Discover Top Manufacturers of Electrical Control Panels (2025)
Introduction: Navigating the Global Market for Manufacturers of Electrical Control Panels
In today’s fast-paced industrial landscape, sourcing reliable manufacturers of electrical control panels can pose a significant challenge for international B2B buyers. As industries across Africa, South America, the Middle East, and Europe increasingly adopt automation and sophisticated electrical systems, the demand for high-quality control panels has surged. This guide serves as a comprehensive resource to navigate the complexities of the global market, covering various types of electrical control panels, their diverse applications, and essential supplier vetting processes.
By exploring the intricacies of cost structures and compliance with international standards, this guide empowers buyers to make informed purchasing decisions that align with their operational needs and budget constraints. Understanding the nuances of sourcing custom-built solutions and evaluating potential suppliers based on their certifications, experience, and innovation capabilities will enhance the procurement strategy for businesses in emerging markets like Kenya and established ones in Europe.
Whether you are looking for motor control centers, programmable logic controllers, or tailored power distribution solutions, this guide will equip you with the insights needed to identify reputable manufacturers, ultimately ensuring that your business benefits from the reliability and efficiency of top-tier electrical control panels. Prepare to navigate the global marketplace with confidence and leverage the vast opportunities available in this essential sector.
Understanding Manufacturers of Electrical Control Panels Types and Variations
Type Name | Key Distinguishing Features | Primary B2B Applications | Brief Pros & Cons for Buyers |
---|---|---|---|
Motor Control Centers (MCC) | Centralized control, protection for motors, modular design | Manufacturing, Oil & Gas, Water Treatment | Pros: High efficiency, easy maintenance. Cons: Can be complex and costly. |
Programmable Logic Controller (PLC) | Programmable, flexible, integrates with various systems | Automation, Robotics, Industrial Processes | Pros: Customizable, real-time monitoring. Cons: Requires programming expertise. |
Safety Control Panels | Focus on safety features, emergency shutdown capabilities | Manufacturing, Chemical Processing, Construction | Pros: Enhanced safety, compliance with regulations. Cons: May require regular testing and maintenance. |
Remote Monitoring Panels | Connectivity for remote access, data logging, and alerts | Utilities, Smart Grids, Infrastructure Management | Pros: Improved oversight, proactive maintenance. Cons: Potential cybersecurity risks. |
Custom Control Panels | Tailored solutions to specific customer requirements | OEMs, Specialty Manufacturing, Custom Applications | Pros: Meets unique needs, flexibility in design. Cons: Longer lead times, higher costs. |
What Are Motor Control Centers (MCC) and Their Applications?
Motor Control Centers (MCC) are centralized units designed to control and protect electric motors. They are characterized by their modular design, allowing easy expansion and maintenance. MCCs are extensively used in manufacturing, oil and gas, and water treatment sectors, providing high efficiency and straightforward maintenance. However, they can be complex and costly, requiring careful consideration of the installation and operational costs.
How Do Programmable Logic Controllers (PLC) Enhance Automation?
Programmable Logic Controllers (PLC) are essential for modern automation, providing flexibility and programmability. They can integrate seamlessly with various systems, making them suitable for applications in robotics and industrial processes. Their ability to offer real-time monitoring and customization makes them invaluable for businesses seeking to enhance operational efficiency. However, their complexity requires skilled personnel for programming and maintenance, which can be a drawback for some organizations.
Why Are Safety Control Panels Critical for Compliance?
Safety Control Panels are designed to prioritize safety in industrial settings. They include features such as emergency shutdown capabilities and compliance with safety regulations. These panels are crucial in industries like manufacturing, chemical processing, and construction, where safety is paramount. While they enhance workplace safety, regular testing and maintenance are essential to ensure their effectiveness, which can be a logistical challenge for some companies.
What Benefits Do Remote Monitoring Panels Provide?
Remote Monitoring Panels offer the ability to monitor systems from afar, providing data logging, alerts, and real-time insights. They are increasingly utilized in utilities, smart grids, and infrastructure management, improving oversight and enabling proactive maintenance. Although they enhance operational efficiency, potential cybersecurity risks must be managed, requiring robust security measures to protect sensitive data.
How Do Custom Control Panels Meet Unique Business Needs?
Custom Control Panels are tailored solutions designed to meet specific customer requirements. They are particularly beneficial for OEMs and specialty manufacturing, offering flexibility in design and functionality. While they can effectively address unique needs, buyers should be aware of the longer lead times and potentially higher costs associated with custom solutions. Careful planning and consultation with manufacturers can help mitigate these challenges.
Related Video: Introduction to UL 508A Industrial Electrical Control Panels with PLC
Key Industrial Applications of Manufacturers of Electrical Control Panels
Industry/Sector | Specific Application of Manufacturers of Electrical Control Panels | Value/Benefit for the Business | Key Sourcing Considerations for this Application |
---|---|---|---|
Industrial Automation | Custom Motor Control Centers (MCCs) | Enhanced efficiency and safety in motor operations | Compliance with local standards, customization options |
Oil and Gas | Control Panels for Process Automation | Increased operational reliability and safety | Hazardous location certifications, robust design |
Renewable Energy | Solar Power Control Panels | Optimized energy production and grid integration | Compatibility with existing systems, scalability |
Food and Beverage | Control Panels for Automated Processing Systems | Improved consistency and quality in production processes | Hygiene standards, ease of integration with existing lines |
Infrastructure and Utilities | Power Distribution Panels for Smart Grids | Enhanced energy management and reliability | Adaptability to local infrastructure, regulatory compliance |
How Are Electrical Control Panels Used in Industrial Automation?
In the realm of industrial automation, Custom Motor Control Centers (MCCs) are pivotal. These panels manage and protect electric motors, enhancing operational efficiency. Manufacturers must ensure that their MCCs comply with local safety standards, especially in regions like Africa and South America, where regulations may vary. The ability to customize these panels according to specific motor requirements is crucial for international buyers looking to optimize their operations while adhering to safety protocols.
What Role Do Electrical Control Panels Play in Oil and Gas?
For the oil and gas sector, control panels for process automation are essential for managing complex operations. These panels ensure the safe and efficient operation of drilling and refining processes. Given the hazardous nature of the environment, buyers must prioritize sourcing panels that are certified for use in explosive atmospheres. Reliability is key; thus, manufacturers need to provide robust solutions that can withstand extreme conditions typical in oil and gas applications.
How Do Electrical Control Panels Support Renewable Energy Initiatives?
In the renewable energy sector, particularly solar energy, control panels play a significant role in optimizing energy production. They facilitate the integration of solar power into the grid, ensuring a stable and efficient energy supply. Buyers in this sector must consider compatibility with existing energy systems and the scalability of the control panels to accommodate future growth. Additionally, sustainability in manufacturing processes is becoming increasingly important, especially in Europe and the Middle East.
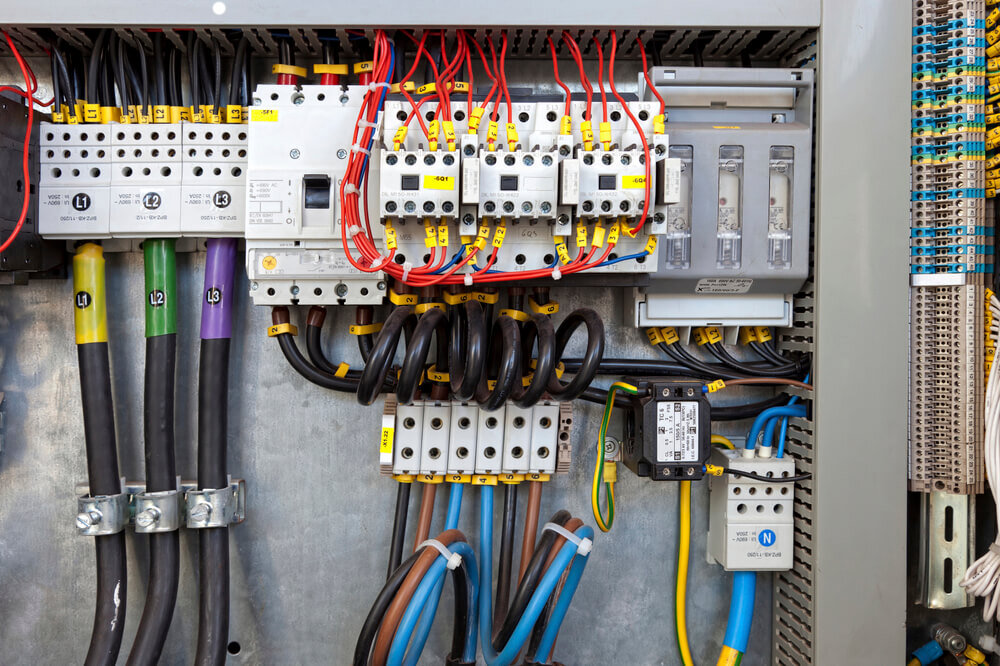
A stock image related to Manufacturers of Electrical Control Panels.
Why Are Control Panels Important in Food and Beverage Processing?
In the food and beverage industry, control panels for automated processing systems are critical for maintaining quality and consistency. These panels help regulate temperature, pressure, and other variables essential for food safety. International buyers should focus on sourcing panels that meet stringent hygiene and safety standards. The ability to integrate these panels seamlessly with existing production lines can significantly enhance operational efficiency, making it easier to meet increasing consumer demands.
How Do Electrical Control Panels Enhance Infrastructure and Utilities?
For infrastructure and utilities, power distribution panels are vital for smart grid management. They enable better energy distribution and management, which is crucial for urban areas experiencing growth. Buyers should look for panels that can adapt to local infrastructure needs and comply with regulatory requirements. The reliability of these panels ensures uninterrupted service, which is essential for maintaining public trust and operational efficiency in utility services.
3 Common User Pain Points for ‘Manufacturers of Electrical Control Panels’ & Their Solutions
Scenario 1: Navigating Compliance and Certification Challenges in Electrical Control Panels
The Problem: International B2B buyers often encounter the daunting task of ensuring that electrical control panels meet varying regional compliance and certification standards. For instance, a manufacturer in Kenya may struggle to understand the requirements set by the Kenya Bureau of Standards (KEBS) while simultaneously trying to source panels that comply with European Union CE marking. This can lead to delays in production, increased costs due to rework, and potential legal issues if panels are not certified for specific markets.
The Solution: To effectively navigate compliance challenges, buyers should prioritize manufacturers who have a proven track record of understanding and meeting international standards. When sourcing, request documentation that certifies compliance with local and international standards (like IEC, UL, and CE). Additionally, engage with manufacturers who offer consultancy services to help interpret and fulfill these requirements. It’s advisable to establish a collaborative relationship with the manufacturer, ensuring they are willing to provide ongoing support for certification processes. This proactive approach not only mitigates compliance risks but also enhances the buyer’s confidence in the panels being sourced.
Scenario 2: Addressing Customization Needs for Diverse Applications
The Problem: Many B2B buyers face the issue of finding manufacturers that can provide customized electrical control panels tailored to specific industrial applications. For example, a food processing plant in Brazil may require panels that can withstand high humidity and temperature variations, while an oil rig in the Middle East may need panels that can operate in extreme conditions. Standardized solutions often fall short, leading to operational inefficiencies and increased maintenance costs.
The Solution: Buyers should seek manufacturers known for their flexibility in customization. Engage in detailed discussions about the specific needs of your application, including environmental conditions, load requirements, and operational capabilities. A thorough requirements analysis will help ensure that the manufacturer understands your needs. Additionally, request prototypes or pilot panels to test before committing to larger orders. This not only verifies performance but also builds trust between the buyer and the manufacturer, ensuring that the final product aligns perfectly with operational requirements.
Scenario 3: Managing Lead Times and Delivery Reliability
The Problem: In many cases, B2B buyers experience significant frustration due to long lead times and unreliable delivery schedules from electrical control panel manufacturers. This is particularly critical for businesses in sectors like renewable energy and infrastructure, where project timelines are tightly linked to delivery. Delays can result in lost revenue and damage to reputation, creating a pressing need for timely solutions.
The Solution: To manage lead times effectively, buyers should conduct thorough market research to identify manufacturers with a strong reputation for timely delivery. It’s beneficial to create a list of preferred suppliers and establish clear communication channels to discuss timelines and expectations upfront. When negotiating contracts, include specific delivery timelines and penalties for delays to ensure accountability. Furthermore, consider manufacturers that offer local assembly or have a presence in the buyer’s region, as this can significantly reduce shipping times and improve overall reliability. Regular follow-ups and status updates during the production phase will also help in managing expectations and addressing any potential delays proactively.
Strategic Material Selection Guide for Manufacturers of Electrical Control Panels
What Are the Key Materials Used in Electrical Control Panels?
When selecting materials for electrical control panels, manufacturers must consider a variety of factors that influence performance, durability, and compliance with international standards. Here, we analyze four common materials: Steel, Aluminum, Polycarbonate, and Copper, focusing on their properties, advantages, disadvantages, and implications for international buyers.
How Does Steel Perform in Electrical Control Panels?
Steel is a widely used material in the construction of electrical control panels due to its strength and durability. Key properties include high tensile strength, excellent impact resistance, and the ability to withstand high temperatures and pressures. Steel panels are often coated with protective finishes to enhance corrosion resistance, making them suitable for various environments.
Pros: Steel offers exceptional durability and can be manufactured to meet stringent safety standards. Its cost-effectiveness makes it a popular choice for large-scale production.
Cons: The primary drawback is its weight, which can complicate installation. Steel also requires regular maintenance to prevent rust and corrosion, especially in humid or corrosive environments.
Impact on Application: Steel is compatible with a variety of media, including electrical components and environmental conditions. However, it may not be suitable for applications requiring lightweight materials.
Considerations for International Buyers: Buyers in regions like Africa and South America should ensure compliance with local standards (e.g., ASTM, DIN). Corrosion-resistant coatings are essential in coastal areas.
Why Choose Aluminum for Electrical Control Panels?
Aluminum is another popular choice for electrical control panels, known for its lightweight and corrosion-resistant properties. It has a lower density than steel, making it easier to handle and install. Aluminum panels can withstand moderate temperatures and are often used in environments where weight is a critical factor.
Pros: The lightweight nature of aluminum reduces shipping and installation costs. It also offers good thermal conductivity, which can be beneficial in managing heat within control panels.
Cons: Aluminum is generally less durable than steel and can be more expensive. It may also require additional treatments to enhance its strength and resistance to certain chemicals.
Impact on Application: Aluminum is suitable for applications where weight savings are crucial, such as in mobile or portable control systems. However, it may not be ideal for high-stress environments.
Considerations for International Buyers: Compliance with international standards is crucial, especially in Europe, where regulations around material safety are stringent. Buyers should also consider the availability of aluminum in local markets.
What Role Does Polycarbonate Play in Electrical Control Panels?
Polycarbonate is a thermoplastic material that is increasingly used in electrical control panels, particularly for enclosures. It is known for its high impact resistance and transparency, allowing for visibility of internal components.
Pros: Polycarbonate is lightweight, offers excellent insulation properties, and is resistant to UV radiation. It is also easy to mold into complex shapes, providing design flexibility.
Cons: While it has good impact resistance, polycarbonate can be less durable than metals in high-temperature environments. It is also more susceptible to scratching.
Impact on Application: Polycarbonate is ideal for applications requiring lightweight and transparent enclosures, such as in monitoring systems. However, it may not be suitable for environments with extreme temperatures.
Considerations for International Buyers: Buyers should check for compliance with safety standards like UL and IEC. Additionally, polycarbonate products should be sourced from reputable manufacturers to ensure quality.
How Does Copper Enhance Electrical Control Panels?
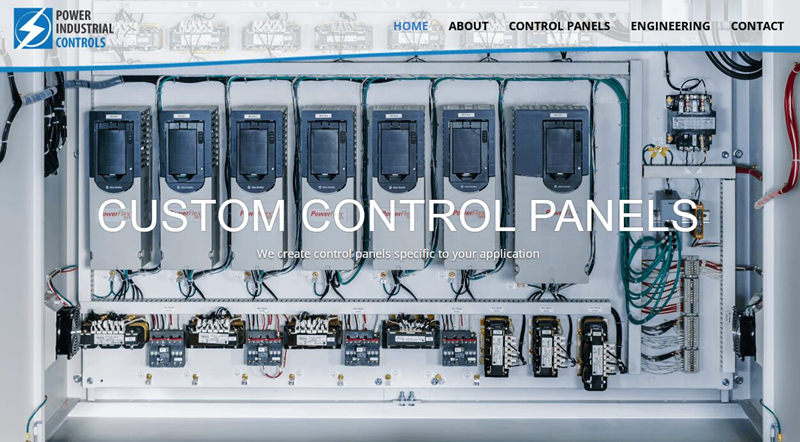
A stock image related to Manufacturers of Electrical Control Panels.
Copper is primarily used for electrical wiring and connections within control panels due to its excellent electrical conductivity. It can also be found in components such as busbars and terminals.
Pros: Copper’s superior conductivity ensures efficient electrical performance, reducing energy losses. It is also highly resistant to corrosion, particularly when properly treated.
Cons: Copper is more expensive than other materials and can be heavy. It is also prone to oxidation, which can affect performance if not properly managed.
Impact on Application: Copper is essential for applications requiring high electrical performance, such as in power distribution systems. However, its weight may be a consideration in portable applications.
Considerations for International Buyers: Buyers should ensure that copper components meet international standards for electrical safety. Additionally, sourcing from certified suppliers can help mitigate risks associated with counterfeit materials.
Summary Table of Material Selection for Electrical Control Panels
Material | Typical Use Case for Manufacturers of Electrical Control Panels | Key Advantage | Key Disadvantage/Limitation | Relative Cost (Low/Med/High) |
---|---|---|---|---|
Steel | Structural frames, enclosures | High durability and strength | Heavy and requires maintenance | Medium |
Aluminum | Lightweight enclosures, portable control panels | Lightweight and corrosion-resistant | Less durable than steel | Medium |
Polycarbonate | Transparent enclosures, monitoring systems | Impact resistance and design flexibility | Less durable in high temperatures | Low |
Copper | Electrical connections, busbars | Excellent electrical conductivity | High cost and weight | High |
This strategic material selection guide provides actionable insights for international B2B buyers, ensuring they make informed decisions based on performance, cost, and compliance with local standards.
In-depth Look: Manufacturing Processes and Quality Assurance for Manufacturers of Electrical Control Panels
What Are the Key Stages in the Manufacturing Process of Electrical Control Panels?
The manufacturing of electrical control panels involves several critical stages that ensure the final product meets the required specifications and quality standards. Understanding these stages helps international B2B buyers identify reliable suppliers capable of delivering high-performance control panels.
Material Preparation: What Materials Are Used?
The first step in the manufacturing process is material preparation, which includes sourcing and selecting high-quality raw materials. Common materials used in electrical control panel manufacturing include:
- Steel: Often used for enclosures due to its strength and durability.
- Copper and Aluminum: Used for wiring and conductive components due to their excellent electrical properties.
- Insulation Materials: Such as PVC or thermoplastics, which ensure safety and compliance with electrical standards.
Buyers should inquire about the sourcing practices of manufacturers to ensure that materials comply with international standards and regulations.
Forming: How Are Components Shaped?
The forming stage involves processes that shape the materials into the required components. Key techniques include:
- Cutting: Steel sheets are cut to size using laser cutting or shearing machines.
- Bending: Components are bent into shape using CNC bending machines, which ensure precision and consistency.
- Machining: Holes and slots are created for mounting components using milling machines.
Buyers should look for manufacturers that employ advanced CNC technology, as this often leads to higher precision and reduced lead times.
Assembly: What Techniques Are Used for Assembly?
Assembly is a crucial stage where all components come together. Techniques include:
- Wiring: Technicians carefully wire the panels according to electrical schematics, ensuring proper connections and safety.
- Mounting: Components such as circuit breakers, relays, and terminals are mounted onto the panel frame.
- Testing: Functional testing is conducted to verify the integrity of the assembly before the panel moves to the finishing stage.
B2B buyers should ask about the manufacturer’s assembly processes to ensure that they follow best practices and employ skilled technicians.
Finishing: What Is Involved in the Final Touches?
The finishing stage includes painting and labeling the panels. This not only enhances aesthetics but also protects against corrosion and wear. Common finishing processes include:
- Painting: Panels are often powder-coated for durability and to meet environmental regulations.
- Labeling: Clear and accurate labeling is applied for safety and ease of use, adhering to local and international standards.
Buyers should confirm that the finishing processes meet their aesthetic and functional requirements.
How Is Quality Assurance Integrated into the Manufacturing Process?
Quality assurance (QA) is vital in ensuring that electrical control panels are safe, reliable, and meet customer specifications. The QA process typically involves several international standards and industry-specific certifications.
What Are the Relevant International Standards for Electrical Control Panels?
Key international standards that apply to electrical control panels include:
- ISO 9001: A widely recognized standard for quality management systems, ensuring consistent quality across production.
- CE Marking: Indicates conformity with health, safety, and environmental protection standards for products sold within the European Economic Area.
- UL Certification: Particularly relevant in North America, this certification ensures that products meet safety standards set by Underwriters Laboratories.
Buyers should verify that manufacturers hold these certifications, as they demonstrate a commitment to quality and safety.
What Are the Quality Control Checkpoints in the Manufacturing Process?
Quality control (QC) is integrated at various checkpoints throughout the manufacturing process:
- Incoming Quality Control (IQC): Raw materials are inspected upon arrival to ensure they meet specified standards.
- In-Process Quality Control (IPQC): Ongoing inspections are conducted during the manufacturing process to catch defects early.
- Final Quality Control (FQC): The finished product undergoes rigorous testing and inspection before shipment.
International B2B buyers should inquire about the specific QC measures in place at each checkpoint.
What Common Testing Methods Are Used to Ensure Quality?
Common testing methods for electrical control panels include:
- Visual Inspection: To check for physical defects and ensure proper assembly.
- Electrical Testing: Including insulation resistance tests and continuity tests to verify electrical integrity.
- Environmental Testing: Simulating various conditions (temperature, humidity) to ensure performance under different environmental factors.
Buyers can request documentation of these tests to ensure that the manufacturer adheres to high-quality standards.
How Can B2B Buyers Verify Supplier Quality Control?
For international B2B buyers, verifying a supplier’s quality control processes is essential for ensuring reliable partnerships. Here are actionable steps:
What Should Buyers Look for in Supplier Audits?
Conducting supplier audits is a critical step in verifying quality control. Buyers should:
- Request Audit Reports: Review reports from previous audits to assess compliance with industry standards.
- Conduct On-Site Visits: If feasible, visiting the manufacturing facility can provide insights into the QA processes and operational practices.
How Can Buyers Use Third-Party Inspections?
Engaging third-party inspection services can provide an unbiased assessment of the manufacturer’s quality control processes. This includes:
- Pre-Shipment Inspections: Ensuring that products meet specifications before they leave the factory.
- Compliance Checks: Verifying that products comply with relevant standards and certifications.
What Are the Quality Control Nuances for International B2B Buyers?
B2B buyers from regions like Africa, South America, the Middle East, and Europe should be aware of specific nuances in quality control:
- Regulatory Differences: Different regions may have varying regulations regarding electrical safety. Familiarizing yourself with local regulations can help avoid compliance issues.
- Language Barriers: Ensure that communication is clear and that documentation is available in languages understood by all parties.
- Cultural Sensitivities: Building relationships with manufacturers may require understanding cultural differences in business practices and negotiation styles.
By taking these factors into account, international B2B buyers can foster successful partnerships with electrical control panel manufacturers, ensuring the delivery of high-quality products tailored to their needs.
Practical Sourcing Guide: A Step-by-Step Checklist for ‘Manufacturers of Electrical Control Panels’
In the competitive landscape of electrical control panel manufacturing, sourcing the right supplier is critical for ensuring quality, reliability, and compliance with industry standards. This checklist will guide B2B buyers through essential steps to effectively evaluate and choose manufacturers of electrical control panels, particularly for those in Africa, South America, the Middle East, and Europe.
Step 1: Define Your Technical Specifications
Clearly outline your technical requirements before approaching potential suppliers. This includes understanding the specific functionalities you need, such as motor control, safety features, or automation capabilities. By having detailed specifications, you can ensure that the panels meet your operational needs and comply with local regulations.
- Consider voltage ratings and environmental conditions: Different regions may have varying standards and requirements based on climate and application.
- Identify customization needs: Determine if off-the-shelf solutions suffice or if you need bespoke designs.
Step 2: Conduct Market Research for Potential Suppliers
Investigate manufacturers that specialize in electrical control panels relevant to your industry. Look for established companies with a proven track record in your region or sector. A thorough market analysis can help you identify suppliers who offer innovative and reliable solutions.
- Utilize industry directories and trade shows: These platforms often highlight reputable manufacturers and provide insights into their offerings.
- Check online reviews and testimonials: Feedback from previous clients can reveal the quality and reliability of the manufacturer’s products.
Step 3: Evaluate Supplier Certifications and Standards
Before finalizing a supplier, verify their compliance with relevant certifications and industry standards. Quality certifications such as ISO 9001 or UL listings ensure that the manufacturer adheres to high production and safety standards.
- Request documentation: Ask for copies of their certifications and any relevant test results to ensure transparency.
- Understand local compliance requirements: Ensure that the supplier’s products meet the regulations specific to your region, particularly for safety and environmental standards.
Step 4: Assess Manufacturing Capabilities and Technology
Investigate the manufacturing processes and technologies utilized by potential suppliers. Advanced manufacturing capabilities can significantly affect the quality and durability of the control panels.
- Inquire about production methods: Understanding whether they use automated processes or manual craftsmanship can impact lead times and cost.
- Evaluate their R&D investment: Suppliers that invest in research and development are likely to offer innovative solutions and improvements.
Step 5: Check References and Case Studies
Request references from previous clients, particularly those in similar industries or geographical locations. Case studies can provide insights into the supplier’s performance, responsiveness, and ability to meet deadlines.
- Contact references directly: Inquire about their experiences regarding product quality, support, and service.
- Review case studies: Look for documented success stories that align with your project requirements.
Step 6: Negotiate Terms and Conditions
Once you have shortlisted potential suppliers, engage in negotiations regarding pricing, lead times, warranty, and after-sales support. Clear agreements help avoid misunderstandings later in the procurement process.
- Discuss payment terms: Understanding payment schedules can help manage cash flow effectively.
- Clarify warranty and support: Ensure you are aware of the support available after purchase, including installation and maintenance services.
Step 7: Finalize Contracts and Place Orders
After thorough evaluation and negotiation, finalize the contracts with your chosen supplier. Ensure that all terms discussed are documented to protect both parties and ensure a smooth transaction process.
- Review the contract thoroughly: Look for any ambiguities that may lead to future disputes.
- Establish a communication plan: Set up regular check-ins to monitor progress and address any issues proactively.
By following these steps, B2B buyers can make informed decisions when sourcing manufacturers of electrical control panels, ensuring they partner with reliable suppliers that meet their specific needs.
Comprehensive Cost and Pricing Analysis for Manufacturers of Electrical Control Panels Sourcing
What Are the Key Cost Components for Electrical Control Panels?
When sourcing electrical control panels, understanding the cost structure is vital for B2B buyers. The primary components of cost include:
-
Materials: This is often the largest expense, comprising components like circuit breakers, relays, wiring, and enclosures. The choice of materials directly impacts durability and functionality, influencing the overall price.
-
Labor: Skilled labor is required for assembly, wiring, and testing. Labor costs vary significantly by region; for instance, manufacturers in Europe may face higher labor costs compared to those in South America or Africa.
-
Manufacturing Overhead: This includes indirect costs associated with the production process, such as utilities, rent, and administrative expenses. Efficient manufacturing processes can help keep these costs down.
-
Tooling: Depending on the complexity of the control panel, tooling costs can vary. Custom tooling for unique designs can significantly increase initial investment but may lead to cost savings over time through increased efficiency.
-
Quality Control (QC): Ensuring that control panels meet safety and performance standards incurs additional costs. Certifications like UL and CE can enhance marketability but also add to the overall cost.
-
Logistics: Shipping and handling costs are crucial, especially for international buyers. Factors such as distance, shipping method, and import duties can affect the final price.
-
Margin: Manufacturers typically add a profit margin to cover risks and provide returns on investment. This margin can vary widely based on competition, market demand, and the manufacturer’s reputation.
How Do Price Influencers Affect Electrical Control Panel Costs?
Several factors can influence the pricing of electrical control panels:
-
Volume and Minimum Order Quantity (MOQ): Larger orders usually qualify for discounts, which can significantly reduce the cost per unit. Understanding the MOQ policies of manufacturers is essential for cost efficiency.
-
Specifications and Customization: Custom panels tailored to specific applications can drive up costs. Buyers should weigh the necessity of customization against budget constraints.
-
Materials and Quality Certifications: Higher quality materials and certifications increase costs but can enhance reliability and reduce long-term maintenance expenses. Buyers must consider the Total Cost of Ownership (TCO) when evaluating these options.
-
Supplier Factors: Supplier reputation, reliability, and location can influence pricing. Established suppliers may offer better warranties and support, which can justify higher prices.
-
Incoterms: The choice of Incoterms (International Commercial Terms) affects logistics and shipping responsibilities. Understanding these terms can help buyers negotiate better shipping rates and terms.
What Are Essential Buyer Tips for Sourcing Electrical Control Panels?
International B2B buyers, particularly from Africa, South America, the Middle East, and Europe, should consider the following tips:
-
Negotiate Terms: Always negotiate pricing, payment terms, and shipping costs. Building a strong relationship with suppliers can lead to better deals and terms.
-
Evaluate Total Cost of Ownership (TCO): Consider not just the upfront costs but also long-term operational and maintenance expenses. A cheaper panel may incur higher costs over time if it requires frequent repairs or replacement.
-
Understand Pricing Nuances: Prices can vary based on local market conditions, demand fluctuations, and currency exchange rates. Stay informed about these factors to make educated purchasing decisions.
-
Leverage Regional Advantages: Buyers from emerging markets like Kenya or Brazil may find local manufacturers who offer competitive pricing due to lower operational costs. Explore regional options to maximize cost-efficiency.
-
Stay Informed on Regulatory Changes: Import tariffs, local regulations, and trade agreements can impact costs. Keeping abreast of these changes can help in making more strategic sourcing decisions.
Disclaimer on Indicative Prices
Prices for electrical control panels can vary widely based on specifications, quantity, and supplier. It is advisable for buyers to obtain detailed quotes and conduct thorough market research before making purchasing decisions.
Alternatives Analysis: Comparing Manufacturers of Electrical Control Panels With Other Solutions
When evaluating the procurement of electrical control panels, it’s essential for B2B buyers to consider not only traditional manufacturers but also alternative solutions. These alternatives can offer varying degrees of functionality, cost efficiency, and operational flexibility. Below, we delve into a comparison of electrical control panel manufacturers with two viable alternatives: Programmable Logic Controllers (PLCs) and Smart Circuit Breakers.
Comparison Table of Electrical Control Panels and Alternatives
Comparison Aspect | Manufacturers of Electrical Control Panels | Programmable Logic Controllers (PLCs) | Smart Circuit Breakers |
---|---|---|---|
Performance | High reliability and customization | Flexible programming for complex tasks | Real-time monitoring and control |
Cost | Moderate to high initial investment | Variable costs based on complexity | Generally lower than panels |
Ease of Implementation | Requires skilled labor for installation | Moderate; programming knowledge needed | Simple installation |
Maintenance | Regular maintenance needed for longevity | Low maintenance; firmware updates | Minimal maintenance required |
Best Use Case | Industrial applications needing robust control | Complex automation systems | Smart homes and energy management |
What Are the Advantages and Disadvantages of Programmable Logic Controllers (PLCs)?
Pros:
PLCs are highly flexible and can be programmed to perform a wide range of tasks, making them suitable for complex automation processes. They can integrate with various sensors and devices, allowing for real-time data analysis and control. Their modular design often means that they can be expanded as needed, accommodating growth without significant overhauls.
Cons:
The initial setup of a PLC can require a steep learning curve, as programming expertise is essential. Additionally, while they tend to have lower maintenance needs, any required updates or changes in programming can lead to downtime, impacting productivity.
How Do Smart Circuit Breakers Compare in Terms of Efficiency?
Pros:
Smart circuit breakers are designed for real-time monitoring and control, providing insights into energy usage and system performance. They can be integrated with home automation systems, allowing for remote management and adjustments. This technology is generally more cost-effective than traditional electrical panels and offers quick installation.
Cons:
Despite their advantages, smart circuit breakers may not deliver the same level of customization as traditional control panels. They are best suited for applications that require basic control and monitoring rather than complex industrial processes. Their reliance on connectivity can also pose risks if the network experiences outages.
How Can B2B Buyers Choose the Right Solution for Their Needs?
When selecting between manufacturers of electrical control panels and alternative solutions like PLCs or smart circuit breakers, B2B buyers should assess their specific operational needs. Factors such as the complexity of tasks, budget constraints, and the level of customization required will guide the decision. For industries with straightforward control needs and a focus on cost efficiency, smart circuit breakers may be the ideal choice. Conversely, sectors requiring intricate automation and high reliability might benefit more from traditional control panels or PLCs.
Ultimately, understanding the nuances of each option allows buyers to align their choice with their operational goals, ensuring optimal performance and return on investment.
Essential Technical Properties and Trade Terminology for Manufacturers of Electrical Control Panels
What Are the Essential Technical Properties of Electrical Control Panels?
When selecting electrical control panels, understanding the technical specifications is crucial for making informed purchasing decisions. Here are some of the key properties you should consider:
1. Material Grade
Electrical control panels are typically constructed from materials such as steel, aluminum, or fiberglass. The choice of material affects durability, weight, and resistance to environmental factors like moisture and temperature. For instance, stainless steel offers excellent corrosion resistance, making it ideal for harsh industrial environments. Selecting the right material ensures longevity and reduces maintenance costs.
2. Tolerance Levels
Tolerance refers to the permissible limit of variation in a physical dimension or measured value. In control panel manufacturing, tight tolerances are essential to ensure components fit correctly and function as intended. Tolerances can affect the performance and reliability of the panel, especially in precision applications like automation systems. Buyers should specify required tolerances to meet their operational standards.
3. Power Rating
The power rating indicates the maximum electrical load that a control panel can handle. It is typically expressed in amperes (A) or kilowatts (kW). Understanding the power rating is vital for ensuring the panel can support the electrical demands of the connected machinery or equipment. Selecting a panel with an appropriate power rating prevents overheating and potential failures.
4. IP Rating (Ingress Protection)
The IP rating provides information on the degree of protection against solids and liquids. For example, an IP67 rating means the panel is dust-tight and can withstand immersion in water up to 1 meter. Knowing the IP rating helps buyers choose panels suitable for specific environments, such as outdoor installations or areas with high humidity.
5. Certification Standards
Electrical control panels often require compliance with industry standards such as UL (Underwriters Laboratories), CE (Conformité Européenne), or CSA (Canadian Standards Association). Certifications ensure that the panels meet safety and performance criteria. Buyers should verify certifications to ensure compliance with local regulations and enhance safety in operations.
What Are Common Trade Terms Used in Electrical Control Panel Manufacturing?
Understanding industry jargon can streamline communication and negotiation processes in B2B transactions. Here are several essential terms:
1. OEM (Original Equipment Manufacturer)
An OEM refers to a company that produces parts or equipment that may be marketed by another manufacturer. In the context of electrical control panels, buyers may seek OEMs for custom solutions tailored to specific machinery or applications. This relationship can foster innovation and efficiency in product development.
2. MOQ (Minimum Order Quantity)
MOQ indicates the smallest quantity of a product that a supplier is willing to sell. For electrical control panels, MOQs can vary widely based on the complexity of the design and the materials used. Understanding MOQs helps buyers plan their inventory and manage budgets effectively.
3. RFQ (Request for Quotation)
An RFQ is a formal document soliciting price quotes from suppliers for specific products or services. When dealing with electrical control panels, an RFQ allows buyers to compare costs, specifications, and lead times from multiple manufacturers. This process is essential for ensuring competitive pricing and informed decision-making.
4. Incoterms (International Commercial Terms)
Incoterms are standardized trade terms that define the responsibilities of buyers and sellers in international transactions. They clarify who is responsible for shipping, insurance, and tariffs. Understanding Incoterms is crucial for B2B buyers, especially when importing electrical control panels from overseas manufacturers, as it affects overall costs and risk management.
5. PLC (Programmable Logic Controller)
A PLC is an industrial digital computer used for automation of electromechanical processes. In the context of control panels, PLCs play a critical role in controlling machinery and equipment. Buyers should ensure that panels are compatible with the PLCs they intend to use, as this impacts system integration and functionality.
By familiarizing yourself with these technical properties and trade terms, you can make more informed purchasing decisions, ensuring that your electrical control panel meets operational needs and industry standards.
Navigating Market Dynamics and Sourcing Trends in the Manufacturers of Electrical Control Panels Sector
What Are the Key Trends Shaping the Electrical Control Panels Market?
The electrical control panels market is witnessing significant growth driven by advancements in automation, the increasing complexity of electrical systems, and a global push towards energy efficiency. International B2B buyers, especially from Africa, South America, the Middle East, and Europe, are increasingly looking for manufacturers that offer innovative solutions tailored to specific industry needs. Key trends include the rise of smart control panels integrated with IoT technology, which facilitate real-time monitoring and data analytics, enhancing operational efficiency.
Moreover, there is a growing demand for custom solutions that can be designed to meet stringent safety standards and regulatory requirements. Manufacturers are responding by investing in advanced manufacturing technologies such as 3D printing and modular designs, which allow for quicker prototyping and reduced lead times. The focus on modularity not only aids in scalability but also reduces costs for buyers who may need to expand or modify their systems over time.
As automation continues to penetrate various sectors, including manufacturing, energy, and infrastructure, the need for reliable and efficient electrical control panels is paramount. Additionally, international buyers are increasingly favoring manufacturers that can provide comprehensive after-sales support and maintenance services, ensuring long-term operational reliability.
How Important Is Sustainability and Ethical Sourcing in the Electrical Control Panels Sector?
Sustainability and ethical sourcing are becoming critical considerations for B2B buyers in the electrical control panels sector. The environmental impact of manufacturing processes and materials used in control panels is under scrutiny, prompting many manufacturers to adopt greener practices. This includes the use of recyclable materials, energy-efficient manufacturing processes, and adherence to international environmental standards.
Buyers are increasingly seeking manufacturers that hold certifications such as ISO 14001 (Environmental Management) and those that utilize eco-friendly materials in their products. These certifications not only demonstrate a commitment to reducing carbon footprints but also provide assurance that the products are sourced responsibly.
Additionally, the trend towards sustainability is influencing the design of electrical control panels. Manufacturers are now focusing on energy-efficient solutions that minimize energy consumption during operation. This aligns with global efforts to reduce greenhouse gas emissions and promote sustainable development, making it a vital factor for international buyers, particularly those from regions with stringent environmental regulations.
What Is the Historical Context of Electrical Control Panels and Its Relevance Today?
The evolution of electrical control panels can be traced back to the early 20th century when they were primarily used for basic circuit control. Over the decades, advancements in technology have transformed these panels into sophisticated systems capable of managing complex electrical networks.
In recent years, the shift towards automation and digitalization has further accelerated the development of control panels. Modern panels are now equipped with features such as programmable logic controllers (PLCs) and integrated communication protocols, allowing for greater flexibility and control. This historical context is essential for B2B buyers as it highlights the continuous innovation in the sector, underscoring the importance of selecting manufacturers who are not only established but also at the forefront of technological advancements.
Understanding this evolution enables buyers to make informed decisions about the manufacturers they partner with, ensuring that they invest in solutions that meet current and future demands.
Frequently Asked Questions (FAQs) for B2B Buyers of Manufacturers of Electrical Control Panels
-
How do I choose the right manufacturer for electrical control panels?
Selecting the right manufacturer involves assessing their experience, certifications, and industry reputation. Look for manufacturers with a proven track record in your specific sector, such as oil and gas or industrial automation. Verify their compliance with international standards like ISO 9001 and UL certifications. Additionally, consider their capacity for customization, lead times, and after-sales support. Engaging with past clients can provide insights into their reliability and quality of service. -
What customization options are available when sourcing electrical control panels?
Most manufacturers offer a variety of customization options to meet specific operational needs. These can include panel size, layout, component selection, and integration with existing systems. Additionally, some manufacturers allow for custom branding and labeling. When discussing customization, clearly communicate your requirements, including any regulatory standards that must be met. This ensures that the final product aligns with your operational demands and enhances efficiency. -
What are the minimum order quantities (MOQs) for electrical control panels?
Minimum order quantities can vary significantly between manufacturers, often depending on the complexity and customization of the panels. Some manufacturers may have MOQs as low as one unit for standard panels, while custom solutions might require higher quantities to justify production costs. It’s advisable to discuss MOQs upfront during negotiations to understand your purchasing options and determine if a manufacturer can accommodate your order size. -
What payment terms should I expect when dealing with international suppliers?
Payment terms can differ based on the manufacturer’s policies and your negotiation. Common options include upfront payments, partial payments during production, or payment upon delivery. For international transactions, letters of credit or escrow services may provide additional security. Always clarify the payment timeline and any potential currency exchange considerations, especially when dealing with suppliers from different regions, to avoid misunderstandings. -
How do I ensure quality assurance in my electrical control panel orders?
Ensuring quality assurance starts with selecting a manufacturer that adheres to recognized quality standards. Request documentation of certifications, such as ISO 9001, and inquire about their quality control processes. Many manufacturers will conduct thorough testing on panels before shipment, including functional and safety tests. Establishing clear specifications and conducting factory audits can further ensure that the products meet your expectations. -
What logistics considerations should I keep in mind when sourcing from international manufacturers?
Logistics plays a crucial role in international sourcing. Consider factors such as shipping methods, estimated delivery times, and customs regulations in your country. Collaborate with manufacturers that have experience in international shipping to ensure compliance with all import/export requirements. Additionally, discuss who will handle logistics and any associated costs upfront to avoid unexpected delays and fees. -
How can I evaluate the reliability of an electrical control panel manufacturer?
Evaluating a manufacturer’s reliability involves researching their history, customer reviews, and industry reputation. Look for case studies or testimonials from clients in similar sectors. Engaging with industry forums or associations can also provide insights into their track record. Requesting references and conducting site visits can further validate their operational capabilities and commitment to quality. -
What are the current trends in electrical control panel manufacturing?
Trends in electrical control panel manufacturing include increased automation, integration of IoT technologies, and a focus on energy efficiency. Manufacturers are adopting smart technologies to enhance monitoring and control capabilities, allowing for real-time data analysis. Additionally, there is a growing emphasis on sustainability, with many manufacturers developing eco-friendly solutions. Staying informed about these trends can help buyers choose modern solutions that align with their operational goals.
Important Disclaimer & Terms of Use
⚠️ Important Disclaimer
The information provided in this guide, including content regarding manufacturers, technical specifications, and market analysis, is for informational and educational purposes only. It does not constitute professional procurement advice, financial advice, or legal advice.
While we have made every effort to ensure the accuracy and timeliness of the information, we are not responsible for any errors, omissions, or outdated information. Market conditions, company details, and technical standards are subject to change.
B2B buyers must conduct their own independent and thorough due diligence before making any purchasing decisions. This includes contacting suppliers directly, verifying certifications, requesting samples, and seeking professional consultation. The risk of relying on any information in this guide is borne solely by the reader.
Strategic Sourcing Conclusion and Outlook for Manufacturers of Electrical Control Panels
As the demand for high-performance electrical control panels continues to rise across various industries, the strategic sourcing of these components has never been more crucial. International B2B buyers, particularly from regions like Africa, South America, the Middle East, and Europe, must prioritize partnerships with manufacturers who demonstrate a commitment to quality, innovation, and customization. Companies such as EBI Electric, IndustLabs, and ESL Power Systems exemplify the benefits of leveraging local expertise and global standards to meet specific operational needs.
How Can Strategic Sourcing Enhance Your Procurement Process?
Effective strategic sourcing not only reduces costs but also fosters long-term relationships with suppliers who understand your market dynamics. By selecting manufacturers that are ISO certified and have a proven track record, buyers can ensure compliance with international standards while gaining access to cutting-edge technology and tailored solutions. This approach enables businesses to maintain a competitive edge in an increasingly automated world.
What Does the Future Hold for Electrical Control Panel Manufacturers?
Looking ahead, the electrical control panel market is poised for growth driven by advancements in IoT and automation. Buyers are encouraged to explore partnerships that facilitate innovation, sustainability, and efficiency. As you consider your sourcing strategy, engage with manufacturers that prioritize customer service and adaptability to help navigate the complexities of modern industrial requirements. Your proactive approach today can lead to enhanced operational success tomorrow.