Find the Best Wire Mesh Manufacturer: Your Complete Guide (2025)
Introduction: Navigating the Global Market for wire mesh manufacturer
In today’s global marketplace, sourcing high-quality wire mesh manufacturers can be a daunting challenge for international B2B buyers, especially those operating in Africa, South America, the Middle East, and Europe. With diverse applications ranging from construction and agriculture to industrial filtration and security, the demand for reliable wire mesh products is ever-increasing. However, navigating the complexities of supplier selection, pricing structures, and product specifications requires a well-informed approach.
This comprehensive guide serves as a crucial resource for B2B buyers seeking to understand the multifaceted world of wire mesh manufacturing. It will cover the various types of wire mesh available, including welded, woven, and expanded mesh, along with their specific applications across different industries. Additionally, the guide will delve into the essential aspects of supplier vetting, offering practical tips on assessing quality, compliance with international standards, and establishing effective communication channels.
Furthermore, buyers will gain insights into cost considerations and procurement strategies that can enhance their purchasing decisions. By equipping B2B buyers with the knowledge and tools necessary to make informed choices, this guide aims to streamline the sourcing process, ensuring that businesses can confidently engage with wire mesh manufacturers and ultimately achieve their operational goals.
Understanding wire mesh manufacturer Types and Variations
Type Name | Key Distinguishing Features | Primary B2B Applications | Brief Pros & Cons for Buyers |
---|---|---|---|
Welded Wire Mesh | Rigid, uniform openings; high strength | Construction, fencing, industrial | Pros: Strong and durable; Cons: Less flexibility in design. |
Stainless Steel Wire Mesh | Corrosion-resistant; high tensile strength | Food processing, pharmaceuticals | Pros: Long-lasting; Cons: Higher initial cost. |
Hexagonal Wire Mesh | Diamond-shaped openings; flexible and lightweight | Poultry fencing, erosion control | Pros: Economical and lightweight; Cons: Less sturdy than welded mesh. |
Expanded Metal Mesh | Sheets with diamond-shaped openings; lightweight | Architectural applications, security | Pros: Excellent airflow; Cons: Limited load-bearing capacity. |
Plastic Wire Mesh | Made from polymers; resistant to chemicals | Agricultural applications, storage | Pros: Lightweight and corrosion-resistant; Cons: Lower strength compared to metal options. |
What Are the Characteristics of Welded Wire Mesh and Its Suitability for B2B Buyers?
Welded wire mesh is created by welding intersecting wires at each junction, resulting in a rigid and uniform structure. This type of mesh is highly suitable for applications requiring strength and stability, such as construction and fencing. B2B buyers should consider its durability and resistance to deformation, making it ideal for long-term installations. However, its lack of flexibility may limit design options, necessitating careful planning in application.
How Does Stainless Steel Wire Mesh Stand Out in Industrial Applications?
Stainless steel wire mesh is renowned for its corrosion resistance and high tensile strength, making it a preferred choice in industries like food processing and pharmaceuticals. It is particularly suitable for environments exposed to moisture or chemicals. B2B buyers should weigh the longevity and cleanliness it offers against the higher initial costs. Investing in stainless steel mesh can lead to reduced maintenance costs and improved product quality in the long run.
What Are the Advantages of Using Hexagonal Wire Mesh in Various Applications?
Hexagonal wire mesh, characterized by its diamond-shaped openings, is lightweight and flexible, making it an economical choice for poultry fencing and erosion control. This type of mesh is easy to install and offers good visibility, which is beneficial in agricultural settings. B2B buyers should consider its cost-effectiveness but be aware that it may not provide the same level of sturdiness as welded options, requiring additional support in high-stress applications.
In What Situations Should B2B Buyers Consider Expanded Metal Mesh?
Expanded metal mesh is produced by cutting and stretching metal sheets, resulting in a series of diamond-shaped openings. It is commonly used in architectural applications and security installations due to its excellent airflow properties. B2B buyers should appreciate its lightweight nature and aesthetic appeal but should also consider its limited load-bearing capacity, which may not suit all applications.
What Are the Key Benefits and Limitations of Plastic Wire Mesh for Buyers?
Plastic wire mesh is made from durable polymers, offering excellent resistance to chemicals and corrosion, making it ideal for agricultural applications and storage solutions. Its lightweight nature allows for easy handling and installation. B2B buyers should note that while plastic mesh is cost-effective and versatile, it generally has lower strength compared to metal options, which could limit its use in high-load situations.
Related Video: IDEAL CSR NC-controlled jig welder for wire mesh and grating
Key Industrial Applications of wire mesh manufacturer
Industry/Sector | Specific Application of Wire Mesh Manufacturer | Value/Benefit for the Business | Key Sourcing Considerations for this Application |
---|---|---|---|
Construction | Reinforcement in concrete structures | Enhances structural integrity and durability | Material grade, mesh size, and compliance with local building codes |
Agriculture | Crop protection and fencing | Protects crops from pests and livestock | Corrosion resistance, mesh size for specific crop types, and local regulations |
Mining and Minerals | Screening and filtration | Efficient separation of materials, reducing waste | Durability under harsh conditions, mesh opening size, and custom sizes |
Oil and Gas | Filter media for drilling operations | Improves efficiency and safety in extraction processes | Material compatibility with fluids, mesh thickness, and certification standards |
Automotive | Noise reduction in vehicle components | Enhances passenger comfort and compliance with regulations | Acoustic properties, size specifications, and weight constraints |
How is Wire Mesh Used in Construction, and What Problems Does It Solve?
In the construction industry, wire mesh is primarily used for reinforcing concrete structures. It enhances the structural integrity and durability of buildings, bridges, and roads, addressing common issues such as cracking and structural failure. Buyers in this sector should consider material grade and mesh size to ensure compliance with local building codes, especially in regions like Africa and South America where regulations may vary significantly.
What Role Does Wire Mesh Play in Agriculture?
Wire mesh serves as an essential tool in agriculture for crop protection and fencing. It protects crops from pests and livestock, ensuring higher yields and reduced losses. For international buyers, particularly in the Middle East and Africa, sourcing considerations include corrosion resistance and mesh size tailored to specific crops. Understanding local regulations regarding agricultural fencing is also crucial.
How Does Wire Mesh Benefit the Mining and Minerals Sector?
In the mining and minerals sector, wire mesh is used for screening and filtration processes. It efficiently separates materials, thereby reducing waste and enhancing productivity. Buyers should focus on the durability of the mesh under harsh conditions, the appropriate mesh opening size for their specific materials, and the availability of custom sizes to fit specialized equipment.
What Are the Applications of Wire Mesh in Oil and Gas?
Wire mesh is critical in the oil and gas industry, serving as filter media for drilling operations. It improves efficiency and safety during extraction processes by preventing contaminants from entering the system. When sourcing wire mesh for this application, buyers must consider material compatibility with various drilling fluids, the thickness of the mesh, and adherence to certification standards, especially in Europe where compliance is stringent.
How is Wire Mesh Utilized for Noise Reduction in Automotive Applications?
In the automotive industry, wire mesh is utilized for noise reduction in vehicle components. It enhances passenger comfort and helps manufacturers comply with noise regulations. Key sourcing considerations include the acoustic properties of the mesh, size specifications to fit various vehicle models, and weight constraints, particularly relevant for European manufacturers focused on efficiency and sustainability.
Related Video: Parametric Wire Mesh Fence in Revit
3 Common User Pain Points for ‘wire mesh manufacturer’ & Their Solutions
Scenario 1: Difficulty in Sourcing Quality Wire Mesh Products
The Problem: International B2B buyers, especially from regions like Africa and South America, often struggle to find reliable wire mesh manufacturers that provide high-quality products. The challenge is exacerbated by varying standards, inconsistent product specifications, and communication barriers due to different languages and business practices. This can lead to receiving subpar products that do not meet project specifications, causing delays and increased costs.
The Solution: To effectively source quality wire mesh, buyers should establish a thorough vetting process for manufacturers. Start by researching manufacturers with a strong reputation in the industry, focusing on customer reviews and case studies. Look for certifications such as ISO 9001, which indicate adherence to quality management systems. Engage in direct communication with potential suppliers to clarify specifications, production capabilities, and quality control measures. It’s also beneficial to request samples before placing large orders. Additionally, consider visiting the manufacturing facility if feasible, or utilizing third-party inspection services to ensure the quality of the products meets your expectations.
Scenario 2: Understanding Wire Mesh Specifications and Standards
The Problem: B2B buyers often encounter confusion regarding wire mesh specifications, including material types, mesh size, and coating options. This confusion can lead to incorrect orders, as buyers may not fully understand the technical details or standards relevant to their specific applications. For instance, a buyer may inadvertently order a mesh that is unsuitable for environmental conditions or load-bearing requirements, resulting in project setbacks and increased costs.
The Solution: To mitigate these issues, buyers should invest time in understanding the various specifications associated with wire mesh products. This involves familiarizing themselves with terms such as “gauge,” “mesh count,” and “material type” (e.g., stainless steel vs. galvanized steel). Consulting with industry experts or hiring a technical consultant can provide valuable insights into the best materials and specifications for specific applications. Manufacturers often provide detailed product catalogs and technical data sheets; leveraging these resources can clarify any doubts. Furthermore, engaging in discussions with sales representatives who have technical expertise can help buyers make informed decisions tailored to their project needs.
Scenario 3: Navigating Payment and Shipping Logistics for International Orders
The Problem: International buyers face significant challenges with payment methods and shipping logistics when dealing with wire mesh manufacturers. Issues such as high shipping costs, long lead times, and complex customs regulations can complicate the procurement process. Additionally, buyers may encounter difficulties in understanding payment methods accepted by manufacturers, leading to delays in order processing.
The Solution: To streamline the procurement process, buyers should clearly communicate with manufacturers regarding accepted payment methods, including ACH transfers and wire payments. Establishing a transparent agreement on payment terms upfront can prevent misunderstandings. For shipping, it’s advisable to work with manufacturers who have experience in international logistics and can provide reliable shipping options. Consider utilizing freight forwarders who specialize in your region to navigate customs regulations efficiently. Additionally, buyers should request detailed shipping timelines and tracking information to manage expectations effectively. By proactively addressing payment and shipping concerns, buyers can ensure smoother transactions and timely deliveries.
Strategic Material Selection Guide for wire mesh manufacturer
What Are the Key Materials Used in Wire Mesh Manufacturing?
Wire mesh manufacturers often utilize a variety of materials, each with distinct properties and applications. Understanding these materials is crucial for international B2B buyers, particularly those from Africa, South America, the Middle East, and Europe. This section explores four common materials used in wire mesh production: stainless steel, carbon steel, aluminum, and galvanized steel.
How Does Stainless Steel Impact Wire Mesh Performance?
Key Properties: Stainless steel wire mesh is renowned for its excellent corrosion resistance, high strength, and durability. It can withstand extreme temperatures and pressures, making it suitable for a variety of applications, including food processing and chemical industries.
Pros & Cons: The primary advantage of stainless steel is its longevity and resistance to rust and corrosion, which translates into lower maintenance costs over time. However, it is generally more expensive than other materials, which can impact budget considerations for projects.
Impact on Application: Stainless steel is ideal for environments where hygiene is paramount, such as in the food and beverage industry. Its compatibility with various cleaning agents and high-temperature processes makes it a preferred choice.
Considerations for International Buyers: Buyers should ensure compliance with international standards such as ASTM A313 or DIN 1.4301. Additionally, understanding local regulations regarding food safety can help in selecting the appropriate grade of stainless steel.
What Are the Benefits of Carbon Steel in Wire Mesh?
Key Properties: Carbon steel wire mesh is characterized by its high tensile strength and ability to endure heavy loads. It is less resistant to corrosion compared to stainless steel but offers good performance in dry environments.
Pros & Cons: Carbon steel is typically more affordable than stainless steel, making it a popular choice for applications where cost is a significant factor. However, its susceptibility to rust necessitates protective coatings or treatments, which can increase manufacturing complexity.
Impact on Application: This material is commonly used in construction, fencing, and industrial applications where strength is critical, but exposure to moisture is limited.
Considerations for International Buyers: Buyers should be aware of compliance with standards such as ASTM A36. Understanding the local climate and environmental conditions can also guide decisions on whether protective coatings are necessary.
Why Choose Aluminum Wire Mesh for Lightweight Applications?
Key Properties: Aluminum wire mesh is lightweight, corrosion-resistant, and has good conductivity. It is often used in applications where weight is a concern, such as in aerospace and automotive industries.
Pros & Cons: The main advantage of aluminum is its lightweight nature, which can reduce shipping and handling costs. However, it is less strong than steel options, which may limit its use in high-load applications.
Impact on Application: Aluminum wire mesh is ideal for applications requiring high strength-to-weight ratios, such as filtration systems and lightweight barriers.
Considerations for International Buyers: Buyers should check for compliance with standards like ASTM B221. Additionally, understanding the specific application requirements is vital to ensure that aluminum mesh meets performance expectations.
What Role Does Galvanized Steel Play in Wire Mesh Manufacturing?
Key Properties: Galvanized steel wire mesh is coated with zinc to enhance corrosion resistance. This material is known for its durability and ability to withstand outdoor conditions.
Pros & Cons: The primary advantage of galvanized steel is its cost-effectiveness and durability in outdoor applications. However, the zinc coating can wear off over time, leading to potential corrosion issues if not monitored.
Impact on Application: This material is widely used in outdoor fencing, agricultural applications, and construction due to its resilience against the elements.
Considerations for International Buyers: Buyers should ensure that the galvanized wire meets standards such as ASTM A641. Additionally, understanding the local environment (e.g., humidity, salt exposure) can help in selecting the appropriate mesh type.
Summary Table of Material Selection for Wire Mesh Manufacturing
Material | Typical Use Case for Wire Mesh Manufacturer | Key Advantage | Key Disadvantage/Limitation | Relative Cost (Low/Med/High) |
---|---|---|---|---|
Stainless Steel | Food processing, chemical industries | Excellent corrosion resistance | Higher cost | High |
Carbon Steel | Construction, fencing | Affordable and strong | Susceptible to rust | Low |
Aluminum | Aerospace, automotive | Lightweight and corrosion-resistant | Lower strength compared to steel | Medium |
Galvanized Steel | Outdoor fencing, agricultural applications | Cost-effective and durable outdoors | Zinc coating may wear off | Medium |
This comprehensive analysis should assist international B2B buyers in making informed decisions regarding material selection for wire mesh applications, ensuring optimal performance and compliance with relevant standards.
In-depth Look: Manufacturing Processes and Quality Assurance for wire mesh manufacturer
What Are the Key Stages in Wire Mesh Manufacturing Processes?
The manufacturing process for wire mesh involves several critical stages, each requiring precision and expertise to ensure high-quality output. Understanding these stages is essential for international B2B buyers looking to source wire mesh efficiently.
1. Material Preparation: What Materials Are Used in Wire Mesh Production?
The first step in wire mesh manufacturing is material preparation. Typically, high-quality steel wire is used, which can be either carbon steel or stainless steel, depending on the desired properties of the final product. Before production, the wire is sourced, inspected, and cut to specific lengths.
Key Techniques:
– Wire Drawing: This process reduces the diameter of the wire and increases its tensile strength. It involves pulling the wire through a series of dies.
– Annealing: For certain applications, the wire may undergo annealing to relieve internal stresses and improve ductility.
2. Forming: How Is Wire Mesh Formed?
Once the wire is prepared, the next stage is forming. This is where the wire is woven or welded into the desired mesh configuration.
Key Techniques:
– Woven Mesh Production: In this method, strands of wire are interlaced in a crisscross pattern. The weaving process can be automated, allowing for high-volume production.
– Welded Mesh Production: Here, wires are arranged in a grid pattern and then welded at intersections. This method provides added strength and is often used for construction applications.
3. Assembly: What Happens During the Assembly Stage?
In the assembly stage, the formed mesh is cut to size and prepared for finishing. This may include additional treatments or coatings to enhance durability and corrosion resistance.
Key Techniques:
– Cutting: The mesh is cut to specified dimensions using cutting machines.
– Edge Treatment: Edges may be treated to prevent fraying, ensuring the product is ready for installation or further processing.
4. Finishing: What Are the Common Finishing Processes for Wire Mesh?
Finishing processes are crucial for enhancing the wire mesh’s performance and longevity. Common finishing techniques include:
- Galvanization: A protective zinc coating is applied to prevent rust and corrosion, especially important for outdoor applications.
- Coating: Other coatings, such as PVC or epoxy, can be applied for additional protection and aesthetic appeal.
How is Quality Assurance Implemented in Wire Mesh Manufacturing?
Quality assurance (QA) is vital in the wire mesh industry, ensuring that products meet international standards and customer specifications. Buyers must understand how manufacturers implement QA processes to ensure product reliability.
What International Standards Should Buyers Be Aware Of?
International standards play a significant role in the quality assurance of wire mesh products. Key standards include:
- ISO 9001: This standard focuses on quality management systems and is essential for manufacturers aiming for consistent quality.
- CE Marking: Required in Europe, this mark indicates that products meet EU safety, health, and environmental protection requirements.
- API Standards: For oil and gas applications, manufacturers may adhere to American Petroleum Institute standards to ensure product reliability and safety.
What Are the Key Quality Control Checkpoints?
Quality control (QC) checkpoints are strategically placed throughout the manufacturing process to ensure product quality. Common QC checkpoints include:
- Incoming Quality Control (IQC): This step involves inspecting raw materials upon receipt to ensure they meet specified standards.
- In-Process Quality Control (IPQC): Continuous monitoring during manufacturing processes to identify defects early.
- Final Quality Control (FQC): A thorough inspection of the finished product, ensuring it meets all specifications before shipping.
What Common Testing Methods Are Used to Ensure Quality?
Manufacturers employ various testing methods to validate the quality of wire mesh products. Common tests include:
- Tensile Strength Testing: Measures the maximum load a material can withstand before failure.
- Corrosion Resistance Testing: Evaluates how well the mesh can withstand corrosive environments, crucial for outdoor applications.
- Dimensional Testing: Ensures that the mesh meets the specified dimensions and tolerances.
How Can B2B Buyers Verify Supplier Quality Control?
For international B2B buyers, verifying a supplier’s quality control processes is critical. Here are some actionable steps buyers can take:
1. Conduct Supplier Audits
Buyers should perform on-site audits of potential suppliers to assess their manufacturing processes and quality control systems. This includes reviewing their adherence to international standards and their internal QA protocols.
2. Request Quality Control Reports
Suppliers should provide detailed quality control reports, including testing results and compliance with relevant standards. Buyers should look for transparency in these documents to ensure the supplier’s commitment to quality.
3. Use Third-Party Inspection Services
Engaging third-party inspection services can provide an unbiased assessment of the supplier’s quality control processes. These services can conduct inspections at various stages of production and provide comprehensive reports.
What Are the Nuances of Quality Control for International B2B Buyers?
When sourcing wire mesh from international suppliers, particularly from regions like Africa, South America, the Middle East, and Europe, buyers should consider the following nuances:
- Cultural Differences: Understanding cultural approaches to quality and business practices can help buyers communicate expectations more effectively.
- Regulatory Compliance: Different regions may have varying regulatory requirements. Buyers must ensure that suppliers comply with both local and international regulations.
- Logistics and Supply Chain: International shipping can introduce additional risks. Buyers should assess how suppliers manage logistics and ensure product quality throughout the supply chain.
By understanding the manufacturing processes and quality assurance measures in place at wire mesh manufacturers, international B2B buyers can make informed sourcing decisions, ultimately leading to higher quality products and greater satisfaction.
Practical Sourcing Guide: A Step-by-Step Checklist for ‘wire mesh manufacturer’
In the competitive landscape of B2B procurement, sourcing from wire mesh manufacturers requires a strategic approach. This checklist is designed to guide international buyers, particularly from Africa, South America, the Middle East, and Europe, through the essential steps of the procurement process.
Step 1: Define Your Technical Specifications
Understanding the specific requirements for your wire mesh is crucial. This includes material type, mesh size, wire diameter, and intended application. Clearly defined specifications will not only help you communicate your needs effectively but will also enable you to assess supplier offerings more accurately.
- Material Considerations: Determine if you need stainless steel, galvanized, or other materials based on environmental factors and application.
- Application Requirements: Consider whether the wire mesh will be used for industrial, agricultural, or construction purposes, as each may have different durability requirements.
Step 2: Conduct Market Research for Suppliers
Research potential wire mesh manufacturers to identify those that align with your needs. Look for suppliers with a strong reputation and experience in your specific industry.
- Geographical Considerations: Suppliers in regions with established wire mesh manufacturing sectors may offer better quality and pricing.
- Online Platforms: Utilize B2B platforms and trade directories to gather a list of potential suppliers and read reviews from previous customers.
Step 3: Evaluate Potential Suppliers
Before making a commitment, it’s essential to thoroughly vet potential suppliers. Request company profiles, case studies, and references from buyers in a similar industry or region.
- Quality Assurance: Inquire about quality control processes and certifications (e.g., ISO standards) to ensure the manufacturer meets international quality standards.
- Production Capacity: Assess whether the supplier can meet your order volume and delivery timelines.
Step 4: Request Samples for Assessment
Obtaining samples is a critical step in evaluating product quality. Request samples of the wire mesh to assess its construction, durability, and compliance with your specifications.
- Testing for Specifications: Check if the sample meets your defined criteria, including tensile strength and resistance to corrosion.
- Application Fit: Ensure the sample is suitable for your intended application by testing it in real-world conditions if possible.
Step 5: Negotiate Pricing and Terms
Once you have identified a potential supplier, negotiate pricing and terms of service. This includes payment methods, delivery schedules, and return policies.
- Payment Methods: Consider using secure payment methods such as wire transfers or letters of credit, which are common in international transactions.
- Delivery Terms: Clarify Incoterms (e.g., FOB, CIF) to avoid misunderstandings about shipping responsibilities and costs.
Step 6: Verify Compliance with Regulations
Ensure that the supplier adheres to local and international regulations regarding wire mesh production and export.
- Environmental Standards: Confirm that the manufacturer complies with environmental regulations relevant to your region.
- Product Certifications: Check for necessary certifications for specific applications, such as safety standards for construction materials.
Step 7: Establish a Communication Plan
Effective communication is key to a successful supplier relationship. Set up a clear plan for regular updates and feedback.
- Point of Contact: Identify a dedicated account manager or point of contact within the supplier’s organization.
- Feedback Loop: Create a structured feedback process to address any issues or concerns promptly, ensuring a smooth procurement process.
By following this checklist, B2B buyers can streamline their sourcing process, ensuring they partner with reliable wire mesh manufacturers that meet their specific needs.
Comprehensive Cost and Pricing Analysis for wire mesh manufacturer Sourcing
What Are the Key Cost Components for Wire Mesh Manufacturing?
When sourcing wire mesh, understanding the cost structure is crucial for international B2B buyers. The primary cost components include:
-
Materials: The type of wire used, such as stainless steel, carbon steel, or galvanized wire, significantly impacts pricing. Prices can fluctuate based on global market trends and availability.
-
Labor: Labor costs vary by region. For manufacturers in Africa and South America, labor may be cheaper than in Europe, which can affect overall pricing. It’s essential to assess the skill level of the workforce and the complexity of the manufacturing processes involved.
-
Manufacturing Overhead: This includes utilities, facility costs, and indirect labor. Efficient operations can minimize these costs, influencing the final price.
-
Tooling: The initial investment in machinery and tools is a significant factor. Custom tooling for unique specifications can raise costs, so consider suppliers with advanced capabilities that may offer a broader range of products at lower tooling costs.
-
Quality Control (QC): Ensuring product quality through inspections and tests adds to the overall cost. Certifications like ISO can also affect pricing but are essential for buyers who prioritize quality.
-
Logistics: Shipping costs vary based on distance, shipping methods, and Incoterms. Understanding these can help in calculating the total landed cost.
-
Margin: The manufacturer’s profit margin is influenced by all the above components. A transparent discussion about margins can lead to better pricing negotiations.
How Do Price Influencers Impact Wire Mesh Pricing?
Several factors can influence the pricing of wire mesh:
-
Volume and Minimum Order Quantity (MOQ): Higher volumes often lead to lower per-unit costs due to economies of scale. Negotiate for better pricing on larger orders.
-
Specifications and Customization: Custom wire mesh specifications (such as size, shape, and coating) can lead to increased costs. Standard products may be more cost-effective.
-
Materials and Quality Certifications: Premium materials and certifications can elevate prices. Assess your needs carefully; sometimes, a lower quality may suffice for specific applications.
-
Supplier Factors: The reputation and reliability of suppliers can affect pricing. Established suppliers may charge more due to their proven quality and service.
-
Incoterms: Understanding the terms of shipping and delivery can significantly impact total costs. For instance, DDP (Delivered Duty Paid) may seem higher but can simplify logistics for international buyers.
What Are Effective Buyer Tips for Negotiating Wire Mesh Prices?
For international B2B buyers, especially those from Africa, South America, the Middle East, and Europe, negotiation and cost-efficiency are paramount. Here are some actionable tips:
-
Negotiate Clearly: Approach negotiations with clear expectations and flexibility. Be prepared to discuss various options, including payment terms and delivery schedules.
-
Focus on Total Cost of Ownership (TCO): Consider not just the purchase price but also shipping, handling, and potential future costs related to quality and durability. A lower upfront cost may lead to higher maintenance costs down the line.
-
Understand Pricing Nuances: Familiarize yourself with regional pricing trends and fluctuations in material costs. This knowledge can empower your negotiations.
-
Leverage Relationships: Build strong relationships with suppliers. Long-term partnerships often yield better pricing and service.
-
Consider Local Suppliers: Sourcing from local manufacturers can reduce shipping costs and lead times, improving overall efficiency.
Disclaimer on Indicative Prices
Prices for wire mesh products can vary widely based on the factors mentioned above. Always request detailed quotes and consider multiple suppliers to gain a comprehensive understanding of the market.
Alternatives Analysis: Comparing wire mesh manufacturer With Other Solutions
Understanding Alternatives in Wire Mesh Solutions
When evaluating wire mesh manufacturing solutions, it’s crucial for B2B buyers to explore viable alternatives that can meet their specific needs. Alternatives may offer different benefits, such as cost-effectiveness, ease of use, or specialized applications. This analysis compares wire mesh manufacturers with two promising alternatives: welded wire fabric and expanded metal mesh.
Comparison Table
Comparison Aspect | Wire Mesh Manufacturer | Welded Wire Fabric | Expanded Metal Mesh |
---|---|---|---|
Performance | High tensile strength | Excellent load-bearing capabilities | Good airflow and light transmission |
Cost | Moderate to high | Generally lower than wire mesh | Often lower than wire mesh |
Ease of Implementation | Requires specialized equipment | Easier installation, often pre-fabricated | Simple to install, lightweight |
Maintenance | Low maintenance | Low maintenance | Low maintenance |
Best Use Case | Security fencing, industrial applications | Concrete reinforcement, agricultural use | Grating, fencing, and architectural features |
In-Depth Analysis of Alternatives
What are the Advantages and Disadvantages of Welded Wire Fabric?
Welded wire fabric consists of steel wires that are welded together to form a grid. This product is widely used in construction, especially for reinforcing concrete.
Pros:
– Cost-Effective: Typically more affordable than traditional wire mesh, making it an excellent choice for large-scale projects.
– High Strength: Offers excellent load-bearing capabilities, suitable for structural applications.
– Ease of Use: Often available in pre-fabricated sheets, which simplifies installation.
Cons:
– Limited Flexibility: Once installed, it is not as adaptable to changes as wire mesh.
– Weight: Heavier than some alternatives, which may complicate transportation and handling.
How Does Expanded Metal Mesh Compare?
Expanded metal mesh is produced by cutting and stretching metal sheets, resulting in a mesh-like pattern. It is commonly used in applications that require ventilation and visibility.
Pros:
– Lightweight: Easier to handle and install, making it suitable for various applications.
– Airflow: Provides excellent airflow and visibility, ideal for architectural applications.
– Versatile Use: Can be employed in a variety of settings, including security, industrial, and decorative applications.
Cons:
– Lower Load-Bearing Capacity: While strong, it does not match the load-bearing capabilities of welded wire fabric or wire mesh.
– Potential for Damage: May be more susceptible to physical damage due to its design.
How Can B2B Buyers Choose the Right Solution?
When selecting between wire mesh manufacturers and alternative solutions, B2B buyers should assess their specific requirements. Considerations such as the intended application, budget constraints, and installation capabilities play vital roles in the decision-making process. If high tensile strength and security are paramount, wire mesh may be the best fit. For construction projects focused on cost-efficiency and ease of installation, welded wire fabric could be ideal. Meanwhile, expanded metal mesh is excellent for applications requiring airflow and visibility without heavy structural demands. By analyzing these factors, buyers can make informed decisions that align with their operational goals.
Essential Technical Properties and Trade Terminology for wire mesh manufacturer
What Are the Essential Technical Properties of Wire Mesh?
Understanding the technical properties of wire mesh is crucial for international B2B buyers, especially when selecting the right product for specific applications. Here are some key specifications to consider:
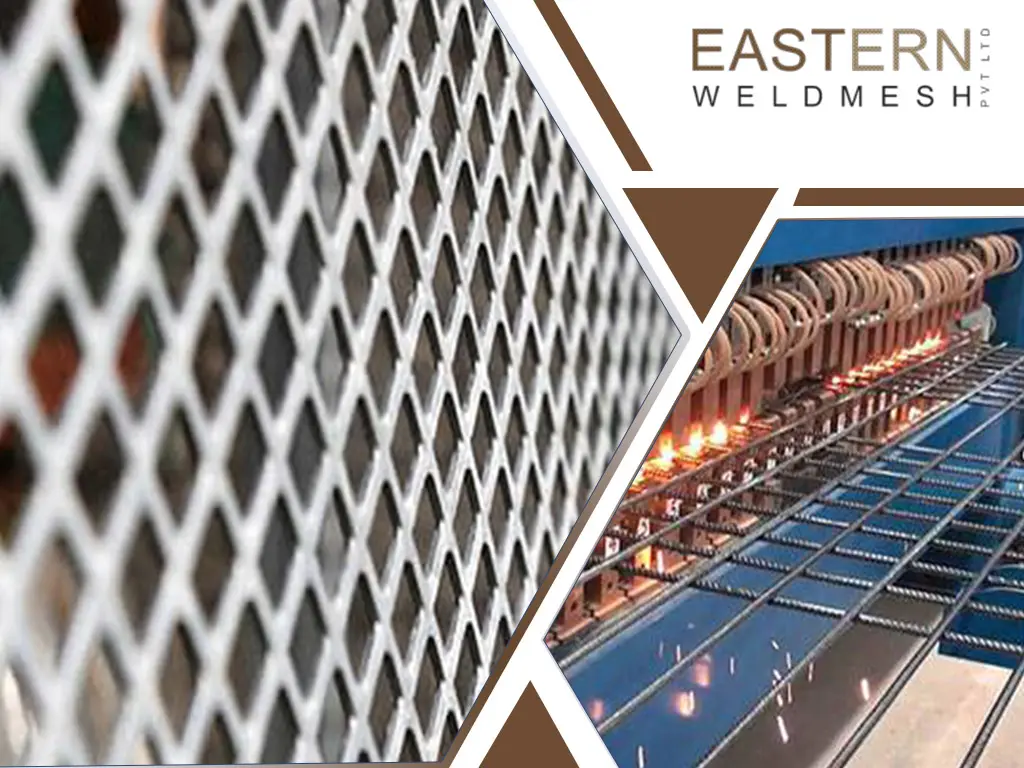
A stock image related to wire mesh manufacturer.
1. Material Grade
Wire mesh can be made from various materials, including stainless steel, galvanized steel, aluminum, and plastic. The material grade significantly impacts durability, corrosion resistance, and tensile strength. For example, stainless steel wire mesh is ideal for applications in corrosive environments, such as in food processing or chemical industries. Buyers should assess their specific needs to select the appropriate material grade.
2. Wire Diameter
The diameter of the wire used in the mesh affects its strength and the size of the openings. A thicker wire typically provides greater strength and resistance to deformation but may limit flexibility. Conversely, a thinner wire may be more suitable for applications requiring fine filtration or aesthetic appeal. Understanding the required wire diameter is essential for ensuring that the wire mesh meets operational requirements.
3. Mesh Opening Size
The size of the openings in wire mesh determines its filtering capabilities and is a critical factor for applications such as sieving, fencing, and reinforcement. Mesh opening size is usually expressed in inches or millimeters and is directly linked to the intended use. Buyers must consider the specific application to choose the right mesh opening size that meets their operational needs.
4. Tolerance
Tolerance refers to the allowable deviation from specified dimensions. In wire mesh manufacturing, maintaining tight tolerances is crucial for ensuring consistent quality and performance. High precision in tolerances is especially important in applications such as aerospace or electronics, where even minor discrepancies can lead to failures. Buyers should inquire about the manufacturer’s tolerance standards to ensure compatibility with their projects.
5. Finish Type
The finish of wire mesh can include options such as electroplated, hot-dipped galvanized, or powder-coated. The finish impacts both the aesthetic appeal and the functional performance of the mesh, particularly in terms of corrosion resistance and durability. Buyers should consider the environmental conditions where the wire mesh will be used to determine the most suitable finish type.
What Are Common Trade Terms in the Wire Mesh Industry?
Familiarity with industry jargon can facilitate smoother transactions and better communication with suppliers. Here are some essential trade terms to know:
1. OEM (Original Equipment Manufacturer)
OEM refers to companies that produce parts or equipment that may be marketed by another company. In the wire mesh industry, an OEM might manufacture wire mesh products that are branded and sold by a different company. Understanding OEM agreements can help buyers ensure they are working with reputable manufacturers.
2. MOQ (Minimum Order Quantity)
MOQ is the minimum quantity of products that a supplier is willing to sell. This term is crucial for B2B buyers, as it impacts purchasing decisions and inventory management. Understanding a supplier’s MOQ can help buyers plan their orders effectively and avoid excess inventory costs.
3. RFQ (Request for Quotation)
An RFQ is a formal process where buyers request price quotes from suppliers for specific products. This term is vital for international buyers to ensure they receive competitive pricing and terms. Including detailed specifications in an RFQ can lead to more accurate quotations.
4. Incoterms (International Commercial Terms)
Incoterms are a set of predefined commercial terms published by the International Chamber of Commerce (ICC) that clarify the responsibilities of buyers and sellers in international transactions. Familiarity with Incoterms can help buyers understand shipping responsibilities, risk transfer, and cost allocation in their wire mesh purchases.
5. Lead Time
Lead time refers to the time taken from placing an order to its delivery. Understanding lead times is essential for effective project planning and ensuring that materials arrive when needed. Buyers should communicate their timelines clearly with suppliers to avoid delays in their operations.
By grasping these technical properties and trade terms, international B2B buyers can make informed decisions when sourcing wire mesh products, ensuring their investments align with their operational requirements.
Navigating Market Dynamics and Sourcing Trends in the wire mesh manufacturer Sector
What Are the Key Market Dynamics and Trends Affecting Wire Mesh Manufacturers?
The wire mesh manufacturing sector is experiencing significant growth driven by various global factors. One of the primary drivers is the increasing demand for wire mesh in construction, agriculture, and industrial applications. As urbanization continues in regions like Africa and South America, the construction industry is expanding, leading to a higher need for durable and versatile materials such as wire mesh. Additionally, the rising emphasis on security and fencing solutions in both residential and commercial properties is propelling the demand for specialized wire mesh products.
Emerging technologies are also reshaping the sourcing landscape in the wire mesh sector. Automation and digital tools for inventory management and supply chain optimization are becoming more prevalent, allowing manufacturers to respond swiftly to market demands. B2B buyers are increasingly turning to e-commerce platforms and digital marketplaces, making it easier to compare suppliers, prices, and product specifications. This shift towards digitalization is especially relevant for international buyers looking to streamline their procurement processes and reduce lead times.
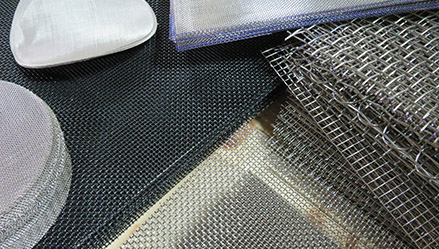
A stock image related to wire mesh manufacturer.
In terms of sourcing trends, ethical sourcing and sustainability are gaining traction. Buyers are seeking suppliers who adhere to responsible sourcing practices, ensuring that materials are sourced in an environmentally friendly manner. This trend is particularly pronounced in Europe, where regulations around sustainable practices are stringent, and businesses are held accountable for their supply chain impacts.
How Is Sustainability Shaping the Wire Mesh Manufacturing Sector?
Sustainability is becoming a core focus for wire mesh manufacturers as environmental concerns escalate. The production of wire mesh can have significant environmental impacts, including resource depletion and waste generation. Therefore, manufacturers are increasingly adopting eco-friendly practices by utilizing recycled materials and reducing energy consumption during production.
Ethical sourcing is equally important, as B2B buyers prioritize suppliers who demonstrate commitment to sustainable practices. Companies that can provide certifications, such as ISO 14001 for environmental management or other green certifications, will stand out in the competitive marketplace. These certifications not only enhance a manufacturer’s credibility but also attract buyers who are keen on minimizing their environmental footprint.
Moreover, the use of sustainable materials, such as galvanized steel or stainless steel, is on the rise. These materials not only have a longer lifespan but also require less frequent replacement, which contributes to reduced waste over time. By investing in sustainable practices, wire mesh manufacturers can meet the growing demand for environmentally responsible products while also improving their operational efficiencies.
What Is the Historical Context of Wire Mesh Manufacturing in B2B?
The evolution of wire mesh manufacturing dates back to the industrial revolution, when advancements in metallurgy and weaving technology enabled the mass production of wire products. Initially, wire mesh was primarily utilized in agriculture and construction for fencing and support structures. However, as industrial applications expanded, so did the variety of wire mesh products available, including those used in filtration, architectural design, and safety solutions.
Over the decades, technological advancements have further transformed the wire mesh industry. Innovations in materials science have led to the development of stronger and more durable wire meshes, while automation in manufacturing processes has improved production efficiency and product consistency. Today, wire mesh manufacturers are not only focused on meeting traditional demands but are also adapting to new market needs driven by sustainability and technological advancements, positioning themselves for future growth in a rapidly evolving landscape.
Frequently Asked Questions (FAQs) for B2B Buyers of wire mesh manufacturer
-
How do I choose the right wire mesh manufacturer for my business needs?
Choosing the right wire mesh manufacturer involves several key considerations. First, assess the manufacturer’s experience and reputation in the industry. Look for certifications and compliance with international standards, particularly those relevant to your region, such as ISO or ASTM. Additionally, evaluate their product range to ensure they can meet your specific requirements, whether for construction, agriculture, or industrial applications. Request samples to evaluate quality and inquire about customization options. Lastly, consider their customer service and responsiveness, as these factors will impact your overall experience and partnership. -
What are the common applications of wire mesh in various industries?
Wire mesh is utilized across multiple industries for diverse applications. In construction, it is often used for reinforcing concrete structures and as fencing solutions. In agriculture, wire mesh serves as pest control and crop protection. The automotive and aerospace sectors employ wire mesh for filtration and safety components. Moreover, it finds use in mining for separation processes and in HVAC systems for air filtration. Understanding these applications can help you identify the best type of wire mesh for your specific industry needs. -
What customization options are available when sourcing wire mesh?
Most wire mesh manufacturers offer various customization options to suit specific project requirements. You can customize the mesh size, wire gauge, material type (such as stainless steel, galvanized, or plastic), and coating finishes. Additionally, some manufacturers may provide specific weaving patterns or mesh configurations, such as welded or woven wire mesh. It’s essential to communicate your requirements clearly during the initial discussions to ensure the manufacturer can meet your specifications effectively. -
What is the minimum order quantity (MOQ) for wire mesh products?
Minimum order quantities (MOQ) for wire mesh products can vary significantly between manufacturers. Typically, MOQs range from a few hundred square meters to several tons, depending on the product type and manufacturer capabilities. Smaller buyers may find manufacturers willing to accommodate lower MOQs, especially for standard products. It’s advisable to discuss your needs directly with the manufacturer and explore potential options if your order volume is below their standard MOQ. -
What payment terms should I expect when dealing with international wire mesh suppliers?
Payment terms can vary widely among international wire mesh suppliers. Common practices include upfront payments, deposits, or payment upon delivery. Some manufacturers may offer flexible terms based on your relationship and order volume. It’s crucial to clarify these terms before finalizing any contracts. Additionally, consider using secure payment methods such as letters of credit or escrow services to protect your financial interests during international transactions. -
How can I ensure the quality of wire mesh products before purchase?
To ensure quality, request detailed product specifications and certifications from the manufacturer. Ask for samples to evaluate the material and construction quality firsthand. Additionally, inquire about their quality assurance processes, such as inspections and testing standards. If possible, visit the manufacturing facility to observe their production methods. Establishing clear quality expectations in your contract can also help mitigate risks associated with subpar products. -
What logistics considerations should I keep in mind when importing wire mesh?
When importing wire mesh, logistics considerations are crucial to ensure timely delivery and cost-effectiveness. First, assess shipping methods and choose between air freight or sea freight based on urgency and budget. Understand the customs regulations and tariffs applicable in your country to avoid unexpected costs. Additionally, work with a reliable freight forwarder who can assist with documentation, customs clearance, and tracking shipments. Planning for potential delays, especially in international trade, is also essential. -
How can I effectively vet potential wire mesh manufacturers?
Vetting potential wire mesh manufacturers involves several steps. Start by researching their background, including years in business, customer reviews, and industry reputation. Request references from previous clients to gauge their reliability and service quality. Evaluate their production capabilities and whether they adhere to international quality standards. Conducting a factory audit, if feasible, can provide insights into their operations and quality control measures. Finally, ensure clear communication during negotiations, as this reflects their willingness to collaborate and meet your needs.
Important Disclaimer & Terms of Use
⚠️ Important Disclaimer
The information provided in this guide, including content regarding manufacturers, technical specifications, and market analysis, is for informational and educational purposes only. It does not constitute professional procurement advice, financial advice, or legal advice.
While we have made every effort to ensure the accuracy and timeliness of the information, we are not responsible for any errors, omissions, or outdated information. Market conditions, company details, and technical standards are subject to change.
B2B buyers must conduct their own independent and thorough due diligence before making any purchasing decisions. This includes contacting suppliers directly, verifying certifications, requesting samples, and seeking professional consultation. The risk of relying on any information in this guide is borne solely by the reader.
Strategic Sourcing Conclusion and Outlook for wire mesh manufacturer
As the global demand for wire mesh continues to rise, strategic sourcing has emerged as a critical approach for B2B buyers to enhance their procurement processes. Understanding the nuances of wire mesh manufacturing—such as material types, production techniques, and regional suppliers—can significantly impact both cost efficiency and product quality. Buyers from Africa, South America, the Middle East, and Europe should prioritize building relationships with reputable manufacturers that can provide tailored solutions to meet their specific needs.
Investing time in strategic sourcing not only ensures a reliable supply chain but also fosters innovation and sustainability in sourcing practices. By leveraging local and international suppliers, buyers can diversify their sourcing strategies, mitigate risks, and enhance their competitive edge in the marketplace.
Looking ahead, the wire mesh industry is poised for growth, driven by technological advancements and evolving market demands. B2B buyers are encouraged to stay informed about emerging trends and continuously evaluate their sourcing strategies. Embrace the opportunity to connect with manufacturers who align with your values and quality standards, ultimately paving the way for long-term partnerships that can thrive in an increasingly interconnected world.