Discover Top Kitchen Equipment Suppliers: Your 2025 Guide
Introduction: Navigating the Global Market for kitchen equipment supplier
In today’s rapidly evolving global market, sourcing kitchen equipment can present significant challenges for international B2B buyers, particularly those operating in diverse regions such as Africa, South America, the Middle East, and Europe, including countries like Turkey and Brazil. The complexity of identifying reliable kitchen equipment suppliers, understanding product specifications, and navigating varying local regulations can create hurdles that hinder operational efficiency. This guide aims to alleviate these challenges by providing a comprehensive overview of the kitchen equipment supply landscape, encompassing various types of equipment, their applications, and essential factors for supplier vetting.
Buyers will discover critical insights into cost considerations, including how to balance quality with budget constraints and the impact of import duties. This resource serves as a practical tool to empower informed purchasing decisions, enabling businesses to optimize their kitchen setups, enhance productivity, and ultimately improve customer satisfaction. By addressing the unique needs of international buyers, this guide not only simplifies the sourcing process but also fosters strategic partnerships with trusted suppliers. As you navigate the global market for kitchen equipment, let this guide be your trusted companion in making well-informed decisions that drive your business forward.
Understanding kitchen equipment supplier Types and Variations
Type Name | Key Distinguishing Features | Primary B2B Applications | Brief Pros & Cons for Buyers |
---|---|---|---|
Commercial Kitchen Suppliers | Focus on large-scale equipment; often include installation services | Restaurants, hotels, catering services | Pros: Comprehensive solutions; expert support. Cons: Higher initial costs. |
Specialty Equipment Suppliers | Offer niche products (e.g., bakery, bar equipment) | Bakeries, cafes, bars | Pros: Tailored solutions; expertise in niche markets. Cons: Limited product range. |
Wholesale Kitchen Suppliers | Bulk purchasing options; competitive pricing | Foodservice distributors, large retailers | Pros: Cost-effective; diverse product options. Cons: Minimum order quantities may apply. |
Online Kitchen Equipment Suppliers | E-commerce platforms with wide selections; often direct shipping | Small businesses, startups | Pros: Convenience; extensive product variety. Cons: Lack of physical inspection before purchase. |
Local Kitchen Equipment Distributors | Focus on regional markets; personalized service | Local restaurants, catering companies | Pros: Quick delivery; strong local support. Cons: Limited inventory compared to larger suppliers. |
What are the characteristics of Commercial Kitchen Suppliers?
Commercial kitchen suppliers are designed to meet the needs of large-scale food operations. They provide a comprehensive range of equipment, from ovens and refrigerators to dishwashers and prep tables. These suppliers often offer installation and maintenance services, making them a one-stop shop for businesses. When considering a commercial kitchen supplier, B2B buyers should evaluate the supplier’s experience in the industry, the range of equipment offered, and the level of customer support available.
How do Specialty Equipment Suppliers differ from others?
Specialty equipment suppliers focus on niche markets, offering products tailored to specific culinary needs such as bakery equipment, bar supplies, or ethnic cuisine tools. They often have in-depth knowledge of their products, which is invaluable for businesses looking for specialized equipment. Buyers should consider the supplier‘s expertise in their specific area of interest, the availability of replacement parts, and the potential for customization when selecting a specialty supplier.
Why choose Wholesale Kitchen Suppliers?
Wholesale kitchen suppliers provide bulk purchasing options, making them ideal for businesses that require large quantities of equipment or ingredients, such as foodservice distributors and large retailers. They typically offer competitive pricing due to their volume sales. However, B2B buyers should be aware of minimum order quantities and ensure that the quality of products meets their operational standards.
What advantages do Online Kitchen Equipment Suppliers offer?
Online kitchen equipment suppliers have revolutionized the purchasing process by providing a vast selection of products that can be ordered from anywhere. They often feature user reviews and detailed specifications, aiding in informed purchasing decisions. While the convenience is a significant advantage, buyers should consider potential drawbacks, such as the inability to physically inspect equipment before purchase and shipping costs.
How do Local Kitchen Equipment Distributors serve businesses?
Local kitchen equipment distributors cater to regional markets, providing personalized service and quick delivery times. This can be particularly beneficial for local restaurants and catering companies that need immediate access to equipment. Buyers should assess the distributor’s inventory levels, delivery capabilities, and customer service reputation to ensure they receive the support needed for their operations.
Related Video: Commercial Kitchen Solutions Design and Equipment Supply
Key Industrial Applications of kitchen equipment supplier
Industry/Sector | Specific Application of kitchen equipment supplier | Value/Benefit for the Business | Key Sourcing Considerations for this Application |
---|---|---|---|
Hospitality | Commercial kitchen equipment for restaurants | Enhances food quality and service efficiency | Durability, energy efficiency, and compliance with local regulations |
Food Processing | Industrial food preparation equipment | Streamlines production processes and reduces waste | Equipment capacity, maintenance support, and sourcing of spare parts |
Catering Services | Mobile kitchen units for events | Flexibility to serve diverse locations and events | Portability, ease of setup, and adaptability to different cuisines |
Retail Food Service | Display and refrigeration units for supermarkets | Improves product visibility and preserves freshness | Energy efficiency, size, and compliance with health regulations |
Institutional Food Service | Bulk cooking equipment for schools and hospitals | Ensures consistent meal quality and quantity | Safety standards, ease of cleaning, and warranty services |
How is Kitchen Equipment Used in the Hospitality Sector?
In the hospitality industry, kitchen equipment suppliers play a crucial role by providing commercial kitchen appliances designed for high-volume food preparation. Equipment such as industrial ovens, grills, and fryers enhances food quality and service efficiency, allowing restaurants to deliver exceptional dining experiences. International B2B buyers, especially from regions like Africa and South America, should prioritize durability and energy efficiency, as well as compliance with local health and safety regulations, to ensure a reliable kitchen operation.
What Are the Applications of Kitchen Equipment in Food Processing?
In food processing, kitchen equipment suppliers provide essential machinery such as mixers, slicers, and food processors that streamline production processes. These tools help reduce waste and improve product consistency, which is vital for maintaining quality standards in mass production. Buyers in the Middle East and Europe should consider equipment capacity and the availability of maintenance support, as these factors directly impact operational efficiency and downtime.
How Do Catering Services Benefit from Kitchen Equipment Suppliers?
Catering services utilize mobile kitchen units and portable cooking equipment to serve food at various locations and events. This flexibility allows caterers to adapt to different settings and cuisines, enhancing their service offerings. For international buyers, especially in regions like Turkey and Brazil, key sourcing considerations include the portability of equipment, ease of setup, and the ability to accommodate diverse menu items while maintaining high standards of food safety.
What Role Does Kitchen Equipment Play in Retail Food Service?
In retail food service, kitchen equipment suppliers provide display and refrigeration units that enhance product visibility and preserve the freshness of perishable items. Supermarkets and grocery stores rely on these units to attract customers and maintain quality standards. B2B buyers should focus on energy efficiency and size to optimize operational costs while ensuring compliance with health regulations, particularly in regions with stringent food safety laws.
How is Kitchen Equipment Essential for Institutional Food Services?
For institutional food services, such as schools and hospitals, bulk cooking equipment is vital for preparing large quantities of meals consistently. Kitchen equipment suppliers offer solutions that ensure meal quality and quantity, meeting the dietary needs of diverse populations. Buyers in Africa and South America must prioritize safety standards, ease of cleaning, and warranty services, as these factors significantly affect long-term operational success and compliance with health regulations.
Related Video: ESSENTIAL BAKING EQUIPMENT & THEIR USES | necessary baking equipment for your kitchen
3 Common User Pain Points for ‘kitchen equipment supplier’ & Their Solutions
Scenario 1: Struggling with Equipment Compatibility
The Problem:
Many B2B buyers in the kitchen equipment sector face the challenge of ensuring that new appliances are compatible with existing setups. This is particularly critical for restaurants and catering businesses that have invested heavily in specific layouts and equipment. For instance, a buyer may purchase a new industrial oven only to discover that it does not fit with the ventilation system or power supply already in place. This not only leads to costly returns but can also disrupt service and harm the business’s reputation.
The Solution:
To avoid compatibility issues, buyers should engage in thorough pre-purchase assessments. This involves creating detailed specifications that include dimensions, electrical requirements, and integration capabilities with existing systems. When sourcing kitchen equipment suppliers, inquire about their experience with similar projects and request case studies. Additionally, consider suppliers who offer virtual consultations or site visits to assess your space prior to making recommendations. This proactive approach ensures that the equipment not only fits physically but also operates efficiently within the established kitchen workflow.
Scenario 2: Navigating Supply Chain Disruptions
The Problem:
In today’s global market, international B2B buyers often encounter supply chain disruptions that delay equipment delivery, causing operational setbacks. For instance, a restaurant in Brazil might place an order for essential kitchen appliances, only to face unexpected delays due to shipping issues or geopolitical tensions. Such interruptions can lead to inventory shortages, forcing businesses to alter their menus or even close temporarily, which directly affects revenue.
The Solution:
To mitigate the risks associated with supply chain disruptions, buyers should diversify their supplier base. This means not relying solely on one supplier or region for all equipment needs. Additionally, establishing strong relationships with multiple suppliers can provide backup options in case of delays. It is also advisable to keep an eye on market trends and potential disruptions by subscribing to industry news and reports. Finally, consider stockpiling essential items that are less likely to be affected by supply chain issues, ensuring that operations can continue smoothly even during unforeseen circumstances.
Scenario 3: Overwhelmed by Equipment Choices
The Problem:
B2B buyers frequently feel overwhelmed by the vast array of kitchen equipment options available in the market. With numerous brands, models, and features to consider, making an informed decision can be daunting. This is especially true for buyers in regions like the Middle East, where culinary trends evolve rapidly, and the demand for high-quality, innovative equipment is high. The fear of making the wrong choice can lead to indecision or rushed purchases that do not meet the business’s needs.
The Solution:
To navigate the complexities of selecting the right kitchen equipment, buyers should develop a structured evaluation process. Begin by clearly defining the specific needs of your kitchen operation, including menu requirements, volume, and space constraints. Create a comparison chart that lists potential suppliers and their offerings, focusing on features, warranty, after-sales support, and customer reviews. Engaging with industry experts through forums or attending trade shows can also provide valuable insights into which equipment performs best in real-world scenarios. Lastly, consider pilot testing equipment in your kitchen environment before making a full commitment, allowing you to gauge its performance and suitability firsthand.
Strategic Material Selection Guide for kitchen equipment supplier
When selecting materials for kitchen equipment, international B2B buyers must consider various factors that impact performance, durability, and compliance with regional standards. Below, we analyze four common materials used in kitchen equipment, focusing on their properties, advantages, disadvantages, and specific considerations for buyers from Africa, South America, the Middle East, and Europe.
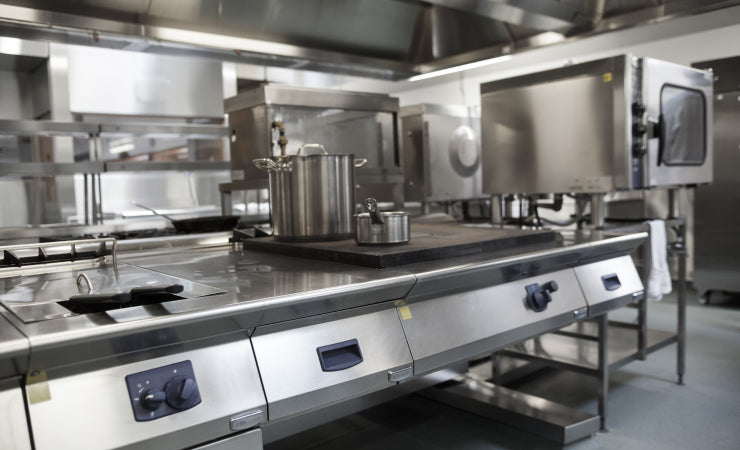
A stock image related to kitchen equipment supplier.
What Are the Key Properties of Stainless Steel in Kitchen Equipment?
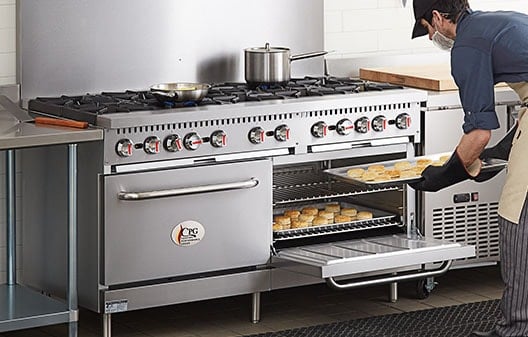
A stock image related to kitchen equipment supplier.
Stainless steel is renowned for its excellent corrosion resistance and ability to withstand high temperatures. It typically has a temperature rating of up to 1,500°F (815°C) and can handle significant pressure, making it ideal for cooking equipment. The alloy’s inherent strength and durability contribute to its long lifespan, reducing the need for frequent replacements.
Pros and Cons: The primary advantage of stainless steel is its durability and resistance to rust and staining. However, it can be more expensive than other materials, and its manufacturing process can be complex, which may lead to higher costs for B2B buyers.
Impact on Application: Stainless steel is compatible with various media, including acidic and alkaline substances, making it suitable for diverse kitchen environments. Buyers must ensure that the grade of stainless steel meets local standards, such as ASTM or DIN.
How Does Aluminum Perform as a Material for Kitchen Equipment?
Aluminum is lightweight and has excellent thermal conductivity, making it a popular choice for cookware and kitchen appliances. Its temperature rating is generally around 1,200°F (650°C), which is sufficient for most cooking applications.
Pros and Cons: The key advantage of aluminum is its low weight, which facilitates easy handling and transportation. However, it is more prone to corrosion and can warp under high heat, limiting its use in certain applications. Additionally, the cost of high-quality aluminum can be moderate to high, depending on the alloy.
Impact on Application: Aluminum is not suitable for acidic foods as it can react adversely, affecting the flavor and safety of the food. Buyers should consider this when selecting aluminum equipment, especially in regions with diverse culinary practices.
What Are the Benefits of Using Cast Iron in Kitchen Equipment?
Cast iron is known for its exceptional heat retention and even cooking capabilities. It can withstand high temperatures, typically rated up to 1,500°F (815°C), making it ideal for frying and baking applications.
Pros and Cons: The primary advantage of cast iron is its durability and ability to develop a natural non-stick surface when seasoned properly. However, it is heavy and requires regular maintenance to prevent rust, which can be a drawback for some users. Additionally, the cost can vary widely based on the quality and brand.
Impact on Application: Cast iron is compatible with various cooking methods, including induction and gas. International buyers should be aware of the specific maintenance requirements and ensure compliance with any food safety regulations in their region.
Why Consider Plastic Composites for Kitchen Equipment?
Plastic composites, such as polypropylene and polycarbonate, are becoming increasingly popular due to their versatility and resistance to impact and chemicals. They can typically withstand temperatures up to 250°F (121°C).
Pros and Cons: The main advantage of plastic composites is their lightweight nature and resistance to corrosion. However, they are less durable than metals and may not perform well under high-temperature conditions. The cost is generally lower than metals, making them an attractive option for budget-conscious buyers.
Impact on Application: Plastic composites are suitable for food storage and preparation but may not be ideal for cooking applications. Buyers should consider local regulations regarding plastic use in food contact applications to ensure compliance.
Summary Table of Material Selection for Kitchen Equipment
Material | Typical Use Case for kitchen equipment supplier | Key Advantage | Key Disadvantage/Limitation | Relative Cost (Low/Med/High) |
---|---|---|---|---|
Stainless Steel | Cookware, countertops, sinks | Excellent corrosion resistance | Higher cost and complex manufacturing | High |
Aluminum | Cookware, appliances | Lightweight and good thermal conductivity | Prone to corrosion and warping | Med |
Cast Iron | Frying pans, Dutch ovens | Exceptional heat retention | Heavy and requires maintenance | Med/High |
Plastic Composites | Food storage containers, cutting boards | Lightweight and corrosion-resistant | Less durable under high temperatures | Low |
In conclusion, understanding the properties, advantages, and limitations of these materials will help international B2B buyers make informed decisions that align with their operational needs and regional standards.
In-depth Look: Manufacturing Processes and Quality Assurance for kitchen equipment supplier
What Are the Key Stages in the Manufacturing Process of Kitchen Equipment?
Manufacturing kitchen equipment involves several critical stages, each designed to ensure the final product meets quality standards and customer specifications. The primary stages include:
-
Material Preparation: The initial phase involves sourcing high-quality raw materials such as stainless steel, aluminum, and plastic. Suppliers must ensure that materials are compliant with international standards and suitable for food safety. For instance, stainless steel should adhere to the ASTM A240 standard, which ensures corrosion resistance and durability.
-
Forming: This stage includes processes such as stamping, bending, and machining. Techniques vary based on the equipment being produced. For example, a commercial sink may undergo deep drawing, while cookware might be formed through casting. Advanced technologies like CNC machining are often employed for precision and efficiency.
-
Assembly: Once the individual components are formed, they are assembled into the final product. This may involve welding, riveting, or using adhesives, depending on the design. Assembly lines should be optimized for speed without compromising quality, often employing Lean Manufacturing principles to reduce waste and increase productivity.
-
Finishing: The last manufacturing stage focuses on enhancing the appearance and functionality of the kitchen equipment. This may involve polishing, coating, or painting to improve aesthetics and protect against corrosion. Quality finishing processes not only meet customer expectations but also ensure compliance with hygiene standards.
How is Quality Assurance Integrated into Kitchen Equipment Manufacturing?
Quality assurance (QA) is crucial in the manufacturing of kitchen equipment to ensure safety, durability, and compliance with international standards. The QA process typically involves several key components:
-
Adherence to International Standards: Many kitchen equipment suppliers adhere to ISO 9001, which outlines requirements for a quality management system. Compliance ensures that the manufacturing process consistently meets customer and regulatory requirements. Additionally, specific certifications like CE marking in Europe or API standards in the Middle East may be necessary, depending on the product type.
-
Quality Control Checkpoints:
– Incoming Quality Control (IQC): This involves inspecting raw materials upon receipt to ensure they meet specified standards. Suppliers should have protocols in place for rejecting substandard materials.
– In-Process Quality Control (IPQC): During the manufacturing stages, regular inspections are conducted to catch defects early. This includes monitoring machine settings and production processes.
– Final Quality Control (FQC): Once the product is assembled, it undergoes thorough testing for functionality and safety before shipment. This may include pressure tests for appliances and visual inspections for cosmetic flaws. -
Common Testing Methods:
– Mechanical Testing: Assessing durability through stress tests and impact resistance.
– Thermal Testing: Ensuring that equipment can withstand high temperatures, particularly for cookware.
– Hygiene Testing: Verifying that surfaces meet health and safety regulations, especially for food contact materials.
What Strategies Can B2B Buyers Use to Verify Supplier Quality Control?
For international B2B buyers, especially from regions like Africa, South America, the Middle East, and Europe, ensuring the quality of kitchen equipment suppliers is essential. Here are actionable strategies to verify supplier QC:
-
Conduct Supplier Audits: Schedule regular audits of potential suppliers to assess their manufacturing processes and quality control systems. During these audits, buyers should look for compliance with ISO standards and check for any certifications relevant to their market.
-
Request Quality Reports: Suppliers should provide detailed quality assurance reports, including data from IQC, IPQC, and FQC stages. These reports should outline the testing methods used, results obtained, and any corrective actions taken for defects.
-
Engage Third-Party Inspection Services: Utilizing independent third-party inspection services can provide an unbiased assessment of the supplier’s manufacturing and QC practices. These services can conduct inspections at various stages of the production process, ensuring adherence to international standards.
-
Understand Quality Control Nuances for Different Regions: It’s essential for buyers to be aware of regional differences in quality standards. For example, while CE marking is critical in Europe, it may not hold the same significance in Africa or South America. Understanding these nuances helps in making informed purchasing decisions.
How Can International B2B Buyers Enhance Their Supplier Relationships?
Building strong relationships with kitchen equipment suppliers can lead to better quality assurance and more reliable service. Here are some strategies:
-
Establish Clear Communication Channels: Open and transparent communication regarding quality expectations, delivery timelines, and product specifications can prevent misunderstandings and improve overall quality.
-
Collaborate on Quality Improvement Initiatives: Work alongside suppliers to develop quality improvement programs. Sharing insights and best practices can lead to enhanced manufacturing processes and product quality.
-
Leverage Technology for Monitoring: Utilizing technology such as IoT devices or quality management software can help buyers monitor supplier performance in real-time, allowing for quicker responses to quality issues.
-
Invest in Training and Development: Providing training for suppliers on international quality standards and best practices can enhance their capabilities and ensure that they meet your quality expectations.
Conclusion
Understanding the intricacies of manufacturing processes and quality assurance in the kitchen equipment industry is crucial for international B2B buyers. By focusing on the key stages of manufacturing, implementing robust quality control measures, and fostering strong supplier relationships, buyers can ensure they receive high-quality kitchen equipment that meets their needs and complies with international standards. This proactive approach not only enhances product reliability but also contributes to the overall success of their operations.
Practical Sourcing Guide: A Step-by-Step Checklist for ‘kitchen equipment supplier’
When sourcing kitchen equipment suppliers, especially for international B2B transactions, a systematic approach can significantly streamline the process. This checklist serves as a comprehensive guide to ensure that you make informed decisions while procuring kitchen equipment that meets your operational needs.
Step 1: Define Your Technical Specifications
Before initiating contact with suppliers, clearly outline your kitchen equipment requirements. This includes the type of equipment needed, capacity, functionality, and any specific features that are essential for your operations. Having a detailed specification helps in communicating your needs accurately and ensures that suppliers can provide relevant solutions.
Step 2: Research Potential Suppliers
Conduct thorough research to identify potential kitchen equipment suppliers. Utilize online platforms, industry forums, and trade shows to gather information. Look for suppliers with experience in your region, such as Africa, South America, the Middle East, or Europe, as they may have better insights into local market demands and regulations.
Step 3: Evaluate Supplier Credentials
It is crucial to verify the credentials of potential suppliers. Check for relevant certifications, such as ISO or local food safety standards, which demonstrate compliance with quality assurance practices. Additionally, inquire about their manufacturing processes and quality control measures to ensure reliability.
Step 4: Request and Compare Quotations
Once you have shortlisted suppliers, request detailed quotations. Ensure that the quotations include all relevant costs, such as shipping, taxes, and after-sales services. Comparing multiple quotes not only helps in identifying the best value but also provides insights into market pricing trends.
Step 5: Assess Supplier Experience and Reputation
Investigate the supplier’s market reputation by seeking references and reading customer reviews. Assess their experience in supplying kitchen equipment similar to your needs. A supplier with a proven track record in your industry is likely to offer better support and reliability.
Step 6: Negotiate Terms and Conditions
Engage in negotiations to establish favorable terms and conditions. This includes payment terms, delivery timelines, and warranty provisions. Be clear about your expectations and ensure that both parties understand the contractual obligations to avoid any future disputes.
Step 7: Plan for After-Sales Support
After selecting a supplier, discuss the after-sales support they offer. This includes installation services, training for staff, and maintenance options. Ensuring robust after-sales support can enhance the longevity and efficiency of your kitchen equipment, ultimately contributing to your operational success.
By following these steps, B2B buyers can effectively navigate the complexities of sourcing kitchen equipment suppliers, ensuring they find reliable partners that meet their specific needs and standards.
Comprehensive Cost and Pricing Analysis for kitchen equipment supplier Sourcing
What Are the Key Cost Components in Sourcing Kitchen Equipment?
When sourcing kitchen equipment, understanding the cost structure is critical for international B2B buyers. The primary cost components include:
-
Materials: The choice of materials significantly affects the overall cost. For instance, stainless steel is more expensive than aluminum but offers better durability and hygiene, which can be a vital consideration in the food service industry.
-
Labor: Labor costs vary widely depending on the country of manufacture. Countries in Africa or South America may offer lower labor costs, but this can also impact the skill level and quality of craftsmanship.
-
Manufacturing Overhead: This includes costs related to utilities, rent, and administrative expenses. Suppliers with higher operational efficiency can offer better pricing.
-
Tooling: Custom tooling for specialized equipment can add significant costs. Buyers should consider whether the investment in tooling is justified by the expected return, particularly for low-volume orders.
-
Quality Control (QC): Ensuring that products meet specific standards often requires additional QC processes, which can increase costs. Suppliers with certifications (like ISO) may charge more, but they also provide assurance of quality.
-
Logistics: Shipping costs can vary based on distance, mode of transport, and current fuel prices. Understanding Incoterms can help buyers manage these costs effectively.
-
Margin: Suppliers typically include a profit margin in their pricing. Knowing the industry standard margins can aid buyers in negotiations.
How Do Price Influencers Affect Kitchen Equipment Sourcing?
Several factors can influence pricing when sourcing kitchen equipment:
-
Volume and Minimum Order Quantity (MOQ): Larger orders usually result in lower per-unit costs. Buyers should evaluate their needs against the MOQ to avoid excess inventory.
-
Specifications and Customization: Custom equipment tailored to specific requirements can drive up costs. Consider whether standard solutions can meet your needs without the additional expense of customization.
-
Material Quality and Certifications: Equipment made from high-quality materials or certified to specific standards (e.g., NSF, CE) will typically command higher prices. Assess whether these certifications are necessary for your market.
-
Supplier Factors: The reputation and reliability of suppliers can impact pricing. Established suppliers with a history of quality may charge more, but they can also reduce risks associated with sourcing.
-
Incoterms: Understanding the implications of different Incoterms (like FOB, CIF, etc.) can help buyers manage shipping costs and responsibilities effectively.
What Are the Best Negotiation Strategies for International B2B Buyers?
For international buyers, particularly those from Africa, South America, the Middle East, and Europe, effective negotiation strategies can lead to significant cost savings:
-
Research and Benchmarking: Before negotiations, conduct thorough research on market prices and competitors. This knowledge can provide leverage during discussions.
-
Emphasize Long-term Relationships: Building a long-term relationship with suppliers can result in better pricing and terms. Suppliers may offer discounts for repeat business or larger orders.
-
Negotiate Total Cost of Ownership (TCO): Rather than focusing solely on the initial purchase price, consider the TCO, which includes maintenance, energy consumption, and potential resale value. This holistic view can lead to better overall value.
-
Utilize Payment Terms to Your Advantage: Flexibility in payment terms can sometimes yield discounts. For example, offering upfront payment might persuade a supplier to lower prices.
-
Be Mindful of Cultural Differences: Understanding cultural nuances in negotiation can foster better communication and outcomes. Different regions may have unique approaches to business and negotiation styles.
Conclusion: Understanding Pricing Nuances for International Buyers
While pricing for kitchen equipment can vary significantly based on numerous factors, international B2B buyers can navigate these complexities by focusing on cost components, understanding price influencers, and employing strategic negotiation techniques. Always seek to balance quality with cost to ensure you make informed purchasing decisions. Keep in mind that prices can fluctuate based on market conditions, and it’s wise to obtain indicative pricing rather than fixed quotes.
Alternatives Analysis: Comparing kitchen equipment supplier With Other Solutions
When considering the procurement of kitchen equipment, B2B buyers often seek alternatives to traditional kitchen equipment suppliers. Exploring various solutions can lead to better cost management, improved efficiency, and enhanced operational capabilities. Below, we compare the conventional kitchen equipment supplier model with two viable alternatives: leasing kitchen equipment and utilizing commercial kitchen co-ops.
Comparison Table of Kitchen Equipment Solutions
Comparison Aspect | Kitchen Equipment Supplier | Leasing Kitchen Equipment | Commercial Kitchen Co-ops |
---|---|---|---|
Performance | High-quality, durable equipment | Variable, depending on supplier | Access to diverse equipment |
Cost | High upfront investment | Lower initial costs but ongoing fees | Shared costs can reduce expenses |
Ease of Implementation | Requires extensive setup | Quick setup; equipment delivered | Requires coordination among users |
Maintenance | Supplier handles maintenance | Maintenance included in lease | Users share maintenance responsibilities |
Best Use Case | Long-term operations, established businesses | Startups, seasonal businesses | Entrepreneurs, food startups needing flexibility |
What Are the Pros and Cons of Leasing Kitchen Equipment?
Leasing kitchen equipment is an attractive alternative for businesses that want to minimize upfront costs. This method allows buyers to access high-quality equipment without the significant capital investment required for outright purchases. Leasing typically includes maintenance services, which can save time and reduce operational disruptions. However, ongoing lease payments can accumulate, potentially leading to higher long-term costs. Additionally, businesses may face limitations in equipment customization, as leased items are often standardized.
How Do Commercial Kitchen Co-ops Work for B2B Buyers?
Commercial kitchen co-ops provide shared access to kitchen facilities and equipment. This model is particularly beneficial for startups or small businesses that may not have the resources to invest in their own kitchen setups. Co-ops allow multiple businesses to share costs and resources, promoting collaboration and reducing waste. However, the need for coordination can create scheduling challenges, and quality may vary based on the collective maintenance efforts. Businesses must also ensure that the co-op meets health and safety standards.
Conclusion: Which Kitchen Equipment Solution Is Right for Your Business?
Choosing the right kitchen equipment solution depends on your business’s specific needs, budget constraints, and operational goals. If you seek high-performance equipment for long-term use and have the capital to invest, traditional kitchen equipment suppliers may be the best fit. On the other hand, if your business is just starting or operates seasonally, leasing could provide the flexibility you need. For food entrepreneurs looking to minimize costs and collaborate with others, commercial kitchen co-ops can be an effective alternative. Ultimately, consider factors like performance, cost, and ease of implementation to make an informed decision that aligns with your business strategy.
Essential Technical Properties and Trade Terminology for kitchen equipment supplier
What Are the Key Technical Properties of Kitchen Equipment?
When sourcing kitchen equipment, understanding technical specifications is vital for making informed purchasing decisions. Here are some essential properties to consider:
1. Material Grade: Why Is It Important for Durability?
The material grade of kitchen equipment (such as stainless steel, aluminum, or plastic) affects durability, corrosion resistance, and overall performance. For instance, 304-grade stainless steel is commonly used for commercial kitchen equipment due to its high resistance to rust and staining, making it ideal for environments with high humidity and temperature fluctuations. Choosing the right material ensures longevity and reduces replacement costs, a crucial factor for B2B buyers in the food service industry.
2. Tolerance Levels: How Do They Affect Equipment Functionality?
Tolerance levels refer to the allowable deviation from specified dimensions in manufacturing. Tight tolerances (e.g., +/- 0.5 mm) are critical for precision equipment such as ovens and refrigerators, where exact measurements ensure optimal performance. For B2B buyers, understanding these tolerances helps in assessing equipment reliability and compatibility with existing kitchen layouts.
3. Capacity: What Should Buyers Consider?
Capacity indicates the volume of food or ingredients an appliance can handle, such as the number of meals a commercial oven can cook simultaneously. This specification is vital for international buyers, particularly in regions like Africa and South America, where demand can vary widely. Selecting equipment with appropriate capacity ensures that operational efficiency meets business needs without overextending resources.
4. Energy Efficiency Ratings: Why Are They Essential?
Energy efficiency ratings, often indicated by certifications such as ENERGY STAR, inform buyers about an appliance’s energy consumption. For B2B buyers, particularly in Europe and the Middle East, this not only impacts operational costs but also aligns with sustainability goals. Investing in energy-efficient kitchen equipment can lead to significant savings over time and enhance corporate responsibility initiatives.
5. Compliance Standards: What Regulations Must Be Met?
Compliance with local and international safety and health regulations (like NSF or CE certifications) is crucial. These standards ensure that kitchen equipment meets the necessary safety and sanitation requirements. For buyers in diverse markets, understanding compliance helps mitigate risks associated with importing non-compliant products, safeguarding their investments.
What Are Common Trade Terms in Kitchen Equipment Supply?
Navigating the kitchen equipment supply chain involves familiarizing oneself with industry jargon. Here are some key terms:
1. OEM (Original Equipment Manufacturer): What Does It Signify?
An OEM refers to a company that produces parts or equipment that may be marketed by another manufacturer. In the kitchen equipment industry, this term is crucial for buyers looking for high-quality components that fit their specific needs. Understanding OEM relationships can help buyers ensure they are sourcing reliable products that uphold brand standards.
2. MOQ (Minimum Order Quantity): How Does It Impact Purchasing?
MOQ is the smallest quantity of a product that a supplier is willing to sell. This term is particularly relevant for B2B buyers who need to plan their inventory and budget accordingly. Knowing the MOQ helps in negotiating better terms and can influence the decision to partner with a supplier.
3. RFQ (Request for Quotation): What Is Its Purpose?
An RFQ is a document sent to suppliers to invite them to bid on specific products or services. For international buyers, submitting an RFQ can streamline the procurement process and ensure competitive pricing. This term is essential for buyers looking to compare offers and negotiate better deals.
4. Incoterms: Why Are They Critical for International Trade?
Incoterms (International Commercial Terms) define the responsibilities of buyers and sellers in international transactions. Familiarity with these terms, such as FOB (Free on Board) or CIF (Cost, Insurance, and Freight), is essential for B2B buyers to understand shipping costs, insurance, and risk management in the supply chain.
5. Lead Time: What Should Buyers Be Aware Of?
Lead time refers to the time between placing an order and receiving it. For kitchen equipment suppliers, understanding lead times is crucial for inventory management and ensuring timely service. Buyers should consider lead times when planning menu changes or new openings to avoid operational delays.
By comprehensively understanding these technical properties and trade terms, international B2B buyers can make informed decisions, optimize their procurement processes, and enhance operational efficiency in their kitchen operations.
Navigating Market Dynamics and Sourcing Trends in the kitchen equipment supplier Sector
What Are the Current Market Dynamics and Key Trends in the Kitchen Equipment Supplier Sector?
The kitchen equipment supplier market is currently experiencing dynamic shifts driven by globalization, technological advancements, and changing consumer preferences. One of the key trends is the increasing demand for smart kitchen appliances, which integrate IoT (Internet of Things) technology. This trend is particularly pronounced in urban areas of Africa, South America, the Middle East, and Europe, where consumers are seeking efficiency and convenience in food preparation.
In addition to technological innovation, sustainability has become a crucial factor influencing purchasing decisions. B2B buyers are increasingly prioritizing suppliers that offer energy-efficient appliances and sustainable materials. The growing awareness of environmental impact is prompting suppliers to innovate in product design, focusing on durability and recyclability, which are essential for appealing to eco-conscious businesses and consumers alike.
Moreover, the ongoing disruptions in global supply chains, exacerbated by geopolitical tensions and the pandemic, have forced international buyers to diversify their sourcing strategies. This has led to a rise in local sourcing initiatives in regions like Turkey and Brazil, where suppliers are adapting to meet the needs of local markets while maintaining quality and compliance with international standards.
How Does Sustainability and Ethical Sourcing Impact the Kitchen Equipment Supplier Market?
Sustainability is no longer just a trend; it has become a necessity for kitchen equipment suppliers aiming to remain competitive in the B2B landscape. The environmental impact of manufacturing processes, including energy consumption and waste generation, is under scrutiny. Suppliers are increasingly adopting ‘green’ certifications, such as Energy Star and ISO 14001, which demonstrate their commitment to sustainable practices.
Ethical sourcing has also gained prominence, with buyers demanding transparency throughout the supply chain. This means that suppliers must not only provide high-quality products but also ensure that their materials are sourced responsibly, without exploiting labor or harming the environment. Engaging in fair trade practices and utilizing recycled materials can enhance a supplier’s reputation and appeal to socially responsible businesses.
Furthermore, the implementation of sustainable practices is often linked to cost savings in the long term. By investing in energy-efficient equipment and sustainable materials, businesses can reduce operational costs and improve their overall environmental footprint, making them more attractive to eco-conscious consumers and partners.
What Is the Evolution of the Kitchen Equipment Supplier Sector?
The kitchen equipment supplier sector has evolved significantly over the last few decades, transitioning from traditional manufacturing methods to advanced technologies. Initially, the market was dominated by local artisans and small manufacturers. However, as globalization took hold, larger companies began to dominate the landscape, offering a wider range of products and innovations.
In recent years, the introduction of digital platforms has transformed how B2B buyers source kitchen equipment. Online marketplaces and e-commerce platforms now allow buyers from diverse regions, including Africa and the Middle East, to connect with suppliers worldwide, fostering competition and innovation. This shift has also enabled suppliers to gather valuable data on consumer preferences, allowing for more tailored product offerings.
As the market continues to evolve, the integration of technology and sustainability into the supply chain will likely define the future of the kitchen equipment supplier sector, ensuring that it remains responsive to the needs of international B2B buyers.
Frequently Asked Questions (FAQs) for B2B Buyers of kitchen equipment supplier
-
How do I choose the right kitchen equipment supplier for my business?
Choosing the right kitchen equipment supplier involves several steps. Start by assessing your specific needs, including equipment type, capacity, and budget. Research suppliers who specialize in your required equipment and have a good reputation in your region, particularly in Africa, South America, the Middle East, and Europe. Look for reviews, client testimonials, and case studies. Additionally, ensure they comply with international quality standards and offer excellent customer support. Meeting suppliers at trade shows or industry events can also provide valuable insights into their offerings and reliability. -
What factors should I consider when sourcing kitchen equipment suppliers internationally?
When sourcing kitchen equipment suppliers internationally, consider factors such as quality certifications, production capabilities, shipping costs, and lead times. Evaluate their experience in exporting to your region and their understanding of local regulations. It’s essential to communicate clearly about your expectations, including customization options and minimum order quantities (MOQs). Building a strong relationship through regular communication can also facilitate smoother transactions and better service. -
What is the minimum order quantity (MOQ) when purchasing kitchen equipment?
Minimum order quantities (MOQs) vary significantly among suppliers and depend on the type of kitchen equipment. Some suppliers may have MOQs as low as a single unit for certain items, while others might require bulk orders to reduce costs. When negotiating with suppliers, discuss your specific needs and the possibility of lower MOQs for your initial orders, especially if you are a new buyer. This flexibility can help you manage cash flow and inventory effectively. -
How can I ensure the quality of kitchen equipment from suppliers?
To ensure the quality of kitchen equipment from suppliers, request samples before placing a large order. Look for suppliers who provide warranties and have quality assurance processes in place, such as ISO certifications. Conduct factory visits if possible, or use third-party inspection services to verify product quality and compliance with specifications. Additionally, review the supplier’s history and ask for references from previous clients to gauge their reliability and commitment to quality. -
What are the common payment terms for international kitchen equipment purchases?
Common payment terms for international kitchen equipment purchases include options like advance payment, letters of credit, and payment upon delivery. Many suppliers prefer a deposit upfront (usually 30-50%) with the balance due before shipment or upon delivery. It’s crucial to clarify payment terms during negotiations to avoid misunderstandings. Consider using secure payment methods that provide buyer protection, especially when dealing with new suppliers. -
What should I do if there are issues with my kitchen equipment order?
If you encounter issues with your kitchen equipment order, such as delays, defects, or incorrect items, contact the supplier immediately to discuss the situation. Document all communications and keep records of the order details. Most reputable suppliers will work with you to resolve issues, whether through refunds, replacements, or adjustments. Knowing your rights under the purchase agreement is essential, and consider involving a third party for mediation if necessary. -
How can I customize kitchen equipment to fit my business needs?
To customize kitchen equipment, communicate your specific requirements clearly to the supplier. Many suppliers offer customization options, such as size, features, and branding. Discuss the available materials and finishes that align with your operational needs. Be prepared to provide detailed specifications and perhaps even design mock-ups to ensure the supplier understands your vision. Establish a timeline for production and ensure that any changes do not compromise quality or delivery schedules.
- What logistics considerations should I keep in mind when importing kitchen equipment?
When importing kitchen equipment, consider logistics factors such as shipping methods, customs clearance, and delivery timelines. Choose a reliable freight forwarder familiar with your region’s import regulations to facilitate the process. It’s vital to understand the costs involved, including tariffs, duties, and shipping fees. Ensure that the supplier provides all necessary documentation, such as invoices and packing lists, to avoid delays at customs. Lastly, plan for potential supply chain disruptions by having contingency plans in place.
Important Disclaimer & Terms of Use
⚠️ Important Disclaimer
The information provided in this guide, including content regarding manufacturers, technical specifications, and market analysis, is for informational and educational purposes only. It does not constitute professional procurement advice, financial advice, or legal advice.
While we have made every effort to ensure the accuracy and timeliness of the information, we are not responsible for any errors, omissions, or outdated information. Market conditions, company details, and technical standards are subject to change.
B2B buyers must conduct their own independent and thorough due diligence before making any purchasing decisions. This includes contacting suppliers directly, verifying certifications, requesting samples, and seeking professional consultation. The risk of relying on any information in this guide is borne solely by the reader.
Strategic Sourcing Conclusion and Outlook for kitchen equipment supplier
Why is Strategic Sourcing Essential for Kitchen Equipment Suppliers?
In the competitive landscape of kitchen equipment supply, strategic sourcing stands out as a vital approach for international B2B buyers. By leveraging data-driven insights and supplier relationships, businesses can optimize procurement processes, enhance cost efficiency, and ensure product quality. Key takeaways emphasize the importance of understanding market trends, evaluating supplier capabilities, and aligning sourcing strategies with business objectives.
How Can International Buyers Benefit from Effective Sourcing Strategies?
For buyers in Africa, South America, the Middle East, and Europe, embracing strategic sourcing not only mitigates risks but also opens avenues for innovation and sustainability. Engaging with suppliers who demonstrate a commitment to quality and ethical practices can lead to long-term partnerships that drive growth. Furthermore, understanding regional market dynamics, such as import regulations and cultural preferences, allows buyers to make informed decisions that align with their operational goals.
What Does the Future Hold for Kitchen Equipment Procurement?
Looking ahead, the emphasis on digital transformation in procurement processes will become increasingly significant. International buyers should consider adopting advanced technologies such as AI and data analytics to enhance sourcing efficiency and responsiveness. As the global market continues to evolve, staying proactive in sourcing strategies will be crucial.
Take action today: Evaluate your sourcing practices and explore new supplier partnerships that can elevate your kitchen equipment procurement strategy to new heights.