Enhance Your Offerings: The Ultimate Platform Bed Custom Guide (2025)
Introduction: Navigating the Global Market for platform bed custom
Navigating the complexities of sourcing platform bed custom solutions can be a daunting task for international B2B buyers, especially those from diverse regions like Africa, South America, the Middle East, and Europe. Buyers often face challenges in finding reliable suppliers that meet specific design requirements and quality standards. This guide aims to demystify the process, providing insights into the various types of platform beds, their applications across different markets, and key considerations for effective supplier vetting.
In this comprehensive resource, we will delve into essential aspects such as material choices, design trends, and customization options that cater to specific regional preferences. Additionally, we will explore cost considerations and pricing strategies to help buyers make informed decisions that align with their budget and market expectations. By equipping B2B buyers with actionable insights and detailed supplier evaluation criteria, this guide empowers them to confidently navigate the global market for platform bed custom solutions.
Ultimately, our goal is to facilitate seamless procurement processes, enabling businesses to enhance their product offerings and meet the evolving demands of their customers. Whether you are looking to source platform beds for hotels, residential projects, or commercial spaces, this guide serves as your essential companion in making strategic purchasing decisions that drive success in your market.
Understanding platform bed custom Types and Variations
Type Name | Key Distinguishing Features | Primary B2B Applications | Brief Pros & Cons for Buyers |
---|---|---|---|
Standard Platform Bed | Simple, low-profile design with a solid base. | Retail furniture stores, hotels, dormitories. | Pros: Cost-effective, easy to assemble. Cons: Limited customization options. |
Storage Platform Bed | Built-in drawers or compartments for storage. | Apartments, smaller hotels, and guesthouses. | Pros: Maximizes space, functional. Cons: Heavier and may require more effort to move. |
Adjustable Platform Bed | Mechanisms for adjusting head and foot positions. | Healthcare facilities, luxury hotels, and spas. | Pros: Enhances comfort, beneficial for health. Cons: Higher cost, complex assembly. |
Customizable Platform Bed | Tailored designs, materials, and sizes to client needs. | High-end retailers, bespoke furniture makers. | Pros: Unique designs, meets specific requirements. Cons: Longer lead times, potentially higher costs. |
Eco-Friendly Platform Bed | Made from sustainable materials and non-toxic finishes. | Green hotels, eco-conscious retailers. | Pros: Attracts environmentally aware customers. Cons: May be pricier than conventional options. |
What Are the Characteristics of Standard Platform Beds?
Standard platform beds are characterized by their straightforward, low-profile design that typically features a solid base without the need for a box spring. These beds are often constructed from wood or metal, providing a sturdy foundation for a mattress. They are particularly suitable for retail furniture stores and budget-conscious buyers, such as hotels and dormitories, where cost-effectiveness is paramount. When considering a standard platform bed, B2B buyers should focus on durability and assembly ease, as these beds are often sold in flat-pack formats.
How Do Storage Platform Beds Maximize Space?
Storage platform beds incorporate built-in drawers or compartments, making them ideal for maximizing space in smaller living environments. This type is especially popular in apartments and guesthouses where room efficiency is critical. B2B buyers must consider the weight and mobility of these beds, as their additional features can make them heavier and less portable. However, the functional design can significantly enhance the usability of a room, making it a valuable investment for businesses catering to space-limited customers.
What Makes Adjustable Platform Beds Beneficial for Health?
Adjustable platform beds feature mechanisms that allow users to adjust the head and foot positions, providing enhanced comfort and support. These beds are commonly found in healthcare facilities, luxury hotels, and spas, where they cater to clients seeking comfort or therapeutic benefits. For B2B buyers, the key considerations include the bed’s complexity and cost, as these models tend to be more expensive and require more intricate assembly. However, their health benefits can justify the investment, especially in environments where guest comfort is a priority.
Why Choose Customizable Platform Beds for Unique Needs?
Customizable platform beds offer tailored designs, materials, and sizes to meet specific client needs. This type is favored by high-end retailers and bespoke furniture makers who cater to discerning customers seeking unique solutions. B2B buyers should be aware of the longer lead times and potentially higher costs associated with these custom orders. Nevertheless, the ability to create a unique product can significantly enhance brand reputation and customer satisfaction, making it a worthwhile option for businesses aiming for differentiation in a competitive market.
How Do Eco-Friendly Platform Beds Appeal to Conscious Consumers?
Eco-friendly platform beds are constructed from sustainable materials and finished with non-toxic coatings, appealing to environmentally conscious consumers. These beds are increasingly popular in green hotels and eco-conscious retailers, where sustainability is a key selling point. B2B buyers should assess the pricing of these beds, as they may be more expensive than conventional options. However, promoting eco-friendly products can attract a growing demographic of environmentally aware customers, enhancing brand loyalty and market reach.
Related Video: How to Build a Floating Platform Bed! (Materials & Instructions in Description)
Key Industrial Applications of platform bed custom
Industry/Sector | Specific Application of platform bed custom | Value/Benefit for the Business | Key Sourcing Considerations for this Application |
---|---|---|---|
Hospitality | Custom platform beds for hotels and resorts | Enhances guest comfort, improves aesthetic appeal | Material quality, durability, design customization options |
Real Estate | Platform beds for furnished apartments or rental units | Attracts tenants, maximizes space efficiency | Cost-effectiveness, ease of assembly, transport logistics |
Healthcare | Adjustable platform beds for patient care facilities | Supports patient comfort and recovery | Compliance with health regulations, material safety standards |
Educational Institutions | Custom platform beds for dormitories | Promotes student wellbeing, optimizes space usage | Bulk purchasing options, warranty, durability against wear |
Furniture Retail | Platform beds for retail display and sale | Boosts sales through attractive displays | Trend alignment, sourcing reliability, delivery timelines |
How Are Custom Platform Beds Used in the Hospitality Industry?
In the hospitality sector, custom platform beds are integral to enhancing the guest experience in hotels and resorts. They provide a modern aesthetic while ensuring superior comfort, which is essential for customer satisfaction and repeat business. Buyers in this industry should prioritize sourcing high-quality materials that offer durability and ease of maintenance, as well as customizable designs to align with the hotel’s branding.
What Role Do Custom Platform Beds Play in Real Estate Applications?
For real estate, particularly in furnished apartments and rental units, custom platform beds serve to maximize space efficiency and appeal to potential tenants. These beds often come with built-in storage options, making them ideal for smaller living spaces. B2B buyers should consider cost-effectiveness and ease of assembly, as well as logistics for transporting these beds to various locations, especially in regions with diverse infrastructure.
Why Are Custom Platform Beds Important in Healthcare Settings?
In healthcare facilities, adjustable platform beds are designed to cater to patient needs, supporting comfort and recovery. These beds can be tailored to accommodate various medical requirements, ensuring compliance with health regulations. Buyers in this sector must focus on sourcing beds that meet safety standards and are easy to sanitize, as well as ensuring they have the necessary features to assist healthcare professionals.
How Do Educational Institutions Benefit from Custom Platform Beds?
Educational institutions utilize custom platform beds in dormitories to promote student wellbeing and optimize space usage. These beds can be designed for multi-functionality, allowing for study space or storage underneath. When sourcing for this application, institutions should consider bulk purchasing options and warranties, as well as the durability of materials to withstand high usage rates.
What Are the Advantages of Custom Platform Beds in Furniture Retail?
In the furniture retail sector, custom platform beds can enhance showroom displays, attracting customers with their modern designs and functionality. They help to differentiate retailers in a competitive market. Retailers should focus on trend alignment and sourcing reliability, ensuring timely delivery to meet consumer demand while maintaining the quality that customers expect.
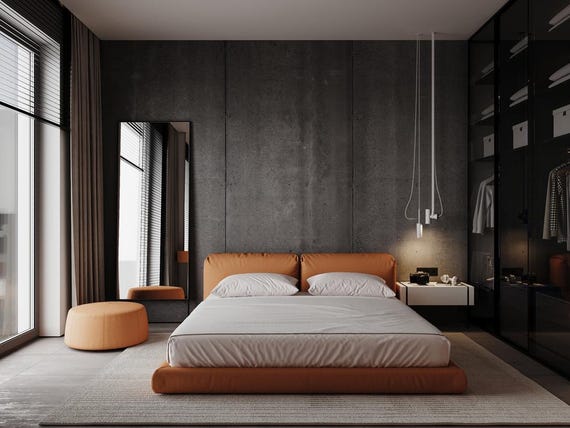
A stock image related to platform bed custom.
Related Video: universal robot – cobot – applications – case studies
3 Common User Pain Points for ‘platform bed custom’ & Their Solutions
Scenario 1: Navigating Quality Control for Custom Platform Beds
The Problem: One of the primary challenges faced by B2B buyers sourcing custom platform beds is ensuring consistent quality across different manufacturers. Buyers, particularly from regions like Africa and South America, may encounter variations in material quality and craftsmanship, leading to dissatisfaction among their customers and potential returns. Inconsistent quality not only affects customer satisfaction but can also tarnish the buyer’s brand reputation.
The Solution: To mitigate quality control issues, B2B buyers should establish clear specifications before placing orders. This includes defining the materials, dimensions, weight capacity, and aesthetic details of the platform beds. Additionally, conducting factory visits or virtual inspections can help ensure that the manufacturer adheres to these specifications. Collaborating with suppliers who offer samples before committing to larger orders can also serve as a safeguard against quality discrepancies. Implementing a quality assurance checklist and maintaining regular communication with suppliers will further enhance the consistency of the products received.
Scenario 2: Understanding Cultural Preferences in Design
The Problem: B2B buyers in diverse markets, such as the Middle East and Europe, often struggle with cultural preferences that influence the design and functionality of platform beds. For instance, certain regions may favor ornate designs, while others prefer minimalist aesthetics. Misunderstanding these cultural nuances can lead to poor sales performance and wasted inventory.
The Solution: To effectively address this issue, buyers should invest time in market research to understand regional preferences. This can be achieved through surveys, focus groups, or engaging local design experts. Additionally, establishing partnerships with regional distributors or retailers can provide valuable insights into consumer trends and preferences. Buyers should also consider offering a range of designs that cater to various tastes, ensuring they meet the diverse demands of their customer base. This approach not only boosts sales but also enhances customer loyalty and brand reputation.
Scenario 3: Managing Logistics and Delivery Timelines
The Problem: International B2B buyers frequently face logistical challenges when importing custom platform beds, particularly regarding shipping times and costs. Delays in delivery can disrupt sales cycles and inventory management, leading to lost revenue opportunities and dissatisfied customers.
The Solution: To effectively manage logistics, buyers should work closely with suppliers to create detailed shipping timelines that account for production and transit times. Utilizing a reliable freight forwarder can streamline the shipping process and reduce unexpected delays. Buyers should also consider using technology to track shipments in real-time, allowing them to proactively address any potential issues. Establishing a buffer stock or safety inventory can also help mitigate the impact of unforeseen delays, ensuring that the business can continue to meet customer demand even when shipments are delayed.
Strategic Material Selection Guide for platform bed custom
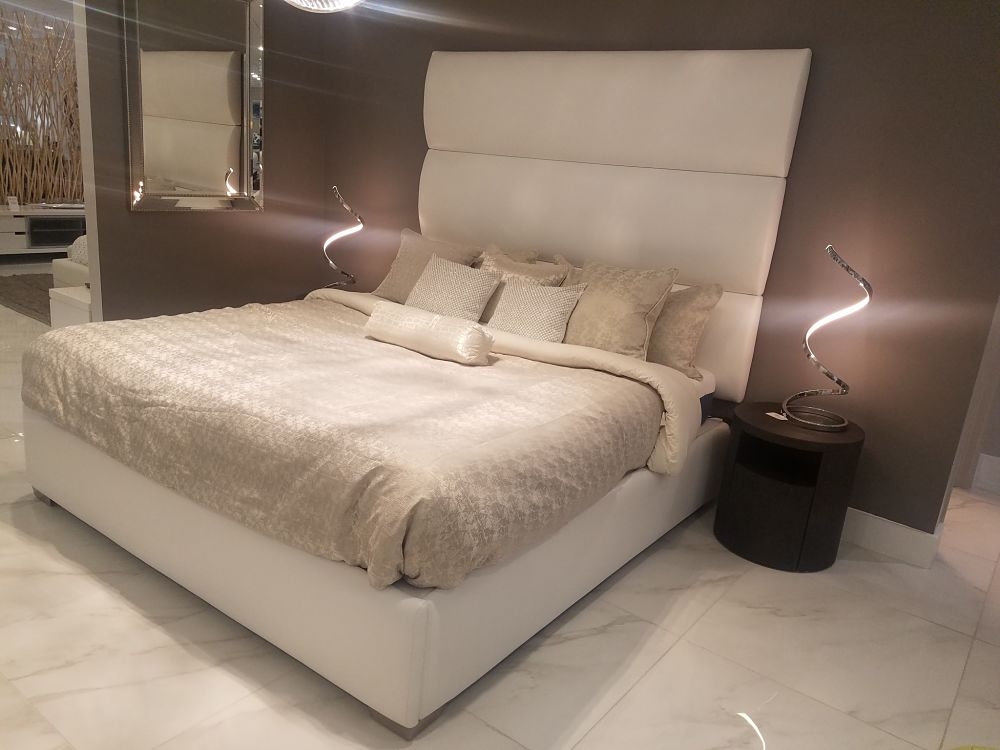
A stock image related to platform bed custom.
When selecting materials for custom platform beds, international B2B buyers must consider various factors that influence product performance, cost, and market preferences. Below are analyses of four common materials used in platform bed manufacturing, focusing on their properties, advantages, disadvantages, and specific considerations for buyers from Africa, South America, the Middle East, and Europe.
What are the Key Properties of Solid Wood in Platform Beds?
Solid wood is a traditional choice for platform beds due to its aesthetic appeal and structural integrity. Key properties include high strength and durability, with excellent resistance to wear and tear. Solid wood can handle significant weight without compromising its structural integrity, making it suitable for various mattress types.
Pros: Solid wood offers a timeless look and can be refinished, enhancing its longevity. It is also a renewable resource, appealing to environmentally conscious buyers.
Cons: The initial cost can be high, and the manufacturing process may require specialized skills. Additionally, solid wood can be susceptible to warping or cracking under extreme humidity or temperature changes.
Impact on Application: Solid wood beds are compatible with various mattress types, including memory foam and innerspring. However, buyers should consider local climate conditions that may affect wood stability.
Considerations for International Buyers: Compliance with local regulations regarding sustainable sourcing is essential. Buyers should also look for certifications like FSC (Forest Stewardship Council) to ensure responsible sourcing.
How Does Metal Compare as a Material for Platform Beds?
Metal, particularly steel and aluminum, is increasingly popular for platform beds due to its strength and modern aesthetic. Key properties include high tensile strength and excellent corrosion resistance, especially when treated with protective coatings.
Pros: Metal frames are often lighter than wood, making them easier to transport and assemble. They also tend to have a longer lifespan with minimal maintenance.
Cons: Metal can be more expensive than wood, and its cold aesthetic may not appeal to all consumers. Additionally, it may conduct heat, which could affect sleep comfort.
Impact on Application: Metal beds are suitable for various mattress types and can support heavier weights effectively. However, compatibility with certain mattress foundations should be verified.
Considerations for International Buyers: Buyers should ensure compliance with international standards such as ASTM for safety and quality. Additionally, regional preferences for design and aesthetics should be taken into account.
What are the Benefits of Plywood in Platform Bed Construction?
Plywood is engineered from layers of wood veneer, providing a balance between strength and weight. Key properties include good dimensional stability and resistance to warping.
Pros: Plywood is generally more affordable than solid wood and can be produced in large sheets, reducing waste. It also offers a modern look and is less prone to the issues of solid wood.
Cons: While durable, plywood may not offer the same longevity as solid wood. It can also be more susceptible to damage from moisture if not properly sealed.
Impact on Application: Plywood is compatible with various mattress types and offers a solid foundation. However, it may require additional treatment for moisture resistance in humid climates.
Considerations for International Buyers: Buyers should look for plywood that meets international standards such as JIS or EN for quality assurance. Additionally, sourcing from reputable suppliers who adhere to sustainable practices is advisable.
Why is MDF a Viable Option for Platform Beds?
Medium Density Fiberboard (MDF) is an engineered wood product made from wood fibers, wax, and resin. Key properties include a smooth surface ideal for painting and finishing, along with good weight-bearing capabilities.
Pros: MDF is cost-effective and can be produced in various designs, making it versatile for custom applications. Its smooth surface allows for high-quality finishes.
Cons: MDF is less durable than solid wood and can be affected by moisture, leading to swelling or warping. It also has a lower weight capacity compared to solid wood or metal.
Impact on Application: MDF is suitable for lighter mattresses and can be used in decorative applications. However, it may not be ideal for heavy-duty use.
Considerations for International Buyers: Compliance with safety standards such as E1 for formaldehyde emissions is crucial. Buyers should also consider the regional market’s acceptance of MDF in terms of quality perception.
Summary Table of Material Selection for Platform Beds
Material | Typical Use Case for platform bed custom | Key Advantage | Key Disadvantage/Limitation | Relative Cost (Low/Med/High) |
---|---|---|---|---|
Solid Wood | High-end, durable platform beds | Timeless aesthetic, renewable | High cost, susceptible to warping | High |
Metal | Modern, lightweight platform beds | High strength, corrosion-resistant | Higher cost, cold aesthetic | Medium |
Plywood | Cost-effective, versatile platform beds | Affordable, less prone to warping | Less durable than solid wood | Low |
MDF | Decorative, lightweight platform beds | Cost-effective, smooth finish | Less durable, moisture-sensitive | Low |
This strategic material selection guide provides valuable insights for international B2B buyers, enabling them to make informed decisions based on material properties, costs, and compliance with regional standards.
In-depth Look: Manufacturing Processes and Quality Assurance for platform bed custom
When considering the manufacturing processes and quality assurance for custom platform beds, international B2B buyers need to be well-informed about the various stages of production, quality checkpoints, and standards that ensure the final product meets their expectations. This guide will delve into the manufacturing processes, quality control measures, and how buyers can effectively verify suppliers.
What Are the Main Stages of Manufacturing Custom Platform Beds?
The production of custom platform beds typically involves four main stages: material preparation, forming, assembly, and finishing. Each stage is crucial in ensuring that the final product meets both design specifications and quality standards.
-
Material Preparation:
– In this initial phase, raw materials such as wood, metal, or upholstery fabric are sourced and prepared. Quality of materials is paramount, as this directly affects durability and aesthetics. Suppliers should provide certifications for sustainably sourced wood or high-grade metals.
– Buyers should look for suppliers who can demonstrate adherence to environmental regulations, particularly those related to sourcing and processing materials. -
Forming:
– This stage involves cutting, shaping, and molding materials into the desired forms. Advanced techniques, such as CNC machining for wood or laser cutting for metal, are often used to achieve precision.
– Customization options, such as unique shapes or sizes, can be accommodated at this stage, making it essential for buyers to communicate their specific requirements clearly. -
Assembly:
– After the components are formed, they are assembled. This may involve joining wooden parts with dowels or screws and welding metal frames. The assembly process is critical for the structural integrity of the platform bed.
– Quality checks during assembly should include verifying alignment and ensuring that all components fit together seamlessly. -
Finishing:
– The final stage includes sanding, painting, or applying protective coatings. This not only enhances the aesthetic appeal but also provides protection against wear and tear.
– Buyers should inquire about the types of finishes used, ensuring they are non-toxic and safe for use in residential settings.
How Is Quality Assurance Implemented in Custom Platform Bed Manufacturing?
Quality assurance (QA) is integral to the manufacturing process, ensuring that the final product meets specified standards. Several international and industry-specific standards guide this process.
-
Relevant International Standards:
– ISO 9001: This standard outlines the criteria for a quality management system and is applicable to any organization. Certification indicates that the supplier has a robust system in place for ensuring product quality.
– CE Marking: For European buyers, CE marking is essential, as it signifies that the product meets EU safety, health, and environmental protection requirements. -
Industry-Specific Standards:
– Depending on the materials used, other standards may apply. For example, the American National Standards Institute (ANSI) provides guidelines specific to furniture safety.
– Buyers should verify that suppliers are compliant with these industry standards, as they can significantly influence product safety and durability.
What Are the Key Quality Control Checkpoints in Manufacturing?
Quality control (QC) checkpoints are strategically placed throughout the manufacturing process to catch defects early and ensure product quality.
-
Incoming Quality Control (IQC):
– This occurs before production begins, where raw materials are inspected for quality and compliance with specifications. Any subpar materials can be rejected, preventing issues later in the process. -
In-Process Quality Control (IPQC):
– During the manufacturing stages, continuous checks are performed to ensure that each step meets quality standards. This includes monitoring machinery settings and verifying that assembly processes are followed correctly. -
Final Quality Control (FQC):
– Once the platform beds are fully assembled, a final inspection is conducted. This includes testing for structural integrity, finish quality, and functionality. Buyers should request detailed reports on FQC procedures.
How Can B2B Buyers Verify Supplier Quality Control?
For international B2B buyers, verifying a supplier’s quality control processes is essential to ensure that products meet their specifications and standards.
-
Conducting Audits:
– Regular audits of suppliers can provide insights into their manufacturing processes and quality assurance measures. Buyers should consider both announced and unannounced audits to get a comprehensive view of operations. -
Requesting Quality Reports:
– Suppliers should be able to provide detailed quality reports, including results from IQC, IPQC, and FQC. These documents should outline the testing methods used and any corrective actions taken for defects. -
Third-Party Inspections:
– Engaging third-party inspection services can provide an unbiased assessment of a supplier’s quality control processes. This is particularly useful for buyers unfamiliar with local manufacturing standards.
What Are the Nuances of Quality Control for International Buyers?
International B2B buyers, particularly from regions such as Africa, South America, the Middle East, and Europe, must navigate various challenges when ensuring quality control.
-
Understanding Local Standards:
– Buyers should familiarize themselves with the local regulations and standards applicable in the supplier’s country. This includes understanding any specific compliance requirements that may differ from their own region. -
Language and Communication Barriers:
– Effective communication is key to ensuring that quality expectations are understood. Buyers may need to employ translators or local representatives to facilitate discussions about quality standards and specifications. -
Cultural Considerations:
– Different cultures may have varying approaches to quality assurance and customer service. Buyers should be sensitive to these differences and establish clear expectations to avoid misunderstandings.
By understanding the manufacturing processes and quality assurance measures in place for custom platform beds, international B2B buyers can make informed decisions and foster successful partnerships with suppliers. Prioritizing quality at every stage of production not only enhances product satisfaction but also builds long-term trust between buyers and manufacturers.
Practical Sourcing Guide: A Step-by-Step Checklist for ‘platform bed custom’
In the competitive landscape of B2B procurement, especially for custom platform beds, having a structured approach can significantly enhance your sourcing effectiveness. This guide provides a practical checklist to ensure you make informed decisions when procuring custom platform beds tailored to your business needs.
Step 1: Define Your Technical Specifications
Establishing clear technical specifications is the first critical step in your sourcing process. This includes determining dimensions, materials, load capacity, and design features that meet your target market’s preferences. Understanding these specifications helps you communicate your needs effectively to suppliers and ensures that the final product aligns with your expectations.
Step 2: Conduct Market Research
Before engaging with suppliers, conduct thorough market research to understand current trends in platform bed designs and materials. This will help you identify what is popular among consumers and what competitors are offering. Look for insights on pricing, material sustainability, and innovative design features that can give your offerings a competitive edge.
Step 3: Evaluate Potential Suppliers
Before committing, it’s crucial to vet suppliers thoroughly. Request company profiles, case studies, and references from buyers in similar industries or regions. Ensure they have a track record of delivering quality products and meeting deadlines, as reliability is key in B2B transactions.
- Check their production capabilities: Assess whether they can meet your volume requirements and whether they have the necessary machinery and technology.
- Inquire about customization options: Understand how flexible they are with design changes and adaptations.
Step 4: Verify Supplier Certifications
Confirm that potential suppliers possess relevant certifications that demonstrate compliance with international quality standards, such as ISO certifications. Certifications can provide assurance regarding the quality of materials used and manufacturing processes employed. This step is particularly important if you are sourcing from regions with varying industry standards.
Step 5: Request Samples
Always request product samples before making a bulk order. This allows you to assess the quality, craftsmanship, and suitability of the materials firsthand. Pay attention to the finishing, sturdiness, and overall aesthetics of the samples provided.
Step 6: Negotiate Pricing and Terms
Once you have shortlisted suppliers, engage in negotiations to establish pricing, payment terms, and delivery schedules. Be transparent about your budget but remain open to discussing value-added services, such as after-sales support or bulk order discounts. This can lead to a mutually beneficial agreement.
Step 7: Establish Communication Channels
After selecting a supplier, establish clear communication channels to facilitate ongoing dialogue. Regular updates on production progress, delivery timelines, and any potential challenges will help maintain a strong partnership. Effective communication is essential for resolving issues quickly and ensuring that your procurement process runs smoothly.
Following this checklist will empower you to make informed decisions, mitigate risks, and ultimately procure high-quality custom platform beds that align with your business objectives.
Comprehensive Cost and Pricing Analysis for platform bed custom Sourcing
What Are the Key Cost Components in Platform Bed Custom Sourcing?
When engaging in custom sourcing for platform beds, understanding the cost structure is crucial. The primary cost components include:
-
Materials: The choice of materials significantly impacts pricing. Options range from solid wood to engineered wood, metal, or upholstered finishes. Each material carries different costs influenced by quality and availability.
-
Labor: Labor costs can vary based on the region and skill level required for production. Countries with lower labor costs may offer competitive pricing, but quality assurance is essential.
-
Manufacturing Overhead: This encompasses utilities, rent, and operational costs of the factory. Efficient manufacturing processes can reduce overhead, thereby influencing the final price.
-
Tooling: Custom designs may require specialized tools and molds, which can add to initial costs. Suppliers often spread these costs over larger production runs, making it essential to consider order volume.
-
Quality Control (QC): Implementing stringent QC measures ensures that products meet specified standards. While this may increase upfront costs, it mitigates risks associated with defects and returns.
-
Logistics: Shipping and handling play a significant role in total cost, particularly for international buyers. Factors such as distance, mode of transport, and customs duties should be factored into the pricing analysis.
-
Margin: Supplier margins can vary widely. Understanding the margin expectations can help in negotiating better prices.
How Do Price Influencers Affect Platform Bed Custom Sourcing?
Several factors influence the pricing of custom platform beds:
-
Volume/MOQ (Minimum Order Quantity): Higher order volumes often lead to lower unit prices. Suppliers may offer discounts for bulk orders, making it advantageous for buyers to plan purchases strategically.
-
Specifications and Customization: Unique designs or features (like integrated storage or adjustable heights) can lead to increased costs. Clear communication of specifications during the quoting process is essential to avoid surprises.
-
Material Choices: Premium materials will naturally elevate costs. Buyers should balance quality and cost to meet their target market needs without compromising on durability.
-
Quality Certifications: Certifications (e.g., ISO, FSC) can add credibility but may also increase costs. Understanding the market requirements for certifications in the buyer’s region can help in making informed decisions.
-
Supplier Factors: The reputation and reliability of the supplier can impact pricing. Established suppliers may charge a premium for their experience and quality assurance processes.
-
Incoterms: The chosen Incoterms (e.g., FOB, CIF) determine who bears the cost of shipping and insurance, significantly affecting the total landed cost.
What Buyer Tips Can Help Negotiate Better Prices for Platform Beds?
International B2B buyers should consider the following strategies to enhance cost-efficiency:
-
Negotiate Effectively: Building a good relationship with suppliers can lead to better negotiation outcomes. Be transparent about your needs and explore options for discounts based on order size or long-term commitments.
-
Focus on Total Cost of Ownership (TCO): Instead of just considering the purchase price, evaluate the TCO, which includes maintenance, durability, and logistics costs. This holistic view can guide better purchasing decisions.
-
Understand Pricing Nuances for International Sourcing: Buyers from Africa, South America, the Middle East, and Europe should be aware of regional market dynamics, currency fluctuations, and potential tariffs that may affect pricing.
-
Request Detailed Quotes: Ask suppliers for itemized quotes that break down costs. This transparency can help identify areas for negotiation and clarify what factors contribute to the final price.
Disclaimer on Indicative Prices
It’s important to note that the prices for custom platform beds can vary significantly based on numerous factors outlined above. Buyers are encouraged to conduct thorough market research and obtain multiple quotes to ensure competitive pricing.
Alternatives Analysis: Comparing platform bed custom With Other Solutions
When considering the procurement of a platform bed custom, it is essential for international B2B buyers to evaluate various alternatives that may suit their specific needs. By comparing different solutions, buyers can make informed decisions that align with their operational goals, budget constraints, and market demands. Below is a comparative analysis of platform bed custom against two viable alternatives: traditional bed frames and modular bedding systems.
Comparison Aspect | Platform Bed Custom | Traditional Bed Frame | Modular Bedding System |
---|---|---|---|
Performance | High durability; tailored design for optimal support | Varies by material; often less sturdy | Flexible configurations; supports various needs |
Cost | Higher initial investment due to customization | Generally lower cost | Moderate cost; depends on configuration |
Ease of Implementation | Requires skilled labor for assembly | Easy to assemble; minimal tools needed | Moderate; requires understanding of modular components |
Maintenance | Low maintenance; durable materials | Varies; can require periodic tightening | Low; easy to replace individual components |
Best Use Case | Luxury hotels, custom residential projects | Budget-conscious consumers, standard hotels | Adaptive spaces, temporary accommodations |
What Are the Pros and Cons of Traditional Bed Frames Compared to Platform Bed Custom?
Traditional bed frames are widely recognized for their affordability and ease of assembly. They typically require minimal tools for setup and can be found in various styles and materials, making them accessible for a broad market. However, their performance can vary significantly based on construction quality, and they often lack the durability and tailored support that a platform bed custom provides. For B2B buyers focused on budget-friendly options, traditional bed frames may serve well in standard accommodations but may not meet the luxury or durability requirements of higher-end projects.
How Do Modular Bedding Systems Compare to Platform Bed Custom?
Modular bedding systems offer flexibility and adaptability, allowing businesses to configure their bedding arrangements according to specific space requirements. This can be particularly beneficial for hotels or facilities that require versatile setups for different guest needs. While the cost is generally moderate and can be tailored to fit various budgets, the initial learning curve associated with assembly can be a drawback. Additionally, while these systems require low maintenance, they may not provide the same level of durability and aesthetic appeal as a well-crafted platform bed custom.
How Can B2B Buyers Choose the Right Solution for Their Needs?
In conclusion, choosing the right bedding solution depends on several factors, including budget, intended use, and desired aesthetics. Buyers should assess their specific needs and consider how each alternative aligns with their operational goals. For luxury and durability, platform bed custom remains the best choice; however, for budget-sensitive projects, traditional bed frames may suffice. If flexibility is paramount, modular bedding systems could be the ideal solution. By evaluating these options thoroughly, B2B buyers from diverse regions, including Africa, South America, the Middle East, and Europe, can select a solution that best fits their market demands and customer expectations.
Essential Technical Properties and Trade Terminology for platform bed custom
What Are the Key Technical Properties of Custom Platform Beds?
When sourcing custom platform beds, understanding the critical technical specifications is vital. These properties not only affect the product’s quality but also impact pricing, durability, and customer satisfaction.
1. Material Grade: Why Is It Crucial for Durability?
The material grade refers to the quality of the materials used in the construction of the platform bed. Common materials include solid wood, engineered wood, and metal. Higher-grade materials typically offer better durability, aesthetics, and resistance to wear and tear. For B2B buyers, selecting the appropriate material grade can mean the difference between a profitable investment and frequent replacements.
2. Weight Capacity: How Does It Affect Design Choices?
Weight capacity is the maximum load a platform bed can safely support. This specification is critical for ensuring the safety and functionality of the product. When negotiating with suppliers, it’s essential to clarify weight limits to meet the needs of your target market, particularly for regions where larger bed frames may be preferred.
3. Tolerance Levels: What Do They Mean for Manufacturing Precision?
Tolerance levels define the permissible deviation in dimensions during the manufacturing process. For example, a tolerance of ±2mm on a platform bed frame means that the actual size can vary slightly from the specified dimensions. Understanding these tolerances is crucial for B2B buyers to ensure that the final product fits well with other components, such as mattresses and headboards.
4. Finish and Coating: How Do They Impact Aesthetics and Longevity?
The finish and coating of a platform bed can significantly influence its appearance and durability. Common finishes include varnish, lacquer, and paint, each offering different levels of protection against moisture and scratches. Selecting the right finish not only enhances visual appeal but also extends the life of the product, which is essential for maintaining customer satisfaction.
5. Assembly Requirements: Why Should You Consider Them?
Assembly requirements refer to the complexity involved in putting together the platform bed. Some designs may require specialized tools or significant time investment. Understanding these requirements can help B2B buyers assess potential shipping costs and labor implications, ultimately affecting the bottom line.
What Are Common Trade Terms in the Platform Bed Industry?
Familiarity with industry jargon is essential for effective communication and negotiation in the B2B space. Here are several key terms you should know:
1. OEM (Original Equipment Manufacturer): What Does It Entail?
OEM refers to a company that manufactures products or components that are purchased by another company and sold under the latter’s brand name. For B2B buyers, working with OEMs can streamline production and allow for customization without investing heavily in manufacturing capabilities.
2. MOQ (Minimum Order Quantity): Why Is It Important?
MOQ is the smallest quantity of a product that a supplier is willing to sell. Understanding MOQs is crucial for B2B buyers, as they influence inventory levels and initial investment costs. It’s often beneficial to negotiate MOQs to align with market demand and cash flow.
3. RFQ (Request for Quotation): How Should You Use It?
An RFQ is a document sent to suppliers requesting a quote for specific quantities of a product. This process allows buyers to compare prices and terms from multiple suppliers, facilitating informed decision-making. Including detailed specifications in an RFQ can lead to more accurate and competitive quotes.
4. Incoterms (International Commercial Terms): How Do They Affect Shipping?
Incoterms are a set of internationally recognized rules that define the responsibilities of buyers and sellers in international transactions. Understanding these terms is essential for B2B buyers to clarify shipping costs, risk, and delivery responsibilities, ultimately impacting the total landed cost of the product.
5. Lead Time: Why Does It Matter for Inventory Management?
Lead time refers to the duration between placing an order and receiving the goods. For B2B buyers, understanding lead times is critical for inventory management and ensuring that products are available to meet customer demand without excessive stockpiling.
By grasping these technical properties and trade terms, international B2B buyers can make informed decisions that enhance their sourcing strategies and operational efficiency in the custom platform bed market.
Navigating Market Dynamics and Sourcing Trends in the platform bed custom Sector
What Are the Current Market Dynamics and Key Trends in the Platform Bed Custom Sector?
The global platform bed custom market is experiencing notable growth, driven by several key factors. One of the primary drivers is the increasing consumer preference for minimalist design and multifunctional furniture, particularly among younger demographics. This trend is further fueled by urbanization, as space constraints in metropolitan areas lead buyers to seek furniture that maximizes utility without sacrificing aesthetics.
For international B2B buyers, particularly from Africa, South America, the Middle East, and Europe, emerging technologies are reshaping sourcing trends in this sector. Innovations such as augmented reality (AR) and virtual reality (VR) are enhancing the buying experience, allowing customers to visualize products in their spaces before making a purchase. Additionally, the rise of e-commerce platforms is making it easier for businesses to connect with manufacturers and suppliers, streamlining the procurement process.
Market dynamics also indicate a shift toward customization, where buyers are increasingly looking for personalized designs that cater to specific needs and preferences. This demand for bespoke solutions encourages manufacturers to adopt flexible production methods, enabling them to respond quickly to changing customer requirements. As a result, partnerships with local artisans and manufacturers can be advantageous for buyers seeking unique offerings.
How Is Sustainability and Ethical Sourcing Addressed in the Platform Bed Custom Sector?
Sustainability is becoming a critical consideration in the platform bed custom sector. With the growing awareness of environmental issues, buyers are increasingly prioritizing products that minimize ecological impact. This includes the use of sustainably sourced materials, such as bamboo and reclaimed wood, which not only reduce deforestation but also appeal to environmentally conscious consumers.
Ethical sourcing is equally important, as businesses are held accountable for their supply chain practices. Buyers should look for manufacturers that prioritize fair labor practices and transparency in their sourcing processes. Certifications such as Forest Stewardship Council (FSC) or Global Organic Textile Standard (GOTS) can serve as indicators of a supplier’s commitment to sustainability and ethical practices.
Investing in “green” certifications and sustainable materials not only supports the environment but can also enhance brand reputation and customer loyalty. B2B buyers who align their sourcing strategies with sustainability goals can differentiate themselves in a competitive market, appealing to the growing demographic of eco-conscious consumers.
What Is the Evolution of the Platform Bed Custom Sector?
The platform bed custom sector has evolved significantly over the past few decades. Initially rooted in traditional craftsmanship, the industry has gradually incorporated modern design principles and manufacturing techniques. The rise of globalization has facilitated access to diverse materials and styles, allowing for a broader range of options in design.
In recent years, the focus has shifted towards personalization and customization, driven by changing consumer preferences and technological advancements. This evolution has led to a more dynamic market where businesses must stay agile to meet the demands of an increasingly discerning clientele. As the sector continues to adapt, the integration of sustainable practices and ethical sourcing will likely play a pivotal role in shaping its future trajectory.
Frequently Asked Questions (FAQs) for B2B Buyers of platform bed custom
- How do I choose the right supplier for custom platform beds?
When selecting a supplier for custom platform beds, consider their experience in manufacturing and customization capabilities. Look for suppliers with a proven track record, positive reviews, and strong communication practices. Request samples to evaluate quality and craftsmanship. It’s also advisable to verify certifications and compliance with international standards, especially if you are sourcing from regions like Africa or South America, where quality assurance may vary.
-
What are the typical minimum order quantities (MOQs) for custom platform beds?
Minimum order quantities for custom platform beds can vary significantly based on the supplier and the complexity of the design. Typically, MOQs range from 50 to 200 units. Suppliers may offer lower MOQs for standard designs but may require higher quantities for fully customized options. Always clarify MOQs during initial discussions to ensure they align with your purchasing capabilities and market demand. -
What customization options should I consider for platform beds?
Customization options for platform beds include material selection (wood, metal, upholstered), size variations (twin, queen, king), color finishes, and design features (storage drawers, headboard styles). Additionally, you may want to explore eco-friendly materials if sustainability is a concern for your market. Discussing these options early with suppliers can help you create a product that meets your brand’s unique requirements. -
What payment terms are common in international B2B transactions for custom furniture?
Common payment terms in international B2B transactions typically include a deposit (often 30-50%) upfront, with the balance paid before shipment or upon delivery. Some suppliers may offer letters of credit or payment through escrow services to secure both parties. Always negotiate terms that protect your investment while ensuring the supplier’s commitment to fulfilling the order.
-
How can I ensure quality assurance for custom platform beds?
To ensure quality assurance, establish a clear set of quality standards and specifications before production begins. Request regular updates and photos during the manufacturing process. Conduct a final inspection before shipment, either in-person or through a third-party quality control service. For international transactions, consider suppliers who have quality certifications like ISO or those who adhere to international furniture standards. -
What logistics considerations should I keep in mind when importing platform beds?
When importing platform beds, consider factors such as shipping costs, transit times, and customs duties. Choose a reliable freight forwarder familiar with your specific region’s regulations to ensure smooth logistics. Additionally, factor in the need for warehousing and distribution in your target market to efficiently manage inventory and fulfill orders. -
What are the best practices for vetting suppliers of custom platform beds?
Vetting suppliers involves assessing their business credentials, production capabilities, and customer service reputation. Request references and check their industry experience, particularly in your desired market. Engage in direct communication to gauge their responsiveness and willingness to collaborate. Conduct site visits if possible, or utilize third-party inspection services to verify operational standards.
- How do I handle disputes with suppliers for custom platform beds?
Handling disputes effectively requires a clear communication channel and documented agreements. Address issues promptly and professionally, referring to the terms outlined in your contract. If informal resolution fails, consider mediation or arbitration as cost-effective alternatives to litigation. Always ensure that your contracts include dispute resolution clauses to protect your interests in international transactions.
Important Disclaimer & Terms of Use
⚠️ Important Disclaimer
The information provided in this guide, including content regarding manufacturers, technical specifications, and market analysis, is for informational and educational purposes only. It does not constitute professional procurement advice, financial advice, or legal advice.
While we have made every effort to ensure the accuracy and timeliness of the information, we are not responsible for any errors, omissions, or outdated information. Market conditions, company details, and technical standards are subject to change.
B2B buyers must conduct their own independent and thorough due diligence before making any purchasing decisions. This includes contacting suppliers directly, verifying certifications, requesting samples, and seeking professional consultation. The risk of relying on any information in this guide is borne solely by the reader.
Strategic Sourcing Conclusion and Outlook for platform bed custom
In navigating the complexities of sourcing custom platform beds, international B2B buyers are positioned to leverage strategic sourcing for maximum advantage. Key takeaways include the importance of establishing strong relationships with manufacturers who understand local market needs and preferences. Buyers should prioritize vendors that demonstrate flexibility in design, quality assurance, and timely delivery, as these factors directly impact customer satisfaction and brand loyalty.
Moreover, understanding regional manufacturing capabilities can enhance cost-effectiveness, especially for buyers in Africa, South America, the Middle East, and Europe. By aligning sourcing strategies with local suppliers, businesses can reduce lead times and foster community economic growth, which is increasingly valued in today’s global marketplace.
Looking ahead, the demand for customizable furniture solutions like platform beds will continue to rise. Buyers are encouraged to stay abreast of emerging trends in sustainable materials and innovative designs that meet evolving consumer preferences. Engaging in continuous dialogue with suppliers and exploring diverse sourcing options will be crucial for staying competitive. Embrace the future of sourcing—connect, collaborate, and create impactful partnerships that will elevate your business in the custom furniture landscape.