Find the Best Air Filter Supplier: The Ultimate Guide (2025)
Introduction: Navigating the Global Market for air filter supplier
Navigating the complexities of sourcing air filters for diverse industrial applications can be a daunting challenge for international B2B buyers, especially in regions like Africa, South America, the Middle East, and Europe. The market for air filter suppliers is vast, with a multitude of options available, each promising superior performance and efficiency. However, the key to successful procurement lies not only in identifying the right supplier but also in understanding the various types of air filters, their applications, and the critical factors influencing cost and quality.
This comprehensive guide serves as an essential resource for B2B buyers, delineating the different types of air filters available—ranging from HEPA filters to activated carbon filters—and their specific uses in sectors such as manufacturing, healthcare, and environmental management. We delve into the intricacies of supplier vetting, offering insights on how to assess potential partners based on quality certifications, customer reviews, and technological advancements. Additionally, we provide actionable strategies for negotiating costs without compromising on quality, ensuring that your organization makes informed purchasing decisions.
By equipping international buyers with the knowledge to navigate the global market for air filter suppliers effectively, this guide empowers them to optimize their sourcing strategies, enhance operational efficiency, and ultimately contribute to a healthier environment. Whether you are based in Spain, Poland, or any other region, understanding these dynamics will be pivotal in securing the best air filtration solutions for your needs.
Understanding air filter supplier Types and Variations
Type Name | Key Distinguishing Features | Primary B2B Applications | Brief Pros & Cons for Buyers |
---|---|---|---|
HEPA Filter Suppliers | High-efficiency particulate air filters, removes 99.97% of particles | Hospitals, cleanrooms, electronics manufacturing | Pros: Excellent air quality, regulatory compliance. Cons: Higher initial cost, requires regular maintenance. |
Activated Carbon Filter Suppliers | Utilizes activated carbon to absorb gases and odors | Food processing, wastewater treatment | Pros: Effective for VOCs and odors, enhances air quality. Cons: Limited lifespan, requires timely replacement. |
Electrostatic Filter Suppliers | Uses electrostatic charge to attract and capture particles | HVAC systems, commercial buildings | Pros: Low energy consumption, reusable. Cons: May not capture all particle sizes, requires cleaning. |
Panel Filter Suppliers | Standardized flat filters, available in various materials | Residential, commercial HVAC systems | Pros: Cost-effective, easy to replace. Cons: Lower efficiency, may need frequent changes. |
Bag Filter Suppliers | Fabric filters in bag form for higher dirt holding capacity | Industrial air filtration, dust collection | Pros: High dust holding capacity, suitable for heavy-duty applications. Cons: Bulkier, may require more space. |
What Are the Key Characteristics of HEPA Filter Suppliers?
HEPA (High-Efficiency Particulate Air) filter suppliers provide filters that can capture 99.97% of particles as small as 0.3 microns. They are essential in environments where air purity is critical, such as hospitals, laboratories, and electronic manufacturing facilities. When purchasing, B2B buyers should consider the filter’s efficiency rating, compatibility with existing systems, and maintenance requirements to ensure compliance with health and safety regulations.
How Do Activated Carbon Filter Suppliers Function?
Activated carbon filter suppliers specialize in filters that absorb volatile organic compounds (VOCs) and odors, making them ideal for applications in food processing and wastewater treatment. The key consideration for buyers is the filter’s lifespan and the frequency of replacement, as these filters can become saturated and lose effectiveness over time. Evaluating the specific contaminants in the environment will help in selecting the right carbon filter.
What Are the Benefits of Electrostatic Filter Suppliers?
Electrostatic filter suppliers offer filters that use an electrostatic charge to trap airborne particles. These filters are increasingly popular in HVAC systems and commercial buildings due to their low energy consumption and the fact that they can be cleaned and reused. However, buyers should be aware that while they are effective for larger particles, they may not capture all sizes, which can impact air quality.
Why Choose Panel Filter Suppliers for B2B Applications?
Panel filter suppliers provide flat, standardized filters made from various materials, making them a common choice for residential and commercial HVAC systems. They are cost-effective and easy to replace, but buyers should be cautious about their lower efficiency compared to other filter types. Regular monitoring and timely replacement are crucial to maintaining indoor air quality.
What Advantages Do Bag Filter Suppliers Offer?
Bag filter suppliers focus on fabric filters that come in bag form, designed to hold a significant amount of dirt and dust. They are commonly used in industrial air filtration and dust collection systems. Buyers should consider the space available for installation and the filter’s capacity to handle heavy-duty applications, as these filters are bulkier but provide superior performance in demanding environments.
Related Video: Sentry Air Systems Demonstrates How Activated Carbon Works in a Filter
Key Industrial Applications of air filter supplier
Industry/Sector | Specific Application of air filter supplier | Value/Benefit for the Business | Key Sourcing Considerations for this Application |
---|---|---|---|
Manufacturing | Dust and particulate filtration in production lines | Enhanced product quality and reduced equipment wear | Filter efficiency, material compatibility, and local regulations |
Pharmaceuticals | Air filtration in cleanrooms | Compliance with health standards and contamination control | Certification standards, filter lifespan, and maintenance requirements |
Food and Beverage | Air filtration in processing and packaging areas | Improved product safety and shelf life | Food-grade certifications, filter types, and installation support |
Automotive | Cabin air filtration systems | Enhanced passenger comfort and vehicle reliability | Performance ratings, compatibility with vehicle models, and supply chain reliability |
HVAC Systems | Air filtration in heating, ventilation, and air conditioning | Energy efficiency and improved indoor air quality | Filter dimensions, MERV ratings, and ease of replacement |
How Air Filter Suppliers Are Integral to Manufacturing
In the manufacturing sector, air filter suppliers play a crucial role by providing dust and particulate filtration systems that protect machinery and improve product quality. These filters help to minimize downtime caused by equipment wear and tear, which can be particularly significant in regions like Africa and South America where dust levels may be higher. Buyers should focus on filter efficiency ratings and material compatibility to ensure optimal performance while adhering to local environmental regulations.
Why Cleanroom Air Filtration is Essential in Pharmaceuticals
Pharmaceutical companies rely on air filter suppliers for cleanroom air filtration to maintain stringent compliance with health standards. This is vital for preventing contamination that could compromise product integrity. International buyers, particularly from Europe and the Middle East, must prioritize suppliers that offer filters with recognized certification standards and a proven track record in cleanroom applications. Additionally, understanding filter lifespan and maintenance requirements can enhance operational efficiency.
Ensuring Safety in Food and Beverage Production
In the food and beverage industry, air filter suppliers provide critical filtration solutions for processing and packaging environments. These filters help to ensure product safety and extend shelf life by removing contaminants from the air. B2B buyers in this sector, especially from regions like South America, should seek suppliers that offer food-grade certified filters and understand the specific filter types necessary for various applications. Installation support is also a key consideration to ensure compliance with industry standards.
Enhancing Passenger Comfort in Automotive Applications
Air filter suppliers are essential for automotive companies, particularly in the production of cabin air filtration systems that improve passenger comfort and vehicle reliability. Filters need to effectively remove pollutants and allergens from the air, which is increasingly important in urban areas across Europe. Buyers should evaluate performance ratings and ensure compatibility with various vehicle models, while also considering the reliability of the supplier’s supply chain to avoid disruptions.
Improving Indoor Air Quality with HVAC Systems
In HVAC systems, air filter suppliers help maintain energy efficiency and improve indoor air quality. This is crucial for businesses in both commercial and residential sectors, especially in regions with varying climate conditions like Africa and the Middle East. Buyers should focus on filter dimensions and Minimum Efficiency Reporting Value (MERV) ratings to select appropriate filters that meet their specific needs. The ease of filter replacement is also a significant factor, as it impacts ongoing maintenance costs and operational efficiency.
3 Common User Pain Points for ‘air filter supplier’ & Their Solutions
Scenario 1: Difficulty in Ensuring Air Quality Compliance
The Problem: In industries such as manufacturing or healthcare, maintaining strict air quality standards is essential for compliance with local and international regulations. B2B buyers often struggle to find air filter suppliers that can guarantee filters meeting specific quality standards, which can lead to operational disruptions or costly fines. For instance, a factory in South America may face challenges in sourcing filters that comply with local environmental regulations, resulting in potential shutdowns or legal repercussions.
The Solution: To address this issue, B2B buyers should conduct thorough due diligence when selecting an air filter supplier. Start by verifying the supplier’s certifications and compliance with relevant regulations, such as ISO 9001 for quality management or specific environmental standards like EN 1822 for air filters. Establish a clear communication channel with the supplier to discuss your specific needs and compliance requirements upfront. Consider requesting samples to test the filters in your operational environment, ensuring they meet your air quality standards before committing to larger orders. Additionally, consider suppliers that provide documentation and support regarding compliance, which can serve as valuable resources during audits.
Scenario 2: Inconsistent Filter Performance Leading to Increased Costs
The Problem: Many B2B buyers experience frustration when dealing with air filters that do not perform consistently. Variability in filter quality can lead to increased energy consumption, frequent replacements, and ultimately higher operational costs. For example, a facility in Europe might find that its air filtration system requires more frequent maintenance and replacement parts due to subpar filters, thereby straining its budget and resources.
The Solution: To combat inconsistent performance, buyers should prioritize sourcing from reputable air filter suppliers known for their reliability and quality. It is essential to request performance data and case studies from potential suppliers, highlighting the longevity and efficiency of their filters in similar applications. Establishing long-term partnerships with suppliers can also lead to better pricing and reliability. Implement a regular monitoring system to track filter performance and energy consumption, allowing for timely interventions if performance dips. Additionally, consider investing in higher-grade filters that might have a higher initial cost but will reduce long-term maintenance and energy expenses.
Scenario 3: Limited Availability of Custom Filters for Specialized Applications
The Problem: Industries often require custom air filters tailored to specific operational environments, which can be a significant pain point when suppliers lack the capability to produce bespoke solutions. For instance, a company in the Middle East may need filters designed to withstand extreme temperatures and high levels of dust and sand, but standard filters do not meet these requirements. This limitation can lead to inefficiencies and even equipment damage.
The Solution: Buyers should actively seek suppliers who specialize in custom air filtration solutions. Initiate discussions about your specific environmental challenges and filtration needs, emphasizing the importance of tailored solutions. Look for suppliers with a proven track record in custom manufacturing, and inquire about their capabilities in designing filters that can withstand specific conditions. Additionally, consider establishing a pilot program where the supplier develops a small batch of custom filters for testing in your environment. This approach allows for adjustments based on performance feedback, ensuring that the final product meets all operational requirements before full-scale implementation. Collaborating closely with suppliers can lead to innovative solutions that not only address immediate needs but also enhance overall efficiency.
Strategic Material Selection Guide for air filter supplier
What Are the Key Materials Used in Air Filters for B2B Applications?
When selecting materials for air filters, international B2B buyers must consider various factors that influence performance, durability, and cost. Here, we analyze four common materials used in air filter manufacturing: fiberglass, polyester, activated carbon, and metal mesh. Each material has unique properties that can significantly impact the performance and suitability of air filters for specific applications.
How Does Fiberglass Perform in Air Filter Applications?
Fiberglass is a widely used material in air filters due to its excellent filtration efficiency and durability. It can withstand high temperatures and pressures, making it suitable for industrial applications. Fiberglass filters typically have a temperature rating of up to 500°F (260°C) and can handle significant pressure drops without compromising performance.
Pros: Fiberglass filters are highly durable, resistant to moisture, and have a long service life. They are also cost-effective for high-volume applications.
Cons: However, they can be less efficient at capturing smaller particles compared to other materials. Additionally, fiberglass can be less environmentally friendly due to its synthetic nature.
Impact on Application: Fiberglass is compatible with various media and is often used in HVAC systems, industrial air filtration, and pre-filters.
Considerations for International Buyers: Buyers should ensure compliance with local regulations regarding material safety and environmental standards, such as ASTM or DIN certifications.
What Advantages Does Polyester Offer for Air Filters?
Polyester is another popular choice for air filter media due to its balance of performance and cost. It is known for its good chemical resistance and can operate effectively in temperatures up to 200°F (93°C).
Pros: Polyester filters are lightweight, easy to handle, and can be manufactured in various thicknesses. They also provide good filtration efficiency for both particulate and gaseous contaminants.
Cons: On the downside, polyester filters may not perform well in high-temperature applications and can degrade under extreme conditions.
Impact on Application: Polyester is commonly used in residential and commercial HVAC systems, as well as in automotive applications.
Considerations for International Buyers: Buyers in regions like Europe should check for compliance with EU regulations regarding VOC emissions and material safety.
How Does Activated Carbon Enhance Air Filter Performance?
Activated carbon is renowned for its ability to adsorb odors and volatile organic compounds (VOCs). It is often used in combination with other filter materials to enhance overall air quality.
Pros: The primary advantage of activated carbon filters is their effectiveness in removing odors and chemical pollutants. They have a high surface area, which allows for greater adsorption capacity.
Cons: However, activated carbon can be more expensive than other materials, and its effectiveness can diminish over time as the carbon becomes saturated.
Impact on Application: Activated carbon filters are ideal for applications requiring odor control, such as in kitchens, laboratories, and hospitals.
Considerations for International Buyers: Buyers should be aware of local regulations regarding chemical emissions and ensure that the activated carbon used meets industry standards.
What Role Does Metal Mesh Play in Air Filtration?
Metal mesh filters are often used in applications requiring high durability and reusability. They can withstand high temperatures and pressures, making them suitable for industrial environments.
Pros: Metal mesh filters are highly durable, washable, and can be reused multiple times, reducing long-term costs.
Cons: However, they may not provide the same level of filtration efficiency as fibrous materials and can be heavy and cumbersome.
Impact on Application: Metal mesh is commonly used in HVAC systems, automotive applications, and industrial air filtration.
Considerations for International Buyers: Buyers should ensure that metal mesh filters comply with relevant standards for corrosion resistance and mechanical strength.
Summary Table of Material Properties for Air Filters
Material | Typical Use Case for air filter supplier | Key Advantage | Key Disadvantage/Limitation | Relative Cost (Low/Med/High) |
---|---|---|---|---|
Fiberglass | HVAC systems, industrial air filtration | Highly durable and cost-effective | Less efficient for small particles | Low |
Polyester | Residential and commercial HVAC | Good chemical resistance and lightweight | Poor performance in high temperatures | Medium |
Activated Carbon | Odor control in kitchens and labs | Excellent for VOC and odor removal | Higher cost and saturation over time | High |
Metal Mesh | Industrial air filtration | Reusable and durable | Lower filtration efficiency | Medium |
This strategic material selection guide provides B2B buyers with essential insights into the materials used in air filters, helping them make informed decisions based on their specific needs and regional compliance requirements.
In-depth Look: Manufacturing Processes and Quality Assurance for air filter supplier
What Are the Main Stages of Manufacturing Processes for Air Filters?
The manufacturing process for air filters consists of several critical stages that ensure the final product meets industry standards and customer specifications. Understanding these stages helps B2B buyers assess the capabilities of suppliers and make informed purchasing decisions.
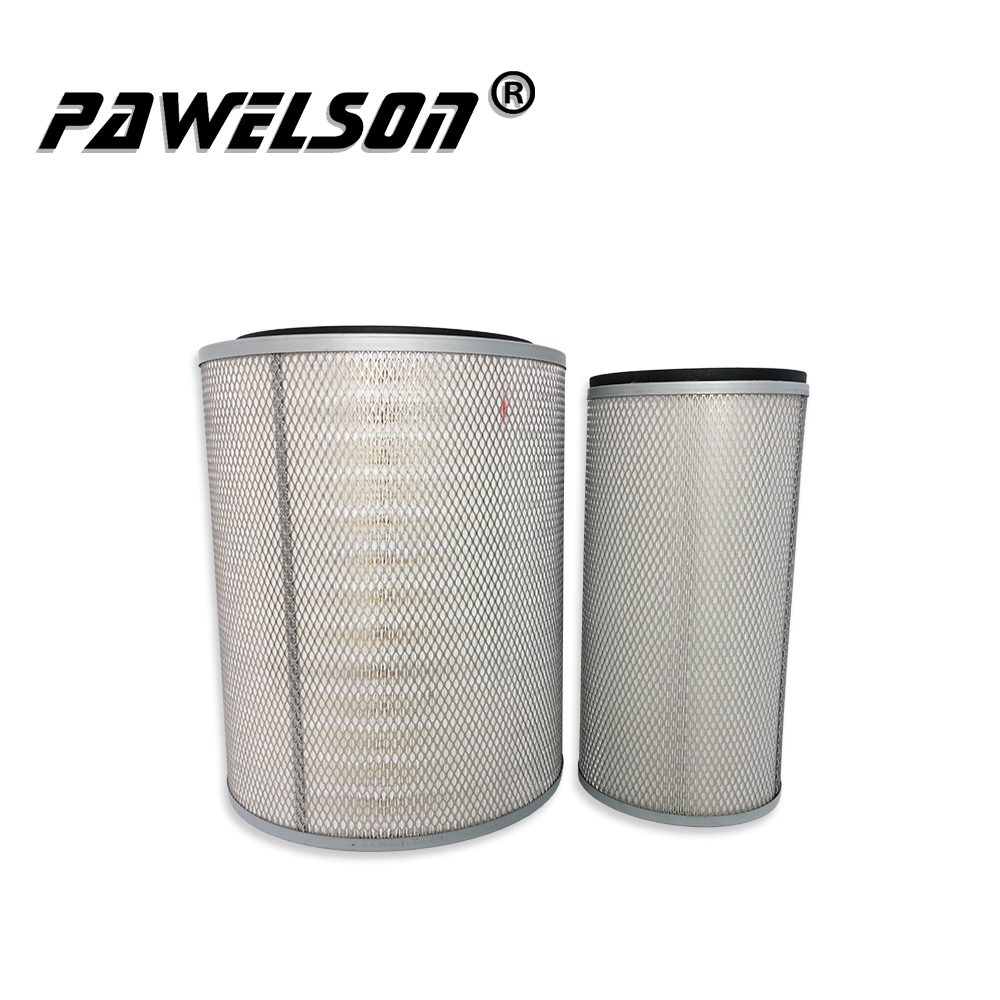
A stock image related to air filter supplier.
1. Material Preparation
The first stage in air filter manufacturing involves sourcing and preparing raw materials. Common materials include synthetic fibers, activated carbon, and metals. Suppliers often utilize advanced technologies such as melt-blown processes to create fine fibers for high-efficiency particulate air (HEPA) filters. B2B buyers should inquire about the suppliers’ material sourcing practices, including sustainability and compliance with environmental regulations.
2. Forming
In the forming stage, the prepared materials are shaped into filter media. This can involve processes like pleating, where the media is folded to increase surface area and enhance filtration efficiency. Techniques such as electrostatic charging may also be employed to improve particle capture rates. Buyers should look for suppliers who utilize state-of-the-art forming technologies, as these can significantly impact the performance of the air filters.
3. Assembly
Once the filter media is formed, it is assembled into the final product. This stage typically includes attaching frames, seals, and end caps. Automation is commonly employed here to ensure consistent quality and reduce labor costs. Buyers should assess whether the supplier’s assembly processes are automated or manual, as this can affect both quality and pricing.
4. Finishing
The finishing stage encompasses various treatments and coatings that enhance the filter’s durability and efficiency. This may include surface treatments to improve resistance to moisture and contaminants. Additionally, finishing processes ensure that the filters are clean and free of any debris that may affect performance. B2B buyers should inquire about the specific finishing techniques used by suppliers to guarantee product longevity and reliability.
How Is Quality Assurance Implemented in Air Filter Manufacturing?
Quality assurance (QA) is crucial in ensuring that air filters meet both international standards and specific industry requirements. For B2B buyers, understanding the QA processes in place can provide confidence in the products they are purchasing.
Relevant International Standards for Air Filters
Air filter manufacturers often adhere to international quality standards such as ISO 9001, which outlines the criteria for a quality management system. Additionally, industry-specific certifications like CE marking (for compliance with European health, safety, and environmental protection standards) and API standards (for American Petroleum Institute compliance) are vital. Buyers should ensure that their suppliers have these certifications, as they reflect a commitment to quality and safety.
What Are the Key Quality Control Checkpoints?
Quality control (QC) in air filter manufacturing typically involves several key checkpoints:
-
Incoming Quality Control (IQC): This initial stage checks the quality of raw materials before they enter the production process. It ensures that only materials meeting specific standards are used.
-
In-Process Quality Control (IPQC): During manufacturing, various checks are performed to monitor the production process and ensure that it adheres to defined parameters. This includes monitoring temperature, humidity, and other environmental factors that can affect quality.
-
Final Quality Control (FQC): Once production is complete, the final products undergo rigorous testing to confirm they meet performance specifications. This may include airflow tests, particle capture efficiency tests, and durability assessments.
Which Testing Methods Are Commonly Used in Air Filter Manufacturing?
To ensure the performance and reliability of air filters, manufacturers employ various testing methods. B2B buyers should be familiar with these methods to understand how suppliers validate their products.
-
Airflow Testing: Measures the amount of air that can pass through the filter at various pressure differentials, providing insight into its efficiency and capacity.
-
Particle Size Distribution Testing: Evaluates the filter’s ability to capture particles of different sizes, ensuring compliance with standards such as HEPA.
-
Dust Holding Capacity Testing: Determines how much dust the filter can hold before it needs replacement, indicating its lifespan and efficiency.
How Can B2B Buyers Verify Supplier Quality Control Processes?
For international B2B buyers, verifying a supplier’s quality control processes is essential to ensure product reliability. Here are effective methods:
-
Audits: Conducting on-site audits of the manufacturing facility allows buyers to assess the supplier’s quality control systems directly. This includes reviewing documentation, observing processes, and evaluating equipment.
-
Quality Assurance Reports: Requesting detailed QA reports can provide insights into the supplier’s testing results, compliance with standards, and any corrective actions taken in response to quality issues.
-
Third-Party Inspections: Engaging third-party inspection agencies can add an extra layer of assurance. These agencies can conduct independent assessments of the manufacturing processes and product quality.
What Are the Quality Control Nuances for International B2B Buyers?
International buyers, especially those from diverse regions like Africa, South America, the Middle East, and Europe, face unique challenges when it comes to quality control. Understanding these nuances can help in making informed decisions.
-
Regulatory Compliance: Different regions have varying regulations regarding air quality and filtration standards. Buyers should ensure that their suppliers are compliant with local regulations in their respective markets.
-
Cultural and Communication Differences: Effective communication is key to ensuring quality expectations are met. Buyers should establish clear lines of communication and possibly engage local representatives to facilitate smoother interactions.
-
Logistics and Supply Chain Management: International shipping can introduce risks related to product integrity. Buyers should evaluate how suppliers manage logistics, including packaging and transportation, to mitigate potential damage during transit.
By understanding these manufacturing processes and quality assurance practices, B2B buyers can make more informed decisions when selecting air filter suppliers, ensuring they receive high-quality products that meet their specific needs.
Practical Sourcing Guide: A Step-by-Step Checklist for ‘air filter supplier’
In the competitive landscape of air filter procurement, international B2B buyers must navigate a series of critical steps to ensure they select the right supplier. This guide offers a structured checklist to streamline the sourcing process, focusing on actionable insights for buyers from Africa, South America, the Middle East, and Europe.
Step 1: Define Your Technical Specifications
Start by clearly outlining your specific air filter requirements, including dimensions, filtration efficiency, and material types. This step is crucial as it ensures that the suppliers you engage with can meet your operational needs. Consider factors such as the environment where the filters will be used and any industry-specific regulations that must be adhered to.
- Filtration Efficiency: Specify the Minimum Efficiency Reporting Value (MERV) ratings or equivalent standards relevant to your application.
- Material Requirements: Identify whether you need HEPA filters, activated carbon filters, or other specialized options.
Step 2: Research Potential Suppliers
Conduct thorough research to compile a list of potential air filter suppliers. Utilize online directories, industry associations, and trade shows to gather information. This research lays the foundation for informed decision-making.
- Supplier Reviews: Look for testimonials and reviews from other businesses in your region to gauge reliability and product quality.
- Industry Experience: Prioritize suppliers with experience in your specific industry sector, as they will better understand your unique needs.
Step 3: Evaluate Supplier Certifications
Before moving forward, verify the certifications and compliance of your shortlisted suppliers. Certifications such as ISO 9001 for quality management and any relevant environmental standards can indicate a supplier’s commitment to quality and sustainability.
- Quality Assurance: Ensure the supplier has a robust quality assurance program in place, including regular audits and testing.
- Sustainability Practices: Investigate whether the supplier adheres to environmentally friendly practices, which can be a significant consideration for many buyers.
Step 4: Request Samples and Product Specifications
Once you have narrowed down your options, request samples of the air filters you are interested in. Testing samples allows you to assess the product quality firsthand and determine if they meet your specifications.
- Performance Testing: Evaluate the samples under your operational conditions to ensure they perform as expected.
- Documentation: Ask for detailed product specifications and testing reports to better understand the filters’ capabilities.
Step 5: Negotiate Pricing and Terms
Engage in discussions with your selected suppliers regarding pricing, payment terms, and delivery schedules. This step is essential for establishing a mutually beneficial relationship.
- Bulk Discounts: Inquire about discounts for bulk orders or long-term contracts, which can significantly reduce costs.
- Lead Times: Ensure that the supplier can meet your required delivery timelines, especially if you have specific project deadlines.
Step 6: Conduct a Site Visit or Virtual Tour
If feasible, arrange for a site visit or a virtual tour of the supplier’s manufacturing facility. This step can provide valuable insights into their production processes and quality control measures.
- Production Capacity: Assess whether the supplier has the capacity to handle your order volume consistently.
- Operational Standards: Observe their adherence to safety and quality standards in the manufacturing process.
Step 7: Establish Communication Channels
Finally, set up effective communication channels with your chosen supplier. Clear and open communication is vital for resolving any issues that may arise during the procurement process.
- Regular Updates: Agree on a schedule for regular updates regarding order status, delivery timelines, and any potential challenges.
- Feedback Mechanism: Establish a feedback mechanism to address any concerns or improvements needed post-purchase.
By following this checklist, international B2B buyers can streamline their sourcing process for air filters, ensuring they partner with reliable suppliers who meet their technical and operational needs.
Comprehensive Cost and Pricing Analysis for air filter supplier Sourcing
What Are the Key Cost Components in Air Filter Supplier Sourcing?
When sourcing air filters for international B2B transactions, understanding the cost structure is crucial. The primary cost components include:
-
Materials: The choice of raw materials significantly impacts the overall cost. High-quality materials, such as HEPA media or activated carbon, may increase costs but offer better filtration performance.
-
Labor: Labor costs can vary widely based on the region and complexity of the manufacturing process. Countries with lower labor costs may provide more competitive pricing, but this should be balanced against quality and reliability.
-
Manufacturing Overhead: This includes indirect costs such as utilities, rent, and equipment maintenance. Efficient manufacturing processes can help minimize overhead costs.
-
Tooling: Custom tooling for specialized filters can be a significant upfront cost. Buyers should consider whether the investment in tooling will lead to long-term savings or efficiencies.
-
Quality Control (QC): Implementing stringent QC measures ensures that the products meet international standards, which may increase costs. However, this is essential for maintaining product reliability and customer satisfaction.
-
Logistics: Shipping and handling costs can fluctuate based on the shipping method, distance, and any tariffs or duties applicable to the destination country. Buyers should factor in these costs when evaluating total expenses.
-
Margin: Supplier profit margins can vary based on market demand and competition. Understanding the margin can help buyers negotiate better pricing.
How Do Price Influencers Affect Air Filter Costs?
Several factors influence the pricing of air filters, particularly in international markets:
-
Volume and Minimum Order Quantity (MOQ): Suppliers often provide discounts for larger orders, making it essential for buyers to assess their needs and negotiate MOQs effectively.
-
Specifications and Customization: Custom filters tailored to specific applications may incur higher costs. Buyers should clearly define their specifications to avoid unexpected expenses.
-
Material Quality and Certifications: Filters that meet higher quality standards or possess certifications (e.g., ISO, CE) usually come at a premium. Buyers should weigh the benefits of these certifications against their budget.
-
Supplier Factors: The reliability, reputation, and location of the supplier can impact pricing. Local suppliers may reduce shipping costs but could have higher material costs, while overseas suppliers might offer lower prices but involve higher logistics expenses.
-
Incoterms: Understanding Incoterms (International Commercial Terms) is critical for determining who bears the cost and risk during transportation. This knowledge can help buyers avoid unexpected charges.
What Tips Can International Buyers Use to Optimize Air Filter Sourcing Costs?
For B2B buyers from regions like Africa, South America, the Middle East, and Europe, implementing effective sourcing strategies can lead to significant savings:
-
Negotiation: Engaging suppliers in open discussions about pricing can yield better terms. Establishing long-term relationships often leads to more favorable pricing structures.
-
Cost-Efficiency: Analyzing the Total Cost of Ownership (TCO) helps buyers understand the long-term implications of their purchases. This includes maintenance, energy efficiency, and replacement costs, not just the initial purchase price.
-
Pricing Nuances: Be aware of regional pricing differences. For instance, European suppliers may have higher labor costs but may offer superior quality or certifications, while suppliers from Africa or South America might provide more competitive pricing but require a thorough evaluation of quality standards.
Are There Any Disclaimers for Indicative Prices?
It’s important to note that prices can fluctuate based on market conditions, currency exchange rates, and changes in material costs. Buyers should conduct thorough market research and request updated quotes from suppliers to ensure they are making informed decisions.
Alternatives Analysis: Comparing air filter supplier With Other Solutions
Understanding Alternatives to Air Filter Suppliers
When selecting air filtration solutions, B2B buyers often face a variety of options, each with its own advantages and limitations. While traditional air filter suppliers offer established technologies and reliability, it is essential to consider alternative solutions that may better suit specific business needs. This analysis compares air filter suppliers with other viable technologies, helping international buyers from regions like Africa, South America, the Middle East, and Europe make informed decisions.
Comparison Table of Air Filtration Solutions
Comparison Aspect | Air Filter Supplier | Electrostatic Air Filters | HEPA Filters |
---|---|---|---|
Performance | High efficiency, reliable | Very effective, self-cleaning | Superior particle removal |
Cost | Moderate initial investment | Higher upfront costs | Higher than standard filters |
Ease of Implementation | Simple installation | Requires electrical setup | Easy to install, but bulky |
Maintenance | Regular replacement needed | Low maintenance | Frequent replacement needed |
Best Use Case | General commercial use | Industrial applications | Hospitals, labs, sensitive environments |
In-Depth Analysis of Alternative Solutions
What Are Electrostatic Air Filters and Their Benefits?
Electrostatic air filters use charged plates to attract and capture particles from the air. These systems can provide very effective filtration and often have a self-cleaning capability that reduces maintenance costs over time. However, they require a higher initial investment and an electrical setup, which may not be feasible for all businesses. Their best use case is in industrial applications where air quality is crucial, but the electrical infrastructure is already in place.
How Do HEPA Filters Compare to Air Filter Suppliers?
HEPA (High-Efficiency Particulate Air) filters are renowned for their ability to capture at least 99.97% of particles that are 0.3 microns in size. This level of filtration makes them ideal for environments such as hospitals, laboratories, and clean rooms where air quality is paramount. While HEPA filters provide superior performance, they can be bulkier and may require frequent replacements, leading to higher ongoing costs. They are best suited for specialized applications where air purity is critical.
Conclusion: How to Choose the Right Air Filtration Solution for Your Business?
Selecting the right air filtration solution requires a careful assessment of your specific needs, including the environment where the filters will be used, budget constraints, and maintenance capabilities. While traditional air filter suppliers provide reliable and moderate-cost options suitable for general commercial use, alternatives like electrostatic and HEPA filters may offer better performance for specialized applications. B2B buyers should weigh the pros and cons of each option, considering factors such as installation ease, ongoing maintenance, and the critical nature of air quality in their operations. By doing so, they can make informed decisions that enhance operational efficiency and ensure compliance with health standards.
Essential Technical Properties and Trade Terminology for air filter supplier
What Are the Essential Technical Properties of Air Filters?
Understanding the technical properties of air filters is crucial for B2B buyers, especially those sourcing from international suppliers. Here are the key specifications to consider:
1. Material Grade
The material used in air filters can significantly affect their performance and lifespan. Common materials include fiberglass, pleated paper, and synthetic fibers. Each material has unique filtration properties and durability, impacting how well the filter can capture pollutants and particles. Selecting the right material ensures optimal air quality and compliance with industry standards.
2. Filter Efficiency Rating (MERV)
The Minimum Efficiency Reporting Value (MERV) rating indicates how effectively a filter captures airborne particles. Ratings range from 1 to 20, with higher numbers representing better filtration capabilities. For instance, a MERV rating of 8 or higher is ideal for commercial applications where air quality is critical. Understanding MERV ratings helps buyers choose filters that meet specific air quality requirements.
3. Airflow Resistance (Pressure Drop)
Airflow resistance measures how much the filter impedes the movement of air. A higher pressure drop can lead to reduced efficiency in HVAC systems, increasing energy costs. It’s essential for buyers to balance filtration efficiency with acceptable pressure drop levels to maintain system performance while ensuring clean air.
4. Service Life and Replacement Interval
Knowing the expected service life of an air filter helps buyers plan maintenance schedules and avoid unplanned downtime. Filters typically need replacement every 3 to 12 months, depending on usage and environmental conditions. Buyers should inquire about the recommended replacement intervals to optimize performance and cost-effectiveness.
5. Size and Compatibility
Filters come in various sizes, and ensuring compatibility with existing systems is critical. Buyers must specify the dimensions required for their equipment to avoid installation issues. Custom sizes may also be available, which can cater to unique operational needs.
6. Certifications and Compliance
Many air filters must meet specific industry standards and certifications, such as ISO, ASHRAE, or HEPA ratings. These certifications indicate that the filters have been tested for quality and performance. Buyers should verify certifications to ensure compliance with local regulations and industry best practices.
What Are Common Trade Terms in the Air Filter Industry?
Familiarity with industry jargon can streamline communication and negotiations with suppliers. Here are essential terms every B2B buyer should know:
1. OEM (Original Equipment Manufacturer)
OEM refers to companies that produce components or products that other companies sell under their brand. In the air filter industry, understanding OEM relationships can help buyers identify quality products that meet specific operational requirements.
2. MOQ (Minimum Order Quantity)
MOQ is the smallest quantity of a product that a supplier is willing to sell. Knowing the MOQ is crucial for budgeting and inventory management. Buyers should negotiate MOQs that align with their purchasing strategies to avoid excess stock or higher costs.
3. RFQ (Request for Quotation)
An RFQ is a formal process where buyers request price quotes from suppliers for specified products or services. This process helps buyers compare prices, terms, and capabilities, leading to informed purchasing decisions.
4. Incoterms (International Commercial Terms)
Incoterms are standardized trade terms that define the responsibilities of buyers and sellers in international transactions. Familiarity with terms like FOB (Free on Board) or CIF (Cost, Insurance, and Freight) helps buyers understand shipping costs and liability, aiding in risk management.
5. Lead Time
Lead time refers to the time taken from placing an order until the product is delivered. Understanding lead times is essential for inventory planning and ensuring that air filters are available when needed.
6. Warranty and Service Agreements
Warranties and service agreements outline the manufacturer’s commitments regarding product quality and support. Buyers should review these terms to ensure they are protected against defects and have access to necessary maintenance services.
By grasping these technical properties and trade terminologies, international B2B buyers can make informed decisions when sourcing air filters, ultimately enhancing operational efficiency and air quality.
Navigating Market Dynamics and Sourcing Trends in the air filter supplier Sector
What Are the Key Market Trends Impacting Air Filter Suppliers?
The air filter supplier sector is experiencing significant transformation driven by global demand for cleaner air and stricter regulations on air quality. Key trends include the increasing adoption of advanced filtration technologies, such as HEPA and electrostatic filters, which enhance efficiency in capturing particulate matter. Additionally, the rise of smart air filtration systems equipped with IoT capabilities is reshaping how businesses approach air quality management. This technology allows for real-time monitoring and predictive maintenance, reducing downtime and operational costs.
For international B2B buyers, particularly from Africa, South America, the Middle East, and Europe, understanding local regulations and market dynamics is crucial. The European market, for instance, is pushing for compliance with stringent EU regulations on indoor air quality, which affects sourcing decisions. Similarly, emerging markets in Africa and South America are seeing a surge in demand for affordable yet effective air filtration solutions as urbanization increases. Buyers should prioritize suppliers who offer a diverse range of products tailored to meet these regional requirements, ensuring compliance and cost-effectiveness.
How Is Sustainability Influencing Sourcing Decisions in the Air Filter Sector?
Sustainability has become a central theme in the procurement strategies of B2B buyers in the air filter industry. The environmental impact of manufacturing processes, including energy consumption and waste generation, is under scrutiny. Buyers are increasingly seeking suppliers committed to ethical sourcing practices and sustainability initiatives. This includes the use of recyclable materials and the implementation of energy-efficient manufacturing processes.
Moreover, certifications such as ISO 14001 (Environmental Management Systems) and Green Seal are becoming essential for suppliers aiming to demonstrate their commitment to sustainability. These certifications not only enhance brand reputation but also provide buyers with the assurance that their suppliers are adhering to environmental standards. Consequently, B2B buyers should engage with suppliers who can provide transparency regarding their sourcing practices and sustainability efforts, as this can significantly influence long-term partnerships and customer loyalty.
What Is the Historical Context of the Air Filter Supplier Sector?
The air filter supplier sector has evolved significantly over the decades, shaped by technological advancements and increasing environmental awareness. Initially dominated by basic mechanical filters, the industry has transitioned to more sophisticated solutions, including HEPA and activated carbon filters. The late 20th century saw a surge in regulations aimed at improving air quality, particularly in industrialized nations, which further propelled innovation in filtration technologies.
As awareness of indoor air quality grew, the demand for high-performance air filters in residential and commercial settings increased. This shift has led to the development of specialized products designed for various applications, from HVAC systems to personal protective equipment. Today, air filter suppliers are not only focused on performance but also on sustainability, reflecting the changing priorities of global consumers and regulatory bodies alike. This historical evolution underscores the importance of adaptability for suppliers and the need for buyers to stay informed about emerging technologies and trends in the market.
Frequently Asked Questions (FAQs) for B2B Buyers of air filter supplier
-
How do I choose the right air filter supplier for my business?
Selecting the right air filter supplier involves assessing several factors, including product quality, compliance with international standards, and the supplier’s ability to meet your specific needs. Start by researching suppliers with a proven track record in your industry. Request samples to evaluate filter performance and durability. Additionally, consider the supplier’s certifications, customer service, and their capacity for customization to ensure they can meet your volume and specification requirements. -
What is the best type of air filter for industrial applications?
The best type of air filter for industrial applications often depends on the specific environment and contaminants present. For instance, HEPA filters are ideal for environments requiring high-efficiency particulate air filtration, while activated carbon filters are effective for odor and chemical control. Evaluate your operational needs, such as air quality standards and maintenance capabilities, to determine the most suitable filter type that balances efficiency and cost. -
What are the typical minimum order quantities (MOQ) for air filters?
Minimum order quantities for air filters can vary significantly between suppliers, typically ranging from 100 to 1,000 units. Factors influencing MOQ include the type of filter, customization requirements, and the supplier’s production capacity. It’s advisable to communicate directly with potential suppliers to negotiate MOQs that align with your business needs, especially if you are entering a new market or testing a product. -
How can I ensure the quality of air filters from international suppliers?
To ensure the quality of air filters from international suppliers, verify their certifications and compliance with industry standards, such as ISO 9001 or other relevant certifications. Request detailed product specifications and test reports to confirm performance claims. Additionally, consider conducting audits of the supplier’s manufacturing processes or using third-party inspection services to assess quality before shipment. -
What payment terms are common when dealing with air filter suppliers?
Common payment terms when working with air filter suppliers include options such as net 30, 50% upfront with the balance before shipment, or letter of credit for larger orders. It’s essential to discuss and agree on payment terms that protect both parties. Consider using escrow services for high-value transactions to ensure that funds are only released upon satisfactory delivery of goods. -
How do I handle logistics and shipping when sourcing air filters internationally?
Handling logistics and shipping for international air filter sourcing requires careful planning. Choose reliable freight forwarders who are experienced in your specific region, whether it’s Africa, South America, the Middle East, or Europe. Understand the Incoterms (e.g., FOB, CIF) to clarify responsibilities for shipping, insurance, and duties. Ensure you have a plan for customs clearance to avoid delays, and track shipments to stay informed of their status. -
What customization options should I consider when sourcing air filters?
Customization options for air filters can include dimensions, filter media type, and specific performance characteristics like MERV ratings or efficiency levels. Discussing these options with your supplier can help align the product with your specific application needs. Additionally, consider branding options, such as custom packaging or labeling, which can enhance your product’s marketability and recognition. -
How can I assess the reliability of an air filter supplier?
Assessing the reliability of an air filter supplier involves reviewing their business history, customer testimonials, and industry reputation. Request references from other clients and check online reviews to gauge their service quality. Additionally, evaluate their communication responsiveness and willingness to provide detailed information about their products and processes. Engaging in a trial order can also help you assess their reliability before committing to larger purchases.
Important Disclaimer & Terms of Use
⚠️ Important Disclaimer
The information provided in this guide, including content regarding manufacturers, technical specifications, and market analysis, is for informational and educational purposes only. It does not constitute professional procurement advice, financial advice, or legal advice.
While we have made every effort to ensure the accuracy and timeliness of the information, we are not responsible for any errors, omissions, or outdated information. Market conditions, company details, and technical standards are subject to change.
B2B buyers must conduct their own independent and thorough due diligence before making any purchasing decisions. This includes contacting suppliers directly, verifying certifications, requesting samples, and seeking professional consultation. The risk of relying on any information in this guide is borne solely by the reader.
Strategic Sourcing Conclusion and Outlook for air filter supplier
What Are the Key Takeaways for Strategic Sourcing in Air Filters?
In conclusion, strategic sourcing for air filter suppliers presents significant opportunities for international B2B buyers, particularly those operating in diverse markets such as Africa, South America, the Middle East, and Europe. By understanding the evolving landscape of air filtration technology and sustainability trends, businesses can optimize their procurement processes and secure high-quality products that meet regulatory standards. Key factors to consider include supplier reliability, cost-effectiveness, and the ability to provide innovative solutions tailored to specific industry needs.
How Can International Buyers Enhance Their Sourcing Strategies?
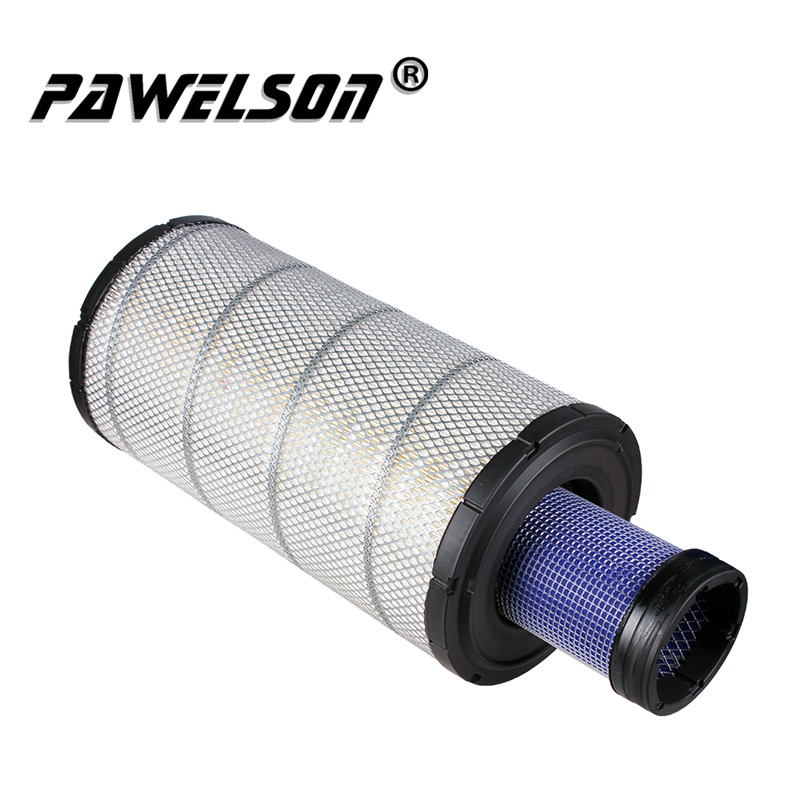
A stock image related to air filter supplier.
Investing in strategic sourcing not only reduces operational risks but also fosters long-term partnerships with suppliers who share a commitment to quality and sustainability. As buyers navigate the complexities of global supply chains, leveraging data analytics and supplier performance metrics can enhance decision-making and drive competitive advantage.
What Does the Future Hold for Air Filter Suppliers?
Looking ahead, the demand for advanced air filtration solutions is expected to rise, driven by increasing environmental regulations and consumer awareness. International B2B buyers should take proactive steps to align their sourcing strategies with these trends. Engaging with innovative suppliers and exploring collaborative opportunities will be vital in ensuring resilience and sustainability in the supply chain. Start evaluating your sourcing strategies today to position your business for success in this dynamic market.