Discover Top Packaging Material Suppliers: Save Costs Today (2025)
Introduction: Navigating the Global Market for packaging material supplier
Navigating the global market for packaging material suppliers presents a formidable challenge for international B2B buyers, particularly those operating in diverse regions such as Africa, South America, the Middle East, and Europe. The sheer variety of packaging materials available, combined with varying regional compliance standards and market dynamics, can make sourcing the right supplier a daunting task. This guide aims to simplify the complex landscape of packaging materials, covering essential types, applications, and critical factors to consider when vetting suppliers.
As businesses increasingly prioritize sustainability and efficiency, understanding the various types of packaging—ranging from biodegradable options to high-strength materials for heavy goods—is crucial. This guide provides actionable insights into selecting the right packaging solutions that not only meet operational needs but also align with corporate social responsibility goals. Furthermore, we delve into supplier vetting processes, offering strategies to assess reliability, quality, and compliance with international standards.
By equipping B2B buyers with the knowledge to make informed purchasing decisions, this comprehensive resource aims to empower organizations to navigate the complexities of the packaging market effectively. Whether you are sourcing for a startup in Nairobi, a manufacturing firm in São Paulo, or a logistics company in Warsaw, this guide serves as a vital tool in ensuring your packaging solutions are both cost-effective and aligned with your business objectives.
Understanding packaging material supplier Types and Variations
Type Name | Key Distinguishing Features | Primary B2B Applications | Brief Pros & Cons for Buyers |
---|---|---|---|
Flexible Packaging | Lightweight, versatile, and often resealable | Food, pharmaceuticals, consumer goods | Pros: Cost-effective, space-saving; Cons: May lack structural integrity. |
Rigid Packaging | Strong, durable containers (plastic, glass) | Electronics, cosmetics, industrial products | Pros: High protection, long shelf-life; Cons: Heavier, often more expensive. |
Sustainable Packaging | Eco-friendly materials (biodegradable, recyclable) | Food, cosmetics, retail | Pros: Positive brand image, compliance with regulations; Cons: Potentially higher costs. |
Bulk Packaging | Large quantities, often for industrial use | Manufacturing, wholesale distribution | Pros: Economies of scale, reduced shipping costs; Cons: Requires more storage space. |
Custom Packaging | Tailored designs to fit specific products | E-commerce, luxury goods, gifts | Pros: Enhanced branding, better product protection; Cons: Longer lead times, higher costs. |
What Are the Characteristics of Flexible Packaging?
Flexible packaging is characterized by its lightweight and adaptable nature, making it suitable for various products, especially in the food and pharmaceutical sectors. It often features resealable options, enhancing convenience for consumers. For B2B buyers, purchasing flexible packaging requires consideration of material types, such as films and laminates, as well as the intended shelf life and storage conditions of the product. The cost-effectiveness and reduced waste associated with flexible packaging make it an attractive choice for businesses aiming to optimize logistics and reduce expenses.
How Does Rigid Packaging Stand Out in B2B Applications?
Rigid packaging includes materials like glass, metal, and hard plastics, known for their durability and strength. This type of packaging is commonly used for electronics, cosmetics, and industrial products, where protection and shelf-life are critical. B2B buyers should evaluate factors such as weight, material quality, and design when selecting rigid packaging. While it offers excellent protection, the higher costs and increased weight compared to flexible alternatives may impact shipping and overall budget.
Why Should Buyers Consider Sustainable Packaging?
Sustainable packaging is made from eco-friendly materials, such as biodegradable or recyclable options, appealing to businesses focused on environmental responsibility. Its applications span food, cosmetics, and retail sectors. Buyers should assess the sustainability credentials of suppliers, including certifications and compliance with local regulations. Although sustainable packaging can enhance brand image and customer loyalty, it may come with a higher price point, which requires careful budgeting and justification.
What Are the Benefits of Bulk Packaging for B2B Transactions?
Bulk packaging is designed for large quantities, catering to industrial and wholesale distribution needs. This type of packaging is ideal for manufacturers looking to streamline their supply chain and reduce costs. Buyers should consider storage requirements and handling logistics when purchasing bulk packaging. While it offers economies of scale and lower shipping costs, the need for more storage space can be a drawback for smaller operations.
How Does Custom Packaging Enhance Branding?
Custom packaging allows businesses to create unique designs tailored to specific products, enhancing brand visibility and consumer appeal. Commonly used in e-commerce, luxury goods, and gift items, this type of packaging can significantly impact customer perception. B2B buyers need to balance the advantages of enhanced branding and product protection with potential drawbacks, such as longer lead times and increased costs. Understanding the target audience and product requirements is essential when opting for custom packaging solutions.
Related Video: Glenroy’s Flexible Packaging Manufacturing Process
Key Industrial Applications of packaging material supplier
Industry/Sector | Specific Application of Packaging Material Supplier | Value/Benefit for the Business | Key Sourcing Considerations for this Application |
---|---|---|---|
Food & Beverage | Flexible packaging for perishable goods | Extends shelf life and maintains freshness | Compliance with food safety regulations, material durability, and sustainability options |
Pharmaceuticals | Child-resistant and tamper-evident packaging | Ensures product safety and compliance | Regulatory compliance, material integrity, and customization capabilities |
Electronics | Anti-static packaging for sensitive components | Protects products from electrostatic discharge | Material specifications, anti-static properties, and cost-effectiveness |
Cosmetics & Personal Care | Eco-friendly packaging solutions | Enhances brand image and meets consumer demand | Sustainability certifications, design flexibility, and material sourcing |
Industrial Products | Bulk packaging for heavy machinery parts | Reduces shipping costs and enhances logistics | Load capacity, material strength, and compatibility with shipping methods |
How is Packaging Material Supplier Used in the Food & Beverage Industry?
In the food and beverage sector, packaging material suppliers provide flexible packaging solutions that are essential for preserving the quality of perishable goods. These materials help extend shelf life, ensuring that products remain fresh and safe for consumption. International buyers must consider compliance with food safety regulations and the durability of materials to withstand transportation and storage conditions. Additionally, sustainable options are increasingly important to meet consumer preferences, particularly in markets across Africa and Europe.
What Role Does Packaging Play in the Pharmaceutical Sector?
Packaging in the pharmaceutical industry is critical for ensuring product safety and compliance with strict regulatory standards. Suppliers offer child-resistant and tamper-evident packaging that protects medications from unauthorized access and contamination. International B2B buyers need to prioritize suppliers who can guarantee regulatory compliance and material integrity. Customization options are also vital to accommodate various product sizes and types, enhancing branding while maintaining safety.
Why is Anti-Static Packaging Important for Electronics?
Electronics manufacturers rely on anti-static packaging to safeguard sensitive components from electrostatic discharge (ESD) during shipping and handling. Packaging material suppliers provide specialized materials that prevent damage and ensure product functionality. Buyers from South America and the Middle East should focus on suppliers that can meet specific material specifications and provide cost-effective solutions without compromising on quality. This is particularly crucial for maintaining competitive advantage in the rapidly evolving electronics market.
How Can Eco-Friendly Packaging Solutions Benefit Cosmetics Brands?
In the cosmetics and personal care industry, eco-friendly packaging solutions are increasingly sought after to align with consumer demand for sustainability. Packaging material suppliers offer biodegradable and recyclable options that enhance brand image and appeal to environmentally conscious consumers. B2B buyers from Europe, including Italy and Poland, should seek suppliers with sustainability certifications and design flexibility to create attractive, responsible packaging that resonates with their target market.
What are the Key Considerations for Bulk Packaging in Industrial Products?
For industrial products, bulk packaging is essential for transporting heavy machinery parts efficiently. Packaging material suppliers provide robust solutions that reduce shipping costs and streamline logistics. Buyers must assess load capacity, material strength, and compatibility with various shipping methods to ensure safe delivery. This is particularly relevant for international transactions, where understanding local regulations and logistics is crucial for success in diverse markets across Africa and South America.
3 Common User Pain Points for ‘packaging material supplier’ & Their Solutions
Scenario 1: Difficulty in Finding Sustainable Packaging Solutions
The Problem: As global awareness of environmental issues increases, many B2B buyers, particularly in Europe and South America, are under pressure to find sustainable packaging materials. The challenge lies not just in sourcing these materials, but in ensuring that they meet regulatory standards and customer expectations for sustainability. Buyers often encounter confusion about which suppliers can provide genuinely eco-friendly options versus those that merely market themselves as “green.”
The Solution: To navigate this complex landscape, international B2B buyers should prioritize suppliers who can provide certifications and transparent sourcing information. Start by asking potential suppliers for third-party certifications such as FSC (Forest Stewardship Council) or ISO 14001 (Environmental Management). This approach ensures that the materials are sourced responsibly. Additionally, consider engaging with suppliers who offer biodegradable or compostable options and can provide samples for testing. Establishing a long-term relationship with a supplier that understands your sustainability goals can also facilitate better sourcing of materials that align with evolving regulations and consumer preferences.
Scenario 2: Inconsistent Quality of Packaging Materials
The Problem: Buyers often face the frustration of receiving packaging materials that do not meet their quality expectations or specifications. This inconsistency can lead to product damage during shipping, increased costs due to returns, and ultimately dissatisfied customers. For international buyers, especially those in Africa and the Middle East, varying quality standards across different suppliers can complicate procurement.
The Solution: To mitigate this issue, B2B buyers should implement a rigorous supplier evaluation process that includes quality audits and performance metrics. Request samples of packaging materials before placing bulk orders and establish clear quality benchmarks that suppliers must meet. It’s also advisable to maintain open communication with suppliers about quality expectations and to develop a system for regular feedback. Additionally, consider building a multi-supplier strategy to avoid dependency on a single source, which can enhance quality assurance and provide alternatives in case of supply chain disruptions.
Scenario 3: Complexity in Customization and Design
The Problem: Many B2B buyers require customized packaging solutions to enhance brand identity and product protection. However, navigating the design process can be daunting. Buyers often struggle with communicating their needs effectively, leading to misaligned expectations and increased turnaround times. This challenge is particularly pronounced for buyers in diverse markets like Europe and Africa, where design standards and consumer preferences can vary widely.
The Solution: To streamline the customization process, buyers should engage with packaging suppliers who offer design consultation services. Start by providing a detailed brief that includes your brand guidelines, target market, and specific functionality requirements. Utilize digital tools like 3D modeling or virtual prototypes to visualize the final product before production. Additionally, maintain an iterative feedback loop during the design phase to ensure that the final product aligns with your vision. Working closely with a supplier that has experience in your target market can provide valuable insights into local preferences and trends, ensuring that the final design resonates with your audience.
Strategic Material Selection Guide for packaging material supplier
When selecting packaging materials, international B2B buyers must consider various factors that affect product performance, compliance, and market suitability. Below is an analysis of four common packaging materials, highlighting their key properties, advantages, disadvantages, and specific considerations for buyers from Africa, South America, the Middle East, and Europe.
What Are the Key Properties of Polyethylene (PE) in Packaging?
Polyethylene (PE) is one of the most widely used plastics in packaging due to its versatility. It offers excellent chemical resistance, making it suitable for packaging various products, including food and chemicals. PE can withstand temperatures ranging from -60°C to 80°C, providing a good thermal range for many applications. Its moisture barrier properties also help in preserving the integrity of the packaged goods.
Pros & Cons of Polyethylene:
– Pros: Lightweight, cost-effective, and recyclable. PE is also resistant to impact and moisture, which enhances its durability.
– Cons: Limited temperature resistance and can become brittle at low temperatures. It also has a lower barrier against gases compared to other materials.
Impact on Application:
PE is particularly effective for packaging food products and consumer goods due to its moisture barrier. However, it may not be suitable for products requiring high gas barrier properties.
Considerations for International Buyers:
Buyers should ensure compliance with food safety standards, such as FDA regulations in the U.S. or EFSA standards in Europe. Understanding local recycling capabilities and regulations is also crucial for sustainable practices.
How Does Polypropylene (PP) Compare in Terms of Durability?
Polypropylene (PP) is known for its high melting point (up to 160°C) and excellent chemical resistance. It is often used in applications requiring higher durability and rigidity. PP is also lightweight and can be produced in various forms, such as films, containers, and bottles.
Pros & Cons of Polypropylene:
– Pros: Strong, resistant to fatigue, and has a higher clarity than PE, making it suitable for transparent packaging.
– Cons: More expensive than PE and can be less flexible, which may limit its use in certain applications.
Impact on Application:
PP is ideal for packaging applications that require durability, such as automotive parts and industrial components. Its resistance to chemicals makes it suitable for packaging hazardous materials.
Considerations for International Buyers:
Buyers should be aware of compliance with international standards such as ASTM and ISO. In regions like Europe, adherence to REACH regulations is essential for chemical safety.
What Are the Advantages of Using Paperboard in Packaging?
Paperboard is a sustainable option that is increasingly popular among environmentally conscious consumers and businesses. It is lightweight, recyclable, and biodegradable, making it an excellent choice for eco-friendly packaging solutions. Paperboard can be treated for moisture resistance, enhancing its usability.
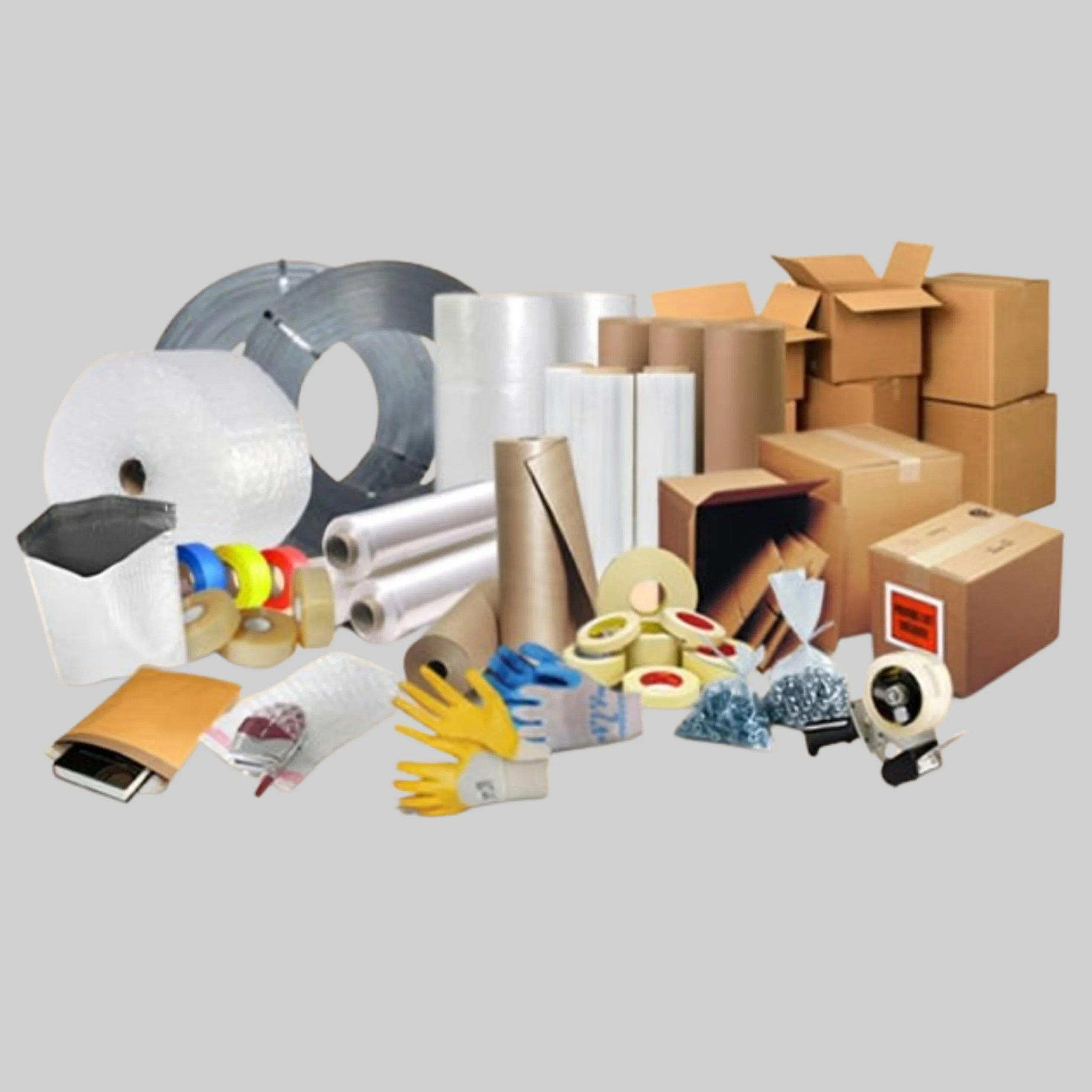
A stock image related to packaging material supplier.
Pros & Cons of Paperboard:
– Pros: Highly customizable, cost-effective, and offers good printability for branding.
– Cons: Less durable than plastics and may not be suitable for moisture-sensitive products without additional treatment.
Impact on Application:
Paperboard is commonly used for packaging consumer goods, food, and cosmetics. Its recyclability appeals to buyers looking to enhance their sustainability profile.
Considerations for International Buyers:
Buyers should consider the sourcing of paperboard, ensuring it meets sustainability certifications such as FSC or PEFC. Understanding local recycling capabilities is also vital for compliance with environmental regulations.
How Does Glass Packaging Stand Out in Terms of Quality?
Glass is a premium packaging material known for its excellent barrier properties, preserving the quality and flavor of products. It is non-reactive and can withstand high temperatures, making it suitable for a variety of applications, including food and beverages.
Pros & Cons of Glass:
– Pros: Recyclable, provides an excellent barrier to gases and moisture, and is perceived as a high-quality packaging option.
– Cons: Heavier and more fragile than other materials, which can increase shipping costs and risk of breakage.
Impact on Application:
Glass is ideal for packaging high-end products, such as spirits, perfumes, and gourmet foods. Its inert nature ensures that it does not alter the product’s flavor or quality.
Considerations for International Buyers:
Buyers must ensure compliance with international packaging regulations, particularly concerning food safety. Understanding the logistics of handling and shipping glass is also crucial to minimize damage.
Summary Table of Packaging Materials
Material | Typical Use Case for packaging material supplier | Key Advantage | Key Disadvantage/Limitation | Relative Cost (Low/Med/High) |
---|---|---|---|---|
Polyethylene | Food packaging, consumer goods | Lightweight and cost-effective | Limited temperature resistance | Low |
Polypropylene | Industrial packaging, automotive parts | High durability and chemical resistance | More expensive than PE | Medium |
Paperboard | Consumer goods, cosmetics, food | Sustainable and customizable | Less durable without treatment | Low |
Glass | High-end beverages, gourmet foods | Excellent barrier and high quality | Heavy and fragile | High |
This guide provides a comprehensive overview of strategic material selection for packaging materials, enabling international B2B buyers to make informed decisions that align with their operational needs and market demands.
In-depth Look: Manufacturing Processes and Quality Assurance for packaging material supplier
What Are the Main Stages of the Manufacturing Process for Packaging Materials?
The manufacturing process for packaging materials involves several critical stages that ensure the final product meets quality and functional standards. Understanding these stages can empower B2B buyers, especially from regions like Africa, South America, the Middle East, and Europe, to make informed decisions.
1. Material Preparation
The first step in the manufacturing process is material preparation. This involves sourcing raw materials, which may include plastics, paper, or metals, depending on the type of packaging required. Buyers should inquire about the origin of these materials, as sustainable sourcing is becoming increasingly important. Effective suppliers often use recycled materials to minimize environmental impact, which can also be a selling point for products in eco-conscious markets.
2. Forming
Once the materials are prepared, they undergo forming processes. Techniques like extrusion, injection molding, and blow molding are commonly used to shape the packaging. For instance, extrusion is often employed for creating plastic films, while injection molding is suitable for producing rigid containers. B2B buyers should be aware of the forming methods employed by their suppliers, as these methods can affect both cost and the quality of the final product.
3. Assembly
After forming, the packaging components often require assembly. This may involve processes like sealing, labeling, or combining different packaging elements into a single unit. The assembly stage is crucial for ensuring that the packaging meets specific regulatory requirements, especially in industries like food and pharmaceuticals. Buyers should confirm that their suppliers adhere to best practices during this phase to ensure product safety and compliance.
4. Finishing
Finishing touches include processes such as printing, coating, and surface treatment. These steps enhance the visual appeal of the packaging and can also provide protective features. For example, UV coatings can protect printed materials from fading. B2B buyers should assess the finishing options available to ensure that their branding needs are met while considering the durability of the packaging.
How Is Quality Assurance Managed in the Packaging Industry?
Quality assurance (QA) is a vital aspect of the manufacturing process for packaging materials. It ensures that products meet both international and industry-specific standards. For B2B buyers, understanding the QA mechanisms in place can significantly influence supplier selection.
Relevant International Standards for Packaging Quality
International standards such as ISO 9001 provide a framework for quality management systems (QMS) in manufacturing. Compliance with ISO 9001 indicates that a supplier has established processes for continuous improvement and customer satisfaction. Additionally, other certifications like CE marking for products sold in Europe or API standards for pharmaceutical packaging can offer further assurance of quality.
What Are the Key Quality Control Checkpoints?
Quality control (QC) checkpoints are integral to maintaining product integrity throughout the manufacturing process. Key checkpoints include:
- Incoming Quality Control (IQC): This involves inspecting raw materials upon arrival to ensure they meet specified requirements.
- In-Process Quality Control (IPQC): During manufacturing, continuous monitoring is conducted to detect any deviations from quality standards.
- Final Quality Control (FQC): This final inspection occurs before products are shipped, ensuring they are free from defects and meet customer specifications.
B2B buyers should inquire about the specific QC measures their suppliers implement at each checkpoint.
What Testing Methods Are Commonly Used for Packaging Quality Assurance?
Several testing methods are employed to verify the quality of packaging materials. These methods may vary based on the type of packaging and its intended use. Common testing techniques include:
- Physical Testing: Evaluating the strength, flexibility, and durability of materials through tensile tests, puncture resistance tests, and drop tests.
- Chemical Testing: Assessing the chemical composition to ensure materials are safe for their intended use, especially in food and pharmaceutical applications.
- Environmental Testing: Conducting tests to determine how packaging performs under varying environmental conditions, such as temperature and humidity.
B2B buyers should ask suppliers for detailed reports on these testing methods and results to verify compliance with applicable standards.
How Can B2B Buyers Verify Supplier Quality Control?
Verifying a supplier’s quality control processes is crucial for B2B buyers looking to mitigate risks associated with packaging materials. Here are several strategies to consider:
Conducting Audits
Regular audits of the supplier’s manufacturing facilities can provide insights into their quality management practices. Buyers should consider both announced and unannounced audits to gauge the supplier’s adherence to quality standards consistently.
Requesting Quality Reports
Suppliers should be able to provide comprehensive quality reports detailing their QC processes, testing results, and compliance with relevant standards. Buyers should request these documents before finalizing contracts to ensure transparency.
Utilizing Third-Party Inspections
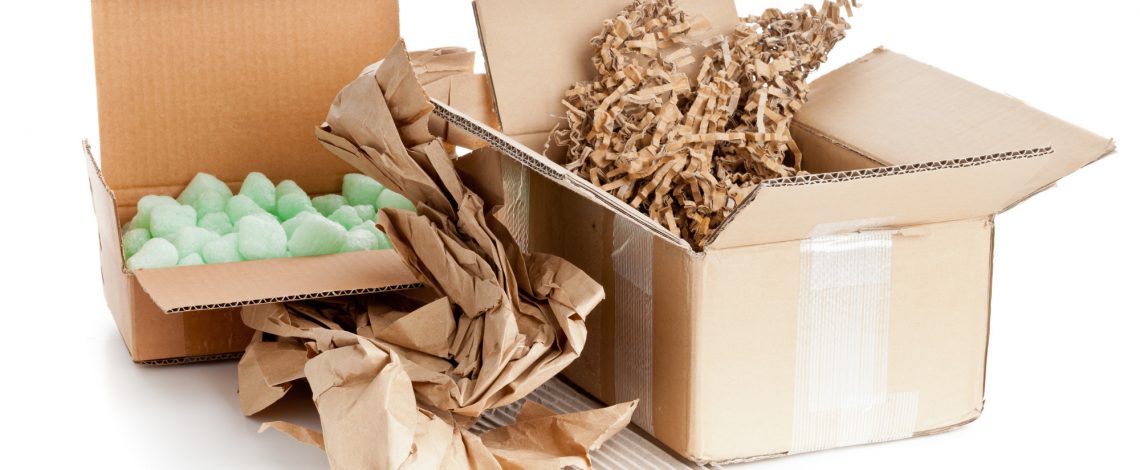
A stock image related to packaging material supplier.
Engaging third-party inspection agencies can provide an unbiased assessment of a supplier’s quality control processes. This can be particularly useful for international buyers who may not have the capacity to conduct audits themselves.
What Are the Quality Control Nuances for International B2B Buyers?
International B2B buyers, particularly from diverse markets like Africa, South America, the Middle East, and Europe, face unique challenges regarding quality control. Here are some nuances to consider:
-
Regulatory Compliance: Different regions may have varying regulatory requirements for packaging materials. Buyers should ensure that their suppliers comply with local regulations, especially when importing goods.
-
Cultural Expectations: Understanding cultural perceptions of quality can influence buyer-supplier relationships. For instance, European buyers may prioritize eco-friendly packaging, while buyers in other regions may focus on cost-effectiveness.
-
Communication Barriers: Language and cultural differences can complicate quality assurance discussions. Establishing clear communication channels and expectations is essential for successful collaboration.
By understanding these factors and implementing robust quality assurance practices, B2B buyers can significantly reduce risks and enhance the reliability of their packaging materials.
Practical Sourcing Guide: A Step-by-Step Checklist for ‘packaging material supplier’
In the global marketplace, sourcing packaging materials requires a strategic approach, particularly for B2B buyers from diverse regions such as Africa, South America, the Middle East, and Europe. This practical checklist is designed to guide you through the essential steps to identify and secure a reliable packaging material supplier.
Step 1: Define Your Packaging Needs
Begin by clearly outlining your specific packaging requirements. Consider factors such as the type of products you are packaging, the target market, and any regulatory compliance that may apply in your region. This foundational step will help you communicate effectively with potential suppliers and ensure that they can meet your specifications.
- Product Type: Identify whether you need flexible packaging, rigid containers, or custom solutions.
- Market Regulations: Research any regional packaging regulations that may impact your materials.
Step 2: Research Potential Suppliers
Conduct thorough research to identify potential suppliers who specialize in the types of packaging materials you need. Utilize online directories, trade shows, and industry-specific forums to compile a list of candidates.
- Online Resources: Leverage platforms like Alibaba or ThomasNet to find suppliers.
- Local Trade Shows: Attend relevant exhibitions to meet suppliers face-to-face and evaluate their offerings.
Step 3: Evaluate Supplier Certifications
Before proceeding, verify that your shortlisted suppliers hold the necessary certifications relevant to your industry. Certifications such as ISO 9001 for quality management systems or FSC certification for sustainable sourcing can provide assurance of their commitment to quality and sustainability.
- Quality Assurance: Ensure that the supplier has a robust quality control process.
- Sustainability Practices: Consider certifications that reflect environmentally friendly practices.
Step 4: Request Samples
Once you have narrowed down your options, request samples of the packaging materials. This step allows you to assess the quality, durability, and suitability of the materials for your products.
- Testing Samples: Evaluate samples under conditions that mimic your packaging and shipping processes.
- Quality Feedback: Collect feedback from your team or stakeholders on the samples provided.
Step 5: Assess Supplier Communication and Support
Effective communication is critical in any supplier relationship. Assess how responsive and supportive potential suppliers are during the inquiry process. Their ability to address your questions and provide information promptly can be indicative of their overall service level.
- Response Time: Track how quickly they respond to inquiries.
- Support Availability: Ensure they provide ongoing support for any issues that may arise during the partnership.
Step 6: Negotiate Terms and Pricing
Once you have selected a preferred supplier, initiate discussions around pricing, delivery terms, and payment conditions. Understanding the full scope of costs, including shipping and handling, is essential to avoid surprises later on.
- Transparent Pricing: Ensure all costs are outlined clearly in the agreement.
- Payment Flexibility: Negotiate payment terms that align with your cash flow needs.
Step 7: Establish a Trial Order
Before committing to a long-term partnership, consider placing a trial order to evaluate the supplier’s performance in real-world conditions. This trial can provide insights into their reliability, delivery times, and product quality.
- Monitoring Performance: Assess the supplier’s adherence to delivery schedules and product specifications.
- Feedback Loop: Create a feedback mechanism to address any issues that may arise during this initial phase.
By following this checklist, B2B buyers can enhance their sourcing process for packaging materials, ensuring they partner with reliable suppliers who meet their specific needs and expectations.
Comprehensive Cost and Pricing Analysis for packaging material supplier Sourcing
What Are the Key Cost Components in Packaging Material Supplier Sourcing?
Understanding the cost structure of packaging materials is vital for international B2B buyers. The primary components that contribute to the overall cost include:
-
Materials: The type of material used significantly affects pricing. For instance, biodegradable materials may cost more than traditional plastics but can offer long-term savings through eco-friendly branding.
-
Labor: Labor costs can vary greatly depending on the country of manufacture. Regions with lower labor costs may present attractive pricing, but it’s essential to consider the potential trade-offs in quality.
-
Manufacturing Overhead: This includes indirect costs associated with production, such as utilities and equipment depreciation. Efficient manufacturing processes can minimize these costs.
-
Tooling: Custom tooling for unique packaging designs can lead to higher upfront costs. However, this can also result in better product differentiation and reduced per-unit costs in larger production runs.
-
Quality Control (QC): Implementing robust QC measures ensures that products meet required standards, which can incur additional costs but ultimately protects brand integrity.
-
Logistics: Transportation costs, influenced by distance and mode of transport, should not be overlooked. International buyers must account for shipping fees, customs duties, and potential delays.
-
Margin: Suppliers will add a profit margin to cover their costs and ensure sustainability. Understanding the typical margin for your region can help in price negotiations.
How Do Price Influencers Affect Packaging Material Costs?
Several factors can influence the final pricing of packaging materials:
-
Volume and Minimum Order Quantity (MOQ): Larger orders typically result in lower per-unit costs. Buyers should evaluate their needs against supplier MOQs to negotiate better pricing.
-
Specifications and Customization: Custom designs or specific material requirements can significantly impact costs. Buyers should clarify their needs upfront to avoid unexpected charges.
-
Material Quality and Certifications: Premium materials and certifications (like ISO or organic certifications) can increase costs but may be necessary for compliance or market positioning.
-
Supplier Factors: Supplier reliability and reputation can affect pricing. Established suppliers may charge more due to their proven track record, while newer suppliers might offer competitive rates to gain market share.
-
Incoterms: Understanding the terms of trade can help buyers determine responsibility for costs and risks associated with shipping. Choosing the right Incoterms can lead to cost savings and better risk management.
What Tips Can B2B Buyers Use for Effective Negotiation and Cost-Efficiency?
International B2B buyers can adopt several strategies to enhance their sourcing experience:
-
Negotiate Terms: Don’t hesitate to negotiate pricing and payment terms. Building a long-term relationship with suppliers can lead to better deals and more favorable terms.
-
Consider Total Cost of Ownership (TCO): Evaluate not just the purchase price but also the long-term costs associated with logistics, storage, and disposal. A lower upfront cost may lead to higher long-term expenses.
-
Research Pricing Nuances: Pricing structures can differ widely between regions. Buyers from Africa, South America, the Middle East, and Europe should familiarize themselves with local market conditions to make informed decisions.
-
Leverage Technology: Utilize digital platforms and marketplaces to compare prices, read reviews, and check supplier credentials. This can provide insights into competitive pricing and supplier reliability.
-
Request Samples: Before committing to large orders, request samples to assess quality and ensure that the product meets your specifications.
Disclaimer About Indicative Prices
It’s crucial to note that the prices for packaging materials can vary significantly based on regional market conditions, supplier relationships, and economic factors. The insights provided are indicative and should be validated through direct engagement with suppliers to obtain the most accurate and relevant pricing information.
Alternatives Analysis: Comparing packaging material supplier With Other Solutions
When considering packaging solutions, it is essential for B2B buyers to explore various alternatives that can meet their specific operational needs and sustainability goals. This section analyzes the traditional packaging material supplier against two viable alternatives: biodegradable packaging solutions and reusable packaging systems. Each option has unique benefits and drawbacks that can significantly impact your supply chain efficiency, cost-effectiveness, and environmental footprint.
Comparison Table of Packaging Solutions
Comparison Aspect | Packaging Material Supplier | Biodegradable Packaging Solutions | Reusable Packaging Systems |
---|---|---|---|
Performance | High durability; varied options | Moderate durability; suitable for single-use | High durability; reusable for multiple cycles |
Cost | Moderate to high depending on materials | Generally higher initial costs; potential long-term savings | Higher upfront investment; savings on repeated use |
Ease of Implementation | Straightforward; established suppliers | May require adjustment in supply chain | Requires system changes; training needed |
Maintenance | Low; minimal upkeep required | Low; disposal methods may vary | Moderate; requires cleaning and inspection |
Best Use Case | General packaging needs across industries | Food packaging, single-use items | E-commerce, bulk shipping, and returns |
What Are the Benefits of Biodegradable Packaging Solutions?
Biodegradable packaging solutions are gaining traction as a sustainable alternative. They decompose naturally, reducing landfill waste and environmental impact. However, they typically possess moderate durability, making them more suitable for single-use applications such as food packaging. Although the initial costs can be higher compared to traditional materials, businesses may benefit from improved brand image and customer loyalty by aligning with eco-friendly practices. The main challenge lies in the varying disposal methods and the need to educate consumers on proper disposal.
How Do Reusable Packaging Systems Work?
Reusable packaging systems involve containers that can be cleaned and used multiple times, making them an excellent choice for businesses focused on sustainability and cost efficiency over time. They provide high durability and are particularly advantageous in sectors like e-commerce and bulk shipping. The initial setup costs can be significant due to the need for durable materials and the establishment of a return system. Additionally, companies must invest in training employees on proper maintenance and cleaning protocols to ensure the longevity of the packaging. Despite these challenges, the long-term savings and reduced environmental impact make them an attractive option for many businesses.
Conclusion: How Can B2B Buyers Choose the Right Packaging Solution?
When selecting a packaging solution, international B2B buyers should assess their specific operational requirements, budget constraints, and sustainability goals. The choice between a traditional packaging material supplier, biodegradable options, or reusable systems should be guided by factors such as product type, target market, and long-term cost implications. By carefully evaluating the performance, cost, and maintenance of each alternative, businesses can make informed decisions that enhance their supply chain efficiency while also meeting consumer demand for environmentally responsible practices.
Essential Technical Properties and Trade Terminology for packaging material supplier
What Are the Key Technical Properties for Packaging Materials?
Understanding the essential technical properties of packaging materials is crucial for international B2B buyers. Here are some critical specifications to consider:
-
Material Grade
Material grade refers to the specific type of material used in packaging, such as polyethylene, polypropylene, or biodegradable options. Each grade has unique characteristics that affect durability, flexibility, and resistance to environmental factors. Selecting the appropriate material grade ensures that the packaging meets product safety standards and enhances shelf life. -
Tolerance
Tolerance is the allowable variation in the dimensions of packaging components. It is vital for ensuring that products fit correctly within their packaging and that the packaging machinery operates efficiently. A tight tolerance can minimize waste and improve production efficiency, which is especially important for buyers looking to streamline operations. -
Barrier Properties
Barrier properties indicate the material’s ability to resist the permeation of gases, moisture, and light. This is particularly important for food and pharmaceutical products, where product integrity is paramount. Understanding barrier properties helps buyers select packaging that preserves product quality and extends shelf life. -
Weight and Thickness
The weight and thickness of packaging materials influence shipping costs and sustainability efforts. Thicker materials may offer more durability but can increase transportation expenses. Buyers should assess their needs to find a balance between protection and cost-effectiveness. -
Recyclability
As sustainability becomes a focal point in global markets, recyclability is an essential property. Buyers need to consider how easily materials can be recycled or disposed of responsibly. Opting for recyclable materials not only meets regulatory requirements but also enhances brand reputation among environmentally conscious consumers.
Which Trade Terms Should B2B Buyers Understand in the Packaging Industry?
Navigating the packaging industry also requires familiarity with common trade terminology. Here are some essential terms every B2B buyer should know:
-
OEM (Original Equipment Manufacturer)
An OEM refers to a company that produces parts and equipment that may be marketed by another manufacturer. In the context of packaging, working with an OEM can provide buyers with customized solutions tailored to their specific needs. -
MOQ (Minimum Order Quantity)
MOQ is the smallest quantity of a product that a supplier is willing to sell. Understanding MOQ is crucial for buyers to ensure they can meet their inventory needs without overcommitting financially. It can also influence decisions on supplier selection based on production volume requirements. -
RFQ (Request for Quotation)
An RFQ is a document that buyers send to suppliers to solicit price quotes for specific products or services. This formal request allows buyers to compare prices and terms from different suppliers, facilitating informed purchasing decisions. -
Incoterms (International Commercial Terms)
Incoterms are a set of predefined international trade terms that clarify the responsibilities of buyers and sellers regarding the delivery of goods. Familiarity with these terms helps buyers understand shipping costs, risk management, and responsibilities, ensuring smoother international transactions. -
Lead Time
Lead time refers to the amount of time it takes from placing an order to receiving the goods. Understanding lead times is essential for buyers to manage inventory levels effectively and to plan for production schedules, especially in fast-paced industries.
By being well-versed in these technical properties and trade terminologies, international B2B buyers can make informed decisions that enhance their operations and ensure product quality in the competitive packaging market.
Navigating Market Dynamics and Sourcing Trends in the packaging material supplier Sector
What Are the Current Market Dynamics and Key Trends in the Packaging Material Supplier Sector?
The packaging material supplier sector is experiencing rapid transformation, driven by globalization, technological advancements, and evolving consumer preferences. International B2B buyers, particularly from Africa, South America, the Middle East, and Europe, must navigate these dynamics to make informed sourcing decisions. A significant trend is the rise of e-commerce, which has increased the demand for diverse and customizable packaging solutions. This shift compels suppliers to adapt their offerings to meet the unique needs of various industries, from food and beverage to pharmaceuticals.
Emerging technologies, such as automation and digitalization, are also shaping the landscape. For example, the integration of artificial intelligence in supply chain management enhances inventory management, streamlining operations and reducing costs. Buyers should seek suppliers who leverage these technologies to improve efficiency and reliability. Furthermore, the COVID-19 pandemic has accelerated the trend toward contactless and sustainable packaging solutions, making it imperative for suppliers to innovate continuously.
Additionally, the geopolitical landscape influences sourcing strategies, especially for buyers in regions like Europe and the Middle East. Tariffs and trade regulations can impact pricing and availability, prompting buyers to diversify their supplier bases. Understanding these market dynamics enables buyers to identify strategic partners who can provide competitive advantages in this evolving landscape.
How Can Sustainability and Ethical Sourcing Impact Your Sourcing Decisions?
Sustainability is no longer a niche concern; it has become a fundamental aspect of the packaging material supplier sector. As environmental regulations tighten globally, B2B buyers must consider the environmental impact of their sourcing choices. Ethical sourcing practices not only enhance brand reputation but also mitigate risks associated with supply chain disruptions.
Buyers should prioritize suppliers who utilize sustainable materials and implement eco-friendly manufacturing processes. Certifications such as FSC (Forest Stewardship Council) and ISO 14001 signal a commitment to sustainable practices, providing buyers with assurance regarding the ethical sourcing of materials. Moreover, the demand for biodegradable and recyclable packaging options is increasing, reflecting a shift in consumer preferences toward greener alternatives.
Incorporating sustainability into sourcing strategies can lead to long-term cost savings and improved market positioning. By aligning with suppliers who share these values, businesses can enhance their competitive edge while contributing to global sustainability efforts. Buyers from Africa, South America, the Middle East, and Europe should actively seek partnerships with suppliers committed to ethical sourcing practices to create a positive impact on the environment and society.
What Is the Historical Context of the Packaging Material Supplier Sector?
The packaging material supplier sector has evolved significantly over the decades, influenced by technological advancements and changing consumer behaviors. Initially focused on functionality, the industry has transitioned towards sustainability and innovation in response to market demands. The introduction of synthetic materials in the mid-20th century revolutionized packaging, allowing for lighter, more durable options.
By the 1990s, the rise of environmental awareness began to reshape the industry, leading to the development of recyclable and biodegradable materials. Today, the sector continues to innovate, driven by the need for sustainable solutions and the integration of digital technologies. This evolution highlights the importance of adaptability for suppliers, as they must continuously respond to the dynamic needs of international B2B buyers. Understanding this historical context can provide valuable insights for buyers looking to navigate the current landscape effectively.
Frequently Asked Questions (FAQs) for B2B Buyers of packaging material supplier
-
How do I evaluate packaging material suppliers for my business needs?
To effectively evaluate packaging material suppliers, start by assessing their product quality and compliance with international standards. Request samples to review material durability and suitability for your products. Additionally, consider their production capacity and reliability in meeting deadlines, especially if you’re sourcing from Africa, South America, the Middle East, or Europe. It’s also important to check references or reviews from other clients to gauge their performance. Lastly, ensure they have a responsive customer service team to address any issues promptly. -
What factors should I consider when negotiating payment terms with packaging suppliers?
When negotiating payment terms, consider the supplier’s payment flexibility, such as options for partial payments or extended credit terms. Assess the currency used for transactions, especially if you’re dealing internationally, as fluctuations can affect costs. Additionally, clarify any upfront fees or deposits required and ensure you understand the implications of late payments. Establishing a mutually beneficial agreement can foster long-term partnerships, so be open to discussing terms that work for both parties. -
What is the minimum order quantity (MOQ) I should expect from packaging suppliers?
Minimum order quantities (MOQs) can vary significantly among suppliers and depend on the type of packaging material. Generally, MOQs range from a few hundred to several thousand units. If you’re a smaller business, look for suppliers that offer flexibility or tiered pricing based on order size. Additionally, consider suppliers who are open to custom orders, as this may allow you to negotiate lower MOQs while still meeting your packaging needs. -
How can I ensure quality assurance in packaging materials sourced internationally?
To ensure quality assurance, request certifications from suppliers that demonstrate compliance with industry standards (e.g., ISO, ASTM). Implement a quality control process by conducting regular inspections of incoming shipments and reviewing samples prior to bulk orders. Establish clear quality specifications in your contracts, and consider engaging third-party inspection services if sourcing from regions with varying quality levels. Open communication with suppliers about quality expectations is also crucial. -
What customization options are available when sourcing packaging materials?
Many packaging suppliers offer a range of customization options, including size, shape, color, and branding elements like logos. When sourcing, inquire about the supplier’s ability to meet specific design requirements and the associated costs. Some suppliers may also provide design assistance or mock-ups before production, which can be invaluable for ensuring your packaging aligns with your brand identity. Always clarify lead times for customized orders to avoid delays in your supply chain. -
How do I handle logistics and shipping when sourcing packaging materials internationally?
Effective logistics management involves understanding shipping options, costs, and timelines. Discuss with your supplier about their preferred shipping methods and whether they can handle logistics on your behalf. Consider using freight forwarders to streamline the process and ensure compliance with international shipping regulations. Be aware of potential customs duties and tariffs that may apply to your shipments, and factor these costs into your budgeting. -
What are the common challenges faced when sourcing packaging materials internationally?
Common challenges include language barriers, differing regulations, and potential delays in shipping. Additionally, quality inconsistencies may arise if suppliers do not adhere to the agreed-upon standards. To mitigate these risks, conduct thorough research on suppliers and consider visiting facilities if feasible. Establish clear communication channels and contractual agreements to define expectations and responsibilities, which can help prevent misunderstandings. -
How can I build a long-term relationship with my packaging material supplier?
Building a long-term relationship with a packaging supplier involves consistent communication and collaboration. Regularly provide feedback on product quality and service, and be open to discussing improvements. Consider establishing a partnership approach by sharing your business goals and challenges with the supplier, allowing them to better understand your needs. Recognizing their efforts through timely payments and loyalty can also strengthen the relationship, fostering mutual growth and success.
Important Disclaimer & Terms of Use
⚠️ Important Disclaimer
The information provided in this guide, including content regarding manufacturers, technical specifications, and market analysis, is for informational and educational purposes only. It does not constitute professional procurement advice, financial advice, or legal advice.
While we have made every effort to ensure the accuracy and timeliness of the information, we are not responsible for any errors, omissions, or outdated information. Market conditions, company details, and technical standards are subject to change.
B2B buyers must conduct their own independent and thorough due diligence before making any purchasing decisions. This includes contacting suppliers directly, verifying certifications, requesting samples, and seeking professional consultation. The risk of relying on any information in this guide is borne solely by the reader.
Strategic Sourcing Conclusion and Outlook for packaging material supplier
As the global packaging landscape evolves, strategic sourcing remains pivotal for international B2B buyers. Understanding the nuances of packaging material suppliers can significantly impact your supply chain efficiency and product sustainability. By prioritizing strong supplier relationships and leveraging market intelligence, businesses can not only reduce costs but also enhance their environmental footprint through eco-friendly packaging solutions.
What Are the Key Takeaways for International B2B Buyers?
- Supplier Diversity: Engage with suppliers across different regions, such as Africa, South America, the Middle East, and Europe, to mitigate risks and ensure a steady supply of materials.
- Sustainability Focus: As consumers increasingly demand sustainable products, aligning with suppliers who prioritize green practices will enhance your brand’s reputation and appeal.
- Technological Integration: Utilize digital tools and platforms for better visibility and communication with suppliers, which can streamline procurement processes and improve decision-making.
How Can You Prepare for Future Trends in Packaging?
Looking ahead, the packaging industry will continue to innovate, driven by technology and sustainability demands. Now is the time for international B2B buyers to reassess their sourcing strategies and adopt a proactive approach. By embracing these insights and remaining adaptable, you can position your business for success in an increasingly competitive market. Engage with your suppliers today to explore new opportunities and ensure your packaging solutions meet future demands.