Find the Best Rigging Supplier: A Complete Guide for 2025
Introduction: Navigating the Global Market for rigging supplier
In the ever-evolving landscape of global trade, sourcing rigging suppliers presents a unique set of challenges for B2B buyers, particularly those in Africa, South America, the Middle East, and Europe. The complexity of finding reliable suppliers who offer high-quality rigging equipment at competitive prices can be daunting. This guide aims to simplify the process, providing you with actionable insights into the various types of rigging materials, their applications, and effective supplier vetting strategies.
Navigating the global market requires a keen understanding of regional nuances and industry standards, which can significantly influence purchasing decisions. Throughout this guide, you will discover comprehensive information on the diverse range of rigging products, from synthetic slings to wire ropes, as well as their specific uses in industries such as construction, maritime, and logistics. We will also delve into essential factors for assessing supplier credibility, such as certifications, customer reviews, and delivery capabilities.
Moreover, understanding the cost structures associated with rigging supplies is crucial for making informed financial decisions. By equipping yourself with this knowledge, you will be empowered to negotiate better terms and ensure that your procurement process aligns with your operational needs. Ultimately, this guide serves as a vital resource for international B2B buyers, enabling them to confidently navigate the complexities of sourcing rigging suppliers in a competitive global market.
Understanding rigging supplier Types and Variations
Type Name | Key Distinguishing Features | Primary B2B Applications | Brief Pros & Cons for Buyers |
---|---|---|---|
Manufacturers | Produce rigging equipment in-house | Construction, shipping, entertainment | Pros: Custom solutions, quality control. Cons: Higher costs, longer lead times. |
Distributors | Supply a wide range of rigging products from various manufacturers | Retail, industrial supply, marine | Pros: Variety of options, faster delivery. Cons: May lack specialized knowledge. |
Rental Companies | Provide rigging equipment for temporary use | Events, construction, maintenance | Pros: Cost-effective for short-term needs. Cons: Limited availability, potential wear and tear. |
Specialty Suppliers | Focus on niche products or unique rigging solutions | Aerospace, oil & gas, heavy industry | Pros: Expertise in specific applications. Cons: Higher prices, limited product range. |
Online Marketplaces | E-commerce platforms offering various rigging products | Global trade, small businesses | Pros: Competitive pricing, convenience. Cons: Quality assurance issues, lack of direct support. |
What Are the Key Characteristics of Rigging Manufacturers?
Manufacturers of rigging equipment play a vital role in the supply chain by producing custom solutions tailored to specific needs. They typically maintain stringent quality control processes and can accommodate large orders. When considering a manufacturer, B2B buyers should evaluate their production capabilities, certifications, and lead times, as these factors can significantly impact project timelines.
How Do Distributors Enhance the Rigging Supply Chain?
Distributors act as intermediaries between manufacturers and end-users, offering a broad selection of rigging products. They are advantageous for businesses seeking quick access to various items without the need for large inventories. Buyers should assess the distributor’s inventory levels, delivery options, and customer service capabilities to ensure they can meet their ongoing needs effectively.
Why Should You Consider Rigging Rental Companies?
For businesses that require rigging equipment for short-term projects, rental companies present a cost-effective solution. They provide access to high-quality equipment without the burden of ownership costs. However, buyers must be mindful of the rental terms, equipment condition, and availability, as these factors can affect operational efficiency.
What Makes Specialty Suppliers Unique in the Rigging Market?
Specialty suppliers focus on specific industries or unique rigging solutions, such as aerospace or oil and gas. Their expertise allows them to provide tailored products that meet stringent industry standards. B2B buyers should consider the supplier’s reputation, technical knowledge, and ability to provide support for specialized applications, as these factors can influence the success of complex projects.
How Do Online Marketplaces Change the Rigging Purchasing Landscape?
Online marketplaces have revolutionized how businesses procure rigging equipment by offering competitive pricing and convenience. They provide access to a wide range of products from various suppliers, making it easier for buyers to compare options. However, B2B buyers must be cautious regarding product quality and supplier reliability, as these platforms can sometimes lack the necessary oversight.
Related Video: Variations In Construction Projects Explained
Key Industrial Applications of rigging supplier
Industry/Sector | Specific Application of rigging supplier | Value/Benefit for the Business | Key Sourcing Considerations for this Application |
---|---|---|---|
Construction | Heavy lifting for structural assembly | Increases efficiency and safety in lifting heavy materials | Compliance with local safety standards and certifications |
Shipping and Logistics | Container handling and securing | Enhances cargo safety and reduces risk of damage during transit | Durability and weather resistance of materials |
Oil and Gas | Lifting and moving equipment in drilling sites | Minimizes downtime and increases operational efficiency | Supplier’s experience with industry-specific applications |
Entertainment | Stage rigging for events and concerts | Ensures safety and reliability in complex setups | Proven track record and quality of rigging equipment |
Mining | Material handling and transport | Optimizes workflow and reduces manual labor costs | Local availability of parts and support services |
How is Rigging Used in the Construction Industry?
In the construction sector, rigging suppliers play a crucial role in heavy lifting operations, particularly during the assembly of large structures. This includes the use of cranes, hoists, and other lifting equipment to move steel beams, concrete panels, and other heavy materials into place. The benefits include improved efficiency, reduced manual labor, and enhanced safety on job sites. International buyers, especially from regions like Africa and South America, should prioritize suppliers who adhere to local safety regulations and possess the necessary certifications to ensure compliance and safety during operations.
What Role Does Rigging Play in Shipping and Logistics?
In the shipping and logistics industry, rigging suppliers are essential for handling and securing containers during loading and unloading processes. Proper rigging ensures that cargo is safely secured, minimizing the risk of damage during transit. This is particularly important in regions with high humidity or extreme weather conditions, such as the Middle East and parts of South America. Buyers should consider sourcing materials that are durable and weather-resistant, as well as suppliers who can provide robust support and training for their staff on best practices for cargo handling.
Why is Rigging Important in the Oil and Gas Sector?
Within the oil and gas industry, rigging suppliers facilitate the lifting and moving of heavy equipment at drilling sites. This application is critical as it helps to minimize downtime and enhances operational efficiency, allowing for quicker responses to extraction needs. Buyers should seek suppliers with extensive experience in this sector, as they will be familiar with the unique challenges and safety considerations involved in oil and gas operations, particularly in remote locations.
How is Rigging Used in the Entertainment Industry?
In the entertainment sector, rigging suppliers are vital for stage rigging in concerts and events. They provide the necessary equipment to safely suspend lighting, sound systems, and other technical gear overhead. The reliability and safety of rigging setups are paramount, as failures can lead to accidents and significant liability issues. B2B buyers from Europe and Australia should look for suppliers with a proven track record in the entertainment industry, ensuring that the rigging equipment meets industry standards for safety and performance.
What is the Application of Rigging in Mining Operations?
Rigging suppliers are also integral to the mining industry, where they assist in material handling and transportation. Rigging systems are employed to lift and move heavy mining equipment and materials, optimizing workflow and reducing labor costs. For international buyers, particularly in Africa and South America, sourcing from suppliers who can provide local support and readily available parts is crucial for minimizing downtime and ensuring seamless operations in remote mining locations.
Related Video: Basic Rigging Terms You Should Know
3 Common User Pain Points for ‘rigging supplier’ & Their Solutions
Scenario 1: Navigating Quality Assurance in Rigging Supplies
The Problem: B2B buyers often face the challenge of ensuring that the rigging supplies they purchase meet industry standards and safety regulations. This is particularly crucial in regions like Africa and South America, where regulatory frameworks may vary significantly. Buyers may receive products that look good on paper but fail to perform under real-world conditions, leading to safety risks and financial losses.
The Solution: To overcome this challenge, buyers should prioritize suppliers with a proven track record of quality and compliance. Start by conducting thorough research on potential suppliers, focusing on their certifications and past client testimonials. Engage in direct conversations with suppliers to understand their manufacturing processes and quality control measures. Additionally, consider requesting product samples or conducting site visits to verify the quality of the rigging materials firsthand. Collaborating with local industry associations can also provide insights into reliable suppliers who adhere to the necessary safety standards.
Scenario 2: Managing Lead Times and Delivery Reliability
The Problem: Timely delivery of rigging supplies is crucial for maintaining project schedules, yet many international B2B buyers struggle with long lead times and unreliable shipping from suppliers. This issue can be particularly acute for companies in the Middle East and Europe, where projects often operate on tight timelines and delays can lead to significant financial penalties.
The Solution: To mitigate risks associated with lead times, buyers should establish clear expectations with suppliers upfront regarding delivery timelines. Opt for suppliers that offer transparent tracking systems, allowing you to monitor the progress of your orders in real time. Additionally, consider negotiating for expedited shipping options, especially for critical projects. Building strong relationships with suppliers can also lead to better communication and flexibility, enabling them to prioritize your orders during peak times. Finally, diversifying your supplier base can help ensure that you have backup options if one supplier faces delays.
Scenario 3: Understanding Product Specifications and Compatibility
The Problem: Many buyers struggle with understanding the technical specifications of rigging supplies, leading to compatibility issues with existing equipment. This is especially prevalent in Europe and South America, where different standards and specifications might apply across various industries. Misunderstandings in this area can result in costly mistakes, such as purchasing the wrong type of rigging hardware that doesn’t fit with existing systems.
The Solution: To address this problem, buyers should invest time in educating themselves about the specific requirements and standards relevant to their industry. This includes understanding different rigging types, load capacities, and material strengths. Engaging with suppliers to clarify product specifications is crucial; don’t hesitate to ask for detailed technical documentation. Additionally, consider leveraging online tools or software that help match rigging supplies to your existing equipment. Finally, collaborating with engineers or rigging specialists can provide valuable insights, ensuring that you select the right products for your specific needs and avoid costly errors.
Strategic Material Selection Guide for rigging supplier
When selecting materials for rigging applications, international B2B buyers must consider various factors that influence performance, durability, and cost. Here, we analyze four common materials used in rigging, focusing on their properties, advantages and disadvantages, and specific considerations for buyers from Africa, South America, the Middle East, and Europe.
What Are the Key Properties of Steel in Rigging Applications?
Steel is one of the most widely used materials in rigging due to its high tensile strength and durability. It typically has a temperature rating of up to 400°F (204°C) and can withstand significant pressure without deforming. Steel’s corrosion resistance can be enhanced through galvanization or coating, making it suitable for various environments, including marine and industrial settings.
Pros & Cons: Steel is highly durable and can handle heavy loads, making it ideal for construction and heavy lifting applications. However, it is heavier than other materials, which can complicate transport and handling. The manufacturing complexity can also increase costs, especially for custom solutions.
Impact on Application: Steel is compatible with a wide range of media, including water, oil, and chemicals, which makes it versatile for different industries. However, its weight may limit its use in applications where weight is a critical factor.
Considerations for International Buyers: Buyers should ensure compliance with international standards such as ASTM A36 or DIN 17100. In regions like Europe and Australia, certifications for quality and safety are crucial, while in Africa and South America, local regulations may vary significantly.
How Does Synthetic Fiber Compare for Rigging Needs?
Synthetic fibers, such as nylon and polyester, are increasingly popular in rigging due to their lightweight nature and high strength-to-weight ratio. These materials can typically handle temperatures up to 180°F (82°C) and are resistant to UV degradation, making them suitable for outdoor applications.
Pros & Cons: The primary advantage of synthetic fibers is their lightweight and flexibility, which allows for easier handling and installation. However, they generally have lower tensile strength compared to steel, which may limit their use in heavy-duty applications. Additionally, synthetic fibers can be more susceptible to abrasion and chemical damage.
Impact on Application: Synthetic fibers are ideal for applications requiring flexibility, such as sailing and climbing. However, they may not be suitable for environments with extreme temperatures or aggressive chemicals.
Considerations for International Buyers: It’s essential to check for compliance with standards such as ISO 9001 for quality management. Buyers in the Middle East and Africa should also consider the availability of synthetic materials, as local supply chains may differ.
What Are the Benefits of Aluminum in Rigging Systems?
Aluminum is known for its lightweight and corrosion-resistant properties, making it a preferred choice for applications where weight savings are critical. It typically has a temperature rating of up to 300°F (149°C) and can handle moderate pressure.
Pros & Cons: The lightweight nature of aluminum allows for easier transport and installation, which can reduce labor costs. However, it has lower tensile strength compared to steel, which may limit its use in heavy-duty applications. The cost of aluminum can also be higher than steel, depending on market conditions.
Impact on Application: Aluminum is suitable for marine applications due to its corrosion resistance but may not be ideal for environments with high abrasive materials.
Considerations for International Buyers: Buyers should verify compliance with standards like ASTM B221 and ensure that the aluminum used is of high quality to prevent failure in critical applications. In Europe, adherence to EN standards is also essential.
How Does Composite Material Enhance Rigging Performance?
Composite materials, often a blend of fibers and resins, offer unique advantages in rigging applications. They can withstand a range of temperatures and are designed to be lightweight while providing high strength.
Pros & Cons: Composites are resistant to corrosion and chemical damage, making them suitable for harsh environments. However, they can be more expensive and may require specialized manufacturing processes, which can complicate sourcing.
Impact on Application: Composites are ideal for specialized applications, such as aerospace and high-performance sports, where weight and strength are critical. However, their cost may limit their use in more conventional applications.
Considerations for International Buyers: Buyers should ensure that composites meet relevant standards, such as ASTM D3039 for tensile properties. In regions like South America, where composite technology may be less developed, sourcing can be a challenge.
Summary Table of Material Selection for Rigging Suppliers
Material | Typical Use Case for rigging supplier | Key Advantage | Key Disadvantage/Limitation | Relative Cost (Low/Med/High) |
---|---|---|---|---|
Steel | Heavy lifting, construction | High tensile strength | Heavy and complex to manufacture | Medium |
Synthetic Fiber | Sailing, climbing | Lightweight and flexible | Lower tensile strength | Low |
Aluminum | Marine applications | Corrosion resistant and light | Lower strength than steel | Medium |
Composite | Aerospace, high-performance sports | Corrosion and chemical resistance | Higher cost and sourcing issues | High |
This strategic material selection guide provides a comprehensive overview for B2B buyers in diverse regions, helping them make informed decisions based on performance, cost, and compliance requirements.
In-depth Look: Manufacturing Processes and Quality Assurance for rigging supplier
What Are the Key Stages in the Manufacturing Process of Rigging Equipment?
Manufacturing rigging equipment involves several critical stages, each crucial for ensuring the final product meets the required specifications and quality standards. Understanding these processes will help B2B buyers select suppliers that align with their quality expectations.
-
Material Preparation: The manufacturing process begins with selecting high-quality raw materials, such as steel, synthetic fibers, or aluminum. Suppliers must ensure that these materials comply with international standards to guarantee durability and safety. B2B buyers should inquire about the suppliers’ sourcing practices and whether they use materials with certifications like ASTM or ISO.
-
Forming: This stage involves shaping the raw materials into the desired forms. Techniques such as forging, casting, and extrusion are commonly employed. Each method has its advantages; for instance, forging typically results in a stronger product. Buyers should consider the forming techniques used by suppliers to ensure they align with their performance requirements.
-
Assembly: After forming, various components are assembled to create the final rigging product. This stage may involve welding, bolting, or the use of adhesives. It is essential for suppliers to have skilled labor and precise machinery to ensure the integrity of the assembly process. Buyers should assess the supplier’s capabilities in assembly and inquire about their workforce training and experience.
-
Finishing: The final stage involves applying protective coatings, such as galvanization or powder coating, to enhance durability and resistance to corrosion. The finishing process is critical for ensuring the longevity of rigging equipment, especially in harsh environments. B2B buyers should request information on the finishing techniques employed by suppliers and any associated certifications.
How Is Quality Assurance Integrated into Rigging Manufacturing?
Quality assurance (QA) is a fundamental aspect of the manufacturing process for rigging suppliers. A robust QA program ensures that products not only meet but exceed industry standards. Here are the key components of QA in rigging manufacturing:
-
International and Industry-Specific Standards: Suppliers should adhere to international quality standards, such as ISO 9001, which outlines the requirements for a quality management system. Additionally, industry-specific standards like CE marking for European markets and API standards for oil and gas applications are essential. B2B buyers should confirm that their suppliers are certified and regularly audited for compliance with these standards.
-
Quality Control Checkpoints: Effective quality control (QC) involves several checkpoints throughout the manufacturing process:
– Incoming Quality Control (IQC): This involves inspecting raw materials upon arrival to ensure they meet specifications.
– In-Process Quality Control (IPQC): Inspections during the manufacturing process help identify defects early, reducing waste and ensuring consistency.
– Final Quality Control (FQC): The final product is rigorously tested to confirm it meets all specifications before shipping. -
Common Testing Methods for Rigging Products: Suppliers utilize various testing methods to validate product safety and performance. Common methods include tensile testing, fatigue testing, and load testing. B2B buyers should inquire about the specific tests conducted and request documentation to verify results.
What Steps Can B2B Buyers Take to Verify Supplier Quality Control?
For international B2B buyers, particularly from Africa, South America, the Middle East, and Europe, verifying a supplier’s quality control practices is crucial. Here are some actionable steps:
-
Conduct Supplier Audits: Regular audits help assess the supplier’s compliance with quality standards and their manufacturing processes. Buyers can perform these audits in person or hire third-party firms to conduct them on their behalf.
-
Request Quality Assurance Documentation: Suppliers should provide detailed quality assurance documentation, including certificates of compliance, test reports, and inspection records. Buyers should review these documents to ensure they meet required standards.
-
Engage Third-Party Inspection Services: Utilizing third-party inspection services can provide an unbiased assessment of the supplier’s quality control practices. This is particularly important for buyers who may lack the resources for in-house inspections.
What Are the Nuances of Quality Control for International B2B Buyers?
International buyers must navigate various challenges when assessing quality control in rigging suppliers:
-
Understanding Regional Standards: Different regions may have varying quality standards and regulations. For example, products sold in Europe must comply with CE marking requirements, while those in North America may need to meet OSHA regulations. Buyers should familiarize themselves with these regional standards to ensure compliance.
-
Cultural Differences in Quality Expectations: Quality perceptions can vary significantly across regions. Buyers from Africa may prioritize cost-effectiveness, while European buyers may focus on premium quality. Understanding these cultural nuances can aid in negotiations and supplier selection.
-
Supply Chain Transparency: In international trade, transparency is critical. Buyers should seek suppliers who provide clear visibility into their supply chain processes, including sourcing, manufacturing, and logistics. This transparency helps build trust and ensures that quality expectations are met.
Conclusion: Ensuring Quality in Rigging Supply
For B2B buyers in diverse regions like Africa, South America, the Middle East, and Europe, understanding the manufacturing processes and quality assurance practices of rigging suppliers is vital. By focusing on material preparation, forming, assembly, and finishing, buyers can better evaluate potential suppliers. Furthermore, implementing stringent quality control measures and actively verifying supplier practices can lead to successful long-term partnerships and high-quality rigging products.
Practical Sourcing Guide: A Step-by-Step Checklist for ‘rigging supplier’
In the competitive landscape of international B2B procurement, especially for critical components like rigging supplies, having a clear and actionable sourcing guide is essential. This checklist aims to streamline the process, helping buyers from Africa, South America, the Middle East, and Europe make informed decisions when selecting a rigging supplier.
Step 1: Define Your Technical Specifications
Before reaching out to suppliers, clarify your technical requirements. This includes understanding the specific rigging materials, load capacities, and environmental conditions the equipment will face. A well-defined specification not only helps in narrowing down potential suppliers but also ensures that you receive accurate quotes and appropriate products tailored to your needs.
Step 2: Conduct Market Research
Invest time in researching the market landscape. Identify potential suppliers in your target regions and evaluate their market presence and reputation. Look for reviews, testimonials, and case studies to gauge their reliability. This step is crucial as it provides insights into which suppliers are most respected and trusted within the industry.
Step 3: Verify Supplier Certifications
Ensure that the suppliers you consider are certified and comply with international quality standards. Certifications such as ISO 9001 or specific industry-related accreditations demonstrate a commitment to quality and safety. This verification not only protects your investment but also mitigates risks associated with substandard products.
Step 4: Request and Compare Quotes
Once you have a list of potential suppliers, request detailed quotations. Compare these quotes not only based on price but also on terms of service, delivery timelines, and payment options. A comprehensive comparison helps in identifying the best overall value, not just the lowest price, which can sometimes lead to hidden costs.
Step 5: Evaluate Potential Suppliers
Before committing, it’s crucial to vet suppliers thoroughly. Request company profiles, case studies, and references from buyers in a similar industry or region. Focus on their experience with projects similar to yours, as this can indicate their capability to meet your specific needs effectively.
Step 6: Assess Customer Service and Support
Consider the level of customer service and support offered by potential suppliers. Prompt and effective communication is vital, especially when addressing urgent needs or issues. Evaluate their responsiveness during the initial contact phase; a supplier that prioritizes customer service is likely to be more reliable in the long term.
Step 7: Finalize the Contract and Terms
Once you’ve selected a supplier, ensure that all terms are clearly documented in a contract. This should include delivery schedules, payment terms, warranties, and any other relevant details. A well-structured contract protects both parties and sets clear expectations, minimizing the risk of disputes later on.
By following this step-by-step checklist, B2B buyers can confidently navigate the sourcing process for rigging supplies, ensuring they choose a supplier that meets their technical, financial, and service-related requirements.
Comprehensive Cost and Pricing Analysis for rigging supplier Sourcing
What Are the Key Cost Components for Rigging Supplier Sourcing?
When evaluating rigging suppliers, understanding the comprehensive cost structure is crucial for making informed purchasing decisions. The primary cost components that affect the overall pricing include:
-
Materials: The choice of materials significantly impacts cost. High-strength steel, synthetic fibers, and specialized coatings can vary widely in price. Buyers should assess material specifications against project requirements to avoid unnecessary expenses.
-
Labor: Labor costs encompass skilled workers involved in manufacturing and assembly. Regions with higher labor costs, such as Europe, may have a different pricing structure compared to countries in Africa or South America, where labor might be more affordable.
-
Manufacturing Overhead: This includes all indirect costs associated with production, such as utilities, rent, and equipment maintenance. Understanding these costs can help buyers gauge the supplier’s efficiency and pricing strategy.
-
Tooling: Custom tooling for specific rigging solutions can add to initial costs. Buyers should consider whether the tooling will be amortized over a large production run to reduce per-unit costs.
-
Quality Control (QC): Rigging products often require stringent quality checks. Suppliers with robust QC processes may charge more, but this can lead to higher reliability and safety standards, which are critical in industries like construction and shipping.
-
Logistics: Transportation and handling costs vary based on the supplier’s location and the buyer’s destination. Incoterms also play a crucial role in determining who bears these costs.
-
Margin: Supplier profit margins can fluctuate based on their market positioning, brand reputation, and competitive landscape. A thorough analysis of multiple suppliers can provide insights into reasonable margins within the industry.
How Do Price Influencers Impact Rigging Supplier Costs?
Several factors influence the pricing strategies of rigging suppliers, including:
-
Volume and Minimum Order Quantity (MOQ): Bulk orders often attract discounts. Understanding the MOQ can help buyers negotiate better terms or combine orders with other projects to meet these thresholds.
-
Specifications and Customization: Custom solutions tailored to specific project needs can lead to higher costs. Buyers should clearly define their requirements to avoid overspending on unnecessary features.
-
Materials and Quality Certifications: High-quality materials and certifications (such as ISO or CE) can justify premium pricing. Buyers should assess whether these certifications are necessary for their applications.
-
Supplier Factors: The supplier’s reputation, experience, and location can influence pricing. Established suppliers may charge more due to their proven track record, while new entrants might offer lower prices to gain market share.
-
Incoterms: Different Incoterms (e.g., FOB, CIF) dictate the responsibilities of buyers and sellers in shipping. Understanding these can help buyers accurately calculate total costs.
What Buyer Tips Can Enhance Cost-Efficiency in Rigging Supplier Sourcing?
To maximize cost-efficiency when sourcing rigging suppliers, consider the following tips:
-
Negotiate Terms: Engage in discussions about pricing, payment terms, and delivery schedules. Suppliers may be willing to adjust terms based on the potential for a long-term relationship.
-
Evaluate Total Cost of Ownership (TCO): Look beyond the initial purchase price. Consider maintenance, operational costs, and the longevity of rigging products. A cheaper upfront cost may lead to higher TCO if the product fails prematurely.
-
Understand Pricing Nuances for International Transactions: Buyers from regions like Africa or South America should be aware of potential tariffs, exchange rate fluctuations, and shipping costs that may affect the final price.
-
Research and Compare Suppliers: Don’t settle for the first supplier. Obtain quotes from multiple sources, and assess their offerings, quality, and service. This can provide leverage in negotiations.
-
Stay Informed About Market Trends: Keep abreast of industry trends and economic factors that may influence pricing. Awareness of market dynamics can empower buyers to make strategic purchasing decisions.
Disclaimer on Indicative Prices
The prices associated with rigging supplies can vary significantly based on the factors discussed. It is essential for buyers to conduct thorough research and obtain detailed quotes from suppliers to ensure accurate budgeting and cost planning.
Alternatives Analysis: Comparing rigging supplier With Other Solutions
Understanding the Importance of Evaluating Alternatives for Rigging Solutions
When considering the procurement of rigging supplies, international B2B buyers should not only evaluate the rigging supplier but also explore alternative solutions that may better suit their operational needs. Understanding the performance, cost, implementation ease, maintenance requirements, and best use cases of each option is crucial for making informed decisions that align with business objectives and budget constraints. This analysis will compare rigging suppliers with two viable alternatives: synthetic slings and modular lifting systems.
Comparison Aspect | Rigging Supplier | Synthetic Slings | Modular Lifting Systems |
---|---|---|---|
Performance | High tensile strength; diverse applications | Lightweight; high strength-to-weight ratio | Versatile; customizable for various loads |
Cost | Moderate to high; includes shipping and handling | Generally lower; minimal shipping costs | Higher initial investment; cost-effective over time |
Ease of Implementation | Requires trained personnel for setup | Simple to use; minimal training needed | Requires specialized training for assembly |
Maintenance | Regular inspection required | Minimal maintenance; periodic checks recommended | Moderate; depends on system complexity |
Best Use Case | Heavy industrial applications, lifting of complex loads | General lifting tasks, where weight-saving is crucial | Large-scale projects requiring adaptability and precision |
What Are the Advantages and Disadvantages of Synthetic Slings?
Synthetic slings are an alternative that appeals to many international buyers due to their lightweight and high strength-to-weight ratio. They are particularly advantageous for lifting operations where weight savings are critical, such as in construction and logistics. However, while they offer ease of use and lower costs, their performance may not match that of traditional rigging solutions in extreme environments. Buyers should consider the specific lifting conditions and potential wear factors when opting for synthetic slings.
How Do Modular Lifting Systems Compare to Traditional Rigging Solutions?
Modular lifting systems present a flexible option for businesses with diverse lifting requirements. These systems can be tailored to meet specific load needs and can be easily reconfigured for different projects. While the initial investment might be higher compared to rigging suppliers, modular systems can provide long-term savings due to their reusability and adaptability. However, they do require specialized training for assembly and operation, which can be a barrier for some companies. Buyers should evaluate their workforce’s capabilities and project variability when considering this option.
Conclusion: How Can B2B Buyers Choose the Right Rigging Solution?
Choosing the right rigging solution involves assessing the specific operational needs, budget constraints, and workforce capabilities. While rigging suppliers offer reliable products for heavy-duty applications, alternatives like synthetic slings and modular lifting systems can provide unique benefits in terms of cost efficiency and flexibility. By carefully analyzing the performance, ease of implementation, and maintenance requirements of each option, B2B buyers from Africa, South America, the Middle East, and Europe can make informed decisions that enhance their operational efficiency and safety.
Essential Technical Properties and Trade Terminology for rigging supplier
When selecting a rigging supplier, understanding the essential technical properties and trade terminology is crucial for making informed decisions. Below are key specifications and commonly used terms that B2B buyers should familiarize themselves with to streamline their procurement process.
What Are the Critical Technical Properties for Rigging Supplies?
1. Material Grade: Why Does It Matter?
The material grade indicates the strength and durability of rigging products, which can include steel, synthetic fibers, or other composites. Higher grades typically offer better performance under load and resist corrosion. For buyers in regions like Africa and the Middle East, where environmental factors can be harsh, selecting the right material grade can significantly impact the lifespan and safety of rigging equipment.
2. Load Capacity: How Much Can It Handle?
Load capacity refers to the maximum weight a rigging component can safely lift or support. It is essential to select products that meet or exceed your operational requirements to prevent accidents and equipment failure. For buyers in Europe and South America, understanding local regulations regarding load capacities can also influence procurement decisions and compliance.
3. Tolerance: What Is Its Importance?
Tolerance defines the acceptable limits of variation in dimensions of rigging components. High tolerance levels ensure better fitting and functionality, which is especially critical in applications requiring precision, such as construction or maritime operations. For B2B buyers, this translates to reduced downtime and maintenance costs.
4. Working Load Limit (WLL): What Should You Know?
The Working Load Limit is the maximum load that a rigging component can handle during normal operations. This specification is crucial for safety and operational efficiency. Buyers must ensure that the WLL aligns with their specific applications to avoid overloading and potential failures.
5. Safety Factor: Why Is It Essential?
The safety factor is a ratio that indicates how much stronger a rigging product is compared to its maximum load. A higher safety factor means greater reliability, making it a vital consideration for industries with high-risk environments. For international buyers, understanding the safety standards in their region can help in selecting the right products that ensure compliance and safety.
Which Trade Terms Should B2B Buyers Understand?
1. What Does OEM Mean in Rigging Supplies?
OEM stands for Original Equipment Manufacturer. In the rigging industry, this term refers to suppliers that produce parts or equipment that are sold under another company’s brand. Understanding OEM products can help buyers ensure they are sourcing quality materials that meet industry standards.
2. What Is MOQ and Why Is It Important?
MOQ, or Minimum Order Quantity, is the smallest quantity a supplier is willing to sell. This term is vital for budget-conscious buyers, particularly in regions like South America and Africa, where bulk purchasing may be necessary to reduce costs. Knowing the MOQ can help in planning inventory and cash flow.
3. How to Use RFQ in Your Procurement Process?
RFQ, or Request for Quotation, is a document sent to suppliers to obtain price quotes for specific quantities of goods or services. Utilizing RFQs can streamline the procurement process, allowing buyers to compare costs and negotiate better deals with rigging suppliers.
4. What Are Incoterms and Why Are They Relevant?
Incoterms, or International Commercial Terms, define the responsibilities of buyers and sellers in international transactions. They clarify who is responsible for shipping, insurance, and tariffs, which is particularly important for B2B buyers operating across different continents. Understanding Incoterms can prevent misunderstandings and financial disputes.
5. What Does Lead Time Mean in Procurement?
Lead time refers to the amount of time it takes from placing an order until it is received. For international buyers, especially in fast-paced markets, knowing the lead time is essential for project planning and maintaining operational continuity.
By familiarizing yourself with these technical properties and trade terms, you can make more informed decisions when selecting rigging suppliers, enhancing your procurement strategy and operational efficiency.
Navigating Market Dynamics and Sourcing Trends in the rigging supplier Sector
What are the Key Market Dynamics and Trends in the Rigging Supplier Sector?
The rigging supplier sector is experiencing significant shifts driven by technological advancements, globalization, and changing customer demands. One of the primary global drivers is the ongoing industrialization in emerging markets across Africa and South America. These regions are witnessing a surge in construction and infrastructure projects, creating a robust demand for reliable rigging equipment. In Europe and the Middle East, the focus is on upgrading existing infrastructure, thus leading to increased investment in high-quality rigging solutions.
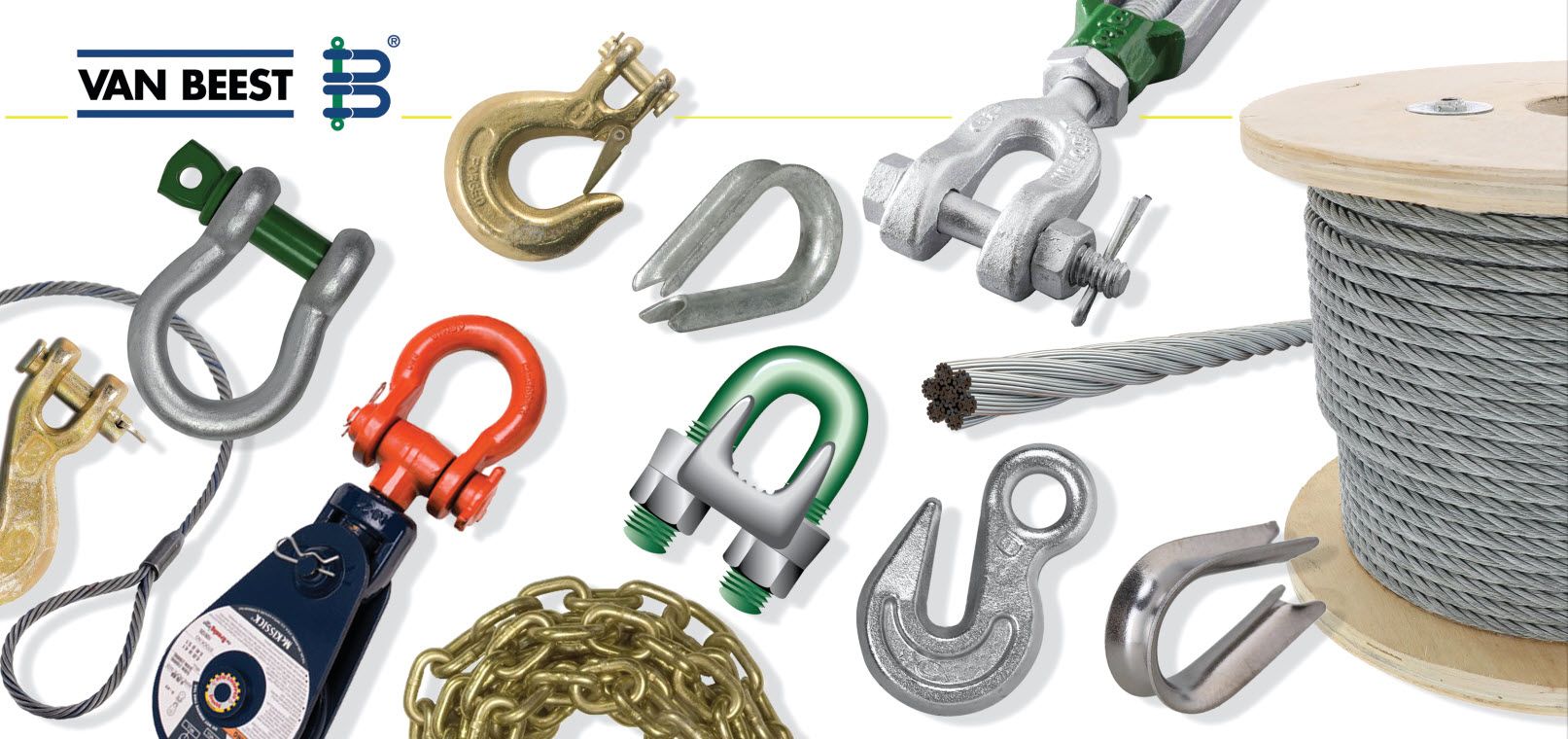
A stock image related to rigging supplier.
Current trends indicate a growing adoption of digital tools and platforms for sourcing rigging supplies. B2B buyers are increasingly utilizing e-commerce platforms and digital marketplaces to streamline procurement processes. This shift not only enhances efficiency but also broadens access to a wider array of suppliers and products, allowing buyers to compare options easily. Additionally, there is a rising emphasis on customization, with suppliers offering tailored solutions that meet specific industry requirements, particularly in sectors like construction, maritime, and entertainment.
Emerging technologies such as IoT and AI are also transforming how rigging suppliers operate. These innovations facilitate better inventory management and predictive maintenance, leading to reduced downtime and enhanced safety. For international B2B buyers, understanding these dynamics is crucial for making informed sourcing decisions and optimizing supply chain strategies.
How is Sustainability Impacting the Rigging Supplier Sector?
Sustainability has become a cornerstone of business strategy across industries, and the rigging supplier sector is no exception. The environmental impact of manufacturing processes and the importance of ethical sourcing are at the forefront of buyer considerations. B2B buyers are increasingly prioritizing suppliers who demonstrate a commitment to sustainable practices, such as reducing carbon footprints and minimizing waste.
Ethical supply chains are essential not only for compliance with regulations but also for meeting the expectations of socially-conscious consumers and businesses. Rigging suppliers are now focusing on transparent sourcing practices, ensuring that materials are obtained responsibly. Certifications such as ISO 14001 for environmental management and the use of sustainable materials like recycled steel are gaining traction. These initiatives not only enhance brand reputation but also appeal to buyers looking to align with environmentally responsible partners.
Moreover, the demand for ‘green’ rigging solutions is on the rise. Buyers are actively seeking suppliers that provide eco-friendly products, which can include rigging equipment made from sustainable materials or those designed for energy efficiency. By prioritizing sustainability, international B2B buyers can foster long-term partnerships that contribute to both their corporate social responsibility goals and their bottom line.
What is the Evolution of the Rigging Supplier Industry?
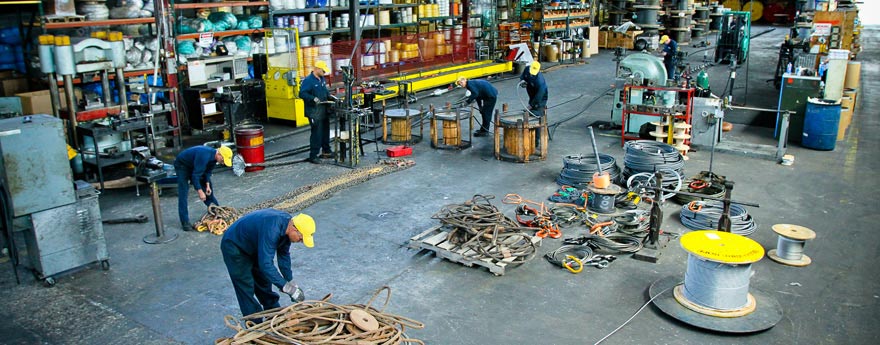
A stock image related to rigging supplier.
The rigging supplier industry has evolved significantly over the decades, transitioning from a focus on traditional materials and methods to embracing innovation and technology. Initially centered around basic lifting and hoisting equipment, the sector has expanded to include advanced solutions that leverage modern engineering and materials science.
The introduction of synthetic ropes and advanced rigging systems has revolutionized the industry, providing lighter, stronger, and more durable options for various applications. This evolution has been particularly beneficial for sectors such as construction and shipping, where efficiency and safety are paramount.
As the industry continues to grow, the integration of digital technologies and sustainability practices will likely shape its future trajectory. International B2B buyers must stay abreast of these developments to effectively navigate the evolving landscape and make strategic sourcing decisions that align with their operational goals.
Frequently Asked Questions (FAQs) for B2B Buyers of rigging supplier
-
How do I choose the right rigging supplier for my business needs?
Selecting the appropriate rigging supplier involves evaluating their experience, certifications, and product range. Look for suppliers that specialize in your industry, whether it’s construction, shipping, or manufacturing. Request client references to gauge their reliability and customer service. Additionally, assess their ability to provide customized solutions that meet your specific operational requirements. Make sure they have a robust quality assurance process to ensure safety and compliance with local regulations. -
What are the most important certifications for rigging suppliers?
Key certifications to look for in rigging suppliers include ISO 9001 for quality management systems, ASME (American Society of Mechanical Engineers) for lifting devices, and CE marking for compliance with European safety standards. In regions like Africa and South America, local certifications may also be relevant. Ensure that the supplier can provide documentation for these certifications, as they reflect the supplier’s commitment to quality and safety in their products. -
What are the typical minimum order quantities (MOQs) for rigging supplies?
Minimum order quantities can vary significantly among rigging suppliers, often ranging from 100 to 1,000 units depending on the product type and supplier policies. Smaller suppliers may offer lower MOQs to accommodate new businesses, while larger suppliers may require higher quantities to maintain cost-effectiveness. It’s advisable to communicate your needs upfront to negotiate MOQs that align with your purchasing strategy without overcommitting your resources. -
How can I ensure the quality of rigging products from international suppliers?
To ensure product quality, request samples before placing a large order, and conduct thorough inspections upon receipt. Additionally, inquire about the supplier’s quality assurance protocols, including testing methods and compliance with international safety standards. Establishing a clear communication channel for ongoing quality feedback is crucial, especially when dealing with suppliers from different countries, as it helps maintain product standards over time. -
What payment terms should I expect when dealing with rigging suppliers?
Payment terms can vary widely, but common options include upfront payment, partial payment upon order confirmation, and balance upon delivery. For international transactions, consider using secure payment methods such as letters of credit or escrow services to protect your investment. Always clarify payment terms in the contract to avoid misunderstandings, and be aware of any currency exchange implications that could affect overall costs. -
How do I handle logistics and shipping for rigging supplies from abroad?
When sourcing rigging supplies internationally, factor in logistics from the outset. Discuss shipping options with your supplier, including freight costs, insurance, and delivery timelines. Consider using a freight forwarder who can manage customs clearance and ensure compliance with import regulations in your country. It’s also wise to plan for potential delays and have contingency plans in place, especially for critical projects. -
What customization options are available for rigging products?
Many rigging suppliers offer customization options such as tailored lengths, specific materials, and unique fittings to meet your project requirements. When engaging with a supplier, clearly outline your customization needs and ask for their capabilities in this area. Understanding the lead times for customized products is also essential, as it can affect project timelines significantly. -
How can I vet a rigging supplier for reliability and reputation?
To vet a rigging supplier, conduct thorough research by checking online reviews, industry forums, and social media. Look for testimonials from previous clients and ask for references. Additionally, consider visiting their facility if possible or request a virtual tour to assess their operations. Engaging in preliminary discussions about your needs can also reveal their responsiveness and willingness to collaborate, which are crucial indicators of reliability.
Important Disclaimer & Terms of Use
⚠️ Important Disclaimer
The information provided in this guide, including content regarding manufacturers, technical specifications, and market analysis, is for informational and educational purposes only. It does not constitute professional procurement advice, financial advice, or legal advice.
While we have made every effort to ensure the accuracy and timeliness of the information, we are not responsible for any errors, omissions, or outdated information. Market conditions, company details, and technical standards are subject to change.
B2B buyers must conduct their own independent and thorough due diligence before making any purchasing decisions. This includes contacting suppliers directly, verifying certifications, requesting samples, and seeking professional consultation. The risk of relying on any information in this guide is borne solely by the reader.
Strategic Sourcing Conclusion and Outlook for rigging supplier
What Are the Key Takeaways for International B2B Buyers in Strategic Sourcing?
Strategic sourcing in the rigging supply sector is essential for ensuring operational efficiency and cost-effectiveness. International B2B buyers should prioritize suppliers who not only offer competitive pricing but also demonstrate reliability and compliance with international safety standards. Establishing strong relationships with suppliers across Africa, South America, the Middle East, and Europe can lead to enhanced negotiation power and more favorable terms, ultimately driving value for your business.
How Can Buyers Leverage Technology in Strategic Sourcing?
Investing in digital tools can streamline the sourcing process, making it easier to assess supplier capabilities and performance. Platforms that provide real-time data and analytics empower buyers to make informed decisions, ensuring they select the right partners that align with their strategic goals. Embracing technology also facilitates better communication and collaboration, crucial for navigating the complexities of international logistics.
What is the Future Outlook for Rigging Suppliers?
Looking ahead, the rigging supply landscape will likely evolve with increased emphasis on sustainability and innovation. Buyers should stay attuned to emerging trends, such as eco-friendly materials and automation in rigging solutions, which can provide a competitive edge. By continuously adapting sourcing strategies to these trends, international buyers can not only meet current demands but also anticipate future market shifts.
In conclusion, the importance of strategic sourcing for rigging suppliers cannot be overstated. By fostering strong supplier relationships, leveraging technology, and remaining agile to market changes, B2B buyers can secure a robust supply chain. Now is the time to take proactive steps in refining your sourcing strategy to capitalize on these opportunities for growth and success.