Discover Top Label Suppliers: Your Ultimate Sourcing Guide (2025)
Introduction: Navigating the Global Market for label supplier
Navigating the global market for label suppliers can be a daunting task for international B2B buyers, especially those operating in diverse regions such as Africa, South America, the Middle East, and Europe. With an ever-expanding range of label types and applications—from product labeling to logistics and compliance—companies face the critical challenge of sourcing the right labels that meet their specific needs while maintaining quality and cost-effectiveness. This guide serves as a comprehensive resource for buyers looking to make informed decisions in this complex landscape.
Throughout this guide, we will explore various types of labels, including adhesive, thermal, and custom options, alongside their respective applications across multiple industries. Additionally, we will provide actionable insights on how to effectively vet suppliers, ensuring that you partner with reliable manufacturers who can deliver both quality and service. Understanding cost structures and pricing models will also be a focal point, empowering you to negotiate better terms and ensure your budget aligns with your operational goals.
By equipping international B2B buyers with essential knowledge and strategic tips, this guide aims to simplify the sourcing process. Whether you are based in Indonesia, the UK, or elsewhere, our insights will help you navigate the global label supply chain with confidence, ultimately enhancing your business operations and product offerings.
Understanding label supplier Types and Variations
Type Name | Key Distinguishing Features | Primary B2B Applications | Brief Pros & Cons for Buyers |
---|---|---|---|
Custom Label Suppliers | Tailored solutions, diverse materials, unique designs | Product branding, promotional items | Pros: High personalization, brand uniqueness. Cons: Higher costs, longer lead times. |
Thermal Transfer Suppliers | Specialize in thermal printing technology, durable labels | Logistics, shipping, inventory management | Pros: Cost-effective for high-volume needs. Cons: Limited design flexibility. |
Digital Label Suppliers | Advanced printing technology, quick turnaround, short runs | Specialty products, limited edition items | Pros: Ideal for small batches, high-quality graphics. Cons: Potentially higher per-unit cost. |
Eco-Friendly Label Suppliers | Focus on sustainable materials and processes | Organic products, environmentally conscious brands | Pros: Aligns with sustainability goals, appealing to eco-conscious consumers. Cons: May have limited options and higher prices. |
Industrial Label Suppliers | Heavy-duty materials, specialized for harsh environments | Manufacturing, chemical industries | Pros: Durable and long-lasting. Cons: May lack aesthetic appeal for consumer goods. |
What are the Characteristics of Custom Label Suppliers?
Custom label suppliers offer tailored solutions that cater to specific branding needs. They utilize diverse materials and unique designs, allowing businesses to create labels that align with their brand identity. These suppliers are suitable for companies looking to enhance their product visibility and customer engagement through distinctive labels. When purchasing, buyers should consider the level of customization offered, production timelines, and costs associated with bespoke designs.
How Do Thermal Transfer Suppliers Operate?
Thermal transfer suppliers focus on labels that are printed using thermal printing technology. This method produces durable labels that can withstand various conditions, making them ideal for logistics and inventory management applications. Businesses that require high-volume labeling solutions often find thermal transfer suppliers to be cost-effective. Key purchasing considerations include the volume of labels needed and the specific durability requirements for the labels.
What Makes Digital Label Suppliers Unique?
Digital label suppliers leverage advanced printing technology to produce high-quality labels quickly and efficiently. They are particularly well-suited for businesses that require short runs or specialty products, as they can accommodate a variety of designs without the need for extensive setup. While the initial per-unit cost may be higher, the ability to produce small batches can lead to cost savings in inventory management. Buyers should evaluate their design needs and volume requirements when considering digital label suppliers.
Why Choose Eco-Friendly Label Suppliers?
Eco-friendly label suppliers prioritize sustainability by using environmentally friendly materials and processes. These suppliers are particularly appealing to businesses in the organic and natural product sectors, as they align with the growing consumer demand for sustainable practices. While eco-friendly labels may come at a premium and offer fewer options, they provide significant value for brands looking to enhance their environmental credentials. Buyers should assess the sustainability certifications of the materials used and the overall impact on their brand image.
What Are the Benefits of Industrial Label Suppliers?
Industrial label suppliers specialize in creating heavy-duty labels designed for use in harsh environments, such as manufacturing and chemical industries. These labels are built to be durable and long-lasting, ensuring they remain intact in challenging conditions. While they may lack aesthetic appeal compared to consumer-focused labels, their robustness makes them indispensable for industrial applications. Buyers should focus on the specific durability and compliance requirements of their industry when selecting an industrial label supplier.
Related Video: WHMIS 2015 – Supplier Labeling
Key Industrial Applications of label supplier
Industry/Sector | Specific Application of label supplier | Value/Benefit for the Business | Key Sourcing Considerations for this Application |
---|---|---|---|
Food and Beverage | Product labeling for compliance and branding | Ensures regulatory compliance and enhances brand recognition | Quality of materials, compliance with local regulations, design customization options |
Pharmaceuticals | Serialization and tracking labels | Improves traceability and reduces counterfeiting risks | Compliance with international standards, security features, integration with tracking systems |
Logistics and Supply Chain | Shipping and inventory management labels | Streamlines operations and reduces errors in shipping | Durability, weather resistance, barcode compatibility, and scalability |
Consumer Electronics | Product information and warranty labels | Enhances customer trust and provides essential product information | Material quality, design flexibility, and adherence to international standards |
Chemicals and Hazardous Materials | Safety and hazard warning labels | Protects workers and complies with safety regulations | Compliance with GHS (Globally Harmonized System), durability under harsh conditions, customization options |
How is ‘label supplier’ used in the Food and Beverage Industry?
In the food and beverage sector, label suppliers provide essential product labeling that adheres to local and international food safety regulations. These labels must include nutritional information, ingredients, and allergen warnings, ensuring compliance with legislation in various regions. For international B2B buyers, sourcing labels that meet specific regulatory standards is crucial, as these requirements can vary significantly between countries. High-quality, durable materials are also important to withstand various storage conditions.
What role do label suppliers play in Pharmaceuticals?
Label suppliers in the pharmaceutical industry focus on serialization and tracking labels that enhance product traceability. These labels are vital for preventing counterfeiting and ensuring patient safety. International buyers must consider compliance with stringent regulations, such as those imposed by the FDA or EMA, which dictate label accuracy and security features. Additionally, suppliers should provide integration capabilities with existing tracking systems to streamline operations.
How do label suppliers optimize logistics and supply chain operations?
In logistics and supply chain management, label suppliers offer shipping and inventory management labels that help streamline processes and minimize errors. These labels can include barcodes and QR codes that facilitate real-time tracking of shipments. For international B2B buyers, sourcing labels that are durable and weather-resistant is essential, particularly for shipments that may encounter harsh environments. Compatibility with various barcode scanning systems is also a critical consideration.
Why are labels important for Consumer Electronics?
In the consumer electronics sector, label suppliers provide product information and warranty labels that enhance customer trust and convey essential information about the product. These labels often include QR codes that link to online resources, enhancing the customer experience. Buyers should prioritize sourcing labels that are made from high-quality materials to ensure longevity and adherence to international standards, as these products often face rigorous testing and scrutiny.
How do label suppliers address safety in Chemicals and Hazardous Materials?
Label suppliers play a crucial role in the chemicals and hazardous materials industry by providing safety and hazard warning labels that protect workers and comply with safety regulations. These labels must adhere to the Globally Harmonized System (GHS) standards, ensuring that they communicate hazards effectively. Buyers in this sector should focus on sourcing labels that are durable and resistant to chemicals, as well as customizable to meet specific safety requirements in different regions.
Related Video: LABORATORY APPARATUS AND THEIR USES
3 Common User Pain Points for ‘label supplier’ & Their Solutions
Scenario 1: Inconsistent Label Quality Across Suppliers
The Problem:
B2B buyers often face the challenge of inconsistent label quality when sourcing from multiple suppliers. This inconsistency can lead to branding issues, operational inefficiencies, and customer dissatisfaction. For example, a manufacturer in South America may find that labels sourced from different suppliers vary in color accuracy, material durability, or adhesive performance. This not only affects the product’s visual appeal but also raises concerns about brand integrity and customer trust, particularly in competitive markets.
The Solution:
To mitigate this problem, buyers should adopt a standardized quality assurance process when selecting label suppliers. Start by establishing clear specifications for label requirements, including material types, adhesive properties, and color matching standards. It’s crucial to communicate these standards to potential suppliers during the sourcing process. Additionally, conducting thorough quality audits and requesting samples before placing large orders can help ensure consistency. Implementing a periodic review of supplier performance based on these quality metrics will also help in maintaining high standards and building long-term partnerships with reliable suppliers.
Scenario 2: Difficulty in Meeting Regulatory Compliance for Labels
The Problem:
International B2B buyers, particularly those in industries like food and pharmaceuticals, often struggle with ensuring that their labels comply with varying regional regulations. For instance, a European company exporting products to Africa may find that the labeling requirements differ significantly, including language, ingredient disclosures, and safety warnings. Non-compliance can lead to hefty fines, product recalls, and damage to reputation, creating a significant barrier to market entry.
The Solution:
To effectively navigate regulatory compliance, buyers should invest in thorough research on the labeling laws in each target market. Collaborating with legal experts or consultants who specialize in international trade can provide invaluable insights into specific requirements. Additionally, engaging with label suppliers who have experience in your target markets can streamline the process. They should offer guidance on meeting local regulations and provide templates or design services that incorporate necessary information. Regularly updating this knowledge base will help buyers stay compliant as regulations evolve.
Scenario 3: Challenges in Label Design and Customization
The Problem:
Many B2B buyers encounter difficulties when it comes to label design and customization. Custom labels are essential for branding, but the process can be fraught with challenges, such as limited design capabilities or a lack of understanding of printing technologies. A company in Africa seeking to launch a new product line may find it hard to create labels that are not only visually appealing but also functional and compliant with local standards.
The Solution:
To overcome these design challenges, buyers should partner with label suppliers that offer comprehensive design services. This includes access to experienced graphic designers who understand both market trends and printing technologies. Buyers should provide detailed input regarding their brand vision, target audience, and specific requirements for the labels. Utilizing digital mockups can also facilitate the design process, allowing for real-time feedback and adjustments before printing. Additionally, opting for suppliers that offer flexible printing options—such as digital printing—can enhance customization capabilities, enabling quick turnaround times for new designs without compromising quality.
Strategic Material Selection Guide for label supplier
When selecting materials for labels, international B2B buyers must consider various factors that influence both performance and compliance. Here, we analyze four common materials used in label production: paper, vinyl, polyester, and polypropylene. Each material has distinct properties, advantages, disadvantages, and suitability for different applications, particularly relevant to buyers from Africa, South America, the Middle East, and Europe.
What Are the Key Properties of Paper Labels?
Paper labels are a popular choice due to their versatility and cost-effectiveness. They typically have a temperature rating of up to 70°C and are suitable for indoor applications. However, they are not inherently water-resistant, which limits their use in humid environments.
Pros and Cons:
– Advantages: Cost-effective, easy to print, and available in various finishes (e.g., matte, gloss).
– Disadvantages: Limited durability, susceptible to moisture damage, and not ideal for outdoor use.
Impact on Application:
Paper labels are best suited for products with short shelf lives or indoor use, such as food packaging or retail items. Buyers should ensure that the paper used complies with food safety standards, particularly in regions with strict regulations.
How Does Vinyl Compare for Label Applications?
Vinyl is a synthetic material known for its durability and weather resistance, making it ideal for outdoor applications. It can withstand temperatures ranging from -20°C to 80°C and offers excellent resistance to chemicals and UV light.
Pros and Cons:
– Advantages: Highly durable, water-resistant, and suitable for outdoor use.
– Disadvantages: Higher cost compared to paper and can be more complex to manufacture.
Impact on Application:
Vinyl labels are commonly used for products exposed to harsh conditions, such as automotive parts or outdoor equipment. International buyers should check for compliance with regional standards like ASTM for durability.
What Are the Benefits of Polyester Labels?
Polyester labels are known for their strength and resistance to tearing, making them suitable for high-demand applications. They can endure temperatures from -40°C to 120°C and are resistant to chemicals, moisture, and UV light.
Pros and Cons:
– Advantages: Excellent durability and resistance to various environmental factors.
– Disadvantages: Higher manufacturing complexity and cost.
Impact on Application:
These labels are ideal for industrial applications, such as equipment labeling or chemical containers. Buyers should consider compliance with international standards, including DIN for chemical resistance.
Why Choose Polypropylene for Labeling Needs?
Polypropylene is a versatile plastic material that offers a good balance between cost and performance. It has a temperature range of -20°C to 80°C and is resistant to moisture and chemicals.
Pros and Cons:
– Advantages: Cost-effective, lightweight, and suitable for a variety of applications.
– Disadvantages: Less durable than polyester and may not withstand extreme conditions.
Impact on Application:
Polypropylene labels are often used for packaging and consumer goods. Buyers should ensure that the material meets local regulations regarding recyclability and environmental impact.
Summary Table of Material Selection for Label Suppliers
Material | Typical Use Case for label supplier | Key Advantage | Key Disadvantage/Limitation | Relative Cost (Low/Med/High) |
---|---|---|---|---|
Paper | Food packaging, retail items | Cost-effective and easy to print | Limited durability and moisture resistance | Low |
Vinyl | Outdoor products, automotive parts | Highly durable and weather-resistant | Higher cost and manufacturing complexity | Med |
Polyester | Industrial applications, chemical containers | Excellent durability and chemical resistance | Higher complexity and cost | High |
Polypropylene | Packaging, consumer goods | Cost-effective and versatile | Less durable than polyester | Med |
By understanding the properties, advantages, and limitations of these materials, international B2B buyers can make informed decisions that align with their specific needs and compliance requirements.
In-depth Look: Manufacturing Processes and Quality Assurance for label supplier
What Are the Key Stages in the Manufacturing Process of Labels?
The manufacturing process for labels typically involves several crucial stages that ensure the final product meets quality and functionality standards. Understanding these stages can help B2B buyers make informed decisions when selecting a label supplier.
Material Preparation: What Materials Are Used in Label Manufacturing?
The first step in label manufacturing is the preparation of materials. Common materials used include paper, vinyl, polyester, and polypropylene. Each material has unique properties that affect durability, printability, and adhesion. For instance, vinyl is often used for outdoor labels due to its weather resistance, while paper may be preferred for temporary or indoor applications. Suppliers often source materials from certified vendors to ensure quality and compliance with international standards.
Forming: How Are Labels Formed?
Once materials are prepared, the next stage is forming. This involves cutting the material into the desired shapes and sizes using techniques such as die-cutting or laser cutting. Advanced equipment can produce intricate designs and shapes, which is particularly valuable for branding purposes. The forming stage also includes the application of adhesives, which is critical for ensuring that labels stick effectively to their intended surfaces.
Assembly: What Techniques Are Used in Label Assembly?
The assembly stage includes the integration of various components, such as additional protective layers or embellishments like foil stamping or embossing. This stage may also involve printing, where ink or digital printing techniques are employed to apply designs, logos, and other necessary information onto the labels. High-quality printing technologies, such as flexographic or digital printing, can enhance the visual appeal and functionality of labels.
Finishing: How Is Quality Ensured in the Finishing Stage?
The final stage of manufacturing is finishing, which includes processes like laminating or varnishing to protect the printed surface from wear and tear. This stage is crucial for ensuring that labels maintain their quality over time, especially in challenging environments. Quality checks during this stage can identify any defects before the labels are shipped, which is vital for maintaining customer satisfaction.
What Quality Assurance Standards Should International Buyers Consider?
Quality assurance is a critical component of label manufacturing, especially for international B2B buyers. Understanding the relevant standards can help buyers assess the credibility of their suppliers.
Which International Standards Are Relevant for Label Suppliers?
One of the most recognized international quality standards is ISO 9001, which outlines criteria for a quality management system. Suppliers certified under this standard demonstrate their commitment to consistent quality and customer satisfaction. Additionally, industry-specific certifications such as CE marking (for products sold in the European Economic Area) and API (American Petroleum Institute) standards for labels used in the oil and gas industry can also be significant indicators of quality.
What Are the Key Quality Control Checkpoints in the Manufacturing Process?
Quality control (QC) checkpoints are essential for ensuring that labels meet both customer and regulatory requirements. The main QC checkpoints include:
Incoming Quality Control (IQC)
This initial checkpoint focuses on raw materials. Suppliers perform inspections to ensure that incoming materials meet specified criteria before they are used in production. This may include checking material specifications, certifications, and physical inspections.
In-Process Quality Control (IPQC)
During the manufacturing process, IPQC measures various parameters, such as print quality, adhesion strength, and dimensional accuracy. This ongoing monitoring allows for immediate corrections and adjustments, minimizing waste and ensuring that the final product meets quality standards.
Final Quality Control (FQC)
Before shipment, FQC is performed to verify that the finished labels meet all specifications and standards. This may involve visual inspections, adhesion tests, and durability assessments. A comprehensive FQC process can help identify any defects that may have been overlooked during earlier checkpoints.
How Can B2B Buyers Verify Supplier Quality Control Practices?
For B2B buyers, verifying a supplier’s QC practices is essential for ensuring product reliability. Here are several actionable steps:
Conduct Supplier Audits
Regular audits of the supplier’s facilities can provide insights into their manufacturing processes and quality control measures. Buyers should look for a structured audit program that evaluates compliance with ISO 9001 and other relevant standards.
Request Quality Assurance Reports
Buyers should ask suppliers for quality assurance documentation, including test results and certifications. These reports should detail the QC processes undertaken, the results of inspections, and any corrective actions taken in response to defects.
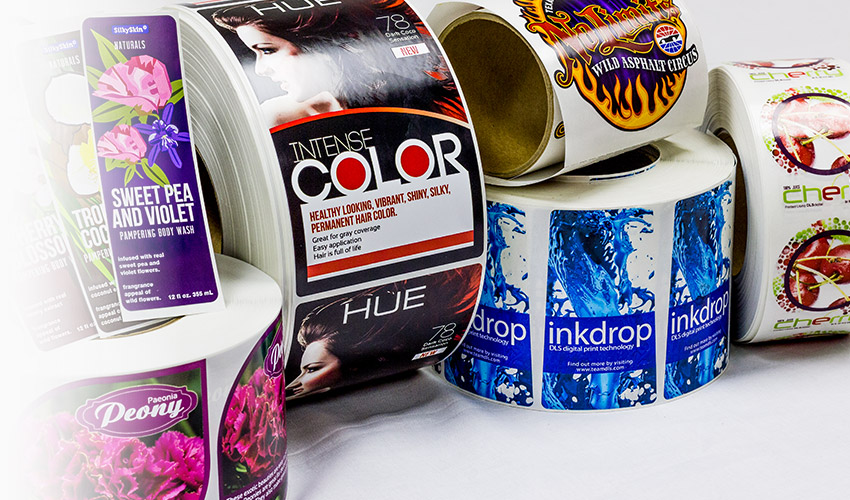
A stock image related to label supplier.
Utilize Third-Party Inspections
Engaging third-party inspection services can provide an unbiased assessment of a supplier’s quality control measures. Third-party inspectors can conduct audits, verify compliance with industry standards, and provide detailed reports that help buyers make informed decisions.
What Nuances Should International B2B Buyers Be Aware of Regarding Quality Control?
International B2B buyers, particularly from Africa, South America, the Middle East, and Europe, should be aware of specific nuances in quality control that can impact their purchasing decisions:
Regulatory Compliance
Different regions may have unique regulatory requirements that affect label specifications. Buyers should ensure that their suppliers are compliant with local regulations, especially when exporting or importing goods.
Cultural Differences in Quality Expectations
Cultural perceptions of quality can vary significantly across regions. Buyers should communicate clearly with suppliers about their quality expectations and ensure that both parties have a mutual understanding of what constitutes an acceptable product.
Logistical Considerations
Supply chain logistics can also influence quality control. Buyers should assess the supplier’s ability to maintain quality throughout the shipping process, particularly for labels that may be sensitive to environmental factors such as temperature or humidity.
By understanding the manufacturing processes and quality assurance practices specific to label suppliers, B2B buyers can make more informed decisions, ensuring that they partner with reliable suppliers who meet their quality standards.
Practical Sourcing Guide: A Step-by-Step Checklist for ‘label supplier’
This guide serves as a practical checklist for international B2B buyers looking to source label suppliers effectively. By following these steps, you can ensure that your procurement process is thorough, efficient, and aligned with your business needs.
Step 1: Define Your Technical Specifications
Before reaching out to potential suppliers, clearly outline your requirements for labels. This includes specifications such as size, material, adhesive type, and printing methods.
– Why it matters: Defining these details helps you communicate your needs effectively and ensures suppliers can meet your expectations.
– Look for: Any specific regulatory requirements relevant to your industry or region, especially in regions like Africa and the Middle East where compliance can vary significantly.
Step 2: Conduct Market Research
Investigate the label supply market to identify potential suppliers. Use online directories, trade shows, and industry forums to gather a list of companies.
– Why it matters: Understanding the market landscape allows you to compare suppliers based on reputation, capabilities, and pricing.
– Look for: Reviews and testimonials from other B2B buyers, particularly those in your industry or geographical area.
Step 3: Evaluate Potential Suppliers
Once you have a list of potential suppliers, assess their credibility and capabilities. Request company profiles, case studies, and references from existing clients.
– Why it matters: A thorough evaluation minimizes the risk of partnering with unreliable suppliers who may not deliver quality products.
– Look for: Evidence of previous work that aligns with your requirements, such as similar projects or clients within your sector.
Step 4: Verify Supplier Certifications
Ensure that the suppliers you consider have the necessary certifications relevant to your industry. This may include ISO certifications or compliance with local regulations.
– Why it matters: Certifications can indicate a supplier’s commitment to quality and adherence to industry standards.
– Look for: Documentation of certifications and any third-party audits that validate their compliance.
Step 5: Request Samples
Before making a bulk order, request samples of the labels to evaluate quality and durability. This step is crucial for ensuring that the final product meets your expectations.
– Why it matters: Physical samples allow you to assess the material, printing quality, and overall finish before committing to a large purchase.
– Look for: Consistency in quality across samples, as well as adherence to the specifications you defined in Step 1.
Step 6: Negotiate Terms and Pricing
Once you’ve selected a supplier, engage in negotiations to agree on pricing, delivery timelines, and payment terms.
– Why it matters: Effective negotiation can lead to better pricing and terms that suit your budget and operational needs.
– Look for: Flexibility in terms of order quantities and payment options, especially if you’re a smaller business or a startup.
Step 7: Establish a Communication Plan
After finalizing your supplier, set up a clear communication strategy to ensure ongoing dialogue throughout the procurement process.
– Why it matters: Regular communication helps address any issues quickly and ensures that both parties are aligned on expectations.
– Look for: A dedicated point of contact within the supplier’s organization who can provide updates and handle inquiries.
By following this checklist, B2B buyers can navigate the complexities of sourcing label suppliers, ensuring that they find a partner that meets their specific needs and contributes to their business success.
Comprehensive Cost and Pricing Analysis for label supplier Sourcing
What Are the Key Cost Components for Label Supplier Sourcing?
When sourcing labels, understanding the cost structure is crucial for making informed purchasing decisions. The primary components that contribute to the overall cost include:
-
Materials: The choice of material—whether paper, vinyl, or polyester—greatly impacts the pricing. High-quality materials often come with a premium, but they can enhance durability and appearance.
-
Labor: Labor costs vary significantly based on the region. In areas with higher wages, such as Europe, labor can constitute a larger share of the overall cost compared to regions with lower labor costs.
-
Manufacturing Overhead: This includes utilities, facility maintenance, and equipment depreciation. Efficient production processes can help reduce these costs.
-
Tooling: Custom tooling can be a significant upfront investment, especially for unique label shapes or designs. Understanding the tooling costs associated with your order is essential for accurate budgeting.
-
Quality Control (QC): Implementing robust QC processes ensures product consistency and reduces the risk of defects, which can save costs in the long run.
-
Logistics: Shipping and handling fees can fluctuate based on distance, shipping method, and the volume of labels being ordered. Understanding the logistics involved in your supply chain is vital for accurate cost projections.
-
Margin: Supplier profit margins can vary widely based on their pricing strategies and market positioning. Always inquire about margin expectations to gauge the fairness of the pricing.
How Do Price Influencers Affect Label Supplier Costs?
Several factors can influence the pricing of labels, making it essential for buyers to consider these when negotiating:
-
Volume and Minimum Order Quantities (MOQ): Larger orders often qualify for bulk pricing discounts. Understanding the MOQ can help you determine the best order size for cost savings.
-
Specifications and Customization: Custom designs, special finishes, or unique sizes can increase costs. Ensure you have a clear understanding of the specifications required before requesting quotes.
-
Materials and Quality Certifications: Labels that require specific certifications (e.g., food safety, environmental standards) may incur additional costs. Always verify if these certifications are necessary for your application.
-
Supplier Factors: Supplier reputation, reliability, and location can impact pricing. A well-established supplier may charge more but could offer better quality and service.
-
Incoterms: The terms of shipment (like FOB or CIF) can significantly affect the total cost. Buyers should be familiar with Incoterms to understand their responsibilities regarding shipping and customs duties.
What Are Some Effective Buyer Tips for Sourcing Labels?
International B2B buyers, especially from Africa, South America, the Middle East, and Europe, should consider the following strategies to optimize their sourcing experience:
-
Negotiation: Engage in open discussions with suppliers about pricing and terms. Don’t hesitate to ask for discounts, especially for larger orders or long-term contracts.
-
Cost-Efficiency: Look for ways to reduce costs without compromising quality. Consider alternative materials or simpler designs that could lower manufacturing expenses.
-
Total Cost of Ownership (TCO): Evaluate the long-term costs associated with labels, including maintenance, durability, and replacement rates. This holistic view can help justify higher initial costs for superior quality.
-
Pricing Nuances for International Buyers: Be aware of currency fluctuations and import duties, which can affect the final cost of your labels. Establishing a clear understanding of these factors can help mitigate unexpected expenses.
Disclaimer on Indicative Prices
While this analysis provides a framework for understanding costs and pricing, actual prices can vary widely based on specific project requirements, supplier capabilities, and market conditions. Always request detailed quotations tailored to your unique needs to ensure accurate budgeting.
Alternatives Analysis: Comparing label supplier With Other Solutions
Understanding Alternative Solutions to Label Suppliers
In the dynamic landscape of international B2B transactions, businesses often seek to optimize their labeling processes to enhance efficiency, reduce costs, and improve product visibility. While traditional label suppliers offer a range of services, it is essential to evaluate alternative solutions that may better suit specific operational needs. This analysis will compare ‘label supplier’ with two viable alternatives: in-house labeling systems and digital printing solutions.
Comparison Table
Comparison Aspect | Label Supplier | In-House Labeling System | Digital Printing Solutions |
---|---|---|---|
Performance | High-quality labels | Variable quality | High-quality, customizable |
Cost | Moderate to high | Initial investment high | Variable, often lower in bulk |
Ease of Implementation | Quick setup | Requires training | Minimal setup, user-friendly |
Maintenance | Low (outsourced) | Moderate (ongoing costs) | Low (software updates) |
Best Use Case | Large volume orders | Custom, small batch needs | On-demand, short runs |
What Are the Pros and Cons of In-House Labeling Systems?
In-house labeling systems allow businesses to create and apply their labels on-site. This solution offers flexibility and control over the labeling process, enabling companies to quickly adapt to changing product lines or regulatory requirements. However, it often requires significant initial investment in equipment and training. Additionally, the quality of labels may vary depending on the skill of the personnel and the capabilities of the equipment used. For companies with a diverse product range or those needing frequent label updates, in-house solutions can be a viable choice despite the associated costs and training requirements.
How Do Digital Printing Solutions Compare?
Digital printing solutions present a modern alternative to traditional label suppliers. They allow businesses to produce high-quality, customized labels on-demand, which is particularly beneficial for short-run projects or products with frequent design changes. The cost-effectiveness of digital printing increases with volume, making it an attractive option for businesses looking to minimize waste. However, the initial setup can be complex, and ongoing software updates may be necessary. This solution is ideal for companies that require flexibility and quick turnaround times without the need for large quantities.
Conclusion: How Can B2B Buyers Choose the Right Labeling Solution?
When selecting a labeling solution, B2B buyers must consider their specific operational needs, budget constraints, and the nature of their products. If the business typically manages large volume orders, a traditional label supplier may be the most efficient choice. Conversely, for organizations that require flexibility and customization, in-house labeling systems or digital printing solutions could prove more advantageous. Ultimately, the decision should align with the company’s strategic goals, ensuring that the chosen solution enhances productivity while maintaining cost-effectiveness.
Essential Technical Properties and Trade Terminology for label supplier
What Are the Essential Technical Properties of Labels in B2B Transactions?
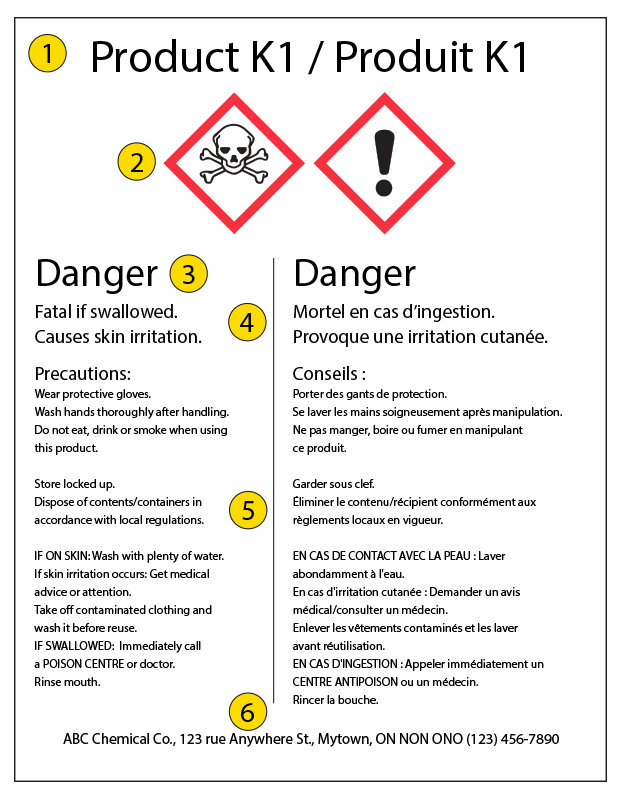
A stock image related to label supplier.
When sourcing labels from suppliers, understanding the technical properties is crucial for ensuring product quality and compliance with industry standards. Below are critical specifications that international B2B buyers should consider:
1. Material Grade
The material used for labels can vary widely, including paper, vinyl, polyester, and polypropylene. Each material has its unique properties that affect durability, printability, and suitability for specific applications. For example, vinyl labels are often used for outdoor applications due to their weather-resistant properties, while paper labels are suitable for indoor use. Choosing the right material is essential for product longevity and performance.
2. Adhesive Type
Adhesive properties determine how well a label sticks to its intended surface. There are permanent, removable, and repositionable adhesives, each serving different purposes. Permanent adhesives are ideal for products that require long-lasting labeling, while removable adhesives are suitable for temporary applications, such as promotions or seasonal products. Understanding adhesive types helps in selecting the right label for your specific needs.
3. Tolerance
Tolerance refers to the allowable variation in label dimensions. In B2B transactions, precise tolerances are vital for ensuring that labels fit properly on products. For example, a tolerance of ±0.5 mm may be acceptable for some products, while others may require tighter tolerances. Ensuring that your supplier can meet these specifications can prevent costly production errors.
4. Print Quality
Print quality is assessed based on resolution (measured in DPI – dots per inch) and color fidelity. High-quality labels should have sharp images and vibrant colors that are true to the brand. In B2B contexts, labels often serve as a critical marketing tool, so ensuring high print quality can enhance brand perception and customer satisfaction.
5. Finish
Label finishes can include matte, gloss, or textured options. The finish affects not only the aesthetic appeal but also the functionality of the label. For instance, gloss finishes can enhance color vibrancy but may be more prone to scratching. Understanding the implications of different finishes helps in making informed decisions based on the label’s intended use.
What Are Common Trade Terms in the Label Supply Industry?
Familiarity with industry jargon is essential for effective communication and negotiation with suppliers. Here are some common terms you should know:
1. OEM (Original Equipment Manufacturer)
OEM refers to companies that manufacture products or components that are sold under another company’s brand name. In the labeling industry, this could mean that a supplier produces labels designed for a specific brand but does not sell them under their own name. Understanding OEM relationships can help buyers assess quality and reliability.
2. MOQ (Minimum Order Quantity)
MOQ is the minimum number of units a supplier requires for an order. This term is crucial for B2B buyers as it affects inventory management and costs. Knowing the MOQ helps businesses plan their purchases effectively and avoid excess inventory or stockouts.
3. RFQ (Request for Quotation)
An RFQ is a document sent to suppliers requesting pricing and terms for specific products. It is a vital step in the procurement process, allowing buyers to compare offers from different suppliers. A well-structured RFQ can lead to better pricing and terms, benefiting the buyer in the long run.
4. Incoterms (International Commercial Terms)
Incoterms are standardized trade terms that define the responsibilities of buyers and sellers in international transactions. They clarify who is responsible for shipping, insurance, and tariffs. Familiarity with Incoterms helps buyers manage risks and understand their obligations in cross-border transactions.
5. Lead Time
Lead time refers to the time taken from placing an order until the product is delivered. In the labeling industry, understanding lead times is crucial for planning production schedules and ensuring timely product launches. Buyers should always inquire about lead times to avoid delays.
By mastering these technical properties and trade terms, B2B buyers can make more informed decisions, ensuring they choose the right label suppliers to meet their specific needs while optimizing costs and efficiency.
Navigating Market Dynamics and Sourcing Trends in the label supplier Sector
What Are the Current Market Dynamics and Key Trends in the Label Supplier Sector?
The label supplier sector is undergoing significant transformation driven by global market dynamics and technological advancements. A key trend is the increasing demand for customized labeling solutions, which has been fueled by the rise of e-commerce and the need for brands to differentiate themselves. International B2B buyers, particularly from Africa, South America, the Middle East, and Europe, are seeking suppliers that can provide agile and responsive service, allowing for quick adaptations to changing market demands.
Moreover, technological innovations such as digital printing and automation are reshaping sourcing strategies. Digital printing, in particular, allows for shorter runs and more personalized labels, which is essential for small to medium enterprises looking to scale without incurring high inventory costs. This shift towards digital solutions is complemented by data analytics, enabling suppliers to forecast trends and manage inventory more efficiently.
Another notable trend is the increasing importance of integrated supply chains. Buyers are prioritizing suppliers who can offer end-to-end solutions, from design to delivery, facilitating smoother operations and reducing lead times. This is especially pertinent in regions like Europe and the Middle East, where regulatory compliance and quality assurance are paramount. As such, buyers are encouraged to evaluate suppliers based on their technological capabilities and integration within the supply chain.
How Is Sustainability Impacting Sourcing Decisions in the Label Supplier Sector?
Sustainability is no longer just a buzzword; it is becoming a critical factor in the decision-making processes of B2B buyers in the label supplier sector. The environmental impact of packaging materials has prompted companies to reassess their sourcing strategies. Buyers from Africa, South America, and Europe are increasingly looking for suppliers who prioritize eco-friendly materials and practices. This includes sourcing from manufacturers that utilize recycled materials and those that adopt sustainable production methods.
Ethical sourcing practices are also gaining traction. International buyers are more inclined to partner with suppliers who maintain transparency in their supply chains, ensuring fair labor practices and minimizing environmental harm. Certifications such as FSC (Forest Stewardship Council) and ISO 14001 (Environmental Management) are becoming essential for suppliers aiming to establish credibility in the market.
Furthermore, the move towards biodegradable and compostable labeling solutions is reshaping product offerings. Buyers should actively seek suppliers who can provide these innovative materials, as they not only align with sustainability goals but also appeal to environmentally-conscious consumers.
What Is the Evolution of the Label Supplier Sector and Its Relevance to B2B Buyers?
The label supplier sector has evolved significantly over the past few decades, transitioning from traditional printing methods to advanced digital technologies. Initially dominated by large-scale manufacturers, the market has diversified, with many smaller players entering the space, particularly in emerging markets. This shift has enabled greater competition and innovation, providing buyers with a wider array of options.
Historically, labels served a functional purpose, mainly for identification and compliance. However, as branding and marketing have become increasingly crucial, labels now play a pivotal role in consumer engagement. For B2B buyers, understanding this evolution is vital, as it highlights the need to partner with suppliers that not only meet technical specifications but also align with branding strategies and sustainability initiatives.
In conclusion, navigating the label supplier sector requires international B2B buyers to stay informed about market dynamics, prioritize sustainability, and consider the historical context of the industry to make informed sourcing decisions.
Frequently Asked Questions (FAQs) for B2B Buyers of label supplier
-
How do I choose the right label supplier for my business needs?
Choosing the right label supplier involves assessing their capabilities in terms of product quality, customization options, and delivery times. Start by identifying your specific labeling requirements, such as materials, sizes, and adhesive types. Research potential suppliers by looking at their portfolio, customer reviews, and case studies. It’s also beneficial to request samples to evaluate quality. Finally, consider their customer service responsiveness and willingness to collaborate on unique projects, as these factors can significantly influence your long-term relationship. -
What are the key factors to consider when vetting international label suppliers?
When vetting international label suppliers, focus on their compliance with industry standards and certifications, such as ISO or FDA regulations. Evaluate their production capabilities, including technology and equipment used, to ensure they can meet your volume and quality requirements. Additionally, assess their financial stability and reputation in the industry through references and reviews. Understanding their logistics capabilities, such as shipping methods and delivery timelines, is crucial to prevent delays in your supply chain. -
What customization options should I look for in label suppliers?
Look for suppliers that offer a wide range of customization options, including material types, sizes, colors, and finishes. Ensure they can accommodate your design requirements, such as printing methods (digital, flexographic, etc.) and artwork specifications. Additionally, inquire about their ability to produce variable data labels, which can be essential for tracking and compliance. A supplier with a strong design support team can help you refine your label concepts and ensure they align with branding guidelines. -
What is the typical minimum order quantity (MOQ) for label suppliers?
Minimum order quantities (MOQs) for label suppliers can vary significantly based on the supplier’s production capabilities and your specific requirements. Generally, MOQs range from 1,000 to 10,000 labels, but some suppliers may offer lower MOQs for custom designs. It’s advisable to discuss your needs with potential suppliers to find one that aligns with your order volume and budget. Understanding the pricing structure related to different order quantities can also help you optimize your purchasing decisions. -
What payment terms are common with international label suppliers?
Payment terms can vary widely among international label suppliers, but common practices include upfront deposits (typically 30-50%) with the balance due upon delivery. Some suppliers may offer net terms (e.g., net 30 or net 60 days) for established customers. It’s essential to clarify these terms early in negotiations to ensure they fit your cash flow requirements. Additionally, consider discussing payment methods that offer buyer protection, such as letters of credit, to mitigate risks in international transactions. -
How can I ensure quality assurance (QA) with my label supplier?
To ensure quality assurance with your label supplier, establish clear quality standards and specifications upfront. Request a quality control plan that outlines the supplier’s QA processes, including inspections at various production stages. It’s also beneficial to conduct regular audits or inspections, especially for large orders. Consider implementing a sample approval process before full production begins. Building a collaborative relationship with your supplier can foster open communication regarding quality expectations and any potential issues that may arise. -
What logistics considerations should I keep in mind when sourcing labels internationally?
When sourcing labels internationally, consider logistics factors such as shipping methods, lead times, and customs regulations. Evaluate the supplier’s shipping options to ensure they can meet your delivery deadlines. Understanding potential import duties and taxes is crucial to accurately calculating total costs. Additionally, establish clear communication regarding tracking shipments and handling potential delays. It’s advisable to work with suppliers who have experience in international shipping to streamline the process and minimize disruptions. -
How do I handle disputes or issues with my label supplier?
Handling disputes with your label supplier requires clear communication and documentation. Start by addressing the issue directly with the supplier, presenting any evidence or documentation supporting your claims. Aim for a collaborative resolution by discussing potential solutions, such as reprints or refunds. If direct communication fails, refer to your contract terms for dispute resolution processes, which may include mediation or arbitration. Maintaining a professional demeanor throughout the process can help preserve the business relationship while seeking a fair outcome.
Important Disclaimer & Terms of Use
⚠️ Important Disclaimer
The information provided in this guide, including content regarding manufacturers, technical specifications, and market analysis, is for informational and educational purposes only. It does not constitute professional procurement advice, financial advice, or legal advice.
While we have made every effort to ensure the accuracy and timeliness of the information, we are not responsible for any errors, omissions, or outdated information. Market conditions, company details, and technical standards are subject to change.
B2B buyers must conduct their own independent and thorough due diligence before making any purchasing decisions. This includes contacting suppliers directly, verifying certifications, requesting samples, and seeking professional consultation. The risk of relying on any information in this guide is borne solely by the reader.
Strategic Sourcing Conclusion and Outlook for label supplier
In the evolving landscape of global trade, the importance of strategic sourcing for label suppliers cannot be overstated. By leveraging a well-defined sourcing strategy, international B2B buyers can enhance their supply chain efficiency, reduce costs, and ensure quality. Key takeaways include the need for thorough market research, understanding supplier capabilities, and fostering strong relationships with reliable partners.
How can international buyers optimize their sourcing strategies for labels? By prioritizing suppliers that demonstrate sustainability and innovation, businesses can not only meet regulatory requirements but also resonate with the growing consumer demand for environmentally responsible products. Furthermore, diversifying supplier bases across regions like Africa, South America, the Middle East, and Europe can mitigate risks associated with geopolitical uncertainties.
Looking ahead, the label industry is poised for growth, driven by technological advancements and changing market dynamics. International B2B buyers are encouraged to stay proactive in their sourcing approaches, embracing digital tools and analytics to make informed decisions. Engage with suppliers who align with your strategic goals and leverage the opportunities that arise in this dynamic market. Your proactive sourcing decisions today will shape your competitive edge tomorrow.