Discover Top Kitchen Table Manufacturers: Your Sourcing Guide (2025)
Introduction: Navigating the Global Market for kitchen table manufacturer
In the competitive landscape of the global market, sourcing high-quality kitchen tables can pose significant challenges for international B2B buyers, particularly those in regions like Africa, South America, the Middle East, and Europe. The demand for durable, aesthetically pleasing, and functional kitchen tables continues to rise, driven by evolving consumer preferences and trends. This guide aims to simplify the complexities of finding the right kitchen table manufacturer by providing actionable insights into various types of kitchen tables, their applications, and the nuances of supplier vetting.
As an international buyer, understanding the diverse manufacturing capabilities across different regions is crucial. This guide delves into factors such as material selection, craftsmanship, and design trends that influence the quality and pricing of kitchen tables. Additionally, it highlights essential considerations for evaluating suppliers, including certifications, production capacity, and lead times, ensuring that you make informed purchasing decisions.
By equipping B2B buyers with a comprehensive understanding of the kitchen table manufacturing landscape, this guide empowers you to navigate potential pitfalls and identify reliable partners. Whether you’re looking to source unique artisan pieces or mass-produced items for a retail operation, having the right information at your fingertips will enhance your procurement strategy and ultimately drive your business success.
Understanding kitchen table manufacturer Types and Variations
Type Name | Key Distinguishing Features | Primary B2B Applications | Brief Pros & Cons for Buyers |
---|---|---|---|
Solid Wood Manufacturers | Crafted from hardwoods like oak or maple | Restaurants, hotels, and upscale dining | Pros: Durability, aesthetic appeal. Cons: Higher cost, heavier weight. |
Metal Frame Manufacturers | Use of steel or aluminum frames with wood tops | Cafés, outdoor dining, and modern eateries | Pros: Lightweight, modern design. Cons: Less warmth, can be prone to rust. |
Custom Furniture Makers | Tailored designs based on client specifications | High-end restaurants, bespoke projects | Pros: Unique designs, tailored solutions. Cons: Longer lead times, potentially higher costs. |
Folding Table Suppliers | Portable tables that can be easily stored | Catering services, events, and temporary setups | Pros: Space-saving, versatile. Cons: May lack durability, limited style options. |
Eco-Friendly Manufacturers | Made from sustainable materials | Health-conscious brands, eco-friendly venues | Pros: Sustainability appeal, unique materials. Cons: May have higher price points, limited availability. |
What Are the Characteristics of Solid Wood Kitchen Tables?
Solid wood manufacturers produce tables from durable hardwoods such as oak, maple, or cherry. These tables are highly valued for their longevity and classic aesthetic, making them a popular choice in upscale dining environments, including restaurants and hotels. When considering a purchase, B2B buyers should evaluate the wood species, finish options, and potential for customization. While solid wood tables often come with a higher price tag, their durability can lead to cost savings in the long run due to reduced replacement needs.
How Do Metal Frame Kitchen Tables Differ in Design and Use?
Metal frame manufacturers create tables that feature a combination of steel or aluminum frames with wooden or laminate tops. These tables are ideal for modern eateries and outdoor dining setups due to their lightweight construction and sleek design. B2B buyers should consider the type of metal used, as well as the finish, to ensure resistance to rust and wear. While metal tables can offer a contemporary aesthetic, they may lack the warmth associated with wood, which could be a drawback for certain dining environments.
What Should Buyers Know About Custom Furniture Makers?
Custom furniture makers specialize in creating bespoke kitchen tables tailored to specific client needs. These manufacturers often work with high-end restaurants and bespoke projects, providing unique designs that stand out in competitive markets. Buyers should consider lead times and the potential for higher costs due to the customization process. While the investment may be significant, the result is a distinctive piece that can enhance brand identity and customer experience.
Why Are Folding Tables a Practical Choice for B2B Buyers?
Folding table suppliers offer portable solutions that are ideal for catering services, events, and temporary setups. These tables can be easily stored and transported, making them a versatile option for businesses that require flexibility. B2B buyers should assess the durability and stability of the folding mechanism, as well as the materials used. Although folding tables may lack the durability and style of more permanent options, their convenience and space-saving features make them a practical choice for many businesses.
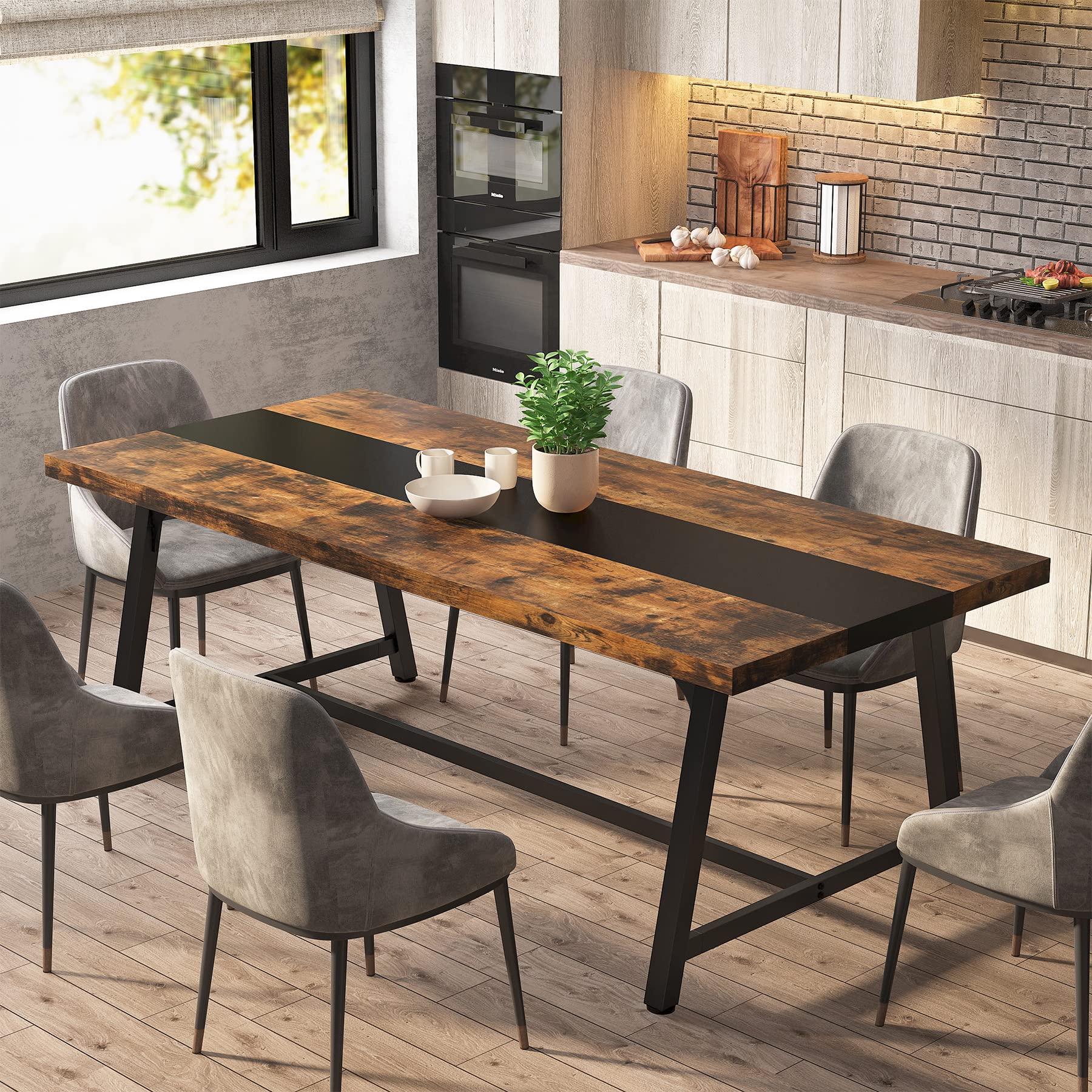
A stock image related to kitchen table manufacturer.
How Do Eco-Friendly Kitchen Table Manufacturers Cater to Modern Needs?
Eco-friendly manufacturers focus on creating kitchen tables from sustainable materials such as reclaimed wood or bamboo. These products appeal to health-conscious brands and eco-friendly venues that prioritize sustainability in their operations. When purchasing from eco-friendly manufacturers, B2B buyers should consider the certifications and sourcing practices of the materials used. While these tables may come at a premium, the increasing demand for sustainable products can enhance a brand’s reputation and attract a conscientious customer base.
Related Video: Modern Metal Dining Table Legs 2021 / Metal Table Design / Industrial Table
Key Industrial Applications of kitchen table manufacturer
Industry/Sector | Specific Application of Kitchen Table Manufacturer | Value/Benefit for the Business | Key Sourcing Considerations for this Application |
---|---|---|---|
Hospitality | Restaurant Dining Tables | Enhances customer experience and encourages repeat visits | Durability, design aesthetics, ease of maintenance |
Education | Cafeteria and School Dining Tables | Facilitates social interaction and improves dining efficiency | Safety standards, space optimization, material selection |
Residential Development | Multi-family Housing Common Area Tables | Promotes community engagement and adds value to properties | Customization options, durability, and weather resistance |
Retail | Display and Checkout Tables | Increases product visibility and improves customer flow | Size adaptability, design versatility, and material quality |
Event Management | Banquet and Conference Tables | Supports large gatherings and enhances event experience | Portability, easy setup and breakdown, and sturdiness |
How Are Kitchen Tables Utilized in the Hospitality Sector?
In the hospitality industry, particularly in restaurants and cafes, kitchen tables serve as essential dining furniture that directly impacts customer experience. A well-designed table can enhance the ambiance and encourage diners to stay longer, ultimately increasing sales. For international buyers, sourcing durable materials that withstand heavy use and are easy to clean is crucial. Additionally, aesthetic appeal matters, as it aligns with the restaurant’s theme and branding.
What Role Do Kitchen Tables Play in Educational Settings?
In educational institutions, cafeteria and school dining tables are vital for promoting social interaction among students. These tables need to be designed with safety in mind, adhering to specific regulations, especially for younger users. Buyers should consider the table’s ability to optimize space in often crowded dining areas, as well as the materials used, which should be resilient to wear and tear. Sourcing tables that are easy to maintain and can withstand daily use is essential for schools.
How Are Kitchen Tables Beneficial in Residential Developments?
In multi-family housing projects, common area tables foster community engagement among residents. These tables are not only functional but also add aesthetic value to shared spaces. Buyers from the residential development sector should prioritize customization options to match the overall design of the property. Additionally, the material must be durable and weather-resistant if placed outdoors. Ensuring that the tables can accommodate various activities, from casual gatherings to formal meetings, adds significant value.
Why Are Kitchen Tables Important in Retail Environments?
In retail settings, display and checkout tables are crucial for product visibility and customer flow. These tables should be adaptable in size and design to fit different store layouts and product types. International buyers must focus on sourcing tables made from high-quality materials that can withstand constant use while maintaining their appearance. Versatile designs that can be easily reconfigured for different promotional events can significantly enhance the shopping experience.
How Do Kitchen Tables Enhance Event Management?
For event management companies, banquet and conference tables are essential for hosting large gatherings. These tables need to be portable and easy to set up, allowing for quick transitions between different event styles. Buyers should consider the sturdiness of the tables, as they must support various setups and decorations. Additionally, sourcing options that allow for easy breakdown and storage can optimize space and reduce logistical challenges for event planners.
Related Video: What is Industrial Automation?
3 Common User Pain Points for ‘kitchen table manufacturer’ & Their Solutions
Scenario 1: Navigating Quality Control Challenges in Sourcing Kitchen Tables
The Problem:
One of the most significant challenges international B2B buyers face when sourcing kitchen tables is ensuring quality control. For buyers from regions like Africa and South America, where local manufacturing standards may vary, the risk of receiving subpar products can lead to severe financial losses and damage to reputation. Many manufacturers may promise high-quality materials and craftsmanship but fail to deliver upon shipment. This inconsistency can create trust issues and complicate future business relationships.
The Solution:
To mitigate quality control concerns, B2B buyers should implement a robust supplier evaluation process. Start by conducting thorough research on potential manufacturers, looking for those with certifications like ISO 9001 or other relevant quality standards. Engage in direct communication to clarify product specifications and quality expectations. Additionally, consider using third-party inspection services that can conduct on-site evaluations during the production phase. This proactive approach not only helps ensure that the kitchen tables meet the desired quality standards but also builds a foundation of trust with suppliers, paving the way for long-term partnerships.
Scenario 2: Addressing Supply Chain Disruptions in Kitchen Table Manufacturing
The Problem:
Supply chain disruptions can significantly impact the availability of kitchen tables, particularly for buyers in the Middle East and Europe, where demand can fluctuate dramatically. Factors such as political instability, natural disasters, or even logistical issues can lead to delays in production and delivery, causing frustration for buyers who depend on timely shipments for their business operations. These disruptions can result in lost sales opportunities and strained relationships with end customers.
The Solution:
To combat supply chain risks, international B2B buyers should diversify their supplier base. Instead of relying on a single manufacturer, consider establishing relationships with multiple suppliers across different regions. This strategy not only provides alternatives in case one supplier encounters issues but can also enhance negotiation power regarding pricing and terms. Additionally, implementing just-in-time inventory management can help balance the need for stock while minimizing excess inventory. Regular communication with suppliers about potential risks and updates can further ensure that buyers are prepared for any unforeseen challenges.
Scenario 3: Managing Customization Requests for Kitchen Tables
The Problem:
Customization is a critical factor for many B2B buyers, especially those serving niche markets or specific customer demographics. However, kitchen table manufacturers may struggle to accommodate unique design requests or specific material needs, leading to frustration and unmet expectations. This scenario is particularly common among buyers in Europe, where trends and consumer preferences shift rapidly. The inability to customize products can result in lost sales and diminished competitive advantage.
The Solution:
To successfully manage customization requests, B2B buyers should establish clear communication channels with kitchen table manufacturers from the outset. Provide detailed specifications and examples of desired designs, and inquire about the manufacturer’s capabilities regarding customization. It may also be beneficial to negotiate terms for minimum order quantities that allow for custom orders without incurring excessive costs. Furthermore, consider collaborating with manufacturers who have a strong track record of flexibility and innovation in design. This partnership approach not only enhances the likelihood of successful customization but also strengthens the overall business relationship, positioning both parties for future growth.
Strategic Material Selection Guide for kitchen table manufacturer
When selecting materials for kitchen tables, manufacturers must consider various factors that influence performance, durability, and cost. This section delves into four common materials used in kitchen table manufacturing: wood, metal, glass, and composite materials. Each material has distinct properties, advantages, and limitations that can significantly impact the final product’s suitability for international markets, particularly in Africa, South America, the Middle East, and Europe.
What Are the Key Properties of Wood for Kitchen Tables?
Wood is a traditional choice for kitchen tables, prized for its aesthetic appeal and versatility. The key properties of wood include its natural insulation, which provides a warm feel, and its ability to withstand moderate temperature variations. However, wood can be susceptible to moisture and pests, which may lead to warping or decay if not treated properly.
Pros and Cons of Wood:
– Pros: Wood is durable, repairable, and offers a classic look that appeals to many consumers. It can be sourced sustainably, aligning with increasing environmental awareness.
– Cons: The cost can vary significantly based on the type of wood, and high-quality options can be expensive. Additionally, wood requires regular maintenance to prevent damage.
Impact on Application:
Wood is compatible with various finishes and coatings, making it suitable for diverse kitchen environments. However, buyers should consider the local climate and humidity levels, as these factors can affect wood’s longevity.
How Does Metal Compare as a Material for Kitchen Tables?
Metal, particularly stainless steel and aluminum, is gaining popularity for kitchen tables due to its modern aesthetic and durability. Stainless steel offers excellent corrosion resistance and can withstand high temperatures, making it ideal for kitchen environments.
Pros and Cons of Metal:
– Pros: Metal tables are highly durable, easy to clean, and resistant to heat and stains. They often require less maintenance compared to wood.
– Cons: Metal can be cold to the touch and may not provide the same warmth as wood. Additionally, the manufacturing process can be more complex and costly.
Impact on Application:
Metal tables are suitable for high-traffic areas and can be used in both residential and commercial settings. However, international buyers should ensure compliance with local standards for metal finishes and coatings, particularly in regions with strict regulations.
What Are the Advantages of Glass in Kitchen Table Manufacturing?
Glass is often used in contemporary kitchen tables for its sleek appearance and ability to create an illusion of space. Tempered glass is commonly used for its strength and safety features, making it a practical choice for kitchen environments.
Pros and Cons of Glass:
– Pros: Glass is easy to clean, resistant to stains, and can enhance the aesthetic appeal of a kitchen. It is also available in various thicknesses and finishes.
– Cons: Glass can be prone to chipping and scratching, and its fragility may limit its use in certain environments. Additionally, it can be more expensive than other materials.
Impact on Application:
Glass tables can complement various kitchen styles but may not be suitable for families with young children due to safety concerns. International buyers should consider local preferences for glass thickness and safety standards.
Why Consider Composite Materials for Kitchen Tables?
Composite materials, such as engineered wood or resin, combine the benefits of various materials to create a durable and versatile product. These materials often mimic the appearance of wood or stone while offering enhanced durability and resistance to moisture.
Pros and Cons of Composite Materials:
– Pros: Composites are typically more affordable than solid wood and can be designed to resist scratches, stains, and moisture. They are also lightweight and easy to transport.
– Cons: The aesthetic may not appeal to all consumers, particularly those seeking the authenticity of natural materials. Additionally, the manufacturing process can involve chemicals that may raise environmental concerns.
Impact on Application:
Composite materials are suitable for a wide range of kitchen styles and can be tailored to meet specific design requirements. International buyers should be aware of local regulations regarding the use of composites and potential off-gassing issues.
Summary Table of Material Selection for Kitchen Tables
Material | Typical Use Case for kitchen table manufacturer | Key Advantage | Key Disadvantage/Limitation | Relative Cost (Low/Med/High) |
---|---|---|---|---|
Wood | Residential and rustic-style tables | Aesthetic appeal and repairability | Susceptible to moisture and pests | Medium to High |
Metal | Modern and commercial kitchen tables | Durability and easy maintenance | Cold feel and complex manufacturing | Medium to High |
Glass | Contemporary and space-enhancing tables | Sleek appearance and easy to clean | Prone to chipping and higher cost | Medium to High |
Composite | Versatile and budget-friendly tables | Affordable and moisture-resistant | Aesthetic may not appeal to all buyers | Low to Medium |
This guide provides international B2B buyers with a clear understanding of the materials available for kitchen table manufacturing, enabling informed decisions that align with market demands and compliance standards.
In-depth Look: Manufacturing Processes and Quality Assurance for kitchen table manufacturer
What Are the Key Stages in the Manufacturing Process of Kitchen Tables?
The manufacturing process of kitchen tables is a multi-stage procedure that requires careful planning and execution to ensure quality and durability. Here are the main stages involved:
Material Preparation
This initial stage involves selecting high-quality raw materials, which may include various types of wood, metal, glass, or composite materials. The choice of material directly impacts the table’s aesthetics, durability, and functionality. For instance, hardwoods like oak or maple are preferred for their strength and longevity, while softwoods like pine offer affordability but may require more frequent replacement.
Before production begins, materials undergo a treatment process to remove impurities and enhance their properties. This can involve drying wood to a specific moisture level or applying chemical treatments to metals to prevent corrosion. International B2B buyers should ensure their suppliers utilize sustainable sourcing practices and comply with environmental regulations.
How Are Kitchen Tables Formed?
Once the materials are prepared, the forming stage begins. This can involve various techniques:
- Cutting: Materials are cut to size using precision tools like saws or CNC machines, ensuring uniformity and accuracy.
- Shaping: This process may include bending, molding, or carving to create the desired design. Techniques like steam bending for wood can add aesthetic value while maintaining structural integrity.
- Joining: Components are assembled using adhesives, screws, or dowels. The choice of joining method can affect the table’s strength and longevity, so buyers should inquire about the techniques used.
What Is the Assembly Process for Kitchen Tables?
In the assembly stage, all formed components come together. This step is crucial as it determines the overall stability and functionality of the kitchen table. Key considerations during assembly include:
- Alignment: Ensuring all parts fit together perfectly to avoid wobbling or instability.
- Finishing Touches: This includes sanding rough edges, applying stains or paints, and ensuring that surfaces are smooth. A well-finished product not only looks better but also enhances durability.
Effective assembly processes often employ jigs and fixtures to maintain accuracy, which is essential for mass production. Buyers should verify that suppliers have robust assembly techniques to minimize defects.
How Is the Finishing Stage Executed?
The finishing stage is where the kitchen table is transformed into a market-ready product. This typically involves:
- Surface Treatment: Applying protective coatings like varnishes, lacquers, or oils to enhance durability and aesthetics. This step also helps in protecting the material from moisture and wear.
- Quality Checks: Before final packaging, tables undergo a series of inspections to ensure they meet design specifications and quality standards.
What Are the Quality Assurance Measures for Kitchen Tables?
Quality assurance is a critical aspect of kitchen table manufacturing, ensuring that the final product meets both international standards and customer expectations.
Which International Standards Should Buyers Be Aware Of?
International standards like ISO 9001 set the framework for quality management systems. Compliance with these standards is a significant indicator of a manufacturer’s commitment to quality. In addition to ISO, specific certifications such as CE (Conformité Européenne) for European markets or API (American Petroleum Institute) for materials used in kitchen tables can provide additional assurance of product safety and quality.
What Are the Key Quality Control Checkpoints?
Quality control (QC) is integral to ensuring the consistency and reliability of kitchen tables. The QC process typically includes three critical checkpoints:
-
Incoming Quality Control (IQC): This involves inspecting raw materials upon arrival at the manufacturing facility. Buyers should ensure that suppliers conduct thorough checks for material quality and certifications.
-
In-Process Quality Control (IPQC): During the manufacturing process, regular inspections are conducted to identify defects early. Techniques such as visual inspections and measurements ensure that components meet predefined specifications.
-
Final Quality Control (FQC): Once the tables are fully assembled, a final inspection is conducted to ensure they meet quality standards. This stage may involve functionality tests, load tests, and surface quality checks.
What Common Testing Methods Are Used in Quality Assurance?
Manufacturers employ various testing methods to ensure product quality, including:
- Mechanical Testing: Assessing the strength and durability of materials through stress tests.
- Visual Inspections: Checking for surface imperfections, alignment, and overall finish.
- Dimensional Testing: Verifying that all components meet specified measurements.
How Can B2B Buyers Verify Supplier Quality Control?
For international B2B buyers, particularly from Africa, South America, the Middle East, and Europe, verifying a supplier’s quality control processes is essential to avoid costly mistakes.
What Auditing Practices Should Be Considered?
Buyers should conduct thorough audits of potential suppliers. This can include:
- On-Site Inspections: Visiting manufacturing facilities to assess production capabilities and quality assurance practices.
- Reviewing Quality Reports: Requesting documentation that outlines previous QC checks, certifications, and compliance with international standards.
- Third-Party Inspections: Engaging independent inspection agencies to evaluate the manufacturing processes and product quality.
What Are the QC Certification Nuances for Different Regions?
Different regions may have varying standards and certifications that can affect the kitchen table manufacturing process. For example, European buyers may prioritize CE marking, while buyers in Africa might look for compliance with local standards. Understanding these nuances is vital for establishing reliable partnerships and ensuring that products meet market requirements.
Conclusion: How to Ensure Quality in Your Kitchen Table Supply Chain?
By understanding the manufacturing processes and quality assurance measures involved in kitchen table production, B2B buyers can make informed decisions when selecting suppliers. Emphasizing quality control, compliance with international standards, and thorough supplier verification will not only enhance product reliability but also foster long-term business relationships.
Practical Sourcing Guide: A Step-by-Step Checklist for ‘kitchen table manufacturer’
The following practical sourcing guide provides a comprehensive checklist for international B2B buyers interested in procuring kitchen tables from manufacturers. This guide is designed to help you navigate the complexities of sourcing, ensuring you make informed decisions that align with your business needs.
Step 1: Define Your Technical Specifications
Clearly outline the specifications for the kitchen tables you intend to source. Consider materials, dimensions, finishes, and design styles that resonate with your target market. This step is crucial as it sets the foundation for your sourcing process and helps in filtering out suppliers who cannot meet your requirements.
- Materials: Decide if you prefer solid wood, metal, or composite materials.
- Size and Shape: Determine the dimensions and whether you want rectangular, round, or custom shapes.
Step 2: Research Potential Markets and Suppliers
Conduct thorough research on the regions known for kitchen table manufacturing. Countries like Turkey, Indonesia, and various European nations have established reputations in furniture production. This step is vital to identify reliable suppliers who understand your market’s trends and consumer preferences.
- Market Trends: Investigate what styles are currently in demand in your region.
- Supplier Directories: Utilize platforms like Alibaba or Global Sources to find potential manufacturers.
Step 3: Evaluate Supplier Capabilities
Before committing to any manufacturer, it is essential to assess their production capabilities. Request detailed information about their manufacturing processes, production capacity, and lead times. This evaluation helps ensure that the supplier can meet your demand without compromising quality.
- Production Capacity: Inquire about their ability to scale production based on your orders.
- Quality Control: Ask about their quality assurance processes to ensure standards are met.
Step 4: Verify Supplier Certifications and Compliance
Ensure that your selected suppliers hold relevant certifications, such as ISO 9001 for quality management systems or compliance with international safety standards. This step protects your business from potential legal issues and reinforces trust in your supplier’s reliability.
- Safety Standards: Check if they comply with regulations specific to your target markets.
- Sustainability Certifications: If eco-friendliness is a priority, look for certifications like FSC (Forest Stewardship Council).
Step 5: Request Samples for Quality Assessment
Before finalizing any orders, request samples of the kitchen tables. This allows you to evaluate the quality, craftsmanship, and materials firsthand. It is a critical step to avoid costly mistakes in your procurement process.
- Material Quality: Assess the durability and finish of the materials used.
- Design Accuracy: Ensure that the samples match your specified designs and dimensions.
Step 6: Negotiate Terms and Conditions
Once you have identified a potential supplier, engage in negotiations regarding pricing, payment terms, and delivery schedules. Clear agreements are essential to prevent misunderstandings and ensure a smooth transaction process.
- Payment Terms: Decide on upfront payments versus payment upon delivery.
- Delivery Schedules: Confirm lead times and any penalties for delays.
Step 7: Establish a Communication Plan
Set up a clear communication plan with your supplier to facilitate ongoing dialogue. Regular check-ins can help address any issues that may arise during production and ensure that your project stays on track.
- Preferred Communication Channels: Decide on email, phone calls, or messaging apps.
- Frequency of Updates: Agree on how often you will receive updates on production status.
By following this step-by-step checklist, B2B buyers can effectively navigate the sourcing process for kitchen tables, ensuring they partner with reliable manufacturers that meet their business needs.
Comprehensive Cost and Pricing Analysis for kitchen table manufacturer Sourcing
What Are the Key Cost Components in Kitchen Table Manufacturing?
When sourcing kitchen tables, understanding the cost structure is essential for effective budgeting and negotiation. The primary cost components include:
-
Materials: The type of wood, metal, or composite materials significantly influences the price. For instance, solid hardwoods like oak or walnut will typically be more expensive than engineered wood. Additionally, sourcing sustainable materials can also affect costs.
-
Labor: Labor costs vary widely depending on the location of the manufacturer. Countries with lower labor costs, such as those in South America or parts of Africa, may offer more competitive pricing, but this must be balanced against quality and craftsmanship.
-
Manufacturing Overhead: This includes utilities, rent, and equipment maintenance. Manufacturers with advanced technology may have higher overhead costs, but they can also achieve efficiencies that reduce overall production costs.
-
Tooling: Custom tooling for unique designs can add significant upfront costs. However, this investment can lead to economies of scale in mass production.
-
Quality Control (QC): Ensuring high-quality standards incurs costs. Implementing rigorous QC processes can prevent defects, but these costs need to be factored into the overall price.
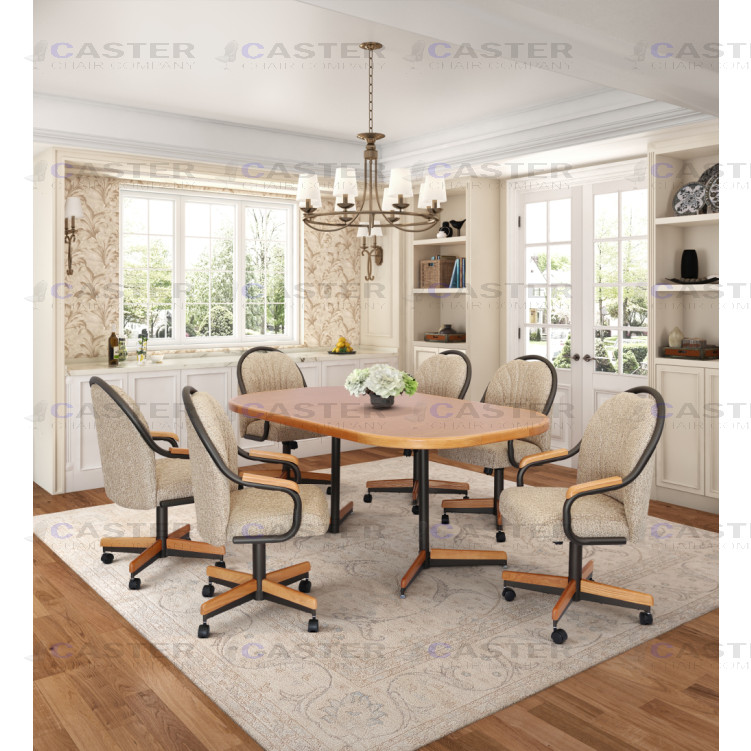
A stock image related to kitchen table manufacturer.
-
Logistics: Shipping and handling costs are critical, especially for international buyers. These can vary based on the mode of transport (air vs. sea), distance, and the chosen Incoterms.
-
Margin: Manufacturers typically add a markup to cover their profit margin. Understanding the industry standard for margins can help buyers negotiate better.
How Do Price Influencers Affect Kitchen Table Costs?
Several factors influence the pricing of kitchen tables, which international B2B buyers should consider:
-
Volume and Minimum Order Quantity (MOQ): Larger orders often lead to lower per-unit costs. Buyers should negotiate MOQs that align with their purchasing capacity to maximize savings.
-
Specifications and Customization: Custom designs or specific finishes can increase costs. Buyers should be clear about their requirements and explore options for standard models that may reduce expenses.
-
Material Quality and Certifications: Higher quality materials and certifications (such as FSC for sustainable sourcing) can elevate costs. Buyers should assess the value of these certifications against their target market demands.
-
Supplier Factors: The reputation and reliability of the supplier can impact pricing. Established suppliers may charge more due to their track record of quality and service.
-
Incoterms: Understanding the terms of shipping can affect total costs. Incoterms dictate who bears the cost and risk at various stages of the shipping process, and clarity here can prevent unexpected expenses.
What Buyer Tips Can Enhance Cost Efficiency in Sourcing?
International B2B buyers can adopt several strategies to improve cost efficiency when sourcing kitchen tables:
-
Negotiate Effectively: Leverage your buying power and market knowledge to negotiate better terms. Building a relationship with suppliers can also lead to favorable pricing adjustments.
-
Consider Total Cost of Ownership (TCO): Evaluate not just the purchase price, but also the long-term costs associated with maintenance, warranty, and potential returns. This holistic view can help in making better purchasing decisions.
-
Be Aware of Pricing Nuances: Different regions have unique pricing structures. For instance, buyers in Europe may encounter higher labor costs, while South American manufacturers might offer more competitive rates due to lower overhead. Understanding these nuances can aid in strategic sourcing decisions.
-
Stay Informed about Market Trends: Keep abreast of industry trends that may affect material costs or labor availability. This knowledge can give buyers a competitive edge in negotiations.
Disclaimer on Indicative Prices
It is crucial for buyers to recognize that prices can vary widely based on the aforementioned factors, and any provided figures should be seen as indicative rather than definitive. Engaging directly with manufacturers for tailored quotes is advisable to obtain accurate pricing aligned with specific requirements.
Alternatives Analysis: Comparing kitchen table manufacturer With Other Solutions
Exploring Alternatives to Kitchen Table Manufacturing Solutions
In the realm of kitchen table manufacturing, various solutions exist that cater to diverse business needs. As international B2B buyers, especially those from Africa, South America, the Middle East, and Europe, understanding these alternatives can help in making informed decisions that align with your operational goals. Here, we compare the traditional kitchen table manufacturing process with two alternative solutions: modular furniture systems and custom 3D printing.
Comparison Aspect | Kitchen Table Manufacturer | Modular Furniture Systems | Custom 3D Printing |
---|---|---|---|
Performance | High durability and quality | Versatile design options | Highly customizable |
Cost | Moderate to high | Varies by design | Potentially high initial cost |
Ease of Implementation | Longer lead times | Quick assembly | Requires technical expertise |
Maintenance | Regular upkeep needed | Low maintenance | Depends on material used |
Best Use Case | Traditional settings | Flexible spaces | Unique, tailored designs |
What are the benefits and drawbacks of Modular Furniture Systems?
Modular furniture systems offer an innovative alternative to traditional kitchen table manufacturing. These systems are designed for quick assembly and disassembly, making them ideal for businesses that require flexibility in their layouts. The versatility in design allows for easy adaptation to various spaces and styles. However, while they can be cost-effective, the overall price can vary based on the complexity of the design. Maintenance is relatively low, as many modular systems are built from durable materials that withstand regular use.
How does Custom 3D Printing compare to traditional kitchen table manufacturing?
Custom 3D printing represents a cutting-edge method for creating kitchen tables and other furniture. This technology allows for high levels of customization, enabling businesses to design unique pieces that fit specific requirements. While the initial setup costs for 3D printing can be significant, it offers the advantage of reduced waste and the ability to produce intricate designs that may be challenging with traditional methods. However, the implementation of 3D printing requires technical expertise and may not be as suitable for large-scale production.
Making the Right Choice: How Can B2B Buyers Decide?
When evaluating which solution to pursue, B2B buyers should consider their specific needs, budget constraints, and operational capabilities. For businesses prioritizing traditional aesthetics and durability, a kitchen table manufacturer may be the best fit. Conversely, if flexibility and modern design are essential, modular furniture systems could provide significant advantages. For those seeking unique, customized solutions and willing to invest in technology, custom 3D printing may be the optimal choice. Ultimately, aligning the selected solution with your business objectives will facilitate better decision-making and enhance operational efficiency.
Essential Technical Properties and Trade Terminology for kitchen table manufacturer
What Are the Essential Technical Properties for Kitchen Table Manufacturing?
When sourcing kitchen tables, international B2B buyers must understand several critical technical properties that affect the product’s quality, durability, and suitability for various markets. Below are key specifications to consider:
1. Material Grade
The material grade defines the quality and characteristics of the raw materials used in manufacturing kitchen tables. Common materials include solid wood, engineered wood, metal, and glass. For instance, hardwoods like oak and maple offer durability and aesthetic appeal, while engineered wood provides cost-effectiveness. Understanding material grades helps buyers select products that meet their quality standards and consumer expectations.
2. Tolerance
Tolerance refers to the allowable deviation from specified dimensions in the manufacturing process. It is crucial in ensuring that kitchen tables fit well in the intended space and function correctly. For example, a tolerance of ±1mm on table dimensions can be acceptable for most residential applications. Buyers should inquire about tolerance levels to avoid issues with assembly and ensure product consistency.
3. Finish Durability
The finish of a kitchen table affects its resistance to scratches, stains, and moisture. Common finishes include lacquer, varnish, and oil. A durable finish not only enhances the visual appeal but also prolongs the product’s lifespan. Buyers must assess the type of finish used and its suitability for their target market, especially in regions with varying humidity levels.
4. Weight Capacity
Understanding the weight capacity of kitchen tables is essential for ensuring they can support the intended use, whether for dining, homework, or other activities. Tables designed for commercial use may require higher weight capacities than residential ones. Buyers should request this specification to ensure safety and functionality.
5. Stability and Structural Integrity
Stability refers to how well a kitchen table maintains its shape and does not wobble during use. Structural integrity involves the strength of the joints and overall construction. Buyers should look for tables with reinforced joints and stable designs, especially for high-traffic environments.
What Are Common Trade Terms in the Kitchen Table Manufacturing Industry?
Familiarity with industry jargon is vital for effective communication with manufacturers and suppliers. Here are some essential trade terms:
1. OEM (Original Equipment Manufacturer)
OEM refers to a company that produces parts or equipment that may be marketed by another manufacturer. In the kitchen table industry, buyers might work with OEMs to customize designs or incorporate brand-specific features. Understanding OEM relationships helps buyers ensure they receive quality products that align with their brand vision.
2. MOQ (Minimum Order Quantity)
MOQ is the smallest number of units a supplier is willing to sell. This term is critical for budget planning and inventory management. Buyers should negotiate MOQs that align with their business needs while ensuring they can maintain a diverse product range.
3. RFQ (Request for Quotation)
An RFQ is a formal process where buyers request price quotes from suppliers for specific products. It is essential for comparing costs and terms across different manufacturers. Crafting a clear RFQ can lead to better pricing and terms, ultimately benefiting the buyer’s bottom line.
4. Incoterms (International Commercial Terms)
Incoterms are standardized trade terms that define the responsibilities of buyers and sellers in international transactions. Understanding Incoterms, such as FOB (Free on Board) or CIF (Cost, Insurance, and Freight), helps buyers clarify shipping costs and responsibilities, reducing the risk of misunderstandings during the procurement process.
5. Lead Time
Lead time refers to the period between placing an order and receiving the goods. This is particularly important for kitchen tables, as trends can change rapidly. Buyers should inquire about lead times to ensure they can meet market demands and avoid stockouts.
By grasping these technical properties and trade terms, international B2B buyers can make informed decisions when sourcing kitchen tables, ultimately leading to successful procurement strategies and enhanced market competitiveness.
Navigating Market Dynamics and Sourcing Trends in the kitchen table manufacturer Sector
What Are the Current Market Dynamics and Sourcing Trends in the Kitchen Table Manufacturing Sector?
The global kitchen table manufacturing sector is currently influenced by several dynamic factors that international B2B buyers must understand. A surge in demand for multifunctional and customizable furniture is reshaping product offerings. This trend is particularly pronounced in emerging markets across Africa and South America, where consumers are increasingly seeking versatile solutions for smaller living spaces. Additionally, the growth of e-commerce platforms has facilitated direct sourcing from manufacturers, enabling buyers to access a broader range of products without geographical limitations.
Technological advancements are also playing a crucial role. Innovations such as augmented reality (AR) for virtual showrooms and artificial intelligence (AI) for personalized marketing are transforming how buyers interact with manufacturers. Furthermore, the rise of Industry 4.0 has led to increased automation in production processes, resulting in faster turnaround times and enhanced quality control. For buyers in Europe and the Middle East, understanding these trends can facilitate better sourcing decisions and partnerships with manufacturers who are leveraging these technologies.
How Is Sustainability Shaping the Kitchen Table Manufacturing Sector?
Sustainability is becoming a non-negotiable element in the kitchen table manufacturing sector. The environmental impact of production processes and materials used is under increasing scrutiny from consumers and regulatory bodies alike. International B2B buyers are now prioritizing suppliers that demonstrate a commitment to sustainability. This includes sourcing from manufacturers that utilize eco-friendly materials, such as reclaimed wood and non-toxic finishes, which not only mitigate environmental harm but also appeal to a growing demographic of environmentally conscious consumers.
Ethical sourcing practices are also gaining traction, with buyers keen to ensure that their suppliers uphold fair labor standards and promote transparency throughout their supply chains. Certifications such as Forest Stewardship Council (FSC) for wood products and ISO certifications for sustainable practices can serve as indicators of a manufacturer’s commitment to ethical sourcing. By prioritizing suppliers that adhere to these standards, B2B buyers can align their purchasing decisions with the values of sustainability and corporate responsibility, thereby enhancing their brand reputation and consumer loyalty.
How Has the Kitchen Table Manufacturing Sector Evolved Over Time?
The kitchen table manufacturing sector has undergone significant evolution over the decades. Initially dominated by traditional craftsmanship, the industry has shifted towards mass production, driven by globalization and technological advancements. This transition allowed for more affordable pricing but often at the expense of customization and quality.
In recent years, however, there has been a resurgence of interest in artisanal and bespoke furniture, influenced by consumer preferences for unique, high-quality products. This evolution reflects broader market trends, where personalization and sustainability are increasingly valued, offering B2B buyers an opportunity to tap into niche markets. By understanding this historical context, buyers can better navigate current market trends and make informed sourcing decisions that align with consumer demands.
Frequently Asked Questions (FAQs) for B2B Buyers of kitchen table manufacturer
-
How do I choose the right kitchen table manufacturer for my business?
Choosing the right kitchen table manufacturer involves assessing several factors. Start by researching potential manufacturers’ reputations and customer reviews. Verify their production capabilities, materials used, and design flexibility. Consider their location for logistical advantages and potential tariffs. Additionally, request samples to evaluate the quality of craftsmanship. Establish communication to gauge responsiveness and support during the sourcing process. Lastly, ensure they comply with international standards and regulations relevant to your target market. -
What are the common payment terms with kitchen table manufacturers?
Payment terms can vary significantly among kitchen table manufacturers. Common arrangements include a 30% upfront deposit with the balance paid upon shipment or delivery. Some manufacturers may offer payment through letters of credit, which can provide additional security for both parties. It’s crucial to clarify payment methods, currency, and any potential fees upfront. Additionally, consider negotiating terms based on your order size or frequency to secure more favorable conditions. -
What is the minimum order quantity (MOQ) for kitchen tables?
The minimum order quantity (MOQ) for kitchen tables typically ranges from 50 to 500 units, depending on the manufacturer and the complexity of the design. Smaller manufacturers might accommodate lower MOQs, while larger factories may have stricter requirements. Always inquire about flexibility in MOQs, especially if you are testing new products or entering a new market. Some manufacturers may allow a trial order at a higher price per unit. -
How do I ensure the quality of kitchen tables from international suppliers?
To ensure quality from international suppliers, start by conducting thorough research and vetting potential manufacturers. Request certifications that comply with international standards, such as ISO or CE marking. Establish a quality assurance (QA) process, which may include on-site inspections or third-party quality checks before shipment. Additionally, ask for samples and conduct material tests. Building a good relationship with the manufacturer can also facilitate better quality control throughout the production process. -
What customization options are available when sourcing kitchen tables?
Customization options for kitchen tables can vary widely among manufacturers. Common customizations include size, shape, material, finish, and design elements. Some manufacturers may also offer branding options, such as custom logos or packaging. When discussing customization, be clear about your requirements and ask for design prototypes or mock-ups. Understand any implications on lead times and costs associated with custom orders, as these can impact your overall budget and timeline. -
What logistics considerations should I keep in mind when importing kitchen tables?
Logistics plays a critical role in the successful importation of kitchen tables. Consider the shipping methods available, such as sea freight or air freight, and their associated costs and transit times. Verify the manufacturer’s ability to handle packaging that ensures safe transport. Be aware of customs regulations in your country and ensure all necessary documentation is in order to avoid delays. Additionally, plan for warehousing and distribution once the products arrive to manage inventory effectively. -
How can I effectively communicate with kitchen table manufacturers in different countries?
Effective communication with manufacturers from different countries requires understanding cultural differences and language barriers. Utilize clear and concise language in your correspondence and consider using translation tools if necessary. Establish regular communication channels, such as email, video calls, or instant messaging, to facilitate discussions. Be specific about your expectations, timelines, and feedback to minimize misunderstandings. Building a rapport with your manufacturer can also enhance collaboration and responsiveness. -
What are the potential risks of sourcing kitchen tables internationally, and how can I mitigate them?
Sourcing kitchen tables internationally carries risks such as quality discrepancies, shipping delays, and regulatory compliance issues. To mitigate these risks, conduct thorough due diligence on potential suppliers, including background checks and customer references. Consider engaging a third-party inspection service to verify product quality before shipment. Establish clear contracts that outline terms, conditions, and penalties for non-compliance. Lastly, maintain open lines of communication throughout the process to address any issues promptly.
Important Disclaimer & Terms of Use
⚠️ Important Disclaimer
The information provided in this guide, including content regarding manufacturers, technical specifications, and market analysis, is for informational and educational purposes only. It does not constitute professional procurement advice, financial advice, or legal advice.
While we have made every effort to ensure the accuracy and timeliness of the information, we are not responsible for any errors, omissions, or outdated information. Market conditions, company details, and technical standards are subject to change.
B2B buyers must conduct their own independent and thorough due diligence before making any purchasing decisions. This includes contacting suppliers directly, verifying certifications, requesting samples, and seeking professional consultation. The risk of relying on any information in this guide is borne solely by the reader.
Strategic Sourcing Conclusion and Outlook for kitchen table manufacturer
In today’s competitive landscape, strategic sourcing is more critical than ever for kitchen table manufacturers aiming to thrive in the global market. By focusing on key factors such as supplier relationships, cost efficiency, and sustainable practices, businesses can enhance their operational effectiveness and product quality. International B2B buyers, particularly from Africa, South America, the Middle East, and Europe, must prioritize these elements to ensure they are sourcing from the most reliable and innovative manufacturers.
How can international buyers leverage strategic sourcing for better procurement? By establishing clear criteria for evaluating potential suppliers, including their production capabilities, compliance with international standards, and commitment to sustainability, buyers can make informed decisions that align with their business goals. Engaging in continuous market research and maintaining open communication with suppliers will also facilitate adaptability in a dynamic market.
Looking ahead, the kitchen table manufacturing sector is poised for growth, driven by evolving consumer preferences and technological advancements. Now is the time for international buyers to take proactive steps toward optimizing their sourcing strategies. Embrace these insights, forge strong partnerships, and position your business for success in the ever-evolving global marketplace.