Elevate Your Space: Custom Sectional Sofa Solutions (2025)
Introduction: Navigating the Global Market for sectional sofa custom
Navigating the global market for custom sectional sofas can be a daunting task for B2B buyers, especially when sourcing high-quality products that meet specific design and comfort needs. This guide addresses the critical challenge of selecting the right suppliers and products in a competitive landscape, ensuring that your business stands out. As you delve into the intricacies of custom sectional sofas, you’ll discover various types, applications, and essential considerations for vetting suppliers effectively.
In this comprehensive guide, we aim to empower international B2B buyers—particularly those from Africa, South America, the Middle East, and Europe (including countries like France and Germany)—with the knowledge necessary to make informed purchasing decisions. We will explore different styles of sectional sofas, ranging from contemporary to traditional designs, and discuss their applications in various settings, such as hotels, offices, and residential projects.
Additionally, we will provide insights into cost factors, including material selection and manufacturing processes, helping you understand the investment required for quality products. By the end of this guide, you will have a robust framework for evaluating potential suppliers and making purchasing decisions that align with your business objectives, ultimately enhancing your offerings and customer satisfaction.
Understanding sectional sofa custom Types and Variations
Type Name | Key Distinguishing Features | Primary B2B Applications | Brief Pros & Cons for Buyers |
---|---|---|---|
L-Shaped Sectional | Configured in an L-shape, ideal for corners | Office lounges, small apartments | Pros: Space-efficient, versatile layout. Cons: Limited seating capacity compared to larger models. |
U-Shaped Sectional | Offers ample seating, shaped like a U | Large offices, family entertainment areas | Pros: Comfortable for large gatherings. Cons: Requires more space, can be bulky. |
Chaise Sectional | Features an extended seat for lounging | Waiting areas, relaxation lounges | Pros: Provides relaxation, stylish. Cons: Less formal seating arrangement. |
Modular Sectional | Composed of separate pieces for flexible arrangements | Co-working spaces, event venues | Pros: Highly customizable, easy to reconfigure. Cons: May require additional purchases for full setup. |
Sleeper Sectional | Converts into a bed for overnight guests | Hotels, guest rooms, multi-functional spaces | Pros: Space-saving, dual functionality. Cons: May sacrifice comfort for bed feature. |
What are the characteristics of L-Shaped Sectionals and their suitability for B2B buyers?
L-shaped sectionals are designed to fit snugly into corners, making them an excellent choice for maximizing space in smaller environments. They typically provide a comfortable seating area while allowing for easy movement around the room. For B2B buyers, such as those outfitting office lounges or small apartments, these sectionals offer a practical solution that balances aesthetics and functionality. When purchasing, consider fabric durability and ease of maintenance, especially in high-traffic areas.
Why choose U-Shaped Sectionals for large spaces in B2B environments?
U-shaped sectionals are perfect for larger spaces, providing ample seating for gatherings. Their design encourages social interaction, making them ideal for offices or family entertainment areas. B2B buyers should assess the dimensions of their space to ensure that the sectional fits comfortably without overwhelming the room. Additionally, consider upholstery options that can withstand frequent use, as these sectionals are often the centerpiece of social spaces.
How does a Chaise Sectional enhance relaxation in commercial settings?
Chaise sectionals feature an extended seat that invites relaxation, making them a stylish addition to waiting areas or relaxation lounges. They offer a more casual seating option, which can create a welcoming atmosphere for guests. When considering a chaise sectional for B2B use, focus on comfort and aesthetic appeal, as these factors can significantly impact the overall ambiance of the space. Additionally, choose materials that are easy to clean and maintain.
What advantages do Modular Sectionals provide for dynamic workspaces?
Modular sectionals consist of separate pieces that can be rearranged to suit various layouts, making them highly adaptable for co-working spaces and event venues. This flexibility allows businesses to respond to changing needs, such as accommodating different group sizes or purposes. B2B buyers should evaluate the ease of assembly and disassembly, as well as the durability of the connectors between pieces, ensuring that the sectional can withstand frequent reconfigurations.
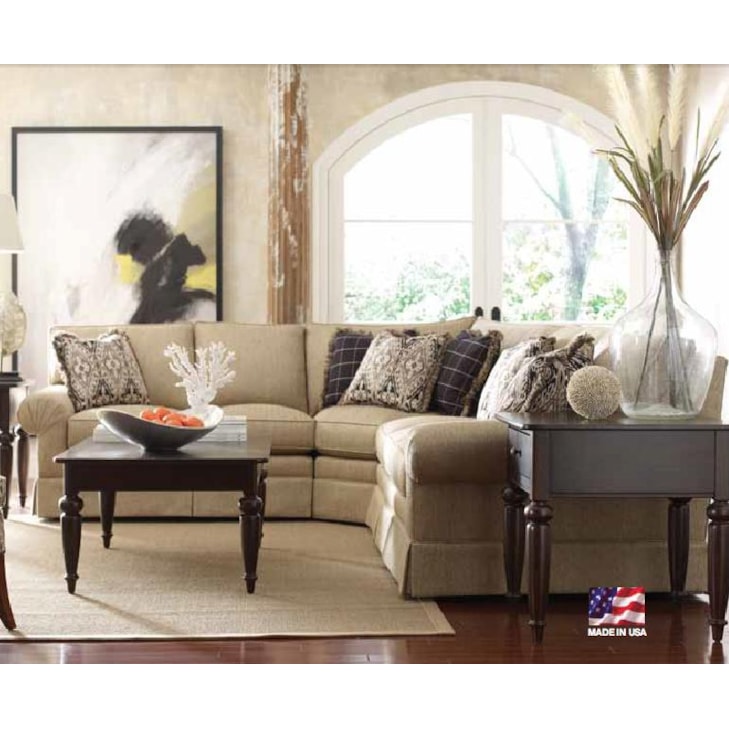
A stock image related to sectional sofa custom.
Why consider Sleeper Sectionals for multi-functional spaces in B2B?
Sleeper sectionals serve dual purposes by converting into beds, making them an excellent choice for hotels or guest rooms that require versatility. They allow businesses to maximize their space without compromising on comfort. When selecting a sleeper sectional, B2B buyers should assess the mattress quality and ease of conversion, as this can influence guest satisfaction. Additionally, consider the sectional’s overall design to ensure it aligns with the brand’s aesthetic.
Related Video: Smart and Durable VALLENTUNA Sectional Sofa – IKEA Home Tour
Key Industrial Applications of sectional sofa custom
Industry/Sector | Specific Application of sectional sofa custom | Value/Benefit for the Business | Key Sourcing Considerations for this Application |
---|---|---|---|
Hospitality | Custom lounge areas in hotels and resorts | Enhances guest comfort and satisfaction, leading to repeat business | Durability, design aesthetics, and ease of maintenance |
Corporate Offices | Collaborative spaces with sectional sofas for break rooms | Fosters employee interaction and creativity | Ergonomics, modularity, and customization options |
Healthcare | Waiting areas in clinics and hospitals | Provides comfort for patients and families | Hygiene standards, durability, and easy cleaning materials |
Event Management | Lounge setups for conferences and exhibitions | Creates inviting environments that encourage networking | Portability, design flexibility, and quick assembly |
Retail Spaces | Display areas in furniture and lifestyle stores | Attracts customers and enhances the shopping experience | Trend alignment, durability, and the ability to customize for seasonal themes |
How Can Hospitality Benefit from Custom Sectional Sofas?
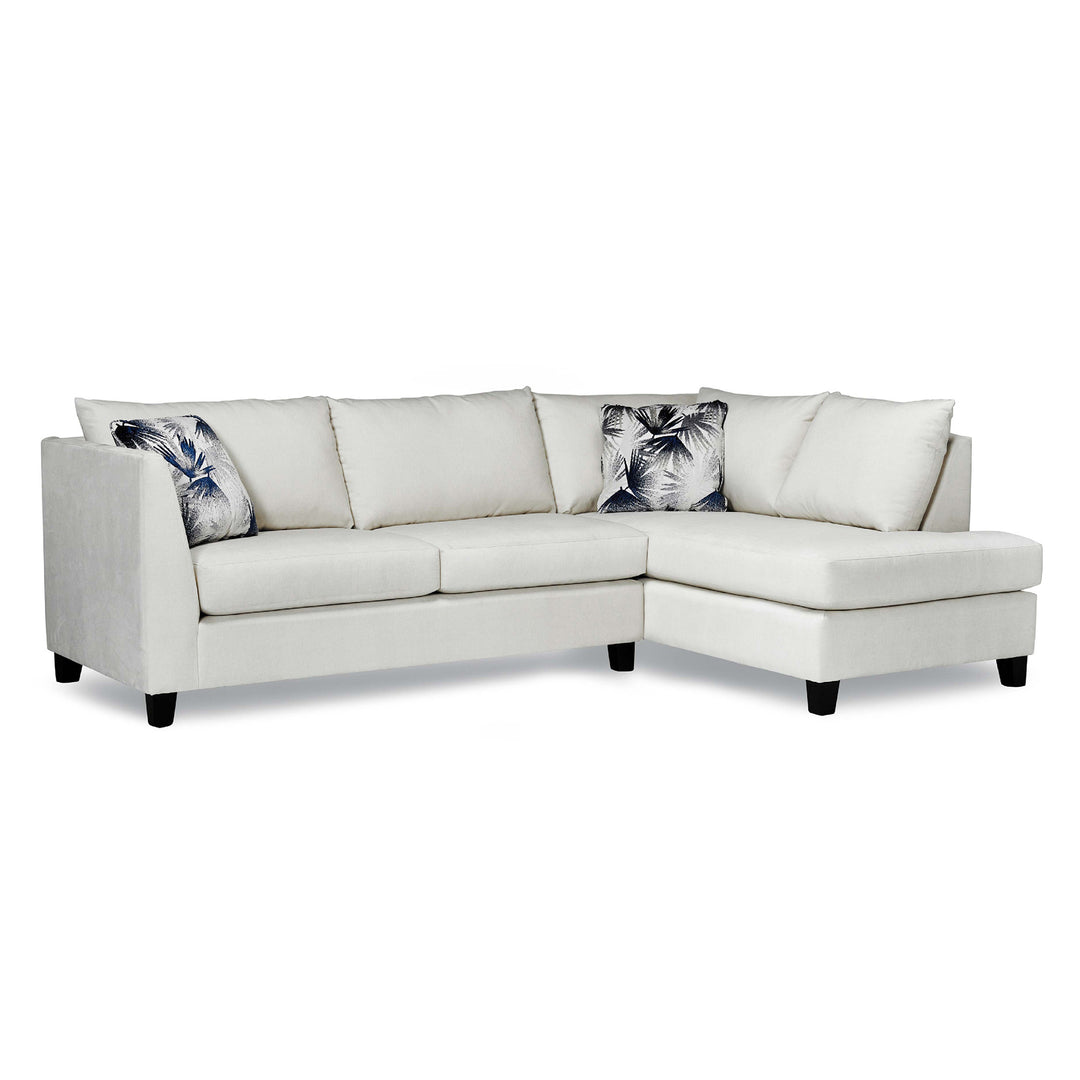
A stock image related to sectional sofa custom.
In the hospitality industry, custom sectional sofas are pivotal in creating inviting lounge areas within hotels and resorts. These tailored seating solutions enhance guest comfort, positively impacting their overall experience and encouraging repeat visits. International buyers, particularly from regions like Africa and Europe, need to consider the durability and maintenance of the materials used in these sofas, as they must withstand heavy use while maintaining aesthetic appeal.
What Role Do Custom Sectional Sofas Play in Corporate Offices?
In corporate settings, custom sectional sofas are increasingly used in collaborative spaces and break rooms. These sofas promote employee interaction and creativity, essential for fostering a positive work environment. For B2B buyers from South America and the Middle East, ergonomic design and modularity are critical factors, allowing for easy rearrangement to meet the changing needs of the workspace.
Why Are Custom Sectional Sofas Important in Healthcare?
Healthcare facilities, such as clinics and hospitals, utilize custom sectional sofas in waiting areas to provide comfort for patients and their families. This approach not only enhances the patient experience but also contributes to a calming atmosphere. Buyers in this sector must prioritize hygiene standards and select materials that are durable and easy to clean, ensuring that the furniture remains functional and visually appealing over time.
How Do Event Management Companies Utilize Custom Sectional Sofas?
Event management companies leverage custom sectional sofas to create lounge setups for conferences and exhibitions. These sofas help form inviting environments that encourage networking and social interaction among attendees. For buyers in Europe and Africa, considerations around portability and design flexibility are vital, as they often require furniture that can be easily transported and reconfigured to suit various event layouts.
What Benefits Do Retail Spaces Gain from Custom Sectional Sofas?
In retail spaces, custom sectional sofas serve as display areas that attract customers and enhance the shopping experience. By integrating stylish and comfortable seating, retailers can create inviting atmospheres that encourage longer visits. B2B buyers should focus on trend alignment and the durability of these sofas, as they need to withstand the rigors of high foot traffic while remaining visually appealing throughout different seasons.
Related Video: How to Build a 2×4 Outdoor Sectional Tutorial
3 Common User Pain Points for ‘sectional sofa custom’ & Their Solutions
Scenario 1: Difficulty in Customizing Sectional Sofas to Fit Unique Spaces
The Problem: International B2B buyers often encounter challenges when trying to customize sectional sofas to fit unique spaces, especially in commercial environments like hotels, offices, or showrooms. Many manufacturers offer limited sizes or configurations, which can lead to wasted space or awkward layouts. Additionally, buyers may struggle with understanding the dimensions and configurations that would work best for their specific environments, causing delays and dissatisfaction with the final product.
The Solution: To overcome these challenges, B2B buyers should conduct a thorough space analysis before placing an order. This involves measuring the area where the sectional sofa will be placed, considering factors such as doorways, window placements, and existing furniture. It’s advisable to collaborate with an interior designer who specializes in commercial spaces to create a layout plan that maximizes usability and aesthetics. Once the measurements are established, buyers can communicate their needs to manufacturers, specifying not only the dimensions but also any particular features they require, such as modular designs or built-in storage. Utilizing 3D modeling software can also help visualize how different configurations will fit within the space, ensuring that the final product meets expectations.
Scenario 2: Concerns Over Material Quality and Durability
The Problem: Buyers from regions such as Africa and South America may have concerns about the quality and durability of materials used in sectional sofas, especially given varying climate conditions that can affect furniture longevity. For instance, high humidity or intense heat can cause some materials to deteriorate faster than others. Additionally, buyers often worry about the long-term investment and whether the chosen materials will withstand heavy usage in commercial settings.
The Solution: To address these concerns, B2B buyers should prioritize sourcing sectional sofas made from high-quality, climate-appropriate materials. This involves researching manufacturers who specialize in durable upholstery fabrics that are resistant to wear and tear, such as commercial-grade vinyl or treated leathers. Buyers should request samples and inquire about the testing processes that materials undergo to ensure they can withstand local environmental conditions. Furthermore, establishing a relationship with suppliers who offer warranties or guarantees on their products can provide an added layer of security for buyers, ensuring they are making a sound investment.
Scenario 3: Inefficiencies in Ordering and Delivery Processes
The Problem: B2B buyers often face inefficiencies in the ordering and delivery processes when sourcing sectional sofas. Delays in production or shipping can disrupt project timelines, leading to frustration and potential financial loss. Furthermore, international shipping can complicate logistics, with buyers unsure of how to navigate customs regulations or manage potential tariffs.
The Solution: To mitigate these issues, buyers should develop a clear timeline that outlines key milestones for the project. This includes establishing deadlines for ordering, production, and delivery. Engaging with manufacturers who have a reputation for efficient production timelines and reliable shipping practices is crucial. Buyers should also consider partnering with logistics companies that specialize in international shipping to streamline the process. These companies can provide insights into customs regulations and help manage documentation, ensuring that the sectional sofas arrive on time and in compliance with local laws. Additionally, maintaining open communication with manufacturers throughout the process can help preemptively address any potential delays or issues.
Strategic Material Selection Guide for sectional sofa custom
When selecting materials for custom sectional sofas, international B2B buyers must consider various factors, including durability, cost, and compliance with local standards. Below is an analysis of four common materials used in sectional sofa construction, focusing on their properties, advantages, disadvantages, and specific considerations for buyers from Africa, South America, the Middle East, and Europe.
What Are the Key Properties of Fabric Upholstery for Sectional Sofas?
Fabric upholstery is a popular choice for sectional sofas due to its versatility and comfort. Common fabrics include polyester, linen, and cotton blends.
- Key Properties: Fabric upholstery is breathable, providing comfort in varying climates. It typically has a moderate temperature rating and is resistant to fading and wear.
- Pros & Cons: While fabric is generally affordable and available in numerous designs, it can be less durable than leather, especially in high-traffic environments. Maintenance often requires regular cleaning to prevent stains and wear.
- Impact on Application: Fabric upholstery is suitable for residential and commercial applications, but it may not withstand heavy use in some settings.
- Considerations for International Buyers: Buyers should ensure compliance with fire safety standards, such as those outlined by ASTM in the U.S. or DIN in Europe. Preferences may vary by region, with some markets favoring eco-friendly or hypoallergenic options.
How Does Leather Compare as a Material for Custom Sectional Sofas?
Leather is synonymous with luxury and durability, making it a favored choice for high-end sectional sofas.
- Key Properties: Leather has high durability and is resistant to tearing and fading. It also has excellent temperature regulation properties, keeping users comfortable in various climates.
- Pros & Cons: The primary advantage of leather is its longevity and ease of cleaning, but it comes at a higher cost. Additionally, it may require conditioning to prevent cracking over time.
- Impact on Application: Leather is ideal for upscale residential settings and commercial spaces where aesthetics are paramount. However, it may not be suitable for environments prone to high humidity, as it can absorb moisture.
- Considerations for International Buyers: Buyers should be aware of animal welfare standards and sourcing certifications, especially in regions where ethical sourcing is a concern. Compliance with local regulations regarding chemical treatments is also essential.
What Are the Advantages of Using Wood Frames in Sectional Sofas?
Wood frames provide the structural integrity necessary for sectional sofas, impacting overall durability and aesthetics.
- Key Properties: Solid wood frames are strong and can support significant weight. They also offer good resistance to deformation under pressure.
- Pros & Cons: While wood frames add to the overall quality and longevity of the sofa, they can increase manufacturing complexity and costs. Additionally, they may be susceptible to warping in humid conditions.
- Impact on Application: Wood frames are suitable for both residential and commercial applications, ensuring stability and support.
- Considerations for International Buyers: Buyers should ensure that the wood used complies with sustainable forestry practices and international standards, such as those set by the Forest Stewardship Council (FSC).
Why Is Foam Padding Important for Comfort in Sectional Sofas?
Foam padding is essential for providing comfort and support in sectional sofas.
- Key Properties: High-density foam offers excellent support and durability, while memory foam provides additional comfort by contouring to the body.
- Pros & Cons: Foam padding enhances user comfort and can be cost-effective. However, lower-quality foam may degrade faster and lose its shape over time.
- Impact on Application: Foam padding is suitable for various applications, but its performance can vary based on density and type.
- Considerations for International Buyers: Compliance with health and safety standards regarding flame retardants and chemical emissions is crucial. Buyers should also consider the environmental impact of foam production.
Summary Table of Material Selection for Custom Sectional Sofas
Material | Typical Use Case for sectional sofa custom | Key Advantage | Key Disadvantage/Limitation | Relative Cost (Low/Med/High) |
---|---|---|---|---|
Fabric Upholstery | Residential and light commercial settings | Versatile and comfortable | Less durable than leather | Medium |
Leather | High-end residential and commercial spaces | Luxurious and long-lasting | Higher cost and maintenance | High |
Wood Frames | Structural support for all types of sofas | Strong and stable | Susceptible to warping | Medium to High |
Foam Padding | Comfort layer in all types of sofas | Enhances comfort | Lower quality can degrade quickly | Low to Medium |
This strategic material selection guide equips international B2B buyers with essential insights to make informed decisions when sourcing custom sectional sofas, ensuring they meet regional preferences and compliance standards.
In-depth Look: Manufacturing Processes and Quality Assurance for sectional sofa custom
What Are the Main Stages of the Manufacturing Process for Custom Sectional Sofas?
The manufacturing process for custom sectional sofas typically involves several key stages: material preparation, forming, assembly, and finishing. Each of these stages is critical to ensuring that the final product meets both aesthetic and functional requirements.
-
Material Preparation: The first step involves selecting high-quality materials, including wood for the frame, foam for cushioning, and various fabrics for upholstery. Suppliers must ensure that materials are sourced sustainably and comply with relevant international standards. For B2B buyers, verifying the quality of these materials at the outset can prevent future issues with durability and aesthetics.
-
Forming: In this stage, the selected materials are shaped into components. For wooden frames, this involves cutting, sanding, and sometimes bending wood to achieve the desired shape. Advanced techniques like CNC machining can enhance precision. For foam, various densities and firmness levels can be chosen to meet customer specifications. Buyers should inquire about the technology and machinery used during this phase to ensure efficiency and quality.
-
Assembly: Once components are formed, they are assembled into the sectional sofa. This process may involve traditional joinery methods or modern techniques like doweling or pocket screws. Quality assurance is crucial here, as improper assembly can lead to structural weaknesses. B2B buyers should look for suppliers who use robust assembly methods and offer warranties on their products.
-
Finishing: The final stage includes upholstery, applying finishes, and quality inspections. Upholstering involves covering the frame with selected fabrics, ensuring that seams are tight and patterns align perfectly. Finishing may include staining, painting, or applying protective coatings to enhance durability. Buyers should ask for samples of finishes and upholstery options to ensure they align with their branding and quality expectations.
How Is Quality Assurance Implemented in Custom Sofa Manufacturing?
Quality assurance (QA) in sectional sofa manufacturing is vital to ensuring that products meet safety and performance standards. The QA process typically follows several international and industry-specific standards.
-
Adherence to International Standards: Many manufacturers comply with ISO 9001, which outlines requirements for a quality management system. This certification demonstrates a commitment to quality and customer satisfaction. Additionally, CE marking may be relevant for buyers in Europe, indicating that products meet health, safety, and environmental protection standards.
-
Quality Control Checkpoints: Effective QA incorporates several checkpoints:
– Incoming Quality Control (IQC): Inspection of raw materials upon arrival to ensure they meet specifications.
– In-Process Quality Control (IPQC): Regular inspections during the manufacturing process to identify and rectify defects early.
– Final Quality Control (FQC): A thorough examination of the completed sofas, checking for defects in assembly, upholstery, and overall finish. -
Common Testing Methods: Manufacturers may employ various testing methods, including:
– Durability Testing: Simulating long-term use to assess the resilience of materials and construction.
– Flammability Testing: Ensuring that fabrics and materials comply with fire safety regulations.
– Comfort Testing: Evaluating seating comfort through user trials or ergonomic assessments.
How Can B2B Buyers Verify Supplier Quality Control?
B2B buyers must take proactive steps to ensure that their suppliers adhere to strict quality control measures. Here are several strategies to verify supplier QC:
-
Conduct Supplier Audits: Regular audits of manufacturing facilities can provide insight into a supplier’s adherence to quality standards. Buyers should establish a checklist based on their requirements and the relevant international standards.
-
Request Quality Reports: Suppliers should provide detailed quality assurance reports, including results from their QC checkpoints and any corrective actions taken. Reviewing these reports can help buyers gauge the reliability of the supplier’s processes.
-
Engage Third-Party Inspectors: Hiring independent third-party inspectors can offer an unbiased evaluation of the manufacturing process. These inspectors can verify compliance with both international and industry-specific standards, providing peace of mind to buyers.
What Are the Quality Control Nuances for International B2B Buyers?
International buyers must navigate specific challenges related to quality control that can vary by region:
-
Understanding Local Standards: Different countries may have varying standards for materials and manufacturing processes. For example, European buyers must be aware of REACH regulations concerning chemical safety in materials.
-
Cultural Differences in Quality Expectations: Buyers from Africa, South America, the Middle East, and Europe may have different expectations regarding quality and aesthetics. Understanding these nuances can facilitate better communication with suppliers and ensure that products meet market demands.
-
Logistics and Transportation Considerations: Quality can be affected during transportation. B2B buyers should discuss packaging and shipping methods with suppliers to mitigate risks associated with damage during transit.
By focusing on these manufacturing processes and quality assurance practices, international B2B buyers can make informed decisions and establish strong relationships with suppliers, ensuring that their custom sectional sofas meet the highest standards of quality and durability.
Practical Sourcing Guide: A Step-by-Step Checklist for ‘sectional sofa custom’
Introduction: How to Source Custom Sectional Sofas Effectively
Sourcing custom sectional sofas for your business requires a strategic approach to ensure quality, cost-effectiveness, and reliability. This checklist is designed for B2B buyers, particularly from Africa, South America, the Middle East, and Europe, to streamline the procurement process. By following these steps, you can make informed decisions that align with your business needs.
Step 1: Define Your Technical Specifications
Start by outlining the specific requirements for your sectional sofas. Consider factors such as dimensions, materials, design style, and functionality.
- Why It Matters: Clear specifications help eliminate misunderstandings with suppliers and ensure that the final product meets your expectations.
- What to Look For: Ensure that you detail any special features, such as modular designs, upholstery options, or eco-friendly materials.
Step 2: Research Potential Suppliers
Conduct thorough research to identify suppliers that specialize in custom sectional sofas. Utilize industry databases, trade shows, and online platforms to gather information.
- Why It Matters: A well-researched list of suppliers increases your chances of finding a reliable partner who meets your quality and delivery standards.
- What to Look For: Check for supplier reviews, ratings, and their experience in the industry.
Step 3: Evaluate Supplier Capabilities
Once you have a shortlist, assess each supplier’s manufacturing capabilities. This includes their production capacity, technology, and quality control processes.
- Why It Matters: Understanding a supplier’s capabilities ensures they can meet your order volume and quality requirements.
- What to Look For: Request information on their production processes and any certifications related to quality assurance (e.g., ISO standards).
Step 4: Request Samples and Prototypes
Before finalizing a supplier, request samples or prototypes of their sectional sofas. This allows you to evaluate the quality of materials and craftsmanship.
- Why It Matters: Physical samples provide a tangible sense of what you can expect, reducing the risk of dissatisfaction upon delivery.
- What to Look For: Pay attention to the stitching, upholstery quality, and overall finish of the sample.
Step 5: Verify Supplier Certifications
Check if the suppliers hold relevant certifications that ensure compliance with industry standards, such as safety regulations and environmental guidelines.
- Why It Matters: Certifications indicate a commitment to quality and sustainability, which is increasingly important for businesses.
- What to Look For: Look for certifications like GREENGUARD or OEKO-TEX, which signify low chemical emissions and safe materials.
Step 6: Negotiate Terms and Conditions
Once you’ve selected a supplier, engage in negotiations regarding pricing, payment terms, lead times, and warranty conditions.
- Why It Matters: Clear terms help avoid disputes later and ensure both parties are aligned on expectations.
- What to Look For: Ensure that the agreement includes clauses for quality assurance and remedies for non-compliance.
Step 7: Establish a Communication Plan
Create a communication plan that outlines how you will keep in touch with the supplier throughout the production process.
- Why It Matters: Regular communication fosters a collaborative relationship and allows you to address any issues promptly.
- What to Look For: Define key points of contact, preferred communication channels, and frequency of updates.
By following this sourcing checklist, you can navigate the complexities of procuring custom sectional sofas, ensuring a successful partnership that meets your business needs.
Comprehensive Cost and Pricing Analysis for sectional sofa custom Sourcing
What Are the Key Cost Components in Custom Sectional Sofa Sourcing?
When sourcing custom sectional sofas, understanding the comprehensive cost structure is crucial for B2B buyers. The primary cost components include:
-
Materials: The choice of upholstery, frame materials, and cushioning significantly impacts costs. High-quality fabrics and sustainable materials may come at a premium but can enhance the product’s lifespan and appeal.
-
Labor: Skilled labor is essential for crafting custom furniture. Labor costs vary depending on the region and the complexity of the design. Countries with lower labor costs may offer significant savings but could compromise quality.
-
Manufacturing Overhead: This includes utilities, rent, and other operational costs associated with running a manufacturing facility. Buyers should consider suppliers with efficient overhead management to keep overall costs down.
-
Tooling: Custom designs often require specialized tools or molds. The initial investment in tooling can be substantial but is necessary for producing unique designs.
-
Quality Control (QC): Implementing robust QC processes ensures that the final product meets specifications. While this adds to costs, it helps prevent costly returns and damage to reputation.
-
Logistics: Shipping and handling fees can vary widely based on distance, shipping method, and volume. Buyers should factor in potential customs duties and taxes, especially when sourcing from overseas.
-
Margin: Suppliers typically add a markup to cover their costs and generate profit. Understanding typical margins in the market can help buyers gauge if they’re receiving a fair price.
How Do Price Influencers Affect Custom Sofa Costs?
Several factors influence the pricing of custom sectional sofas:
-
Volume and Minimum Order Quantity (MOQ): Larger orders often lead to discounts. Buyers should evaluate their needs against MOQ requirements to optimize pricing.
-
Specifications and Customization: The level of customization affects pricing. Unique features or finishes generally increase costs, so buyers should balance customization with budget constraints.
-
Materials and Quality Certifications: Premium materials and certifications (e.g., eco-friendly labels) add to the cost. Buyers should assess whether these factors align with their target market’s preferences.
-
Supplier Factors: The reputation and reliability of suppliers can influence pricing. Established suppliers may charge more but often provide better quality and service.
-
Incoterms: Understanding the shipping terms is vital. They define responsibilities for costs and risks during transportation, which can affect the total landed cost of the product.
What Are the Best Negotiation Tips for International B2B Buyers?
For international B2B buyers, particularly in regions like Africa, South America, the Middle East, and Europe, effective negotiation can lead to substantial savings:
-
Research Market Prices: Conduct thorough market research to understand typical pricing for custom sectional sofas. This knowledge provides leverage during negotiations.
-
Leverage Volume: If possible, consolidate orders to increase volume, which can lead to better pricing. Suppliers are often more willing to negotiate on larger orders.
-
Discuss Payment Terms: Flexible payment terms can be a negotiation point. Offering upfront payments might secure a discount, while longer payment terms can help with cash flow.
-
Consider Total Cost of Ownership (TCO): Evaluate not just the initial price but also long-term costs, including maintenance, durability, and potential warranty issues. A higher upfront cost might be justified if it leads to lower TCO.
-
Be Open to Alternatives: If a supplier cannot meet your price, be open to discussing alternative materials or designs that might be more cost-effective.
Why Is It Important to Understand Pricing Nuances for International Sourcing?
International sourcing introduces complexities that can impact pricing significantly. Factors such as currency fluctuations, geopolitical stability, and trade tariffs can all affect final costs. Buyers should stay informed about these nuances to make informed decisions and avoid unexpected expenses.
Disclaimer on Indicative Prices
Prices for custom sectional sofas can vary widely based on the aforementioned factors. The information provided is indicative and should be validated through direct quotes from suppliers to ensure accuracy and relevance to specific sourcing needs.
Alternatives Analysis: Comparing sectional sofa custom With Other Solutions
When considering the purchase of a sectional sofa custom, it is essential to explore viable alternatives that can meet the diverse needs of B2B buyers. This analysis provides a comparative overview of sectional sofas against two popular alternatives: modular seating systems and traditional sofas. Each solution has unique characteristics that cater to various business environments and customer preferences.
Comparison Table
Comparison Aspect | Sectional Sofa Custom | Modular Seating System | Traditional Sofa |
---|---|---|---|
Performance | High comfort and adaptability | Versatile configurations for different spaces | Standard comfort, less adaptable |
Cost | Generally higher due to customization | Moderate, depending on configuration | Lower initial investment |
Ease of Implementation | Requires planning and measurement | Easy to set up and rearrange | Simple setup, no planning needed |
Maintenance | Moderate; fabric care and repair may be needed | Low; easy to clean and maintain | Varies by material; often requires more upkeep |
Best Use Case | Ideal for tailored office environments or lounges | Perfect for collaborative spaces and dynamic environments | Suitable for traditional offices and waiting areas |
What Are the Benefits of Modular Seating Systems Compared to Sectional Sofas?
Modular seating systems are designed for flexibility, allowing businesses to rearrange seating configurations easily. This adaptability is particularly advantageous in dynamic workspaces or collaborative environments, where the layout may need to change frequently. Additionally, modular options often come with lower maintenance needs, making them suitable for high-traffic areas. However, they may lack the personalized comfort and aesthetic appeal that a custom sectional sofa can provide.
How Do Traditional Sofas Compare to Sectional Sofas in Terms of Cost and Use Cases?
Traditional sofas typically have a lower upfront cost, making them an attractive option for budget-conscious businesses. They are straightforward to implement, requiring minimal planning or space measurement. However, traditional sofas often offer less flexibility in terms of layout and design, which can be a drawback for modern office environments looking for adaptable seating solutions. Their maintenance can vary based on the material used, and they may not provide the same level of comfort or support as a custom sectional sofa.
Conclusion: Which Seating Solution Should B2B Buyers Choose?
When choosing between sectional sofas, modular seating systems, and traditional sofas, B2B buyers should consider their specific needs, budget constraints, and the intended use of the seating. If a business requires a tailored solution that enhances comfort and aesthetics, a sectional sofa custom may be the best option. Conversely, for those who prioritize flexibility and ease of maintenance, modular seating could be more suitable. Traditional sofas offer a cost-effective solution for businesses focused on straightforward, classic designs. Ultimately, the right choice will depend on aligning the seating solution with the unique demands of the business environment.
Essential Technical Properties and Trade Terminology for sectional sofa custom
What Are the Essential Technical Properties of Custom Sectional Sofas?
When considering custom sectional sofas, B2B buyers must understand several key technical properties that influence product quality and suitability for their specific market needs. Here are some critical specifications to consider:
1. Material Grade: How Does It Affect Durability?
The material grade refers to the quality of the fabrics and structural components used in the sectional sofa. Common materials include high-density foam, hardwood frames, and durable upholstery fabrics. A higher material grade typically signifies better durability and longevity, which is crucial for businesses aiming for repeat sales and customer satisfaction. Buyers should look for certifications that indicate material quality, such as ISO or BIFMA.
2. Construction Tolerance: Why Is It Important?
Construction tolerance is the permissible limit of variation in the dimensions and assembly of the sofa components. This property is vital for ensuring that sectional pieces fit together seamlessly and maintain structural integrity. For B2B buyers, understanding these tolerances can help in assessing the reliability of the manufacturer and the final product’s fit and finish, which are essential for customer satisfaction.
3. Weight Capacity: What Should You Look For?
Weight capacity indicates the maximum weight the sectional sofa can support without compromising its structure or safety. This specification is particularly important for businesses targeting specific demographics or usage scenarios, such as family-friendly or commercial environments. A higher weight capacity often correlates with better materials and construction techniques.
4. Fire Resistance Rating: What Are the Standards?
Fire resistance ratings are critical for compliance with safety regulations, especially in commercial settings. Sofas that meet specific fire safety standards, such as CAL 117 in the United States or BS 5852 in the UK, can help businesses avoid legal liabilities and enhance their marketability. Buyers should confirm that their suppliers provide documentation for these ratings.
5. Upholstery Finish: How Does It Impact Maintenance?
The upholstery finish refers to the treatment applied to the fabric to enhance its durability, stain resistance, and ease of cleaning. Fabrics with a higher resistance to wear and tear are essential for commercial applications, where sofas are subject to heavy use. Buyers should inquire about the finish and care instructions to ensure the longevity of their product.
What Common Trade Terms Should B2B Buyers Understand?
Understanding trade terminology is essential for navigating the complexities of international B2B transactions. Here are several key terms relevant to the custom sectional sofa market:
1. OEM (Original Equipment Manufacturer): What Does It Mean?
OEM refers to companies that manufacture products for other brands to sell under their label. For buyers, working with an OEM can provide opportunities for customization without needing to invest in manufacturing facilities. This relationship can lead to cost efficiencies and quicker time-to-market for new products.
2. MOQ (Minimum Order Quantity): Why Is It Crucial?
MOQ is the smallest quantity of a product that a supplier is willing to sell. Understanding the MOQ helps buyers budget and plan their inventory effectively. For international buyers, negotiating MOQs can also impact shipping costs and lead times.
3. RFQ (Request for Quotation): How Should It Be Used?
An RFQ is a document used to solicit price quotes from suppliers. It should detail specifications, quantities, and delivery requirements. A well-structured RFQ can help buyers compare offers from different manufacturers, ensuring they choose a supplier that meets their quality and budget expectations.
4. Incoterms: What Are They and Why Do They Matter?
Incoterms are international commercial terms that define the responsibilities of buyers and sellers regarding shipping, insurance, and tariffs. Familiarity with Incoterms can help buyers avoid misunderstandings about costs and risks associated with international shipping, facilitating smoother transactions.
5. Lead Time: How Does It Affect Your Business?
Lead time refers to the time it takes from placing an order to receiving the product. Understanding lead times is crucial for inventory management and ensuring that products are available when customers demand them. Buyers should always clarify lead times with suppliers to align with their business needs.
In summary, being well-informed about the technical properties and trade terminology associated with custom sectional sofas can significantly enhance decision-making for B2B buyers, ensuring they select the best products for their markets.
Navigating Market Dynamics and Sourcing Trends in the sectional sofa custom Sector
What Are the Key Market Dynamics and Sourcing Trends in the Sectional Sofa Custom Sector?
The global sectional sofa custom market is witnessing significant transformation driven by evolving consumer preferences, technological advancements, and changing market dynamics. International B2B buyers, particularly from Africa, South America, the Middle East, and Europe, are now focusing on customization options that cater to specific aesthetic and functional needs. The rise of e-commerce platforms and digital showrooms has made it easier for buyers to source products directly from manufacturers, reducing lead times and costs.
Emerging trends include the integration of smart technology into furniture design, such as built-in USB ports and adjustable configurations that enhance user experience. Additionally, the demand for modular sectional sofas that allow for versatile arrangements is increasing, appealing to both residential and commercial buyers. In regions like Europe, particularly in countries such as France and Germany, there is a notable emphasis on minimalistic designs that promote space efficiency, aligning with urban living trends.
Moreover, international buyers are increasingly seeking suppliers who can provide innovative solutions, such as 3D visualization tools for product customization. As global logistics improve, sourcing from manufacturers in different regions becomes more feasible, allowing buyers to leverage competitive pricing and unique design offerings. Understanding these dynamics is essential for B2B buyers looking to navigate the complexities of the sectional sofa custom market effectively.
How Is Sustainability Influencing Ethical Sourcing in the Sectional Sofa Custom Market?
Sustainability has emerged as a critical factor in the purchasing decisions of international B2B buyers. The environmental impact of furniture manufacturing is under scrutiny, prompting companies to adopt more sustainable practices. This shift towards eco-friendly sourcing includes the use of sustainable materials such as reclaimed wood, organic fabrics, and low-VOC (volatile organic compound) finishes. Buyers are increasingly prioritizing suppliers who demonstrate a commitment to reducing their carbon footprint through responsible sourcing and production processes.
Ethical supply chains are becoming a non-negotiable aspect of the sectional sofa custom sector. Buyers are expected to ensure that their suppliers adhere to fair labor practices and environmental standards. Certifications such as Forest Stewardship Council (FSC) for wood products and Global Organic Textile Standard (GOTS) for fabrics are gaining importance as they provide assurance of sustainability and ethical practices.
Furthermore, the demand for transparency in the supply chain is on the rise. International buyers are leveraging technologies like blockchain to trace the origin of materials, ensuring that they are sourced responsibly. By aligning with sustainable and ethical sourcing practices, B2B buyers not only meet regulatory requirements but also enhance their brand reputation among environmentally-conscious consumers.
What Is the Historical Context of the Sectional Sofa Custom Market?
The sectional sofa custom market has evolved significantly over the past few decades. Initially, the focus was primarily on mass production, with limited options for customization. However, as consumer preferences shifted towards personalization, manufacturers began to adapt by offering modular designs that could be tailored to individual needs. The rise of the internet and e-commerce further accelerated this trend, allowing buyers to explore a broader range of products from global suppliers.
In recent years, technological advancements have played a pivotal role in the market’s evolution. Innovations in manufacturing processes, such as CNC machining and automated upholstery techniques, have improved product quality and reduced lead times. This evolution continues to shape the sectional sofa custom market, making it essential for B2B buyers to stay informed about historical trends and current innovations to remain competitive.
Frequently Asked Questions (FAQs) for B2B Buyers of sectional sofa custom
-
How do I choose the right supplier for custom sectional sofas?
Choosing the right supplier involves thorough research and vetting. Start by assessing their portfolio to understand their design capabilities and quality. Look for suppliers with positive reviews and testimonials from previous clients, especially in your region. It’s also beneficial to request samples of their work and inquire about their production process, materials used, and lead times. Establishing a good communication channel and checking their responsiveness can also indicate their reliability. -
What are the key factors to consider when customizing sectional sofas?
When customizing sectional sofas, consider dimensions, fabric choices, style, and functionality. Ensure the design fits the intended space and aligns with your branding. Discuss material durability, especially for high-traffic areas, and explore options for eco-friendly materials if sustainability is a priority. Additionally, consider the modularity of the design, which can offer flexibility in configuration, making it easier to adapt to changing needs. -
What is the minimum order quantity (MOQ) for custom sectional sofas?
The MOQ for custom sectional sofas varies by supplier. Many manufacturers set an MOQ to ensure cost-efficiency in production. Typically, MOQs can range from 10 to 50 units, but it’s essential to communicate your requirements directly with the supplier. Some suppliers may offer lower MOQs for first-time orders or special arrangements, so don’t hesitate to negotiate based on your business needs. -
What payment terms should I expect when ordering custom sectional sofas internationally?
Payment terms can vary significantly among suppliers. Common practices include a deposit (usually 30-50%) upfront, with the balance due before shipping. Consider using secure payment methods like letters of credit or escrow services to protect your investment. Always clarify payment timelines, any additional fees, and currency considerations, particularly when dealing with international suppliers to avoid misunderstandings. -
How can I ensure quality assurance for custom sectional sofas?
To ensure quality assurance, request detailed specifications and a sample or prototype before full production. Establish a clear quality control process, including inspections at different stages of manufacturing. Consider hiring a third-party quality inspection service, especially for international orders, to verify that the products meet your standards and specifications. Regular communication with the supplier throughout the production process is also crucial. -
What logistics considerations should I keep in mind for international shipping?
When planning logistics for shipping sectional sofas, consider shipping methods, costs, and transit times. Evaluate whether you need to use air freight for faster delivery or sea freight for cost-effectiveness. Be aware of customs regulations and duties in your country, which can impact delivery times and overall costs. Partnering with a reliable freight forwarder can help streamline the process and ensure compliance with international shipping regulations. -
How can I effectively communicate my customization needs to suppliers?
Effective communication with suppliers involves providing clear and detailed specifications. Use visual aids like sketches or CAD drawings to illustrate your ideas. Create a comprehensive list of requirements, including dimensions, materials, colors, and any specific design elements. Regular follow-ups and open dialogue will help clarify any uncertainties and ensure the final product meets your expectations. -
What trends should I be aware of in the custom sectional sofa market?
Staying informed about trends in the custom sectional sofa market is crucial for making competitive decisions. Current trends include sustainable materials, multifunctional designs, and modular systems that adapt to various spaces. Additionally, keep an eye on color trends and upholstery innovations, such as stain-resistant fabrics. Engaging with industry publications and attending trade shows can help you stay updated on market shifts and consumer preferences.
Important Disclaimer & Terms of Use
⚠️ Important Disclaimer
The information provided in this guide, including content regarding manufacturers, technical specifications, and market analysis, is for informational and educational purposes only. It does not constitute professional procurement advice, financial advice, or legal advice.
While we have made every effort to ensure the accuracy and timeliness of the information, we are not responsible for any errors, omissions, or outdated information. Market conditions, company details, and technical standards are subject to change.
B2B buyers must conduct their own independent and thorough due diligence before making any purchasing decisions. This includes contacting suppliers directly, verifying certifications, requesting samples, and seeking professional consultation. The risk of relying on any information in this guide is borne solely by the reader.
Strategic Sourcing Conclusion and Outlook for sectional sofa custom
What Are the Key Takeaways for B2B Buyers in the Sectional Sofa Custom Market?
In the competitive landscape of sectional sofa custom sourcing, strategic partnerships and informed decision-making are paramount. Buyers from Africa, South America, the Middle East, and Europe must prioritize understanding their market dynamics, including regional preferences and trends in sustainability. Leveraging data analytics can facilitate better demand forecasting and inventory management, ultimately leading to cost reductions and improved service delivery.
How Does Strategic Sourcing Enhance Business Outcomes?
Strategic sourcing not only improves supplier relationships but also ensures that quality and innovation remain at the forefront of product offerings. By focusing on long-term collaborations rather than transactional relationships, businesses can enhance their competitive edge and foster innovation in design and functionality. This approach is crucial for meeting the diverse needs of customers across various regions.
What Does the Future Hold for the Sectional Sofa Custom Market?
As the global market evolves, B2B buyers are encouraged to stay proactive. Embrace technological advancements and sustainability initiatives to align with consumer expectations. The future of sectional sofas lies in customization, eco-friendly materials, and smart furniture solutions. By investing in these areas, international buyers can position themselves as leaders in the market. Engage with suppliers who share your vision for innovation and sustainability, and take the next step towards transforming your offerings in the sectional sofa custom space.