Improve Quality & Cut Costs with a Hardware Supplier Guide (2025)
Introduction: Navigating the Global Market for hardware supplier
Navigating the complexities of the global market for hardware suppliers can be a daunting task for international B2B buyers, especially when sourcing essential components like industrial machinery or electronic devices. The challenge lies not only in identifying reliable suppliers but also in ensuring that they meet specific quality standards, compliance regulations, and cost-effectiveness. This guide aims to demystify the hardware sourcing process by providing comprehensive insights into various types of hardware products, their applications across diverse industries, and effective supplier vetting techniques.
In this resource, you will explore key factors influencing hardware procurement decisions, including market trends, pricing strategies, and logistical considerations. We delve into the nuances of different supplier categories, from manufacturers and distributors to wholesalers, and highlight how to assess their credibility and service levels. Additionally, we will cover cost analysis techniques to help you optimize your purchasing budget without compromising on quality.
By empowering B2B buyers from Africa, South America, the Middle East, and Europe—such as Spain and Poland—with actionable knowledge and strategic frameworks, this guide equips you to make informed purchasing decisions. Whether you are looking for bulk purchasing options or specialized equipment, understanding the global landscape of hardware suppliers is essential for successful procurement in today’s interconnected marketplace.
Understanding hardware supplier Types and Variations
Type Name | Key Distinguishing Features | Primary B2B Applications | Brief Pros & Cons for Buyers |
---|---|---|---|
OEM Suppliers | Produce hardware components for other brands | Manufacturing, Technology | Pros: High-quality components; Cons: Limited customization. |
Distributors | Act as intermediaries, offering a wide range of brands | Retail, Construction, Industrial | Pros: Diverse product offerings; Cons: Potential for higher prices. |
Value-Added Resellers | Provide additional services like installation and support | IT Solutions, Telecommunications | Pros: Enhanced service offerings; Cons: May have higher costs. |
Direct Manufacturers | Sell products directly to businesses without intermediaries | Large Scale Production, Custom Solutions | Pros: Better pricing; Cons: Limited product variety. |
Specialty Suppliers | Focus on niche markets or specific hardware types | Specialized Industries, Custom Manufacturing | Pros: Tailored solutions; Cons: Limited scalability. |
What Are the Key Characteristics of OEM Suppliers?
OEM (Original Equipment Manufacturer) suppliers are crucial for businesses that require high-quality hardware components. They produce parts that are then branded and sold by other companies. For B2B buyers, OEM suppliers are ideal when quality and reliability are paramount, as they often adhere to strict manufacturing standards. However, buyers should consider that customization options may be limited, which could affect product differentiation.
How Do Distributors Serve B2B Buyers?
Distributors play a vital role in the supply chain by acting as intermediaries between manufacturers and end-users. They offer a wide range of products from various brands, making it easier for businesses to source multiple items from a single supplier. This variety is beneficial for B2B buyers looking for convenience and choice. However, buyers may encounter higher prices due to the added costs of distribution.
What Advantages Do Value-Added Resellers Offer?
Value-added resellers (VARs) enhance the basic offerings of hardware suppliers by providing additional services such as installation, support, and customization. This can be particularly advantageous for businesses that lack the technical expertise to implement hardware solutions. While VARs can deliver significant added value, their services may come at a premium, so buyers should weigh the benefits against potential costs.
Why Choose Direct Manufacturers for Purchases?
Direct manufacturers sell their products straight to businesses, eliminating intermediaries. This can result in better pricing and direct access to the latest products. For B2B buyers, working directly with manufacturers can also facilitate better communication regarding product specifications and customization. However, buyers might find a narrower range of products compared to distributors.
What Are the Benefits of Specialty Suppliers?
Specialty suppliers focus on niche markets or specific types of hardware, catering to businesses with unique needs. They often provide tailored solutions that are not available from larger suppliers, making them invaluable for specialized industries. However, buyers should be mindful that specialty suppliers may have limited scalability, which could impact supply in the long term.
Related Video: Heat Pump Thermostat O, B, and C Terminal Variations Explained
Key Industrial Applications of hardware supplier
Industry/Sector | Specific Application of hardware supplier | Value/Benefit for the Business | Key Sourcing Considerations for this Application |
---|---|---|---|
Manufacturing | Production Line Equipment | Increased efficiency and reduced downtime | Quality standards, supplier reliability, and lead times |
Construction | Heavy Machinery and Tools | Enhanced productivity and safety on job sites | Equipment durability, maintenance support, and warranties |
Information Technology | Computer Hardware and Networking Equipment | Improved data processing and communication capabilities | Compatibility, scalability, and support services |
Retail | Point of Sale (POS) Systems | Streamlined transactions and inventory management | Integration with existing systems and cost-effectiveness |
Telecommunications | Communication Infrastructure Equipment | Enhanced connectivity and service delivery | Technology compatibility and long-term support |
How is hardware supplier used in the manufacturing sector?
In the manufacturing sector, hardware suppliers provide critical production line equipment such as conveyor belts, robotics, and assembly tools. These components enhance efficiency by automating processes, which significantly reduces downtime and labor costs. For international B2B buyers, especially from Africa and South America, it’s essential to consider the quality standards and certifications of the equipment to ensure compliance with local regulations. Additionally, suppliers should offer reliable after-sales support and spare parts availability.
What role does hardware supplier play in construction projects?
In the construction industry, hardware suppliers are vital for providing heavy machinery and tools, including cranes, excavators, and safety equipment. These tools not only boost productivity but also enhance worker safety on job sites. Buyers from the Middle East and Europe, such as Spain and Poland, should prioritize sourcing durable equipment that can withstand harsh conditions. Moreover, understanding the warranty terms and maintenance support offered by suppliers is crucial for long-term project success.
How does hardware supplier impact the information technology sector?
In the information technology sector, hardware suppliers deliver essential components like servers, networking devices, and computer hardware. These products are pivotal for improving data processing, storage, and communication capabilities within organizations. For B2B buyers in Europe, sourcing equipment that is compatible with existing systems and scalable for future needs is crucial. Additionally, evaluating the supplier’s support services can ensure minimal disruption to business operations.
Why are hardware suppliers important for retail businesses?
Retail businesses rely on hardware suppliers for Point of Sale (POS) systems, which streamline transactions and inventory management. These systems enhance customer service and operational efficiency, making them indispensable for modern retail operations. Buyers from South America and Africa should focus on suppliers that offer cost-effective solutions and integration capabilities with existing retail systems. It’s also beneficial to consider suppliers that provide training and technical support for their products.
How does hardware supplier enhance telecommunications infrastructure?
In the telecommunications sector, hardware suppliers provide equipment that supports communication infrastructure, such as routers, switches, and transmission devices. This equipment is essential for enhancing connectivity and ensuring reliable service delivery. International buyers, particularly from Africa and the Middle East, should assess the technology compatibility of the hardware with current systems and the long-term support offered by suppliers. This ensures that the infrastructure can adapt to future technological advancements and increasing demand.
Related Video: Applications and Uses of Computer
3 Common User Pain Points for ‘hardware supplier’ & Their Solutions
Scenario 1: Difficulty in Finding Reliable Hardware Suppliers
The Problem: One of the primary challenges faced by B2B buyers, especially in regions like Africa and South America, is sourcing reliable hardware suppliers. Many suppliers may present themselves as reputable but fail to deliver on quality or timelines. This can lead to significant project delays, increased costs, and even reputational damage for businesses relying on timely hardware delivery. Buyers often feel overwhelmed by the sheer volume of options and the risk of poor supplier performance, which can hinder their ability to make informed purchasing decisions.
The Solution: To navigate this challenge, international buyers should invest time in thorough research and vetting processes. Start by leveraging platforms such as industry-specific forums or trade networks to gather feedback on potential suppliers. Establish criteria for evaluation, such as years in business, past project references, and certifications. Additionally, consider engaging in small pilot projects before committing to large orders. This phased approach allows buyers to assess product quality and supplier reliability without significant upfront investment. Furthermore, maintaining open lines of communication with suppliers can foster transparency and trust, which is crucial for long-term partnerships.
Scenario 2: Inadequate Technical Support and After-Sales Service
The Problem: Once a purchase is made, the lack of adequate technical support and after-sales service can be a significant pain point for B2B buyers. This is particularly crucial in regions like the Middle East and Europe, where buyers expect timely assistance for hardware issues that may arise. A supplier’s inability to provide effective support can lead to prolonged downtimes, impacting productivity and operational efficiency. Buyers often feel stranded, leading to frustration and dissatisfaction with their supplier relationships.
The Solution: To mitigate this issue, buyers should prioritize selecting suppliers that offer comprehensive after-sales support as part of their service package. Before finalizing a deal, inquire about the supplier’s support services, including response times for technical inquiries and availability of on-site assistance. Buyers should also seek out suppliers that provide extensive documentation and online resources for troubleshooting. Establishing a clear service level agreement (SLA) can further protect buyers by outlining expected response times and support processes. Regular check-ins with suppliers can also help address issues proactively, ensuring that any potential problems are resolved before they escalate.
Scenario 3: Uncertainty in Product Specifications and Compatibility
The Problem: Another prevalent issue for B2B buyers is the uncertainty surrounding product specifications and compatibility with existing systems. This is especially relevant for companies in diverse markets like Europe and Africa, where hardware needs may vary significantly based on infrastructure and technological environments. Misunderstandings regarding product capabilities can lead to costly mistakes, including purchasing the wrong hardware or equipment that doesn’t integrate well with current systems.
The Solution: To overcome this challenge, buyers should engage in detailed discussions with suppliers regarding their specific needs and existing setups. Create a comprehensive list of requirements, including compatibility needs, performance expectations, and any regulatory standards applicable in your region. Request detailed product specifications and documentation to ensure clarity. Additionally, consider asking for sample units or conducting compatibility tests before making bulk purchases. This due diligence helps ensure that the hardware not only meets your specifications but also integrates seamlessly into your operations, minimizing the risk of costly errors and ensuring smooth functionality.
Strategic Material Selection Guide for hardware supplier
When selecting materials for hardware applications, international B2B buyers must consider a range of factors, including performance characteristics, cost, and compliance with regional standards. Below, we analyze four common materials used in hardware supply, highlighting their key properties, advantages, disadvantages, and specific considerations for buyers from Africa, South America, the Middle East, and Europe.
What Are the Key Properties of Steel in Hardware Applications?
Steel is one of the most widely used materials in hardware due to its strength and versatility. Key properties include high tensile strength, excellent ductility, and good weldability. Steel can withstand high temperatures and pressures, making it suitable for various applications, including structural components and fasteners.
Pros and Cons:
– Pros: Durable, cost-effective, and widely available. Steel components can be easily manufactured and customized.
– Cons: Prone to corrosion if not treated, which may require additional coatings or finishes. Heavier than alternative materials, which can impact shipping costs.
Impact on Application:
Steel is compatible with a range of media, including water and oil, but may not be suitable for corrosive environments without proper treatment.
Considerations for International Buyers:
Buyers should ensure compliance with regional standards such as ASTM (American Society for Testing and Materials) or DIN (Deutsches Institut für Normung) to guarantee quality and safety.
How Does Aluminum Compare as a Material for Hardware?
Aluminum is known for its lightweight and corrosion-resistant properties. It has a lower density than steel, which makes it an excellent choice for applications where weight savings are critical, such as in aerospace and automotive components.
Pros and Cons:
– Pros: Lightweight, good corrosion resistance, and excellent thermal conductivity. Aluminum can be anodized for enhanced surface protection.
– Cons: Generally more expensive than steel and has lower tensile strength, which may limit its use in high-stress applications.
Impact on Application:
Aluminum is compatible with various media, including water and air, but may not be suitable for high-temperature applications without specific alloys.
Considerations for International Buyers:
Buyers should be aware of the specific aluminum grades and their corresponding certifications, such as JIS (Japanese Industrial Standards), to ensure compliance with local regulations.
What Are the Benefits of Using Plastic in Hardware Manufacturing?
Plastics, such as polycarbonate and nylon, are increasingly used in hardware due to their versatility and resistance to corrosion. They are lightweight and can be molded into complex shapes, making them ideal for intricate designs.
Pros and Cons:
– Pros: Corrosion-resistant, lightweight, and cost-effective for mass production. Plastics can also be insulated, making them suitable for electrical applications.
– Cons: Limited temperature resistance and potential for degradation under UV light unless treated.
Impact on Application:
Plastics are compatible with a wide range of media, including chemicals and moisture, but may not be suitable for high-temperature or high-stress applications.
Considerations for International Buyers:
Buyers should verify that the plastics used meet relevant safety and environmental standards, such as REACH (Registration, Evaluation, Authorisation and Restriction of Chemicals) in Europe.
How Does Copper Stand Out as a Material for Electrical Hardware?
Copper is renowned for its electrical conductivity and is often used in electrical hardware applications, including wiring and connectors. It also has good thermal conductivity and resistance to corrosion.
Pros and Cons:
– Pros: Excellent electrical and thermal conductivity, durable, and resistant to corrosion. Copper can be easily soldered and formed.
– Cons: Higher cost compared to other metals and may require protective coatings to prevent oxidation.
Impact on Application:
Copper is ideal for electrical applications but may not be suitable for environments with aggressive chemicals without proper treatment.
Considerations for International Buyers:
Buyers should ensure compliance with international electrical standards, such as IEC (International Electrotechnical Commission) standards, to guarantee safety and reliability.
Summary Table of Material Selection for Hardware Supply
Material | Typical Use Case for hardware supplier | Key Advantage | Key Disadvantage/Limitation | Relative Cost (Low/Med/High) |
---|---|---|---|---|
Steel | Structural components, fasteners | High strength and durability | Prone to corrosion without treatment | Medium |
Aluminum | Aerospace, automotive components | Lightweight and corrosion-resistant | More expensive and lower tensile strength | High |
Plastic | Insulation, intricate designs | Cost-effective and versatile | Limited temperature resistance | Low |
Copper | Electrical wiring and connectors | Excellent conductivity | Higher cost and oxidation risk | Medium |
This guide aims to equip international B2B buyers with the knowledge necessary to make informed decisions regarding material selection for hardware applications, ensuring compliance with regional standards and optimizing performance for their specific needs.
In-depth Look: Manufacturing Processes and Quality Assurance for hardware supplier
What Are the Main Stages of the Manufacturing Process for Hardware Suppliers?
When sourcing hardware from international suppliers, understanding the manufacturing process is crucial for ensuring product quality and reliability. The typical manufacturing process can be broken down into four main stages: material preparation, forming, assembly, and finishing.
-
Material Preparation: This initial stage involves selecting the right materials based on the specifications of the hardware product. Suppliers often utilize advanced techniques like computer-aided design (CAD) to ensure precise material dimensions. This phase may also include sourcing raw materials that meet specific standards, such as those outlined in ISO certifications, to ensure consistency and quality.
-
Forming: In this stage, raw materials are shaped into the desired components. Common techniques include machining, stamping, and injection molding. Each method has its own advantages; for instance, injection molding is highly efficient for producing complex shapes at high volumes, while machining provides greater precision for critical components.
-
Assembly: After the components are formed, they are assembled into the final product. This can involve manual or automated processes, depending on the complexity of the hardware. Automation is becoming increasingly popular, especially for high-volume production runs, as it reduces labor costs and increases consistency.
-
Finishing: The final stage involves applying any necessary coatings, surface treatments, or inspections to ensure that the hardware meets quality standards. Techniques such as anodizing, painting, or plating can enhance corrosion resistance and improve aesthetics. This stage is critical for ensuring the product’s longevity and performance in its intended application.
How Is Quality Assurance Implemented in Hardware Manufacturing?
Quality assurance (QA) is a systematic process that ensures products meet specified quality standards throughout the manufacturing process. For international B2B buyers, understanding the QA measures in place is vital to mitigate risks associated with sourcing hardware.
-
International Standards: Many hardware suppliers adhere to international standards such as ISO 9001, which outlines the criteria for a quality management system. Compliance with these standards demonstrates a commitment to quality and continuous improvement. Additionally, industry-specific standards like CE marking for European products or API specifications for oil and gas components may also apply.
-
Quality Control Checkpoints: Effective quality control involves multiple checkpoints throughout the manufacturing process, including:
– Incoming Quality Control (IQC): Inspecting raw materials upon arrival to ensure they meet specifications.
– In-Process Quality Control (IPQC): Monitoring the manufacturing process to catch defects early.
– Final Quality Control (FQC): Conducting thorough inspections of the finished product before shipment. -
Common Testing Methods: Hardware suppliers typically employ various testing methods to verify product quality, including:
– Functional Testing: Ensuring the product operates as intended.
– Durability Testing: Assessing how well the product withstands wear and tear.
– Safety Testing: Verifying compliance with safety standards relevant to the product category.
How Can B2B Buyers Verify Supplier Quality Control?
For international B2B buyers, verifying a supplier’s quality control processes is essential to ensure they receive products that meet their specifications and standards.
-
Supplier Audits: Conducting audits of potential suppliers can provide insights into their manufacturing processes and quality control measures. Buyers should look for transparency in operations, adherence to international standards, and evidence of previous successful audits.
-
Quality Control Reports: Requesting detailed quality control reports from suppliers can help buyers understand their QA processes. These reports should include information about testing methods, results, and any corrective actions taken in case of defects.
-
Third-Party Inspections: Engaging third-party inspection services can provide an unbiased assessment of the supplier’s quality control practices. These inspections can be scheduled at various stages of the manufacturing process to ensure compliance with agreed-upon standards.
What Are the Quality Control Nuances for International B2B Buyers?
Navigating the quality control landscape can be complex for B2B buyers, especially when sourcing from diverse regions like Africa, South America, the Middle East, and Europe. Here are some nuances to consider:
-
Cultural Differences: Different regions may have varying interpretations of quality standards and practices. Buyers should be aware of these cultural differences and adapt their expectations accordingly.
-
Documentation Requirements: Ensure that all necessary documentation, such as certificates of compliance, testing reports, and quality assurance documentation, is available and meets the legal requirements in both the buyer’s and supplier’s countries.
-
Regulatory Compliance: Different regions may have unique regulatory requirements that affect product quality. For example, European buyers must ensure that products comply with EU regulations, while Middle Eastern buyers may need to consider local standards.
-
Communication: Establishing clear communication channels with suppliers can help mitigate misunderstandings regarding quality expectations. Regular updates and feedback loops can foster a collaborative environment, leading to improved quality outcomes.
Conclusion
Understanding the manufacturing processes and quality assurance measures employed by hardware suppliers is critical for international B2B buyers. By focusing on the main stages of manufacturing, recognizing the importance of quality control, and actively verifying supplier practices, buyers can make informed decisions that align with their quality requirements. This proactive approach not only enhances product reliability but also fosters long-term partnerships with reputable suppliers across Africa, South America, the Middle East, and Europe.
Practical Sourcing Guide: A Step-by-Step Checklist for ‘hardware supplier’
In the competitive landscape of hardware procurement, having a well-structured sourcing strategy is vital for international B2B buyers. This step-by-step checklist is designed to help you navigate the complexities of sourcing hardware suppliers effectively, ensuring that you make informed decisions that align with your business needs.
Step 1: Define Your Technical Specifications
Before you start searching for suppliers, clarify your technical requirements. This includes the types of hardware you need, performance specifications, and compliance standards relevant to your industry.
– Key Considerations: Identify the specific features and functionalities your hardware must have to meet your operational goals.
Step 2: Research Potential Suppliers
Conduct thorough research to identify potential suppliers that meet your specifications. Utilize online platforms, industry forums, and trade publications to compile a list of candidates.
– Useful Tools: Leverage B2B marketplaces like Alibaba or ThomasNet, and consult reviews and ratings to gauge supplier reputation.
Step 3: Evaluate Supplier Certifications
It’s crucial to ensure that your suppliers hold the necessary certifications and comply with international standards. This helps mitigate risks related to quality and compliance.
– What to Look For: Check for ISO certifications, CE marking, and any industry-specific certifications that validate the supplier’s credibility.
Step 4: Request Samples or Prototypes
Before making a significant investment, request samples or prototypes of the hardware. This allows you to assess quality, compatibility, and performance in real-world applications.
– Testing Procedures: Conduct rigorous testing to ensure the hardware meets your specifications and performs reliably in your environment.
Step 5: Verify Supplier References
Reach out to previous clients of the supplier to gain insights into their experiences. Understanding how a supplier has performed with other businesses can provide valuable context.
– Questions to Ask: Inquire about delivery times, product quality, and the supplier’s responsiveness to issues or concerns.
Step 6: Negotiate Terms and Conditions
Once you’ve narrowed down your options, negotiate the terms of the contract. This includes pricing, delivery schedules, payment terms, and warranty conditions.
– Best Practices: Ensure that all agreements are documented clearly to avoid misunderstandings later on.
Step 7: Establish a Communication Plan
Effective communication is key to a successful partnership. Set up a communication plan that defines how and when you will interact with your supplier.
– Important Elements: Include regular check-ins, updates on order status, and protocols for addressing issues or changes in requirements.
By following this checklist, you can streamline your sourcing process and establish a reliable partnership with your hardware suppliers, paving the way for successful procurement and operational efficiency.
Comprehensive Cost and Pricing Analysis for hardware supplier Sourcing
What Are the Key Cost Components in Hardware Supplier Sourcing?
Understanding the cost structure of hardware suppliers is critical for B2B buyers aiming to optimize their procurement strategies. The primary cost components include:
-
Materials: The raw materials used in manufacturing hardware play a significant role in determining overall costs. Prices can fluctuate based on global market trends, making it essential for buyers to stay informed about material costs relevant to their specific needs.
-
Labor: The cost of labor varies significantly by region. For instance, suppliers in Europe may have higher labor costs compared to those in Africa or South America. Understanding these variances can help buyers negotiate better terms.
-
Manufacturing Overhead: This includes costs related to utilities, rent, and equipment maintenance. Buyers should inquire about overhead percentages to gauge how they impact the final price.
-
Tooling Costs: Custom tooling can be a significant upfront expense, particularly for specialized hardware. Buyers should evaluate whether these costs can be amortized over large orders to minimize the impact on unit pricing.
-
Quality Control (QC): Ensuring product quality often incurs additional costs. Suppliers may charge extra for rigorous QC processes, which are crucial for maintaining product standards.
-
Logistics: Shipping and handling costs can vary based on the supplier’s location and the chosen shipping method. Understanding these costs is essential, especially for international transactions.
-
Margin: Suppliers typically add a margin to cover risks and ensure profitability. Buyers should be aware of typical margins in the industry to assess whether they are receiving fair pricing.
How Do Price Influencers Affect Hardware Supplier Costs?
Several factors influence the pricing of hardware products, particularly in an international context:
-
Volume/MOQ (Minimum Order Quantity): Larger orders often lead to lower unit prices due to economies of scale. Buyers should consider combining orders with other businesses to meet MOQs and reduce costs.
-
Specifications and Customization: Custom specifications can significantly increase costs. Buyers should clearly outline their requirements to avoid unexpected charges.
-
Materials and Quality Certifications: Higher-quality materials and certifications (such as ISO or CE marking) often come at a premium. Understanding the necessity of these certifications for your market can help manage costs effectively.
-
Supplier Factors: The supplier’s reputation, reliability, and service levels can impact pricing. Established suppliers may charge more due to their perceived value.
-
Incoterms: The choice of Incoterms (International Commercial Terms) affects logistics and liability, influencing total costs. Buyers must understand these terms to negotiate better shipping arrangements.
What Buyer Tips Can Help Optimize Hardware Sourcing Costs?
When sourcing hardware suppliers, particularly from diverse regions like Africa, South America, the Middle East, and Europe, consider the following strategies:
-
Effective Negotiation: Engage suppliers in discussions about pricing and terms. Building a strong relationship can lead to better deals and discounts.
-
Focus on Total Cost of Ownership (TCO): Evaluate not just the purchase price but also long-term costs associated with maintenance, logistics, and disposal. This approach helps in making more informed sourcing decisions.
-
Understand Pricing Nuances: Different regions may have unique pricing strategies influenced by local market conditions. For example, suppliers in Spain may have different pricing structures compared to those in Poland or South Africa. Conducting thorough market research can reveal opportunities for cost savings.
-
Seek Multiple Quotes: Obtaining quotes from various suppliers can provide leverage in negotiations and help identify the most competitive offers.
Disclaimer on Indicative Prices
Please note that the prices mentioned in this analysis are indicative and subject to change based on market conditions, supplier negotiations, and other external factors. It is advisable for buyers to conduct their own market research and verify costs with suppliers directly.
Alternatives Analysis: Comparing hardware supplier With Other Solutions
When considering a hardware supplier, it’s crucial to explore alternative solutions that may better meet the specific needs of your business. This analysis will compare traditional hardware suppliers with two viable alternatives: cloud-based infrastructure solutions and custom-built hardware solutions. Each option presents distinct advantages and challenges that can significantly impact your organization’s performance, costs, and operational flexibility.
Comparison Table of Hardware Supplier vs Alternatives
Comparison Aspect | Hardware Supplier | Cloud-Based Infrastructure | Custom-Built Hardware |
---|---|---|---|
Performance | High, but hardware-dependent | Scalable, performance varies with provider | Tailored for specific needs, potentially very high |
Cost | Upfront capital expenditure; ongoing maintenance | Pay-as-you-go; potentially lower total cost of ownership | High initial development costs; long-term savings possible |
Ease of Implementation | Moderate; requires setup and integration | Quick setup; minimal IT overhead | High complexity; requires significant IT involvement |
Maintenance | Regular maintenance required; dependent on supplier | Minimal; managed by the service provider | Ongoing maintenance burden; may require specialized skills |
Best Use Case | Stable environments needing reliable hardware | Flexible, rapidly changing workloads | Specialized applications requiring unique hardware |
What Are the Advantages and Disadvantages of Cloud-Based Infrastructure Solutions?
Cloud-based infrastructure offers significant flexibility and scalability, allowing businesses to scale resources up or down based on demand. This is particularly advantageous for companies experiencing fluctuating workloads. The cost model is typically pay-as-you-go, which can lower the total cost of ownership compared to traditional hardware suppliers. However, performance can vary significantly based on the chosen provider, and businesses may face concerns regarding data security and compliance, particularly in regulated industries.
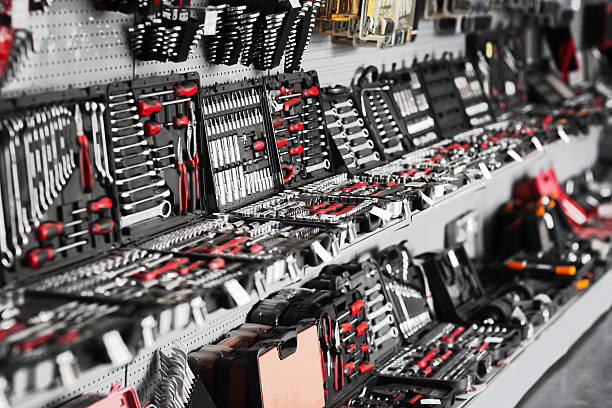
A stock image related to hardware supplier.
Why Consider Custom-Built Hardware Solutions?
Custom-built hardware solutions are ideal for organizations with very specific operational requirements that off-the-shelf products cannot meet. These solutions can be optimized for unique workloads, potentially delivering superior performance. However, the initial investment is often substantial, and ongoing maintenance can be resource-intensive. Companies must ensure they have the necessary expertise in-house or accessible to manage these systems effectively, which can add to operational costs.
How to Choose the Right Solution for Your Business Needs?
Selecting the right solution involves assessing your specific business needs, financial constraints, and technical capabilities. Companies should consider their workload patterns, budgetary limits, and the level of customization required. For organizations that require flexibility and scalability, cloud-based solutions may be more suitable. Conversely, those with specialized needs and the resources to manage complex systems might find that custom-built hardware offers the best long-term benefits.
In conclusion, while traditional hardware suppliers remain a viable option, exploring alternatives such as cloud-based infrastructure and custom-built hardware can provide B2B buyers with tailored solutions that better align with their operational requirements and strategic goals. Understanding the strengths and weaknesses of each option will empower decision-makers to choose the most appropriate technology for their organization.
Essential Technical Properties and Trade Terminology for hardware supplier
What Are the Essential Technical Properties for Hardware Suppliers?
Understanding the technical specifications of hardware products is crucial for B2B buyers. Here are some key properties that influence purchasing decisions:
1. Material Grade: Why Does It Matter?
Material grade refers to the classification of materials based on their mechanical and chemical properties. In hardware sourcing, this is vital as it affects durability, strength, and overall performance. For example, stainless steel has different grades (like 304 and 316), with 316 offering better corrosion resistance, making it ideal for marine applications. Buyers should specify the required material grade to ensure the product meets their operational needs.
2. Tolerance: How Does It Impact Product Quality?
Tolerance is the allowable deviation from a specified dimension in manufacturing. High precision in tolerances is critical for ensuring that parts fit and function correctly, especially in assembly processes. For instance, if a component is manufactured with a tolerance of ±0.01 mm, it can significantly affect the final product’s quality if the actual dimensions fall outside this range. Understanding tolerance levels helps buyers avoid costly rework and delays.
3. Surface Finish: What Role Does It Play in Functionality?
Surface finish describes the texture and smoothness of a material’s surface. A proper finish can enhance aesthetic appeal and functional properties, such as reducing friction or improving adhesion. For example, a polished finish on a metal part may be necessary for applications requiring minimal friction, while a rough finish might be better for components needing strong adhesion. Buyers should consider the required surface finish to match their application needs.
4. Load Capacity: How Is It Determined?
Load capacity indicates the maximum load a hardware component can support without failure. This property is especially important in structural applications, such as machinery or building components. Load capacity is determined by factors like material strength and design. Buyers must verify load capacities to ensure safety and reliability in their projects.
5. Coating and Plating: Why Are They Important?
Coatings and platings are applied to protect materials from corrosion and wear. For instance, zinc plating is often used for steel components to enhance corrosion resistance. Understanding the types of coatings available can help buyers select products that will last longer in specific environments, reducing maintenance costs and downtime.
What Trade Terms Should B2B Buyers Understand?
Familiarity with industry jargon can streamline communication and negotiations with suppliers. Here are some essential terms:
1. OEM (Original Equipment Manufacturer): What Does It Mean?
OEM refers to companies that produce parts or equipment that may be marketed by another manufacturer. In the hardware industry, working with OEMs can provide access to high-quality components tailored to specific needs. Buyers should seek OEM partnerships to ensure product reliability and quality.
2. MOQ (Minimum Order Quantity): How Does It Affect Purchases?
MOQ is the smallest quantity of a product that a supplier is willing to sell. Understanding MOQs is crucial for buyers to avoid overcommitting to inventory that may not be needed. Negotiating lower MOQs can help smaller businesses manage cash flow while still obtaining the necessary materials.
3. RFQ (Request for Quotation): Why Is It Essential?
An RFQ is a document issued by a buyer to solicit price quotes from suppliers. It typically includes specifications, quantities, and delivery requirements. Using an RFQ helps buyers compare different suppliers and make informed purchasing decisions.
4. Incoterms: How Do They Simplify International Trade?
Incoterms (International Commercial Terms) are a set of predefined commercial terms published by the International Chamber of Commerce. They clarify the responsibilities of buyers and sellers regarding shipping, insurance, and tariffs. Familiarity with Incoterms helps buyers avoid misunderstandings and ensure smooth international transactions.
5. Lead Time: What Should Buyers Consider?
Lead time is the time taken from placing an order to receiving the goods. Understanding lead times is essential for effective project planning. Buyers should factor in lead times when scheduling production or construction to avoid delays.
By grasping these technical properties and trade terminologies, international B2B buyers can make more informed decisions, ultimately leading to successful procurement strategies.
Navigating Market Dynamics and Sourcing Trends in the hardware supplier Sector
What Are the Current Market Dynamics and Sourcing Trends in the Hardware Supplier Sector?
The hardware supplier sector is experiencing significant transformation, driven by global technological advancements and changing consumer behaviors. Key trends include the increasing adoption of smart technologies and IoT devices, which are prompting suppliers to innovate continuously. Buyers from regions such as Africa, South America, the Middle East, and Europe (including countries like Spain and Poland) are increasingly focused on sourcing versatile, high-performance hardware that can integrate seamlessly with these technologies.
Emerging trends also point towards a shift in procurement practices, with more B2B buyers seeking direct relationships with manufacturers. This trend is largely fueled by the desire for enhanced transparency and reduced lead times. Additionally, the rise of digital platforms for procurement is reshaping traditional supply chains, making it easier for international buyers to compare prices and quality across borders. Buyers are encouraged to leverage these digital tools to optimize their sourcing strategies and gain competitive advantages.
Moreover, geopolitical factors and economic fluctuations are influencing market dynamics. For instance, trade agreements between regions can open up new opportunities for sourcing hardware at competitive prices. International buyers should stay informed about these developments to navigate potential risks and seize emerging opportunities effectively.
How Important Is Sustainability and Ethical Sourcing for B2B Hardware Suppliers?
Sustainability and ethical sourcing have become pivotal in the hardware supplier sector, reflecting the growing demand for environmentally responsible products. International buyers are increasingly aware of the environmental impact of their procurement choices, leading to a heightened focus on sourcing from suppliers that prioritize sustainability. This trend is particularly strong in Europe, where regulations around environmental standards are more stringent.
Buyers should consider suppliers that offer “green” certifications, such as Energy Star or RoHS compliance, which indicate adherence to environmental standards. Additionally, the use of recycled materials in hardware production is gaining traction, providing buyers with more sustainable options. By prioritizing ethical supply chains, companies can not only reduce their carbon footprint but also enhance their brand image and customer loyalty.
Furthermore, transparent supply chains are critical for ensuring ethical practices throughout the sourcing process. Buyers should engage suppliers that can provide clear information about their sourcing practices and labor conditions. This not only mitigates risks associated with unethical sourcing but also aligns with the values of socially conscious consumers.
How Has the Hardware Supplier Sector Evolved Over Time?
The hardware supplier sector has undergone substantial evolution over the decades, shaped by technological advancements and shifts in consumer demand. Initially dominated by traditional manufacturing practices, the sector has progressively embraced automation and digitalization, enhancing production efficiency and product quality.
The rise of personal computing in the late 20th century marked a significant turning point, leading to a surge in demand for various hardware components. As technology continued to advance, suppliers began diversifying their offerings to include not just basic components, but also integrated systems and smart devices. This evolution has paved the way for a more competitive landscape where innovation and adaptability are crucial for success.
In recent years, the impact of globalization has further transformed the sector, enabling suppliers to tap into international markets and establish cross-border partnerships. As international buyers increasingly seek high-quality, innovative solutions, understanding this historical context can provide valuable insights into current sourcing strategies and market dynamics.
Frequently Asked Questions (FAQs) for B2B Buyers of hardware supplier
-
How do I evaluate the credibility of a hardware supplier?
To assess the credibility of a hardware supplier, start by checking their business registration and certification credentials. Look for reviews and testimonials from previous clients, and consider contacting them for firsthand accounts. Additionally, verify their production capabilities and quality control processes. Engaging in direct communication with suppliers can also provide insights into their customer service approach and responsiveness, which are critical for long-term partnerships. -
What are the key factors to consider when choosing a hardware supplier?
When selecting a hardware supplier, consider factors such as product quality, reliability, lead times, and pricing. Additionally, assess their capacity to meet your specific needs, including customization options. It’s also essential to evaluate their logistics capabilities, including shipping times and costs, especially if you are sourcing internationally. Finally, ensure they have robust customer support and warranty policies, as these can significantly impact your purchasing experience. -
What is the minimum order quantity (MOQ) for hardware suppliers?
The MOQ varies widely among hardware suppliers and can depend on the type of product, manufacturing processes, and market demand. Some suppliers may have low MOQs to accommodate small businesses, while others may require larger orders to ensure cost-effectiveness. It’s advisable to communicate directly with potential suppliers to understand their MOQ policies and explore flexibility based on your specific needs. -
How can I customize hardware products from suppliers?
Many hardware suppliers offer customization options to meet specific business requirements. To initiate the process, clearly outline your customization needs, including design, dimensions, and material specifications. Discuss your requirements with the supplier to understand their capabilities and any additional costs involved. Request samples or prototypes to evaluate before placing a full order, ensuring the final product aligns with your expectations. -
What payment terms should I negotiate with a hardware supplier?
Payment terms can vary significantly between suppliers. Common options include upfront payments, net 30/60/90 days, or payment upon delivery. When negotiating, consider your cash flow and the supplier’s reputation. It may be beneficial to establish a payment schedule that aligns with your production and sales cycles. Always ensure that terms are documented in the contract to avoid misunderstandings later. -
How do I ensure quality assurance when sourcing hardware internationally?
To ensure quality assurance when sourcing hardware from international suppliers, implement a comprehensive vetting process. This includes requesting certifications, conducting factory audits, and requiring detailed quality control documentation. Utilize third-party inspection services to verify product quality before shipment. Establish clear quality expectations in your contract, and consider including penalties for non-compliance to encourage adherence to your standards.
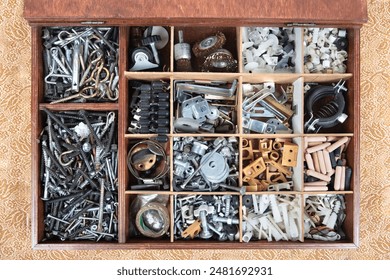
A stock image related to hardware supplier.
-
What logistics considerations are important for international hardware sourcing?
Logistics play a crucial role in international sourcing. Key considerations include shipping methods, lead times, customs regulations, and potential tariffs. Work closely with your supplier to understand their logistics capabilities and ensure they can meet your timelines. Additionally, partner with a reliable freight forwarder who can navigate the complexities of international shipping, including documentation and clearance processes. -
How can I build a long-term relationship with my hardware supplier?
Building a long-term relationship with your hardware supplier involves consistent communication and transparency. Regularly provide feedback on product performance and service quality to foster improvement. Engage in joint problem-solving for any issues that arise and explore opportunities for collaboration, such as co-developing new products. Demonstrating loyalty and reliability can encourage your supplier to prioritize your needs, leading to better pricing and service over time.
Important Disclaimer & Terms of Use
⚠️ Important Disclaimer
The information provided in this guide, including content regarding manufacturers, technical specifications, and market analysis, is for informational and educational purposes only. It does not constitute professional procurement advice, financial advice, or legal advice.
While we have made every effort to ensure the accuracy and timeliness of the information, we are not responsible for any errors, omissions, or outdated information. Market conditions, company details, and technical standards are subject to change.
B2B buyers must conduct their own independent and thorough due diligence before making any purchasing decisions. This includes contacting suppliers directly, verifying certifications, requesting samples, and seeking professional consultation. The risk of relying on any information in this guide is borne solely by the reader.
Strategic Sourcing Conclusion and Outlook for hardware supplier
What Are the Key Takeaways for B2B Buyers in Hardware Sourcing?
In an increasingly interconnected global market, strategic sourcing remains a critical component for B2B buyers seeking hardware suppliers. Understanding local market conditions, regulatory frameworks, and cultural nuances can significantly enhance procurement efficiency. Buyers should prioritize supplier relationships that offer transparency and reliability, as these factors are essential for fostering long-term partnerships. Moreover, leveraging technology for data analysis can streamline decision-making processes, enabling buyers to identify the best suppliers based on performance metrics and market trends.
How Can International B2B Buyers Position Themselves for Future Success?
As we look to the future, the importance of agility and adaptability in sourcing strategies cannot be overstated. Buyers from Africa, South America, the Middle East, and Europe must remain vigilant to emerging trends, such as sustainability and technological innovations, which are reshaping the hardware landscape. By proactively engaging with suppliers who align with these trends, businesses can not only enhance their competitive edge but also contribute to a more sustainable industry.
What Should You Do Next?
Now is the time for international B2B buyers to assess their sourcing strategies critically. Invest in building relationships with diverse suppliers, embrace digital tools for procurement, and stay informed about global market shifts. The path forward is ripe with opportunities; seizing them will require a commitment to strategic sourcing excellence.