Find Reliable Safety Glasses Suppliers: Your Ultimate Guide (2025)
Introduction: Navigating the Global Market for safety glasses supplier
In today’s global market, sourcing high-quality safety glasses can be a daunting challenge for international B2B buyers, particularly for those in regions like Africa, South America, the Middle East, and Europe. With stringent safety regulations and diverse workplace environments, ensuring that employees are equipped with the right protective eyewear is not just a legal obligation but a critical component of workplace safety. This comprehensive guide aims to demystify the process of selecting a reliable safety glasses supplier, addressing key factors such as product types, applications, supplier vetting processes, and cost considerations.
By understanding the various types of safety glasses available—ranging from impact-resistant models to specialized eyewear for specific industries—B2B buyers can make informed decisions that meet both safety standards and budget constraints. Additionally, this guide will provide actionable insights on how to effectively evaluate potential suppliers, ensuring that they align with your company’s quality and compliance requirements.
For businesses operating in regions with distinct safety challenges, such as the construction industries in South America or manufacturing sectors in Europe, this guide serves as a valuable resource. It empowers buyers to navigate the complexities of the global market with confidence, enabling them to secure the best products for their workforce while minimizing risk and maximizing safety.
Understanding safety glasses supplier Types and Variations
Type Name | Key Distinguishing Features | Primary B2B Applications | Brief Pros & Cons for Buyers |
---|---|---|---|
General Safety Glasses | Basic impact resistance, UV protection | Manufacturing, Construction | Pros: Affordable, versatile. Cons: Limited features. |
Prescription Safety Glasses | Custom lenses, tailored fit | Laboratories, Healthcare | Pros: Enhanced vision, compliance with safety standards. Cons: Higher cost. |
Anti-Fog Safety Glasses | Special coatings to prevent fogging | Outdoor Work, Emergency Services | Pros: Clear visibility in humid conditions. Cons: Coating may wear off. |
Welding Safety Glasses | Darkened lenses, heat resistance | Welding, Metal Fabrication | Pros: Protects against bright light and sparks. Cons: Limited visibility in low light. |
High-Performance Safety Glasses | Advanced materials, specialized features | Aerospace, Heavy Industry | Pros: Superior protection, durability. Cons: Higher price point. |
What are the Characteristics of General Safety Glasses?
General safety glasses are designed to provide basic eye protection against impact and UV radiation. They typically feature polycarbonate lenses, which are lightweight and resistant to shattering. These glasses are widely used in various industries such as manufacturing and construction, where the risk of flying debris is prevalent. When purchasing, buyers should consider compliance with safety standards, comfort, and the potential for additional features like anti-scratch coatings.
How Do Prescription Safety Glasses Meet Specific Needs?
Prescription safety glasses cater to individuals who require vision correction while ensuring eye safety. These glasses are fitted with custom lenses that meet specific visual needs, making them ideal for environments where precision is crucial, such as laboratories and healthcare settings. When sourcing these glasses, buyers should evaluate the supplier’s ability to provide accurate prescriptions and the availability of various frame styles that comply with safety regulations.
Why Choose Anti-Fog Safety Glasses for Humid Conditions?
Anti-fog safety glasses are specially designed with coatings that prevent condensation on lenses, making them essential for outdoor work or emergency services where visibility can be compromised by humidity or temperature changes. These glasses are particularly useful in climates prevalent in Africa and South America. Buyers should consider the longevity of the anti-fog coating and ensure that the glasses meet the necessary safety standards for their specific applications.
What Makes Welding Safety Glasses Unique?
Welding safety glasses are equipped with darkened lenses to protect the eyes from intense light and heat generated during welding processes. They are essential in industries like metal fabrication and construction, where workers face exposure to harmful rays and flying sparks. Buyers should assess the lens shade suitable for their specific welding applications and ensure compliance with relevant safety standards to prevent eye injuries.
How Do High-Performance Safety Glasses Offer Enhanced Protection?
High-performance safety glasses are crafted from advanced materials and often include specialized features such as adjustable frames, enhanced impact resistance, and anti-fog properties. These glasses are ideal for high-risk environments such as aerospace and heavy industry, where maximum protection is paramount. Buyers should prioritize suppliers who offer certifications for high-performance standards and consider the long-term durability and warranty options available.
Related Video: SAFETY GLASSES IMPACT TEST | ANSI Z87 VS Nail Gun, Wrench, and Dust
Key Industrial Applications of safety glasses supplier
Industry/Sector | Specific Application of Safety Glasses Supplier | Value/Benefit for the Business | Key Sourcing Considerations for this Application |
---|---|---|---|
Construction | Protective eyewear for on-site workers | Reduces risk of eye injuries, ensuring compliance with safety regulations | Certifications (ANSI, CE), anti-fog and scratch-resistant features |
Manufacturing | Safety glasses for assembly line personnel | Increases productivity by minimizing distractions from potential hazards | Customization options, bulk purchasing discounts |
Mining | Goggles designed for heavy-duty environments | Protects against dust, debris, and chemical exposure, enhancing worker safety | Durability, compatibility with other PPE, comfort for long wear |
Healthcare | Safety glasses for laboratory and medical staff | Prevents contamination and protects against splashes, ensuring staff safety | Anti-fog properties, lightweight design for extended use |
Automotive | Eyewear for mechanics and technicians | Improves visibility while protecting eyes from flying debris and chemicals | UV protection, impact resistance, style options for comfort |
What Are the Key Applications of Safety Glasses in the Construction Industry?
In the construction sector, safety glasses are essential for protecting workers from flying debris, dust, and chemical splashes. They help ensure compliance with stringent safety regulations, significantly reducing the risk of eye injuries on-site. International buyers, particularly in regions like Africa and South America, should prioritize sourcing safety glasses that meet local and international standards, such as ANSI or CE certifications. Additionally, features like anti-fog and scratch-resistant coatings are crucial for maintaining visibility in various environmental conditions.
How Are Safety Glasses Utilized in the Manufacturing Sector?
Within manufacturing, safety glasses are vital for assembly line workers who face risks from sharp objects and chemical exposure. These glasses not only protect against injuries but also enhance productivity by minimizing distractions. For B2B buyers in Europe and the Middle East, sourcing options that allow for customization, such as lens tinting or company branding, can be beneficial. Furthermore, suppliers offering bulk purchasing discounts can help businesses manage costs effectively while ensuring their workforce is adequately protected.
What Role Do Safety Glasses Play in Mining Operations?
In the mining industry, specialized safety goggles are crucial for protecting workers from hazardous conditions, including dust, flying debris, and chemical exposure. These goggles are designed to withstand harsh environments, thereby enhancing worker safety and compliance with health regulations. For international buyers, especially in regions with developing mining sectors, sourcing durable eyewear that is compatible with other personal protective equipment (PPE) is essential. Comfort and fit are also important, as workers may need to wear these goggles for extended periods.
Why Are Safety Glasses Important in Healthcare Settings?
In healthcare, safety glasses are critical for laboratory personnel and medical staff who are exposed to biological and chemical hazards. They prevent contamination and protect against splashes, ensuring a safe working environment. Buyers from various regions, including Europe and South America, should look for eyewear with anti-fog properties and lightweight designs that allow for prolonged use without discomfort. Compliance with health and safety regulations is also a key consideration when sourcing these products.
How Do Safety Glasses Benefit Automotive Workers?
In the automotive industry, safety glasses are essential for mechanics and technicians who work with tools and materials that can create flying debris. These glasses improve visibility while providing protection from harmful chemicals and sharp objects. For B2B buyers, sourcing eyewear with UV protection and impact resistance is critical. Additionally, comfort and style options can enhance user acceptance, leading to better compliance with safety protocols among workers.
Related Video: Eyes Safety Training Video
3 Common User Pain Points for ‘safety glasses supplier’ & Their Solutions
Scenario 1: Inconsistent Quality of Safety Glasses
The Problem: Many B2B buyers struggle with sourcing safety glasses that consistently meet quality standards. Variability in product quality can lead to safety risks for employees, especially in high-risk environments such as construction or manufacturing. Buyers often receive batches of glasses that vary in clarity, durability, or UV protection, resulting in dissatisfaction and potential liabilities. This inconsistency can disrupt operations and lead to increased costs for replacements or injuries.
The Solution: To mitigate quality issues, buyers should establish clear criteria for safety glasses before sourcing. This includes obtaining certifications (such as ANSI Z87.1 or ISO 12312-1) and requesting samples for testing. Conducting thorough due diligence on suppliers by checking their production processes and quality control measures is vital. Engage in direct communication with suppliers, asking detailed questions about their sourcing of materials, manufacturing methods, and compliance with international safety standards. Regular audits and reviews of supplier performance can also ensure ongoing quality assurance.
Scenario 2: Lack of Customization for Specific Industries
The Problem: Different industries have unique safety requirements, and many suppliers offer one-size-fits-all solutions. Buyers in sectors like oil and gas, pharmaceuticals, or electronics often find that standard safety glasses do not meet their specific needs, such as anti-fogging coatings or specialized tints for glare reduction. This lack of customization can lead to discomfort and decreased productivity among workers, as they might not be able to perform their tasks efficiently with unsuitable eyewear.
The Solution: To address this challenge, B2B buyers should proactively communicate their specific requirements to suppliers. When sourcing safety glasses, consider companies that offer customization options, such as adjustable frames or specialized lens coatings. Providing suppliers with detailed usage scenarios and environments can help them recommend tailored solutions. Additionally, exploring partnerships with suppliers that specialize in custom safety gear can enhance safety compliance and employee satisfaction, ultimately improving workplace productivity.
Scenario 3: Difficulty in Ensuring Compliance with Local Regulations
The Problem: Navigating the complex landscape of safety regulations can be daunting for B2B buyers, especially when sourcing safety glasses across different regions such as Africa, South America, the Middle East, and Europe. Regulations vary significantly, and failing to comply can result in fines, legal issues, and damage to a company’s reputation. Buyers often find it challenging to determine which certifications are necessary for their specific market or industry.
The Solution: To ensure compliance, buyers should familiarize themselves with local regulations and standards governing safety eyewear in their target markets. This may involve consulting with local safety organizations or regulatory bodies. It is advisable to partner with suppliers who are well-versed in these regulations and can provide documentation proving compliance. Furthermore, buyers should conduct regular training sessions for their teams about the importance of using compliant safety glasses and keeping abreast of any changes in regulations. Establishing a compliance checklist for safety gear procurement can streamline this process, minimizing the risk of oversight.
Strategic Material Selection Guide for safety glasses supplier
What Are the Key Materials Used in Safety Glasses for B2B Buyers?
When selecting safety glasses, understanding the materials used is crucial for ensuring optimal performance and compliance with international standards. Here, we analyze four common materials: polycarbonate, tempered glass, Trivex, and acetate. Each material has distinct properties, advantages, and limitations that can influence purchasing decisions for international B2B buyers, particularly in regions such as Africa, South America, the Middle East, and Europe.
How Does Polycarbonate Perform as a Material for Safety Glasses?
Polycarbonate is a popular choice for safety glasses due to its high impact resistance and lightweight nature. It can withstand significant force without shattering, making it ideal for environments where physical hazards are present. Polycarbonate lenses typically have a temperature rating of up to 135°C and offer UV protection.
Pros: The key advantages of polycarbonate include its durability, lightweight design, and inherent UV protection. It is also relatively inexpensive compared to other materials.
Cons: However, polycarbonate is prone to scratching and may require additional coatings to enhance its surface durability. This can increase manufacturing complexity and costs.
Impact on Application: Polycarbonate is suitable for various applications, including construction, manufacturing, and laboratory work, where impact resistance is critical.
Considerations for International Buyers: Buyers should ensure compliance with standards such as ANSI Z87.1 in the U.S. and EN166 in Europe, as well as consider the availability of anti-scratch coatings to enhance performance.
What Are the Benefits of Using Tempered Glass in Safety Glasses?
Tempered glass is known for its strength and resistance to thermal stress. It is produced by heating the glass to high temperatures and then cooling it rapidly, which increases its durability and makes it less likely to break.
Pros: The primary advantage of tempered glass is its scratch resistance and optical clarity. It provides excellent visibility, which is crucial in many work environments.
Cons: On the downside, tempered glass is heavier than polycarbonate and can be more expensive to manufacture. It is also less impact-resistant than polycarbonate, making it less suitable for high-risk environments.
Impact on Application: Tempered glass is often used in settings where clarity and scratch resistance are prioritized, such as in laboratories or for eyewear that needs to withstand chemical exposure.
Considerations for International Buyers: Compliance with safety standards like ASTM C1036 and EN12150 is essential. Buyers should also assess local market preferences for weight and comfort.
How Does Trivex Compare as a Material for Safety Glasses?
Trivex is a relatively new material that combines properties of both polycarbonate and glass. It offers excellent optical clarity, lightweight characteristics, and high impact resistance.
Pros: Trivex lenses are known for their superior optical quality and lightweight design, making them comfortable for prolonged wear. They also provide UV protection and are less prone to scratching than polycarbonate.
Cons: The primary disadvantage is that Trivex can be more expensive than polycarbonate, which may affect budget considerations for bulk purchases.
Impact on Application: Trivex is ideal for use in environments requiring both clarity and durability, such as in medical or precision engineering fields.
Considerations for International Buyers: Buyers should verify compliance with relevant standards, such as ANSI Z87.1 and ISO 12312-1, and consider the cost implications of sourcing Trivex materials.
What Role Does Acetate Play in Safety Glasses?
Acetate is a biodegradable plastic commonly used in the frames of safety glasses rather than the lenses. It is known for its flexibility and comfort, making it suitable for extended wear.
Pros: The flexibility and comfort of acetate frames can enhance user satisfaction. They are also available in various colors and styles, allowing for customization.
Cons: Acetate is less durable than other materials and can be affected by heat and chemicals, which may limit its use in certain industrial environments.
Impact on Application: Acetate is often used in less hazardous environments where comfort and style are prioritized over impact resistance.
Considerations for International Buyers: Compliance with environmental regulations and standards for eyewear frame materials is crucial, particularly in regions with stringent sustainability practices.
Summary of Material Selection for Safety Glasses
Material | Typical Use Case for Safety Glasses Supplier | Key Advantage | Key Disadvantage/Limitation | Relative Cost (Low/Med/High) |
---|---|---|---|---|
Polycarbonate | Construction, manufacturing | High impact resistance | Prone to scratching | Low |
Tempered Glass | Laboratories, chemical exposure | Scratch resistance | Heavier, less impact-resistant | Medium |
Trivex | Medical, precision engineering | Superior optical clarity | Higher cost | High |
Acetate | Fashion eyewear, general use | Comfort and customization | Less durable | Medium |
This guide provides insights into the strategic selection of materials for safety glasses, helping international B2B buyers make informed decisions that align with their specific operational needs and compliance requirements.
In-depth Look: Manufacturing Processes and Quality Assurance for safety glasses supplier
What Are the Key Stages in the Manufacturing Process of Safety Glasses?
The manufacturing process of safety glasses involves several critical stages that ensure both functionality and compliance with safety standards. Understanding these stages is essential for B2B buyers looking to source high-quality products.
Material Preparation: What Materials Are Used in Safety Glasses?
The first step in manufacturing safety glasses is material preparation. Common materials include polycarbonate, which is lightweight and impact-resistant, and CR-39, a plastic that offers excellent optical clarity. Some manufacturers may also use tempered glass for certain applications. The selection of materials must align with the specific safety requirements of the target industry, whether it be construction, manufacturing, or healthcare.
How Are Safety Glasses Formed?
Once the materials are prepared, the next stage is forming. This involves shaping the lenses and frames using techniques such as injection molding and die-cutting. Injection molding allows for complex shapes and ensures uniform thickness, which is critical for maintaining optical clarity and impact resistance. Die-cutting is often used for producing frames from sheets of material, ensuring precise dimensions that fit comfortably.
What Assembly Techniques Are Commonly Used?
After forming, the components are assembled. This stage includes attaching the lenses to the frames, incorporating any additional features such as anti-fog coatings or UV protection. Automated assembly lines are increasingly common, reducing human error and improving efficiency. Manual assembly may still be used for specialized or high-end products, ensuring quality and attention to detail.
What Finishing Processes Are Essential for Quality?
Finishing processes enhance the durability and aesthetic appeal of safety glasses. This may include polishing, coating, and final inspections. Anti-scratch and anti-fog coatings are applied to improve usability in various environments. Final inspections ensure that the glasses meet both aesthetic standards and functional requirements before they are packaged for shipment.
How Is Quality Assurance Implemented in Safety Glasses Manufacturing?
Quality assurance (QA) is a critical aspect of the manufacturing process, particularly for safety glasses that must meet stringent standards. B2B buyers should be aware of the QA protocols employed by suppliers to ensure product reliability.
What International Standards Should B2B Buyers Look For?
International standards such as ISO 9001 play a significant role in quality assurance for safety glasses manufacturers. ISO 9001 focuses on establishing a quality management system that ensures consistent product quality and customer satisfaction. Additionally, industry-specific standards like CE marking in Europe indicate compliance with health, safety, and environmental protection standards.
What Are the Key Quality Control Checkpoints?
Quality control (QC) checkpoints are established throughout the manufacturing process to identify defects early. These checkpoints typically include:
- Incoming Quality Control (IQC): Assessing raw materials for compliance with specifications before production begins.
- In-Process Quality Control (IPQC): Monitoring production processes to ensure adherence to established standards.
- Final Quality Control (FQC): Conducting comprehensive inspections of finished products to verify they meet quality and safety criteria.
Which Testing Methods Are Commonly Used?
Common testing methods for safety glasses include:
- Impact Resistance Testing: Evaluating how well the glasses withstand high-velocity impacts.
- Optical Clarity Testing: Ensuring that lenses provide clear vision without distortion.
- UV Protection Testing: Measuring the effectiveness of UV coatings in blocking harmful rays.
- Scratch Resistance Testing: Assessing the durability of surface coatings.
How Can B2B Buyers Verify Supplier Quality Control?
Verifying the quality control measures of a supplier is crucial for B2B buyers, especially those operating in international markets. Here are several methods to ensure the reliability of suppliers:
What Should Buyers Look for in Supplier Audits?
Conducting supplier audits is a robust method to evaluate quality control processes. Audits should review the supplier’s manufacturing practices, compliance with international standards, and overall quality management systems. Buyers can request audit reports or even arrange for third-party audits to gain an objective view of the supplier’s capabilities.
How Can Buyers Assess Supplier Reporting Practices?
Regular reporting from suppliers on quality metrics is another way to ensure product consistency. Buyers should seek transparency in reporting, including details on defect rates, compliance with testing standards, and corrective actions taken for any issues that arise. This information can help buyers make informed decisions about ongoing partnerships.
Why Is Third-Party Inspection Important?
Engaging third-party inspection services can provide an additional layer of assurance. Independent inspectors can evaluate production processes, conduct testing, and verify that products meet specified standards before they are shipped. This is particularly beneficial for buyers in Africa, South America, the Middle East, and Europe, where supply chain reliability is paramount.
What Nuances Should International B2B Buyers Consider?
Understanding the nuances of quality control and manufacturing processes is essential for international B2B buyers. Different regions may have varying regulations and standards for safety glasses, which can impact sourcing decisions.
How Do Regional Standards Affect Sourcing Decisions?
For example, in Europe, compliance with CE marking is mandatory for safety glasses, whereas other regions may have different certification requirements. Buyers must familiarize themselves with local regulations to ensure that the products they source will be accepted in their markets.
What Role Do Cultural Differences Play in Quality Expectations?
Cultural differences can also influence quality expectations. Buyers from regions with stringent safety regulations may have higher expectations for quality control processes compared to those from areas with less rigorous standards. Understanding these differences is crucial for establishing clear communication and expectations with suppliers.
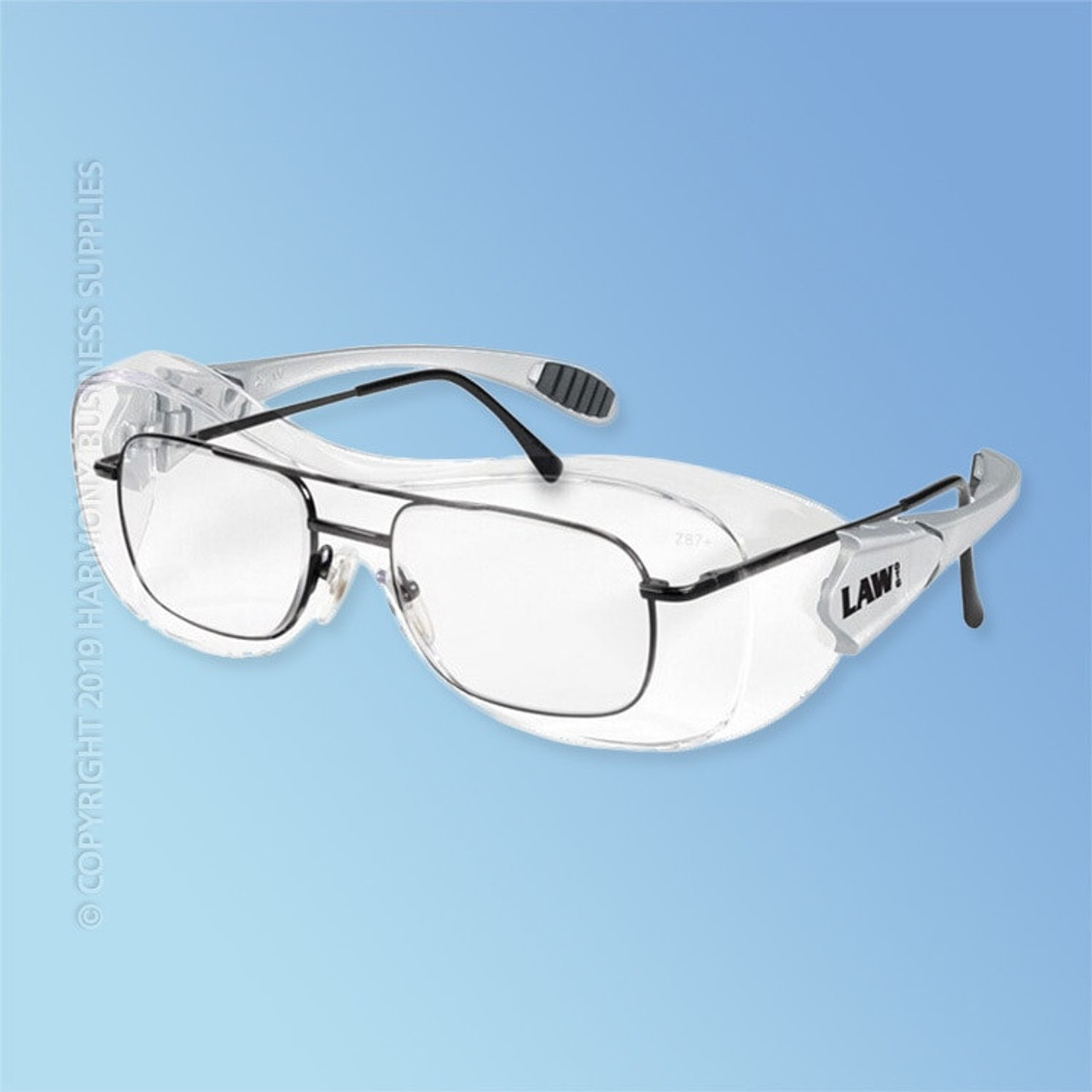
A stock image related to safety glasses supplier.
By navigating the complexities of manufacturing processes and quality assurance, B2B buyers can make informed decisions when sourcing safety glasses, ensuring that they receive products that meet their specific needs and regulatory requirements.
Practical Sourcing Guide: A Step-by-Step Checklist for ‘safety glasses supplier’
In the increasingly global marketplace, sourcing safety glasses from reliable suppliers is essential for ensuring workplace safety and compliance with industry standards. This guide provides a structured checklist to help international B2B buyers, particularly from Africa, South America, the Middle East, and Europe, navigate the procurement process effectively.
Step 1: Define Your Technical Specifications
Establishing clear technical specifications for safety glasses is critical to meet your specific safety requirements. Consider factors such as the type of hazards present in your workplace, the level of protection needed (e.g., impact resistance, UV protection), and comfort features (e.g., anti-fogging, adjustable frames). This will help you communicate your needs accurately to potential suppliers.
Step 2: Research Regulatory Compliance Standards
Safety glasses must adhere to specific regulations and standards, which vary by region. Familiarize yourself with relevant local and international standards such as ANSI Z87.1 in the U.S. or EN166 in Europe. Ensuring that suppliers’ products meet these standards not only guarantees quality but also protects your business from legal liabilities.
Step 3: ✅ Verify Supplier Certifications
Before moving forward with any supplier, it’s essential to confirm their certifications. Look for ISO certifications or compliance with occupational health and safety regulations. These certifications indicate that the supplier adheres to industry best practices and quality control measures.
Step 4: Evaluate Potential Suppliers
Conduct a thorough evaluation of potential suppliers to ensure they align with your business values and quality expectations. Request detailed company profiles, product catalogs, and references from existing clients in your industry. Pay attention to the supplier’s reputation, reliability, and customer service track record.
Step 5: Request Product Samples
Before making a large purchase, request samples of the safety glasses to evaluate their quality firsthand. Assess factors such as fit, comfort, visibility, and durability. Testing samples allows you to ensure that the product meets your technical specifications and is suitable for your workforce.
Step 6: Negotiate Pricing and Terms
Once you have identified a suitable supplier, engage in negotiations to secure favorable pricing and terms. Be clear about your budget, order quantities, and delivery timelines. Additionally, discuss warranty options and return policies to protect your investment.
Step 7: Establish a Long-term Relationship
Building a strong, long-term relationship with your chosen supplier can lead to better pricing, priority service, and collaboration on new product developments. Regular communication and feedback can help maintain quality and ensure that your safety glasses supplier remains aligned with your evolving needs.
By following these steps, you will be well-equipped to source high-quality safety glasses from reliable suppliers, ensuring the safety and well-being of your workforce while complying with relevant regulations.
Comprehensive Cost and Pricing Analysis for safety glasses supplier Sourcing
When sourcing safety glasses from suppliers, international B2B buyers must carefully analyze the cost structure and pricing strategies to ensure they make informed decisions. Understanding the various cost components and price influencers can significantly impact the overall procurement strategy and lead to better negotiation outcomes.
What Are the Key Cost Components in Sourcing Safety Glasses?
-
Materials: The primary cost driver in safety glasses manufacturing is the quality of materials used. This includes polycarbonate or other high-impact resistant lenses and durable frames. Buyers should consider the balance between cost and quality, as lower-quality materials may lead to higher injury risks and potential liability issues.
-
Labor: Labor costs vary significantly based on geographic location and local wage standards. In regions with higher labor costs, such as Europe, the manufacturing expenses can increase. Understanding these factors can help buyers assess the total cost accurately.
-
Manufacturing Overhead: This encompasses all indirect costs associated with production, such as utilities, rent, and administrative expenses. Suppliers with efficient production processes can offer competitive pricing, making it crucial for buyers to evaluate supplier operations.
-
Tooling: Initial tooling costs can be substantial, especially for custom designs. Buyers should inquire about tooling fees and whether these costs will be amortized over large orders to reduce the price per unit.
-
Quality Control (QC): Ensuring safety glasses meet international standards requires robust QC processes. Suppliers who invest in quality assurance may charge higher prices, but this can be justified by the reduced risk of defects and compliance failures.
-
Logistics: Shipping and handling costs can vary based on the supplier’s location and the buyer’s destination. Consideration of Incoterms is vital, as they define the responsibilities of each party concerning transportation costs and risks.
-
Margin: Finally, suppliers will include their profit margin in the pricing. Understanding typical margins in the industry can help buyers identify whether a quote is reasonable.
How Do Price Influencers Affect Safety Glasses Procurement?
Several factors can influence the pricing of safety glasses, including:
-
Volume/MOQ (Minimum Order Quantity): Bulk purchases often lead to discounts. Buyers should negotiate for better rates based on their projected volumes.
-
Specifications and Customization: Customized safety glasses with specific features (e.g., anti-fog, anti-scratch) can significantly increase costs. Buyers must weigh the benefits against additional expenses.
-
Material Quality and Certifications: Glasses that meet higher safety standards or certifications may command higher prices. Buyers in regions with stringent safety regulations should prioritize certified products.
-
Supplier Factors: The supplier’s reputation, reliability, and service level can impact pricing. Established suppliers may charge more due to their proven track record.
-
Incoterms: The choice of Incoterms can affect the total landed cost of safety glasses. Buyers should understand how terms like FOB (Free on Board) or CIF (Cost, Insurance, and Freight) influence their final expenses.
What Are the Best Practices for Negotiating Prices and Ensuring Cost Efficiency?
-
Conduct Total Cost of Ownership Analysis: Beyond the purchase price, consider maintenance, replacement, and compliance costs over the product’s lifecycle. This analysis can reveal the true cost and inform better purchasing decisions.
-
Leverage Relationships: Building strong relationships with suppliers can lead to better pricing and terms. Regular communication can also facilitate negotiations for future orders.
-
Negotiate Payment Terms: Flexible payment terms can help manage cash flow. Discuss options such as extended payment periods or discounts for early payments.
-
Stay Informed About Market Trends: Keeping abreast of market conditions, material costs, and global supply chain issues can give buyers leverage during negotiations.
-
Be Cautious of Indicative Prices: Always remember that the prices quoted may fluctuate based on market conditions. Buyers should request detailed quotes that include all potential costs to avoid surprises.
By understanding the cost structure and price influencers, B2B buyers can make informed choices when sourcing safety glasses, ultimately leading to safer working environments and compliance with regulations across different regions.
Alternatives Analysis: Comparing safety glasses supplier With Other Solutions
When it comes to ensuring worker safety, especially in industries with high-risk environments, selecting the right protective equipment is crucial. While safety glasses suppliers provide a specific solution, several alternatives exist that can also serve to protect workers from potential hazards. This section explores these alternatives, offering insights for international B2B buyers in Africa, South America, the Middle East, and Europe.
Comparison Table of Safety Solutions
Comparison Aspect | Safety Glasses Supplier | Face Shields | Safety Goggles |
---|---|---|---|
Performance | High UV and impact resistance | Offers full-face protection | Excellent chemical splash protection |
Cost | Moderate | Higher initial investment | Moderate |
Ease of Implementation | Easy to distribute and train | Requires training for proper use | Simple, but may require fitting adjustments |
Maintenance | Minimal care needed | Regular cleaning necessary | Requires thorough cleaning and inspection |
Best Use Case | General industrial work | Laboratory and medical applications | Chemical handling and heavy machinery work |
What Are the Pros and Cons of Using Face Shields?
Face shields provide comprehensive facial protection and are particularly beneficial in environments where splashes or airborne particles pose a risk. They are ideal for medical settings, laboratories, and during certain manufacturing processes. However, face shields can be more expensive than traditional safety glasses and may require additional training for proper usage and maintenance. While they offer full-face coverage, they may not provide the same level of optical clarity as safety glasses, which can be a drawback in tasks requiring precision.
How Do Safety Goggles Compare to Safety Glasses?
Safety goggles are designed to offer a snug fit around the eyes, providing superior protection against chemical splashes, dust, and flying debris. They are particularly useful in environments with hazardous materials or where fine particles are present. However, goggles can be less comfortable for extended wear compared to safety glasses and may fog up, reducing visibility. The maintenance for goggles can also be more demanding, as they require regular inspection and cleaning to ensure effectiveness.
Conclusion: How to Choose the Right Safety Solution for Your Needs
When selecting between a safety glasses supplier and alternative solutions like face shields or safety goggles, B2B buyers should assess their specific industry requirements, the nature of the hazards involved, and the comfort of the end-users. Factors such as cost, ease of implementation, and maintenance should also be considered. By understanding the strengths and weaknesses of each option, businesses can make informed decisions that enhance worker safety while aligning with their operational needs. Ultimately, the choice should reflect a balance between protection, practicality, and employee comfort.
Essential Technical Properties and Trade Terminology for safety glasses supplier
What Are the Key Technical Properties of Safety Glasses?
When sourcing safety glasses, understanding the essential technical properties is critical for ensuring worker safety and compliance with industry standards. Here are some of the most important specifications to consider:
-
Material Grade
– Safety glasses are typically made from polycarbonate or Trivex materials. Polycarbonate is lightweight, impact-resistant, and provides excellent optical clarity. Trivex offers similar benefits but is known for its superior optical performance. Choosing the right material grade ensures durability and protection in hazardous environments. -
Lens Thickness
– The thickness of the lenses can affect their impact resistance and optical clarity. Thicker lenses provide better protection but may also increase weight. It’s essential for B2B buyers to balance safety and comfort to ensure that employees will wear the glasses consistently. -
Optical Clarity
– The optical clarity of safety glasses is crucial for tasks requiring precision. Lenses should meet ANSI Z87.1 standards, which dictate the minimum optical performance for safety eyewear. High optical clarity reduces eye strain and enhances productivity, making it a vital consideration for employers. -
UV Protection
– Many safety glasses come with UV protection to shield workers from harmful ultraviolet rays. This feature is particularly important for outdoor work environments. Ensuring that safety glasses have appropriate UV filters helps prevent long-term eye damage. -
Anti-Fog and Anti-Scratch Coatings
– Anti-fog coatings help maintain visibility in humid or temperature-variable environments, while anti-scratch coatings enhance durability. These features are essential for maintaining safety and functionality, particularly in industries like construction or manufacturing. -
Fit and Comfort
– The design and fit of safety glasses can greatly impact user compliance. Glasses should feature adjustable temples and nose pads for a customizable fit. Comfortable safety glasses are more likely to be worn consistently, thus providing better protection.
Which Trade Terms Should International B2B Buyers Know?
Understanding industry jargon can facilitate smoother transactions and negotiations. Here are some common trade terms relevant to safety glasses suppliers:
-
OEM (Original Equipment Manufacturer)
– An OEM refers to a company that produces parts or equipment that may be marketed by another manufacturer. In the context of safety glasses, this could relate to suppliers that create custom eyewear for specific brands. Knowing your OEM can help in understanding product quality and supply chain reliability. -
MOQ (Minimum Order Quantity)
– MOQ indicates the smallest quantity of a product that a supplier is willing to sell. This term is crucial for B2B buyers to understand, as it affects purchasing decisions and inventory management. Suppliers with low MOQs can provide flexibility for small to medium-sized businesses. -
RFQ (Request for Quotation)
– An RFQ is a document issued by a buyer to request pricing and other terms from potential suppliers. This is a standard practice in B2B transactions, allowing companies to compare offers and make informed decisions. Crafting a clear RFQ can streamline the procurement process. -
Incoterms (International Commercial Terms)
– Incoterms are international trade terms that define the responsibilities of buyers and sellers in the shipping process. Familiarity with these terms can help B2B buyers understand shipping costs, risk allocation, and delivery responsibilities, which are crucial for international transactions. -
Lead Time
– Lead time refers to the amount of time it takes for an order to be fulfilled, from the moment it is placed until delivery. Understanding lead times is vital for inventory planning and project timelines, especially in industries with tight schedules. -
Certification Standards
– Certification standards, such as ANSI Z87.1 or EN166, indicate that safety glasses meet specific safety criteria. Knowing which certifications are relevant to your market helps ensure compliance with local regulations and enhances product credibility.
Conclusion
Navigating the world of safety glasses requires a solid understanding of both technical specifications and trade terminology. By familiarizing yourself with these key properties and terms, you can make more informed purchasing decisions that prioritize safety and compliance for your workforce.
Navigating Market Dynamics and Sourcing Trends in the safety glasses supplier Sector
What Are the Current Market Dynamics and Key Trends in the Safety Glasses Supplier Sector?
The safety glasses supplier market is experiencing significant transformation driven by global health and safety regulations, technological advancements, and heightened awareness regarding workplace safety. Internationally, the increasing incidence of workplace injuries—approximately 395 million non-fatal injuries per year—has prompted businesses across sectors to prioritize protective eyewear. This urgency is particularly evident in regions like Africa and South America, where industrial growth is accompanied by a rising focus on occupational safety standards.
Emerging technologies are reshaping the sourcing landscape, with a notable shift towards smart safety glasses equipped with augmented reality (AR) features. These innovations allow workers to access real-time data while keeping their hands free, significantly enhancing productivity and safety in various industries, including construction and manufacturing. Additionally, the trend towards online sourcing platforms is becoming prominent. These platforms provide international B2B buyers access to a broader range of suppliers, facilitating competitive pricing and improved supply chain transparency.
Furthermore, the demand for customized safety eyewear is on the rise. Buyers are increasingly looking for products that cater to specific industry needs, such as anti-fog, anti-scratch, and UV protection features. This trend underscores the importance of suppliers being agile and responsive to market demands, especially in diverse markets like Europe and the Middle East.
How Is Sustainability and Ethical Sourcing Impacting the Safety Glasses Supplier Sector?
Sustainability has become a cornerstone of procurement strategies for B2B buyers in the safety glasses sector. Environmental concerns related to the production and disposal of safety eyewear have led to a greater emphasis on sourcing practices that minimize ecological footprints. Suppliers are increasingly adopting sustainable materials, such as bio-based plastics and recycled content, to meet the growing demand for environmentally friendly products.
Ethical sourcing is also gaining traction, with buyers seeking suppliers that adhere to fair labor practices and transparent supply chains. Certifications such as ISO 14001 for environmental management and Fair Trade are becoming essential for suppliers to demonstrate their commitment to sustainability. This shift not only aligns with corporate social responsibility goals but also appeals to a growing segment of consumers who prioritize ethical practices in their purchasing decisions.
Moreover, brands that invest in sustainability often enjoy a competitive advantage, as they are viewed as more trustworthy and responsible. International buyers, especially in Europe, are increasingly scrutinizing their suppliers’ sustainability credentials, making it imperative for safety glasses suppliers to integrate environmental and social governance (ESG) into their business models.
What Is the Brief Evolution and History of the Safety Glasses Supplier Sector?
The safety glasses supplier sector has evolved significantly over the last century, driven by technological advancements and changing workplace safety regulations. Initially, protective eyewear was rudimentary, primarily designed to shield the eyes from physical hazards. However, the increasing awareness of occupational health risks in the mid-20th century led to the establishment of stringent safety standards and regulations worldwide.
In the 1970s and 1980s, the introduction of polycarbonate lenses revolutionized the market, offering lightweight, impact-resistant options that enhanced comfort and usability. The late 20th and early 21st centuries saw the rise of specialized safety eyewear tailored to specific industries, including construction, healthcare, and manufacturing. Today, the sector is characterized by continuous innovation, with a strong focus on integrating technology and sustainability into product offerings, reflecting the evolving needs of global B2B buyers.
Frequently Asked Questions (FAQs) for B2B Buyers of safety glasses supplier
-
How do I ensure the quality of safety glasses when sourcing from suppliers?
To ensure quality, begin by verifying the supplier’s certifications and compliance with international standards such as ANSI (American National Standards Institute) and ISO (International Organization for Standardization). Request samples to assess product quality firsthand and conduct factory audits if possible. Additionally, inquire about their quality assurance processes, including regular inspections and testing protocols. Establishing clear communication regarding specifications and expectations can further mitigate risks related to product quality. -
What are the essential certifications for safety glasses suppliers?
Look for suppliers that hold certifications relevant to safety glasses, such as ANSI Z87.1 for impact resistance and EN 166 for European standards. Additionally, check for compliance with ISO 9001, which indicates a commitment to quality management systems. Certifications from local regulatory bodies may also be necessary, depending on the market you are targeting. Ensuring that your supplier has these certifications can help you meet legal requirements and protect your workforce. -
What customization options should I consider when purchasing safety glasses?
Customization options can include lens tinting, anti-fog coatings, and frame styles tailored to specific industries or user preferences. Many suppliers also offer branding options, such as adding logos or specific color schemes to align with corporate identity. Discuss your requirements with potential suppliers to explore available customization options that enhance user comfort and safety. This can also improve employee compliance with safety gear usage. -
What is the minimum order quantity (MOQ) for safety glasses, and how does it vary by supplier?
Minimum order quantities (MOQ) can vary significantly between suppliers, often ranging from 100 to 1,000 units or more, depending on the manufacturer’s production capabilities and the complexity of the order. Smaller suppliers may have lower MOQs, while larger manufacturers might require larger orders to justify production costs. Always clarify MOQ details during negotiations, and consider combining orders with other products to meet the minimum requirement if necessary. -
What payment terms should I negotiate with a safety glasses supplier?
Negotiating favorable payment terms is crucial for managing cash flow. Common terms include a deposit (usually 30-50%) upfront, with the balance due upon delivery or after inspection. Some suppliers may offer net payment terms, such as net 30 or net 60, which allow you to pay after a set period. Always ensure that payment terms are clearly outlined in the contract to avoid misunderstandings and consider using secure payment methods to mitigate risks. -
How can I vet a safety glasses supplier before making a purchase?
Begin by researching the supplier’s reputation through online reviews and testimonials from previous clients. Request references and conduct background checks to assess their reliability. Evaluate their production capacity and lead times to ensure they can meet your demands. Additionally, consider visiting their facility or arranging a virtual tour to verify their operations and quality control measures. A thorough vetting process can help you avoid potential issues down the line. -
What logistics considerations should I keep in mind when importing safety glasses?
When importing safety glasses, consider shipping methods, customs clearance, and potential tariffs or duties that may apply. Establish a clear timeline for delivery, factoring in production lead times and shipping durations. Collaborate with a freight forwarder who understands the regulations of the importing country to streamline the process. Additionally, ensure that the packaging meets international shipping standards to prevent damage during transit. -
What are the best practices for ensuring compliance with local regulations when sourcing safety glasses?
To ensure compliance, familiarize yourself with the safety regulations specific to your industry and region. Engage with local safety authorities to understand the necessary standards for personal protective equipment (PPE). Work closely with your supplier to ensure that all products meet these regulations before shipment. Regularly review compliance requirements, as they may change, to maintain adherence and protect your workforce from potential legal liabilities.
Important Disclaimer & Terms of Use
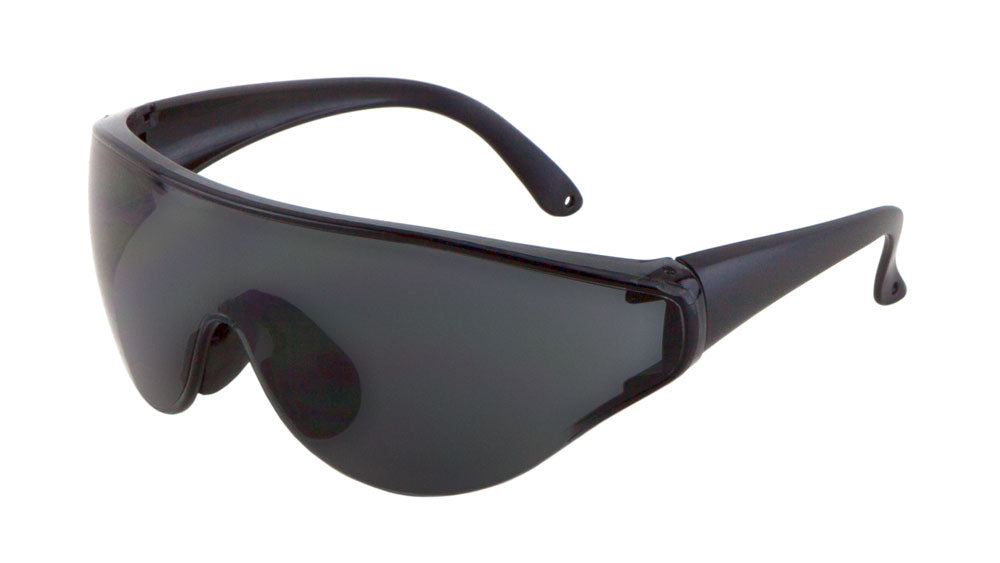
A stock image related to safety glasses supplier.
⚠️ Important Disclaimer
The information provided in this guide, including content regarding manufacturers, technical specifications, and market analysis, is for informational and educational purposes only. It does not constitute professional procurement advice, financial advice, or legal advice.
While we have made every effort to ensure the accuracy and timeliness of the information, we are not responsible for any errors, omissions, or outdated information. Market conditions, company details, and technical standards are subject to change.
B2B buyers must conduct their own independent and thorough due diligence before making any purchasing decisions. This includes contacting suppliers directly, verifying certifications, requesting samples, and seeking professional consultation. The risk of relying on any information in this guide is borne solely by the reader.
Strategic Sourcing Conclusion and Outlook for safety glasses supplier
As the global market for safety glasses continues to expand, strategic sourcing emerges as a critical approach for international B2B buyers. By prioritizing safety and compliance, companies can ensure they meet the evolving regulatory standards across different regions, including Africa, South America, the Middle East, and Europe. Collaborating with reliable suppliers not only enhances product quality but also strengthens the overall supply chain resilience.
What are the key takeaways for B2B buyers when sourcing safety glasses? First, understanding local safety regulations and market demands is essential. Buyers should leverage data-driven insights to assess supplier capabilities and product innovations. Additionally, fostering long-term relationships with suppliers can lead to better pricing, improved service levels, and access to the latest technologies.
Looking ahead, the emphasis on worker safety will only intensify, making it imperative for international buyers to adopt proactive sourcing strategies. By engaging with suppliers who prioritize quality and compliance, businesses can significantly mitigate risks associated with workplace safety. Now is the time for B2B buyers to take action—evaluate your sourcing strategies, invest in high-quality safety glasses, and commit to creating safer working environments across all regions.