Elevate Your Space: Custom Dining Room Table Solutions (2025)
Introduction: Navigating the Global Market for dining room table custom
In today’s global marketplace, sourcing custom dining room tables presents a unique set of challenges for B2B buyers. With diverse styles, materials, and design preferences, it can be daunting to navigate the options while ensuring quality and cost-effectiveness. This guide is designed to equip international B2B buyers, especially those from Africa, South America, the Middle East, and Europe, with essential insights into the custom dining room table market.
We will explore a variety of types, including contemporary, rustic, and multifunctional designs, and delve into their applications across different sectors, from hospitality to residential. Additionally, the guide will cover critical aspects such as supplier vetting processes, pricing strategies, and best practices for negotiating contracts. By addressing common concerns such as quality assurance, shipping logistics, and after-sales support, this comprehensive resource empowers buyers to make informed purchasing decisions.
As you embark on your journey to source custom dining room tables, this guide will serve as a valuable tool, helping you navigate market complexities while maximizing your investment. Whether you’re looking to enhance a restaurant’s ambiance or provide clients with bespoke furniture solutions, understanding these dynamics will be key to your success in the competitive global landscape.
Understanding dining room table custom Types and Variations
Type Name | Key Distinguishing Features | Primary B2B Applications | Brief Pros & Cons for Buyers |
---|---|---|---|
Rectangular Tables | Classic shape, versatile sizing options | Restaurants, conference rooms | Pros: Space-efficient; Cons: Limited seating flexibility. |
Round Tables | Promotes conversation, often smaller footprint | Cafés, intimate dining settings | Pros: Encourages interaction; Cons: Less formal appearance. |
Extendable Tables | Adjustable length for varying guest counts | Event spaces, banquet halls | Pros: Flexible for events; Cons: Mechanism can wear over time. |
Square Tables | Equal seating arrangement, compact design | Modern eateries, co-working spaces | Pros: Stylish and modern; Cons: Limited capacity for larger groups. |
Customizable Tables | Tailored designs, materials, and finishes | High-end restaurants, luxury hotels | Pros: Unique branding opportunity; Cons: Higher cost and longer lead time. |
What Are the Key Characteristics of Rectangular Tables?
Rectangular dining tables are the most traditional and widely used type in both commercial and residential settings. Their classic shape allows for various sizes, accommodating a range of seating configurations. They are particularly suited for restaurants and conference rooms where space efficiency and functionality are crucial. When purchasing, consider the material and finish, as these can significantly impact durability and aesthetic appeal.
How Do Round Tables Enhance Dining Experiences?
Round tables are designed to foster conversation and create an intimate dining experience. Their smaller footprint makes them ideal for cafés and intimate dining settings, where space is often at a premium. B2B buyers should evaluate the table’s size and the number of seats it can accommodate, as this can affect customer satisfaction and turnover rates in dining establishments.
What Advantages Do Extendable Tables Offer for B2B Buyers?
Extendable tables are a versatile solution for businesses that host events or need to adjust seating capacity based on guest numbers. They feature a mechanism that allows for easy expansion, making them suitable for banquet halls and event spaces. Buyers should consider the quality of the extension mechanism, as well as the table’s aesthetic, to ensure it fits their brand image while remaining practical.
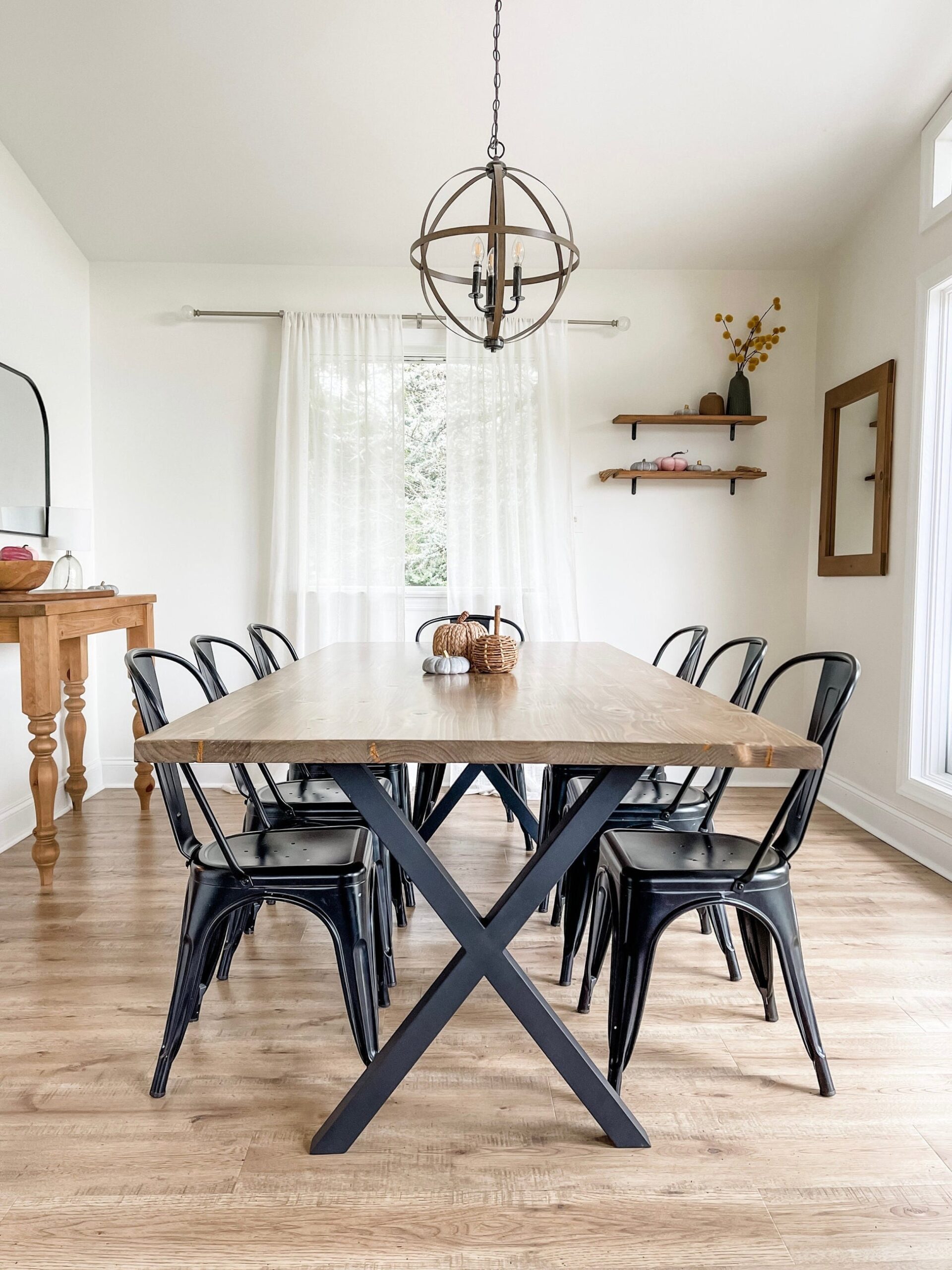
A stock image related to dining room table custom.
Why Choose Square Tables for Modern Dining Spaces?
Square tables provide an equal seating arrangement that can be visually appealing in modern eateries and co-working spaces. They offer a compact design but may limit seating capacity for larger groups. When selecting square tables, B2B buyers should think about the overall layout of their space and how these tables can complement their design while maximizing seating efficiency.
How Can Customizable Tables Enhance Branding for Businesses?
Customizable dining tables allow businesses to create unique designs that align with their branding and aesthetic. This option is particularly popular among high-end restaurants and luxury hotels looking to make a lasting impression on their clientele. Buyers must weigh the benefits of bespoke designs against the potential for higher costs and longer lead times in production, ensuring that the investment aligns with their overall business strategy.
Related Video: DIY Modern Dining Table | Woodbrew
Key Industrial Applications of dining room table custom
Industry/Sector | Specific Application of dining room table custom | Value/Benefit for the Business | Key Sourcing Considerations for this Application |
---|---|---|---|
Hospitality | Custom dining tables for restaurants and hotels | Enhances customer experience and brand image | Material quality, design aesthetics, durability, and cost |
Corporate Offices | Conference room tables | Facilitates effective meetings and professional environment | Size, shape, modularity, and integration with existing decor |
Residential Real Estate | Staging homes for sale | Increases property appeal and potential sale price | Versatility, style matching with home aesthetics, and pricing |
Event Management | Custom tables for banquets and events | Creates a unique and memorable experience for guests | Customization options, ease of transport, and setup time |
Education | Dining tables for school cafeterias | Promotes social interaction and student engagement | Safety standards, maintenance requirements, and capacity |
How Are Custom Dining Tables Used in the Hospitality Industry?
In the hospitality sector, custom dining tables are essential for restaurants and hotels looking to create a distinct ambiance and enhance customer experience. These tables can be tailored to match the theme of the establishment, thereby reinforcing the brand identity. For international buyers, particularly those from Africa, South America, and Europe, considerations such as durability against high traffic, ease of cleaning, and style coherence with the overall decor are crucial. Sourcing high-quality materials that withstand wear while offering aesthetic appeal is a top priority.
What Role Do Custom Tables Play in Corporate Offices?
In corporate environments, custom dining tables are increasingly used in conference rooms to facilitate meetings and foster collaboration. These tables can be designed to accommodate various group sizes and configurations, which is essential for dynamic workspaces. Buyers in regions like the Middle East and Europe should consider factors like modularity, the ability to integrate technology (such as power outlets), and the overall professional look. Sourcing should focus on quality materials that reflect the company’s image while being functional.
How Do Custom Dining Tables Benefit Residential Real Estate?
For residential real estate, custom dining tables are often utilized in home staging to enhance the appeal of properties on the market. A well-chosen table can create a welcoming atmosphere, making the space more attractive to potential buyers. For B2B buyers in South Africa and Poland, it is important to select tables that offer versatility in style and size to cater to various home layouts. Cost-effectiveness and the ability to match the local market’s aesthetic trends are also critical considerations.
Why Are Custom Tables Important for Event Management?
In event management, custom tables are vital for creating unique experiences at banquets, weddings, and corporate events. These tables can be tailored to specific themes and layouts, allowing event planners to offer personalized services. International buyers should focus on customization options that allow for easy transport and quick setup, especially in regions with diverse event styles. Sourcing considerations include durability, ease of maintenance, and the ability to accommodate different guest capacities.
How Do Custom Dining Tables Enhance Educational Settings?
In educational institutions, dining tables in cafeterias serve as social hubs for students, promoting interaction and community building. Custom designs can cater to specific age groups or dining styles, enhancing the overall dining experience. Buyers from regions like Europe and Africa should prioritize safety standards, ease of maintenance, and the capacity to accommodate large groups. Sourcing durable materials that can withstand daily use while being easy to clean is essential for this sector.
Related Video: Industrial Steel and Walnut Dining Table
3 Common User Pain Points for ‘dining room table custom’ & Their Solutions
Scenario 1: Understanding Customization Options for Dining Room Tables
The Problem: Many B2B buyers, especially from regions like Africa and South America, struggle to find dining room tables that meet their specific needs and preferences. Buyers often find themselves overwhelmed by the variety of customization options, including size, shape, material, and finish. This lack of clarity can lead to confusion and dissatisfaction, as they may purchase a table that does not align with their intended use or aesthetic preferences.
The Solution: To effectively navigate the customization options for dining room tables, B2B buyers should first conduct thorough research on potential suppliers. This includes reviewing their catalogs, visiting showrooms if possible, or utilizing virtual consultations. Buyers should create a checklist outlining their specific requirements, such as dimensions, materials (e.g., solid wood, glass, or metal), and finishes that match their brand identity or target market aesthetics. Engaging in open communication with suppliers about these requirements can lead to tailored solutions that meet their needs. Additionally, requesting samples or mock-ups can help visualize the final product before making a commitment.
Scenario 2: Dealing with Long Lead Times for Custom Orders
The Problem: Another common issue faced by B2B buyers is the extended lead times associated with custom dining room table orders. In regions such as the Middle East and Europe, where the demand for bespoke furniture is rising, delays in production can disrupt business operations, especially for those in the hospitality and retail sectors who rely on timely delivery for new projects.
The Solution: To mitigate the impact of long lead times, buyers should prioritize suppliers who offer clear timelines and guarantees. It’s essential to establish a timeline during the initial discussions and to include penalties for delays in contracts. Additionally, buyers can consider placing orders well in advance of their anticipated need dates. Another effective strategy is to explore local manufacturers or suppliers who may have shorter production cycles compared to overseas options. Establishing a reliable relationship with a few key suppliers can also create opportunities for quicker turnaround times on future orders.
Scenario 3: Ensuring Quality and Durability in Custom Dining Room Tables
The Problem: Quality assurance is a significant concern for B2B buyers, particularly when investing in custom dining room tables that need to withstand frequent use in commercial settings. Buyers from Europe and Africa, where quality standards can vary widely, often face challenges in determining whether a supplier can deliver a product that meets their durability expectations.
The Solution: To ensure the quality and durability of custom dining room tables, buyers should ask for detailed specifications and certifications from suppliers. This includes inquiries about the materials used, construction techniques, and any warranties provided. Conducting factory visits or audits can also be beneficial in assessing production standards. Additionally, buyers can request references from previous clients to gauge satisfaction levels regarding the quality and longevity of the tables. It is advisable to consider manufacturers that have a solid reputation for producing commercial-grade furniture, as they are more likely to adhere to rigorous quality standards.
Strategic Material Selection Guide for dining room table custom
When selecting materials for custom dining room tables, international B2B buyers must consider various factors that affect the performance, durability, and aesthetic appeal of their products. Here’s an analysis of four common materials used in the manufacturing of dining room tables, along with actionable insights tailored for buyers from Africa, South America, the Middle East, and Europe.
What Are the Key Properties of Solid Wood for Dining Room Tables?
Solid wood is a traditional choice for dining room tables, prized for its natural beauty and durability. Key properties include its strength and resistance to wear, making it suitable for high-traffic areas. It can withstand moderate temperature fluctuations but may warp under extreme conditions.
Pros: Solid wood tables are highly durable and can last for generations if maintained properly. They can be refinished to remove scratches or dents, enhancing their longevity. Additionally, solid wood offers a timeless aesthetic that appeals to a wide range of consumers.
Cons: The main drawbacks are the cost and weight. Solid wood can be expensive, especially for high-quality species like oak or walnut. It is also susceptible to moisture damage and requires regular maintenance, which may not be ideal for all buyers.
Impact on Application: Solid wood is compatible with various finishes, allowing for customization. However, buyers should be aware of the specific wood species’ environmental impact and sourcing regulations, particularly in regions with strict forestry laws.
How Does Plywood Compare as a Material for Dining Room Tables?
Plywood, made from thin layers of wood veneer glued together, offers a versatile alternative to solid wood. Its key properties include excellent dimensional stability and resistance to warping, making it suitable for various climates.
Pros: Plywood is generally more affordable than solid wood and lighter in weight, making it easier to transport and assemble. It also allows for a wide range of design options, including curved shapes and intricate patterns.
Cons: While plywood is durable, it may not have the same aesthetic appeal as solid wood. Additionally, lower-quality plywood can delaminate or warp under extreme conditions, which may affect the table’s longevity.
Impact on Application: Plywood tables can be finished with veneers or laminate for enhanced aesthetics. Buyers should ensure that the plywood meets international quality standards, such as those set by ASTM or JIS, to guarantee performance.
What Are the Advantages of Metal in Dining Room Table Construction?
Metal, particularly stainless steel or aluminum, is increasingly popular for modern dining room tables. Its key properties include high strength, corrosion resistance, and ease of maintenance.
Pros: Metal tables are incredibly durable and can withstand heavy use. They are also resistant to moisture and pests, making them ideal for various environments, including humid regions.
Cons: The main disadvantage is the potential for scratching and denting, which can detract from the table’s appearance. Additionally, metal tables can be heavier and may require specialized handling during transport.
Impact on Application: Metal tables can be combined with wood or glass for a mixed-material aesthetic. Buyers should consider the weight restrictions of their shipping methods and ensure compliance with international shipping standards.
Why Choose Glass for Dining Room Tables?
Glass is a stylish choice for dining room tables, offering a contemporary look. Key properties include transparency and ease of cleaning, but it is less durable than other materials.
Pros: Glass tables can create an illusion of space and are easy to maintain. They are also resistant to stains and odors, making them suitable for dining environments.
Cons: The fragility of glass is a significant limitation; it can chip or shatter if not handled carefully. Additionally, glass tables may require more frequent replacements compared to solid wood or metal options.
Impact on Application: Glass tables can be paired with various bases, including metal or wood. Buyers should ensure that the glass meets safety standards, such as tempered glass regulations, to prevent accidents.
Summary Table of Material Selection for Dining Room Tables
Material | Typical Use Case for dining room table custom | Key Advantage | Key Disadvantage/Limitation | Relative Cost (Low/Med/High) |
---|---|---|---|---|
Solid Wood | Traditional dining tables | Highly durable and refinishable | Expensive and moisture-sensitive | High |
Plywood | Versatile designs and modern aesthetics | Affordable and lightweight | Lower aesthetic appeal and potential delamination | Medium |
Metal | Modern and industrial-style tables | Extremely durable and moisture-resistant | Can scratch easily and heavier to handle | Medium |
Glass | Contemporary and stylish dining tables | Easy to clean and maintain | Fragile and requires careful handling | Medium |
This strategic material selection guide provides valuable insights for B2B buyers looking to make informed decisions when sourcing custom dining room tables. By understanding the properties, advantages, and limitations of each material, buyers can better align their product offerings with market demands and regional preferences.
In-depth Look: Manufacturing Processes and Quality Assurance for dining room table custom
What Are the Main Stages of Manufacturing Custom Dining Room Tables?
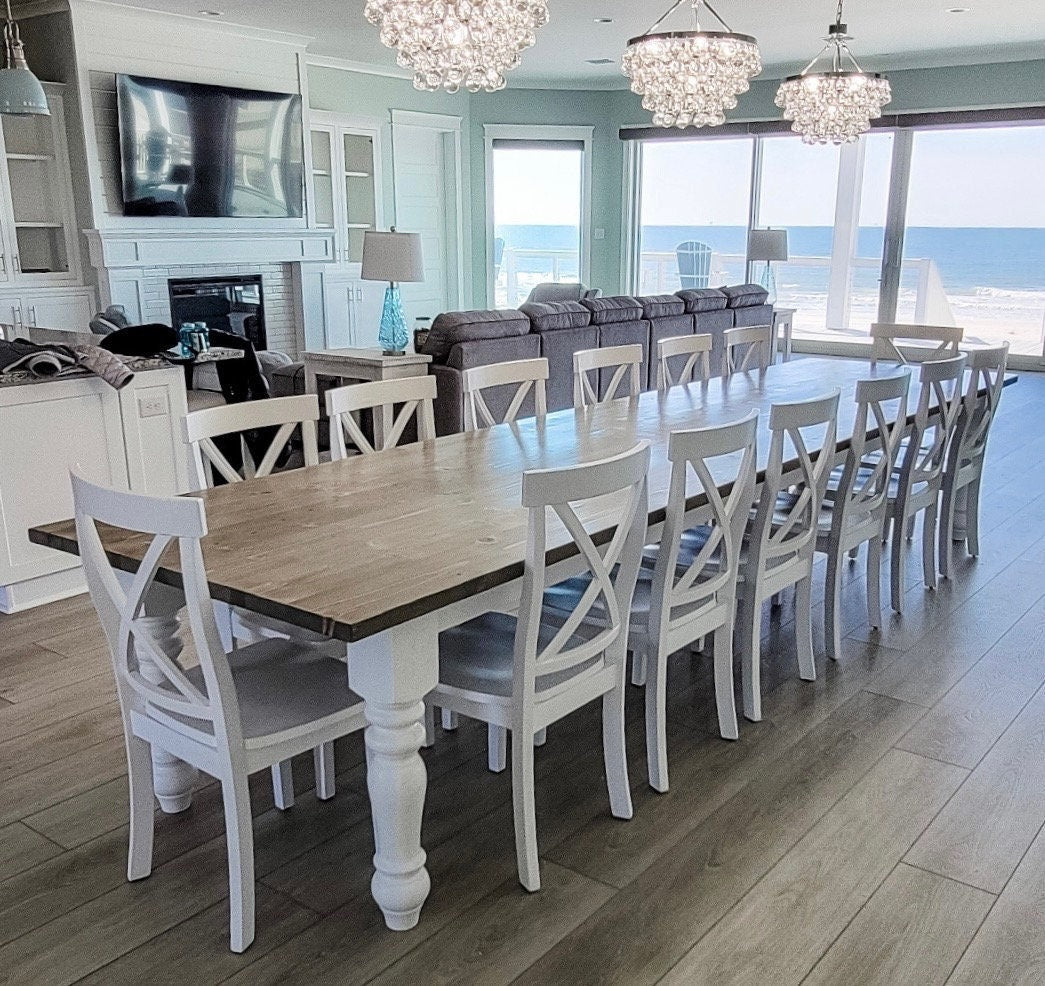
A stock image related to dining room table custom.
The manufacturing process for custom dining room tables involves several critical stages, each designed to ensure quality, precision, and durability. Understanding these stages is vital for international B2B buyers who are sourcing furniture from manufacturers, especially in regions like Africa, South America, the Middle East, and Europe.
-
Material Preparation
– Selection of Raw Materials: The process begins with sourcing high-quality materials such as hardwood, veneer, or engineered wood. Buyers should inquire about the origin of the wood and any sustainable practices employed by suppliers.
– Cutting and Drying: The raw materials are cut to size and then dried to a specific moisture content. This step is crucial as it prevents warping and cracking in the final product. B2B buyers should request certificates of moisture content and wood treatment processes. -
Forming the Table Components
– Shaping: The cut materials are shaped into the various components of the table, including the tabletop, legs, and any additional features like extensions or drawers. Techniques such as CNC machining provide precision and consistency.
– Joining Techniques: Different methods like mortise and tenon, dowel joints, or modern adhesives are employed to ensure strong connections. Buyers should understand the joining techniques used as they directly affect the table’s durability. -
Assembly
– Initial Assembly: The table components are assembled using appropriate fasteners and techniques. During this stage, manufacturers check for fit and finish.
– Final Assembly and Detailing: After initial assembly, the table undergoes final adjustments, including sanding and smoothing edges. This ensures that the table is not only functional but also aesthetically pleasing. -
Finishing
– Staining and Sealing: The finished table is stained and sealed to enhance its appearance and protect it from moisture and scratches. Common finishes include polyurethane, lacquer, and oil-based products.
– Quality Checks: Before moving to the next stage, the table undergoes a quality check to ensure that the finish is even and free of defects.
How Is Quality Assurance Implemented in Custom Dining Room Table Manufacturing?
Quality assurance (QA) is a fundamental aspect of manufacturing custom dining room tables, ensuring that the final product meets both regulatory standards and customer expectations. B2B buyers should be familiar with the various QA protocols and international standards that apply.
-
International Standards and Certifications
– ISO 9001: Many manufacturers adhere to ISO 9001, a quality management standard that outlines the requirements for an effective quality management system (QMS). This certification indicates a commitment to quality and customer satisfaction.
– CE Marking: In Europe, the CE marking indicates that the product meets EU safety, health, and environmental protection requirements. Buyers should ensure that their suppliers possess this certification if they are exporting to European markets. -
Quality Control Checkpoints
– Incoming Quality Control (IQC): At this stage, raw materials are inspected for quality and compliance with specifications before they are accepted into the manufacturing process.
– In-Process Quality Control (IPQC): Ongoing inspections are conducted during the manufacturing process to catch defects early. This includes checking the dimensions, fit, and assembly of components.
– Final Quality Control (FQC): Once the tables are fully assembled and finished, a final inspection is performed to ensure that they meet the required standards and specifications. -
Common Testing Methods
– Durability Testing: Manufacturers often conduct stress tests to evaluate the table’s strength and stability under load.
– Finish Testing: This includes scratch resistance and moisture absorption tests to ensure that the finish will withstand daily use.
How Can B2B Buyers Verify Supplier Quality Control?
For international B2B buyers, verifying the quality control measures of potential suppliers is essential to ensure that they receive products that meet their expectations. Here are some actionable strategies:
-
Conducting Supplier Audits
– Site Visits: If feasible, conducting site visits to the manufacturing facility allows buyers to assess the production processes, quality control systems, and overall working conditions.
– Third-Party Audits: Engaging third-party inspection services can provide an unbiased evaluation of the supplier’s quality control measures and manufacturing capabilities. -
Requesting Quality Assurance Documentation
– Certificates and Reports: Buyers should request copies of relevant certifications (ISO, CE) and recent quality control reports. This documentation provides insight into the supplier’s adherence to quality standards.
– Testing Results: Suppliers should be willing to share results from durability and finish testing. This transparency is a good indicator of the supplier’s commitment to quality. -
Understanding QC/CERT Nuances for International Buyers
– Regulatory Compliance: Buyers from different regions should be aware of local regulations that may affect the import of furniture. Understanding these regulations helps ensure compliance and avoid costly delays.
– Cultural Considerations: Different regions may have varying standards for quality. Buyers should communicate clearly with suppliers about their specific quality expectations to avoid misunderstandings.
Conclusion: Prioritizing Quality in Sourcing Custom Dining Room Tables
By understanding the manufacturing processes and quality assurance measures involved in producing custom dining room tables, international B2B buyers can make informed decisions. The key lies in thorough supplier evaluations, a clear understanding of international standards, and proactive engagement in the quality assurance process. This approach not only enhances the likelihood of receiving high-quality products but also fosters long-term relationships with reliable suppliers.
Practical Sourcing Guide: A Step-by-Step Checklist for ‘dining room table custom’
To effectively source a custom dining room table, B2B buyers must navigate a structured process that ensures quality, compliance, and alignment with business needs. This guide serves as a practical checklist, providing actionable insights tailored for international buyers from regions such as Africa, South America, the Middle East, and Europe.
Step 1: Define Your Requirements Clearly
Establishing precise specifications for your custom dining room table is crucial. This includes dimensions, materials (wood type, finish), design style, and functionality (e.g., extendable options). Clear requirements help in obtaining accurate quotes and prevent misunderstandings with suppliers.
- Key Considerations:
- What style fits your brand’s aesthetic?
- Are there specific materials that align with sustainability goals?
Step 2: Research Potential Suppliers
Conduct thorough research to identify suppliers with a strong track record in custom furniture manufacturing. Look for reviews, testimonials, and industry reputation. This step is critical to finding reliable partners who can meet your standards.
- Tips for Research:
- Use online directories and trade platforms like Alibaba or Global Sources.
- Attend industry trade shows or exhibitions to meet suppliers in person.
Step 3: Evaluate Supplier Certifications and Compliance
Ensure that potential suppliers possess relevant certifications, such as ISO or FSC, which indicate adherence to quality standards and sustainable practices. This not only enhances trust but also aligns with global regulations that may affect your business.
- What to Check:
- Are their certifications up-to-date?
- Do they comply with your country’s import regulations?
Step 4: Request Samples and Prototypes
Before placing a bulk order, request samples or prototypes to evaluate the quality of materials and craftsmanship. This is a vital step to confirm that the final product will meet your expectations.
- Sample Evaluation:
- Examine the finish and durability of the materials.
- Test the functionality if applicable (e.g., extendable mechanisms).
Step 5: Compare Pricing and Payment Terms
Gather quotes from multiple suppliers and compare not just the prices but also the payment terms. Look for transparency in pricing structures, including shipping and taxes, to avoid unexpected costs.
- Considerations for Comparison:
- Are there bulk order discounts?
- What are the payment milestones (e.g., deposits, balance)?
Step 6: Negotiate Terms and Conditions
Once you have selected a supplier, negotiate terms and conditions, including lead times, warranties, and after-sales support. Clear agreements help mitigate risks and set expectations for both parties.
- Important Aspects to Cover:
- What is the expected delivery timeline?
- What warranty or return policy is offered?
Step 7: Establish Ongoing Communication and Support
Maintain open lines of communication with your supplier throughout the production process. Regular updates on progress can help manage expectations and address any issues promptly.
- Communication Tips:
- Schedule regular check-ins via email or video calls.
- Utilize project management tools for transparency and tracking.
By following this step-by-step checklist, B2B buyers can streamline the sourcing process for custom dining room tables, ensuring they partner with the right suppliers and receive quality products that meet their business needs.
Comprehensive Cost and Pricing Analysis for dining room table custom Sourcing
What Are the Key Cost Components in Custom Dining Room Table Sourcing?
When sourcing custom dining room tables, it’s crucial to understand the cost structure involved. The main components include:
-
Materials: The choice of wood, metal, or composite materials significantly impacts the overall cost. High-quality woods such as oak or walnut will demand a premium, while more economical options like pine may reduce costs.
-
Labor: Labor costs vary based on the complexity of the design and the skill level required for craftsmanship. Custom designs often require skilled artisans, which can raise labor costs.
-
Manufacturing Overhead: This encompasses the indirect costs associated with production, such as utilities, rent, and equipment maintenance. These expenses can be substantial, especially for small-scale manufacturers.
-
Tooling: Custom designs may necessitate specific tools or molds, which can incur additional one-time costs. It’s important to factor in these expenses when budgeting.
-
Quality Control (QC): Ensuring that the final product meets quality standards is critical. QC processes can add to labor and overhead costs, but they are essential for maintaining product integrity.
-
Logistics: Transportation and handling costs are significant, especially for international shipments. Consider the distance, mode of transport, and any potential tariffs or duties.
-
Margin: Suppliers will typically add a profit margin to cover their costs and ensure profitability. Understanding typical margins in the industry can help buyers negotiate better prices.
How Do Price Influencers Impact Custom Dining Room Table Costs?
Several factors can influence the pricing of custom dining room tables:
-
Volume/MOQ (Minimum Order Quantity): Ordering in larger quantities can lead to significant discounts. Suppliers often have tiered pricing models, so understanding these can help in negotiations.
-
Specifications and Customization: The more customized the table, the higher the cost. Buyers should clearly define their specifications to avoid unexpected charges.
-
Materials and Quality: Higher quality materials and certifications (e.g., FSC-certified wood) can increase costs. Buyers should assess their quality requirements against their budget.
-
Supplier Factors: The reputation and location of the supplier can affect pricing. Established suppliers may charge more due to their experience and reliability.
-
Incoterms: The chosen Incoterms (International Commercial Terms) dictate who bears shipping costs and risks. Understanding these terms can prevent cost surprises down the line.
What Are the Best Tips for Negotiating Custom Dining Room Table Prices?
For international B2B buyers, particularly those from Africa, South America, the Middle East, and Europe, here are actionable tips:
-
Conduct Comprehensive Research: Understand the market rates for materials and craftsmanship in your region. Knowledge of local pricing can empower your negotiations.
-
Leverage Total Cost of Ownership (TCO): Consider not only the purchase price but also long-term costs such as maintenance and durability. A slightly higher upfront cost may lead to savings over time.
-
Negotiate Terms: Don’t hesitate to negotiate payment terms, delivery schedules, and warranties. Favorable terms can enhance the overall value of the deal.
-
Evaluate Supplier Relationships: Building long-term relationships with suppliers can lead to better pricing and priority service. Consider establishing partnerships rather than one-off transactions.
-
Be Aware of Pricing Nuances: Understand the cultural differences in negotiating styles across regions. For example, European buyers may prioritize quality, while South American buyers might focus on price.
Conclusion: What Should You Remember About Custom Dining Room Table Pricing?
In summary, understanding the comprehensive cost and pricing structure for custom dining room tables is essential for making informed purchasing decisions. By considering the various cost components, price influencers, and negotiation strategies, international B2B buyers can ensure they secure the best value for their investment. Keep in mind that prices can vary widely based on the factors discussed, and it is advisable to obtain multiple quotes before making a decision. Always treat quoted prices as indicative and subject to change based on specific requirements and market conditions.
Alternatives Analysis: Comparing dining room table custom With Other Solutions
When considering the purchase of a dining room table, B2B buyers have several alternatives to explore beyond custom solutions. Each option comes with its own set of advantages and challenges, which can significantly affect the decision-making process. This analysis will compare ‘dining room table custom’ with two viable alternatives: ‘Pre-fabricated Dining Room Tables’ and ‘Reclaimed Wood Tables’.
Comparison Table of Dining Room Table Custom and Alternatives
Comparison Aspect | Dining Room Table Custom | Pre-fabricated Dining Room Tables | Reclaimed Wood Tables |
---|---|---|---|
Performance | High durability and design flexibility | Moderate durability, limited customization | High durability, unique aesthetics |
Cost | Higher cost due to custom materials and craftsmanship | Lower cost, mass-produced | Moderate cost, varies based on sourcing |
Ease of Implementation | Requires design and manufacturing time | Immediate availability | Requires sourcing and restoration time |
Maintenance | Low maintenance, depends on materials used | Low maintenance | Moderate maintenance, prone to wear |
Best Use Case | Unique spaces or high-end markets | Budget-conscious clients or quick setups | Eco-conscious clients or rustic designs |
What Are the Pros and Cons of Pre-fabricated Dining Room Tables?
Pre-fabricated dining room tables are mass-produced, making them readily available and often more affordable than custom options. They come in various styles and finishes, appealing to a broad audience. However, the trade-off is a lack of personalization, which may not suit businesses seeking a unique identity or specific brand aesthetics. For example, a restaurant aiming to create a distinctive dining experience might find pre-fabricated tables insufficiently aligned with their brand image.
What Are the Advantages and Disadvantages of Reclaimed Wood Tables?
Reclaimed wood tables present a sustainable option, appealing to eco-conscious buyers. Each piece carries a unique history, providing character and charm that can enhance a dining space. However, the sourcing process can be time-consuming, and the condition of reclaimed wood can vary significantly, which may lead to higher maintenance costs in the long term. Businesses that prioritize sustainability and unique aesthetics may find reclaimed wood tables particularly attractive, while others might struggle with the variability in quality.
How Can B2B Buyers Choose the Right Dining Room Table Solution?
When selecting a dining room table solution, B2B buyers should consider their specific needs, including budget, aesthetics, and intended use. Custom tables offer unparalleled personalization and quality, ideal for high-end establishments or unique spaces. In contrast, pre-fabricated tables can meet the demands of budget-conscious clients who need quick solutions without the wait. Reclaimed wood tables serve a niche market focused on sustainability and unique design but may require more effort in sourcing and maintenance. By carefully evaluating these factors, buyers can make informed decisions that align with their business objectives and brand identity.
Essential Technical Properties and Trade Terminology for dining room table custom
When sourcing custom dining room tables, understanding essential technical properties and trade terminology is crucial for international B2B buyers. This knowledge not only streamlines the purchasing process but also ensures that the final product meets quality standards and operational needs.
What Are the Key Technical Properties for Custom Dining Room Tables?
1. Material Grade
The material grade refers to the quality and type of materials used in the construction of the table, such as hardwood, softwood, or engineered wood. High-grade materials ensure durability and aesthetic appeal, which is vital for long-term investment. Buyers should request certifications or specifications to verify material quality.
2. Tolerance Levels
Tolerance levels indicate the allowable variation in dimensions during manufacturing. For instance, a dining table may need to adhere to specific height and width tolerances to ensure compatibility with existing furniture. Precise tolerances are essential to avoid issues during assembly and usage, especially in commercial settings.
3. Finish and Coating
The finish of the table can affect both aesthetics and durability. Common finishes include lacquer, varnish, or oil, each providing different levels of protection and appearance. Understanding the finish is crucial for maintenance and longevity, as some finishes may require more frequent care than others.
4. Load Capacity
Load capacity refers to the maximum weight the table can safely support. This is particularly important for commercial buyers who may use the table for dining services or events. Buyers should inquire about load testing and certifications to ensure the table meets safety standards.
5. Dimensions and Customization Options
Understanding the dimensions of the table is critical for fitting into designated spaces. Buyers should also consider customization options, such as shape, size, and additional features like extendable leaves. Clear communication about these specifications can prevent costly adjustments later.
Which Trade Terms Should B2B Buyers Understand When Ordering Custom Dining Room Tables?
1. OEM (Original Equipment Manufacturer)
OEM refers to a company that produces goods for another company under the latter’s brand name. In the context of custom dining room tables, understanding OEM relationships can help buyers identify reliable manufacturers who can meet their specific design and quality requirements.
2. MOQ (Minimum Order Quantity)
MOQ is the smallest quantity of a product that a supplier is willing to sell. For custom dining room tables, MOQs can vary significantly based on material and design complexity. Buyers should negotiate MOQs to align with their inventory needs while ensuring cost-effectiveness.
3. RFQ (Request for Quotation)
An RFQ is a document that solicits price bids from suppliers for specific products or services. When seeking custom dining room tables, submitting an RFQ allows buyers to compare prices and terms from multiple manufacturers, facilitating informed decision-making.
4. Incoterms (International Commercial Terms)
Incoterms are a series of predefined commercial terms published by the International Chamber of Commerce (ICC) that clarify the responsibilities of buyers and sellers in international transactions. Familiarity with Incoterms helps buyers understand shipping costs, risks, and responsibilities, ensuring smooth logistics.
5. Lead Time
Lead time refers to the time taken from placing an order to receiving the product. For custom dining room tables, lead times can vary based on complexity and supplier capacity. Understanding lead times is crucial for planning inventory and meeting customer demands.
Conclusion
For international B2B buyers, especially those in Africa, South America, the Middle East, and Europe, grasping these technical properties and trade terminologies is vital. This knowledge empowers buyers to make informed decisions, ensuring that the custom dining room tables they procure meet their specifications and business needs. By prioritizing quality materials, understanding manufacturing tolerances, and navigating trade terms effectively, buyers can enhance their procurement processes and build lasting supplier relationships.
Navigating Market Dynamics and Sourcing Trends in the dining room table custom Sector
What Are the Current Market Dynamics and Sourcing Trends in the Dining Room Table Custom Sector?
The dining room table custom sector is experiencing significant shifts driven by globalization, changing consumer preferences, and advancements in technology. International B2B buyers, particularly from regions such as Africa, South America, the Middle East, and Europe, are increasingly looking for suppliers who can provide unique, customized solutions. This trend is largely fueled by the rise of e-commerce platforms and digital marketplaces, which facilitate easier access to a broader range of manufacturers.
Moreover, the demand for multifunctional furniture has surged, as buyers seek products that can adapt to various needs, especially in urban environments where space is limited. Custom dining tables that offer flexibility in size and design are particularly appealing. Another key trend is the integration of smart technology into dining furniture, such as tables equipped with charging ports or Bluetooth speakers, aligning with the modern consumer’s lifestyle.
Additionally, trends in materials are evolving. Sustainable materials, including reclaimed wood and eco-friendly finishes, are gaining traction, reflecting a broader shift towards environmentally responsible sourcing. B2B buyers should be proactive in identifying suppliers who align with these trends, as doing so can provide a competitive edge in the market.
How Can Sustainability and Ethical Sourcing Impact Your Dining Room Table Custom Purchases?
Sustainability and ethical sourcing have become critical considerations for B2B buyers in the dining room table custom sector. The environmental impact of furniture production, including deforestation and waste generation, has prompted many companies to adopt more responsible practices. Buyers are increasingly prioritizing suppliers who demonstrate a commitment to sustainability through certifications such as Forest Stewardship Council (FSC) or sustainable materials like bamboo.
Ethical supply chains are also essential, especially in regions where labor practices may be scrutinized. Ensuring that suppliers adhere to fair labor practices and provide safe working conditions not only supports ethical business practices but also enhances brand reputation.
Furthermore, the demand for “green” certifications is on the rise among consumers, who are willing to pay a premium for environmentally friendly products. B2B buyers should consider partnering with manufacturers who offer transparency in their sourcing and production processes, as this can lead to more sustainable business practices and cater to a growing market segment focused on ethical consumption.
How Has the Dining Room Table Custom Market Evolved Over Time?
The dining room table custom market has undergone significant transformation over the decades. Initially dominated by traditional craftsmanship, the sector has increasingly embraced industrial methods to meet growing demand. The introduction of mass production techniques allowed for greater scalability, but it often compromised uniqueness and quality.
In recent years, there has been a resurgence of interest in artisanal and handcrafted products, as consumers seek to differentiate their homes with unique pieces. This shift has been bolstered by advancements in technology, such as 3D modeling and CNC machining, which enable manufacturers to offer customization at scale without sacrificing quality.
Today, the dining room table custom market is characterized by a blend of traditional craftsmanship and modern technology, catering to a diverse clientele that values both aesthetics and functionality. For B2B buyers, understanding this evolution is crucial for making informed sourcing decisions that align with current market demands.
Frequently Asked Questions (FAQs) for B2B Buyers of dining room table custom
-
How do I ensure quality when sourcing custom dining room tables?
To ensure quality when sourcing custom dining room tables, start by conducting thorough research on potential suppliers. Look for manufacturers with a solid reputation, verified certifications, and positive customer reviews. Request samples of their previous work to assess the craftsmanship and materials used. Additionally, consider visiting the factory if feasible or using third-party inspection services to evaluate the production process. Establish clear quality assurance standards in your contract to hold suppliers accountable for meeting your specifications. -
What are the best materials for custom dining room tables?
The best materials for custom dining room tables depend on your target market’s preferences and durability requirements. Solid wood, such as oak or walnut, offers timeless elegance and durability. Metal bases can provide a modern touch while ensuring stability. For a more cost-effective option, consider engineered wood or laminate surfaces that mimic the look of natural materials. Ensure that the materials you select align with your brand identity and the expectations of your customers in regions like Africa, South America, the Middle East, and Europe. -
What customization options are typically available for dining room tables?
Customization options for dining room tables can include size, shape, finish, and material. Many manufacturers offer choices between rectangular, round, or square designs, accommodating various dining spaces. You can also specify color finishes, such as stains or paints, to match existing décor. Additionally, consider offering features like extendable leaves for larger gatherings or unique designs that cater to cultural preferences in your target markets. Discuss these options early in the negotiation process to ensure they fit your business model.
-
How do I determine the minimum order quantity (MOQ) for custom dining room tables?
The minimum order quantity (MOQ) for custom dining room tables varies by supplier and can depend on factors such as material costs and production capabilities. To negotiate a favorable MOQ, research industry standards and communicate your expected sales volume to suppliers. Some manufacturers may be willing to accommodate smaller orders for new clients or offer tiered pricing based on order size. Always clarify the MOQ upfront to avoid unexpected costs or delays in production. -
What payment terms should I negotiate when sourcing custom dining room tables?
When negotiating payment terms, consider options such as a deposit upfront, followed by the balance upon delivery or inspection of the goods. Standard practices often involve a 30-50% deposit, with the remaining payment due before shipment. For larger orders, you might negotiate more favorable terms, such as extended payment periods or installment payments. Ensure that these terms are clearly outlined in your contract to protect both parties and facilitate smoother transactions. -
How can I vet suppliers for custom dining room tables effectively?
Vetting suppliers for custom dining room tables involves multiple steps. Start by checking their business licenses and certifications to ensure legitimacy. Review customer testimonials and case studies to gauge their reliability. Utilize platforms like Alibaba or Global Sources to access supplier ratings. Furthermore, consider conducting video calls or factory visits to assess their production capabilities and quality control processes. Establishing a relationship based on transparency and communication will lead to successful long-term partnerships. -
What logistics considerations should I keep in mind when importing custom dining room tables?
Logistics for importing custom dining room tables involve several key considerations, including shipping methods, customs clearance, and delivery timelines. Choose between air freight for speed or sea freight for cost-effectiveness, factoring in your budget and urgency. Research customs regulations in your destination countries to avoid delays and additional fees. Collaborate with experienced freight forwarders to manage shipping logistics and ensure that your products are delivered safely and on time. -
How do I handle quality assurance (QA) for custom dining room tables after delivery?
To handle quality assurance (QA) for custom dining room tables after delivery, implement a systematic inspection process. Upon receipt, check for any damages or defects and ensure that the tables meet the agreed-upon specifications. Establish a feedback loop with your customers to gather insights on product performance and quality. If issues arise, maintain open communication with your supplier to address concerns promptly and negotiate resolutions. Regularly review QA processes to enhance future orders and maintain high standards.
Important Disclaimer & Terms of Use
⚠️ Important Disclaimer
The information provided in this guide, including content regarding manufacturers, technical specifications, and market analysis, is for informational and educational purposes only. It does not constitute professional procurement advice, financial advice, or legal advice.
While we have made every effort to ensure the accuracy and timeliness of the information, we are not responsible for any errors, omissions, or outdated information. Market conditions, company details, and technical standards are subject to change.
B2B buyers must conduct their own independent and thorough due diligence before making any purchasing decisions. This includes contacting suppliers directly, verifying certifications, requesting samples, and seeking professional consultation. The risk of relying on any information in this guide is borne solely by the reader.
Strategic Sourcing Conclusion and Outlook for dining room table custom
As the global market for custom dining room tables continues to evolve, the importance of strategic sourcing cannot be overstated. By prioritizing quality, sustainability, and supplier relationships, international B2B buyers can secure a competitive edge. Understanding the unique needs of diverse markets in Africa, South America, the Middle East, and Europe is crucial for tailoring product offerings that resonate with local consumers.
What are the key takeaways for B2B buyers in the custom dining room table sector? First, leverage data-driven insights to identify trends and preferences within target markets. Second, establish transparent communication with suppliers to ensure alignment on design specifications, timelines, and ethical sourcing practices. Lastly, remain adaptable to changing market dynamics, as consumer preferences shift towards eco-friendly materials and innovative designs.
Looking forward, the potential for growth in the custom dining room table market is substantial. By engaging with reputable suppliers and embracing a proactive sourcing strategy, businesses can not only meet current demands but also anticipate future trends. Now is the time to act—invest in strategic sourcing initiatives that will elevate your product offerings and enhance customer satisfaction in a competitive landscape.