Discover Top Traffic Cone Suppliers: Save Time & Money (2025)
Introduction: Navigating the Global Market for traffic cone supplier
In today’s global marketplace, sourcing high-quality traffic cones is a critical challenge for B2B buyers, particularly those operating in diverse regions such as Africa, South America, the Middle East, and Europe. Traffic cones play an essential role in road safety, construction sites, and event management, making it imperative for international buyers to identify reliable suppliers who can meet their specific needs. This comprehensive guide is designed to equip buyers with the insights necessary for effective decision-making, covering various types of traffic cones, their applications, and essential factors to consider when vetting suppliers.
Throughout this guide, we will explore the different categories of traffic cones available in the market, from basic safety cones to advanced models equipped with reflective materials for enhanced visibility. Additionally, we will delve into the logistical aspects of sourcing these products, including cost considerations, shipping, and compliance with local regulations in regions like Egypt and Germany.
By providing a detailed analysis of the supplier landscape, including tips on identifying reputable manufacturers and distributors, this guide empowers B2B buyers to make informed purchasing decisions. Whether you are looking to enhance safety on construction sites, manage traffic during events, or improve public safety in urban areas, understanding the nuances of the traffic cone market will ensure you find the right solutions for your business needs.
Understanding traffic cone supplier Types and Variations
Type Name | Key Distinguishing Features | Primary B2B Applications | Brief Pros & Cons for Buyers |
---|---|---|---|
Standard Traffic Cones | Typically made of PVC or rubber, 28-inch height | Road construction, event management | Pros: Durable, cost-effective; Cons: Limited visibility in low light. |
Reflective Traffic Cones | Equipped with reflective bands for visibility | Nighttime roadwork, emergency services | Pros: Enhanced visibility; Cons: Slightly higher cost. |
Collapsible Traffic Cones | Flexible and lightweight, easy to transport | Urban areas, temporary setups | Pros: Space-saving, portable; Cons: Less stable in high winds. |
Heavy-Duty Traffic Cones | Made from thicker materials, designed for high traffic | Construction sites, high-traffic zones | Pros: Very stable, long-lasting; Cons: Heavier, may require more storage space. |
Eco-Friendly Traffic Cones | Made from recycled materials, biodegradable options | Green initiatives, environmentally conscious projects | Pros: Sustainable, positive brand image; Cons: May be less durable than traditional cones. |
What Are Standard Traffic Cones and Their B2B Applications?
Standard traffic cones are the most common type used in various applications, primarily constructed from PVC or rubber. With a typical height of 28 inches, they are ideal for road construction and event management. When purchasing, buyers should consider durability and cost-effectiveness, as these cones are generally affordable and reliable. However, they may lack visibility in low-light conditions, which could be a disadvantage in certain applications.
How Do Reflective Traffic Cones Enhance Safety?
Reflective traffic cones feature reflective bands that significantly improve visibility during nighttime operations. This makes them particularly suitable for nighttime roadwork and emergency services, where clear visibility is crucial. Buyers should weigh the enhanced safety benefits against the slightly higher cost compared to standard cones. Reflective cones can be an excellent investment for businesses focused on safety.
Why Choose Collapsible Traffic Cones for Urban Environments?
Collapsible traffic cones are designed for flexibility and portability, making them perfect for urban areas and temporary setups. They are lightweight and can be easily transported, which is beneficial for companies needing to set up and dismantle traffic control quickly. However, buyers should be aware that these cones may be less stable in high winds, which could compromise safety in adverse weather conditions.
What Are the Benefits of Heavy-Duty Traffic Cones?
Heavy-duty traffic cones are constructed from thicker materials, making them suitable for high-traffic areas and construction sites. Their stability and long-lasting durability make them a preferred choice for businesses that require reliable traffic management solutions. However, their heavier weight can pose storage challenges and may require more effort to transport. Buyers should assess their specific needs to determine if the benefits outweigh the logistical considerations.
How Do Eco-Friendly Traffic Cones Support Sustainability?
Eco-friendly traffic cones are made from recycled materials and often come in biodegradable options, appealing to businesses focused on sustainability. These cones can enhance a company’s brand image by demonstrating a commitment to environmental responsibility. While they may not match the durability of traditional cones, they provide an important option for projects aimed at reducing environmental impact. Buyers should consider their sustainability goals when selecting these products.
Related Video: pi-lit® Smart Sequential Cone-Top Lamp: Temporary Lane Closure
Key Industrial Applications of traffic cone supplier
Industry/Sector | Specific Application of traffic cone supplier | Value/Benefit for the Business | Key Sourcing Considerations for this Application |
---|---|---|---|
Construction | Site safety and traffic management during construction projects | Enhances worker safety and minimizes accidents | Ensure compliance with local safety regulations and standards. |
Event Management | Crowd control and traffic direction at large events | Improves attendee safety and event flow | Consider durability for outdoor use and visibility in various lighting conditions. |
Road Maintenance | Temporary road closure and detour signage | Reduces traffic congestion and enhances safety | Look for cones that are weather-resistant and highly visible. |
Emergency Services | Accident scene management and traffic diversion | Increases response time and safety for first responders | Ensure quick deployment features and compliance with emergency protocols. |
Logistics and Warehousing | Traffic flow management within warehouses | Streamlines operations and reduces bottlenecks | Assess the need for customizable options for different warehouse layouts. |
How Are Traffic Cones Used in Construction Projects?
In the construction industry, traffic cones are essential for site safety and traffic management. They are strategically placed to redirect traffic away from construction zones, protecting workers and pedestrians. The use of brightly colored cones helps in alerting drivers of potential hazards. International buyers should ensure that the cones meet local safety standards and regulations, which can vary significantly between regions, particularly in Africa and Europe.
What Role Do Traffic Cones Play in Event Management?
For event management, traffic cones are vital for crowd control and directing traffic flow during large gatherings, such as concerts or festivals. They help in creating designated pathways and parking areas, ensuring the safety of attendees. Buyers should consider the durability of the cones, especially for outdoor events, and their visibility in different lighting conditions. Additionally, having customizable options with branding can enhance the event’s professional appearance.
How Are Traffic Cones Utilized in Road Maintenance?
Traffic cones are commonly used in road maintenance to signify temporary road closures and detours. They help in reducing traffic congestion and enhancing overall safety by clearly marking hazardous areas. B2B buyers in this sector must look for cones that are weather-resistant and designed for high visibility, ensuring that they remain effective in various environmental conditions. Understanding local road safety regulations is crucial for compliance.
Why Are Traffic Cones Important for Emergency Services?
In emergency situations, traffic cones play a critical role in managing accident scenes and diverting traffic to ensure the safety of first responders. Their quick deployment is essential for minimizing risks during critical incidents. Buyers should prioritize features like lightweight design for easy transport and compliance with emergency management protocols. Additionally, the cones must be highly visible to ensure they are effective in low-light conditions.
How Do Traffic Cones Improve Operations in Logistics and Warehousing?
Within logistics and warehousing, traffic cones help manage vehicle and pedestrian traffic flow, preventing bottlenecks and enhancing operational efficiency. They can be used to mark loading zones and pedestrian pathways, ensuring a safer working environment. When sourcing cones for this application, buyers should assess the need for customizable options that fit different warehouse layouts and consider the durability needed for high-traffic areas.
Related Video: Introduction to Automated Cone Laying Machine
3 Common User Pain Points for ‘traffic cone supplier’ & Their Solutions
Scenario 1: Inconsistent Quality of Traffic Cones
The Problem:
B2B buyers often face issues with the quality of traffic cones supplied, which can vary significantly between manufacturers. A construction company in Egypt, for example, might find that the cones received from a supplier are not durable enough for their needs, leading to frequent replacements and additional costs. This inconsistency can hinder project timelines and affect safety on job sites, especially in regions where traffic regulations are strict.
The Solution:
To ensure consistent quality when sourcing traffic cones, buyers should prioritize suppliers with robust quality assurance processes. Look for suppliers that provide certifications or third-party testing results for their products. It’s advisable to request samples before placing bulk orders to evaluate the durability and visibility of the cones. Furthermore, establish a clear communication channel with the supplier to discuss specifications, expected use cases, and any industry standards that must be met. By taking these proactive steps, buyers can mitigate risks associated with poor-quality products and ensure that they are investing in reliable traffic cones.
Scenario 2: Difficulty in Sourcing Traffic Cones for Diverse Needs
The Problem:
International B2B buyers often struggle to find a traffic cone supplier that can meet their specific requirements, such as varying sizes, colors, and reflective properties. For instance, a government contractor in Germany may need traffic cones that are suitable for both urban and rural road conditions, which may require different specifications. This challenge can lead to delays in project execution and increased logistical costs.
The Solution:
To address this issue, buyers should engage with suppliers that offer a wide range of customizable options. When evaluating potential suppliers, ask about their capabilities for producing cones in various sizes and colors, as well as any additional features like reflective strips or weighted bases for stability. Utilizing a supplier that specializes in custom orders can streamline the procurement process. Additionally, consider forming partnerships with suppliers who have experience working in multiple regions, as they will understand the specific requirements and regulations that apply to different markets. This approach ensures that the traffic cones sourced are fit for purpose, enhancing project efficiency.
Scenario 3: Challenges with Timely Delivery and Logistics
The Problem:
Timely delivery of traffic cones can be a significant pain point for B2B buyers, especially when working on projects with tight deadlines. A construction firm in South America may face delays from suppliers who cannot meet shipping timelines, resulting in costly downtime and project overruns. This issue is exacerbated in regions where transportation infrastructure may be less developed, leading to unpredictable delivery schedules.
The Solution:
To overcome logistical challenges, buyers should establish clear expectations regarding delivery timelines at the outset of negotiations. When selecting a supplier, prioritize those who have a proven track record of on-time deliveries and robust logistics networks. It’s beneficial to work with suppliers who have local warehouses or distribution centers in your region, as this can significantly reduce lead times. Additionally, implementing a contingency plan, such as identifying alternative suppliers or maintaining a small inventory of critical items, can help mitigate the impact of any unexpected delays. By taking these steps, buyers can enhance their project management capabilities and reduce the risk of disruptions.
Strategic Material Selection Guide for traffic cone supplier
When selecting materials for traffic cones, international B2B buyers must consider several factors, including the properties of the materials, their performance in various environments, and compliance with regional standards. The following analysis focuses on four common materials used in traffic cone manufacturing: PVC, Polyethylene, Rubber, and ABS. Each material has unique characteristics that can significantly impact product performance and suitability for specific applications.
What Are the Key Properties of PVC for Traffic Cones?
Polyvinyl Chloride (PVC) is a widely used material for traffic cones due to its favorable properties. PVC is known for its excellent flexibility, resistance to impact, and good weatherability. It can withstand a temperature range from -10°C to 60°C, making it suitable for various climates, including the hot temperatures of Africa and the cold winters in Europe. Additionally, PVC exhibits good chemical resistance, which is essential for outdoor applications where exposure to oils and solvents may occur.
Pros: PVC cones are lightweight and cost-effective, making them an attractive option for bulk purchases. They are also easy to manufacture and can be produced in various colors, enhancing visibility.
Cons: While durable, PVC can become brittle over time, especially in extreme cold. It may not perform well under high-pressure conditions, limiting its use in heavy traffic areas.
How Does Polyethylene Compare as a Material for Traffic Cones?
Polyethylene (PE) is another popular choice for traffic cones, particularly high-density polyethylene (HDPE). HDPE offers superior impact resistance and is less prone to cracking compared to PVC. It can handle temperatures ranging from -40°C to 80°C, making it suitable for diverse climatic conditions.
Pros: HDPE cones are highly durable and resistant to UV light, ensuring long-lasting performance outdoors. They are also recyclable, aligning with sustainability goals.
Cons: The manufacturing process for HDPE can be more complex and costly compared to PVC, which may impact pricing for bulk orders. Additionally, while HDPE is resistant to many chemicals, it may not be suitable for environments with aggressive solvents.
What Are the Benefits of Using Rubber for Traffic Cones?
Rubber is often used in traffic cones designed for high-visibility applications, such as construction sites or emergency situations. Rubber cones are known for their exceptional durability and flexibility, allowing them to withstand harsh conditions and heavy impacts.
Pros: The inherent weight of rubber cones provides stability, making them less likely to be knocked over by wind or vehicles. They are also resistant to abrasion and can last longer in demanding environments.
Cons: The primary drawback of rubber cones is their higher cost and weight, which can complicate transportation and storage. Additionally, rubber may degrade over time when exposed to certain chemicals.
Why Is ABS a Suitable Material for Traffic Cones?
Acrylonitrile Butadiene Styrene (ABS) is a thermoplastic known for its strength and rigidity. ABS cones are often used in environments requiring high visibility and structural integrity.
Pros: ABS offers excellent impact resistance and can withstand a wide temperature range. Its smooth surface allows for easy cleaning, making it ideal for urban settings.
Cons: ABS can be more expensive than PVC and PE, which may deter budget-conscious buyers. It is also less flexible, making it more susceptible to cracking under extreme stress.
Summary Table of Material Selection for Traffic Cones
Material | Typical Use Case for traffic cone supplier | Key Advantage | Key Disadvantage/Limitation | Relative Cost (Low/Med/High) |
---|---|---|---|---|
PVC | General traffic control | Lightweight and cost-effective | Can become brittle in extreme cold | Low |
Polyethylene | Outdoor applications in varying climates | Highly durable and UV resistant | More complex manufacturing process | Medium |
Rubber | High-visibility zones like construction | Exceptional durability and stability | Higher cost and weight | High |
ABS | Urban environments requiring high visibility | Excellent impact resistance | More expensive and less flexible | Medium |
In conclusion, international B2B buyers, especially from regions like Africa, South America, the Middle East, and Europe, should carefully consider the properties, advantages, and limitations of these materials when selecting traffic cones. Compliance with local standards such as ASTM, DIN, or JIS is crucial to ensure product suitability and safety in their specific markets.
In-depth Look: Manufacturing Processes and Quality Assurance for traffic cone supplier
What Are the Main Stages of Manufacturing Traffic Cones?
The manufacturing process for traffic cones involves several key stages that ensure the final product meets safety and quality standards. The main stages include material preparation, forming, assembly, and finishing.
-
Material Preparation: The process typically begins with selecting high-quality materials, often made from durable polyethylene or PVC. These materials are chosen for their weather resistance and flexibility. Suppliers must ensure that raw materials meet industry specifications, which can vary by region.
-
Forming: Once the materials are prepared, they are subjected to forming techniques. Common methods include injection molding and blow molding. Injection molding is favored for its precision, allowing manufacturers to create cones with consistent dimensions. Blow molding is useful for producing hollow cones, which can be lighter and easier to transport.
-
Assembly: After forming, any additional components, such as reflective bands or weights, are attached. This stage is critical for enhancing the visibility and stability of the traffic cones. The assembly process must be conducted carefully to ensure that all components are securely fitted.
-
Finishing: The final stage involves surface finishing, which may include applying UV-resistant coatings to enhance durability against sun exposure. The cones may also undergo quality checks to ensure they meet the necessary aesthetic and functional standards.
How Do Quality Assurance Processes Ensure High-Quality Traffic Cones?
Quality assurance (QA) is an integral part of the manufacturing process, ensuring that the final products meet both international and industry-specific standards. For traffic cone suppliers, adhering to QA protocols can significantly impact buyer trust and market competitiveness.
-
Adherence to International Standards: Many suppliers comply with ISO 9001, which outlines a framework for quality management systems. This certification signifies that the manufacturer has robust processes in place to ensure consistent quality and customer satisfaction. Additionally, traffic cones may require compliance with CE marking for products sold in Europe, indicating conformity with safety standards.
-
Industry-Specific Standards: Depending on the region, suppliers may also need to adhere to other specific standards, such as those set by the American Petroleum Institute (API) or local traffic safety regulations. These standards often outline specific material properties, dimensional tolerances, and performance criteria.
-
Quality Control Checkpoints: The quality assurance process typically includes several checkpoints:
– Incoming Quality Control (IQC): This stage involves inspecting raw materials upon arrival to ensure they meet specified standards.
– In-Process Quality Control (IPQC): During manufacturing, regular inspections are conducted to monitor the production process and identify any deviations from standards.
– Final Quality Control (FQC): After production, the finished cones undergo comprehensive testing for durability, visibility, and stability.
What Testing Methods Are Commonly Used for Traffic Cones?
Testing methods are crucial for verifying that traffic cones meet safety and performance standards. Some common testing methods include:
-
Durability Testing: This involves subjecting cones to extreme weather conditions, including UV exposure, high temperatures, and heavy impacts, to assess their resilience.
-
Visibility Testing: Reflective materials are tested to ensure they meet visibility standards under various lighting conditions, which is vital for nighttime use.
-
Stability Testing: Traffic cones are tested for stability under wind and impact to ensure they remain upright and visible in various conditions.
How Can B2B Buyers Verify Supplier Quality Control?
B2B buyers from Africa, South America, the Middle East, and Europe should take proactive steps to verify the quality control measures of potential suppliers. Here are actionable insights:
-
Conduct Supplier Audits: Regular audits help buyers assess the manufacturing processes, quality assurance protocols, and compliance with standards. An on-site audit can provide deeper insights into the supplier’s operations.
-
Request Quality Assurance Reports: Suppliers should be able to provide documentation that details their quality control processes, testing results, and compliance certifications. This transparency builds trust and accountability.
-
Engage Third-Party Inspection Services: Utilizing third-party inspectors can provide an unbiased assessment of the supplier’s quality control processes and final products. This is particularly useful for international buyers who may not be able to visit suppliers personally.
What Are the Nuances of Quality Control for International B2B Buyers?
International B2B buyers need to be aware of specific nuances when it comes to quality control in different regions:
-
Understanding Regional Standards: Each region may have different safety and quality standards. For example, regulations in Europe may differ from those in Africa or South America. Buyers should familiarize themselves with local requirements to ensure compliance.
-
Cultural Considerations: Communication styles and business practices can vary significantly between regions. Understanding these cultural nuances can aid in building effective relationships with suppliers and ensuring clarity in quality expectations.
-
Supply Chain Logistics: Quality control can also be affected by logistics and transportation. Buyers should consider how products are stored and transported, as these factors can impact the quality and condition of the cones upon arrival.
Conclusion: Why Quality Assurance Matters in Traffic Cone Manufacturing
For international B2B buyers, understanding the manufacturing processes and quality assurance protocols for traffic cones is essential. By focusing on robust quality control measures, suppliers can ensure that their products meet the necessary safety standards, ultimately leading to increased buyer confidence and satisfaction. Buyers should take an active role in verifying these processes to ensure they are partnering with reliable suppliers who prioritize quality and compliance.
Practical Sourcing Guide: A Step-by-Step Checklist for ‘traffic cone supplier’
Introduction
Sourcing traffic cones requires careful consideration and strategic planning, especially for international B2B buyers from regions like Africa, South America, the Middle East, and Europe. This step-by-step checklist is designed to guide you through the essential stages of procurement, ensuring you find a reliable supplier that meets your specific needs while complying with regional regulations.
Step 1: Define Your Technical Specifications
Before reaching out to suppliers, clearly outline the technical specifications of the traffic cones you require. Consider factors such as size, color, material, and reflectivity. Each region may have different standards for safety and visibility, so it’s crucial to ensure your specifications comply with local regulations.
- Size and Weight: Determine the appropriate height and weight that suits your application, whether for construction sites or traffic management.
- Material Durability: Select materials that withstand environmental conditions specific to your region, like UV resistance in sunny climates.
Step 2: Research and Identify Potential Suppliers
Start by conducting thorough research to compile a list of potential traffic cone suppliers. Use online resources, industry directories, and trade shows to find reputable suppliers with a solid track record.
- Industry Reputation: Look for suppliers with positive reviews and testimonials from previous clients.
- Geographical Considerations: Identify suppliers that are strategically located to minimize shipping costs and delivery times.
Step 3: Evaluate Supplier Credentials
Before making a decision, it is essential to verify the credentials of your shortlisted suppliers. This step helps ensure they are legitimate and capable of meeting your needs.
- Certifications: Check for relevant certifications such as ISO standards that reflect quality and safety compliance.
- Experience: Assess how long the supplier has been in the industry and their experience with similar projects.
Step 4: Request Samples and Prototypes
Once you have narrowed down your options, request samples or prototypes of the traffic cones. This allows you to evaluate the quality and suitability of the products before committing to a large order.
- Quality Assessment: Examine the physical properties of the cones, including flexibility, weight, and reflectivity.
- Compliance Check: Ensure the samples meet your defined specifications and any local safety regulations.
Step 5: Review Pricing and Payment Terms
Discuss pricing structures and payment terms with your potential suppliers. Understanding the total cost, including shipping and taxes, is crucial for budgeting.
- Bulk Discounts: Inquire about discounts for larger orders, which can significantly reduce costs.
- Payment Flexibility: Explore payment options that suit your cash flow, such as installments or credit terms.
Step 6: Negotiate Delivery Terms and Lead Times
Clarifying delivery terms is vital to ensure you receive your order on time. Discuss lead times and shipping methods with your supplier to avoid potential delays.
- Shipping Method: Decide on the most cost-effective and timely shipping option, considering your location.
- Tracking Options: Ensure that the supplier provides tracking information for your shipment to monitor its progress.
Step 7: Establish a Long-term Relationship
After successfully sourcing traffic cones, consider establishing a long-term relationship with your supplier. This can lead to better pricing, priority service, and collaborative opportunities for future projects.
- Feedback Loop: Provide feedback on product quality and service to foster a mutually beneficial relationship.
- Regular Communication: Maintain open lines of communication to address any concerns promptly and strengthen the partnership.
By following these steps, international B2B buyers can effectively navigate the sourcing process for traffic cones, ensuring they select a supplier that aligns with their operational needs and regional standards.
Comprehensive Cost and Pricing Analysis for traffic cone supplier Sourcing
What Are the Key Cost Components for Traffic Cone Suppliers?
When sourcing traffic cones, understanding the cost structure is essential for making informed purchasing decisions. The primary cost components include:
-
Materials: The type of materials used directly affects the cost. Common materials include PVC for flexibility and durability, and reflective sheeting for visibility. Higher-quality materials may lead to increased costs but can also enhance product longevity and safety.
-
Labor: Labor costs vary by region and can significantly impact the overall pricing. In countries with higher wage standards, labor costs will contribute more to the final price. Conversely, regions with lower labor costs might offer more competitive pricing but could raise concerns about product quality.
-
Manufacturing Overhead: This includes costs associated with factory operations, such as utilities, rent, and equipment maintenance. Efficient manufacturing processes can help minimize these overhead costs, ultimately benefiting buyers.
-
Tooling: If custom designs or specifications are required, tooling costs can be substantial. This is particularly relevant for buyers looking for unique branding or specialized features in their traffic cones.
-
Quality Control (QC): Robust QC processes ensure that products meet safety and quality standards, which can add to the cost. However, investing in quality control can prevent costly returns or safety issues in the long run.
-
Logistics: Shipping and handling costs can vary widely depending on the origin of the product and the destination. Factors such as shipping distance, mode of transport, and customs duties must be considered.
-
Margin: Suppliers will add a margin to cover their expenses and profit. This margin can vary based on market competition, supplier reputation, and product demand.
How Do Pricing Influencers Affect Traffic Cone Costs?
Several factors influence the pricing of traffic cones that international buyers should be aware of:
-
Volume and Minimum Order Quantity (MOQ): Suppliers often provide better pricing for larger orders. Understanding the MOQ can help buyers negotiate better rates.
-
Specifications and Customization: Customized traffic cones will typically incur additional costs. Buyers should weigh the benefits of customization against the added expense.
-
Quality and Certifications: Products that meet specific safety and quality certifications may command higher prices. However, these certifications can provide assurance of product reliability, especially in regions with strict safety regulations.
-
Supplier Factors: The reputation and reliability of the supplier can influence pricing. Established suppliers may charge higher prices due to their proven track record, while newer suppliers might offer lower prices to gain market entry.
-
Incoterms: Understanding the delivery terms outlined in Incoterms (International Commercial Terms) is critical. These terms dictate who bears the cost and risk at each stage of the shipping process, impacting the overall cost structure.
What Buyer Tips Can Help Optimize Traffic Cone Sourcing?
International B2B buyers can leverage various strategies to ensure cost-effective sourcing of traffic cones:
-
Negotiation: Always negotiate pricing with suppliers. Highlighting your business’s potential for repeat orders can strengthen your negotiating position.
-
Focus on Total Cost of Ownership (TCO): Consider not just the purchase price but also the long-term costs associated with the product, including maintenance and replacement costs. A cheaper cone may not be cost-effective if it needs frequent replacement.
-
Understand Pricing Nuances: Be aware that prices may fluctuate based on market demand, seasonality, and geopolitical factors, especially for buyers in regions like Africa and South America, where economic conditions can vary significantly.
-
Research Local Regulations: In regions like Europe, specific regulations may dictate the standards for traffic cones. Ensuring compliance can save costs related to fines or product recalls.
What Should Buyers Keep in Mind Regarding Indicative Prices?
While indicative prices can provide a useful benchmark, they should be treated with caution. Prices can vary widely based on the factors mentioned above, and it’s advisable for buyers to request detailed quotes from multiple suppliers. Engaging in thorough market research and building relationships with suppliers can lead to better pricing and terms.
Alternatives Analysis: Comparing traffic cone supplier With Other Solutions
When evaluating the best solutions for managing traffic and ensuring safety on roadways, B2B buyers must consider various alternatives to traditional traffic cone suppliers. Alternatives can provide different benefits, costs, and implementation processes that may better suit specific business needs, especially in diverse markets across Africa, South America, the Middle East, and Europe. Below, we compare traffic cone suppliers with other viable solutions: smart traffic management systems and mobile traffic alert applications.
Comparison Aspect | Traffic Cone Supplier | Smart Traffic Management Systems | Mobile Traffic Alert Applications |
---|---|---|---|
Performance | Effective for short-term use, visible under various conditions | Real-time data analysis, adaptive traffic control | Provides live updates and alerts, enhances driver awareness |
Cost | Moderate initial investment, ongoing replacement costs | High initial investment, potential long-term savings | Low-cost option, often subscription-based |
Ease of Implementation | Simple installation, requires manual setup | Complex installation, may require integration with existing infrastructure | Easy to implement, user-friendly applications |
Maintenance | Regular physical checks needed, susceptible to wear | Requires software updates and system checks | Minimal maintenance, updates handled by developers |
Best Use Case | Temporary traffic management for construction zones | Permanent solutions for urban traffic flow management | Real-time navigation and traffic updates for drivers |
What Are the Advantages and Disadvantages of Smart Traffic Management Systems?
Smart traffic management systems leverage advanced technology to manage traffic flow, using sensors and cameras to adapt to real-time conditions.
Pros:
– These systems can significantly reduce congestion and improve road safety by dynamically managing traffic signals based on current traffic volumes.
– They also provide valuable data for long-term urban planning.
Cons:
– The initial investment is considerably higher than traditional traffic cones, which may not be feasible for smaller businesses or projects.
– Implementation can be complex and time-consuming, requiring coordination with local authorities and infrastructure adjustments.
How Do Mobile Traffic Alert Applications Serve as an Alternative?
Mobile traffic alert applications, such as Waze, provide real-time updates to drivers about traffic conditions, accidents, and road hazards.
Pros:
– These applications are user-friendly and can be implemented quickly, making them accessible to a wide range of users.
– They are generally low-cost and can improve safety by keeping drivers informed.
Cons:
– Mobile applications depend on user engagement and may not effectively manage traffic flow in a proactive manner.
– They do not provide physical barriers or guidance like traffic cones do, which may be crucial in certain scenarios.
Conclusion: How Can B2B Buyers Choose the Right Traffic Management Solution?
When selecting a traffic management solution, B2B buyers should assess their specific needs, including the nature of their projects, budget constraints, and the level of technology they are comfortable implementing. For short-term projects requiring immediate visibility, traditional traffic cones may suffice. However, for long-term urban planning and traffic flow optimization, investing in smart traffic management systems could yield significant benefits. Mobile applications serve as a supplementary tool, enhancing safety and communication among drivers. Ultimately, the best choice will align with the buyer’s operational objectives and resource availability.
Essential Technical Properties and Trade Terminology for traffic cone supplier
What Are the Essential Technical Properties of Traffic Cones?
When considering traffic cones for procurement, understanding their technical properties is vital for ensuring safety and compliance with regulations. Here are some critical specifications to evaluate:
-
Material Grade
Traffic cones are typically made from PVC (Polyvinyl Chloride) or PE (Polyethylene). PVC cones offer durability and resistance to extreme weather conditions, while PE cones are lightweight and flexible. The choice of material affects the cone’s lifespan, visibility, and ability to withstand impacts, making it essential to select the right grade based on the intended use. -
Height and Weight
Standard traffic cones vary in height from 18 inches to 36 inches. The weight is also a critical factor; heavier cones provide stability against wind and accidental bumps. For B2B buyers, selecting the appropriate height and weight ensures that the cones meet local traffic regulations and remain effective in controlling traffic. -
Reflectivity
Reflective bands on traffic cones enhance visibility, especially in low-light conditions. The effectiveness of these reflective materials is often measured by their retroreflectivity, which indicates how well they return light to its source. For international buyers, ensuring high retroreflectivity standards can significantly improve road safety. -
Base Design
The base of a traffic cone is designed to provide stability. Cones with a wider base are less likely to tip over, especially in adverse weather conditions. Understanding the base design helps buyers assess the performance of the cones in various environments, particularly in regions with high winds or heavy traffic. -
Tolerance Levels
Tolerance refers to the allowable variation in the dimensions of the cones. Ensuring that cones meet specified tolerances is crucial for uniformity and performance. In the B2B context, this can affect how well cones stack for storage and transport, impacting logistics and operational efficiency.
Which Trade Terms Should International Buyers Understand?
Familiarity with industry jargon is essential for effective communication and negotiation in the procurement process. Here are some common terms that B2B buyers should know:
-
OEM (Original Equipment Manufacturer)
This term refers to companies that produce parts or equipment that may be marketed by another manufacturer. For traffic cone buyers, understanding OEM relationships can provide insights into product quality and sourcing options. -
MOQ (Minimum Order Quantity)
MOQ is the smallest amount of a product that a supplier is willing to sell. Knowing the MOQ helps buyers plan their inventory and budget effectively, ensuring they meet supplier requirements while minimizing excess stock. -
RFQ (Request for Quotation)
An RFQ is a document sent to suppliers requesting pricing and other terms for specific products. Crafting a comprehensive RFQ can streamline the procurement process, allowing buyers to compare offers and negotiate better deals. -
Incoterms (International Commercial Terms)
These are standardized trade terms that define the responsibilities of buyers and sellers in international transactions. Familiarity with Incoterms is crucial for understanding shipping costs, risks, and obligations, especially when importing traffic cones from different regions. -
Lead Time
Lead time refers to the time it takes from placing an order to receiving the goods. Understanding lead times helps buyers manage project timelines and avoid delays, particularly in regions with longer shipping routes. -
Certification Standards
Various regions have specific certification standards for traffic safety products. Buyers should be aware of these standards to ensure compliance and enhance the credibility of their procurement choices.
By grasping these technical properties and trade terms, international B2B buyers can make informed decisions, ensuring that their procurement of traffic cones aligns with safety regulations and operational needs.
Navigating Market Dynamics and Sourcing Trends in the traffic cone supplier Sector
What Are the Current Market Dynamics and Key Trends in the Traffic Cone Supplier Sector?
The traffic cone supplier sector is experiencing notable shifts driven by several global factors. Increased urbanization, infrastructure development, and a surge in road safety initiatives are pivotal in shaping the market landscape. Emerging markets in Africa and South America are ramping up their infrastructure projects, leading to a higher demand for traffic management products, including traffic cones. Furthermore, advancements in technology are influencing sourcing trends. The rise of e-commerce platforms and digital supply chain solutions is enabling international B2B buyers to access a broader range of suppliers, facilitating easier comparisons and procurement processes.
Another key trend is the adoption of smart technologies in traffic management. Traffic cones integrated with IoT sensors are gaining traction, providing real-time data on traffic conditions and enhancing safety measures. For buyers in regions like the Middle East and Europe, the focus on smart city initiatives aligns with this trend, creating opportunities for suppliers who can offer innovative solutions. Additionally, sustainability is becoming an essential criterion for sourcing decisions. Buyers are increasingly seeking suppliers who prioritize eco-friendly materials and processes, reflecting a broader commitment to corporate social responsibility.
How Does Sustainability and Ethical Sourcing Impact the Traffic Cone Supplier Sector?
Sustainability and ethical sourcing have emerged as critical considerations for international B2B buyers in the traffic cone sector. The environmental impact of manufacturing and disposing of traffic cones is significant, given that traditional materials like PVC can contribute to pollution and waste. As a result, buyers are increasingly prioritizing suppliers who utilize recycled materials and environmentally friendly production methods.
Certifications such as ISO 14001 for environmental management and the use of green materials are becoming essential in supplier evaluations. Buyers from Europe, for instance, are particularly attuned to sustainability practices, often favoring suppliers with transparent supply chains that demonstrate ethical labor practices and minimal environmental footprints. By opting for sustainable products, buyers not only comply with regulatory requirements but also enhance their corporate image, appealing to environmentally conscious consumers and stakeholders.
What Is the Brief Evolution and History of Traffic Cone Suppliers?
The traffic cone, initially introduced in the 1940s, has evolved significantly from its humble beginnings. Originally made of rubber and designed for temporary road closures, the traffic cone has transformed into a versatile tool in traffic management. Innovations in materials have led to the development of lightweight, durable cones that can withstand harsh weather conditions and are highly visible due to reflective materials.
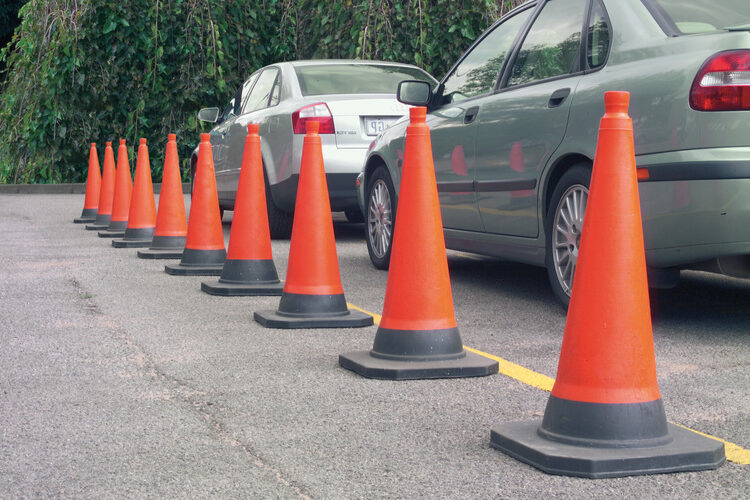
A stock image related to traffic cone supplier.
Over the decades, the traffic cone supplier sector has seen increased standardization and regulation, particularly in developed markets. The introduction of safety regulations and guidelines has necessitated higher quality and more effective products. Today, suppliers are not only focused on producing traditional cones but also on developing smart solutions that integrate technology for enhanced safety and traffic management. This evolution reflects the growing complexity of urban environments and the need for innovative traffic control measures, positioning traffic cones as essential components in modern infrastructure development.
Frequently Asked Questions (FAQs) for B2B Buyers of traffic cone supplier
-
How do I evaluate the quality of traffic cones from suppliers?
When sourcing traffic cones, assess the supplier’s quality control processes. Request samples to examine materials used, durability, and reflectivity. Look for compliance with international safety standards such as EN 13422 in Europe or ASTM D4956 in the U.S. Additionally, ask for certifications that validate the manufacturing process and product quality. Reviews and testimonials from other businesses can also provide insights into the supplier’s reliability. -
What is the best type of traffic cone for construction sites?
The best type of traffic cone for construction sites typically features high visibility, durable materials, and a weighted base to withstand wind and traffic. Look for cones that are at least 28 inches tall with reflective bands for enhanced visibility. Consider cones made from PVC or rubber, as these materials are resistant to wear and tear. For international buyers, ensure the cones meet local regulations regarding color and reflectivity. -
What are the common minimum order quantities (MOQ) for traffic cones?
Minimum order quantities for traffic cones can vary significantly among suppliers. Typically, MOQs range from 100 to 1,000 units, depending on the supplier’s production capacity and your specific needs. It’s advisable to discuss your requirements directly with suppliers, as many are willing to negotiate MOQs for first-time buyers or larger contracts. Be sure to consider shipping costs and logistics when determining your order size. -
How can I customize traffic cones for my business?
Customization options for traffic cones often include color, size, and branding elements like logos or text. When selecting a supplier, inquire about their capabilities for customization and any additional costs involved. Some suppliers may offer digital proofs before production, allowing you to visualize the final product. Ensure that the customization adheres to local safety regulations, especially if the cones will be used in public spaces. -
What payment terms should I expect when dealing with international traffic cone suppliers?
Payment terms with international suppliers can vary widely. Common practices include upfront payments, deposits, or letters of credit. Be sure to clarify terms such as net 30 or net 60 days, which refer to the time frame in which payment is due after receiving an invoice. Consider using secure payment methods like PayPal or escrow services to minimize risks. Understanding the currency exchange rates and potential fees is also crucial for international transactions.
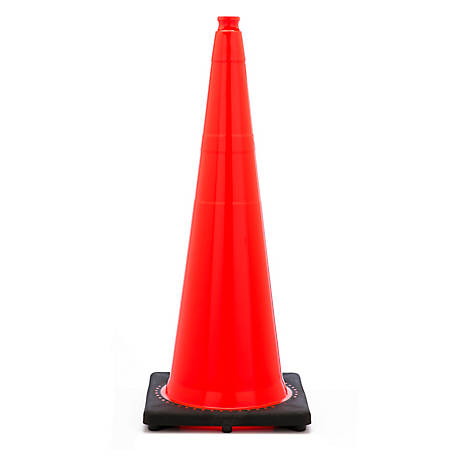
A stock image related to traffic cone supplier.
-
What are the key logistical considerations for importing traffic cones?
Logistical considerations for importing traffic cones include shipping methods, customs clearance, and delivery timelines. Air freight is faster but more expensive, while sea freight is cost-effective for larger orders. Ensure that the supplier provides the necessary documentation for customs clearance, including invoices and certificates of origin. Familiarize yourself with local import regulations to avoid delays or unexpected tariffs upon arrival. -
How do I verify the credibility of a traffic cone supplier?
To verify a supplier’s credibility, conduct thorough research, including checking their business license and certifications. Request references from previous clients, especially those in your region. Utilize platforms like Alibaba or Global Sources to assess supplier ratings and reviews. Additionally, consider visiting their manufacturing facility if possible, or engage a third-party inspection service to evaluate the supplier’s operations and quality assurance processes. -
What safety standards should traffic cones meet in my region?
Traffic cones must adhere to specific safety standards that vary by region. For instance, in Europe, cones should comply with EN 13422, which covers dimensions, materials, and reflectivity. In the U.S., ASTM D4956 outlines similar requirements. Research your local regulations to ensure compliance and enhance safety on construction sites or public roadways. Suppliers should provide documentation proving that their products meet these standards.
Important Disclaimer & Terms of Use
⚠️ Important Disclaimer
The information provided in this guide, including content regarding manufacturers, technical specifications, and market analysis, is for informational and educational purposes only. It does not constitute professional procurement advice, financial advice, or legal advice.
While we have made every effort to ensure the accuracy and timeliness of the information, we are not responsible for any errors, omissions, or outdated information. Market conditions, company details, and technical standards are subject to change.
B2B buyers must conduct their own independent and thorough due diligence before making any purchasing decisions. This includes contacting suppliers directly, verifying certifications, requesting samples, and seeking professional consultation. The risk of relying on any information in this guide is borne solely by the reader.
Strategic Sourcing Conclusion and Outlook for traffic cone supplier
As the global demand for effective traffic management solutions continues to rise, strategic sourcing in the traffic cone supply sector is more critical than ever. By understanding the unique needs of your region—whether in Africa, South America, the Middle East, or Europe—international B2B buyers can make informed decisions that enhance safety and operational efficiency.
How Can Strategic Sourcing Enhance Your Supply Chain for Traffic Cones?
Investing in strategic sourcing not only streamlines procurement processes but also fosters long-term partnerships with reliable suppliers. This approach helps in negotiating better terms, ensuring quality compliance, and maintaining timely deliveries, which are essential for projects that require immediate execution.
What Should You Consider When Sourcing Traffic Cones?
When evaluating suppliers, prioritize factors such as product durability, compliance with local regulations, and the supplier’s ability to scale with your needs. Engaging with suppliers who have a solid reputation and understanding of your market can lead to significant cost savings and improved service levels.
What Is the Future Outlook for Traffic Cone Suppliers?
Looking ahead, the emphasis on sustainable practices and innovative designs will shape the traffic cone market. Buyers are encouraged to seek suppliers who incorporate eco-friendly materials and technologies. By aligning with forward-thinking suppliers, you position your business to adapt to changing regulations and customer expectations.
In conclusion, leveraging strategic sourcing will not only optimize your supply chain but also contribute to safer road environments. Embrace this opportunity to build resilient partnerships and ensure your projects are equipped with the best traffic management solutions available.