Discover Top Tumbler Manufacturers: A Complete Sourcing Guide (2025)
Introduction: Navigating the Global Market for tumbler manufacturer
In today’s global marketplace, sourcing high-quality tumblers for diverse applications can pose significant challenges for international B2B buyers. Whether you are in the hospitality sector, retail, or promotional merchandise, understanding the nuances of tumbler manufacturing is critical. This guide delves into the multifaceted world of tumbler manufacturers, covering various types—from insulated travel mugs to elegant barware—along with their applications in different industries.
Navigating supplier vetting, pricing structures, and quality control processes is essential for making informed purchasing decisions. This comprehensive resource empowers buyers from Africa, South America, the Middle East, and Europe, including key markets like Spain and Saudi Arabia, to streamline their procurement strategies. By addressing specific concerns such as material selection, customization options, and sustainability practices, this guide will equip you with actionable insights to enhance your purchasing power.
Furthermore, it highlights best practices for establishing long-term relationships with reliable suppliers, ensuring that your business can consistently meet customer demands while maintaining product integrity. With this knowledge, you can confidently approach the global market for tumblers, transforming potential challenges into opportunities for growth and success.
Understanding tumbler manufacturer Types and Variations
Type Name | Key Distinguishing Features | Primary B2B Applications | Brief Pros & Cons for Buyers |
---|---|---|---|
Glass Tumblers | Made from various types of glass; elegant and sturdy | Bars, restaurants, catering | Pros: Aesthetic appeal, durability; Cons: Fragility, heavier than plastic. |
Plastic Tumblers | Lightweight, often BPA-free; available in various colors | Events, outdoor catering, schools | Pros: Cost-effective, shatterproof; Cons: Less premium feel, potential for lower durability. |
Stainless Steel Tumblers | Insulated, durable, often double-walled; modern design | Coffee shops, promotional items | Pros: Excellent insulation, long-lasting; Cons: Higher cost, potential for scratches. |
Customizable Tumblers | Can be personalized with logos or designs; available in various materials | Corporate gifts, promotional events | Pros: Brand visibility, unique offerings; Cons: Longer lead times, potential minimum order quantities. |
Ceramic Tumblers | Available in various glazes and finishes; often heavier | Coffee shops, upscale restaurants | Pros: Unique designs, heat retention; Cons: Heavier, more prone to chipping. |
What Are the Characteristics of Glass Tumblers for B2B Buyers?
Glass tumblers are a popular choice for businesses seeking an upscale presentation. They are available in a variety of styles, from classic to modern, and can be used in bars, restaurants, and catering services. The primary consideration for B2B buyers is durability, as glass can be fragile. Buyers should also consider the weight and ease of cleaning, particularly for high-volume environments.
Why Choose Plastic Tumblers for Events?
Plastic tumblers are ideal for events and outdoor catering due to their lightweight and shatterproof nature. They come in various colors and designs, making them suitable for casual settings like schools and festivals. B2B buyers should focus on the cost-effectiveness and the availability of BPA-free options, but they may sacrifice the premium feel that glass provides.
How Do Stainless Steel Tumblers Benefit Coffee Shops?
Stainless steel tumblers are increasingly popular in coffee shops and for promotional items due to their excellent insulation properties and modern aesthetic. They are durable and long-lasting, making them a wise investment for B2B buyers looking for products that withstand daily use. However, the higher upfront cost and potential for scratches are factors to consider when making bulk purchases.
What Are the Advantages of Customizable Tumblers?
Customizable tumblers offer businesses the opportunity to enhance brand visibility through personalized logos and designs. They are available in multiple materials, catering to diverse customer preferences. For B2B buyers, the key considerations include lead times and minimum order quantities, as these can impact budgets and promotional timelines.
When Should You Consider Ceramic Tumblers?
Ceramic tumblers provide a unique aesthetic with various glazes and finishes, making them suitable for upscale restaurants and coffee shops. They retain heat well, enhancing the drinking experience. However, B2B buyers should be aware of their weight and susceptibility to chipping, which can affect usability in high-traffic environments.
Related Video: Stainless steel tumbler travel mug manufacturing process
Key Industrial Applications of tumbler manufacturer
Industry/Sector | Specific Application of tumbler manufacturer | Value/Benefit for the Business | Key Sourcing Considerations for this Application |
---|---|---|---|
Food and Beverage | Use in bars and restaurants for serving drinks | Enhances customer experience and brand image | Quality, design, and compliance with health regulations |
Hospitality | Hotel room service and mini-bars | Increases guest satisfaction and convenience | Durability, aesthetic appeal, and ease of cleaning |
Retail | Promotional items for branding | Boosts brand visibility and customer engagement | Customization options and minimum order quantities |
Events and Catering | Disposable or reusable tumblers for events | Cost-effective and practical for large gatherings | Bulk pricing, delivery timelines, and product variety |
Corporate Gifts | Customized tumblers for corporate giveaways | Strengthens client relationships and brand loyalty | Personalization capabilities and lead times |
How Are Tumblers Used in the Food and Beverage Industry?
In the food and beverage sector, tumblers are essential for serving a variety of drinks, from cocktails to soft drinks. They enhance the overall customer experience, contributing to a restaurant or bar’s ambiance. International buyers, particularly from regions like Africa and South America, should prioritize sourcing tumblers that meet local health regulations while ensuring quality and durability, as these products withstand frequent use. Aesthetic design also plays a vital role in attracting customers and reinforcing brand image.
What Role Do Tumblers Play in the Hospitality Sector?
In the hospitality industry, tumblers are commonly used in hotel room service and mini-bars, providing guests with a convenient way to enjoy beverages. High-quality tumblers can significantly enhance guest satisfaction, as they reflect the establishment’s commitment to quality service. Buyers from Europe, particularly Spain, should consider tumblers that are not only visually appealing but also durable and easy to clean, addressing the high turnover rates in hotel environments.
How Can Retailers Benefit from Tumblers as Promotional Items?
Retailers often use tumblers as promotional items to increase brand visibility and customer engagement. Customizable tumblers can serve as effective marketing tools during events or as part of loyalty programs. Buyers should focus on suppliers that offer diverse customization options and reasonable minimum order quantities, especially in emerging markets in Africa and South America where brand differentiation is crucial for success.
Why Are Tumblers Important for Events and Catering?
In events and catering, tumblers are crucial for both disposable and reusable options, catering to various client preferences. They provide a practical solution for serving beverages at large gatherings, ensuring that hosts can manage costs effectively while still delivering quality service. Buyers should consider bulk pricing and product variety when sourcing tumblers for events, as these factors can significantly influence overall cost and guest experience.
How Do Customized Tumblers Enhance Corporate Gifting?
Customized tumblers are increasingly popular as corporate gifts, helping businesses strengthen client relationships and foster brand loyalty. By providing a useful and stylish item, companies can leave a lasting impression on clients. Buyers should look for manufacturers that offer personalization capabilities and reasonable lead times to ensure timely delivery, particularly for international events or campaigns in the Middle East and Europe.
3 Common User Pain Points for ‘tumbler manufacturer’ & Their Solutions
Scenario 1: Navigating Quality Control Challenges in Tumblers
The Problem: International B2B buyers often face significant challenges related to quality control when sourcing tumblers from manufacturers, especially when dealing with overseas suppliers. Inconsistent product quality can lead to customer dissatisfaction, returns, and financial losses. Buyers may find themselves receiving tumblers with defects, poor finishes, or materials that do not meet the specified standards, making it difficult to maintain brand integrity and customer loyalty.
The Solution: To overcome quality control challenges, B2B buyers should implement a comprehensive supplier assessment strategy. Start by conducting thorough due diligence on potential manufacturers, including requesting product samples and reviewing certifications related to quality standards (such as ISO 9001). Establish clear specifications for the tumblers, detailing material requirements, dimensions, and performance expectations. This clarity will help manufacturers understand your needs better.
Furthermore, consider engaging third-party quality control services that can inspect the production process and final products before shipment. This proactive approach not only mitigates risks but also enhances trust between you and the manufacturer, ensuring that the tumblers you receive meet your exact requirements.
Scenario 2: Managing Supply Chain Disruptions
The Problem: Supply chain disruptions are a common issue that can affect the timely delivery of tumblers, particularly in a global market. Factors such as geopolitical tensions, natural disasters, and transportation delays can lead to unexpected inventory shortages, affecting your ability to meet customer demand. This can be especially problematic for businesses in regions like Africa and South America, where logistics infrastructure may not be as robust.
The Solution: To effectively manage supply chain disruptions, B2B buyers should diversify their supplier base. Rather than relying on a single manufacturer, consider establishing relationships with multiple suppliers across different regions. This strategy allows for flexibility and reduces the risk of significant delays should one supplier encounter issues.
Additionally, implement a robust inventory management system that includes safety stock levels and reorder points. Use forecasting tools to better predict demand fluctuations and adjust orders accordingly. By maintaining open communication with suppliers about their production schedules and potential challenges, you can better plan for contingencies and ensure a steady supply of tumblers.
Scenario 3: Sourcing Eco-Friendly Tumblers for Sustainability Goals
The Problem: As sustainability becomes a focal point for many companies, sourcing eco-friendly tumblers can be a daunting task. B2B buyers often struggle to find manufacturers that offer sustainable options without compromising quality or increasing costs. This challenge is particularly relevant for businesses in Europe, where environmental regulations and consumer preferences increasingly favor eco-conscious products.
The Solution: To successfully source eco-friendly tumblers, start by defining what sustainability means for your organization—whether it’s using recycled materials, reducing carbon footprints, or ensuring ethical labor practices. Research manufacturers that specialize in sustainable products and have certifications such as FSC (Forest Stewardship Council) or other eco-labels.
Engage with suppliers about their production processes and material sourcing to ensure they align with your sustainability goals. Additionally, consider investing in custom tumbler designs that utilize biodegradable or recyclable materials. This not only meets your sustainability requirements but also differentiates your product in the marketplace, appealing to environmentally conscious consumers. Collaborate with your marketing team to highlight the eco-friendly aspects of your tumblers, enhancing your brand’s reputation and increasing market competitiveness.
Strategic Material Selection Guide for tumbler manufacturer
When selecting materials for tumbler manufacturing, it is essential to consider various properties, advantages, and limitations that can significantly impact product performance and marketability. Below, we analyze four common materials used in tumbler production, focusing on their key properties, pros and cons, and specific considerations for international B2B buyers.
What Are the Key Properties of Stainless Steel for Tumblers?
Stainless steel is a popular choice for tumbler manufacturing due to its excellent durability and corrosion resistance. Typically, food-grade stainless steel (like 304 or 316) is used, which can withstand high temperatures and is resistant to rust and staining. This makes stainless steel tumblers ideal for both hot and cold beverages.
Pros & Cons:
The primary advantages of stainless steel include its long lifespan, ease of cleaning, and resistance to flavor retention. However, it can be more expensive than other materials and may require more complex manufacturing processes, such as welding or specialized finishing techniques.
Impact on Application:
Stainless steel tumblers are compatible with a wide range of beverages, including acidic drinks, without risk of leaching harmful chemicals. This makes them suitable for both consumer and commercial markets.
Considerations for International Buyers:
Buyers from regions like Europe and the Middle East should ensure compliance with health and safety standards, such as those set by the European Union or local regulations. Understanding the specific grades of stainless steel and their certifications (e.g., ASTM, DIN) is crucial for maintaining quality.
How Does Glass Perform as a Material for Tumblers?
Glass tumblers are valued for their aesthetic appeal and ability to showcase the beverage inside. They can be produced in various styles, including tempered glass for enhanced durability. Glass is non-reactive, meaning it won’t alter the taste of the drink.
Pros & Cons:
While glass tumblers offer a premium feel and are easy to clean, they are prone to breakage, which can be a significant drawback in high-traffic environments. Additionally, the manufacturing process can be more energy-intensive and costly compared to other materials.
Impact on Application:
Glass is suitable for beverages that are served cold or at room temperature, making it ideal for cafes, restaurants, and upscale events. However, it is not recommended for hot liquids unless specifically designed for heat resistance.
Considerations for International Buyers:
In regions like South America and Africa, where transportation may be more challenging, the fragility of glass can be a concern. Buyers should consider the logistics of shipping and handling to avoid breakage.
What Are the Advantages of Plastic in Tumbler Manufacturing?
Plastic tumblers are lightweight and versatile, making them a cost-effective option for mass production. Common plastics used include polypropylene and polycarbonate, which can be molded into various shapes and sizes.
Pros & Cons:
The main advantages of plastic tumblers are their affordability and durability. They are less likely to break compared to glass and can be produced in vibrant colors. However, some plastics can retain odors and flavors, and there are concerns about chemical leaching, especially with hot liquids.
Impact on Application:
Plastic tumblers are widely used in casual settings, outdoor events, and for promotional items. They are suitable for cold beverages and some hot drinks, depending on the plastic type.
Considerations for International Buyers:
Buyers should be aware of regulations regarding food-safe plastics, especially in Europe, where strict standards are enforced. Additionally, the environmental impact of plastic use is a growing concern, prompting many buyers to seek recyclable or biodegradable options.
Why Choose Silicone for Tumblers?
Silicone is an increasingly popular material for tumbler manufacturing due to its flexibility and heat resistance. It can be used for both the outer casing and the inner lining of tumblers.
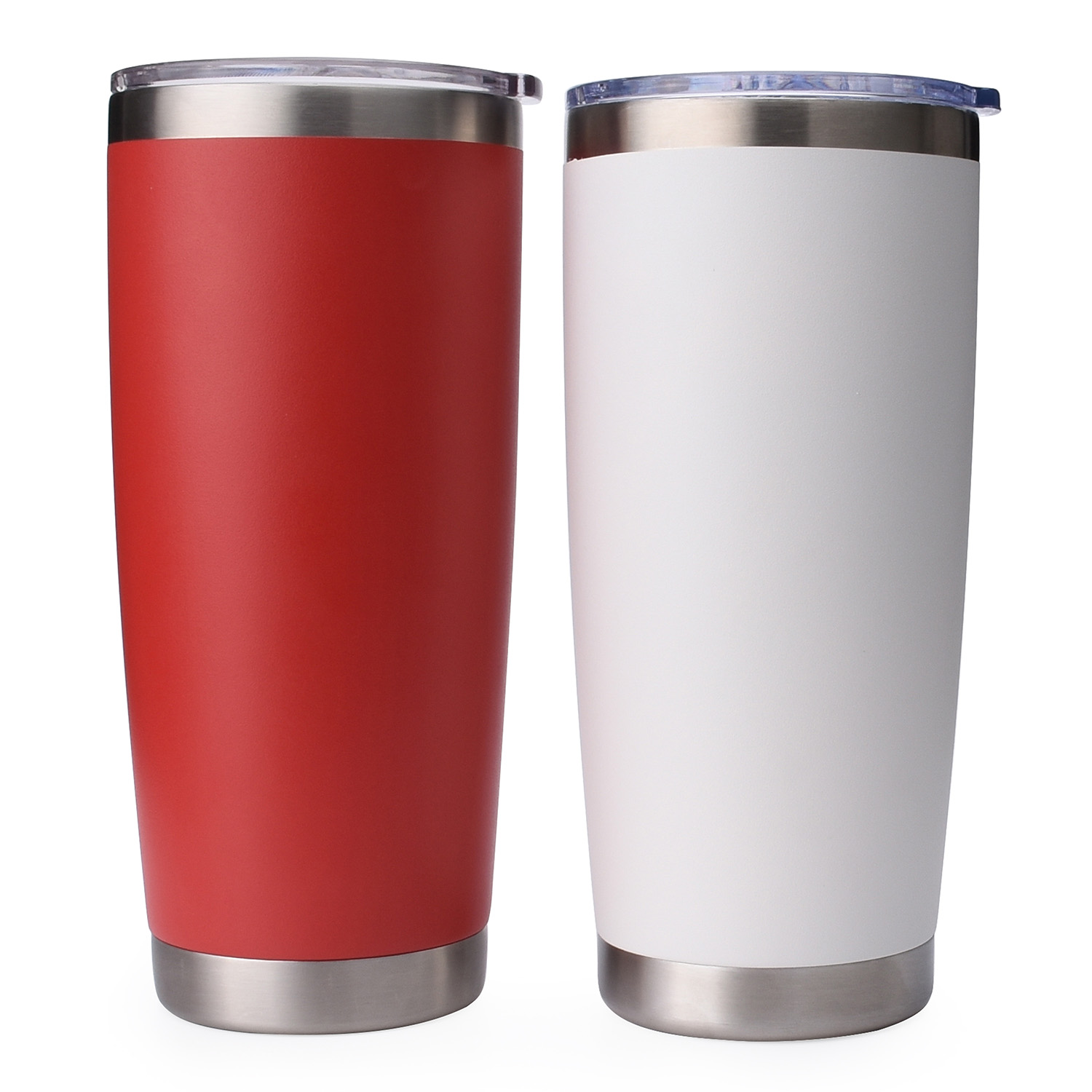
A stock image related to tumbler manufacturer.
Pros & Cons:
Silicone tumblers are highly durable, resistant to temperature extremes, and non-toxic. However, they may not provide the same premium feel as glass or stainless steel and can be perceived as less sophisticated.
Impact on Application:
Silicone is suitable for a variety of beverages and is particularly useful for travel mugs due to its lightweight and unbreakable nature.
Considerations for International Buyers:
Buyers should verify that silicone products comply with relevant food safety standards and certifications, especially in regions like the Middle East, where regulations can vary significantly.
Summary Table of Material Selection for Tumblers
Material | Typical Use Case for tumbler manufacturer | Key Advantage | Key Disadvantage/Limitation | Relative Cost (Low/Med/High) |
---|---|---|---|---|
Stainless Steel | Hot and cold beverages, commercial use | Durability and corrosion resistance | Higher cost, complex manufacturing | High |
Glass | Upscale events, cafes | Aesthetic appeal, non-reactive | Prone to breakage, higher energy use | Med |
Plastic | Casual settings, outdoor events | Lightweight and cost-effective | Odor retention, potential leaching | Low |
Silicone | Travel mugs, flexible applications | Heat resistance, unbreakable | Less premium feel | Med |
By understanding these materials and their implications, international B2B buyers can make informed decisions that align with their market needs and regulatory requirements.
In-depth Look: Manufacturing Processes and Quality Assurance for tumbler manufacturer
What Are the Main Stages of Tumbler Manufacturing?
The manufacturing of tumblers involves several key stages that ensure quality and durability. Understanding these processes is crucial for B2B buyers looking to source high-quality products.
Material Preparation: What Materials Are Commonly Used?
The first step in tumbler manufacturing is material preparation, where manufacturers select appropriate materials based on the tumbler’s intended use. Common materials include:
- Stainless Steel: Known for its durability and resistance to rust, making it ideal for both hot and cold beverages.
- Glass: Often used for its aesthetic appeal and ability to maintain the temperature of drinks.
- Plastic: Lightweight and often used for disposable tumblers; however, quality varies significantly.
Manufacturers should ensure that materials meet international safety and quality standards, particularly for food contact items.
How Are Tumblers Formed?
The forming stage involves various techniques depending on the material used:
- Metal Tumblers: For stainless steel, processes such as stamping and deep drawing are common. Sheets of metal are cut and shaped into the desired form, often using hydraulic presses.
- Glass Tumblers: Glass blowing or molding techniques are used, where molten glass is shaped into tumbler forms. This requires precise temperature control to ensure uniform thickness.
- Plastic Tumblers: Injection molding is a prevalent method, where heated plastic is injected into molds to form the tumbler shape.
Each of these methods requires specialized equipment and skilled labor to ensure consistent quality and design.
What Happens During Assembly and Finishing?
Once the tumblers are formed, they undergo assembly and finishing processes:
- Assembly: For tumblers with additional components (like lids or straws), assembly is done either manually or with automated machines. Ensuring that all parts fit correctly is crucial for usability.
- Finishing: This includes polishing, coating, or printing designs on the tumblers. Techniques such as powder coating or silk screening can enhance aesthetics and provide additional protection.
The finishing touches not only improve the visual appeal but also contribute to the tumbler’s functionality and longevity.
What Quality Assurance Standards Should B2B Buyers Consider?
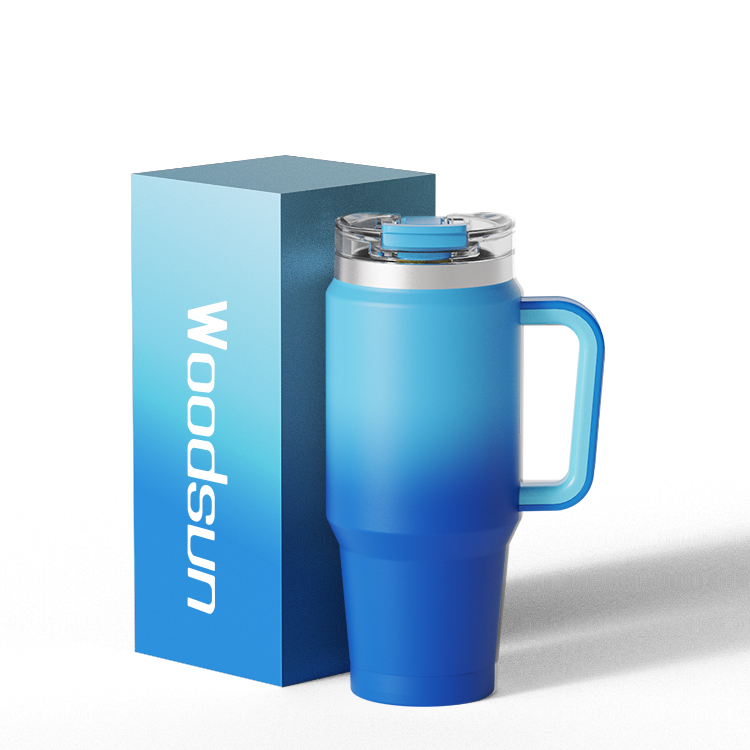
A stock image related to tumbler manufacturer.
Quality assurance (QA) is critical in tumbler manufacturing to ensure that products meet customer expectations and regulatory requirements. B2B buyers should be aware of several international standards and certifications:
Which International Standards Are Relevant for Tumblers?
- ISO 9001: This standard focuses on quality management systems and is applicable to all organizations. Manufacturers adhering to ISO 9001 demonstrate their commitment to consistent quality and customer satisfaction.
- CE Marking: Particularly relevant in Europe, CE marking indicates that products meet EU safety, health, and environmental protection standards.
- API (American Petroleum Institute): For tumblers designed for specific industrial applications, compliance with API standards can be crucial.
Buyers should verify that their suppliers possess these certifications, as they reflect a manufacturer’s commitment to quality.
How Is Quality Control Implemented Throughout the Manufacturing Process?
Quality Control (QC) is essential at various stages of the manufacturing process. Here are the key QC checkpoints:
What Are the Key QC Checkpoints in Tumbler Manufacturing?
-
Incoming Quality Control (IQC): This initial checkpoint ensures that the raw materials meet specified quality standards before production begins. It involves inspecting material samples for defects and verifying certificates of compliance.
-
In-Process Quality Control (IPQC): During the manufacturing process, IPQC monitors production parameters and inspects products at various stages. This includes checking dimensions, material properties, and visual inspections for defects.
-
Final Quality Control (FQC): At the end of production, FQC involves a comprehensive review of the finished tumblers. This may include functional testing (e.g., leakage tests), aesthetic checks, and packaging inspections.
By implementing these checkpoints, manufacturers can identify and rectify issues early, reducing waste and ensuring product quality.
How Can B2B Buyers Verify Supplier Quality Control?
For international buyers, especially from regions like Africa, South America, the Middle East, and Europe, verifying a supplier’s quality control processes is essential. Here are actionable steps:
What Actions Can Buyers Take to Ensure Supplier Quality?
-
Conduct Audits: Regular on-site audits of suppliers can provide insights into their manufacturing processes and quality assurance practices. This allows buyers to assess compliance with international standards firsthand.
-
Request Quality Reports: Suppliers should provide detailed QC reports, including information on testing methods and results. This documentation helps buyers understand the quality assurance measures in place.
-
Engage Third-Party Inspectors: Hiring independent third-party inspection services can ensure unbiased evaluations of product quality. This is especially useful for large orders where in-person audits may not be feasible.
What Nuances Should International Buyers Be Aware Of?
When sourcing tumblers internationally, B2B buyers should consider specific nuances that can affect quality assurance:
How Do Regional Regulations Impact Tumbler Quality?
-
Regional Standards: Different countries may have unique regulations regarding materials, safety, and environmental impact. For instance, buyers in the EU must be aware of REACH regulations that govern chemical safety.
-
Cultural Expectations: Buyers from different regions may have varying expectations regarding design and functionality. Understanding these preferences can guide buyers in selecting the right supplier.
-
Supply Chain Dynamics: International logistics can impact product quality. Delays or improper handling during shipping may lead to defects. Buyers should ensure that suppliers have robust logistics and handling protocols.
By understanding these factors, international B2B buyers can make informed decisions when selecting tumbler manufacturers, ensuring they receive high-quality products that meet their specific needs.
Practical Sourcing Guide: A Step-by-Step Checklist for ‘tumbler manufacturer’
Introduction
Sourcing the right tumbler manufacturer can significantly impact your business’s success, especially in a competitive global market. This guide provides a practical checklist to help international B2B buyers from regions such as Africa, South America, the Middle East, and Europe navigate the complexities of procurement. Following these steps will ensure you find a reliable supplier that meets your quality and budgetary requirements.
Step 1: Define Your Technical Specifications
Clearly outline the specifications for the tumblers you need. Consider factors such as materials (e.g., stainless steel, glass), sizes, and design features. This clarity will help you communicate effectively with suppliers and ensure that the products meet your expectations.
- Material Requirements: Specify if you need BPA-free or eco-friendly materials.
- Customization Needs: Determine if you require branding or unique designs.
Step 2: Conduct Market Research for Suppliers
Investigate potential suppliers by leveraging industry directories, trade shows, and online platforms. A thorough market analysis will provide insights into supplier capabilities, pricing structures, and market reputation.
- Regional Considerations: Pay attention to suppliers in regions that are known for tumbler manufacturing.
- Customer Reviews: Look for feedback from other buyers to gauge reliability.
Step 3: Evaluate Potential Suppliers
Before committing, it’s crucial to vet suppliers thoroughly. Request company profiles, case studies, and references from buyers in a similar industry or region. This step ensures that you partner with manufacturers who have a proven track record.
- Quality Assurance: Ask about their quality control processes and certifications.
- Production Capacity: Verify if they can meet your order volume and timeline.
Step 4: Verify Supplier Certifications
Check if the manufacturers hold necessary certifications, such as ISO, FDA, or other relevant standards. Certifications indicate compliance with international safety and quality standards, which is essential for maintaining your brand’s reputation.
- Sustainability Practices: Inquire about eco-certifications if sustainability is a priority for your brand.
- Production Methods: Ensure that their manufacturing processes align with your ethical sourcing goals.
Step 5: Request Samples for Quality Assessment
Always request product samples before making a large order. Evaluating samples allows you to assess the quality, functionality, and overall appeal of the tumblers. This step is essential to avoid costly mistakes later.
- Test for Durability: Check if the tumblers meet your performance standards.
- Design Evaluation: Ensure that the design aligns with your brand’s aesthetic.
Step 6: Negotiate Terms and Conditions
Once you’ve selected a supplier, negotiate terms such as pricing, payment methods, delivery timelines, and return policies. Clear agreements will prevent misunderstandings and ensure a smooth procurement process.
- Payment Flexibility: Consider discussing payment terms that suit your cash flow.
- Delivery Assurance: Establish penalties for delays to safeguard your supply chain.
Step 7: Establish Ongoing Communication
After securing a supplier, maintain regular communication to ensure that production stays on track. Open lines of communication will help you address any issues promptly and foster a strong business relationship.
- Regular Updates: Schedule periodic check-ins to monitor progress.
- Feedback Mechanism: Create a system for providing feedback on product quality and service.
By following this step-by-step checklist, international B2B buyers can effectively source reliable tumbler manufacturers that meet their specific needs, ultimately leading to better business outcomes.
Comprehensive Cost and Pricing Analysis for tumbler manufacturer Sourcing
What Are the Key Cost Components for Tumbler Manufacturing?
Understanding the cost structure of tumbler manufacturing is essential for international B2B buyers. The primary cost components include:
-
Materials: The choice of materials, such as stainless steel, glass, or plastic, significantly impacts costs. High-quality materials typically command higher prices but can enhance durability and customer satisfaction.
-
Labor: Labor costs vary by region and skill level required. For instance, countries with lower labor costs can reduce overall expenses, but this may affect product quality.
-
Manufacturing Overhead: This encompasses indirect costs associated with production, such as utilities, rent, and administrative expenses. Efficient management of these costs is crucial for maintaining competitive pricing.
-
Tooling: Initial tooling costs can be significant, especially for custom designs. Buyers should factor in these costs when considering customization.
-
Quality Control (QC): Investment in QC processes ensures that the final product meets industry standards. This may involve additional costs, but it can prevent costly returns and enhance brand reputation.
-
Logistics: Shipping and handling costs vary based on distance, weight, and chosen Incoterms. Understanding these factors can help buyers negotiate better terms with suppliers.
-
Margin: The margin set by the manufacturer can fluctuate based on market demand, competition, and perceived value. Buyers should be aware of this as they negotiate prices.
How Do Price Influencers Affect Tumbler Sourcing?
Several factors influence the pricing of tumblers, which buyers should consider:
-
Volume and Minimum Order Quantity (MOQ): Bulk purchases typically lead to lower per-unit costs. Understanding a supplier’s MOQ can help buyers maximize their budget.
-
Specifications and Customization: Custom designs or specific specifications can increase costs. It’s advisable for buyers to balance the need for uniqueness with budget constraints.
-
Materials and Quality Certifications: Higher quality materials and certifications (e.g., food safety standards) can increase costs but may be necessary for specific markets, particularly in Europe and North America.
-
Supplier Factors: Supplier reputation, reliability, and manufacturing capabilities can influence pricing. Buyers should conduct thorough due diligence to find the best fit.
-
Incoterms: The chosen Incoterms can significantly impact total costs. Buyers should clarify whether costs include shipping, insurance, and duties to avoid unexpected expenses.
What Are the Best Practices for Negotiating Tumbler Prices?
For international B2B buyers, particularly those in Africa, South America, the Middle East, and Europe, employing strategic negotiation tactics can lead to better pricing outcomes:
-
Understand Total Cost of Ownership (TCO): Assess all costs associated with a tumbler, including purchase price, shipping, and potential warranty costs. This holistic view can aid in negotiations.
-
Leverage Volume Discounts: When feasible, commit to larger orders to negotiate better prices. Suppliers are often willing to provide discounts for higher volume purchases.
-
Benchmark Pricing: Research and compare prices from multiple suppliers to establish a baseline for negotiations. This can empower buyers with knowledge of market rates.
-
Build Relationships: Establishing a long-term relationship with suppliers can lead to better pricing and preferential treatment in future dealings.
-
Be Transparent About Your Needs: Clearly communicating your requirements and constraints can foster a collaborative negotiation environment, leading to mutually beneficial agreements.
What Pricing Nuances Should International Buyers Consider?
International buyers face unique challenges and opportunities when sourcing tumblers:
-
Currency Fluctuations: Be aware of currency exchange rates, as they can affect pricing. Locking in prices at favorable rates can mitigate risks.
-
Regulatory Compliance: Different regions have varying compliance requirements. Ensuring that products meet local regulations can prevent costly delays or penalties.
-
Cultural Sensitivities: Understanding cultural preferences and trends in target markets can influence product specifications, which in turn affects pricing.
Disclaimer on Indicative Prices
Prices for tumblers can vary widely based on the aforementioned factors. This analysis provides a framework for understanding costs and pricing, but buyers should always seek updated quotes from multiple suppliers to ensure they receive the best value for their investment.
Alternatives Analysis: Comparing tumbler manufacturer With Other Solutions
When considering the procurement of tumblers for business purposes, international buyers must evaluate various alternatives to ensure they select the most suitable solution for their specific needs. Below, we compare traditional tumbler manufacturers against two viable alternatives: custom-branded promotional tumblers and reusable plastic tumblers. Each option has its own set of advantages and drawbacks, making it crucial to analyze them in detail.
Comparison Aspect | Tumbler Manufacturer | Custom-Branded Promotional Tumblers | Reusable Plastic Tumblers |
---|---|---|---|
Performance | High durability and quality | Variable quality based on supplier | Moderate durability |
Cost | Higher initial investment | Often lower cost per unit | Generally cost-effective |
Ease of Implementation | Requires detailed specifications | Quick turnaround for designs | Readily available in bulk |
Maintenance | Low maintenance needs | May require branding upkeep | Easy to clean, but less durable |
Best Use Case | Corporate gifting, high-end events | Marketing campaigns, giveaways | Everyday use, casual events |
What Are the Pros and Cons of Custom-Branded Promotional Tumblers?
Custom-branded promotional tumblers serve as an excellent marketing tool, especially for businesses looking to enhance brand visibility. They can be produced in bulk at a relatively low cost, making them appealing for events or giveaways. However, the quality can vary significantly depending on the supplier, which can impact customer perception of your brand. Additionally, while they are effective for short-term marketing, they may not provide the same level of durability as products from dedicated tumbler manufacturers.
How Do Reusable Plastic Tumblers Compare?
Reusable plastic tumblers are an economical alternative, often used for casual settings such as outdoor events or everyday office use. Their cost-effectiveness makes them attractive for businesses on a budget. However, they typically offer moderate durability and might not withstand heavy usage as well as glass or stainless steel tumblers. They are easy to clean and maintain, but their less robust nature may deter some buyers from considering them for high-end events or corporate gifting.
How Can B2B Buyers Choose the Right Tumbler Solution?
Selecting the right tumbler solution hinges on understanding your specific use case and budget constraints. If your business aims to foster high-quality impressions during formal events or corporate gifting, investing in a traditional tumbler manufacturer may be the best route. Conversely, if you’re looking to promote your brand through cost-effective giveaways, custom-branded tumblers could be the ideal choice. For casual use or large gatherings where budget constraints are paramount, reusable plastic tumblers may suffice. Ultimately, evaluating the performance, cost, and intended use will guide you in making an informed decision that aligns with your business objectives.
Essential Technical Properties and Trade Terminology for tumbler manufacturer
What Are the Key Technical Properties of Tumblers for B2B Buyers?
When sourcing tumblers, understanding the essential technical properties is crucial for making informed purchasing decisions. Here are some critical specifications to consider:
1. Material Grade: What Should You Know About Tumbler Materials?
The material grade refers to the quality and type of material used in tumbler production, commonly stainless steel, glass, or BPA-free plastic. Stainless steel offers durability and resistance to corrosion, making it ideal for both hot and cold beverages. Glass provides an elegant presentation but may not withstand rough handling. Choosing the right material impacts both the longevity and usability of the product, which is essential for businesses looking to maintain high standards in their offerings.
2. Tolerance: How Does Tolerance Affect Tumbler Performance?
Tolerance refers to the permissible limits of variation in the dimensions of the tumbler. For example, a tumbler with tight tolerances ensures a snug fit for lids and stacking capabilities, which is vital for storage and transportation. Understanding the tolerance levels can help you assess the quality of the manufacturing process, impacting customer satisfaction and reducing returns.
3. Capacity: Why Is Tumbler Capacity Important?
Capacity indicates the volume of liquid the tumbler can hold, typically measured in ounces or milliliters. For B2B buyers, knowing the capacity is essential for meeting customer demands, especially in hospitality and catering industries. Tumblers come in various sizes, and selecting the appropriate capacity can enhance the user experience and align with market trends.
4. Insulation Properties: What Role Does Insulation Play in Tumblers?
Insulation properties determine how well a tumbler retains temperature, whether hot or cold. Double-walled vacuum insulation is a common feature that enhances thermal efficiency. For businesses, insulated tumblers can be a selling point, especially in regions with extreme temperatures. Understanding insulation helps buyers choose products that meet their customers’ expectations for performance.
5. Finish and Coating: How Do Finishes Impact Tumbler Appeal?
The finish refers to the surface treatment applied to the tumbler, which can include powder coating, polishing, or etching. A quality finish not only enhances aesthetics but also improves grip and resistance to scratches. For B2B buyers, selecting tumblers with appealing finishes can enhance branding opportunities and customer loyalty.
What Are Common Trade Terms in the Tumbler Manufacturing Industry?
Understanding industry terminology is vital for effective communication and negotiation in the B2B landscape. Here are some common terms:
1. OEM (Original Equipment Manufacturer): What Does OEM Mean for Tumblers?
OEM refers to companies that produce components that are used in another company’s end product. In the tumbler industry, an OEM might manufacture tumblers for a brand that sells them under its name. Understanding OEM relationships can help buyers evaluate potential partners and ensure quality control.
2. MOQ (Minimum Order Quantity): Why Is MOQ Important?
MOQ is the smallest quantity of a product that a supplier is willing to sell. This term is crucial for B2B buyers as it affects inventory management and cash flow. Knowing the MOQ helps businesses plan their purchasing strategies and negotiate better terms with suppliers.
3. RFQ (Request for Quotation): How to Use RFQs Effectively?
RFQ is a document sent to suppliers requesting a quote for specific products or services. For tumbler buyers, issuing an RFQ can streamline the procurement process, allowing them to compare prices, lead times, and terms from multiple manufacturers efficiently.
4. Incoterms: What Are Incoterms and Why Do They Matter?
Incoterms are international commercial terms that define the responsibilities of buyers and sellers in shipping and logistics. Understanding Incoterms is essential for B2B buyers to clarify shipping costs, risks, and responsibilities, ensuring smooth international transactions, especially for buyers from Africa, South America, the Middle East, and Europe.
5. Lead Time: How Does Lead Time Affect Your Procurement Strategy?
Lead time refers to the time it takes from placing an order until it is received. This term is vital for planning and inventory management, especially in industries where demand fluctuates. By understanding lead times, buyers can better manage their supply chains and meet customer expectations.
By familiarizing yourself with these technical properties and trade terms, you can make more informed decisions when sourcing tumblers, ensuring your business remains competitive and responsive to market needs.
Navigating Market Dynamics and Sourcing Trends in the tumbler manufacturer Sector
What Are the Current Market Dynamics and Sourcing Trends in the Tumbler Manufacturing Sector?
The tumbler manufacturing sector has experienced significant growth driven by rising consumer demand for versatile drinkware that caters to both personal use and corporate gifting. Key trends include an increasing preference for customized tumblers, particularly among businesses looking to enhance brand visibility. International B2B buyers from Africa, South America, the Middle East, and Europe are actively seeking suppliers who can provide innovative designs, durability, and functional features such as insulation and spill-proof lids.
Emerging technologies in manufacturing, including automation and advanced materials, are revolutionizing production processes. B2B buyers should consider suppliers who leverage these technologies to ensure quality and efficiency. Additionally, there is a growing trend towards online marketplaces that facilitate international sourcing, allowing buyers to compare options, verify suppliers, and streamline procurement processes. Understanding regional preferences is also crucial; for instance, Middle Eastern markets may favor ornate designs, while European consumers often lean towards minimalist aesthetics.
How Is Sustainability Influencing Tumbler Manufacturing and Sourcing?
Sustainability has become a pivotal factor in the tumbler manufacturing industry, influencing purchasing decisions across all markets. As global awareness of environmental issues increases, B2B buyers are prioritizing suppliers who adopt eco-friendly practices. This includes utilizing recyclable materials, reducing waste in production, and minimizing carbon footprints.
Furthermore, the importance of ethical sourcing cannot be overstated. Buyers should look for manufacturers with transparent supply chains that prioritize fair labor practices and community support. Certifications such as FSC (Forest Stewardship Council) for wood-based products, or ISO 14001 for environmental management, serve as indicators of a manufacturer’s commitment to sustainability. By aligning with suppliers who uphold these values, international B2B buyers can not only meet their corporate social responsibility goals but also appeal to environmentally conscious consumers.
What Is the Historical Context of the Tumbler Manufacturing Sector?
The tumbler has evolved significantly over the past few decades, transitioning from a simple drinking vessel to a multifaceted product that serves diverse consumer needs. Initially popularized in the hospitality industry, tumblers have found their way into everyday life, with innovations in materials and design enhancing their appeal.
Historically, tumblers were made primarily from glass and plastic. However, the introduction of stainless steel and insulated models has reshaped the market, allowing for greater functionality and longer-lasting products. This evolution reflects broader trends in consumer preferences towards health, convenience, and sustainability, making the tumbler a staple in both personal and commercial contexts. Understanding this historical backdrop can provide B2B buyers with insights into market evolution and future trends, enabling more informed sourcing decisions.
Frequently Asked Questions (FAQs) for B2B Buyers of tumbler manufacturer
-
How do I choose the right tumbler manufacturer for my business needs?
Selecting the right tumbler manufacturer involves assessing several key factors. First, evaluate their product range to ensure they offer the styles and materials you require. Next, look for manufacturers with a proven track record in quality control and compliance with international standards, especially if you’re sourcing from regions like Africa or South America. Additionally, consider their ability to customize products to meet your branding needs. Finally, check reviews and testimonials from other businesses to gauge their reliability and customer service. -
What are the typical minimum order quantities (MOQs) for tumbler manufacturing?
Minimum order quantities can vary significantly among tumbler manufacturers. Generally, MOQs range from 500 to 5,000 units, depending on the type of tumbler and the manufacturer’s capabilities. For international buyers, it’s essential to discuss MOQs upfront to ensure they align with your business needs. Some manufacturers may offer flexibility for first-time buyers or smaller businesses, but be prepared for potential increased costs per unit if you order below their MOQ. -
What customization options should I consider when sourcing tumblers?
Customization options for tumblers typically include size, color, material, and branding elements like logos and designs. Some manufacturers also offer unique features, such as insulated layers or eco-friendly materials. When discussing customization, clarify your specific needs and ask for samples to evaluate the quality of the customization process. This is particularly important for international buyers looking to differentiate their products in competitive markets. -
How can I ensure quality assurance when sourcing tumblers internationally?
To ensure quality assurance when sourcing tumblers, request certifications that demonstrate compliance with safety and quality standards, such as ISO or FDA certifications. It’s also advisable to conduct pre-shipment inspections through third-party quality control firms to assess product quality before shipment. Establishing a clear communication channel with the manufacturer about your quality expectations will help mitigate any potential issues. -
What payment terms are commonly offered by tumbler manufacturers?
Payment terms can vary widely among tumbler manufacturers, often depending on your negotiation and relationship with the supplier. Common terms include a 30% deposit upfront with the balance due before shipment, or net 30 days after delivery. For international transactions, consider using secure payment methods such as letters of credit or escrow services to protect your investment. Always clarify payment terms in your contract to avoid misunderstandings. -
What logistical considerations should I keep in mind when importing tumblers?
When importing tumblers, consider the logistics of shipping, including freight costs, delivery times, and customs duties. Work with a freight forwarder to navigate the complexities of international shipping and ensure compliance with local regulations. Additionally, factor in the time required for production and potential delays due to customs clearance. Understanding the logistics involved will help you plan better and maintain efficient inventory levels. -
How do I evaluate the reliability of a tumbler supplier?
Evaluating the reliability of a tumbler supplier involves researching their business history, production capacity, and customer reviews. Request references from previous clients and inquire about their experience with order fulfillment and after-sales support. Additionally, check for industry certifications that validate their operational standards. A reliable supplier should also be transparent in communication and responsive to your inquiries throughout the sourcing process. -
What are the trends in tumbler design and materials that I should be aware of?
Current trends in tumbler design include eco-friendly materials, such as bamboo and recycled plastics, catering to the growing consumer demand for sustainable products. Insulated tumblers that maintain beverage temperature are also increasingly popular. Additionally, unique designs that allow for personalization or multifunctionality, like built-in straws or lids, are gaining traction. Staying informed about these trends will help you select products that resonate with your target market.
Important Disclaimer & Terms of Use
⚠️ Important Disclaimer
The information provided in this guide, including content regarding manufacturers, technical specifications, and market analysis, is for informational and educational purposes only. It does not constitute professional procurement advice, financial advice, or legal advice.
While we have made every effort to ensure the accuracy and timeliness of the information, we are not responsible for any errors, omissions, or outdated information. Market conditions, company details, and technical standards are subject to change.
B2B buyers must conduct their own independent and thorough due diligence before making any purchasing decisions. This includes contacting suppliers directly, verifying certifications, requesting samples, and seeking professional consultation. The risk of relying on any information in this guide is borne solely by the reader.
Strategic Sourcing Conclusion and Outlook for tumbler manufacturer
What Are the Key Takeaways for B2B Buyers in Tumbler Manufacturing?
In summary, strategic sourcing for tumbler manufacturing is essential for B2B buyers looking to enhance their supply chain efficiency and product quality. By prioritizing partnerships with reliable manufacturers, buyers can secure high-quality tumblers that meet diverse market demands. Understanding local regulations and cultural preferences is also vital, particularly for international buyers from Africa, South America, the Middle East, and Europe.
How Can Strategic Sourcing Enhance Your Competitive Edge?
Effective strategic sourcing not only reduces costs but also fosters innovation and sustainability within your product offerings. As consumers increasingly seek eco-friendly options, aligning with manufacturers who prioritize sustainable practices can significantly enhance your brand’s reputation and appeal in competitive markets.
What Is the Future Outlook for International B2B Buyers?
Looking ahead, the tumbler market is poised for growth, driven by rising demand across various sectors, including hospitality and retail. International B2B buyers should actively engage with manufacturers to explore customized solutions that cater to their unique needs. By leveraging strategic sourcing, businesses can position themselves to capitalize on emerging trends and consumer preferences.
Take the next step in your sourcing journey by evaluating your current partnerships and exploring new opportunities within the tumbler manufacturing landscape. The time to act is now—secure your place in this evolving market!