Discover Top Oximeter Manufacturers: The Ultimate Buying Guide (2025)
Introduction: Navigating the Global Market for oximeter manufacturer
In today’s fast-paced healthcare environment, sourcing reliable oximeter manufacturers presents a significant challenge for B2B buyers, especially those operating in diverse markets like Africa, South America, the Middle East, and Europe. The demand for high-quality, accurate, and affordable pulse oximeters is on the rise, driven by increased awareness of respiratory health and the need for efficient patient monitoring solutions. This comprehensive guide aims to demystify the global market for oximeter manufacturing, providing actionable insights into the types of devices available, their applications, and the critical factors to consider when selecting a supplier.
Understanding the intricate landscape of oximeter manufacturers involves exploring various aspects such as product specifications, regulatory compliance, and market trends. This guide will equip international B2B buyers with essential knowledge on vetting potential suppliers, evaluating costs, and ensuring product quality. By addressing these key components, buyers can make informed purchasing decisions that align with their operational needs and budget constraints.
Whether you are a healthcare provider in Kenya, a distributor in Argentina, or an importer in Europe, this guide serves as your roadmap to navigating the complexities of the oximeter market. With expert insights and practical strategies, you will be empowered to choose the right manufacturer that meets your specific requirements, ensuring that your organization remains competitive in an increasingly globalized industry.
Understanding oximeter manufacturer Types and Variations
Type Name | Key Distinguishing Features | Primary B2B Applications | Brief Pros & Cons for Buyers |
---|---|---|---|
Finger Pulse Oximeters | Compact, portable, easy-to-use; measures oxygen saturation | Clinics, home health monitoring | Pros: Affordable, user-friendly. Cons: Limited to finger measurements. |
Handheld Oximeters | Larger, often more accurate; suitable for diverse settings | Hospitals, emergency services | Pros: High accuracy, versatile use. Cons: Less portable, higher cost. |
Tabletop Oximeters | Stationary, designed for continuous monitoring | ICUs, surgical settings | Pros: Continuous monitoring capability. Cons: Requires dedicated space. |
Wearable Oximeters | Integrated into wristbands or smart devices | Telemedicine, fitness tracking | Pros: Convenient, promotes patient engagement. Cons: May lack clinical accuracy. |
Veterinary Oximeters | Designed for animal use, often with specialized sensors | Veterinary clinics, animal hospitals | Pros: Tailored for animal physiology. Cons: Limited availability and higher costs. |
What Are the Key Characteristics of Finger Pulse Oximeters?
Finger pulse oximeters are compact devices that provide a quick and easy way to measure blood oxygen saturation levels and heart rate. Their portability makes them ideal for clinics and home health monitoring, especially in regions with limited access to advanced medical facilities. When purchasing, consider factors like battery life, ease of use, and whether they meet local regulatory standards.
How Do Handheld Oximeters Differ in Functionality?
Handheld oximeters are larger and typically more accurate than finger models. They are designed for use in hospitals and emergency services, where precise measurements are critical. These devices can accommodate a variety of measurement sites (e.g., finger, toe, earlobe), making them versatile for different patient populations. B2B buyers should evaluate the calibration frequency, warranty, and service support offered by manufacturers to ensure reliable performance.
Why Choose Tabletop Oximeters for Continuous Monitoring?
Tabletop oximeters are designed for stationary use, often found in intensive care units (ICUs) and surgical settings. They offer continuous monitoring capabilities, essential for critically ill patients. When considering a purchase, buyers should assess the device’s data management capabilities and compatibility with existing hospital information systems to streamline patient monitoring and reporting.
What Are the Advantages of Wearable Oximeters?
Wearable oximeters, such as those integrated into fitness trackers, provide a convenient way for patients to monitor their oxygen levels and heart rates in real-time. These devices are particularly beneficial in telemedicine and fitness tracking, engaging patients in their health management. However, B2B buyers should be cautious about the accuracy of these devices compared to clinical-grade oximeters and consider the technological support available for integration with health apps.
How Are Veterinary Oximeters Specialized for Animal Use?
Veterinary oximeters are specifically designed to accommodate the physiological differences in animals, often featuring specialized sensors for various species. These devices are crucial in veterinary clinics and animal hospitals for monitoring oxygen saturation in pets and livestock. Buyers should consider the device’s adaptability to different animal sizes and species, as well as the availability of support and training from manufacturers.
Related Video: How to use Pulse oximeter accurately (Helpful tips and tricks)
Key Industrial Applications of oximeter manufacturer
Industry/Sector | Specific Application of oximeter manufacturer | Value/Benefit for the Business | Key Sourcing Considerations for this Application |
---|---|---|---|
Healthcare | Patient monitoring in hospitals | Enhances patient care and reduces mortality rates | Regulatory compliance, calibration standards |
Sports and Fitness | Performance tracking in athletes | Improves training efficiency and performance | Durability, accuracy under extreme conditions |
Home Care | Remote patient monitoring | Enables better management of chronic conditions | Connectivity features, ease of use |
Veterinary Medicine | Monitoring animal health | Ensures timely medical interventions for pets | Animal-specific adaptations, ruggedness |
Research Laboratories | Clinical trials and studies | Facilitates accurate data collection for research | Precision, data logging capabilities |
How is Oximeter Manufacturer Used in Healthcare?
In the healthcare sector, oximeters are crucial for patient monitoring in hospitals and clinics. These devices measure blood oxygen saturation levels, providing real-time data that can influence treatment decisions. For international buyers, particularly from regions like Africa and South America, sourcing oximeters that comply with local regulatory standards is essential. Additionally, calibration standards must be adhered to ensure accuracy, which is vital in emergency situations to reduce mortality rates.
What Role Do Oximeters Play in Sports and Fitness?
In the sports and fitness industry, oximeters are used to track athletes’ performance by monitoring oxygen levels during training sessions. This data helps coaches and athletes optimize their training regimens, ensuring that athletes are training effectively without risking overexertion. Buyers from Europe and the Middle East should look for devices that can withstand rigorous physical conditions and offer high durability. Accurate readings in various environments are critical for maximizing performance outcomes.
How Do Oximeters Benefit Home Care Providers?
Oximeters play a significant role in home care, particularly for patients with chronic respiratory conditions. They enable remote monitoring, allowing healthcare providers to track patients’ oxygen levels without the need for frequent office visits. For international B2B buyers, selecting devices with robust connectivity features is key, as these allow for seamless data transmission to healthcare professionals. Ease of use is also crucial to ensure that patients can operate the device without assistance.
What is the Importance of Oximeters in Veterinary Medicine?
In veterinary medicine, oximeters are essential for monitoring the health of animals, especially during surgeries or in critical care situations. These devices help veterinarians ensure that pets receive timely medical interventions by monitoring their oxygen saturation levels. Buyers in Africa and South America should consider oximeters that are specifically adapted for animals, offering ruggedness to handle various environments. The ability to withstand rough handling is also an important factor for veterinary applications.
How Are Oximeters Utilized in Research Laboratories?
In research laboratories, oximeters are used in clinical trials to collect precise data on blood oxygen levels among study participants. This information is critical for understanding the effects of new drugs or treatments. For B2B buyers in Europe and the Middle East, sourcing oximeters with high precision and reliable data logging capabilities is essential. Ensuring that the devices can integrate with other laboratory equipment can also enhance the efficiency of research studies, making it a vital consideration for international buyers.
Related Video: Types Of Flowmeters And Their Industrial Applications.
3 Common User Pain Points for ‘oximeter manufacturer’ & Their Solutions
Scenario 1: Navigating Quality Assurance Challenges in Oximeter Manufacturing
The Problem: B2B buyers often face significant challenges in ensuring the quality and reliability of oximeters sourced from manufacturers. This is particularly true for buyers in regions like Africa and South America, where regulatory standards may vary. Buyers may find themselves with devices that do not meet local health regulations, leading to potential liability issues and financial losses. Additionally, inconsistent product quality can hinder trust between buyers and suppliers, complicating long-term partnerships.
The Solution: To navigate these quality assurance challenges, buyers should prioritize manufacturers that have robust quality management systems certified by recognized international standards, such as ISO 13485. When sourcing, it is advisable to request documentation of compliance with local and international regulations. Furthermore, conducting factory audits or third-party inspections can be invaluable. Buyers should also engage in direct communication with manufacturers to discuss quality control processes and product testing methods. Establishing a clear quality assurance agreement that outlines expectations and penalties for non-compliance can solidify trust and accountability.
Scenario 2: Overcoming Supply Chain Disruptions for Oximeter Procurement
The Problem: Supply chain disruptions are a common pain point for B2B buyers, especially in the context of global events like pandemics or geopolitical tensions. Buyers in the Middle East and Europe may experience delays in receiving oximeters due to shipping bottlenecks or shortages of raw materials. This can lead to stockouts, affecting the ability of healthcare providers to offer timely patient care and damaging the buyer’s reputation in the market.
The Solution: To mitigate supply chain risks, buyers should diversify their supplier base by engaging with multiple manufacturers across different regions. This reduces dependency on a single source and enhances resilience against disruptions. Additionally, implementing just-in-time inventory practices can help manage stock levels more effectively. Buyers should also consider establishing long-term contracts with manufacturers that include clauses for expedited shipping during emergencies. Regular communication with suppliers to monitor inventory levels and anticipated shipping timelines is crucial for proactive management.
Scenario 3: Addressing the Need for Customization in Oximeter Devices
The Problem: Many B2B buyers encounter difficulties when the standard oximeter offerings do not meet specific clinical needs. For instance, healthcare providers in Kenya may require oximeters that can function effectively in remote locations with limited power supply or in environments with high humidity. When manufacturers fail to offer customizable solutions, buyers may be forced to compromise, resulting in suboptimal patient care.
The Solution: Buyers should actively seek out manufacturers that specialize in customization and have a flexible product development process. When engaging with potential suppliers, clearly articulate specific needs and constraints, such as environmental conditions or technological features. It is beneficial to request prototypes or samples to evaluate performance in real-world settings before making bulk purchases. Establishing a collaborative relationship with the manufacturer can also facilitate the development of tailored solutions, ensuring that the final product aligns with clinical requirements. Regular feedback loops during the product development phase can lead to better outcomes and enhanced satisfaction.
Strategic Material Selection Guide for oximeter manufacturer
When selecting materials for manufacturing oximeters, it is crucial to consider their properties, advantages, and limitations. This guide analyzes common materials used in oximeter production, providing actionable insights for international B2B buyers, particularly from regions such as Africa, South America, the Middle East, and Europe.
What are the Key Properties of Common Oximeter Materials?
1. Polycarbonate (PC)
Polycarbonate is a robust thermoplastic known for its high impact resistance and optical clarity. It can withstand temperatures ranging from -40°C to 120°C, making it suitable for various environments. Its excellent dimensional stability and resistance to UV light also enhance its longevity in medical applications.
Pros & Cons:
– Pros: High durability, lightweight, and good optical properties.
– Cons: Higher manufacturing complexity and cost compared to other plastics.
Impact on Application:
Polycarbonate is often used in the housing of oximeters, ensuring protection against physical shocks and environmental factors.
Considerations for International Buyers:
Buyers should verify compliance with international standards such as ISO 13485 for medical devices and check for certifications that validate the material’s safety and efficacy.
2. Stainless Steel
Stainless steel is a popular choice due to its corrosion resistance and mechanical strength. It can withstand a wide range of temperatures and is easy to sterilize, making it ideal for medical devices.
Pros & Cons:
– Pros: Exceptional durability, resistance to corrosion, and ease of cleaning.
– Cons: Higher weight and cost compared to plastics; potential for thermal conductivity issues.
Impact on Application:
Stainless steel components are often used in the internal mechanisms of oximeters, where durability and sterility are paramount.
Considerations for International Buyers:
Buyers should ensure that the stainless steel used meets ASTM standards and is suitable for medical applications, particularly in regions with stringent health regulations.
3. Silicone Rubber
Silicone rubber is favored for its flexibility, biocompatibility, and temperature stability. It can operate effectively in temperatures ranging from -60°C to 200°C, making it versatile for various applications.
Pros & Cons:
– Pros: Excellent flexibility, biocompatibility, and resistance to extreme temperatures.
– Cons: Generally more expensive and can be less durable than other materials under certain conditions.
Impact on Application:
Silicone rubber is often utilized in the sealing and cushioning components of oximeters, providing comfort and protection for users.
Considerations for International Buyers:
Ensure that silicone materials comply with biocompatibility standards, such as ISO 10993, especially for markets with strict health regulations.
4. Acrylic (PMMA)
Acrylic is a lightweight, transparent thermoplastic known for its clarity and UV resistance. It is less impact-resistant than polycarbonate but offers excellent optical properties.
Pros & Cons:
– Pros: Cost-effective, good optical clarity, and lightweight.
– Cons: Less durable than polycarbonate and can scratch easily.
Impact on Application:
Acrylic is typically used in the display screens of oximeters, where visual clarity is essential.
Considerations for International Buyers:
Buyers should consider the environmental impact of acrylic production and ensure that it meets local regulations regarding plastics.
Summary Table of Material Selection for Oximeter Manufacturing
Material | Typical Use Case for oximeter manufacturer | Key Advantage | Key Disadvantage/Limitation | Relative Cost (Low/Med/High) |
---|---|---|---|---|
Polycarbonate | Housing and protective casing | High impact resistance | Higher manufacturing complexity | Medium |
Stainless Steel | Internal mechanisms | Exceptional durability | Higher weight and cost | High |
Silicone Rubber | Sealing and cushioning components | Excellent flexibility and comfort | More expensive, less durable | Medium |
Acrylic | Display screens | Cost-effective and lightweight | Less durable, scratches easily | Low |
This strategic material selection guide provides essential insights into the materials used in oximeter manufacturing, helping international B2B buyers make informed decisions tailored to their specific market needs and regulatory environments.
In-depth Look: Manufacturing Processes and Quality Assurance for oximeter manufacturer
What Are the Key Stages in the Manufacturing Process of Oximeters?
The manufacturing process for oximeters involves several critical stages, each designed to ensure the final product meets strict quality standards. Understanding these stages can help international B2B buyers assess the reliability and capability of potential suppliers.
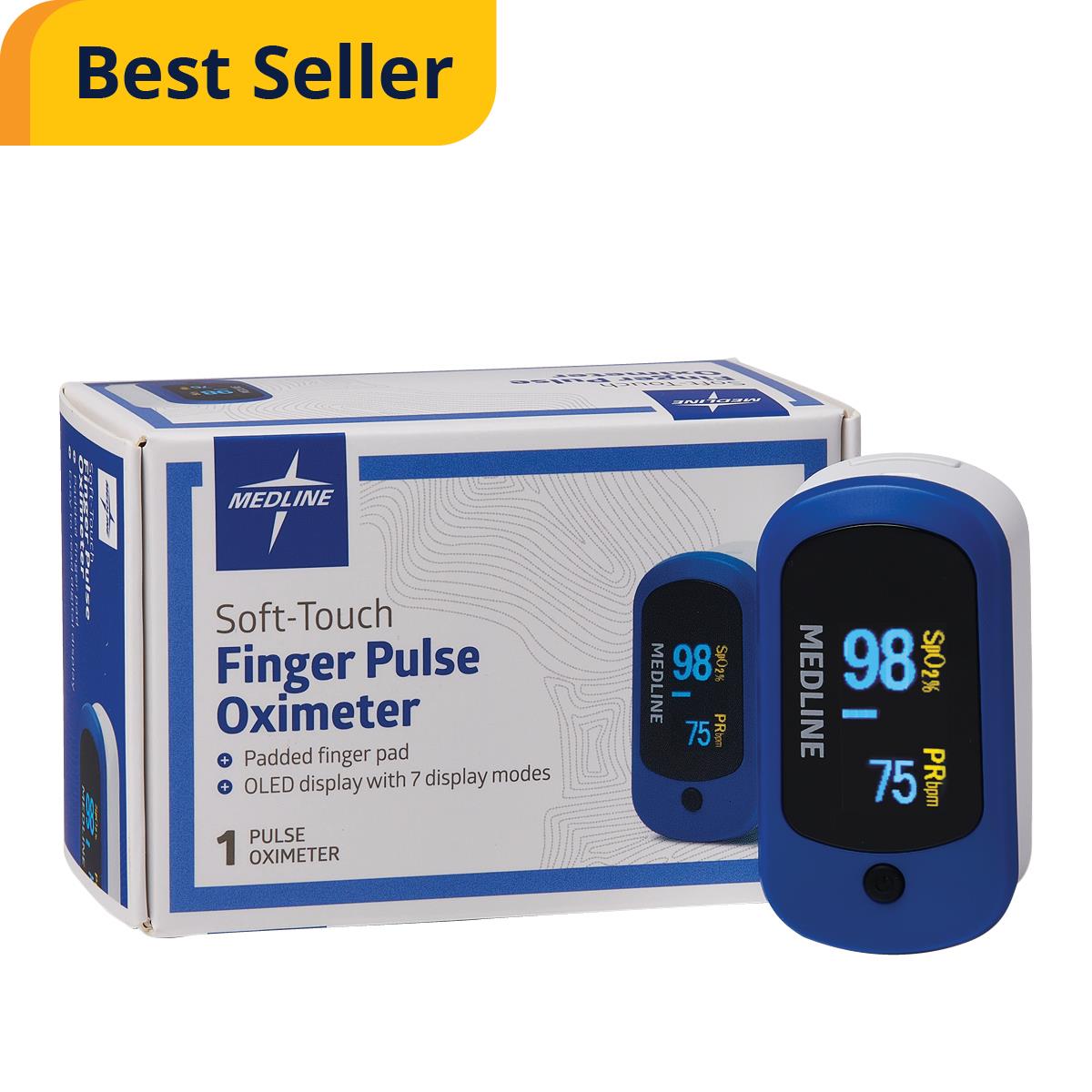
A stock image related to oximeter manufacturer.
1. Material Preparation
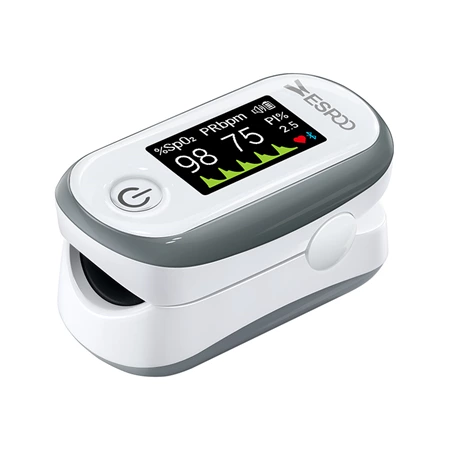
A stock image related to oximeter manufacturer.
The first stage in the manufacturing process is material preparation. This involves sourcing high-quality components such as sensors, microcontrollers, and display units. Manufacturers often utilize durable materials like medical-grade plastics and metals that can withstand sterilization processes. Key considerations include:
- Supplier Selection: Buyers should ensure that suppliers have a robust supply chain for sourcing materials that meet industry regulations.
- Material Specifications: Confirm that materials are compliant with international standards such as ISO 13485, which is critical for medical devices.
2. Forming and Component Fabrication
Once materials are prepared, the next step is forming and fabricating components. This process typically includes:
- Injection Molding: Used for creating plastic housings and components. Precision is vital to ensure a proper fit and finish.
- Circuit Board Fabrication: This includes soldering components onto printed circuit boards (PCBs) that are essential for the oximeter’s functionality.
- Sensor Calibration: Sensors must be calibrated to ensure accurate readings, which is a critical aspect of the manufacturing process.
Buyers should inquire about the types of machinery used and the level of automation in this stage to assess efficiency and quality.
3. Assembly
The assembly stage combines all the fabricated components into a finished oximeter. This process includes:
- Component Integration: Each part, from the sensor to the display, must be assembled with precision. Automated assembly lines can enhance consistency.
- Software Installation: The software that operates the oximeter is uploaded and tested during this stage. Buyers should verify that manufacturers use up-to-date software protocols.
B2B buyers should consider the manufacturer’s experience with assembly processes and their ability to scale production based on demand.
4. Finishing
Finishing involves final touches that enhance the product’s aesthetic and functional qualities. This may include:
- Surface Treatment: Processes like painting or coating to provide durability and resistance to wear.
- Final Assembly Checks: Inspecting the assembled product for any defects or assembly issues.
At this stage, buyers should look for manufacturers who implement rigorous final inspection protocols to ensure product readiness.
How Is Quality Assurance Integrated into Oximeter Manufacturing?
Quality assurance (QA) is critical in ensuring that oximeters meet safety and performance standards. Understanding the QA processes can help buyers make informed decisions about their suppliers.
Relevant International Standards for Oximeter Manufacturers
Oximeter manufacturers must comply with various international standards to ensure product safety and efficacy. Key standards include:
- ISO 9001: A general quality management system standard that provides a framework for consistent quality in manufacturing.
- ISO 13485: Specifically tailored for medical devices, this standard focuses on meeting regulatory requirements and ensuring quality throughout the manufacturing process.
- CE Marking: Required for products sold in the European market, indicating compliance with health, safety, and environmental protection standards.
B2B buyers should verify that suppliers have appropriate certifications and understand the implications of these standards for product quality.
What Are the Common Quality Control Checkpoints?
Quality control (QC) is an integral part of the manufacturing process, ensuring that each stage meets established standards. Common QC checkpoints include:
- Incoming Quality Control (IQC): Inspecting raw materials and components upon arrival to ensure they meet specifications.
- In-Process Quality Control (IPQC): Monitoring the manufacturing process at various stages to detect and address issues in real time.
- Final Quality Control (FQC): Conducting comprehensive tests on the finished product to ensure it meets all regulatory and performance standards.
Buyers should ask manufacturers about their specific QC processes and how they document compliance.
What Testing Methods Are Commonly Used for Oximeters?
Testing is crucial in the manufacturing of oximeters to ensure they perform accurately and reliably. Common testing methods include:
- Functional Testing: Verifying that the oximeter operates correctly and provides accurate readings.
- Environmental Testing: Assessing the device’s performance under various environmental conditions such as temperature and humidity.
- Durability Testing: Evaluating the product’s longevity and resistance to wear and tear.
B2B buyers should request information on the testing protocols used by manufacturers and review test reports to ensure compliance with international standards.
How Can B2B Buyers Verify Supplier Quality Control?
Verifying the quality control measures of potential suppliers is essential for B2B buyers. Here are several ways to conduct this verification:
1. Supplier Audits
Conducting on-site audits allows buyers to assess the manufacturing processes, quality control systems, and compliance with international standards firsthand. This can include:
- Process Observations: Watching the production line in action to gauge efficiency and adherence to protocols.
- Document Review: Examining quality control documentation and records of past audits.
2. Quality Reports
Requesting detailed quality reports can provide insights into a manufacturer’s performance over time. Look for:
- Defect Rates: Information on how often products fail quality checks can indicate overall reliability.
- Corrective Actions: Understanding how manufacturers address and rectify quality issues is crucial.
3. Third-Party Inspections
Engaging third-party inspection services can add an additional layer of assurance. These services offer unbiased evaluations of the manufacturing process and final products. Buyers should seek recommendations for reputable inspection agencies.
Conclusion: Navigating Quality Assurance for International Buyers
For international B2B buyers, particularly in regions like Africa, South America, the Middle East, and Europe, understanding the manufacturing processes and quality assurance measures of oximeter manufacturers is vital. By focusing on key manufacturing stages, relevant standards, and rigorous quality control practices, buyers can make informed decisions and establish strong partnerships with reliable suppliers.
Practical Sourcing Guide: A Step-by-Step Checklist for ‘oximeter manufacturer’
When sourcing oximeters for your business, it’s essential to have a clear and structured approach. This guide provides a step-by-step checklist that will help international B2B buyers, particularly those from Africa, South America, the Middle East, and Europe, navigate the procurement process effectively.
Step 1: Define Your Technical Specifications
Before reaching out to manufacturers, it’s crucial to outline your specific requirements for the oximeters. Consider factors such as accuracy, size, battery life, and any special features (e.g., Bluetooth connectivity or data storage capabilities). This clarity will not only streamline communication with suppliers but also ensure that you receive products that meet your operational needs.
Step 2: Conduct Market Research for Suppliers
Explore various manufacturers and suppliers in the oximeter market. Utilize platforms like Alibaba, ThomasNet, or industry-specific trade fairs to identify potential partners. Pay attention to reviews, ratings, and any feedback from other buyers to gauge reliability and quality.
Step 3: Evaluate Potential Suppliers
Before committing, it’s crucial to vet suppliers thoroughly. Request company profiles, case studies, and references from buyers in a similar industry or region. Key aspects to investigate include:
– Certifications: Ensure they have relevant certifications (e.g., ISO, CE marking) that guarantee quality and safety.
– Experience: Look for suppliers with a proven track record in manufacturing medical devices.
Step 4: Request Samples for Testing
Once you have shortlisted potential suppliers, ask for samples of their oximeters. Testing these samples is vital to evaluate performance, user-friendliness, and durability. During this stage, consider:
– Functionality: Does the device meet your technical specifications?
– User Feedback: Gather input from your team on ease of use and reliability.
Step 5: Negotiate Pricing and Terms
After testing and evaluating samples, initiate negotiations with your preferred suppliers. Discuss pricing, payment terms, and bulk order discounts. It’s also crucial to clarify:
– Minimum Order Quantities (MOQ): Understand their MOQ to avoid excess inventory.
– Delivery Times: Confirm lead times for production and shipping, especially for international orders.
Step 6: Verify Compliance with Local Regulations
Before finalizing your purchase, ensure that the oximeters comply with the regulatory standards of your region. This may include certifications specific to medical devices in your country. Non-compliance can lead to legal issues and financial losses.
Step 7: Establish a Long-Term Relationship
After successfully sourcing oximeters, focus on building a long-term relationship with your supplier. Regular communication and feedback can lead to better service, improved product offerings, and potential cost savings in future orders. Consider setting up periodic reviews to assess performance and address any issues promptly.
By following this checklist, B2B buyers can streamline their sourcing process for oximeters, ensuring they find reliable manufacturers that meet their specific needs while maintaining quality and compliance.
Comprehensive Cost and Pricing Analysis for oximeter manufacturer Sourcing
What are the Key Cost Components in Oximeter Manufacturing?
When sourcing oximeters, understanding the cost structure is critical for international B2B buyers. The primary cost components include:
-
Materials: The choice of sensors, casings, and electronic components significantly impacts pricing. High-quality materials that comply with medical standards, such as biocompatible plastics and precise optical sensors, may increase initial costs but enhance product longevity and reliability.
-
Labor: Labor costs can vary based on the manufacturing location. Countries with lower labor costs, such as those in South America or Africa, might offer competitive pricing, but this must be balanced against the skill level required for high-quality assembly and testing.
-
Manufacturing Overhead: This includes utilities, rent, and other indirect costs associated with production. Efficient production processes can minimize overhead, making it essential to evaluate potential manufacturers on their operational efficiencies.
-
Tooling: Custom tooling for specific designs can be a significant upfront investment. Buyers should consider whether the manufacturer has the capability to produce custom designs without excessive tooling costs.
-
Quality Control (QC): Stringent quality control processes are necessary for medical devices. The cost associated with QC can vary, but it is crucial to ensure compliance with international standards, which can mitigate future liabilities.
-
Logistics: Shipping costs can vary widely depending on the Incoterms agreed upon. Understanding the implications of terms like FOB (Free on Board) or CIF (Cost, Insurance, and Freight) can help buyers manage overall costs effectively.
-
Margin: Manufacturers typically apply a markup to cover their costs and profit. This margin can fluctuate based on the volume of the order and market demand.
How Do Price Influencers Affect Oximeter Costs?
Several factors can influence the final price of oximeters:
-
Volume and Minimum Order Quantity (MOQ): Bulk orders often result in lower per-unit costs due to economies of scale. Buyers should negotiate favorable terms based on their purchasing capacity.
-
Specifications and Customization: Customized oximeters with specific features or branding will generally incur higher costs. It’s advisable to assess whether the additional features justify the price increase.
-
Materials and Quality Certifications: Oximeters that meet higher quality standards or possess necessary certifications (like CE or FDA) may command higher prices. Buyers should ensure that the certification aligns with their market requirements.
-
Supplier Factors: The reputation and reliability of the supplier can impact pricing. Established manufacturers with a proven track record may charge a premium, but they often provide better support and quality assurance.
-
Incoterms: The choice of shipping terms can significantly affect the total cost. Buyers should evaluate the risks and costs associated with various Incoterms to determine the most cost-effective option.
What are Effective Buyer Tips for Oximeter Sourcing?
For international B2B buyers, particularly from regions like Africa, South America, the Middle East, and Europe, consider the following tips:
-
Negotiate Effectively: Leverage your purchasing power to negotiate better pricing. Long-term contracts or larger orders can often yield discounts.
-
Focus on Cost-Efficiency: Evaluate the Total Cost of Ownership (TCO), which includes not just the purchase price but also operational costs, maintenance, and potential wastage due to quality issues.
-
Understand Pricing Nuances: Pricing can vary significantly based on regional market conditions. Buyers should conduct thorough market research to understand local pricing dynamics.
- Assess Supplier Relationships: Building strong relationships with suppliers can lead to better pricing and terms over time. Regular communication and feedback can enhance collaboration.
Disclaimer
The prices mentioned in this analysis are indicative and may vary based on market fluctuations, manufacturing conditions, and specific buyer agreements. Always conduct thorough due diligence when negotiating prices and terms with manufacturers.
Alternatives Analysis: Comparing oximeter manufacturer With Other Solutions
When considering the procurement of healthcare equipment, particularly for monitoring oxygen levels, international B2B buyers must evaluate various solutions against the traditional oximeter manufacturer. Exploring alternatives can provide insights into performance, cost-effectiveness, and suitability for specific healthcare settings. This analysis aims to compare the oximeter manufacturer with two viable alternatives: wearable pulse oximeters and blood gas analyzers.
Comparison Table of Oximeter Manufacturer and Alternatives
Comparison Aspect | Oximeter Manufacturer | Wearable Pulse Oximeter | Blood Gas Analyzer |
---|---|---|---|
Performance | High accuracy, reliable readings | Moderate accuracy, portability | High accuracy, detailed analysis |
Cost | Moderate to high | Low to moderate | High |
Ease of Implementation | Straightforward setup | Easy integration, user-friendly | Complex setup, requires training |
Maintenance | Low maintenance | Low maintenance | High maintenance, frequent calibration needed |
Best Use Case | Hospital settings, critical care | Home monitoring, outpatient care | Intensive care, emergency settings |
What Are the Pros and Cons of Wearable Pulse Oximeters?
Wearable pulse oximeters have gained popularity due to their convenience and portability. They can be easily worn on the wrist or finger, allowing continuous monitoring of oxygen saturation levels. This is particularly beneficial for patients requiring home care or those who are mobile. However, the accuracy of these devices can vary, especially in individuals with poor circulation or skin pigmentation issues. Additionally, while they are generally cost-effective, the lack of comprehensive data compared to traditional oximeters might be a drawback in critical situations.
How Do Blood Gas Analyzers Compare to Oximeter Manufacturers?
Blood gas analyzers provide a detailed assessment of a patient’s respiratory function, measuring not just oxygen saturation but also carbon dioxide levels and blood pH. This makes them invaluable in intensive care settings where comprehensive respiratory monitoring is crucial. However, the high cost and complex setup make them less accessible for smaller healthcare facilities. Furthermore, these devices require regular maintenance and calibration, which can increase operational costs. For facilities that prioritize detailed analysis and have the resources to support such equipment, blood gas analyzers may be the preferred choice.
How Can B2B Buyers Choose the Right Solution for Their Needs?
Selecting the appropriate monitoring solution depends on various factors, including the specific healthcare setting, patient needs, and budget constraints. For hospitals and critical care environments, the traditional oximeter may offer the reliability and accuracy required for patient monitoring. Conversely, for outpatient settings or home healthcare, wearable pulse oximeters may provide the necessary convenience and cost savings. Blood gas analyzers, while expensive, are ideal for facilities needing detailed respiratory analysis and can justify their costs through improved patient outcomes.
Ultimately, B2B buyers should carefully assess their operational requirements, financial considerations, and the level of patient care they aim to provide when choosing between these alternatives.
Essential Technical Properties and Trade Terminology for oximeter manufacturer
What Are the Essential Technical Properties of Oximeters?
When selecting an oximeter for B2B procurement, understanding its technical properties is crucial. Here are some key specifications to consider:
1. Accuracy and Precision
Accuracy refers to how closely the oximeter’s readings match the true oxygen saturation levels, while precision indicates the consistency of those readings across multiple tests. In a clinical setting, even slight inaccuracies can lead to misdiagnosis or improper treatment, making it vital for buyers to assess these metrics thoroughly.
2. Material Grade
The materials used in oximeter manufacturing—often medical-grade plastics and metals—affect durability and safety. High-quality materials reduce the risk of device failure and contamination, which is particularly important in healthcare environments. Buyers should inquire about the material standards to ensure compliance with local regulations.
3. Battery Life
Battery life is critical for portable oximeters, especially in emergency settings or remote areas where power supply may be unreliable. A longer battery life means less frequent replacements and increased usability. Prospective buyers should look for devices that offer extended battery performance, especially in regions with logistical challenges.
4. Display Quality
The clarity and size of the display are essential for ease of use, particularly in low-light conditions. A bright, high-contrast display can enhance readability and reduce the chances of misinterpretation. Buyers should evaluate whether the display includes features such as backlighting or adjustable brightness settings.
5. Data Connectivity
With the rise of telemedicine, oximeters with data connectivity (like Bluetooth or Wi-Fi) allow for remote monitoring and data sharing. This feature is especially beneficial for healthcare providers looking to integrate devices into electronic health records (EHR) systems. Buyers should assess the compatibility of data-sharing capabilities with their existing systems.
What Are Common Trade Terms Used in Oximeter Manufacturing?
Understanding industry jargon is equally important for effective communication and negotiation in the B2B space. Here are some commonly used terms:
1. OEM (Original Equipment Manufacturer)
An OEM refers to a company that produces parts or equipment that may be marketed by another manufacturer. In oximeter manufacturing, buyers may deal with OEMs to source components or entire devices. Understanding OEM relationships can help buyers negotiate better terms and ensure quality.
2. MOQ (Minimum Order Quantity)
MOQ is the smallest quantity of a product that a supplier is willing to sell. Knowing the MOQ is crucial for buyers to ensure that they can meet their inventory needs without overcommitting to excess stock. This is especially relevant for smaller healthcare facilities or startups.
3. RFQ (Request for Quotation)
An RFQ is a document sent to suppliers to request pricing and terms for specific products. It is an essential step in the procurement process, allowing buyers to compare costs and features across multiple suppliers. Crafting a detailed RFQ can lead to more accurate and competitive quotations.
4. Incoterms (International Commercial Terms)
Incoterms define the responsibilities of buyers and sellers in international trade, covering aspects such as shipping costs, insurance, and risk transfer. Familiarity with these terms helps buyers understand their liabilities and rights in cross-border transactions, which is particularly important for international buyers from Africa, South America, the Middle East, and Europe.
5. Lead Time
Lead time refers to the period between placing an order and receiving the goods. This is a crucial factor for B2B buyers, as longer lead times can affect inventory management and patient care. Buyers should clarify lead times during negotiations to ensure timely deliveries.
By familiarizing themselves with these technical properties and trade terms, B2B buyers can make informed decisions, ensuring that they procure high-quality oximeters that meet their specific needs and regulatory requirements.
Navigating Market Dynamics and Sourcing Trends in the oximeter manufacturer Sector
What Are the Current Market Dynamics and Key Trends in the Oximeter Manufacturing Sector?
The global oximeter manufacturing market is witnessing significant growth, driven by increasing health awareness and advancements in medical technology. The demand for non-invasive monitoring solutions has surged, particularly in response to the COVID-19 pandemic, which emphasized the importance of respiratory health. Emerging B2B technology trends include the integration of IoT and AI in oximeters, enabling real-time data analysis and remote patient monitoring. This shift towards smart healthcare solutions is particularly relevant for international buyers in regions like Africa and South America, where access to healthcare can be limited.
In addition, suppliers are adapting to the dynamic regulatory landscape by ensuring compliance with international standards, which is crucial for buyers looking to import oximeters. Increased collaboration between manufacturers and healthcare providers is also a trend, facilitating the development of tailored solutions that meet specific market needs. For instance, buyers from the Middle East and Europe can leverage these partnerships to access innovative products that cater to their local healthcare challenges.
How Is Sustainability Influencing Oximeter Manufacturing and Sourcing Practices?
As global awareness of environmental issues rises, sustainability has become a critical factor in the oximeter manufacturing sector. B2B buyers are increasingly prioritizing suppliers that demonstrate a commitment to ethical sourcing and sustainable practices. This includes using environmentally friendly materials, minimizing waste, and adopting energy-efficient manufacturing processes.
Certifications such as ISO 14001 for environmental management and the use of sustainable materials are becoming essential in the sourcing criteria for international buyers. In regions like Africa and South America, where environmental regulations may be less stringent, buyers should proactively seek manufacturers who prioritize sustainability. This not only enhances brand reputation but also meets the growing demand from end-users for eco-conscious products.
Furthermore, ethical supply chains contribute to social responsibility, ensuring fair labor practices and community engagement. By choosing manufacturers committed to sustainability, B2B buyers can support the global transition towards a more responsible healthcare ecosystem.
What Is the Brief Evolution of the Oximeter Manufacturing Sector?
The oximeter manufacturing sector has evolved significantly since its inception in the late 20th century. Initially, oximeters were bulky and primarily used in hospital settings. However, advancements in technology led to the development of portable, user-friendly devices that can be used in various settings, including home care.
The introduction of pulse oximetry in the 1980s revolutionized patient monitoring, allowing healthcare professionals to assess oxygen saturation levels non-invasively. Over the years, the integration of digital technology and connectivity features has transformed oximeters into sophisticated devices capable of providing real-time data, thus enhancing patient care. This evolution reflects the broader trend of digital transformation in healthcare, which is crucial for B2B buyers seeking innovative solutions in an increasingly competitive market.
In conclusion, understanding the market dynamics, sustainability imperatives, and historical context of the oximeter manufacturing sector equips international B2B buyers with the insights needed to make informed sourcing decisions. Prioritizing technological innovation and ethical practices will not only enhance the quality of healthcare delivery but also align with global sustainability goals.
Frequently Asked Questions (FAQs) for B2B Buyers of oximeter manufacturer
-
How can I ensure the quality of oximeters from a manufacturer?
To ensure the quality of oximeters from a manufacturer, request certifications such as ISO 13485 or CE marking, which indicate compliance with international quality management standards. Additionally, consider conducting audits or inspections at the manufacturer’s facility to verify their production processes. It’s also beneficial to obtain product samples for testing and evaluation before placing large orders, ensuring the devices meet your specifications and performance expectations. -
What are the key factors to consider when choosing an oximeter manufacturer?
When selecting an oximeter manufacturer, prioritize factors such as product quality, certifications, manufacturing capabilities, and industry experience. Assess their ability to provide customization options to meet specific market needs, and inquire about their after-sales support and warranty policies. Additionally, consider their delivery times and logistics capabilities, especially if you are sourcing from different regions such as Africa or South America. -
What is the typical minimum order quantity (MOQ) for oximeters?
The typical minimum order quantity (MOQ) for oximeters varies by manufacturer, but it generally ranges from 100 to 1,000 units. Some manufacturers may offer lower MOQs for initial orders or pilot projects, while others might require higher quantities for better pricing. It’s crucial to communicate your needs with potential suppliers to negotiate favorable terms that align with your business strategy and market demand.
-
How do I negotiate payment terms with an oximeter supplier?
When negotiating payment terms with an oximeter supplier, aim for flexibility that suits both parties. Common terms include a deposit upfront, with the balance due upon delivery or after inspection. Discuss options for letters of credit, bank transfers, or payment via escrow services to minimize risk. Ensure that all payment terms are documented in the contract to avoid misunderstandings and protect your investment. -
What customization options are available for oximeters?
Many oximeter manufacturers offer customization options, including branding with your logo, specific color schemes, and packaging designs tailored to your market. Additionally, you may request features such as data connectivity, extended battery life, or unique sensor types based on your target audience’s needs. Discuss your requirements in detail with potential suppliers to ensure they can meet your specifications. -
How can I vet an oximeter manufacturer for reliability?
To vet an oximeter manufacturer for reliability, research their reputation through online reviews, testimonials, and industry references. Request case studies or examples of previous projects to gauge their experience and expertise. Additionally, verify their production capacity and supply chain management practices to ensure they can consistently meet your demands. Engaging with other buyers in your network can provide valuable insights into their reliability. -
What are the logistics considerations when sourcing oximeters internationally?
When sourcing oximeters internationally, consider logistics factors such as shipping costs, lead times, and customs regulations in your country. Assess the manufacturer’s shipping capabilities and whether they can handle logistics or if you need to arrange for a freight forwarder. Understanding import duties and taxes will also help in calculating the total landed cost of the products, ensuring that your pricing strategy remains competitive. -
What quality assurance processes should I expect from oximeter manufacturers?
Expect oximeter manufacturers to implement rigorous quality assurance processes, including incoming material inspections, in-process testing, and final product evaluations. Look for manufacturers who conduct regular audits and maintain documentation of their quality control procedures. Request information on how they handle non-conformities and product recalls to ensure they prioritize quality and safety throughout their manufacturing process.
Important Disclaimer & Terms of Use
⚠️ Important Disclaimer
The information provided in this guide, including content regarding manufacturers, technical specifications, and market analysis, is for informational and educational purposes only. It does not constitute professional procurement advice, financial advice, or legal advice.
While we have made every effort to ensure the accuracy and timeliness of the information, we are not responsible for any errors, omissions, or outdated information. Market conditions, company details, and technical standards are subject to change.
B2B buyers must conduct their own independent and thorough due diligence before making any purchasing decisions. This includes contacting suppliers directly, verifying certifications, requesting samples, and seeking professional consultation. The risk of relying on any information in this guide is borne solely by the reader.
Strategic Sourcing Conclusion and Outlook for oximeter manufacturer
In the evolving landscape of healthcare, strategic sourcing remains pivotal for international B2B buyers looking to procure high-quality oximeters. By aligning with reliable manufacturers, businesses can ensure a consistent supply of advanced medical devices that meet regulatory standards and local market needs. As we have discussed, assessing suppliers based on their innovation capabilities, compliance with international certifications, and adaptability to market demands is essential for securing a competitive edge.
How Can International Buyers Benefit from Strategic Sourcing of Oximeters?
Investing in strategic sourcing not only streamlines procurement processes but also enhances product quality and reduces costs in the long run. Buyers in regions such as Africa, South America, the Middle East, and Europe can leverage this approach to build resilient supply chains that are responsive to local healthcare challenges.
What’s Next for B2B Buyers in the Oximeter Market?
As we look to the future, the importance of technology integration and sustainability in sourcing strategies cannot be overstated. Engage with manufacturers who prioritize eco-friendly practices and innovative technologies, ensuring that your sourcing decisions align with global health trends. Take action today by evaluating potential suppliers and forming partnerships that foster growth and innovation in your healthcare offerings.