Discover Top Tips to Choose a Filling Machine Supplier (2025)
Introduction: Navigating the Global Market for filling machine supplier
In today’s rapidly evolving global market, sourcing the right filling machine supplier can be a daunting challenge for international B2B buyers, particularly those from regions like Africa, South America, the Middle East, and Europe, including countries such as Spain and Egypt. With diverse industries ranging from food and beverage to pharmaceuticals, understanding the nuances of filling machine technology is critical for ensuring efficiency, compliance, and quality in production processes.
This comprehensive guide aims to equip buyers with the knowledge needed to navigate the complexities of sourcing filling machines. We will explore various types of filling machines, their applications across different sectors, and essential criteria for supplier vetting. Additionally, we will address key considerations such as cost analysis, technological advancements, and post-purchase support that can significantly impact your investment decisions.
By delving into this guide, B2B buyers will gain valuable insights that empower them to make informed purchasing decisions, ultimately enhancing their operational efficiency and competitiveness in the global market. With a focus on actionable strategies, this resource is designed to help you identify reliable suppliers who align with your specific needs and standards, ensuring a successful partnership in your manufacturing journey.
Understanding filling machine supplier Types and Variations
Type Name | Key Distinguishing Features | Primary B2B Applications | Brief Pros & Cons for Buyers |
---|---|---|---|
Gravity Filling Machines | Uses gravity to fill containers, ideal for low-viscosity liquids. | Beverage, food, and chemical industries. | Pros: Simple design, low maintenance. Cons: Limited to specific liquid types. |
Pressure Filling Machines | Utilizes pressure to fill containers, suitable for high-viscosity products. | Cosmetics, pharmaceuticals, and sauces. | Pros: Fast filling, can handle thicker liquids. Cons: Higher complexity, requires more maintenance. |
Vacuum Filling Machines | Employs vacuum to fill containers, minimizing air exposure. | Food preservation, pharmaceuticals. | Pros: Extends shelf life, prevents oxidation. Cons: Higher initial costs, more technical setup. |
Piston Filling Machines | Uses a piston to measure and fill precise volumes, versatile for various products. | Food, cosmetics, and pharmaceuticals. | Pros: High accuracy, adaptable to different viscosities. Cons: More moving parts can lead to higher wear. |
Auger Filling Machines | Incorporates a screw mechanism for filling powders and granules. | Food, chemicals, and pharmaceuticals. | Pros: Efficient for solids, customizable for various materials. Cons: Limited to dry products, potential for clogging. |
What Are the Key Characteristics of Gravity Filling Machines?
Gravity filling machines are designed for low-viscosity liquids, relying on gravity to dispense the product into containers. Commonly used in the beverage and food industries, these machines are favored for their straightforward operation and low maintenance needs. However, buyers should consider that gravity fillers are limited to products with a specific viscosity range, making them less versatile for thicker liquids.
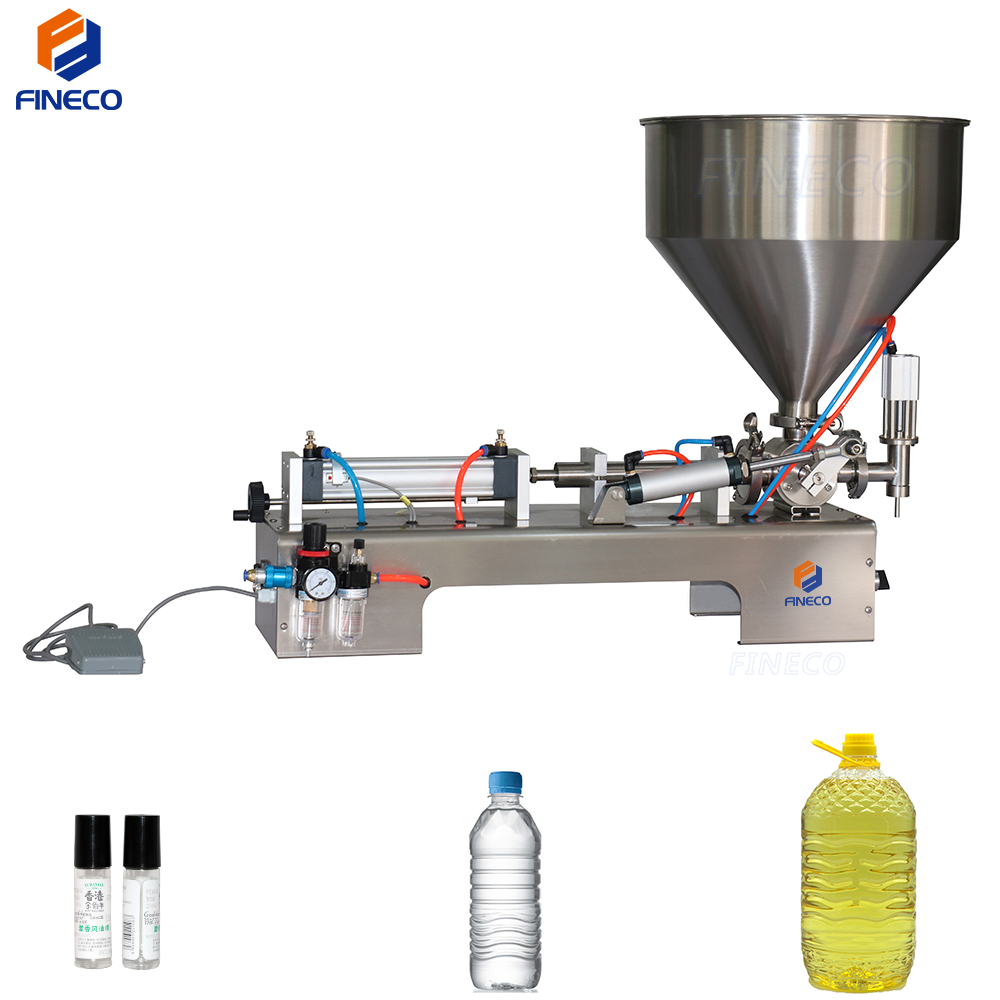
A stock image related to filling machine supplier.
How Do Pressure Filling Machines Work for High-Viscosity Products?
Pressure filling machines utilize pressurized air or gas to facilitate the filling process, making them ideal for high-viscosity products like creams and sauces. They are widely used in cosmetics and pharmaceuticals, where speed and efficiency are crucial. While they offer quick filling capabilities, buyers should be aware of their complexity, which can lead to increased maintenance requirements.
What Advantages Do Vacuum Filling Machines Provide?
Vacuum filling machines are engineered to fill containers while minimizing air exposure, which is essential for products sensitive to oxidation, such as certain foods and pharmaceuticals. This technology helps extend shelf life and maintain product integrity. However, the initial investment and technical setup can be higher, which may be a consideration for budget-conscious buyers.
Why Choose Piston Filling Machines for Precision?
Piston filling machines are versatile and known for their accuracy in dispensing precise volumes of liquid, making them suitable for a wide range of products, including those with varying viscosities. They are commonly used in food, cosmetics, and pharmaceutical applications. Although they provide high precision, buyers should note that the increased number of moving parts can lead to higher wear and potential maintenance issues over time.
How Do Auger Filling Machines Cater to Solid Products?
Auger filling machines utilize a screw mechanism to dispense powders and granules, making them ideal for industries dealing with dry products such as food and chemicals. Their efficiency and customization options make them popular among manufacturers. However, potential clogging issues and limitations to dry products should be considered when making purchasing decisions.
Related Video: 400pcs Manual capsule filling machine
Key Industrial Applications of filling machine supplier
Industry/Sector | Specific Application of Filling Machine Supplier | Value/Benefit for the Business | Key Sourcing Considerations for this Application |
---|---|---|---|
Food and Beverage | Liquid filling for beverages like juices and sauces | Increased production efficiency and reduced waste | Compliance with food safety standards and certifications |
Pharmaceutical | Filling of liquid medicines and vaccines | Ensures precision in dosage and minimizes contamination | Need for sterile environments and specialized machinery |
Cosmetic and Personal Care | Filling creams, lotions, and other beauty products | Enhances product consistency and brand presentation | Customization options for different container types |
Chemical Manufacturing | Filling of industrial chemicals and oils | Reduces spillage and enhances safety during handling | Need for robust machinery that can handle corrosive materials |
Agriculture | Filling of fertilizers and pesticides | Streamlined packaging process and reduced labor costs | Equipment capable of handling varying material viscosities |
How is Filling Machine Supplier Used in Food and Beverage Industries?
In the food and beverage sector, filling machine suppliers play a crucial role in the efficient packaging of liquids such as juices, sauces, and dairy products. These machines are designed to handle high-volume production while ensuring accuracy in filling to reduce product waste. For international buyers, especially in Africa and South America, it is essential to source equipment that complies with local food safety regulations and standards. Additionally, flexibility in machine design to accommodate different bottle sizes can enhance operational efficiency.
What are the Applications in the Pharmaceutical Industry?
In the pharmaceutical industry, filling machines are vital for the precise filling of liquid medications and vaccines. These machines help maintain stringent hygiene standards and ensure dosage accuracy, which is critical for patient safety. Buyers from the Middle East and Europe must consider sourcing machines that are capable of operating in sterile environments and are compliant with international health regulations. The ability to customize the filling process for different types of liquids can also be a significant advantage.
How are Filling Machines Applied in Cosmetic and Personal Care?
Filling machines for cosmetic and personal care products, such as lotions and creams, are essential for maintaining product consistency and enhancing brand presentation. These machines can fill various container types, from jars to tubes, which is particularly important for brands looking to differentiate themselves in competitive markets. Buyers in Europe, especially in Spain, should focus on suppliers that offer customization options and high-quality machinery that meets cosmetic industry standards to ensure product integrity.
Why are Filling Machines Important in Chemical Manufacturing?
In the chemical manufacturing sector, filling machines are used for packaging industrial chemicals and oils. These machines are designed to minimize spillage and enhance safety during the filling process, which is crucial given the hazardous nature of many chemicals. International buyers, particularly from regions with stringent safety regulations, should prioritize sourcing robust machinery that can handle corrosive materials and operate efficiently under various conditions.
What is the Role of Filling Machines in Agriculture?
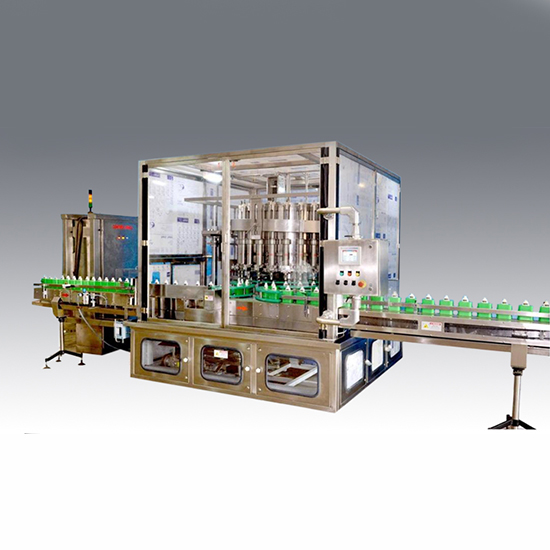
A stock image related to filling machine supplier.
Filling machines are increasingly used in the agriculture sector for the packaging of fertilizers and pesticides. These machines streamline the packaging process, allowing for greater efficiency and reduced labor costs. Buyers should look for equipment that can handle varying viscosities and is designed for safe handling of potentially hazardous materials. Additionally, sourcing machines that comply with environmental regulations is essential for sustainable agricultural practices.
Related Video: Capsugel Ultra™ III Capsule Filling Machine
3 Common User Pain Points for ‘filling machine supplier’ & Their Solutions
Scenario 1: Inconsistent Filling Accuracy Leading to Product Waste
The Problem: One of the most common pain points for B2B buyers of filling machines is achieving consistent filling accuracy. This issue can lead to significant product waste, affecting the bottom line. For instance, a beverage manufacturer in South America might experience variations in fill levels, causing overfilling or underfilling of bottles. This inconsistency not only results in product loss but also affects customer satisfaction and regulatory compliance.
The Solution: To overcome this challenge, buyers should prioritize sourcing filling machines equipped with advanced metering technologies, such as servo-driven pumps or load cells. These technologies provide precise control over fill volumes and reduce variability. Additionally, conducting thorough testing before full-scale implementation can ensure the machine meets specific requirements. Buyers should also consider suppliers that offer robust after-sales support and training to help operators maintain accuracy. Regular calibration and maintenance checks should be established as part of the operational protocol to uphold filling standards.
Scenario 2: Difficulty in Handling Diverse Packaging Formats
The Problem: International B2B buyers often face the challenge of sourcing filling machines that can accommodate a wide range of packaging formats. For instance, a manufacturer in Egypt may need to switch between filling glass bottles, plastic containers, and pouches, each requiring different filling techniques and machine settings. This variability can lead to downtime and increased operational costs due to the need for multiple machines or constant adjustments.
The Solution: Buyers should look for versatile filling machines designed for quick changeovers. Suppliers that offer modular systems can facilitate easy transitions between different packaging formats. It’s beneficial to request demonstrations of the machine’s adaptability during the sourcing process. Furthermore, investing in filling machines with automated settings can streamline operations and minimize the need for manual adjustments, thereby enhancing efficiency. Engaging with suppliers that provide comprehensive training for staff on machine versatility can also maximize the benefits of the equipment.
Scenario 3: Challenges with Compliance and Regulatory Standards
The Problem: Compliance with local and international regulations is a significant concern for B2B buyers in the filling machine market. For example, companies in Europe must adhere to stringent food safety standards, which can be daunting for manufacturers who are new to the region or are expanding their operations. Failure to comply can lead to costly fines, product recalls, and damage to the brand’s reputation.
The Solution: To mitigate compliance issues, buyers should partner with filling machine suppliers who understand the regulatory landscape relevant to their industry. When sourcing equipment, it’s crucial to ensure that the machines are compliant with the necessary certifications and standards, such as ISO or HACCP. Buyers should also request documentation from suppliers demonstrating compliance with applicable regulations. Additionally, establishing a relationship with suppliers that offer ongoing support and updates on regulatory changes can help businesses stay compliant as they scale operations. Investing in training for employees on compliance best practices can further enhance adherence to regulatory standards.
Strategic Material Selection Guide for filling machine supplier
When selecting materials for filling machines, international B2B buyers must consider several factors that influence performance, durability, and compliance with industry standards. Below is an analysis of four common materials used in filling machines, focusing on their properties, advantages, disadvantages, and specific considerations for buyers from Africa, South America, the Middle East, and Europe.
What are the Key Properties of Stainless Steel in Filling Machines?
Stainless steel is one of the most popular materials used in filling machines due to its excellent corrosion resistance and durability. It can withstand high temperatures and pressures, making it suitable for a wide range of applications, including food and beverage, pharmaceuticals, and chemicals. The most commonly used grades include 304 and 316, with 316 offering superior corrosion resistance, especially in saline environments.
Pros and Cons:
– Advantages: High durability, long lifespan, and easy to clean, making it ideal for sanitary applications.
– Disadvantages: Higher cost compared to other materials and can be challenging to machine due to its toughness.
Impact on Application:
Stainless steel is compatible with various media, including acidic and alkaline substances, making it versatile for different industries. However, buyers should ensure that the specific grade selected meets their application requirements.
Considerations for International Buyers:
Buyers should verify compliance with relevant standards such as ASTM and DIN, particularly in Europe. In regions like Africa and the Middle East, local regulations regarding food safety and material certifications should also be considered.
How Does Plastic Compare as a Material for Filling Machines?
Plastic, particularly high-density polyethylene (HDPE) and polypropylene (PP), is increasingly used in filling machines due to its lightweight nature and resistance to chemicals. These materials are often used in applications where cost is a significant factor and where the media being filled does not require high-temperature processing.
Pros and Cons:
– Advantages: Lower cost, lightweight, and good chemical resistance.
– Disadvantages: Generally less durable than metals and may not withstand high temperatures or pressures.
Impact on Application:
Plastic is suitable for non-corrosive media and applications where weight savings are crucial. However, it may not be suitable for high-temperature processes or where mechanical strength is critical.
Considerations for International Buyers:
Buyers should check for compliance with local regulations regarding plastic materials, especially in food and pharmaceutical applications. Standards such as FDA approvals for food-grade plastics are essential in markets like Europe and North America.
What Role Does Aluminum Play in Filling Machine Construction?
Aluminum is another material commonly used in filling machines, particularly for components that require a balance between weight and strength. It has good corrosion resistance and is often anodized to enhance its properties. Aluminum is particularly popular in industries where weight savings are essential, such as in mobile or portable filling machines.
Pros and Cons:
– Advantages: Lightweight, good strength-to-weight ratio, and excellent corrosion resistance.
– Disadvantages: Can be more expensive than other non-metal options and may not be as durable as stainless steel in harsh environments.
Impact on Application:
Aluminum is suitable for a variety of applications, including food and beverage, but care should be taken with acidic products, which can corrode aluminum over time.
Considerations for International Buyers:
Buyers should ensure that the aluminum used meets relevant international standards, such as ASTM or JIS, and consider the specific environmental conditions of their operational regions.
How Does Glass Fit into the Material Selection for Filling Machines?
Glass is often used in filling machines for applications requiring high levels of purity and visibility of the filled product. It is inert and does not react with most chemicals, making it ideal for sensitive products like pharmaceuticals and certain food items.
Pros and Cons:
– Advantages: Excellent chemical resistance, high purity, and visibility of contents.
– Disadvantages: Fragility and weight, which can complicate handling and transport.
Impact on Application:
Glass is particularly suited for filling applications where contamination must be minimized. However, its weight and fragility can be a disadvantage in high-volume operations.
Considerations for International Buyers:
International buyers should be aware of the handling and transportation challenges associated with glass. Compliance with safety standards and regulations for packaging and transport is crucial, especially in regions with varying infrastructure capabilities.
Summary Table of Material Selection for Filling Machines
Material | Typical Use Case for filling machine supplier | Key Advantage | Key Disadvantage/Limitation | Relative Cost (Low/Med/High) |
---|---|---|---|---|
Stainless Steel | Food and beverage, pharmaceuticals | High durability and corrosion resistance | Higher cost and machining complexity | High |
Plastic | Non-corrosive media applications | Lightweight and cost-effective | Less durable and temperature-sensitive | Low |
Aluminum | Portable filling machines | Good strength-to-weight ratio | More expensive and less durable than stainless steel | Medium |
Glass | Pharmaceuticals, sensitive food products | High purity and visibility | Fragility and weight | Medium |
This strategic material selection guide provides a comprehensive overview for international B2B buyers, helping them make informed decisions based on their specific needs and regional considerations.
In-depth Look: Manufacturing Processes and Quality Assurance for filling machine supplier
What Are the Main Stages in the Manufacturing Process of Filling Machines?
Understanding the manufacturing processes involved in producing filling machines is essential for international B2B buyers. The production typically consists of four main stages: material preparation, forming, assembly, and finishing.
-
Material Preparation: This initial stage involves sourcing high-quality materials such as stainless steel, plastics, and electronic components. Suppliers must conduct thorough assessments to ensure that materials meet industry standards and specifications. Buyers should inquire about the origin of materials and any certifications they hold, particularly if they are sourcing from regions like Africa or South America, where material quality can vary significantly.
-
Forming: In this stage, raw materials are shaped into components through techniques such as machining, stamping, and molding. Advanced technologies like CNC (Computer Numerical Control) machining are often employed to achieve precise dimensions. Buyers should look for suppliers that utilize modern forming techniques, as this impacts the durability and performance of the filling machines.
-
Assembly: The assembly stage involves putting together the various components to create the final product. This process can be manual or automated, depending on the supplier’s capabilities. Buyers should assess the supplier’s assembly line efficiency, as well as their ability to customize machines according to specific needs, such as different bottle sizes or product types.
-
Finishing: After assembly, the machines undergo finishing processes, which may include surface treatments, painting, or coating. These processes not only enhance aesthetics but also protect against corrosion and wear. It’s crucial for buyers to verify that the finishing processes meet international standards, especially if the machines will be used in industries with strict hygiene requirements, such as food and pharmaceuticals.
How Does Quality Assurance Work in Filling Machine Manufacturing?
Quality assurance (QA) is a critical aspect of the manufacturing process that ensures the final product meets the required standards. For filling machine suppliers, adherence to international and industry-specific standards is vital.
- International Standards: Many manufacturers comply with ISO 9001, which outlines requirements for a quality management system. This certification indicates that the supplier has established processes to enhance customer satisfaction and ensure consistent quality. Additionally, certifications like CE mark (for European markets) and API (for the petroleum industry) demonstrate compliance with specific industry regulations.
-
Quality Control Checkpoints: The QA process typically includes several checkpoints:
– Incoming Quality Control (IQC): This involves inspecting raw materials upon receipt to ensure they meet specifications.
– In-Process Quality Control (IPQC): During manufacturing, regular checks are performed to monitor the process and identify any issues early.
– Final Quality Control (FQC): Once the machines are assembled, they undergo final inspections and testing to ensure they function correctly and meet safety standards. -
Common Testing Methods: Various testing methods are employed to assess machine performance, including:
– Functional Testing: Ensures the machine operates as intended.
– Leak Testing: Particularly important for liquid filling machines to prevent product loss and ensure safety.
– Durability Testing: Assesses how well the machine withstands normal operating conditions over time.
How Can B2B Buyers Verify a Supplier’s Quality Control Procedures?
For international B2B buyers, particularly from diverse regions like Africa, South America, the Middle East, and Europe, verifying a supplier’s quality control processes is essential to ensure product reliability.
-
Audits: Conducting regular audits of potential suppliers can provide insights into their manufacturing and quality assurance processes. Buyers should request access to audit reports or offer to conduct their own audits, focusing on quality management systems and compliance with relevant standards.
-
Documentation and Reports: Suppliers should provide documentation that outlines their quality control procedures, including records of inspections, testing results, and certifications. This transparency is crucial for building trust and ensuring that the supplier adheres to their stated quality standards.
-
Third-Party Inspections: Engaging third-party inspection services can provide an unbiased assessment of the supplier’s quality control processes. This is particularly beneficial for buyers who may not have the resources to perform comprehensive audits themselves.
What Are the Nuances of Quality Control for International B2B Buyers?
When sourcing filling machines internationally, buyers must navigate various nuances in quality control that can differ by region.
-
Regional Standards: Different regions may have specific regulations and standards that suppliers must comply with. For example, in Europe, compliance with CE marking is mandatory, whereas, in Africa, the standards may vary significantly from one country to another. Buyers should familiarize themselves with these regional differences to avoid compliance issues.
-
Cultural Considerations: Understanding the cultural context of the supplier’s country can affect communication and expectations regarding quality control. For instance, suppliers in the Middle East may have different approaches to quality assurance than those in Europe. Building a relationship based on mutual understanding can facilitate smoother transactions.
-
Supply Chain Risks: International buyers should be aware of potential supply chain risks, such as delays or disruptions that can impact quality. Establishing clear communication channels and contingency plans with suppliers can help mitigate these risks.
In conclusion, a comprehensive understanding of the manufacturing processes and quality assurance practices for filling machine suppliers is crucial for B2B buyers. By focusing on these areas, buyers can make informed decisions that ensure they select suppliers capable of delivering high-quality, reliable products that meet their specific needs.
Practical Sourcing Guide: A Step-by-Step Checklist for ‘filling machine supplier’
This practical sourcing guide is designed to assist international B2B buyers in effectively procuring filling machines from reliable suppliers. By following this step-by-step checklist, businesses can ensure they select the right filling machine supplier that meets their specific operational needs and quality standards.
Step 1: Define Your Technical Specifications
Clearly outline the technical requirements for the filling machine you need. This includes determining the type of products you will be filling (liquids, powders, granules, etc.), the volume and speed of production, and any specific features such as automation or integration with existing systems.
– Why It Matters: Defining these specifications helps you narrow down potential suppliers who specialize in the type of machine that suits your needs.
Step 2: Research Potential Suppliers
Conduct thorough research to identify potential filling machine suppliers. Utilize online directories, industry trade shows, and business networks to compile a list of candidates.
– What to Look For: Focus on suppliers with a strong reputation in your industry. Check reviews and testimonials from previous customers to gauge their reliability and service quality.
Step 3: Evaluate Supplier Certifications
Verify that the suppliers you are considering hold relevant certifications, such as ISO, CE, or FDA approvals. These certifications ensure that the machines meet international safety and quality standards.
– Importance of Certifications: Suppliers with the right certifications are more likely to provide reliable and safe machines, which is crucial for maintaining compliance in your production processes.
Step 4: Request Detailed Proposals
Reach out to shortlisted suppliers and request detailed proposals, including technical specifications, pricing, lead times, and warranty terms. Make sure to ask for information on after-sales support and maintenance services.
– What to Compare: Use these proposals to compare not only costs but also the value-added services that each supplier offers, which can influence your total cost of ownership.
Step 5: Visit Supplier Facilities (if possible)
If feasible, arrange to visit the supplier’s manufacturing facility. This on-site evaluation allows you to assess their production capabilities, quality control processes, and overall operations.
– Why On-Site Visits Are Crucial: Meeting with the supplier face-to-face can enhance trust and provide deeper insights into their operational standards and commitment to quality.
Step 6: Negotiate Terms and Conditions
Once you have selected a preferred supplier, engage in negotiations regarding payment terms, delivery schedules, and service agreements. Ensure all terms are documented in a formal contract.
– Key Considerations: Pay attention to lead times and penalties for late delivery, as these can significantly impact your production timelines.
Step 7: Establish Communication Protocols
Set up clear communication channels and protocols with your chosen supplier. Determine who will be your point of contact for any queries or issues that arise during the procurement and installation process.
– Importance of Communication: Effective communication helps to quickly resolve any potential issues and ensures a smoother procurement process.
By following these steps, international B2B buyers can confidently navigate the procurement process for filling machines, ensuring they select suppliers that align with their operational needs and quality expectations.
Comprehensive Cost and Pricing Analysis for filling machine supplier Sourcing
What Are the Key Cost Components in Filling Machine Supplier Sourcing?
When sourcing filling machines, understanding the cost structure is essential for international B2B buyers. The main cost components include:
-
Materials: The quality and type of materials used in the construction of filling machines significantly influence the overall price. High-grade stainless steel, for example, may cost more but offers better durability and hygiene, which is crucial for food and beverage industries.
-
Labor: Labor costs vary by region and can greatly impact the pricing of filling machines. In regions with higher labor costs, such as Western Europe, expect to pay more compared to regions like South America or parts of Africa.
-
Manufacturing Overhead: This encompasses indirect costs associated with production, including utilities, rent, and administrative expenses. Suppliers with efficient manufacturing processes may offer more competitive pricing.
-
Tooling: Custom tooling for specialized filling machines can add to the upfront costs. If your production requires unique specifications, be prepared for additional expenses related to custom tooling.
-
Quality Control (QC): Ensuring that machines meet international standards can incur extra costs. Look for suppliers who provide certifications (ISO, CE) as these can be indicative of quality assurance practices.
-
Logistics: Shipping and handling costs can vary widely based on the location of the supplier and the destination. Understanding Incoterms is crucial as they define the responsibilities of buyers and sellers in shipping.
-
Margin: Supplier profit margins can vary significantly. It’s essential to inquire about pricing transparency to understand what factors contribute to the final price.
How Do Price Influencers Impact the Cost of Filling Machines?
Several factors can influence the pricing of filling machines:
-
Volume and Minimum Order Quantity (MOQ): Larger orders often lead to bulk pricing discounts. Suppliers may have minimum order quantities, so understanding your production needs is critical.
-
Specifications and Customization: Custom features can drive up costs. Be clear about your requirements to avoid unnecessary expenses.
-
Materials and Quality Certifications: Machines built from higher-quality materials and those that meet stringent quality certifications tend to be more expensive. Assess the trade-off between cost and quality for your specific needs.
-
Supplier Factors: The reputation and experience of the supplier can influence pricing. Established suppliers may charge a premium for their reliability and service.
-
Incoterms: Understanding Incoterms can help buyers manage logistics costs effectively. Terms such as FOB (Free on Board) or CIF (Cost, Insurance, and Freight) will define who bears the cost of shipping and insurance.
What Are the Best Buyer Tips for Negotiating Filling Machine Prices?
To ensure cost-efficiency in your sourcing process, consider the following tips:
-
Negotiate Wisely: Always negotiate prices, especially if you are placing large orders. Suppliers often have some flexibility in their pricing.
-
Evaluate Total Cost of Ownership (TCO): Consider not just the purchase price, but also maintenance, operational costs, and potential downtime. A slightly more expensive machine that requires less maintenance can be more cost-effective in the long run.
-
Research Local Suppliers: For buyers in Africa, South America, the Middle East, and Europe, sourcing from local suppliers can reduce shipping costs and lead times.
-
Stay Informed About Pricing Nuances: Be aware of fluctuations in material costs and labor rates in different regions, as these can impact supplier pricing.
-
Get Multiple Quotes: Always seek quotes from several suppliers to compare pricing and features. This helps in making informed decisions and negotiating better terms.
Disclaimer on Indicative Prices
Prices for filling machines can vary widely based on the factors discussed. It’s important to obtain detailed quotes from suppliers tailored to your specific needs and project requirements. Always ensure clarity in pricing to avoid unexpected costs in your sourcing journey.
Alternatives Analysis: Comparing filling machine supplier With Other Solutions
Introduction to Alternative Solutions for Filling Machines
When considering the procurement of filling machines, international B2B buyers must evaluate various solutions that can meet their operational needs. While traditional filling machine suppliers offer dedicated equipment, there are alternative technologies and methods that can also fulfill the requirements of different industries. This section compares filling machine suppliers with alternative solutions, helping buyers make informed decisions based on performance, cost, implementation ease, maintenance, and specific use cases.
Comparison Table of Filling Machine Supplier and Alternatives
Comparison Aspect | Filling Machine Supplier | Alternative 1: Manual Filling Systems | Alternative 2: Automated Filling Systems |
---|---|---|---|
Performance | High throughput; precise | Lower throughput; manual precision | Very high throughput; automated precision |
Cost | Moderate to high initial investment | Low initial cost; variable labor costs | High initial investment; lower variable costs |
Ease of Implementation | Requires professional installation | Easy to set up; minimal training needed | Complex setup; requires technical expertise |
Maintenance | Regular maintenance needed | Low maintenance; periodic checks | High maintenance; specialized technicians needed |
Best Use Case | Large-scale production | Small batches; startups | Large-scale, consistent production |
Detailed Breakdown of Alternatives
What are Manual Filling Systems and their Benefits?
Manual filling systems are a cost-effective alternative for businesses that operate on a smaller scale or require flexibility in their production processes. These systems often involve using hand-operated devices or simple gravity-fed solutions.
Pros:
– Cost-Effective: With low initial investment, they are ideal for small businesses or startups.
– Flexibility: Easily adaptable for various products and batch sizes.
Cons:
– Labor-Intensive: Requires more human resources, which can lead to higher long-term costs.
– Lower Efficiency: Not suitable for high-volume production due to slower throughput.
How do Automated Filling Systems Compare?
Automated filling systems are designed for high-volume production environments where speed and efficiency are paramount. These systems utilize sophisticated technology to fill products with minimal human intervention.
Pros:
– High Efficiency: Capable of processing large volumes quickly, reducing labor costs.
– Consistency: Provides uniform filling, which is critical for quality control.
Cons:
– High Initial Costs: Requires a significant upfront investment, which may not be feasible for smaller businesses.
– Complex Maintenance: Needs specialized technicians for repair and maintenance, increasing operational complexity.
Conclusion: Choosing the Right Filling Solution
For international B2B buyers, selecting the right filling solution involves assessing specific operational needs and resources. A filling machine supplier may offer the best performance for large-scale production, while manual filling systems are suitable for smaller operations or startups. Automated filling systems excel in high-volume environments but come with higher costs and maintenance requirements. By carefully analyzing these alternatives, buyers can align their choices with their production goals, budget constraints, and operational capabilities, ensuring they invest in a solution that meets their unique requirements.
Essential Technical Properties and Trade Terminology for filling machine supplier
What Are the Essential Technical Properties of Filling Machines?
When sourcing filling machines, understanding their technical specifications is crucial for making informed purchasing decisions. Here are several key properties that buyers should consider:
1. Material Grade
The material used in the construction of filling machines significantly impacts their durability and resistance to corrosion and wear. Common materials include stainless steel and food-grade plastics. For industries like food and beverage, adherence to sanitary standards is essential, as these materials must withstand cleaning processes and prevent contamination.
2. Tolerance Levels
Tolerance refers to the permissible limit or limits of variation in a physical dimension. In filling machines, tight tolerances ensure accurate filling volumes, which are critical for compliance with regulatory standards and maintaining product quality. For B2B buyers, understanding tolerance levels helps ensure that the machines will meet their production specifications and reduce waste.
3. Capacity
The capacity of a filling machine indicates the volume it can process within a certain timeframe. This specification is vital for businesses that require high throughput to meet market demand. Buyers should assess whether the machine’s capacity aligns with their production goals, as underperformance can lead to bottlenecks in operations.
4. Speed of Operation
Speed is a critical parameter that affects overall productivity. Filling machines are rated by their filling speed, typically measured in bottles per minute (BPM) or liters per hour (LPH). Buyers should evaluate their operational needs to choose a machine that balances speed with filling accuracy, ensuring efficiency without sacrificing quality.
5. Automation Level
Filling machines can be manual, semi-automatic, or fully automatic. The level of automation affects labor costs, efficiency, and consistency. Fully automatic machines, for instance, can significantly reduce human error and speed up production. Understanding the level of automation that fits your operation’s scale and budget is essential for maximizing ROI.
What Are Common Trade Terms Used in the Filling Machine Industry?
Familiarizing yourself with industry jargon is essential for effective communication and negotiation with suppliers. Here are several key terms:
1. OEM (Original Equipment Manufacturer)
OEM refers to companies that produce parts or equipment that may be marketed by another manufacturer. In the filling machine industry, understanding OEM relationships can help buyers identify reliable suppliers and negotiate better terms based on the manufacturer’s reputation and product quality.
2. MOQ (Minimum Order Quantity)
MOQ is the smallest number of units that a supplier is willing to sell. Knowing the MOQ is crucial for budget planning and inventory management. Buyers should inquire about MOQs when evaluating suppliers to ensure they can meet their production needs without overcommitting financially.
3. RFQ (Request for Quotation)
An RFQ is a document that a buyer sends to suppliers to request pricing information for specific products or services. When considering filling machines, submitting an RFQ can help buyers gather comparative pricing and specifications, enabling them to make more informed decisions.
4. Incoterms (International Commercial Terms)
Incoterms are a set of international trade terms that define the responsibilities of buyers and sellers regarding shipping, insurance, and tariffs. Understanding Incoterms is vital for international buyers, as they clarify who bears the risk at different stages of the shipping process, influencing total costs and logistics planning.
5. Lead Time
Lead time refers to the time it takes from placing an order to receiving the product. For filling machines, this period can vary based on customization, manufacturing capacity, and shipping. Buyers should consider lead times when planning production schedules to avoid delays in their operations.
By understanding these essential technical properties and trade terminology, international B2B buyers can navigate the complexities of sourcing filling machines more effectively, ensuring they make informed decisions that align with their operational goals.
Navigating Market Dynamics and Sourcing Trends in the filling machine supplier Sector
What Are the Key Market Dynamics and Trends Influencing the Filling Machine Supplier Sector?
The filling machine supplier sector is experiencing significant growth driven by various global factors. One of the primary drivers is the increasing demand for packaged goods across industries such as food and beverage, pharmaceuticals, and cosmetics. As urbanization continues to rise, particularly in Africa and South America, the need for efficient packaging solutions has surged. Furthermore, technological advancements, including automation and IoT integration, are reshaping how companies approach filling processes, enhancing efficiency and reducing operational costs.
Emerging trends in B2B sourcing include a shift toward multi-functional machinery that can handle various types of products and packaging formats. This versatility is increasingly important for suppliers aiming to meet diverse customer needs without the need for multiple machines. Additionally, data-driven decision-making is becoming crucial, as businesses utilize analytics to optimize supply chain management and enhance productivity. International buyers from regions like the Middle East and Europe are particularly focused on suppliers that can provide innovative technology and reliable support services, which can significantly influence their purchasing decisions.
How Can Sustainability and Ethical Sourcing Impact My Business in the Filling Machine Sector?
Sustainability and ethical sourcing have become paramount in the filling machine supplier sector, reflecting a growing awareness of environmental impact among businesses and consumers alike. The production and operation of filling machines can contribute to significant waste and energy consumption, necessitating a shift towards more sustainable practices. Buyers are increasingly seeking suppliers who adopt eco-friendly materials and processes, such as energy-efficient machinery and recyclable packaging options.
Incorporating ‘green’ certifications, such as ISO 14001 for environmental management, can serve as a key differentiator for suppliers. These certifications not only enhance a company’s reputation but also appeal to a broader customer base that prioritizes sustainability in their purchasing decisions. Furthermore, ethical supply chains that ensure fair labor practices and transparency are becoming essential, especially for international buyers who must navigate complex regulations and cultural expectations in their sourcing decisions.
What Is the Historical Context of the Filling Machine Supplier Sector?
The filling machine supplier sector has undergone significant transformation over the decades. Initially dominated by manual processes, the industry has evolved with technological advancements that began in the late 20th century. The introduction of automated systems revolutionized the filling processes, allowing for increased speed and precision.
In recent years, the focus has shifted towards smart technologies, such as AI and IoT, enabling real-time monitoring and data analytics. This evolution not only enhances operational efficiency but also allows suppliers to offer customized solutions that meet the specific needs of diverse markets. As the industry continues to innovate, understanding this historical context can provide valuable insights for international B2B buyers looking to make informed decisions.
Frequently Asked Questions (FAQs) for B2B Buyers of filling machine supplier
-
1. How do I choose the right filling machine supplier for my business?
Selecting the right filling machine supplier involves evaluating their experience, product range, and customer reviews. Start by researching suppliers that specialize in your industry, whether it’s food and beverage, pharmaceuticals, or cosmetics. Consider reaching out to existing customers for feedback on their experiences. Verify their certifications and quality assurance processes, and assess their capacity for customization to meet your specific needs. Lastly, ensure they have a reliable after-sales support system in place. -
2. What is the minimum order quantity (MOQ) for filling machines?
MOQs can vary significantly among suppliers. Many manufacturers set MOQs based on the type of machine and the complexity of customization required. Generally, expect MOQs to range from one unit for standard machines to several units for highly customized equipment. It’s advisable to discuss your requirements directly with the supplier to negotiate an MOQ that aligns with your business strategy, especially if you’re a smaller enterprise. -
3. What payment terms should I expect from filling machine suppliers?
Payment terms can differ widely among suppliers. Common arrangements include partial upfront payments (20-50%) followed by the balance upon delivery or prior to shipment. Some suppliers may offer credit terms based on your purchasing history. Always confirm payment methods accepted, such as bank transfers, letters of credit, or digital payment platforms. It’s critical to negotiate terms that protect your interests while ensuring the supplier’s security. -
4. How can I ensure quality assurance when sourcing filling machines internationally?
To ensure quality assurance, request detailed documentation of the supplier’s quality control processes. This includes certifications like ISO 9001 and relevant industry standards. Conducting factory audits, if feasible, can provide firsthand insight into their operations. Additionally, consider ordering a sample unit before committing to larger orders. Establishing a clear agreement on quality expectations in your contract can also safeguard against discrepancies. -
5. What are the logistics considerations when importing filling machines?
Logistics play a crucial role in the importation of filling machines. Factors to consider include shipping methods (air vs. sea), transit times, and customs clearance processes. Ensure that the supplier provides all necessary documentation for customs, including invoices, packing lists, and certificates of origin. Partnering with a reliable freight forwarder can streamline this process and help navigate any potential challenges, especially in regions with complex customs regulations. -
6. How customizable are filling machines for specific production needs?
Most filling machine suppliers offer a range of customization options to suit various production requirements. Customizations may include adjustments in filling volume, speed, and machine dimensions to fit existing production lines. Discuss your specific needs with the supplier early in the process to determine the extent of customization available. Some suppliers may also provide modular solutions that allow for future upgrades as your business grows. -
7. What should I know about the warranty and after-sales support for filling machines?
When sourcing filling machines, inquire about the warranty period and what it covers. A standard warranty typically covers defects in materials and workmanship for a specified duration, often one to two years. After-sales support is equally important; ensure the supplier offers technical support, spare parts availability, and maintenance services. Understanding these aspects can help you avoid unexpected downtime and additional costs post-purchase. -
8. How do I vet a potential filling machine supplier for reliability?
Vetting a potential supplier involves multiple steps. Start by checking their company history, including years in operation and industry reputation. Look for reviews and testimonials from previous customers, and consider their responsiveness during initial communications. Assess their production capabilities and visit their facilities if possible. Additionally, verify their certifications and ask for references to ensure they have a proven track record of reliability and quality in the market.
Important Disclaimer & Terms of Use
⚠️ Important Disclaimer
The information provided in this guide, including content regarding manufacturers, technical specifications, and market analysis, is for informational and educational purposes only. It does not constitute professional procurement advice, financial advice, or legal advice.
While we have made every effort to ensure the accuracy and timeliness of the information, we are not responsible for any errors, omissions, or outdated information. Market conditions, company details, and technical standards are subject to change.
B2B buyers must conduct their own independent and thorough due diligence before making any purchasing decisions. This includes contacting suppliers directly, verifying certifications, requesting samples, and seeking professional consultation. The risk of relying on any information in this guide is borne solely by the reader.
Strategic Sourcing Conclusion and Outlook for filling machine supplier
The landscape of filling machine suppliers is rapidly evolving, driven by advancements in technology and shifting market demands. For international B2B buyers, particularly those in Africa, South America, the Middle East, and Europe, strategic sourcing is essential. It not only optimizes supply chain efficiency but also enhances product quality and reduces costs. By leveraging local and global suppliers, businesses can secure competitive pricing and innovative solutions tailored to their specific needs.
Key takeaways include the importance of evaluating supplier capabilities, understanding regional compliance requirements, and fostering strong relationships with manufacturers. Buyers should prioritize suppliers who demonstrate flexibility and a commitment to sustainability, as these factors are increasingly influencing purchasing decisions.
Looking ahead, the future of filling machine suppliers will be shaped by the integration of automation and smart technology. International buyers are encouraged to stay informed about industry trends and emerging technologies that can enhance operational efficiency. Engaging with suppliers who are at the forefront of innovation will position businesses to capitalize on new market opportunities. Take proactive steps now to secure your supply chain and ensure your operations remain competitive in an ever-changing global marketplace.