Discover Top Wall Cladding Suppliers: Your Complete Guide (2025)
Introduction: Navigating the Global Market for wall cladding supplier
Navigating the complexities of sourcing wall cladding suppliers can be a daunting task for international B2B buyers, especially those operating in diverse markets like Africa, South America, the Middle East, and Europe. As the demand for innovative and sustainable building materials continues to rise, understanding how to effectively identify and collaborate with reliable wall cladding suppliers becomes critical. This guide aims to equip you with the knowledge necessary to make informed purchasing decisions, covering a broad spectrum of wall cladding options, their applications in various industries, and the essential criteria for supplier vetting.
The wall cladding market is multifaceted, with various materials such as wood, metal, vinyl, and stone available, each serving distinct purposes in construction and design. This comprehensive resource will delve into the nuances of each type, helping you identify the right cladding solutions for your projects. Additionally, we will explore the cost implications of different materials and suppliers, providing insights into budgeting and procurement strategies.
By the end of this guide, you will be empowered to navigate the global market more effectively, armed with actionable insights and best practices. Whether you are a construction firm in Brazil looking for sustainable options or a developer in the Middle East seeking innovative designs, this guide will serve as your roadmap to successful supplier partnerships and enhanced project outcomes.
Understanding wall cladding supplier Types and Variations
Type Name | Key Distinguishing Features | Primary B2B Applications | Brief Pros & Cons for Buyers |
---|---|---|---|
Natural Stone Cladding | Made from granite, marble, or slate; offers unique aesthetics | High-end residential and commercial projects | Pros: Durability, aesthetic appeal. Cons: High cost, requires skilled installation. |
Metal Cladding | Composed of aluminum, steel, or copper; often pre-finished | Industrial buildings, warehouses, facades | Pros: Lightweight, low maintenance. Cons: Can dent, thermal expansion issues. |
Vinyl Cladding | Made from PVC; available in various colors and textures | Affordable residential construction | Pros: Cost-effective, easy installation. Cons: Less durable, can fade over time. |
Fiber Cement Cladding | Mixture of cement, sand, and cellulose; mimics wood or stone | Commercial buildings, multifamily homes | Pros: Fire-resistant, low maintenance. Cons: Heavier than other options, installation can be complex. |
Wood Cladding | Natural wood boards; offers warmth and character | Eco-friendly projects, luxury homes | Pros: Aesthetic warmth, sustainable options. Cons: Requires maintenance, susceptible to pests. |
What are the Characteristics of Natural Stone Cladding?
Natural stone cladding is renowned for its unique aesthetic appeal, making it a popular choice for high-end residential and commercial projects. This type of cladding utilizes materials like granite, marble, and slate, each offering distinct textures and colors. B2B buyers should consider the sourcing and availability of these materials, as well as the installation requirements, which often necessitate skilled labor. While natural stone is exceptionally durable and visually striking, the costs can be significant, making it essential for buyers to weigh the investment against the desired aesthetic and longevity.
How Does Metal Cladding Stand Out in B2B Applications?
Metal cladding, typically composed of aluminum, steel, or copper, is favored for its lightweight nature and modern appearance. It is commonly used in industrial buildings, warehouses, and facades, where durability and low maintenance are key concerns. B2B buyers should consider the specific metal type, as each has unique properties, such as corrosion resistance and thermal expansion characteristics. While metal cladding can offer long-term savings due to its minimal upkeep, potential issues like denting and thermal expansion should be factored into purchasing decisions.
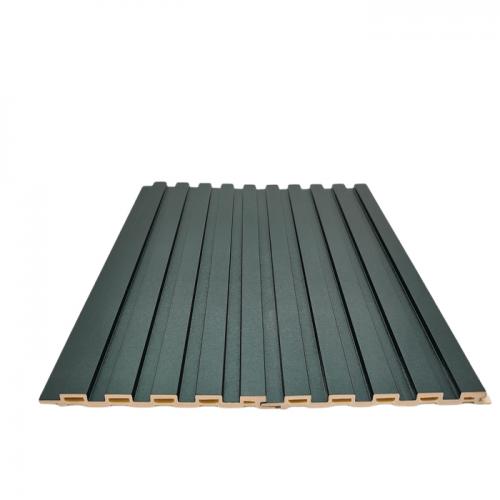
A stock image related to wall cladding supplier.
What Makes Vinyl Cladding a Popular Choice for B2B Buyers?
Vinyl cladding, made from PVC, is an attractive option for budget-conscious projects, particularly in residential construction. Its affordability and ease of installation make it appealing for contractors and builders looking to streamline costs. However, B2B buyers must be aware that while vinyl can mimic the appearance of wood or stone, it may not offer the same durability, and color fading can occur over time. Understanding the long-term performance and warranty options is crucial for making an informed purchasing decision.
Why is Fiber Cement Cladding Gaining Popularity?
Fiber cement cladding is a composite material made from cement, sand, and cellulose, designed to mimic wood or stone. Its fire-resistant properties and low maintenance requirements make it a strong contender for commercial buildings and multifamily homes. B2B buyers should consider the installation complexity, as fiber cement can be heavier than other options, requiring careful handling and skilled labor. While it offers durability and aesthetic versatility, the initial investment can be higher, necessitating a thorough cost-benefit analysis.
What are the Benefits and Drawbacks of Wood Cladding?
Wood cladding provides a natural and warm aesthetic that appeals to eco-conscious projects and luxury homes. It is available in various types, allowing for customization based on the desired look. However, B2B buyers must factor in maintenance requirements, as wood is susceptible to pests and weathering. Sustainable sourcing is also a consideration, as the demand for eco-friendly materials grows. While wood cladding can enhance a building’s character, the ongoing maintenance and potential for degradation should be carefully evaluated against the project’s long-term goals.
Related Video: Wall Cladding Types and Prices In The Philippines.
Key Industrial Applications of wall cladding supplier
Industry/Sector | Specific Application of Wall Cladding Supplier | Value/Benefit for the Business | Key Sourcing Considerations for this Application |
---|---|---|---|
Construction | Exterior wall cladding for commercial buildings | Enhances aesthetic appeal, provides insulation and weather resistance | Compliance with local building codes and environmental standards |
Food and Beverage | Hygienic wall cladding in food processing facilities | Easy to clean, resistant to bacteria, meets health regulations | Certification for food safety standards and ease of maintenance |
Healthcare | Wall cladding in hospitals and clinics | Improves hygiene, durability, and aesthetics, reduces noise | Antimicrobial properties and compliance with health regulations |
Retail | Interior wall cladding for retail spaces | Creates an inviting atmosphere, enhances brand image | Customization options and durability for high-traffic areas |
Transportation | Wall cladding for transportation hubs | Provides safety, weather protection, and visual appeal | Lightweight materials and resistance to environmental factors |
How is Wall Cladding Used in the Construction Industry?
In the construction sector, wall cladding serves as an exterior finish for commercial buildings, providing both aesthetic appeal and functional benefits. It acts as a protective layer against weather elements, enhancing the building’s energy efficiency. For international B2B buyers, especially in Africa and South America, sourcing durable materials that comply with local building codes is crucial. The choice of cladding can significantly affect construction timelines and costs, making it essential to collaborate with suppliers who understand regional regulations and climate challenges.
What are the Applications of Wall Cladding in the Food and Beverage Sector?
Wall cladding is critical in food processing facilities, where hygiene is paramount. Suppliers offer materials that are easy to clean, non-porous, and resistant to bacteria, helping businesses comply with health regulations. For buyers in regions like the Middle East and Europe, it’s vital to choose cladding that meets specific food safety certifications. Additionally, the ability to maintain a clean environment can significantly reduce operational risks and enhance product safety, making the right cladding choice a strategic investment.
How Does Wall Cladding Benefit Healthcare Facilities?
In healthcare settings, wall cladding is utilized to create hygienic, durable, and aesthetically pleasing environments. Materials with antimicrobial properties are preferred, as they help reduce the spread of infections. B2B buyers from Europe and Africa should consider suppliers who can provide cladding that meets stringent health regulations and offers soundproofing benefits. Investing in high-quality wall cladding not only improves patient comfort but also contributes to the overall efficiency of healthcare operations.
Why is Wall Cladding Important for Retail Spaces?
Retail environments benefit greatly from attractive interior wall cladding that enhances the shopping experience. Cladding can be customized to reflect brand identity, creating an inviting atmosphere for customers. For B2B buyers in South America and Europe, sourcing durable materials that withstand high foot traffic is essential. Suppliers should offer a range of design options while ensuring that the cladding is easy to maintain, allowing businesses to focus on customer engagement rather than upkeep.
What Role Does Wall Cladding Play in Transportation Hubs?
Wall cladding in transportation hubs, such as airports and bus stations, provides safety and weather protection while contributing to the aesthetic appeal of the space. Lightweight materials that are resistant to environmental factors are crucial for these applications. International buyers, particularly from Africa and the Middle East, should prioritize sourcing cladding that meets safety standards and is designed for high-traffic areas. Effective cladding solutions can significantly enhance the user experience and operational efficiency of transportation facilities.
Related Video: WPC Wall Cladding Installation – How to Install Composite Cladding – Tutorial by Intco Decor
3 Common User Pain Points for ‘wall cladding supplier’ & Their Solutions
Scenario 1: Delays in Delivery and Supply Chain Issues
The Problem: One of the most pressing challenges for B2B buyers of wall cladding materials is the unpredictability of supply chains. Buyers often find themselves facing delays in delivery, which can halt construction projects and lead to significant financial losses. For instance, a construction company in Brazil may order wall cladding from a supplier in Europe, only to discover that shipping delays have pushed back their timeline, affecting contracts and client trust.
The Solution: To mitigate supply chain issues, buyers should engage in thorough supplier vetting before placing orders. This includes evaluating the supplier’s logistics capabilities, reviewing their track record for on-time delivery, and understanding their inventory management systems. Establishing clear communication channels with suppliers can also help buyers receive timely updates on order status. Furthermore, considering suppliers with local distribution centers can reduce lead times and provide backup options in case of unforeseen delays. Investing in technology that tracks shipments in real time can also provide buyers with greater visibility and control over their orders.
Scenario 2: Quality Assurance and Material Performance Concerns
The Problem: B2B buyers often grapple with the challenge of ensuring that wall cladding materials meet the required quality standards and perform well in various environmental conditions. For example, a buyer in the Middle East might need cladding that withstands extreme heat and humidity, but they may be uncertain about the performance of materials sourced from different regions.
The Solution: To address quality assurance concerns, buyers should request detailed specifications and certifications from potential suppliers. This includes asking for performance data, warranty information, and third-party testing results. Additionally, establishing a close relationship with suppliers can facilitate better communication regarding material properties and suitability for specific climates. Buyers should also consider conducting site visits to supplier facilities when possible to assess quality control processes firsthand. Collaborating with architects and engineers to ensure that material choices align with local building codes and climate considerations is another effective strategy.
Scenario 3: Navigating Regulatory Compliance and Standards
The Problem: International buyers often face the challenge of navigating different regulatory frameworks and building codes across regions. For instance, a construction firm in South America may struggle to understand the European Union’s stringent safety and environmental standards when sourcing wall cladding materials for a project in their home country.
The Solution: To effectively navigate regulatory compliance, buyers should invest time in understanding the specific regulations that apply to their projects. This can involve consulting with local building authorities or legal experts familiar with international trade and compliance. Buyers should also seek out suppliers who demonstrate a robust understanding of these regulations and can provide guidance on compliance requirements. Engaging in continuous education—such as attending industry seminars or webinars—can also equip buyers with the knowledge they need to stay updated on regulatory changes. Additionally, creating a checklist of compliance requirements tailored to each project can streamline the sourcing process and ensure all standards are met before procurement.
Strategic Material Selection Guide for wall cladding supplier
When selecting materials for wall cladding, international B2B buyers must consider various factors that impact performance, cost, and suitability for specific applications. Below, we analyze four common materials used in wall cladding, focusing on their key properties, advantages, disadvantages, and specific considerations for buyers from Africa, South America, the Middle East, and Europe.
What Are the Key Properties of Metal Wall Cladding?
Metal wall cladding, typically made from aluminum or steel, is known for its strength and durability. It boasts high corrosion resistance, making it suitable for environments with high humidity or exposure to chemicals. Metal cladding can withstand significant temperature fluctuations, which is crucial for regions experiencing extreme weather conditions.
Pros & Cons:
Metal cladding is highly durable and requires minimal maintenance, making it a cost-effective long-term solution. However, its initial cost can be high, and it may require complex manufacturing processes, which can lead to longer lead times. Additionally, metal can conduct heat, which may not be suitable for all climates.
Impact on Application:
Metal cladding is ideal for commercial buildings and industrial applications where durability and aesthetics are paramount. However, buyers must ensure compatibility with local building codes and standards, such as ASTM in the U.S. or EN in Europe.
What Are the Advantages of Fiber Cement Wall Cladding?
Fiber cement wall cladding is composed of cement, sand, and cellulose fibers, providing a robust and versatile option. It is highly resistant to fire, rot, and pests, making it a popular choice in various climates.
Pros & Cons:
The key advantage of fiber cement is its durability and resistance to environmental factors. It can mimic the appearance of wood or stone while being more affordable and easier to maintain. On the downside, it can be heavier than other materials, which may require additional structural support during installation.
Impact on Application:
Fiber cement is suitable for residential and commercial buildings, especially in regions prone to severe weather. Buyers should look for compliance with local standards, such as EN 12467 in Europe, to ensure quality and safety.
How Does Vinyl Wall Cladding Compare?
Vinyl wall cladding is a lightweight, cost-effective option made from polyvinyl chloride (PVC). It is known for its excellent weather resistance and low maintenance requirements.
Pros & Cons:
Vinyl is available in various colors and styles, making it a versatile choice for aesthetic applications. Its affordability is a significant advantage; however, it may not offer the same level of durability as metal or fiber cement. Additionally, vinyl can be susceptible to fading and cracking over time, particularly in extreme temperatures.
Impact on Application:
Vinyl cladding is commonly used in residential applications and light commercial projects. Buyers should consider regional preferences and compliance with standards such as ASTM D3679, particularly in areas with strict building codes.
What Are the Unique Features of Natural Stone Wall Cladding?
Natural stone wall cladding, such as granite or limestone, offers a timeless aesthetic and exceptional durability. Its unique properties include high resistance to heat and moisture, making it suitable for various climates.
Pros & Cons:
The primary advantage of natural stone is its aesthetic appeal and longevity. However, it is one of the most expensive options and can be challenging to install due to its weight. Additionally, natural stone requires sealing to prevent staining and water damage.
Impact on Application:
Natural stone is ideal for high-end residential and commercial projects. Buyers should ensure that the stone meets local standards and regulations, as well as consider the environmental impact of sourcing and transporting the material.
Summary Table of Material Selection for Wall Cladding
Material | Typical Use Case for wall cladding supplier | Key Advantage | Key Disadvantage/Limitation | Relative Cost (Low/Med/High) |
---|---|---|---|---|
Metal | Commercial buildings, industrial applications | High durability and low maintenance | High initial cost and complex manufacturing | High |
Fiber Cement | Residential and commercial buildings | Fire and pest resistant | Heavier, may require structural support | Medium |
Vinyl | Residential and light commercial projects | Cost-effective and versatile | Less durable, susceptible to fading | Low |
Natural Stone | High-end residential and commercial projects | Aesthetic appeal and longevity | High cost and installation complexity | High |
By understanding the properties, advantages, and limitations of these materials, international B2B buyers can make informed decisions that align with their project requirements and regional standards.
In-depth Look: Manufacturing Processes and Quality Assurance for wall cladding supplier
What Are the Main Stages of Manufacturing Wall Cladding?
The manufacturing of wall cladding involves several crucial stages, each designed to ensure the final product meets both aesthetic and functional requirements. Understanding these stages can help B2B buyers evaluate suppliers more effectively.
-
Material Preparation
This initial stage involves sourcing high-quality raw materials, which can include natural stones, metals, or composites. Suppliers often conduct rigorous quality checks on incoming materials to ensure they meet specified standards. This step is critical, as the quality of the raw materials directly impacts the durability and performance of the cladding. -
Forming
The forming process typically involves cutting, shaping, and molding the raw materials into the desired dimensions. Techniques such as extrusion, casting, or CNC machining are commonly employed. For instance, in the case of metal cladding, extrusion is a popular method that allows for uniform shapes and sizes. B2B buyers should inquire about the specific techniques used, as these can affect both the quality and cost of the final product. -
Assembly
In this stage, the various components of wall cladding are assembled. This may include attaching insulation layers or additional protective coatings. Automated assembly lines can enhance precision and reduce labor costs, but manual assembly might be used for more intricate designs. Buyers should assess whether the supplier has the capability to customize assembly processes to meet specific project requirements. -
Finishing
The finishing process is vital for both aesthetics and functionality. This includes surface treatments like painting, coating, or sealing to enhance durability and appearance. Advanced techniques, such as powder coating or anodizing for metals, can provide superior resistance to environmental factors. B2B buyers should verify that suppliers offer finishing options that align with their project needs and regional climatic conditions.
How Is Quality Assurance Implemented in Wall Cladding Manufacturing?
Quality assurance (QA) is essential in the manufacturing process of wall cladding to ensure that products meet international standards and client specifications. Here are some critical aspects to consider:
-
What International Standards Should Buyers Look For?
International standards such as ISO 9001 are fundamental for ensuring consistent quality management practices. ISO 9001 certification indicates that a supplier has established and maintains an effective quality management system. Additionally, industry-specific certifications like CE marking in Europe or API standards for petrochemical applications can serve as indicators of quality. B2B buyers should prioritize suppliers who adhere to these standards, as they can significantly reduce risks associated with product failure. -
What Are the Key Quality Control Checkpoints?
Effective quality control (QC) involves several checkpoints throughout the manufacturing process:
– Incoming Quality Control (IQC): This stage assesses the quality of raw materials before production begins.
– In-Process Quality Control (IPQC): Conducted during manufacturing, this ensures that processes are being followed correctly and that products are meeting quality standards.
– Final Quality Control (FQC): This final check examines the completed products for defects before they are shipped. Each stage is critical for minimizing errors and maintaining product integrity. -
Which Testing Methods Are Commonly Used?
Various testing methods are employed to evaluate the quality of wall cladding, including:
– Visual Inspection: A primary method for assessing surface defects and finish quality.
– Mechanical Testing: This may involve tensile strength, impact resistance, and adhesion tests to determine the material’s performance under stress.
– Environmental Testing: Such as resistance to UV exposure, moisture, and temperature fluctuations, which is particularly important for outdoor applications.
How Can B2B Buyers Verify Supplier Quality Control?
Verifying a supplier’s quality control processes is crucial for B2B buyers to ensure they are partnering with reliable manufacturers. Here are actionable steps to undertake:
-
Conduct Supplier Audits
Regular audits allow buyers to assess suppliers’ facilities, processes, and adherence to quality standards firsthand. During an audit, buyers should evaluate the documentation of quality procedures, training of staff, and maintenance of equipment. This proactive approach can reveal potential issues before they become significant problems. -
Request Quality Reports
Suppliers should provide detailed quality reports, including testing results and compliance with relevant standards. B2B buyers can use these documents to verify that the supplier is meeting its stated quality commitments. Look for consistency in reporting and any trends that might indicate potential quality issues. -
Engage Third-Party Inspectors
Utilizing third-party inspection services can provide an unbiased evaluation of a supplier’s quality practices. These inspectors can conduct thorough assessments and provide certification, ensuring that products meet both international and local standards. This step is particularly important for buyers in regions like Africa and South America, where local regulations may differ significantly from international norms.
What Are the Quality Control Nuances for International Buyers?
International B2B buyers must navigate several nuances in quality control that can vary significantly across regions:
-
Understanding Regional Standards
Buyers should familiarize themselves with local building codes and standards in their respective markets, whether in Europe, Africa, the Middle East, or South America. For instance, European standards might require CE certification, while other regions may prioritize different compliance measures. This knowledge is crucial for ensuring that products are not only high quality but also legally compliant. -
Cultural and Communication Considerations
Effective communication with suppliers is vital. Language barriers and cultural differences can affect the understanding of quality requirements. Buyers should ensure that specifications are clearly communicated and that there is a mutual understanding of quality expectations. -
Logistical Challenges and Their Impact on Quality
International shipping can introduce risks such as damage during transit. Buyers must discuss with suppliers how they manage these risks and what quality assurance measures are in place to protect products during shipping and handling. This aspect is especially pertinent for buyers in remote locations where logistics can be complex.
By understanding the manufacturing processes and quality assurance practices in wall cladding production, international B2B buyers can make informed decisions that align with their project requirements and standards.
Practical Sourcing Guide: A Step-by-Step Checklist for ‘wall cladding supplier’
The process of sourcing wall cladding suppliers can be complex, especially for international B2B buyers. This checklist provides a structured approach to ensure you make informed decisions when selecting suppliers that meet your project’s needs.
Step 1: Define Your Technical Specifications
Before initiating contact with suppliers, clearly outline the specifications of the wall cladding you require. This includes materials, dimensions, finishes, and any industry standards that must be adhered to. Having precise specifications helps in obtaining accurate quotes and ensures that the products meet your project requirements.
Step 2: Conduct Market Research on Suppliers
Research potential suppliers in regions like Africa, South America, the Middle East, and Europe. Utilize online platforms, trade directories, and industry associations to compile a list of candidates. Pay attention to supplier reputation, customer reviews, and their presence in your target market, as this can significantly influence reliability and product quality.
Step 3: Evaluate Potential Suppliers
Before committing, it’s crucial to vet suppliers thoroughly. Request company profiles, case studies, and references from buyers in a similar industry or region. Look for suppliers with a proven track record and relevant experience in wall cladding projects similar to yours.
- Check for Industry Experience: Ensure the supplier has experience in your specific type of project, whether it be commercial, residential, or industrial.
- Request Samples: Ask for product samples to assess quality and finish before making a larger commitment.
Step 4: Verify Supplier Certifications and Compliance
Ensure that your chosen suppliers possess the necessary certifications and comply with local and international regulations regarding wall cladding. This includes quality certifications, environmental standards, and safety compliance.
- International Standards: Check if the supplier meets standards such as ISO, CE marking, or local certifications specific to your region.
- Sustainability Practices: Investigate the supplier’s commitment to sustainable practices, as this is increasingly important in global sourcing.
Step 5: Assess Pricing and Payment Terms
Once you’ve narrowed down your options, compare pricing structures and payment terms. Understand what is included in the quoted price, such as shipping, taxes, and any additional fees.
- Negotiate Terms: Don’t hesitate to negotiate payment terms, especially for larger orders. Consider options like payment upon delivery or financing arrangements.
- Review Total Cost of Ownership: Evaluate the long-term costs, including installation and maintenance, rather than just the upfront price.
Step 6: Establish Communication Protocols
Effective communication is vital throughout the sourcing process. Set clear expectations regarding timelines, updates, and points of contact.
- Regular Check-ins: Schedule regular updates to discuss project progress and any potential issues that may arise.
- Language Considerations: Ensure that you can communicate effectively in the supplier’s primary language or have access to translation services if necessary.
Step 7: Finalize Contracts and Agreements
Once you have selected a supplier, finalize the contract ensuring all terms are clear and agreed upon. This should include delivery timelines, payment terms, and warranty information.
- Legal Review: Consider having a legal professional review the contract to ensure compliance with local laws and protection of your interests.
- Contingency Plans: Establish clauses for potential delays or quality issues to safeguard your project timeline.
By following this step-by-step checklist, international B2B buyers can effectively navigate the sourcing process for wall cladding suppliers, ensuring they select reliable partners that meet their project needs.
Comprehensive Cost and Pricing Analysis for wall cladding supplier Sourcing
What Are the Key Cost Components in Wall Cladding Supplier Sourcing?
When sourcing wall cladding, understanding the cost structure is crucial for making informed purchasing decisions. The primary cost components include:
-
Materials: The choice of materials significantly impacts the overall cost. Common materials for wall cladding include wood, metal, vinyl, and composite materials. Each material has its own price range influenced by quality and availability.
-
Labor: Labor costs can vary based on the region and the complexity of the installation process. Skilled labor may demand higher wages, particularly in regions where such expertise is scarce.
-
Manufacturing Overhead: This encompasses the indirect costs associated with production, such as utilities, rent, and equipment maintenance. Suppliers in regions with lower operational costs may offer more competitive pricing.
-
Tooling: Initial tooling costs for customized designs can be significant. Understanding the tooling requirements can help buyers gauge whether a supplier can meet their specifications without incurring excessive costs.
-
Quality Control (QC): Implementing rigorous quality control measures ensures that the cladding meets industry standards. Suppliers with strong QC processes may charge a premium, but this can lead to cost savings in the long run by reducing returns and replacements.
-
Logistics: Transportation costs can vary widely based on the distance from the supplier to the buyer. International shipping, particularly to regions like Africa or South America, may incur additional tariffs or duties that impact the final price.
-
Margin: Suppliers will typically include a markup to cover their operating expenses and profit. Understanding the margin structure can help buyers negotiate better terms.
How Do Price Influencers Affect Wall Cladding Procurement?
Several factors can influence the pricing of wall cladding, which B2B buyers should consider:
-
Volume and Minimum Order Quantity (MOQ): Larger orders often come with discounts. Buyers should assess their needs carefully to determine the optimal order size that balances cost with inventory management.
-
Specifications and Customization: Customized products generally incur higher costs. Buyers need to clearly communicate their requirements to avoid unexpected expenses.
-
Materials and Quality Certifications: Higher-quality materials and certifications (like ISO or CE marking) can increase costs. However, they may also provide assurance of durability and performance, which is essential for long-term projects.
-
Supplier Factors: The reputation and reliability of suppliers can affect pricing. Established suppliers may charge more due to their proven track record, while newer suppliers might offer competitive rates to build their client base.
-
Incoterms: Understanding Incoterms (International Commercial Terms) is vital for international transactions. They define who is responsible for shipping, insurance, and tariffs, which can significantly influence total costs.
What Buyer Tips Can Enhance Cost-Efficiency in Wall Cladding Sourcing?
To maximize cost-efficiency when sourcing wall cladding, consider the following actionable tips:
-
Negotiate Effectively: Leverage volume purchases or long-term contracts to negotiate better pricing. Be prepared to discuss your requirements and the potential for future business.
-
Evaluate Total Cost of Ownership (TCO): Look beyond the initial purchase price. Consider installation, maintenance, and potential replacement costs when evaluating suppliers.
-
Research Pricing Nuances: Understand regional pricing trends and economic conditions in your target markets (e.g., Africa, South America, Middle East, and Europe). This knowledge can inform negotiations and help you identify the best suppliers.
-
Request Detailed Quotes: Ensure that quotes include a breakdown of all costs to facilitate easier comparisons. This transparency can help identify areas where savings can be achieved.
-
Stay Informed on Market Trends: Regularly review market conditions, material availability, and supplier performance. This will enable you to make timely decisions that can lead to cost savings.
Disclaimer on Indicative Prices
Prices for wall cladding can fluctuate based on a variety of factors, including market conditions, material availability, and supplier capabilities. It is essential to conduct thorough research and engage with multiple suppliers to obtain the most accurate and current pricing information tailored to your specific needs.
Alternatives Analysis: Comparing wall cladding supplier With Other Solutions
When considering the procurement of wall cladding solutions, it’s essential for B2B buyers to evaluate not just wall cladding suppliers but also alternative solutions that may meet their specific project needs. This comparison allows international buyers, especially from regions such as Africa, South America, the Middle East, and Europe, to make informed decisions regarding the best material or method for their construction projects.
Comparison Table of Wall Cladding Supplier and Alternatives
Comparison Aspect | Wall Cladding Supplier | Prefabricated Panels | Insulated Concrete Forms (ICFs) |
---|---|---|---|
Performance | High durability and aesthetics | Good insulation and design flexibility | Excellent thermal performance and strength |
Cost | Moderate to high | Variable, often lower than traditional methods | Generally higher upfront costs but long-term savings |
Ease of Implementation | Requires skilled labor | Faster installation with minimal labor | Complex setup requiring skilled labor |
Maintenance | Low maintenance required | Moderate maintenance, depending on material | Very low maintenance due to durability |
Best Use Case | Commercial and residential buildings | Quick build projects, commercial use | Energy-efficient buildings, residential homes |
What Are the Pros and Cons of Prefabricated Panels?
Prefabricated panels are a popular alternative to traditional wall cladding. They offer a range of design options and can be customized to suit specific aesthetic requirements. One of the main advantages of prefabricated panels is their speed of installation, significantly reducing labor costs and project timelines. However, the quality of materials can vary, and buyers must ensure they select panels that meet local building codes and standards. Additionally, while initial costs may be lower, ongoing maintenance can add up depending on the material used.
How Do Insulated Concrete Forms (ICFs) Compare?
Insulated Concrete Forms (ICFs) provide an innovative approach to wall construction. They consist of expanded polystyrene (EPS) foam panels that are filled with concrete, creating a highly insulated and durable wall structure. The main benefits of ICFs include excellent thermal performance and sound insulation, making them ideal for energy-efficient buildings. However, the initial cost is typically higher than that of wall cladding suppliers, and the installation process can be more complex, requiring specialized knowledge and labor. This makes ICFs best suited for long-term projects where energy efficiency is a primary concern.
How Can B2B Buyers Choose the Right Solution for Their Needs?
Selecting the right wall cladding solution involves assessing various factors including project requirements, budget constraints, and long-term goals. B2B buyers should consider the specific performance needs of their project, such as insulation, durability, and aesthetics. Cost considerations should also include both initial investment and long-term maintenance. Finally, ease of implementation and the availability of skilled labor in the region can significantly influence the decision-making process. By carefully weighing these aspects, buyers can ensure they choose the solution that best aligns with their operational goals and project specifications.
Essential Technical Properties and Trade Terminology for wall cladding supplier
When engaging with wall cladding suppliers, understanding the essential technical properties and trade terminology is crucial for making informed purchasing decisions. This section outlines key specifications and jargon that will help international B2B buyers navigate the complexities of wall cladding procurement.
What are the Key Technical Properties of Wall Cladding?
1. Material Grade
Material grade refers to the classification of the wall cladding material based on its physical and chemical properties. Common materials include metal, vinyl, wood, and composite. Understanding the grade is important as it directly impacts durability, aesthetic appeal, and suitability for specific environments, such as coastal areas or regions with extreme weather. Buyers should assess how the material grade aligns with their project requirements, particularly in terms of longevity and maintenance.
2. Tolerance
Tolerance indicates the permissible limit of variation in the dimensions of the wall cladding components. This specification is critical for ensuring that panels fit together correctly during installation. For B2B buyers, tight tolerances can reduce the likelihood of installation errors and material waste, thereby lowering overall project costs. It’s essential to communicate specific tolerance requirements to suppliers to avoid issues during the construction phase.
3. Thermal Resistance (R-Value)
The R-value measures a material’s ability to resist heat flow, providing insights into its insulation properties. High thermal resistance is vital for energy efficiency, particularly in climates with extreme temperatures. B2B buyers should consider the R-value of wall cladding materials to enhance energy performance in buildings, which can lead to significant cost savings over time.
4. Fire Rating
Fire rating defines how well a material can withstand fire exposure and is often categorized into classes (e.g., Class A, B, or C). In many regions, building codes require specific fire ratings for wall cladding materials to ensure safety. B2B buyers must verify that the cladding products meet local regulations and standards, especially in commercial projects where safety is paramount.
5. Weather Resistance
Weather resistance refers to a material’s ability to withstand environmental factors such as moisture, UV radiation, and temperature fluctuations. This property is particularly relevant for outdoor applications in diverse climates. Buyers should inquire about weather resistance ratings to ensure long-lasting performance and minimal maintenance needs.
Which Trade Terms Should B2B Buyers Understand?
1. OEM (Original Equipment Manufacturer)
An OEM is a company that produces parts or equipment that may be marketed by another manufacturer. In the context of wall cladding, buyers might work with OEMs to procure customized solutions that meet specific design or performance criteria. Understanding this term helps buyers identify potential suppliers that can offer tailored products.
2. MOQ (Minimum Order Quantity)
MOQ refers to the smallest quantity of a product that a supplier is willing to sell. This term is crucial for budgeting and inventory management. B2B buyers need to clarify MOQs with suppliers to ensure they can meet their project demands without overcommitting resources.
3. RFQ (Request for Quotation)
An RFQ is a document that solicits price proposals from suppliers for specific goods or services. B2B buyers should prepare a comprehensive RFQ that includes technical specifications and quantities to receive accurate and competitive pricing. This process is essential for effective cost comparison and supplier selection.
4. Incoterms (International Commercial Terms)
Incoterms are a set of predefined international trade terms that clarify the responsibilities of buyers and sellers regarding shipping, insurance, and tariffs. Familiarity with Incoterms, such as FOB (Free on Board) and CIF (Cost, Insurance, and Freight), can help buyers negotiate better shipping terms and understand their liabilities in international transactions.
5. Lead Time
Lead time refers to the time taken from placing an order to delivery. It is vital for project planning and scheduling. Buyers should always inquire about lead times during negotiations to ensure that their projects remain on schedule, particularly in regions where delays can significantly impact timelines.
By understanding these essential technical properties and trade terminology, international B2B buyers can make informed decisions and foster successful partnerships with wall cladding suppliers.
Navigating Market Dynamics and Sourcing Trends in the wall cladding supplier Sector
What Are the Key Market Dynamics Influencing Wall Cladding Suppliers?
The wall cladding supplier sector is experiencing transformative changes driven by various global factors. Key trends include an increasing demand for aesthetic building solutions that enhance energy efficiency and sustainability. As urbanization accelerates in regions like Africa, South America, and the Middle East, international B2B buyers are looking for innovative cladding solutions that not only meet functional requirements but also contribute to a building’s visual appeal. In Europe, the market is heavily influenced by stringent building regulations focused on energy conservation and environmental impact, which compel suppliers to adopt advanced technologies and sustainable practices.
Emerging B2B technologies such as Building Information Modeling (BIM) and digital procurement platforms are reshaping how buyers engage with suppliers. These tools facilitate more informed decision-making and streamline sourcing processes, allowing international buyers to assess supplier capabilities and product offerings with greater precision. Additionally, the rise of e-commerce in the construction sector is enabling suppliers to reach new markets directly, making it essential for buyers to stay updated on the latest digital tools and platforms.
How Does Sustainability Impact Sourcing Trends for Wall Cladding Suppliers?
Sustainability has become a cornerstone of the wall cladding supply chain, influencing sourcing strategies for international B2B buyers. The environmental impact of building materials is under scrutiny, with a growing emphasis on reducing carbon footprints and promoting circular economy practices. Buyers are increasingly prioritizing suppliers that offer eco-friendly materials, such as recycled or sustainably sourced products, as well as those with certifications like LEED, BREEAM, or FSC (Forest Stewardship Council).
Ethical sourcing practices are also gaining traction, as buyers seek to ensure that their supply chains are transparent and socially responsible. This involves vetting suppliers for compliance with environmental regulations and labor standards. As a result, international buyers from regions like Africa and South America may need to adapt their sourcing strategies to align with these emerging standards, ensuring that they not only meet regulatory requirements but also respond to consumer demand for greener building solutions.
What Is the Evolution of the Wall Cladding Supplier Sector?
The evolution of the wall cladding supplier sector can be traced back to the industrial revolution, which marked the beginning of mass production techniques in construction materials. Over the decades, innovations in material science have led to the development of various cladding materials, including metal, vinyl, and composite options. The late 20th century saw a significant shift towards sustainability, spurred by the global environmental movement, prompting suppliers to explore alternative materials and production methods.
In recent years, the introduction of advanced manufacturing technologies, such as 3D printing and smart materials, has further transformed the landscape. This evolution is particularly relevant for B2B buyers, as it opens up new avenues for sourcing unique and customized wall cladding solutions that meet both aesthetic and functional requirements. Understanding this historical context is essential for buyers aiming to navigate the current market dynamics effectively.
Frequently Asked Questions (FAQs) for B2B Buyers of wall cladding supplier
-
How do I choose the right wall cladding supplier for my business needs?
Choosing the right wall cladding supplier involves several key factors. Start by assessing the supplier’s experience in your specific industry and their range of products. Look for suppliers who have a proven track record in international trade, especially in your region, such as Africa or South America. Request samples to evaluate quality, and check references or reviews from other businesses. It’s crucial to ensure that the supplier can meet your customization requirements and understands your specific regulatory standards. -
What types of wall cladding materials are available for international buyers?
International buyers can access a diverse range of wall cladding materials, including metal, wood, vinyl, and stone. Each material offers unique benefits, such as durability, aesthetic appeal, and insulation properties. When selecting a material, consider the local climate and building regulations in your country, as they may influence material performance. Additionally, some suppliers offer composite materials that combine the benefits of various substances, which may be ideal for specific applications in different regions. -
What are the minimum order quantities (MOQ) for wall cladding products?
Minimum order quantities (MOQ) can vary significantly between suppliers and depend on the type of wall cladding material. Many suppliers set MOQs to optimize production efficiency and reduce costs. For international buyers, it’s essential to discuss MOQs upfront to determine if they align with your project needs. If the MOQ is too high, consider negotiating terms or exploring suppliers who cater specifically to smaller orders, especially if you are starting a new project or business. -
How can I ensure quality assurance when sourcing wall cladding internationally?
To ensure quality assurance when sourcing wall cladding, establish clear specifications and standards before engaging with suppliers. Request certifications, such as ISO or ASTM, which indicate adherence to international quality standards. Conduct audits or inspections during production and upon delivery to verify product quality. Additionally, consider suppliers who offer warranties or guarantees, as this reflects their confidence in the quality of their products. -
What payment terms should I expect when dealing with wall cladding suppliers?
Payment terms can vary widely among wall cladding suppliers and are often influenced by the supplier’s location and your relationship with them. Common terms include upfront payments, letters of credit, or payment upon delivery. As an international buyer, it’s advisable to negotiate terms that mitigate risk while ensuring timely delivery. Be aware of currency exchange rates and potential transaction fees, which can affect the overall cost of your purchase. -
What logistics considerations should I keep in mind when importing wall cladding?
When importing wall cladding, logistics considerations include shipping methods, customs regulations, and delivery timelines. Determine the most cost-effective shipping option that balances speed and reliability. Ensure you understand the customs duties and taxes applicable in your country, as they can significantly impact the total cost. Collaborate with logistics partners experienced in international trade to streamline the import process and avoid delays. -
How can I customize wall cladding products to suit my project needs?
Customization options for wall cladding products can vary by supplier. Most suppliers offer choices in color, texture, size, and finish to match your project requirements. Initiate discussions about your specific needs early in the procurement process to gauge the supplier’s flexibility. Additionally, consider suppliers who specialize in bespoke solutions, as they may provide design support and insights into the latest trends in wall cladding. -
What are the common challenges faced when sourcing wall cladding suppliers internationally?
Common challenges when sourcing wall cladding suppliers internationally include language barriers, cultural differences, and varying standards of quality. Time zone discrepancies can also complicate communication. To mitigate these challenges, establish clear channels of communication and use technology tools for collaboration. Conduct thorough research on potential suppliers and their capabilities, and consider visiting their facilities if feasible to build trust and ensure alignment with your expectations.
Important Disclaimer & Terms of Use
⚠️ Important Disclaimer
The information provided in this guide, including content regarding manufacturers, technical specifications, and market analysis, is for informational and educational purposes only. It does not constitute professional procurement advice, financial advice, or legal advice.
While we have made every effort to ensure the accuracy and timeliness of the information, we are not responsible for any errors, omissions, or outdated information. Market conditions, company details, and technical standards are subject to change.
B2B buyers must conduct their own independent and thorough due diligence before making any purchasing decisions. This includes contacting suppliers directly, verifying certifications, requesting samples, and seeking professional consultation. The risk of relying on any information in this guide is borne solely by the reader.
Strategic Sourcing Conclusion and Outlook for wall cladding supplier
What Are the Key Takeaways for B2B Buyers in Wall Cladding Sourcing?
In conclusion, strategic sourcing for wall cladding suppliers offers international B2B buyers a pathway to enhance operational efficiency and cost-effectiveness. By focusing on supplier reliability, product quality, and sustainable materials, buyers can create a competitive advantage in their respective markets. Understanding regional market dynamics—particularly in Africa, South America, the Middle East, and Europe—enables companies to tailor their sourcing strategies effectively.
How Can Strategic Sourcing Transform Your Procurement Process?
The value of strategic sourcing lies in its ability to foster long-term relationships with suppliers, ensuring consistent quality and innovation. This is particularly vital in regions like Mexico and Brazil, where local suppliers can offer unique insights into market trends and consumer preferences. By leveraging these relationships, buyers can not only secure better pricing but also gain access to cutting-edge materials and technologies.
What Is the Future Outlook for Wall Cladding Supply Chains?
Looking ahead, the demand for wall cladding is expected to grow, driven by urbanization and sustainability trends. International B2B buyers should remain proactive in exploring new supplier partnerships and innovations in materials, particularly eco-friendly options. Engaging with suppliers who prioritize sustainability can enhance brand reputation and meet increasingly stringent regulatory requirements.
How Should B2B Buyers Proceed?
As you navigate the evolving landscape of wall cladding suppliers, consider implementing a comprehensive sourcing strategy that emphasizes collaboration and adaptability. Stay informed about industry trends and market shifts, and be prepared to pivot as necessary. By taking these steps, you position your business for success in an increasingly competitive environment.