Discover Top Kitchen Tool Manufacturers: Your Ultimate Guide (2025)
Introduction: Navigating the Global Market for kitchen tool manufacturer
In the competitive landscape of international trade, sourcing high-quality kitchen tools can be a daunting task for B2B buyers. Particularly in regions like Africa, South America, the Middle East, and Europe, the challenge lies not only in identifying reliable kitchen tool manufacturers but also in navigating diverse market demands, regulatory standards, and supplier capabilities. This guide aims to illuminate the complexities of sourcing kitchen tools, equipping buyers with the necessary insights to make informed purchasing decisions.
Throughout this comprehensive guide, we will explore various types of kitchen tools, their applications in both commercial and domestic settings, and the critical factors to consider when vetting potential suppliers. Understanding the nuances of pricing structures, quality standards, and logistical considerations will empower buyers to negotiate effectively and secure favorable terms.
Additionally, we will delve into regional market trends and consumer preferences that can influence sourcing decisions, ensuring that buyers are well-prepared to meet the expectations of their target markets. By harnessing the information presented in this guide, international B2B buyers will gain a strategic advantage, allowing them to confidently navigate the global kitchen tool market and select manufacturers that align with their business goals.
Understanding kitchen tool manufacturer Types and Variations
Type Name | Key Distinguishing Features | Primary B2B Applications | Brief Pros & Cons for Buyers |
---|---|---|---|
Mass Production Manufacturers | High-volume production, standardized designs | Restaurants, catering businesses | Pros: Cost-effective, quick delivery. Cons: Less customization options. |
Custom Kitchen Tool Makers | Tailored designs, small batch production | Specialty restaurants, gourmet shops | Pros: Unique products, high quality. Cons: Higher costs, longer lead times. |
Eco-Friendly Kitchen Tool Producers | Sustainable materials, environmentally conscious practices | Health-focused businesses, eco-friendly retailers | Pros: Appeals to eco-conscious consumers. Cons: Potentially higher prices. |
Specialty Kitchen Tool Suppliers | Focus on niche markets (e.g., baking, grilling) | Culinary schools, professional chefs | Pros: Expertise in niche areas, high-quality tools. Cons: Limited product range. |
Import/Export Kitchen Tool Traders | Global sourcing, diverse product offerings | International retailers, wholesalers | Pros: Wide variety, competitive pricing. Cons: Potential quality control issues. |
What Are the Key Characteristics of Mass Production Manufacturers?
Mass production manufacturers specialize in creating large quantities of standardized kitchen tools. These manufacturers are ideal for businesses looking to equip multiple locations or manage high-volume sales. The key characteristics include streamlined production processes and efficient supply chains, which allow for lower prices per unit. However, buyers should consider that the trade-off often comes with limited customization options, which may not meet the specific needs of niche markets.
How Do Custom Kitchen Tool Makers Differ in Their Offerings?
Custom kitchen tool makers focus on producing tailored solutions, often in small batches. This type of manufacturer is particularly suitable for specialty restaurants or gourmet shops that require unique tools to differentiate their offerings. The key characteristics include a high degree of craftsmanship and the ability to work closely with clients to develop bespoke products. However, buyers should be prepared for higher costs and longer lead times compared to mass-produced options, which can impact inventory management.
Why Choose Eco-Friendly Kitchen Tool Producers?
Eco-friendly kitchen tool producers prioritize sustainability by using environmentally friendly materials and practices. These manufacturers appeal to health-focused businesses and eco-conscious retailers, aligning with the growing consumer demand for sustainable products. The key characteristics include innovative designs that minimize environmental impact. While these tools can often command higher prices, they offer a competitive advantage in markets where sustainability is a key purchasing factor.
What Are the Advantages of Specialty Kitchen Tool Suppliers?
Specialty kitchen tool suppliers focus on niche markets such as baking, grilling, or gourmet cooking. They provide high-quality tools that cater specifically to the needs of culinary schools, professional chefs, and passionate home cooks. The key characteristics include a deep understanding of specific culinary techniques and the ability to offer expert advice. However, buyers should be aware that the limited product range may not meet all their kitchen tool needs, making it essential to evaluate their specific requirements before purchasing.
How Do Import/Export Kitchen Tool Traders Operate?
Import/export kitchen tool traders specialize in sourcing products from various global manufacturers, offering a diverse range of kitchen tools at competitive prices. This type of manufacturer is ideal for international retailers and wholesalers looking to expand their product offerings. The key characteristics include a broad selection of tools and the ability to leverage global supply chains. However, buyers should be cautious about potential quality control issues that can arise when dealing with multiple suppliers, emphasizing the importance of thorough vetting processes.
Related Video: ESSENTIAL BAKING EQUIPMENT & THEIR USES | necessary baking equipment for your kitchen
Key Industrial Applications of kitchen tool manufacturer
Industry/Sector | Specific Application of Kitchen Tool Manufacturer | Value/Benefit for the Business | Key Sourcing Considerations for this Application |
---|---|---|---|
Food Service | Commercial Kitchen Equipment and Utensils | Enhanced efficiency and consistency in food preparation | Quality certifications, compliance with health standards |
Hospitality | Customized Kitchen Tools for Restaurants | Improved customer satisfaction through better service | Customization options, delivery timelines, bulk pricing |
Food Processing | Specialized Food Preparation Tools | Increased production speed and reduced labor costs | Durability, ease of cleaning, compatibility with machinery |
Retail | Retail Display and Kitchen Tools for Consumers | Increased sales through attractive product displays | Packaging options, branding capabilities, cost-effectiveness |
Catering Services | Portable Kitchen Tools for Events | Flexibility and mobility for on-site food preparation | Portability features, ease of setup, supplier reliability |
How Are Kitchen Tool Manufacturers Used in the Food Service Industry?
In the food service sector, kitchen tool manufacturers provide essential commercial kitchen equipment, such as knives, cutting boards, and cooking utensils. These tools are crucial for maintaining high efficiency and consistency in food preparation. International B2B buyers must prioritize suppliers that offer products meeting specific health and safety standards, particularly in regions like Africa and the Middle East, where regulations may vary. Ensuring that tools are durable and easy to clean can significantly reduce operational downtime and enhance overall kitchen productivity.
What Role Do Customized Kitchen Tools Play in the Hospitality Sector?
The hospitality industry relies heavily on customized kitchen tools to enhance the dining experience. Restaurants often seek unique utensils and equipment tailored to their culinary styles, which can lead to improved customer satisfaction. For B2B buyers in South America and Europe, sourcing from manufacturers that offer customization options is vital. Considerations such as lead times for custom orders and bulk pricing can impact budgeting and operational efficiency. Additionally, ensuring that these tools align with the restaurant’s branding can further enhance the customer experience.
How Do Specialized Food Preparation Tools Benefit Food Processing?
In food processing, specialized kitchen tools are integral to enhancing production speed and reducing labor costs. Tools such as industrial mixers, slicers, and food processors streamline operations, allowing businesses to meet high demand efficiently. For international buyers, particularly in developing markets, sourcing durable and easy-to-clean equipment is essential to maintain hygiene standards and minimize downtime. Compatibility with existing machinery is another critical factor, as it can influence overall workflow and productivity.
Why Are Retail Displays and Kitchen Tools Important for Retailers?
Retailers benefit from kitchen tool manufacturers by acquiring both practical tools and visually appealing displays to attract consumers. The right kitchen tools can significantly increase sales, particularly when paired with effective branding and packaging. B2B buyers in regions like Europe should focus on suppliers that provide comprehensive solutions, including marketing support and attractive packaging options. Cost-effectiveness is also a key consideration, as retailers often operate on tight margins and need to maximize return on investment.
How Do Portable Kitchen Tools Enhance Catering Services?
Catering services require portable kitchen tools that enable flexibility and mobility for on-site food preparation. These tools must be lightweight yet durable, allowing caterers to transport them easily to various locations. For international B2B buyers in the Middle East and Africa, sourcing reliable suppliers that offer high-quality, portable solutions is crucial for maintaining service quality. Key considerations include the ease of setup and breakdown of tools, as well as the supplier’s reliability in meeting delivery deadlines, which can directly affect event success.
Related Video: Types of Kitchen Knives and Their Uses
3 Common User Pain Points for ‘kitchen tool manufacturer’ & Their Solutions
Scenario 1: Sourcing High-Quality Kitchen Tools at Competitive Prices
The Problem: Many B2B buyers, particularly those in regions like Africa and South America, often struggle with finding reliable kitchen tool manufacturers that offer high-quality products at competitive prices. This challenge is exacerbated by the influx of low-quality imports that can damage a business’s reputation. Buyers may encounter difficulties in identifying suppliers who adhere to stringent quality standards while also being cost-effective, which can impact their profitability and customer satisfaction.
The Solution: To navigate this challenge, buyers should conduct thorough market research and supplier evaluations. Utilize platforms like Alibaba or Global Sources to compare manufacturers based on reviews and certifications. Establish clear quality criteria and ask for product samples before making bulk orders. Additionally, consider forming partnerships with local representatives who understand the market dynamics and can negotiate better pricing. Leveraging group purchasing agreements with other businesses in your network can also help in obtaining better rates, ensuring quality without compromising on costs.
Scenario 2: Managing Supply Chain Disruptions
The Problem: Supply chain disruptions are a common pain point for B2B buyers in the kitchen tool manufacturing sector, particularly in the Middle East and Europe. Factors such as political instability, shipping delays, and fluctuating tariffs can cause significant interruptions, resulting in inventory shortages and lost sales opportunities. Buyers often find themselves in a position where they cannot fulfill customer orders due to a lack of reliable supply sources.
The Solution: To mitigate supply chain risks, buyers should diversify their supplier base by identifying multiple manufacturers across different regions. This strategy not only reduces dependency on a single supplier but also allows for flexibility in sourcing materials during disruptions. Implementing a robust inventory management system can also help track stock levels and forecast demand more accurately. Building strong relationships with suppliers through regular communication can enhance transparency and lead to quicker resolutions during disruptions. Additionally, consider exploring local manufacturing options to reduce shipping times and costs.
Scenario 3: Ensuring Compliance with Safety Standards
The Problem: International B2B buyers, especially those in Europe, face the challenge of ensuring that kitchen tools comply with stringent safety and regulatory standards. Non-compliance can lead to legal issues, product recalls, and damage to brand reputation. Buyers may feel overwhelmed by the complexity of navigating these regulations, particularly when sourcing from manufacturers in regions with varying compliance levels.
The Solution: To address compliance concerns, buyers should prioritize working with manufacturers who have a proven track record of adhering to international safety standards, such as ISO and FDA regulations. Request documentation that proves compliance, such as safety certifications and test reports. Additionally, engaging third-party quality assurance firms to conduct audits on potential suppliers can provide an extra layer of security. Investing in training for procurement teams about relevant regulations can also enhance awareness and ensure informed decision-making when selecting kitchen tool manufacturers. Finally, consider incorporating compliance checks into the procurement process to ensure ongoing adherence to safety standards.
Strategic Material Selection Guide for kitchen tool manufacturer
When selecting materials for kitchen tools, manufacturers must consider various factors that influence product performance, compliance, and market acceptance. Below is an analysis of four common materials used in kitchen tool manufacturing, focusing on their properties, pros and cons, and specific considerations for international B2B buyers, particularly from Africa, South America, the Middle East, and Europe.
What Are the Key Properties of Stainless Steel for Kitchen Tools?
Stainless steel is a popular choice due to its excellent corrosion resistance and durability. It can withstand high temperatures, making it suitable for tools used in cooking and food preparation. Stainless steel also has a smooth surface that prevents food from sticking, which is essential for hygiene and ease of cleaning.
Pros & Cons: The primary advantage of stainless steel is its longevity; it does not rust or stain easily, ensuring a longer product life. However, it can be more expensive than other materials, which may impact the overall cost of the kitchen tools. Manufacturing complexity can be moderate, depending on the design and finishing processes.
Impact on Application: Stainless steel is compatible with a wide range of food media, including acidic and alkaline substances, making it versatile for various kitchen applications.
Considerations for International Buyers: Compliance with food safety standards such as ASTM and DIN is crucial. Buyers from regions like Europe may prefer products that meet stringent EU regulations, while those in Africa and South America may prioritize cost-effectiveness without compromising quality.
How Does Plastic Compare as a Material for Kitchen Tools?
Plastic is widely used in kitchen tools due to its lightweight nature and versatility. It can be molded into various shapes and is available in a range of colors and finishes. Certain plastics, such as polypropylene, are resistant to heat and chemicals, making them suitable for kitchen environments.
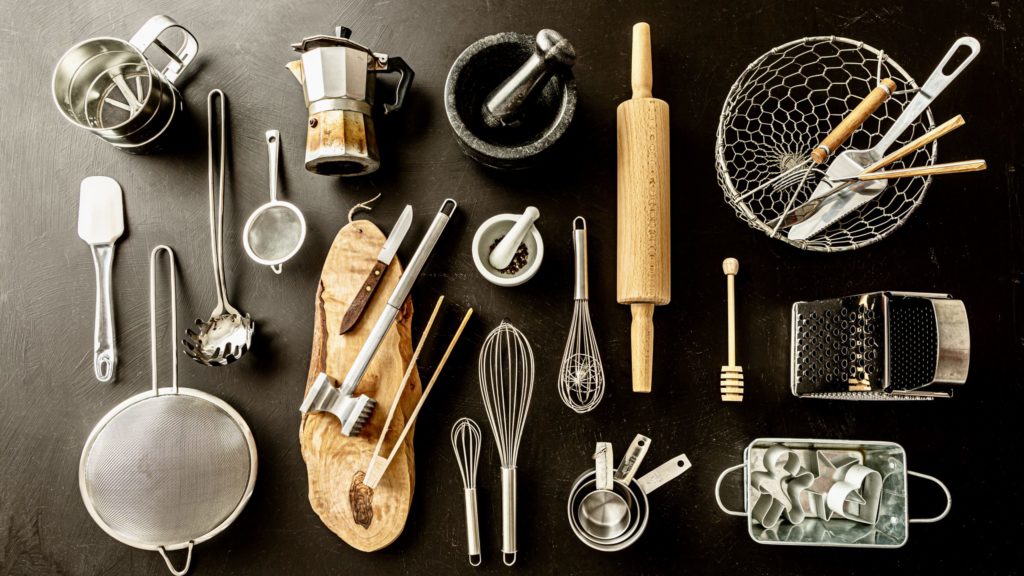
A stock image related to kitchen tool manufacturer.
Pros & Cons: The main advantage of plastic is its low cost and ease of manufacturing, allowing for mass production. However, it may not be as durable as metals and can warp or degrade over time, especially under high temperatures.
Impact on Application: Plastic tools are generally suitable for non-stick cookware, as they prevent scratching. However, they may not be suitable for high-temperature applications, which could limit their use in some kitchens.
Considerations for International Buyers: Buyers should ensure that the plastic used is BPA-free and complies with local food safety regulations. In regions like the Middle East, where high temperatures can affect plastic integrity, selecting heat-resistant materials is essential.
What Are the Advantages of Silicone in Kitchen Tool Manufacturing?
Silicone is increasingly popular for kitchen tools due to its flexibility, heat resistance, and non-stick properties. It can withstand temperatures ranging from -40°C to 230°C, making it ideal for baking and cooking applications.
Pros & Cons: Silicone’s key advantage is its ability to be used in both the oven and freezer without losing integrity. However, its manufacturing cost can be higher compared to plastic, which may deter some budget-conscious buyers.
Impact on Application: Silicone is compatible with most food types and is non-reactive, making it safe for cooking and baking. Its flexibility allows for easy release of baked goods, enhancing usability.
Considerations for International Buyers: Compliance with FDA and EU food safety standards is vital. Buyers in Europe may have specific preferences for silicone that meets stringent regulations, while those in South America may focus on affordability and availability.
What Role Does Wood Play in Kitchen Tool Manufacturing?
Wood has a traditional appeal and is often used for utensils and cutting boards. It is naturally antimicrobial and provides a warm aesthetic that many consumers prefer.
Pros & Cons: The primary advantage of wood is its durability and resistance to scratching, making it suitable for use with non-stick surfaces. However, wood can be more challenging to maintain, requiring regular oiling to prevent drying and cracking.
Impact on Application: Wood is compatible with most food types and does not react with acids, making it ideal for various culinary tasks. However, it is not suitable for high-temperature applications like stovetop cooking.
Considerations for International Buyers: Buyers should consider the sourcing of wood materials, ensuring they comply with sustainability practices. In Europe, for instance, there is a strong emphasis on eco-friendly products, while buyers in Africa may prioritize local sourcing.
Summary Table of Material Selection for Kitchen Tool Manufacturing
Material | Typical Use Case for kitchen tool manufacturer | Key Advantage | Key Disadvantage/Limitation | Relative Cost (Low/Med/High) |
---|---|---|---|---|
Stainless Steel | Cookware, utensils, knives | Excellent durability and hygiene | Higher cost compared to plastics | High |
Plastic | Mixing bowls, spatulas, measuring cups | Low manufacturing cost | Less durable, can warp under heat | Low |
Silicone | Baking mats, spatulas, molds | Heat resistant and flexible | Higher cost than plastic | Medium |
Wood | Utensils, cutting boards | Naturally antimicrobial | Requires maintenance, can crack | Medium |
This strategic material selection guide provides essential insights for international B2B buyers, helping them make informed decisions based on performance, compliance, and market preferences.
In-depth Look: Manufacturing Processes and Quality Assurance for kitchen tool manufacturer
What Are the Key Stages in the Manufacturing Process of Kitchen Tools?
The manufacturing process for kitchen tools is a multi-stage operation that requires precision and attention to detail. This process typically involves four main stages: material preparation, forming, assembly, and finishing.
-
Material Preparation: This initial stage involves sourcing high-quality raw materials, such as stainless steel, silicone, or wood, depending on the type of kitchen tool being produced. Suppliers should be vetted for their material quality and sustainability practices, as these factors directly affect the final product’s durability and safety. For international buyers, especially from Africa and South America, it’s crucial to ensure that suppliers can provide certification for raw materials that comply with local and international regulations.
-
Forming: In this stage, the prepared materials undergo various shaping processes. Common techniques include stamping, molding, and machining. For instance, a stainless steel spatula might be stamped from a sheet of metal, while silicone utensils are typically produced through injection molding. Buyers should inquire about the forming techniques used by suppliers, as advanced methods can enhance product consistency and reduce waste.
-
Assembly: This phase involves putting together the components of the kitchen tools. Depending on the complexity of the product, this could include attaching handles, integrating electronic components, or adding decorative elements. Automation is increasingly used in assembly processes to improve efficiency and reduce labor costs. B2B buyers should assess whether the manufacturer utilizes automated systems, as this often correlates with higher precision and lower defect rates.
-
Finishing: The final stage includes surface treatments, coatings, and packaging. Techniques such as polishing, anodizing, or applying non-stick coatings are common. For buyers, understanding the finishing processes is essential, as they can significantly impact the tool’s performance and longevity. It’s advisable to request samples to evaluate the finish quality before placing larger orders.
How Is Quality Assurance Implemented in Kitchen Tool Manufacturing?
Quality assurance (QA) is a critical aspect of the manufacturing process that ensures products meet specific standards and customer expectations. Kitchen tool manufacturers often adhere to international standards such as ISO 9001, which outlines requirements for a quality management system. This standard is particularly relevant for international buyers, as it signifies a commitment to quality and continuous improvement.
What International and Industry-Specific Standards Should B2B Buyers Know?
B2B buyers should be familiar with various standards that pertain to kitchen tools:
- ISO 9001: Focuses on quality management and customer satisfaction.
- CE Marking: Required for products sold in the European Economic Area, indicating compliance with health, safety, and environmental protection standards.
- API (American Petroleum Institute): While primarily for oil and gas, some kitchen tools may require specific API certifications for components used in food-grade applications.
Understanding these standards can help buyers ensure that their suppliers are compliant, thereby reducing the risk of product recalls or safety issues.
What Are the Key Quality Control Checkpoints in Manufacturing?
Quality control (QC) checkpoints are integral to maintaining product quality throughout the manufacturing process. Common QC checkpoints include:
-
Incoming Quality Control (IQC): This initial inspection verifies that raw materials meet specified standards before they enter the production line. Suppliers should provide documentation of their IQC processes, including material certifications and test results.
-
In-Process Quality Control (IPQC): Conducted at various stages during production, IPQC ensures that the manufacturing processes are correctly followed and that any defects are caught early. This can include monitoring temperature, pressure, and other variables during forming and assembly.
-
Final Quality Control (FQC): At this stage, the finished products undergo thorough inspection and testing to ensure they meet all quality standards before shipping. Common tests may include durability testing, safety evaluations, and performance assessments.
What Testing Methods Are Commonly Used in Kitchen Tool Manufacturing?
B2B buyers should be aware of the common testing methods employed during the QC process:
- Mechanical Testing: Assesses the strength and durability of materials.
- Chemical Testing: Ensures that materials are food-safe and free from harmful substances.
- Functional Testing: Evaluates whether the kitchen tools perform as intended under various conditions.
By understanding these testing methods, buyers can better assess the reliability of their suppliers’ QC processes.
How Can B2B Buyers Verify Supplier Quality Control Practices?
Verifying a supplier’s QC practices is essential for ensuring product quality. Here are several actionable steps B2B buyers can take:
-
Conduct Supplier Audits: Regular audits allow buyers to assess the manufacturing processes, quality control systems, and compliance with relevant standards. This can be done by internal teams or through third-party inspection services.
-
Request Quality Reports: Suppliers should provide detailed QC reports that outline their processes, test results, and any corrective actions taken in case of defects.
-
Third-Party Inspections: Engaging third-party inspection agencies can provide an unbiased evaluation of a supplier’s QC practices. This is particularly useful for international buyers who may not have the capability to conduct on-site audits.
What Are the Quality Control Nuances for International B2B Buyers?
For international B2B buyers, particularly those from regions like Africa, South America, the Middle East, and Europe, there are several nuances to consider:
-
Local Regulations: Understanding local regulations and standards is crucial. For example, food safety standards can vary significantly between regions, impacting the types of materials and processes used.
-
Cultural Differences: Communication and expectations around quality can differ by region. Establishing clear guidelines and maintaining open lines of communication is essential to avoid misunderstandings.
-
Logistical Challenges: Consider the implications of international shipping on product quality. Factors such as temperature fluctuations and handling can affect the integrity of kitchen tools during transport.
By being aware of these nuances, B2B buyers can make more informed decisions and establish stronger partnerships with their kitchen tool manufacturers.
Practical Sourcing Guide: A Step-by-Step Checklist for ‘kitchen tool manufacturer’
In the competitive landscape of kitchen tool manufacturing, sourcing the right supplier is critical for success. This step-by-step guide provides a practical checklist for international B2B buyers looking to procure kitchen tools efficiently. By following these steps, you can streamline your sourcing process, mitigate risks, and ensure quality in your purchases.
Step 1: Define Your Technical Specifications
Before engaging with suppliers, it’s essential to outline your technical requirements clearly. This includes dimensions, materials, and functionality of the kitchen tools you need. A well-defined specification helps prevent misunderstandings and ensures that suppliers can meet your expectations effectively.
- Considerations:
- What materials are essential for your products (e.g., stainless steel, silicone)?
- Are there specific industry standards or certifications that your products must meet?
Step 2: Conduct Market Research
Understanding the current market trends and supplier landscape is vital. This step involves researching potential suppliers from different regions, including Africa, South America, the Middle East, and Europe.
- Key Actions:
- Analyze competitors’ suppliers and identify leading manufacturers.
- Use online platforms and trade shows to gather insights on supplier offerings and innovations.
Step 3: Evaluate Potential Suppliers
Before committing, it’s crucial to vet suppliers thoroughly. Request company profiles, case studies, and references from buyers in a similar industry or region. Don’t just rely on their website.
- Important Aspects:
- Check for customer reviews and testimonials to gauge reliability.
- Ask for references to understand their experience with similar orders.
Step 4: Verify Supplier Certifications
Ensure that the suppliers hold relevant certifications and comply with international quality standards. This is particularly important for kitchen tools that must adhere to health and safety regulations.
- Types of Certifications to Look For:
- ISO 9001 for quality management.
- FDA or EU certifications for food safety, depending on your target market.
Step 5: Request Samples and Conduct Quality Checks
Before placing a large order, request samples to evaluate the quality of the kitchen tools. This step is crucial for assessing the supplier’s manufacturing capabilities and ensuring that the products meet your specifications.
- Quality Assurance:
- Check for durability, design, and functionality.
- Conduct tests to ensure compliance with safety standards.
Step 6: Negotiate Terms and Conditions
Once you have identified a suitable supplier, enter negotiations regarding pricing, payment terms, and delivery schedules. Clear communication during this phase can prevent future disputes and misunderstandings.
- Negotiation Tips:
- Be transparent about your budget and expectations.
- Discuss potential discounts for bulk orders or long-term contracts.
Step 7: Establish a Logistics Plan
After finalizing the supplier, develop a logistics plan that outlines shipping, handling, and delivery processes. This ensures a smooth transition from production to your warehouse or distribution center.
- Logistics Considerations:
- Determine the most cost-effective shipping methods.
- Ensure compliance with customs regulations in your importing country.
By following this structured sourcing checklist, B2B buyers can make informed decisions when procuring kitchen tools, ultimately leading to successful partnerships and high-quality products.
Comprehensive Cost and Pricing Analysis for kitchen tool manufacturer Sourcing
What Are the Key Cost Components in Kitchen Tool Manufacturing?
When sourcing kitchen tools, understanding the cost structure is crucial for effective budgeting and negotiation. The primary cost components include:
-
Materials: The choice of raw materials significantly impacts cost. Stainless steel, silicone, and bamboo are popular but vary in price. Sustainable or specialty materials may incur higher costs but can attract eco-conscious consumers.
-
Labor: Labor costs can fluctuate based on the manufacturing location. Regions with lower labor costs, such as parts of Asia, may offer competitive pricing but consider the trade-offs in quality and reliability.
-
Manufacturing Overhead: This encompasses indirect costs such as utilities, rent, and administrative expenses. High overhead can indicate inefficiencies, so assessing this in your supplier’s pricing is vital.
-
Tooling: Initial tooling costs for custom designs can be substantial. Buyers should inquire about these costs upfront, especially for unique or specialized kitchen tools.
-
Quality Control (QC): Implementing rigorous QC processes ensures product reliability and compliance with international standards. While this may increase upfront costs, it can reduce returns and enhance brand reputation in the long run.
-
Logistics: Shipping and handling can significantly affect total costs, especially for international buyers. Consider the distance, mode of transportation, and any potential tariffs or customs fees.
-
Margin: Supplier margins can vary widely. Understanding the typical margin in your market will help assess whether a quote is competitive or inflated.
How Do Price Influencers Affect Kitchen Tool Sourcing?
Several factors influence the pricing of kitchen tools, and international buyers should be aware of these:
-
Volume/MOQ (Minimum Order Quantity): Larger orders often attract discounts. It’s essential to assess your demand forecast to negotiate effectively.
-
Specifications and Customization: Customized designs or specific material requirements can lead to higher costs. Ensure that the specifications align with your market needs to justify these expenses.
-
Quality and Certifications: Products that meet international quality standards or have certifications (like FDA or CE) may come at a premium. However, these certifications can significantly enhance marketability.
-
Supplier Factors: The supplier’s reputation, production capacity, and reliability can influence pricing. Established manufacturers may charge more for their proven quality and service.
-
Incoterms: Understanding Incoterms (International Commercial Terms) is crucial for calculating total costs, including shipping, insurance, and other logistics. Different terms can lead to varying responsibilities and costs for buyers.
What Buyer Tips Can Help Optimize Kitchen Tool Sourcing Costs?
For international buyers, particularly from regions like Africa, South America, the Middle East, and Europe, here are actionable tips to optimize sourcing costs:
-
Negotiate Effectively: Leverage your purchasing power and market knowledge. Don’t hesitate to negotiate prices, especially when dealing with large quantities or long-term contracts.
-
Focus on Cost-Efficiency: Evaluate the Total Cost of Ownership (TCO) rather than just the purchase price. Consider factors like durability, maintenance, and potential warranty claims.
-
Understand Pricing Nuances: Be aware of regional pricing differences and how they affect your sourcing strategy. For example, kitchen tools sourced from Asia may be cheaper, but consider shipping times and potential customs delays.
-
Conduct Supplier Audits: Regularly assess supplier performance in terms of quality, delivery times, and compliance with agreements. This helps in maintaining a reliable supply chain and avoiding unexpected costs.
-
Stay Informed on Market Trends: Being aware of trends in kitchen tool design and consumer preferences can help in making informed sourcing decisions. This can also aid in negotiating better prices based on demand forecasts.
Disclaimer on Indicative Prices
Prices for kitchen tools can vary widely based on the factors discussed above. The insights provided here are meant to serve as a guideline for international B2B buyers. Always conduct thorough research and obtain multiple quotes to ensure competitive pricing tailored to your specific needs.
Alternatives Analysis: Comparing kitchen tool manufacturer With Other Solutions
Understanding the Importance of Alternatives in Kitchen Tool Manufacturing
In the ever-evolving culinary landscape, B2B buyers must consider various solutions when sourcing kitchen tools. While traditional kitchen tool manufacturers offer a wide range of products, alternatives such as custom fabrication services and automated kitchen systems present unique advantages. This analysis aims to provide insights into these options, helping international buyers make informed decisions based on performance, cost, and other critical factors.
Comparison Table of Kitchen Tool Manufacturing Alternatives
Comparison Aspect | Kitchen Tool Manufacturer | Custom Fabrication Services | Automated Kitchen Systems |
---|---|---|---|
Performance | High quality, standardized products | Tailored solutions for specific needs | High efficiency, consistent results |
Cost | Moderate to high, depending on volume | Variable; can be high for low quantities | High initial investment, but cost-effective long-term |
Ease of Implementation | Straightforward, established supply chains | Requires detailed specifications and time | Complex setup; requires skilled personnel |
Maintenance | Regular maintenance needed | Depends on materials used | Requires technical support; can be expensive |
Best Use Case | General kitchen tools for restaurants and hotels | Unique designs or specialized tools | High-volume production environments |
What Are the Pros and Cons of Custom Fabrication Services?
Custom fabrication services allow businesses to create kitchen tools tailored to their specific requirements. The primary advantage of this approach is the ability to design tools that meet unique operational needs, enhancing efficiency and functionality. However, the cost can be prohibitive for small orders, and the lead time for manufacturing may be longer than anticipated. Additionally, buyers must provide precise specifications to ensure the final product meets their expectations.
How Do Automated Kitchen Systems Enhance Efficiency?
Automated kitchen systems represent a significant leap forward in kitchen operations, offering high efficiency and consistent results. These systems can integrate various functions, such as cooking, plating, and cleaning, into a streamlined process that reduces labor costs and increases output. However, the initial investment can be substantial, making it a less viable option for smaller businesses. Additionally, the complexity of setup and the need for skilled personnel to operate and maintain these systems can pose challenges.
Conclusion: How to Choose the Right Solution for Your Kitchen Needs
When selecting a kitchen tool solution, B2B buyers should assess their specific operational needs, budget constraints, and the scalability of the solution. While traditional kitchen tool manufacturers provide reliable options for standard tools, alternatives like custom fabrication and automated systems can offer tailored benefits for unique requirements. By carefully weighing the pros and cons of each option, international buyers from regions such as Africa, South America, the Middle East, and Europe can make strategic decisions that enhance their culinary operations and contribute to long-term success.
Essential Technical Properties and Trade Terminology for kitchen tool manufacturer
What Are the Key Technical Properties for Kitchen Tool Manufacturers?
When sourcing kitchen tools, understanding essential technical properties can significantly impact product quality, durability, and performance. Here are some critical specifications to consider:
1. Material Grade
Material grade refers to the classification of the materials used in manufacturing kitchen tools, such as stainless steel, silicone, or plastic. Each material has unique properties affecting durability, heat resistance, and food safety. For instance, high-grade stainless steel is often preferred for its corrosion resistance and longevity. Buyers should ensure that the material grade meets international standards, particularly for health and safety compliance.
2. Tolerance
Tolerance defines the permissible limit of variation in a physical dimension or property of a kitchen tool. This specification is crucial for ensuring parts fit together correctly, especially in tools that require precision, like knives and measuring instruments. A tight tolerance can enhance functionality and user safety, making it essential for buyers to understand the tolerances required for their specific applications.
3. Finish Quality
Finish quality refers to the surface treatment of kitchen tools, which can impact aesthetics and performance. Common finishes include polished, brushed, or coated surfaces. A high-quality finish can prevent food adhesion, enhance durability, and improve overall hygiene. Buyers should evaluate the finish quality based on how the tools will be used in commercial environments, where visual appeal and hygiene are paramount.
4. Ergonomics
Ergonomics involves the design of kitchen tools to maximize user comfort and efficiency. This includes handle design, weight distribution, and ease of use. For B2B buyers, especially those in hospitality, investing in ergonomically designed tools can improve user satisfaction and reduce fatigue among staff, ultimately enhancing productivity.
5. Heat Resistance
Heat resistance is the ability of a kitchen tool to withstand high temperatures without degrading or losing functionality. This property is especially important for tools used in cooking or baking. Buyers should verify the heat resistance ratings of materials to ensure they meet the demands of their specific culinary applications.
What Are Common Trade Terminology Terms in Kitchen Tool Manufacturing?
Understanding industry jargon is vital for effective communication and negotiation in the B2B landscape. Here are some common trade terms relevant to kitchen tool manufacturers:
1. OEM (Original Equipment Manufacturer)
OEM refers to a company that produces parts or equipment that may be marketed by another manufacturer. In the kitchen tools sector, this often involves manufacturers that create tools designed to be sold under different brand names. B2B buyers can leverage OEM partnerships to enhance product offerings without incurring high development costs.
2. MOQ (Minimum Order Quantity)
MOQ represents the smallest quantity of a product that a supplier is willing to sell. Understanding MOQ is critical for B2B buyers as it affects inventory management and cash flow. Buyers should negotiate MOQs to align with their sales forecasts and operational capacities, ensuring they do not overcommit financially.
3. RFQ (Request for Quotation)
An RFQ is a formal process where buyers request price quotes from suppliers for specific products or services. This process is essential for obtaining competitive pricing and understanding supplier capabilities. B2B buyers should provide detailed specifications in their RFQs to receive accurate and relevant quotes.
4. Incoterms
Incoterms are international commercial terms that define the responsibilities of buyers and sellers in a transaction. They clarify who is responsible for shipping, insurance, and tariffs, which is vital for international B2B transactions. Understanding Incoterms can help buyers mitigate risks and ensure smoother logistics.
5. Lead Time
Lead time is the time taken from placing an order to receiving the goods. This metric is crucial for B2B buyers to plan inventory and operations effectively. Buyers should discuss lead times with suppliers upfront to ensure they align with their production schedules and market demands.
By familiarizing themselves with these technical properties and trade terms, B2B buyers can make informed decisions that enhance their sourcing strategies and improve overall business efficiency in the kitchen tools sector.
Navigating Market Dynamics and Sourcing Trends in the kitchen tool manufacturer Sector
What Are the Key Market Dynamics and Trends Impacting Kitchen Tool Manufacturers?
The kitchen tool manufacturing sector is undergoing significant transformation driven by several global factors. Increasing urbanization in regions like Africa and South America is fueling demand for innovative kitchen solutions that cater to smaller living spaces. Additionally, the rise of e-commerce platforms has made sourcing kitchen tools more accessible for B2B buyers, allowing them to explore a wider array of products from different manufacturers. Notably, the integration of smart technology into kitchen tools is emerging as a game-changer, with smart kitchen devices gaining traction among consumers, thus influencing manufacturers to pivot towards tech-enhanced offerings.
B2B buyers should also be aware of the rising importance of customization and personalization in product offerings. Businesses that can provide tailored solutions are more likely to stand out in a crowded market. Moreover, manufacturers are increasingly adopting lean production techniques to optimize supply chains, reduce waste, and enhance efficiency. This is particularly relevant for buyers in regions like the Middle East, where operational costs can significantly impact profitability.
How Is Sustainability and Ethical Sourcing Reshaping the Kitchen Tool Manufacturing Sector?
Sustainability is no longer a niche concern; it has become a core aspect of the kitchen tool manufacturing industry. B2B buyers are increasingly prioritizing suppliers that demonstrate a commitment to environmentally friendly practices. This includes sourcing materials that are biodegradable or recyclable, thereby minimizing environmental impact. Manufacturers are also adopting sustainable production methods that lower carbon footprints and reduce waste.
Ethical sourcing is equally crucial. Buyers must ensure that their suppliers adhere to fair labor practices and maintain transparency in their supply chains. The demand for ‘green’ certifications, such as FSC (Forest Stewardship Council) for wooden products or certifications for recycled materials, is on the rise. By choosing suppliers who prioritize sustainability and ethics, B2B buyers not only enhance their brand image but also meet the growing expectations of environmentally conscious consumers.
How Has the Kitchen Tool Manufacturing Sector Evolved Over Time?
The kitchen tool manufacturing sector has a rich history that reflects broader technological and social changes. In the early 20th century, kitchen tools were primarily utilitarian, designed for functionality rather than aesthetics. However, the post-World War II era saw a shift towards more innovative designs, influenced by rising consumerism and the advent of modern manufacturing techniques.
The late 20th century brought the introduction of new materials such as plastics and stainless steel, which revolutionized kitchen tool design. Today, manufacturers are not just focused on functionality but also on integrating technology and sustainability into their products. As the market continues to evolve, international B2B buyers must stay abreast of these changes to make informed sourcing decisions that align with both their business needs and consumer expectations.
Frequently Asked Questions (FAQs) for B2B Buyers of kitchen tool manufacturer
-
How do I choose the right kitchen tool manufacturer for my business?
Selecting the right kitchen tool manufacturer involves evaluating several key factors. First, assess the manufacturer’s experience and reputation in the industry. Look for certifications that demonstrate quality assurance, such as ISO standards. Additionally, consider their production capabilities and whether they can meet your specific needs, such as customization options. Request samples and customer references to gauge product quality and service reliability. Finally, ensure that they can meet your delivery timelines and are familiar with logistics in your region. -
What are the common minimum order quantities (MOQs) for kitchen tools?
Minimum order quantities (MOQs) vary by manufacturer and product type. Typically, MOQs can range from 100 to 1,000 units, depending on the complexity of the kitchen tool and manufacturing processes involved. Some manufacturers may offer lower MOQs for custom or specialized items, while others may require higher quantities for standard products. It’s essential to discuss MOQs upfront and explore options for smaller initial orders, especially if you are testing a new product line. -
What payment terms should I expect when sourcing kitchen tools internationally?
Payment terms for international B2B transactions often include options like advance payment, partial payment before production, and balance payment upon delivery. Standard practices might involve using letters of credit (LC) or escrow services to secure transactions. It’s crucial to negotiate terms that protect your interests while ensuring the manufacturer feels secure in their commitment. Be aware of any potential currency exchange risks and consider discussing payment in a stable currency to mitigate financial exposure. -
How can I ensure quality assurance in kitchen tools from manufacturers?
To ensure quality assurance, establish clear product specifications and standards before production begins. Request samples for evaluation and consider implementing a quality control process that includes inspections during production and before shipment. Many manufacturers offer third-party quality assurance services, which can add an extra layer of trust. Additionally, inquire about the manufacturer’s warranty and return policies, as these can indicate their confidence in product quality. -
What are the shipping and logistics considerations when importing kitchen tools?
When importing kitchen tools, consider the logistics of shipping methods, costs, and timelines. Air freight is faster but more expensive, while sea freight is cost-effective for bulk orders but takes longer. Understand the customs regulations in your country, as well as any tariffs or duties that may apply. Collaborating with a freight forwarder can streamline the logistics process and ensure compliance with international shipping standards. Always factor in lead times for production and shipping when planning your inventory. -
How can I customize kitchen tools to meet my brand’s needs?
Customization options for kitchen tools can include changes in design, material, size, and branding elements such as logos and packaging. Most manufacturers will work with you to create prototypes that fit your specifications. It’s important to communicate your vision clearly and provide detailed design files. Additionally, inquire about the costs associated with customization, as these can vary significantly depending on the complexity of the changes and the manufacturer’s capabilities. -
What certifications should I look for in a kitchen tool manufacturer?
Key certifications to consider include ISO 9001 for quality management, ISO 14001 for environmental management, and specific safety standards relevant to kitchen tools, such as FDA approval in the U.S. or CE marking in Europe. These certifications indicate that the manufacturer adheres to strict quality and safety protocols. Additionally, look for certifications related to ethical sourcing and labor practices, especially if you are concerned about sustainability and social responsibility. -
How do I vet a kitchen tool manufacturer before placing an order?
Vetting a manufacturer involves conducting thorough research and due diligence. Start by reviewing their website, product catalogs, and customer testimonials. Request references from other clients, especially those in your region or industry. Conduct virtual or in-person visits to their facilities if possible, and inquire about their production processes and quality control measures. Additionally, consider using third-party verification services that can assess the manufacturer’s legitimacy and reliability before making a commitment.
Important Disclaimer & Terms of Use
⚠️ Important Disclaimer
The information provided in this guide, including content regarding manufacturers, technical specifications, and market analysis, is for informational and educational purposes only. It does not constitute professional procurement advice, financial advice, or legal advice.
While we have made every effort to ensure the accuracy and timeliness of the information, we are not responsible for any errors, omissions, or outdated information. Market conditions, company details, and technical standards are subject to change.
B2B buyers must conduct their own independent and thorough due diligence before making any purchasing decisions. This includes contacting suppliers directly, verifying certifications, requesting samples, and seeking professional consultation. The risk of relying on any information in this guide is borne solely by the reader.
Strategic Sourcing Conclusion and Outlook for kitchen tool manufacturer
What Are the Key Takeaways for B2B Buyers in the Kitchen Tool Industry?
In today’s competitive market, strategic sourcing is essential for kitchen tool manufacturers aiming to optimize costs, improve quality, and enhance supply chain resilience. B2B buyers should prioritize suppliers that demonstrate sustainability practices, innovative product development, and robust logistics capabilities. This not only ensures a consistent supply of high-quality products but also aligns with the growing consumer demand for eco-friendly solutions.
How Can International Buyers Leverage Strategic Sourcing?
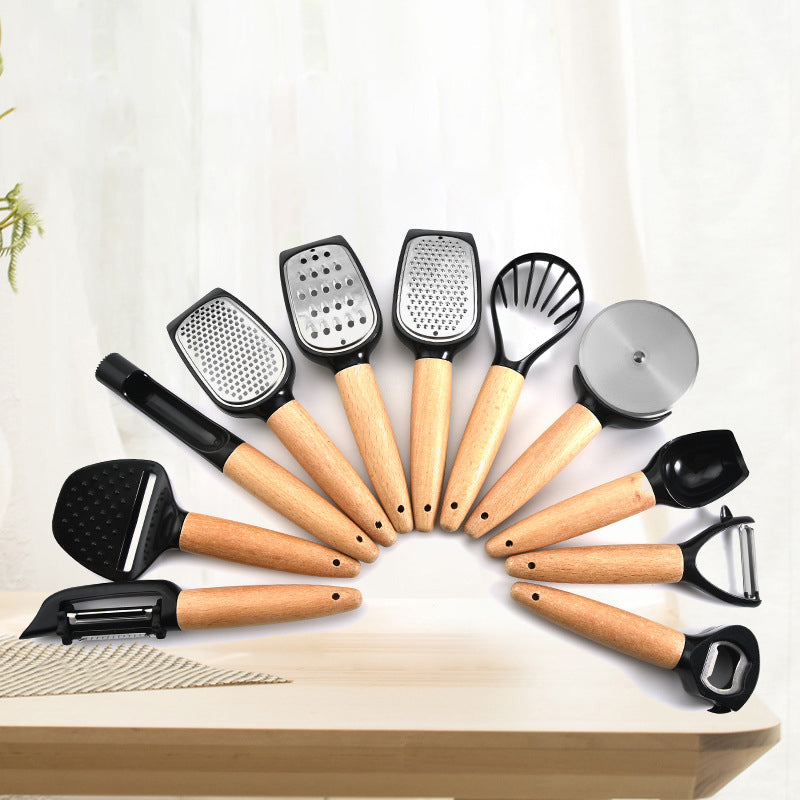
A stock image related to kitchen tool manufacturer.
For international buyers, particularly from regions like Africa, South America, the Middle East, and Europe, understanding local market dynamics is crucial. Building relationships with regional suppliers can lead to better pricing, reduced lead times, and tailored product offerings. Engaging in direct negotiations and fostering long-term partnerships will enhance procurement strategies, ultimately leading to increased profitability.
What Is the Future Outlook for Kitchen Tool Manufacturing?
Looking ahead, the kitchen tool manufacturing landscape will likely evolve with advancements in technology and changing consumer preferences. Buyers are encouraged to stay informed about industry trends, such as smart kitchen appliances and sustainable materials. Embracing these innovations will not only position businesses competitively but also cater to the demands of a more conscious consumer base.
How Should B2B Buyers Take Action?
In conclusion, international B2B buyers should actively seek out strategic sourcing opportunities that enhance their operations and align with market trends. Now is the time to evaluate your current sourcing strategies, invest in supplier relationships, and adapt to the future of kitchen tools. By doing so, you will not only secure your supply chain but also drive growth in an increasingly dynamic marketplace.