Discover Top Paper Making Machine Manufacturers for 2025
Introduction: Navigating the Global Market for Paper Making Machine Manufacturers
In an increasingly competitive landscape, sourcing paper making machines poses significant challenges for international B2B buyers. With the growing demand for sustainable and efficient production, understanding the intricacies of selecting the right equipment is crucial. This guide offers a comprehensive overview of the various types of paper making machines, their applications across diverse industries, and essential criteria for supplier vetting. By examining factors such as cost, technology, and support services, buyers can make informed decisions that align with their operational needs.
Navigating the global market can be daunting, especially for businesses in regions like Africa, South America, the Middle East, and Europe. Each of these markets presents unique opportunities and challenges that require tailored strategies. For instance, buyers from Italy may prioritize advanced technology for high-quality production, while those in Africa might focus on cost-effective solutions that support local economies. This guide aims to empower B2B buyers by providing actionable insights and best practices that facilitate smart purchasing decisions.
Whether you are a startup looking to establish your paper production line or an established company seeking to upgrade your equipment, this resource is designed to help you identify reputable manufacturers, assess machine performance, and ultimately enhance your competitive edge in the global market. With the right knowledge, you can streamline your sourcing process and drive your business towards greater efficiency and sustainability.
Understanding Paper Making Machine Manufacturers Types and Variations
Type Name | Key Distinguishing Features | Primary B2B Applications | Brief Pros & Cons for Buyers |
---|---|---|---|
Fourdrinier Machines | Continuous sheet formation, versatile for various paper types | Newsprint, packaging, and specialty papers | Pros: High efficiency, lower cost per unit. Cons: Limited to thin paper grades. |
Cylinder Mould Machines | Cylindrical wire for sheet formation, ideal for heavier papers | Cardboard, tissue, and art papers | Pros: Better for thicker papers, less waste. Cons: Slower production rate. |
Twin Wire Machines | Two wires for sheet formation, enhanced drainage | High-quality printing and writing papers | Pros: Superior quality, higher speeds. Cons: More complex maintenance. |
Specialty Paper Machines | Customizable for unique paper types and applications | Filter papers, thermal papers, and more | Pros: Tailored solutions, niche markets. Cons: Higher initial investment. |
Recycled Paper Machines | Focused on processing recycled materials | Eco-friendly paper products, packaging | Pros: Sustainable, growing market demand. Cons: Variability in raw material quality. |
What Are Fourdrinier Machines and Their Suitability for B2B Buyers?
Fourdrinier machines are the backbone of the paper industry, known for their ability to produce continuous sheets of paper at high speeds. These machines are particularly suitable for producing newsprint, packaging materials, and specialty papers. B2B buyers should consider the efficiency and cost-effectiveness of Fourdrinier machines, as they typically offer a lower cost per unit for mass production. However, they are limited to producing thinner paper grades, which may not meet the needs of all buyers.
How Do Cylinder Mould Machines Differ in Performance and Application?
Cylinder mould machines are designed for producing thicker paper grades, such as cardboard and tissue paper. They utilize a cylindrical wire to form the sheet, allowing for better control over the paper’s thickness and quality. This type of machine is ideal for B2B buyers focused on high-quality outputs. While cylinder mould machines tend to have a slower production rate compared to Fourdrinier machines, their ability to create heavier papers makes them a valuable option for specific applications.
What Advantages Do Twin Wire Machines Offer to Buyers?
Twin wire machines are characterized by their dual-wire system, which enhances drainage and results in superior sheet quality. These machines are particularly suitable for producing high-quality printing and writing papers. B2B buyers looking for efficiency and quality will find twin wire machines advantageous, as they can operate at higher speeds while maintaining excellent product standards. However, buyers should be prepared for more complex maintenance requirements associated with these machines.
Why Choose Specialty Paper Machines for Unique Production Needs?
Specialty paper machines provide customizable solutions for producing unique paper types, including filter papers and thermal papers. These machines cater to niche markets, allowing B2B buyers to meet specific customer demands. The ability to tailor production capabilities can justify the higher initial investment, especially for companies focusing on specialized paper products. However, potential buyers should evaluate the long-term return on investment and market demand for their unique offerings.
How Do Recycled Paper Machines Contribute to Sustainable Production?
Recycled paper machines are designed to process recycled materials, allowing manufacturers to produce eco-friendly paper products. As sustainability becomes increasingly important in global markets, B2B buyers may find significant opportunities in this sector. While the demand for recycled products is growing, buyers must be aware of the variability in raw material quality, which can impact production consistency and product quality. Investing in recycled paper machines can position businesses favorably in the competitive landscape, appealing to environmentally conscious consumers.
Related Video: The Paper Making Process
Key Industrial Applications of Paper Making Machine Manufacturers
Industry/Sector | Specific Application of Paper Making Machine Manufacturers | Value/Benefit for the Business | Key Sourcing Considerations for this Application |
---|---|---|---|
Packaging | Production of corrugated boxes and paperboard packaging | Enhanced product protection and reduced shipping costs | Machine capacity, material compatibility, and automation level |
Hygiene Products | Manufacturing of tissue paper and sanitary products | High demand for eco-friendly products and increased market share | Sustainability certifications, production speed, and quality control |
Printing and Publishing | Production of specialty papers for printing and publishing | High-quality finishes and customization options for diverse markets | Paper quality, customization capabilities, and delivery times |
Stationery | Production of notepads, envelopes, and writing paper | Consistent quality and branding opportunities for stationery products | Customization options, durability, and supply chain reliability |
Construction | Creation of paper-based insulation and construction materials | Cost-effective solutions for energy efficiency in buildings | Material sourcing, thermal performance, and regulatory compliance |
What Are the Key Industrial Applications of Paper Making Machine Manufacturers?
How is Paper Making Machinery Used in the Packaging Industry?
In the packaging sector, paper making machines are crucial for producing corrugated boxes and paperboard packaging. These machines create durable and lightweight materials that protect products during transport. For international buyers, especially in regions like Africa and South America, sourcing machines that can handle diverse raw materials and produce custom sizes is essential. The machines must also ensure compliance with international packaging standards, which can vary by region.
What Role Do Paper Making Machines Play in Hygiene Product Manufacturing?
Paper making machines are integral to the production of tissue paper and sanitary products, catering to a growing demand for hygiene solutions. Manufacturers need machines that can deliver high-speed production while maintaining quality, especially in markets in the Middle East and Europe where hygiene standards are stringent. Buyers should prioritize sourcing from manufacturers with proven sustainability practices, as eco-friendly products are increasingly preferred by consumers.
How Are Paper Making Machines Utilized in Printing and Publishing?
In the printing and publishing industry, specialized paper making machines produce high-quality paper that can be tailored for various applications, including books, magazines, and marketing materials. The ability to customize paper grades and finishes is vital for meeting diverse client needs. International buyers, particularly from Europe, should consider the machine’s compatibility with different printing technologies and its ability to deliver consistent quality across large print runs.
What is the Importance of Paper Making Machines in Stationery Production?
For the stationery sector, paper making machines facilitate the production of notepads, envelopes, and various writing papers. These machines are designed to ensure uniformity and quality, which are crucial for branding and consumer trust. Buyers should focus on sourcing machines that offer customization options and durability, as these factors significantly impact the stationery’s marketability in competitive regions like South America and Africa.
How Do Paper Making Machines Contribute to the Construction Industry?
In the construction industry, paper making machines are used to create paper-based insulation and other building materials. These products offer cost-effective solutions for energy efficiency and sustainability in construction projects. International buyers must consider sourcing machines that comply with local building codes and environmental regulations, ensuring that the products meet the growing demand for green building materials in Europe and the Middle East.
Related Video: How Toilet Paper Is Made in Factory – Toilet Tissue Paper Making Machine
3 Common User Pain Points for ‘Paper Making Machine Manufacturers’ & Their Solutions
Scenario 1: Navigating Complex Specifications for Paper Production Needs
The Problem: B2B buyers often face the challenge of understanding the complex specifications required for different types of paper production. Many manufacturers offer a wide range of machines designed for specific applications, but without a clear understanding of how these specifications translate to their production needs, buyers can feel overwhelmed. This complexity can lead to purchasing decisions that do not align with their operational requirements, resulting in costly mistakes and inefficiencies in production.
The Solution: To effectively navigate these complexities, B2B buyers should begin by conducting thorough needs assessments that define their specific paper production goals. Engaging directly with manufacturers during the sourcing process is crucial. Buyers should request detailed product specifications and capabilities, and consider forming a partnership with a manufacturer that offers customized solutions. Additionally, leveraging industry experts or consultants can provide valuable insights into the latest technologies and best practices in paper production. By ensuring that they clearly communicate their production goals and constraints, buyers can receive tailored advice that aligns with their operational needs, reducing the risk of costly errors.
Scenario 2: Managing Cost and Investment for Paper Making Machines
The Problem: In regions such as Africa and South America, budget constraints can significantly impact the decision-making process for purchasing paper-making machines. Many companies find themselves torn between investing in high-quality equipment that promises efficiency and durability, and cheaper alternatives that may compromise performance. This dilemma is further complicated by the varying costs of maintenance and the potential need for future upgrades, which can strain financial resources.
The Solution: To alleviate financial pressure, B2B buyers should develop a comprehensive cost-benefit analysis that factors in not only the initial purchase price but also long-term operational costs, including maintenance and energy consumption. Establishing relationships with multiple manufacturers can provide competitive quotes and financing options, allowing buyers to compare offers effectively. Additionally, buyers should explore leasing options or second-hand equipment from reputable manufacturers, which can offer significant savings while still meeting production needs. It’s also beneficial to consider the total lifecycle of the machine, including potential resale value, as this can influence overall investment return.
Scenario 3: Ensuring Reliable After-Sales Support and Maintenance
The Problem: After-sales support is often a significant concern for B2B buyers in the paper manufacturing sector, especially in regions like the Middle East and Europe, where machine downtime can lead to substantial financial losses. Buyers frequently encounter difficulties with obtaining timely maintenance services or spare parts, which can disrupt production schedules and impact overall business operations.
The Solution: To ensure reliable after-sales support, buyers should prioritize manufacturers with strong reputations for customer service and technical support. Before finalizing any purchase, they should inquire about the availability of local service centers, response times for maintenance requests, and warranty terms. Establishing clear communication channels with the manufacturer can facilitate quicker resolutions to any issues that arise. Additionally, buyers can benefit from investing in training for their staff on routine maintenance practices, which can help mitigate downtime caused by minor issues. By fostering a proactive relationship with the manufacturer and ensuring that they have access to necessary resources, buyers can enhance their operational efficiency and reduce the risk of unexpected disruptions.
Strategic Material Selection Guide for Paper Making Machine Manufacturers
When selecting materials for paper-making machines, manufacturers must consider various factors that influence performance, durability, and compliance with international standards. Below, we analyze four common materials used in the construction of paper-making machines: stainless steel, carbon steel, rubber, and ceramics. Each material has unique properties, advantages, and limitations that can significantly impact the manufacturing process and final product quality.
What Are the Key Properties of Stainless Steel in Paper Making Machines?
Stainless steel is a popular choice due to its excellent corrosion resistance, high strength, and ability to withstand high temperatures and pressures. Typically, grades like 304 and 316 are used in paper-making machinery. The key properties include:
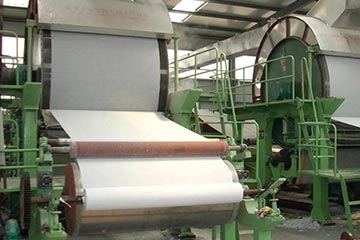
A stock image related to Paper Making Machine Manufacturers.
- Corrosion Resistance: Stainless steel is highly resistant to rust and corrosion, making it suitable for wet environments common in paper production.
- Temperature and Pressure Ratings: It can handle high temperatures up to 800°C and pressures up to 20 bar, ensuring reliability in various operational conditions.
Pros:
– Long lifespan due to corrosion resistance.
– Low maintenance requirements.
Cons:
– Higher initial cost compared to carbon steel.
– More challenging to machine and fabricate.
How Does Carbon Steel Compare for Paper Making Applications?
Carbon steel is another widely used material, especially in components that do not require high corrosion resistance. Its properties include:
- Strength: Carbon steel offers excellent tensile strength, making it suitable for structural components.
- Cost-Effectiveness: It is generally less expensive than stainless steel, making it a budget-friendly option.
Pros:
– Lower material costs.
– Easier to machine and fabricate.
Cons:
– Prone to rust and corrosion, requiring protective coatings.
– Limited lifespan in humid environments.
What Role Does Rubber Play in Paper Making Machinery?
Rubber is primarily used for seals, gaskets, and belts in paper-making machines. Its key properties include:
- Flexibility: Rubber provides excellent flexibility and can absorb vibrations, which is crucial for smooth operation.
- Chemical Resistance: Certain types of rubber can resist various chemicals used in the paper-making process.
Pros:
– Cost-effective and easy to replace.
– Good vibration dampening properties.
Cons:
– Limited temperature resistance, typically up to 100°C.
– Degradation over time, especially in harsh environments.
Why Are Ceramics Important in Paper Making Machines?
Ceramics are used in specific applications, such as wear-resistant components and coatings. Their properties include:
- Hardness: Ceramics are extremely hard and can withstand abrasive materials, making them suitable for areas with high wear.
- Chemical Resistance: They are highly resistant to chemicals, ensuring longevity in harsh environments.
Pros:
– Long lifespan due to wear resistance.
– Low friction properties can enhance efficiency.
Cons:
– Brittle nature can lead to cracking under stress.
– Higher manufacturing complexity and costs.
Summary Table of Material Selection for Paper Making Machine Manufacturers
Material | Typical Use Case for Paper Making Machine Manufacturers | Key Advantage | Key Disadvantage/Limitation | Relative Cost (Low/Med/High) |
---|---|---|---|---|
Stainless Steel | Structural components, frames, and rollers | Excellent corrosion resistance | Higher initial cost | High |
Carbon Steel | Structural components, non-corrosive parts | Cost-effective | Prone to rust, requires coatings | Medium |
Rubber | Seals, gaskets, and belts | Good flexibility and vibration dampening | Limited temperature resistance | Low |
Ceramics | Wear-resistant components and coatings | Long lifespan due to hardness | Brittle and higher manufacturing complexity | Medium |
This strategic material selection guide provides international B2B buyers with essential insights into the properties, advantages, and limitations of materials used in paper-making machines. Understanding these factors is crucial for making informed purchasing decisions, especially when considering compliance with regional standards and operational requirements.
In-depth Look: Manufacturing Processes and Quality Assurance for Paper Making Machine Manufacturers
What Are the Main Stages in the Manufacturing Process of Paper Making Machines?
The manufacturing process of paper making machines is intricate and involves several critical stages to ensure high efficiency and quality. Here are the main stages:
1. Material Preparation
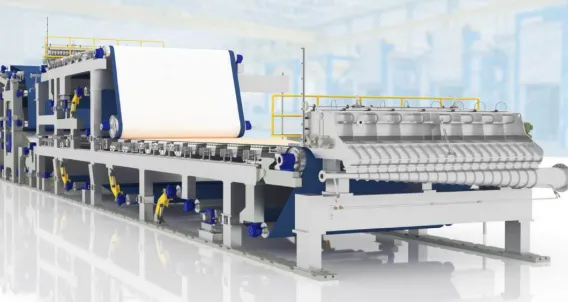
A stock image related to Paper Making Machine Manufacturers.
Material preparation is the foundation of the manufacturing process. It involves sourcing high-quality raw materials, primarily steel and various alloys, which are essential for machine construction. Suppliers must ensure that materials meet international standards, including tensile strength and corrosion resistance. For B2B buyers, it is crucial to verify that suppliers have a robust supply chain management system to avoid delays in production.
2. Forming
The forming stage is where raw materials are shaped into various components of the paper making machine. This includes processes such as cutting, bending, and welding. Advanced techniques like laser cutting and CNC machining are often employed to achieve precision. Buyers should inquire about the technologies used and whether they adhere to relevant international standards to ensure product reliability.
3. Assembly
Once individual components are formed, they undergo assembly. This stage is critical as it integrates various parts into a cohesive unit. Manufacturers often use automated assembly lines to enhance efficiency and reduce human error. For international buyers, understanding the assembly techniques and workforce training programs can provide insights into the expected quality of the final product.
4. Finishing
The finishing stage involves painting, coating, and final inspections. This is where machines receive protective coatings to enhance durability and aesthetics. It’s also the phase where any adjustments are made to ensure optimal performance. Buyers should check if suppliers use environmentally-friendly finishing processes, which are increasingly important in global markets.
How Is Quality Assurance Implemented in Paper Making Machine Manufacturing?
Quality assurance (QA) is a vital aspect of the manufacturing process. It ensures that every machine produced meets predefined standards and customer expectations. Here are the essential components of quality assurance in this industry:
Relevant International Standards for Quality Assurance
Many paper making machine manufacturers adhere to international quality standards, such as ISO 9001, which focuses on quality management systems. Additionally, certifications like CE (Conformité Européenne) and API (American Petroleum Institute) are relevant, especially for machines intended for specific applications. Buyers should ensure that suppliers hold these certifications to guarantee compliance with international safety and quality standards.
What Are the Key Quality Control Checkpoints?
Quality control (QC) is implemented at various checkpoints throughout the manufacturing process:
-
Incoming Quality Control (IQC): This stage involves inspecting raw materials and components before they enter the production line. It ensures that only high-quality materials are used, which is crucial for the machine’s longevity and performance.
-
In-Process Quality Control (IPQC): During manufacturing, regular inspections are conducted to monitor the production process and detect defects early. This minimizes waste and rework, saving time and costs.
-
Final Quality Control (FQC): This final inspection checks the assembled machine against specifications and performance standards. It often includes rigorous testing to ensure functionality.
What Testing Methods Are Commonly Used in Paper Making Machine Manufacturing?
Testing methods vary, but several are commonly employed to ensure machines meet quality standards:
-
Performance Testing: Machines are run under controlled conditions to verify their performance metrics, such as speed, efficiency, and output quality.
-
Durability Testing: This involves subjecting machines to extreme conditions to test their resilience and longevity.
-
Safety Testing: Ensures that machines comply with safety regulations and can operate without posing risks to users.
Buyers should inquire about the specific testing methods employed by suppliers and request documentation of results to ensure compliance with industry standards.
How Can B2B Buyers Verify Supplier Quality Control Measures?
To ensure that suppliers maintain high-quality standards, B2B buyers should take several proactive steps:
Conduct Audits
Regular audits of manufacturing facilities can provide buyers with insights into a supplier’s quality control processes. This includes reviewing production practices, employee training, and adherence to safety standards. Audits can be conducted by the buyer or a third-party organization to ensure objectivity.
Request Quality Reports
Suppliers should be willing to provide detailed quality reports that outline their QC processes, testing results, and any corrective actions taken. This documentation serves as a testament to their commitment to quality and can help buyers make informed decisions.
Utilize Third-Party Inspections
Engaging third-party inspection services can provide additional assurance of product quality. These services can conduct independent inspections at various stages of the manufacturing process, offering an unbiased assessment of the supplier’s capabilities.
What Are the Quality Control Nuances for International B2B Buyers?
For international buyers, understanding the nuances of quality control is essential, especially when sourcing from regions like Africa, South America, the Middle East, and Europe. Here are some considerations:
-
Cultural Differences: Different regions may have varying approaches to quality assurance and manufacturing practices. It’s vital for buyers to understand these cultural nuances and how they may affect supplier performance.
-
Regulatory Compliance: Ensure that suppliers comply with both local and international regulations. This is particularly important when importing machinery, as non-compliance can lead to costly delays and penalties.
-
Language Barriers: Communication can sometimes be a challenge, particularly in regions where English is not the primary language. Buyers should ensure that they have clear lines of communication with suppliers to avoid misunderstandings regarding quality expectations.
By thoroughly understanding the manufacturing processes and quality assurance measures, B2B buyers can make informed decisions when sourcing paper making machines. This not only ensures the acquisition of high-quality machinery but also fosters long-term partnerships with reliable suppliers.
Practical Sourcing Guide: A Step-by-Step Checklist for ‘Paper Making Machine Manufacturers’
In the competitive landscape of paper production, sourcing the right machinery is pivotal for businesses aiming for efficiency and sustainability. This practical sourcing guide provides a structured checklist for international B2B buyers, particularly those in Africa, South America, the Middle East, and Europe, to effectively procure paper-making machines.
Step 1: Define Your Technical Specifications
Establishing clear technical specifications is the first step in your procurement journey. This involves detailing the capacity, size, and type of paper you intend to produce. Understanding these parameters ensures that you select a machine that meets your production needs while optimizing operational efficiency.
- Capacity Requirements: Determine the volume of paper needed daily or weekly.
- Paper Type: Specify whether you need machines for recycled paper, specialty paper, or standard printing paper.
Step 2: Conduct Market Research on Manufacturers
Researching potential manufacturers is essential to identify reliable suppliers. Look for companies with a proven track record in producing high-quality paper-making machines. Utilize industry reports, trade shows, and online platforms to gather information on leading manufacturers.
- Reputation: Check reviews and ratings from other buyers.
- Industry Experience: Prioritize manufacturers with extensive experience in the paper industry.
Step 3: Evaluate Potential Suppliers
Before making a commitment, it is crucial to thoroughly vet potential suppliers. Request company profiles, case studies, and references from buyers in similar industries or regions. This evaluation helps ensure that the supplier can meet your specific requirements and maintain quality standards.
- Financial Stability: Assess the supplier’s financial health to ensure long-term reliability.
- Client References: Speak directly with other businesses that have purchased from the supplier.
Step 4: Verify Compliance and Certifications
Ensure that the manufacturers you are considering comply with international quality standards and safety regulations. Certifications such as ISO 9001 or CE mark are indicators of quality management and product safety.
- Documentation: Request copies of relevant certifications.
- Regulatory Compliance: Verify adherence to local and international regulations regarding machinery safety and emissions.
Step 5: Request Quotes and Compare Pricing
Once you have shortlisted potential suppliers, request detailed quotes that include machine specifications, warranties, and after-sales support. Comparing these quotes can help you identify the best value for your investment.
- Cost Breakdown: Ensure quotes include all costs, such as shipping and installation.
- Payment Terms: Clarify payment schedules and financing options.
Step 6: Assess After-Sales Support and Warranty Options
After-sales support is a critical aspect of your decision-making process. Ensure that the suppliers offer comprehensive support, including installation, training, and maintenance services. A robust warranty can also safeguard your investment against unforeseen issues.
- Support Services: Inquire about training for your staff and ongoing technical support.
- Warranty Terms: Understand the duration and coverage of the warranty provided.
Step 7: Finalize the Contract and Ensure Clear Terms
Before finalizing your purchase, ensure that all terms are clearly outlined in a contract. This includes delivery timelines, payment schedules, and responsibilities for both parties. A well-drafted contract protects your interests and facilitates a smooth transaction.
- Legal Review: Consider having the contract reviewed by a legal professional.
- Clarity on Deliverables: Confirm that all specifications and commitments are documented to avoid disputes.
By following this step-by-step checklist, international B2B buyers can make informed decisions when sourcing paper-making machines, ultimately enhancing their production capabilities and contributing to business growth.
Comprehensive Cost and Pricing Analysis for Paper Making Machine Manufacturers Sourcing
What Are the Key Cost Components for Paper Making Machines?
Understanding the cost structure of paper making machines is crucial for international B2B buyers. The primary components influencing the total cost include:
-
Materials: Raw materials, such as steel, aluminum, and various components like motors and belts, constitute a significant portion of the overall cost. Prices can fluctuate based on global market trends and availability.
-
Labor: Labor costs vary significantly by region. For instance, labor in Southeast Asia may be less expensive compared to Europe. Skilled labor for assembly and maintenance can also impact pricing.
-
Manufacturing Overhead: This includes costs associated with factory operations, such as utilities, rent, and indirect labor. The efficiency of the manufacturing process can directly influence these costs.
-
Tooling: Custom tooling may be required for specific machine configurations, adding to the initial investment. Tooling costs are especially relevant for customized machines tailored to specific production needs.
-
Quality Control (QC): Implementing strict quality control measures ensures that machines meet industry standards and certifications. While this may increase upfront costs, it mitigates long-term risks associated with machine failures.
-
Logistics: Shipping costs, which can be substantial for heavy machinery, vary based on distance, shipping method, and logistics provider. Understanding Incoterms is essential for calculating these costs accurately.
-
Margin: Manufacturers typically apply a profit margin that can vary widely based on market demand, competition, and brand reputation.
How Do Price Influencers Affect Paper Making Machine Costs?
Several factors can influence the pricing of paper making machines, particularly for international buyers:
-
Volume and Minimum Order Quantity (MOQ): Purchasing in larger volumes often yields discounts. Understanding the MOQ set by manufacturers can help buyers negotiate better deals.
-
Specifications and Customization: Custom specifications can significantly affect the price. Buyers must clearly define their needs to avoid unexpected costs during production.
-
Material Quality and Certifications: Machines built with high-quality materials or those that meet specific certifications may command a higher price. However, these investments often lead to better performance and durability.
-
Supplier Factors: The reputation and reliability of the supplier can affect pricing. Established manufacturers may charge a premium due to their proven track record, while newer entrants might offer lower prices to attract buyers.
-
Incoterms: Understanding the terms of shipping and delivery is crucial. Different Incoterms (like FOB, CIF, etc.) can influence total landed costs, affecting the overall budget.
What Are the Best Negotiation Tips for International Buyers?
For B2B buyers, especially from regions like Africa, South America, the Middle East, and Europe, negotiating effectively is key to achieving favorable pricing:
-
Research Market Prices: Gather data on average prices for similar machines to establish a baseline for negotiations.
-
Build Relationships: Establishing a rapport with suppliers can lead to better pricing and favorable terms in the long run.
-
Be Transparent: Clearly communicate your requirements and budget constraints. Suppliers may be more willing to negotiate if they understand your needs.
-
Consider Total Cost of Ownership (TCO): While the initial purchase price is important, consider the TCO, including maintenance, energy consumption, and potential downtime. A higher upfront cost may be justified by lower operational costs.
-
Leverage Multiple Quotes: Obtaining quotes from multiple manufacturers can provide leverage in negotiations. It also helps to compare specifications and services offered.
Why Is It Important to Understand Pricing Nuances for International B2B Buyers?
International buyers must navigate additional complexities, such as currency fluctuations, import tariffs, and varying tax regulations. These factors can significantly affect the final price of machinery. Being aware of these nuances allows buyers to make informed decisions and better manage their budgets.
Disclaimer for Indicative Prices
Prices for paper making machines are subject to change based on market conditions, supplier pricing strategies, and other external factors. It is advisable for buyers to conduct thorough market research and obtain up-to-date quotations to ensure accurate budgeting.
Alternatives Analysis: Comparing Paper Making Machine Manufacturers With Other Solutions
When considering the procurement of paper-making machinery, international B2B buyers must evaluate various solutions to ensure they meet operational needs efficiently and cost-effectively. While traditional paper-making machine manufacturers offer robust solutions, alternative technologies and methods can also achieve similar goals. This section explores viable alternatives, providing a comprehensive comparison to help buyers make informed decisions.
Comparison Aspect | Paper Making Machine Manufacturers | Automated Pulping Systems | Recycled Paper Processing Units |
---|---|---|---|
Performance | High throughput, consistent quality | Moderate throughput, variable quality | Variable throughput, dependent on raw material quality |
Cost | High initial investment, long-term ROI | Moderate initial cost, lower operational costs | Low initial investment, variable operational costs |
Ease of Implementation | Requires skilled workforce, complex installation | Easier to integrate with existing setups | Quick setup, minimal training required |
Maintenance | Regular maintenance required, specialized service | Lower maintenance due to fewer moving parts | Moderate maintenance, depends on equipment age |
Best Use Case | Large-scale production, high-quality paper | Intermediate production, eco-friendly pulp | Sustainable production, lower-grade paper |
What are Automated Pulping Systems and How Do They Compare?
Automated pulping systems are designed to convert raw materials into pulp with minimal human intervention. They typically employ advanced technology to streamline the pulping process, making it more efficient.
Pros: These systems generally have a lower initial cost compared to traditional paper-making machines and can significantly reduce operational costs over time. Additionally, they are easier to integrate into existing production lines.
Cons: However, automated pulping systems often exhibit variable quality in the output, which may not meet the standards required for high-end paper products. Their performance can be influenced by the quality of raw materials, leading to inconsistencies.
How Do Recycled Paper Processing Units Function as an Alternative?
Recycled paper processing units focus on converting waste paper into new paper products. This method is increasingly popular due to its sustainability and cost-effectiveness.
Pros: The initial investment for recycled paper processing units is typically lower than that for traditional paper-making machines. They also contribute to environmental sustainability by reducing waste and promoting recycling.
Cons: The downside is that the throughput can be variable and heavily dependent on the quality of the incoming raw materials. Additionally, the end products may not match the quality of paper produced from virgin fibers, which could limit marketability in some segments.
Conclusion: How Should B2B Buyers Choose the Right Paper Production Solution?
When selecting a paper production solution, B2B buyers must assess their specific operational requirements, budget constraints, and sustainability goals. Traditional paper-making machines are ideal for large-scale production with stringent quality demands, while automated pulping systems and recycled paper processing units offer cost-effective and eco-friendly alternatives. By carefully evaluating these options based on performance, cost, ease of implementation, and maintenance needs, buyers can make a strategic choice that aligns with their business objectives and market demands.
Essential Technical Properties and Trade Terminology for Paper Making Machine Manufacturers
What Are the Key Technical Properties for Paper Making Machines?
Understanding the essential technical properties of paper making machines is crucial for B2B buyers seeking to optimize their production processes. Here are some of the most critical specifications:
1. Material Grade
Material grade refers to the quality of materials used in the construction of the machine. High-grade materials, such as stainless steel, enhance durability and resistance to corrosion. For international buyers, selecting machines with superior material grades ensures longevity and reduces maintenance costs.
2. Tolerance
Tolerance indicates the permissible limits of variation in a machine’s dimensions and performance. High tolerance levels are vital for ensuring consistent product quality. In the B2B context, this property can significantly affect production efficiency and waste reduction, making it a key factor in procurement decisions.
3. Production Capacity
Production capacity is the maximum output a paper making machine can achieve within a specified timeframe. It is typically measured in tons per day. For buyers, understanding the production capacity helps in aligning machine specifications with their operational demands, thereby optimizing resource allocation and supply chain management.
4. Energy Consumption
Energy consumption rates indicate the efficiency of the machine in terms of power usage. Machines that consume less energy while maintaining high output levels are preferred in the B2B market, as they can lead to significant cost savings over time. This is especially relevant for businesses in regions where energy costs are high.
5. Automation Level
The level of automation in a paper making machine affects labor costs and operational efficiency. Machines with higher automation levels require fewer manual interventions, which can streamline production processes. For international buyers, investing in highly automated systems can enhance competitiveness and reduce the risk of human error.
Which Trade Terms Are Essential for Paper Making Machine Transactions?
Familiarizing yourself with industry jargon is crucial when dealing with paper making machine manufacturers. Here are some key terms:
1. OEM (Original Equipment Manufacturer)
An OEM is a company that produces parts or equipment that may be marketed by another manufacturer. Understanding OEM relationships helps buyers ensure they are sourcing components that meet specific quality standards and are compatible with their existing machines.
2. MOQ (Minimum Order Quantity)
MOQ refers to the smallest quantity of a product that a supplier is willing to sell. This term is critical for B2B buyers who need to manage inventory levels and budget constraints. Knowing the MOQ helps in negotiating better terms and planning purchases effectively.
3. RFQ (Request for Quotation)
An RFQ is a document sent to suppliers requesting pricing and terms for specific products or services. For buyers, issuing an RFQ can lead to competitive pricing and better contract terms, making it an essential step in the procurement process.
4. Incoterms (International Commercial Terms)
Incoterms define the responsibilities of buyers and sellers regarding shipping, insurance, and tariffs. Familiarity with these terms helps B2B buyers understand their liabilities and ensures smooth international transactions, especially when dealing with cross-border suppliers.
5. Lead Time
Lead time refers to the time it takes from placing an order to the product’s delivery. This term is crucial for supply chain management, as longer lead times can affect production schedules. By understanding lead times, buyers can better plan their inventory and avoid production delays.
In summary, grasping the key technical properties and trade terminology associated with paper making machines empowers international B2B buyers to make informed decisions, negotiate effectively, and optimize their procurement processes.
Navigating Market Dynamics and Sourcing Trends in the Paper Making Machine Manufacturers Sector
What Are the Current Market Dynamics and Key Trends in the Paper Making Machine Sector?
The global paper making machine market is witnessing robust growth, driven by increasing demand for sustainable packaging solutions and the rise of eco-friendly products. Key trends include the integration of automation and Industry 4.0 technologies, which enhance productivity and efficiency. Manufacturers are increasingly adopting smart technologies, such as IoT-enabled machines, to optimize production processes, reduce waste, and improve quality control. This trend is particularly relevant for international B2B buyers from regions like Africa, South America, the Middle East, and Europe, who seek to upgrade their production capabilities.
Furthermore, a noticeable shift towards recycled paper production is reshaping sourcing trends. Buyers are looking for machines that can handle a variety of raw materials, including recycled fibers, which not only meet sustainability goals but also lower operational costs. Emerging markets in Africa and South America are investing in modernizing their paper production infrastructure to cater to local and international demands, thus creating opportunities for B2B partnerships.
How Is Sustainability Influencing Sourcing Trends in the Paper Making Industry?
Sustainability is becoming a cornerstone of sourcing strategies in the paper making sector. Environmental impact considerations are driving B2B buyers to prioritize suppliers that adhere to ethical practices and sustainable resource management. This includes sourcing from manufacturers that utilize eco-friendly materials and processes, thereby reducing carbon footprints and promoting a circular economy.
Buyers are increasingly seeking suppliers with recognized green certifications, such as FSC (Forest Stewardship Council) and PEFC (Programme for the Endorsement of Forest Certification). These certifications assure that the paper making machines are sourced from responsibly managed forests and that the manufacturing processes comply with environmental standards. Additionally, the demand for biodegradable and compostable paper products is on the rise, pushing manufacturers to innovate and adopt more sustainable practices.
What Is the Evolution of the Paper Making Machine Industry and Its Impact on B2B Buyers?
The paper making machine industry has evolved significantly over the past century. Originally characterized by manual processes, the sector has transitioned to mechanized production, leading to increased efficiency and output. The introduction of computerized systems in the late 20th century revolutionized the industry, allowing for precise control and monitoring of production parameters.
In recent years, this evolution has accelerated with advancements in technology, such as automation, AI, and IoT. These innovations are not only enhancing production capabilities but also enabling manufacturers to offer tailored solutions to meet specific buyer needs. For B2B buyers, understanding this evolution is crucial, as it informs their purchasing decisions and helps them align with suppliers that are at the forefront of technological advancements. Embracing these changes can facilitate better quality products, reduced costs, and enhanced sustainability efforts in their operations.
Frequently Asked Questions (FAQs) for B2B Buyers of Paper Making Machine Manufacturers
-
How do I choose the right paper making machine for my business needs?
Choosing the right paper making machine depends on several factors including production capacity, the type of paper you intend to produce, and the raw materials you have access to. Assess your current market demand and production goals to determine the specifications you need. It’s also advisable to consult with manufacturers to understand their offerings and tailor a solution that meets your specific requirements. Lastly, consider the machine’s energy efficiency and technological features, as these can significantly affect operational costs. -
What are the key features to look for in paper making machines?
When evaluating paper making machines, prioritize features such as automation level, energy efficiency, production speed, and the ability to handle various raw materials. Additionally, consider the machine’s maintenance requirements and the availability of spare parts. Advanced technologies like monitoring systems and quality control mechanisms can enhance production reliability and product quality. Lastly, ensure that the machine complies with international quality standards to facilitate smoother trade and export processes. -
What is the minimum order quantity (MOQ) for paper making machines?
Minimum order quantities for paper making machines can vary widely depending on the manufacturer and the complexity of the machine. Typically, MOQs can range from one unit for customized solutions to several units for standard models. It is essential to communicate your needs clearly with suppliers and negotiate MOQs that fit your budget and production capabilities. Some manufacturers may offer flexibility in MOQs, especially for first-time buyers or long-term partnerships. -
What payment terms should I expect when sourcing paper making machines?
Payment terms for purchasing paper making machines can differ by supplier and region. Common arrangements include a deposit (usually 30-50%) at order confirmation, followed by the balance upon shipment or installation. Some suppliers may offer financing options or extended payment plans, especially for larger purchases. It is crucial to clarify these terms upfront and review any associated fees or interest rates to avoid surprises later on. -
How can I ensure the quality of paper making machines from manufacturers?
To ensure quality, start by vetting manufacturers thoroughly. Look for certifications such as ISO 9001, which indicate adherence to quality management standards. Request samples of their previous work and references from other clients. Conduct factory visits if possible, or utilize third-party inspection services to evaluate the machines before purchase. Establishing a clear quality assurance protocol in your contract can also protect your investment. -
What logistics considerations should I keep in mind when importing paper making machines?
Logistics play a crucial role in importing paper making machines. Consider the shipping methods (air vs. sea), customs regulations, and potential tariffs that may apply. Ensure that you have a reliable logistics partner familiar with handling machinery imports. It’s also wise to factor in lead times for production and shipping, as delays can impact your business operations. Additionally, consider insurance for your shipment to mitigate risks during transit.
-
How do I handle after-sales support for paper making machines?
After-sales support is vital for the smooth operation of your paper making machines. Before finalizing your purchase, inquire about the manufacturer’s support policies, including warranty terms, maintenance services, and access to spare parts. Many manufacturers offer training sessions for your operators, which can enhance efficiency and safety. Establishing a relationship with the supplier for ongoing support can also facilitate quicker resolutions to any issues that may arise. -
What are the common challenges in sourcing paper making machines internationally?
Common challenges include navigating different regulations and standards across countries, language barriers, and cultural differences in business practices. Additionally, fluctuations in currency exchange rates can impact costs. To mitigate these risks, conduct thorough market research and consider working with local agents or consultants who understand the regional landscape. Clear communication and well-defined contracts can also help prevent misunderstandings and ensure a smooth procurement process.
Important Disclaimer & Terms of Use
⚠️ Important Disclaimer
The information provided in this guide, including content regarding manufacturers, technical specifications, and market analysis, is for informational and educational purposes only. It does not constitute professional procurement advice, financial advice, or legal advice.
While we have made every effort to ensure the accuracy and timeliness of the information, we are not responsible for any errors, omissions, or outdated information. Market conditions, company details, and technical standards are subject to change.
B2B buyers must conduct their own independent and thorough due diligence before making any purchasing decisions. This includes contacting suppliers directly, verifying certifications, requesting samples, and seeking professional consultation. The risk of relying on any information in this guide is borne solely by the reader.
Strategic Sourcing Conclusion and Outlook for Paper Making Machine Manufacturers
In the ever-evolving landscape of paper manufacturing, strategic sourcing stands as a cornerstone for B2B buyers seeking to optimize their procurement processes. Understanding the unique requirements of your market—whether you are operating in Africa, South America, the Middle East, or Europe—can significantly impact your sourcing decisions. Key takeaways include the importance of evaluating suppliers based on technological advancements, production capacity, and after-sales support. Prioritizing manufacturers who demonstrate sustainability practices can also enhance your brand’s reputation and compliance with international regulations.
As you navigate the complexities of sourcing paper making machines, consider engaging in collaborative partnerships with manufacturers that are willing to adapt to your specific needs. This not only fosters innovation but also ensures a consistent supply chain that can withstand market fluctuations.
Looking ahead, the demand for high-efficiency and eco-friendly paper production will continue to rise. Now is the time to leverage strategic sourcing to secure competitive advantages in your operations. Embrace the opportunity to connect with reputable suppliers who can support your growth ambitions. Your proactive approach today will position your business favorably for the challenges of tomorrow.