Discover Top Tips to Choose a Reliable Jerrycan Supplier (2025)
Introduction: Navigating the Global Market for jerrycan supplier
In today’s global marketplace, sourcing reliable jerrycan suppliers can be a daunting challenge for B2B buyers, particularly those operating in diverse regions such as Africa, South America, the Middle East, and Europe. The variability in quality, compliance with international standards, and logistical complexities can create significant hurdles. This guide aims to equip you with the essential knowledge needed to navigate these challenges effectively.
From understanding the various types of jerrycans available—such as plastic, metal, and collapsible options—to exploring their applications in industries ranging from agriculture to chemicals, this resource covers a comprehensive spectrum. You will learn how to vet suppliers to ensure they meet your specific requirements, identify cost factors, and understand the importance of certifications and quality standards.
Moreover, this guide empowers international B2B buyers by providing actionable insights tailored to the unique needs and conditions of your region. Whether you are based in Thailand, Spain, or anywhere in between, the information presented will facilitate informed purchasing decisions, ultimately leading to improved operational efficiency and product reliability. By understanding the nuances of the jerrycan supply chain, you can optimize your sourcing strategies and build strong supplier relationships that stand the test of time.
Understanding jerrycan supplier Types and Variations
Type Name | Key Distinguishing Features | Primary B2B Applications | Brief Pros & Cons for Buyers |
---|---|---|---|
Plastic Jerrycans | Lightweight, corrosion-resistant, and cost-effective. | Chemicals, oils, food & beverages. | Pros: Affordable, versatile. Cons: Less durable than metal options. |
Metal Jerrycans | Robust, high durability, and often used for hazardous materials. | Fuel storage, chemicals, military. | Pros: Long-lasting, secure. Cons: Heavier, can be more expensive. |
Collapsible Jerrycans | Space-saving design, often made of flexible materials. | Emergency supplies, transport. | Pros: Easy to store, lightweight. Cons: May have lower durability. |
UN-Certified Jerrycans | Designed for the safe transport of hazardous materials, compliant with UN regulations. | Hazardous waste, chemicals. | Pros: Regulatory compliance, safety. Cons: Higher cost, limited use cases. |
Custom Jerrycans | Tailored designs for specific needs, including branding options. | Specialty products, branding. | Pros: Meets specific requirements, unique branding. Cons: Longer lead times, potentially higher costs. |
What Are the Characteristics of Plastic Jerrycans?
Plastic jerrycans are widely recognized for their lightweight and corrosion-resistant properties. Typically manufactured from high-density polyethylene (HDPE), these containers are ideal for a variety of applications, including the storage and transportation of chemicals, oils, and food products. B2B buyers should consider the cost-effectiveness of plastic jerrycans, especially for bulk purchases. However, it’s essential to note that while they are versatile, they may not withstand extreme conditions as well as their metal counterparts.
How Do Metal Jerrycans Differ in Durability and Application?
Metal jerrycans are synonymous with durability and are often the preferred choice for transporting hazardous materials and fuels. Constructed from steel or aluminum, they offer a robust solution for businesses requiring secure storage options. Their strength makes them suitable for industries such as military, automotive, and chemical manufacturing. B2B buyers should weigh the benefits of longevity and security against the higher weight and cost, which can impact shipping and handling logistics.
Why Consider Collapsible Jerrycans for Your Business?
Collapsible jerrycans are an innovative solution for businesses that prioritize space-saving designs. These containers, often made from flexible materials, can be easily stored when not in use, making them ideal for emergency supplies and transport. While they offer significant advantages in terms of storage and weight, B2B buyers must consider their lower durability compared to rigid options. This trade-off can be crucial for companies that need reliable containers for long-term use.
What Are the Advantages of UN-Certified Jerrycans?
UN-certified jerrycans are specifically designed for the safe transport of hazardous materials, adhering to strict United Nations regulations. These containers provide peace of mind for B2B buyers involved in industries that handle chemicals or waste, ensuring compliance with safety standards. While the cost may be higher, the investment is justified by the protection they offer against leaks and spills. Buyers should evaluate their specific regulatory needs when considering these jerrycans.
How Can Custom Jerrycans Enhance Your Brand?
Custom jerrycans allow businesses to tailor their storage solutions to specific needs, including branding and unique design features. This personalization can be particularly beneficial for companies looking to differentiate their products in competitive markets. While they offer flexibility and uniqueness, B2B buyers should be mindful of longer lead times and potentially increased costs associated with custom orders. Understanding your supply chain and production timelines is essential when opting for these specialized containers.
Related Video: The Calculus of Variations and the Euler-Lagrange Equation
Key Industrial Applications of jerrycan supplier
Industry/Sector | Specific Application of jerrycan supplier | Value/Benefit for the Business | Key Sourcing Considerations for this Application |
---|---|---|---|
Chemical Manufacturing | Storage and transportation of hazardous chemicals | Ensures compliance with safety regulations and minimizes leakage risks | Look for suppliers with certifications for hazardous materials and durable materials. |
Agriculture | Liquid fertilizer and pesticide distribution | Enhances efficiency in application processes and reduces waste | Consider suppliers that offer UV-resistant and robust jerrycans to withstand outdoor conditions. |
Food and Beverage | Packaging and transportation of liquids | Maintains product integrity and extends shelf life | Ensure food-grade materials are used and check for certifications like FDA or EU regulations. |
Oil and Gas | Transporting fuel and lubricants | Provides safe, secure, and efficient fuel storage solutions | Select suppliers experienced in oil and gas applications with a focus on anti-corrosion features. |
Pharmaceuticals | Distribution of liquid medicines | Guarantees safe handling and compliance with health regulations | Prioritize suppliers with experience in the pharmaceutical sector and quality assurance processes. |
How are jerrycans utilized in chemical manufacturing?
In the chemical manufacturing sector, jerrycans are essential for the safe storage and transportation of hazardous chemicals. These containers are designed to minimize risks associated with leaks and spills, ensuring compliance with stringent safety regulations. For international B2B buyers, it’s crucial to source jerrycans that meet industry standards for hazardous materials, including certifications and durability. Suppliers should provide options made from resistant materials that can withstand the chemical properties of the contents.
What role do jerrycans play in agriculture?
In agriculture, jerrycans are commonly used for distributing liquid fertilizers and pesticides. They enhance efficiency by allowing for precise application while significantly reducing waste. Buyers in regions like Africa and South America should consider jerrycans that are UV-resistant and made from robust materials to endure harsh environmental conditions. Sourcing from suppliers who understand agricultural needs can lead to better product performance and improved crop yields.
How are jerrycans important for food and beverage industries?
The food and beverage industry relies on jerrycans for the packaging and transportation of liquids, such as juices, oils, and sauces. These containers maintain product integrity and can extend shelf life, which is crucial in a highly competitive market. For B2B buyers, it’s essential to ensure that jerrycans are made from food-grade materials and comply with health regulations, such as FDA or EU standards. Suppliers should provide certifications to guarantee the safety and quality of their products.
Why are jerrycans critical in the oil and gas sector?
In the oil and gas industry, jerrycans are used for transporting fuel and lubricants, providing safe and secure storage solutions. These containers must be robust and resistant to corrosion, ensuring that they can withstand the harsh conditions often found in this sector. Buyers should prioritize suppliers with experience in oil and gas applications, focusing on those who offer jerrycans specifically designed for fuel storage, as this will enhance safety and efficiency in operations.
How do jerrycans facilitate pharmaceutical distribution?
For the pharmaceutical industry, jerrycans are vital for the safe distribution of liquid medicines. They ensure safe handling and compliance with health regulations, which is paramount in this sector. International buyers should look for suppliers with a strong quality assurance process and experience in pharmaceutical applications. It’s important to source jerrycans that meet specific regulatory requirements, ensuring that the integrity of the medicinal products is maintained throughout the supply chain.
3 Common User Pain Points for ‘jerrycan supplier’ & Their Solutions
Scenario 1: Sourcing High-Quality Jerrycans for Chemical Transport
The Problem: B2B buyers in industries such as agriculture, chemicals, or oil often face the challenge of sourcing jerrycans that meet stringent regulatory standards for transporting hazardous materials. For instance, a buyer in South Africa looking for jerrycans to transport pesticides may find that many suppliers offer products that do not comply with local or international safety standards. This can lead to costly delays, legal penalties, and safety hazards.
The Solution: To overcome this challenge, buyers should prioritize suppliers that have proven certifications and compliance with both local and international standards, such as ISO 9001 or UN certification for hazardous materials. Conduct thorough research on potential suppliers by requesting documentation that verifies their compliance. Additionally, establish a clear set of specifications that detail the required material properties, capacity, and safety features. Engaging with suppliers who specialize in your industry can also enhance your procurement process, as they often have tailored solutions that meet specific needs.
Scenario 2: Addressing Supply Chain Disruptions in Jerrycan Availability
The Problem: International buyers often face supply chain disruptions due to geopolitical issues, natural disasters, or pandemic-related challenges. For example, a jerrycan supplier in Europe may experience delays in production or shipping, leading to stock shortages for a buyer in the Middle East who relies on timely deliveries for their operations. This can severely impact business continuity and customer satisfaction.
The Solution: To mitigate the risk of supply chain disruptions, B2B buyers should diversify their supplier base. Instead of relying on a single supplier, consider establishing relationships with multiple jerrycan suppliers across different regions. This strategy not only provides alternatives in case of disruptions but also allows for competitive pricing. Additionally, implementing a just-in-time inventory system can help manage stock levels effectively and ensure that you always have the necessary supplies on hand. Regular communication with suppliers about their capacity and production timelines can further enhance planning and reduce the impact of unforeseen delays.
Scenario 3: Finding Cost-Effective Jerrycan Solutions without Compromising Quality
The Problem: Many B2B buyers are under pressure to reduce costs while maintaining product quality. This is particularly true for buyers in emerging markets in Africa and South America, where budget constraints are common. A buyer might find themselves inundated with low-cost jerrycan options that compromise on durability, leading to leaks or breakages during transport.
The Solution: To strike the right balance between cost and quality, buyers should conduct a total cost of ownership analysis rather than simply focusing on upfront costs. This involves evaluating factors such as durability, potential for reuse, and long-term reliability. Look for suppliers that offer a warranty or guarantee on their products, as this can be an indicator of quality. Consider investing in jerrycans made from high-density polyethylene (HDPE) or other durable materials, which may have a higher initial cost but provide better longevity and reduced replacement expenses. Additionally, negotiating bulk purchase agreements can lead to significant savings without compromising on the quality of the jerrycans.
Strategic Material Selection Guide for jerrycan supplier
When selecting materials for jerrycans, international B2B buyers must consider various factors that influence product performance, cost, and compliance with regional standards. Below is an analysis of four common materials used in jerrycan manufacturing: High-Density Polyethylene (HDPE), Polypropylene (PP), Steel, and Aluminum. Each material has distinct properties that affect its suitability for different applications.
What are the Key Properties of High-Density Polyethylene (HDPE) for Jerrycans?
High-Density Polyethylene (HDPE) is a widely used material for jerrycans due to its excellent chemical resistance and durability. It can withstand temperatures ranging from -40°C to 60°C, making it suitable for various climates, especially in regions like Africa and the Middle East. HDPE is also resistant to impact and does not corrode, which is crucial for transporting liquids.
Pros & Cons: The primary advantages of HDPE include its lightweight nature, cost-effectiveness, and recyclability. However, it may not be suitable for high-pressure applications and can become brittle at low temperatures, which could be a concern in colder climates.
Impact on Application: HDPE is compatible with a wide range of chemicals, including acids and bases, making it ideal for agricultural and industrial applications. Buyers should ensure that the specific chemical compatibility meets their operational needs.
Considerations for International Buyers: Compliance with standards such as ASTM D3350 for HDPE is essential. Buyers in Europe, for example, may also need to consider REACH regulations regarding chemical safety.
How Does Polypropylene (PP) Compare for Jerrycan Manufacturing?
Polypropylene (PP) is another popular choice for jerrycans, known for its higher temperature resistance compared to HDPE, withstanding temperatures up to 100°C. This makes PP suitable for applications involving hot liquids or sterilization processes.
Pros & Cons: The advantages of PP include its excellent fatigue resistance and ability to be molded into complex shapes. However, it is generally more expensive than HDPE and may not offer the same level of chemical resistance for certain solvents.
Impact on Application: PP is particularly effective for storing food products and chemicals that require a higher temperature tolerance. It is essential for buyers to verify the specific grades of PP used to ensure they meet food safety standards.
Considerations for International Buyers: Buyers should look for compliance with international standards such as ISO 22000 for food safety and consider regional regulations that may affect the choice of PP.
What Role Does Steel Play in Jerrycan Applications?
Steel jerrycans are renowned for their strength and durability, making them suitable for heavy-duty applications. They can handle high pressures and temperatures, making them ideal for transporting fuels and hazardous materials.
Pros & Cons: The primary advantage of steel is its robustness and resistance to punctures. However, steel jerrycans are heavier and prone to corrosion if not properly coated, which can increase maintenance costs.
Impact on Application: Steel is compatible with a wide variety of liquids, including petroleum products. Buyers must ensure that the jerrycans are treated to prevent rust and corrosion, especially in humid climates.
Considerations for International Buyers: Compliance with standards such as ASTM A653 for galvanized steel is crucial. Buyers in regions like South America and Europe should also be aware of environmental regulations regarding the transport of hazardous materials.
How Does Aluminum Compare as a Material for Jerrycans?
Aluminum jerrycans are lightweight and resistant to corrosion, making them an excellent choice for transporting beverages and chemicals. They can withstand temperatures from -30°C to 70°C, offering versatility in various climates.
Pros & Cons: The key advantages of aluminum include its lightweight nature and resistance to rust. However, aluminum can be more expensive than plastic options and may not be suitable for all chemical applications due to potential reactivity.
Impact on Application: Aluminum is particularly suitable for food and beverage storage, as it does not impart flavors or odors. Buyers should ensure that the aluminum used is food-grade and complies with relevant health standards.
Considerations for International Buyers: Compliance with standards such as ISO 9001 for quality management systems is essential for aluminum products. Buyers should also consider the recycling capabilities of aluminum in their region.
Summary Table of Material Selection for Jerrycans
Material | Typical Use Case for jerrycan supplier | Key Advantage | Key Disadvantage/Limitation | Relative Cost (Low/Med/High) |
---|---|---|---|---|
HDPE | Chemical storage, agricultural use | Lightweight, cost-effective | Brittle at low temperatures | Low |
Polypropylene | Food storage, hot liquids | Higher temperature resistance | More expensive than HDPE | Medium |
Steel | Fuels, hazardous materials | Strong and durable | Heavier, prone to corrosion | Medium |
Aluminum | Beverages, food products | Lightweight, corrosion-resistant | More expensive, potential reactivity | High |
This strategic material selection guide provides international B2B buyers with critical insights into choosing the right jerrycan material based on performance, application, and compliance factors.
In-depth Look: Manufacturing Processes and Quality Assurance for jerrycan supplier
What Are the Key Stages in the Manufacturing Process of Jerrycans?
The manufacturing process of jerrycans involves several critical stages that ensure the final product meets industry standards for durability and usability. Understanding these stages can help international B2B buyers assess the efficiency and reliability of potential suppliers.
Material Preparation: What Materials Are Used?
The primary material used in the production of jerrycans is high-density polyethylene (HDPE), chosen for its strength, chemical resistance, and lightweight properties. The first step involves sourcing high-quality raw materials from reputable suppliers, followed by material inspection. Buyers should inquire about the source of these materials and any certifications the suppliers hold, which can indicate the quality and safety of the jerrycans.
Forming: How Are Jerrycans Shaped?
The forming process typically employs techniques such as blow molding or injection molding. In blow molding, a preform is heated and then inflated within a mold to achieve the desired shape. Injection molding involves injecting molten plastic into a mold to create the jerrycan shape. Each method has its benefits, with blow molding generally being more efficient for larger production runs. B2B buyers should ask suppliers about their specific forming techniques and the associated production capacities to ensure they can meet demand.
Assembly: What Happens During Assembly?
Once the jerrycans are formed, the assembly stage focuses on adding components such as lids and spouts. This may involve welding or snap-fitting, depending on the design. Quality buyers should ensure that the assembly process is automated where possible, as this reduces human error and improves consistency. Additionally, they should inquire about the use of automated quality checks during this stage to enhance product reliability.
Finishing: How Are Jerrycans Finished?
The finishing stage involves surface treatments such as printing labels, applying UV protection, and inspecting for imperfections. This is a crucial phase, as it not only enhances the aesthetic appeal of the jerrycans but also improves their resistance to environmental factors. Buyers should verify if the finishing processes adhere to international standards, particularly for products intended for export.
What Quality Assurance Practices Should B2B Buyers Expect?
Quality assurance is paramount in jerrycan manufacturing, as it directly impacts the product’s performance and safety. Understanding the quality control practices can help buyers ensure they are partnering with reliable suppliers.
What Are the Relevant International Standards for Jerrycans?
Manufacturers of jerrycans should comply with international quality management standards such as ISO 9001, which focuses on consistent quality and customer satisfaction. Additionally, industry-specific certifications like CE marking (for compliance with European safety standards) and API certification (for petroleum containers) may be relevant. B2B buyers should request proof of these certifications to verify compliance.
What Are the Key Quality Control Checkpoints?
Quality control in jerrycan manufacturing typically involves several checkpoints, including:
- Incoming Quality Control (IQC): Materials are inspected upon arrival to ensure they meet specifications.
- In-Process Quality Control (IPQC): Continuous monitoring during production to catch defects early.
- Final Quality Control (FQC): A thorough inspection of finished products before shipment.
Buyers should inquire about the specific QC processes their suppliers have in place and request documentation of any quality audits conducted.
What Common Testing Methods Are Used?
Testing methods for jerrycans may include:
- Drop Tests: Assessing the impact resistance of the jerrycans.
- Leak Tests: Ensuring that the containers do not leak under pressure.
- Chemical Resistance Tests: Evaluating how well the jerrycans withstand various substances.
B2B buyers should ask for test reports or certifications that demonstrate these tests have been performed and passed.
How Can Buyers Verify Supplier Quality Control?
Verifying a supplier’s quality control practices is crucial for international B2B buyers. Here are some actionable steps:
What Should Buyers Look for in Supplier Audits?
Buyers should conduct thorough audits of potential suppliers. This involves visiting manufacturing facilities to observe processes firsthand and assess the effectiveness of their quality control systems. During the audit, buyers should evaluate the cleanliness of the production environment, the machinery used, and the qualifications of personnel.
How Can Buyers Use Reports and Certifications?
Requesting quality control reports and certifications from suppliers is essential. These documents provide insight into the supplier’s commitment to quality and compliance with international standards. Buyers should look for recent reports that reflect current practices, as older documents may not accurately represent the supplier’s capabilities.
What Role Do Third-Party Inspections Play?
Engaging third-party inspection services can provide an unbiased evaluation of a supplier’s quality control practices. These inspections can occur at various stages of the manufacturing process and can help identify potential issues before products are shipped. Buyers should consider incorporating third-party inspections into their procurement process, especially when dealing with suppliers from regions with varying quality standards.
What Are the Quality Control Nuances for International B2B Buyers?
For international buyers, especially those in Africa, South America, the Middle East, and Europe, understanding the nuances of quality control is vital. Different regions may have varying regulatory requirements and quality expectations.
How Do Regional Standards Affect Quality Assurance?
Buyers should familiarize themselves with the specific quality standards applicable in their own regions. For instance, Europe has stringent regulations for plastic products, while certain countries in Africa may have less rigorous standards. Suppliers should demonstrate awareness of these standards and provide products that meet or exceed them.
What Should Buyers Know About Import Regulations?
Import regulations can also affect the quality of jerrycans. Buyers should ensure that suppliers are compliant with the import regulations of their respective countries, which may include certifications, labeling, and safety requirements. Failure to comply can result in delays or additional costs.
Conclusion: How to Ensure Quality in Your Jerrycan Supply Chain
In conclusion, the manufacturing processes and quality assurance practices of jerrycan suppliers are fundamental to ensuring product reliability. By understanding the key stages of production, verifying supplier capabilities, and being aware of regional standards, international B2B buyers can make informed decisions. This proactive approach not only mitigates risks but also enhances supply chain efficiency, ultimately leading to better business outcomes.
Practical Sourcing Guide: A Step-by-Step Checklist for ‘jerrycan supplier’
In the competitive landscape of international B2B procurement, sourcing the right jerrycan supplier is critical for ensuring quality, reliability, and compliance with regional standards. This checklist serves as a practical guide for buyers from Africa, South America, the Middle East, and Europe, helping you navigate the sourcing process effectively.
Step 1: Define Your Technical Specifications
Understanding your specific requirements is the foundation of effective sourcing. Begin by detailing the dimensions, materials (e.g., HDPE or metal), capacities, and any certifications necessary for your jerrycans, such as UN approval for hazardous materials. Clearly defined specifications will streamline the selection process and ensure suppliers can meet your needs.
Step 2: Research Potential Suppliers
Utilize online platforms and trade directories to identify potential suppliers. Look for companies with a strong reputation in the industry, particularly those with experience in your region. Pay attention to reviews and ratings to gauge their reliability and service quality.
Step 3: Evaluate Supplier Certifications
✅ Verify Supplier Certifications
Certifications are crucial for ensuring that your supplier meets industry standards. Check for ISO certifications, safety standards, and compliance with local regulations in the regions you operate in. This step helps to mitigate risks associated with product quality and legal compliance.
Step 4: Request Product Samples
Before making a large order, request samples of the jerrycans to evaluate their quality firsthand. This step allows you to assess the durability, design, and suitability for your specific applications. It’s also an opportunity to check for any customization options that may be necessary for your business needs.
Step 5: Assess Manufacturing Capabilities
Understanding a supplier’s manufacturing capabilities can provide insights into their ability to meet your volume and delivery timelines. Inquire about production capacities, lead times, and technology used in the manufacturing process. This assessment can help you avoid delays and ensure that the supplier can scale with your business growth.
Step 6: Negotiate Terms and Pricing
Once you have shortlisted potential suppliers, it’s time to discuss pricing and terms. Be transparent about your budget and expectations, and don’t hesitate to negotiate for better terms, such as bulk discounts, payment plans, and delivery schedules. Ensure all agreements are documented to protect your interests.
Step 7: Establish a Communication Plan
Effective communication is key to a successful supplier relationship. Establish a clear communication plan that outlines preferred channels, frequency of updates, and points of contact. Regular check-ins can help identify potential issues early and foster a strong partnership.
By following this checklist, international B2B buyers can streamline their sourcing process for jerrycans, ensuring they partner with suppliers that meet their technical, quality, and compliance needs.
Comprehensive Cost and Pricing Analysis for jerrycan supplier Sourcing
What Are the Key Cost Components in Jerrycan Supplier Sourcing?
Understanding the cost structure of jerrycan suppliers is essential for international B2B buyers aiming to optimize their sourcing decisions. The primary cost components include:
-
Materials: The choice of materials significantly impacts pricing. Common materials for jerrycans include high-density polyethylene (HDPE) and polypropylene, which vary in cost based on market fluctuations. Prices can be affected by the global supply chain, making it crucial to monitor trends.
-
Labor: Labor costs are influenced by the location of the manufacturing facility. Countries with lower labor costs may offer more competitive pricing, but this could come at the expense of quality. It’s essential to assess labor quality and efficiency when evaluating suppliers.
-
Manufacturing Overhead: This encompasses costs related to utilities, rent, and operational expenses. A manufacturer with efficient overhead management can provide more competitive pricing without compromising quality.
-
Tooling: Custom tooling can be a significant upfront cost, especially for specialized jerrycan designs. Buyers should factor in these costs when considering custom solutions, as they can impact the overall price.
-
Quality Control (QC): Implementing rigorous QC processes adds to the cost but is vital for ensuring product reliability. Certifications like ISO can also influence pricing, as they require compliance with international standards.
-
Logistics: Transportation and warehousing costs can vary widely based on the supplier’s location and the chosen shipping method. Understanding Incoterms is crucial for managing these costs effectively.
-
Margin: Suppliers will typically include a profit margin in their pricing. This margin can vary based on supplier reputation, market demand, and negotiation leverage.
What Influences Pricing for International B2B Buyers?
Several factors can influence the pricing of jerrycans, particularly for international buyers:
-
Volume and Minimum Order Quantity (MOQ): Purchasing in bulk can lead to significant discounts. Negotiating MOQs is essential, especially for buyers looking to minimize costs.
-
Specifications and Customization: Custom designs or specifications can increase costs. Buyers should weigh the benefits of customization against potential price increases.
-
Materials and Quality Certifications: Higher quality materials and certifications (like FDA approval for food-grade jerrycans) can raise prices. Buyers should assess the necessity of these features based on their end-use.
-
Supplier Factors: The reputation and reliability of suppliers can impact pricing. Established suppliers may charge more due to perceived quality, while newer entrants may offer lower prices to gain market share.
-
Incoterms: Understanding the implications of Incoterms can help buyers manage logistics costs effectively. Terms like FOB (Free on Board) or CIF (Cost, Insurance, and Freight) can significantly affect the total cost of ownership.
How Can Buyers Optimize Costs When Sourcing Jerrycans?
To enhance cost-efficiency in sourcing jerrycans, buyers should consider the following strategies:
-
Negotiate Effectively: Leverage volume purchases to negotiate better terms. Building long-term relationships with suppliers can also lead to favorable pricing.
-
Evaluate Total Cost of Ownership (TCO): Instead of focusing solely on unit price, assess the TCO, which includes logistics, quality, and potential waste. This holistic approach can reveal better value options.
-
Research Market Trends: Stay informed about material costs and market dynamics. Engaging in regular market analysis can empower buyers to make timely sourcing decisions.
-
Consider Regional Suppliers: For buyers in Africa, South America, the Middle East, and Europe, sourcing from regional suppliers can reduce logistics costs and lead times.
-
Request Samples: Before committing to large orders, request samples to evaluate quality and ensure they meet specifications. This can prevent costly mistakes down the line.
What Should Buyers Keep in Mind Regarding Pricing Nuances?
International B2B buyers must be aware of various pricing nuances when sourcing jerrycans:
-
Indicative Prices: Prices can fluctuate based on market conditions, so always request updated quotes. Understand that the quoted prices may not include all costs, such as tariffs or local taxes.
-
Currency Exchange Rates: For buyers purchasing from foreign suppliers, currency fluctuations can impact total costs. It may be beneficial to negotiate prices in a stable currency.
-
Cultural Considerations: Understanding the business culture of the supplier’s country can aid in negotiations and establish a more favorable purchasing environment.
By considering these factors, international B2B buyers can make informed, strategic decisions in sourcing jerrycans, ultimately leading to cost savings and enhanced operational efficiency.
Alternatives Analysis: Comparing jerrycan supplier With Other Solutions
When evaluating jerrycan suppliers, it’s crucial for international B2B buyers to consider various alternatives that may provide similar functionalities. The right choice can significantly impact logistics, cost efficiency, and product integrity. Below, we will compare jerrycan suppliers against two notable alternatives: bulk containers and reusable pouches.
Comparison Aspect | Jerrycan Supplier | Bulk Containers | Reusable Pouches |
---|---|---|---|
Performance | High durability and protection for liquids | Suitable for large volumes but may lack flexibility | Good for smaller quantities, lightweight, but less robust |
Cost | Moderate initial investment with long-term savings | Lower cost per unit at large scale, but high upfront cost | Generally low cost, especially for small quantities |
Ease of Implementation | Straightforward procurement and use | Requires additional infrastructure for storage and handling | Easy to deploy but may require training for proper use |
Maintenance | Minimal maintenance needed | May require regular cleaning and inspections | Typically low maintenance but can wear out quickly |
Best Use Case | Ideal for transporting hazardous materials and liquids | Best for bulk shipping and storage of non-hazardous liquids | Perfect for smaller businesses with limited space and budget |
What Are the Advantages and Disadvantages of Bulk Containers?
Bulk containers are designed for transporting large quantities of liquids, making them an appealing choice for businesses dealing with high volumes. Their primary advantage lies in cost efficiency; the more you buy, the lower the per-unit cost becomes. However, they require specialized handling and storage, which can complicate logistics. Additionally, bulk containers may not provide the same level of protection as jerrycans, particularly for sensitive or hazardous materials.
How Do Reusable Pouches Compare to Jerrycans?
Reusable pouches offer a lightweight and flexible alternative, ideal for businesses that need to transport smaller quantities of liquids. They are generally more affordable and can be easily deployed, making them a good fit for startups or companies with limited budgets. However, they may lack the durability and protection offered by jerrycans, which could lead to potential leaks or contamination. While they require less investment, their lifespan may be shorter, resulting in more frequent replacements.
Conclusion: How Can B2B Buyers Choose the Right Solution?
Choosing between a jerrycan supplier, bulk containers, and reusable pouches hinges on several factors, including the type of liquid being transported, volume requirements, and budget constraints. For businesses handling hazardous materials or needing high durability, jerrycans may be the best option despite a moderate initial investment. Conversely, bulk containers can offer significant savings for larger operations, while reusable pouches cater to smaller businesses looking for cost-effective solutions. Understanding these alternatives allows international B2B buyers to make informed decisions tailored to their unique operational needs.
Essential Technical Properties and Trade Terminology for jerrycan supplier
What Are the Essential Technical Properties of Jerrycans?
When sourcing jerrycans, understanding their technical properties is crucial for ensuring they meet your operational needs. Here are some key specifications to consider:
1. Material Grade: Why Is It Important?
Jerrycans are primarily made from materials like high-density polyethylene (HDPE) or polypropylene. The material grade affects durability, resistance to chemicals, and UV stability. For instance, HDPE is known for its excellent resistance to impact and a broad range of chemicals, making it suitable for various applications, from fuel storage to transporting food products. When selecting a supplier, inquire about the specific material grade to ensure it aligns with your intended use.
2. Tolerance Levels: How Do They Impact Quality?
Tolerance levels refer to the permissible limits of variation in jerrycan dimensions. This property is vital as it ensures that the jerrycans fit securely with closures and within any transportation systems. High tolerance levels can reduce leaks and spills, thereby protecting your product integrity. Ensure your supplier provides detailed tolerance specifications that comply with industry standards.
3. Capacity: What Size Do You Need?
Jerrycans come in various capacities, typically ranging from 1 liter to 60 liters. Selecting the right capacity is essential for logistics and storage efficiency. For instance, a larger capacity can reduce the number of trips needed for transportation but may require more robust handling processes. Assess your operational needs to determine the appropriate sizes to order.
4. Chemical Compatibility: Why Does It Matter?
Chemical compatibility indicates how well a jerrycan can withstand the substances it will contain. Different materials react differently to various chemicals, which can lead to degradation, leaks, or contamination. Always consult with your supplier regarding the chemical compatibility of the jerrycans with the intended contents, especially for hazardous materials.
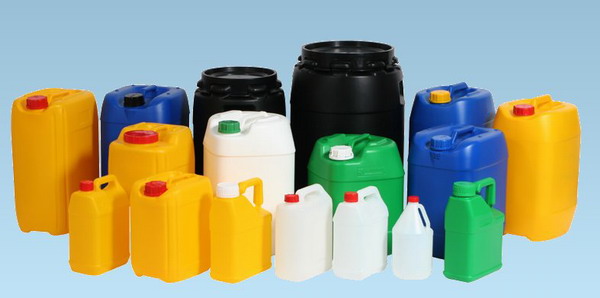
A stock image related to jerrycan supplier.
5. UV Resistance: What Should You Consider?
If you plan to store jerrycans outdoors or in areas exposed to sunlight, UV resistance becomes a significant factor. Jerrycans lacking UV protection can become brittle over time, leading to leaks or structural failures. Verify that your supplier provides jerrycans designed for UV stability, particularly if you operate in regions with high sun exposure.
What Are Common Trade Terms Used in the Jerrycan Industry?
Familiarizing yourself with industry jargon can facilitate smoother negotiations and transactions. Here are some essential terms:
1. OEM (Original Equipment Manufacturer): What Does It Mean?
OEM refers to companies that produce parts or products that can be marketed by another company. In the context of jerrycans, an OEM supplier may manufacture jerrycans that are branded and sold under another company’s name. Understanding OEM relationships can help you identify potential suppliers who can provide custom solutions.
2. MOQ (Minimum Order Quantity): How Does It Affect Your Purchase?
MOQ is the minimum number of units a supplier is willing to sell in a single order. This term is crucial for B2B buyers, as it can impact cash flow and inventory management. When sourcing jerrycans, be aware of the MOQ to ensure it aligns with your purchasing strategy and budget.
3. RFQ (Request for Quotation): Why Is It Necessary?
An RFQ is a document sent to suppliers to request pricing and terms for specific products or services. This process is essential for comparing suppliers and ensuring you receive competitive pricing for jerrycans. Always include detailed specifications in your RFQ to receive accurate quotes.
4. Incoterms (International Commercial Terms): What Should You Know?
Incoterms are a set of predefined international rules that clarify the responsibilities of buyers and sellers in global trade. They dictate who is responsible for shipping, insurance, and tariffs. Understanding these terms can help you avoid unexpected costs and ensure smooth logistics when importing jerrycans.
5. Lead Time: How Does It Impact Your Supply Chain?
Lead time refers to the time it takes from placing an order to receiving the goods. This is a critical factor for B2B operations as it affects inventory levels and production schedules. Discuss lead times with your supplier to ensure that they can meet your operational requirements.
By grasping these technical properties and trade terms, international B2B buyers can make informed decisions when sourcing jerrycans, ensuring they select the right products for their specific needs.
Navigating Market Dynamics and Sourcing Trends in the jerrycan supplier Sector
What Are the Current Market Dynamics and Key Trends in the Jerrycan Supplier Sector?
The jerrycan supplier sector is experiencing significant shifts driven by global demand for versatile and durable packaging solutions. Increasing industrial activities across Africa, South America, the Middle East, and Europe are propelling the need for jerrycans, particularly in sectors like chemicals, food and beverage, and pharmaceuticals. The rise in e-commerce and logistics services has further amplified the demand for reliable packaging to ensure product safety during transportation.
Emerging technologies such as advanced polymer materials and manufacturing automation are reshaping how jerrycans are produced. Suppliers are increasingly adopting digital tools for inventory management, supply chain optimization, and customer relationship management, enhancing operational efficiency. International buyers should be aware of these technological advancements, as they can impact pricing and lead times. Additionally, the trend towards custom packaging solutions is gaining traction, allowing buyers to meet specific regulatory requirements and branding needs.
Furthermore, the growing emphasis on cost-effectiveness and just-in-time (JIT) sourcing strategies is compelling suppliers to streamline their operations. Buyers from diverse regions, including Europe and the Middle East, should leverage these market dynamics to negotiate better terms and ensure they are sourcing from manufacturers capable of adapting to changing demands.
How Are Sustainability and Ethical Sourcing Affecting the Jerrycan Supplier Sector?
Sustainability is becoming a pivotal factor in the jerrycan supplier sector, as international buyers increasingly prioritize environmentally friendly practices. The production of jerrycans, particularly those made from virgin plastics, poses environmental challenges, leading to calls for more sustainable alternatives. Buyers should seek suppliers who utilize recycled materials and implement eco-friendly production processes, reducing their carbon footprint.
Ethical sourcing is also gaining prominence, with buyers demanding transparency in supply chains. Suppliers that can demonstrate responsible sourcing practices, such as fair labor conditions and compliance with environmental regulations, are more likely to attract business. Certifications like ISO 14001 (Environmental Management) and the use of biodegradable materials are indicators of a supplier’s commitment to sustainability.
For B2B buyers, aligning with suppliers who prioritize sustainability not only enhances brand reputation but also meets increasing regulatory pressures in various markets. By choosing jerrycan suppliers with a focus on ethical and sustainable practices, businesses can contribute to a greener future while ensuring compliance with local and international standards.
What Is the Brief Evolution of the Jerrycan Supplier Sector?
The jerrycan has a storied history that dates back to World War II when it was originally designed for military use, providing a robust solution for transporting fuel and water. Over the decades, the versatility of jerrycans has led to their widespread adoption across various industries. Initially made from metal, the evolution to high-density polyethylene (HDPE) has transformed the sector, offering lighter, more durable, and cost-effective options.
As consumer preferences shift towards sustainable packaging, the jerrycan supplier sector is poised for further evolution, adapting to both technological advancements and environmental imperatives. Understanding this historical context can provide international B2B buyers with insights into the current market landscape and future trends, enabling more informed sourcing decisions.
Frequently Asked Questions (FAQs) for B2B Buyers of jerrycan supplier
-
How do I choose the right jerrycan supplier for my business needs?
Choosing the right jerrycan supplier involves evaluating several key factors. First, assess their product quality and compliance with industry standards, as this ensures safety and durability. Second, consider the supplier’s experience in your specific industry and their ability to meet your customization needs. Third, review customer testimonials and case studies to gauge reliability and service quality. Finally, engage in direct communication to discuss your requirements and gauge their responsiveness and expertise. -
What are the minimum order quantities (MOQ) for jerrycans from suppliers?
Minimum order quantities can vary significantly between suppliers and depend on factors such as material, size, and customization options. Typically, MOQs for jerrycans range from 500 to 5,000 units. For international buyers, negotiating MOQs is often possible, especially if you are willing to establish a long-term relationship. It’s advisable to discuss your specific needs with potential suppliers to find a mutually beneficial arrangement. -
What customization options are available for jerrycans?
Many jerrycan suppliers offer a range of customization options, including color, size, and branding. You can often request specific features such as spouts, handles, or unique cap designs to suit your product’s storage and transportation needs. Additionally, suppliers may provide printing services for your logo or other branding elements. When considering customization, ensure that your supplier has the capability and experience to deliver high-quality results. -
What payment terms should I expect when working with jerrycan suppliers?
Payment terms can vary widely among jerrycan suppliers, often influenced by the supplier’s location and your relationship with them. Common terms include a deposit upfront, followed by payment upon shipment or net 30/60 days after delivery. International buyers should be aware of currency exchange rates and transaction fees. Always clarify payment terms in the contract to avoid misunderstandings and ensure that they align with your cash flow requirements. -
How can I ensure quality assurance when sourcing jerrycans internationally?
To ensure quality assurance, conduct thorough supplier vetting by checking certifications, quality control processes, and past customer feedback. Request samples before placing a bulk order to evaluate material quality and construction. Additionally, consider employing third-party inspection services to verify product standards before shipment. Establishing clear quality benchmarks in your contract can also help hold suppliers accountable for product quality. -
What logistics considerations should I keep in mind when importing jerrycans?
Logistics is crucial when importing jerrycans. Consider factors such as shipping methods, lead times, and customs clearance procedures. Evaluate whether your supplier offers assistance with logistics or if you need to engage a freight forwarder. Be mindful of import regulations in your country, as well as any tariffs or duties applicable to jerrycans. Planning for potential delays and ensuring you have the necessary documentation will facilitate a smoother import process. -
What are the common materials used in jerrycan production, and how do they affect pricing?
Jerrycans are commonly made from high-density polyethylene (HDPE) or metal. HDPE jerrycans are lightweight, durable, and resistant to chemicals, making them popular for various applications. Metal jerrycans, while heavier, offer superior strength and are often used for hazardous materials. Pricing can fluctuate based on material costs, manufacturing processes, and customization options. Understanding your specific requirements will help you choose the right material without compromising your budget. -
How can I build a long-term relationship with my jerrycan supplier?
Building a long-term relationship with your jerrycan supplier involves consistent communication and mutual trust. Start by clearly outlining your expectations and requirements from the beginning. Regularly provide feedback on product quality and service, fostering a partnership approach. Consider negotiating favorable terms for bulk orders or long-term contracts to strengthen the relationship. Attending industry events or trade shows can also facilitate personal connections and enhance collaboration.
Important Disclaimer & Terms of Use
⚠️ Important Disclaimer
The information provided in this guide, including content regarding manufacturers, technical specifications, and market analysis, is for informational and educational purposes only. It does not constitute professional procurement advice, financial advice, or legal advice.
While we have made every effort to ensure the accuracy and timeliness of the information, we are not responsible for any errors, omissions, or outdated information. Market conditions, company details, and technical standards are subject to change.
B2B buyers must conduct their own independent and thorough due diligence before making any purchasing decisions. This includes contacting suppliers directly, verifying certifications, requesting samples, and seeking professional consultation. The risk of relying on any information in this guide is borne solely by the reader.
Strategic Sourcing Conclusion and Outlook for jerrycan supplier
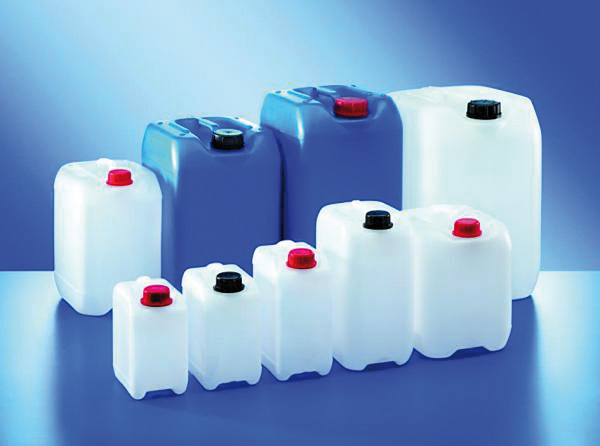
A stock image related to jerrycan supplier.
As the global market for jerrycan suppliers continues to evolve, strategic sourcing emerges as a pivotal component for international B2B buyers. By focusing on quality, cost-effectiveness, and supplier reliability, businesses can streamline their procurement processes and enhance their supply chain resilience. Buyers from Africa, South America, the Middle East, and Europe must prioritize partnerships with suppliers who not only meet product specifications but also align with their sustainability goals and compliance requirements.
What are the key benefits of strategic sourcing for jerrycan procurement? Leveraging robust supplier networks can lead to significant cost savings, improved product availability, and enhanced innovation through collaboration. Additionally, understanding regional market dynamics will empower buyers to make informed decisions that align with local regulations and customer expectations.
Looking ahead, the demand for durable and eco-friendly jerrycans is set to rise, driven by increasing environmental awareness and regulatory changes. B2B buyers should act now to reassess their sourcing strategies and engage with suppliers who are committed to sustainable practices. By doing so, they will not only secure a competitive edge but also contribute positively to their respective markets. Take the next step in your sourcing journey and explore partnerships that will drive your business forward.