Discover Top Metal Furniture Suppliers: A Complete Guide (2025)
Introduction: Navigating the Global Market for metal furniture supplier
Navigating the global market for metal furniture suppliers presents a unique set of challenges for international B2B buyers, particularly when sourcing durable and stylish office solutions that meet diverse regional preferences. In a world increasingly focused on sustainability and functionality, finding the right metal furniture—whether for ergonomic desk chairs or resilient shelving units—can be daunting. This comprehensive guide is designed to demystify the complexities of sourcing metal furniture, covering various types, applications, and essential supplier vetting processes.
In the coming sections, buyers will gain insights into the latest trends in metal furniture design, the benefits of different materials, and tips for assessing quality and pricing. Special attention is given to the unique needs of buyers from Africa, South America, the Middle East, and Europe, including countries like Kenya and France, ensuring that the recommendations are relevant and actionable.
This guide empowers B2B purchasers to make informed decisions by providing a clear understanding of market dynamics, supplier credibility, and cost considerations. By leveraging this knowledge, international buyers can confidently navigate the global metal furniture landscape, ensuring that their investments not only enhance their workspace aesthetics but also align with their operational needs and sustainability goals.
Understanding metal furniture supplier Types and Variations
Type Name | Key Distinguishing Features | Primary B2B Applications | Brief Pros & Cons for Buyers |
---|---|---|---|
Custom Metal Furniture | Tailored designs, unique specifications, and materials | High-end retail, luxury hotels, offices | Pros: Personalization, exclusivity. Cons: Higher cost, longer lead times. |
Modular Metal Furniture | Flexible configurations, easy assembly, and reconfiguration | Co-working spaces, educational institutions | Pros: Versatile, space-efficient. Cons: May lack aesthetic appeal. |
Industrial Metal Furniture | Raw finishes, robust construction, and utilitarian design | Warehouses, factories, cafes | Pros: Durability, low maintenance. Cons: Limited design options, heavier. |
Office Metal Furniture | Ergonomic designs, integrated technology, and aesthetics | Corporate offices, call centers | Pros: Professional appearance, functionality. Cons: Can be expensive. |
Outdoor Metal Furniture | Weather-resistant materials, rust-proof coatings | Parks, outdoor dining, hospitality venues | Pros: Long-lasting, easy to clean. Cons: Can be less comfortable without cushions. |
What are the Characteristics of Custom Metal Furniture Suppliers?
Custom metal furniture suppliers specialize in creating bespoke pieces tailored to the specific needs and preferences of businesses. This type often involves intricate designs and unique specifications that cater to high-end markets, such as luxury hotels and upscale retail spaces. When considering a custom supplier, B2B buyers should evaluate their design capabilities, material options, and lead times, as these factors significantly influence project timelines and costs.
How Do Modular Metal Furniture Suppliers Benefit Businesses?
Modular metal furniture suppliers provide flexible and adaptable solutions that can be easily reconfigured to meet changing business needs. This type is particularly beneficial for co-working spaces and educational institutions, where the layout may frequently change. Buyers should consider the ease of assembly, durability, and aesthetic options when selecting modular solutions, as these factors impact both functionality and the overall ambiance of the space.
What Defines Industrial Metal Furniture Suppliers?
Industrial metal furniture suppliers focus on creating robust and utilitarian designs that are perfect for demanding environments such as warehouses and factories. Their products typically feature raw finishes and sturdy construction, making them ideal for high-traffic areas. Buyers should assess the durability, maintenance requirements, and potential design limitations when choosing industrial furniture, as these elements are crucial for long-term satisfaction and utility.
What Should Buyers Look for in Office Metal Furniture Suppliers?
Office metal furniture suppliers offer ergonomic and stylish solutions that enhance workplace productivity and aesthetics. Their products often integrate technology and cater to various office layouts, making them suitable for corporate environments and call centers. B2B buyers should prioritize functionality, comfort, and price when evaluating these suppliers, as a well-designed office space can significantly impact employee morale and efficiency.
Why Choose Outdoor Metal Furniture Suppliers?
Outdoor metal furniture suppliers specialize in weather-resistant and durable products designed for outdoor settings such as parks and hospitality venues. These suppliers often use rust-proof coatings and sturdy materials to ensure longevity. When selecting outdoor furniture, buyers should consider comfort, maintenance, and design aesthetics, as these factors will influence the appeal and usability of outdoor spaces.
Related Video: How To Make An Industrial Furniture Wood and Metal Coffee Table
Key Industrial Applications of metal furniture supplier
Industry/Sector | Specific Application of Metal Furniture Supplier | Value/Benefit for the Business | Key Sourcing Considerations for this Application |
---|---|---|---|
Hospitality | Custom metal furniture for hotels and restaurants | Enhances aesthetic appeal and durability | Quality of materials, design flexibility, and lead times |
Education | Metal desks and chairs for schools and universities | Provides long-lasting, sturdy solutions for students | Ergonomic design, safety standards, and bulk pricing |
Healthcare | Metal furniture for hospitals and clinics | Ensures hygiene, easy maintenance, and durability | Compliance with health regulations, easy-to-clean finishes |
Retail | Display racks and counters in stores | Increases product visibility and enhances shopping experience | Customization options, weight capacity, and design trends |
Office | Metal office workstations and storage solutions | Improves workspace organization and employee productivity | Modular designs, space optimization, and warranty terms |
How is Metal Furniture Used in the Hospitality Industry?
In the hospitality sector, metal furniture suppliers provide custom solutions such as tables, chairs, and benches for hotels and restaurants. These products are designed to withstand high usage while maintaining aesthetic appeal. By offering durable and attractive options, suppliers help businesses enhance their environment, which can lead to increased customer satisfaction and repeat visits. For international buyers, understanding local design preferences and material availability is crucial for successful sourcing.
What Role Does Metal Furniture Play in Education?
Metal furniture is widely used in educational institutions, providing robust desks and chairs that can endure the wear and tear from students. This application not only supports an organized learning environment but also promotes ergonomic seating to ensure student comfort. Buyers from Africa and South America should consider local educational needs, such as classroom layouts and safety standards, when sourcing metal furniture.
How Does Metal Furniture Benefit Healthcare Facilities?
In the healthcare industry, metal furniture suppliers offer essential items like hospital beds, examination tables, and waiting room seating. The primary benefits include durability, hygiene, and ease of maintenance, crucial for a sterile environment. International buyers must ensure that products comply with health regulations and standards specific to their region, especially in the Middle East and Europe, where compliance can vary significantly.
What are the Applications of Metal Furniture in Retail?
Retail environments utilize metal furniture for display racks, counters, and checkout stations. These products are designed to be visually appealing while providing robust support for various merchandise. Suppliers can enhance a store’s layout, thus improving customer flow and product visibility. Buyers should focus on customization options and weight capacity to meet specific retail needs, particularly in diverse markets across Europe and Africa.
How is Metal Furniture Optimizing Office Spaces?
In office environments, metal furniture suppliers provide workstations, desks, and storage solutions that enhance organization and productivity. Metal furniture is favored for its durability and modern aesthetic, which can create a professional atmosphere. International B2B buyers need to consider modular designs that allow for flexible workspace configurations and warranty terms that ensure long-term investment protection.
3 Common User Pain Points for ‘metal furniture supplier’ & Their Solutions
Scenario 1: Sourcing Quality Metal Furniture for Diverse Markets
The Problem: International B2B buyers often struggle to find metal furniture suppliers that meet their specific quality standards and design preferences. This challenge is compounded when sourcing from regions like Africa or South America, where local suppliers may not have the necessary certifications or quality assurance processes in place. Buyers may encounter issues such as inconsistent product quality, lack of customization options, or products that do not comply with local regulations, which can lead to costly delays and customer dissatisfaction.
The Solution: To effectively source quality metal furniture, buyers should prioritize suppliers who provide transparent information about their manufacturing processes and quality control measures. Begin by conducting thorough research on potential suppliers, looking for those with international certifications (such as ISO 9001) that demonstrate a commitment to quality. Additionally, request samples to evaluate the craftsmanship and durability of the furniture before placing bulk orders. Establishing a clear communication channel with the supplier can help address specific design needs and ensure that the final products align with your market’s expectations. Consider using third-party inspection services to verify quality before shipment to avoid potential issues upon arrival.
Scenario 2: Understanding Pricing Structures and Hidden Costs
The Problem: Many B2B buyers face confusion regarding the pricing of metal furniture, which can vary significantly based on factors such as material quality, design complexity, and order volume. Hidden costs such as shipping fees, tariffs, and import duties can further complicate the purchasing process, leading to budget overruns and financial strain. Buyers in regions with fluctuating currencies may also struggle to get accurate pricing, making it difficult to forecast expenses.
The Solution: To navigate pricing complexities, buyers should ask for a detailed breakdown of costs from suppliers, including production, shipping, and any additional fees. Developing a strong relationship with suppliers can facilitate more transparent pricing discussions and enable buyers to negotiate better terms. It’s also beneficial to understand the local market dynamics, such as currency trends and import regulations, which can impact overall costs. Utilizing a cost calculator tool or consulting with a logistics expert can provide insights into total landed costs, allowing for better budgeting and decision-making. Lastly, consider establishing long-term contracts with suppliers to lock in prices and mitigate the risk of sudden price increases.
Scenario 3: Ensuring Timely Deliveries Amidst Supply Chain Disruptions
The Problem: B2B buyers often experience delays in receiving their orders due to supply chain disruptions, which can be exacerbated by global events such as pandemics or political instability. Delays can lead to missed deadlines, negatively impacting client relationships and the overall reputation of the buyer’s business. In regions like the Middle East or Europe, where market demands can be high, the pressure for timely deliveries is even more pronounced.
The Solution: To ensure timely deliveries, buyers should implement a proactive approach to supply chain management. Start by selecting suppliers with a proven track record of reliability and who have contingency plans in place for unforeseen disruptions. Establish clear deadlines and communicate them to suppliers, making it clear that adherence to these timelines is crucial. Regularly review the order status and maintain open lines of communication to quickly address any issues that may arise. Additionally, consider diversifying your supplier base to mitigate risks associated with relying on a single source. This strategy allows for flexibility and ensures that you can meet customer demands even if one supplier faces challenges. Finally, leveraging technology such as supply chain management software can provide real-time updates and improve the overall efficiency of the procurement process.
Strategic Material Selection Guide for metal furniture supplier
When selecting materials for metal furniture, international B2B buyers must consider various factors that impact product performance, durability, and compliance with regional standards. Here, we analyze four common materials used in metal furniture manufacturing: steel, aluminum, stainless steel, and wrought iron. Each material has its distinct properties, advantages, and limitations that can influence purchasing decisions.
What Are the Key Properties of Steel for Metal Furniture?
Steel is a widely used material in metal furniture due to its strength and versatility. It typically has a high tensile strength and excellent temperature and pressure ratings, making it suitable for various applications. Steel can be treated for additional properties, such as corrosion resistance through galvanization or powder coating.
Pros: Steel furniture is known for its durability and longevity, making it ideal for high-traffic areas. It is also relatively cost-effective compared to other metals, which can be a significant advantage for budget-conscious buyers.
Cons: On the downside, steel is susceptible to rust if not properly treated, and its weight can make transportation and assembly more challenging. Additionally, the manufacturing complexity can increase costs if intricate designs are required.
Impact on Application: Steel is compatible with various finishes and can be used in both indoor and outdoor settings, provided it is adequately treated for corrosion resistance.
Considerations for International Buyers: Buyers from regions like Africa and South America should ensure compliance with local standards such as ASTM or ISO, particularly regarding safety and durability.
How Does Aluminum Compare as a Material for Metal Furniture?
Aluminum is another popular choice for metal furniture, known for its lightweight and corrosion-resistant properties. It has lower density compared to steel, making it easier to handle and transport.
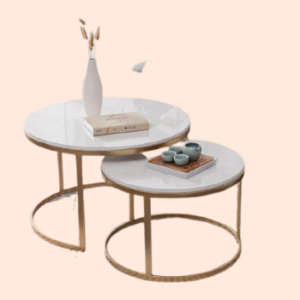
A stock image related to metal furniture supplier.
Pros: The primary advantage of aluminum is its resistance to corrosion, which makes it ideal for outdoor furniture. It is also highly malleable, allowing for more intricate designs without compromising strength.
Cons: However, aluminum is generally less strong than steel, which may limit its use in heavy-duty applications. Additionally, it can be more expensive, particularly when considering high-quality alloys.
Impact on Application: Aluminum is well-suited for environments with high humidity or exposure to saltwater, such as coastal areas.
Considerations for International Buyers: Buyers in Europe may prefer aluminum for its sustainability and recyclability, aligning with the EU’s environmental standards. Compliance with EN standards is crucial for market acceptance.
What Are the Benefits of Using Stainless Steel in Metal Furniture?
Stainless steel is renowned for its aesthetic appeal and corrosion resistance, making it a premium choice for metal furniture. It combines the strength of steel with the added benefit of resistance to rust and staining.
Pros: The key advantage of stainless steel is its durability and low maintenance requirements, which make it suitable for both residential and commercial applications. Its sleek appearance also enhances the visual appeal of furniture.
Cons: The primary disadvantage is the higher cost compared to regular steel and aluminum. Additionally, welding and machining stainless steel can be more complex, potentially increasing manufacturing costs.
Impact on Application: Stainless steel is ideal for high-end furniture designs and applications where hygiene is essential, such as in healthcare settings.
Considerations for International Buyers: Buyers from the Middle East and Africa should be aware of the specific grades of stainless steel (e.g., 304 vs. 316) and their suitability for different environments. Compliance with local standards is critical for ensuring product longevity.
Why Choose Wrought Iron for Metal Furniture?
Wrought iron is often chosen for its classic aesthetic and exceptional durability. It is characterized by its fibrous structure, which provides excellent strength and flexibility.
Pros: Wrought iron furniture is highly durable and can withstand harsh weather conditions, making it suitable for outdoor use. Its ability to be molded into intricate designs adds to its appeal.
Cons: However, wrought iron is heavier than other materials, which can complicate shipping and assembly. It is also more prone to rusting if not properly coated.
Impact on Application: Wrought iron is commonly used in garden furniture and decorative pieces due to its aesthetic qualities.
Considerations for International Buyers: Buyers in Europe may favor wrought iron for its traditional look, while those in Africa should consider protective coatings to prevent rust in humid climates.
Summary Table of Material Properties for Metal Furniture
Material | Typical Use Case for Metal Furniture Supplier | Key Advantage | Key Disadvantage/Limitation | Relative Cost (Low/Med/High) |
---|---|---|---|---|
Steel | Office and industrial furniture | High durability | Susceptible to rust | Medium |
Aluminum | Outdoor furniture and lightweight designs | Corrosion-resistant | Less strength compared to steel | High |
Stainless Steel | High-end residential and commercial furniture | Low maintenance and aesthetic appeal | Higher cost and manufacturing complexity | High |
Wrought Iron | Garden and decorative furniture | Exceptional durability and design flexibility | Heavy and prone to rust | Medium |
This strategic material selection guide provides valuable insights for international B2B buyers, enabling informed decisions based on the unique properties and applications of each material.
In-depth Look: Manufacturing Processes and Quality Assurance for metal furniture supplier
What Are the Key Stages in the Manufacturing Process of Metal Furniture?
The manufacturing process for metal furniture involves several critical stages, each essential for ensuring the final product’s quality and durability. Understanding these stages will help B2B buyers make informed decisions when selecting suppliers.
Material Preparation: What Materials Are Used and How Are They Processed?
The first stage in manufacturing metal furniture is material preparation. Common materials include steel, aluminum, and wrought iron, which are chosen for their strength, durability, and aesthetic appeal.
- Cutting: Raw metal sheets are cut into required shapes using plasma cutting, laser cutting, or shearing techniques. The choice of cutting method affects precision and material waste.
- Surface Treatment: Before further processing, materials undergo surface treatment to remove impurities, rust, or oil. Techniques such as sandblasting or chemical cleaning are often employed.
How is Forming Done in Metal Furniture Manufacturing?
Forming is the next crucial step where the metal pieces are shaped into the desired designs.
- Bending: Metal sheets are bent using hydraulic or mechanical presses to create curves and angles. This process requires precise calculations to ensure the correct angles and dimensions.
- Welding: After bending, parts are welded together using MIG, TIG, or spot welding techniques. The welding method impacts the strength and aesthetics of the joints.
- Punching and Stamping: For decorative elements or functional holes, punching and stamping techniques are utilized. This step is vital for enhancing both the functionality and design of the furniture.
What Assembly Techniques Are Used in Metal Furniture Production?
Once the components are formed, the assembly process begins, integrating all parts into a cohesive unit.
- Mechanical Assembly: Components are joined using screws, bolts, or rivets, which allows for easy disassembly and repair. This is particularly important for B2B buyers looking for transportable or modular furniture.
- Final Adjustments: After mechanical assembly, final adjustments are made to ensure that all components fit perfectly and function as intended.
What Finishing Techniques Enhance the Aesthetics and Durability of Metal Furniture?
Finishing is the final step in the manufacturing process, significantly impacting the furniture’s appearance and longevity.
- Painting and Powder Coating: Aesthetic finishes are applied through painting or powder coating, which also provides a protective layer against rust and wear. Powder coating is preferred for its durability and variety of colors.
- Varnishing: In some cases, varnish is applied to achieve a specific look or to protect the surface further.
- Quality Inspection: Before the furniture is packaged, a thorough inspection is conducted to ensure that all finishes are applied correctly, and there are no defects.
What International Quality Standards Should B2B Buyers Consider?
Understanding the quality assurance (QA) measures is crucial for B2B buyers, especially when dealing with international suppliers. Many suppliers adhere to recognized international standards to ensure product quality.
- ISO 9001 Certification: This standard demonstrates that a supplier has established a quality management system. B2B buyers should prioritize suppliers with this certification as it reflects their commitment to quality.
- CE Marking: For suppliers in Europe, CE marking indicates compliance with EU safety, health, and environmental requirements, making it crucial for buyers in the European market.
What Are the Key Quality Control Checkpoints in Metal Furniture Manufacturing?
Quality control (QC) checkpoints are integral to maintaining high standards throughout the manufacturing process. Here are the main QC stages:
- Incoming Quality Control (IQC): This initial checkpoint involves inspecting raw materials upon arrival to ensure they meet specified standards. It prevents defective materials from entering the production line.
- In-Process Quality Control (IPQC): During manufacturing, periodic inspections occur to monitor processes and identify potential issues before they escalate. This includes checking dimensions, weld quality, and surface finishes.
- Final Quality Control (FQC): Before products leave the facility, FQC involves a comprehensive examination of the finished furniture. This includes functional tests and aesthetic evaluations.
What Common Testing Methods Are Used for Metal Furniture Quality Assurance?
To ensure that metal furniture meets quality standards, various testing methods are employed:
- Mechanical Testing: This includes tensile strength tests, hardness tests, and impact tests to assess the material’s durability and performance.
- Environmental Testing: Furniture may undergo corrosion resistance tests, particularly for outdoor metal furniture, to ensure it can withstand environmental elements.
- Visual Inspection: A thorough visual inspection checks for cosmetic defects, ensuring that the product meets aesthetic standards.
How Can B2B Buyers Verify Supplier Quality Control?
B2B buyers can take several steps to verify a supplier’s quality control processes:
- Supplier Audits: Conducting on-site audits of the supplier’s facility allows buyers to assess the manufacturing and QC processes firsthand.
- Requesting Reports: Buyers should request documentation on quality control practices, including IQC, IPQC, and FQC reports, to understand how the supplier maintains quality.
- Third-Party Inspections: Engaging third-party inspection services can provide an unbiased evaluation of the supplier’s quality assurance processes.
What QC and Certification Nuances Should International B2B Buyers Be Aware Of?
For international B2B buyers, particularly from regions like Africa, South America, the Middle East, and Europe, understanding certification nuances is essential.
- Regional Standards: Different regions may have specific standards and certifications. For instance, CE marking is essential in Europe, while buyers in Africa may need to consider local compliance requirements.
- Cultural Considerations: Awareness of cultural differences in business practices can affect negotiations and quality expectations. Establishing clear communication about quality standards is vital.
- Logistics and Transport: Quality assurance does not end with production. B2B buyers should ensure that suppliers have measures in place to protect products during shipping to prevent damage.
Conclusion
By understanding the manufacturing processes and quality assurance measures involved in metal furniture production, B2B buyers can make more informed decisions. Recognizing the significance of quality standards, checkpoints, and testing methods will lead to better supplier relationships and ultimately, a superior product offering.
Practical Sourcing Guide: A Step-by-Step Checklist for ‘metal furniture supplier’
In the world of B2B procurement, sourcing a reliable metal furniture supplier is crucial for ensuring quality, durability, and timely delivery of products. This step-by-step checklist is designed to guide international buyers, particularly those from Africa, South America, the Middle East, and Europe, through the process of selecting the right supplier.
Step 1: Define Your Technical Specifications
Clearly outlining your technical requirements is the foundation of a successful sourcing process. This includes dimensions, materials, finishes, and functionality of the metal furniture you need.
– Why It Matters: Defining specifications ensures that suppliers understand your needs, which helps in getting accurate quotes and prevents miscommunication.
– What to Look For: Be detailed about the types of metal (e.g., steel, aluminum), finishes (e.g., powder-coated, galvanized), and any additional features (e.g., stackability, mobility).
Step 2: Conduct Market Research
Understanding the market landscape is essential for identifying potential suppliers. Research suppliers that specialize in metal furniture and have a proven track record.
– Why It Matters: This step helps you gauge the variety of options available and the reputation of different suppliers in the industry.
– What to Look For: Check online directories, trade shows, and industry publications for supplier listings. Look for reviews or testimonials from previous customers.
Step 3: Evaluate Potential Suppliers
Before committing, it’s crucial to vet suppliers thoroughly. Request company profiles, case studies, and references from buyers in a similar industry or region.
– Why It Matters: Evaluating suppliers reduces the risk of working with unreliable partners and ensures that they meet your quality standards.
– What to Look For: Assess their production capacity, quality control processes, and delivery timelines. Check if they have experience working with international clients.
Step 4: Verify Supplier Certifications
Ensure that potential suppliers hold the necessary certifications for quality and safety standards, such as ISO 9001 or CE marking.
– Why It Matters: Certifications are indicators of a supplier’s commitment to quality and compliance with international standards, which is critical for durability and safety.
– What to Look For: Request copies of certifications and verify them with the issuing bodies.
Step 5: Request Samples
Before finalizing your order, ask for samples of the metal furniture to assess quality and craftsmanship.
– Why It Matters: Physical samples provide a tangible representation of what to expect and allow you to evaluate the material, finish, and construction quality.
– What to Look For: Pay attention to the finish, sturdiness, and overall design. Ensure that the sample matches the specifications provided.
Step 6: Negotiate Terms and Pricing
Once you’ve shortlisted suppliers, engage in negotiations regarding pricing, payment terms, and delivery schedules.
– Why It Matters: Effective negotiation can lead to better pricing and terms, which can significantly affect your overall procurement budget.
– What to Look For: Be clear about your budget constraints and ask for bulk discounts or flexible payment options.
Step 7: Establish a Communication Plan
Set up a communication plan for ongoing discussions during the procurement process, including updates on order status and any issues that may arise.
– Why It Matters: Clear communication helps in building a strong relationship with your supplier and ensures that any potential issues are addressed promptly.
– What to Look For: Agree on preferred communication channels (e.g., email, phone) and response times to facilitate smooth interactions.
By following this practical checklist, B2B buyers can enhance their sourcing strategy for metal furniture suppliers, ensuring they make informed decisions that align with their business needs.
Comprehensive Cost and Pricing Analysis for metal furniture supplier Sourcing
What Are the Key Cost Components in Metal Furniture Supplier Sourcing?
When sourcing metal furniture, understanding the cost structure is vital for international B2B buyers. The primary cost components include:
-
Materials: The choice of metal (e.g., steel, aluminum) significantly impacts costs. High-quality, rust-resistant materials may come at a premium, but they enhance durability and longevity.
-
Labor: Labor costs vary by region. Countries with lower labor costs can offer competitive pricing, but it is essential to ensure that quality is not compromised. Skilled labor may demand higher wages but can result in superior craftsmanship.
-
Manufacturing Overhead: This includes utilities, rent, and equipment costs. Efficient manufacturing processes can reduce overhead, allowing suppliers to offer better pricing.
-
Tooling: Custom tooling for unique designs or specifications can lead to higher upfront costs. However, investing in quality tooling may reduce long-term production costs.
-
Quality Control (QC): Implementing robust QC processes ensures that the furniture meets required standards. While this may increase initial costs, it can minimize returns and dissatisfaction, ultimately enhancing the supplier’s reputation.
-
Logistics: Shipping and handling costs can vary widely based on distance, shipping method, and Incoterms. Buyers should consider these expenses when evaluating supplier quotes.
-
Margin: Suppliers typically include a profit margin in their pricing. Understanding the market rates in different regions can help buyers gauge whether a supplier’s margin is reasonable.
How Do Price Influencers Affect Metal Furniture Sourcing?
Several factors can influence the pricing of metal furniture, particularly for international buyers:
-
Volume/MOQ (Minimum Order Quantity): Suppliers often provide discounts for larger orders. Buyers should assess their needs to determine if they can meet MOQs to capitalize on these savings.
-
Specifications and Customization: Custom designs may incur additional costs. Buyers should clarify the extent of customization required and how it will affect pricing.
-
Materials: As mentioned, the choice of materials directly impacts costs. Buyers should consider the trade-off between material quality and price.
-
Quality Certifications: Certifications (such as ISO or environmental certifications) may influence costs. Suppliers with recognized certifications might charge more due to the higher standards they maintain.
-
Supplier Factors: The supplier’s reputation, location, and operational efficiency can affect pricing. Established suppliers with a track record may command higher prices but could offer better reliability and service.
-
Incoterms: The chosen Incoterms (e.g., FOB, CIF) will influence logistics costs. Buyers should fully understand these terms to avoid unexpected charges.
What Are the Best Practices for Negotiating Metal Furniture Prices?
International B2B buyers, especially from regions like Africa, South America, the Middle East, and Europe, can benefit from specific negotiation strategies:
-
Research and Benchmarking: Understand market pricing and compare quotes from multiple suppliers to identify reasonable pricing.
-
Establish Long-Term Relationships: Building strong relationships with suppliers can lead to better pricing over time. Loyal buyers may receive preferential treatment and pricing.
-
Discuss Total Cost of Ownership (TCO): Highlight the importance of TCO, which includes not only purchase price but also maintenance, durability, and potential resale value. A higher upfront cost may be justifiable if the furniture lasts longer.
-
Be Clear About Requirements: Clearly articulate your needs and specifications to avoid misunderstandings that could lead to unexpected costs.
-
Flexibility in Terms: Be open to negotiating payment terms and delivery schedules, which can sometimes lead to cost reductions or added value.
Are There Any Pricing Nuances International Buyers Should Consider?
International buyers should be aware of several nuances when sourcing metal furniture:
-
Currency Fluctuations: Changes in currency exchange rates can impact costs. It’s advisable to negotiate pricing in a stable currency.
-
Import Tariffs and Duties: Understand the import regulations and potential tariffs for metal furniture in your country. These can significantly affect the overall cost.
-
Cultural Considerations: Different regions may have varying expectations regarding negotiation styles and business practices. Understanding these cultural nuances can facilitate smoother transactions.
Disclaimer on Pricing
Prices in this analysis are indicative and may vary based on market conditions, supplier negotiations, and specific buyer requirements. Always consult multiple sources and conduct thorough due diligence to ensure the best pricing strategy for your needs.
Alternatives Analysis: Comparing metal furniture supplier With Other Solutions
Introduction: Understanding Alternative Solutions for Metal Furniture Suppliers
When considering the procurement of metal furniture, international B2B buyers often encounter various options that can serve similar purposes. Understanding these alternatives is crucial in making informed decisions that align with specific business needs, budget constraints, and operational efficiencies. This section compares metal furniture suppliers with other viable solutions, emphasizing performance, cost, ease of implementation, maintenance, and best use cases.
Comparison Table of Metal Furniture Supplier and Alternatives
Comparison Aspect | Metal Furniture Supplier | Alternative 1: Wooden Furniture Supplier | Alternative 2: Modular Furniture Systems |
---|---|---|---|
Performance | High durability and longevity; resistant to corrosion and wear | Moderate durability; susceptible to damage from moisture and pests | Versatile design and functionality; customizable layouts |
Cost | Generally higher initial investment | Lower initial costs but potentially higher long-term maintenance | Mid-range costs with potential for scalability |
Ease of Implementation | Requires specialized assembly and tools | Easy to assemble; less specialized knowledge needed | Moderate; may require professional installation for complex designs |
Maintenance | Low maintenance; occasional cleaning needed | Regular maintenance required to prevent damage | Low maintenance; easy to clean and reconfigure |
Best Use Case | Industrial settings, outdoor use, high-traffic areas | Residential, offices with less wear and tear | Dynamic workspaces, collaborative environments |
Detailed Breakdown of Alternatives
What are the benefits and drawbacks of using a Wooden Furniture Supplier?
Wooden furniture suppliers offer a more traditional approach to furnishing spaces. The primary advantage is the lower upfront cost, making it an attractive option for businesses with tight budgets. Additionally, wooden furniture can provide a warm and inviting aesthetic, suitable for offices and homes. However, it is essential to consider its susceptibility to damage from moisture, pests, and wear, which may lead to higher long-term maintenance costs. For environments with less foot traffic and where aesthetics play a critical role, wooden furniture can be a viable choice.
How do Modular Furniture Systems compare to Metal Furniture Suppliers?
Modular furniture systems are designed for flexibility and adaptability, allowing businesses to customize their layouts as needed. This option is particularly beneficial for dynamic workspaces where collaboration and quick reconfiguration are essential. While the initial cost may fall in the mid-range, the ability to scale and adapt can lead to cost savings over time. However, the complexity of some modular systems may require professional installation, which can add to the overall expense. Modular systems are ideal for companies prioritizing collaboration and space optimization.
Conclusion: How to Choose the Right Solution for Your Business Needs
Selecting the right furnishing solution for your business involves assessing your specific requirements and constraints. Metal furniture suppliers offer unmatched durability and low maintenance, making them suitable for high-traffic and outdoor environments. In contrast, wooden furniture can be more cost-effective initially but may require more upkeep. Modular systems provide flexibility and scalability, catering to dynamic workspaces. By carefully evaluating each option’s performance, cost, and maintenance needs, B2B buyers can make informed decisions that best suit their operational goals and enhance their work environment.
Essential Technical Properties and Trade Terminology for metal furniture supplier
What Are the Essential Technical Properties for Metal Furniture Suppliers?
When selecting a metal furniture supplier, understanding the critical technical properties is vital for ensuring quality, durability, and compliance with industry standards. Here are some key specifications to consider:
1. Material Grade: Why Is It Important in Metal Furniture?
Material grade refers to the classification of metals based on their composition and properties. Common grades for metal furniture include stainless steel (e.g., 304, 316) and carbon steel (e.g., S235, S275). The choice of material affects not only the aesthetics but also the strength, corrosion resistance, and longevity of the furniture. For B2B buyers in regions like Africa and South America, where environmental conditions can vary widely, selecting the right material grade can significantly impact product performance.
2. Tolerance: What Does This Mean for Metal Furniture Manufacturing?
Tolerance indicates the allowable variation in dimensions during the manufacturing process. It is crucial for ensuring that parts fit together correctly and function as intended. For example, a tolerance of ±0.5 mm might be acceptable for some components, while others may require tighter tolerances. Understanding tolerances helps buyers ensure that the final product meets their specifications, which is essential for maintaining quality and reducing returns.
3. Surface Finish: How Does It Affect Metal Furniture Quality?
Surface finish refers to the texture and appearance of the metal surface after manufacturing. Common finishes include powder coating, anodizing, and galvanizing. Each finish offers different aesthetic qualities and protective benefits. For instance, powder coating can enhance durability and color options, while anodizing improves corrosion resistance. Buyers should consider the intended use of the furniture and the environmental conditions it will face to select the appropriate finish.
4. Load Capacity: Why Is This a Key Specification?
Load capacity is the maximum weight that a piece of furniture can safely support. This specification is particularly important for commercial buyers who require furniture that can withstand heavy use. Understanding load capacity helps prevent accidents and ensures that the furniture meets safety standards, which is crucial in sectors like hospitality and office environments.
5. Welding Standards: What Should Buyers Know?
Welding standards refer to the guidelines and specifications that govern how metal components are joined together. Compliance with standards such as ISO 3834 ensures that the welds are strong and reliable. Buyers should inquire about the welding processes used by suppliers to ensure that they meet industry standards, as this affects the overall strength and durability of the furniture.
What Trade Terminology Should B2B Buyers Understand?
Familiarity with trade terminology can streamline communication and negotiation processes with suppliers. Here are some common terms relevant to metal furniture procurement:
1. OEM (Original Equipment Manufacturer): What Does This Mean for Buyers?
An OEM is a company that produces parts or products that are used in another company’s final product. In the context of metal furniture, buyers may work with OEMs to create custom designs. Understanding OEM relationships can help buyers assess the quality and reliability of the supplier.
2. MOQ (Minimum Order Quantity): Why Is It Significant?
MOQ refers to the smallest quantity of an item that a supplier is willing to sell. This term is crucial for B2B buyers, as it can impact inventory costs and cash flow. Understanding MOQ helps buyers plan their purchasing strategies effectively, especially in regions with different supply chain dynamics.
3. RFQ (Request for Quotation): How Can It Aid the Purchasing Process?
An RFQ is a document that buyers send to suppliers to request pricing and terms for specific products. This process helps buyers compare different suppliers and negotiate better deals. Utilizing RFQs can lead to cost savings and ensure that buyers receive competitive offers.
4. Incoterms: What Are They and Why Are They Important?
Incoterms (International Commercial Terms) are standardized trade terms that define the responsibilities of buyers and sellers in international transactions. Knowing the relevant Incoterms, such as FOB (Free on Board) or CIF (Cost, Insurance, and Freight), helps buyers understand shipping costs and risks, facilitating smoother logistics and clearer agreements.
By comprehending these essential technical properties and trade terminologies, international B2B buyers can make informed decisions when sourcing metal furniture, ultimately leading to better quality products and successful business relationships.
Navigating Market Dynamics and Sourcing Trends in the metal furniture supplier Sector
What Are the Current Market Dynamics and Sourcing Trends in the Metal Furniture Sector?
Market Overview & Key Trends
The global metal furniture market is witnessing substantial growth driven by urbanization, an increasing demand for modern and functional designs, and the rise of e-commerce platforms. International B2B buyers, particularly from regions like Africa, South America, the Middle East, and Europe, are seeking durable and aesthetically pleasing metal furniture solutions for both residential and commercial spaces. Key trends include customization, with suppliers offering tailored designs to meet specific client needs, and the integration of technology, such as augmented reality (AR) for virtual showrooms, which enhances the buyer’s experience.
Another significant dynamic is the shift towards local sourcing to reduce lead times and shipping costs. Buyers are increasingly looking for suppliers who can provide just-in-time manufacturing capabilities, allowing for quicker fulfillment without the burden of extensive inventory. This trend is particularly noticeable in Africa and South America, where local suppliers are leveraging regional materials to create unique products that resonate with cultural preferences. The emergence of digital platforms is also transforming sourcing processes, enabling buyers to connect with suppliers globally, compare prices, and evaluate product quality more effectively.
How Is Sustainability Shaping the Metal Furniture Supply Chain?
Sustainability has become a critical consideration for B2B buyers in the metal furniture sector. The environmental impact of manufacturing processes, particularly in terms of energy consumption and waste, is under scrutiny. Buyers are increasingly prioritizing suppliers who demonstrate a commitment to sustainable practices, such as using recycled materials or adopting energy-efficient production methods.
Ethical sourcing is equally important, with buyers seeking suppliers who ensure fair labor practices and transparency in their supply chains. Certifications such as ISO 14001 (Environmental Management) and FSC (Forest Stewardship Council) can significantly influence purchasing decisions, as they provide assurance of a supplier’s commitment to sustainability. Additionally, the demand for ‘green’ materials, such as low-VOC paints and finishes, is on the rise, as buyers aim to minimize the ecological footprint of their purchases.
What Is the Evolution of the Metal Furniture Supplier Sector?
The metal furniture sector has evolved significantly over the decades, transitioning from traditional handcrafted methods to advanced manufacturing technologies. Initially, metal furniture was predominantly utilitarian, designed for functionality rather than aesthetics. However, with the advent of modern design movements in the mid-20th century, the focus shifted towards creating stylish and contemporary pieces that cater to diverse tastes.
The introduction of advanced welding techniques and machinery has allowed manufacturers to produce high-quality products with intricate designs at scale. Furthermore, the digital transformation of the industry, marked by the rise of e-commerce and virtual showrooms, has changed how buyers interact with suppliers, leading to more informed purchasing decisions. This evolution underscores the importance of adaptability for suppliers in meeting the changing preferences and demands of international B2B buyers.
Through understanding these dynamics, buyers can make informed choices, align with forward-thinking suppliers, and contribute to a sustainable future in the metal furniture industry.
Frequently Asked Questions (FAQs) for B2B Buyers of metal furniture supplier
-
How do I identify a reliable metal furniture supplier for my business?
To identify a reliable metal furniture supplier, start by researching their reputation in the industry. Look for reviews and testimonials from previous clients, and check their presence on trade platforms such as Alibaba or Global Sources. Verify their certifications, such as ISO, which indicate adherence to quality standards. Additionally, request samples to assess the quality of their products firsthand. Engaging with suppliers who have experience in your specific market region, such as Africa or South America, can also enhance trust and facilitate smoother transactions. -
What is the best way to negotiate pricing with a metal furniture supplier?
When negotiating pricing with a metal furniture supplier, prepare by researching market rates and understanding your budget constraints. Initiate discussions by expressing interest in a long-term partnership, which may encourage suppliers to offer better rates. Be clear about your required specifications and volumes, as larger orders can lead to discounts. Consider discussing payment terms, such as deposits or installment payments, to ease financial strain. Lastly, don’t hesitate to ask for additional perks like free shipping or bulk discounts to maximize your investment. -
What customization options should I expect from a metal furniture supplier?
Most metal furniture suppliers offer a range of customization options, including size, color, finish, and design modifications. When engaging a supplier, inquire about their capabilities for bespoke designs or adaptations to meet specific aesthetic or functional needs. Discuss your requirements clearly, providing sketches or examples if necessary. It’s essential to understand the lead times for custom orders, as these may vary significantly from standard products. Additionally, confirm if there are any minimum order quantities (MOQs) for customized pieces, as this can impact your purchasing decisions. -
What are the typical minimum order quantities (MOQs) for metal furniture?
Minimum order quantities (MOQs) for metal furniture can vary widely depending on the supplier and the type of products ordered. Generally, MOQs may range from 50 to 500 units. Some suppliers may be flexible, especially if you are ordering a diverse range of products or establishing a long-term relationship. Always discuss MOQs upfront to avoid surprises later. If you’re a smaller business or a startup, consider looking for suppliers who specialize in smaller batches or are open to negotiation on minimums. -
How can I ensure quality assurance when sourcing metal furniture internationally?
To ensure quality assurance when sourcing metal furniture internationally, start by requesting samples before placing a large order. Establish clear quality standards and specifications, and communicate these with your supplier. Consider implementing third-party inspections at various stages of production and before shipment to validate quality compliance. Additionally, familiarize yourself with the supplier’s quality control processes and certifications. Building a strong relationship with your supplier can also enhance accountability and encourage adherence to quality standards. -
What payment terms are commonly offered by metal furniture suppliers?
Payment terms can vary among metal furniture suppliers, but common options include upfront payments, deposits (often 30% at order confirmation), and balance payments upon delivery or before shipping. Some suppliers may offer flexible payment plans or financing options, particularly for larger orders. It’s important to clarify payment methods accepted, such as bank transfers, letters of credit, or online payment platforms. Always ensure that terms are outlined in a formal contract to avoid misunderstandings. -
What logistics considerations should I keep in mind when importing metal furniture?
When importing metal furniture, logistics considerations include shipping methods, lead times, and customs regulations. Determine whether sea freight or air freight is more suitable for your order size and urgency. Assess the supplier’s experience with international shipping to ensure smooth logistics. Familiarize yourself with import duties and taxes applicable in your country, and factor these into your total cost. Collaborating with a reliable freight forwarder can also help navigate the complexities of customs clearance and delivery. -
How do I handle disputes with a metal furniture supplier?
Handling disputes with a metal furniture supplier requires clear communication and documentation. Start by addressing the issue directly with the supplier, outlining your concerns and providing evidence, such as photographs or contracts. If the issue remains unresolved, refer to any agreements made regarding dispute resolution, which may include mediation or arbitration. Maintaining a professional tone during discussions can facilitate a more amicable resolution. If necessary, consider seeking legal advice, especially if significant financial investments are involved.
Important Disclaimer & Terms of Use
⚠️ Important Disclaimer
The information provided in this guide, including content regarding manufacturers, technical specifications, and market analysis, is for informational and educational purposes only. It does not constitute professional procurement advice, financial advice, or legal advice.
While we have made every effort to ensure the accuracy and timeliness of the information, we are not responsible for any errors, omissions, or outdated information. Market conditions, company details, and technical standards are subject to change.
B2B buyers must conduct their own independent and thorough due diligence before making any purchasing decisions. This includes contacting suppliers directly, verifying certifications, requesting samples, and seeking professional consultation. The risk of relying on any information in this guide is borne solely by the reader.
Strategic Sourcing Conclusion and Outlook for metal furniture supplier
The importance of strategic sourcing in the metal furniture sector cannot be overstated. By establishing robust supplier relationships, international B2B buyers can ensure access to high-quality materials, competitive pricing, and innovative designs. This strategic approach not only mitigates risks associated with supply chain disruptions but also enhances overall operational efficiency.
How Can International Buyers Leverage Strategic Sourcing for Metal Furniture?
For buyers in Africa, South America, the Middle East, and Europe, understanding local market dynamics and supplier capabilities is essential. Engaging with multiple suppliers allows for a diversified sourcing strategy that can adapt to fluctuating market conditions and evolving consumer preferences. Additionally, leveraging technology to streamline procurement processes can lead to significant cost savings and improved lead times.
What is the Future Outlook for Metal Furniture Sourcing?
As the demand for sustainable and customizable metal furniture continues to rise, suppliers who invest in eco-friendly practices and innovative designs will gain a competitive edge. International buyers should prioritize partnerships with manufacturers committed to sustainability and quality assurance.
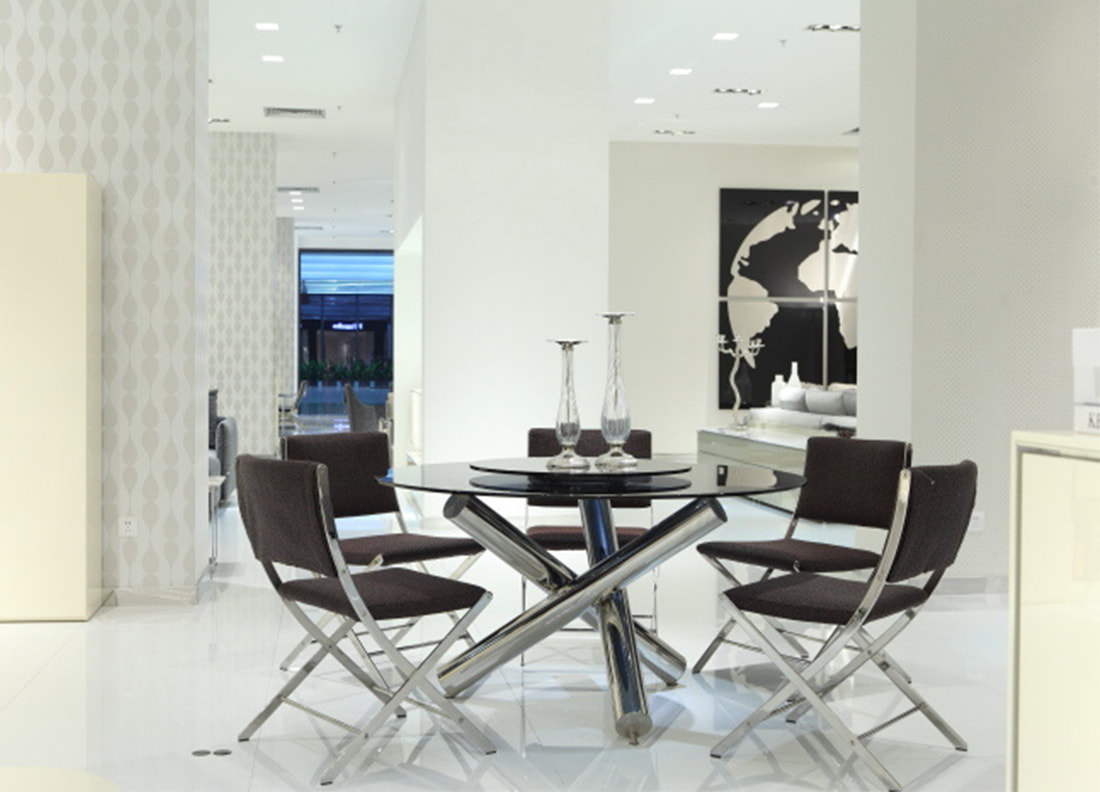
A stock image related to metal furniture supplier.
By taking these proactive steps, businesses can position themselves for long-term success in the global marketplace. Embrace strategic sourcing today to unlock new opportunities and elevate your metal furniture offerings to meet the needs of a diverse clientele.