Discover Top Kitchen Tools Suppliers: Save Costs & Time (2025)
Introduction: Navigating the Global Market for kitchen tools supplier
In an increasingly competitive global market, sourcing reliable kitchen tools suppliers can pose significant challenges for international B2B buyers. Whether you are in the bustling culinary scene of Germany or the vibrant food industry in Nigeria, the need for high-quality, durable kitchen tools is paramount. This guide aims to simplify the complex process of finding the right kitchen tools supplier, addressing critical factors such as product variety, supplier reliability, and cost-effectiveness.
This comprehensive resource covers a broad spectrum of kitchen tools, from basic utensils to advanced cooking equipment, highlighting their various applications across different culinary settings. We delve into essential considerations for vetting suppliers, ensuring that quality, compliance, and customer service standards are met. Additionally, we provide insights into pricing strategies and negotiation tips, enabling you to make informed purchasing decisions that align with your business objectives.
By equipping B2B buyers from Africa, South America, the Middle East, and Europe with actionable insights, this guide empowers you to navigate the global market effectively. With a strategic approach, you can not only enhance your procurement process but also secure partnerships that foster long-term growth and success in the culinary industry. Explore the nuances of sourcing kitchen tools and unlock the potential of your business with informed decisions that cater to your specific regional needs.
Understanding kitchen tools supplier Types and Variations
Type Name | Key Distinguishing Features | Primary B2B Applications | Brief Pros & Cons for Buyers |
---|---|---|---|
Wholesale Suppliers | Bulk purchasing options, competitive pricing | Restaurants, catering services | Pros: Cost-effective; Cons: Minimum order quantities |
Specialty Suppliers | Niche products, high-quality materials, unique designs | Gourmet restaurants, specialty stores | Pros: Unique offerings; Cons: Higher prices |
OEM Manufacturers | Customizable products, branding options | Private label brands, retail chains | Pros: Tailored solutions; Cons: Longer lead times |
Online Marketplaces | Wide selection, user reviews, convenient ordering | Small businesses, startups | Pros: Easy access; Cons: Variability in quality |
Local Distributors | Regional focus, faster shipping, local market knowledge | Local restaurants, food service companies | Pros: Quick delivery; Cons: Limited product range |
What are the Characteristics of Wholesale Suppliers in the Kitchen Tools Industry?
Wholesale suppliers are characterized by their ability to provide large quantities of kitchen tools at competitive prices. They typically cater to businesses looking to stock up on essential items like utensils, cookware, and appliances. B2B buyers should consider the minimum order quantities and shipping costs, as these can significantly affect the overall expense. Additionally, understanding the supplier’s reputation can help ensure product quality.
How Do Specialty Suppliers Stand Out in the Kitchen Tools Market?
Specialty suppliers focus on niche markets, offering high-quality materials and unique designs that are not commonly found in general retail. They are ideal for gourmet restaurants and specialty stores that prioritize quality and uniqueness over price. When purchasing from specialty suppliers, B2B buyers should evaluate the supplier’s expertise in the specific type of kitchen tools they require, as well as their ability to provide consistent quality and service.
What Advantages Do OEM Manufacturers Offer for Kitchen Tools?
OEM (Original Equipment Manufacturer) manufacturers provide customizable kitchen tools that can be branded to a buyer’s specifications. This is particularly beneficial for private label brands and retail chains looking to create a unique product line. B2B buyers should consider the lead times for customization and the minimum order quantities, as these can impact inventory management. A clear understanding of the manufacturing process and quality control measures is crucial for ensuring product reliability.
Why Choose Online Marketplaces for Kitchen Tools Procurement?
Online marketplaces offer a vast selection of kitchen tools from various suppliers, making it easy for small businesses and startups to find what they need. The convenience of ordering online, coupled with user reviews, helps buyers make informed decisions. However, B2B buyers should be cautious about the variability in product quality and the reliability of different sellers. It’s advisable to check return policies and ratings before making bulk purchases.
What Benefits Do Local Distributors Provide for B2B Buyers?
Local distributors have a strong regional focus, which allows them to understand local market trends and customer preferences better. They offer faster shipping times, which is critical for businesses needing immediate stock replenishment. B2B buyers should assess the distributor’s product range and availability to ensure they can meet their specific needs. While local distributors might have a limited selection compared to larger suppliers, their personalized service and local insights can be invaluable.
Related Video: ESSENTIAL BAKING EQUIPMENT & THEIR USES | necessary baking equipment for your kitchen
Key Industrial Applications of kitchen tools supplier
Industry/Sector | Specific Application of Kitchen Tools Supplier | Value/Benefit for the Business | Key Sourcing Considerations for this Application |
---|---|---|---|
Food Service Industry | Bulk kitchen tools for restaurants and catering | Enhanced efficiency and consistency in food preparation | Quality, durability, and compliance with health regulations |
Hospitality Sector | Custom kitchen tools for hotels and resorts | Improved guest experience and operational efficiency | Customization options, supplier reliability, and lead times |
Food Processing Facilities | Specialized kitchen tools for food manufacturing | Streamlined production processes and waste reduction | Scalability, material specifications, and maintenance support |
Retail and Wholesale | Kitchen tools for resale in supermarkets and stores | Increased product range and customer satisfaction | Pricing, packaging, and distribution logistics |
Culinary Education Institutions | Educational kitchen tools for training programs | Enhanced learning experiences and skill development | Safety standards, educational value, and supplier support |
How Are Kitchen Tools Suppliers Used in the Food Service Industry?
In the food service industry, kitchen tools suppliers provide bulk kitchen utensils and equipment that are essential for restaurants and catering businesses. These tools help streamline food preparation processes, ensuring consistency and quality across dishes. For international B2B buyers, especially in regions like Africa and South America, sourcing high-quality, durable kitchen tools is crucial for maintaining operational efficiency and adhering to local health regulations. Suppliers must offer a range of products that can withstand the demands of a busy kitchen environment while complying with safety standards.
What Are the Benefits of Custom Kitchen Tools in the Hospitality Sector?
Hotels and resorts often require custom kitchen tools tailored to their specific culinary needs. Kitchen tools suppliers can provide bespoke solutions that enhance the guest experience through unique culinary offerings. For B2B buyers in Europe and the Middle East, the ability to customize tools not only improves operational efficiency but also aligns with branding strategies. Key considerations for sourcing include the supplier’s ability to deliver high-quality custom products, reliability, and the timelines for production and delivery.
How Do Specialized Kitchen Tools Aid Food Processing Facilities?
Food processing facilities rely on specialized kitchen tools to optimize their manufacturing processes. Suppliers provide equipment designed to enhance production efficiency, reduce waste, and ensure product quality. For international buyers, particularly in emerging markets, it is vital to assess suppliers based on their ability to scale operations and provide ongoing maintenance support. Moreover, understanding material specifications is essential to meet both local and international food safety standards.
Why Are Kitchen Tools Important for Retail and Wholesale Operations?
In the retail and wholesale sector, kitchen tools suppliers play a critical role in providing a diverse range of products for supermarkets and specialty stores. By offering high-quality kitchen tools, retailers can increase their product assortment, thereby enhancing customer satisfaction and driving sales. For B2B buyers in Africa and Europe, sourcing considerations include competitive pricing, effective packaging, and reliable distribution logistics to ensure timely stock availability.
How Do Educational Institutions Benefit from Kitchen Tools Suppliers?
Culinary education institutions depend on kitchen tools suppliers to provide educational-grade utensils and equipment for training programs. These tools are designed to enhance the learning experience and develop essential culinary skills among students. For international B2B buyers, particularly from regions like South America and the Middle East, it is important to ensure that suppliers adhere to safety standards and offer products that are both educationally valuable and durable. Additionally, suppliers should provide ongoing support and resources to enhance the educational experience.
Related Video: 50 Essential Kitchen Tools and Their Uses (Ultimate Guide)
3 Common User Pain Points for ‘kitchen tools supplier’ & Their Solutions
Scenario 1: Inconsistent Quality of Kitchen Tools
The Problem:
B2B buyers often encounter the challenge of inconsistent quality when sourcing kitchen tools from suppliers. This inconsistency can lead to frustrations, especially in regions where high standards are expected, such as Europe and the Middle East. For instance, a restaurant in Germany might order a batch of stainless steel knives, but upon delivery, some knives are dull or have manufacturing defects. Such issues not only tarnish the buyer’s reputation but also disrupt operations, resulting in wasted time and resources.
The Solution:
To mitigate quality inconsistencies, buyers should implement a rigorous supplier vetting process. Begin by requesting samples before placing a larger order. This allows you to assess the quality firsthand. Additionally, establishing a quality assurance protocol is essential. Collaborate with the supplier to set clear quality standards and conduct regular inspections. If feasible, consider visiting the supplier’s manufacturing facility, especially for long-term partnerships. This proactive approach not only ensures that the products meet your expectations but also strengthens the relationship with the supplier, fostering trust and reliability.
Scenario 2: Difficulty in Navigating Import Regulations
The Problem:
Navigating import regulations can be a daunting task for B2B buyers in regions like Africa and South America. For example, a catering company in Nigeria looking to import specialized kitchen tools may face complex customs requirements and tariffs that can delay shipments. This can lead to unforeseen costs and disruptions in service, ultimately impacting customer satisfaction and business operations.
The Solution:
To effectively manage import regulations, B2B buyers should partner with local customs brokers who specialize in kitchen tools and similar products. These experts can provide invaluable insights into the specific regulations and documentation required for smooth importation. Additionally, staying informed about regional trade agreements and tariffs can help mitigate unexpected costs. Buyers should also consider working closely with their suppliers to ensure that all necessary documentation is prepared in advance. This collaboration will facilitate a smoother import process, allowing for timely deliveries and minimizing disruptions.
Scenario 3: Limited Product Variety and Customization Options
The Problem:
B2B buyers often find themselves restricted by a limited variety of kitchen tools and customization options from suppliers. For instance, a restaurant chain in South America may require unique kitchen tools tailored to their specific cuisine, but the supplier offers only generic solutions. This lack of variety can hinder operational efficiency and prevent businesses from meeting their customers’ diverse needs.
The Solution:
To overcome this limitation, buyers should seek suppliers that specialize in customizable kitchen tools. Engage in open dialogue with potential suppliers about your specific needs and inquire about their capability to accommodate customization requests. Additionally, consider leveraging technology by exploring suppliers that utilize 3D printing or modular designs, which can offer greater flexibility in product development. Attending industry trade shows can also be beneficial, as it provides opportunities to discover innovative suppliers who may offer unique solutions tailored to your business. By prioritizing suppliers that can deliver customized products, businesses can enhance their operational efficiency and better serve their clientele.
Strategic Material Selection Guide for kitchen tools supplier
When selecting materials for kitchen tools, international B2B buyers must consider various factors that influence product performance, compliance, and market preferences. Here, we analyze four common materials used in kitchen tools, highlighting their properties, advantages, limitations, and specific considerations for buyers from Africa, South America, the Middle East, and Europe.
What Are the Key Properties of Stainless Steel for Kitchen Tools?
Stainless steel is renowned for its excellent corrosion resistance, high tensile strength, and ability to withstand extreme temperatures. These properties make it ideal for a variety of kitchen tools, including knives, cookware, and utensils. Additionally, stainless steel is non-reactive, ensuring that it does not alter the taste of food.
Pros and Cons:
The durability of stainless steel is a significant advantage, as it can endure rigorous use without easily bending or breaking. However, the manufacturing complexity can lead to higher costs compared to other materials. Moreover, while stainless steel is generally easy to clean, it may require specific care to maintain its shine and prevent scratching.
Impact on Application:
Stainless steel is compatible with a wide range of food media, making it suitable for diverse culinary applications. Its resistance to rust and staining ensures longevity, which is crucial for commercial kitchens.
Considerations for Buyers:
Buyers from regions like Germany and Nigeria should be aware of compliance with international standards such as ASTM and DIN. Additionally, preferences for high-quality, durable kitchen tools are common in these markets, making stainless steel a favored choice.
How Does Plastic Compare for Kitchen Tools?
Plastic is a versatile material often used in kitchen tools like measuring cups, spatulas, and cutting boards. It is lightweight and available in various colors and designs, catering to aesthetic preferences.
Pros and Cons:
The primary advantage of plastic is its low cost and ease of manufacturing, allowing for mass production. However, its durability is often questioned, as it can warp or break under high temperatures. Furthermore, not all plastics are food-safe, which can pose health risks.
Impact on Application:
Plastic tools are generally suitable for cold or room-temperature media but may not perform well with hot foods or liquids. This limitation can affect their usability in professional kitchens.
Considerations for Buyers:
International buyers should ensure that the plastic used complies with food safety regulations specific to their region. In Europe, for instance, compliance with REACH regulations is crucial, while buyers in South America may need to consider local certifications.
What Advantages Does Silicone Offer in Kitchen Tools?
Silicone has gained popularity for its flexibility, heat resistance, and non-stick properties. It is commonly used in baking mats, spatulas, and molds.
Pros and Cons:
Silicone’s heat resistance allows it to withstand temperatures up to 450°F (232°C), making it ideal for baking and cooking. However, while it is durable, it may not be suitable for sharp tools, as it can wear down over time. Additionally, silicone products can be more expensive than their plastic counterparts.
Impact on Application:
Silicone is non-reactive and safe for use with a variety of food types, including acidic ingredients. This versatility makes it a popular choice in both home and commercial kitchens.
Considerations for Buyers:
Buyers should look for silicone products that meet FDA or EU food safety standards. Understanding the specific heat ratings and certifications can help in selecting the right silicone tools for diverse culinary applications.
Why Is Wood Still a Preferred Material for Kitchen Tools?
Wood remains a classic choice for kitchen tools such as cutting boards, spoons, and rolling pins. Its natural aesthetic and tactile feel appeal to many chefs and home cooks alike.
Pros and Cons:
Wood is durable and can withstand significant wear, making it suitable for heavy-duty use. However, it requires more maintenance than synthetic materials, as it can absorb moisture and odors. Additionally, wood tools may not be dishwasher safe, which can complicate cleaning.
Impact on Application:
Wood is compatible with most food types and does not react with acidic ingredients, making it a safe choice for food preparation. However, its porous nature can harbor bacteria if not properly cared for.
Considerations for Buyers:
Buyers should ensure that wood products are sourced from sustainable forests and comply with local regulations regarding food safety. In regions like Europe, certifications such as FSC (Forest Stewardship Council) can enhance marketability.
Summary Table of Material Selection for Kitchen Tools
Material | Typical Use Case for kitchen tools supplier | Key Advantage | Key Disadvantage/Limitation | Relative Cost (Low/Med/High) |
---|---|---|---|---|
Stainless Steel | Knives, cookware, utensils | Excellent durability and strength | Higher manufacturing complexity | High |
Plastic | Measuring cups, spatulas, cutting boards | Low cost and lightweight | Can warp or break under heat | Low |
Silicone | Baking mats, spatulas, molds | Heat resistant and non-stick | May wear down over time | Medium |
Wood | Cutting boards, spoons, rolling pins | Aesthetic appeal and durability | Requires maintenance and care | Medium |
This strategic material selection guide provides B2B buyers with crucial insights into the properties, advantages, and limitations of various materials used in kitchen tools. Understanding these factors can significantly influence purchasing decisions and ensure compliance with international standards.
In-depth Look: Manufacturing Processes and Quality Assurance for kitchen tools supplier
What Are the Main Stages of Manufacturing Kitchen Tools?
The manufacturing process for kitchen tools typically involves several key stages: material preparation, forming, assembly, and finishing. Each of these stages plays a vital role in determining the quality and usability of the final product.
-
Material Preparation: This initial stage involves selecting the right materials, which may include stainless steel, plastic, silicone, or wood. The materials must be sourced from reputable suppliers to ensure they meet safety and durability standards. Proper storage conditions and handling practices are crucial to prevent contamination or degradation of the materials.
-
Forming: The forming stage is where the raw materials are shaped into the desired forms. Techniques such as stamping, injection molding, or die-casting are commonly used. For instance, stainless steel kitchen tools may undergo processes like forging or machining to achieve precise dimensions. B2B buyers should inquire about the methods used, as they significantly impact the strength and finish of the product.
-
Assembly: Once the components are formed, they are assembled into final products. This stage may involve manual labor or automated processes, depending on the complexity of the tool. For example, a multi-functional kitchen gadget might require intricate assembly, while a simple knife may need minimal handling. Understanding the assembly process can provide insights into the labor costs and efficiency of the supplier.
-
Finishing: The finishing stage enhances the aesthetic appeal and functionality of the kitchen tools. Techniques such as polishing, coating, or heat treatment are used to improve surface quality and resistance to corrosion. This stage is critical for ensuring that the tools not only look good but also perform well over time. B2B buyers should request samples to evaluate the finish quality before making bulk purchases.
How Do Quality Assurance Practices Enhance Kitchen Tool Manufacturing?
Quality assurance (QA) is integral to the manufacturing process, ensuring that kitchen tools meet both international standards and customer expectations. Implementing robust QA practices can help suppliers maintain consistency and reliability.
-
International Standards: Suppliers often adhere to international quality management standards such as ISO 9001, which outlines criteria for establishing an effective quality management system. Compliance with these standards indicates that the manufacturer has a systematic approach to managing quality, from production to delivery.
-
Industry-Specific Certifications: Kitchen tools may also require specific certifications like CE marking for safety in the European market or FDA approval for food-safe materials in the U.S. Buyers should verify that suppliers possess the necessary certifications for their target markets.
What Are the Key Quality Control Checkpoints in Kitchen Tool Manufacturing?
Quality control (QC) checkpoints are critical in identifying defects and ensuring that products meet specified standards. The following checkpoints are commonly implemented in the manufacturing process:
-
Incoming Quality Control (IQC): This initial checkpoint involves inspecting raw materials upon arrival. Suppliers assess the quality and specifications of materials to prevent defects from entering the production line.
-
In-Process Quality Control (IPQC): Throughout the manufacturing process, IPQC is employed to monitor production activities. This includes regular inspections during forming and assembly to ensure adherence to quality standards. Statistical process control (SPC) techniques are often used here to identify variations in the production process.
-
Final Quality Control (FQC): Once the kitchen tools are completed, FQC involves a comprehensive examination of the finished products. This includes functional testing, visual inspections, and packaging checks to ensure that each item meets the required quality standards before shipment.
What Common Testing Methods Are Used to Ensure Quality in Kitchen Tools?
Various testing methods are employed to validate the quality of kitchen tools. These methods help ensure that the products are safe, durable, and effective for their intended use.
-
Mechanical Testing: This includes tensile tests, hardness tests, and impact tests to assess the strength and durability of materials. For instance, kitchen knives may undergo sharpness tests to ensure they meet performance expectations.
-
Chemical Testing: To confirm that materials are food-safe, suppliers may conduct chemical analysis to check for harmful substances or contaminants. This is particularly important for tools that come into direct contact with food.
-
Functional Testing: Each kitchen tool is subjected to functional tests to verify its usability. For example, measuring cups may be tested for accuracy, while non-stick pans might undergo heat resistance tests.
How Can B2B Buyers Verify Supplier Quality Control Practices?
Verifying a supplier’s quality control practices is essential for ensuring that the kitchen tools meet your business’s standards. Here are several strategies that B2B buyers can employ:
-
Supplier Audits: Conducting audits of potential suppliers allows buyers to assess their manufacturing processes and quality control measures firsthand. This includes reviewing documentation related to their QA systems and observing their production lines.
-
Quality Reports: Requesting quality reports from suppliers can provide insights into their QC processes and performance. These reports should detail inspection results, defect rates, and any corrective actions taken.
-
Third-Party Inspections: Engaging third-party inspection services can add an extra layer of assurance. These independent entities can verify compliance with international standards and conduct random checks on the manufacturing process.
What Nuances Should International B2B Buyers Consider Regarding Quality Control?
When sourcing kitchen tools from international suppliers, particularly in Africa, South America, the Middle East, and Europe, buyers should be aware of several nuances related to quality control:
-
Cultural Differences: Understanding cultural attitudes toward quality and manufacturing can impact supplier relationships. Some regions may prioritize cost over quality, while others may have stringent quality control practices.
-
Regulatory Variances: Different countries have varying regulations regarding product safety and quality. Buyers should familiarize themselves with the specific regulations that apply to their target markets to ensure compliance.
-
Communication Challenges: Language barriers can lead to misunderstandings regarding quality expectations. Establishing clear communication channels and using standardized documentation can help mitigate these issues.
By focusing on these manufacturing processes and quality assurance practices, international B2B buyers can make informed decisions when selecting kitchen tools suppliers. Prioritizing quality not only enhances the reputation of your business but also ensures customer satisfaction in an increasingly competitive market.
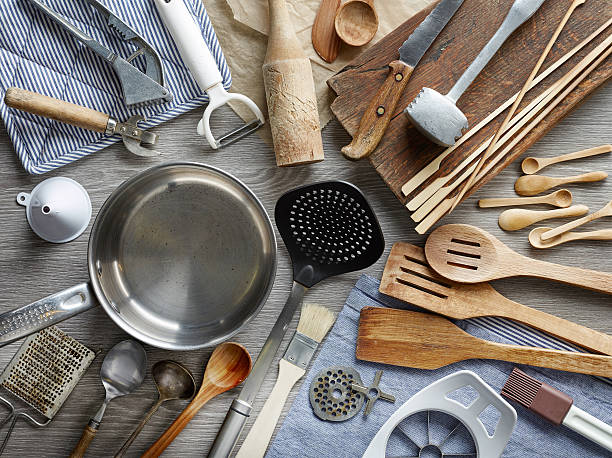
A stock image related to kitchen tools supplier.
Practical Sourcing Guide: A Step-by-Step Checklist for ‘kitchen tools supplier’
The purpose of this sourcing guide is to equip international B2B buyers, particularly from Africa, South America, the Middle East, and Europe, with actionable insights and a structured approach to procuring kitchen tools from suppliers. By following these steps, buyers can ensure they are making informed decisions that align with their operational needs and market standards.
Step 1: Define Your Technical Specifications
Establishing clear technical specifications for the kitchen tools you need is essential. This includes identifying the types of tools (e.g., knives, utensils, cookware) and their materials (e.g., stainless steel, silicone). Providing detailed specifications helps suppliers understand your requirements and minimizes the risk of receiving substandard products.
- Consider market trends: Research popular materials and designs in your target market to ensure the tools meet consumer preferences.
- Include compliance standards: Specify any relevant safety and quality standards that the products must adhere to.
Step 2: Conduct Market Research for Suppliers
Researching potential suppliers is vital for finding reliable partners. Use online platforms, trade shows, and industry forums to compile a list of suppliers specializing in kitchen tools. This research should also include checking their reputation and track record in the industry.
- Utilize trade directories: Websites like Alibaba, Global Sources, and industry-specific directories can provide a comprehensive list of suppliers.
- Engage with industry associations: Connecting with local or regional associations can provide insights into reputable suppliers.
Step 3: Evaluate Potential Suppliers
Before committing to a supplier, it’s crucial to conduct thorough evaluations. Request company profiles, product catalogs, and references from previous clients, especially those in similar industries or regions. This step helps you gauge the supplier’s reliability and product quality.
- Assess their production capacity: Ensure the supplier can meet your volume requirements without compromising quality.
- Look for previous collaborations: Understanding their experience with international clients can indicate their ability to handle cross-border transactions.
Step 4: Verify Supplier Certifications and Compliance
Ensure that the suppliers possess the necessary certifications and comply with international standards. This is particularly important for kitchen tools that will be used in food preparation and service.
- Check for ISO certifications: These indicate adherence to quality management standards.
- Confirm compliance with local regulations: Each region may have specific regulations regarding food safety and materials used in kitchen tools.
Step 5: Request Samples Before Finalizing Orders
Obtaining samples before placing bulk orders is a critical step in the sourcing process. Samples allow you to assess the quality, functionality, and durability of the kitchen tools.
- Evaluate usability: Test the samples in real-world conditions to ensure they meet your operational needs.
- Check for consistency: Ensure the samples reflect the quality you can expect from larger orders.
Step 6: Negotiate Terms and Conditions
Once you have selected a supplier, the next step is to negotiate favorable terms and conditions. This includes pricing, delivery timelines, payment terms, and after-sales support.
- Discuss bulk order discounts: Many suppliers offer reduced prices for larger orders, which can significantly impact your bottom line.
- Clarify warranty and return policies: Understanding these terms upfront can save you from potential disputes later on.
Step 7: Establish a Communication Plan
Effective communication is key to a successful supplier relationship. Establish a clear communication plan that outlines how you will interact with your supplier throughout the procurement process.
- Set regular check-ins: Schedule periodic updates to monitor progress and address any issues promptly.
- Utilize multiple communication channels: Ensure you have contact through email, phone, and messaging apps to facilitate quick resolution of queries.
By following these steps, B2B buyers can streamline their sourcing process and develop robust relationships with kitchen tools suppliers, ultimately enhancing their business operations and market presence.
Comprehensive Cost and Pricing Analysis for kitchen tools supplier Sourcing
What Are the Key Cost Components for Kitchen Tools Supplier Sourcing?
When sourcing kitchen tools, understanding the cost structure is essential for making informed purchasing decisions. The primary cost components include:
-
Materials: The type and quality of materials directly impact the cost of kitchen tools. Stainless steel, silicone, and high-grade plastics are common materials, each varying in price. Buyers should evaluate the long-term durability and usability of materials to ensure they align with their quality expectations.
-
Labor: Labor costs can vary significantly by region. In areas with higher wages, such as Europe, labor costs will be a larger component of the overall price. Suppliers in regions like Africa or South America may offer lower labor costs, but this can sometimes affect the quality of craftsmanship.
-
Manufacturing Overhead: This includes costs associated with utilities, rent, and administrative expenses related to production. Efficient manufacturing processes can reduce these costs, so it’s beneficial to assess the supplier’s operational efficiency.
-
Tooling: Custom tooling can represent a substantial upfront investment. Buyers should understand whether the supplier has the capability to produce specific designs without incurring excessive tooling costs, especially for customized products.
-
Quality Control (QC): Implementing a robust QC process is critical to ensuring product quality. Suppliers may charge more for stringent QC measures, but this can prevent costly returns and replacements down the line.
-
Logistics: Shipping costs can significantly affect the final price. Factors such as distance, mode of transport, and shipping frequency should be considered. For international buyers, understanding the implications of shipping delays and customs duties is crucial.
-
Margin: Supplier profit margins can vary widely. Understanding the industry standard for margins in the kitchen tools sector can help buyers gauge whether a supplier’s pricing is competitive.
How Do Price Influencers Impact Kitchen Tools Supplier Pricing?
Several factors influence the pricing of kitchen tools, including:
-
Volume and Minimum Order Quantity (MOQ): Bulk purchases often lead to discounts. Buyers should negotiate MOQs to optimize pricing while ensuring they have adequate inventory.
-
Specifications and Customization: Custom designs or specific features can increase costs. Clear communication of specifications upfront can help avoid unexpected costs later in the process.
-
Materials and Quality Certifications: Premium materials and certifications (e.g., FDA, ISO) can drive up costs. Buyers should assess whether these certifications are necessary for their market.
-
Supplier Factors: Reputation, reliability, and experience can influence pricing. Established suppliers may charge more but often provide better service and product consistency.
-
Incoterms: Understanding Incoterms is crucial for pricing negotiations. They define the responsibilities of buyers and sellers regarding shipping costs, insurance, and risk management.
What Tips Can Help Buyers Optimize Costs in Kitchen Tools Sourcing?
International B2B buyers can implement several strategies to enhance cost-efficiency:
-
Negotiate Terms: Leverage your position as a bulk buyer to negotiate better terms, including price, payment schedules, and delivery timelines. Establishing a long-term relationship can also yield better pricing over time.
-
Evaluate Total Cost of Ownership (TCO): Rather than focusing solely on the purchase price, consider the TCO, which includes maintenance, shipping, and disposal costs. This holistic view can lead to more sustainable purchasing decisions.
-
Understand Pricing Nuances: Buyers from different regions should be aware of local market conditions that may affect pricing. For example, currency fluctuations can impact costs, so locking in prices in a stable currency can mitigate risks.
-
Research Market Trends: Keeping abreast of market trends, such as emerging materials or production technologies, can provide insights into potential cost savings. This knowledge empowers buyers to make strategic sourcing decisions.
Disclaimer on Indicative Prices
Prices for kitchen tools can vary widely based on the factors discussed above. It is advisable to conduct thorough market research and engage in direct negotiations with suppliers to obtain accurate pricing tailored to specific needs.
Alternatives Analysis: Comparing kitchen tools supplier With Other Solutions
Understanding the Importance of Alternatives in Kitchen Tools Supply
When considering kitchen tools suppliers, it’s vital for international B2B buyers to explore various alternatives that can meet their operational needs. This analysis will compare kitchen tools suppliers with two viable alternatives: in-house production of kitchen tools and sourcing from local artisans. Each option has unique advantages and disadvantages that can significantly impact your business strategy, especially in diverse markets across Africa, South America, the Middle East, and Europe.
Comparison Table of Kitchen Tools Supplier and Alternatives
Comparison Aspect | Kitchen Tools Supplier | In-House Production | Sourcing from Local Artisans |
---|---|---|---|
Performance | High quality & variety | Variable quality | Unique designs, quality varies |
Cost | Moderate to high | High initial investment, low long-term | Variable, often low initial cost |
Ease of Implementation | Quick and straightforward | Complex setup and training | Requires relationship building |
Maintenance | Supplier handles maintenance | Full responsibility | Minimal, depends on agreement |
Best Use Case | Large scale production | Customization needs | Unique or specialty items |
In-House Production of Kitchen Tools: Pros and Cons
In-house production allows companies to maintain complete control over the manufacturing process. This can lead to high customization and the ability to meet specific needs of your business. However, it comes with significant initial investment costs for machinery and workforce training. Over time, it can result in lower unit costs, but the complexity of setup and ongoing management can be challenging, especially for businesses without prior manufacturing experience.
Sourcing from Local Artisans: Advantages and Disadvantages
Sourcing from local artisans can be an attractive option for B2B buyers looking for unique designs and cultural craftsmanship. This method often supports local economies and can lead to lower initial costs. However, the quality can be inconsistent, and the supply may not meet high-volume demands. Building strong relationships with artisans is crucial, as it ensures reliability in supply and quality assurance, which can be time-consuming.
How to Choose the Right Solution for Your Kitchen Tool Needs
Selecting the right kitchen tools solution requires a thorough understanding of your business’s specific needs and operational capabilities. If you require a diverse range of high-quality tools for large-scale operations, a kitchen tools supplier may be the best fit. Conversely, if customization and unique offerings are your priority, in-house production or sourcing from local artisans could be more advantageous. Evaluate your budget, capacity for maintenance, and the level of quality control you need to make an informed decision. By analyzing these factors, you can align your choice with your business strategy and market demands effectively.
Essential Technical Properties and Trade Terminology for kitchen tools supplier
Understanding the essential technical properties and trade terminology in the kitchen tools supply industry is crucial for international B2B buyers. This knowledge not only facilitates informed purchasing decisions but also enhances negotiation capabilities and supplier relationships.
What Are the Key Technical Properties of Kitchen Tools?
1. Material Grade: Why Is It Important for Kitchen Tools?
Material grade refers to the specific classification of the materials used in kitchen tools, which can significantly impact durability, safety, and usability. Common materials include stainless steel, silicone, and high-density plastics. Buyers should prioritize tools made from food-grade materials to ensure compliance with health regulations, especially when exporting to markets in Europe and North America.
2. Tolerance: How Does It Affect Product Quality?
Tolerance is the allowable deviation in dimensions and specifications of kitchen tools. High tolerance levels ensure that parts fit together correctly, which is vital for tools like knives and measuring cups. In the B2B context, understanding tolerance helps buyers assess quality and reliability, reducing the likelihood of defects that could lead to returns or customer dissatisfaction.
3. Weight Capacity: What Should Buyers Consider?
Weight capacity indicates the maximum load a kitchen tool can handle without risking damage. This specification is particularly important for products like mixing bowls and cutting boards. Buyers must consider the weight capacity to ensure that the tools will withstand their intended use in both commercial and domestic settings.
4. Heat Resistance: Why Is It Critical for Kitchen Tools?
Heat resistance refers to the ability of materials to withstand high temperatures without deforming or releasing harmful substances. This property is crucial for tools exposed to heat, such as spatulas and baking trays. B2B buyers should prioritize heat-resistant materials to ensure the safety and longevity of their kitchen tools.
5. Finish: How Does It Influence Aesthetic and Functionality?
The finish of kitchen tools can affect both their appearance and functionality. Options include matte, polished, or non-stick finishes. A well-chosen finish can enhance user experience and ease of cleaning, which are important selling points in competitive markets.
What Are Common Trade Terms Every B2B Buyer Should Know?
1. OEM (Original Equipment Manufacturer): What Does It Mean?
OEM refers to companies that produce parts or equipment that may be marketed by another manufacturer. For B2B buyers, understanding OEM relationships can help in sourcing unique kitchen tools that meet specific design requirements, ensuring brand differentiation in the marketplace.
2. MOQ (Minimum Order Quantity): How Does It Impact Purchasing Decisions?
MOQ is the smallest quantity of a product that a supplier is willing to sell. This term is critical for B2B buyers as it influences inventory management and cash flow. Understanding MOQ helps buyers negotiate better terms and avoid over-commitment on stock that may not sell.
3. RFQ (Request for Quotation): Why Is It Essential?
An RFQ is a document issued by a buyer to solicit price quotes from suppliers for specific products or services. For kitchen tools suppliers, submitting RFQs is a standard practice that allows buyers to compare costs and evaluate suppliers based on pricing, delivery times, and other terms.
4. Incoterms (International Commercial Terms): How Do They Affect Shipping?
Incoterms are a set of international rules that define the responsibilities of buyers and sellers in shipping agreements. Familiarity with Incoterms is vital for B2B buyers as they clarify who is responsible for shipping costs, insurance, and tariffs, thereby reducing misunderstandings in international transactions.
5. Lead Time: What Should Buyers Expect?
Lead time refers to the time taken from placing an order to receiving the goods. Understanding lead times is essential for B2B buyers to manage their inventory effectively and ensure that they can meet customer demands without delays.
By grasping these technical properties and trade terms, international B2B buyers can enhance their sourcing strategies, improve supplier negotiations, and ultimately achieve better outcomes in their kitchen tools procurement processes.
Navigating Market Dynamics and Sourcing Trends in the kitchen tools supplier Sector
What Are the Current Market Dynamics and Key Trends in the Kitchen Tools Supplier Sector?
The kitchen tools supplier sector is experiencing significant shifts driven by globalization, technological advancements, and changing consumer preferences. International B2B buyers, particularly from Africa, South America, the Middle East, and Europe, must stay informed about these dynamics to make strategic sourcing decisions. One notable trend is the increasing demand for multifunctional kitchen tools, which cater to the growing consumer interest in efficiency and space-saving solutions. This trend is particularly prominent in urban areas where kitchen spaces are limited.
Moreover, the rise of e-commerce platforms has transformed how suppliers and buyers interact. B2B buyers can now access a wider array of products and suppliers online, facilitating more competitive pricing and enhanced negotiation capabilities. Additionally, advancements in supply chain technology, such as AI and blockchain, are improving transparency and efficiency in sourcing processes. These technologies help in tracking product origins and ensuring compliance with safety standards, which is crucial for international trade.
Another dynamic influencing the market is the growing emphasis on local sourcing. Buyers are increasingly inclined to support local manufacturers in their regions to reduce lead times, shipping costs, and carbon footprints. This trend is especially relevant for buyers in Africa and South America, where local suppliers can offer competitive pricing and culturally relevant products.
How Is Sustainability and Ethical Sourcing Shaping the Kitchen Tools Supplier Sector?
Sustainability has emerged as a critical factor for B2B buyers in the kitchen tools supplier sector. The environmental impact of manufacturing processes is under scrutiny, leading companies to adopt sustainable practices. Ethical sourcing is not just a trend; it is becoming a prerequisite for many buyers who are committed to minimizing their carbon footprints and promoting fair labor practices.
Buyers should look for suppliers who prioritize sustainable materials, such as recycled plastics, bamboo, and other renewable resources. Certifications like FSC (Forest Stewardship Council) and ISO 14001 (Environmental Management) are indicators of a supplier’s commitment to sustainability. Furthermore, adopting eco-friendly packaging solutions is increasingly important, as consumers are more aware of waste and environmental issues.
In regions like Europe, where regulations around sustainability are stringent, suppliers who can demonstrate their commitment to green practices may have a competitive advantage. Buyers from Africa and the Middle East should also consider how local regulations and consumer expectations around sustainability can influence their sourcing decisions. Engaging with suppliers who prioritize sustainability can enhance brand reputation and appeal to environmentally conscious consumers.
What Is the Evolution of the Kitchen Tools Supplier Sector and Its Implications for B2B Buyers?
The kitchen tools supplier sector has evolved significantly over the decades, transitioning from traditional craftsmanship to modern manufacturing techniques. In the early stages, kitchen tools were often handmade, limiting availability and scalability. However, the industrial revolution introduced mass production, allowing for a wider range of products at lower costs.
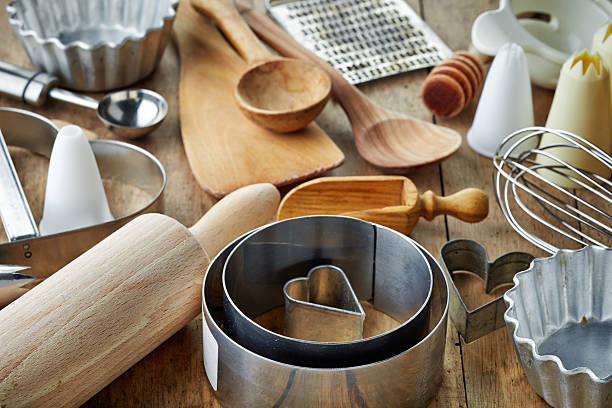
A stock image related to kitchen tools supplier.
Today, the sector is characterized by rapid innovation, with smart kitchen tools equipped with IoT capabilities entering the market. This shift towards technology-driven solutions offers B2B buyers opportunities to invest in advanced products that enhance user experience and operational efficiency.
Understanding this evolution helps international buyers make informed sourcing decisions. As the market continues to develop, staying updated on emerging technologies and trends will be essential for maintaining a competitive edge in the kitchen tools industry. By aligning their sourcing strategies with these historical trends, buyers can better anticipate future needs and opportunities in the market.
Frequently Asked Questions (FAQs) for B2B Buyers of kitchen tools supplier
-
How do I solve sourcing challenges for kitchen tools in international markets?
Sourcing kitchen tools internationally can pose challenges such as language barriers, cultural differences, and varying quality standards. To address these issues, conduct thorough research on potential suppliers, utilizing platforms like Alibaba or Global Sources. Establish clear communication channels, preferably in the supplier’s language, and request samples to evaluate quality. Additionally, consider hiring a local sourcing agent who understands the market dynamics and can facilitate negotiations and logistics. -
What is the best way to vet a kitchen tools supplier for my business needs?
To effectively vet a kitchen tools supplier, begin by checking their credentials, including business licenses and certifications. Request references from previous clients to gauge their reliability and quality of service. Conduct site visits if possible, or utilize third-party inspection services to assess their production capabilities. Furthermore, evaluate their financial stability and production capacity to ensure they can meet your order requirements consistently. -
How can I customize kitchen tools to fit my brand requirements?
Customization of kitchen tools typically involves selecting materials, designs, and branding elements like logos. When working with a supplier, discuss your specific needs early in the negotiation process. Most suppliers offer customization options, but be prepared to meet minimum order quantities (MOQs) and provide detailed specifications. Consider collaborating with the supplier’s design team to create prototypes that align with your brand identity before finalizing large orders. -
What are common minimum order quantities (MOQs) for kitchen tools suppliers?
MOQs can vary significantly depending on the supplier and the type of kitchen tools being sourced. Generally, MOQs range from 100 to 1,000 units. Suppliers may set higher MOQs for customized products due to additional production costs. When negotiating, consider your budget and storage capacity, and discuss the possibility of lower MOQs for initial orders or trial runs to establish a working relationship. -
What payment terms should I expect when dealing with international suppliers?
Payment terms can vary based on the supplier’s policies and the nature of the order. Common terms include a deposit (usually 30-50%) upfront, with the balance due before shipment. Some suppliers may offer letters of credit or payment upon delivery for established relationships. Always clarify payment methods accepted (e.g., wire transfer, PayPal) and ensure that terms are documented in a contract to avoid misunderstandings. -
How do I ensure quality assurance when sourcing kitchen tools?
To ensure quality assurance, establish clear specifications and standards with your supplier before production begins. Request samples for inspection and consider setting up a quality control process that includes on-site inspections during manufacturing. Additionally, consider third-party quality assurance services to conduct inspections before shipment. Regular communication with the supplier throughout the production process can help address any potential issues early. -
What logistics considerations should I keep in mind when importing kitchen tools?
When importing kitchen tools, consider logistics factors such as shipping methods, customs regulations, and lead times. Evaluate whether air freight or sea freight is more suitable based on your timeline and budget. Familiarize yourself with the import duties and tariffs applicable in your country, as these can affect your overall costs. Collaborating with a freight forwarder can streamline the shipping process and ensure compliance with all regulatory requirements. -
How do I navigate trade regulations and tariffs when importing kitchen tools?
Navigating trade regulations and tariffs involves understanding the specific requirements of your country regarding imported goods. Research the Harmonized System (HS) codes for kitchen tools to identify applicable duties and tariffs. Stay updated on trade agreements that may impact your import costs. Consulting with a customs broker can provide valuable insights and help ensure that all documentation is correctly prepared, reducing the risk of delays or fines.
Important Disclaimer & Terms of Use
⚠️ Important Disclaimer
The information provided in this guide, including content regarding manufacturers, technical specifications, and market analysis, is for informational and educational purposes only. It does not constitute professional procurement advice, financial advice, or legal advice.
While we have made every effort to ensure the accuracy and timeliness of the information, we are not responsible for any errors, omissions, or outdated information. Market conditions, company details, and technical standards are subject to change.
B2B buyers must conduct their own independent and thorough due diligence before making any purchasing decisions. This includes contacting suppliers directly, verifying certifications, requesting samples, and seeking professional consultation. The risk of relying on any information in this guide is borne solely by the reader.
Strategic Sourcing Conclusion and Outlook for kitchen tools supplier
In today’s competitive market, the significance of strategic sourcing for kitchen tools suppliers cannot be overstated. By leveraging data-driven insights and fostering strong supplier relationships, international B2B buyers can ensure access to high-quality products while optimizing costs. This approach not only enhances supply chain efficiency but also enables businesses to respond swiftly to changing consumer demands.
What are the key benefits of strategic sourcing for kitchen tools suppliers? Buyers can expect improved product quality, reduced lead times, and increased flexibility in their procurement processes. By focusing on collaboration and innovation, companies can differentiate themselves in diverse markets across Africa, South America, the Middle East, and Europe.
As we look toward the future, it is essential for B2B buyers to remain proactive in their sourcing strategies. Embracing digital tools and sustainability practices will be crucial for staying ahead in the evolving landscape of kitchen tools supply. Now is the time to take action—evaluate your sourcing strategies, invest in supplier partnerships, and position your business for sustainable growth in the global market.