Discover Top Safety Gear Suppliers: Your Complete Guide (2025)
Introduction: Navigating the Global Market for safety gear supplier
In today’s global market, sourcing safety gear suppliers poses a significant challenge for international B2B buyers, especially those operating in regions such as Africa, South America, the Middle East, and Europe. The need for high-quality, compliant, and cost-effective safety gear is paramount, as businesses strive to maintain workplace safety while adhering to increasingly stringent regulations. This guide aims to navigate the complexities of the safety gear supply chain, providing insights into various types of safety gear, their applications, and the critical considerations for supplier vetting.
Understanding the nuances of safety gear procurement is vital for ensuring compliance with local and international occupational safety and health (OSH) standards. By delving into supplier qualifications, product certifications, and pricing strategies, this guide empowers B2B buyers to make informed purchasing decisions. From personal protective equipment (PPE) for construction workers in South Africa to specialized safety gear for industrial operations in the UAE, we cover a comprehensive range of topics tailored to meet the diverse needs of buyers across different sectors.
Through actionable insights and expert recommendations, this guide not only facilitates better procurement strategies but also enhances workplace safety and operational efficiency. It serves as a valuable resource for organizations committed to fostering a culture of safety and compliance, ultimately contributing to business continuity and employee well-being in the global marketplace.
Understanding safety gear supplier Types and Variations
Type Name | Key Distinguishing Features | Primary B2B Applications | Brief Pros & Cons for Buyers |
---|---|---|---|
Personal Protective Equipment (PPE) Suppliers | Focused on individual safety gear like helmets, gloves, and masks. | Construction, manufacturing, healthcare. | Pros: High compliance with safety standards. Cons: Can be costly, requiring bulk purchases. |
Industrial Safety Equipment Suppliers | Provides heavy-duty safety gear designed for industrial environments. | Oil and gas, mining, heavy manufacturing. | Pros: Durable and reliable for extreme conditions. Cons: May lack customization options. |
Safety Consulting and Training Providers | Offer expertise in safety protocols and training programs. | Corporate safety audits, compliance training. | Pros: Enhances workplace safety culture. Cons: Ongoing costs for training programs. |
Safety Gear Rental Services | Provides temporary safety gear solutions for short-term projects. | Events, construction projects, emergency services. | Pros: Cost-effective for short-term needs. Cons: Limited availability of specific gear. |
Wholesale Safety Gear Distributors | Focused on bulk sales of various safety equipment brands. | Retailers, contractors, government agencies. | Pros: Competitive pricing for bulk purchases. Cons: Less personalized service. |
What Are the Characteristics of Personal Protective Equipment (PPE) Suppliers?
Personal Protective Equipment (PPE) suppliers specialize in providing individual safety gear, including helmets, gloves, and respiratory masks. These suppliers often comply with strict safety standards and regulations, making them suitable for industries such as construction, manufacturing, and healthcare. When purchasing from PPE suppliers, B2B buyers should consider factors like product certifications, the range of available sizes, and the supplier‘s reputation for quality.
How Do Industrial Safety Equipment Suppliers Differ?
Industrial safety equipment suppliers focus on heavy-duty safety gear designed for extreme industrial environments, such as the oil and gas sector, mining, and heavy manufacturing. Their products often include specialized items like flame-resistant clothing and heavy-duty helmets. B2B buyers should evaluate the durability, compliance with industry-specific standards, and the supplier’s ability to provide customized solutions for unique operational hazards.
What Benefits Do Safety Consulting and Training Providers Offer?
Safety consulting and training providers offer expert guidance on workplace safety protocols and compliance training. They are crucial for organizations looking to enhance their safety culture and ensure adherence to local regulations. B2B buyers should consider the provider’s experience, the comprehensiveness of training programs, and the potential for long-term partnerships to foster a safer work environment.
When Should Businesses Consider Safety Gear Rental Services?
Safety gear rental services are ideal for companies that require temporary safety solutions for short-term projects, such as events or construction undertakings. These suppliers can provide a wide range of equipment without the need for significant upfront investment. B2B buyers should assess the availability of specific gear, rental terms, and the condition of equipment to ensure safety and compliance.
What Are the Advantages of Wholesale Safety Gear Distributors?
Wholesale safety gear distributors focus on bulk sales of various safety equipment brands, making them a preferred choice for retailers, contractors, and government agencies. They typically offer competitive pricing, which can significantly reduce costs for bulk purchases. However, B2B buyers should be aware that these distributors may provide less personalized service compared to smaller suppliers, making it essential to establish clear communication regarding specific needs.
Related Video: Types of Personal Protective Equipment (PPE) – Safety Training
Key Industrial Applications of safety gear supplier
Industry/Sector | Specific Application of Safety Gear Supplier | Value/Benefit for the Business | Key Sourcing Considerations for this Application |
---|---|---|---|
Construction | Personal Protective Equipment (PPE) for workers | Reduces workplace accidents, ensuring compliance with safety regulations | Certifications, durability, and comfort of the gear |
Manufacturing | Industrial safety helmets and gloves | Enhances worker safety, reducing downtime due to injuries | Customization options and compliance with local regulations |
Oil and Gas | Fire-resistant clothing and respiratory protection | Protects workers from hazardous environments, minimizing liability | Resistance ratings and certifications for specific environments |
Mining | High-visibility clothing and safety footwear | Improves visibility in low-light conditions, preventing accidents | Material quality and adherence to industry safety standards |
Healthcare | Infection control gowns and face shields | Protects healthcare workers from biological hazards | Compliance with health regulations and comfort for long wear |
How is Safety Gear Used in Construction, and What Problems Does It Solve?
In the construction industry, safety gear suppliers provide essential Personal Protective Equipment (PPE) such as helmets, gloves, and high-visibility clothing. These items mitigate risks associated with heavy machinery, falling objects, and hazardous materials. For international buyers, particularly in regions like South Africa and the UAE, sourcing PPE that meets local safety standards and certifications is critical. Additionally, the durability and comfort of the gear are vital to encourage consistent usage among workers, thereby enhancing overall site safety.
What Role Does Safety Gear Play in Manufacturing?
In manufacturing, safety gear suppliers supply industrial safety helmets and gloves designed to protect workers from machinery-related injuries. These items are crucial for maintaining compliance with stringent safety regulations. B2B buyers from South America and Europe must consider customization options to fit the specific needs of their workforce, as well as the gear’s compliance with local regulations. Ensuring the comfort and usability of the gear can significantly reduce workplace accidents and enhance productivity.
Why is Safety Gear Crucial in the Oil and Gas Sector?
In the oil and gas industry, safety gear suppliers provide specialized fire-resistant clothing and respiratory protection to safeguard workers in high-risk environments. These products are essential for minimizing liability and ensuring compliance with occupational safety regulations. Buyers from the Middle East and Africa should prioritize sourcing gear with appropriate resistance ratings and certifications tailored to their operational environments. This focus not only protects employees but also enhances the company’s reputation for prioritizing safety.
How Does Visibility Gear Impact Safety in Mining?
Mining operations require high-visibility clothing and safety footwear to improve worker visibility in often low-light and hazardous conditions. Safety gear suppliers offer these products to significantly reduce the risk of accidents and injuries. For international buyers, especially in regions like South America and Africa, sourcing quality materials that meet industry safety standards is crucial. Understanding the specific requirements of the mining environment will help in selecting gear that ensures worker safety and compliance with regulations.
What Safety Gear is Essential in Healthcare Settings?
In healthcare, suppliers of safety gear provide infection control gowns and face shields to protect healthcare workers from biological hazards. This gear is essential for minimizing the risk of infection, particularly in the wake of global health crises. B2B buyers in Europe and the Middle East should focus on sourcing products that comply with health regulations while also ensuring comfort for extended wear. Investing in high-quality protective gear not only safeguards employees but also enhances patient care and trust in healthcare facilities.
Related Video: All Types Of Gear And Applications – 3D Animation
3 Common User Pain Points for ‘safety gear supplier’ & Their Solutions
Scenario 1: Sourcing Quality Safety Gear at Competitive Prices
The Problem: B2B buyers often struggle to find a reliable safety gear supplier that offers both quality products and competitive pricing. Many suppliers may provide low-cost options, but these often compromise on safety standards, leading to potential hazards for employees. Buyers from regions like South Africa or the Middle East face additional challenges due to varying local regulations and standards, making it even harder to identify suppliers who can meet their specific needs.
The Solution: To overcome this issue, buyers should conduct thorough research on potential suppliers by examining their certifications and compliance with international safety standards, such as ISO 45001. It is crucial to request product samples to evaluate quality before making bulk purchases. Additionally, buyers can leverage platforms like Alibaba or industry-specific trade shows to connect with multiple suppliers, allowing for price comparisons and negotiations. Establishing long-term relationships with suppliers who demonstrate reliability and quality can also lead to better pricing and service over time. Engaging in direct communication about safety requirements and local regulations can further enhance the collaboration.
Scenario 2: Navigating Compliance with Local Safety Regulations
The Problem: International B2B buyers often face difficulties in ensuring that the safety gear they procure aligns with local safety regulations. For instance, a buyer in Europe may be unaware of specific PPE requirements mandated by the EU’s Personal Protective Equipment Regulation. This oversight can lead to significant liabilities, including fines and workplace accidents, which can be detrimental to business operations and reputation.
The Solution: To effectively navigate compliance, it is essential for buyers to familiarize themselves with local regulations regarding safety gear in their target markets. Consulting local safety experts or legal advisors can provide insights into specific requirements. Buyers should also inquire with suppliers about their knowledge and adherence to these regulations. A proactive approach includes requesting documentation proving compliance, such as CE marking in Europe or SANS certification in South Africa. Regular training sessions for staff on compliance and proper use of safety gear will also ensure that safety standards are consistently met.
Scenario 3: Ensuring Proper Fit and Functionality of Safety Gear
The Problem: One common pain point for B2B buyers is ensuring that the safety gear purchased fits properly and functions effectively for their workforce. Ill-fitting gear can lead to discomfort, reduced productivity, and increased risk of accidents. Buyers from South America and the Middle East may find it particularly challenging to source gear that accommodates diverse body types and specific work environments.
The Solution: To address this challenge, buyers should prioritize suppliers that offer a range of sizes and customizable options for safety gear. Conducting a thorough needs assessment to understand the specific requirements of the workforce is vital. This can include taking measurements and involving employees in the selection process to ensure comfort and fit. Suppliers that provide fitting sessions or virtual try-on technologies can greatly enhance the buying experience. Additionally, implementing a return policy that allows for exchanges on poorly fitting items can mitigate the risk associated with bulk orders. Regular feedback from employees on the performance and comfort of the gear should be encouraged to make informed future purchases.
Strategic Material Selection Guide for safety gear supplier
When selecting materials for safety gear, international B2B buyers must consider various factors that influence product performance, compliance, and end-user satisfaction. Below are analyses of four common materials used in safety gear, focusing on their properties, advantages, disadvantages, and specific considerations for buyers from Africa, South America, the Middle East, and Europe.
What are the Key Properties of Polyethylene in Safety Gear?
Polyethylene (PE) is a widely used thermoplastic known for its lightweight and flexible nature. It offers good chemical resistance and can withstand temperatures up to 80°C (176°F). PE is often used in protective clothing, gloves, and helmets.
Pros & Cons:
The primary advantages of polyethylene include its low cost and ease of manufacturing, making it suitable for mass production. However, its durability can be a concern, especially in high-abrasion environments, as it may wear out faster compared to more robust materials.
Impact on Application:
Polyethylene is compatible with various chemicals, making it ideal for industries such as agriculture and food processing. However, it may not provide adequate protection against extreme temperatures or heavy impacts.
Considerations for International Buyers:
Buyers should ensure that the polyethylene products comply with relevant safety standards such as ASTM and ISO. In regions like South Africa and the UAE, understanding local regulations regarding chemical resistance and environmental impact is crucial.
How Does Nylon Perform as a Material for Safety Gear?
Nylon is a synthetic polymer known for its strength and elasticity. It can withstand temperatures up to 120°C (248°F) and is resistant to abrasion, making it a popular choice for protective clothing and gear.
Pros & Cons:
Nylon’s key advantage is its high durability and resistance to wear and tear, which is essential in heavy-duty applications. However, it can be more expensive than polyethylene and may require more complex manufacturing processes.
Impact on Application:
Due to its strength, nylon is suitable for applications requiring high tensile strength, such as harnesses and protective suits in construction and industrial sectors. However, its moisture absorption can lead to discomfort in humid conditions.
Considerations for International Buyers:
B2B buyers should verify compliance with international standards like EN and ANSI, especially in Europe and the Middle East, where safety regulations are stringent. Additionally, understanding the climate conditions in the target market can influence material selection.
What are the Benefits of Using Kevlar in Safety Gear?
Kevlar is a high-performance aramid fiber known for its exceptional strength-to-weight ratio and heat resistance, withstanding temperatures up to 400°C (752°F). It is commonly used in cut-resistant gloves and bulletproof vests.
Pros & Cons:
The primary advantage of Kevlar is its superior protection against cuts and impacts, making it ideal for high-risk environments. However, it comes at a higher cost and may require specialized manufacturing techniques, which can lead to longer lead times.
Impact on Application:
Kevlar is particularly effective in industries such as law enforcement, military, and construction, where high levels of protection are necessary. Its lightweight nature also enhances user comfort during prolonged use.
Considerations for International Buyers:
Buyers should ensure that Kevlar products meet specific standards such as NIJ for ballistic protection and EN 388 for cut resistance. Understanding the local market’s willingness to invest in high-quality safety gear is vital, especially in regions with varying economic conditions.
Why is Leather a Traditional Choice for Safety Gear?
Leather has been a traditional material in safety gear due to its durability and natural abrasion resistance. It can withstand high temperatures and is often used in gloves, aprons, and protective footwear.
Pros & Cons:
The main advantage of leather is its durability and comfort, providing excellent protection in various environments. However, it can be more expensive and may require more maintenance than synthetic materials.
Impact on Application:
Leather is suitable for industries such as welding and construction, where heat and abrasion resistance are critical. However, its performance can be compromised in wet conditions unless treated properly.
Considerations for International Buyers:
B2B buyers should consider the sourcing and treatment of leather, ensuring compliance with environmental regulations, especially in regions with strict animal welfare laws. Understanding local preferences for leather quality can also influence purchasing decisions.
Summary Table of Material Selection for Safety Gear
Material | Typical Use Case for Safety Gear Supplier | Key Advantage | Key Disadvantage/Limitation | Relative Cost (Low/Med/High) |
---|---|---|---|---|
Polyethylene | Protective clothing, gloves, helmets | Low cost, lightweight | Less durable in high-abrasion settings | Low |
Nylon | Protective suits, harnesses | High durability, abrasion resistance | Higher cost, complex manufacturing | Medium |
Kevlar | Cut-resistant gloves, bulletproof vests | Superior protection against cuts | High cost, specialized manufacturing | High |
Leather | Gloves, aprons, protective footwear | Durable, comfortable | Higher maintenance, expensive | Medium to High |
This strategic material selection guide provides a comprehensive overview of key materials used in safety gear, enabling international B2B buyers to make informed decisions based on their specific needs and market conditions.
In-depth Look: Manufacturing Processes and Quality Assurance for safety gear supplier
What Are the Key Stages in Manufacturing Safety Gear?
Manufacturing safety gear involves several critical stages that ensure the final product meets the required safety standards and performs effectively in various environments. The main stages of the manufacturing process include:
Material Preparation
The first step in manufacturing safety gear is sourcing high-quality raw materials. Depending on the type of gear, materials may include synthetic fibers, metals, rubber, and plastics. B2B buyers should ensure that suppliers provide documentation on the sourcing of materials, confirming compliance with international safety standards. For example, materials used for personal protective equipment (PPE) should meet standards such as ASTM or EN specifications.
Forming Techniques
Once the materials are prepared, the next stage is forming. This process can involve cutting, molding, or weaving the materials into the desired shapes. For instance, helmets may undergo injection molding, while gloves are typically made through a dipping process. Buyers should inquire about the techniques used and their efficiency, as this can impact both the quality and cost of the final product.
Assembly Processes
Assembly is where the individual components come together to create the final safety gear. This could involve sewing fabric components together or integrating hardware such as straps and buckles. It is vital for B2B buyers to understand the assembly techniques used by suppliers, as this can affect the durability and performance of the gear. Automation in assembly lines can improve consistency, but manual assembly might be necessary for complex products.
Finishing Touches
The finishing stage includes any final treatments or coatings that enhance the gear’s performance and appearance. This may involve applying flame retardants, anti-static treatments, or reflective coatings. B2B buyers should ask for details on the finishing processes to ensure that they meet the specific safety requirements for their industry.
How Is Quality Assurance Implemented in Safety Gear Manufacturing?
Quality assurance (QA) is crucial in the production of safety gear, ensuring that products are reliable and compliant with industry standards. The following QA practices are typical in this sector:
What International Standards Should B2B Buyers Be Aware Of?
International standards play a significant role in quality assurance for safety gear. Common standards include:
- ISO 9001: This standard focuses on quality management systems and is applicable to any organization, including safety gear manufacturers. Compliance indicates a commitment to quality processes.
- CE Marking: In Europe, CE marking signifies that products meet safety, health, and environmental protection standards. Buyers in Europe should ensure that suppliers provide CE certification for relevant products.
- API Standards: For safety gear used in industrial applications, API (American Petroleum Institute) standards may apply, particularly for gear used in the oil and gas sector.
What Are the Key Quality Control Checkpoints?
Quality control (QC) is implemented through several checkpoints throughout the manufacturing process:
- Incoming Quality Control (IQC): This initial checkpoint verifies the quality of raw materials before production begins. It is essential for preventing defects from the outset.
- In-Process Quality Control (IPQC): During manufacturing, IPQC ensures that processes are adhered to and that products are being made according to specifications.
- Final Quality Control (FQC): Once products are assembled, FQC involves a thorough inspection to ensure that the final product meets all specifications and standards.
What Testing Methods Are Commonly Used for Safety Gear?
Testing is a vital part of the quality assurance process. Common testing methods include:
- Mechanical Testing: This assesses the physical properties of materials, such as tensile strength and abrasion resistance, which are critical for safety gear.
- Chemical Testing: To ensure that materials are safe and non-toxic, chemical testing may be conducted, particularly for PPE that comes into contact with skin.
- Performance Testing: Depending on the type of gear, performance testing may include flame resistance, water resistance, or electrical conductivity tests.
How Can B2B Buyers Verify Supplier Quality Control?
Verifying a supplier’s quality control processes is essential for B2B buyers, particularly when sourcing from international suppliers. Here are some actionable steps:
What Should Buyers Look for in Supplier Audits and Reports?
- Supplier Audits: Conducting an audit of the supplier’s manufacturing facility can provide insights into their quality control processes. Buyers should check for documented procedures and compliance with international standards.
- Quality Reports: Requesting quality assurance reports can help buyers understand the supplier’s performance metrics, including defect rates and compliance with safety standards.
How Can Third-Party Inspections Enhance Confidence?
Engaging third-party inspection services can provide an unbiased assessment of a supplier’s quality control processes. These inspections can occur at various stages of production, ensuring adherence to required standards and specifications.
What Are the Nuances of Quality Control for International B2B Buyers?
B2B buyers from regions like Africa, South America, the Middle East, and Europe must consider specific nuances when dealing with international suppliers:
- Regulatory Compliance: Different regions may have varying regulations regarding safety gear. Buyers should familiarize themselves with local regulations to ensure that the products they import comply with local laws.
- Cultural Considerations: Understanding cultural differences in business practices can facilitate smoother negotiations and partnerships. This is especially true in regions with distinct business customs.
- Logistics and Supply Chain: Shipping and logistics can impact the quality of safety gear upon arrival. Buyers should discuss packaging and transportation methods with suppliers to minimize risks during transit.
Conclusion: Ensuring Quality in Safety Gear Procurement
For international B2B buyers, understanding the manufacturing processes and quality assurance measures in place for safety gear is crucial. By asking the right questions and verifying supplier claims, buyers can ensure they receive high-quality products that meet the necessary safety standards. This not only protects their workforce but also enhances their reputation and operational efficiency.
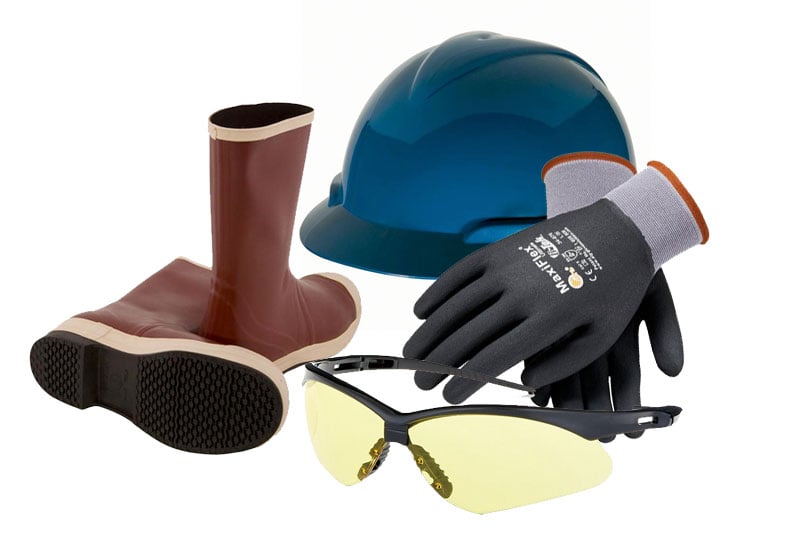
A stock image related to safety gear supplier.
Practical Sourcing Guide: A Step-by-Step Checklist for ‘safety gear supplier’
To assist international B2B buyers in sourcing safety gear suppliers effectively, this guide outlines essential steps to ensure a successful procurement process. By following these steps, buyers can make informed decisions that prioritize safety, compliance, and quality.
Step 1: Define Your Technical Specifications
Begin by clearly defining the technical requirements for the safety gear you need. This includes understanding the specific hazards present in your work environment and the corresponding protective measures required.
– Consider industry standards: Ensure that your specifications align with local and international safety regulations, such as those established by the International Labour Organization (ILO).
– Identify necessary certifications: Different types of safety gear may require specific certifications, such as ISO or ANSI, which ensure that products meet safety standards.
Step 2: Conduct Market Research for Suppliers
Next, perform thorough market research to identify potential suppliers. Look for companies with a strong reputation in the industry and a proven track record of delivering quality safety gear.
– Utilize industry directories: Resources like trade associations or B2B platforms can provide lists of certified suppliers in your region.
– Seek recommendations: Networking with industry peers can lead to valuable insights and recommendations for reputable suppliers.
Step 3: Evaluate Supplier Certifications
Before narrowing down your options, verify that potential suppliers hold the necessary certifications and adhere to safety standards.
– Check for compliance: Look for certifications that demonstrate adherence to occupational safety and health conventions, such as ILO Convention No. 155.
– Request documentation: Ask suppliers for copies of their certifications and any relevant quality assurance processes they follow.
Step 4: Request Samples for Testing
Once you have shortlisted potential suppliers, request samples of the safety gear to evaluate their quality and performance.
– Test under real conditions: Ensure that the samples are subjected to the same conditions your workforce will experience. This will help assess the gear’s durability and effectiveness.
– Gather feedback: Involve end-users in testing to gather feedback on comfort, fit, and usability, which are critical factors in ensuring compliance with safety practices.
Step 5: Assess Supplier Capabilities and Reliability
Evaluate the operational capabilities of your shortlisted suppliers to ensure they can meet your demands consistently.
– Examine production capacity: Verify that suppliers can produce the required volume of safety gear within your timeline.
– Review delivery performance: Investigate their track record for on-time delivery and responsiveness to order changes, which can impact your operations.
Step 6: Negotiate Terms and Conditions
Once you have selected a supplier, negotiate favorable terms and conditions that reflect the quality and volume of gear you are purchasing.
– Discuss pricing and payment terms: Ensure that the pricing aligns with your budget while considering the quality of the products.
– Clarify warranty and return policies: Establish clear agreements regarding warranties, return policies, and after-sales support to safeguard your investment.
Step 7: Establish a Long-term Relationship
Finally, aim to build a long-term partnership with your chosen supplier to enhance collaboration and ensure ongoing quality.
– Regular communication: Maintain open lines of communication to discuss any issues, feedback, or adjustments needed in the future.
– Evaluate supplier performance: Periodically assess the supplier’s performance against agreed-upon standards to ensure they continue to meet your needs.
By following this structured checklist, B2B buyers can effectively source safety gear suppliers that not only meet their immediate needs but also contribute to a safer working environment in the long run.
Comprehensive Cost and Pricing Analysis for safety gear supplier Sourcing
What are the Key Cost Components in Sourcing Safety Gear?
When evaluating suppliers for safety gear, understanding the cost structure is essential for effective budgeting and decision-making. The primary cost components include:
-
Materials: The choice of materials significantly impacts the final price. High-quality, durable materials will typically cost more but can offer better protection and longevity, which is crucial in safety applications.
-
Labor: Labor costs vary depending on the region and the skill level required for production. Regions with lower labor costs may offer cheaper products, but this could affect quality.
-
Manufacturing Overhead: This includes costs related to production facilities, utilities, and indirect labor. Efficient manufacturing processes can help reduce overhead, which can be passed on to buyers.
-
Tooling: Initial tooling costs can be substantial, especially for custom designs. Buyers should consider whether these costs are amortized over large production runs or if they will be charged for each order.
-
Quality Control (QC): Investing in robust QC processes ensures that products meet safety standards and specifications. While this adds to the cost, it can prevent costly recalls and liability issues later.
-
Logistics: Shipping and handling costs can vary widely based on distance, mode of transport, and the chosen Incoterms. Understanding these costs is vital for accurate pricing.
-
Margin: Suppliers typically apply a margin to cover their costs and generate profit. This margin can be influenced by market conditions, supplier reputation, and the uniqueness of the product.
How Do Price Influencers Affect Safety Gear Procurement?
Several factors can influence the pricing of safety gear, and understanding them can help buyers negotiate better deals:
-
Volume/MOQ: Suppliers often offer better pricing for larger orders due to economies of scale. Buyers should assess their needs and consider bulk purchasing to reduce costs.
-
Specifications/Customization: Custom products usually come with higher costs. Buyers should clarify their specifications upfront to avoid unexpected charges later.
-
Materials and Quality Certifications: Products that meet international safety standards or certifications may have higher costs but are often worth the investment for compliance and safety assurance.
-
Supplier Factors: The supplier’s reputation, production capacity, and location can influence pricing. Established suppliers may charge more but offer reliability and quality assurance.
-
Incoterms: The chosen Incoterms can significantly affect the total landed cost. Buyers should understand terms like FOB (Free on Board) or CIF (Cost, Insurance, and Freight) to accurately calculate costs.
What Tips Can Help Buyers Negotiate Better Prices for Safety Gear?
To optimize procurement, international B2B buyers should consider the following strategies:
-
Negotiate Effectively: Leverage the knowledge of your market and competitor prices during negotiations. Presenting data can strengthen your position and lead to better terms.
-
Focus on Cost-Efficiency: Analyze the Total Cost of Ownership (TCO), which includes purchase price, maintenance, and disposal costs. A higher initial price may be justified if the product offers lower long-term costs.
-
Understand Pricing Nuances: Be aware of regional pricing trends and market dynamics. For instance, suppliers in Africa or South America may have different pricing structures compared to those in Europe or the Middle East.
-
Build Relationships: Establishing long-term relationships with suppliers can lead to better pricing and terms. Regular communication and consistent orders can enhance trust and cooperation.
-
Stay Informed: Keep abreast of changes in regulations and standards that may affect pricing and product availability. This knowledge can provide leverage during negotiations.
Disclaimer on Pricing
It is essential to note that prices for safety gear can fluctuate based on market conditions, supplier negotiations, and specific order requirements. Always request detailed quotes and consider all cost factors before making procurement decisions.
Alternatives Analysis: Comparing safety gear supplier With Other Solutions
Understanding Alternatives to Safety Gear Suppliers
In the realm of occupational safety, businesses often seek to enhance their protective measures through various solutions. While traditional safety gear suppliers provide essential personal protective equipment (PPE), there are alternative methods and technologies that can also contribute to workplace safety. This section compares safety gear suppliers with alternative solutions, enabling B2B buyers to make informed decisions based on their specific needs.
Comparison Aspect | Safety Gear Supplier | Alternative 1: Safety Training Programs | Alternative 2: Smart Wearable Technology |
---|---|---|---|
Performance | High protection against injuries and hazards | Increases safety awareness, reduces incidents | Provides real-time data on worker safety |
Cost | Varies by product and volume | Typically lower, ongoing investment needed | Higher initial investment, but long-term savings possible |
Ease of Implementation | Requires training for proper use | Can be implemented with minimal setup | Requires integration with existing systems |
Maintenance | Regular inspection and replacement needed | Low maintenance; updates needed for content | Regular software updates and device maintenance |
Best Use Case | Industries with high physical risks (construction, manufacturing) | Any industry needing safety culture improvement | Tech-savvy industries focusing on data-driven safety |
What Are the Benefits and Drawbacks of Safety Training Programs?
Safety training programs are designed to educate employees about workplace hazards, proper safety practices, and emergency procedures. Their primary advantage lies in fostering a culture of safety, which can significantly reduce the likelihood of accidents. Furthermore, training can often be tailored to specific industry needs and is generally less expensive than ongoing PPE purchases. However, the effectiveness of training depends on employee engagement and retention of information, which can vary widely.
How Do Smart Wearable Technologies Enhance Workplace Safety?
Smart wearable technology includes devices like helmets equipped with sensors, smart vests, and wristbands that monitor environmental conditions and worker health metrics. These devices can provide real-time alerts regarding hazardous conditions, enhancing immediate response capabilities. While the technology can lead to substantial long-term savings by reducing accident rates and insurance costs, the initial investment can be significant. Additionally, businesses must ensure that their workforce is comfortable with technology use, which may require further training.
Conclusion: How to Choose the Right Safety Solution for Your Business
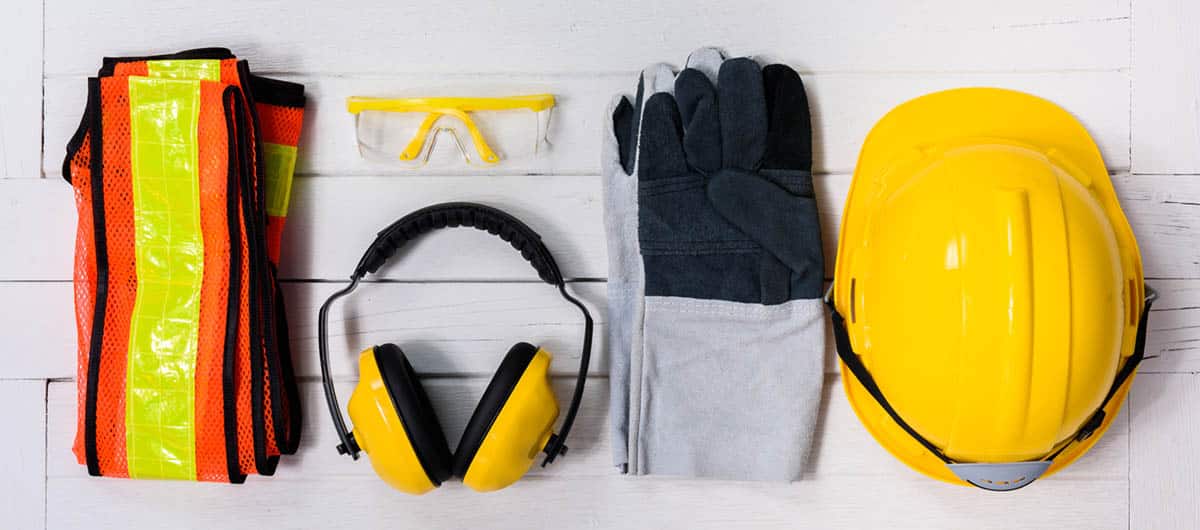
A stock image related to safety gear supplier.
When selecting the appropriate safety solution, B2B buyers should assess their specific workplace needs, budget constraints, and the level of risk associated with their operations. Safety gear suppliers are essential for industries with high physical risks, while training programs are beneficial for fostering a safety culture across various sectors. Smart wearable technology represents an innovative approach that may suit tech-oriented companies looking to leverage data for improved safety outcomes. Ultimately, the choice will depend on balancing immediate protective needs with long-term safety strategies and investments.
Essential Technical Properties and Trade Terminology for safety gear supplier
What Are the Essential Technical Properties of Safety Gear?
When sourcing safety gear, understanding the technical specifications is crucial for ensuring product quality and compliance with safety standards. Here are some key properties to consider:
-
Material Grade
The material grade of safety gear determines its durability and protection level. Common materials include high-grade polyester, Kevlar, and rubber, each offering varying levels of resistance to abrasion, heat, and chemicals. For B2B buyers, selecting the right material grade can directly influence the longevity of the gear and the safety of employees. -
Tolerance Levels
Tolerance refers to the allowable deviation from specified dimensions in safety equipment. For instance, helmets must meet strict dimensional tolerances to ensure proper fit and maximum protection. Understanding tolerance levels is essential for buyers to ensure that the safety gear will function correctly and provide the intended protection. -
Impact Resistance Rating
This rating indicates how well safety gear can withstand sudden forces or impacts. For example, safety helmets often have an impact resistance rating that complies with international standards (like EN 397 in Europe). Buyers should look for these ratings to ensure that the gear meets local regulations and provides adequate safety. -
Chemical Resistance
Many industries require safety gear that can protect against harmful chemicals. Gear with specified chemical resistance ratings can prevent injuries from spills or exposure. B2B buyers in sectors like manufacturing or chemical processing should prioritize gear with these specifications to ensure employee safety. -
Breathability and Comfort
Comfort is vital for the effective use of safety gear. Products designed with breathable materials can help workers stay comfortable during long shifts, which is crucial for maintaining productivity. Buyers should evaluate breathability specifications when selecting gear, particularly for regions with hot climates.
What Are Common Trade Terms Used in Safety Gear Procurement?
Navigating the procurement process for safety gear involves familiarizing oneself with industry jargon. Here are some essential trade terms:
-
OEM (Original Equipment Manufacturer)
An OEM refers to a company that produces parts or equipment that may be marketed by another manufacturer. In the safety gear industry, understanding OEM relationships is essential for ensuring product authenticity and quality. Buyers should verify OEM status to ensure they are sourcing from reputable suppliers. -
MOQ (Minimum Order Quantity)
MOQ is the smallest quantity of a product that a supplier is willing to sell. Knowing the MOQ is crucial for B2B buyers to budget appropriately and manage inventory effectively. In markets like Africa and South America, where cash flow may be limited, negotiating MOQs can lead to significant cost savings. -
RFQ (Request for Quotation)
An RFQ is a document that solicits price quotations from suppliers. It details the specifications, quantities, and delivery requirements for the safety gear needed. For international buyers, issuing RFQs can streamline the procurement process and ensure competitive pricing. -
Incoterms (International Commercial Terms)
Incoterms are a set of international trade terms that define the responsibilities of buyers and sellers in shipping agreements. Familiarity with these terms, such as FOB (Free on Board) or CIF (Cost, Insurance, and Freight), is essential for B2B buyers to understand their obligations and costs associated with shipping safety gear across borders. -
Lead Time
Lead time refers to the amount of time it takes from placing an order to receiving the product. Understanding lead times is vital for planning and ensuring that safety gear is available when needed. B2B buyers must communicate lead times clearly with suppliers to avoid operational delays. -
Certification Standards
Certification standards, such as ISO or ANSI, indicate that the safety gear meets specific safety and quality benchmarks. Buyers should ensure that the gear they procure is certified according to relevant standards in their region, as this ensures compliance and enhances workplace safety.
By mastering these technical properties and trade terms, international B2B buyers can make informed decisions that enhance workplace safety and comply with local regulations.
Navigating Market Dynamics and Sourcing Trends in the safety gear supplier Sector
What Are the Key Market Dynamics and Trends in the Safety Gear Supplier Sector?
The global safety gear supplier market is experiencing significant growth, driven by several factors including increased regulatory requirements and a heightened focus on workplace safety. In regions like Africa, South America, the Middle East, and Europe, there is a growing awareness among businesses of the importance of occupational safety and health (OSH), as highlighted by international standards such as the ILO’s Convention No. 155. This awareness is pushing companies to invest in quality safety gear, thereby elevating demand for suppliers who can meet these standards.
Emerging technologies are reshaping sourcing trends in the safety gear sector. The adoption of smart safety gear, which incorporates IoT (Internet of Things) technology, is gaining traction. This innovation allows for real-time monitoring of workplace conditions, significantly enhancing safety protocols. Additionally, e-procurement platforms are facilitating easier access to a wider range of suppliers, enabling buyers to compare products and prices more effectively. For international B2B buyers, especially in regions like South Africa and the UAE, leveraging these technologies can streamline the sourcing process and improve overall procurement efficiency.
Furthermore, the market is witnessing an increased emphasis on customization and personalization of safety gear. Buyers are seeking suppliers who can provide tailored solutions that fit specific industry needs and regulatory standards. This trend not only enhances the effectiveness of safety gear but also fosters stronger supplier-buyer relationships, as businesses are more likely to partner with suppliers who understand their unique challenges and requirements.
How Does Sustainability Impact Sourcing Decisions in the Safety Gear Sector?
Sustainability is becoming a critical factor in the sourcing decisions of international B2B buyers in the safety gear sector. The environmental impact of manufacturing processes and materials used in safety gear is under scrutiny, prompting buyers to prioritize suppliers who adopt eco-friendly practices. This includes the use of recycled materials, sustainable production methods, and minimizing waste throughout the supply chain.
Ethical sourcing is equally important, as businesses are increasingly held accountable for their supply chain practices. Buyers are looking for suppliers that can provide transparency regarding their sourcing methods and labor practices. Certifications such as ISO 14001 for environmental management and Fair Trade certifications for labor practices are becoming essential credentials that suppliers must possess to remain competitive in the market.
Moreover, the demand for “green” safety gear made from biodegradable or recycled materials is on the rise. Buyers are not only interested in compliance with safety standards but also in ensuring that their purchases contribute positively to environmental sustainability. By aligning with suppliers who prioritize ethical and sustainable practices, businesses can enhance their corporate social responsibility (CSR) profiles, which is increasingly important to consumers and stakeholders alike.
How Has the Safety Gear Supplier Sector Evolved Over Time?
The safety gear supplier sector has evolved significantly over the last few decades, primarily in response to changing regulatory landscapes and increased awareness of occupational safety. Initially dominated by basic protective equipment, the sector has transitioned towards more advanced solutions that incorporate technology and innovative materials.
The introduction of global standards and conventions, such as those from the ILO, has spurred the adoption of comprehensive safety management systems within organizations. This evolution has not only transformed the types of products available but has also influenced the sourcing strategies of businesses seeking to ensure compliance and enhance workplace safety.
As companies recognize the business case for investing in safety gear, the sector is poised for continued growth. Buyers are encouraged to stay informed about emerging trends and technologies to make informed sourcing decisions that align with both safety and sustainability objectives.
Frequently Asked Questions (FAQs) for B2B Buyers of safety gear supplier
-
How do I choose the right safety gear supplier for my business needs?
Selecting the right safety gear supplier involves assessing their product range, compliance with international safety standards, and their reputation in the industry. Look for suppliers who provide certifications such as ISO or ANSI, ensuring the gear meets safety requirements. Additionally, consider their experience in your specific industry and their ability to customize products to suit your needs. Request samples to evaluate quality before making a decision, and check references from other businesses to gauge reliability and service. -
What is the best type of safety gear for construction workers?
For construction workers, the best safety gear includes hard hats, high-visibility vests, safety glasses, gloves, and steel-toed boots. Additionally, consider hearing protection and respiratory masks, especially in environments with loud machinery or airborne particles. Ensure that the gear complies with local regulations and standards such as OSHA in the U.S. or EN standards in Europe. Customization options for branding and fit can also enhance safety and company identity. -
How can I verify the credibility of a safety gear supplier?
To verify a safety gear supplier’s credibility, check their certifications and compliance with international safety standards. Research their history, looking for reviews or testimonials from other businesses. It’s also beneficial to request case studies or references from clients in similar industries. Attend industry trade shows or conferences where they exhibit to assess their professionalism and product quality firsthand. Lastly, consider their customer service responsiveness as a measure of their reliability. -
What are typical payment terms when dealing with international safety gear suppliers?
Payment terms can vary significantly among international suppliers, but common practices include advance payment, letters of credit, or net 30/60 days after delivery. It’s essential to negotiate terms that protect your cash flow while ensuring the supplier feels secure. Be aware of currency exchange rates and potential fees associated with international transactions. Establishing a good relationship with the supplier can also lead to more favorable terms in the long run. -
What is the minimum order quantity (MOQ) for safety gear suppliers?
The minimum order quantity (MOQ) for safety gear can vary widely based on the supplier and the specific products. Some suppliers may have MOQs as low as 50 units, while others might require orders of 500 or more. Discuss your needs with potential suppliers to see if they can accommodate smaller orders, especially if you’re a new business. Some suppliers may offer flexible MOQ terms for first-time buyers or bulk discounts for larger orders. -
How do I ensure quality assurance when sourcing safety gear?
Quality assurance can be ensured by selecting suppliers who provide detailed product specifications and certifications, such as ISO 9001. Request samples to evaluate the quality of materials and workmanship. Implementing a quality control process, including periodic inspections during production and pre-shipment checks, can help maintain standards. Establishing clear communication regarding expectations and conducting audits on suppliers can also enhance quality assurance efforts. -
What logistics considerations should I keep in mind when importing safety gear?
When importing safety gear, consider shipping methods, lead times, and customs regulations. Choose a reliable freight forwarder familiar with your destination country’s import laws. Be aware of duties, taxes, and any restrictions on specific safety equipment. Planning for potential delays is crucial, especially for high-demand periods. Additionally, ensure proper packaging to prevent damage during transit and verify that suppliers can provide necessary shipping documentation. -
Can safety gear be customized for my company’s branding?
Yes, many safety gear suppliers offer customization options to incorporate your company’s branding, such as logos or color schemes. Customization can enhance team identity and professionalism. When discussing customization, inquire about the minimum order quantities and any additional costs involved. Ensure that the quality of the gear is not compromised during the customization process. This approach can also serve as a marketing tool, showcasing your commitment to safety while promoting your brand.
Important Disclaimer & Terms of Use
⚠️ Important Disclaimer
The information provided in this guide, including content regarding manufacturers, technical specifications, and market analysis, is for informational and educational purposes only. It does not constitute professional procurement advice, financial advice, or legal advice.
While we have made every effort to ensure the accuracy and timeliness of the information, we are not responsible for any errors, omissions, or outdated information. Market conditions, company details, and technical standards are subject to change.
B2B buyers must conduct their own independent and thorough due diligence before making any purchasing decisions. This includes contacting suppliers directly, verifying certifications, requesting samples, and seeking professional consultation. The risk of relying on any information in this guide is borne solely by the reader.
Strategic Sourcing Conclusion and Outlook for safety gear supplier
Why is Strategic Sourcing Essential for B2B Buyers of Safety Gear?
In conclusion, strategic sourcing plays a pivotal role in enhancing the procurement processes of safety gear suppliers, ensuring compliance with occupational safety and health standards. By leveraging strategic sourcing, businesses can not only reduce costs but also elevate their safety standards, which is crucial in maintaining a competitive edge in industries across Africa, South America, the Middle East, and Europe.
How Can International Buyers Benefit from Effective Sourcing Strategies?
For international B2B buyers, understanding the nuances of local regulations and safety requirements is paramount. Engaging with suppliers who prioritize occupational safety—backed by adherence to ILO standards—can lead to improved workplace safety and efficiency. Furthermore, aligning sourcing strategies with suppliers who are committed to sustainable practices fosters stronger partnerships and enhances brand reputation.
What’s Next for B2B Buyers in Safety Gear Procurement?
As we look ahead, the emphasis on safety gear will only intensify, driven by evolving regulations and heightened awareness of occupational health. International buyers should actively seek out suppliers who offer innovative solutions and robust support services. Take the next step by evaluating your current sourcing strategies and consider how integrating safety gear suppliers can enhance your overall operational resilience and compliance. Engage with your suppliers today to foster a culture of safety that benefits your workforce and business longevity.