Discover Top Welding Rod Manufacturers: Save Costs in 2025
Introduction: Navigating the Global Market for welding rod manufacturer
In today’s competitive landscape, sourcing high-quality welding rods can pose significant challenges for international B2B buyers. With a plethora of manufacturers across various regions, including Africa, South America, the Middle East, and Europe, making the right choice can seem daunting. This comprehensive guide aims to demystify the global market for welding rod manufacturers, offering insights into different types of welding rods, their applications, and the critical factors to consider when vetting suppliers.
By exploring essential topics such as material specifications, performance standards, and pricing strategies, this guide empowers buyers to navigate complex purchasing decisions confidently. Understanding the nuances of supplier capabilities and production processes is crucial for ensuring that the welding rods meet specific project requirements and industry standards. Additionally, we will delve into cost analysis, helping you identify cost-effective solutions without compromising on quality.
Whether you’re a buyer in Nigeria seeking reliable local suppliers or a procurement officer in the UK looking for international options, this guide provides actionable insights tailored to your unique market dynamics. Equip yourself with the knowledge needed to make informed decisions, enhance your procurement strategy, and ultimately foster successful partnerships with welding rod manufacturers around the globe.
Understanding welding rod manufacturer Types and Variations
Type Name | Key Distinguishing Features | Primary B2B Applications | Brief Pros & Cons for Buyers |
---|---|---|---|
Mild Steel Welding Rods | High ductility, easy to use, versatile | General fabrication, automotive | Pros: Cost-effective, widely available. Cons: Limited in high-stress applications. |
Stainless Steel Welding Rods | Corrosion-resistant, high strength | Food processing, chemical industries | Pros: Durable, excellent for harsh environments. Cons: Higher cost than mild steel. |
Cast Iron Welding Rods | Designed for joining cast iron materials | Machinery repair, automotive parts | Pros: Strong joint formation. Cons: Requires skilled handling, brittle nature. |
Aluminum Welding Rods | Lightweight, good corrosion resistance | Aerospace, marine applications | Pros: Lightweight and strong. Cons: More challenging to weld, requires specific techniques. |
TIG Welding Rods | High precision, typically used with inert gas | High-quality fabrication, art metal | Pros: Clean welds, excellent control. Cons: Slower process, requires skilled operators. |
What Are the Key Characteristics of Mild Steel Welding Rods?
Mild steel welding rods are among the most common types utilized in various industries due to their high ductility and ease of use. These rods are particularly suitable for general fabrication and automotive applications, where strength and flexibility are paramount. When purchasing mild steel rods, buyers should consider the rod diameter, coating type, and specific welding processes (such as SMAW or MIG) that will be employed. Their cost-effectiveness and availability make them a preferred choice for many B2B buyers, especially in regions with high demand for general welding solutions.
How Do Stainless Steel Welding Rods Differ in Applications?
Stainless steel welding rods are known for their corrosion resistance and high strength, making them ideal for industries such as food processing and chemical manufacturing. These rods are suitable for applications where durability and hygiene are critical. When selecting stainless steel rods, buyers should evaluate the specific grade of stainless steel, which impacts the weld’s mechanical properties and resistance to environmental factors. While they tend to be more expensive than mild steel options, the long-term benefits in corrosive environments often justify the investment.
What Makes Cast Iron Welding Rods Unique for Specific Uses?
Cast iron welding rods are specially designed to join cast iron materials, which are prevalent in machinery repair and automotive parts. These rods create strong joints but require skilled handling due to the brittle nature of cast iron. B2B buyers should prioritize the compatibility of the welding rod with the specific cast iron type being used. While they provide excellent joint strength, the need for expertise in welding techniques can be a drawback, making it essential for buyers to assess the skill level of their workforce before procurement.
Why Choose Aluminum Welding Rods for Lightweight Applications?
Aluminum welding rods are favored for their lightweight properties and good corrosion resistance, making them essential in aerospace and marine applications. The suitability of these rods lies in their ability to provide strong welds while minimizing weight, which is critical in industries where performance is linked to weight reduction. Buyers should consider the welding process and equipment needed for aluminum, as it often requires specialized techniques. Although aluminum rods can be more challenging to work with, their benefits in specific applications often outweigh the difficulties.
What Are the Advantages of Using TIG Welding Rods in High-Quality Fabrication?
TIG (Tungsten Inert Gas) welding rods are known for their precision and ability to produce clean welds, making them ideal for high-quality fabrication and artistic metalwork. These rods allow for greater control over the welding process, which is essential for applications requiring a high level of detail. B2B buyers should consider the skill level of their operators and the time constraints of their projects, as TIG welding is generally slower than other methods. While the initial investment in equipment and training can be significant, the quality of the finished product often justifies the costs.
Related Video: Stick Welding Rod Overview
Key Industrial Applications of welding rod manufacturer
Industry/Sector | Specific Application of Welding Rod Manufacturer | Value/Benefit for the Business | Key Sourcing Considerations for this Application |
---|---|---|---|
Construction | Structural steel fabrication | Ensures structural integrity and safety of buildings | Compliance with local regulations and certifications |
Automotive | Repair and maintenance of vehicle frames | Enhances vehicle durability and reduces repair costs | Availability of specific alloy types and sizes |
Oil & Gas | Pipeline construction and maintenance | Facilitates efficient transport of resources | Resistance to corrosion and high-temperature performance |
Shipbuilding | Hull construction and repair | Improves longevity and performance of vessels | Certification for marine-grade materials |
Manufacturing | Fabrication of machinery and equipment | Increases production efficiency and reliability | Customization options for specific applications |
How is Welding Rod Used in the Construction Industry?
In the construction sector, welding rods are essential for structural steel fabrication. They are used to join steel beams and columns, ensuring the stability and safety of buildings. International B2B buyers, particularly from regions like Africa and Europe, must prioritize sourcing rods that meet local building codes and standards. This includes verifying certifications and ensuring that the welding rods possess the necessary strength and ductility for various environmental conditions.
What Role Do Welding Rods Play in the Automotive Sector?
In the automotive industry, welding rods are crucial for the repair and maintenance of vehicle frames. They help restore structural integrity after accidents, ensuring vehicles can withstand operational stresses. Buyers from South America and the Middle East should consider rods that are compatible with various steel grades used in modern vehicles. Additionally, sourcing from manufacturers who provide detailed technical support and training can enhance the efficiency of repair operations.
How Do Welding Rods Contribute to Oil & Gas Applications?
Welding rods are vital in the oil and gas sector for the construction and maintenance of pipelines. They are used to join sections of pipe, enabling the safe transport of crude oil and natural gas. B2B buyers need to focus on rods that offer resistance to corrosion and can withstand high temperatures and pressures. Ensuring compliance with industry standards and certifications is crucial for maintaining operational safety and efficiency.
Why Are Welding Rods Important in Shipbuilding?
In shipbuilding, welding rods are employed in the construction and repair of hulls, which are critical for the vessel’s performance and longevity. The use of high-quality rods ensures that ships can endure harsh marine environments. Buyers, especially from Europe and the Middle East, should prioritize sourcing marine-grade welding rods that comply with international maritime regulations. This ensures that the vessels meet safety and performance standards essential for successful operations.
What Benefits Do Welding Rods Provide in Manufacturing?
In the manufacturing sector, welding rods are used for the fabrication of machinery and equipment. They contribute to assembling durable components that enhance production efficiency. International buyers from Africa and South America should consider sourcing customized welding rods tailored to specific manufacturing processes. This includes options that provide improved wear resistance and thermal stability, which can lead to lower maintenance costs and increased operational uptime.
Related Video: What is MIG Welding? (GMAW)
3 Common User Pain Points for ‘welding rod manufacturer’ & Their Solutions
Scenario 1: Inconsistent Quality of Welding Rods
The Problem: B2B buyers often face challenges related to the inconsistency in the quality of welding rods supplied by manufacturers. This inconsistency can lead to defective welds, increased rework, and potential safety hazards. For companies in sectors such as construction and automotive, where structural integrity is crucial, using subpar welding materials can result in significant financial losses and reputational damage.
The Solution: To mitigate this risk, buyers should prioritize sourcing welding rods from manufacturers with established quality assurance processes. Look for suppliers that provide detailed product specifications, compliance certifications, and third-party testing results. Engaging in direct communication with the manufacturer can also help clarify their quality control measures. Additionally, implementing a pilot testing phase—where a small batch of rods is evaluated before full-scale purchase—can help ensure that the quality meets operational standards. Building long-term relationships with reliable manufacturers can also facilitate better oversight and quality assurance.
Scenario 2: Challenges in Custom Specifications
The Problem: Another common issue faced by international buyers is the difficulty in obtaining welding rods that meet specific project requirements. Different applications may necessitate unique rod compositions or sizes, and many manufacturers offer limited options. This can lead to delays in project timelines and increased costs, particularly if a buyer must source rods from multiple suppliers.
The Solution: To overcome this challenge, buyers should clearly define their project requirements upfront and communicate these specifications to potential manufacturers. It’s essential to collaborate closely with manufacturers that offer customization options. Requesting samples or prototypes can provide insight into how well the rods will perform for specific applications. Buyers can also consider partnering with manufacturers that have a robust R&D department, as they are more likely to accommodate unique specifications. Establishing a clear line of communication about needs and timelines will also help streamline the sourcing process.
Scenario 3: Navigating Compliance and Regulatory Standards
The Problem: For international B2B buyers, navigating the complex landscape of compliance and regulatory standards can be daunting. Different regions—especially in Africa, South America, the Middle East, and Europe—have varying regulations regarding materials used in construction and manufacturing. Failure to adhere to these standards can lead to legal issues and project delays.
The Solution: To effectively manage compliance risks, buyers should conduct thorough research into the regulatory requirements specific to their region and industry. When evaluating welding rod manufacturers, it is crucial to inquire about their compliance with local and international standards. Buyers should seek manufacturers that provide documentation proving adherence to regulations, such as ISO certifications or regional compliance reports. Additionally, leveraging the expertise of a local consultant or regulatory advisor can help navigate the complexities of compliance. Regular audits of supplier practices can also ensure ongoing adherence to necessary regulations, safeguarding the buyer’s interests.
By addressing these common pain points with actionable strategies, international B2B buyers can enhance their procurement processes, ensuring that they receive high-quality welding rods that meet their specific needs while remaining compliant with relevant regulations.
Strategic Material Selection Guide for welding rod manufacturer
When selecting materials for welding rods, manufacturers must consider various factors that affect performance, durability, and application compatibility. Below, we analyze four common materials used in welding rod production, focusing on their properties, advantages, disadvantages, and specific considerations for international B2B buyers, particularly those from Africa, South America, the Middle East, and Europe.
What Are the Key Properties of Mild Steel Welding Rods?
Mild steel welding rods are widely used due to their excellent weldability and strength. They typically have a carbon content of around 0.05% to 0.25%, which provides good ductility and toughness. These rods can withstand moderate temperatures and pressures, making them suitable for various applications, including structural and automotive welding.
Pros & Cons: The primary advantage of mild steel rods is their cost-effectiveness and ease of availability. However, they have limited corrosion resistance, which can be a drawback in humid or corrosive environments. Additionally, their performance can be affected by high temperatures, leading to potential deformation.
Impact on Application: Mild steel rods are compatible with a wide range of media, including structural steel and low-alloy steels. However, they may not be suitable for applications requiring high corrosion resistance, such as marine or chemical industries.
Considerations for International Buyers: Buyers should ensure compliance with local standards such as ASTM A615 or EN 10025. In regions like Nigeria and South America, sourcing reliable suppliers who adhere to these standards is crucial to avoid quality issues.
How Do Stainless Steel Welding Rods Compare?
Stainless steel welding rods are known for their superior corrosion resistance and strength, making them ideal for applications in food processing, pharmaceuticals, and marine environments. They typically contain chromium, which enhances their resistance to oxidation and corrosion.
Pros & Cons: The key advantage of stainless steel rods is their durability and ability to withstand harsh environments. However, they are generally more expensive than mild steel rods, and their welding process can be more complex, requiring specialized techniques to prevent issues such as cracking.
Impact on Application: Stainless steel rods are suitable for welding stainless steel components and are often used in applications where hygiene and corrosion resistance are critical. They are not recommended for high-temperature applications due to potential scaling.
Considerations for International Buyers: Compliance with standards such as ASTM A276 or EN 10088 is essential. Buyers in Europe and the Middle East should also consider the specific grades of stainless steel that meet local regulations.
What Are the Advantages of Using Aluminum Welding Rods?
Aluminum welding rods are lightweight and have excellent corrosion resistance, making them suitable for applications in the aerospace and automotive industries. They typically have a melting point of around 660°C, allowing for quick and efficient welding.
Pros & Cons: The main advantage of aluminum rods is their low weight and high strength-to-weight ratio. However, they can be more challenging to weld due to their thermal conductivity and require specialized equipment. Additionally, they may be less suitable for high-stress applications compared to steel rods.
Impact on Application: Aluminum rods are compatible with aluminum alloys and are often used in applications where weight reduction is a priority. However, they may not perform well in high-temperature environments.
Considerations for International Buyers: Buyers should be aware of the relevant standards such as ASTM B221 or EN 573. In regions like Africa, where aluminum is increasingly used in construction, sourcing from reputable manufacturers is vital for quality assurance.
Why Consider Nickel-Based Welding Rods?
Nickel-based welding rods are known for their exceptional resistance to high temperatures and corrosion, making them ideal for applications in the oil and gas industry, as well as in power generation. These rods typically contain nickel and chromium, providing excellent mechanical properties.
Pros & Cons: The key advantage of nickel-based rods is their ability to withstand extreme conditions, including high temperatures and corrosive environments. However, they are among the most expensive options and require skilled welders to ensure quality.
Impact on Application: Nickel rods are suitable for welding high-performance alloys and are often used in critical applications where failure is not an option. Their cost may limit their use in less demanding environments.
Considerations for International Buyers: Compliance with standards such as AWS A5.14 or EN ISO 18274 is crucial. Buyers in the Middle East should consider the specific requirements for oil and gas applications, ensuring that they source from manufacturers with proven expertise.
Summary Table of Material Selection for Welding Rods
Material | Typical Use Case for welding rod manufacturer | Key Advantage | Key Disadvantage/Limitation | Relative Cost (Low/Med/High) |
---|---|---|---|---|
Mild Steel | Structural and automotive welding | Cost-effective and widely available | Limited corrosion resistance | Low |
Stainless Steel | Food processing and marine applications | Superior corrosion resistance | Higher cost and complex welding | High |
Aluminum | Aerospace and automotive industries | Lightweight and corrosion-resistant | Challenging to weld | Medium |
Nickel-Based | Oil and gas, power generation | Exceptional high-temperature resistance | Very high cost | High |
This guide aims to equip international B2B buyers with the necessary insights to make informed decisions regarding welding rod materials, taking into account their specific needs and regional standards.
In-depth Look: Manufacturing Processes and Quality Assurance for welding rod manufacturer
What Are the Main Stages of the Welding Rod Manufacturing Process?
The manufacturing of welding rods is a multi-stage process that involves careful planning and execution to ensure quality and performance. Here are the main stages involved:
-
Material Preparation
The first step in manufacturing welding rods is the preparation of raw materials, which typically include metal powders, fluxes, and other alloying elements. This stage involves sourcing high-quality materials that meet specific chemical compositions. Rigorous testing of these materials is critical to ensure they meet industry standards and performance requirements. -
Forming the Welding Rods
Once the materials are prepared, they undergo forming processes such as extrusion or drawing. Extrusion involves forcing the material through a die to create the desired rod shape. Drawing reduces the diameter of the rods through pulling, ensuring uniformity and strength. Advanced techniques, such as hot or cold working, may be employed to enhance the mechanical properties of the rods. -
Assembly and Coating
After forming, the rods may require additional assembly steps, particularly if they are composite rods with multiple layers. Coating processes are also crucial at this stage, where flux materials are applied to the rod surface. This coating plays a vital role in the welding process, providing protection against oxidation and improving arc stability. -
Finishing Processes
The final stage in manufacturing involves finishing processes such as cutting to length, surface cleaning, and packaging. These steps ensure that the welding rods are ready for shipment and meet the exact specifications required by international standards. Proper packaging is essential to prevent damage during transport.
How Is Quality Assurance Managed in Welding Rod Manufacturing?
Quality assurance (QA) is critical in the welding rod manufacturing process to ensure that products meet industry standards and customer expectations. Here’s how QA is typically structured:
-
International Standards and Certifications
Many welding rod manufacturers adhere to international quality management standards such as ISO 9001. Additionally, industry-specific certifications like CE marking for Europe and API (American Petroleum Institute) certifications for oil and gas applications are essential. These certifications provide buyers with confidence that the products meet safety and performance criteria. -
Quality Control Checkpoints
The quality control process is structured around several checkpoints:
– Incoming Quality Control (IQC): This involves inspecting raw materials upon arrival to ensure they meet the specified standards before production begins.
– In-Process Quality Control (IPQC): During manufacturing, regular inspections are conducted to monitor the production process and identify any deviations from quality standards.
– Final Quality Control (FQC): After production, the final products undergo thorough testing and inspection to ensure they meet the required specifications and standards before shipment. -
Common Testing Methods for Welding Rods
Various testing methods are employed to assess the quality of welding rods, including:
– Tensile Testing: Measures the strength and ductility of the rods.
– Chemical Composition Analysis: Ensures that the materials meet the specified chemical requirements.
– Bend Testing: Evaluates the flexibility and ductility of the rods under stress.
– Visual Inspection: Identifies surface defects or irregularities that could affect performance.
How Can B2B Buyers Verify Supplier Quality Control?
For international B2B buyers, particularly those from Africa, South America, the Middle East, and Europe, verifying the quality control processes of a welding rod manufacturer is crucial. Here are some strategies to consider:
-
Conducting Audits
Regular audits of suppliers can provide insights into their manufacturing processes and quality control measures. Buyers should request access to audit reports and findings to assess compliance with international standards and industry best practices. -
Requesting Quality Assurance Documentation
Buyers should ask suppliers for detailed quality assurance documentation, including certificates of compliance, test reports, and inspection records. This information is vital for understanding the quality control measures in place and ensuring they align with the buyer’s standards. -
Engaging Third-Party Inspection Services
Utilizing third-party inspection services can provide an unbiased evaluation of the manufacturing processes and final products. These services can conduct independent tests and assessments, offering buyers additional assurance of product quality.
What Are the Quality Control Nuances for International B2B Buyers?
When sourcing welding rods from manufacturers across different regions, B2B buyers must be aware of specific quality control nuances:
-
Regional Standards and Compliance
Different regions may have varying standards and regulations governing welding products. For instance, European buyers may prioritize compliance with CE standards, while buyers in the Middle East may focus on local specifications. Understanding these nuances is essential for successful procurement. -
Cultural and Communication Barriers
Differences in language and business practices can lead to misunderstandings regarding quality expectations. Buyers should establish clear communication channels and ensure that all quality requirements are explicitly stated in contracts and agreements. -
Supply Chain Reliability
The reliability of the supply chain can significantly impact quality assurance. Buyers should evaluate suppliers not only on their manufacturing capabilities but also on their logistics and delivery systems to ensure consistent product availability and quality.
Conclusion
Understanding the manufacturing processes and quality assurance practices of welding rod manufacturers is essential for B2B buyers, especially in diverse markets like Africa, South America, the Middle East, and Europe. By focusing on the main stages of production, implementing effective quality control measures, and verifying supplier practices, buyers can ensure they procure high-quality welding rods that meet their specific needs.
Practical Sourcing Guide: A Step-by-Step Checklist for ‘welding rod manufacturer’
The following checklist serves as a practical guide for international B2B buyers looking to source welding rod manufacturers. This step-by-step approach will help you navigate the complexities of the procurement process while ensuring quality and reliability in your supply chain.
Step 1: Define Your Technical Specifications
Understanding your specific welding requirements is crucial. Begin by detailing the types of welding applications you will use the rods for, such as MIG, TIG, or stick welding. This clarity will guide you in selecting a manufacturer that specializes in the appropriate welding rods suited for your needs.
- Consider material types: Different applications may require different rod compositions (e.g., stainless steel, aluminum, or mild steel).
- Evaluate rod diameter and length: These dimensions can significantly affect the welding process and the end results.
Step 2: Research Potential Manufacturers
Conduct comprehensive research to identify potential welding rod manufacturers. Utilize online directories, industry forums, and trade shows to compile a list of suppliers.
- Check their market presence: A manufacturer with a solid reputation and years of experience is more likely to deliver quality products.
- Look for region-specific suppliers: For buyers in Africa, South America, the Middle East, and Europe, sourcing from local or regionally-based manufacturers can reduce shipping costs and lead times.
Step 3: Evaluate Potential Suppliers
Before committing, it’s crucial to vet suppliers thoroughly. Request company profiles, case studies, and references from buyers in a similar industry or region.
- Inspect product samples: This allows you to assess the quality firsthand.
- Examine their production capabilities: Ensure they can meet your quantity requirements consistently.
Step 4: Verify Supplier Certifications
Check for relevant industry certifications that demonstrate compliance with international standards, such as ISO 9001 or AWS (American Welding Society) certifications.
- Assess compliance with local regulations: Make sure that the manufacturer adheres to the legal standards in your region, as this can affect product acceptance.
- Understand warranty and support: A reliable manufacturer should offer warranties and customer support for their products.
Step 5: Request and Compare Quotes
Once you’ve narrowed down your options, request quotes from multiple suppliers. This will not only give you a sense of market pricing but also allow you to evaluate the terms and conditions offered.
- Review payment terms and delivery timelines: Ensure that the payment options align with your budget and that the delivery timelines meet your project deadlines.
- Look for additional services: Some manufacturers may offer technical support or after-sales service, which can add value.
Step 6: Conduct a Factory Visit (if possible)
If feasible, arrange a visit to the manufacturing facility. This provides an opportunity to see the production process, quality control measures, and overall operational capabilities.
- Engage with the production team: Understanding their processes and workforce can offer insights into the manufacturer’s reliability and commitment to quality.
- Assess the facility’s cleanliness and organization: A well-maintained factory often indicates a higher standard of production.
Step 7: Finalize the Agreement and Monitor Performance
After selecting a supplier, finalize the contract by clearly outlining all terms, including pricing, delivery schedules, and quality expectations. Once the partnership is established, monitor their performance regularly.
- Establish key performance indicators (KPIs): This will help you assess the supplier’s reliability and quality over time.
- Maintain open communication: Regular check-ins can help address any issues promptly and strengthen the business relationship.
By following this checklist, international B2B buyers can ensure they make informed decisions when sourcing welding rod manufacturers, ultimately leading to successful procurement and project outcomes.
Comprehensive Cost and Pricing Analysis for welding rod manufacturer Sourcing
What Are the Key Components of Cost Structure in Welding Rod Manufacturing?
When sourcing welding rods, understanding the cost structure is crucial for international B2B buyers. The primary components include:
-
Materials: The quality and type of materials used in welding rod production significantly affect costs. Common materials include mild steel, stainless steel, and various alloys. Premium materials may enhance performance but also increase costs.
-
Labor: Labor costs can vary widely based on geographic location and skill level. In regions like Africa and South America, labor may be more affordable, whereas Europe might incur higher labor costs due to stricter regulations and higher living standards.
-
Manufacturing Overhead: This encompasses indirect costs such as utilities, rent, and administrative expenses. Efficient manufacturing processes can help minimize these costs, which is vital for maintaining competitive pricing.
-
Tooling: The initial investment in machinery and tooling can be significant. However, a well-maintained and efficient production line can lead to lower costs over time, making it essential to consider long-term benefits versus short-term expenses.
-
Quality Control (QC): Implementing stringent QC processes ensures product reliability and compliance with international standards. While this adds to the cost, it can prevent costly recalls and enhance customer trust.
-
Logistics: Transportation costs can fluctuate based on distance, mode of transport, and geopolitical factors. Buyers should assess shipping routes and local regulations that could impact delivery times and costs.
-
Margin: Manufacturers typically apply a profit margin to their costs. Understanding the typical margins in the welding rod industry can help buyers gauge fair pricing.
How Do Price Influencers Affect Welding Rod Sourcing?
Several factors influence pricing when sourcing welding rods:
-
Volume and Minimum Order Quantity (MOQ): Larger orders often lead to lower per-unit costs. Buyers should negotiate MOQs that align with their needs without incurring excess inventory.
-
Specifications and Customization: Custom specifications can increase costs due to the need for specialized materials or production processes. Buyers should weigh the benefits of customization against potential price increases.
-
Material Quality and Certifications: Higher quality materials and certifications (e.g., ISO, AWS) enhance product credibility but can raise prices. Buyers should consider the long-term value of investing in certified products.
-
Supplier Factors: The supplier’s reputation, reliability, and production capabilities can affect pricing. Established suppliers may charge a premium for their proven quality and service.
-
Incoterms: The chosen Incoterms (International Commercial Terms) determine who is responsible for shipping and insurance costs. Understanding these terms can help buyers manage their total costs effectively.
What Tips Can Help International Buyers Optimize Welding Rod Costs?
-
Effective Negotiation: Buyers should approach negotiations prepared with data on market prices and competitor offerings. Establishing a good relationship with suppliers can also facilitate better pricing terms.
-
Focus on Total Cost of Ownership (TCO): TCO goes beyond the initial purchase price. Consider long-term costs related to performance, maintenance, and potential rework when evaluating suppliers.
-
Understand Pricing Nuances: Different regions may have varying pricing structures due to local economic conditions, tariffs, and trade agreements. Buyers from Africa, South America, the Middle East, and Europe should conduct thorough market research.
-
Leverage Technology: Utilizing procurement software can streamline sourcing processes and enable better tracking of costs and supplier performance.
-
Plan for Currency Fluctuations: International buyers should account for potential currency fluctuations that can impact costs. Working with suppliers who can offer stable pricing or currency hedging options can mitigate these risks.
Disclaimer on Indicative Prices
It is essential to note that prices for welding rods can vary significantly based on the aforementioned factors. Buyers should conduct thorough due diligence and seek multiple quotes to ensure competitive pricing tailored to their specific needs.
Alternatives Analysis: Comparing welding rod manufacturer With Other Solutions
When evaluating welding solutions, it is essential to consider not only the welding rod manufacturers but also alternative methods that could meet specific business needs. This analysis will compare welding rods with two other viable solutions: welding wire and arc welding machines. Each option has unique advantages and disadvantages, making it crucial for B2B buyers to assess which solution best aligns with their operational requirements.
Comparison Aspect | Welding Rod Manufacturer | Welding Wire | Arc Welding Machine |
---|---|---|---|
Performance | High durability and strength, suitable for various metals | Flexible and adaptable for different applications | High precision and speed, great for thick materials |
Cost | Moderate to high initial investment | Generally lower cost | High initial investment, but lower operational costs |
Ease of Implementation | Requires skilled labor for application | Easier to handle, often requires less training | Requires specialized training and setup |
Maintenance | Regular inventory management needed | Minimal maintenance, easy to store | Requires regular checks and maintenance for optimal performance |
Best Use Case | Heavy-duty applications like construction and shipbuilding | General fabrication and repair work | Industrial applications requiring precision and speed |
What are the Advantages and Disadvantages of Welding Wire as an Alternative?
Welding wire is a flexible alternative that offers various benefits. Its ease of handling allows for quicker setup and less training for operators, making it ideal for smaller projects and repair work. Additionally, welding wire is often more cost-effective than welding rods, providing a more budget-friendly option for businesses. However, its performance may not match the durability required for heavy-duty applications, and it may not provide the same level of strength in certain conditions.
How Does an Arc Welding Machine Compare?
Arc welding machines represent a more advanced technology for welding, delivering high precision and speed. This method is particularly beneficial for industrial applications where thick materials are involved, making it an excellent choice for manufacturing and assembly lines. While the initial investment is higher than welding rods or wire, the operational costs can be lower due to efficiency gains. However, the requirement for specialized training and regular maintenance can make this option less accessible for some businesses, particularly smaller ones in developing regions.
How Can International B2B Buyers Choose the Right Welding Solution?
Selecting the appropriate welding solution requires a comprehensive assessment of specific business needs, budget constraints, and the intended application. Buyers should consider the scale of their projects, the materials they will be working with, and the skill level of their workforce. For heavy-duty applications in sectors like construction or shipbuilding, welding rods may provide the best performance. Conversely, for smaller tasks or repairs, welding wire could be the more practical choice. Arc welding machines, while costly, may be justified in high-volume manufacturing settings where speed and precision are paramount. Ultimately, understanding these alternatives allows B2B buyers to make informed decisions that align with their operational goals and financial strategies.
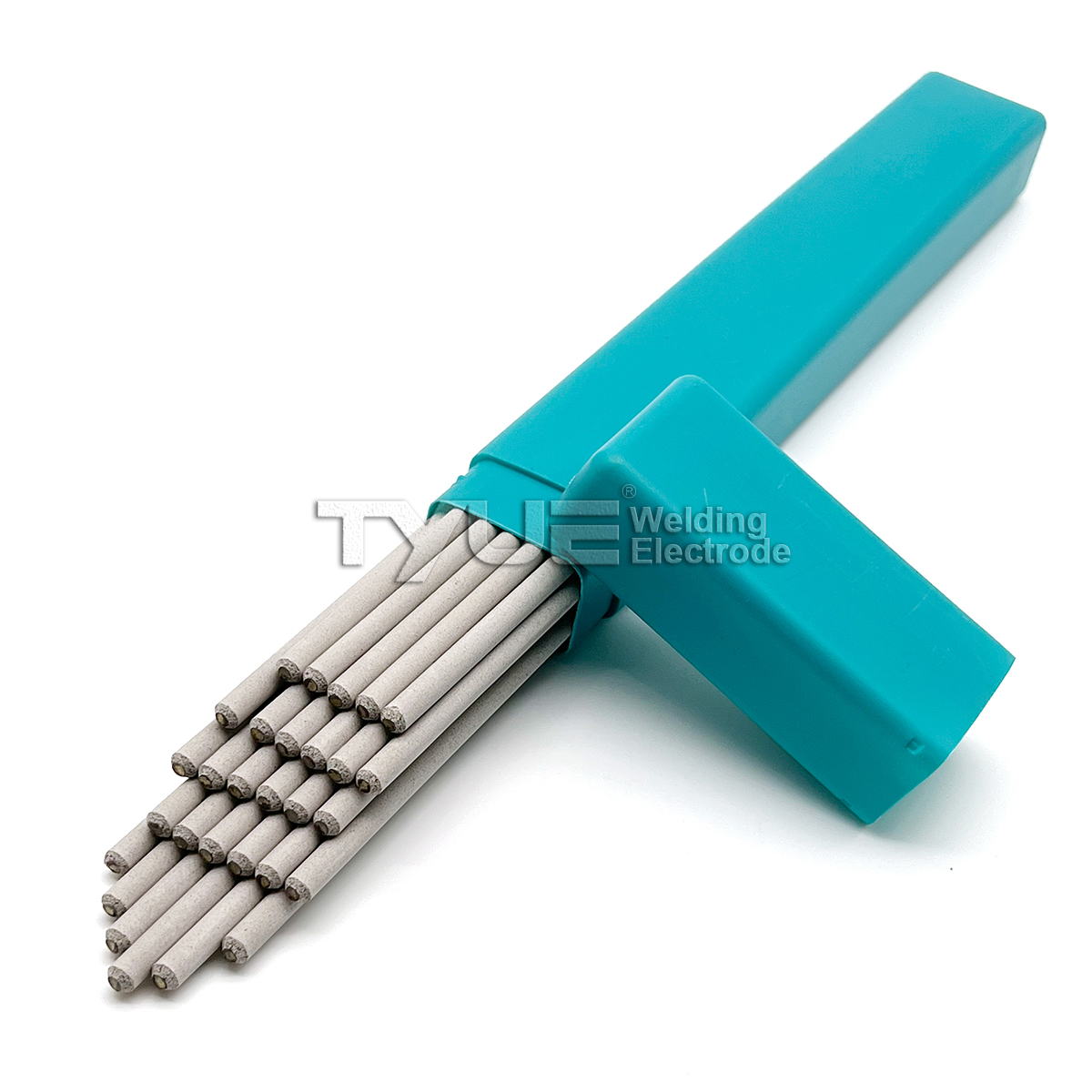
A stock image related to welding rod manufacturer.
Essential Technical Properties and Trade Terminology for welding rod manufacturer
What Are the Key Technical Properties of Welding Rods?
When sourcing welding rods, international B2B buyers must understand specific technical properties that directly impact the performance and suitability of the product for their applications. Here are some critical specifications:
-
Material Grade
Material grade refers to the composition and mechanical properties of the welding rod. Common grades include E6010, E6011, E7018, and others, each designed for specific applications. Understanding the material grade helps buyers select rods that meet their project requirements, ensuring strength and durability in the final weld. -
Diameter
The diameter of a welding rod affects the amount of heat generated during the welding process. Typically ranging from 1.6 mm to 5.0 mm, the diameter chosen depends on the thickness of the base metal and the type of welding being performed. Buyers should assess their welding equipment and the intended application to select the appropriate diameter for optimal results. -
Tensile Strength
Tensile strength is the maximum amount of tensile (pulling) stress that a material can withstand before failure. It is usually measured in megapascals (MPa). For B2B buyers, this property is crucial as it ensures that the welded joint can withstand the stresses it will encounter in service, providing reliability and safety. -
Weldability
Weldability indicates how easily a material can be welded, which is influenced by factors like composition and microstructure. High weldability means fewer defects and a more straightforward welding process. Buyers should consider this property to avoid costly rework and ensure efficient production. -
Coating Type
The coating on a welding rod serves multiple purposes, including protecting the weld pool from contaminants and stabilizing the arc. Common coatings include cellulose, rutile, and basic. Understanding the coating type helps buyers select rods suitable for their specific environmental conditions and welding techniques. -
Impact Toughness
Impact toughness measures a material’s ability to absorb energy and resist fracture under sudden loads or impacts. This property is particularly important in industries such as construction and manufacturing, where welded joints may face dynamic loads. Buyers should evaluate the impact toughness to ensure long-term performance in demanding applications.
What Are Common Trade Terminologies in the Welding Rod Industry?
Navigating the welding rod market requires familiarity with specific industry terms that can significantly affect purchasing decisions. Here are some commonly used terms:
-
OEM (Original Equipment Manufacturer)
An OEM refers to a company that produces parts or equipment that may be marketed by another manufacturer. For B2B buyers, understanding OEM relationships can help in sourcing high-quality welding rods that meet specific standards and specifications. -
MOQ (Minimum Order Quantity)
MOQ is the smallest quantity of a product that a supplier is willing to sell. This term is essential for buyers as it can affect inventory levels and cash flow. Understanding the MOQ helps businesses plan their purchases and avoid overstocking or understocking situations. -
RFQ (Request for Quotation)
An RFQ is a document issued by a buyer to solicit price quotes from suppliers for specific products or services. For welding rod procurement, issuing an RFQ enables buyers to compare prices, terms, and conditions from multiple suppliers, ensuring the best deal. -
Incoterms
Incoterms are international commercial terms that define the responsibilities of buyers and sellers in international transactions. Knowing these terms helps buyers understand shipping costs, risks, and responsibilities, facilitating smoother international trade agreements. -
Lead Time
Lead time refers to the amount of time from placing an order to receiving it. Understanding lead times is critical for project planning and inventory management, particularly in industries where timing can significantly impact operations. -
Certification
Certification indicates that a product meets specific industry standards and regulations. For welding rods, certifications such as ISO or AWS standards assure buyers of the quality and reliability of the products they are sourcing.
By familiarizing themselves with these technical properties and trade terminologies, B2B buyers can make informed decisions that enhance their procurement strategies and optimize their welding operations.
Navigating Market Dynamics and Sourcing Trends in the welding rod manufacturer Sector
What Are the Current Market Dynamics in the Welding Rod Manufacturer Sector?
The welding rod manufacturing sector is experiencing significant transformation driven by global economic trends, technological advancements, and evolving customer needs. As international B2B buyers, particularly from Africa, South America, the Middle East, and Europe, navigate these dynamics, understanding the key drivers becomes essential.
One of the primary global drivers is the robust demand for construction and infrastructure projects, especially in developing regions. Countries like Nigeria and those in South America are seeing increased investments in infrastructure, which directly boosts the demand for welding rods. Additionally, there is a shift towards automation and digitalization in manufacturing processes. B2B buyers should look for suppliers who utilize advanced technologies such as IoT and AI in their production processes, as these can enhance quality and reduce lead times.
Emerging sourcing trends also indicate a growing preference for suppliers who provide comprehensive solutions rather than just raw materials. This trend reflects a need for value-added services, such as technical support and customized products, which can enhance operational efficiency. Furthermore, the rise of online marketplaces is reshaping how buyers source welding rods. Platforms that facilitate direct communication with manufacturers can streamline procurement processes and enhance transparency in pricing and product availability.
How Does Sustainability Impact Sourcing in the Welding Rod Industry?
Sustainability is becoming a cornerstone of sourcing strategies in the welding rod manufacturing sector. The environmental impact of production processes is under scrutiny, with an increasing number of international buyers prioritizing suppliers that adopt sustainable practices. This shift is particularly pronounced among buyers in Europe and the Middle East, where regulatory frameworks are more stringent regarding environmental compliance.
Ethical sourcing is equally important, as it ensures that materials are procured responsibly and that labor practices are fair. International buyers should actively seek manufacturers who are certified under recognized green standards, such as ISO 14001 for environmental management or ISO 45001 for occupational health and safety. Additionally, the use of recycled materials in the production of welding rods can significantly reduce the carbon footprint, appealing to eco-conscious buyers.
By aligning with suppliers committed to sustainability and ethical sourcing, B2B buyers can not only fulfill regulatory requirements but also enhance their brand reputation. This can lead to greater customer loyalty and a competitive edge in the market.
What Is the Historical Context of the Welding Rod Manufacturing Sector?
The welding rod manufacturing sector has evolved considerably since its inception in the early 20th century. Initially focused on basic materials for construction and industrial applications, the industry has witnessed significant technological advancements. Over the decades, the introduction of new alloys and welding techniques has expanded the functionality of welding rods, catering to diverse applications from automotive to aerospace.
The globalization of manufacturing has also played a pivotal role in shaping the sector. As companies sought cost-effective production methods, many welding rod manufacturers established operations in developing countries, allowing them to offer competitive pricing while maintaining quality. This trend has led to a more interconnected market, where international buyers can source products from various regions, benefiting from both quality and cost efficiency.
Understanding this historical context helps B2B buyers appreciate the current market landscape and anticipate future trends, ultimately guiding their sourcing strategies more effectively.
Frequently Asked Questions (FAQs) for B2B Buyers of welding rod manufacturer
-
How do I choose the right welding rod manufacturer for my needs?
Choosing the right welding rod manufacturer involves assessing several key factors. Start by evaluating the manufacturer’s reputation in the industry, particularly in your region, such as Africa or Europe. Look for certifications that indicate quality standards, like ISO or AWS. Additionally, consider the manufacturer’s experience with your specific application, whether it’s for construction, automotive, or another sector. Request samples to test their products and verify their claims. Engaging with other businesses in your network can also provide insights into reliable manufacturers. -
What types of welding rods are best suited for different applications?
The best welding rod for a particular application depends on the materials being welded and the welding process used. For example, E6011 rods are excellent for general-purpose welding on mild steel, while E7018 rods are preferred for structural welding due to their low hydrogen content. Stainless steel applications often require E308 or E316 rods. For B2B buyers in diverse markets, understanding local industry standards and requirements is crucial. Always consult with the manufacturer for recommendations based on your specific needs. -
What are the minimum order quantities (MOQ) when sourcing welding rods?
Minimum order quantities can vary significantly among manufacturers, often ranging from 100 kg to several tons. For international buyers, especially from regions like Africa and South America, negotiating the MOQ can be beneficial, particularly if you are a smaller company or new to sourcing. Some manufacturers may offer flexibility based on your purchasing power or the potential for long-term partnerships. Always clarify MOQ during initial discussions to avoid unexpected costs. -
How can I ensure the quality of welding rods from international suppliers?
To ensure quality when sourcing welding rods internationally, start by requesting quality assurance documents and certifications from the manufacturer. Conduct factory audits if possible, or use third-party inspection services to verify product quality before shipment. Additionally, establish a clear quality control protocol, including product testing upon receipt. Engaging in regular communication with the supplier can also help address any quality concerns promptly. -
What payment terms are commonly offered by welding rod manufacturers?
Payment terms can vary widely, but common practices include a 30% deposit upon order confirmation and the remaining 70% before shipment. For international transactions, consider using letters of credit or escrow services to secure your investment. Some manufacturers may offer flexible payment plans or discounts for bulk orders. Always discuss and negotiate payment terms upfront to avoid misunderstandings later in the transaction. -
What logistical considerations should I keep in mind when importing welding rods?
Logistics is a crucial aspect of importing welding rods. Ensure you understand the shipping methods available, as well as customs regulations in your country. Consider the lead times for production and shipping, which can impact your project schedules. Work with reliable freight forwarders who have experience in handling industrial goods. Additionally, be aware of any tariffs or import duties that may apply, as these can affect your overall costs. -
How can I evaluate the reliability of a welding rod supplier?
Evaluating a supplier’s reliability involves several steps. Start by researching their history, customer reviews, and case studies. Look for references or testimonials from other businesses, particularly those in your industry. Check for certifications that indicate adherence to quality standards. Engaging in direct communication can also reveal insights about their customer service responsiveness and willingness to collaborate. Consider starting with a smaller order to gauge their reliability before committing to larger purchases. -
Can I customize welding rods to meet specific project requirements?
Many manufacturers offer customization options for welding rods to meet specific project needs, such as unique alloy compositions or packaging requirements. When discussing customization, provide detailed specifications, including the type of materials to be welded and the desired mechanical properties. Customization may affect pricing and lead times, so be prepared for potential adjustments. Collaborating closely with the manufacturer will help ensure that the final product aligns with your project goals.
Important Disclaimer & Terms of Use
⚠️ Important Disclaimer
The information provided in this guide, including content regarding manufacturers, technical specifications, and market analysis, is for informational and educational purposes only. It does not constitute professional procurement advice, financial advice, or legal advice.
While we have made every effort to ensure the accuracy and timeliness of the information, we are not responsible for any errors, omissions, or outdated information. Market conditions, company details, and technical standards are subject to change.
B2B buyers must conduct their own independent and thorough due diligence before making any purchasing decisions. This includes contacting suppliers directly, verifying certifications, requesting samples, and seeking professional consultation. The risk of relying on any information in this guide is borne solely by the reader.
Strategic Sourcing Conclusion and Outlook for welding rod manufacturer
As international B2B buyers navigate the complexities of sourcing welding rods, strategic sourcing emerges as a pivotal practice. By focusing on quality, supplier reliability, and cost-effectiveness, companies can not only enhance their operational efficiency but also ensure compliance with local standards and regulations. Buyers from regions such as Africa, South America, the Middle East, and Europe must prioritize building relationships with manufacturers who understand their unique market needs, thereby facilitating smoother transactions and better service delivery.
What are the benefits of forging long-term partnerships with welding rod manufacturers? Establishing lasting connections can lead to favorable pricing, consistent supply chains, and access to innovative products tailored to specific applications. Moreover, by leveraging technology and data analytics, buyers can gain insights into market trends, helping them to make informed decisions that align with their strategic objectives.
Looking ahead, the welding rod manufacturing industry is poised for growth, driven by advancements in technology and increasing demand across various sectors. International B2B buyers should actively engage with manufacturers to explore opportunities for collaboration and innovation. Now is the time to invest in strategic sourcing initiatives that not only meet current needs but also position businesses for future success in an evolving market landscape.