Find Top Filling Machine Manufacturers: The Ultimate Guide (2025)
Introduction: Navigating the Global Market for Filling Machine Manufacturers
Navigating the global market for filling machine manufacturers presents a unique challenge for international B2B buyers, particularly those in regions like Africa, South America, the Middle East, and Europe. Sourcing reliable filling machines that cater to diverse production needs—whether for beverages, cosmetics, or pharmaceuticals—can be daunting. This guide aims to demystify the process by providing a comprehensive overview of filling machine types, their applications, and essential factors to consider when selecting suppliers.
B2B buyers will benefit from insights on how to effectively vet suppliers, ensuring they meet quality and compliance standards. Additionally, the guide will address cost considerations, helping businesses make informed financial decisions that align with their operational budgets. Understanding the intricacies of filling machines, from automated systems to semi-automatic options, enables companies to choose the right equipment tailored to their production requirements.
This resource empowers buyers by equipping them with actionable knowledge, enabling them to navigate the complexities of the filling machine market with confidence. Whether you are a manufacturer in Kenya looking to enhance production efficiency or a distributor in Brazil seeking to expand your product offerings, this guide will serve as a vital tool in your purchasing decision-making process. By leveraging the information provided, international B2B buyers can streamline their sourcing efforts and foster successful partnerships with reputable filling machine manufacturers.
Understanding Filling Machine Manufacturers Types and Variations
Type Name | Key Distinguishing Features | Primary B2B Applications | Brief Pros & Cons for Buyers |
---|---|---|---|
Volumetric Filling Machines | Measure and dispense specific volumes; suitable for liquids and pastes | Food and beverage, pharmaceuticals | Pros: High accuracy; Cons: Limited to uniform viscosity liquids |
Gravity Filling Machines | Utilize gravity to fill containers; ideal for free-flowing liquids | Beverage bottling, oil filling | Pros: Simple design; Cons: Slower filling speed |
Piston Filling Machines | Use a piston mechanism to fill containers; versatile with various viscosities | Cosmetics, sauces, industrial liquids | Pros: Handles thick products; Cons: More complex maintenance |
Aseptic Filling Machines | Designed for sterile environments; often used with heat and pressure | Dairy, pharmaceuticals | Pros: Ensures product sterility; Cons: Higher upfront costs |
Pump Filling Machines | Employ pumps to move liquid into containers; good for high-viscosity products | Chemical, food production | Pros: Efficient for thick liquids; Cons: Requires precise pump calibration |
What are the Key Characteristics of Volumetric Filling Machines?
Volumetric filling machines are designed to dispense a precise volume of product into containers, making them ideal for applications requiring high accuracy. They work well with liquids and pastes, ensuring consistent fill levels across batches. When considering a volumetric filling machine, buyers should assess the machine’s compatibility with their product’s viscosity and the required fill volume, as these factors significantly impact performance and efficiency.
How Do Gravity Filling Machines Operate?
Gravity filling machines utilize the force of gravity to fill containers with free-flowing liquids. Their straightforward design makes them easy to operate and maintain, making them a popular choice in beverage bottling and oil filling industries. However, buyers should be aware that while gravity fillers are cost-effective, their filling speed may be slower compared to other types, which can affect production rates.
Why Choose Piston Filling Machines for Thick Products?
Piston filling machines are particularly suited for handling products with varying viscosities, including thick sauces and creams. They operate using a piston mechanism that allows for precise filling, making them versatile across multiple sectors such as cosmetics and industrial liquids. Buyers should consider the maintenance complexity and the need for regular calibration, as these machines can require more upkeep compared to simpler filling solutions.
What Makes Aseptic Filling Machines Essential for Sterile Products?
Aseptic filling machines are crucial in industries where product sterility is paramount, such as dairy and pharmaceuticals. They operate under controlled conditions, often involving heat and pressure, to ensure that the product remains free from contamination. While the investment in aseptic technology can be higher, the benefits of maintaining product integrity and extending shelf life often justify the cost for businesses prioritizing quality.
How Do Pump Filling Machines Enhance Efficiency?
Pump filling machines are designed to handle high-viscosity products effectively, utilizing pumps to transfer liquid into containers. This type of filling machine is commonly used in chemical and food production sectors. Buyers should evaluate the precision of pump calibration and the potential need for adjustments over time, as these factors can influence the overall efficiency and reliability of the filling process.
Related Video: automatic stand up pouch filling and packing machine
Key Industrial Applications of Filling Machine Manufacturers
Industry/Sector | Specific Application of Filling Machine Manufacturers | Value/Benefit for the Business | Key Sourcing Considerations for this Application |
---|---|---|---|
Food and Beverage | Automated liquid filling for beverages | Increases efficiency, reduces labor costs, ensures consistent quality | Compatibility with various container types, speed of operation, hygiene standards |
Pharmaceuticals | Precision filling for syringes and vials | Ensures dosage accuracy, compliance with regulations, minimizes waste | Regulatory compliance, ease of cleaning, integration with existing systems |
Cosmetics and Personal Care | Filling creams and lotions into containers | Enhances production speed, reduces contamination risk, improves product consistency | Material compatibility, production speed, ease of maintenance |
Chemicals | Filling hazardous liquids and chemicals | Enhances safety, reduces spillage, ensures precise measurements | Safety certifications, material compatibility, automation capabilities |
Agriculture | Filling fertilizers and pesticides | Optimizes packaging processes, reduces waste, ensures accurate dosing | Bulk handling capabilities, resistance to corrosive materials, customization options |
What Are the Key Industrial Applications of Filling Machines in the Food and Beverage Sector?
In the food and beverage industry, filling machines play a crucial role in automating the process of filling liquid products into bottles or containers. These machines are designed to handle various types of beverages, including juices, soft drinks, and alcoholic beverages. They help businesses increase efficiency by minimizing manual labor and ensuring that each container is filled to the exact required volume, thereby maintaining product quality and consistency. For international buyers, especially from regions like Africa and South America, sourcing machines that comply with local food safety regulations and can adapt to different container sizes is essential.
How Do Filling Machines Benefit the Pharmaceutical Industry?
In the pharmaceutical sector, filling machines are vital for accurately dispensing liquids into syringes, vials, and other containers. Precision is paramount in this industry, as incorrect dosages can lead to severe consequences. These machines not only ensure compliance with stringent regulations but also help minimize waste through accurate filling. Buyers from the Middle East and Europe should consider machines that offer easy integration with existing production lines and can be thoroughly cleaned to prevent cross-contamination between batches.
What Role Do Filling Machines Play in the Cosmetics and Personal Care Industry?
Filling machines in the cosmetics and personal care industry are used to fill creams, lotions, and gels into various types of packaging. These machines enhance production speed and reduce the risk of contamination, ensuring that products maintain their quality and effectiveness. For B2B buyers in Europe and Africa, sourcing filling machines that are compatible with different viscosities and container shapes is crucial, as it allows for greater flexibility in product offerings.
Why Are Filling Machines Important for Chemical Manufacturing?
In chemical manufacturing, filling machines are essential for dispensing hazardous liquids and chemicals safely and accurately. These machines are designed to minimize spillage and ensure precise measurements, which is crucial for maintaining safety standards. Buyers from regions like South America and the Middle East need to prioritize machines that come with necessary safety certifications and are made from materials resistant to corrosive substances, ensuring longevity and reliability in harsh environments.
How Are Filling Machines Used in Agriculture?
Filling machines are increasingly utilized in agriculture for packaging fertilizers and pesticides. These machines optimize the packaging process, ensuring that products are filled accurately and efficiently, which reduces waste and enhances overall productivity. For international buyers, especially in developing markets, it is important to source machines that can handle bulk quantities and are customizable to meet specific product requirements, ensuring adaptability in a rapidly changing market.
Related Video: Capsugel Ultra™ III Capsule Filling Machine
3 Common User Pain Points for ‘Filling Machine Manufacturers’ & Their Solutions
Scenario 1: Navigating High Initial Costs for Filling Machines
The Problem: Many B2B buyers, especially in regions like Africa and South America, face the daunting challenge of high initial investment costs when purchasing filling machines. These machines are often seen as a significant capital expenditure, which can strain budgets, particularly for small to medium-sized enterprises. The fear of making a poor investment can lead to prolonged decision-making processes, causing potential delays in scaling production capabilities.
The Solution: To alleviate the financial burden, buyers should consider exploring leasing options or financing plans offered by filling machine manufacturers. These alternatives allow businesses to acquire advanced machinery without the upfront costs associated with outright purchases. Additionally, buyers should conduct a thorough cost-benefit analysis to understand the long-term savings that can be achieved through increased efficiency and reduced labor costs. Engaging with manufacturers who provide flexible payment terms can also facilitate a smoother transition into acquiring new technology. It is essential to communicate openly with suppliers about budget constraints; many manufacturers are willing to tailor solutions that fit the financial capabilities of their clients.
Scenario 2: Ensuring Compatibility with Existing Production Lines
The Problem: A common pain point for international B2B buyers is ensuring that new filling machines integrate seamlessly with existing production lines. Incompatibility can lead to significant downtime, costly modifications, and potential disruptions in the supply chain. This issue is particularly prevalent among businesses looking to upgrade equipment without overhauling their entire system.
The Solution: To mitigate this risk, buyers should conduct a comprehensive assessment of their current production lines and identify specific requirements for new filling machines. Engaging in detailed discussions with manufacturers about technical specifications, compatibility, and customization options is crucial. Buyers should ask for case studies or references from similar businesses that have successfully integrated new machines into existing setups. Additionally, investing in machines that offer modular designs can provide flexibility and adaptability, allowing for easier upgrades in the future without extensive changes to the entire system. Manufacturers that provide on-site consultations or virtual assessments can also help identify compatibility issues before purchase.
Scenario 3: Overcoming Technical Support Challenges
The Problem: Many B2B buyers encounter significant challenges related to technical support and maintenance after purchasing filling machines. This is especially true for companies operating in remote areas or regions with limited access to specialized service technicians. A lack of timely support can lead to prolonged downtime, negatively impacting production schedules and profitability.
The Solution: To ensure robust ongoing support, buyers should prioritize manufacturers known for their excellent customer service and technical assistance. It is advisable to review service level agreements (SLAs) that guarantee response times for maintenance and support. Additionally, buyers can invest in training programs offered by manufacturers to empower their staff with the necessary skills to troubleshoot minor issues independently. Establishing a direct line of communication with the manufacturer’s support team can also facilitate quicker resolutions. Furthermore, opting for machines that come with comprehensive user manuals and online support resources can be beneficial. Buyers should not hesitate to inquire about the availability of local service representatives or partners in their region, ensuring that help is always within reach.
Strategic Material Selection Guide for Filling Machine Manufacturers
When selecting materials for filling machines, manufacturers must consider the unique properties and performance characteristics of various materials. This decision impacts not only the machine’s efficiency but also its longevity and suitability for specific applications. Here, we analyze four common materials used in filling machine manufacturing: stainless steel, plastic, aluminum, and rubber.
What Are the Key Properties of Stainless Steel for Filling Machines?
Stainless steel is renowned for its exceptional strength and corrosion resistance, making it ideal for filling machines that handle aggressive substances. It typically withstands high temperatures and pressures, which is crucial for applications involving hot liquids or gases. The most common grades used in the industry, such as 304 and 316, offer varying levels of resistance to chlorides and acids, further enhancing their suitability for food and pharmaceutical applications.
Pros: Stainless steel is durable, easy to clean, and compliant with sanitary standards, making it a preferred choice in industries requiring high hygiene levels.
Cons: The primary downside is its cost, which can be significantly higher than other materials. Additionally, machining stainless steel can be complex, requiring specialized tools and techniques.
Impact on Application: Stainless steel is compatible with a wide range of media, including corrosive chemicals and high-temperature fluids, making it versatile for various filling applications.
Considerations for International Buyers: Buyers from regions like Africa and South America should ensure compliance with international standards such as ASTM and DIN, as well as local regulations regarding food safety and material certification.
How Does Plastic Compare for Filling Machine Applications?
Plastic materials, particularly high-density polyethylene (HDPE) and polypropylene (PP), are increasingly used in filling machines due to their lightweight nature and resistance to corrosion. These materials can be molded into complex shapes, allowing for innovative design solutions in filling systems.
Pros: Plastics are generally less expensive than metals, and their resistance to chemical corrosion makes them suitable for a variety of applications.
Cons: However, plastics may not withstand high temperatures or pressures as effectively as metals, limiting their use in certain environments. They can also be less durable over time, particularly under mechanical stress.
Impact on Application: Plastic is ideal for filling non-corrosive liquids and powders but may not be suitable for hot or highly corrosive substances.
Considerations for International Buyers: Buyers should be aware of the specific grade of plastic used and its compliance with food safety standards, especially in Europe, where regulations are stringent.
What Are the Advantages of Aluminum in Filling Machine Manufacturing?
Aluminum is another popular material due to its lightweight properties and good corrosion resistance. It is often used in components that require a balance between weight and strength, such as frames and housings.
Pros: Aluminum is relatively inexpensive and easy to machine, allowing for rapid production and customization. It also offers good thermal conductivity, which can be beneficial in certain filling applications.
Cons: The main limitation of aluminum is its susceptibility to corrosion when exposed to certain chemicals, which may restrict its use in aggressive environments. It is also not as durable as stainless steel.
Impact on Application: Aluminum is suitable for filling applications involving less aggressive media but should be avoided for corrosive substances.
Considerations for International Buyers: Buyers should check for compliance with relevant standards and consider the local availability of aluminum components, especially in regions with developing supply chains.
Why is Rubber Important for Seals and Gaskets in Filling Machines?
Rubber is primarily used for seals, gaskets, and hoses in filling machines due to its flexibility and excellent sealing properties. Various types of rubber, such as nitrile and silicone, are chosen based on their compatibility with the media being filled.
Pros: Rubber provides a tight seal, preventing leaks and contamination, which is critical in maintaining product integrity.
Cons: However, rubber can degrade over time, especially when exposed to heat, chemicals, or UV light, necessitating regular replacement.
Impact on Application: Rubber is essential for applications requiring airtight seals, particularly in food and beverage industries.
Considerations for International Buyers: Buyers should ensure that rubber components meet international standards for food safety and chemical compatibility, particularly in regions with strict regulations.
Summary Table of Material Selection for Filling Machines
Material | Typical Use Case for Filling Machine Manufacturers | Key Advantage | Key Disadvantage/Limitation | Relative Cost (Low/Med/High) |
---|---|---|---|---|
Stainless Steel | Food and pharmaceutical filling applications | High durability and corrosion resistance | Higher cost and manufacturing complexity | High |
Plastic | Non-corrosive liquid and powder filling | Lightweight and cost-effective | Limited temperature and pressure tolerance | Low |
Aluminum | Frames and housings in filling machines | Lightweight and easy to machine | Susceptible to corrosion | Medium |
Rubber | Seals and gaskets in filling machines | Excellent sealing properties | Degradation over time | Medium |
By carefully considering the properties, advantages, and limitations of these materials, B2B buyers can make informed decisions that align with their operational needs and compliance requirements.
In-depth Look: Manufacturing Processes and Quality Assurance for Filling Machine Manufacturers
What Are the Key Stages in the Manufacturing Process for Filling Machines?
Manufacturing filling machines involves several critical stages, each contributing to the overall functionality, reliability, and quality of the final product. Understanding these stages can help international B2B buyers assess potential suppliers effectively.
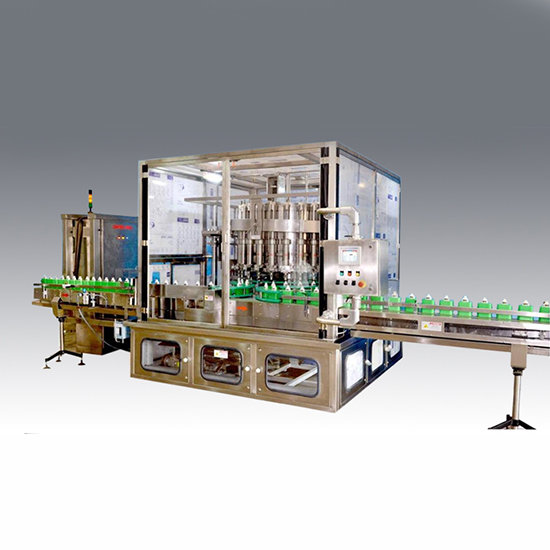
A stock image related to Filling Machine Manufacturers.
1. Material Preparation
The first step in manufacturing filling machines is material preparation. This involves selecting the right materials based on the machine’s intended use—whether it is for liquids, powders, or granular substances. Common materials include stainless steel for its corrosion resistance and durability, as well as plastics and other composites.
During this phase, suppliers typically conduct thorough inspections to ensure that the materials meet industry standards. Buyers should inquire about the sourcing of these materials and request certificates of authenticity or quality to verify compliance with international standards.
2. Forming
Once materials are prepared, the next step is forming. This includes processes such as cutting, bending, and molding to create the components of the filling machine. Advanced techniques such as CNC (Computer Numerical Control) machining are often employed to ensure precision and consistency.
Buyers should consider suppliers who utilize modern manufacturing technologies, as these can enhance the accuracy and reduce the likelihood of defects. Requesting examples of past work or case studies can provide insight into the supplier’s capabilities in this area.
3. Assembly
Assembly is where the individual components come together to form the complete filling machine. This stage often involves both manual and automated processes, depending on the complexity of the machine.
Quality assurance begins at this stage, with operators conducting inspections to verify that all parts fit correctly and function as intended. B2B buyers should ask about the assembly line’s layout and workflow to understand how efficiently the supplier operates.
4. Finishing
The finishing stage includes surface treatment processes such as polishing, coating, and painting, which not only enhance the machine’s appearance but also improve its resistance to wear and tear. This stage may also involve installing electronic components and calibrating the machine for optimal performance.
Buyers should look for suppliers who adhere to international finishing standards, as this can significantly impact the machine’s lifespan and operational efficiency.
How Is Quality Assurance Implemented in Filling Machine Manufacturing?
Quality assurance (QA) is a vital part of the manufacturing process that ensures the filling machines meet both customer expectations and regulatory requirements.
Relevant International Standards for Quality Assurance
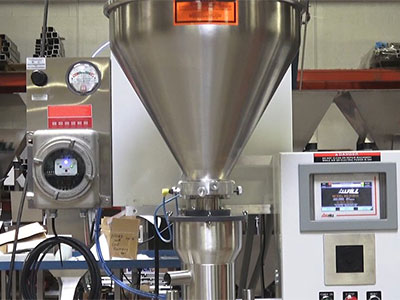
A stock image related to Filling Machine Manufacturers.
International standards such as ISO 9001 are crucial for establishing a robust quality management system. This standard emphasizes customer satisfaction, continuous improvement, and the importance of process documentation. Additionally, industry-specific certifications like CE marking for European markets and API standards for oil and gas applications further validate the quality of filling machines.
B2B buyers should request copies of these certifications and inquire about the supplier’s adherence to these standards as part of their due diligence.
What Are the Key Quality Control Checkpoints?
Quality control (QC) involves several checkpoints throughout the manufacturing process to ensure the product meets the required specifications:
-
Incoming Quality Control (IQC): This initial checkpoint verifies the quality of raw materials before they are used in production. Suppliers should document the inspection results and provide these records to buyers.
-
In-Process Quality Control (IPQC): During the manufacturing process, IPQC involves monitoring production to detect any deviations from quality standards. This can include periodic inspections and testing of components.
-
Final Quality Control (FQC): Once the filling machines are assembled, FQC ensures that the final product meets all specifications before shipment. This includes functional testing, safety checks, and performance evaluations.
B2B buyers should inquire about the frequency and methods of these inspections to understand how the supplier maintains quality throughout the manufacturing process.
What Common Testing Methods Are Used for Filling Machines?
Testing methods are essential for verifying the functionality and reliability of filling machines. Common approaches include:
-
Functional Testing: This evaluates whether the machine operates as intended under various conditions, simulating real-world usage.
-
Performance Testing: Assessing the machine’s efficiency, including speed and accuracy of filling, is crucial for determining its suitability for specific applications.
-
Durability Testing: This involves subjecting the machine to stress tests to ensure it can withstand operational demands over time.
B2B buyers should ask suppliers to provide detailed testing reports, including methodologies and results, to verify the machine’s reliability.
How Can B2B Buyers Verify Supplier Quality Control?
For international buyers, particularly those from Africa, South America, the Middle East, and Europe, verifying a supplier’s quality control processes is vital. Here are several methods to accomplish this:
-
Conduct Audits: Regular audits of the manufacturing facility can provide insights into the supplier’s quality management practices. Buyers should consider hiring third-party auditors to ensure an unbiased review.
-
Request Quality Reports: Suppliers should be able to provide comprehensive quality reports that detail their QC processes, inspection results, and any corrective actions taken in response to defects.
-
Third-Party Inspections: Engaging independent inspection agencies can help verify that the machines meet the required quality standards before shipment.
-
Check References and Reviews: Speaking with other clients or checking online reviews can offer additional perspectives on the supplier’s reliability and quality assurance practices.
What Are the Quality Control and Certification Nuances for International B2B Buyers?
For buyers from diverse regions, understanding the nuances of quality control and certifications can be crucial. Here are key considerations:
-
Regional Standards Compliance: Different regions may have specific standards and certifications that must be met. Buyers should familiarize themselves with these requirements to ensure compliance when importing machinery.
-
Documentation Requirements: Ensure that all quality certificates and test reports are available in a language and format that is understandable and acceptable in your country.
-
Cultural Differences: Be aware of cultural differences in business practices that may affect communication and expectations regarding quality assurance.
By following these guidelines, international B2B buyers can navigate the complexities of manufacturing processes and quality assurance in filling machine manufacturing, ultimately leading to more informed purchasing decisions.
Practical Sourcing Guide: A Step-by-Step Checklist for ‘Filling Machine Manufacturers’
To successfully procure filling machines from manufacturers, international B2B buyers must navigate a complex landscape of suppliers, technology options, and regional market dynamics. This checklist serves as a practical guide to streamline the sourcing process, ensuring that buyers from Africa, South America, the Middle East, and Europe can make informed decisions that meet their operational needs.
Step 1: Define Your Technical Specifications
Before engaging with manufacturers, clearly outline your technical requirements. Specify the types of products to be filled, the required production speed, and the machine’s compatibility with different container types. This step ensures that you approach suppliers who can meet your precise needs, minimizing the risk of purchasing equipment that is ill-suited for your operations.
Step 2: Research and Identify Potential Suppliers
Conduct thorough research to compile a list of potential filling machine manufacturers. Utilize online directories, trade shows, and industry publications to identify reputable suppliers. Focus on manufacturers with a strong track record in your region and industry to ensure reliability and compatibility with local standards.
Step 3: Evaluate Supplier Certifications
Verification of supplier certifications is crucial to ensure compliance with international standards. Look for certifications such as ISO 9001 for quality management systems and CE marking for European compliance. These certifications demonstrate a commitment to quality and safety, which is essential for maintaining operational integrity in your production line.
Step 4: Request Detailed Proposals
Once you have shortlisted suppliers, request detailed proposals that include pricing, delivery timelines, and warranty information. This step is vital for comparing offers and understanding the total cost of ownership, which includes not only the purchase price but also maintenance and operational costs over time.
Step 5: Assess After-Sales Support and Service
Evaluate the after-sales support offered by manufacturers. Reliable after-sales service is essential for minimizing downtime and ensuring continuous operation. Inquire about warranty terms, availability of spare parts, and the responsiveness of technical support. A supplier that offers robust support can be a significant asset in maintaining your production efficiency.
Step 6: Conduct Site Visits or Virtual Tours
If feasible, arrange site visits to the manufacturing facilities of your shortlisted suppliers. This allows you to assess their production capabilities, quality control processes, and overall operational environment. If a physical visit is not possible, request virtual tours or video demonstrations to gain insight into their manufacturing processes.
Step 7: Negotiate Terms and Finalize the Contract
After selecting a supplier, negotiate the terms of the contract carefully. Focus on payment terms, delivery schedules, and service level agreements. Ensure that all agreements are documented clearly to avoid misunderstandings later. A well-negotiated contract protects your investment and establishes a solid foundation for your business relationship.
By following this checklist, B2B buyers can navigate the complexities of sourcing filling machines, ensuring they make informed decisions that align with their operational goals.
Comprehensive Cost and Pricing Analysis for Filling Machine Manufacturers Sourcing
What Are the Key Cost Components in Filling Machine Manufacturing?
When sourcing filling machines, understanding the cost structure is essential for making informed purchasing decisions. The main cost components include:
-
Materials: This accounts for a significant portion of the total cost. Common materials used in manufacturing filling machines include stainless steel, plastics, and electronic components. The choice of materials affects not only the price but also the durability and functionality of the machines.
-
Labor: Labor costs vary significantly depending on the region and the complexity of the manufacturing process. Countries with higher labor costs may produce more sophisticated machines, while lower-cost regions may focus on basic models.
-
Manufacturing Overhead: This includes costs related to utilities, rent, and equipment maintenance. It is crucial for buyers to inquire about how these overheads are calculated and their impact on the final price.
-
Tooling: Tooling costs encompass the equipment needed for production. Custom tooling can lead to higher initial costs but may reduce long-term expenses through enhanced efficiency.
-
Quality Control (QC): Implementing strict QC measures ensures the machines meet safety and operational standards. Although this can increase upfront costs, it ultimately leads to lower maintenance and operational costs.
-
Logistics: Shipping and handling costs should not be overlooked, especially for international buyers. Factors such as distance, shipping methods, and packaging can significantly influence overall expenses.
-
Margin: Manufacturers typically apply a profit margin to cover their operational costs and ensure sustainability. Understanding the margin can help buyers gauge the fairness of the quoted prices.
How Do Price Influencers Affect Filling Machine Costs?
Several factors can influence the pricing of filling machines, including:
-
Volume and Minimum Order Quantity (MOQ): Purchasing in bulk often results in lower per-unit costs. Buyers should negotiate MOQs that align with their operational needs.
-
Specifications and Customization: Customized machines tailored to specific production requirements usually come at a premium. Buyers should weigh the benefits of customization against their budget constraints.
-
Material Quality and Certifications: Higher quality materials and certified machines (such as ISO standards) can increase costs but also enhance longevity and performance, making them a worthwhile investment.
-
Supplier Factors: The reputation and reliability of suppliers can affect pricing. Established manufacturers may charge more but offer better quality assurance and service.
-
Incoterms: Understanding Incoterms is vital for international transactions. They define the responsibilities of buyers and sellers, influencing shipping costs and risk management.
What Tips Can Help International B2B Buyers Optimize Costs?
For international B2B buyers, particularly from regions like Africa, South America, the Middle East, and Europe, here are some actionable tips:
-
Negotiate Effectively: Leverage your purchasing power. Discuss pricing openly and explore options for discounts or better payment terms based on your order volume.
-
Focus on Total Cost of Ownership (TCO): Rather than just considering the purchase price, evaluate the TCO, including maintenance, energy costs, and potential downtimes. This approach can lead to more cost-effective long-term decisions.
-
Understand Pricing Nuances: Be aware that pricing can vary significantly based on regional economic conditions, currency fluctuations, and import tariffs. Stay informed about these factors to avoid unexpected costs.
-
Request Detailed Quotes: Ensure that quotes include a breakdown of costs associated with materials, labor, and overhead. This transparency will help you make comparisons across different suppliers.
-
Consider Local Suppliers: Whenever feasible, explore local manufacturers. This can reduce logistics costs and lead to faster delivery times, enhancing overall supply chain efficiency.
Disclaimer on Indicative Prices
Prices for filling machines can vary widely based on specifications, regional factors, and market demand. Always seek updated quotes from multiple suppliers to ensure you have the most accurate and competitive pricing information.
Alternatives Analysis: Comparing Filling Machine Manufacturers With Other Solutions
Understanding Alternatives to Filling Machine Manufacturers
When evaluating filling solutions, international B2B buyers must consider various alternatives to traditional filling machine manufacturers. Each alternative presents unique benefits and drawbacks, making it essential to analyze these options thoroughly. This analysis aims to empower decision-makers from regions such as Africa, South America, the Middle East, and Europe to make informed purchasing choices.
Comparison Table of Filling Solutions
Comparison Aspect | Filling Machine Manufacturers | Manual Filling Systems | Semi-Automatic Filling Systems |
---|---|---|---|
Performance | High throughput, consistent filling | Variable output, labor-dependent | Moderate throughput, consistent with operator skill |
Cost | High initial investment, low long-term cost | Low initial cost, high labor costs | Moderate initial investment, moderate operational costs |
Ease of Implementation | Requires professional setup and training | Simple to implement | Requires training but less complex than fully automated systems |
Maintenance | Requires regular maintenance and skilled technicians | Minimal maintenance | Moderate maintenance needs, can be managed by trained staff |
Best Use Case | High-volume production lines | Small batches or artisanal products | Medium to high-volume production with flexibility |
Detailed Breakdown of Alternatives
What Are the Pros and Cons of Manual Filling Systems?
Manual filling systems are ideal for smaller operations or artisanal producers who require flexibility and lower initial costs. These systems rely on labor for filling products, which can lead to variability in output and quality. While the initial investment is low, ongoing labor costs can accumulate, especially in regions where wages are rising. This method is best suited for niche markets or startups that prioritize craftsmanship over speed.
How Do Semi-Automatic Filling Systems Compare?
Semi-automatic filling systems bridge the gap between manual labor and fully automated machines. They offer moderate throughput and require some operator skill, making them suitable for businesses looking to scale production without a significant investment in fully automated systems. The initial costs are higher than manual systems but lower than fully automated solutions, providing a balanced approach for medium-sized enterprises. Maintenance is also manageable, allowing businesses to keep operational costs in check.
Conclusion: How to Choose the Right Filling Solution for Your Business
Choosing the right filling solution depends on various factors, including production volume, budget, and the specific needs of your business. For high-volume operations, investing in filling machine manufacturers may be the best option due to their efficiency and consistency. In contrast, smaller businesses might benefit from manual systems for their cost-effectiveness and flexibility. Semi-automatic systems offer a middle ground, providing a blend of efficiency and lower costs. By carefully assessing these alternatives and aligning them with your operational goals, you can make a decision that enhances productivity and profitability in your enterprise.
Essential Technical Properties and Trade Terminology for Filling Machine Manufacturers
When considering filling machines for your production line, understanding essential technical properties and trade terminology is crucial. This knowledge not only aids in making informed purchasing decisions but also ensures that the equipment meets your specific operational needs.
What Are the Key Technical Properties of Filling Machines?
1. Material Grade
The material grade of a filling machine, typically stainless steel or food-grade plastic, is pivotal for durability and compliance with safety regulations. High-grade materials resist corrosion and contamination, making them essential in sectors like food and pharmaceuticals. Choosing the right material can significantly extend the lifespan of your equipment and minimize maintenance costs.
2. Tolerance
Tolerance refers to the allowable deviation in the filling volume. It is crucial for ensuring product consistency and compliance with regulatory standards. For instance, in pharmaceutical applications, maintaining strict tolerances is vital for dosage accuracy. Understanding the tolerance levels of filling machines helps buyers avoid costly penalties and product recalls.
3. Speed and Efficiency
The speed at which a filling machine operates is a key factor for production efficiency. Measured in bottles or containers per minute, a machine’s speed can affect overall productivity. Buyers should assess their production demands and choose a machine that aligns with their operational goals without sacrificing quality.
4. Automation Level
The level of automation in a filling machine affects labor costs and operational efficiency. Machines with higher automation can reduce the need for manual intervention, which is particularly beneficial in high-volume production environments. Understanding the degree of automation necessary for your operations can help in selecting the most suitable equipment.
5. Compatibility with Different Container Types
Filling machines vary in their ability to handle different container types and sizes. Understanding the range of compatibility is essential for businesses that offer diverse product lines. A machine that can easily adapt to various containers can provide significant flexibility and reduce the need for multiple machines.
Which Trade Terms Should B2B Buyers Know?
What Does OEM Mean in the Filling Machine Industry?
OEM stands for Original Equipment Manufacturer. This term refers to companies that produce parts and equipment that may be marketed by another manufacturer. Understanding OEM relationships is important for buyers seeking reliable components and service support.
Why Is MOQ Important for Filling Machine Purchases?
MOQ, or Minimum Order Quantity, is the smallest number of units a supplier is willing to sell. This term is vital for buyers to understand as it affects inventory management and budgeting. Knowing the MOQ can help businesses negotiate better deals and avoid excess stock.
How to Use RFQ Effectively When Sourcing Filling Machines?
RFQ stands for Request for Quotation. It is a standard business process used to invite suppliers to submit price proposals. Buyers should clearly outline their requirements in an RFQ to receive accurate quotes, which can streamline the decision-making process.
What Are Incoterms and Why Do They Matter?
Incoterms, or International Commercial Terms, define the responsibilities of buyers and sellers in international trade. Familiarity with these terms is crucial for understanding shipping costs, risk transfer, and delivery timelines, especially for buyers sourcing machines from overseas.
What Is the Importance of Lead Time in Equipment Procurement?
Lead time refers to the amount of time it takes from placing an order until it is delivered. Understanding lead times is essential for production planning and inventory management. Buyers should factor lead times into their schedules to avoid production delays.
By grasping these essential technical properties and trade terms, international B2B buyers can make more informed decisions when procuring filling machines, ultimately enhancing their operational efficiency and competitiveness in the market.
Navigating Market Dynamics and Sourcing Trends in the Filling Machine Manufacturers Sector
What Are the Current Market Dynamics for Filling Machine Manufacturers?
The global filling machine market is experiencing significant transformation driven by technological advancements, changing consumer preferences, and the need for efficiency in manufacturing processes. Key trends include automation and smart technology integration, which enhance operational efficiency and reduce labor costs. For international B2B buyers, particularly in regions like Africa, South America, the Middle East, and Europe, understanding these dynamics is crucial for making informed purchasing decisions.
Emerging technologies such as IoT-enabled machines allow manufacturers to monitor production in real-time, improving accuracy and reducing waste. Additionally, the shift towards sustainable packaging solutions is influencing the types of filling machines being developed and sourced. For instance, manufacturers are increasingly focusing on machines that can handle biodegradable materials and flexible packaging options. Buyers should consider suppliers that are investing in these technologies to ensure they remain competitive.
Moreover, the market is seeing an uptick in demand for customized filling solutions tailored to specific industry needs, such as food and beverage, pharmaceuticals, and cosmetics. This trend opens opportunities for buyers to collaborate closely with manufacturers to develop bespoke solutions that meet their unique operational requirements.
How Is Sustainability Shaping Sourcing Trends in the Filling Machine Sector?
Sustainability is becoming a cornerstone of sourcing strategies in the filling machine manufacturing sector. Environmental impacts associated with traditional manufacturing processes have prompted buyers to seek out suppliers that prioritize eco-friendly practices. This includes the use of sustainable materials, energy-efficient machinery, and waste reduction strategies throughout the production process.
For B2B buyers, the importance of ethical supply chains cannot be overstated. Suppliers that are transparent about their sourcing practices and demonstrate a commitment to sustainability are more likely to build long-term partnerships. Certifications such as ISO 14001 for environmental management and other ‘green’ certifications are indicators of a supplier’s commitment to sustainability. These certifications not only enhance the credibility of suppliers but also provide buyers with the assurance that they are engaging in responsible sourcing.
Moreover, the demand for sustainable filling solutions is not limited to the materials used but extends to the machinery itself. Buyers should look for filling machines designed to minimize energy consumption and optimize resource use, as these features can significantly lower operational costs in the long run.
What Is the Historical Context of the Filling Machine Industry?
The filling machine industry has evolved significantly since its inception in the early 20th century. Initially dominated by manual processes, the sector began to adopt mechanical solutions in response to increasing production demands during the industrial revolution. By the mid-20th century, advancements in automation transformed filling machines into sophisticated equipment capable of handling high volumes efficiently.
As technology continued to progress, the late 20th and early 21st centuries saw the introduction of computerized controls and robotics, allowing for greater precision and flexibility in production. This evolution has paved the way for current trends in smart manufacturing and sustainability, positioning filling machine manufacturers at the forefront of innovation. For international B2B buyers, understanding this historical context can provide valuable insights into the capabilities and reliability of current machinery, aiding in more strategic sourcing decisions.
Frequently Asked Questions (FAQs) for B2B Buyers of Filling Machine Manufacturers
-
How do I choose the right filling machine for my business needs?
Selecting the appropriate filling machine involves assessing your product type, viscosity, and production volume. Start by identifying whether your product is liquid, powder, or granulated, as each requires different filling technologies (e.g., volumetric, gravimetric). Additionally, consider the speed and efficiency required for your production line. Consult with manufacturers to discuss your specific needs and request samples to ensure compatibility with your product. -
What are the key features to look for in a filling machine?
Essential features to consider include versatility for different container sizes, ease of cleaning, automation level, and integration capabilities with existing production lines. Look for machines that offer adjustable filling volumes, user-friendly interfaces, and robust construction for durability. Safety features, such as emergency stops and guards, are also crucial for ensuring a safe working environment. -
How can I ensure the quality of filling machines from international suppliers?
To guarantee quality, conduct thorough research on potential suppliers by checking their certifications (ISO, CE), customer reviews, and case studies. Request references and reach out to other businesses that have sourced machines from them. Additionally, consider visiting their manufacturing facility or arranging virtual inspections. Quality assurance processes should be transparent, and you may also want to inquire about warranty and after-sales support. -
What are the common payment terms for international B2B transactions?
Payment terms can vary widely, but common options include advance payment, letter of credit, or payment upon delivery. It’s essential to negotiate terms that protect both parties. For larger orders, a staggered payment approach may be beneficial, allowing you to make partial payments based on milestones or delivery phases. Always ensure that payment terms are clearly outlined in the contract to avoid disputes. -
What is the minimum order quantity (MOQ) when sourcing filling machines?
The MOQ can differ significantly among manufacturers, often influenced by the machine type and complexity. Some manufacturers may have a MOQ of one unit for standard machines, while others may require larger quantities for customized solutions. Discuss your requirements with potential suppliers and be open to negotiation, especially if you are willing to consider standard options that align with their production runs. -
How do I handle logistics and shipping when importing filling machines?
Logistics planning involves coordinating with your supplier and a reliable freight forwarder. Discuss shipping options, including air or sea freight, based on your urgency and budget. Ensure that all necessary import documentation is prepared in advance, including customs clearance paperwork. Familiarize yourself with local regulations and taxes related to importing machinery to avoid unexpected costs and delays. -
What are the customization options available for filling machines?
Many manufacturers offer customization based on specific production needs. Customizations may include adjustments to filling volume, speed, nozzle types, and additional features like capping and labeling systems. When discussing your needs with suppliers, be clear about your production requirements and ask for examples of previous custom projects to gauge their capabilities. -
How can I ensure compliance with international standards when using filling machines?
Compliance with international standards is critical for quality and safety. Familiarize yourself with the regulations applicable in your region, such as GMP (Good Manufacturing Practices) and HACCP (Hazard Analysis Critical Control Point). Work with suppliers who provide documentation proving compliance with these standards. Regular audits and employee training on best practices can further ensure ongoing compliance.
Important Disclaimer & Terms of Use
⚠️ Important Disclaimer
The information provided in this guide, including content regarding manufacturers, technical specifications, and market analysis, is for informational and educational purposes only. It does not constitute professional procurement advice, financial advice, or legal advice.
While we have made every effort to ensure the accuracy and timeliness of the information, we are not responsible for any errors, omissions, or outdated information. Market conditions, company details, and technical standards are subject to change.
B2B buyers must conduct their own independent and thorough due diligence before making any purchasing decisions. This includes contacting suppliers directly, verifying certifications, requesting samples, and seeking professional consultation. The risk of relying on any information in this guide is borne solely by the reader.
Strategic Sourcing Conclusion and Outlook for Filling Machine Manufacturers
In the ever-evolving landscape of filling machine manufacturing, strategic sourcing remains crucial for international B2B buyers. By prioritizing partnerships with reliable manufacturers, buyers can not only ensure the quality and efficiency of their production processes but also gain access to innovative technologies that can enhance their operational capabilities. Key takeaways include evaluating suppliers based on their technological advancements, production capacity, and adherence to international quality standards, which are particularly important for markets in Africa, South America, the Middle East, and Europe.
Furthermore, understanding regional market dynamics and regulatory requirements can empower buyers to make informed decisions that align with their business objectives. The outlook for filling machine manufacturers is optimistic, with increasing demand for sustainable and automated solutions driving growth across various sectors.
As you navigate your sourcing strategy, consider leveraging digital platforms and trade shows to connect with potential suppliers and industry peers. This proactive approach will not only streamline your procurement process but also position your business for long-term success in a competitive market. Engage with manufacturers today to explore how they can meet your unique filling needs and drive your business forward.