Discover Top Strategies to Choose a Brakes Supplier (2025)
Introduction: Navigating the Global Market for brakes supplier
Navigating the complex landscape of sourcing reliable brakes suppliers can be a daunting challenge for international B2B buyers, especially when operating across diverse regions such as Africa, South America, the Middle East, and Europe. The demand for high-quality braking systems is universal, yet the nuances of supplier selection can vary significantly based on local regulations, market dynamics, and logistical considerations. This guide aims to demystify the process, providing a comprehensive overview of the different types of brakes, their applications, and essential criteria for vetting suppliers effectively.
From understanding the intricacies of brake technology to evaluating the cost implications and identifying trustworthy manufacturers, this resource is designed to empower B2B buyers with the knowledge needed to make informed purchasing decisions. Whether you are seeking disc brakes for automotive applications or specialized industrial braking systems, the insights provided herein will facilitate a more strategic approach to sourcing.
Furthermore, this guide emphasizes the importance of building strong relationships with suppliers who align with your business goals and compliance requirements. By leveraging the actionable insights and expert recommendations detailed in this guide, international buyers can enhance their procurement strategies, ensuring they not only meet their operational needs but also gain a competitive edge in the global market.
Understanding brakes supplier Types and Variations
Type Name | Key Distinguishing Features | Primary B2B Applications | Brief Pros & Cons for Buyers |
---|---|---|---|
OEM Brake Suppliers | Manufacture original equipment parts for vehicles. | Automotive manufacturers, fleet services | Pros: High compatibility, quality assurance. Cons: Often more expensive, limited customization. |
Aftermarket Brake Suppliers | Provide replacement parts not made by OEMs. | Independent repair shops, auto parts retailers | Pros: Cost-effective, variety of options. Cons: Variable quality, compatibility issues. |
Specialized Brake Suppliers | Focus on niche markets or specific brake technologies (e.g., hydraulic, pneumatic). | Heavy machinery, industrial equipment | Pros: Expertise in specific applications, tailored solutions. Cons: May have limited product ranges, higher costs. |
Global Brake Suppliers | Operate internationally, often with extensive distribution networks. | Large-scale automotive and industrial sectors | Pros: Wide availability, competitive pricing. Cons: Potential language barriers, varying quality standards. |
Local Brake Suppliers | Serve regional markets with localized service and support. | Small businesses, local repair shops | Pros: Quick response times, personalized service. Cons: Limited product range, may lack competitive pricing. |
What Are OEM Brake Suppliers and Their Suitability for B2B Buyers?
OEM (Original Equipment Manufacturer) brake suppliers are crucial for businesses that prioritize quality and compatibility. These suppliers provide parts specifically designed to fit original vehicle specifications, ensuring optimal performance and safety. B2B buyers, especially in the automotive manufacturing sector, should consider OEM suppliers for their high-quality standards and reliability. However, the cost can be a significant factor, as these parts are typically more expensive than aftermarket options. Buyers should weigh the long-term benefits of performance and warranty against upfront costs.
How Do Aftermarket Brake Suppliers Differ and When Should B2B Buyers Choose Them?
Aftermarket brake suppliers offer a wide range of replacement parts that are not manufactured by the original vehicle makers. They are an attractive option for independent repair shops and auto parts retailers due to their cost-effectiveness and variety. B2B buyers can benefit from lower prices and diverse product choices, but they should be cautious about the potential for variable quality and compatibility issues. It’s essential for buyers to conduct thorough research and select reputable aftermarket suppliers to ensure they receive reliable products.
What Are the Advantages of Specialized Brake Suppliers for Niche Markets?
Specialized brake suppliers cater to specific industries, such as heavy machinery or specialized vehicles, providing tailored solutions that meet unique operational requirements. These suppliers often possess in-depth knowledge and expertise in their niche, making them ideal for businesses that require specific brake technologies, such as hydraulic or pneumatic systems. B2B buyers should consider these suppliers when they need specialized solutions, although they may face higher costs and limited product ranges compared to more general suppliers.
Why Choose Global Brake Suppliers for Large-Scale Operations?
Global brake suppliers have a significant advantage for businesses operating on an international scale. They typically have extensive distribution networks, allowing for wide availability and competitive pricing. These suppliers are well-suited for large automotive and industrial sectors that demand consistent supply and quality. However, B2B buyers should be mindful of potential language barriers and varying quality standards across regions. Conducting thorough due diligence and establishing clear communication channels can help mitigate these challenges.
What Benefits Do Local Brake Suppliers Offer to Small Businesses?
Local brake suppliers are vital for small businesses and repair shops that require quick and personalized service. Their localized presence allows for faster response times and the ability to build strong customer relationships. While they may offer a limited product range and potentially higher prices, the convenience and service quality can outweigh these drawbacks for many B2B buyers. Choosing a local supplier can enhance operational efficiency and support community engagement, which is increasingly valued in today’s market.
Related Video: Electromagnetic Brakes (Power-on)
Key Industrial Applications of brakes supplier
Industry/Sector | Specific Application of brakes supplier | Value/Benefit for the Business | Key Sourcing Considerations for this Application |
---|---|---|---|
Automotive Manufacturing | Brake systems for vehicles | Enhanced safety and compliance with regulations | Quality certifications, compatibility with vehicle models, and local regulations. |
Food and Beverage Processing | Conveyor systems with braking controls | Improved operational efficiency and safety in transport | Durability in harsh environments, maintenance support, and energy efficiency. |
Industrial Machinery | Braking systems for heavy machinery | Increased productivity and reduced downtime | Load capacity, response time, and integration with existing systems. |
Public Transport | Brake systems for trains and buses | Passenger safety and adherence to transport regulations | Compliance with international safety standards and local sourcing options. |
Mining and Construction | Brakes for heavy-duty vehicles | Enhanced operational safety and reliability | Robustness to withstand extreme conditions and service support availability. |
How Are Brakes Suppliers Used in Automotive Manufacturing?
In automotive manufacturing, brakes suppliers provide essential brake systems that ensure vehicle safety. These systems must meet stringent regulatory standards and are integral to vehicle performance. International B2B buyers need to consider quality certifications and the compatibility of brake components with various vehicle models. Suppliers should also demonstrate a solid understanding of local regulations, especially in regions like Africa and South America, where safety compliance can vary significantly.
What Role Do Brakes Suppliers Play in Food and Beverage Processing?
Brakes suppliers are crucial in food and beverage processing, particularly in conveyor systems where braking controls are essential for safe and efficient transport of goods. These systems enhance operational efficiency by preventing accidents and ensuring smooth transitions between processing stages. Buyers should prioritize suppliers that offer durable components capable of withstanding harsh environments, such as extreme temperatures and humidity, while also providing maintenance support to minimize downtime.
How Are Brakes Suppliers Integrated into Industrial Machinery?
In the industrial machinery sector, brakes suppliers provide braking systems designed for heavy machinery, ensuring increased productivity and reduced downtime. These systems must handle varying loads and deliver quick response times to ensure safety during operations. Buyers should focus on sourcing suppliers that offer solutions tailored to their specific machinery and operational requirements, including load capacity and ease of integration with existing systems.
Why Are Brakes Suppliers Important for Public Transport Systems?
Brakes suppliers play a vital role in public transport, providing brake systems for trains and buses that prioritize passenger safety and regulatory compliance. The reliability of these systems is crucial, as they directly impact the safety of thousands of passengers daily. Buyers in this sector must ensure that suppliers comply with international safety standards and can offer local sourcing options to facilitate timely maintenance and support.
How Do Brakes Suppliers Contribute to Mining and Construction?
In the mining and construction industries, brakes suppliers provide braking solutions for heavy-duty vehicles that operate in challenging environments. The robustness and reliability of these brakes are paramount to ensure the safety of operators and equipment. B2B buyers should consider the ability of suppliers to deliver products that can withstand extreme conditions, as well as their availability of service support to ensure ongoing operational safety and efficiency.
Related Video: Permanent Magnet Brakes – How it works
3 Common User Pain Points for ‘brakes supplier’ & Their Solutions
Scenario 1: Inconsistent Product Quality from Brakes Suppliers
The Problem:
B2B buyers often face the challenge of inconsistent product quality when sourcing brakes from various suppliers. This inconsistency can lead to severe operational issues, including safety hazards and increased maintenance costs. For instance, a manufacturer in South America may find that brakes supplied for their vehicles do not meet the required safety standards, resulting in unexpected failures. Such incidents not only disrupt production but also damage the company’s reputation and financial stability.
The Solution:
To mitigate the risk of inconsistent product quality, B2B buyers should establish robust supplier evaluation criteria focused on quality assurance. This includes reviewing the supplier’s certifications, such as ISO 9001, and their history of compliance with industry standards. Conducting audits and quality checks before making large purchases can also be beneficial. Additionally, buyers should consider establishing long-term relationships with a select few suppliers who have proven reliability, enabling better communication regarding quality expectations and facilitating quicker resolutions to any issues that arise. Regular feedback loops and performance reviews can further enhance this partnership.
Scenario 2: Difficulty in Sourcing Specific Brake Types
The Problem:
Many B2B buyers encounter difficulties when trying to source specific types of brakes tailored to their unique operational needs. For example, a construction company in Africa may require heavy-duty brakes that can withstand extreme conditions, yet find that most suppliers only offer standard options. This challenge can result in delays, increased costs, and ultimately, project setbacks.
The Solution:
To overcome sourcing challenges, buyers should invest time in researching specialized suppliers who focus on niche markets or custom solutions. Leveraging online platforms that allow for direct communication with manufacturers can help buyers articulate their specific requirements more effectively. Additionally, participating in industry trade shows and networking events can provide opportunities to connect with suppliers who may not have a strong online presence. Buyers should also consider collaborating with engineering teams to develop specifications that can be shared with suppliers, enabling them to create tailored products that meet exact needs.
Scenario 3: High Shipping Costs and Delays in Brake Supply Chains
The Problem:
International B2B buyers often face high shipping costs and delays when importing brakes, particularly from suppliers located in different continents. This can be particularly problematic for businesses in the Middle East and South America, where logistical challenges can lead to increased lead times and unpredictability in inventory management. For example, a company may place an order only to face unexpected tariffs or delays, causing production halts.
The Solution:
To address shipping challenges, buyers should evaluate logistics partners and negotiate terms that allow for more favorable shipping rates and timelines. Establishing a local inventory or utilizing a just-in-time inventory strategy can also minimize the impact of shipping delays. Furthermore, buyers should consider regional suppliers who can provide similar quality products with shorter shipping distances and reduced costs. Utilizing technology for real-time tracking and predictive analytics can help anticipate delays, allowing companies to adjust their production schedules proactively. Engaging in a thorough cost-benefit analysis of different shipping methods and suppliers can also lead to more informed decisions that optimize the supply chain.
Strategic Material Selection Guide for brakes supplier
What Are the Key Properties of Common Materials Used in Brake Systems?
When selecting materials for brake components, several factors come into play, including temperature resistance, pressure ratings, and corrosion resistance. Understanding these properties can help international B2B buyers make informed decisions that align with their operational needs and regulatory compliance.
1. Cast Iron: A Traditional Choice for Brake Components
Key Properties: Cast iron is known for its excellent wear resistance and ability to withstand high temperatures, making it a staple in brake disc manufacturing. It typically has a temperature rating of up to 600°C and offers good thermal conductivity.
Pros & Cons:
– Advantages: Cast iron is durable and cost-effective, providing a long service life. It also has good damping properties, which helps reduce noise during operation.
– Disadvantages: However, it is relatively heavy, which can affect vehicle performance. Additionally, cast iron is prone to corrosion if not properly coated.
Impact on Application: Cast iron is compatible with various braking systems, including those used in heavy vehicles. However, buyers should consider the environmental conditions of their operating regions, as moisture can lead to rust.
Considerations for International Buyers: Compliance with standards like ASTM A48 is crucial. Buyers from regions like Africa and South America should ensure that local regulations on material properties are met, particularly in harsh environments.
2. Carbon-Carbon Composites: Advanced Performance Materials
Key Properties: Carbon-carbon composites are designed for high-performance applications, offering exceptional heat resistance and lightweight characteristics. They can withstand temperatures exceeding 1,000°C and have low thermal expansion rates.
Pros & Cons:
– Advantages: Their lightweight nature improves vehicle efficiency, and they provide excellent braking performance under extreme conditions.
– Disadvantages: The cost of carbon-carbon composites is significantly higher than traditional materials, and they require specialized manufacturing processes, which can complicate supply chains.
Impact on Application: Ideal for high-speed and high-performance vehicles, these materials are often used in motorsport and aerospace applications. They may not be suitable for everyday commercial vehicles due to their cost.
Considerations for International Buyers: Buyers in Europe and the Middle East should be aware of the stringent regulations regarding carbon composites, including compliance with JIS and DIN standards.
3. Ceramic Materials: The Future of Brake Technology
Key Properties: Ceramic materials are known for their excellent thermal stability and low wear rates. They can operate effectively at high temperatures, typically around 800°C, and exhibit strong corrosion resistance.
Pros & Cons:
– Advantages: Ceramics provide superior braking performance and reduced dust emissions, making them environmentally friendly. They are also lighter than cast iron.
– Disadvantages: However, ceramics can be brittle, leading to potential failure under extreme stress. Their manufacturing process is complex and can increase overall costs.
Impact on Application: Ceramic brakes are increasingly used in luxury and high-performance vehicles. They are particularly suitable for urban environments where reduced noise and dust are priorities.
Considerations for International Buyers: Compliance with international standards such as ISO 9001 is essential. Buyers from regions like Brazil and Thailand should consider local market preferences for brake performance and environmental impact.
4. Steel Alloys: A Versatile Option
Key Properties: Steel alloys offer a good balance of strength, ductility, and corrosion resistance. They typically have a temperature rating of up to 500°C and can be engineered for specific applications.
Pros & Cons:
– Advantages: Steel alloys are versatile and can be tailored to meet various performance requirements. They are generally more affordable than carbon composites and ceramics.
– Disadvantages: While they offer good performance, steel alloys may not perform as well as specialized materials under extreme conditions.
Impact on Application: Steel alloys are widely used in commercial vehicles and heavy machinery, making them a practical choice for many applications.
Considerations for International Buyers: Buyers should ensure compliance with ASTM A36 or similar standards, particularly in regions with specific regulatory requirements.
Summary Table of Material Selection for Brake Components
Material | Typical Use Case for brakes supplier | Key Advantage | Key Disadvantage/Limitation | Relative Cost (Low/Med/High) |
---|---|---|---|---|
Cast Iron | Heavy vehicle brake discs | Durable and cost-effective | Heavy and prone to corrosion | Low |
Carbon-Carbon Composites | High-performance vehicles | Lightweight and high heat resistance | High cost and complex manufacturing | High |
Ceramic Materials | Luxury and high-performance vehicles | Superior performance and low dust | Brittle and complex manufacturing | High |
Steel Alloys | Commercial vehicles and machinery | Versatile and affordable | Moderate performance under extremes | Medium |
This guide provides a comprehensive overview of material selection for brake components, focusing on key properties, advantages, disadvantages, and considerations for international B2B buyers. Understanding these factors will enable buyers to make informed decisions that align with their specific operational needs and regulatory requirements.
In-depth Look: Manufacturing Processes and Quality Assurance for brakes supplier
What Are the Main Stages of Manufacturing for Brake Suppliers?
The manufacturing process for brake components is complex and involves several critical stages to ensure performance and safety. The primary stages include material preparation, forming, assembly, and finishing.
Material Preparation
The first step in manufacturing brakes is selecting the appropriate materials, which typically include metals such as cast iron, aluminum, and various composite materials. Each material is chosen based on its mechanical properties, including strength, weight, and thermal conductivity.
Once the materials are selected, they undergo preparation processes like cutting, machining, and heat treatment to achieve desired specifications. For instance, cast iron might be melted and poured into molds, while aluminum may be extruded to form specific shapes.
What Techniques Are Used in Brake Manufacturing?
After material preparation, the forming stage utilizes various techniques to shape the components. Common methods include:
- Casting: This involves pouring molten metal into molds to create complex shapes. It is widely used for brake calipers and rotors.
- Forging: A process where metal is shaped by applying compressive forces, enhancing the material’s strength and integrity.
- Stamping: Metal sheets are cut and shaped using a press, often used for producing brake pads and backing plates.
The assembly stage follows, where various components are brought together. For instance, brake pads are assembled with backing plates, and calipers are fitted with pistons. This stage requires precision to ensure that all parts fit correctly and function as intended.
Finally, the finishing stage includes processes such as machining, coating, and quality checks. Machining ensures that parts meet precise tolerances, while coatings can provide corrosion resistance and improve aesthetics.
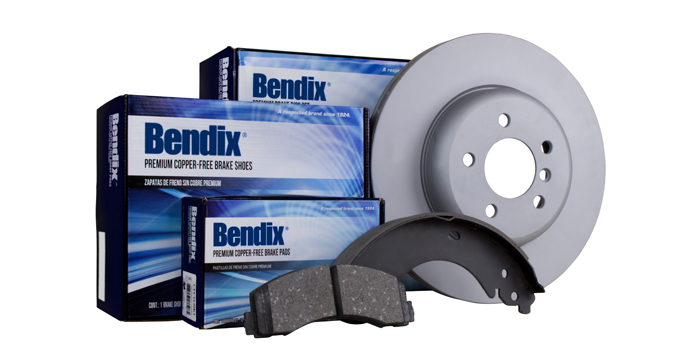
A stock image related to brakes supplier.
How Is Quality Assurance Implemented in Brake Manufacturing?
Quality assurance (QA) is critical in brake manufacturing, as safety is paramount. The QA process typically adheres to international standards such as ISO 9001 and industry-specific certifications like CE and API.
What Are the Relevant International Standards for Brake Components?
- ISO 9001: This standard focuses on quality management systems and ensures that organizations consistently meet customer and regulatory requirements.
- CE Marking: Required for products sold within the European Economic Area, indicating compliance with health, safety, and environmental protection standards.
- API Standards: Primarily relevant for brake components used in the oil and gas industry, ensuring safety and reliability under extreme conditions.
These standards not only enhance product quality but also build trust with international B2B buyers.
What Are the Key Quality Control Checkpoints in Brake Manufacturing?
Quality control (QC) checkpoints are essential throughout the manufacturing process to ensure that products meet specified standards. Key QC stages include:
- Incoming Quality Control (IQC): This initial checkpoint assesses the quality of raw materials before they enter the production process. Materials that do not meet specifications are rejected.
- In-Process Quality Control (IPQC): Conducted during the manufacturing stages, IPQC involves monitoring and testing components at various points to catch defects early.
- Final Quality Control (FQC): This is the last line of defense before products are shipped. FQC checks ensure that the final products meet all specifications and are free from defects.
Which Testing Methods Are Commonly Used for Brake Components?
Testing methods for brake components are diverse, focusing on performance, durability, and safety. Common methods include:
- Static and Dynamic Testing: These tests evaluate the braking force, response times, and efficiency under various conditions.
- Fatigue Testing: Simulates long-term use to identify potential failure points.
- Thermal Testing: Assesses how components perform under extreme temperatures, crucial for ensuring reliability in various environments.
How Can B2B Buyers Verify Supplier Quality Control?
For B2B buyers, especially those from Africa, South America, the Middle East, and Europe, verifying a supplier’s quality control is essential. Here are actionable steps:
- Conduct Audits: Schedule regular audits to assess the supplier’s manufacturing processes and quality assurance practices. This firsthand evaluation can reveal compliance with international standards.
- Request Quality Reports: Suppliers should provide documentation of their QC processes, including records of IQC, IPQC, and FQC results.
- Engage Third-Party Inspectors: Consider hiring independent organizations to conduct inspections and testing. Third-party validation can provide an unbiased assessment of product quality.
What Are the QC and Certification Nuances for International B2B Buyers?
International buyers must navigate various certification requirements that can differ by region. For example, European buyers need to ensure that products comply with CE marking requirements, while those in the Middle East may require GSO certification.
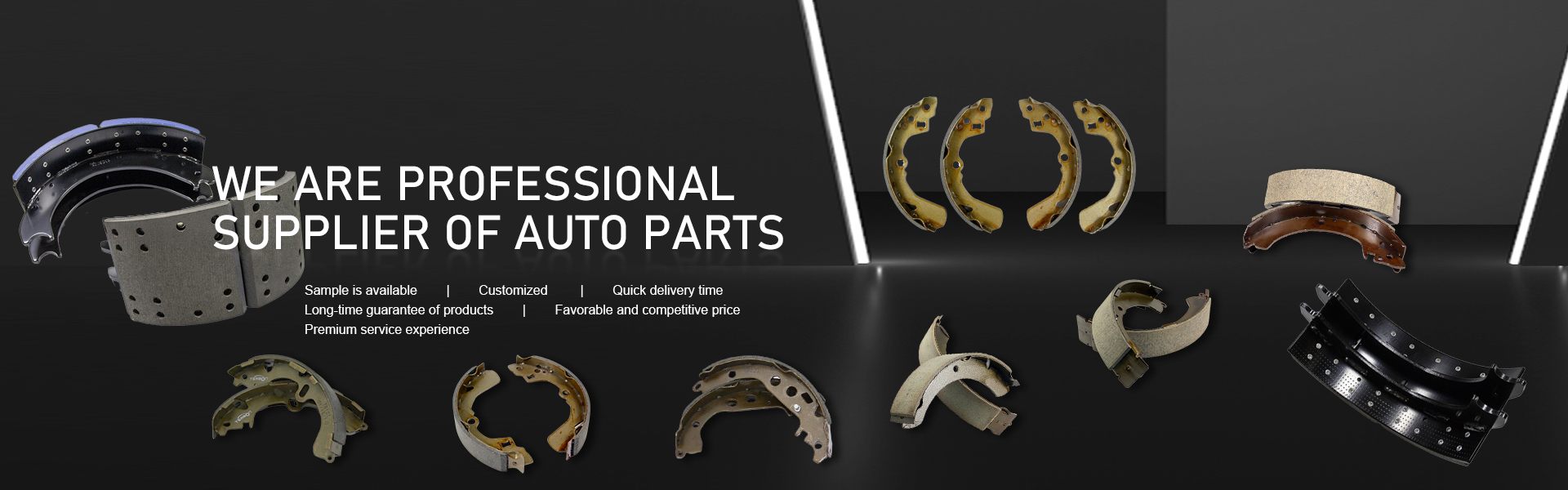
A stock image related to brakes supplier.
Understanding these nuances is crucial for successful procurement. Buyers should familiarize themselves with local regulations and standards, and confirm that suppliers have the necessary certifications to avoid compliance issues.
In conclusion, a detailed understanding of the manufacturing processes and quality assurance practices of brake suppliers is vital for international B2B buyers. By focusing on material selection, rigorous testing, and verification of quality control measures, buyers can ensure they procure reliable and safe brake components for their needs.
Practical Sourcing Guide: A Step-by-Step Checklist for ‘brakes supplier’
This guide is designed to help international B2B buyers navigate the process of sourcing brakes suppliers effectively. By following these steps, you can ensure that you select a reliable partner that meets your technical specifications, quality standards, and operational needs.
Step 1: Define Your Technical Specifications
Before engaging with potential suppliers, clearly outline the technical requirements for the brakes you need. This includes factors such as:
– Material Composition: Determine whether you need organic, ceramic, or metallic brakes based on application and performance requirements.
– Size and Fit: Specify dimensions and compatibility with existing systems to avoid mismatches.
Having well-defined specifications helps suppliers provide accurate quotes and ensures that you receive products that meet your operational needs.
Step 2: Research Supplier Background and Reputation
Conduct thorough research on potential suppliers to gauge their reliability and industry standing. Look for:
– Years in Business: A longer history often indicates stability and experience in the market.
– Customer Reviews and Case Studies: Insights from previous clients can provide valuable information about product quality and service reliability.
Understanding a supplier’s background helps you assess whether they align with your business values and quality expectations.
Step 3: Evaluate Potential Suppliers
Before committing, it’s crucial to vet suppliers thoroughly. Request:
– Company Profiles: Look for information about their manufacturing capabilities, quality control processes, and workforce expertise.
– References from Similar Industries: Speak to other buyers in your sector to learn about their experiences and satisfaction levels.
This evaluation process ensures you partner with a supplier that can meet your specific needs effectively.
Step 4: Verify Supplier Certifications
Ensure that potential suppliers hold relevant industry certifications. This may include:
– ISO Certifications: Indicative of adherence to international quality management standards.
– Compliance with Local Regulations: Verify that they meet the regulatory requirements in your region, especially if you are importing.
Certifications serve as proof of a supplier’s commitment to quality and safety standards.
Step 5: Request Samples and Conduct Testing
Before finalizing any order, request product samples for testing. This step allows you to:
– Assess Quality and Performance: Test the brakes under real operational conditions to ensure they meet your expectations.
– Evaluate Compatibility: Confirm that the samples fit and function correctly with your existing systems.
Testing samples can prevent costly mistakes and ensure that you are satisfied with your purchase.
Step 6: Negotiate Terms and Conditions
Once you identify a suitable supplier, engage in negotiations to finalize terms. Focus on:
– Pricing and Payment Terms: Ensure the pricing aligns with your budget and understand payment schedules.
– Delivery Timelines: Confirm lead times and shipping arrangements to avoid disruptions in your supply chain.
Clear agreements help prevent misunderstandings and ensure a smooth procurement process.
Step 7: Establish Communication Channels
Effective communication is vital for successful long-term partnerships. Set up:
– Regular Check-Ins: Schedule periodic meetings to discuss performance, feedback, and potential improvements.
– Points of Contact: Ensure you have direct lines to key personnel for prompt issue resolution.
Establishing strong communication channels fosters collaboration and builds trust between you and your supplier.
By following this checklist, B2B buyers can enhance their sourcing process for brakes suppliers, ensuring they choose a partner that aligns with their operational goals and quality standards.
Comprehensive Cost and Pricing Analysis for brakes supplier Sourcing
What Are the Key Cost Components in Brake Supplier Pricing?
Understanding the cost structure for sourcing brakes is crucial for international B2B buyers. The main components include:
-
Materials: The cost of raw materials, such as steel, rubber, and composites, can significantly affect pricing. Fluctuations in global commodity prices often impact these costs.
-
Labor: Labor costs vary by region and can be influenced by local wage standards and skill levels. In regions with higher labor costs, such as Europe, this can lead to increased overall pricing.
-
Manufacturing Overhead: This includes costs associated with production facilities, utilities, and administrative expenses. Efficient manufacturing processes can reduce these costs, which can be beneficial for both suppliers and buyers.
-
Tooling: The initial investment in molds and machinery for producing specific brake components can be substantial. This is particularly relevant for custom or specialized products, where tooling costs are amortized over smaller production runs.
-
Quality Control (QC): Ensuring that products meet safety and performance standards incurs additional costs. Comprehensive QC processes are crucial for maintaining product integrity, especially for international markets that require certifications.
-
Logistics: Shipping, handling, and storage costs are significant, particularly for international shipments. The choice of Incoterms can also influence logistics expenses, as they determine responsibilities between buyers and sellers.
-
Margin: Suppliers will add a markup to cover their costs and generate profit. Understanding the typical margins in the industry can help buyers gauge pricing fairness.
How Do Volume and Customization Affect Brake Pricing?
Volume discounts are a common practice in B2B transactions. Suppliers often offer lower prices for larger orders, which can significantly reduce the cost per unit. Minimum Order Quantities (MOQ) can also dictate pricing structures.
Customization, such as specific dimensions or materials, can lead to higher costs due to the need for specialized tooling and increased manufacturing complexity. Buyers should assess whether the benefits of customization outweigh the added costs.
What Influences Brake Pricing Beyond Basic Costs?
Several external factors can influence brake pricing:
-
Material Quality and Certifications: High-quality materials and compliance with international standards (e.g., ISO certifications) often lead to higher costs but also ensure better performance and durability. Buyers should consider the Total Cost of Ownership (TCO) when evaluating these aspects.
-
Supplier Factors: The reputation and reliability of a supplier can impact pricing. Established suppliers may charge a premium for their products due to their proven track record and customer service.
-
Incoterms: The choice of Incoterms can significantly affect costs related to shipping and logistics. Buyers must understand their responsibilities under different terms to avoid unexpected expenses.
What Are Effective Negotiation Strategies for B2B Buyers?
Negotiation is a critical aspect of sourcing brake components. Here are some actionable tips:
-
Research and Benchmarking: Understand market prices and competitor offerings to strengthen your negotiating position.
-
Build Relationships: Establishing rapport with suppliers can lead to better pricing and more favorable terms.
-
Leverage Volume: If possible, consolidate orders to achieve higher volumes and negotiate better rates.
-
Discuss Total Cost of Ownership: Highlight the long-term benefits of quality and reliability, which can justify a higher initial price.
What Should International Buyers Consider Regarding Pricing Nuances?
For international buyers, particularly in Africa, South America, the Middle East, and Europe, several pricing nuances should be kept in mind:
-
Currency Fluctuations: Exchange rates can significantly impact pricing. It’s advisable to negotiate prices in a stable currency or to hedge against currency risk.
-
Import Duties and Taxes: Be aware of tariffs and taxes that can inflate the final cost of imported products.
-
Cultural Sensitivity: Different regions may have varied approaches to negotiation. Understanding local business customs can enhance communication and lead to better outcomes.
Final Thoughts on Brake Supplier Pricing
While this analysis provides a comprehensive overview of the cost and pricing structure associated with brake suppliers, it’s important to note that prices can vary widely based on numerous factors. Buyers should approach negotiations with a clear understanding of their needs and the market landscape to ensure they achieve the best possible outcomes.
Alternatives Analysis: Comparing brakes supplier With Other Solutions
When considering suppliers for brake systems, international B2B buyers often explore various alternatives that can meet their operational needs while optimizing costs and efficiency. Understanding these alternatives can lead to better decision-making and alignment with specific business requirements.
Comparison Aspect | Brakes Supplier | Alternative 1: In-House Manufacturing | Alternative 2: Local Distributors |
---|---|---|---|
Performance | High-quality products with strict quality assurance protocols. | Variable; depends on equipment and expertise. | Moderate; quality can vary by supplier. |
Cost | Competitive pricing with bulk discounts. | Potentially higher due to initial setup and labor costs. | Generally lower than branded suppliers but may lack consistency. |
Ease of Implementation | Streamlined ordering and delivery processes. | Complex setup with long lead times for equipment. | Quick access, but may require multiple suppliers for full range. |
Maintenance | Comprehensive support and warranty services. | Requires ongoing training and maintenance investment. | Varies by supplier; may lack formal support. |
Best Use Case | Large operations needing reliable supply and consistency. | Custom solutions for niche requirements. | Small to medium businesses seeking cost-effective solutions. |
What Are the Pros and Cons of In-House Manufacturing?
In-house manufacturing of brake systems can provide significant customization options. Companies can tailor products to meet specific requirements, which is ideal for specialized applications. However, this approach demands a substantial upfront investment in equipment and skilled labor. Additionally, the ongoing maintenance and training needs can become a burden, particularly for smaller operations without dedicated resources. While performance can be high, the variability in quality based on staff expertise may pose risks.
How Do Local Distributors Compare as an Alternative?
Local distributors often offer a more flexible and cost-effective solution for businesses that require quick access to brake products. They can provide a variety of brands and types, allowing buyers to mix and match according to their needs. However, the quality of products can be inconsistent, and the lack of formal support may lead to complications if issues arise. This option is typically best for small to medium enterprises that prioritize affordability over brand reliability.
Conclusion: How to Choose the Right Brake Solution for Your Business?
When selecting the right brake solution, international B2B buyers should evaluate their specific needs against the characteristics of each alternative. If a business prioritizes quality and reliability, partnering with a reputable brakes supplier may be the best choice, especially for larger operations. Conversely, companies with specialized needs or those operating on tighter budgets might find in-house manufacturing or local distributors to be more beneficial. Ultimately, understanding the unique demands of your business will guide you to the most suitable brake solution.
Essential Technical Properties and Trade Terminology for brakes supplier
What Are the Key Technical Properties of Brake Components?
When selecting brake components for B2B applications, understanding the essential technical properties is vital. Here are some critical specifications that international buyers should consider:
1. Material Grade
The material grade defines the quality and performance of brake components. Common materials include cast iron, carbon composite, and ceramics. Each material has specific attributes such as heat resistance and weight, affecting performance and durability. For instance, carbon composites offer lightweight solutions with high thermal stability, making them ideal for high-performance applications.
2. Tolerance
Tolerance refers to the permissible limit of variation in a component’s dimensions. Tight tolerances are crucial in brake systems to ensure proper fit and function, reducing the risk of failure. Inaccurate tolerances can lead to increased wear and tear, impacting the safety and efficiency of the vehicle. Buyers should specify tolerance levels that meet or exceed industry standards.
3. Friction Coefficient
This property measures the effectiveness of the brake material in generating friction against the braking surface. A higher friction coefficient typically translates to better stopping power. Understanding the friction characteristics is crucial for applications requiring precise braking performance, especially in heavy-duty vehicles. Buyers should evaluate friction coefficients based on the intended use of the brake components.
4. Thermal Conductivity
Thermal conductivity indicates how well a material can dissipate heat generated during braking. High thermal conductivity helps maintain optimal braking performance and reduces the risk of brake fade. Buyers in regions with extreme temperatures should prioritize materials with excellent thermal management properties to ensure reliability.
5. Wear Resistance
Wear resistance is a measure of a material’s ability to withstand abrasion and degradation over time. Components with high wear resistance prolong the lifespan of brakes, reducing maintenance costs. Buyers should consider wear resistance in conjunction with the expected operating conditions to ensure longevity and performance.
What Are Common Trade Terms Used in the Brake Supply Industry?
Familiarity with industry jargon can facilitate smoother negotiations and ensure better communication with suppliers. Here are some essential trade terms relevant to brake suppliers:
1. OEM (Original Equipment Manufacturer)
An OEM is a company that manufactures products that are sold under another company’s brand. In the brake industry, OEM components are typically designed to meet the specific requirements of vehicle manufacturers. Buyers should prioritize OEM parts when seeking reliability and compatibility with existing systems.
2. MOQ (Minimum Order Quantity)
MOQ refers to the smallest number of units that a supplier is willing to sell. This term is critical for B2B buyers as it can impact inventory costs and cash flow. Understanding MOQ helps buyers negotiate better terms and avoid excess inventory.
3. RFQ (Request for Quotation)
An RFQ is a document that buyers use to solicit price quotes from suppliers for specific products or services. Providing detailed specifications in an RFQ can lead to more accurate pricing and better supplier responses. This process is essential for cost management and ensuring competitive pricing.
4. Incoterms (International Commercial Terms)
Incoterms are a series of predefined commercial terms used in international trade. They define the responsibilities of buyers and sellers regarding shipping, insurance, and tariffs. Familiarity with Incoterms helps buyers understand the risks and costs associated with international shipping, ensuring smoother transactions.
5. Lead Time
Lead time refers to the amount of time it takes from placing an order to receiving the goods. Understanding lead times is crucial for inventory management and planning. Buyers should communicate their timelines clearly to suppliers to avoid delays that could disrupt operations.
By grasping these technical properties and trade terms, international B2B buyers can make informed decisions and foster more effective partnerships with brake suppliers.
Navigating Market Dynamics and Sourcing Trends in the brakes supplier Sector
What Are the Current Market Dynamics in the Brakes Supplier Sector?
The brakes supplier sector is currently experiencing significant shifts driven by several global factors. The increasing demand for electric vehicles (EVs) is reshaping the landscape, as traditional brake systems are being adapted or replaced with advanced technologies such as regenerative braking systems. Furthermore, the rise of e-commerce has led to a surge in logistics and transportation needs, prompting an increase in demand for high-performance braking solutions.
Additionally, international trade dynamics are influencing sourcing strategies. For B2B buyers from Africa, South America, the Middle East, and Europe, understanding local regulations and tariffs is essential for effective supply chain management. The integration of advanced technologies like artificial intelligence (AI) and the Internet of Things (IoT) is also notable, providing suppliers with real-time data analytics that improve inventory management and demand forecasting.
Emerging markets, particularly in Africa and South America, present opportunities for growth as urbanization increases and infrastructure projects expand. Buyers are encouraged to consider local suppliers who understand regional challenges and can offer tailored solutions. This trend highlights the importance of establishing strong relationships with suppliers who are agile and responsive to market changes.
How Is Sustainability Shaping Sourcing Trends in the Brakes Supplier Sector?
Sustainability is becoming a cornerstone of sourcing strategies in the brakes supplier sector. With increasing awareness of environmental impacts, businesses are prioritizing ethical sourcing practices that minimize ecological footprints. B2B buyers are now looking for suppliers who adhere to sustainable practices, including the use of eco-friendly materials and processes.
Certifications such as ISO 14001 (Environmental Management) and the use of recycled materials are gaining traction. Suppliers that can demonstrate compliance with these standards not only meet regulatory requirements but also appeal to environmentally conscious buyers. The shift towards sustainable production methods is often accompanied by innovations in materials, such as bio-based composites and lower-emission manufacturing techniques, which are crucial for reducing the overall environmental impact of braking systems.
Moreover, as consumers increasingly demand corporate social responsibility (CSR), B2B buyers must ensure their suppliers are transparent about their supply chain practices. This includes evaluating the social and environmental impacts of sourcing decisions. Engaging with suppliers who prioritize sustainability can enhance a company’s brand reputation and drive loyalty among customers.
What Is the Evolution of the Brakes Supplier Sector?
The brakes supplier sector has evolved significantly over the past few decades. Initially dominated by traditional mechanical systems, the industry has seen a shift toward more complex electronic and hybrid braking systems in response to advancements in automotive technology. This evolution has been fueled by the need for improved safety, efficiency, and performance in vehicles.
In the early 2000s, the introduction of anti-lock braking systems (ABS) marked a turning point, leading to increased regulatory requirements for safety features in vehicles. Today, the focus is not only on performance but also on integration with emerging technologies such as autonomous driving systems. As a result, suppliers must continuously innovate to meet the evolving demands of the automotive industry while also addressing sustainability concerns.
This historical context is vital for international B2B buyers, as understanding the trajectory of technological advancements can inform better sourcing decisions and foster strategic partnerships with suppliers that are aligned with future trends.
Frequently Asked Questions (FAQs) for B2B Buyers of brakes supplier
-
How do I solve quality assurance issues with brake suppliers?
To address quality assurance issues when sourcing brake suppliers, first, establish clear quality standards and performance metrics that suppliers must meet. Conduct thorough audits and inspections of their production facilities and processes, ensuring they comply with international standards such as ISO certifications. Additionally, consider requesting samples for testing and validation before placing larger orders. Establishing a strong communication channel with suppliers can also help in promptly addressing any quality concerns. -
What is the best approach for vetting brake suppliers internationally?
The best approach to vetting international brake suppliers includes researching their reputation in the market, reviewing client testimonials, and checking their certifications. Utilize platforms like Alibaba or ThomasNet to find verified suppliers. Conducting site visits, if feasible, allows for firsthand evaluation of their production capabilities. Also, consider engaging third-party inspection services to assess the supplier’s quality control processes and overall operational practices. -
What are the typical minimum order quantities (MOQs) for brake suppliers?
Minimum order quantities (MOQs) for brake suppliers can vary significantly based on the supplier’s production capabilities and the type of brake components required. Generally, MOQs can range from 100 to 1,000 units. It’s essential to discuss MOQs upfront during negotiations, as some suppliers may be flexible, especially for first-time orders or long-term partnerships. Always clarify whether the MOQ affects pricing and lead times. -
What payment terms should I expect when dealing with brake suppliers?
Payment terms for brake suppliers typically vary, but common arrangements include payment upfront, a deposit with the balance upon delivery, or net terms (e.g., net 30 days). It’s crucial to negotiate terms that provide you with adequate cash flow while also ensuring the supplier’s confidence in the transaction. Consider using secure payment methods or escrow services for larger orders to mitigate risks. -
How can I ensure timely logistics and delivery from brake suppliers?
To ensure timely logistics and delivery from brake suppliers, establish clear delivery timelines and expectations during the initial negotiations. Discuss the supplier’s shipping methods, freight forwarders, and any potential customs issues that may arise. Regular follow-ups on order status can help in managing delays. Additionally, consider working with suppliers who have a proven track record of on-time deliveries and can provide tracking information for your shipments. -
What customization options are available when sourcing brakes?
Customization options for brakes can include variations in size, materials, and performance characteristics tailored to specific applications. When discussing with suppliers, clearly outline your requirements and inquire about their ability to modify existing products or create bespoke solutions. Many suppliers can accommodate custom branding, packaging, or specific technical specifications, so ensure to communicate your needs early in the sourcing process. -
What regulatory compliance should I be aware of when importing brakes?
When importing brakes, it’s vital to be aware of the regulatory compliance requirements in your region. This may include safety standards, environmental regulations, and import tariffs. Familiarize yourself with the local laws governing automotive parts, and ensure that your suppliers can provide the necessary documentation, such as compliance certificates. Engaging a local customs broker can also help navigate the complexities of international trade regulations. -
How do I handle disputes with brake suppliers effectively?
Handling disputes with brake suppliers effectively requires clear communication and documentation. Start by addressing the issue directly with the supplier to seek a resolution. If informal discussions do not yield results, refer to your contract for any specified dispute resolution processes, such as mediation or arbitration. Maintaining a professional demeanor throughout the process can help preserve the business relationship while ensuring that your concerns are taken seriously.
Important Disclaimer & Terms of Use
⚠️ Important Disclaimer
The information provided in this guide, including content regarding manufacturers, technical specifications, and market analysis, is for informational and educational purposes only. It does not constitute professional procurement advice, financial advice, or legal advice.
While we have made every effort to ensure the accuracy and timeliness of the information, we are not responsible for any errors, omissions, or outdated information. Market conditions, company details, and technical standards are subject to change.
B2B buyers must conduct their own independent and thorough due diligence before making any purchasing decisions. This includes contacting suppliers directly, verifying certifications, requesting samples, and seeking professional consultation. The risk of relying on any information in this guide is borne solely by the reader.
Strategic Sourcing Conclusion and Outlook for brakes supplier
What Are the Key Takeaways for Strategic Sourcing in Brake Suppliers?
In the realm of international B2B sourcing, especially for brakes suppliers, the value of strategic sourcing cannot be overstated. It encompasses not only cost savings but also quality assurance, supplier relationship management, and risk mitigation. By prioritizing sustainable practices and leveraging technology, businesses can enhance their procurement processes, ensuring they remain competitive in dynamic markets across Africa, South America, the Middle East, and Europe.
How Can International Buyers Benefit from Strategic Sourcing?
International buyers should focus on building long-term partnerships with reliable suppliers who demonstrate a commitment to innovation and sustainability. Engaging with suppliers that offer comprehensive product assurance and adhere to local regulations will foster trust and reliability. Furthermore, understanding regional market trends and consumer preferences can empower buyers to make informed decisions that align with their business goals.
What’s Next for B2B Buyers in the Brake Industry?
As we look to the future, international B2B buyers are encouraged to embrace digital transformation and data-driven decision-making. By integrating advanced analytics and procurement technologies, companies can optimize their sourcing strategies and respond swiftly to market changes. Now is the time to act—evaluate your sourcing strategies, engage with forward-thinking suppliers, and position your business for growth in an ever-evolving landscape.