find a trustworthy kitchen basket manufacturer, start by researching potential suppliers through online directories like Alibaba, TradeIndia, or Global Sources. Check for verified supplier statuses and read reviews from previous buyers. It’s also advisable to request samples to evaluate product quality before placing a bulk order. Furthermore, consider manufacturers with established track records in international trade, particularly those familiar with regulations in your region, such as Africa, South America, or Europe. -
What factors should I consider when evaluating kitchen basket manufacturers?
When assessing kitchen basket manufacturers, consider factors such as production capacity, lead times, and quality assurance processes. Evaluate their certifications, such as ISO or CE, which indicate adherence to quality standards. Additionally, inquire about their experience in exporting to your region and their ability to handle customs processes. Communication and responsiveness are also critical; a manufacturer that prioritizes clear communication can help streamline your purchasing experience. -
What are the minimum order quantities (MOQ) for kitchen baskets?
Minimum order quantities can vary significantly among manufacturers, typically ranging from 100 to 1,000 units. Some manufacturers may offer lower MOQs for initial orders, especially if you are testing the market. It’s essential to discuss your needs upfront and negotiate MOQs that align with your business strategy. Be mindful that larger orders often lead to better pricing, so consider your inventory management when deciding on quantities. -
What customization options are available for kitchen baskets?
Most manufacturers offer customization options, including size, design, material, and color. When discussing customization, provide detailed specifications and examples of your desired outcomes. Be clear about the intended market, as preferences can vary widely across regions like Africa, South America, and Europe. Ensure that the manufacturer can accommodate your requests within the agreed timelines and budget. -
What payment terms should I expect when sourcing kitchen baskets?
Payment terms can vary by manufacturer but typically include options like advance payments, letters of credit, or payment upon delivery. It’s common for manufacturers to request a 30% deposit upfront, with the balance due before shipment. Always clarify payment methods accepted, such as wire transfers, PayPal, or escrow services. Understanding these terms helps mitigate risks and ensures that both parties are aligned on financial expectations. -
How can I ensure quality assurance when sourcing kitchen baskets?
To ensure quality assurance, request detailed product specifications and quality control measures from the manufacturer. Inquire about their inspection processes and whether they perform third-party quality checks. It’s also beneficial to conduct pre-shipment inspections, especially for large orders, to verify that products meet your standards before they leave the factory. Consider establishing a clear return policy in case of defects or discrepancies. -
What logistics considerations should I keep in mind when importing kitchen baskets?
Logistics is a critical component of the import process. Assess shipping options, including sea freight and air freight, based on your budget and urgency. Understand the customs regulations in your country and any import duties applicable to kitchen baskets. Collaborating with a logistics provider familiar with international shipping can help streamline the process, ensuring compliance and timely delivery. -
How do I handle potential disputes with a kitchen basket manufacturer?
To manage potential disputes, establish clear communication and maintain a written record of all agreements, including contracts, specifications, and payment terms. If issues arise, start by discussing them directly with the manufacturer to seek resolution. If necessary, consider mediation or arbitration as alternatives to legal action. It’s also wise to research the manufacturer’s dispute resolution policies before finalizing any agreements.
Important Disclaimer & Terms of Use
⚠️ Important Disclaimer
The information provided in this guide, including content regarding manufacturers, technical specifications, and market analysis, is for informational and educational purposes only. It does not constitute professional procurement advice, financial advice, or legal advice.
While we have made every effort to ensure the accuracy and timeliness of the information, we are not responsible for any errors, omissions, or outdated information. Market conditions, company details, and technical standards are subject to change.
B2B buyers must conduct their own independent and thorough due diligence before making any purchasing decisions. This includes contacting suppliers directly, verifying certifications, requesting samples, and seeking professional consultation. The risk of relying on any information in this guide is borne solely by the reader.
Strategic Sourcing Conclusion and Outlook for kitchen basket manufacturer
As the global market for kitchen baskets continues to evolve, strategic sourcing remains a pivotal element for B2B buyers aiming to enhance their supply chain efficiency and product offerings. By prioritizing strong relationships with manufacturers, particularly those located in emerging markets such as Africa and South America, businesses can not only secure high-quality products but also leverage competitive pricing and innovative designs.
Understanding the unique demands of diverse markets—from the aesthetic preferences in Europe to the functional requirements in the Middle East—can significantly influence sourcing decisions. Additionally, employing a data-driven approach to evaluate supplier performance and market trends will empower buyers to make informed choices that align with their long-term business goals.
Looking ahead, international B2B buyers are encouraged to remain agile and proactive in their sourcing strategies. Embrace collaboration with kitchen basket manufacturers who are committed to sustainability and innovation, as this will not only enhance product quality but also resonate with today’s environmentally conscious consumers. By taking these steps, businesses can position themselves favorably in the competitive landscape, ensuring they remain ahead of market trends and consumer expectations. Now is the time to invest in strategic sourcing partnerships that will drive growth and success in the kitchen basket industry.