Find the Best Flange Supplier: The Ultimate Sourcing Guide (2025)
Introduction: Navigating the Global Market for flange supplier
Navigating the global market for flange suppliers can be a daunting task for international B2B buyers, particularly those operating in Africa, South America, the Middle East, and Europe, including countries like the UAE and Saudi Arabia. The challenge often lies in identifying the right type of flange that meets specific operational requirements while ensuring compliance with local standards. This guide aims to demystify the complexities of sourcing flanges by offering an extensive overview of various flange types, their applications, and the critical factors to consider when selecting a supplier.
In this comprehensive resource, you will discover detailed information on different flange categories such as weld neck, slip-on, and threaded flanges, as well as their specific uses across industries. Additionally, we will delve into essential topics such as supplier vetting processes, cost considerations, and regulatory compliance, enabling you to make informed purchasing decisions.
By equipping international B2B buyers with actionable insights and practical knowledge, this guide not only simplifies the sourcing process but also empowers you to establish reliable partnerships with reputable flange suppliers. Whether you are managing a small-scale project or a large industrial operation, understanding the nuances of flanges will enhance your procurement strategy and ensure the longevity of your piping systems.
Understanding flange supplier Types and Variations
Type Name | Key Distinguishing Features | Primary B2B Applications | Brief Pros & Cons for Buyers |
---|---|---|---|
Weld Neck Flange | Long tapered hub for welding; provides strong connection | High-pressure and high-temperature systems | Pros: Excellent strength; suitable for critical applications. Cons: Higher cost; requires skilled labor for installation. |
Slip-on Flange | Larger bore size; easy to install with external welding | Low-pressure liquid systems | Pros: Cost-effective; simple installation. Cons: Less robust under high pressure; potential for leakage. |
Threaded Flange | Tapered internal threads; no welding needed | Low-pressure applications, especially gas | Pros: Quick assembly; ideal for explosive environments. Cons: Limited to smaller pipe sizes; less durable under high stress. |
Socket Weld Flange | Pipe inserted into flange; secured with a fillet weld | Small high-pressure piping systems | Pros: Strong connection; reduces risk of leaks. Cons: Not suitable for corrosive fluids; installation complexity. |
Lap Joint Flange | Two-piece construction; requires a matching stub end | Piping systems needing frequent disassembly | Pros: Easy to align; allows for quick assembly/disassembly. Cons: Requires additional components; not suitable for high-pressure systems. |
What Are the Characteristics of Weld Neck Flanges?
Weld neck flanges feature a long tapered hub, making them ideal for high-pressure and high-temperature environments. Their design allows for smooth flow and minimizes turbulence, which is crucial in critical applications such as oil and gas pipelines. When purchasing, consider the flange material and pressure rating, as these factors significantly impact performance and longevity.
How Do Slip-on Flanges Compare for B2B Applications?
Slip-on flanges are characterized by their larger bore size, allowing pipes to slide inside before being welded. They are commonly used in low-pressure liquid applications due to their cost-effectiveness and ease of installation. However, buyers should be cautious about their limitations under high-pressure conditions, which could lead to potential leakage.
What Are the Advantages of Threaded Flanges for Buyers?
Threaded flanges eliminate the need for welding, featuring internal tapered threads that connect to matching male threads on pipes. This design is particularly advantageous in low-pressure applications, such as gas lines. While they offer quick assembly and are ideal for environments where welding poses risks, buyers should note their size limitations and reduced durability under stress.
Why Choose Socket Weld Flanges for High-Pressure Systems?
Socket weld flanges provide a robust connection by inserting the pipe into the flange and securing it with a fillet weld. They are best suited for small, high-pressure piping systems, offering enhanced leak resistance. However, buyers should consider the potential for corrosion in the socket area and the complexity of installation, especially in tight spaces.
When Should You Consider Lap Joint Flanges?
Lap joint flanges consist of a two-piece design that allows for easy alignment and assembly. They are particularly useful in applications requiring frequent disassembly, such as maintenance in industrial settings. While they offer flexibility, buyers must ensure compatibility with stub ends and be aware that they are not suitable for high-pressure applications.
Related Video: Piping Flange Types, Faces, and Surfaces – Explained!
Key Industrial Applications of flange supplier
Industry/Sector | Specific Application of flange supplier | Value/Benefit for the Business | Key Sourcing Considerations for this Application |
---|---|---|---|
Oil & Gas | Flange connections in pipelines for transporting fluids | Ensures secure, leak-proof connections under high pressure | Compliance with international standards and certifications |
Water Treatment | Flanges in water purification systems | Facilitates maintenance and replacement of components | Material compatibility with corrosive substances |
Chemical Processing | Flanges in reactors and storage tanks | Supports safe handling of hazardous materials | High-temperature and pressure ratings |
Construction | Flanges in HVAC systems and plumbing installations | Provides flexibility for repairs and modifications | Availability of various flange types and sizes |
Marine Engineering | Flanges in shipbuilding for piping systems | Enhances the durability and reliability of systems | Resistance to corrosion and harsh environmental conditions |
How Are Flanges Used in the Oil & Gas Industry?
In the oil and gas sector, flanges are critical for establishing secure connections in pipelines that transport crude oil, natural gas, and other fluids. These flanges must be capable of withstanding high pressures and extreme temperatures, making it essential for buyers to source flanges that comply with international standards. B2B buyers from regions like the Middle East, where oil extraction is prevalent, should prioritize suppliers who offer flanges with certifications such as API 6A or ASME B16.5 to ensure reliability and safety in their operations.
What Role Do Flanges Play in Water Treatment Systems?
Flanges are integral to water treatment facilities, connecting various components such as pumps, filters, and valves. They allow for easy assembly and disassembly, which is crucial for maintenance and repairs. Buyers must consider the material compatibility of flanges with water treatment chemicals to avoid corrosion. For international buyers in Africa and South America, it is vital to work with suppliers who understand local regulations and can provide flanges that meet specific safety and environmental standards.
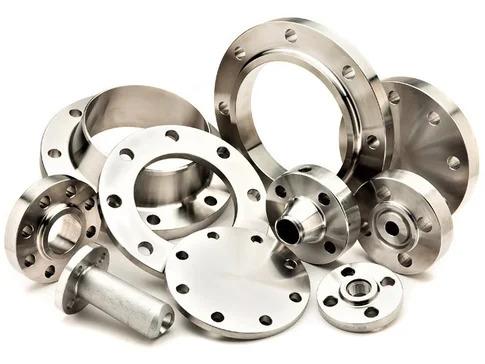
A stock image related to flange supplier.
Why Are Flanges Important in Chemical Processing?
In chemical processing, flanges are used in reactors, storage tanks, and piping systems to safely transport hazardous materials. The integrity of these connections is paramount to prevent leaks and ensure safety. B2B buyers need to focus on sourcing flanges that offer high-temperature and pressure ratings, as well as chemical resistance. Suppliers should provide detailed specifications and certifications to assure compliance with safety regulations, especially for companies in Europe that face stringent industry standards.
How Do Flanges Benefit Construction Projects?
In construction, flanges are commonly used in HVAC systems and plumbing installations, providing flexibility for future modifications. They facilitate easy access for maintenance, which is essential in large buildings. When sourcing flanges, buyers should consider the availability of various types and sizes to match their project requirements. International buyers, particularly in Europe, should also evaluate the supplier’s ability to deliver on time and provide technical support for installation.
What Is the Significance of Flanges in Marine Engineering?
Flanges play a vital role in marine engineering, particularly in shipbuilding, where they connect piping systems that handle fuel, water, and waste. The durability and reliability of these connections are crucial for the safe operation of vessels. Buyers in the Middle East and Europe should source flanges that are resistant to corrosion and designed to withstand harsh marine environments. It is essential to partner with suppliers who specialize in marine-grade materials and understand the unique challenges of the industry.
Related Video: What is a Flange?
3 Common User Pain Points for ‘flange supplier’ & Their Solutions
Scenario 1: Difficulty in Identifying the Right Flange Type for Specific Applications
The Problem:
International B2B buyers often face the challenge of selecting the appropriate type of flange for their specific industrial applications. With a multitude of flange types—such as weld neck, slip-on, and threaded—each designed for different pressure ratings and environmental conditions, it can be overwhelming. For instance, a buyer from South America might be tasked with sourcing flanges for an oil and gas project that requires high-pressure ratings. Misjudging the flange type could lead to operational failures, safety hazards, or costly delays in project timelines.
The Solution:
To effectively navigate this challenge, buyers should invest time in understanding the specific requirements of their applications, including pressure, temperature, and fluid type. Consulting with engineers or flange suppliers who specialize in their industry can provide invaluable insights. Additionally, creating a detailed specifications document outlining these requirements will facilitate more accurate quotes and recommendations from suppliers. Leveraging online resources, such as technical datasheets and flange comparison charts, can also help buyers visualize their options. This proactive approach ensures that the correct flange type is sourced, ultimately enhancing system reliability and safety.
Scenario 2: Challenges in Flange Sizing and Standardization
The Problem:
Another common issue faced by B2B buyers is the confusion surrounding flange sizing and standardization, especially when sourcing from international suppliers. Standards such as ASA/ASME, PN/DIN, and BS10 can vary significantly, and discrepancies in sizing can lead to compatibility problems. A buyer from the Middle East may find themselves with flanges that do not fit existing piping systems due to a lack of standardization, resulting in wasted resources and increased procurement costs.
The Solution:
Buyers should familiarize themselves with the relevant flange standards applicable to their region and industry. Creating a standardized sizing chart that includes both imperial and metric measurements can help streamline the purchasing process. When engaging with suppliers, it’s essential to specify the required standards clearly and request confirmation of compatibility with existing systems. Additionally, using a reliable flange supplier who can provide certification and testing data for their products will ensure that the purchased flanges meet the necessary specifications. This diligence minimizes the risk of costly errors and ensures smooth project execution.
Scenario 3: Delays in Supply Chain and Delivery Timelines
The Problem:
Delays in supply chain logistics are a significant pain point for B2B buyers sourcing flanges, particularly for projects with tight deadlines. A buyer in Europe may face unexpected lead times due to shipping delays or production bottlenecks at the supplier’s facility. Such delays can halt critical operations, leading to financial losses and strained relationships with clients.
The Solution:
To mitigate the risk of supply chain delays, buyers should establish strong relationships with multiple flange suppliers to create a diversified sourcing strategy. Conducting thorough research to identify suppliers with a proven track record for timely delivery is crucial. It’s also beneficial to negotiate clear delivery timelines and incorporate penalties for late shipments in contracts. Implementing a just-in-time (JIT) inventory strategy can further reduce the impact of delays by ensuring that flanges are ordered only when needed, thus minimizing excess stock. Regular communication with suppliers about project timelines and potential challenges can foster transparency and improve delivery reliability. By proactively managing their supply chain, buyers can ensure that their projects remain on track and within budget.
Strategic Material Selection Guide for flange supplier
When selecting materials for flanges, international B2B buyers must consider various factors that can significantly impact performance, cost, and compliance with industry standards. Below is an analysis of four common materials used in flange manufacturing, along with their properties, advantages, disadvantages, and specific considerations for buyers from regions such as Africa, South America, the Middle East, and Europe.
What Are the Key Properties of Carbon Steel Flanges?
Carbon Steel is a popular choice for flange manufacturing due to its excellent mechanical properties. It can withstand high pressures and temperatures, making it suitable for a variety of industrial applications. Carbon steel flanges typically have a temperature rating up to 500°F (260°C) and can handle pressures ranging from 150 to 2500 psi, depending on the specific grade.
Pros:
– High strength and durability.
– Cost-effective compared to other materials.
– Widely available and easily machinable.
Cons:
– Prone to corrosion if not properly coated or maintained.
– Limited performance in highly corrosive environments.
Impact on Application:
Carbon steel flanges are ideal for water, oil, and gas pipelines. However, they may not be suitable for applications involving aggressive chemicals unless protective coatings are applied.
Considerations for International Buyers:
Buyers should ensure compliance with ASTM standards and consider local corrosion factors, especially in humid or saline environments common in coastal regions.
How Do Stainless Steel Flanges Compare in Terms of Performance?
Stainless Steel is renowned for its corrosion resistance and aesthetic appeal. With a temperature rating that can reach up to 1200°F (650°C) and pressure ratings similar to carbon steel, stainless steel flanges are versatile for various applications, particularly in the food and pharmaceutical industries.
Pros:
– Exceptional corrosion resistance.
– High-temperature tolerance.
– Low maintenance due to durability.
Cons:
– Generally more expensive than carbon steel.
– More challenging to machine, which can increase manufacturing costs.
Impact on Application:
Stainless steel flanges are perfect for applications involving chemicals, food processing, and high-temperature steam systems. They are less suitable for environments with extreme pH levels unless specific grades (like Duplex or Super Duplex) are used.
Considerations for International Buyers:
Ensure compliance with DIN and JIS standards, especially in regions like Europe and Japan. Buyers should also verify the grade of stainless steel to ensure it meets specific application needs.
What Are the Advantages of Using Alloy Steel Flanges?
Alloy Steel flanges are engineered to provide enhanced mechanical properties and resistance to wear and corrosion. They can handle temperatures up to 1000°F (540°C) and pressures exceeding 2000 psi, making them suitable for high-stress applications.
Pros:
– Improved strength and toughness.
– Good resistance to wear and fatigue.
– Versatile for various industrial applications.
Cons:
– Higher cost compared to carbon and stainless steel.
– More complex manufacturing processes.
Impact on Application:
Ideal for heavy-duty applications in the oil and gas sector, alloy steel flanges can also be used in high-pressure steam systems. However, they may require specialized coatings for corrosion resistance in aggressive environments.
Considerations for International Buyers:
Buyers should look for compliance with ASTM standards and consider the specific alloy composition to ensure compatibility with their operational environment.
When Should You Use PVC Flanges?
PVC (Polyvinyl Chloride) flanges are a non-metallic option that is gaining popularity in specific applications, particularly in plumbing and chemical processing. They can typically handle temperatures up to 140°F (60°C) and are rated for lower pressures compared to metal flanges.
Pros:
– Lightweight and easy to install.
– Excellent resistance to corrosion and chemicals.
– Cost-effective for low-pressure applications.
Cons:
– Limited temperature and pressure ratings.
– Not suitable for high-stress applications.
Impact on Application:
PVC flanges are commonly used in water treatment, irrigation systems, and chemical processing where corrosive media is present. They are not suitable for high-temperature applications.
Considerations for International Buyers:
Buyers should ensure compliance with local plumbing codes and standards, particularly in regions with stringent regulations like Europe.
Summary Table of Material Selection for Flange Suppliers
Material | Typical Use Case for flange supplier | Key Advantage | Key Disadvantage/Limitation | Relative Cost (Low/Med/High) |
---|---|---|---|---|
Carbon Steel | Oil and gas pipelines | Cost-effective and durable | Prone to corrosion | Low |
Stainless Steel | Food and pharmaceutical industries | Exceptional corrosion resistance | Higher cost and machining complexity | High |
Alloy Steel | Heavy-duty industrial applications | Improved strength and toughness | Higher cost and complex manufacturing | Medium |
PVC | Plumbing and chemical processing | Lightweight and easy to install | Limited temperature and pressure ratings | Low |
This strategic material selection guide provides a comprehensive overview for international B2B buyers, enabling informed decisions based on application needs and regional compliance requirements.
In-depth Look: Manufacturing Processes and Quality Assurance for flange supplier
What Are the Typical Manufacturing Processes for Flange Suppliers?
Understanding the manufacturing processes involved in flange production is crucial for international B2B buyers looking for reliability and quality. The manufacturing of flanges generally involves several key stages: material preparation, forming, assembly, and finishing. Each stage incorporates specific techniques to ensure the final product meets stringent quality standards.
How Is Material Prepared for Flange Manufacturing?
Material preparation is the first step in the flange manufacturing process. It involves selecting the appropriate raw materials, which can include carbon steel, stainless steel, and other alloys, depending on the intended application of the flange.
-
Material Selection: Buyers should ensure that suppliers utilize high-quality materials that comply with international standards such as ASTM or ISO specifications. This is crucial for flanges intended for high-pressure applications.
-
Cutting and Shaping: After selecting the material, it is cut into blanks using methods like plasma cutting or laser cutting. The precision of these cuts is critical, as it affects the integrity and fit of the final product.
What Techniques Are Used in Forming Flanges?
Once the material is prepared, the next step is forming. This phase typically employs several methods to shape the flanges into their desired forms.
-
Forging: Many flange manufacturers prefer forging over casting due to its ability to produce stronger and more durable components. In this process, the heated metal is shaped under pressure, aligning the grain structure for enhanced strength.
-
Machining: After forging, flanges undergo machining processes such as turning, milling, and drilling to achieve precise dimensions and tolerances. This is essential for ensuring that flanges fit correctly in piping systems.
-
Welding (if applicable): For flanges that require welded connections, skilled welders employ techniques such as TIG or MIG welding to create robust joints. Quality control at this stage is critical to avoid weaknesses that can lead to failure under pressure.
How Is the Assembly of Flanges Conducted?
The assembly stage involves bringing together various components to form the final flange product.
-
Alignment and Fitting: Flanges must be accurately aligned with gaskets and other fittings. This ensures a proper seal when installed.
-
Bolting: Depending on the design, flanges are bolted together. The use of quality fasteners is important to maintain the integrity of the connection under operational conditions.
What Finishing Techniques Are Commonly Used in Flange Production?
Finishing processes enhance the appearance and functionality of flanges.
-
Surface Treatment: Common techniques include shot blasting, sandblasting, and coating with protective materials to prevent corrosion. Buyers should inquire about the types of finishes used, especially for flanges intended for harsh environments.
-
Quality Inspection: Before the flanges leave the factory, they undergo rigorous quality inspections to ensure they meet all specified standards.
How Is Quality Assurance Implemented in Flange Manufacturing?
Quality assurance is a critical aspect of flange manufacturing, ensuring that products meet the required standards and specifications.
What International Standards Should Flange Suppliers Comply With?
International standards such as ISO 9001 are essential for ensuring quality in manufacturing processes. Suppliers should be certified in these standards to demonstrate their commitment to quality management systems.
-
ISO 9001 Certification: This certification focuses on maintaining consistent quality and improving customer satisfaction. Buyers should request proof of this certification from suppliers.
-
Industry-Specific Certifications: Depending on the application, flanges may need to comply with additional standards such as CE marking for European markets or API standards for oil and gas applications. These certifications indicate that the flanges are safe and suitable for their intended use.
What Are the Key Quality Control Checkpoints in Flange Manufacturing?
Quality control is integrated into various stages of the manufacturing process. Key checkpoints include:
-
Incoming Quality Control (IQC): This step involves inspecting raw materials upon arrival at the facility to ensure they meet specified standards.
-
In-Process Quality Control (IPQC): Throughout the manufacturing process, inspections are performed to catch any defects early. This may include dimensional checks and visual inspections of welds.
-
Final Quality Control (FQC): Before shipping, flanges undergo final inspections, including pressure testing and dimensional verification, to ensure they meet all specifications.
What Common Testing Methods Are Used for Flanges?
Testing methods are crucial to verify the integrity and functionality of flanges. Common methods include:
-
Hydrostatic Testing: This method involves filling the flange with water and pressurizing it to check for leaks. It is particularly important for flanges used in high-pressure applications.
-
Ultrasonic Testing: This non-destructive testing method helps identify internal flaws within the material, ensuring that the flange is free from defects that could compromise its performance.
-
Visual Inspection: Simple yet effective, visual inspections can identify surface defects or irregularities.
How Can B2B Buyers Verify Supplier Quality Control?
For international B2B buyers, particularly from regions like Africa, South America, the Middle East, and Europe, verifying a supplier’s quality control processes is essential.
-
Supplier Audits: Conducting on-site audits of suppliers allows buyers to assess their manufacturing processes and quality control measures firsthand. This also helps establish trust and transparency.
-
Quality Control Reports: Requesting regular quality control reports from suppliers can provide insights into their performance over time. These reports should detail inspection results and any corrective actions taken.
-
Third-Party Inspections: Engaging third-party inspection services can offer an impartial assessment of the supplier’s products. This is particularly valuable for buyers unfamiliar with local standards and practices.
What Are the QC/Certifications Nuances for International B2B Buyers?
International buyers must navigate various certification requirements, which can differ significantly from one region to another. For example, flanges exported to Europe must often bear the CE mark, while those for the Middle East may need to comply with GSO standards.
-
Understanding Regional Standards: It is crucial for buyers to familiarize themselves with the specific standards applicable to their market. This ensures compliance and mitigates risks associated with non-conformity.
-
Documentation: Buyers should request and verify all relevant certifications and test reports before finalizing orders. This documentation serves as proof of compliance with the necessary quality standards.
-
Cultural and Regulatory Considerations: Different regions may have unique cultural and regulatory considerations that affect quality control practices. Buyers should consider these factors when engaging suppliers to ensure smooth transactions.
By understanding the manufacturing processes and quality assurance measures that flange suppliers implement, international B2B buyers can make informed decisions and secure high-quality products that meet their specific needs.
Practical Sourcing Guide: A Step-by-Step Checklist for ‘flange supplier’
In the intricate world of B2B sourcing, particularly for flanges, having a structured approach can significantly enhance your procurement process. This checklist serves as a practical guide for international buyers from regions like Africa, South America, the Middle East, and Europe to ensure they select the right flange supplier.
Step 1: Define Your Technical Specifications
Before initiating the sourcing process, clearly outline your technical requirements for flanges. Consider factors such as size, material (e.g., stainless steel, carbon steel), pressure rating, and specific standards (e.g., ASME, DIN). Having precise specifications helps in narrowing down suppliers who can meet your unique needs.
- Identify application requirements: Determine the operating conditions where the flanges will be used, including temperature and pressure.
- Consider industry standards: Different industries may have specific regulations or standards that your flanges must adhere to.
Step 2: Conduct Market Research
Research potential flange suppliers globally, focusing on those with a robust reputation. Explore industry-specific directories, trade shows, and online platforms to gather a list of viable suppliers.
- Utilize industry forums: Engage with peers or industry forums to gather insights on reputable suppliers.
- Assess regional capabilities: Look for suppliers that have experience serving your geographical area, as they may better understand local regulations and market conditions.
Step 3: Evaluate Supplier Certifications
It’s essential to verify that your potential suppliers possess the necessary certifications and quality assurance standards. This step ensures that the products you receive will meet industry requirements.
- Check for ISO certifications: Suppliers with ISO 9001 certification demonstrate their commitment to quality management systems.
- Review product certifications: Look for specific certifications relevant to the materials or applications (e.g., ASME, PED).
Step 4: Request Samples and Specifications
Before finalizing any supplier, request samples of their flanges. This will allow you to evaluate the quality and suitability of the products for your applications.
- Assess material quality: Examine the samples for material integrity, finish, and adherence to your specifications.
- Test for compatibility: Ensure that the flange samples fit well with existing systems or components you intend to use them with.
Step 5: Negotiate Terms and Pricing
Engage in negotiations to establish favorable terms and pricing. Be transparent about your budget and seek competitive pricing without compromising quality.
- Consider bulk purchase discounts: Suppliers may offer significant price reductions for larger orders.
- Review payment terms: Understand the payment structures, including deposits and credit options, to manage cash flow effectively.
Step 6: Evaluate Logistics and Delivery Capabilities
Assess the supplier’s ability to deliver products within your required timelines. Logistics can significantly impact your project schedules.
- Inquire about shipping methods: Understand how the supplier handles international shipping and customs clearance, especially for buyers in Africa and South America.
- Confirm lead times: Get clarity on production lead times and any potential delays that may affect your operations.
Step 7: Establish a Long-Term Relationship
Once you have successfully sourced your flanges, aim to build a long-term partnership with your supplier. This can lead to better pricing, priority service, and access to new products.
- Maintain regular communication: Keep the lines of communication open to discuss any future needs or concerns.
- Solicit feedback: Provide feedback on product quality and service to help improve the relationship.
Following this checklist will guide you through a systematic approach to sourcing flange suppliers, ensuring you make informed decisions that meet your operational needs.
Comprehensive Cost and Pricing Analysis for flange supplier Sourcing
What Are the Key Cost Components in Flange Supplier Pricing?
When evaluating the cost structure for flange suppliers, several key components come into play. Understanding these elements can help international B2B buyers make informed decisions.
-
Materials: The type of material used significantly impacts the cost. Common materials for flanges include carbon steel, stainless steel, and alloy steels. Prices can vary based on the market trends of these raw materials.
-
Labor: Labor costs vary by region and are influenced by local wage standards and the complexity of the manufacturing process. High-skilled labor may be necessary for producing specialized flanges, which can increase costs.
-
Manufacturing Overhead: This includes costs associated with factory maintenance, utilities, and administrative expenses. Efficient manufacturing processes can help lower overhead costs, making the supplier more competitive.
-
Tooling: Initial tooling costs can be substantial, especially for custom flanges. Buyers should consider whether the supplier has the necessary tooling for their specific requirements, as this can influence the overall pricing.
-
Quality Control (QC): Implementing rigorous QC processes ensures the integrity of the flanges. Suppliers with robust QC measures might charge higher prices, but this can lead to cost savings in the long run by reducing failures and replacements.
-
Logistics: Shipping and handling can add significant costs, particularly for international orders. Factors such as distance, shipping method, and the nature of the goods (e.g., weight, fragility) will influence logistics costs.
-
Margin: Suppliers typically add a profit margin to their costs. Understanding the supplier’s pricing strategy can provide insight into potential negotiation opportunities.
How Do Pricing Influencers Affect Flange Sourcing?
Several factors can influence the pricing of flanges, which are crucial for B2B buyers to consider.
-
Volume and Minimum Order Quantity (MOQ): Larger orders often come with discounts. Buyers should evaluate their needs and consider negotiating MOQs to achieve better pricing.
-
Specifications and Customization: Custom flanges tailored to specific applications may lead to higher costs. Buyers should balance the need for customization against potential price increases.
-
Materials: The choice of materials can significantly affect pricing. Buyers should assess the performance needs versus material costs to find a suitable balance.
-
Quality and Certifications: Flanges that meet industry standards and certifications (e.g., ISO, ASME) may come at a premium. However, these certifications often ensure reliability and longevity, which can justify the investment.
-
Supplier Factors: Supplier reputation, reliability, and history of performance can also impact pricing. A reputable supplier may charge more but often provides better service and product quality.
-
Incoterms: Understanding the Incoterms (International Commercial Terms) is vital for managing shipping and responsibility for costs. Terms like FOB (Free on Board) or CIF (Cost, Insurance, and Freight) can influence overall pricing.
What Are the Best Buyer Tips for Flange Sourcing?
For international B2B buyers, especially those from regions like Africa, South America, the Middle East, and Europe, several strategies can enhance cost-efficiency:
-
Negotiate Effectively: Approach negotiations with a clear understanding of your needs and the supplier’s costs. Leverage volume purchases and long-term partnerships to negotiate better terms.
-
Focus on Total Cost of Ownership (TCO): Evaluate the overall costs associated with the flanges, including installation, maintenance, and potential downtime due to failures. A higher upfront cost may lead to lower TCO if the quality is superior.
-
Understand Pricing Nuances for International Buyers: Fluctuations in currency exchange rates, tariffs, and local taxes can affect the final cost of flanges. Buyers should factor these elements into their budgeting and pricing assessments.
-
Research Suppliers Thoroughly: Conduct due diligence on potential suppliers. Check for reviews, certifications, and past project success to ensure they can meet your needs without compromising quality.
Disclaimer on Indicative Prices
Prices for flanges can fluctuate based on market conditions, material availability, and supplier pricing strategies. It is advisable for buyers to obtain quotes from multiple suppliers and consider the factors outlined above to achieve the best possible deal.
Alternatives Analysis: Comparing flange supplier With Other Solutions
When considering solutions for piping and mechanical connections, B2B buyers must evaluate various options that can fulfill their operational requirements. While flange suppliers offer a reliable and standardized approach, alternative solutions may provide different benefits depending on the specific application. Understanding these alternatives can help buyers make informed decisions that align with their business goals.
Comparison Aspect | Flange Supplier | Alternative 1 Name: Welded Connections | Alternative 2 Name: Mechanical Couplings |
---|---|---|---|
Performance | High-pressure tolerance; reliable sealing; various types for specific applications | Excellent for permanent connections; very strong | Good for quick assembly and disassembly; moderate pressure tolerance |
Cost | Moderate initial investment; long-term reliability can reduce overall costs | Generally lower initial cost; may require higher labor costs | Higher upfront costs but can save on labor; reusable |
Ease of Implementation | Requires precise alignment; installation may need skilled labor | Labor-intensive; requires skilled welders | Easy to install; often requires no special tools |
Maintenance | Requires periodic inspection; gaskets may need replacement | Difficult to inspect without cutting; permanent | Easy to disassemble for inspection; reusable components |
Best Use Case | Ideal for high-pressure systems and industries with strict standards | Best for permanent installations where flexibility is not required | Suitable for temporary setups or applications needing frequent maintenance |
What are the Pros and Cons of Welded Connections Compared to Flange Suppliers?
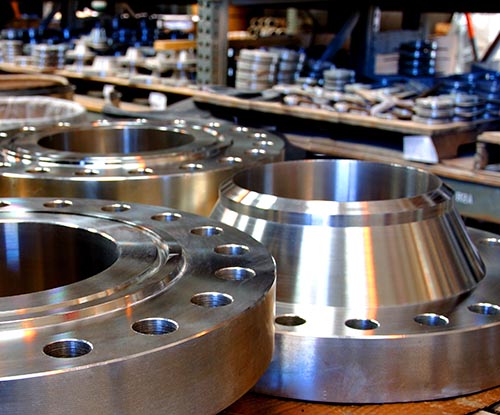
A stock image related to flange supplier.
Welded connections are an alternative that offers robust performance, especially in environments where a permanent solution is necessary. These connections provide excellent sealing and can handle high pressures. However, the main drawback is the requirement for skilled labor to execute the welding process effectively. Additionally, once installed, welded joints can be challenging to inspect and may necessitate cutting for maintenance, which can increase downtime and costs.
How Do Mechanical Couplings Compare to Flange Suppliers?
Mechanical couplings present another viable alternative for B2B buyers. These fittings allow for quick assembly and disassembly, making them a practical choice for applications that require frequent maintenance or adjustments. They do not necessitate welding, which can streamline the installation process. However, mechanical couplings may not provide the same high-pressure capabilities as flanges, making them less suitable for certain industrial applications. Their cost can also be higher initially, but they offer the advantage of reusability, which can be economically beneficial over time.
Conclusion: How Can B2B Buyers Choose the Right Solution?
Choosing the right solution among flange suppliers, welded connections, and mechanical couplings requires careful consideration of several factors, including the specific application, pressure requirements, and maintenance needs. B2B buyers should assess their operational priorities—whether they need a permanent solution or one that allows for flexibility and ease of maintenance. By weighing the performance, cost, and practicality of each option, buyers can select the best fit that aligns with their business objectives and operational efficiency.
Essential Technical Properties and Trade Terminology for flange supplier
What Are the Essential Technical Properties of Flanges for B2B Buyers?
When sourcing flanges for industrial applications, understanding the technical specifications is crucial. Here are key properties that B2B buyers should consider:
How Does Material Grade Impact Flange Performance?
Material grade is one of the most critical specifications for flanges. Common materials include carbon steel, stainless steel, and alloy steel, each offering different levels of corrosion resistance, strength, and temperature tolerance. For instance, A105 is widely used for carbon steel flanges, while 316L is preferred for stainless steel due to its superior corrosion resistance. Selecting the right material ensures the flange can withstand the specific environmental conditions it will face, thereby enhancing the longevity and reliability of the piping system.
Why Are Tolerances Important in Flange Manufacturing?
Tolerances refer to the acceptable limits of variation in a flange’s dimensions. They play a vital role in ensuring that flanges fit together correctly during installation. A tolerance of ±0.5 mm is standard for many flange types. Poor tolerances can lead to leaks or mechanical failures, affecting system performance and safety. Understanding tolerance specifications allows buyers to ensure compatibility with existing systems and avoid costly downtime.
What Role Does Pressure Rating Play in Flange Selection?
The pressure rating indicates the maximum allowable pressure a flange can handle. Flanges are categorized under various ratings, such as Class 150, Class 300, or Class 600, which correlate with the pressure and temperature capabilities of the materials used. Buyers must match the flange pressure rating with the operational requirements of their systems to prevent catastrophic failures or leaks.
How Does Flange Size Affect Application Suitability?
Flange size, which includes both the nominal diameter and the thickness, is crucial for ensuring that the flange fits the intended piping system. Sizes are typically specified in inches or millimeters, and choosing the correct size is essential for maintaining a secure and leak-proof connection. For international buyers, it’s important to be aware of the relevant sizing standards in their region, such as ANSI, DIN, or JIS, to ensure compatibility.
What Are Common Trade Terms in Flange Procurement?
Navigating the procurement process for flanges involves understanding specific trade terminologies. Here are some essential terms:
What Does OEM Mean in the Flange Industry?
OEM stands for Original Equipment Manufacturer. In the context of flanges, it refers to companies that manufacture flanges specifically for another company that sells them under its brand. Understanding OEM relationships can help buyers ensure they are sourcing high-quality products that meet industry standards.
Why Is MOQ Important When Ordering Flanges?
MOQ, or Minimum Order Quantity, is the smallest quantity of a product that a supplier is willing to sell. It is crucial for buyers to consider MOQ as it can impact inventory management and cash flow. For international buyers, meeting MOQ can also affect shipping costs and lead times.
How to Use RFQ for Efficient Flange Sourcing?
A Request for Quotation (RFQ) is a document used by buyers to solicit price quotes from suppliers. An RFQ typically includes specifications, quantities, and delivery requirements. For B2B buyers, submitting a well-defined RFQ can lead to more accurate quotes and better supplier responses, ultimately streamlining the procurement process.
What Are Incoterms and Their Relevance in Flange Trade?
Incoterms, or International Commercial Terms, are a set of rules that define the responsibilities of buyers and sellers in international transactions. Understanding Incoterms like FOB (Free On Board) or CIF (Cost, Insurance, and Freight) is essential for B2B buyers as they dictate shipping responsibilities, risk transfer, and cost implications, thereby influencing overall procurement strategy.
By familiarizing themselves with these technical properties and trade terminologies, international B2B buyers can make informed decisions that align with their operational needs and enhance supply chain efficiency.
Navigating Market Dynamics and Sourcing Trends in the flange supplier Sector
What Are the Current Market Dynamics and Key Trends in the Flange Supplier Sector?
The flange supplier sector is witnessing significant growth driven by various global factors, including increasing industrialization and infrastructural development across Africa, South America, the Middle East, and Europe. The demand for flanges is primarily fueled by their critical role in the oil and gas, water treatment, and chemical processing industries. Emerging technologies such as Industry 4.0 and the Internet of Things (IoT) are reshaping sourcing trends, with B2B buyers increasingly seeking suppliers who offer digital integration and real-time inventory management solutions.
Another trend is the rise of e-commerce platforms that facilitate international trade, making it easier for buyers to compare prices and quality from multiple suppliers. This shift is particularly relevant for buyers in regions like the UAE and Saudi Arabia, where rapid urbanization and economic diversification projects are underway. Additionally, the trend toward modular construction and prefabrication in the construction sector is increasing the demand for specific flange types, such as slip-on and weld neck flanges, which are preferred for their ease of installation and reliability.
In terms of market dynamics, international buyers must navigate fluctuating raw material prices and supply chain disruptions exacerbated by geopolitical tensions and the COVID-19 pandemic. As a result, establishing strong relationships with reliable suppliers and understanding local regulations and standards—such as ASME, DIN, and BS—are essential for successful procurement.
How Important Is Sustainability and Ethical Sourcing in the Flange Supplier Sector?
Sustainability and ethical sourcing are increasingly vital for B2B buyers in the flange supplier sector. The environmental impact of industrial operations is under scrutiny, prompting buyers to prioritize suppliers who demonstrate commitment to sustainable practices. This includes sourcing raw materials responsibly, reducing carbon footprints, and implementing energy-efficient manufacturing processes.
Buyers should look for suppliers who hold ‘green’ certifications, such as ISO 14001, which indicates a commitment to environmental management systems. Moreover, the use of sustainable materials, such as recycled metals or eco-friendly coatings, is becoming a key differentiator in supplier selection. As companies aim to align their operations with the United Nations Sustainable Development Goals (SDGs), those engaged in ethical sourcing are likely to build stronger reputations and customer loyalty.
For international B2B buyers, particularly from regions like Africa and South America, understanding the implications of sustainability can enhance their market competitiveness. It not only aligns with global trends but also opens opportunities for collaboration with other businesses that prioritize corporate social responsibility (CSR) in their supply chains.
What Is the Historical Context of the Flange Supplier Sector?
The flange supplier sector has evolved significantly over the past century, transitioning from basic mechanical components to sophisticated products tailored for specific industrial applications. Initially, flanges were primarily made from wrought iron and steel, designed to meet the basic requirements of piping systems. However, the industrial revolution and advancements in metallurgy led to the development of high-performance materials such as stainless steel, carbon steel, and various alloys, enabling flanges to withstand extreme pressures and temperatures.
In recent decades, globalization has further transformed the sector, with the emergence of international standards such as ASME, ANSI, and DIN, allowing for better interoperability and quality assurance across borders. This evolution has been crucial for B2B buyers, who must now navigate a complex landscape of standards and specifications to ensure their sourcing decisions align with both local regulations and global best practices. Understanding this historical context can provide valuable insights for today’s buyers, informing their strategies for selecting the right suppliers in a competitive market.
Frequently Asked Questions (FAQs) for B2B Buyers of flange supplier
-
How do I choose the right flange supplier for my international needs?
Choosing the right flange supplier involves assessing their experience in the specific flanges you require. Check their certifications, compliance with international standards (like ASME, DIN, or JIS), and the range of materials offered. It’s also crucial to evaluate their logistics capabilities, especially for international shipping, and their ability to provide timely delivery. Consider suppliers with a strong reputation in your region—particularly in Africa, South America, the Middle East, and Europe—to ensure they understand local regulations and market demands. -
What are the most common types of flanges used in B2B applications?
The most common types of flanges include Weld Neck, Slip-on, Socket Weld, and Threaded flanges. Each type serves different applications; for instance, Weld Neck flanges are ideal for high-pressure systems, while Slip-on flanges are commonly used for low-pressure applications. Understanding the specific requirements of your project—such as pressure, temperature, and material compatibility—will help you select the appropriate flange type. Always consult with your supplier for recommendations based on your project’s unique needs. -
How can I ensure the quality of flanges purchased from international suppliers?
To ensure quality, request certifications and quality assurance documentation from your supplier, such as ISO 9001 certification. Conducting factory visits or audits can provide firsthand insight into their manufacturing processes. Additionally, ask for samples or third-party testing reports to verify material integrity and performance under specified conditions. Engaging with suppliers who have a transparent quality control process will also help mitigate risks associated with international sourcing. -
What are the typical minimum order quantities (MOQs) for flange suppliers?
Minimum order quantities (MOQs) can vary significantly depending on the supplier and the type of flange. Many suppliers may set MOQs to optimize production and shipping costs, which can range from 10 to several hundred units. For specialized or customized flanges, MOQs may be higher. It’s advisable to discuss your needs directly with the supplier to negotiate suitable terms, particularly if you are a smaller buyer or require a trial order. -
What payment terms should I expect when sourcing flanges internationally?
Payment terms for international transactions can vary widely. Common practices include advance payment, letters of credit, or payment upon delivery. Many suppliers may require a deposit, particularly for customized orders. Always clarify the payment terms upfront and ensure they are documented in your purchase agreement. Consider using secure payment methods to protect your investment, especially when dealing with new suppliers or those from regions with less familiar trade practices. -
How can I communicate my customization needs to a flange supplier?
When communicating customization needs, provide detailed specifications including dimensions, material types, and any applicable standards. It’s beneficial to share drawings or models to ensure clarity. Establishing a direct line of communication with your supplier can facilitate this process—consider using email, video calls, or collaborative platforms. Be open to their suggestions, as they may have insights on manufacturing feasibility and cost-effectiveness that can enhance your design. -
What logistics considerations should I keep in mind when sourcing flanges internationally?
Logistics is a critical aspect of international sourcing. Consider shipping methods, lead times, and customs regulations for your specific regions, such as Africa, South America, the Middle East, and Europe. Work with suppliers who have reliable logistics partners and can provide tracking options. Additionally, assess the total landed cost, including shipping, tariffs, and handling fees, to avoid unexpected expenses upon delivery. -
How do I handle disputes or quality issues with an international flange supplier?
In the event of disputes or quality issues, start by reviewing your contract and any warranties provided. Document all communications and issues clearly, and approach the supplier with a detailed report of your concerns. Many suppliers have established procedures for handling complaints, so inquire about their process. If resolution is not achieved, consider involving a third-party mediator or legal advisor familiar with international trade agreements to facilitate a fair outcome.
Important Disclaimer & Terms of Use
⚠️ Important Disclaimer
The information provided in this guide, including content regarding manufacturers, technical specifications, and market analysis, is for informational and educational purposes only. It does not constitute professional procurement advice, financial advice, or legal advice.
While we have made every effort to ensure the accuracy and timeliness of the information, we are not responsible for any errors, omissions, or outdated information. Market conditions, company details, and technical standards are subject to change.
B2B buyers must conduct their own independent and thorough due diligence before making any purchasing decisions. This includes contacting suppliers directly, verifying certifications, requesting samples, and seeking professional consultation. The risk of relying on any information in this guide is borne solely by the reader.
Strategic Sourcing Conclusion and Outlook for flange supplier
In today’s competitive landscape, effective strategic sourcing for flanges is paramount for international B2B buyers, especially those operating in Africa, South America, the Middle East, and Europe. Understanding the diverse types of flanges—such as weld neck, slip-on, and socket weld—alongside their specific applications ensures that buyers can select the most suitable options for their projects. This knowledge not only enhances operational efficiency but also minimizes costs and risks associated with improper material choices.
Furthermore, establishing strong relationships with reliable flange suppliers enables buyers to leverage best practices, negotiate favorable terms, and secure high-quality materials that meet international standards. This strategic approach to sourcing is essential for maintaining competitiveness in industries that rely heavily on robust piping and connection systems.
As we look to the future, the demand for customized flange solutions will continue to grow, driven by advancements in technology and evolving industry needs. International B2B buyers are encouraged to actively seek partnerships with suppliers who demonstrate innovation and adaptability. By doing so, businesses can ensure they remain at the forefront of their industries, ready to tackle challenges and seize new opportunities. Embrace strategic sourcing today to drive success and sustainability in your operations.