Discover Top Tips to Choose a Tray Manufacturer (2025)
Introduction: Navigating the Global Market for tray manufacturer
Navigating the complexities of the global market for tray manufacturers can be a daunting task for international B2B buyers, especially when sourcing high-quality trays that meet specific needs. With a diverse range of applications—from food service to industrial packaging—the challenge lies not only in identifying the right type of tray but also in ensuring that suppliers can deliver consistent quality and value. This comprehensive guide aims to illuminate the various types of trays available, their applications across different industries, and the critical considerations for vetting suppliers effectively.
International buyers from regions such as Africa, South America, the Middle East, and Europe, including countries like Italy and Nigeria, face unique market dynamics and regulatory environments that influence their purchasing decisions. Understanding these factors is essential for making informed choices that align with business objectives. Throughout this guide, you will find actionable insights on cost considerations, quality standards, and logistical aspects that can impact your sourcing strategy.
By equipping you with the knowledge to navigate supplier landscapes, assess product specifications, and negotiate effectively, this guide empowers you to make well-informed purchasing decisions. Whether you are looking for eco-friendly options or specialized designs, the insights provided will help you streamline your procurement process and enhance your operational efficiency.
Understanding tray manufacturer Types and Variations
Type Name | Key Distinguishing Features | Primary B2B Applications | Brief Pros & Cons for Buyers |
---|---|---|---|
Plastic Trays | Lightweight, versatile, and available in various colors and sizes | Food service, medical, and retail sectors | Pros: Cost-effective, easy to clean. Cons: Less durable than metal options. |
Metal Trays | Durable, often rust-resistant, and can be customized with coatings | Industrial, culinary, and packaging sectors | Pros: Long-lasting, high heat resistance. Cons: Heavier and more expensive. |
Foam Trays | Lightweight, disposable, and typically used for food packaging | Food service, grocery, and takeaway sectors | Pros: Convenient for single-use, affordable. Cons: Environmental concerns with disposability. |
Wooden Trays | Eco-friendly, aesthetically pleasing, and often handcrafted | Gift, hospitality, and decorative sectors | Pros: Unique designs, sustainable. Cons: Higher cost, less durability for heavy use. |
Custom Trays | Tailored designs to specific needs, materials, and sizes | Specialized manufacturing and logistics | Pros: Meets exact specifications, enhances brand image. Cons: Longer lead times, potentially higher costs. |
What are the characteristics and suitability of plastic trays for B2B buyers?
Plastic trays are renowned for their lightweight and versatile nature, making them suitable for a broad range of applications, especially in the food service and medical sectors. They come in various sizes and colors, allowing businesses to select options that fit their specific needs. When purchasing plastic trays, buyers should consider factors such as durability, ease of cleaning, and compliance with health regulations. While they are cost-effective and practical for everyday use, it is essential to note that they may not withstand heavy loads or extreme temperatures as well as metal trays.
How do metal trays differ from other tray types?
Metal trays are distinguished by their durability and resistance to rust, making them an excellent choice for industrial and culinary applications. These trays can be customized with various coatings to enhance their usability, such as non-stick surfaces for easy food release. Buyers should consider the weight and cost of metal trays, as they tend to be heavier and more expensive than plastic alternatives. However, their longevity and heat resistance make them a worthwhile investment for businesses that require reliable and robust tray solutions.
Why are foam trays popular in the food service industry?
Foam trays are lightweight and designed primarily for disposable use, making them ideal for the food service, grocery, and takeaway sectors. Their affordability and convenience are significant advantages for businesses that prioritize efficiency and cost-effectiveness. However, buyers should be mindful of the environmental implications associated with disposability. When selecting foam trays, it is crucial to ensure they comply with food safety standards, as this can impact the overall quality and safety of food packaging.
What makes wooden trays a unique option for B2B buyers?
Wooden trays stand out for their eco-friendly properties and aesthetic appeal, often used in the gift and hospitality sectors. Their handcrafted nature can provide a unique touch that enhances brand image and customer experience. However, buyers should consider the higher costs associated with wooden trays and their limited durability for heavy-duty applications. When opting for wooden trays, it is essential to evaluate their treatment and finishes to ensure they meet the necessary health and safety standards for food contact.
How do custom trays cater to specific business needs?
Custom trays are tailored to meet the exact specifications of a business, including size, material, and design. This customization allows companies to enhance their branding and ensure functionality aligns with operational needs. While the primary advantages of custom trays include meeting specific requirements and improving brand visibility, buyers should be prepared for longer lead times and potentially higher costs. Understanding the manufacturing process and timelines is essential for businesses looking to integrate custom trays into their supply chain effectively.
Related Video: Types Of Cable Trays | Cable Tray manufacturer | Cable tray information | No.1 Quality of Cable Tray
Key Industrial Applications of tray manufacturer
Industry/Sector | Specific Application of tray manufacturer | Value/Benefit for the Business | Key Sourcing Considerations for this Application |
---|---|---|---|
Food and Beverage | Food trays for packaging and transportation | Enhances product presentation and minimizes spoilage | Material compliance, temperature resistance, and hygiene standards |
Pharmaceuticals | Trays for medical device and pharmaceutical packaging | Ensures safety and integrity of sensitive products | Regulatory compliance, customization options, and sterilization capabilities |
Electronics | Trays for component storage and transport | Protects components from damage and facilitates logistics | Anti-static properties, durability, and size specifications |
Agriculture | Seedling trays for plant propagation | Promotes healthy growth and efficient planting | Material type (biodegradable vs. plastic), drainage features, and size |
Automotive | Trays for parts storage and assembly line organization | Increases efficiency and reduces handling errors | Customization for specific parts, durability, and stackability |
How Are Tray Manufacturers Utilized in the Food and Beverage Sector?
In the food and beverage industry, tray manufacturers produce food trays designed for packaging and transportation. These trays not only enhance the visual appeal of products but also help minimize spoilage during transit. Buyers from regions like Africa and South America should prioritize sourcing trays that comply with food safety regulations and possess temperature resistance to ensure the integrity of perishable goods. Additionally, hygiene standards are critical, necessitating materials that are easy to clean and safe for food contact.
What Role Do Tray Manufacturers Play in Pharmaceuticals?
Tray manufacturers serve a crucial role in the pharmaceutical sector by providing trays for medical device and pharmaceutical packaging. These trays are designed to ensure the safety and integrity of sensitive products, which is essential given the stringent regulations governing this industry. International B2B buyers should consider the regulatory compliance of the trays they purchase, including customization options that meet specific product requirements and sterilization capabilities to maintain product efficacy.
How Are Tray Manufacturers Beneficial to the Electronics Industry?
In the electronics sector, tray manufacturers create specialized trays for the storage and transport of components. These trays protect sensitive electronic parts from damage during handling and transport, thus ensuring operational efficiency. Buyers should focus on sourcing trays with anti-static properties to prevent component damage and durability to withstand various logistical challenges. Size specifications are also vital to ensure compatibility with existing storage systems.
Why Are Trays Important in Agriculture?
Tray manufacturers produce seedling trays that are essential for plant propagation in the agriculture industry. These trays promote healthy growth by providing the right environment for seedlings before they are transplanted. Buyers, particularly from regions with diverse agricultural practices, should evaluate the material type—choosing between biodegradable options and traditional plastic—based on environmental considerations. Additionally, drainage features and size are important for optimizing plant health and growth efficiency.
How Do Tray Manufacturers Support the Automotive Sector?
In the automotive industry, tray manufacturers supply trays that aid in parts storage and organization along assembly lines. These trays are designed to increase operational efficiency and reduce handling errors, which is crucial in high-volume production environments. When sourcing trays, buyers should look for customization options tailored to specific automotive parts, as well as durability and stackability to maximize space and ease of handling.
Related Video: 【Perforated Cable Tray Machine】: Cable tray installation | Types of cable tray
3 Common User Pain Points for ‘tray manufacturer’ & Their Solutions
Scenario 1: Sourcing Durable Trays for Harsh Environments
The Problem: B2B buyers in industries such as agriculture or food processing often require trays that can withstand extreme conditions, including high temperatures, moisture, and exposure to chemicals. For instance, a Nigerian agricultural exporter may find that standard trays deteriorate quickly, leading to product damage and loss during transport. This not only affects operational efficiency but also impacts customer satisfaction and trust.
The Solution: To address this issue, buyers should seek manufacturers that specialize in producing trays from advanced materials such as high-density polyethylene (HDPE) or polypropylene, known for their durability and chemical resistance. When sourcing, it’s crucial to ask for samples to test the product under real-world conditions before placing large orders. Additionally, engaging in discussions about custom manufacturing options can lead to tailored solutions that meet specific needs. Buyers should also verify the manufacturer’s certifications and quality control processes to ensure the trays will perform as expected in harsh environments.
Scenario 2: Navigating Compliance and Safety Standards
The Problem: International B2B buyers often face the challenge of ensuring that the trays they purchase comply with local and international safety and hygiene standards. For example, a South American food manufacturer might struggle to find trays that meet both FDA regulations and local health codes, risking fines or product recalls if non-compliant products are used.
The Solution: Buyers should prioritize manufacturers who provide clear documentation of compliance with relevant standards, such as ISO certifications or specific food safety certifications like HACCP. It is advisable to conduct thorough research on the regulatory requirements specific to their industry and region. Engaging with manufacturers who offer transparency about their production processes can be beneficial. Moreover, establishing a dialogue with the supplier regarding their quality assurance practices will further ensure that the trays will not only meet compliance but also support the buyer’s operational integrity.
Scenario 3: Managing Supply Chain Disruptions
The Problem: Global supply chain issues can significantly impact the availability of trays, leading to delays and increased costs. For instance, a Middle Eastern logistics company may experience prolonged lead times due to disruptions caused by geopolitical tensions or natural disasters, which can halt production lines and affect service delivery.
The Solution: To mitigate this risk, B2B buyers should diversify their supplier base by establishing relationships with multiple tray manufacturers across different regions. This strategy can provide alternatives during disruptions and ensure continuity of supply. Additionally, buyers should consider manufacturers that offer flexible production capabilities, allowing for smaller batch orders that can be fulfilled quickly in times of uncertainty. Utilizing technology, such as supply chain management software, can help track inventory levels and anticipate needs, making it easier to adjust orders based on market conditions. Establishing long-term partnerships with reliable manufacturers can also foster better communication and responsiveness during crises.
Strategic Material Selection Guide for tray manufacturer
What Are the Key Properties of Common Materials Used in Tray Manufacturing?
When selecting materials for tray manufacturing, it’s crucial to consider their properties, as they directly influence the performance and suitability of the trays for specific applications. Below, we analyze four common materials used in tray manufacturing: plastic, metal, wood, and composite materials.
How Does Plastic Perform in Tray Manufacturing?
Key Properties: Plastic trays, often made from polyethylene (PE) or polypropylene (PP), are lightweight and resistant to moisture and chemicals. They can withstand temperatures up to 120°C (248°F) without deforming, making them suitable for various applications.
Pros & Cons: The primary advantages of plastic trays include their low cost, ease of manufacturing, and versatility. However, they may not be as durable as metal trays and can be susceptible to UV degradation over time. Additionally, while they are resistant to corrosion, they can warp under extreme heat.
Impact on Application: Plastic trays are ideal for food service, medical supplies, and electronics, where moisture resistance is critical. However, they may not be suitable for high-temperature applications or environments with harsh chemicals.
Considerations for International Buyers: Buyers should ensure compliance with food safety standards such as FDA and EU regulations, particularly in regions like Europe and North America. In Africa and South America, local regulations may vary, so it’s essential to verify compliance with local standards.
What Are the Advantages of Metal Trays in Manufacturing?
Key Properties: Metal trays, commonly made from stainless steel or aluminum, offer exceptional strength and durability. Stainless steel trays can withstand high temperatures (up to 500°C or 932°F) and are highly resistant to corrosion, making them suitable for a wide range of applications.
Pros & Cons: The key advantages of metal trays include their longevity and ability to withstand harsh environments. However, they tend to be heavier and more expensive than plastic trays. Manufacturing metal trays can also be more complex due to the need for specialized equipment.
Impact on Application: Metal trays are often used in industrial settings, laboratories, and kitchens where heat and chemical resistance are paramount. Their robustness makes them suitable for heavy-duty applications.
Considerations for International Buyers: Compliance with international standards such as ASTM and DIN is critical, particularly in Europe and the Middle East. Buyers should also consider the availability of metal recycling options in their region, as sustainability is increasingly important.
Why Choose Wood for Tray Manufacturing?
Key Properties: Wood trays, typically made from hardwoods like oak or maple, offer a natural aesthetic and are biodegradable. They can handle a variety of temperatures but may not be suitable for prolonged exposure to moisture.
Pros & Cons: The primary advantage of wood trays is their unique appearance and eco-friendliness. They are generally less expensive than metal trays but can be more susceptible to damage from moisture and pests.
Impact on Application: Wood trays are often used in the food service industry, particularly for serving and presentation. However, they may not be suitable for environments that require high hygiene standards or exposure to liquids.
Considerations for International Buyers: Buyers should ensure that wood products comply with international regulations regarding sustainability and sourcing. This is especially important in Europe, where there are strict guidelines regarding deforestation and sustainable practices.
How Do Composite Materials Benefit Tray Manufacturing?
Key Properties: Composite materials, such as fiberglass-reinforced plastics, combine the benefits of various materials to offer enhanced strength and durability. They can withstand temperatures up to 200°C (392°F) and are resistant to chemicals and UV light.
Pros & Cons: The main advantage of composite trays is their lightweight nature combined with high strength. However, they can be more expensive than traditional materials and may require specialized manufacturing processes.
Impact on Application: Composite trays are suitable for high-performance applications, including aerospace and automotive industries, where weight and strength are critical.
Considerations for International Buyers: Compliance with industry-specific standards is essential, particularly in high-tech sectors. Buyers should also consider the environmental impact of composite materials and their recyclability.
Summary Table of Material Selection for Tray Manufacturing
Material | Typical Use Case for tray manufacturer | Key Advantage | Key Disadvantage/Limitation | Relative Cost (Low/Med/High) |
---|---|---|---|---|
Plastic | Food service, medical supplies | Lightweight and moisture-resistant | Less durable than metal | Low |
Metal | Industrial settings, kitchens | High strength and durability | Heavier and more expensive | High |
Wood | Serving and presentation | Eco-friendly and aesthetically pleasing | Susceptible to moisture and pests | Medium |
Composite | Aerospace, automotive industries | Lightweight with high strength | More expensive and complex to manufacture | High |
This guide provides actionable insights for international B2B buyers, enabling informed decisions on material selection for tray manufacturing based on performance, cost, and compliance considerations.
In-depth Look: Manufacturing Processes and Quality Assurance for tray manufacturer
What Are the Main Stages of Manufacturing Processes for Tray Manufacturers?
The manufacturing of trays involves several critical stages, each designed to ensure high quality and efficiency. Understanding these processes is vital for international B2B buyers looking for reliable suppliers.
-
Material Preparation
The first step in tray manufacturing is material preparation, where raw materials such as plastics, metals, or composite materials are sourced and processed. This may involve cutting, shredding, or heating the materials to make them suitable for shaping. For instance, high-density polyethylene (HDPE) is commonly used for its durability and resistance to various chemicals. Buyers should inquire about the sourcing and quality of raw materials to ensure they meet industry standards. -
Forming
The forming stage involves shaping the prepared materials into the desired tray configuration. Techniques such as injection molding, thermoforming, and extrusion are commonly used. Injection molding allows for precise shapes and sizes, making it ideal for high-volume production. Thermoforming involves heating a plastic sheet until pliable, then forming it over a mold. Buyers should consider suppliers’ capabilities in employing advanced forming technologies to produce trays that meet specific design requirements. -
Assembly
Once the individual components are formed, they may require assembly. This can include attaching handles, lids, or other elements that enhance functionality. Automated assembly lines are often employed to improve efficiency and reduce labor costs. For buyers, understanding the assembly process can help assess how well a supplier can meet custom specifications or modifications. -
Finishing
The finishing stage is crucial for both aesthetic and functional purposes. This may involve surface treatments, painting, or adding anti-slip coatings. Finishing not only enhances the product’s appearance but also contributes to its durability and usability. Buyers should verify that the finishing techniques used by suppliers comply with industry standards and are suitable for the intended application of the trays.
How Is Quality Assurance Implemented in Tray Manufacturing?
Quality assurance (QA) is a fundamental aspect of tray manufacturing, ensuring that products meet specified standards and customer expectations. Here are the main components involved:
-
Adherence to International Standards
Many tray manufacturers follow international quality standards, such as ISO 9001, which outlines criteria for a quality management system. Compliance with ISO standards indicates that a supplier has robust processes for quality control and continuous improvement. Additionally, industry-specific certifications like CE (Conformité Européenne) for products sold in Europe or API (American Petroleum Institute) certifications for trays used in oil and gas can further assure quality. -
Quality Control Checkpoints
Implementing quality control checkpoints throughout the manufacturing process is essential for maintaining standards. Key checkpoints include:
– Incoming Quality Control (IQC): Raw materials are inspected upon arrival to ensure they meet specified quality criteria.
– In-Process Quality Control (IPQC): Continuous monitoring during the manufacturing process helps detect issues early. This can involve real-time testing of materials and components.
– Final Quality Control (FQC): Finished trays undergo a thorough inspection before packaging and shipping. This includes dimensional checks, visual inspections, and functional tests. -
Common Testing Methods
Testing methods vary based on the materials and intended use of the trays. Common methods include tensile strength tests, impact resistance tests, and thermal stability assessments. Buyers should ask suppliers about the specific testing protocols they follow to ensure compliance with relevant safety and performance standards.
How Can B2B Buyers Verify Supplier Quality Control?
For B2B buyers, especially those from diverse regions like Africa, South America, the Middle East, and Europe, verifying a supplier’s quality control measures is crucial for ensuring product reliability. Here are some strategies:
-
Supplier Audits
Conducting regular audits of potential suppliers can provide insight into their quality management systems. Audits can evaluate the adherence to ISO standards, the effectiveness of their quality control processes, and their overall manufacturing capabilities. Buyers should develop a checklist based on their requirements to facilitate thorough audits. -
Requesting Quality Reports
Suppliers should be willing to provide quality reports detailing their testing results and compliance with industry standards. These reports should include information on raw material sourcing, production processes, and testing outcomes. Buyers should scrutinize these documents to assess the supplier’s commitment to quality. -
Third-Party Inspections
Engaging third-party inspection services can offer an unbiased evaluation of a supplier’s quality control practices. These inspections can be conducted at various stages of production, providing additional assurance regarding the quality of the trays. Buyers can request third-party certification as a prerequisite for supplier selection.
What Are the Quality Control Nuances for International B2B Buyers?
International B2B buyers face unique challenges when assessing quality control in tray manufacturing. Here are some nuances to consider:
-
Cultural and Regulatory Differences
Understanding the local regulations and quality standards in different regions is critical. For instance, European buyers may have stricter requirements regarding environmental sustainability compared to suppliers in other regions. Buyers should familiarize themselves with regional standards to ensure compliance. -
Communication Barriers
Language and cultural differences can create challenges in clearly communicating quality expectations. Establishing a common language and utilizing visual aids, such as diagrams or samples, can help bridge these gaps. -
Logistics and Supply Chain Considerations
Transportation and storage conditions can impact the quality of trays during shipment. Buyers should discuss logistics with suppliers to ensure that products are stored and transported under conditions that preserve their integrity.
By understanding the manufacturing processes and quality assurance practices of tray manufacturers, international B2B buyers can make informed decisions, ensuring they source high-quality products that meet their specific needs.
Practical Sourcing Guide: A Step-by-Step Checklist for ‘tray manufacturer’
Introduction
When sourcing a tray manufacturer, especially for international B2B transactions, it’s essential to have a structured approach. This step-by-step checklist aims to guide buyers through the critical stages of the sourcing process, ensuring they make informed decisions that align with their business needs and regulatory requirements.
Step 1: Define Your Technical Specifications
Clearly outline the specifications for the trays you need, including size, material, weight capacity, and design features. This step is crucial as it sets the foundation for your sourcing process, allowing you to communicate effectively with potential manufacturers. Ensure your specifications align with industry standards and local regulations to avoid compliance issues later.
Step 2: Conduct Market Research
Research potential manufacturers in regions like Africa, South America, the Middle East, and Europe. Understanding the market landscape helps identify reputable suppliers and allows you to compare pricing and capabilities. Look for trade shows, industry reports, and online directories that can provide insights into the leading tray manufacturers within your target regions.
Step 3: Evaluate Potential Suppliers
Before committing, it’s crucial to vet suppliers thoroughly. Request company profiles, case studies, and references from buyers in a similar industry or region. Don’t just rely on their website; instead, look for independent reviews and testimonials to assess their reliability and reputation in the market.
- Key Considerations:
- Production Capacity: Ensure the supplier can meet your order volume and delivery timelines.
- Quality Assurance: Inquire about their quality control processes and certifications.
Step 4: Verify Supplier Certifications
Confirm that potential suppliers hold relevant certifications, such as ISO or other industry-specific qualifications. Certifications indicate a manufacturer’s commitment to quality and compliance with international standards. This step minimizes the risk of sourcing products that do not meet your quality expectations or legal requirements.
Step 5: Request Samples
Before finalizing any contracts, request samples of the trays. This allows you to evaluate the quality, design, and functionality of the products firsthand. Pay attention to details such as finish, durability, and any specific features you require.
- What to Look For:
- Material Quality: Ensure the materials used meet your requirements.
- Functionality: Test the trays for their intended use to confirm they perform as expected.
Step 6: Negotiate Terms and Conditions
Once you have selected a manufacturer, negotiate the terms of the contract, including pricing, payment terms, delivery schedules, and return policies. Clear agreements help prevent misunderstandings and ensure that both parties are aligned on expectations.
Step 7: Establish Communication Channels
Maintain open lines of communication with your chosen supplier throughout the production process. Regular updates on production status, shipping schedules, and any potential issues are vital for timely delivery and overall satisfaction. Establishing a good rapport can also facilitate smoother negotiations in the future.
By following this checklist, international B2B buyers can effectively navigate the complexities of sourcing tray manufacturers, ensuring they select the best partner for their business needs.
Comprehensive Cost and Pricing Analysis for tray manufacturer Sourcing
What Are the Key Cost Components in Tray Manufacturing?
When sourcing from tray manufacturers, understanding the cost structure is critical. The primary cost components include:
-
Materials: The type of materials used (e.g., plastic, metal, wood) significantly affects pricing. High-quality materials typically increase costs but enhance durability and performance.
-
Labor: Labor costs can vary widely by region. Countries with lower labor costs, such as those in parts of Africa and South America, might offer competitive pricing, while European countries may have higher labor costs due to stricter labor regulations.
-
Manufacturing Overhead: This includes costs associated with the manufacturing facility, utilities, and equipment maintenance. Efficient factories often have lower overhead, translating to better pricing for buyers.
-
Tooling: Custom tooling can be a significant upfront cost, especially for unique designs. However, these costs can be amortized over larger production runs, making it critical to consider volume when negotiating.
-
Quality Control (QC): Effective QC processes can add to costs but are essential for ensuring product reliability. Buyers should inquire about QC measures to ensure compliance with their specifications.
-
Logistics: Shipping and handling costs can vary significantly based on the destination and the Incoterms chosen. Understanding logistics can help buyers anticipate total costs.
-
Margin: Manufacturers will typically include a profit margin in their pricing. This can be negotiated based on the order size and long-term partnership potential.
How Do Price Influencers Affect Tray Manufacturing Costs?
Several factors can influence pricing beyond basic cost components:
-
Volume/MOQ (Minimum Order Quantity): Purchasing in larger volumes can lead to discounts. Manufacturers often have set MOQs, so negotiating this can impact overall costs.
-
Specifications and Customization: Custom designs or unique specifications can raise production costs. Buyers should balance the need for customization against budget constraints.
-
Material Quality and Certifications: Higher quality materials or certifications (e.g., ISO, FDA compliance) can increase costs but may be necessary for certain applications. Buyers should weigh the importance of these factors against price.
-
Supplier Factors: The reputation and reliability of the supplier can affect pricing. Established suppliers might charge a premium for their experience and quality assurance.
-
Incoterms: The choice of Incoterms affects shipping costs and responsibilities. For example, CIF (Cost, Insurance, and Freight) means the seller covers shipping costs, while FOB (Free on Board) places those costs on the buyer. Understanding these terms can help buyers manage costs effectively.
What Are Effective Buyer Tips for Sourcing Tray Manufacturers?
-
Negotiation: Engage in open discussions about pricing, particularly regarding volume discounts or long-term agreements. Building a relationship with suppliers can lead to better deals.
-
Cost-Efficiency: Analyze the total cost of ownership (TCO), which includes purchase price, shipping, handling, and potential future costs like maintenance. This holistic view can lead to better purchasing decisions.
-
Pricing Nuances for International Buyers: Buyers from Africa, South America, the Middle East, and Europe should be aware of currency fluctuations, tariffs, and trade regulations that can impact pricing. Establishing clear contracts that outline pricing adjustments can mitigate risks.
-
Seek Multiple Quotes: Obtaining quotes from several manufacturers can provide leverage during negotiations and help identify the best value.
-
Understand Local Market Conditions: Familiarize yourself with local economic conditions, such as labor availability and material costs, as these can impact supplier pricing.
Disclaimer on Indicative Prices
Prices for tray manufacturing can vary significantly based on the factors discussed. It is advisable for buyers to request detailed quotations and consult with suppliers to gain accurate pricing tailored to their specific needs.
Alternatives Analysis: Comparing tray manufacturer With Other Solutions
Understanding the Importance of Alternatives in Tray Manufacturing
In the competitive landscape of manufacturing, particularly for international B2B buyers, understanding alternative solutions to tray manufacturing can significantly impact operational efficiency and cost-effectiveness. While tray manufacturing offers unique advantages, exploring alternatives can help companies optimize their supply chain and meet specific needs that may not be fully addressed by traditional methods. This section provides a comparative analysis of tray manufacturing against other viable solutions, enabling buyers to make informed decisions.
Comparison Table of Tray Manufacturing and Alternatives
Comparison Aspect | Tray Manufacturer | Injection Molding | 3D Printing |
---|---|---|---|
Performance | High durability and customization | Excellent for high volumes and precision | Flexible design, rapid prototyping |
Cost | Moderate initial investment, variable per unit | High initial setup cost, low per unit | Lower initial cost, but high per unit for large volumes |
Ease of Implementation | Requires skilled labor and machinery | Complex setup, requires specialized equipment | Simple setup, accessible technology |
Maintenance | Moderate, depends on materials used | Low, but requires skilled technicians | Low, but technology updates are frequent |
Best Use Case | Custom or low-volume production | Mass production of identical parts | Rapid prototyping and complex designs |
What Are the Advantages and Disadvantages of Injection Molding as an Alternative to Tray Manufacturing?
Injection molding is a well-established manufacturing process that offers high precision and efficiency for producing large quantities of identical parts. One of the primary advantages is its ability to create complex geometries with high repeatability, making it ideal for large-scale production runs. However, the initial setup costs can be significant, as it requires specialized molds and machinery. Moreover, the process can be less flexible in terms of design changes once the mold is created. For B2B buyers focused on high-volume production, injection molding can provide substantial cost savings over time, but it may not suit those needing customization or lower volumes.
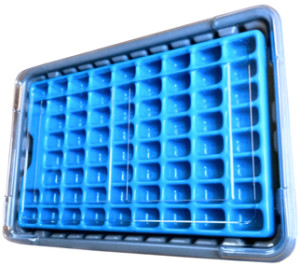
A stock image related to tray manufacturer.
How Does 3D Printing Compare to Tray Manufacturing in Terms of Flexibility and Cost?
3D printing, or additive manufacturing, is another alternative that stands out for its flexibility and ability to produce complex designs without the need for molds. This method allows for rapid prototyping and customization, making it an attractive option for companies that require quick turnarounds and unique designs. The initial cost is typically lower than that of injection molding, but the per-unit cost can become higher for large-scale production due to slower printing speeds. For international buyers, especially in sectors requiring customization, 3D printing can be a compelling choice, although it may not be the best solution for mass production scenarios.
Conclusion: How to Choose the Right Manufacturing Solution for Your Needs
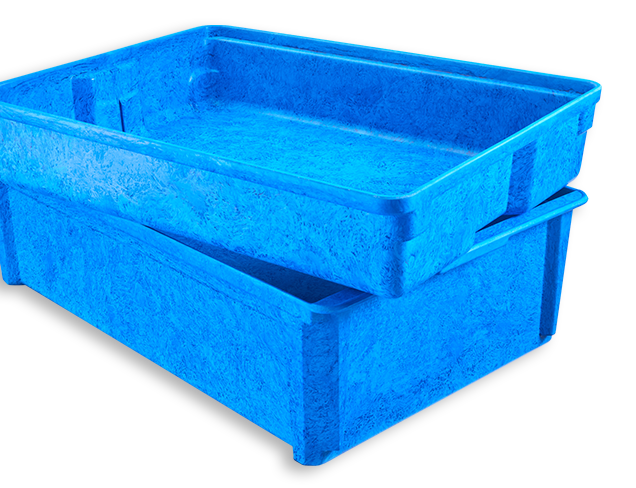
A stock image related to tray manufacturer.
When deciding between tray manufacturing and its alternatives, B2B buyers must evaluate their specific needs, including production volume, budget, and design flexibility. For companies focused on high-volume, uniform production, injection molding may offer the best value despite higher upfront costs. Conversely, if flexibility and rapid prototyping are critical, 3D printing could be the optimal solution. Ultimately, understanding the strengths and weaknesses of each method will empower international buyers from diverse regions, such as Africa, South America, the Middle East, and Europe, to select the most suitable manufacturing solution tailored to their operational requirements.
Essential Technical Properties and Trade Terminology for tray manufacturer
What Are the Essential Technical Properties of Tray Manufacturing?
When considering the purchase of trays for B2B applications, understanding the technical properties is crucial for ensuring quality and compatibility with your needs. Here are some key specifications to consider:
-
Material Grade
– The material used in tray manufacturing can significantly impact durability, weight, and cost. Common materials include high-density polyethylene (HDPE), polypropylene (PP), and aluminum. HDPE is known for its resistance to impact and chemicals, while aluminum offers lightweight strength. Choosing the right material ensures that trays meet specific use-case requirements, such as temperature tolerance or chemical exposure. -
Tolerance
– Tolerance refers to the permissible limit of variation in a physical dimension of the tray. In manufacturing, tighter tolerances mean higher precision, which is critical in industries such as food service, where trays must fit specific equipment or packaging. Understanding tolerance levels helps buyers determine if the trays will fit seamlessly into their operational processes. -
Load Capacity
– This specification indicates the maximum weight a tray can support without deformation or failure. For B2B buyers, especially in logistics and storage, knowing the load capacity is vital to ensure that the trays can handle the intended goods without risk of damage or breakage. -
Surface Finish
– The surface finish of trays can affect their usability and maintenance. Options may include smooth, textured, or non-stick finishes. A smooth finish may be easier to clean, while textured surfaces can provide better grip for handling. Buyers should consider the intended use when evaluating surface finishes. -
Dimensions and Volume
– The size and shape of trays are critical for storage and transportation efficiency. Custom dimensions may be necessary for specific applications, and understanding the volume helps in planning inventory and maximizing space utilization. Ensure that the tray dimensions align with your operational requirements.
Which Common Trade Terms Should B2B Buyers Know in Tray Manufacturing?
In the world of tray manufacturing, specific jargon and trade terms can often lead to confusion. Here are some essential terms that every B2B buyer should be familiar with:
-
OEM (Original Equipment Manufacturer)
– An OEM refers to a company that produces parts or equipment that may be marketed by another manufacturer. For tray buyers, working with an OEM can ensure that the trays meet the exact specifications needed for integration into their products. -
MOQ (Minimum Order Quantity)
– MOQ is the smallest quantity of a product that a supplier is willing to sell. Understanding the MOQ is essential for budget planning and inventory management. Buyers should ensure that their order volumes align with the supplier’s MOQ to avoid excess costs. -
RFQ (Request for Quotation)
– An RFQ is a document used by buyers to solicit price quotes from suppliers. It typically includes specifications, quantities, and delivery requirements. Submitting a well-defined RFQ helps buyers receive accurate pricing and terms from manufacturers, facilitating better purchasing decisions. -
Incoterms (International Commercial Terms)
– These are internationally recognized rules that define the responsibilities of buyers and sellers in international trade. Familiarity with Incoterms helps buyers understand their obligations regarding shipping, insurance, and customs, thereby reducing potential disputes in international transactions. -
Lead Time
– Lead time refers to the time taken from placing an order to its delivery. This is a critical factor for supply chain management. Buyers should inquire about lead times when negotiating contracts to ensure that they can meet their operational timelines. -
Customization Options
– This term refers to the ability to modify standard products to meet specific customer requirements. Understanding customization options is vital for buyers who need trays tailored to unique applications, enhancing functionality and efficiency in their operations.
By familiarizing yourself with these technical properties and trade terminologies, you can make more informed decisions when sourcing trays for your business, ultimately leading to better operational efficiency and product quality.
Navigating Market Dynamics and Sourcing Trends in the tray manufacturer Sector
What Are the Key Market Dynamics and Sourcing Trends in the Tray Manufacturer Sector?
The global tray manufacturing sector is experiencing robust growth, driven by an increase in demand across various industries, including food and beverage, pharmaceuticals, and logistics. For international B2B buyers, particularly from Africa, South America, the Middle East, and Europe, understanding these market dynamics is crucial. A significant driver of growth is the rising consumer preference for sustainable and eco-friendly packaging solutions, which has pushed manufacturers to innovate with biodegradable materials and recyclable designs.
Emerging technologies such as automation and Industry 4.0 are also reshaping the tray manufacturing landscape. Companies are increasingly investing in advanced manufacturing technologies, including 3D printing and smart factory solutions, to enhance productivity and reduce lead times. This trend is particularly relevant for buyers in competitive markets, where time-to-market can significantly impact profitability. Furthermore, the integration of data analytics in supply chain management allows manufacturers to forecast demand more accurately, thus optimizing inventory levels and reducing waste.
Another noteworthy trend is the shift towards localized sourcing and production. Given the disruptions caused by global supply chain challenges, including the COVID-19 pandemic, many companies are reconsidering their sourcing strategies. B2B buyers are encouraged to explore partnerships with local manufacturers to mitigate risks associated with long lead times and transportation costs. This localized approach can also enhance collaboration and innovation, resulting in customized solutions that better meet specific market needs.
How Is Sustainability Shaping the Tray Manufacturing Sector?
Sustainability has become a cornerstone of business strategies in the tray manufacturing sector. The environmental impact of plastic waste has led to increased scrutiny from consumers and regulatory bodies, compelling manufacturers to prioritize ethical sourcing and production practices. For B2B buyers, understanding the importance of sustainability in the sourcing process is essential. Buyers are increasingly seeking suppliers who can demonstrate a commitment to reducing their carbon footprint and implementing sustainable practices throughout their supply chains.
One way manufacturers are addressing these concerns is through the use of green certifications and materials. Certifications such as FSC (Forest Stewardship Council) and ISO 14001 (Environmental Management) are becoming critical factors in supplier selection for B2B buyers. These certifications not only enhance the credibility of manufacturers but also assure buyers that their products are sourced responsibly. Additionally, many companies are exploring alternative materials such as recycled plastics, biodegradable composites, and plant-based options, which can significantly reduce environmental impact.
The emphasis on ethical sourcing extends beyond materials to include labor practices and community engagement. Buyers should prioritize partnerships with manufacturers that uphold fair labor practices and contribute to community development. By doing so, they not only enhance their corporate social responsibility (CSR) profile but also foster long-term relationships with suppliers, which can lead to more resilient supply chains.
What Is the Historical Context of Tray Manufacturing for B2B Buyers?
The tray manufacturing industry has evolved significantly over the past few decades, transitioning from traditional manufacturing methods to highly automated processes. Initially, trays were primarily produced from wood and metal, with limited customization options. However, the introduction of plastics in the mid-20th century revolutionized the sector, allowing for more versatile designs and mass production capabilities.
As the market matured, manufacturers began to adopt advanced technologies, such as injection molding and thermoforming, which enabled the production of complex shapes and sizes tailored to specific industry needs. This evolution has made it essential for B2B buyers to stay informed about the latest technological advancements and material innovations, ensuring they select suppliers capable of meeting their unique requirements.
Today, the focus on sustainability and ethical sourcing represents the next phase in the industry’s evolution. As B2B buyers increasingly prioritize environmental considerations, manufacturers are compelled to innovate not only in product design but also in their overall business practices. This ongoing transformation emphasizes the need for buyers to engage with suppliers who are not just manufacturers but also partners in sustainable development.
Frequently Asked Questions (FAQs) for B2B Buyers of tray manufacturer
-
How can I determine the right tray manufacturer for my needs?
To find the ideal tray manufacturer, start by assessing your specific requirements, such as material type, size, and intended use. Research potential suppliers through online directories, trade shows, and industry referrals. Evaluate their expertise in your desired material, production capacity, and customization options. Request samples to assess quality and ensure they can meet your volume needs. Additionally, check customer reviews and case studies to gauge their reliability and service quality. -
What types of trays can I customize with a manufacturer?
Most tray manufacturers offer a range of customization options, including size, shape, color, and material. Common types include plastic, metal, and wooden trays, each suitable for different applications. You can also customize features like handles, compartments, and branding elements. Discuss your specific needs with the manufacturer to explore all available options and ensure the final product aligns with your brand and operational requirements. -
What is the typical minimum order quantity (MOQ) for tray manufacturers?
Minimum order quantities (MOQ) can vary significantly between manufacturers and depend on factors like material, complexity, and production capabilities. Generally, MOQs for trays can range from 100 to 1,000 units. It’s essential to communicate your needs and expectations upfront to the manufacturer, as they may offer flexible options for smaller orders, especially for new clients or sample runs. -
What payment terms should I expect when working with international tray manufacturers?
Payment terms can vary widely based on the manufacturer and the relationship established. Common terms include upfront deposits (usually 30% to 50%) with the balance due upon delivery or before shipment. Some manufacturers may offer letters of credit or payment through secure platforms. Ensure you clarify these terms before finalizing your order to avoid any misunderstandings or delays in production. -
How do I ensure quality assurance when sourcing trays internationally?
To ensure quality assurance, start by requesting certifications and compliance documentation from potential manufacturers. It’s advisable to conduct factory visits, if possible, or hire third-party inspection services to assess production quality. Establish clear quality standards and specifications in your purchase agreement. Regular communication throughout the manufacturing process can help address any issues promptly and ensure that the final product meets your expectations. -
What logistics considerations should I keep in mind when importing trays?
When importing trays, consider shipping methods, customs regulations, and potential tariffs. Choose between air freight for faster delivery or sea freight for cost-effectiveness, depending on your timeline and budget. Ensure that your manufacturer is familiar with international shipping requirements and can provide necessary documentation. Collaborate with a reliable freight forwarder to navigate logistics efficiently and minimize delays. -
How do I handle language barriers with international tray manufacturers?
Language barriers can be addressed by using clear, concise communication and visual aids. Consider hiring a translator if necessary, especially for technical specifications. Using standardized terminology and avoiding jargon can help ensure both parties understand the requirements. Establishing a primary point of contact fluent in your language can also facilitate smoother communication throughout the sourcing process.
- What are the common challenges faced when sourcing trays internationally?
Common challenges include navigating cultural differences, understanding regulatory compliance, and managing shipping delays. Additionally, quality control issues may arise if the manufacturer does not meet your specifications. To mitigate these challenges, conduct thorough research on potential suppliers, establish clear communication channels, and consider working with local agents or consultants familiar with the market dynamics in the manufacturer’s country.
Important Disclaimer & Terms of Use
⚠️ Important Disclaimer
The information provided in this guide, including content regarding manufacturers, technical specifications, and market analysis, is for informational and educational purposes only. It does not constitute professional procurement advice, financial advice, or legal advice.
While we have made every effort to ensure the accuracy and timeliness of the information, we are not responsible for any errors, omissions, or outdated information. Market conditions, company details, and technical standards are subject to change.
B2B buyers must conduct their own independent and thorough due diligence before making any purchasing decisions. This includes contacting suppliers directly, verifying certifications, requesting samples, and seeking professional consultation. The risk of relying on any information in this guide is borne solely by the reader.
Strategic Sourcing Conclusion and Outlook for tray manufacturer
In navigating the complex landscape of tray manufacturing, international B2B buyers from Africa, South America, the Middle East, and Europe must prioritize strategic sourcing to maximize value and efficiency. By understanding local market dynamics and aligning procurement strategies with global trends, businesses can secure high-quality trays that meet diverse operational needs.
What Are the Key Benefits of Strategic Sourcing in Tray Manufacturing?
Strategic sourcing not only enhances cost-effectiveness but also fosters strong supplier relationships, ensuring reliability and innovation in product offerings. By leveraging data-driven insights, buyers can make informed decisions that minimize risks and streamline supply chains. It’s essential to evaluate suppliers based on quality, sustainability practices, and logistical capabilities to ensure a competitive edge in the market.
How Can International Buyers Stay Ahead in the Tray Manufacturing Market?
Looking ahead, the demand for sustainable and customized tray solutions is set to rise. Buyers should actively engage with manufacturers that prioritize eco-friendly practices and are equipped to adapt to changing customer preferences. Embracing this proactive approach will not only meet current market demands but also position businesses for future growth.
In conclusion, international B2B buyers are encouraged to refine their sourcing strategies and embrace innovation within the tray manufacturing sector. By doing so, they can unlock new opportunities and drive sustainable success in their operations.