Discover Top Tips to Choose a Packaging Machinery Supplier (2025)
Introduction: Navigating the Global Market for packaging machinery supplier
Navigating the global market for packaging machinery suppliers can be a daunting task for international B2B buyers, particularly those operating in rapidly evolving markets across Africa, South America, the Middle East, and Europe. The challenge lies not only in identifying reliable suppliers but also in understanding the diverse range of machinery types and their applications, which can significantly impact operational efficiency and product quality. This guide is designed to demystify the complexities of sourcing packaging machinery, providing insights into various types of equipment, from automated packing lines to eco-friendly packaging solutions.
Within these pages, you will find comprehensive information on supplier vetting processes, cost considerations, and the latest trends in packaging technology. Each section is tailored to empower you, the buyer, with actionable insights that lead to informed purchasing decisions. By addressing critical questions such as “What are the key factors to consider when selecting a packaging machinery supplier?” and “How can I ensure compliance with regional packaging regulations?”, this guide serves as a strategic resource for navigating the intricate landscape of global suppliers.
In an increasingly competitive marketplace, equipping yourself with the right knowledge not only streamlines your procurement process but also enhances your overall supply chain strategy. Whether you are looking to expand your production capabilities or seeking innovative packaging solutions, this guide will help you make decisions that align with your business objectives and market demands.
Understanding packaging machinery supplier Types and Variations
Type Name | Key Distinguishing Features | Primary B2B Applications | Brief Pros & Cons for Buyers |
---|---|---|---|
Flexible Packaging Suppliers | Specialize in materials like films and pouches | Food, cosmetics, pharmaceuticals | Pros: Cost-effective, lightweight; Cons: Limited durability compared to rigid options. |
Automated Packaging Systems | High-speed machinery with integrated technology | E-commerce, food & beverage, electronics | Pros: Increased efficiency, reduced labor costs; Cons: High initial investment. |
Custom Packaging Solutions | Tailored designs and materials based on specific needs | Specialty foods, luxury goods, pharmaceuticals | Pros: Unique branding, optimized protection; Cons: Potentially higher costs and longer lead times. |
Eco-friendly Packaging Suppliers | Focus on sustainable materials and processes | Retail, food service, cosmetics | Pros: Appeals to environmentally conscious consumers; Cons: May have higher production costs. |
Contract Packaging Providers | Outsourcing packaging processes to third-party experts | Various industries needing scalability | Pros: Flexibility, access to expertise; Cons: Less control over quality and timelines. |
What are the characteristics of Flexible Packaging Suppliers?
Flexible packaging suppliers focus on lightweight materials such as films, pouches, and bags. They are particularly suited for industries like food, cosmetics, and pharmaceuticals, where shelf life and product freshness are crucial. When purchasing, B2B buyers should consider the material specifications, barrier properties, and compliance with safety standards. While flexible packaging is cost-effective and offers branding opportunities, it may not provide the same durability as rigid packaging options.
How do Automated Packaging Systems enhance efficiency?
Automated packaging systems are designed for high-speed operations, integrating advanced technologies like robotics and AI. These systems are ideal for sectors such as e-commerce, food & beverage, and electronics, where efficiency and speed are essential. Buyers should assess the system’s compatibility with existing production lines, maintenance requirements, and scalability. Although these systems significantly reduce labor costs and increase throughput, they often require a substantial upfront investment.
What benefits do Custom Packaging Solutions offer?
Custom packaging solutions allow businesses to create tailored designs that meet specific product requirements. This type of supplier is particularly valuable in specialty foods, luxury goods, and pharmaceuticals, where branding and product protection are paramount. B2B buyers should evaluate the design capabilities, material options, and turnaround times when considering custom solutions. While they offer unique branding opportunities and optimized protection, the costs can be higher, and production times may be extended.
Why are Eco-friendly Packaging Suppliers gaining popularity?
Eco-friendly packaging suppliers prioritize sustainable materials and processes, catering to a growing market of environmentally conscious consumers. This type of packaging is commonly used in retail, food service, and cosmetics. B2B buyers should look for certifications, material sourcing, and lifecycle assessments to ensure sustainability claims. Although eco-friendly options can enhance brand reputation and appeal, they may come with higher production costs compared to traditional packaging.
What role do Contract Packaging Providers play in the supply chain?
Contract packaging providers offer outsourcing solutions for companies looking to scale their packaging processes without investing in new infrastructure. They serve a variety of industries, providing flexibility and access to specialized expertise. Buyers should consider the provider‘s reliability, quality control measures, and capacity to meet demand fluctuations. While contract packaging can enhance operational flexibility and reduce overhead, it may lead to less control over quality and timelines, which is a critical factor for many businesses.
Related Video: Automatic packaging machines and packaging systems for Kits
Key Industrial Applications of packaging machinery supplier
Industry/Sector | Specific Application of packaging machinery supplier | Value/Benefit for the Business | Key Sourcing Considerations for this Application |
---|---|---|---|
Food and Beverage | Automated filling and sealing machines | Increases production efficiency and reduces labor costs | Ensure compliance with food safety standards and certifications |
Pharmaceuticals | Blister packaging machines | Protects product integrity and extends shelf life | Look for machines that offer flexibility for different product sizes |
Cosmetics and Personal Care | Labeling and cartoning machines | Enhances brand visibility and reduces packaging errors | Consider machinery that accommodates various container shapes |
Consumer Electronics | Shrink wrapping machines | Provides protection during shipping and enhances presentation | Evaluate machinery for speed and compatibility with diverse products |
Chemical Industry | Bulk packaging systems | Improves safety and efficiency in handling hazardous materials | Assess for compliance with safety regulations and durability |
How is Packaging Machinery Used in the Food and Beverage Industry?
In the food and beverage sector, packaging machinery suppliers provide automated filling and sealing machines that streamline production processes. These machines ensure accurate portioning and sealing, which minimizes waste and enhances product freshness. For international buyers, particularly those in Africa and South America, it is crucial to source equipment that meets local food safety regulations, ensuring compliance while maximizing operational efficiency.
What Role Does Packaging Machinery Play in Pharmaceuticals?
Pharmaceutical companies rely on blister packaging machines to safeguard their products against contamination and degradation. These machines are designed to create airtight seals that preserve medication potency and shelf life. Buyers from the Middle East and Europe should prioritize suppliers that offer customizable solutions for varying product sizes and types, ensuring flexibility in their production lines while maintaining stringent quality control standards.
Why is Labeling Machinery Important for Cosmetics and Personal Care?
Labeling and cartoning machines are vital for cosmetics and personal care products as they improve brand visibility and compliance with regulatory labeling requirements. These machines can handle various container shapes and sizes, which is essential for brands looking to differentiate themselves in competitive markets. For international buyers, particularly in Europe, sourcing machinery that integrates seamlessly with existing production lines can significantly reduce downtime and enhance operational efficiency.
How Does Shrink Wrapping Machinery Benefit Consumer Electronics?
Shrink wrapping machines are essential for protecting consumer electronics during transit and enhancing product presentation on retail shelves. This type of packaging ensures that products remain safe from dust and moisture while also providing a visually appealing display. B2B buyers, especially from South Africa and the UAE, should consider machinery that offers high-speed operation and adaptability to various product dimensions to meet the demands of a fast-paced market.
What Are the Key Considerations for Bulk Packaging in the Chemical Industry?
In the chemical industry, bulk packaging systems are critical for safely handling hazardous materials. These systems not only improve efficiency but also minimize the risk of spills and accidents. International buyers must ensure that the machinery sourced complies with local safety regulations and is built to withstand harsh environments, enhancing both safety and productivity in their operations.
Related Video: Glenroy’s Flexible Packaging Manufacturing Process
3 Common User Pain Points for ‘packaging machinery supplier’ & Their Solutions
Scenario 1: Navigating Complex Machinery Specifications for Diverse Markets
The Problem: International B2B buyers often face the daunting task of selecting packaging machinery that meets their unique specifications and local regulations. For instance, a buyer from South Africa looking to import machinery suitable for food packaging must consider both the technical specifications required for food safety and the local packaging norms. This complexity can lead to confusion and costly missteps if the machinery does not comply with local standards or is incompatible with existing production lines.
The Solution: To effectively navigate this challenge, buyers should start by conducting thorough market research to understand both the technical and regulatory requirements in their region. Engage directly with packaging machinery suppliers who have a proven track record in your specific market. Request detailed documentation on machinery compliance with local standards, such as ISO certifications or specific food safety regulations. Additionally, consider using a checklist that includes key specifications like material compatibility, energy efficiency, and production capacity. Collaborating closely with suppliers during the specification phase can ensure that the selected machinery aligns with both operational needs and local regulations, ultimately avoiding costly adjustments post-purchase.
Scenario 2: Managing Maintenance and Downtime Risks
The Problem: A significant concern for B2B buyers is the risk of equipment downtime due to maintenance issues. For example, a buyer from Europe may invest in advanced packaging machinery, but if the supplier does not offer adequate after-sales support or spare parts availability, production can come to a halt, affecting profitability. This scenario is exacerbated in regions with limited access to technical support, resulting in prolonged downtime and increased operational costs.
The Solution: To mitigate these risks, buyers should prioritize suppliers that provide robust after-sales support, including maintenance contracts and readily available spare parts. Before finalizing a purchase, inquire about the supplier’s service level agreements (SLAs) and the average response time for service calls. Establish a preventive maintenance schedule in collaboration with the supplier to ensure regular checks and servicing of the machinery. Additionally, consider investing in training programs for in-house staff to perform basic troubleshooting and maintenance. This proactive approach not only minimizes downtime but also empowers your team to handle minor issues swiftly, ensuring seamless production flow.
Scenario 3: Balancing Cost and Quality in Machinery Procurement
The Problem: International buyers often struggle with the balance between cost and quality when sourcing packaging machinery. A buyer from the Middle East may find a low-cost option that promises high performance but lacks proven reliability, leading to fears of poor quality and potential long-term losses. Conversely, opting for high-end machinery can strain budgets, particularly for smaller businesses looking to expand their packaging capabilities.
The Solution: To achieve a balance between cost and quality, buyers should adopt a strategic sourcing approach that includes thorough supplier evaluation. Start by obtaining multiple quotes and assessing not only the initial purchase price but also the total cost of ownership (TCO), which includes maintenance, energy consumption, and potential downtime costs. Look for suppliers with positive customer reviews and case studies that demonstrate their machinery’s reliability and performance in similar industries. Additionally, consider arranging factory visits to see the machinery in action and to understand the supplier’s production capabilities. By focusing on long-term value rather than just upfront costs, buyers can make more informed decisions that align with their operational goals and budget constraints.
Strategic Material Selection Guide for packaging machinery supplier
When selecting materials for packaging machinery, international B2B buyers must consider various factors that influence performance, cost, and compliance with industry standards. This section analyzes four common materials used in packaging machinery, focusing on their properties, advantages, disadvantages, and specific considerations for buyers from Africa, South America, the Middle East, and Europe.
What Are the Key Properties of Stainless Steel in Packaging Machinery?
Stainless steel is a widely used material in packaging machinery due to its excellent corrosion resistance and durability. It can withstand high temperatures and pressures, making it suitable for various applications, including food and pharmaceutical packaging. The key properties of stainless steel include:
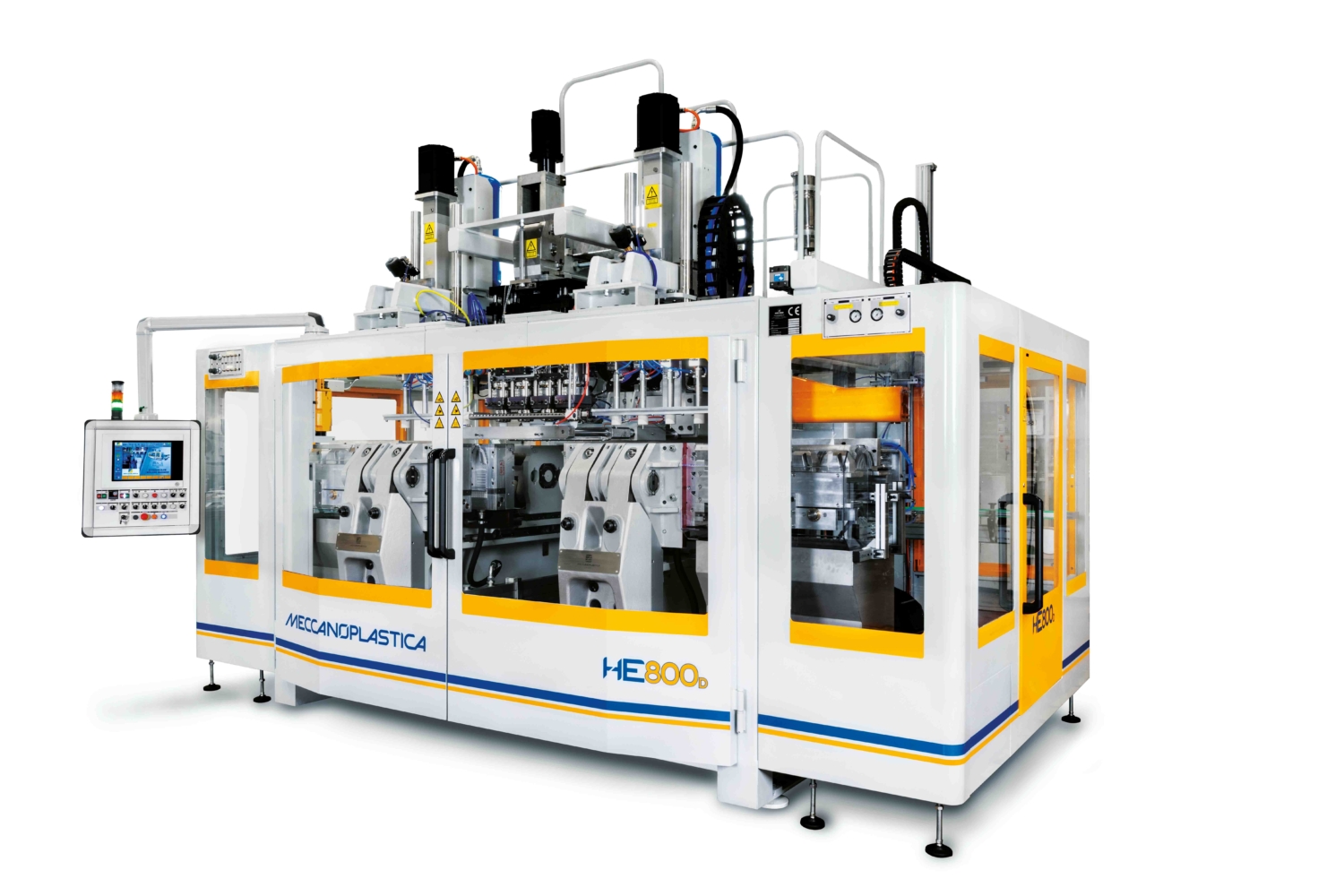
A stock image related to packaging machinery supplier.
- Corrosion Resistance: Essential for maintaining hygiene and preventing contamination.
- Temperature and Pressure Ratings: Capable of handling extreme conditions without deforming.
- Durability: Long lifespan, reducing the need for frequent replacements.
Pros and Cons:
– Pros: High durability, easy to clean, and compliant with food safety standards.
– Cons: Higher initial cost compared to other materials and potential for scratching.
Impact on Application:
Stainless steel is particularly compatible with media that require strict hygiene standards, such as food and pharmaceuticals.
Considerations for International Buyers:
Buyers should ensure compliance with international standards such as ASTM and DIN, especially in regions with stringent regulations like Europe and the UAE.
How Does Aluminum Compare for Packaging Machinery Applications?
Aluminum is another popular choice for packaging machinery, known for its lightweight and good corrosion resistance. It is often used in applications where weight is a critical factor.
- Key Properties:
- Lightweight: Reduces transportation costs.
- Corrosion Resistance: Suitable for various environments.
- Thermal Conductivity: Excellent for heat transfer applications.
Pros and Cons:
– Pros: Lower cost than stainless steel and easier to machine.
– Cons: Less durable than stainless steel and can be prone to denting.
Impact on Application:
Aluminum is suitable for applications involving dry products or where weight savings are essential, such as in packaging lines.
Considerations for International Buyers:
Buyers should verify the alloy specifications and ensure compliance with local standards, particularly in regions like South America where regulations may vary.
What Are the Advantages of Plastic Materials in Packaging Machinery?
Plastics, such as polyethylene and polypropylene, are increasingly used in packaging machinery due to their versatility and cost-effectiveness.
- Key Properties:
- Chemical Resistance: Suitable for a wide range of products.
- Flexibility: Can be molded into complex shapes.
- Lightweight: Reduces shipping costs.
Pros and Cons:
– Pros: Cost-effective, lightweight, and resistant to many chemicals.
– Cons: Lower durability compared to metals and can degrade under UV light.
Impact on Application:
Plastics are ideal for packaging non-perishable goods and can be tailored for specific applications through additives.
Considerations for International Buyers:
Ensure compliance with food safety regulations and consider the environmental impact of plastic use, especially in regions with strict recycling laws.
How Does Composite Material Fit into Packaging Machinery?
Composite materials, which combine different substances to leverage their strengths, are becoming more common in packaging machinery.
- Key Properties:
- Strength-to-Weight Ratio: High strength while remaining lightweight.
- Corrosion Resistance: Can be engineered to resist specific chemicals.
- Thermal Stability: Suitable for high-temperature applications.
Pros and Cons:
– Pros: Excellent performance in demanding applications and customizable properties.
– Cons: Higher manufacturing complexity and cost.
Impact on Application:
Composites are ideal for specialized applications where traditional materials may fail, such as in high-speed packaging lines.
Considerations for International Buyers:
Buyers must assess the manufacturing capabilities of suppliers and ensure that the composites meet relevant standards.
Summary Table of Material Selection for Packaging Machinery
Material | Typical Use Case for packaging machinery supplier | Key Advantage | Key Disadvantage/Limitation | Relative Cost (Low/Med/High) |
---|---|---|---|---|
Stainless Steel | Food and pharmaceutical packaging machinery | High durability and corrosion resistance | Higher initial cost | High |
Aluminum | Lightweight packaging applications | Cost-effective and easy to machine | Less durable than stainless steel | Medium |
Plastic | Non-perishable goods packaging | Lightweight and versatile | Lower durability | Low |
Composite | High-speed packaging lines | Excellent strength-to-weight ratio | Higher manufacturing complexity | High |
This strategic material selection guide provides insights that will assist international B2B buyers in making informed decisions when sourcing packaging machinery, ensuring compliance with industry standards while considering performance and cost-effectiveness.
In-depth Look: Manufacturing Processes and Quality Assurance for packaging machinery supplier
What Are the Key Manufacturing Processes for Packaging Machinery Suppliers?
When considering packaging machinery suppliers, understanding their manufacturing processes is crucial for B2B buyers. These processes typically encompass four main stages: material preparation, forming, assembly, and finishing. Each stage involves specific techniques that ensure the machinery meets the required specifications and standards.
1. Material Preparation: What Materials Are Used in Packaging Machinery?
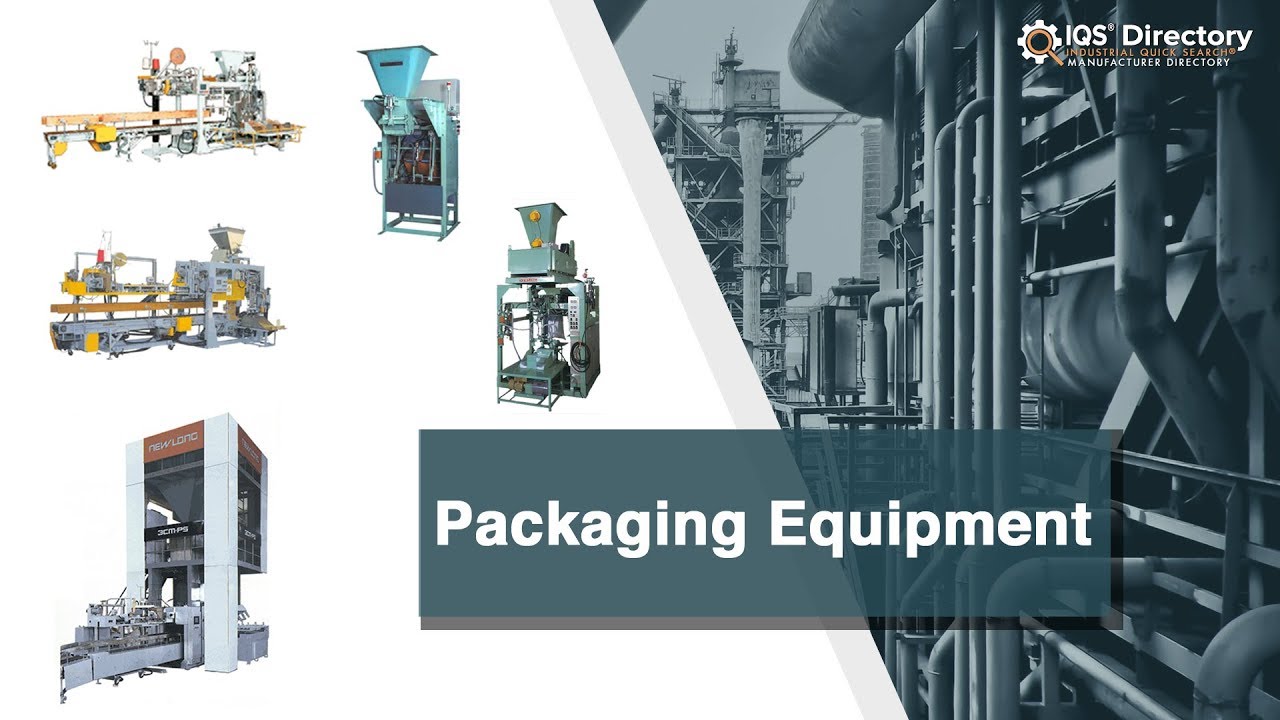
A stock image related to packaging machinery supplier.
The first stage involves selecting and preparing the right materials. Common materials include stainless steel, aluminum, and various plastics, which are chosen based on durability, corrosion resistance, and the type of products being packaged.
Key techniques in this stage include:
- Material Cutting: Using laser cutting, water jet cutting, or CNC machining to achieve precise dimensions.
- Surface Treatment: Techniques such as sandblasting or chemical cleaning to enhance adhesion and prevent corrosion.
B2B buyers should ensure that suppliers source high-quality materials that comply with international standards, which can significantly affect the machine’s lifespan and performance.
2. Forming: How Is Packaging Machinery Shaped?
In the forming stage, the prepared materials undergo various processes to create the components of the machinery. This may include:
- Bending and Shaping: Techniques like stamping and die-casting are used to form parts like frames and covers.
- Welding: Critical for assembling metal parts together, ensuring structural integrity. Techniques can include MIG, TIG, or spot welding, depending on the material type.
Buyers should look for suppliers that employ advanced forming technologies, as these can lead to more robust and efficient machinery.
3. Assembly: What Steps Are Involved in the Assembly of Packaging Machinery?
The assembly process involves integrating the various components into a complete unit. This stage often includes:
- Mechanical Assembly: Connecting parts using screws, bolts, or rivets.
- Electrical Assembly: Installing control panels, sensors, and wiring to ensure functionality.
Quality control during this phase is essential. B2B buyers should inquire about the assembly processes and whether they include automated systems to enhance precision and reduce human error.
4. Finishing: How Is the Final Product Prepared for Delivery?
The finishing stage ensures that the machinery is ready for operation and meets aesthetic and functional standards. This may involve:
- Painting and Coating: Applying protective coatings to prevent corrosion and enhance appearance.
- Final Inspections: Conducting thorough checks to ensure all components function correctly and meet specifications.
Buyers should request information on the finishing processes, as they can impact the machine’s reliability and maintenance needs.
What Quality Assurance Standards Should B2B Buyers Expect from Packaging Machinery Suppliers?
Quality assurance is critical in the manufacturing of packaging machinery. Suppliers should adhere to international quality standards to ensure their products are reliable and safe for use.
1. What Are the Relevant International Quality Standards?
Two of the most significant quality standards include:
- ISO 9001: This standard focuses on quality management systems and ensures that suppliers maintain consistent quality in their products and services.
- CE Marking: Required for products sold in the European Economic Area, indicating compliance with health, safety, and environmental protection standards.
For buyers in regions like Africa, South America, the Middle East, and Europe, understanding these certifications can help mitigate risks associated with product failures and non-compliance.
2. What Are the Key Quality Control Checkpoints?
Quality control checkpoints are essential throughout the manufacturing process. Key checkpoints include:
- Incoming Quality Control (IQC): Inspecting raw materials for quality before they are used in production.
- In-Process Quality Control (IPQC): Continuous monitoring during the manufacturing process to ensure that each stage meets quality standards.
- Final Quality Control (FQC): A comprehensive inspection of the finished product before shipment.
B2B buyers should verify that suppliers have robust IQC, IPQC, and FQC processes in place to minimize defects.
3. How Can B2B Buyers Verify Supplier Quality Control?
Verifying a supplier’s quality control practices can be accomplished through various methods:
- Audits: Conducting on-site audits to assess the manufacturing processes and quality management systems.
- Quality Reports: Requesting documentation that outlines quality checks and results from each stage of production.
- Third-Party Inspections: Engaging independent inspectors to evaluate the machinery before delivery.
These steps are vital for buyers to ensure they partner with reliable suppliers who prioritize quality.
What Testing Methods Are Commonly Used in Packaging Machinery Quality Assurance?
Various testing methods are employed to validate the performance and safety of packaging machinery. Common methods include:
- Functional Testing: Ensuring that the machinery operates as intended under various conditions.
- Stress Testing: Applying loads to determine the durability and reliability of the machinery over time.
- Safety Testing: Verifying that safety features, such as emergency stops and guards, function correctly.
B2B buyers should ask suppliers about their testing protocols to ensure the machinery meets industry standards and operational needs.
What Are the Quality Control Nuances for International B2B Buyers?
International B2B buyers face unique challenges in quality control, particularly concerning compliance with local regulations and standards. Factors to consider include:
- Cultural Differences: Understanding the local practices and expectations regarding quality assurance can help mitigate misunderstandings.
- Logistical Challenges: Ensuring that quality is maintained throughout the supply chain can be complex, especially when dealing with multiple regions.
Buyers from Africa, South America, the Middle East, and Europe should conduct thorough due diligence on suppliers to navigate these nuances effectively. Establishing strong communication and clear expectations regarding quality standards will foster successful partnerships and mitigate risks associated with international procurement.
Practical Sourcing Guide: A Step-by-Step Checklist for ‘packaging machinery supplier’
Introduction
When sourcing packaging machinery, international B2B buyers must navigate a complex landscape filled with various suppliers, technologies, and compliance regulations. This guide provides a comprehensive checklist to streamline your procurement process, ensuring that you make informed decisions that align with your business needs and regional standards.
Step 1: Define Your Technical Specifications
Establishing clear technical specifications is crucial for ensuring that the machinery meets your operational needs. Consider factors such as production capacity, types of packaging materials, and automation levels. This clarity helps suppliers provide accurate quotes and solutions tailored to your requirements.
Step 2: Conduct Market Research for Suppliers
Research potential suppliers to understand their capabilities and market reputation. Look for reviews, case studies, and testimonials from other businesses in your industry. This step not only helps you identify reputable suppliers but also provides insights into their product offerings and customer service levels.
Step 3: Evaluate Supplier Certifications and Compliance
Ensure that the suppliers you consider are certified to international standards such as ISO 9001 or industry-specific certifications. Compliance with local regulations is also critical, especially in regions like the EU or the Middle East, where standards can vary significantly. This guarantees that the machinery meets safety and quality requirements.
Step 4: Request Detailed Quotations
Once you’ve shortlisted potential suppliers, request detailed quotations that outline pricing, lead times, and warranty options. Compare these quotes not just on price but also on what is included, such as installation and training services. A lower price may not be beneficial if it comes with limited support.
Step 5: Assess After-Sales Support and Maintenance
After-sales support is a vital component of your purchasing decision. Inquire about the availability of spare parts, the process for repairs, and the level of technical support offered. Suppliers with robust support systems can significantly minimize downtime and enhance your operational efficiency.
Step 6: Visit Supplier Facilities (If Possible)
If feasible, visiting the supplier’s manufacturing facilities can provide invaluable insights into their production processes and quality control measures. This firsthand experience helps you assess their capabilities and reliability, fostering a stronger supplier relationship.
Step 7: Negotiate Terms and Conditions
Before finalizing your purchase, negotiate the terms and conditions of the agreement. Discuss payment terms, delivery schedules, and any guarantees or warranties. Clear agreements help prevent misunderstandings and set the foundation for a successful partnership.
By following this checklist, B2B buyers from Africa, South America, the Middle East, and Europe can enhance their sourcing strategies and make informed decisions when procuring packaging machinery. Each step ensures a thorough evaluation of suppliers, ultimately leading to successful procurement outcomes.
Comprehensive Cost and Pricing Analysis for packaging machinery supplier Sourcing
When sourcing packaging machinery, understanding the comprehensive cost structure is essential for international B2B buyers, particularly those from Africa, South America, the Middle East, and Europe. This section delves into the key cost components, pricing influencers, and actionable buyer tips to ensure effective procurement.
What Are the Key Cost Components in Packaging Machinery Sourcing?
-
Materials: The cost of raw materials significantly affects the overall price of packaging machinery. Common materials include metals like stainless steel and aluminum, as well as plastics for various components. Prices can fluctuate based on market demand and availability, making it crucial for buyers to stay informed about material trends.
-
Labor: Labor costs vary widely by region and can influence the total cost of machinery. Countries with higher wage standards, such as those in Western Europe, may have higher labor costs compared to regions like South Africa or South America. Understanding local labor markets can help buyers anticipate costs.
-
Manufacturing Overhead: This includes expenses related to factory operations, such as utilities, equipment maintenance, and facility costs. Buyers should inquire about how manufacturers allocate overhead in their pricing, as this can vary significantly between suppliers.
-
Tooling: Custom tooling is often required for specialized machinery. This cost can be substantial, especially for unique designs or specifications. Buyers should consider whether suppliers have existing tooling that can reduce costs or if new tooling is necessary.
-
Quality Control (QC): Implementing strict quality control measures ensures that machinery meets industry standards, but it also adds to the cost. Buyers should evaluate suppliers’ QC processes to ensure they align with their quality expectations without inflating costs unnecessarily.
-
Logistics: Shipping and handling costs can vary based on the supplier’s location, shipping method, and the Incoterms agreed upon. Understanding these factors is critical for budgeting and ensuring timely delivery.
-
Margin: Suppliers typically mark up their costs to ensure profitability. Buyers should be aware of the typical margins in the industry, which can range from 10% to 30%, depending on competition and product demand.
How Do Pricing Influencers Impact Packaging Machinery Costs?
Several factors can influence the pricing of packaging machinery:
-
Volume and Minimum Order Quantity (MOQ): Larger orders often lead to reduced per-unit costs due to economies of scale. Buyers should negotiate MOQs that align with their production needs while optimizing costs.
-
Specifications and Customization: Customized machinery tailored to specific production needs can increase costs. Buyers should clearly define their requirements to avoid unexpected charges and ensure suppliers can meet these needs efficiently.
-
Material Quality and Certifications: Higher quality materials and certifications (such as ISO or CE) can increase machinery costs but may offer long-term savings through durability and compliance. Assess the value of these certifications against your operational needs.
-
Supplier Factors: The supplier’s reputation, experience, and location can also influence pricing. Established suppliers with a track record of quality may charge more but offer better reliability.
-
Incoterms: Understanding the agreed-upon Incoterms is vital, as they dictate responsibility for shipping costs, insurance, and risk. This can significantly affect the total cost of ownership.
What Are the Best Practices for Negotiating Packaging Machinery Prices?
For international B2B buyers, particularly from regions like Africa, South America, the Middle East, and Europe, effective negotiation strategies can lead to better pricing and terms:
-
Research Market Prices: Understand the standard pricing for similar machinery in your region. This knowledge empowers you to negotiate confidently.
-
Evaluate Total Cost of Ownership (TCO): Consider not just the upfront costs but also maintenance, operation, and potential downtime costs over the machinery’s lifespan.
-
Leverage Volume: If possible, consolidate orders to increase your purchasing volume, thus securing better pricing and terms.
-
Be Transparent About Expectations: Clear communication about your needs can lead to better alignment with suppliers, potentially reducing costs associated with miscommunication or rework.
-
Seek Multiple Quotes: Don’t settle for the first offer. Obtaining multiple quotes allows for comparison and strengthens your negotiating position.
Conclusion
While pricing for packaging machinery can vary widely based on numerous factors, understanding the cost components and pricing influencers enables international B2B buyers to make informed decisions. By employing effective negotiation strategies and considering the total cost of ownership, buyers can optimize their procurement processes and achieve better value for their investments. Always remember that indicative prices can vary based on market conditions and supplier dynamics, so continuous monitoring is essential.
Alternatives Analysis: Comparing packaging machinery supplier With Other Solutions
In the competitive landscape of packaging, businesses often face the challenge of selecting the best machinery or method to meet their operational needs. While traditional packaging machinery suppliers offer robust solutions, there are viable alternatives worth considering. This section will explore these alternatives, highlighting their strengths and weaknesses in comparison to conventional packaging machinery suppliers.
Comparison Table of Packaging Solutions
Comparison Aspect | Packaging Machinery Supplier | Alternative 1: Manual Packaging | Alternative 2: Contract Packaging Services |
---|---|---|---|
Performance | High efficiency and speed | Moderate efficiency; labor-intensive | Variable; depends on the provider’s capabilities |
Cost | High initial investment | Low initial cost; ongoing labor costs | Moderate; pay per service, potentially variable |
Ease of Implementation | Complex installation; training required | Simple setup; minimal training needed | Quick to implement; relies on third-party expertise |
Maintenance | Regular maintenance required | Low maintenance; manual oversight | Minimal maintenance; handled by provider |
Best Use Case | High-volume production | Small batches, artisanal products | Businesses without in-house packaging capability |
What Are the Advantages and Disadvantages of Manual Packaging?
Pros:
Manual packaging is often more cost-effective for small businesses or startups. It requires minimal initial investment, making it accessible for companies looking to test the market without significant financial risk. Additionally, manual methods allow for flexibility in packaging designs, which can be beneficial for niche products.
Cons:
On the downside, manual packaging is labor-intensive and can lead to inconsistencies in product quality and speed. As demand grows, businesses may find it challenging to scale operations efficiently. The reliance on human labor also introduces the potential for errors, which could impact customer satisfaction.
How Do Contract Packaging Services Compare?
Pros:
Contract packaging services provide a tailored solution for businesses lacking the resources for in-house packaging. These services can handle a variety of packaging needs, from product design to fulfillment, allowing companies to focus on core operations. Additionally, they often have specialized equipment and expertise, leading to potentially higher-quality packaging solutions.
Cons:
However, the cost can vary significantly based on the provider and the scope of services. Businesses may face challenges with control over the packaging process, which can lead to issues with consistency or quality if the provider does not meet expectations. Additionally, long-term reliance on a third party can complicate logistics and supply chain management.
Conclusion: How to Choose the Right Packaging Solution for Your Business?
When selecting the right packaging solution, B2B buyers should carefully assess their specific operational needs and constraints. For high-volume production, a packaging machinery supplier may offer the efficiency and speed required. Conversely, businesses focused on small-batch production or those looking to minimize initial costs may benefit from manual packaging or contract packaging services. Understanding the pros and cons of each option will empower international buyers, particularly from Africa, South America, the Middle East, and Europe, to make informed decisions that align with their strategic goals and market demands.
Essential Technical Properties and Trade Terminology for packaging machinery supplier
What Are the Essential Technical Properties of Packaging Machinery?
Understanding the technical specifications of packaging machinery is crucial for B2B buyers, especially in diverse markets like Africa, South America, the Middle East, and Europe. Here are some key specifications to consider:
-
Material Grade
The material grade of packaging machinery components, such as stainless steel or aluminum, directly impacts durability and hygiene. For industries like food and pharmaceuticals, high-grade materials are essential to meet regulatory standards and ensure product safety. -
Tolerance Levels
Tolerance refers to the allowable deviation in dimensions during manufacturing. Precise tolerances are vital for ensuring that machinery parts fit together correctly, which minimizes wear and tear and enhances operational efficiency. Buyers should inquire about the tolerance levels when evaluating suppliers. -
Production Capacity
This specification indicates the maximum output the machinery can handle within a specific timeframe. Understanding production capacity is essential for buyers to ensure that the equipment can meet their operational demands, especially during peak seasons. -
Energy Consumption
Energy-efficient machinery not only reduces operational costs but also aligns with sustainability goals. Buyers should assess the energy consumption ratings of packaging machinery to calculate potential savings and environmental impact. -
Automation Features
Advanced automation features, such as programmable logic controllers (PLCs) and sensors, enhance efficiency and reduce the need for manual labor. Buyers should evaluate how these features can improve their packaging processes and overall productivity. -
Maintenance Requirements
Knowing the maintenance needs of the machinery, including frequency and types of services required, can help buyers manage downtime and extend the equipment’s lifespan. This information is critical for budgeting and operational planning.
What Are Common Trade Terms Used in Packaging Machinery Supply?
Familiarity with industry jargon can streamline communication and negotiations with suppliers. Here are several essential trade terms:
-
OEM (Original Equipment Manufacturer)
This term refers to companies that produce equipment that may be marketed by another company. Understanding the OEM relationship can help buyers identify quality assurance and warranty conditions for the machinery. -
MOQ (Minimum Order Quantity)
MOQ indicates the smallest number of units a supplier is willing to sell. Knowing the MOQ is crucial for budgeting and inventory planning, especially for international buyers who may need to manage shipping costs. -
RFQ (Request for Quotation)
An RFQ is a standard business process where buyers invite suppliers to submit price quotes for specific products or services. Crafting a clear RFQ can lead to better pricing and terms from suppliers. -
Incoterms (International Commercial Terms)
These terms define the responsibilities of buyers and sellers in international transactions, including shipping costs, insurance, and risk transfer. Familiarity with Incoterms can help prevent misunderstandings and protect against unexpected costs. -
Lead Time
Lead time refers to the time taken from placing an order to receiving the goods. Understanding lead times is critical for inventory management and ensuring that production schedules remain on track. -
Warranty and Service Agreements
These agreements outline the terms of repair and maintenance services provided by the supplier. A clear warranty can protect buyers from unexpected repair costs and ensure they receive prompt service when needed.
By understanding these technical properties and trade terms, B2B buyers can make informed decisions, negotiate effectively, and establish successful partnerships with packaging machinery suppliers.
Navigating Market Dynamics and Sourcing Trends in the packaging machinery supplier Sector
What Are the Key Market Dynamics and Trends in the Packaging Machinery Sector?
The packaging machinery sector is experiencing significant growth driven by several global factors. A surge in e-commerce and the demand for sustainable packaging solutions are reshaping the industry landscape. For international B2B buyers from regions like Africa, South America, the Middle East, and Europe, understanding these dynamics is crucial.
Emerging technologies such as automation, robotics, and Industry 4.0 are leading to enhanced efficiency and cost-effectiveness in packaging operations. Buyers are increasingly looking for suppliers who can provide smart machinery that integrates with existing systems, enabling real-time monitoring and data analytics. Furthermore, innovations in machine design are facilitating faster changeovers and versatility in handling various packaging formats, which is particularly advantageous for businesses aiming to reduce downtime and increase productivity.
Another vital trend is the growing emphasis on sustainability. As consumers demand eco-friendly packaging, suppliers are responding by developing machinery capable of using biodegradable materials and reducing waste. This focus on sustainability is not just a regulatory requirement but also a competitive advantage that buyers should consider when sourcing packaging machinery. Understanding local market regulations regarding packaging waste and recycling is essential for buyers in regions like the UAE and South Africa, where compliance can impact supply chain efficiency and brand reputation.
How Is Sustainability and Ethical Sourcing Influencing the Packaging Machinery Sector?
Sustainability is no longer just a buzzword; it has become a core consideration in the packaging machinery sector. The environmental impact of packaging materials and processes is prompting buyers to seek suppliers that prioritize sustainable practices. This includes sourcing from manufacturers that offer equipment designed to minimize energy consumption and waste production.
Ethical sourcing is equally important. Buyers are increasingly aware of the need for transparency in their supply chains. This means selecting suppliers who adhere to ethical labor practices and environmental standards. Certifications such as ISO 14001 (Environmental Management) and FSC (Forest Stewardship Council) can serve as indicators of a supplier’s commitment to sustainability.
Moreover, the rise of ‘green’ materials—such as recyclable plastics and compostable films—is influencing machinery design. Packaging machinery suppliers that can adapt to these materials will be more attractive to buyers looking to align their operations with sustainability goals. By prioritizing sustainable machinery and ethical sourcing, B2B buyers can not only reduce their environmental footprint but also enhance their brand’s image in a market increasingly focused on corporate responsibility.
What Is the Evolution of the Packaging Machinery Sector?
The packaging machinery sector has evolved significantly over the past few decades, transitioning from manual operations to highly automated and sophisticated systems. Initially, packaging was a labor-intensive process, but technological advancements have led to the development of machinery that offers enhanced precision, speed, and flexibility.
In the late 20th century, the introduction of computer-controlled systems revolutionized the industry, allowing for greater customization and efficiency. Today, the focus is on integrating smart technologies that enable predictive maintenance and real-time data analysis. This evolution is particularly relevant for international B2B buyers, who must consider how these advancements can impact their operational efficiency and competitive positioning in the market.
As the sector continues to grow, understanding its history provides valuable insights into current trends and future developments, ensuring that buyers are well-equipped to make informed sourcing decisions.
Frequently Asked Questions (FAQs) for B2B Buyers of packaging machinery supplier
-
How do I choose the right packaging machinery supplier for my business?
Selecting the right packaging machinery supplier involves several steps. First, assess your specific needs, such as the type of products you package and the production volume. Research potential suppliers by checking their industry reputation, customer reviews, and case studies. It’s crucial to request samples or demonstrations of their machinery to evaluate performance and reliability. Additionally, consider the supplier’s technical support, warranty, and after-sales service to ensure they can assist you if issues arise. -
What is the typical lead time for packaging machinery orders?
Lead times can vary significantly based on the supplier’s location, the complexity of the machinery, and customization requirements. Generally, standard machinery can have a lead time of 4 to 12 weeks, while custom-built solutions may take longer. To avoid delays, it’s advisable to communicate your timelines and expectations upfront with the supplier. Consider factors like shipping time, customs clearance, and installation when planning your purchase. -
What are the key factors to consider when vetting packaging machinery suppliers?
When vetting suppliers, prioritize their experience in your industry, quality certifications (such as ISO), and customer references. Evaluate their manufacturing capabilities, including technology and machinery used, to ensure they can meet your production demands. Additionally, assess their financial stability and willingness to provide customization options. A reliable supplier should also have a solid after-sales support system to address any potential issues post-purchase. -
Can I customize packaging machinery to fit my specific needs?
Yes, many suppliers offer customization options to tailor machinery to your business requirements. Customization can include specific dimensions, features, and functionality based on your product type and packaging methods. It’s essential to discuss your needs in detail with the supplier and request a proposal outlining the customization process, costs, and expected timelines. Ensure that the supplier has experience with similar custom projects to mitigate risks. -
What is the minimum order quantity (MOQ) for packaging machinery?
The MOQ can vary by supplier and the type of machinery you are ordering. Some suppliers may have an MOQ for custom machinery, while others may allow smaller orders for standard equipment. When negotiating, clarify the MOQ upfront to align with your budget and production needs. If your order falls below the MOQ, inquire about potential options such as purchasing used machinery or collaborating with other buyers to meet the requirement. -
What payment terms should I expect when purchasing packaging machinery?
Payment terms can vary widely among suppliers and often depend on the size of the order and the supplier’s policies. Common terms include a deposit (typically 30-50%) upon order confirmation, with the balance due before shipping or upon delivery. Some suppliers may offer financing options or payment plans. Always ensure that payment terms are clearly defined in the purchase agreement to avoid misunderstandings. -
How do I ensure quality assurance for the packaging machinery I purchase?
To ensure quality assurance, request detailed specifications and certifications from the supplier, including compliance with international standards. It’s advisable to conduct factory visits or request third-party inspections before shipment. Additionally, consider implementing a trial period or a warranty that covers any defects or operational issues. Establishing clear communication with the supplier regarding quality expectations will also help mitigate risks. -
What logistics considerations should I keep in mind when sourcing packaging machinery internationally?
When sourcing machinery internationally, consider shipping methods, customs regulations, and potential tariffs that may affect your total cost. Work closely with your supplier to determine the best shipping options and timelines. It’s essential to have a clear understanding of who is responsible for shipping costs and logistics (Incoterms). Additionally, ensure that the machinery is properly packaged for transportation to prevent damage during transit.
Important Disclaimer & Terms of Use
⚠️ Important Disclaimer
The information provided in this guide, including content regarding manufacturers, technical specifications, and market analysis, is for informational and educational purposes only. It does not constitute professional procurement advice, financial advice, or legal advice.
While we have made every effort to ensure the accuracy and timeliness of the information, we are not responsible for any errors, omissions, or outdated information. Market conditions, company details, and technical standards are subject to change.
B2B buyers must conduct their own independent and thorough due diligence before making any purchasing decisions. This includes contacting suppliers directly, verifying certifications, requesting samples, and seeking professional consultation. The risk of relying on any information in this guide is borne solely by the reader.
Strategic Sourcing Conclusion and Outlook for packaging machinery supplier
In today’s competitive global market, the strategic sourcing of packaging machinery is crucial for international B2B buyers, particularly those operating in Africa, South America, the Middle East, and Europe. Effective sourcing strategies not only reduce costs but also enhance operational efficiency and product quality. Buyers should prioritize suppliers that demonstrate innovation, sustainability, and reliability, ensuring that they can adapt to changing market demands and regulatory requirements.
What should buyers consider when sourcing packaging machinery? Key factors include the supplier’s reputation, technological advancements, and the availability of after-sales support. Engaging in thorough market research and establishing long-term partnerships with trusted suppliers can significantly enhance supply chain resilience.
As we move forward, the packaging machinery landscape will continue to evolve, driven by advancements in automation and sustainability. International buyers are encouraged to stay informed about emerging technologies and trends to make informed decisions. By strategically sourcing from reputable suppliers, businesses can not only meet current needs but also position themselves for future growth. Embrace the journey of strategic sourcing to unlock new opportunities and drive your business forward.