Enhance Efficiency: The Ultimate Toyota Dyna Custom Guide (2025)
Introduction: Navigating the Global Market for toyota dyna custom
In today’s interconnected world, sourcing the right vehicle for your business needs can be a daunting task, especially when considering options like the Toyota Dyna Custom. This versatile truck is increasingly favored by companies across various sectors due to its reliability and adaptability. However, international B2B buyers, particularly from regions like Africa, South America, the Middle East, and Europe, face unique challenges in navigating the complexities of global sourcing.
This comprehensive guide delves into the multifaceted landscape of the Toyota Dyna Custom, exploring its various types and applications tailored for different industries. From logistics to construction, understanding the specific requirements of your sector is crucial for making an informed decision. Furthermore, we will cover essential aspects such as supplier vetting processes, cost analysis, and after-sales support to ensure that you are equipped with the knowledge needed to select the best option for your business.
By the end of this guide, you will have a clearer understanding of how to navigate the global market for the Toyota Dyna Custom. You will be empowered to make strategic purchasing decisions that align with your operational needs and budget constraints, ultimately enhancing your business’s efficiency and productivity. Whether you are located in bustling cities or remote regions, this resource aims to simplify your sourcing journey and facilitate successful acquisitions in a competitive marketplace.
Understanding toyota dyna custom Types and Variations
Type Name | Key Distinguishing Features | Primary B2B Applications | Brief Pros & Cons for Buyers |
---|---|---|---|
Toyota Dyna 130 | Medium-duty truck, payload capacity of 3,500 kg | Logistics, construction, and distribution | Pros: Versatile, good fuel efficiency. Cons: Limited cargo space compared to larger models. |
Toyota Dyna 150 | Enhanced payload capacity up to 4,000 kg | Heavy-duty transport, agricultural use | Pros: High payload, robust design. Cons: Higher operating costs. |
Toyota Dyna 200 | Larger chassis with customizable body options | Large-scale deliveries, waste management | Pros: Customizable, spacious. Cons: May require larger parking space. |
Toyota Dyna 4WD | All-wheel drive capability for off-road conditions | Mining, forestry, and rugged terrain transport | Pros: Excellent traction, durable. Cons: More expensive maintenance. |
Toyota Dyna Refrigerated | Insulated body for temperature-sensitive goods | Food distribution, pharmaceuticals | Pros: Maintains temperature, ideal for perishables. Cons: Higher initial investment. |
What Are the Key Characteristics of the Toyota Dyna 130?
The Toyota Dyna 130 is a medium-duty truck recognized for its impressive payload capacity of up to 3,500 kg. It is particularly suitable for logistics companies and construction businesses that require a reliable vehicle for transporting materials. When considering a purchase, B2B buyers should evaluate the truck’s fuel efficiency and versatility, which make it an attractive option for various applications. However, its limited cargo space in comparison to larger models may be a drawback for businesses needing to carry larger loads.
How Does the Toyota Dyna 150 Stand Out in the Market?
The Toyota Dyna 150 is designed for heavy-duty transport, boasting an enhanced payload capacity of up to 4,000 kg. This model is ideal for agricultural use and industries that require robust transportation solutions. B2B buyers should consider its durability and high payload capacity, which can contribute to efficiency in operations. However, the Dyna 150 may incur higher operating costs, making it essential for businesses to assess their budget and operational needs before committing to a purchase.
What Makes the Toyota Dyna 200 a Popular Choice?
The Toyota Dyna 200 features a larger chassis and customizable body options, making it suitable for large-scale deliveries and waste management. Its spacious interior allows for various configurations, catering to different business requirements. B2B buyers should focus on its customizability and spaciousness as key advantages. However, potential buyers must also consider the need for larger parking space, as this model may not be suitable for all urban environments.
Why Should Businesses Consider the Toyota Dyna 4WD?
The Toyota Dyna 4WD offers all-wheel drive capabilities, making it an excellent choice for industries that operate in rugged terrain, such as mining and forestry. The truck’s durability and excellent traction are significant advantages for B2B buyers looking for a reliable vehicle in challenging conditions. However, maintenance costs can be higher due to the complexity of the 4WD system, so businesses should factor this into their operational budgets.
How Can the Toyota Dyna Refrigerated Model Benefit B2B Buyers?
The Toyota Dyna Refrigerated model is specifically designed to transport temperature-sensitive goods, making it invaluable for food distribution and pharmaceuticals. Its insulated body ensures that products remain at the required temperatures during transit. B2B buyers should weigh the benefits of maintaining product integrity against the higher initial investment required for refrigerated trucks. For businesses in the perishable goods sector, this model can be a game-changer in ensuring compliance with safety standards.
Related Video: Toyota Prius How-To: Prius Multi-Information Display (MID) | Toyota
Key Industrial Applications of toyota dyna custom
Industry/Sector | Specific Application of Toyota Dyna Custom | Value/Benefit for the Business | Key Sourcing Considerations for this Application |
---|---|---|---|
Logistics and Transport | Urban Delivery Services | Enhanced maneuverability in congested areas, reducing delivery times. | Consider payload capacity and fuel efficiency. |
Construction | On-Site Material Transport | Reliable transport of materials to remote sites, improving project timelines. | Evaluate durability and off-road capabilities. |
Agriculture | Farming Equipment Transport | Efficient movement of farming tools and produce, increasing productivity. | Assess compatibility with agricultural equipment. |
Retail and E-commerce | Last-Mile Delivery Solutions | Optimized for small, frequent deliveries, enhancing customer satisfaction. | Focus on vehicle size and loading configurations. |
Healthcare | Medical Supply Transport | Reliable and timely delivery of medical supplies, crucial for patient care. | Ensure compliance with health regulations and temperature controls. |
How is Toyota Dyna Custom Used in Logistics and Transport?
In the logistics and transport sector, the Toyota Dyna Custom is particularly valuable for urban delivery services. Its compact design allows for enhanced maneuverability in congested city environments, which significantly reduces delivery times. For international B2B buyers, especially in regions like Africa and South America where urban areas are densely populated, the Dyna Custom’s payload capacity and fuel efficiency are critical factors to consider when sourcing vehicles for their fleets.
What Role Does Toyota Dyna Custom Play in Construction?
In the construction industry, the Toyota Dyna Custom is employed for on-site material transport. It provides a reliable solution for moving building materials to remote construction sites, thereby improving project timelines and minimizing delays. Buyers from the Middle East and Europe should evaluate the vehicle’s durability and off-road capabilities, as construction sites often require robust vehicles that can handle challenging terrains.
How Does Toyota Dyna Custom Benefit Agriculture?
The agricultural sector utilizes the Toyota Dyna Custom for transporting farming equipment and produce. Its efficient design aids in the swift movement of tools and harvested goods, ultimately increasing overall productivity. For buyers in regions like South Africa and South America, it’s essential to assess the vehicle’s compatibility with various agricultural equipment to ensure seamless operations.
In What Ways is Toyota Dyna Custom Useful for Retail and E-commerce?
For retail and e-commerce businesses, the Toyota Dyna Custom serves as an effective last-mile delivery solution. Its size and loading configurations make it ideal for small, frequent deliveries, which is crucial for enhancing customer satisfaction in competitive markets. International B2B buyers should focus on the vehicle’s adaptability to different delivery needs and assess how it can streamline their logistics operations.
How is Toyota Dyna Custom Applied in Healthcare Logistics?
In the healthcare sector, the Toyota Dyna Custom is critical for the timely transport of medical supplies. Reliable delivery is essential for patient care, making this vehicle a vital asset for healthcare providers. Buyers must ensure that the vehicle complies with health regulations, especially concerning temperature controls for sensitive medical items, to maintain the integrity of the supplies being transported.
Related Video: Commercial Graphene Production // Allotropes and Applications
3 Common User Pain Points for ‘toyota dyna custom’ & Their Solutions
Scenario 1: Navigating Parts Availability for Maintenance
The Problem: One of the most pressing challenges for B2B buyers of the Toyota Dyna Custom is the availability of spare parts. In regions such as Africa and South America, where the vehicle is often used in demanding conditions, delays in obtaining parts can lead to increased downtime. This situation not only affects operational efficiency but also impacts customer satisfaction, as businesses may struggle to meet delivery deadlines.
The Solution: To mitigate this issue, B2B buyers should establish relationships with reliable local suppliers and distributors who specialize in Toyota vehicles. Conducting thorough research on suppliers’ reputations and their stock levels can significantly reduce lead times for parts. Additionally, implementing an inventory management system that tracks the most frequently needed components can help businesses maintain a buffer stock. For critical parts, consider sourcing from multiple suppliers to ensure availability. Regular communication with suppliers about upcoming needs can also facilitate timely procurement, thus minimizing operational disruptions.
Scenario 2: Understanding Vehicle Compliance and Regulations
The Problem: B2B buyers in different regions often face confusion regarding compliance with local vehicle regulations when purchasing the Toyota Dyna Custom. Regulations can vary significantly between countries in Europe, the Middle East, and Africa, affecting emissions standards, safety features, and modifications permissible for commercial vehicles. Navigating these regulations can be overwhelming, leading to potential legal issues and financial penalties.
The Solution: To address this challenge, buyers should conduct comprehensive research into the specific regulations applicable in their target market. Engaging with local automotive compliance experts or legal consultants can provide valuable insights into the necessary certifications and modifications required for the Toyota Dyna Custom. Additionally, partnering with a supplier who is familiar with local regulations can streamline the purchasing process. Buyers should also consider investing in vehicles that are already compliant with regional standards to avoid the hassle of retrofitting or modifying vehicles post-purchase.
Scenario 3: Maximizing Payload Capacity for Operational Efficiency
The Problem: Another common pain point for B2B buyers of the Toyota Dyna Custom is understanding how to maximize the vehicle’s payload capacity without compromising safety or performance. Many businesses may underestimate the impact of payload on fuel efficiency and vehicle longevity, leading to increased operational costs and potential vehicle failures.
The Solution: To effectively maximize payload capacity, buyers should first familiarize themselves with the vehicle’s specifications, particularly its Gross Vehicle Weight Rating (GVWR) and payload limits. Training drivers on best practices for loading and weight distribution can greatly enhance safety and performance. Additionally, utilizing technology, such as load sensors or telematics systems, can help monitor payload in real-time, ensuring that the vehicle is not overloaded. Establishing standard operating procedures for loading and unloading can also promote consistency and safety in operations. Regular vehicle maintenance and inspections can further ensure that the Toyota Dyna Custom remains in optimal condition, even under heavy loads.
By addressing these common pain points with actionable solutions, international B2B buyers can enhance their operational efficiency and ensure a successful investment in the Toyota Dyna Custom.
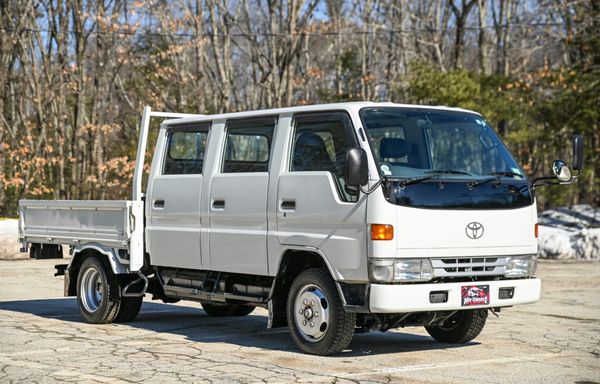
A stock image related to toyota dyna custom.
Strategic Material Selection Guide for toyota dyna custom
When selecting materials for the Toyota Dyna Custom, it’s crucial to understand the properties, advantages, and limitations of various materials. This guide focuses on four common materials used in the manufacturing of the Toyota Dyna Custom, providing actionable insights for international B2B buyers.
What are the Key Properties of Steel for Toyota Dyna Custom?
Steel is a widely used material in automotive applications due to its strength and versatility. It typically offers high tensile strength, excellent ductility, and good weldability, making it suitable for structural components. Steel can withstand high temperatures and pressures, which is essential for parts exposed to engine heat and mechanical stress.
Pros & Cons:
The durability of steel is one of its main advantages, providing long-lasting performance in various conditions. However, it is susceptible to corrosion unless treated, which may increase maintenance costs over time. Manufacturing complexity can also be a concern, as intricate designs may require advanced machining techniques.
Impact on Application:
Steel is compatible with a variety of media, including oils and fuels, making it suitable for engine components and chassis. However, it may not perform well in highly corrosive environments without proper coatings.
Considerations for International Buyers:
For buyers in regions like Africa and South America, where environmental conditions can vary significantly, it is essential to consider corrosion-resistant treatments. Compliance with local standards such as ASTM or DIN is also crucial to ensure quality and safety.
How Does Aluminum Benefit the Toyota Dyna Custom?
Aluminum is increasingly popular in automotive manufacturing due to its lightweight nature and resistance to corrosion. It has a lower density compared to steel, which can lead to improved fuel efficiency and handling.
Pros & Cons:
The primary advantage of aluminum is its weight reduction, which enhances vehicle performance. However, it is generally more expensive than steel and may require specialized welding techniques, increasing manufacturing complexity.
Impact on Application:
Aluminum is particularly suitable for components that require weight savings, such as body panels and structural elements. Its corrosion resistance makes it ideal for vehicles operating in humid or coastal environments.
Considerations for International Buyers:
In the Middle East and Europe, where lightweight vehicles are preferred, aluminum’s benefits can be significant. Buyers should ensure compliance with JIS standards for aluminum components to maintain quality.
What Role Does Composite Material Play in Toyota Dyna Custom?
Composite materials, such as fiberglass and carbon fiber, are gaining traction in automotive applications due to their high strength-to-weight ratio and design flexibility. They are particularly effective in applications where weight savings are critical.
Pros & Cons:
Composites offer excellent durability and resistance to environmental factors, but they can be expensive and may require specific manufacturing processes. Additionally, repair and recycling of composite materials can be more challenging compared to metals.
Impact on Application:
Composites are ideal for non-structural components, such as interior panels and exterior body parts, where aesthetics and weight are important. They are also compatible with various media, making them versatile for different applications.
Considerations for International Buyers:
For buyers in Europe and South America, understanding the specific regulations surrounding composite materials is essential, especially concerning recycling and environmental impact.
How Does Plastic Compare for Use in Toyota Dyna Custom?
Plastics are commonly used in automotive applications for their versatility and cost-effectiveness. They can be molded into complex shapes and are resistant to corrosion and chemical exposure.
Pros & Cons:
The primary advantage of plastics is their lightweight nature and low cost, making them suitable for various applications. However, they may not offer the same level of strength and durability as metals, particularly in high-stress environments.
Impact on Application:
Plastics are often used for interior components, dashboards, and non-structural parts. They are compatible with a wide range of media, including water and oils, but may degrade under extreme temperatures.
Considerations for International Buyers:
Buyers should consider the specific grades of plastic required for different applications and ensure compliance with local standards to avoid quality issues.
Summary Table of Material Selection for Toyota Dyna Custom
Material | Typical Use Case for Toyota Dyna Custom | Key Advantage | Key Disadvantage/Limitation | Relative Cost (Low/Med/High) |
---|---|---|---|---|
Steel | Structural components, chassis | High durability | Susceptible to corrosion | Medium |
Aluminum | Body panels, structural elements | Lightweight, corrosion-resistant | Higher cost, complex welding | High |
Composite | Interior panels, non-structural parts | High strength-to-weight ratio | Expensive, challenging repairs | High |
Plastic | Dashboards, non-structural components | Cost-effective, versatile | Lower strength in high-stress | Low |
This guide provides a comprehensive overview of material selection for the Toyota Dyna Custom, tailored for international B2B buyers. Understanding these materials will help in making informed decisions that align with performance requirements and regional standards.
In-depth Look: Manufacturing Processes and Quality Assurance for toyota dyna custom
What Are the Main Stages of the Manufacturing Process for Toyota Dyna Custom?
The manufacturing process for the Toyota Dyna Custom is a multi-step operation that ensures the vehicle meets both performance and quality standards. Understanding these stages is crucial for international B2B buyers looking to source reliable vehicles.
-
Material Preparation
The process begins with the selection of high-quality raw materials, including steel, aluminum, and various polymers. Each material undergoes rigorous testing to ensure it meets industry standards. For B2B buyers, sourcing suppliers who provide certified materials can enhance the reliability of the final product. -
Forming
In this stage, materials are shaped into components using techniques such as stamping, bending, and welding. Advanced technologies like computer numerical control (CNC) machines ensure precision in forming. Buyers should inquire about the technologies used by suppliers, as this directly impacts the durability and fit of the parts. -
Assembly
The assembly stage involves combining the various components, including the chassis, engine, and electrical systems. Automated assembly lines often enhance efficiency, but skilled labor is also critical for ensuring quality. B2B buyers should evaluate the assembly process of potential suppliers to ensure it aligns with their quality expectations. -
Finishing
Finally, the finishing stage includes painting, coating, and other treatments to improve aesthetics and protect against corrosion. This is a vital step, especially for vehicles that will operate in challenging environments. Buyers should request information on the types of finishes used and their long-term performance guarantees.
How Is Quality Assurance Implemented in the Manufacturing of Toyota Dyna Custom?
Quality assurance (QA) is a cornerstone of the manufacturing process for the Toyota Dyna Custom, ensuring that each vehicle meets international standards and customer expectations.
What International Standards Apply to Toyota Dyna Custom Manufacturing?
For B2B buyers, understanding the relevant international standards is essential. Toyota Dyna Custom manufacturing adheres to ISO 9001, a standard that emphasizes a strong quality management system. This certification demonstrates a commitment to consistent quality and continuous improvement.
In addition to ISO 9001, industry-specific certifications such as CE (Conformité Européenne) for European markets and API (American Petroleum Institute) standards for specific components may also apply. Buyers should request documentation proving compliance with these standards to ensure the supplier’s commitment to quality.
What Are the Key QC Checkpoints in the Manufacturing Process?
Quality control (QC) checkpoints are integrated throughout the manufacturing process, providing critical oversight at various stages:
-
Incoming Quality Control (IQC): This initial checkpoint assesses the quality of raw materials upon delivery. Suppliers should have robust IQC processes to catch issues before production begins.
-
In-Process Quality Control (IPQC): Throughout the manufacturing process, IPQC involves regular inspections of components and assemblies. This helps identify defects early, reducing waste and rework.
-
Final Quality Control (FQC): At the end of the production line, FQC involves comprehensive testing of the finished vehicles. This may include performance tests, safety checks, and emissions assessments.
B2B buyers should inquire about the specific QC processes employed by suppliers, as these can vary significantly.
Which Common Testing Methods Are Used to Ensure Quality?
Various testing methods are employed to validate the quality of the Toyota Dyna Custom. These may include:
-
Dimensional Inspection: Ensuring that components meet specified dimensions is crucial for proper assembly and functionality.
-
Functional Testing: This includes tests on engine performance, braking systems, and electrical components to ensure everything operates as intended.
-
Durability Testing: Vehicles may undergo stress tests to evaluate their performance under extreme conditions, simulating real-world usage.
By understanding these testing methods, international B2B buyers can better assess the reliability of potential suppliers.
How Can B2B Buyers Verify Supplier Quality Control?
B2B buyers need to conduct thorough due diligence when evaluating suppliers. Here are several actionable strategies:
-
Supplier Audits: Regular audits of potential suppliers can provide insights into their manufacturing processes and QC practices. Buyers should develop a checklist based on industry standards to guide these audits.
-
Request Quality Reports: Suppliers should be willing to provide detailed reports on their QC processes, including statistics on defect rates and corrective actions taken. This data can help buyers gauge the reliability of the supplier.
-
Third-Party Inspections: Engaging a third-party inspection service can add an additional layer of verification. These services can assess compliance with international standards and provide unbiased evaluations.
What Are the QC and Certification Nuances for International B2B Buyers?
For international B2B buyers, understanding the nuances of QC and certification is essential, especially when sourcing from different regions such as Africa, South America, the Middle East, and Europe.
-
Regional Standards: Each region may have specific quality standards and certifications that differ from global norms. Buyers should familiarize themselves with these local standards to ensure compliance.
-
Cultural Considerations: Different countries may have varying practices in quality assurance and manufacturing. Understanding these cultural nuances can facilitate better communication and expectations with suppliers.
-
Logistics and Supply Chain: Quality assurance doesn’t end at the factory gate. Buyers must consider the entire supply chain, including transportation and storage conditions, which can impact the final product’s quality.
By focusing on these aspects, international B2B buyers can better navigate the complexities of sourcing Toyota Dyna Custom vehicles, ensuring they partner with reliable suppliers committed to quality.
Practical Sourcing Guide: A Step-by-Step Checklist for ‘toyota dyna custom’
Introduction
Sourcing a Toyota Dyna Custom involves a strategic approach that ensures you get the best value while meeting your business requirements. This step-by-step checklist is designed for international B2B buyers from regions such as Africa, South America, the Middle East, and Europe. By following these actionable steps, you can streamline the procurement process, mitigate risks, and enhance your overall purchasing strategy.
Step 1: Define Your Technical Specifications
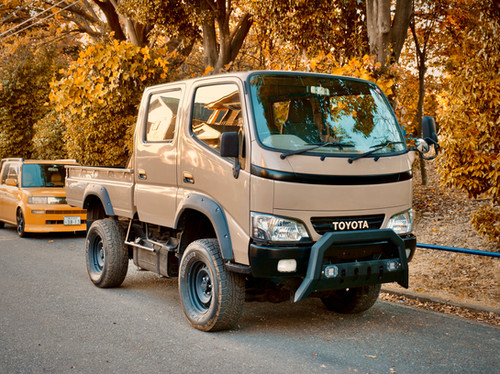
A stock image related to toyota dyna custom.
Begin by outlining the specific technical requirements for the Toyota Dyna Custom. This includes details such as payload capacity, engine specifications, dimensions, and any custom features you may need.
- Importance: A clear specification helps avoid misunderstandings with suppliers and ensures that the vehicle meets your operational needs.
- Tip: Consult with your operations team to identify must-have features versus nice-to-haves.
Step 2: Research Potential Suppliers
Conduct thorough research to identify reputable suppliers specializing in Toyota Dyna Customs. Use online platforms, industry directories, and trade shows to compile a list of potential candidates.
- Importance: The right supplier can significantly impact the quality and reliability of your purchase.
- Tip: Focus on suppliers with a proven track record and positive reviews from previous buyers in your region.
Step 3: Evaluate Supplier Certifications
Before moving forward, ensure that potential suppliers possess the necessary certifications and compliance with international quality standards, such as ISO certifications.
- Importance: Certifications are indicators of a supplier’s commitment to quality and can safeguard your investment.
- Tip: Request documentation and verify their authenticity directly with issuing organizations.
Step 4: Request Detailed Quotes
Once you have shortlisted suppliers, request detailed quotes that outline pricing, payment terms, delivery schedules, and warranty information.
- Importance: A comprehensive quote allows for better comparisons and negotiations.
- Tip: Ensure quotes include all potential costs, including shipping and customs duties, to avoid unexpected expenses.
Step 5: Conduct On-Site Visits or Virtual Tours
If feasible, conduct on-site visits to the suppliers’ facilities or arrange for virtual tours to inspect their operations and quality control processes.
- Importance: Seeing the supplier’s operations firsthand helps verify their capabilities and commitment to quality.
- Tip: Prepare a checklist of what to look for during the visit, such as machinery, staff qualifications, and safety standards.
Step 6: Negotiate Terms and Conditions
Engage in negotiations to finalize terms and conditions, including price, delivery timelines, after-sales support, and return policies.
- Importance: Effective negotiation can lead to better pricing and terms that align with your business goals.
- Tip: Be clear about your expectations and flexible where possible to foster a collaborative relationship.
Step 7: Finalize the Purchase Agreement
Once negotiations are complete, draft and finalize a purchase agreement that clearly outlines all terms discussed.
- Importance: A well-documented agreement protects both parties and serves as a reference throughout the transaction.
- Tip: Have legal counsel review the agreement to ensure all aspects are covered and compliant with local laws.
By following this checklist, B2B buyers can navigate the complexities of sourcing a Toyota Dyna Custom effectively, ensuring a successful procurement process that aligns with their business objectives.
Comprehensive Cost and Pricing Analysis for toyota dyna custom Sourcing
What Are the Key Cost Components for Sourcing Toyota Dyna Custom?
When analyzing the cost structure for sourcing a Toyota Dyna Custom, several components need to be taken into account. The primary cost elements include materials, labor, manufacturing overhead, tooling, quality control (QC), logistics, and profit margins.
-
Materials: The choice of materials significantly influences the overall cost. High-quality materials may increase the initial expenses but can lead to better durability and performance, which is essential for B2B buyers focusing on long-term value.
-
Labor: Labor costs vary by region and depend on local wage standards and the availability of skilled labor. For example, sourcing from countries with lower labor costs may reduce expenses but could impact the quality of craftsmanship.
-
Manufacturing Overhead: This includes costs related to utilities, rent, and equipment maintenance. Understanding the overhead costs of potential suppliers helps in making informed decisions.
-
Tooling: Tooling costs can be substantial, especially for custom specifications. Buyers should factor in these costs when requesting quotes, as they can vary widely among suppliers.
-
Quality Control (QC): Investing in quality control processes ensures that the end product meets industry standards. This can lead to higher upfront costs but reduces the risk of defects and returns, ultimately saving money.
-
Logistics: Transportation costs, including shipping and handling, need to be carefully evaluated. These costs can fluctuate based on the shipping method, distance, and current market conditions.
-
Margin: Suppliers typically add a profit margin to cover their risks and operational costs. Understanding the average margins in the industry can provide insights into pricing strategies.
How Do Price Influencers Impact the Cost of Toyota Dyna Custom?
Several factors influence the pricing of the Toyota Dyna Custom, which international B2B buyers should consider:
-
Volume/MOQ: Minimum order quantities (MOQ) can significantly affect pricing. Bulk orders often lead to discounts, making it essential for buyers to assess their purchasing capabilities.
-
Specifications/Customization: Customization options can increase costs. Buyers should clearly define their requirements to avoid unexpected charges.
-
Materials: The choice of materials not only impacts the cost but also the quality. Buyers should consider the trade-off between cost and quality when selecting materials.
-
Quality and Certifications: Products meeting international standards or possessing certifications may command higher prices. However, they can also reduce liability and enhance marketability.
-
Supplier Factors: The reputation and reliability of suppliers can influence pricing. Established suppliers might charge more due to their track record, but they often provide better assurance of quality and timely delivery.
-
Incoterms: Understanding Incoterms is crucial for international transactions. Different Incoterms can shift responsibility for shipping costs and risks, impacting the total cost.
What Buyer Tips Can Enhance Cost-Efficiency in Sourcing Toyota Dyna Custom?
To navigate the complexities of sourcing Toyota Dyna Custom effectively, international B2B buyers should consider the following strategies:
-
Negotiate Wisely: Engage in negotiations to secure better pricing and terms. Understanding the supplier’s cost structure can provide leverage during negotiations.
-
Evaluate Total Cost of Ownership (TCO): Beyond the initial purchase price, consider the TCO, which includes maintenance, operational costs, and potential resale value. This holistic view can lead to more informed purchasing decisions.
-
Explore Multiple Suppliers: Diversifying suppliers can lead to competitive pricing and reduced risks. It’s prudent to request quotes from multiple sources to gauge market rates.
-
Stay Informed on Pricing Nuances: Be aware of currency fluctuations, trade tariffs, and market demand in different regions, as these can significantly affect pricing.
-
Build Long-term Relationships: Establishing a strong partnership with suppliers can lead to better pricing, priority service, and access to exclusive offerings over time.
Disclaimer on Pricing
Please note that prices for the Toyota Dyna Custom can vary widely based on the factors discussed. It is essential for buyers to conduct thorough research and obtain multiple quotes to ensure they are making well-informed purchasing decisions.
Alternatives Analysis: Comparing toyota dyna custom With Other Solutions
Understanding Alternatives for Toyota Dyna Custom in the B2B Landscape
When evaluating the Toyota Dyna Custom for your business needs, it’s essential to consider alternative solutions that might offer similar functionalities or advantages. This analysis helps international B2B buyers make informed decisions based on performance, cost, and suitability for specific applications. Below, we compare the Toyota Dyna Custom with two viable alternatives: the Isuzu NPR and the Mitsubishi Fuso Canter.
Comparison Table
Comparison Aspect | Toyota Dyna Custom | Isuzu NPR | Mitsubishi Fuso Canter |
---|---|---|---|
Performance | 4-cylinder diesel, reliable load capacity | 4-cylinder diesel, excellent fuel efficiency | 4-cylinder diesel, robust engine options |
Cost | Moderate initial investment, competitive long-term costs | Lower initial cost, potential for higher long-term maintenance | Mid-range pricing, good resale value |
Ease of Implementation | User-friendly, minimal training required | Simple to operate, commonly available parts | Requires basic training, but widely used |
Maintenance | Low maintenance, widespread service network | Moderate maintenance costs, good parts availability | Slightly higher maintenance, but durable |
Best Use Case | Urban delivery, light construction | Local deliveries, logistics | Construction, heavy-duty transport |
In-Depth Analysis of Alternatives
Isuzu NPR: What Makes It a Strong Competitor?
The Isuzu NPR is known for its cost-effectiveness and fuel efficiency, making it an attractive option for businesses focused on reducing operational costs. With a lower initial purchase price compared to the Toyota Dyna Custom, it allows for a more accessible entry point for startups and small businesses. However, while the NPR is generally reliable, its maintenance costs can accumulate over time, especially if used for heavier loads or frequent short trips.
Mitsubishi Fuso Canter: How Does It Compare?
The Mitsubishi Fuso Canter stands out for its robust engine options and suitability for heavy-duty applications. It is particularly favored in construction and logistics, where durability is paramount. Though its initial investment is on the higher end compared to the Isuzu NPR, the Canter often retains good resale value, which can be beneficial for businesses looking to upgrade their fleet over time. However, it may require slightly more training for operators unfamiliar with its systems.
Conclusion: Choosing the Right Solution for Your Business Needs
Selecting the right vehicle for your business operations involves careful consideration of various factors, including performance, cost, and specific use cases. The Toyota Dyna Custom offers reliable performance and low maintenance, making it a strong contender for urban delivery and light construction tasks. However, alternatives like the Isuzu NPR and Mitsubishi Fuso Canter provide competitive advantages in cost and heavy-duty capabilities, respectively. By assessing your operational requirements and budget constraints, you can choose the most suitable vehicle that aligns with your business goals and regional demands.
Essential Technical Properties and Trade Terminology for toyota dyna custom
What Are the Key Technical Properties of the Toyota Dyna Custom?
When considering the procurement of the Toyota Dyna Custom, understanding its essential technical properties is crucial for B2B buyers. These specifications not only influence the vehicle’s performance but also its suitability for various applications across different markets.
1. Payload Capacity
The payload capacity of the Toyota Dyna Custom typically ranges from 1,500 kg to 2,500 kg, depending on the specific model and configuration. This property is vital for businesses that require a vehicle capable of transporting heavy goods. For buyers in industries such as logistics and construction, knowing the payload capacity ensures that the vehicle can meet operational demands without compromising safety or efficiency.
2. Engine Specifications
The engine of the Toyota Dyna Custom often features a 4.0L diesel engine, delivering substantial torque and power. This specification is critical for B2B buyers as it affects fuel efficiency, maintenance costs, and overall performance. A robust engine translates to better reliability, especially in challenging terrains common in regions like Africa and South America.
3. Towing Capacity
Understanding the towing capacity, which can reach up to 3,500 kg, is essential for businesses that require the transport of trailers or additional equipment. This property enables companies to utilize the Dyna Custom for various logistics and transport needs, enhancing its versatility. Buyers should consider their specific towing requirements to ensure the vehicle meets operational needs.
4. Fuel Efficiency
Fuel efficiency ratings for the Toyota Dyna Custom generally hover around 12-14 km/l. For B2B buyers, especially in regions where fuel costs can be high, this property directly impacts operational expenses. A more fuel-efficient vehicle can lead to significant cost savings over time, making it a key consideration in the purchasing decision.
5. Dimensions and Wheelbase
The dimensions of the Toyota Dyna Custom, with a wheelbase of approximately 3,400 mm, play a crucial role in maneuverability and stability. For urban deliveries or navigating tight spaces, understanding these measurements helps buyers assess whether the vehicle is suitable for their specific needs, particularly in densely populated areas.
What Are Common Trade Terminology and Jargon Related to the Toyota Dyna Custom?
Navigating the procurement process for the Toyota Dyna Custom involves understanding key trade terminologies that can significantly impact the purchasing experience.
1. OEM (Original Equipment Manufacturer)
OEM refers to companies that produce parts and equipment that may be marketed by another manufacturer. For international buyers, working with OEMs can ensure that they receive high-quality, compatible components for the Toyota Dyna Custom, which can be crucial for maintenance and repairs.
2. MOQ (Minimum Order Quantity)
MOQ is the smallest quantity of a product that a supplier is willing to sell. Understanding the MOQ for the Toyota Dyna Custom is essential for B2B buyers who may be looking to purchase in bulk. This term helps businesses plan their procurement strategies and manage inventory effectively.
3. RFQ (Request for Quotation)
An RFQ is a standard business process where buyers request price quotes from suppliers for specific products or services. For international buyers, submitting an RFQ for the Toyota Dyna Custom can help in comparing prices, understanding delivery times, and evaluating supplier capabilities.
4. Incoterms
Incoterms, or International Commercial Terms, are a set of rules that define the responsibilities of buyers and sellers in international transactions. Familiarity with Incoterms is crucial for B2B buyers as it clarifies shipping costs, risks, and delivery obligations, thereby facilitating smoother trade processes across borders.
5. Warranty Terms
Warranty terms define the conditions under which a product is repaired or replaced by the manufacturer. For the Toyota Dyna Custom, understanding the warranty can help buyers assess the long-term value of their investment and the level of support they can expect from the manufacturer, particularly in different regions.
By grasping these essential technical properties and trade terminologies, international B2B buyers can make informed decisions when considering the Toyota Dyna Custom, ensuring that their investments align with their operational needs and market conditions.
Navigating Market Dynamics and Sourcing Trends in the toyota dyna custom Sector
What Are the Key Market Dynamics and Trends in the Toyota Dyna Custom Sector?
The Toyota Dyna Custom sector is experiencing significant growth, driven by several global factors that international B2B buyers should consider. Firstly, there is an increasing demand for versatile and reliable commercial vehicles, particularly in emerging markets across Africa and South America. The rise of e-commerce and logistics sectors in these regions has heightened the need for efficient transportation solutions, positioning the Toyota Dyna Custom as an ideal option due to its adaptability and payload capacity.
In addition to this, technological advancements are reshaping sourcing strategies. The integration of digital platforms for procurement is becoming prevalent, enabling buyers to access real-time information and streamline their purchasing processes. B2B buyers from Europe and the Middle East are particularly benefiting from these technologies, which facilitate cross-border transactions and enhance transparency in supply chains.
Furthermore, sustainability is emerging as a pivotal consideration in procurement decisions. Buyers are increasingly inclined to partner with suppliers who demonstrate a commitment to environmentally friendly practices. This trend is not only shaping sourcing strategies but also influencing product development within the Toyota Dyna Custom sector, as manufacturers adapt to meet these evolving buyer expectations.
How Is Sustainability Shaping the Sourcing of Toyota Dyna Custom Vehicles?
Sustainability has become a cornerstone of modern procurement strategies, especially in the automotive sector. For international B2B buyers, understanding the environmental impact of their sourcing choices is crucial. The Toyota Dyna Custom, like many vehicles, has a carbon footprint associated with its production and lifecycle. Buyers are encouraged to engage with manufacturers who actively work to minimize this impact through innovative practices and technologies.
Ethical sourcing is equally significant. Suppliers that prioritize fair labor practices and responsible sourcing of materials not only enhance their brand reputation but also attract conscientious buyers. Certifications such as ISO 14001 (Environmental Management) and ISO 26000 (Social Responsibility) are indicators of a supplier’s commitment to sustainability and ethical practices. International buyers should seek out partners who hold these certifications, as they often translate to higher quality standards and reduced risk in the supply chain.
Additionally, the adoption of ‘green’ materials in the production of the Toyota Dyna Custom can significantly influence purchasing decisions. Buyers should inquire about the use of sustainable materials and the recyclability of vehicle components, as these factors can contribute to a more sustainable fleet and align with corporate social responsibility goals.
How Has the Toyota Dyna Custom Evolved Over Time?
The evolution of the Toyota Dyna Custom reflects broader trends in the commercial vehicle market. Initially launched as a robust and reliable truck, the Dyna series has undergone significant enhancements to meet the changing needs of businesses. Over the years, it has integrated advanced technologies such as fuel-efficient engines and improved safety features, making it increasingly attractive to international B2B buyers.
This evolution is not only about technology; it also includes a shift towards customization. Buyers now seek vehicles that can be tailored to specific operational needs, whether for logistics, construction, or other sectors. As a result, the Toyota Dyna Custom has expanded its range of configurations and options, offering buyers flexibility that aligns with their unique business requirements.
In summary, understanding the market dynamics, prioritizing sustainability, and recognizing the evolution of the Toyota Dyna Custom are essential for international B2B buyers looking to make informed and strategic procurement decisions.
Frequently Asked Questions (FAQs) for B2B Buyers of toyota dyna custom
-
How do I ensure the quality of a Toyota Dyna Custom before purchase?
To ensure the quality of a Toyota Dyna Custom, conduct a thorough supplier vetting process. Request detailed product specifications, certifications, and compliance with international standards. It is advisable to visit the manufacturing facility if possible or engage a third-party quality assurance service to conduct inspections. Additionally, request sample units to assess performance and durability firsthand. Establishing clear communication with the supplier about quality expectations is also crucial. -
What is the best way to customize a Toyota Dyna Custom for my business needs?
The best way to customize a Toyota Dyna Custom is to start by identifying your specific operational requirements. Work closely with the supplier to explore available customization options, such as cargo space modifications, engine upgrades, and interior fittings. Ensure the customization aligns with local regulations and market demands. It’s beneficial to create a prototype or mock-up to visualize the changes before finalizing the order, allowing for adjustments based on your feedback. -
What are the minimum order quantities (MOQ) for Toyota Dyna Custom?
Minimum order quantities (MOQ) for Toyota Dyna Custom can vary significantly based on the supplier and the customization required. Generally, MOQs can range from a single unit for standard models to larger quantities for customized vehicles. It’s crucial to discuss MOQs upfront during negotiations, as some suppliers may be flexible, especially if you can provide a solid business case for your order. This flexibility can be especially useful for smaller businesses or startups. -
What payment terms should I negotiate when sourcing Toyota Dyna Custom?
When sourcing Toyota Dyna Custom, it is vital to negotiate favorable payment terms that protect your cash flow. Common payment structures include upfront deposits (typically 30-50%), followed by milestone payments throughout the production process, and a final payment upon delivery. Consider using secure payment methods that offer buyer protection. Additionally, inquire about financing options or credit terms that may be available, especially if you are purchasing in larger quantities. -
How can I manage logistics when importing Toyota Dyna Custom?
Managing logistics for importing Toyota Dyna Custom involves several key steps. First, select a reliable freight forwarder experienced in handling vehicle shipments. Ensure that you understand the shipping terms (FOB, CIF, etc.) and associated costs. Prepare all necessary documentation, including import permits and customs clearance paperwork. Consider the delivery timeline and potential delays, and establish a clear communication plan with your supplier to track the shipment progress. -
What are the common customs duties and taxes for importing Toyota Dyna Custom?
Customs duties and taxes for importing Toyota Dyna Custom can vary by country and are typically based on the vehicle’s value, engine size, and emissions standards. Research the specific tariffs applicable in your region and factor these costs into your budget. Consulting with a customs broker can provide clarity on the exact duties and help navigate the import process efficiently, ensuring compliance with local regulations. -
How can I assess the reputation of a supplier for Toyota Dyna Custom?
To assess a supplier’s reputation for Toyota Dyna Custom, start by reviewing online testimonials and ratings from previous customers. Engage with industry forums or trade groups for recommendations and insights. Request references and case studies from the supplier, and verify their track record in delivering quality vehicles on time. Additionally, consider their certifications, years in business, and response time to inquiries as indicators of reliability. -
What after-sales support should I expect from suppliers of Toyota Dyna Custom?
When sourcing Toyota Dyna Custom, it’s essential to understand the after-sales support offered by the supplier. This includes warranty coverage, parts availability, and technical support for maintenance and repairs. Inquire about training programs for your staff on vehicle operation and upkeep. A reputable supplier will provide a clear after-sales service plan, ensuring you have the necessary resources to manage any issues post-purchase efficiently.
Important Disclaimer & Terms of Use
⚠️ Important Disclaimer
The information provided in this guide, including content regarding manufacturers, technical specifications, and market analysis, is for informational and educational purposes only. It does not constitute professional procurement advice, financial advice, or legal advice.
While we have made every effort to ensure the accuracy and timeliness of the information, we are not responsible for any errors, omissions, or outdated information. Market conditions, company details, and technical standards are subject to change.
B2B buyers must conduct their own independent and thorough due diligence before making any purchasing decisions. This includes contacting suppliers directly, verifying certifications, requesting samples, and seeking professional consultation. The risk of relying on any information in this guide is borne solely by the reader.
Strategic Sourcing Conclusion and Outlook for toyota dyna custom
What Are the Key Takeaways for Strategic Sourcing of Toyota Dyna Custom?
In conclusion, effective strategic sourcing of the Toyota Dyna Custom is essential for international B2B buyers seeking to maximize value and operational efficiency. Understanding the diverse supply chain dynamics and leveraging local partnerships can significantly enhance procurement strategies. Buyers from Africa, South America, the Middle East, and Europe should prioritize suppliers that offer robust after-sales support and flexible financing options, which are crucial for maintaining competitiveness in their respective markets.
How Can Strategic Sourcing Enhance Your Business Operations?
The value of strategic sourcing lies in its ability to not only reduce costs but also improve product availability and quality. By fostering long-term relationships with manufacturers and distributors, businesses can benefit from more favorable terms and increased reliability. Furthermore, staying informed about market trends and technological advancements related to the Toyota Dyna Custom will empower companies to make informed purchasing decisions.
What Is the Future Outlook for International Buyers?
Looking ahead, the demand for versatile and efficient vehicles like the Toyota Dyna Custom will continue to grow. B2B buyers are encouraged to engage in proactive sourcing strategies, exploring emerging markets and innovative financing models. By doing so, they can position themselves for success in an increasingly competitive landscape. Take the next step in your sourcing journey—evaluate your current suppliers and seek partnerships that align with your long-term business goals.