Discover Top Tips to Choose a Weight Scale Manufacturer (2025)
Introduction: Navigating the Global Market for weight scale manufacturer
In the ever-evolving global market, sourcing reliable weight scale manufacturers can be a daunting challenge for international B2B buyers. With the increasing demand for precision and efficiency across various industries—from logistics to healthcare—understanding the nuances of weight scales is crucial. This comprehensive guide is designed to equip you with vital insights into the diverse types of weight scales available, their applications, and the critical factors for supplier vetting.
Whether you are a buyer from Nigeria seeking robust industrial scales, or a procurement officer in Europe looking for high-accuracy medical scales, this guide will help you navigate the complexities of the global weight scale market. We will explore essential topics such as cost considerations, technological advancements, and best practices for ensuring quality and compliance.
By empowering B2B buyers from regions like Africa, South America, the Middle East, and Europe, this resource aims to facilitate informed purchasing decisions. It addresses key concerns, from understanding weight measurement standards to identifying reputable suppliers, ensuring that you can confidently invest in the right weight scale solutions for your business needs. With this guide, you’ll be better equipped to make strategic choices that enhance your operational efficiency and drive your business forward.
Understanding weight scale manufacturer Types and Variations
Type Name | Key Distinguishing Features | Primary B2B Applications | Brief Pros & Cons for Buyers |
---|---|---|---|
Digital Weight Scales | High accuracy, easy to read, often includes advanced features like Bluetooth connectivity | Retail, logistics, and food service | Pros: Easy to use, precise measurements; Cons: Requires batteries, may be more expensive. |
Mechanical Weight Scales | Simple design, no power needed, generally more durable | Warehousing, shipping, and agriculture | Pros: Low maintenance, cost-effective; Cons: Less accurate, harder to read. |
Platform Scales | Large surface area for heavy and bulky items | Freight handling, manufacturing, and shipping | Pros: Accommodates large weights; Cons: Requires space, can be costly. |
Bench Scales | Compact, portable, designed for smaller items | Retail, laboratories, and food industry | Pros: Space-saving, versatile; Cons: Limited weight capacity, may lack advanced features. |
Crane Scales | Designed to weigh items suspended from a crane | Heavy industries, construction, and shipping | Pros: Ideal for large loads; Cons: Requires crane for operation, can be expensive. |
What Are the Key Characteristics of Digital Weight Scales?
Digital weight scales are characterized by their high accuracy and user-friendly interfaces, often featuring LCD displays. They may also offer advanced functionalities such as Bluetooth connectivity, allowing integration with inventory management systems. For B2B buyers, these scales are ideal for environments that require precise measurements, such as retail and logistics, where accuracy is critical for inventory management. However, the reliance on batteries and a higher upfront cost can be a drawback for some businesses.
How Do Mechanical Weight Scales Differ from Other Types?
Mechanical weight scales utilize a straightforward design that does not require electricity, making them highly durable and low-maintenance. They are particularly suited for warehousing and agricultural applications where heavy items need to be weighed without the risk of electronic failure. While they are cost-effective and can withstand harsh environments, mechanical scales may lack the precision of digital models and can be harder to read, which may hinder operational efficiency.
What Are the Advantages of Platform Scales for Heavy Items?
Platform scales are designed to handle large and heavy items, making them essential in freight handling and manufacturing sectors. Their large surface area allows for easy placement of bulky products, and they often come with robust construction to withstand heavy use. However, their size requires ample space, and they can be more expensive than smaller scales, which may be a consideration for budget-conscious buyers.
What Makes Bench Scales a Good Choice for Small Businesses?
Bench scales are compact and portable, making them an excellent choice for small businesses in retail and laboratories. They are versatile, capable of weighing a variety of items, and their space-saving design is ideal for limited workspaces. However, they typically have lower weight capacities compared to larger scales and may lack some advanced features, which could limit their use in more demanding applications.
Why Are Crane Scales Essential for Heavy Industries?
Crane scales are specifically designed to weigh items suspended from a crane, making them indispensable in heavy industries such as construction and shipping. They provide the ability to measure large loads accurately and are engineered for durability. However, they require a crane for operation, which can limit their use to specific environments, and their higher cost might be a concern for some businesses looking to minimize expenses.
Related Video: HD How to Balance and Calibrating a Manual Scale
Key Industrial Applications of weight scale manufacturer
Industry/Sector | Specific Application of weight scale manufacturer | Value/Benefit for the Business | Key Sourcing Considerations for this Application |
---|---|---|---|
Manufacturing | Precision weighing for raw materials | Ensures accurate material allocation, reducing waste | Calibration standards, load capacity, durability |
Logistics and Shipping | Freight and cargo weighing | Optimizes shipping costs and compliance with regulations | Weight limits, portability, integration with software |
Food and Beverage | Portion control in food processing | Enhances product consistency and quality assurance | Hygiene standards, accuracy, ease of cleaning |
Agriculture | Livestock and crop weighing | Improves inventory management and market pricing | Environmental resistance, accuracy, capacity |
Pharmaceuticals | Weighing active ingredients | Ensures dosage accuracy and compliance with regulations | Precision, validation processes, certification |
How is Weight Scale Manufacturing Applied in the Manufacturing Sector?
In the manufacturing industry, weight scale manufacturers provide precision weighing solutions for raw materials. Accurate measurement is crucial as it directly influences production efficiency and cost management. By ensuring that the right amount of materials is used, businesses can minimize waste and optimize their inventory management processes. Buyers in this sector should consider calibration standards, load capacity, and the durability of scales to withstand industrial environments, particularly when sourcing from international suppliers.
What Role Does Weight Scale Manufacturing Play in Logistics and Shipping?
Weight scales are essential in logistics and shipping for accurately weighing freight and cargo. This application helps businesses optimize shipping costs and ensures compliance with various regulations, including weight limits imposed by transport authorities. For international B2B buyers, it is important to assess the weight limits, portability, and the ability of scales to integrate with existing logistics software systems to enhance operational efficiency.
How is Weight Scale Manufacturing Utilized in the Food and Beverage Industry?
In the food and beverage sector, weight scale manufacturers provide solutions for portion control in food processing. Accurate weighing ensures product consistency and quality assurance, which are critical for maintaining customer satisfaction and compliance with food safety regulations. Buyers should focus on hygiene standards, accuracy, and the ease of cleaning when selecting scales, especially in regions with strict food safety laws.
Why is Weight Scale Manufacturing Important in Agriculture?
In agriculture, weight scale manufacturers supply scales for weighing livestock and crops. This application aids in inventory management and helps farmers determine market pricing effectively. For buyers in Africa and South America, selecting scales that are resistant to environmental conditions, accurate, and capable of handling large capacities is essential for ensuring reliable operations in diverse agricultural settings.
How Does Weight Scale Manufacturing Benefit the Pharmaceutical Industry?
Weight scale manufacturing is crucial in the pharmaceutical industry for weighing active ingredients accurately. This application is vital for ensuring dosage accuracy and compliance with stringent regulations governing drug production. International B2B buyers should prioritize precision, validation processes, and certification when sourcing scales for pharmaceutical applications, ensuring that they meet the high standards required in this highly regulated sector.
Related Video: An Easy Way to Connect Your Weighing Scale to a Computer & Send Weight Data
3 Common User Pain Points for ‘weight scale manufacturer’ & Their Solutions
Scenario 1: Inconsistent Weight Measurements Affecting Business Operations
The Problem: One of the most common issues faced by international B2B buyers of weight scales is inconsistent weight measurements. For businesses in sectors such as logistics, manufacturing, and food distribution, even minor discrepancies can lead to significant operational disruptions. For instance, a manufacturer in Nigeria may find that their scales are underreporting weights, leading to shortages in shipping or even disputes with customers over delivered quantities. This not only affects revenue but also damages relationships with clients.
The Solution: To combat this issue, B2B buyers should prioritize sourcing weight scales that feature automatic calibration and high precision. When selecting a manufacturer, inquire about their calibration processes and whether they offer regular maintenance services. It is advisable to conduct routine checks and recalibrations as part of your operational protocol. Additionally, consider investing in digital weight scales equipped with real-time monitoring technology that alerts users to any measurement inconsistencies. Implementing a quality assurance protocol that includes periodic testing of weight scales can significantly mitigate the risk of operational disruptions.
Scenario 2: Limited Support and Service from Manufacturers
The Problem: B2B buyers often encounter challenges related to inadequate customer support and service from weight scale manufacturers, especially when dealing with international suppliers. For companies in South America or the Middle East, difficulties in obtaining timely repairs or support can lead to prolonged downtime. This is especially problematic in industries like agriculture, where precise measurements are critical for production and compliance with regulations.
The Solution: When selecting a weight scale manufacturer, opt for those with a strong global presence and a proven track record of customer support. Ensure they offer comprehensive after-sales service, including warranty coverage, remote troubleshooting, and access to local service technicians. Establish clear communication channels with the manufacturer before making a purchase, and consider signing service agreements that guarantee response times for maintenance and repairs. Additionally, look for manufacturers that provide training for your staff on using and maintaining the equipment, which can enhance operational efficiency and reduce reliance on external support.
Scenario 3: Difficulty in Adapting to Local Regulations and Standards
The Problem: Navigating local regulations and standards can be a significant pain point for B2B buyers of weight scales, particularly in regions like Europe and Africa, where compliance requirements can vary widely. A company may invest in scales that meet international standards but discover that they do not comply with local regulations, resulting in costly fines or the need for replacements.
The Solution: To avoid compliance issues, B2B buyers must engage manufacturers who are well-versed in local regulations and standards applicable to weight scales. Before making a purchase, conduct thorough research to understand the specific requirements in your target market. Collaborate with manufacturers who can provide documentation and certifications that verify compliance with local laws. Additionally, consider consulting with local regulatory bodies or industry associations to stay updated on any changes in regulations that may affect your operations. Forming partnerships with local distributors can also ensure that you receive products tailored to your regional compliance needs.
Strategic Material Selection Guide for weight scale manufacturer
When selecting materials for weight scale manufacturing, international B2B buyers must consider various factors, including the properties of the materials, their advantages and disadvantages, and how they meet specific application needs. Below, we analyze four common materials used in weight scale manufacturing: stainless steel, aluminum, plastic, and composite materials.
What are the Key Properties of Stainless Steel for Weight Scales?
Stainless steel is a popular choice for weight scales due to its excellent corrosion resistance, durability, and ability to withstand high temperatures and pressures. It typically features a temperature rating of up to 600°F (315°C) and can handle significant mechanical stress.
Pros & Cons of Stainless Steel
- Pros: Highly durable, resistant to corrosion and rust, suitable for a wide range of environments, and easy to clean.
- Cons: Higher manufacturing costs and weight compared to other materials, which can affect portability.
Impact on Application
Stainless steel is compatible with various media, including liquids and powders, making it ideal for industrial applications. Its robustness ensures longevity, especially in harsh environments found in sectors like food processing and pharmaceuticals.
Considerations for International Buyers
For buyers in Africa, South America, the Middle East, and Europe, compliance with international standards such as ASTM and DIN is crucial. Stainless steel scales should meet these standards to ensure reliability and safety in operations.
How Does Aluminum Compare as a Material for Weight Scales?
Aluminum is another widely used material in weight scale manufacturing. It is lightweight, which enhances portability and ease of use. Aluminum scales typically have a pressure rating suitable for moderate loads.
Pros & Cons of Aluminum
- Pros: Lightweight, cost-effective, and resistant to corrosion.
- Cons: Less durable than stainless steel, especially under high-stress conditions, and may not be suitable for extreme temperatures.
Impact on Application
Aluminum scales are best suited for applications requiring portability, such as retail and personal use. However, they may not perform well in environments where heavy-duty use is expected.
Considerations for International Buyers
Buyers should ensure that aluminum scales comply with relevant standards for weight accuracy and safety. In regions like Europe, adherence to EU regulations is essential.
What Role Does Plastic Play in Weight Scale Manufacturing?
Plastic is often utilized in the production of lightweight and cost-effective weight scales. It is particularly useful for consumer-grade scales.
Pros & Cons of Plastic
- Pros: Very lightweight, low cost, and available in various colors and designs.
- Cons: Limited durability and lower resistance to extreme temperatures and heavy loads.
Impact on Application
Plastic scales are ideal for domestic use and applications where weight accuracy is less critical. They are often used in kitchens and for personal weight management.
Considerations for International Buyers
For buyers in developing markets, plastic scales can offer an affordable option. However, they should verify that the materials used are safe and compliant with local regulations.
How Do Composite Materials Benefit Weight Scale Manufacturing?
Composite materials combine various components to enhance performance characteristics, such as strength and weight. They are increasingly used in high-end weight scales.
Pros & Cons of Composite Materials
- Pros: High strength-to-weight ratio, customizable properties, and resistance to corrosion and temperature fluctuations.
- Cons: Generally higher manufacturing costs and complexity in production.
Impact on Application
Composite scales are suitable for specialized applications, such as laboratory settings, where precision and durability are paramount.
Considerations for International Buyers
Buyers should ensure that composite scales meet specific industry standards and certifications relevant to their region, particularly in sectors like healthcare and research.
Summary Table of Material Selection for Weight Scale Manufacturing
Material | Typical Use Case for weight scale manufacturer | Key Advantage | Key Disadvantage/Limitation | Relative Cost (Low/Med/High) |
---|---|---|---|---|
Stainless Steel | Industrial scales for food and pharmaceuticals | Highly durable and corrosion-resistant | Higher cost and weight | High |
Aluminum | Retail and portable scales | Lightweight and cost-effective | Less durable under stress | Medium |
Plastic | Domestic and personal scales | Very lightweight and low cost | Limited durability and accuracy | Low |
Composite | Laboratory and specialized scales | High strength-to-weight ratio | Higher manufacturing costs | High |
This comprehensive analysis provides international B2B buyers with actionable insights to guide their material selection process for weight scale manufacturing, ensuring they choose the best materials suited to their specific needs and compliance requirements.
In-depth Look: Manufacturing Processes and Quality Assurance for weight scale manufacturer
What Are the Main Stages in the Manufacturing Process of Weight Scales?
The manufacturing process of weight scales involves several critical stages that ensure the final product meets both quality and performance standards. Here’s a breakdown of the main stages:
Material Preparation
The first step in the manufacturing process is the selection and preparation of materials. Common materials used include high-grade stainless steel for the body and precision load cells for accurate weight measurement. Suppliers should ensure that the materials are sourced from reputable vendors who provide certificates of compliance with international standards. This step is crucial as the durability and accuracy of the scale depend significantly on the quality of the materials used.
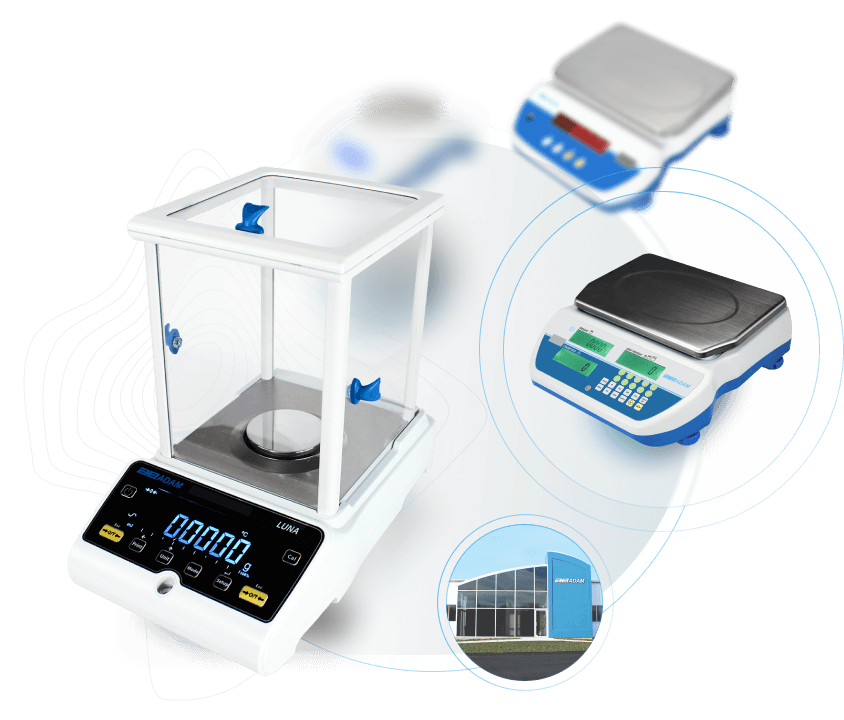
A stock image related to weight scale manufacturer.
Forming Techniques
Once the materials are prepared, they undergo various forming techniques. This may include processes such as stamping, machining, and laser cutting to create the scale’s structural components. For instance, laser cutting offers high precision and allows for intricate designs, which can be essential for specialized applications like laboratory scales. Buyers should inquire about the specific forming techniques used, as this can affect the scale’s accuracy and longevity.
Assembly Process
The assembly stage involves the integration of all components, including the load cell, electronic circuitry, display, and housing. Automated assembly lines are often employed for efficiency, but manual assembly may be used for more complex scales. During this phase, it’s important to ensure that the assembly is done in a dust-free environment to prevent contamination of sensitive components. Buyers should ask about the assembly methods and whether they include quality checks at each stage to ensure proper function.
Finishing Touches
The final stage of the manufacturing process is finishing. This includes painting, coating, and labeling. The finishing not only enhances the aesthetic appeal of the scales but also protects them from corrosion and wear. Buyers should verify that the finishing processes comply with environmental regulations, particularly if they are sourcing from regions with stringent environmental standards.
How Is Quality Assurance Implemented in Weight Scale Manufacturing?
Quality assurance (QA) is a fundamental aspect of weight scale manufacturing, ensuring that products meet the required standards and specifications.
What International Standards Should B2B Buyers Look For?
B2B buyers should prioritize suppliers that comply with international quality management standards such as ISO 9001. This certification indicates that the manufacturer has a quality management system in place that meets global standards. Additionally, industry-specific certifications like CE marking (for products sold in the European Economic Area) and API (American Petroleum Institute) certifications for scales used in the oil and gas industry are crucial. Compliance with these standards not only ensures product reliability but also facilitates easier acceptance in international markets.
What Are the Key QC Checkpoints in the Manufacturing Process?
Quality control (QC) should be integrated at various checkpoints throughout the manufacturing process, including:
-
Incoming Quality Control (IQC): This stage verifies the quality of raw materials and components before they enter production. Suppliers should provide documentation that confirms the quality of incoming materials.
-
In-Process Quality Control (IPQC): During manufacturing, random checks should be performed to ensure that processes are being followed correctly. This includes checking tolerances and dimensions of components as they are produced.
-
Final Quality Control (FQC): Before products are shipped, they should undergo a comprehensive final inspection. This includes functional testing, calibration checks, and visual inspections to ensure that the scales meet specified criteria.
What Testing Methods Are Commonly Used in Weight Scale Manufacturing?
Testing methods play a critical role in verifying that weight scales function accurately and consistently. Common testing methods include:
-
Calibration Testing: Scales must be calibrated against known weights to ensure accuracy. This process is vital for both electronic and mechanical scales.
-
Load Testing: This involves applying weights to the scale to check its response and ensure that it can handle its rated capacity without distortion or failure.
-
Environmental Testing: Scales should be tested under various environmental conditions (temperature, humidity, etc.) to verify performance in real-world applications.
How Can B2B Buyers Verify Supplier Quality Control?
To ensure that their suppliers maintain high-quality standards, B2B buyers can take several proactive steps:
-
Supplier Audits: Regular audits of suppliers can help verify compliance with quality standards. Buyers should assess the supplier’s manufacturing processes, quality control measures, and overall operational efficiency.
-
Request for Quality Reports: Buyers should ask for detailed quality reports that outline testing methods, results, and any corrective actions taken. This transparency can build trust and ensure accountability.
-
Third-Party Inspections: Engaging third-party inspection services can provide an unbiased assessment of the supplier’s quality control processes. These inspections can confirm compliance with international standards and provide additional assurance.
What Are the QC and Certification Nuances for International B2B Buyers?
For international B2B buyers, particularly those from Africa, South America, the Middle East, and Europe, understanding the nuances of QC and certification is essential. Different regions may have specific requirements and standards. For example:
-
African Markets: Buyers should be aware of local regulations that may require additional certifications or testing to ensure products meet regional safety and performance standards.
-
South American Markets: There may be specific labeling requirements and certifications that vary by country. Buyers should ensure that suppliers are knowledgeable about these regulations.
-
Middle Eastern Markets: Compliance with both international and local standards is crucial, particularly in sectors such as oil and gas, where API certification may be required.
-
European Markets: The CE marking is essential for products sold in the EU, and buyers should ensure that their suppliers can provide documentation proving compliance.
By understanding these nuances, B2B buyers can make informed decisions and build successful partnerships with weight scale manufacturers.
Practical Sourcing Guide: A Step-by-Step Checklist for ‘weight scale manufacturer’
In today’s global market, sourcing weight scales from manufacturers requires a strategic approach. This guide provides international B2B buyers, especially from Africa, South America, the Middle East, and Europe, with a step-by-step checklist to ensure a successful procurement process.
Step 1: Define Your Technical Specifications
Before initiating the sourcing process, it’s essential to clearly outline your technical requirements for the weight scales. Consider factors such as the scale’s capacity, precision, and intended applications (e.g., industrial, commercial, or laboratory use). This step is crucial because having well-defined specifications helps you communicate effectively with suppliers and ensures that the products meet your operational needs.
Step 2: Research Potential Suppliers
Conduct thorough research to identify reputable weight scale manufacturers. Utilize online directories, trade platforms, and industry-specific forums to gather a list of potential suppliers. Pay attention to their experience in the market, customer reviews, and product offerings. This background information will help you narrow down your options and focus on manufacturers that align with your specifications and quality expectations.
Step 3: Evaluate Supplier Certifications
Verification of supplier certifications is a critical step in the sourcing process. Ensure that the manufacturers possess relevant industry certifications, such as ISO 9001 for quality management or other specific certifications related to weight scales. These certifications indicate a commitment to quality and compliance with international standards, which is especially important when dealing with imports.
Step 4: Request Samples for Evaluation
Once you’ve shortlisted potential suppliers, request samples of the weight scales you are interested in. Evaluating samples allows you to assess the quality, functionality, and accuracy of the scales firsthand. This step is vital as it helps you make an informed decision based on actual product performance rather than relying solely on marketing materials.
Step 5: Understand Pricing and Payment Terms
Discuss pricing structures and payment terms with your selected suppliers. It’s important to have a clear understanding of the cost per unit, any bulk discounts, and additional fees such as shipping and customs duties. Additionally, clarify payment terms, including deposit requirements and payment methods. This knowledge helps you budget accurately and avoid unexpected costs later in the procurement process.
Step 6: Negotiate Contracts Carefully
When you are ready to proceed with a supplier, negotiate the contract terms carefully. Ensure that the contract includes detailed specifications, delivery timelines, warranty information, and after-sales support. A well-structured contract protects your interests and provides a clear framework for the transaction, reducing the risk of misunderstandings.
Step 7: Plan for Logistics and After-Sales Support
Finally, consider logistics and after-sales support as part of your sourcing strategy. Discuss shipping options, estimated delivery times, and the supplier’s policy for handling defective products or returns. A reliable after-sales support system is essential for maintaining operational efficiency and ensuring the longevity of your weight scales.
By following these steps, international B2B buyers can navigate the complexities of sourcing weight scales effectively, ensuring they partner with manufacturers that meet their specific needs and standards.
Comprehensive Cost and Pricing Analysis for weight scale manufacturer Sourcing
What Are the Key Cost Components in Weight Scale Manufacturing?
When sourcing weight scales, understanding the cost structure is crucial for effective budgeting and negotiations. The primary components of cost include:
-
Materials: The quality of materials significantly affects the overall cost. Common materials include stainless steel for durability and precision components for accuracy. Sourcing high-quality materials can increase initial expenses but may reduce long-term maintenance costs.
-
Labor: Labor costs vary by region, with higher wages in developed countries compared to emerging markets. Consider the skill level required for assembly and quality control, as this can influence labor costs significantly.
-
Manufacturing Overhead: This includes utilities, rent, and general factory expenses. Manufacturers in regions with lower operational costs, such as parts of Africa and South America, might offer competitive pricing due to lower overhead.
-
Tooling: Initial tooling costs can be substantial, especially for custom scales. These costs are typically amortized over the production run, making larger orders more cost-effective.
-
Quality Control (QC): Implementing rigorous QC processes ensures product reliability but adds to manufacturing costs. Certifications (e.g., ISO) also contribute to overall expenses.
-
Logistics: Shipping costs can be significant, particularly for international buyers. Factors such as distance, mode of transport, and customs duties must be considered in the total cost.
-
Margin: Manufacturers typically include a profit margin in their pricing. Understanding the average margins in the industry can help buyers gauge whether a price is fair.
How Do Price Influencers Affect Weight Scale Sourcing?
Several factors influence the pricing of weight scales, and recognizing these can help buyers make informed decisions:
-
Volume/MOQ (Minimum Order Quantity): Higher order volumes often lead to discounts. Manufacturers are generally willing to negotiate better pricing for larger orders, which can be advantageous for buyers with predictable demand.
-
Specifications and Customization: Custom features can significantly increase costs. Buyers should clearly define their requirements to avoid unexpected charges and ensure that the manufacturer can meet those specifications.
-
Materials and Quality Certifications: The choice of materials and compliance with international quality standards can affect pricing. Ensure that suppliers can provide necessary certifications to avoid costly compliance issues later.
-
Supplier Factors: The supplier’s reputation, reliability, and location can impact costs. Established suppliers may charge more for their reputation and service quality but can often deliver better reliability.
-
Incoterms: Understanding Incoterms is essential for managing logistics costs. Terms like FOB (Free on Board) or CIF (Cost, Insurance, and Freight) can shift cost responsibilities between buyers and suppliers, affecting the total price.
What Are Effective Buyer Tips for Negotiating Weight Scale Prices?
For international B2B buyers, particularly from Africa, South America, the Middle East, and Europe, effective negotiation strategies can lead to significant cost savings:
-
Negotiate with Clarity: Clearly communicate your requirements and budget constraints. This transparency encourages suppliers to offer tailored solutions that meet your needs.
-
Focus on Total Cost of Ownership (TCO): Consider not just the purchase price but also long-term costs associated with maintenance, logistics, and potential downtime. A lower initial price may lead to higher TCO if quality and durability are compromised.
-
Understand Pricing Nuances: Different regions may have varying pricing structures due to local market conditions. Researching regional trends can provide leverage during negotiations.
-
Build Relationships: Establishing a strong relationship with suppliers can lead to better pricing and priority service. Regular communication and collaboration can foster trust and loyalty.
-
Request Samples: Before committing to a large order, request samples to assess quality. This step can prevent costly mistakes and ensure that the products meet your standards.
Conclusion
Navigating the cost and pricing landscape of weight scale manufacturing requires a strategic approach. By understanding the key components of cost, recognizing price influencers, and employing effective negotiation tactics, international B2B buyers can make informed decisions that optimize their sourcing strategies. Always remember that prices can vary widely based on numerous factors, and thorough research is essential for achieving the best value.
Alternatives Analysis: Comparing weight scale manufacturer With Other Solutions
When evaluating the best solutions for weight measurement in various industries, it’s essential to consider alternatives to traditional weight scale manufacturers. These alternatives can provide unique advantages depending on the specific needs of a business. In this analysis, we will compare weight scale manufacturers with two viable alternatives: load cells and RFID-based weight measurement systems.
Comparison Table
Comparison Aspect | Weight Scale Manufacturer | Load Cells | RFID-Based Weight Measurement |
---|---|---|---|
Performance | High accuracy and reliability for direct weight measurement | Excellent accuracy, can be used in various applications | Moderate accuracy, dependent on integration |
Cost | Typically higher upfront costs | Varies widely, generally lower than traditional scales | Often lower initial costs but may require additional infrastructure |
Ease of Implementation | Requires calibration and setup | Can be complex, depending on installation | Generally easy to implement, especially with existing RFID systems |
Maintenance | Regular calibration needed | Minimal, but can require replacement | Low maintenance, mostly software updates |
Best Use Case | Direct weight measurement in retail, logistics | Industrial applications, dynamic weighing | Inventory management, automated systems |
Detailed Breakdown of Alternatives
1. Load Cells
Load cells are transducers that convert force or weight into an electrical signal. They are widely used in industrial settings for their durability and precision.
Pros:
– High accuracy and can handle dynamic loads, making them suitable for industries like manufacturing and transportation.
– Versatile in application, as they can be integrated into various systems.
Cons:
– Installation can be complex and may require specialized knowledge.
– Calibration is essential for maintaining accuracy, which can add to ongoing costs.
2. RFID-Based Weight Measurement
RFID (Radio Frequency Identification) technology can be utilized for weight measurement by integrating weight sensors with RFID tags. This method is particularly useful in inventory management.
Pros:
– Lower initial costs, especially if an RFID system is already in place.
– Streamlines operations by automating the weight measurement process, enhancing efficiency.
Cons:
– Accuracy can be compromised if the system is not well integrated or calibrated.
– May require significant changes to existing processes or systems to implement effectively.
Conclusion: How to Choose the Right Solution for Your Needs
For international B2B buyers, selecting the right weight measurement solution hinges on specific operational needs and budget constraints. Weight scale manufacturers provide robust, reliable options ideal for direct weight measurement in retail and logistics. In contrast, load cells offer flexibility and high accuracy for industrial applications, while RFID-based systems facilitate efficient inventory management with potentially lower costs. Evaluating these alternatives based on performance, cost, ease of implementation, and maintenance will guide businesses in making informed decisions tailored to their operational demands.
Essential Technical Properties and Trade Terminology for weight scale manufacturer
What Are the Essential Technical Properties of Weight Scales?
When sourcing weight scales for industrial or commercial applications, understanding the technical specifications is crucial. Here are some key properties that buyers should consider:
-
Material Grade
– Definition: The material used in the construction of the weight scale, commonly stainless steel or aluminum.
– B2B Importance: High-grade materials ensure durability, resistance to corrosion, and longevity, which are essential for scales used in harsh environments, such as warehouses or manufacturing facilities. -
Tolerance
– Definition: The acceptable range of variation in the weight measurement, usually expressed in grams or milligrams.
– B2B Importance: Precision is vital in sectors like pharmaceuticals and food production, where accurate weight readings affect product quality and compliance with regulations. -
Capacity
– Definition: The maximum weight that the scale can measure, typically ranging from a few grams to several tons.
– B2B Importance: Knowing the capacity is critical for industries that deal with heavy materials, ensuring that the scale meets operational needs without compromising safety. -
Readability
– Definition: The smallest increment that the scale can display, such as 0.1g or 1kg.
– B2B Importance: High readability is essential for applications requiring detailed weight measurements, like in laboratory settings, where precision is key. -
Power Supply
– Definition: The method by which the scale operates, which can be battery-powered or plugged into a wall outlet.
– B2B Importance: Flexibility in power supply options can influence operational efficiency, particularly in remote locations or when portability is needed.
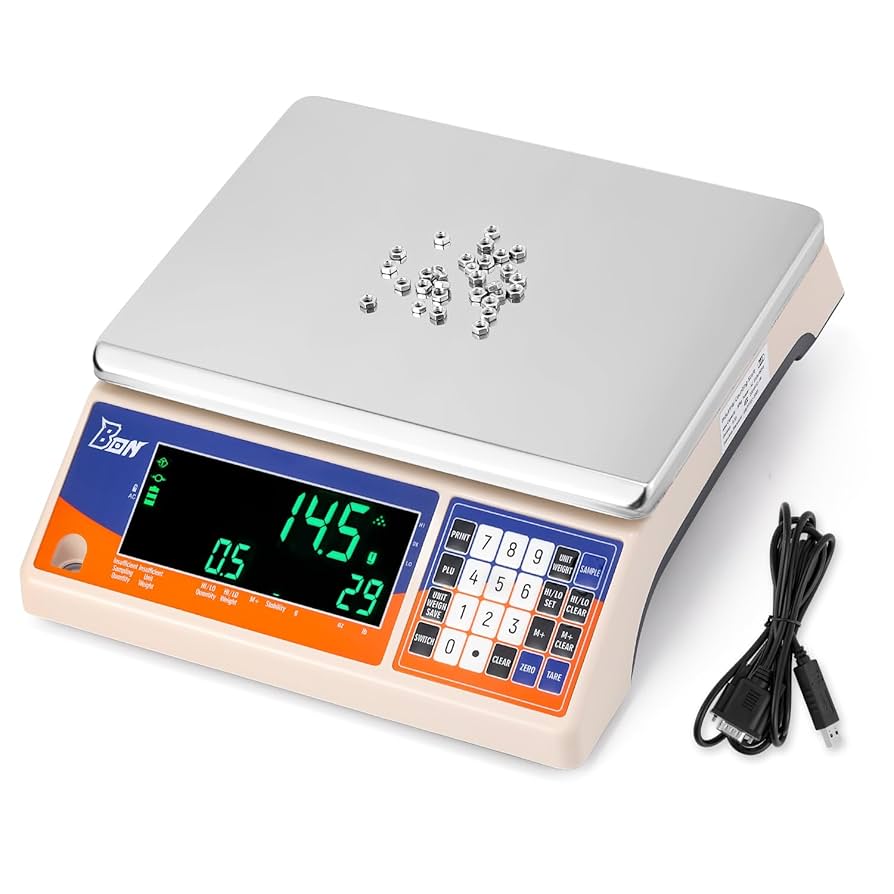
A stock image related to weight scale manufacturer.
- Calibration
– Definition: The process of adjusting the scale to ensure its accuracy, often required periodically.
– B2B Importance: Regular calibration is essential to maintain compliance with industry standards and to ensure that weight measurements are reliable.
What Are Common Trade Terms Related to Weight Scale Manufacturing?
Understanding industry jargon can streamline communication and negotiations between buyers and manufacturers. Here are some common terms:
-
OEM (Original Equipment Manufacturer)
– Definition: A company that produces parts or equipment that may be marketed by another manufacturer.
– B2B Importance: Buyers often seek OEM partnerships for specialized scales, ensuring quality and consistency in product design and manufacturing. -
MOQ (Minimum Order Quantity)
– Definition: The smallest number of units that a supplier is willing to sell.
– B2B Importance: Knowing the MOQ helps buyers plan their inventory and budget, especially when entering new markets or launching new products. -
RFQ (Request for Quotation)
– Definition: A document issued by a buyer to solicit price proposals from suppliers for specific products or services.
– B2B Importance: An RFQ is crucial for comparing prices and terms from multiple suppliers, ensuring that buyers get the best deal. -
Incoterms (International Commercial Terms)
– Definition: A set of predefined international rules that clarify the responsibilities of buyers and sellers in international transactions.
– B2B Importance: Understanding Incoterms helps buyers manage shipping costs, risks, and logistics effectively when importing weight scales from abroad. -
Lead Time
– Definition: The time it takes from placing an order to receiving the product.
– B2B Importance: Lead time affects inventory management and planning, making it vital for buyers to understand this aspect when sourcing weight scales. -
Warranty
– Definition: A guarantee provided by the manufacturer regarding the condition of the product and the terms for repair or replacement.
– B2B Importance: A strong warranty can provide peace of mind to buyers, indicating the manufacturer’s confidence in their product’s quality and reliability.
By familiarizing yourself with these essential properties and terms, you can make informed decisions when sourcing weight scales, ensuring that your operations run smoothly and efficiently.
Navigating Market Dynamics and Sourcing Trends in the weight scale manufacturer Sector
What Are the Key Market Dynamics and Trends Affecting Weight Scale Manufacturers?
The weight scale manufacturing sector is experiencing significant growth driven by several global factors. One of the primary drivers is the increasing demand for precision measurement in various industries, including logistics, healthcare, and food production. With the rise of e-commerce and global trade, accurate weight measurement has become crucial for shipping and inventory management. Furthermore, advancements in technology, such as the integration of IoT (Internet of Things) and AI (Artificial Intelligence), are transforming traditional weight scales into smart devices that provide real-time data and analytics.
International B2B buyers, particularly from Africa, South America, the Middle East, and Europe, should be aware of the emerging trends in sourcing weight scales. There is a notable shift towards digital procurement platforms that facilitate seamless transactions and product comparisons. Additionally, manufacturers are increasingly focusing on customization options to cater to specific industry needs, enhancing the value proposition for buyers. The emphasis on automation and efficiency is prompting manufacturers to invest in high-tech solutions, which can yield significant long-term cost savings for businesses.
How Are Sustainability and Ethical Sourcing Impacting the Weight Scale Manufacturing Sector?
Sustainability has become a critical concern in the weight scale manufacturing sector, reflecting a broader shift towards environmentally responsible practices. The environmental impact of manufacturing processes, including waste generation and energy consumption, is under scrutiny. As such, international B2B buyers should prioritize suppliers that demonstrate a commitment to sustainability through transparent practices and eco-friendly materials.
Ethical sourcing is equally important, particularly for buyers in regions such as Africa and South America, where supply chain integrity is paramount. Manufacturers are increasingly obtaining certifications that validate their adherence to ethical sourcing standards, including fair labor practices and responsible resource management. Buyers should look for certifications such as ISO 14001 for environmental management and ISO 45001 for occupational health and safety, as these can serve as indicators of a manufacturer’s commitment to sustainable and ethical practices.
What Is the Historical Context of Weight Scale Manufacturing Relevant to B2B Buyers?
The evolution of weight scale manufacturing has been marked by significant technological advancements. Historically, weight scales were simple mechanical devices; however, the introduction of digital technology in the late 20th century revolutionized the industry. Digital scales offered enhanced accuracy and ease of use, which quickly gained popularity across various sectors.
In recent years, the advent of smart scales equipped with connectivity features has further transformed the landscape. These innovations not only streamline operations but also provide data analytics capabilities that are invaluable for businesses looking to optimize their supply chains. Understanding this historical context allows B2B buyers to appreciate the technological progression and the importance of investing in modern weight scale solutions that align with their operational needs.
In summary, international B2B buyers should stay attuned to market dynamics and sourcing trends in the weight scale manufacturing sector, prioritize sustainable and ethical sourcing practices, and understand the historical advancements that shape current offerings.
Frequently Asked Questions (FAQs) for B2B Buyers of weight scale manufacturer
-
How do I choose the right weight scale for my business needs?
Selecting the right weight scale involves assessing your specific requirements, such as the types of products you will weigh, the weight capacity needed, and the accuracy required. Consider whether you need portable scales for fieldwork or stationary scales for a warehouse setting. Additionally, evaluate features like connectivity options (Bluetooth, Wi-Fi), data logging capabilities, and compliance with local regulations. Consulting with manufacturers for recommendations based on your industry can also provide valuable insights. -
What are the advantages of purchasing from a weight scale manufacturer versus a distributor?
Buying directly from a manufacturer often provides benefits such as better pricing, access to a wider range of products, and the ability to customize features to suit your needs. Manufacturers typically have more knowledge about their products, which can lead to better support and service. Additionally, purchasing directly can shorten lead times, as you may avoid additional handling by intermediaries. -
What is the minimum order quantity (MOQ) when sourcing weight scales?
Minimum order quantities can vary significantly between manufacturers, ranging from as low as one unit to several hundred units depending on the scale type and manufacturer’s policies. When negotiating with suppliers, clarify the MOQ upfront to ensure it aligns with your purchasing capabilities. Some manufacturers may offer flexibility for first-time buyers or smaller businesses, so it’s worth discussing your specific needs. -
How can I verify the quality of weight scales from international suppliers?
To verify the quality of weight scales, request product certifications and quality assurance documents from the manufacturer. Look for compliance with international standards such as ISO 9001 or specific industry standards relevant to your region. Additionally, consider visiting the manufacturing facility if possible or requesting samples for testing. Online reviews and testimonials from other buyers can also provide insights into product reliability and performance. -
What payment terms should I expect when purchasing weight scales internationally?
Payment terms can vary by manufacturer and region. Common options include upfront payments, letters of credit, and payment upon delivery. For larger orders, negotiating favorable terms, such as partial payments based on milestones, can help manage cash flow. Always confirm the payment methods accepted by the supplier and ensure they are secure to protect your investment. -
What are the logistics considerations when importing weight scales?
Logistics plays a crucial role in international purchases. Consider factors such as shipping methods (air vs. sea), transit times, and customs clearance processes. Work with a freight forwarder to navigate international shipping regulations, and ensure you have the necessary import permits and documentation. Additionally, factor in delivery costs and potential tariffs to calculate the total landed cost of your order.
-
How do I ensure that the weight scales meet my local regulations?
Before placing an order, research the regulations governing weighing equipment in your country or region. Many countries have specific requirements for accuracy, calibration, and certification of weight scales. Request documentation from the manufacturer that confirms compliance with these regulations. It’s also advisable to collaborate with local authorities or industry associations to ensure that your selected equipment meets all necessary standards. -
Can weight scales be customized to fit specific industry needs?
Yes, many manufacturers offer customization options for weight scales to cater to specific industry needs. This can include modifications in design, size, weight capacity, and additional features such as integrated software for data management. When discussing your requirements with a manufacturer, be clear about your intended use and any specific functionalities you need, which can help them provide tailored solutions that enhance your operational efficiency.
Important Disclaimer & Terms of Use
⚠️ Important Disclaimer
The information provided in this guide, including content regarding manufacturers, technical specifications, and market analysis, is for informational and educational purposes only. It does not constitute professional procurement advice, financial advice, or legal advice.
While we have made every effort to ensure the accuracy and timeliness of the information, we are not responsible for any errors, omissions, or outdated information. Market conditions, company details, and technical standards are subject to change.
B2B buyers must conduct their own independent and thorough due diligence before making any purchasing decisions. This includes contacting suppliers directly, verifying certifications, requesting samples, and seeking professional consultation. The risk of relying on any information in this guide is borne solely by the reader.
Strategic Sourcing Conclusion and Outlook for weight scale manufacturer
As the global market for weight scales continues to evolve, strategic sourcing remains a critical component for international B2B buyers, especially those from Africa, South America, the Middle East, and Europe. Understanding local regulations, technological advancements, and supplier capabilities can significantly enhance procurement decisions. By prioritizing quality, reliability, and supplier relationships, buyers can ensure they select the best weight scale manufacturers to meet their operational needs.
Investing in strategic sourcing not only facilitates cost savings but also improves supply chain resilience. Buyers should leverage data analytics to evaluate supplier performance and market trends, ensuring they stay ahead of the competition. The emphasis on sustainability in manufacturing processes is also becoming increasingly important; therefore, sourcing from manufacturers committed to eco-friendly practices can bolster a company’s brand reputation.
Looking ahead, international buyers should embrace digital transformation in their sourcing strategies. By utilizing e-procurement tools and platforms, they can streamline processes, enhance transparency, and foster collaboration. As the market continues to expand, now is the time to act. Engage with suppliers that not only meet technical specifications but also align with your long-term business goals. Your strategic sourcing decisions today will pave the way for a successful and sustainable future in the weight scale industry.