Discover Top Strategies to Choose a Motor Manufacturer (2025)
Introduction: Navigating the Global Market for motor manufacturer
Navigating the global market for motor manufacturers presents a myriad of challenges for international B2B buyers, particularly those operating in diverse regions such as Africa, South America, the Middle East, and Europe. With increasing competition and evolving consumer demands, sourcing high-quality motors that meet specific industrial needs can feel overwhelming. This guide aims to simplify the process, offering a comprehensive overview of motor types, applications, and critical factors for supplier vetting. By understanding the nuances of cost structures, regulatory compliance, and technological advancements, buyers can make informed decisions that enhance their operational efficiency.
In this guide, we delve into various motor classifications, from electric and hydraulic to pneumatic systems, ensuring that you grasp their distinct applications across industries such as automotive, manufacturing, and energy. Additionally, we provide actionable insights on how to evaluate potential suppliers effectively, emphasizing the importance of quality assurance and reliability in your procurement strategy.
By equipping yourself with this knowledge, you will not only streamline your sourcing process but also mitigate risks associated with international procurement. Whether you are based in bustling markets like Germany or emerging economies in Colombia, this guide empowers you to navigate the complexities of the motor manufacturing landscape confidently. Embrace this opportunity to elevate your business operations through informed purchasing decisions.
Understanding motor manufacturer Types and Variations
Type Name | Key Distinguishing Features | Primary B2B Applications | Brief Pros & Cons for Buyers |
---|---|---|---|
Electric Motor Manufacturers | Focus on electric motors with varying power outputs | Automotive, Industrial Machinery | Pros: High efficiency, low maintenance. Cons: Higher initial costs. |
Internal Combustion Engine Manufacturers | Produce engines powered by gasoline or diesel | Automotive, Marine, Aerospace | Pros: Established technology, high power output. Cons: Higher emissions, maintenance needs. |
Hybrid Motor Manufacturers | Combine electric and combustion technologies | Automotive, Public Transport | Pros: Flexibility, reduced emissions. Cons: Complexity, higher costs. |
Custom Motor Manufacturers | Tailor-made motors for specific applications | Aerospace, Robotics, Automation | Pros: Exact specifications, unique solutions. Cons: Longer lead times, potentially higher costs. |
Small Engine Manufacturers | Focus on lightweight engines for various applications | Lawn & Garden, Power Tools | Pros: Cost-effective, versatile. Cons: Limited power, shorter lifespan. |
What Are the Key Characteristics of Electric Motor Manufacturers?
Electric motor manufacturers specialize in producing motors that operate using electrical energy. These motors are known for their high efficiency and lower maintenance requirements compared to their combustion counterparts. B2B buyers in industries such as automotive and industrial machinery can benefit from electric motors for their energy efficiency and reduced operational costs. However, the initial investment can be higher, which may require careful budgeting and financial planning.
How Do Internal Combustion Engine Manufacturers Operate?
Internal combustion engine manufacturers create engines that rely on gasoline or diesel fuel. These engines are widely used across various sectors, including automotive, marine, and aerospace industries. They are known for their high power output and reliability. However, buyers must consider the environmental impact, as these engines produce higher emissions and require regular maintenance. Understanding the lifecycle costs and regulatory requirements is crucial for B2B buyers in this category.
What Are the Benefits of Hybrid Motor Manufacturers?
Hybrid motor manufacturers produce engines that combine electric and internal combustion technologies. This dual approach offers flexibility, allowing businesses to adapt to different operational needs while reducing emissions. Industries such as automotive and public transport can leverage hybrid technology for improved fuel efficiency. However, the complexity of hybrid systems may lead to higher costs and maintenance challenges, making it essential for buyers to evaluate total cost of ownership.
Why Choose Custom Motor Manufacturers for Specific Applications?
Custom motor manufacturers focus on creating tailored solutions for unique applications, such as aerospace, robotics, and automation. These manufacturers provide motors designed to meet specific requirements, ensuring optimal performance in specialized environments. While the ability to customize motors offers significant advantages, buyers should be aware of longer lead times and potentially higher costs associated with bespoke manufacturing. Careful project planning and clear communication with manufacturers are vital for successful procurement.
How Do Small Engine Manufacturers Cater to Various Industries?
Small engine manufacturers produce lightweight engines that serve a variety of applications, including lawn and garden equipment and power tools. These engines are generally cost-effective and versatile, making them suitable for small-scale operations. However, buyers should consider the limitations in power output and potential lifespan when evaluating these engines. Understanding the specific needs of the application will help buyers make informed decisions regarding the best engine type for their operations.
Related Video: Universal Motor Video | Working and Applications of Universal Motor by Daily Electrical
Key Industrial Applications of motor manufacturer
Industry/Sector | Specific Application of Motor Manufacturer | Value/Benefit for the Business | Key Sourcing Considerations for this Application |
---|---|---|---|
Manufacturing | Electric Motors for Assembly Lines | Increased efficiency and productivity | Reliability, energy efficiency, and maintenance support |
Agriculture | Motors for Irrigation Systems | Enhanced crop yield and resource management | Durability in harsh environments and energy consumption |
Transportation & Logistics | Electric Drive Motors for Electric Vehicles | Reduced operational costs and environmental impact | Compliance with international standards and performance metrics |
Mining | Motors for Conveyor Systems | Improved material handling and reduced downtime | Robustness, safety certifications, and supplier reliability |
Construction | Motors for Heavy Machinery | Enhanced performance and operational efficiency | Load capacity, warranty terms, and after-sales service |
How Are Electric Motors Used in Manufacturing?
In the manufacturing sector, electric motors are crucial for driving assembly lines, conveyors, and robotic systems. By implementing high-efficiency motors, businesses can significantly enhance their production rates while minimizing energy consumption. This is particularly beneficial for international buyers looking to optimize their operations in competitive markets. Key considerations include sourcing motors that offer reliability and low maintenance costs, ensuring that they meet specific industry standards.
What Role Do Motors Play in Agriculture?
In agriculture, electric motors are integral to irrigation systems, enabling precise water management for crops. These motors help farmers increase yield by ensuring consistent water supply while conserving resources. For international buyers in regions like Africa and South America, selecting motors that can withstand extreme weather conditions and offer energy efficiency is vital. Buyers should also consider the availability of local support and spare parts to minimize downtime.
How Are Motors Transforming Transportation & Logistics?
Electric drive motors are revolutionizing the transportation and logistics industry by powering electric vehicles (EVs). These motors contribute to lower operational costs through reduced fuel consumption and maintenance needs. International buyers, especially from Europe where EV adoption is high, should prioritize sourcing motors that comply with stringent environmental regulations and performance standards. Understanding the total cost of ownership and long-term reliability is crucial for making informed purchasing decisions.
Why Are Motors Essential in Mining Operations?
In the mining industry, electric motors are used in conveyor systems and other heavy machinery. They enhance the efficiency of material handling and reduce operational downtime, which is critical in such a competitive sector. For buyers in the Middle East and Africa, it is essential to source robust motors designed to operate under extreme conditions, including dust and moisture. Safety certifications and proven performance records should also be key factors in the sourcing process.
How Do Motors Improve Construction Equipment Performance?
Motors are vital in powering heavy machinery used in construction, such as excavators and cranes. By selecting high-performance motors, companies can achieve better operational efficiency, leading to cost savings and improved project timelines. International buyers, particularly from regions with rapid infrastructure development, should focus on motors that offer high load capacity and come with comprehensive warranty terms. Additionally, assessing the supplier’s after-sales service capabilities can ensure ongoing support and maintenance.
Related Video: ‘Complete garbage’: GOP uses gimmick to make Trump’s awful spending bill seem like it’s not so bad
3 Common User Pain Points for ‘motor manufacturer’ & Their Solutions
Scenario 1: Difficulty in Finding Reliable Motor Manufacturers
The Problem: For B2B buyers, especially those in Africa and South America, sourcing reliable motor manufacturers can be a daunting task. Many companies face challenges related to inconsistent quality, lack of transparency, and poor communication. This can lead to delays in production, unexpected costs, and ultimately, a negative impact on their own product offerings. Furthermore, buyers may struggle to verify the credibility of manufacturers, especially when dealing with international suppliers where local regulations and standards may vary significantly.
The Solution: To overcome these challenges, B2B buyers should engage in thorough due diligence before committing to a motor manufacturer. Start by leveraging online platforms that specialize in supplier reviews and ratings, such as Alibaba or ThomasNet, to assess the reputation of potential manufacturers. Additionally, establishing direct communication through video calls or factory visits (if feasible) can foster transparency and trust. Buyers should also request samples and conduct quality control checks prior to large orders. It’s essential to ask for references from previous clients and verify their experience with the manufacturer. This proactive approach not only mitigates risk but also helps build a long-term relationship based on trust and quality assurance.
Scenario 2: Navigating Complex Supply Chains
The Problem: Buyers in the Middle East and Europe often encounter the challenge of navigating complex supply chains that involve multiple stakeholders, from manufacturers to logistics providers. This complexity can lead to delays, increased costs, and difficulties in tracking shipments, particularly when importing motors from different countries. Miscommunication among parties can exacerbate these issues, resulting in unsatisfactory service delivery and product availability.
The Solution: To streamline the supply chain process, B2B buyers should consider working with a logistics partner that specializes in the motor manufacturing industry. These partners can provide insights into the best shipping routes, customs regulations, and inventory management strategies. Additionally, implementing supply chain management software can help buyers monitor their orders in real time, allowing for better forecasting and inventory control. Establishing clear communication channels with all stakeholders involved in the supply chain is crucial. Regular updates and meetings can help resolve any potential issues before they escalate, ensuring that the supply chain operates smoothly and efficiently.
Scenario 3: Ensuring Compliance with Local Regulations
The Problem: Buyers from Europe and Africa often face the challenge of ensuring that the motors they purchase comply with local regulations and standards. Non-compliance can lead to hefty fines, product recalls, and damage to a company’s reputation. With varying regulations across regions, understanding the specific compliance requirements for motors can be both time-consuming and complex.
The Solution: To ensure compliance, B2B buyers must conduct thorough research on local regulations governing motor standards in their respective markets. This includes understanding safety, environmental, and performance standards. Engaging a compliance consultant who specializes in motor manufacturing can provide valuable insights and help buyers navigate these regulations. Buyers should also work closely with their motor manufacturers to ensure that products are designed and tested according to local standards. Requesting certifications and compliance documentation as part of the procurement process can further safeguard against potential issues. By prioritizing compliance, buyers not only protect their business interests but also enhance their brand’s credibility in the marketplace.
Strategic Material Selection Guide for motor manufacturer
When selecting materials for motor manufacturing, international B2B buyers must consider a variety of factors that impact performance, cost, and compliance with regional standards. Below is an analysis of four common materials used in motor manufacturing, along with their key properties, advantages, disadvantages, and specific considerations for buyers from Africa, South America, the Middle East, and Europe.
What Are the Key Properties of Aluminum in Motor Manufacturing?
Aluminum is a lightweight metal known for its excellent strength-to-weight ratio and corrosion resistance. It typically has a temperature rating of up to 300°C and good thermal conductivity, making it suitable for components that require heat dissipation.

A stock image related to motor manufacturer.
Pros:
– Lightweight, which contributes to overall efficiency.
– Corrosion-resistant, enhancing durability.
– Easily machined and formed, reducing manufacturing complexity.
Cons:
– Can be more expensive than steel.
– Lower tensile strength compared to some other metals.
– May require protective coatings for specific applications.
Impact on Application:
Aluminum is ideal for applications where weight reduction is critical, such as in electric motors and high-performance vehicles. However, it may not be suitable for high-pressure environments without additional reinforcement.
Considerations for International Buyers:
Buyers should ensure compliance with local standards such as ASTM and DIN when sourcing aluminum components. Understanding regional preferences for aluminum alloys can also influence material selection.
How Does Steel Compare as a Material for Motor Components?
Steel is a robust and versatile material widely used in motor manufacturing due to its high tensile strength and durability. It can withstand high temperatures and pressures, making it suitable for various applications.
Pros:
– High strength and durability, suitable for heavy-duty applications.
– Cost-effective compared to other metals.
– Good machinability and weldability.
Cons:
– Heavier than aluminum, which can impact efficiency.
– Susceptible to corrosion unless treated.
– Requires more energy for manufacturing processes.
Impact on Application:
Steel is often used in motor frames, shafts, and gears where strength is paramount. Its ability to withstand high loads makes it ideal for industrial motors.
Considerations for International Buyers:
Buyers should be aware of the specific grades of steel required by local regulations and standards. Compliance with JIS and ASTM standards is crucial for ensuring quality and performance.
What Are the Benefits of Using Composite Materials in Motor Manufacturing?
Composite materials, such as carbon fiber and fiberglass, are increasingly popular in motor manufacturing due to their lightweight and high-strength properties. They offer excellent resistance to environmental factors and can be tailored for specific applications.
Pros:
– Lightweight, enhancing performance and efficiency.
– High corrosion resistance and low thermal expansion.
– Customizable properties for specific applications.
Cons:
– Generally higher cost than metals.
– More complex manufacturing processes.
– Limited recyclability compared to metals.
Impact on Application:
Composites are suitable for high-performance applications where weight savings are critical, such as in racing motors and advanced electric vehicles.
Considerations for International Buyers:
Buyers should consider the availability of composite materials in their region and ensure that suppliers comply with relevant standards. Understanding the specific properties required for different applications is essential.
Why Is Copper a Preferred Material for Electrical Components in Motors?
Copper is renowned for its excellent electrical conductivity, making it a preferred choice for windings and electrical connections in motors. It also has good thermal conductivity, which helps in heat dissipation.
Pros:
– Superior electrical and thermal conductivity.
– Ductile and easy to work with.
– Corrosion-resistant when properly treated.
Cons:
– Relatively high cost compared to aluminum.
– Heavy, which may not be ideal for all applications.
– Susceptible to oxidation if not properly coated.
Impact on Application:
Copper is critical in applications requiring efficient electrical performance, such as in electric motors and generators. Its properties ensure reliable operation under various conditions.
Considerations for International Buyers:
Buyers should be aware of the fluctuating prices of copper and ensure compliance with international standards. Understanding local sourcing options can help mitigate costs.
Summary Table of Material Selection for Motor Manufacturing
Material | Typical Use Case for Motor Manufacturer | Key Advantage | Key Disadvantage/Limitation | Relative Cost (Low/Med/High) |
---|---|---|---|---|
Aluminum | Electric motor housings and components | Lightweight and corrosion-resistant | Higher cost than steel | Medium |
Steel | Motor frames and structural components | High strength and durability | Heavier and corrosion-prone | Low |
Composite | Racing motors and advanced electric vehicles | Lightweight and customizable | Higher cost and complex to manufacture | High |
Copper | Electrical windings and connections | Excellent electrical conductivity | Heavy and susceptible to oxidation | Medium |
This strategic material selection guide provides valuable insights for international B2B buyers, facilitating informed decisions that align with performance requirements and regional standards.
In-depth Look: Manufacturing Processes and Quality Assurance for motor manufacturer
What Are the Main Stages of the Manufacturing Process for Motor Manufacturers?
Motor manufacturers engage in a complex manufacturing process that typically involves several key stages: material preparation, forming, assembly, and finishing. Understanding these stages is crucial for international B2B buyers looking to ensure product quality and reliability.
Material Preparation: What Materials Are Used and How Are They Prepared?
The first step in the manufacturing process is material preparation, which involves sourcing high-quality raw materials essential for motor production. Common materials include metals like aluminum and steel, as well as composite materials for lightweight applications.
Materials undergo rigorous quality checks to ensure they meet specific industry standards before processing. This can involve inspecting the material’s mechanical properties, chemical composition, and structural integrity. B2B buyers should inquire about suppliers’ sourcing practices and the certifications of materials used, ensuring they align with international standards.
Forming: What Techniques Are Employed in the Forming Process?
The forming stage includes techniques such as casting, forging, and machining. Each technique has its advantages depending on the required properties of the final product.
- Casting is often used for complex shapes, while forging provides enhanced strength and durability.
- Machining allows for precise dimensions and surface finishes.
B2B buyers should be aware of the forming processes employed by manufacturers, as these can significantly impact product performance. Requesting technical specifications and process documentation can provide insights into the quality of the manufacturing techniques.
Assembly: How Is the Assembly Process Managed?
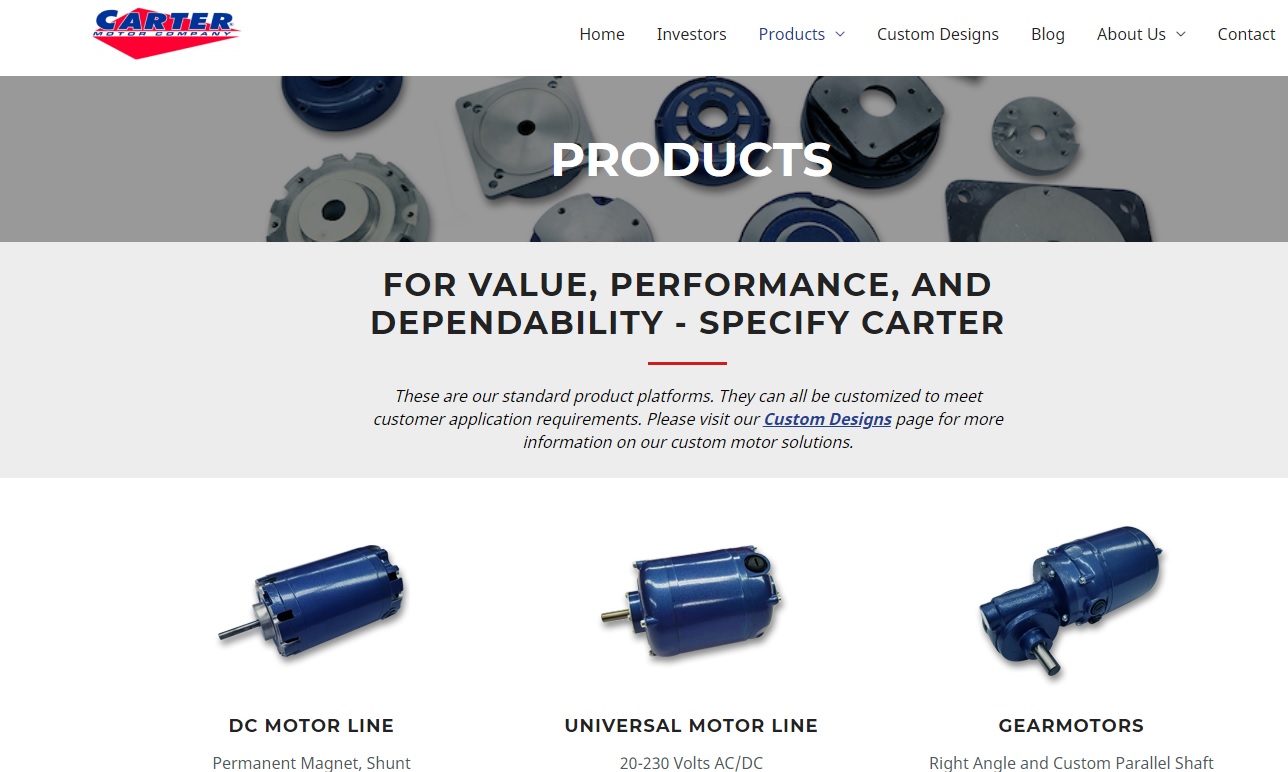
A stock image related to motor manufacturer.
During the assembly phase, various components are brought together to create the final product. This stage may involve manual labor or automated systems, depending on the manufacturer’s capabilities.
Key assembly techniques include:
- Robotic assembly for precision and efficiency.
- Manual assembly for complex or sensitive components.
Quality control checkpoints are essential during assembly to ensure that components fit correctly and function as intended. B2B buyers should inquire about the assembly processes and the technology used to guarantee high-quality outputs.
Finishing: What Processes Are Used for Surface Treatment?
Finishing processes enhance both the aesthetic appeal and performance of motor components. Common finishing techniques include:
- Coating (e.g., powder coating, painting) for protection against corrosion.
- Polishing to achieve a smooth surface finish.
Understanding the finishing processes is vital for B2B buyers, as these can affect durability and maintenance requirements. Buyers should ask for details on the finishing options available and any associated warranties.
What Quality Assurance Standards Should International B2B Buyers Be Aware Of?
Quality assurance (QA) is a critical aspect of the manufacturing process in the motor industry. Buyers should familiarize themselves with both international and industry-specific standards to ensure that the products they procure meet their quality requirements.
What Are the Key International Standards for Motor Manufacturing?
-
ISO 9001: This is a globally recognized standard that outlines the criteria for a quality management system (QMS). Manufacturers adhering to ISO 9001 demonstrate a commitment to consistent quality and continuous improvement.
-
CE Marking: This indicates compliance with European health, safety, and environmental protection standards. Products with CE marking are often required for entry into European markets.
-
API Standards: For manufacturers producing motors for the oil and gas industry, adherence to American Petroleum Institute (API) standards is essential for ensuring safety and reliability.
B2B buyers should verify that their suppliers comply with these standards by requesting documentation and certificates.
What Quality Control Checkpoints Are Commonly Used in Manufacturing?
Motor manufacturers typically implement several quality control checkpoints throughout the production process:
- Incoming Quality Control (IQC): This involves inspecting raw materials before they enter the production line.
- In-Process Quality Control (IPQC): Continuous monitoring during the manufacturing stages to catch defects early.
- Final Quality Control (FQC): A thorough inspection of the finished product to ensure it meets all specifications.
Understanding the QC processes helps buyers gauge the reliability of their suppliers. Inquire about the frequency and methods of these inspections.
How Can B2B Buyers Verify Supplier Quality Control Measures?
To ensure that suppliers maintain high-quality standards, B2B buyers can take several actionable steps:
What Should Buyers Look for in Supplier Audits and Reports?
-
Supplier Audits: Conducting regular audits of suppliers can help verify their adherence to quality standards. Buyers should establish an audit schedule and criteria based on their industry needs.
-
Quality Control Reports: Requesting detailed QC reports can provide insights into a supplier’s performance over time. This includes data on defect rates, corrective actions taken, and compliance with standards.
How Can Third-Party Inspections Enhance Quality Assurance?
Engaging third-party inspection services can add an extra layer of assurance. These independent entities evaluate suppliers against industry standards and provide unbiased reports. B2B buyers should consider incorporating third-party inspections into their procurement process, especially for high-value contracts.
What Are the Quality Control Nuances for International B2B Buyers?
International B2B buyers must navigate specific nuances when it comes to quality control.
How Do Regional Regulations Impact Quality Assurance?
Different regions may have varying regulations regarding quality standards. For instance, European buyers may face stricter environmental regulations compared to those in Africa or South America. It is crucial for buyers to understand the local compliance requirements of their suppliers and how these impact product quality.
What Role Does Communication Play in Maintaining Quality?
Clear communication with suppliers is vital for ensuring that quality expectations are understood and met. Regular updates, feedback mechanisms, and collaborative problem-solving can help mitigate quality issues before they escalate. B2B buyers should establish strong communication channels to foster a partnership based on quality assurance.
By understanding these manufacturing processes and quality assurance practices, international B2B buyers can make informed decisions, ensuring they source high-quality motors that meet their specific needs.
Practical Sourcing Guide: A Step-by-Step Checklist for ‘motor manufacturer’
To successfully navigate the procurement process for motor manufacturing, international B2B buyers must adopt a systematic approach. This checklist serves as a practical guide to ensure you cover all necessary steps to secure quality motors that meet your specific requirements.
Step 1: Define Your Technical Specifications
Before reaching out to potential suppliers, it is essential to clearly outline your technical specifications. This includes the type of motors needed (e.g., AC, DC, servo), power ratings, dimensions, and any specific industry standards required. Having detailed specifications helps streamline your search and ensures that suppliers can meet your exact needs.
Step 2: Research Potential Suppliers
Conduct comprehensive research to identify suppliers that specialize in motor manufacturing. Utilize online databases, industry directories, and trade shows to compile a list of potential manufacturers. Pay attention to suppliers located in your target regions, such as Africa, South America, the Middle East, and Europe, as they may offer localized support and logistics advantages.
Step 3: Evaluate Supplier Certifications
Verify the certifications and compliance of potential suppliers with industry standards. Look for ISO certifications, CE marking, and any other relevant quality assurances. This step is crucial as it guarantees that the motors meet safety and performance standards, reducing the risk of product failure and enhancing your operational reliability.
Step 4: Request Samples and Prototypes
Before making a large order, request samples or prototypes from shortlisted suppliers. This allows you to assess the quality, performance, and compatibility of the motors with your applications. Pay attention to the build quality, functionality, and any specific features that are critical to your operations.
Step 5: Assess Supplier Reliability and Reputation
Investigate the reliability and reputation of potential suppliers by seeking references and reading reviews. Contact previous clients to gather insights about their experiences, focusing on aspects such as delivery timelines, customer service, and after-sales support. A supplier’s reputation can provide valuable information about their ability to meet your expectations.
Step 6: Negotiate Terms and Conditions
Once you have identified a preferred supplier, initiate negotiations regarding pricing, payment terms, and delivery schedules. Ensure that all terms are clearly defined in a formal agreement to avoid misunderstandings later. Consider discussing warranty provisions and return policies, as these can significantly affect your long-term costs and operational risks.
Step 7: Plan for Logistics and Delivery
Finally, develop a logistics plan that outlines how the motors will be delivered to your location. Consider factors such as shipping methods, customs regulations, and potential tariffs, especially if sourcing from international suppliers. A well-planned logistics strategy ensures timely delivery and minimizes disruptions to your operations.
By following these steps, you can streamline the procurement process for motor manufacturing, ensuring that you select the right suppliers while mitigating risks associated with sourcing.
Comprehensive Cost and Pricing Analysis for motor manufacturer Sourcing
What Are the Key Cost Components in Motor Manufacturing?
Understanding the cost structure in motor manufacturing is crucial for B2B buyers aiming to make informed sourcing decisions. The primary cost components include:
-
Materials: Raw materials such as metals, plastics, and composites constitute a significant portion of production costs. Prices can fluctuate based on market demand and availability, so buyers should consider sourcing from multiple suppliers to mitigate risks.
-
Labor: Labor costs vary significantly across regions. Countries with lower wage rates can offer competitive pricing, but it’s essential to evaluate the skill level and efficiency of the workforce to ensure quality output.
-
Manufacturing Overhead: This includes costs related to utilities, rent, and equipment maintenance. Efficient production practices can help minimize overhead, allowing for better pricing strategies.
-
Tooling: Initial tooling costs can be substantial, especially for customized parts. Buyers should be aware of these costs and negotiate tooling fees upfront, as they can impact the overall pricing structure.
-
Quality Control (QC): Implementing rigorous QC processes is essential to maintain product standards. While this adds to costs, it can prevent costly recalls and enhance customer satisfaction in the long run.
-
Logistics: Shipping and handling costs can vary based on location and shipping methods. Buyers should consider the total logistics cost in their pricing analysis, including customs duties and potential delays.
-
Margin: Manufacturers typically add a margin to cover their costs and generate profit. Understanding typical margins in the industry can help buyers gauge the fairness of pricing offers.
How Do Price Influencers Impact Motor Manufacturing Costs?
Several factors influence the pricing of motor components, which can vary significantly across different regions such as Africa, South America, the Middle East, and Europe:
-
Volume/MOQ: Minimum Order Quantities (MOQ) can affect pricing. Higher volumes often lead to discounts, so buyers should assess their purchasing power and negotiate for better terms.
-
Specifications and Customization: Custom parts typically incur higher costs due to specialized tooling and production processes. Buyers should clearly define specifications to avoid unexpected charges.
-
Materials and Quality Certifications: The choice of materials and the requirement for quality certifications (e.g., ISO standards) can influence pricing. Buyers must balance quality with cost to ensure they meet industry standards without overspending.
-
Supplier Factors: The supplier’s reputation, production capacity, and location can all affect pricing. Buyers should conduct due diligence to assess potential suppliers’ reliability and capabilities.
-
Incoterms: Understanding international shipping terms (Incoterms) is vital. These terms dictate who is responsible for shipping costs, insurance, and risk, which can significantly impact the total cost of ownership.
What Are Effective Buyer Tips for Negotiating Motor Manufacturer Pricing?
B2B buyers can employ several strategies to optimize sourcing costs:
-
Negotiation: Approach negotiations with a clear understanding of market prices and the supplier’s cost structure. This knowledge can empower buyers to negotiate better deals and terms.
-
Cost-Efficiency: Consider the Total Cost of Ownership (TCO) rather than just the purchase price. Evaluate factors such as maintenance, durability, and potential downtime, which can all contribute to overall costs.
-
Pricing Nuances for International Buyers: Buyers from diverse regions must account for currency fluctuations, import tariffs, and regional economic conditions that can affect pricing. Building relationships with local suppliers can also yield favorable terms and better service.
-
Long-Term Partnerships: Establishing long-term relationships with suppliers can lead to better pricing agreements and enhanced collaboration on future projects. Suppliers are often more willing to offer discounts to loyal customers.
-
Stay Informed: Keep abreast of industry trends, technological advancements, and shifts in material costs. This knowledge enables buyers to make timely decisions and seize opportunities for cost savings.
Disclaimer on Indicative Prices
Prices in the motor manufacturing sector can vary widely based on numerous factors, including market conditions and specific buyer-supplier agreements. Therefore, the figures discussed here are indicative and should be verified through direct consultation with suppliers.
Alternatives Analysis: Comparing motor manufacturer With Other Solutions
When evaluating solutions for motor manufacturing, it’s essential to understand the various alternatives available that can meet your business needs. Each option comes with its own strengths and weaknesses, making it crucial for international B2B buyers, especially in regions like Africa, South America, the Middle East, and Europe, to carefully analyze their choices.
Comparison Table of Motor Manufacturer and Alternatives
Comparison Aspect | Motor Manufacturer | Alternative 1: Electric Motors | Alternative 2: Hydraulic Systems |
---|---|---|---|
Performance | High torque and efficiency; suitable for various applications. | Excellent energy efficiency; ideal for precision tasks. | Provides high power output; great for heavy-duty applications. |
Cost | Moderate initial investment; long-term ROI through durability. | Higher initial costs but lower operational costs due to energy savings. | Competitive pricing, but may incur high maintenance costs. |
Ease of Implementation | Requires specialized installation and setup. | Generally simpler installation; may require electrical infrastructure. | Complex installation; requires expert knowledge for setup. |
Maintenance | Low maintenance; periodic checks needed. | Minimal maintenance; long lifespan with fewer moving parts. | Higher maintenance frequency due to fluid management. |
Best Use Case | Suitable for diverse industries including automotive and manufacturing. | Best for applications requiring precise control, like robotics. | Ideal for construction and industrial applications needing heavy lifting. |
What Are the Advantages and Disadvantages of Electric Motors?
Electric motors are increasingly popular as an alternative to traditional motor manufacturers. They provide exceptional energy efficiency and are quieter than their counterparts. However, their initial investment can be substantial, particularly if the existing infrastructure requires upgrades. Electric motors excel in applications that require precision, such as robotics and automated systems, making them a favorable choice for tech-savvy industries. The downside includes dependency on electricity, which can be a limitation in areas with unreliable power sources.
How Do Hydraulic Systems Compare as an Alternative?
Hydraulic systems present a robust alternative, especially for applications requiring significant power output, such as in construction and heavy machinery. They are capable of handling heavy loads with ease, making them indispensable in industries where strength is paramount. However, they come with a trade-off: higher maintenance needs due to the management of hydraulic fluids and potential leaks. Additionally, their installation can be complex and requires specialized knowledge, which can lead to increased upfront costs. Therefore, while they are powerful, their operational demands may not suit every business’s capabilities.
How Can B2B Buyers Choose the Right Solution for Their Needs?
In selecting the right motor manufacturing solution, B2B buyers should assess their specific operational requirements, budget constraints, and long-term goals. Consider the performance metrics that matter most for your applications, such as torque, energy efficiency, and power output. Evaluate the total cost of ownership, including initial investments and ongoing maintenance. Finally, factor in your operational environment and existing infrastructure, as these elements will heavily influence the ease of implementation and long-term viability of the chosen solution. By carefully weighing these aspects, you can make an informed decision that aligns with your business objectives and enhances operational efficiency.
Essential Technical Properties and Trade Terminology for motor manufacturer
What Are the Essential Technical Properties for Motor Manufacturers?
Understanding key technical properties is crucial for international B2B buyers in the motor manufacturing industry. Here are some critical specifications that play a significant role in the production and procurement of motors:
-
Material Grade
Material grade refers to the specific classification of the materials used to manufacture motors, such as steel, aluminum, or composites. Different grades offer varying levels of strength, weight, and corrosion resistance. For B2B buyers, selecting the appropriate material grade is vital as it directly impacts the durability and performance of the motor, influencing maintenance costs and lifespan. -
Tolerance
Tolerance indicates the allowable variation in dimensions of motor components. Precise tolerances are essential in ensuring that parts fit together correctly and operate efficiently. In a B2B context, understanding tolerance levels can help buyers avoid costly assembly issues and ensure product quality, which is critical for maintaining customer satisfaction. -
Power Rating
The power rating, usually measured in horsepower or kilowatts, indicates the motor’s ability to perform work over time. It is a fundamental specification for determining the motor’s suitability for specific applications. B2B buyers must evaluate power ratings to ensure that the motor meets the requirements of their intended use, whether for industrial machinery, automotive applications, or consumer products. -
Efficiency Class
Efficiency class categorizes motors based on their energy consumption relative to output. Higher efficiency classes indicate lower energy consumption, which can significantly reduce operational costs. For international buyers, especially in regions focused on sustainability, selecting high-efficiency motors can align with environmental regulations and corporate social responsibility goals. -
Thermal Performance
Thermal performance refers to the motor’s ability to operate under varying temperature conditions without overheating. This property is particularly important for motors used in extreme environments. Buyers should consider thermal ratings to ensure reliability and prevent premature failure, which could lead to costly downtimes.
What Are Common Trade Terms in the Motor Manufacturing Industry?
Familiarity with industry jargon is essential for effective communication and negotiation in the motor manufacturing sector. Here are some common trade terms that B2B buyers should know:
-
OEM (Original Equipment Manufacturer)
An OEM is a company that produces parts or equipment that may be marketed by another manufacturer. Understanding OEM relationships is important for buyers seeking components that meet specific performance standards or are compatible with existing systems. -
MOQ (Minimum Order Quantity)
MOQ refers to the smallest number of units that a supplier is willing to sell. This term is crucial for buyers as it affects inventory management and cash flow. Knowing the MOQ helps businesses plan their purchases and negotiate better terms with suppliers. -
RFQ (Request for Quotation)
An RFQ is a document sent to suppliers requesting pricing and other details for specific products or services. This process allows B2B buyers to compare offers and make informed purchasing decisions. Crafting a clear RFQ can streamline procurement and ensure that all necessary specifications are communicated. -
Incoterms (International Commercial Terms)
Incoterms are a set of predefined commercial terms published by the International Chamber of Commerce that clarify the responsibilities of buyers and sellers in international transactions. Understanding Incoterms is essential for B2B buyers to manage shipping costs, risks, and insurance effectively. -
Lead Time
Lead time is the duration from placing an order to receiving the goods. In the motor manufacturing context, understanding lead times helps buyers manage production schedules and inventory levels. Effective communication about lead times can prevent delays and optimize supply chain efficiency.
By grasping these technical properties and trade terms, B2B buyers can make more informed decisions, streamline procurement processes, and foster better relationships with suppliers in the global motor manufacturing market.
Navigating Market Dynamics and Sourcing Trends in the motor manufacturer Sector
What Are the Key Trends Affecting the Motor Manufacturer Sector?
The motor manufacturing sector is undergoing significant transformations driven by globalization, technological advancements, and evolving consumer preferences. For international B2B buyers, especially from Africa, South America, the Middle East, and Europe, understanding these dynamics is crucial for strategic sourcing decisions.
One of the most prominent trends is the rise of electric vehicles (EVs), spurred by government regulations and consumer demand for more sustainable options. This shift is not only changing the types of vehicles being produced but also the components and materials used in manufacturing. Buyers need to be aware of suppliers that are adapting to these changes by investing in EV technologies and sustainable production methods.
Additionally, digitalization is reshaping supply chains. The adoption of Industry 4.0 technologies, such as IoT (Internet of Things) and AI (Artificial Intelligence), enhances operational efficiency and supply chain transparency. Buyers should seek partners who leverage these technologies to improve production processes and reduce lead times.
Emerging markets, particularly in Africa and South America, present new opportunities for motor manufacturers. As these regions develop, the demand for vehicles increases, making it essential for international buyers to establish relationships with local manufacturers who understand the market nuances.
How Is Sustainability Shaping Sourcing Decisions in the Motor Manufacturing Industry?
Sustainability has become a cornerstone of sourcing strategies in the motor manufacturing sector. The environmental impact of traditional manufacturing processes has prompted buyers to prioritize ethical sourcing practices that minimize ecological footprints.
For B2B buyers, this means evaluating suppliers based on their sustainability credentials. Look for manufacturers that utilize ‘green’ certifications, such as ISO 14001 for environmental management or LEED for sustainable building practices. Additionally, sourcing materials that are recyclable or made from renewable resources is increasingly important. This not only reduces environmental harm but can also enhance brand reputation among eco-conscious consumers.
Ethical supply chains are also gaining traction, with buyers demanding greater transparency regarding labor practices and sourcing origins. Implementing robust supplier assessments and audits can ensure that your supply chain adheres to ethical standards, which is crucial for maintaining compliance and customer trust.
What Is the Historical Context Behind Current Motor Manufacturing Trends?
The evolution of the motor manufacturing sector dates back to the late 19th century when the first gasoline-powered vehicles were introduced. Over the decades, the industry has witnessed profound changes, particularly with the introduction of mass production techniques pioneered by Henry Ford. This made vehicles more accessible to the public, driving global demand.
In recent years, however, the industry has faced challenges such as economic fluctuations, regulatory pressures, and shifting consumer preferences towards sustainability. The 2008 financial crisis prompted manufacturers to reevaluate their business models, leading to increased focus on efficiency and innovation.
As we move further into the 21st century, the convergence of technology, sustainability, and globalization continues to shape the motor manufacturing landscape. For international B2B buyers, understanding this historical context is essential for making informed sourcing decisions that align with current market dynamics and future trends.
Frequently Asked Questions (FAQs) for B2B Buyers of motor manufacturer
-
How do I choose the right motor manufacturer for my business needs?
Choosing the right motor manufacturer involves assessing several factors. Start by evaluating their product range and whether they align with your specific requirements. Research their reputation in the industry, focusing on reviews and testimonials from other B2B buyers. Consider their manufacturing capabilities, including technology and quality control processes. Finally, ensure they can meet your logistics needs and delivery schedules to avoid disruptions in your supply chain. -
What should I look for when vetting a motor manufacturer?
When vetting a motor manufacturer, prioritize their certifications and compliance with international standards, such as ISO 9001. Investigate their track record by requesting case studies or examples of past projects. Assess their customer service responsiveness and willingness to collaborate on custom solutions. Additionally, consider visiting their facility if possible, as this provides insight into their operational practices and quality control measures. -
What is the minimum order quantity (MOQ) for motors?
Minimum order quantities can vary significantly between manufacturers, typically ranging from 50 to several hundred units. When negotiating with suppliers, clarify their MOQ policies, as lower MOQs may be available for new clients or certain product lines. Be aware that lower MOQs might come with higher per-unit costs, so it’s essential to balance your needs with budget constraints. -
What payment terms should I expect when sourcing motors internationally?
Payment terms for international motor procurement usually include options like letter of credit, advance payment, or net 30/60/90 days after delivery. It’s crucial to negotiate terms that protect both parties, ensuring that you only pay for goods that meet your quality expectations. Consider using escrow services for large transactions to mitigate risk. Always review the terms in the context of your cash flow and financing capabilities. -
How can I ensure the quality of motors from a manufacturer?
To ensure quality, request detailed product specifications and quality assurance processes from the manufacturer. Consider conducting third-party inspections or audits before shipping. Establish clear quality control benchmarks and communicate them to the supplier. Regularly review performance metrics post-delivery to ensure compliance with your standards, and maintain open communication for any quality issues that arise.
- What logistics considerations should I keep in mind when importing motors?
Logistics for importing motors involve several key considerations, including shipping methods, customs clearance, and duty tariffs. Choose a reliable freight forwarder experienced in handling motor shipments to navigate these complexities. Ensure that the manufacturer provides proper documentation, such as commercial invoices and packing lists, to facilitate smooth customs processes. Finally, factor in lead times for both manufacturing and shipping to plan your inventory effectively.
-
Can I customize motors to fit my specific requirements?
Many manufacturers offer customization options for motors, allowing you to tailor specifications such as size, power output, and additional features. When discussing customization, be clear about your requirements and any regulatory standards that must be met. Keep in mind that custom solutions may come with longer lead times and higher costs, so it’s essential to weigh the benefits against your budget and timeline. -
What are the common challenges faced when sourcing motors internationally?
Common challenges in international motor sourcing include language barriers, cultural differences, and varying regulatory environments. Shipping delays and customs complications can also hinder timely deliveries. To mitigate these risks, establish clear communication channels with suppliers and consider engaging local experts or intermediaries familiar with the market. Conducting thorough research on the target region’s trade regulations can also help streamline the sourcing process.
Important Disclaimer & Terms of Use
⚠️ Important Disclaimer
The information provided in this guide, including content regarding manufacturers, technical specifications, and market analysis, is for informational and educational purposes only. It does not constitute professional procurement advice, financial advice, or legal advice.
While we have made every effort to ensure the accuracy and timeliness of the information, we are not responsible for any errors, omissions, or outdated information. Market conditions, company details, and technical standards are subject to change.
B2B buyers must conduct their own independent and thorough due diligence before making any purchasing decisions. This includes contacting suppliers directly, verifying certifications, requesting samples, and seeking professional consultation. The risk of relying on any information in this guide is borne solely by the reader.
Strategic Sourcing Conclusion and Outlook for motor manufacturer
In the dynamic landscape of motor manufacturing, strategic sourcing remains a pivotal factor in achieving operational excellence and competitive advantage. By leveraging local suppliers and optimizing global supply chains, international B2B buyers can significantly reduce costs while ensuring the quality and reliability of components. Understanding regional market nuances, particularly in Africa, South America, the Middle East, and Europe, empowers buyers to forge partnerships that enhance product offerings and streamline operations.
How Can Buyers Leverage Strategic Sourcing for Greater Impact?
The value of strategic sourcing extends beyond mere cost savings; it encompasses risk management, innovation, and sustainability. As the industry evolves towards electrification and digitalization, aligning sourcing strategies with these trends is essential. Buyers should prioritize suppliers who demonstrate a commitment to sustainability and technological advancement, ensuring that their sourcing practices contribute positively to both the environment and the bottom line.
What’s Next for International B2B Buyers in Motor Manufacturing?
As we look ahead, the focus should shift towards building resilient supply chains that can adapt to future disruptions. Buyers are encouraged to engage with local manufacturers and technology partners to foster innovation and agility. In this era of transformation, proactive sourcing strategies will not only enhance operational efficiency but also position businesses for long-term success in an increasingly competitive market. Embrace the journey of strategic sourcing today and unlock new avenues for growth and collaboration.