Discover Top Plastic Chair Suppliers: Your Complete Guide (2025)
Introduction: Navigating the Global Market for plastic chair supplier
In today’s global marketplace, sourcing high-quality plastic chairs that meet diverse needs can be a daunting task for international B2B buyers, especially when searching for suppliers who offer both durability and style. Whether you are in Africa, South America, the Middle East, or Europe, the challenge of identifying reliable plastic chair suppliers who can provide competitive pricing and timely delivery is critical to your operational success. This comprehensive guide is designed to assist you in navigating the complexities of the plastic chair market, covering essential aspects such as types of chairs available, their various applications, supplier vetting processes, and cost considerations.
By delving into the intricacies of sourcing plastic chairs, this guide empowers you to make informed purchasing decisions tailored to your specific business needs. From understanding the advantages of different materials to evaluating supplier credentials, you will gain insights that enhance your procurement strategy. The content is specifically curated to address the unique challenges faced by buyers in emerging markets, including Brazil and Vietnam, ensuring that you are well-equipped to engage effectively with suppliers.
Ultimately, this guide serves as your trusted resource for optimizing your purchasing process, enabling you to select the right plastic chair supplier and enhance your product offerings with confidence.
Understanding plastic chair supplier Types and Variations
Type Name | Key Distinguishing Features | Primary B2B Applications | Brief Pros & Cons for Buyers |
---|---|---|---|
Stackable Plastic Chairs | Lightweight, space-efficient, designed for stacking | Events, conferences, schools | Pros: Easy storage, cost-effective. Cons: May lack durability for heavy use. |
Reclining Plastic Chairs | Adjustable backrest, ergonomic design | Lounges, waiting areas | Pros: Enhanced comfort, versatile. Cons: Higher cost, may require more maintenance. |
Outdoor Plastic Chairs | UV-resistant, weatherproof materials | Cafés, patios, public spaces | Pros: Durable, easy to clean. Cons: Can fade over time, limited color options. |
Designer Plastic Chairs | Unique aesthetics, often custom-designed | High-end retail, exhibitions | Pros: Standout appearance, brand enhancement. Cons: Higher investment, may have longer lead times. |
Folding Plastic Chairs | Compact design, portable, easy setup | Trade shows, temporary seating solutions | Pros: Versatile, easy transport. Cons: Stability issues if overloaded. |
What Are Stackable Plastic Chairs and Their B2B Applications?
Stackable plastic chairs are a popular choice for businesses that require flexible seating arrangements. These chairs are lightweight and designed to be stacked, making them ideal for venues that host events, conferences, or educational settings. Buyers should consider the weight capacity and material durability, as lower-quality options may not withstand frequent use. The ability to store them efficiently is a significant advantage, especially for businesses with limited space.
How Do Reclining Plastic Chairs Benefit B2B Buyers?
Reclining plastic chairs offer ergonomic support with adjustable backrests, making them suitable for lounges and waiting areas. They provide enhanced comfort, which can improve customer satisfaction in settings where clients may wait for extended periods. While these chairs may come with a higher price tag, the investment can pay off in terms of customer experience. Buyers should assess the chair’s adjustability and ease of maintenance, as these factors can influence long-term usability.
Why Choose Outdoor Plastic Chairs for Business Needs?
Outdoor plastic chairs are specifically designed to withstand various weather conditions, making them perfect for cafés, patios, and public spaces. Their UV-resistant properties ensure longevity and minimal fading, while their lightweight nature allows for easy rearrangement. Buyers should consider the maintenance requirements and aesthetic appeal, as some options may fade over time. The ease of cleaning is another critical factor, especially for businesses dealing with food or beverages.
What Makes Designer Plastic Chairs a Good Investment?
Designer plastic chairs combine functionality with unique aesthetics, making them ideal for high-end retail spaces and exhibitions. These chairs can enhance brand image and attract customer attention. However, they often come at a premium price and may require longer lead times for custom designs. Buyers should evaluate their specific branding needs and budget constraints when considering these options, as the right choice can significantly impact customer perception.
How Do Folding Plastic Chairs Serve Temporary Seating Needs?
Folding plastic chairs are designed for portability and ease of setup, making them an excellent option for trade shows and temporary seating arrangements. Their compact design allows for easy transport and storage, catering to businesses that require flexibility in seating solutions. However, buyers should be cautious about stability, as these chairs may not support excessive weight. Assessing the quality of hinges and overall construction is essential for ensuring safety and longevity in use.
Related Video: Plastic Chair Collection Chair Shopping
Key Industrial Applications of plastic chair supplier
Industry/Sector | Specific Application of Plastic Chair Supplier | Value/Benefit for the Business | Key Sourcing Considerations for this Application |
---|---|---|---|
Hospitality | Restaurant and Café Furniture | Durable and easy-to-clean seating options | Consider weight, stackability, and UV resistance |
Education | Classroom and Auditorium Seating | Cost-effective and versatile seating solutions | Look for ergonomic design and compliance with safety standards |
Events and Exhibitions | Temporary Event Seating | Lightweight and portable options for easy setup | Ensure weather resistance and aesthetic appeal |
Healthcare | Patient Waiting Area Chairs | Easy-to-sanitize materials to enhance hygiene | Focus on comfort and durability for high-traffic areas |
Outdoor Recreation | Park and Recreational Area Seating | Weather-resistant and low-maintenance furniture | Assess material quality for durability against elements |
What Are the Key Applications of Plastic Chairs in the Hospitality Industry?
In the hospitality sector, plastic chairs are extensively used in restaurants and cafés due to their durability and ease of maintenance. These chairs can withstand heavy use while being easy to clean, making them ideal for high-traffic dining environments. B2B buyers should prioritize options that are stackable for efficient storage and consider UV resistance to prevent fading in outdoor settings.
How Are Plastic Chairs Utilized in Educational Institutions?
Educational institutions use plastic chairs for classrooms and auditoriums, providing cost-effective and versatile seating solutions. These chairs are often lightweight and can be easily rearranged to accommodate different teaching styles or events. When sourcing, buyers should focus on ergonomic designs that promote student comfort and ensure compliance with safety standards, especially for younger users.
What Role Do Plastic Chairs Play in Events and Exhibitions?
In the events and exhibitions sector, plastic chairs are favored for temporary seating arrangements due to their lightweight and portable nature. This allows for quick setup and takedown, which is essential for event planners. Buyers should ensure that the chairs are weather-resistant for outdoor events and aesthetically appealing to enhance the overall ambiance of the venue.
Why Are Plastic Chairs Important in Healthcare Settings?
Plastic chairs are commonly found in healthcare settings, particularly in patient waiting areas. Their ability to be made from easy-to-sanitize materials enhances hygiene, which is critical in medical environments. B2B buyers should look for options that provide comfort and durability, as these chairs often endure prolonged use in busy clinics and hospitals.
How Do Plastic Chairs Benefit Outdoor Recreation Areas?
In outdoor recreation areas, plastic chairs are essential due to their weather-resistant properties and low maintenance requirements. They are designed to withstand various environmental conditions, making them suitable for parks and public spaces. When sourcing, buyers should assess the material quality to ensure longevity and comfort for users in outdoor settings.
Related Video: Top 5 Industrial Robots you must see
3 Common User Pain Points for ‘plastic chair supplier’ & Their Solutions
Scenario 1: Challenges with Quality Control in Plastic Chairs
The Problem: B2B buyers often face the issue of inconsistent quality when sourcing plastic chairs from suppliers. This inconsistency can stem from varying production standards, the use of inferior materials, or lack of quality assurance protocols. For businesses in sectors such as hospitality or education, where durability and aesthetic appeal are paramount, receiving chairs that fail to meet specified quality standards can lead to significant operational disruptions and financial losses. Buyers may find themselves dealing with returns, damaged reputations, and unhappy clients, which can be particularly detrimental in competitive markets.
The Solution: To mitigate these risks, buyers should implement a rigorous supplier evaluation process. Start by requesting samples from multiple suppliers and conducting thorough inspections for durability, finish, and comfort. Establish clear quality specifications and require suppliers to adhere to them. It’s also beneficial to visit manufacturing facilities when feasible, or to engage third-party quality assurance services to oversee production runs. Developing a strong relationship with suppliers can facilitate better communication regarding expectations and quality control, ensuring that the products received consistently meet the desired standards.
Scenario 2: Navigating Import Regulations for Plastic Chairs
The Problem: International B2B buyers often struggle with complex import regulations and tariffs when sourcing plastic chairs from overseas suppliers. These regulations can vary significantly by region, leading to unexpected delays, increased costs, and potential legal issues. For instance, a buyer in South America may encounter stringent environmental regulations affecting the import of certain plastic materials, while a buyer in Europe might face high tariffs on non-EU manufactured products. This uncertainty can create significant challenges in planning and budgeting for procurement.
The Solution: To navigate these complexities, buyers should invest time in understanding the import regulations specific to their region. Engaging a logistics partner or customs broker with expertise in furniture imports can provide invaluable guidance. Additionally, consider sourcing from suppliers who are familiar with international shipping and compliance requirements. They can assist in ensuring that all necessary documentation is prepared and that products meet local regulations, thus minimizing the risk of delays or fines. Establishing a comprehensive logistics plan that includes contingency strategies can also help manage potential disruptions in the supply chain.
Scenario 3: Limited Customization Options from Suppliers
The Problem: Many B2B buyers find themselves frustrated by the limited customization options available from plastic chair suppliers. This is particularly problematic for businesses looking to create a unique brand identity or accommodate specific design needs. For instance, an event planner may require chairs in specific colors or designs that align with a client’s branding, but many suppliers offer a one-size-fits-all approach. This can hinder creativity and result in missed opportunities to enhance the customer experience.
The Solution: To address this challenge, buyers should proactively seek out suppliers that specialize in customizable solutions. When engaging with potential suppliers, inquire about their capabilities in terms of color matching, logo printing, and design modifications. It’s also beneficial to collaborate with manufacturers that have a proven track record in customization, as they are more likely to understand the nuances of bespoke orders. Finally, consider forming partnerships with local artisans or small-scale manufacturers who may be more flexible in accommodating unique requests, thus providing a competitive edge in the market.
Strategic Material Selection Guide for plastic chair supplier
What Are the Key Properties of Common Materials Used in Plastic Chairs?
When selecting materials for plastic chairs, international B2B buyers must consider several factors, including durability, cost, and compliance with local standards. Here, we analyze four common materials used in the production of plastic chairs: Polypropylene (PP), Polyethylene (PE), Polycarbonate (PC), and Acrylonitrile Butadiene Styrene (ABS).
How Does Polypropylene (PP) Perform in Plastic Chair Manufacturing?
Polypropylene is a widely used thermoplastic known for its versatility and resistance to various chemicals. It has a temperature rating of up to 100°C, making it suitable for indoor and outdoor applications.
Pros: Polypropylene is lightweight, durable, and resistant to moisture, which makes it ideal for outdoor furniture. It is also cost-effective, allowing manufacturers to produce affordable chairs.
Cons: However, it has lower UV resistance compared to other materials, which may lead to fading over time if exposed to direct sunlight. Additionally, it can become brittle at lower temperatures.
Impact on Application: PP is compatible with various media, such as water and mild chemicals, but may not perform well in extreme environments.
Considerations for International Buyers: Buyers from regions like Africa and South America should ensure compliance with local standards, such as ASTM and ISO, particularly regarding UV resistance for outdoor use.
What Are the Advantages of Polyethylene (PE) in Chair Production?
Polyethylene is another common thermoplastic used in chair manufacturing. It boasts excellent impact resistance and can withstand temperatures ranging from -50°C to 80°C.
Pros: Its durability and resistance to moisture make it suitable for both indoor and outdoor applications. PE is also recyclable, appealing to environmentally conscious buyers.
Cons: On the downside, PE can be more expensive than PP and may not be as rigid, which could affect the structural integrity of the chair under heavy loads.
Impact on Application: PE is well-suited for environments where moisture is prevalent, such as poolside areas.
Considerations for International Buyers: Buyers in the Middle East should check for compliance with local regulations regarding recyclability and environmental impact.
Why Choose Polycarbonate (PC) for High-End Plastic Chairs?
Polycarbonate is a high-performance thermoplastic with exceptional clarity and strength, often used in premium chair designs. It can withstand temperatures up to 120°C.
Pros: Its high impact resistance makes it an excellent choice for high-traffic areas. Additionally, PC offers excellent UV resistance, ensuring longevity even in outdoor settings.
Cons: However, PC is more expensive than other plastics and can be prone to scratching, which may require additional coatings or treatments.
Impact on Application: PC is ideal for applications requiring transparency, such as modern designs where aesthetics are crucial.
Considerations for International Buyers: Buyers in Europe should consider compliance with EU regulations on chemical safety, especially if the chairs are to be used in public spaces.
What Are the Limitations of Acrylonitrile Butadiene Styrene (ABS) in Chair Design?
ABS is a tough thermoplastic known for its impact resistance and ease of manufacturing. It can handle temperatures up to 80°C.
Pros: Its robustness makes it suitable for various applications, and it can be easily molded into complex shapes, allowing for innovative chair designs.
Cons: However, ABS can be less resistant to UV light, leading to color fading and reduced durability when exposed to sunlight.
Impact on Application: ABS is suitable for indoor use and environments where aesthetic appeal is essential.
Considerations for International Buyers: Buyers from South America should ensure that ABS products meet local safety and quality standards.
Summary Table of Material Selection for Plastic Chairs
Material | Typical Use Case for plastic chair supplier | Key Advantage | Key Disadvantage/Limitation | Relative Cost (Low/Med/High) |
---|---|---|---|---|
Polypropylene (PP) | Outdoor and indoor furniture | Lightweight and cost-effective | Lower UV resistance | Low |
Polyethylene (PE) | Poolside and outdoor applications | Excellent moisture resistance | More expensive than PP | Medium |
Polycarbonate (PC) | High-end, modern chair designs | High impact resistance and UV stability | Higher cost and prone to scratching | High |
Acrylonitrile Butadiene Styrene (ABS) | Indoor furniture and aesthetic designs | Tough and easy to mold | Less UV resistance | Medium |
This material selection guide provides valuable insights for international B2B buyers, enabling them to make informed decisions based on performance, cost, and compliance with local standards.
In-depth Look: Manufacturing Processes and Quality Assurance for plastic chair supplier
What Are the Key Manufacturing Processes for Plastic Chair Suppliers?
Manufacturing plastic chairs involves several critical stages that ensure the final product meets both aesthetic and functional requirements. Understanding these processes is essential for international B2B buyers looking to source quality products.
Material Preparation: How Are Raw Materials Sourced and Processed?
The first step in manufacturing plastic chairs is the preparation of raw materials. Typically, high-density polyethylene (HDPE) or polypropylene (PP) are used due to their durability and resistance to UV light and chemicals. Suppliers usually procure these materials from reputable manufacturers, ensuring that they meet international standards.
Once the raw materials are sourced, they undergo processes such as drying and granulation. This step ensures that the materials are free of moisture and contaminants, which can adversely affect the quality of the final product. B2B buyers should inquire about the suppliers’ sourcing practices and whether they perform quality checks on raw materials.
How Are Plastic Chairs Formed?
The actual forming of plastic chairs can be achieved through various techniques, including injection molding, blow molding, and rotational molding.
- Injection Molding: This is the most common method, where molten plastic is injected into a mold under high pressure. It allows for intricate designs and high precision.
- Blow Molding: Typically used for hollow components, this technique involves inflating molten plastic within a mold to create lightweight structures.
- Rotational Molding: This method is used for larger, hollow items and involves rotating a mold filled with plastic powder to ensure even coating.
Each technique has its advantages, and the choice depends on the design complexity and volume of production. Buyers should ask suppliers about the specific techniques they use and how these impact the chair’s design and durability.
What Are the Assembly and Finishing Steps?
After forming, the chairs go through an assembly process, where components like legs, seats, and backrests are joined together. This may involve mechanical fastening or welding, depending on the design.
Finishing processes include surface treatments, painting, and applying UV-resistant coatings to enhance durability. B2B buyers should inquire about the finishing techniques used, as these directly affect the aesthetic appeal and longevity of the chairs.
What Quality Assurance Measures Should B2B Buyers Expect?
Quality assurance (QA) is integral to the manufacturing process, ensuring that the final products meet international standards and customer expectations.
Which International Standards Are Relevant to Plastic Chair Manufacturing?
International standards such as ISO 9001 are crucial for quality management systems. This certification indicates that the manufacturer has established processes to ensure consistent quality. Additionally, specific certifications like CE (European Conformity) and API (American Petroleum Institute) can be relevant depending on the chair’s intended use.
B2B buyers should verify whether the supplier holds these certifications and understand the implications for product quality and safety.
How Is Quality Control Implemented During Manufacturing?
Quality control (QC) checkpoints are essential in the manufacturing process. These typically include:
- Incoming Quality Control (IQC): This step involves inspecting raw materials for compliance with specifications before they are used in production.
- In-Process Quality Control (IPQC): During manufacturing, random samples are taken to ensure that production processes are being followed correctly.
- Final Quality Control (FQC): Once the chairs are assembled, they undergo final inspections to check for defects and ensure they meet design specifications.
International B2B buyers should request information on these QC processes and any relevant documentation to support claims of product quality.
What Testing Methods Are Commonly Used in Plastic Chair Manufacturing?
Testing methods are varied and depend on the intended use of the chairs. Common testing methods include:
- Mechanical Testing: Assessing strength, durability, and load-bearing capabilities.
- Environmental Testing: Evaluating resistance to UV light, temperature fluctuations, and moisture.
- Safety Testing: Ensuring compliance with safety regulations applicable to the end-use environment.
B2B buyers should inquire about the specific tests conducted on their products and request test reports to verify compliance with international standards.
How Can B2B Buyers Verify Supplier Quality Control?
B2B buyers must perform due diligence to ensure that suppliers adhere to quality standards. This can be achieved through:
- Supplier Audits: Conducting on-site audits to assess manufacturing processes and quality control measures.
- Reviewing Quality Reports: Requesting access to quality assurance documentation, including audit reports and testing certifications.
- Third-Party Inspections: Engaging third-party inspection services to evaluate the manufacturing process and product quality independently.
By implementing these strategies, buyers can mitigate risks associated with quality and ensure that they source reliable products from their suppliers.
What Are the Nuances of Quality Certification for International Buyers?
When sourcing plastic chairs from suppliers in regions like Africa, South America, the Middle East, and Europe, buyers must be aware of the nuances in quality certifications. Some regions may have different compliance requirements, which can affect product acceptance in target markets.
Understanding the local regulatory landscape and how it aligns with international standards is crucial. Buyers should engage suppliers in discussions about their compliance with both local and international quality standards to ensure seamless market entry.
Conclusion
Understanding the manufacturing processes and quality assurance measures in the plastic chair supply chain is crucial for international B2B buyers. By asking the right questions and verifying certifications, buyers can make informed decisions that align with their quality expectations and business needs.
Practical Sourcing Guide: A Step-by-Step Checklist for ‘plastic chair supplier’
In the dynamic world of international trade, sourcing plastic chairs for your business can be a complex yet rewarding task. This practical sourcing guide provides a structured checklist to help international B2B buyers, especially those from Africa, South America, the Middle East, and Europe, navigate the procurement process effectively.
Step 1: Define Your Technical Specifications
Clearly outline what you need. Before reaching out to suppliers, define the technical specifications for the plastic chairs you require. Consider aspects such as size, weight capacity, material quality, and design features. This clarity will help you communicate effectively with potential suppliers and ensure they can meet your needs.
- Consider end-use: Are these chairs for outdoor or indoor use? This can influence the type of plastic and durability required.
- Customization needs: Will you require custom colors or branding options?
Step 2: Research Potential Suppliers
Conduct thorough research on suppliers. Utilize online marketplaces, industry directories, and trade shows to identify potential suppliers. Look for companies with a proven track record in manufacturing plastic chairs and positive reviews from previous clients.
- Check online reviews: Sites like Alibaba and Global Sources can provide insights into supplier reliability.
- Industry reputation: Engage with industry forums or LinkedIn groups to gather opinions on potential suppliers.
Step 3: Evaluate Supplier Certifications
Ensure suppliers meet industry standards. Verify that potential suppliers hold relevant certifications, such as ISO 9001 for quality management systems or environmental certifications like ISO 14001. These certifications indicate adherence to industry standards and practices.
- Quality assurance: Certifications can assure you of consistent product quality.
- Compliance with regulations: Ensure that the supplier complies with local regulations regarding materials and safety standards.
Step 4: Request Samples
Always ask for product samples. Before making a significant investment, request samples of the plastic chairs. This step allows you to evaluate the quality, comfort, and design firsthand.
- Assess durability: Test the samples for stability and resistance to wear and tear.
- User feedback: If possible, gather feedback from your team or potential customers on the comfort and usability of the chairs.
Step 5: Negotiate Pricing and Payment Terms
Engage in transparent negotiations. Once you have selected a few potential suppliers, negotiate pricing and payment terms. Be clear about your budget but remain open to discussions on volume discounts or payment plans.
- Consider total cost: Factor in shipping, taxes, and potential duties to understand the total cost of procurement.
- Payment security: Discuss payment methods that offer security, such as letters of credit or escrow services.
Step 6: Review Logistics and Delivery Options
Understand the logistics involved. Discuss shipping methods, lead times, and delivery options with your selected supplier. Ensure they can meet your timelines and have reliable shipping practices.
- Shipping partners: Inquire about their logistics partners and their track record for on-time delivery.
- Customs clearance: Understand any customs requirements or additional costs that may arise during importation.
Step 7: Establish a Communication Plan
Maintain open lines of communication. Effective communication is vital throughout the sourcing process. Establish a plan for regular updates and check-ins with your supplier to address any issues promptly.
- Point of contact: Designate a primary contact person for both your team and the supplier.
- Feedback loop: Create a system for providing feedback on product quality and service, which can help improve future transactions.
By following this checklist, international B2B buyers can streamline their sourcing process for plastic chairs, ensuring they partner with reliable suppliers who meet their specific needs. This proactive approach not only enhances product quality but also fosters long-term business relationships.
Comprehensive Cost and Pricing Analysis for plastic chair supplier Sourcing
When sourcing plastic chairs, understanding the comprehensive cost structure is essential for international B2B buyers, particularly those from Africa, South America, the Middle East, and Europe. The cost of procurement can significantly impact the overall purchasing decision, and it is crucial to consider various components that contribute to the final pricing.
What Are the Main Cost Components in Plastic Chair Sourcing?
-
Materials: The primary cost component for plastic chairs is the raw materials, typically polypropylene or polyethylene. Prices can fluctuate based on global oil prices, availability, and supplier relationships. Buyers should seek suppliers that offer competitive material pricing without compromising quality.
-
Labor: Labor costs are influenced by the manufacturing location. Countries with lower labor costs may offer more attractive pricing but could compromise on quality or lead times. Understanding the local labor market is vital for evaluating quotes from different suppliers.
-
Manufacturing Overhead: This includes costs associated with utilities, maintenance, and factory management. Buyers should inquire about how these costs are calculated and consider their impact on the overall price.
-
Tooling: If custom designs or specific molds are required, tooling costs can be significant. Buyers should assess whether these costs are included in the quoted price or if they will be charged separately, especially for low-volume orders.
-
Quality Control (QC): Ensuring product quality is paramount, especially for international shipments. Suppliers may charge extra for stringent QC processes. Buyers should ask for certifications and quality assurance measures to mitigate the risk of defects.
-
Logistics: Shipping and handling costs can vary widely based on distance, shipping method, and Incoterms used. Understanding the logistics involved, including duties and taxes, is crucial for calculating the total cost.
-
Margin: Suppliers typically add a profit margin to their costs. This can vary depending on market demand, supplier reputation, and service level provided. Buyers should compare multiple suppliers to identify a reasonable margin.
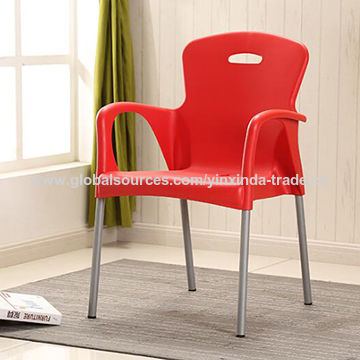
A stock image related to plastic chair supplier.
How Do Price Influencers Affect Plastic Chair Sourcing?
Several factors can influence the pricing of plastic chairs:
-
Volume and Minimum Order Quantity (MOQ): Higher order volumes often lead to lower per-unit costs. Buyers should negotiate MOQs that align with their needs to optimize pricing.
-
Specifications and Customization: Custom designs or specifications can significantly increase costs. Buyers should evaluate whether customization is necessary or if standard designs suffice.
-
Material Quality and Certifications: Higher quality materials or certifications (e.g., ISO, FDA) can increase costs but may be worth the investment for durability and compliance, particularly in regulated markets.
-
Supplier Factors: The reputation and reliability of the supplier can affect pricing. Established suppliers may charge more due to their proven track record, while new entrants may offer lower prices to gain market share.
-
Incoterms: The agreed-upon Incoterms can influence costs related to shipping responsibilities. Understanding who bears the cost of shipping and insurance is critical for total cost calculations.
What Are the Best Buyer Tips for Cost-Efficient Sourcing?
-
Negotiate Effectively: Leverage multiple quotes and be prepared to negotiate terms. Understanding market prices and having alternative suppliers can strengthen your bargaining position.
-
Focus on Total Cost of Ownership (TCO): Assess not only the purchase price but also long-term costs such as maintenance, warranty, and disposal. A higher initial cost may lead to lower TCO if the product is more durable.
-
Be Aware of Pricing Nuances: International buyers should consider currency fluctuations and payment terms, as these can affect final costs. Establishing clear payment terms can help mitigate financial risks.
-
Conduct Due Diligence: Research suppliers thoroughly. Reviews, references, and site visits can provide insights into supplier reliability and product quality.
By considering these factors and tips, B2B buyers can make informed decisions when sourcing plastic chairs, ensuring they achieve the best possible value while meeting their business needs.
Disclaimer: The prices mentioned in this analysis are indicative and may vary based on market conditions, supplier negotiations, and specific order requirements.
Alternatives Analysis: Comparing plastic chair supplier With Other Solutions
Introduction: Why Consider Alternatives to Plastic Chair Suppliers?
When sourcing seating solutions for commercial or institutional use, B2B buyers often consider a variety of options to meet their specific needs. While plastic chairs are popular due to their durability and versatility, exploring alternatives can reveal options that might better align with budget constraints, aesthetic preferences, or sustainability goals. This analysis will compare plastic chair suppliers against two viable alternatives: metal chairs and sustainable wooden chairs.
Comparison Table: Key Aspects of Plastic Chair Suppliers vs. Alternatives
Comparison Aspect | Plastic Chair Supplier | Metal Chair Supplier | Sustainable Wooden Chair Supplier |
---|---|---|---|
Performance | Durable, lightweight, weather-resistant | Sturdy, can be heavier, durable | Strong, can be less weather-resistant |
Cost | Generally low-cost | Moderate to high cost | Moderate to high cost |
Ease of Implementation | Easy to transport and set up | Requires more effort to transport | Moderate; often requires assembly |
Maintenance | Low maintenance needs | Moderate maintenance | Higher maintenance due to wood care |
Best Use Case | Ideal for casual settings and outdoor use | Suitable for industrial and heavy-use environments | Perfect for upscale or eco-conscious settings |
Detailed Breakdown of Alternatives
What Are the Advantages and Disadvantages of Metal Chairs?
Metal chairs are known for their strength and durability, making them suitable for high-traffic environments such as cafes, restaurants, and industrial settings. They often feature a sleek design that complements modern aesthetics. However, they can be heavier and more difficult to move compared to plastic options, which may present logistical challenges in certain settings. Additionally, metal chairs can become hot or cold depending on the weather, potentially affecting comfort levels.
How Do Sustainable Wooden Chairs Compare?
Sustainable wooden chairs offer an eco-friendly alternative that appeals to businesses focused on sustainability and aesthetics. These chairs can provide a warm, inviting look that enhances the ambiance of dining or meeting spaces. However, they typically come at a higher price point and require more maintenance than both plastic and metal options, as wood needs to be treated and cared for to avoid damage from moisture and wear. Furthermore, the weight of wooden chairs can complicate transportation and setup.
Conclusion: How Should B2B Buyers Choose the Right Seating Solution?
When selecting the right seating solution, B2B buyers should carefully assess their specific needs, including budget, intended use, and maintenance capabilities. Plastic chairs can offer a cost-effective and low-maintenance solution, ideal for casual or outdoor settings. In contrast, metal chairs provide durability for more demanding environments, while sustainable wooden chairs cater to businesses emphasizing eco-friendliness and design aesthetics. Ultimately, the choice hinges on aligning the seating solution with operational goals, ensuring both functionality and style in the intended environment.
Essential Technical Properties and Trade Terminology for plastic chair supplier
What Are the Essential Technical Properties of Plastic Chairs for B2B Buyers?
When sourcing plastic chairs, understanding the technical properties is crucial for ensuring product quality and suitability for your needs. Here are some key specifications to consider:
1. Material Grade: Which Plastic Should You Choose?
Plastic chairs are typically made from various materials, including polypropylene, polyethylene, and polycarbonate. Each material has unique properties affecting durability, UV resistance, and flexibility. For instance, polypropylene is lightweight and resistant to chemicals, making it ideal for outdoor use. B2B buyers should evaluate the intended use of the chairs to select the appropriate material grade.
2. Weight Capacity: How Much Load Can the Chair Handle?
The weight capacity of a plastic chair is a critical specification that determines its strength and durability. Most commercial-grade chairs can support between 250 to 500 pounds, depending on the design and material. Buyers need to ensure that the chairs meet the expected load requirements for their specific applications, especially in environments like cafes or event venues.
3. Tolerance: What Is the Importance of Dimensional Accuracy?
Tolerance refers to the allowable variation in dimensions during the manufacturing process. For plastic chairs, maintaining strict tolerances is essential to ensure uniformity and functionality. A well-manufactured chair will fit seamlessly with other furniture and components. Buyers should inquire about the manufacturer’s tolerance standards to avoid issues with assembly or compatibility.
4. Resistance to Weather Conditions: Will the Chairs Survive the Elements?
Plastic chairs should have resistance to various environmental conditions, including UV radiation, moisture, and temperature fluctuations. UV-resistant materials prevent fading and degradation from sunlight, while moisture resistance is vital for outdoor use. Understanding the environmental resilience of the chairs can help buyers choose products that will last longer, reducing replacement costs.
5. Surface Finish: Why Does It Matter?
The surface finish of a plastic chair affects not only aesthetics but also usability and maintenance. Options may include matte, glossy, or textured finishes, each offering different advantages in terms of grip and ease of cleaning. Buyers should consider the chair’s application—chairs in high-traffic areas may require finishes that are more resistant to scratches and stains.
What Trade Terminology Should B2B Buyers Know When Sourcing Plastic Chairs?
Navigating the world of B2B procurement involves understanding specific industry terminology. Here are some essential terms related to sourcing plastic chairs:
1. OEM (Original Equipment Manufacturer): What Does It Mean for Your Purchase?
OEM refers to companies that manufacture products that are then marketed under another company’s brand. In the context of plastic chairs, working with an OEM can provide customization options and potentially lower costs for bulk orders. B2B buyers should consider OEMs for tailored solutions that meet their specific requirements.
2. MOQ (Minimum Order Quantity): How Much Should You Order?
MOQ is the smallest quantity of a product that a supplier is willing to sell. Understanding MOQ is crucial for budgeting and inventory management. Buyers should negotiate MOQs based on their needs and explore suppliers that offer flexible options to avoid overstocking or underordering.
3. RFQ (Request for Quotation): How to Get the Best Price?
An RFQ is a document issued by a buyer to solicit price quotes from suppliers. It typically includes product specifications, quantities, and delivery requirements. B2B buyers should use RFQs to compare pricing and terms from multiple suppliers, ensuring they get the best deal for their purchases.
4. Incoterms (International Commercial Terms): What Are They?
Incoterms are a set of predefined international trade terms used to clarify the responsibilities of buyers and sellers. Understanding Incoterms is essential for managing shipping costs and risks. For example, terms like FOB (Free On Board) specify when the responsibility for the goods transfers from the seller to the buyer, impacting pricing and logistics.
By familiarizing yourself with these technical properties and trade terms, you can make informed decisions when sourcing plastic chairs, ultimately leading to better procurement outcomes for your business.
Navigating Market Dynamics and Sourcing Trends in the plastic chair supplier Sector
What Are the Current Market Dynamics and Key Trends in the Plastic Chair Supplier Sector?
The global plastic chair supplier market is experiencing significant transformations driven by several factors. Rapid urbanization and an increasing focus on outdoor and commercial spaces are propelling demand for versatile and durable seating solutions. International B2B buyers, particularly from Africa, South America, the Middle East, and Europe, are increasingly seeking suppliers that offer innovative designs and functional products. The rise of e-commerce platforms is reshaping sourcing strategies, enabling buyers to connect directly with manufacturers and streamlining the procurement process.
Additionally, technology is playing a pivotal role in the sector. Automation in manufacturing processes enhances efficiency and reduces lead times, while digital design tools allow for customization and rapid prototyping. Buyers are advised to leverage online marketplaces and supplier directories that feature verified reviews and ratings to identify reliable partners. Understanding regional preferences and market nuances is essential; for instance, color and design trends can vary significantly between cultures.
How Is Sustainability and Ethical Sourcing Influencing B2B Buying Decisions?
Sustainability is no longer just a buzzword; it has become a critical criterion in the B2B purchasing process. Buyers are increasingly aware of the environmental impact associated with plastic products, pushing suppliers to adopt sustainable practices. The importance of ethical supply chains cannot be overstated, as consumers globally demand transparency and accountability from businesses. Suppliers who can demonstrate adherence to environmental regulations and ethical labor practices are more likely to gain favor with discerning buyers.
Moreover, certifications such as ISO 14001 (Environmental Management) and FSC (Forest Stewardship Council) can enhance a supplier’s credibility. Utilizing recycled materials in production and offering eco-friendly alternatives not only reduces environmental footprints but also appeals to the growing segment of eco-conscious consumers. For international buyers, it is advisable to prioritize suppliers who provide clear documentation regarding their sustainability practices and material sourcing.
What Is the Historical Context Behind the Plastic Chair Supplier Market?
The evolution of the plastic chair supplier market can be traced back to the mid-20th century when advancements in polymer technology made plastic a viable material for furniture production. Initially popularized by iconic designs in the 1960s, plastic chairs became synonymous with affordability and versatility. Over the decades, the sector has seen a shift towards more sophisticated designs and improved manufacturing techniques, allowing for greater aesthetic appeal and functionality.
This historical context is essential for B2B buyers as it highlights the ongoing innovation within the industry. As the market continues to evolve, staying informed about historical trends can help buyers anticipate future developments and make informed sourcing decisions.
Frequently Asked Questions (FAQs) for B2B Buyers of plastic chair supplier
-
How do I choose the right plastic chair supplier for my business needs?
Selecting the right plastic chair supplier involves evaluating their product range, quality, and reliability. Start by researching suppliers that specialize in the types of chairs you need, whether for office, event, or outdoor use. Look for reviews and testimonials from other B2B buyers, and consider requesting samples to assess quality firsthand. Additionally, check their certifications and compliance with international standards to ensure they meet your requirements. -
What customization options are available when sourcing plastic chairs?
Many plastic chair suppliers offer customization options such as color, size, and branding. When discussing your needs, inquire about the possibility of custom designs that align with your brand identity. Additionally, ask if they can accommodate specific ergonomic features or materials that enhance comfort and durability. Establishing clear communication about your requirements will help ensure the final product meets your expectations. -
What are the minimum order quantities (MOQ) for plastic chairs?
Minimum order quantities can vary significantly between suppliers. Generally, MOQs for plastic chairs range from 50 to 500 units, depending on the supplier’s production capacity and the complexity of your order. It’s essential to clarify MOQs during initial discussions to avoid misunderstandings later. Some suppliers may offer flexibility for first-time buyers or smaller companies, so don’t hesitate to negotiate. -
What payment terms should I expect from plastic chair suppliers?
Payment terms can differ widely among suppliers. Common practices include a deposit upfront (often 30-50%) with the balance due upon delivery or a letter of credit. It’s crucial to discuss payment methods that align with your financial capabilities and risk tolerance. Ensure you understand the implications of each payment option and confirm that the supplier is willing to accommodate your preferred terms. -
How can I ensure quality assurance when sourcing plastic chairs internationally?
To ensure quality assurance, request detailed specifications and certifications from the supplier. Implement a quality control process that includes pre-production samples and in-process inspections. Consider hiring third-party inspection services to conduct quality checks before shipment. Establishing a clear agreement on quality standards in your contract can also safeguard your interests. -
What logistics considerations should I keep in mind when importing plastic chairs?
Logistics plays a vital role in international sourcing. Evaluate shipping options, including freight forwarders, to determine the most cost-effective and timely methods for transporting your chairs. Be aware of customs regulations and duties applicable to your shipment, which can impact your overall costs. Planning for potential delays and having contingency plans can help mitigate risks associated with logistics. -
How do I handle disputes with my plastic chair supplier?
Disputes can arise in any business transaction. To handle them effectively, maintain open lines of communication and document all agreements and discussions. If issues arise, first attempt to resolve them amicably through negotiation. Should this fail, refer to the contract terms regarding dispute resolution, which may include mediation or arbitration. Having a clear process in place can help protect your interests and foster a better working relationship. -
What are the trends in the plastic chair market that I should be aware of?
The plastic chair market is currently seeing trends such as eco-friendly materials and ergonomic designs gaining popularity. Suppliers are increasingly offering sustainable options made from recycled plastics, appealing to environmentally conscious consumers. Additionally, multi-functional chairs that cater to both indoor and outdoor use are becoming more sought after. Staying informed about these trends can help you make strategic sourcing decisions that resonate with your target audience.
Important Disclaimer & Terms of Use
⚠️ Important Disclaimer
The information provided in this guide, including content regarding manufacturers, technical specifications, and market analysis, is for informational and educational purposes only. It does not constitute professional procurement advice, financial advice, or legal advice.
While we have made every effort to ensure the accuracy and timeliness of the information, we are not responsible for any errors, omissions, or outdated information. Market conditions, company details, and technical standards are subject to change.
B2B buyers must conduct their own independent and thorough due diligence before making any purchasing decisions. This includes contacting suppliers directly, verifying certifications, requesting samples, and seeking professional consultation. The risk of relying on any information in this guide is borne solely by the reader.
Strategic Sourcing Conclusion and Outlook for plastic chair supplier
Why Is Strategic Sourcing Essential for Plastic Chair Suppliers?
In the dynamic landscape of international trade, strategic sourcing stands out as a critical factor for B2B buyers, particularly in the plastic chair market. By leveraging strategic sourcing practices, buyers can enhance their procurement efficiency, reduce costs, and ensure quality compliance. The insights gained from understanding supplier capabilities and market trends empower organizations to make informed decisions that align with their operational goals.
What Are the Key Takeaways for International Buyers?
For buyers in regions such as Africa, South America, the Middle East, and Europe, the emphasis should be on building strong relationships with suppliers who understand local market nuances. Prioritizing suppliers that offer flexibility in production and customization can significantly enhance value. Moreover, engaging in collaborative forecasting and planning can lead to better inventory management and timely delivery, ensuring that your business remains competitive.
What’s Next for B2B Buyers in the Plastic Chair Sector?
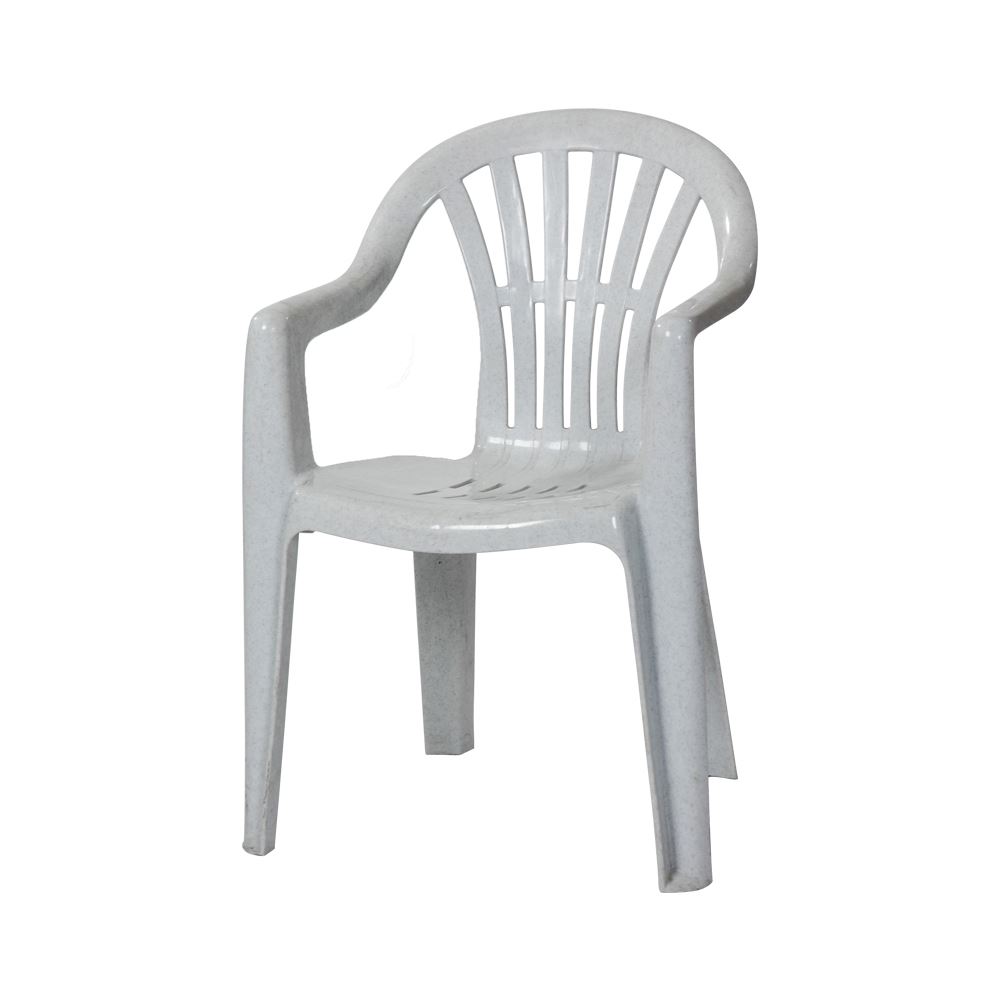
A stock image related to plastic chair supplier.
As the global market continues to evolve, staying ahead of emerging trends and sustainable practices will be paramount. International buyers are encouraged to actively seek suppliers committed to innovation and environmental responsibility. By integrating these practices into your sourcing strategy, you can not only improve your supply chain resilience but also contribute positively to the environment. Now is the time to take action—explore new supplier partnerships and refine your sourcing strategies to position your business for future success.