Discover Top Tips to Choose a Frame Manufacturer (2025)
Introduction: Navigating the Global Market for frame manufacturer
In today’s global marketplace, finding a reliable frame manufacturer can pose significant challenges for international B2B buyers, especially those from regions like Africa, South America, the Middle East, and Europe. With a myriad of options available, the task of sourcing high-quality frames that meet specific business needs—be it for furniture, art, or industrial applications—can feel overwhelming. This comprehensive guide is designed to simplify that process, providing insights into various types of frames, their applications, and essential criteria for supplier vetting.
Throughout this guide, we will delve into the nuances of frame manufacturing, exploring factors such as material choices, design versatility, and cost considerations. Understanding these elements is crucial for making informed purchasing decisions that align with your business goals. Whether you’re looking for custom solutions or standard products, this resource empowers you with the knowledge necessary to navigate the complexities of the global market effectively.
By addressing common concerns and offering actionable strategies, this guide aims to equip B2B buyers with the tools needed to forge successful partnerships with frame manufacturers. You’ll learn how to assess supplier capabilities, negotiate favorable terms, and ultimately, secure products that enhance your offerings. Join us as we embark on this journey to streamline your sourcing efforts and elevate your business’s potential in the competitive landscape of frame manufacturing.
Understanding frame manufacturer Types and Variations
Type Name | Key Distinguishing Features | Primary B2B Applications | Brief Pros & Cons for Buyers |
---|---|---|---|
Aluminum Frame Manufacturers | Lightweight, corrosion-resistant, customizable designs | Aerospace, automotive, construction | Pros: Durable, versatile; Cons: Higher upfront costs compared to steel. |
Steel Frame Manufacturers | Strong, heavy-duty, cost-effective, available in various grades | Industrial buildings, furniture, machinery | Pros: High strength, lower material costs; Cons: Prone to rust without treatment. |
Plastic Frame Manufacturers | Lightweight, resistant to chemicals, various colors and styles | Consumer goods, electronics, packaging | Pros: Cost-effective, lightweight; Cons: Less durable than metal frames. |
Wood Frame Manufacturers | Aesthetic appeal, renewable material, customizable finishes | Furniture, interior design, art framing | Pros: Eco-friendly, versatile; Cons: Vulnerable to moisture and pests. |
Composite Frame Manufacturers | Combination of materials for enhanced properties | Sports equipment, high-performance vehicles | Pros: Lightweight, strong; Cons: Can be expensive, requires specialized manufacturing. |
What Are the Characteristics of Aluminum Frame Manufacturers?
Aluminum frame manufacturers produce lightweight and corrosion-resistant frames that are ideal for various industries, including aerospace and automotive. Their customizable designs cater to specific requirements, making them suitable for projects where weight savings and durability are essential. B2B buyers should consider the upfront costs, which may be higher than steel options, but the long-term benefits of durability and low maintenance can justify the investment.
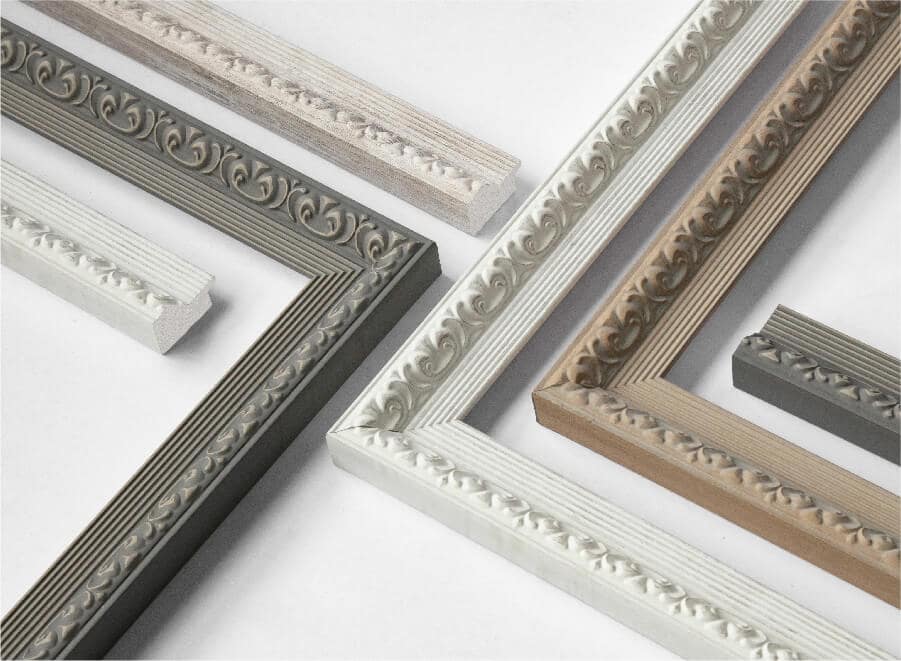
A stock image related to frame manufacturer.
How Do Steel Frame Manufacturers Stand Out?
Steel frame manufacturers are known for producing strong and heavy-duty frames, often utilized in industrial buildings and machinery. The cost-effectiveness of steel, combined with its high strength, makes it a popular choice for large-scale projects. Buyers should be mindful of the potential for rust, which necessitates protective treatments, but the overall lower material costs can make steel an attractive option for budget-conscious businesses.
What Advantages Do Plastic Frame Manufacturers Offer?
Plastic frame manufacturers focus on creating lightweight and chemically resistant frames, which are prevalent in consumer goods and packaging applications. The affordability and variety of styles available make plastic frames appealing for businesses looking to reduce costs without sacrificing functionality. However, buyers should note that while plastic frames are cost-effective, they may not offer the same level of durability as metal frames.
Why Choose Wood Frame Manufacturers?
Wood frame manufacturers provide aesthetically pleasing options that are often used in furniture and interior design. As a renewable material, wood appeals to environmentally conscious businesses. Customizable finishes allow for a unique touch in various applications. However, buyers must consider the potential vulnerabilities of wood to moisture and pests, which may require additional maintenance and care.
What Are the Benefits of Composite Frame Manufacturers?
Composite frame manufacturers specialize in creating frames that combine multiple materials to enhance performance characteristics. These frames are commonly used in high-performance vehicles and sports equipment, where strength and weight are critical. While they offer significant advantages in terms of durability and performance, the specialized manufacturing processes can lead to higher costs. B2B buyers should assess their specific application needs to determine if the investment in composite frames aligns with their business goals.
Related Video: steel structure construction process step by step in site / skelton frame
Key Industrial Applications of frame manufacturer
Industry/Sector | Specific Application of Frame Manufacturer | Value/Benefit for the Business | Key Sourcing Considerations for this Application |
---|---|---|---|
Construction | Structural Frames for Buildings | Enhanced stability and safety of structures | Local regulations, material certifications, and lead times |
Automotive | Chassis and Frame Components | Improved durability and performance of vehicles | Quality control, compatibility with existing systems, and cost-effectiveness |
Renewable Energy | Frames for Solar Panels | Increased efficiency and longevity of energy systems | Material sourcing, resistance to environmental conditions, and scalability |
Electronics | Enclosures and Racks for Equipment | Protection of sensitive components and improved organization | Customization options, thermal management, and compliance with industry standards |
Aerospace | Aircraft Frames and Structural Components | Weight reduction and enhanced aerodynamics | Regulatory compliance, material certifications, and precision engineering |
How is Frame Manufacturing Applied in Construction?
In the construction industry, frame manufacturers produce structural frames that provide the backbone for buildings. These frames are crucial for ensuring the stability and safety of structures, particularly in regions prone to seismic activity or extreme weather. International buyers, especially from Africa and South America, must consider local regulations and material certifications when sourcing frames to ensure compliance and safety. Additionally, lead times can be critical, so establishing reliable partnerships with manufacturers who understand regional challenges is essential.
What Role Does Frame Manufacturing Play in the Automotive Sector?
Frame manufacturers supply chassis and frame components that are vital for the automotive industry. These components must be durable and lightweight to enhance vehicle performance and fuel efficiency. For B2B buyers in Europe and the Middle East, sourcing high-quality frames involves rigorous quality control processes and ensuring compatibility with existing vehicle systems. Cost-effectiveness is also a key consideration, as buyers aim to balance quality with budget constraints to remain competitive in the market.
How are Frames Used in Renewable Energy Applications?
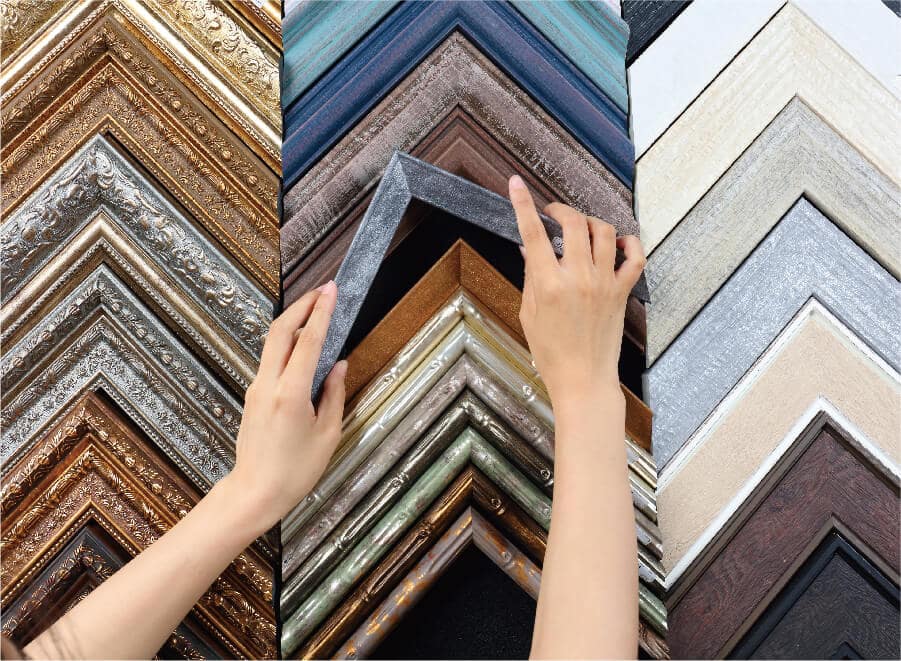
A stock image related to frame manufacturer.
In the renewable energy sector, frame manufacturers create frames for solar panels that optimize energy capture and ensure longevity under various environmental conditions. These frames must be resistant to corrosion and capable of withstanding harsh weather, making material sourcing a critical factor for international buyers, particularly in regions with extreme climates. Scalability is another important consideration, as businesses may need to expand their solar installations over time, requiring frames that can accommodate growth.
What is the Importance of Frame Manufacturing in Electronics?
In the electronics industry, frame manufacturers produce enclosures and racks that protect sensitive equipment from environmental hazards and facilitate efficient organization. These frames often require customization to meet specific thermal management needs and industry compliance standards. B2B buyers, particularly in Europe, must prioritize sourcing from manufacturers who can provide tailored solutions while ensuring adherence to stringent safety and quality regulations.
How Does Frame Manufacturing Contribute to the Aerospace Industry?
In aerospace, frame manufacturers supply aircraft frames and structural components designed to reduce weight while enhancing aerodynamics. This is critical for improving fuel efficiency and overall aircraft performance. International buyers in this sector must navigate complex regulatory compliance and seek manufacturers with the expertise to meet precise engineering requirements. Material certifications are also essential to ensure that components can withstand the demanding conditions of aerospace applications.
Related Video: FANUC Industrial Robots | AUDI Case Study
3 Common User Pain Points for ‘frame manufacturer’ & Their Solutions
Scenario 1: Inconsistent Quality in Frame Manufacturing
The Problem:
International B2B buyers often face the challenge of inconsistent quality in frame manufacturing, particularly when sourcing from different suppliers across regions like Africa, South America, the Middle East, and Europe. This inconsistency can lead to significant issues, such as increased costs due to returns, project delays, and damage to reputation when products do not meet the expected standards. Buyers might receive frames that vary in material quality, finish, or dimensions, which can disrupt their production schedules and impact customer satisfaction.
The Solution:
To mitigate quality inconsistencies, buyers should prioritize establishing strong relationships with reputable frame manufacturers who have a proven track record. It is crucial to conduct thorough due diligence, including checking references, reviewing past projects, and requesting samples before placing large orders. Buyers should also implement clear quality specifications and standards in their contracts, which outline the required materials, dimensions, and tolerances. Regular quality audits and on-site inspections can further ensure compliance with these standards. Additionally, leveraging technology such as 3D modeling can help visualize the final product, reducing the likelihood of discrepancies.
Scenario 2: Lengthy Lead Times Affecting Project Timelines
The Problem:
Another significant pain point for B2B buyers in the frame manufacturing sector is lengthy lead times, which can severely affect project timelines. Many manufacturers may struggle with high demand, limited resources, or logistical challenges, leading to delays in production and delivery. This situation can be particularly problematic for businesses that operate on tight schedules, where any delay can result in financial losses or missed opportunities.
The Solution:
To address lead time issues, buyers should engage in proactive planning and communication with frame manufacturers. By understanding the manufacturer’s production capacity and peak times, buyers can place orders well in advance, allowing for a buffer period. It’s also beneficial to explore partnerships with multiple manufacturers to diversify supply chains, which can reduce dependency on a single source and enhance flexibility. Establishing a clear timeline for production milestones and incorporating penalties for delays in contracts can incentivize manufacturers to adhere to agreed schedules. Finally, utilizing local suppliers or manufacturers closer to the target market can significantly reduce shipping times and logistics complexities.
Scenario 3: Difficulty in Customization and Design Adaptation
The Problem:
B2B buyers often encounter difficulties when seeking customized frames to meet specific project requirements. Frame manufacturers may offer limited customization options, leading to frustration when buyers have unique design needs that cannot be accommodated. This challenge is particularly prevalent in industries like architecture and interior design, where bespoke solutions are essential for project success.
The Solution:
To overcome customization challenges, buyers should clearly articulate their design requirements from the outset. Engaging with manufacturers who specialize in custom solutions can also be beneficial. Buyers should provide detailed specifications, including materials, dimensions, and design aesthetics, and may consider collaborating with manufacturers during the design phase to ensure feasibility. Leveraging design software or tools that allow for virtual prototyping can also help bridge the gap between concept and final product. Additionally, establishing a feedback loop where buyers can review prototypes before full production can ensure that the final frames meet expectations. By fostering open communication and collaboration, buyers can enhance the customization process and achieve the desired outcomes for their projects.
Strategic Material Selection Guide for frame manufacturer
When selecting materials for frame manufacturing, international B2B buyers must consider various factors that can significantly influence product performance, cost, and compliance with regional standards. Below, we analyze four common materials used in frame manufacturing: aluminum, steel, wood, and composite materials. Each material has unique properties, advantages, disadvantages, and considerations that are particularly relevant for buyers from Africa, South America, the Middle East, and Europe.
What are the Key Properties of Aluminum in Frame Manufacturing?
Aluminum is a lightweight metal known for its excellent corrosion resistance and thermal conductivity. It typically has a temperature rating up to 600°F (315°C) and can withstand moderate pressure. Aluminum frames are often used in applications where weight reduction is critical, such as in transportation and aerospace.
Pros and Cons of Aluminum:
– Advantages: Aluminum is highly durable, resistant to rust, and offers a good strength-to-weight ratio. Its manufacturing process is relatively straightforward, allowing for intricate designs.
– Disadvantages: The primary drawback is its cost, which is generally higher than steel. Additionally, aluminum can be less strong than some steel grades, limiting its use in heavy-load applications.
Impact on Application:
Aluminum frames are compatible with various media, including water and air, making them suitable for HVAC systems and structural applications.
Considerations for International Buyers:
Buyers should be aware of compliance with standards such as ASTM B221 for aluminum extrusions. In Europe, EN 573-3 outlines the chemical composition of aluminum alloys, which is crucial for quality assurance.
How Does Steel Compare as a Material for Frame Manufacturing?
Steel is a robust material known for its high tensile strength and durability. It can withstand high temperatures (up to 1,500°F or 815°C) and is highly resistant to deformation under load.
Pros and Cons of Steel:
– Advantages: Steel frames offer exceptional strength and are cost-effective compared to aluminum. They are ideal for heavy-duty applications and can be easily welded and fabricated.
– Disadvantages: Steel is prone to corrosion, requiring protective coatings or treatments. It is also heavier than aluminum, which may be a consideration in specific applications.
Impact on Application:
Steel frames are suitable for structural applications, including buildings and bridges, due to their load-bearing capacity.
Considerations for International Buyers:
Compliance with standards such as ASTM A36 for carbon steel is essential. In Europe, buyers should consider EN 10025, which specifies technical delivery conditions for structural steel.
What Are the Benefits of Using Wood in Frame Manufacturing?
Wood is a traditional material known for its aesthetic appeal and natural insulation properties. It is typically used in applications where appearance is essential, such as furniture and decorative frames.
Pros and Cons of Wood:
– Advantages: Wood is renewable, offers good thermal insulation, and can be less expensive than metals. It is also easy to work with and can be shaped into various designs.
– Disadvantages: Wood is susceptible to moisture, pests, and warping. Its strength is generally lower than that of metals, limiting its use in structural applications.
Impact on Application:
Wood frames are ideal for indoor applications where humidity and temperature are controlled. They are not suitable for outdoor use without proper treatment.
Considerations for International Buyers:
Buyers should ensure compliance with local regulations regarding sustainable sourcing and treatment of wood. Standards such as FSC (Forest Stewardship Council) certification may be relevant.
How Do Composite Materials Enhance Frame Manufacturing?
Composite materials, often made from a combination of polymers and reinforcing fibers, offer unique properties such as lightweight and high strength. They can withstand a wide range of temperatures and pressures, depending on their formulation.
Pros and Cons of Composites:
– Advantages: Composites are corrosion-resistant, lightweight, and can be tailored for specific applications. They often provide superior performance in harsh environments.
– Disadvantages: The manufacturing process can be complex and costly, which may deter some buyers. Additionally, composites may not be recyclable, raising environmental concerns.
Impact on Application:
Composite frames are excellent for applications requiring high strength-to-weight ratios, such as in automotive and aerospace industries.
Considerations for International Buyers:
Buyers should be aware of the varying standards for composites across regions, including ASTM D638 for tensile properties and ISO 527 for plastics.
Summary of Material Considerations for Frame Manufacturing
Material | Typical Use Case for frame manufacturer | Key Advantage | Key Disadvantage/Limitation | Relative Cost (Low/Med/High) |
---|---|---|---|---|
Aluminum | HVAC systems, transportation frames | Lightweight and corrosion-resistant | Higher cost compared to steel | Medium |
Steel | Structural applications, bridges | High strength and cost-effective | Prone to corrosion | Low |
Wood | Furniture, decorative frames | Aesthetic appeal and insulation | Susceptible to moisture and pests | Low |
Composite | Automotive, aerospace | Lightweight and customizable | Complex manufacturing process | High |
This guide provides a comprehensive overview of material selection for frame manufacturers, equipping international B2B buyers with the insights necessary to make informed decisions based on their specific application needs and regional compliance requirements.
In-depth Look: Manufacturing Processes and Quality Assurance for frame manufacturer
What Are the Main Stages of Manufacturing for Frame Manufacturers?
Manufacturing frames involves several critical stages, each essential for ensuring the quality and durability of the final product. The main stages include material preparation, forming, assembly, and finishing.
-
Material Preparation
The first step in frame manufacturing is sourcing and preparing materials, which typically include metals (like aluminum or steel), plastics, or wood. Quality control starts here, as the raw materials must meet specific standards. Suppliers often conduct tests to verify the material’s properties, such as tensile strength and corrosion resistance. B2B buyers should inquire about the suppliers’ sourcing practices and request material certifications to ensure compliance with international standards. -
Forming
During the forming stage, raw materials are shaped into the desired frame structures. Techniques may include extrusion for metals, molding for plastics, or cutting and joining for wood. Advanced technologies, such as CNC machining and laser cutting, are commonly employed to achieve precision. It is crucial for buyers to understand the forming techniques used, as they can significantly affect the product’s performance and aesthetics. -
Assembly
After forming, the various components are assembled. This stage often involves welding, riveting, or using adhesives, depending on the materials. Quality assurance is vital here; manufacturers should have checks in place to ensure that joints are strong and meet design specifications. Buyers should verify if the manufacturer has documented assembly procedures and if they conduct regular training for assembly personnel. -
Finishing
The finishing stage enhances both the appearance and durability of the frames. This may involve surface treatments like painting, powder coating, or anodizing for metals, and varnishing for wood. Each finishing process has specific quality requirements. Buyers should inquire about the finishing techniques used and any tests conducted to ensure longevity and resistance to environmental factors.
How Is Quality Assurance Implemented in Frame Manufacturing?
Quality assurance (QA) is integral to the manufacturing process and involves adherence to international and industry-specific standards.
-
International Standards
Many frame manufacturers comply with ISO 9001, which sets out the criteria for a quality management system. This certification ensures that the manufacturer consistently meets customer and regulatory requirements. Additionally, compliance with CE marking for products sold in Europe is essential, indicating that the products meet EU safety, health, and environmental protection standards. -
Industry-Specific Standards
Depending on the application of the frames, manufacturers may also need to adhere to standards like API (American Petroleum Institute) for oil and gas applications, or other industry-specific regulations. B2B buyers should confirm that the manufacturer has the necessary certifications relevant to their specific sector.
What Are the Key Quality Control Checkpoints in Frame Manufacturing?
Quality control (QC) checkpoints are critical to ensuring that every stage of the manufacturing process meets the required standards.
-
Incoming Quality Control (IQC)
IQC is the first checkpoint, focusing on the quality of raw materials upon arrival. Manufacturers typically conduct inspections and tests to verify that the materials meet specified standards before they are used in production. -
In-Process Quality Control (IPQC)
This involves monitoring the manufacturing process itself. Regular inspections are conducted at various stages of production to ensure that all processes are followed correctly and that any defects are identified early. -
Final Quality Control (FQC)
FQC occurs after the assembly and finishing stages. This comprehensive inspection checks for dimensional accuracy, surface finish, and overall product functionality. Testing methods may include visual inspections, dimensional checks, and functional tests based on the frame’s intended use.
How Can B2B Buyers Verify Supplier Quality Control?
Verifying a supplier’s quality control processes is essential for B2B buyers, especially when sourcing from international manufacturers.
-
Audits and Assessments
Conducting regular audits is a reliable method to assess a manufacturer’s quality control practices. Buyers can request an audit report to understand the supplier’s adherence to quality standards and any areas for improvement. -
Quality Reports and Certifications
Manufacturers should provide documentation of their quality control measures, including test results and certifications. Buyers should review these documents to ensure compliance with relevant standards. -
Third-Party Inspections
Engaging third-party inspection agencies can add an additional layer of assurance. These agencies provide unbiased assessments of the manufacturing process and product quality, which can be especially useful for international transactions.
What Are the Quality Control Nuances for International B2B Buyers?
B2B buyers from Africa, South America, the Middle East, and Europe must consider several nuances regarding quality control:
-
Cultural Differences in Quality Standards
Different regions may have varying expectations regarding quality. Buyers should familiarize themselves with local standards and practices to ensure that they align with their own expectations. -
Logistical Challenges
Shipping products internationally can introduce risks, such as damage during transit. Buyers should discuss packaging and shipping standards with suppliers to minimize these risks. -
Regulatory Compliance
Understanding the regulatory requirements of the buyer’s home country is crucial. Buyers should ensure that the products comply with local regulations, which may differ significantly from those in the supplier’s country.
Conclusion
In summary, a thorough understanding of the manufacturing processes and quality assurance practices in frame manufacturing is essential for international B2B buyers. By focusing on the key stages of manufacturing, relevant quality standards, and effective verification methods, buyers can make informed decisions and select reliable suppliers that meet their specific needs.
Practical Sourcing Guide: A Step-by-Step Checklist for ‘frame manufacturer’
To effectively procure from a frame manufacturer, international B2B buyers need a structured approach to ensure they select the right supplier and product. This guide outlines essential steps to streamline the sourcing process, focusing on key considerations for buyers from Africa, South America, the Middle East, and Europe.
Step 1: Define Your Technical Specifications
Clearly outlining your technical specifications is critical before approaching potential suppliers. This includes details such as material types, frame dimensions, load-bearing capacities, and design requirements. By having well-defined parameters, you can communicate your needs effectively and reduce the likelihood of misunderstandings during the procurement process.
Step 2: Research Market Trends and Supplier Options
Understanding current market trends is essential for making informed purchasing decisions. Research various manufacturers to identify those that align with your requirements, focusing on their product offerings, pricing strategies, and market presence. Look for manufacturers that cater specifically to your region to ensure compliance with local regulations and standards.
Step 3: Evaluate Potential Suppliers
Before making any commitments, thoroughly vet potential suppliers. Request comprehensive company profiles, case studies, and references from previous clients in similar industries. Pay attention to their production capabilities and quality assurance processes to ensure they meet your specifications and standards.
- Check Certifications: Verify any industry certifications or quality standards the manufacturer holds, such as ISO 9001, to ensure they adhere to international quality benchmarks.
Step 4: Request Samples and Prototypes
Once you have narrowed down your list of suppliers, request samples or prototypes of the frames you intend to purchase. This step allows you to assess the quality, durability, and overall craftsmanship of the products firsthand. Evaluating samples helps prevent future issues related to quality and ensures that the products meet your expectations.
Step 5: Negotiate Terms and Conditions
Engage in discussions regarding pricing, payment terms, delivery schedules, and warranty provisions. Clear negotiations can help establish a mutually beneficial relationship. Ensure that you address potential risks, such as delays in delivery or issues with product quality, by incorporating penalty clauses or performance guarantees in the contract.
Step 6: Assess Logistics and Shipping Considerations
Understanding the logistics involved in transporting frames is vital, especially for international transactions. Discuss shipping options, lead times, and any potential customs requirements. Consider the location of the supplier and the associated shipping costs to avoid unexpected expenses and delays.
Step 7: Establish a Communication Plan
Develop a clear communication strategy with your chosen supplier. This should include regular updates on production status, shipment tracking, and any potential issues that may arise. Effective communication fosters transparency and builds trust between you and the manufacturer, ensuring a smoother procurement process.
By following this checklist, B2B buyers can streamline their sourcing process and make informed decisions when procuring frames from manufacturers. Each step is designed to enhance the buyer’s ability to select a reliable supplier while ensuring product quality and compliance with regional requirements.
Comprehensive Cost and Pricing Analysis for frame manufacturer Sourcing
What Are the Key Cost Components in Frame Manufacturing?
Understanding the cost structure of frame manufacturing is essential for international B2B buyers. The primary cost components include:
-
Materials: The type of materials used significantly influences the overall cost. Common materials include wood, metal, and plastic, each varying in price depending on quality and source. Sustainable materials may come at a premium but can enhance brand value.
-
Labor: Labor costs vary by region and skill level. Countries with lower labor costs may provide competitive pricing but could compromise on quality. Understanding local wage standards can help buyers gauge the labor component in pricing.
-
Manufacturing Overhead: This includes costs associated with production facilities, utilities, equipment maintenance, and indirect labor. Overhead can vary widely based on the manufacturer’s operational efficiency and location.
-
Tooling: Custom tooling for specific frame designs can incur significant upfront costs. However, these costs can be amortized over high-volume orders, making them more economical in the long run.
-
Quality Control (QC): Investing in rigorous quality control processes ensures product consistency and reduces the likelihood of defects. This can add to the initial cost but may lead to savings by minimizing returns and dissatisfaction.
-
Logistics: Shipping and handling costs, including freight, insurance, and customs duties, must be factored into the total cost. These can vary significantly based on the shipping method and destination.
-
Margin: Manufacturers typically add a profit margin to cover their costs and generate profit. Understanding industry standards for margin can help buyers negotiate better pricing.
How Do Price Influencers Affect Frame Manufacturing Costs?
Several factors influence the pricing of frame manufacturing:
-
Volume and Minimum Order Quantity (MOQ): Higher order volumes often lead to lower per-unit costs. Manufacturers may offer discounts for bulk purchases, making it advantageous for buyers to consolidate orders.
-
Specifications and Customization: Custom designs or specific material requirements can increase costs. Clear communication of specifications can help avoid unexpected price hikes.
-
Material Quality and Certifications: Higher quality materials and certifications (e.g., ISO, CE) often lead to increased costs. However, they can also enhance product appeal and marketability.
-
Supplier Factors: The reliability and reputation of the supplier can impact pricing. Established suppliers may charge more for their expertise and service, while less-known companies might offer lower prices but with higher risks.
-
Incoterms: Understanding Incoterms is crucial for international buyers as they define the responsibilities of buyers and sellers in shipping. Choosing the right Incoterm can significantly affect the total landed cost of products.
What Buyer Tips Can Help in Negotiating Frame Manufacturing Prices?
For international B2B buyers, particularly from diverse regions such as Africa, South America, the Middle East, and Europe, the following tips can enhance cost efficiency:
-
Negotiate Terms: Always negotiate pricing, payment terms, and delivery schedules. Suppliers may be willing to offer better terms to secure large or repeat orders.
-
Assess Total Cost of Ownership (TCO): Beyond initial purchase price, consider the total cost of ownership, which includes maintenance, shipping, and potential tariffs. This holistic view can lead to better long-term decisions.
-
Stay Informed on Market Trends: Keep abreast of market trends in materials and labor to understand pricing fluctuations. This knowledge can provide leverage in negotiations.
-
Build Relationships: Establishing strong relationships with suppliers can lead to better pricing and service. A trusted supplier may offer favorable terms and prioritize your orders.
-
Explore Multiple Suppliers: Don’t settle for the first quote. Solicit quotes from multiple suppliers to ensure competitive pricing and service levels.
What Should Buyers Be Aware of Regarding Indicative Prices?
While it’s essential to understand cost structures and pricing factors, buyers should be aware that indicative prices can fluctuate based on market conditions, exchange rates, and geopolitical factors. Always seek updated quotes and clarify the validity period of pricing to avoid surprises in your procurement process.
Alternatives Analysis: Comparing frame manufacturer With Other Solutions
In the competitive landscape of frame manufacturing, B2B buyers often explore various solutions to meet their operational needs. Understanding the alternatives available can help businesses make informed decisions that align with their specific requirements. Below, we compare ‘frame manufacturer’ with two viable alternatives: 3D Printing and Traditional Woodworking.
Comparison Table
Comparison Aspect | Frame Manufacturer | 3D Printing | Traditional Woodworking |
---|---|---|---|
Performance | High durability and precision | Customizable designs, but variable quality | Strong, traditional craftsmanship |
Cost | Moderate initial investment | High initial costs, but low long-term | Variable based on materials and labor |
Ease of Implementation | Requires setup and training | Requires skilled operators and software | Familiar processes for skilled artisans |
Maintenance | Regular inspections and repairs | Minimal maintenance required | Regular maintenance needed for tools |
Best Use Case | Mass production of frames | Custom, low-volume production | Artisan frames and bespoke designs |
What Are the Advantages and Disadvantages of 3D Printing as an Alternative to Frame Manufacturing?
Pros:
3D printing allows for high levels of customization, enabling businesses to create unique frame designs tailored to specific needs. It is particularly advantageous for low-volume production, where the cost of traditional manufacturing would be prohibitive. Additionally, the technology can significantly reduce waste, as materials are added layer by layer.
Cons:
The initial investment in 3D printing technology can be substantial, including costs for printers and training. Moreover, the quality of the output can vary significantly based on the machine and materials used, which may not always meet the durability standards of traditional frame manufacturing.
What Are the Key Benefits and Drawbacks of Traditional Woodworking Compared to Frame Manufacturing?
Pros:
Traditional woodworking offers a level of craftsmanship and aesthetic appeal that can be highly desirable for bespoke projects. Skilled artisans can create unique, high-quality frames that reflect intricate designs and durability. This method is often favored for luxury markets where quality is paramount.
Cons:
The costs can vary widely, depending on the quality of materials and the artisans’ labor. Additionally, the production process can be time-consuming, making it less suitable for mass production compared to frame manufacturing. Maintenance of tools and equipment is also necessary, adding to long-term operational costs.
How Can B2B Buyers Choose the Right Solution for Their Needs?
Selecting the right solution requires a thorough analysis of specific business needs, including production volume, budget constraints, and the desired quality of the final product. For businesses focused on high-volume production with consistent quality, a frame manufacturer may be the most suitable choice. On the other hand, for those seeking unique, custom designs in lower quantities, 3D printing could prove beneficial. Lastly, businesses that prioritize craftsmanship and aesthetic appeal may find traditional woodworking to be the best fit. By weighing the pros and cons of each alternative, B2B buyers can make an informed decision that aligns with their operational goals and market demands.
Essential Technical Properties and Trade Terminology for frame manufacturer
What Are the Key Technical Properties for Frame Manufacturers?
When sourcing frames for various applications, understanding the essential technical properties is crucial for international B2B buyers. Here are the critical specifications that frame manufacturers should meet:
1. Material Grade
Material grade refers to the classification of the materials used in frame manufacturing, such as aluminum, steel, or composite materials. Each material has unique properties such as strength, weight, and corrosion resistance, which can significantly impact the frame’s performance and longevity. Selecting the appropriate material grade ensures that the frames meet the required standards for durability and safety, especially in demanding environments.
2. Tolerance
Tolerance defines the acceptable limits of variation in the dimensions of the frames. It is crucial for ensuring that the frames fit precisely into their intended applications, whether for construction, furniture, or automotive use. Tighter tolerances often result in higher costs, but they are essential in applications where precision is critical. Understanding the necessary tolerances helps buyers avoid issues related to misalignment or structural integrity.
3. Load Capacity
Load capacity indicates the maximum weight that a frame can support without failure. This property is particularly important in applications like scaffolding, furniture, and machinery. Buyers must assess the load requirements for their specific use cases to select frames that not only meet safety standards but also enhance operational efficiency.
4. Surface Finish
The surface finish of a frame affects both its aesthetic appeal and functional performance. Common finishes include powder coating, anodizing, and galvanization, each offering different levels of protection against corrosion and wear. A good surface finish can extend the life of the frame and reduce maintenance costs, making it a vital consideration for buyers.
5. Welding and Joining Techniques
The methods used to weld or join frame components significantly influence the structural integrity and performance of the final product. Different techniques, such as MIG welding or TIG welding, provide various strengths and characteristics. Buyers should consider the joining techniques used to ensure that they meet the operational demands of their applications.
What Are Common Trade Terms in Frame Manufacturing?
Familiarity with industry jargon is essential for effective communication and negotiation in frame manufacturing. Here are some common trade terms that B2B buyers should know:
1. OEM (Original Equipment Manufacturer)
An OEM refers to a company that produces parts or equipment that may be marketed by another manufacturer. In frame manufacturing, OEMs can provide custom frames tailored to specific requirements. Understanding OEM relationships can help buyers identify potential suppliers who can deliver specialized products.
2. MOQ (Minimum Order Quantity)
MOQ is the smallest number of units that a supplier is willing to sell. This term is crucial for buyers to understand, as it impacts inventory management and budgeting. Knowing the MOQ helps businesses plan their purchases and avoid overstocking or stockouts.
3. RFQ (Request for Quotation)
An RFQ is a document sent to suppliers to solicit price quotes for specific products or services. For frame manufacturers, issuing an RFQ can help buyers compare prices, terms, and conditions across multiple suppliers, ensuring they make informed purchasing decisions.
4. Incoterms (International Commercial Terms)
Incoterms are a set of predefined commercial terms published by the International Chamber of Commerce (ICC) that define the responsibilities of buyers and sellers in international transactions. Understanding these terms is essential for managing shipping costs, insurance, and liability, particularly when sourcing frames from overseas.
5. Lead Time
Lead time refers to the amount of time it takes from placing an order until the goods are received. This term is vital for planning and inventory management, as longer lead times can affect production schedules and project timelines. Buyers should always inquire about lead times to ensure timely delivery of frames.
By grasping these technical properties and trade terms, international B2B buyers can make more informed decisions, ensuring they select the right frames for their applications while optimizing cost and performance.
Navigating Market Dynamics and Sourcing Trends in the frame manufacturer Sector
What Are the Current Trends Impacting the Frame Manufacturer Market?
The frame manufacturing sector is experiencing significant transformations driven by globalization, technological advancements, and evolving consumer preferences. Key trends include the increasing demand for custom and personalized frames, which allow brands to differentiate themselves in competitive markets. Additionally, the proliferation of e-commerce platforms is reshaping how buyers interact with suppliers, making it essential for manufacturers to develop robust online presence and supply chain strategies.
Emerging technologies such as automation and artificial intelligence are also influencing production processes, leading to improved efficiency and reduced lead times. For international B2B buyers, particularly from Africa, South America, the Middle East, and Europe, understanding these technological advancements is critical for competitive sourcing. Moreover, the shift towards digital solutions for inventory management and customer relationship management is enhancing transparency and traceability in the supply chain, enabling buyers to make informed purchasing decisions.
The market dynamics are further shaped by geopolitical factors and trade agreements, which affect import/export tariffs and regulations. Buyers must stay updated on these developments to navigate potential risks and opportunities effectively. For instance, the African Continental Free Trade Area (AfCFTA) is creating new opportunities for regional sourcing, while European buyers are increasingly looking towards sustainable sourcing options in response to regulatory pressures and consumer demand.
How Does Sustainability Impact Sourcing in the Frame Manufacturing Sector?
Sustainability has become a critical focal point for B2B buyers in the frame manufacturing sector. The environmental impact of manufacturing processes is under increasing scrutiny, prompting companies to adopt sustainable practices. This includes sourcing raw materials responsibly, minimizing waste, and reducing carbon footprints. Ethical supply chains are not just a trend but a necessity for businesses aiming to enhance their brand reputation and meet consumer expectations.
Buyers should prioritize suppliers that demonstrate commitment to sustainability through certifications such as Forest Stewardship Council (FSC) for wood products and ISO 14001 for environmental management systems. Additionally, the use of ‘green’ materials, such as recycled metals and sustainably sourced wood, is gaining traction. These materials not only contribute to environmental conservation but can also be appealing to consumers looking for eco-friendly products.
By aligning sourcing strategies with sustainability goals, B2B buyers can foster long-term partnerships with manufacturers that share their values. This approach not only supports corporate social responsibility initiatives but can also lead to cost savings through improved efficiency and waste reduction.
What Is the Historical Context of the Frame Manufacturing Sector?
The frame manufacturing sector has evolved significantly from traditional craftsmanship to modern industrial production. Initially, frame making was a labor-intensive process, heavily reliant on artisanal skills. As demand increased, particularly during the 20th century, manufacturers began to adopt mechanization, which allowed for mass production and greater consistency in quality.
The late 20th and early 21st centuries marked a pivotal shift as globalization opened new markets and increased competition. Manufacturers began to explore offshore production to reduce costs, leading to complex supply chains that spanned multiple continents. This evolution has set the stage for today’s dynamic market, where technological advancements and sustainability practices are reshaping the landscape, providing opportunities for innovative and responsible sourcing strategies for B2B buyers worldwide.
Frequently Asked Questions (FAQs) for B2B Buyers of frame manufacturer
- How do I find a reliable frame manufacturer for my business?
Finding a reliable frame manufacturer involves thorough research and vetting. Start by identifying potential suppliers through industry directories, trade shows, and online platforms like Alibaba or ThomasNet. Evaluate their credibility by checking customer reviews, requesting references, and assessing their certifications (e.g., ISO). It’s also beneficial to visit their facility if possible to inspect production capabilities and quality control processes. Engaging in preliminary discussions about your specific needs can help gauge their responsiveness and willingness to collaborate on custom solutions.
-
What should I consider when evaluating frame manufacturers?
When evaluating frame manufacturers, consider their experience in your specific industry, production capacity, and quality assurance practices. Look for manufacturers that specialize in the type of frames you need, whether for artworks, glasses, or industrial applications. Assess their ability to customize products based on your specifications and inquire about their Minimum Order Quantities (MOQs) to ensure they can meet your demand without excess costs. Additionally, consider their logistics capabilities, including shipping times and methods, especially for international orders. -
What is the typical Minimum Order Quantity (MOQ) for frame manufacturers?
Minimum Order Quantities (MOQs) can vary significantly among frame manufacturers, often ranging from 50 to several hundred units per order, depending on the type of frame and customization requirements. Smaller manufacturers may offer lower MOQs, which can be advantageous for startups or small businesses. However, higher MOQs might lead to better pricing per unit. It’s essential to discuss your specific needs with potential manufacturers to find a balance between order size and cost-effectiveness. -
How can I ensure the quality of frames from a manufacturer?
To ensure the quality of frames from a manufacturer, request samples before placing a larger order. This allows you to assess the craftsmanship, materials used, and overall finish. Additionally, inquire about their quality assurance processes, including any certifications they hold, such as ISO 9001. Establish clear specifications and standards in your contracts to ensure compliance. Regular communication throughout the production process can also help maintain quality and address any issues early. -
What payment terms are standard when dealing with frame manufacturers?
Payment terms can vary widely, but typical arrangements include a deposit (usually 30-50%) upfront, with the remaining balance due upon completion or prior to shipping. Some manufacturers may offer payment via letters of credit, especially for larger orders or international transactions. It’s crucial to clarify payment terms in advance to avoid misunderstandings. Always ensure that the payment method provides a level of protection, especially in international dealings. -
How do I handle logistics and shipping when sourcing frames internationally?
When sourcing frames internationally, consider logistics and shipping options that align with your timeline and budget. Discuss shipping methods with your manufacturer, such as air freight for speed or sea freight for cost-effectiveness. Ensure that your supplier is aware of customs regulations and tariffs for your specific country. It’s advisable to work with a freight forwarder who can assist with documentation, insurance, and tracking to ensure a smooth delivery process. -
Can I customize frames according to my specifications?
Yes, most reputable frame manufacturers offer customization options to meet your specific needs. This can include variations in size, material, color, and design. When discussing customization, provide detailed specifications and any design files or samples you have. Be clear about your target market and usage to help the manufacturer recommend the most suitable materials and construction methods. Keep in mind that customization might affect MOQs and lead times. -
What are the common challenges faced when sourcing frames internationally?
Common challenges when sourcing frames internationally include language barriers, differences in quality standards, and varying lead times. Cultural differences can also impact communication and expectations. To mitigate these challenges, establish clear communication channels and set realistic timelines. Conducting due diligence and having a solid contract in place can help address potential disputes. Additionally, consider working with local agents or intermediaries who understand the market and can facilitate smoother transactions.
Important Disclaimer & Terms of Use
⚠️ Important Disclaimer
The information provided in this guide, including content regarding manufacturers, technical specifications, and market analysis, is for informational and educational purposes only. It does not constitute professional procurement advice, financial advice, or legal advice.
While we have made every effort to ensure the accuracy and timeliness of the information, we are not responsible for any errors, omissions, or outdated information. Market conditions, company details, and technical standards are subject to change.
B2B buyers must conduct their own independent and thorough due diligence before making any purchasing decisions. This includes contacting suppliers directly, verifying certifications, requesting samples, and seeking professional consultation. The risk of relying on any information in this guide is borne solely by the reader.
Strategic Sourcing Conclusion and Outlook for frame manufacturer
As the global market for frame manufacturing continues to evolve, strategic sourcing emerges as an essential process for international B2B buyers. By carefully selecting suppliers, negotiating favorable terms, and ensuring quality, businesses can optimize their supply chains and reduce costs. Buyers from Africa, South America, the Middle East, and Europe should focus on building strong relationships with manufacturers that prioritize sustainability and innovation. This not only enhances product quality but also aligns with the increasing demand for environmentally friendly practices.
What Are the Key Benefits of Strategic Sourcing for Frame Manufacturers?
The benefits of strategic sourcing extend beyond cost savings; they include improved supplier collaboration, enhanced market responsiveness, and increased agility in adapting to changing consumer demands. For instance, leveraging technology to analyze market trends can help frame manufacturers identify the best sourcing opportunities. Moreover, diversifying supplier bases can mitigate risks associated with geopolitical instability or supply chain disruptions.
How Can International Buyers Prepare for Future Challenges in Frame Manufacturing?
Looking ahead, international B2B buyers must remain vigilant and adaptable. Emphasizing continuous improvement in sourcing strategies will be crucial as market dynamics shift. By staying informed about industry trends and establishing robust partnerships, buyers can position themselves for success.
In conclusion, investing in strategic sourcing is not just a tactical decision but a strategic imperative for frame manufacturers aiming to thrive in a competitive landscape. Now is the time to take action—evaluate your sourcing strategies and engage with innovative suppliers to secure a sustainable future for your business.